Mount HONDA INTEGRA 1998 4.G Manual PDF
[x] Cancel search | Manufacturer: HONDA, Model Year: 1998, Model line: INTEGRA, Model: HONDA INTEGRA 1998 4.GPages: 1681, PDF Size: 54.22 MB
Page 744 of 1681
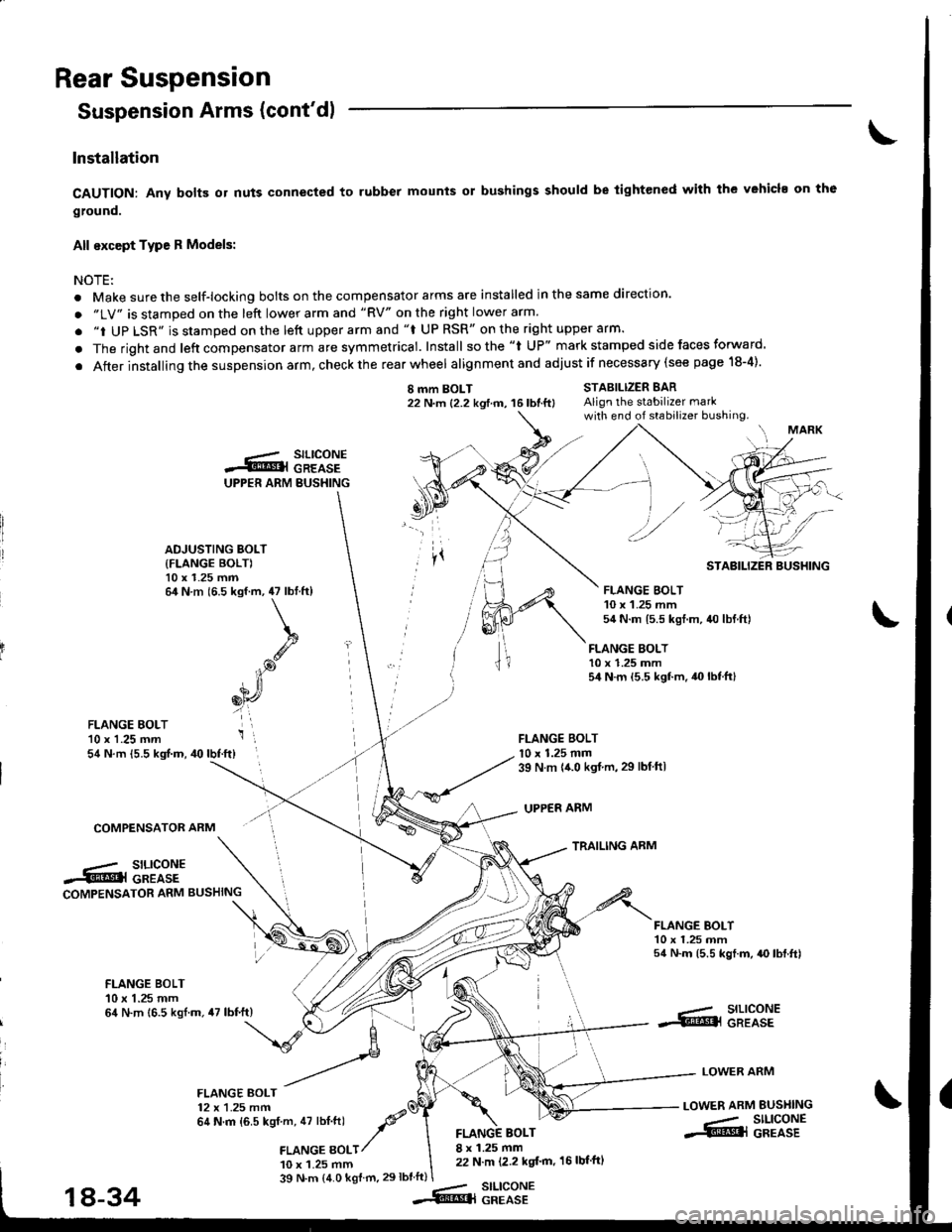
Rear Suspension
Suspension Arms (cont'dl
Installation
CAUTION: Any bolB or nuts connected to rubber mounts or bushings should be tightened with the vehicl. on th6
ground.
All except Type R Models:
NOTEi
. Make sure the self-locking bolts on the compensator arms are installed in the same direction.
. "LV" is stamped on the left lower arm and "RV" on the right lower arm.
. "i UP LSR" is stamped on the lett upper arm and "f UP RSR" on the right upper arm.
. The rightand left compensator arm are symmetrical. Install sothe "l UP" mark stamped side faces forward.
. After installing the suspension arm, check the rear wheel alignmentand adjust if necessary (see page 18-4).
I mm BOLT22 N.m {2.2 kgtm, 16lbtft}STABILIZER BARAlign the stabilizer markwith end of stabilizer bushing.
FLANGE BOLT10 x 1.25 mm54 N.m {5.5 kgf.m.40lbtft}
FLANGE BOLTl0 x 1.25 mm39 N m {{.0 kgt.m,29 lbtftl
UPPER ARM
TRAILING ARM
FLANGE EOLT'10 x 1.25 mm54 N.m {5.5 kgf.m, 40lbf.ft}
COMPENSATOR ARM
.-/ SILICONE.5tr@l GREASECOMPENSATOR ARM BUSHING
FLANGE BOI-T10 x 1.25 mm54 N.m (5.5 kgf.m, {O lbf.ft)
FLANGE BOLT10 x 1.25 mm64 N.m 16.5 kgl.m.47 lbf.ft)--- SILICONE.S!@l GREASE
LOWER ARM
LOWER ARM BUSI{ING
-- SILIGONE.S@l GREASE
FLANGE BOLT12 x 1.25 mm64 N.m {6.5 kgf m, 47 lbt.ftl -P'a
,amce gotr/
10 x 1.25 mm
BOLT8 x 1.25 mm22 N.m (2.2 kgt'm, 16 lbf'ftl
39 N.m (4.0 kgf m.29lbtft)stLtcoNEGREASE
UPPER ARM BUSHING
.-.- SILICONES@l GREASE
ADJUSTING BOLT
{FLANGE BOLT)10 x 1.25 mm64 N.m (6.5 kgf.m, 47 lbtft)
k
.g
iP
6[r,
i',
STABILIZER BUSHING
FLANGE BOLT10 x 1.25 mm54 N.m 15.5 kgt.m, 40 lbf.ftl
18-34--Rq
Page 745 of 1681
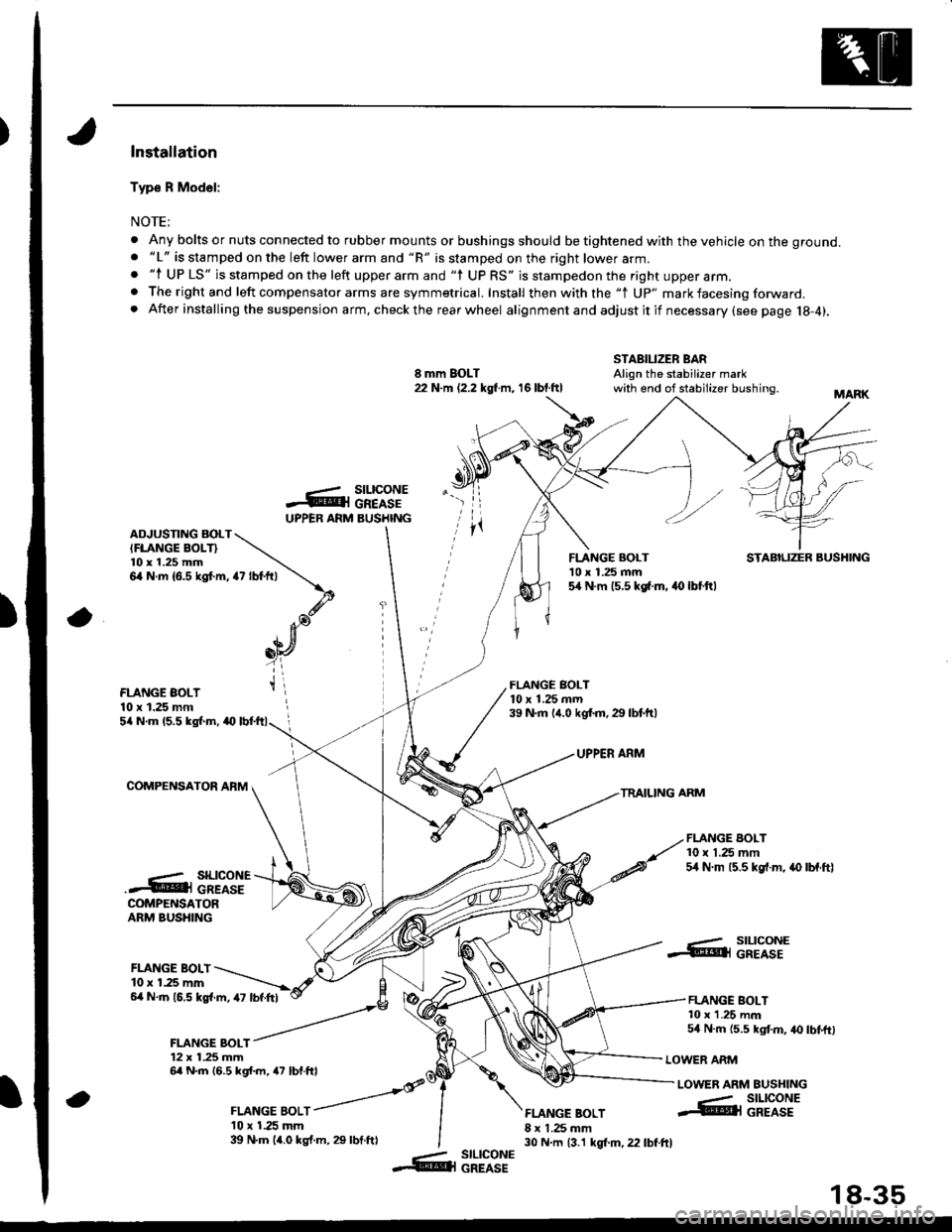
)Installation
Typ€ R Model:
NOTE;
. Any bolts or nuts connected to rubber mounts or bushings should be tightened with the vehicle on the ground.. "L" is stamped on the left lower arm and "R" is stamped on the right lower arm.. "l UP LS" is stamped on the left upper arm and "l UP RS" is stampedon the right upper arm.. The right and left compensator arms are symmetrical. Install then with the "1 Up" mark facesing forward. After installing the suspension arm, checkthe rearwheel alignmentand adjustitif necessary(see page 18-4).
8 mm BOLT22 N.m (2.2 kgl m, 16 lbt.ftl
STABILIZER BARAlign the stabilizer markwith end of stabilizer bushing.
-ArUPPEB ARM
rz tot+,t \
\.d'. Ja),n[
_oY
t\
a
stLtcoNEGREASEBUSHINGADJUSTING BOLTIFLANGE BOLT}l0 x 1.25 mm6,4 N.m {6.5 kgt m,
FLANGE BOLT'10 x 1.25 mm5,[ N.m 15.5 kg[.m. 40 lbt.ftl
STABILIZER BUSHING
FLANGE BOLT10 x 1.25 mm
FLANGE BOLT10 x 1.25 mrn39 N.m (,r.0 kgf.m.29 lbtftl5/a N.m 15.5 kgl.m, a0
COMPENSATOR AFM
UPPER ARM
TRAILING ARM
FLANGE BOLT10 x 1.25 mm54 N.m 15.5 kgf.m, .{) lbf.ftl..- SILICONE.4@i cREAsECOMPENSATORARM BUSHING
FLANGE BOLI10 r 1.25 mm6,4 N.m (6.5 kgl.m, 47 lbf.Itl
FLANGE BOLT12 x 1.25 mm6a N.m 16.5 kgl.m, a7 lbf.ftl
, ror"orr /
l0 x 1.25 mm39 N.m 14.0 kgf.m, 29 lbt.ftl
FLANGE BOLT8 x 1.25 mm30 N.m 13.1 kgt m, 22 lbf.ftl
..- SILICONE.@ll GREASE
FLANGE BOLT10 x 1.25 mm54 N.m {5.5 kgt m, 40 lbtftl
LOWER ARM
LOWER ARM EUSHING
a
--- SILICONE@l GREASE
-- slLlcoNE&l GREASE
18-35
Page 748 of 1681
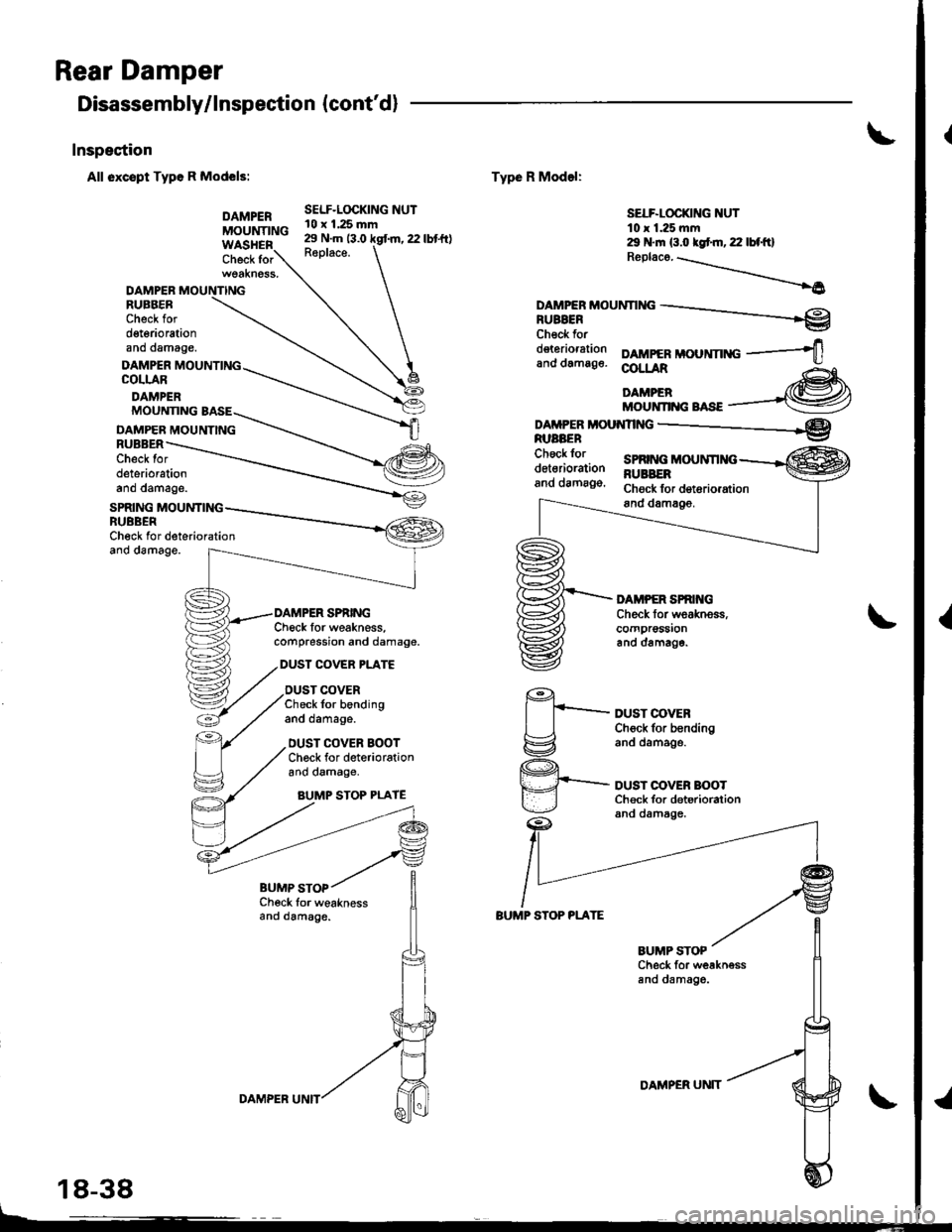
Rear Damper
Disassembly/lnspection {cont'd}
Inspestion
All oxcspt Typo R Models:
DAMPERMOUNTING
Check for
Check Ior weaknessand damag6.
DAMPERRUEBERCheck ford€t6riorationano damage.
DAMPER MOUNTINGCOLLAR
DAMPER
SELF.LOCKING NUT10 x 1.25 mm29 N.m 13.0 kgf.m, 22 lbt'ft)R6place.
Type R Model:
BUMP STOP PLATE
SELF-LOCKING NUTt0 r 1.25 mm29 N.m (3.o kgt m, 22 lbf'ft)Rep|aco. -.\-.--...\
_____6
DAMPTRMoUNnNG -.-__re
Check fordeterioration DAMPERMOUNnNG -----+,and damag6. @L!AR Ag-
liillffi*"*,--@
DAMPTR MoU.{nNG __-_____*e
DUST COVEBCh6ck for b€ndingand oamage.
DUST OOVER BOOTCh€ck for deterioralionand damage.
MOUNNNG BASE
DAMPEB MOUNTINGRUBBERCheck lordeteriorationano oamage.
SPRING MOUNTINGRUBBERCheck for deteriorationano oamage.
Check for weakness,compression and damage.
DUST COVER PLAT€
DUST COVERCheck for bendingano oamage.
DUST COVER BOOTChock for deteriorationano oamage,
AUMP STOP PLAYE
1€')
I t_--tlg:z
q._
Y
Check for weaknessand damage.
BUMP STOP
18-38
DAMPER UNTTDAMPER UN]T
Page 749 of 1681
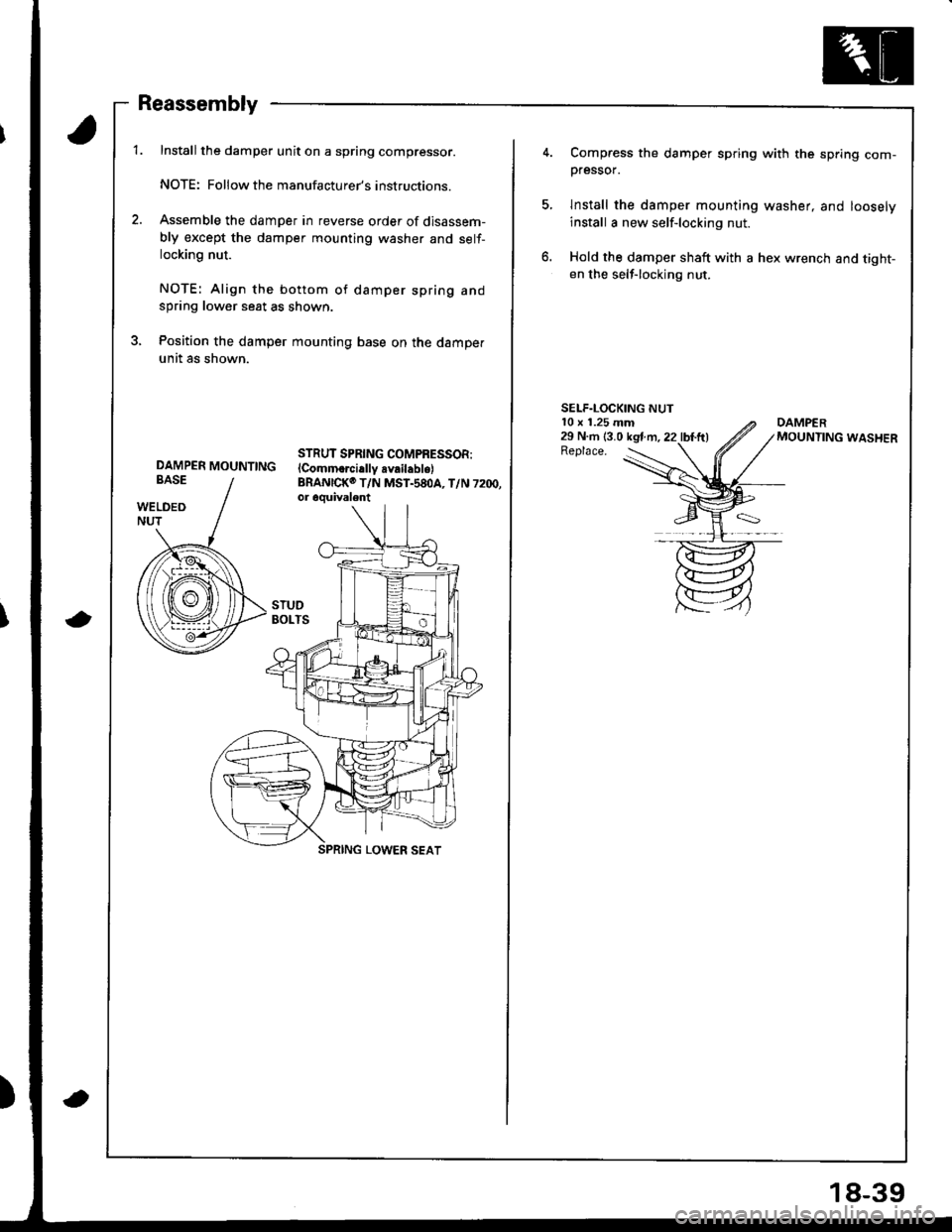
Reassembly
Installthe damper unit on a spring compressor.
NOTE: Followthe manufacturer's instructions.
Assemble the damper in reverse order of disassem-
bly except the damper mounting washer and self-locking nut.
NOTE: Align the bottom of damper spring andspring lower seat as shown.
Position the damper mounting base on the damper
unit as shown.
STRUT SPRING COMPRESSOR:lComm.rci.llv availabls)BRANICKO T/N MST.58OA, T/N 7200,or oquivalent
DAMPER MOUNTTNG
a
a
18-39
Compress the damper spring with the spring com-pressor.
lnstall the damper mounting washer, and loosely
install a new self-locking nut.
Hold the damper shaft with a hex wrench and tight-en the self-locking nut.
SELF.LOCKING NUT10 x 1.25 mm29 N.m (3.0 kstm.22 lbl.ft)Replace.
Page 750 of 1681

Rear Damper
Lower the rear suspension and position the damper
with the welded nut pointed toward the front of the
vehicle.
DAMPER
2. Loosely install the two flange nuts.
Hatchback:Sedan:
lnstallation
. ',.?7,:..r9\,ir '..
EY
FLANGE NUTS10 x 1.25 mmTighten these nuts in step 7 on the next page.
18-40
3. Install the wheel sensor wire bracket.
NOTE: Be careful when installing the sensors to
avoid twisting wires.
Raise the rear suspension with a floor iack until the
vehicle just lifts off the safety stand.
@ The floor jack must be securely posi-
tionod or personal iniury may result.
5. Install the damper mounting bolt and the flange
bolt, then tighten the bolts.
NOTE: The damper mounting bolt and the flange
bolt should be tightened with the damper under
vehicle load.
FLANGE EOLT10 x 1.25 m.n54 N.m (5.5 kgf m, 40 lbt.ftl
FLANGE BOLT10 x 1-25 mm54 N.m ls.s kgf m, 40 lbtft)
6. Tighten the three wheel sensor wire bracket bolts
{for vehicles with ABS).
9.8 N.m {1.0 kg{.m, 7.2 lbtftlBOLTS
Page 762 of 1681
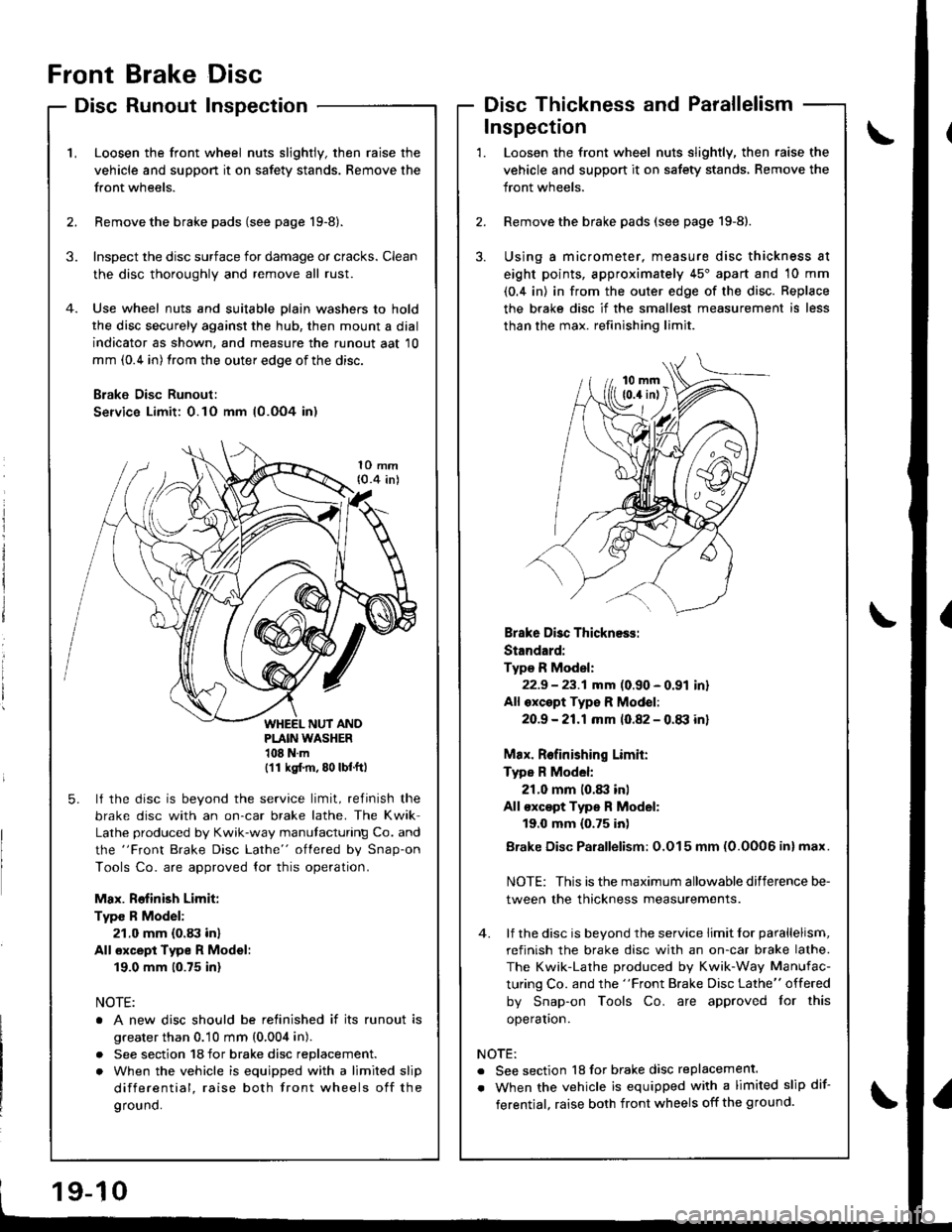
Front
Disc
Brake
Runout
Disc
InspectionDisc Thickness and Parallelism
\'L
2.
Loosen the front wheel nuts slightly, then raise the
vehicle and suppon it on safety stands. Remove the
front wheels.
Remove the brake pads (see page 19-8).
Inspect the disc surface for damage or cracks. Clean
the disc thoroughly and remove all rust.
Use wheel nuts and suitable plain washers to hold
the disc securely against the hub, then mount a dial
indicator as shown, and measure the runout aat 10
mm (0.4 in) from the outer edge of the disc.
B;ake Disc Runoul:
Service Limit: 0.10 mm (0.OO4 in)
3.
1O mm{0.4 inl
PLAIN WASHER108Nm(11 ksl.m, 80 lbf.ft)
5. lf the disc is beyond the service limit, refinish the
brake disc with an on-car brake lathe. The Kwik
Lathe produced by Kwik-way manutacturing Co. and
the "Front Brake Disc Lathe" oflered by Snap-on
Tools Co. are approved {or this operation.
Max. Rofinish Limit:
Type R Model:
21.0 mm (0.83 in)
All €xcept Type R Model:
19.0 mm (0.75 inl
NOTE:
o A new disc should be relinished if its runout is
greater than 0.10 mm (0,004 in).
. See section 18 for brake disc replacement.
. When the vehicle is equipped with a limited slip
differential, raise both front wheels off the
ground.
3.
Loosen the front wheel nuts slightly, then raise the
vehicle and support it on safety stands, Remove the
front wheels.
Remove the brake pads (see page 19-8).
Using a micrometer, measure disc thickness at
eight points, approximately 45'apart and 10 mm
(0.4 in) in from the outer edge of the disc. Replace
the brake disc if the smallest measurement is less
than the max. refinishing limit.
Inspection
2.
1.
Brake Disc Thickness:
Standard:
Type R Model:
22.9 - 23.1 mm (0.90 - 0.91 inr
All oxcept Typ€ R Mod€l:
2O.9 -21.1mm 10.82 - 0.tB inl
Max. Relinishing Limit:
Type R Model:
21.0 mm 10.83 inl
All €xc€pt Type R Model:
19.0 mm {0.75 inl
Brake Disc Parallelism: O.O15 mm (0.0006 inl max.
NOTE: This is the maximum allowable difference be-
tween the thickness measurements.
4. lf the disc is beyond the service limit lor parallelism,
refinish the brake disc with an on-car brake lathe.
The Kwik-Lathe produced by Kwik-Way Manufac-
turing Co. and the "Front Brake Disc Lathe" offered
by Snap-on Tools Co. are approved for this
operaton.
NOTE:
. See section 18 for brake disc replacement.
. When the vehicle is equipped with a limited slip dif-
ferentjal, raise both front wheels off the ground.
Page 765 of 1681
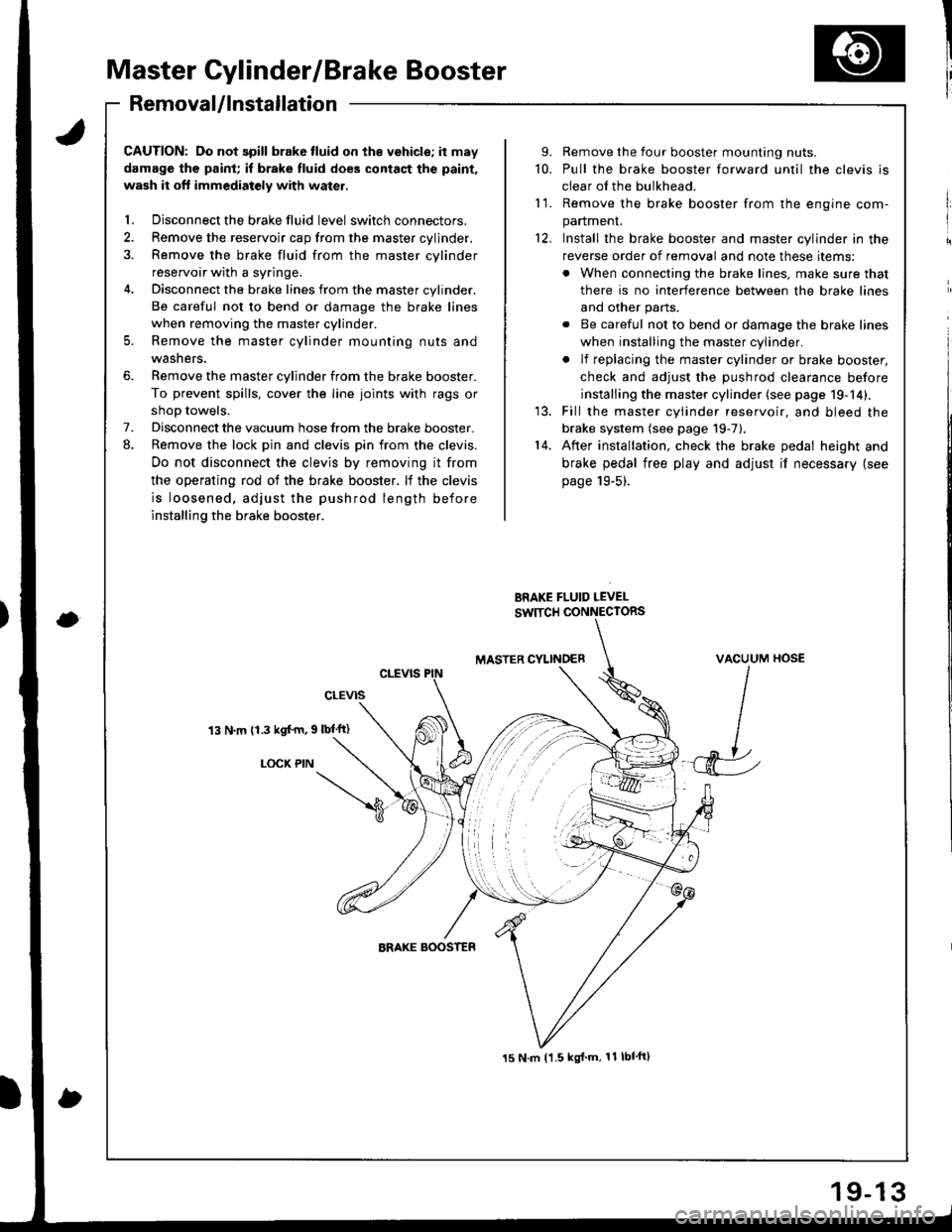
Master Cylinder/Brake Booster
I'RemovaUlnstallation
CAUTION: Do not spill brake tluid on the vehicle; it may
damage the paint; if brake fluid does contact the paint,
wash it oft immediatoly with water.
l. Disconnect the brake fluid level switch connectors.
2. Remove the reservoir cap from the master cylinder.
3. Remove the brake fluid from the master cvlinder
reservoir with a syringe.
4. Disconnect the brake lines from the master cylinder.
Be careful not to bend or damage the brake lines
when removing the master cylinder.
5. Remove the master cylinder mounting nuts and
washers.
6. Remove the master cylinder from the brake booster.
To prevent spills, cover the line joints with rags or
shoD towels.
7. Disconnect the vacuum hose from the brake booster.
8. Remove the lock pin and clevis pin from the clevis.
Do not disconnect the clevis by removing it from
the operating rod of the brake booster. lf the clevis
is loosened, adjust the pushrod length before
installing the brake booster.
13 N.m (1.3 kgf'm, 9 lbl'ft)
LOCX PIN
9. Remove the four booster mounting nuts.
10. Pull the brake booster forward until the clevis is
clear of the bulkhead.
11. Remove the brake booster from the enqine com-
panmenL
12, Install the brake booster and master cylinder in the
reverse order of removal and note these items:
. When connecting the brake lines, make sure that
there is no interference between the brake lines
and other parts.
. Be careful not to bend or damage the brake lines
when installing the master cylinder.
. lf replacing the master cylinder or brake booster,
check and adiust the DUshrod clearance before
installing the master cylinder (see page 19-14).
13. Fill the master cylinder reservoir, and bleed the
brake system (see page 19-7).'14. After installation, check the brake pedal height and
brake pedal free play and adjust if necessary (see
page 19-5).
BRAKE FLUID LEVEL
SW]TCH CONNECTORS
MASTER CYLINOERVACUUM HOSE
J
15 N.m t1.5 kgl'm, 11 lbf'ft)
Page 768 of 1681
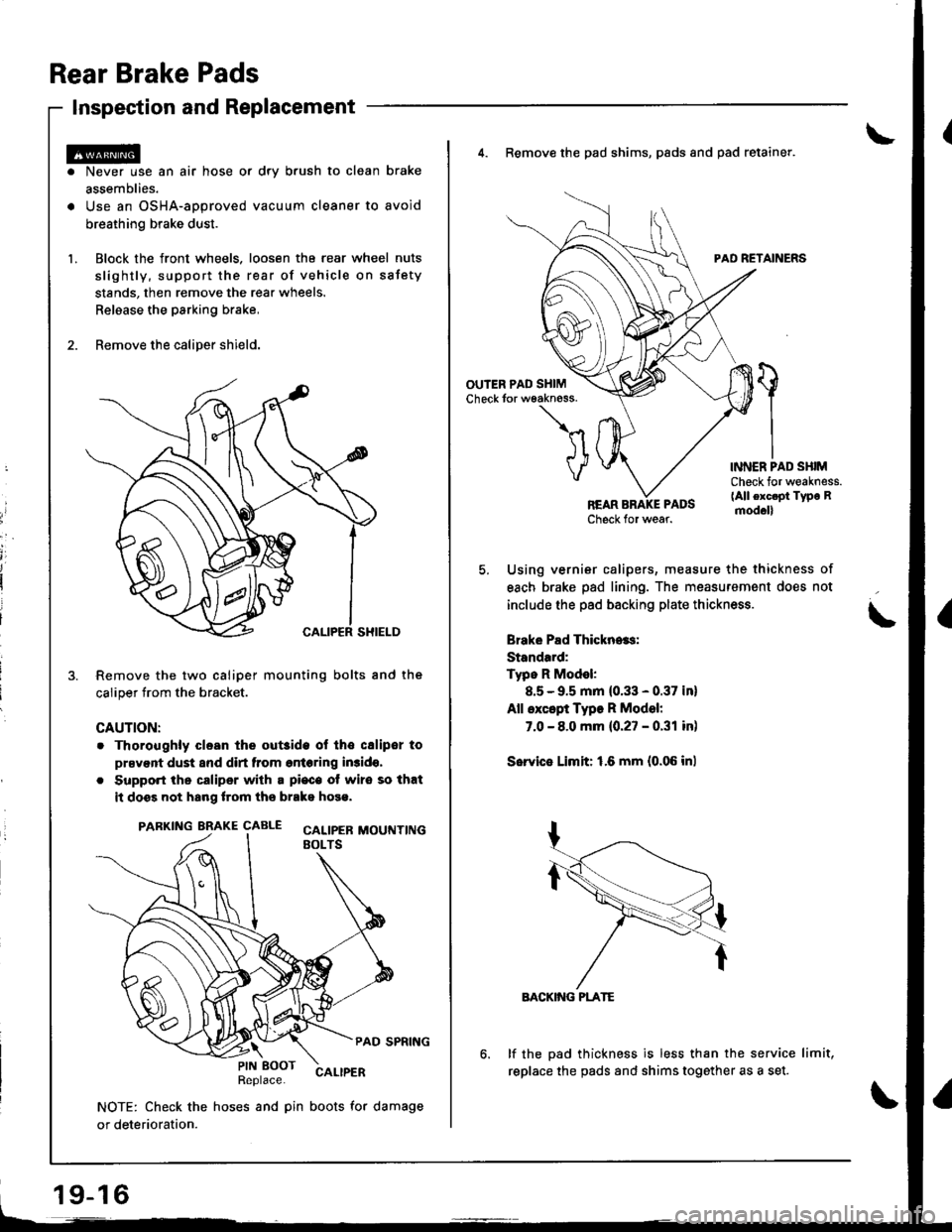
Rear Brake Pads
Inspection and Replacement
Never use an air hose or dry b.ush to clean brake
assemblies.
Use an OSHA-approved vacuum cleaner to avoid
breathing brake dust.
Block the front wheels. loosen tha rear wheel nuts
slightly, support the rear of vehicle on sstety
stands, then remove the rear wheels.
Relaase the parking brake,
Remove the caliper shield.
Remove the two caliper mounting bolts and the
caliper trom the bracket.
CAUTION:
. Thoroughly clesn the out3ide ol tho csliper to
prsvent dust and dirt from entering in3ido,
. Support the caliper with a pi€c€ ot wire so that
it doss not hang lrom ths brako hose.
PARKING BRAKE CAALE cALtpEB MOUTTT|NGEOLTS
PAD SPRING
Replace.CALIPER
NOTE: Check the hoses and pin boots for damage
or deterioration.
\PIN EOOT
19-16
4. Remove the pad shims, pads and pad retainer.
PAD RETAINERS
'l
VINNER PAD SHIMCheck for weakness.(All exc.pt Type Rmod.ll
Using vernier calipers, measure the thickness of
each brake pad lining. The measurement does not
include the pad backing plate thickness.
Brake Pad Thickn..s:
Standard:
Typo R Model:
8.5 - 9.5 mm (0.33 - 0.37 in)
All except Type R Model:
7.0 - 8.0 mm {0.27 - 0.31 in)
Sorvie Limit: 1.6 mm {0.06 inl
BACKIiIG PLATE
lf the pad thickness is less than the service limit,
replace the pads and shims together as a set.
Page 769 of 1681
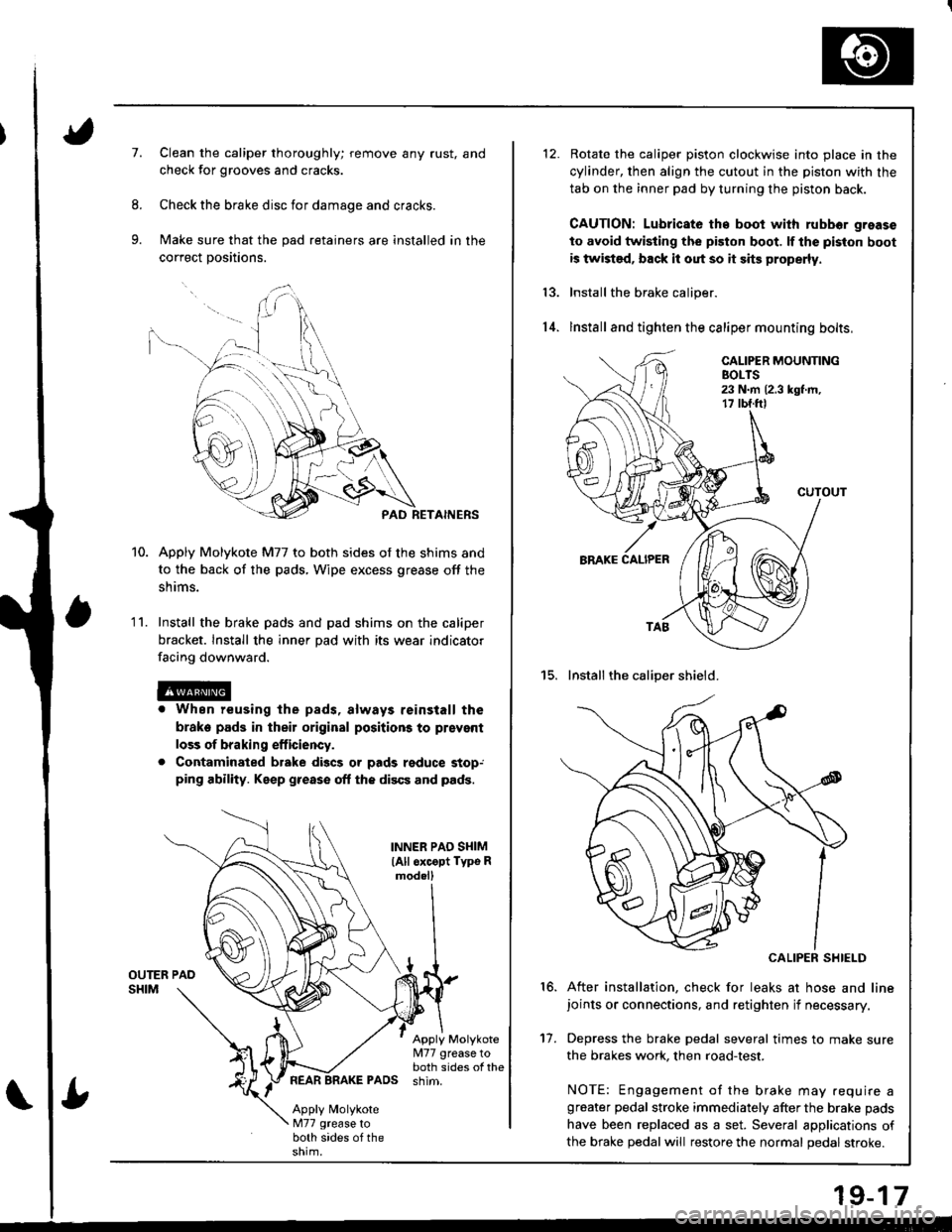
7.Clean the caliper thoroughly; remove any rust, and
check for grooves and cracks.
Check the brake disc for damage and cracks.
Make sure that the pad retainers are installed in the
correct positions.
PAD RETAINERS
Apply Molykote M77 to both sides of the shims and
to the back of the pads, Wipe excess grease off the
snrms.
Install the brake pads and pad shims on the caliper
bracket. Install the inner pad with its wear indicator
facing downward.
r When reusing the pads, always reinstall the
brake pads in their original positions to prsvent
loss of braking efficiency.
. Contaminated brake discs or pads reduce stop,ping ability. Keep grease off the discs and pads.
1 ' I.
INNER PAO SI{IM
lAll oxcopt Typo Rmod.ll
Apply Molykote[I77 grease toboth sides of thePADS shim.
Apply MolykoteM77 grease toboth sides of the
Rotate the caliper piston clockwise into place in the
cylinder, then align the cutout in the piston with the
tab on the inner pad by turning the piston back.
CAUTION: Lubricato th€ boot with rubbor grease
to avoid twisting the piston boot. lf the piston boot
is twist€d, back it out so it sits properly.
Install the brake caliper.
lnstall and tighten the caliper mounting bolts,
15. Installthe caliper shield.
CALIPER SHIELD
After installation, check for leaks at hose and linejoints or connections, and retighten if necessary.
Depress the brake pedal several times to make sure
the brakes work, then road-test.
NOTE: Engagement of the brake may .equire agreater pedal stroke immediately after the brake pads
have been replaced as a set. Several applications of
the brake pedal will restore the normal pedal stroke.
13.
14.
16.
't7.
19-17
Page 770 of 1681
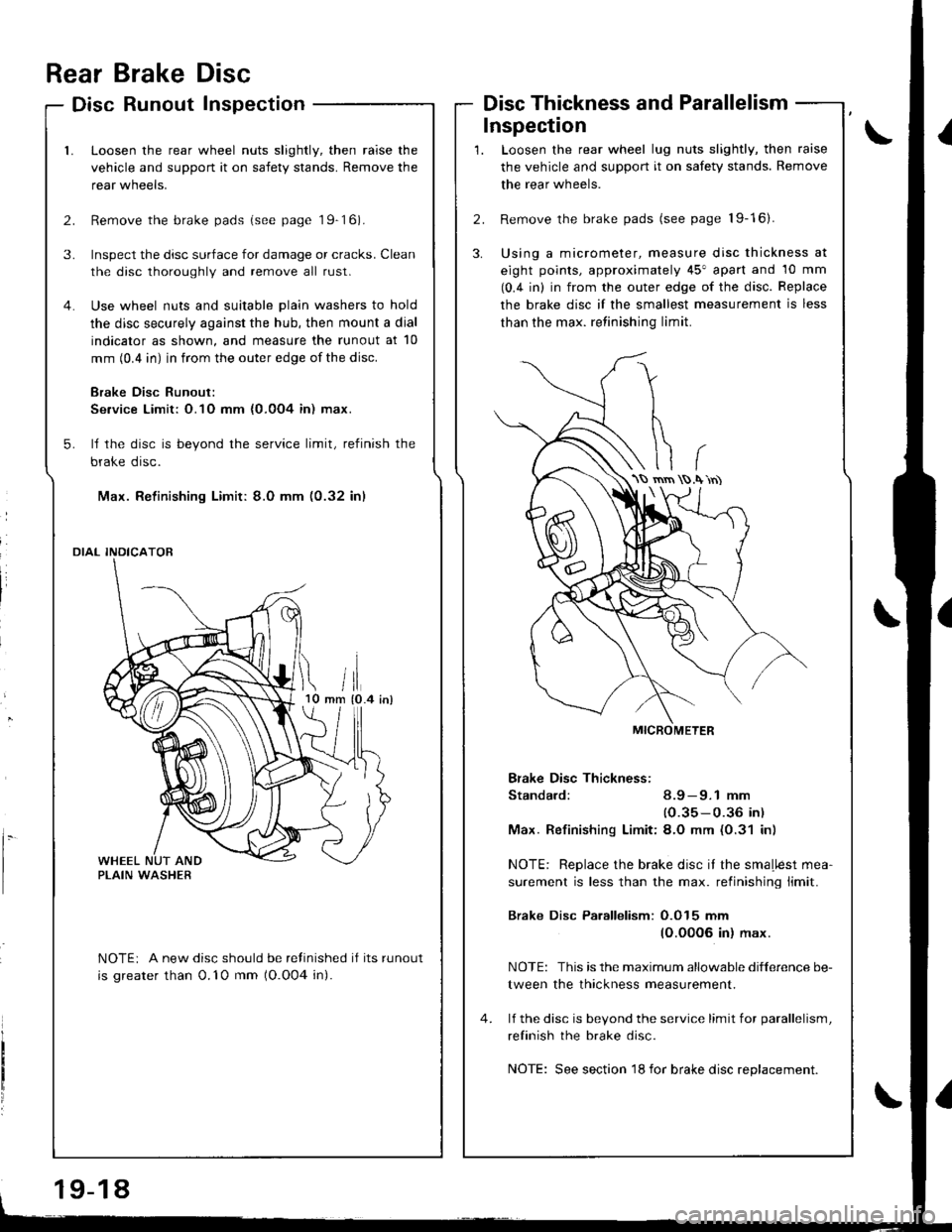
Inspection
rrii tlmm {0.4 inl10
l.
Rear Brake Disc
Disc Runout Inspection
Loosen the rear wheel nuts slightly, then raise the
vehicle and support it on safety stands. Remove the
rear wneers.
Remove the brake pads (see page 19-16).
Inspect the disc surface for damage or cracks. Clean
the disc thoroughly and remove all rust.
Use wheel nuts and suitable plain washers to hold
the disc securely against the hub, then mount a dial
indicator as shown, and measure the runout at 10
mm (0.4 in) in from the outer edge of the disc.
Brake Disc Runout:
Se.vice Limit: O.1O mm {0.0O4 in) max.
ll the disc is beyond the service limit, refinish the
brake disc.
Max. Refinishing Limit: 8.0 mm (0.32 in)
DIAL INDICATOR
NOTEi A new disc should be refinished if its runout
is greater than 0.'10 mm (O.O04 in).
Disc Thickness and Parallelism
Loosen the rear wheel lug nuts slightly, then raise
the vehicle and support it on safety stands. Remove
the rear wheels.
Remove the brake pads (see page 19-16).
Using a micrometer, measure disc thickness at
eight points, approximately 45" apart and 10 mm
(0.4 in) in from the outer edge of the disc. Replace
the brake disc if the smallest measurement is less
than the max. retinishing limit.
Bfake Disc Thickness:
Standard: 8.9 - 9.1 mm
(0.35-0.36 in)
Max. Refinishinq Limit:8.O mm (0.31 in)
NOTE: Replace the brake disc it the smaLlest mea-
surement is less than the max. retinishing limit.
Brake Disc Parallelism: O.O15 mm
(O.00O6 in) max.
NOTE: This is the maximum allowable difference be-
tween the thickness measurement.
lf the disc is bevond the service limit for parallelism,
refinish the brake disc.
NOTE: See section 18 for brake disc replacement.
\S rnrn .\'rn)
19-18