service INFINITI M35 2006 Factory Service Manual
[x] Cancel search | Manufacturer: INFINITI, Model Year: 2006, Model line: M35, Model: INFINITI M35 2006Pages: 5621, PDF Size: 65.56 MB
Page 3067 of 5621
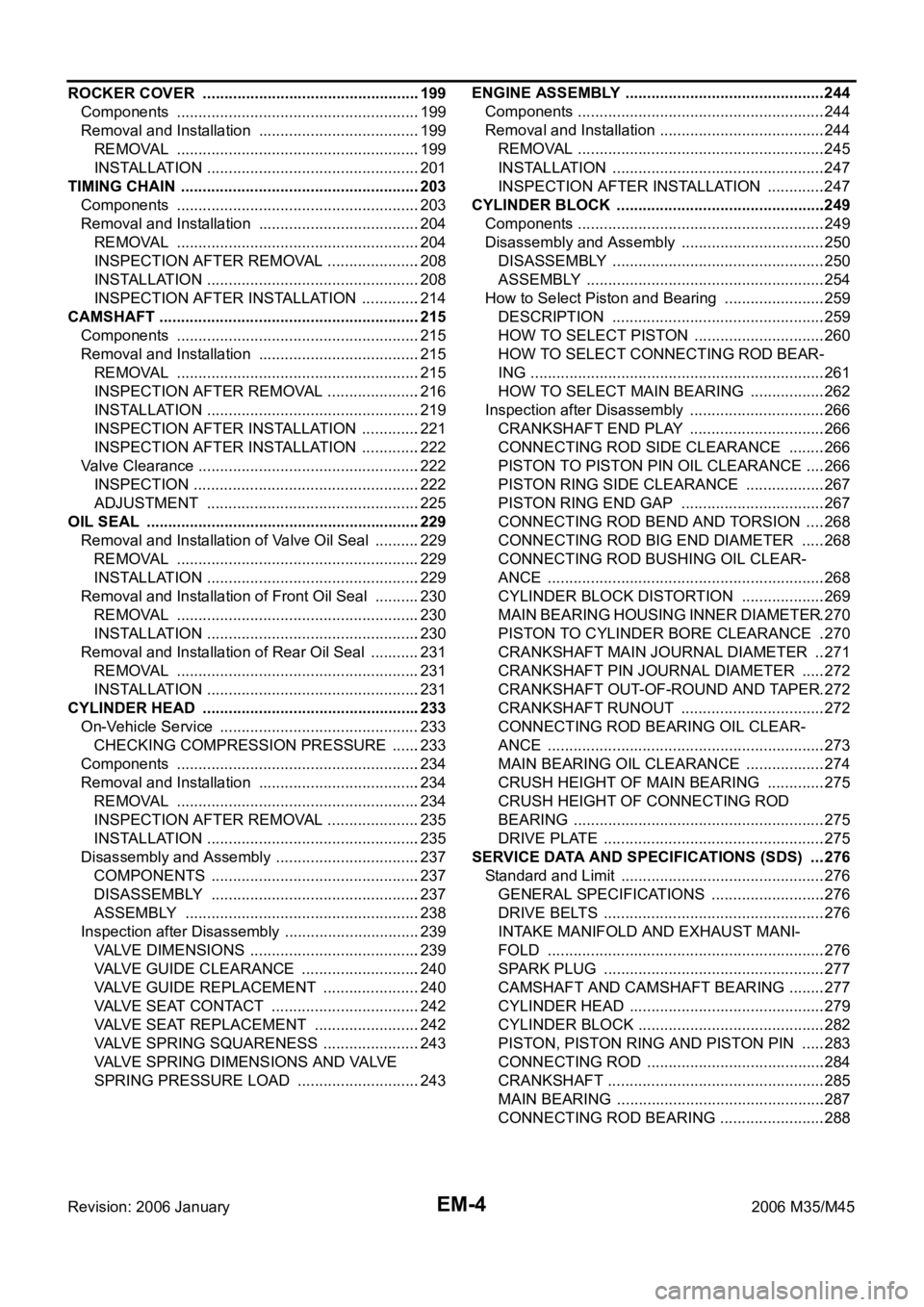
EM-4Revision: 2006 January2006 M35/M45 ROCKER COVER ...................................................199
Components .........................................................199
Removal and Installation ......................................199
REMOVAL ........................................................
.199
INSTALLATION ..................................................201
TIMING CHAIN ........................................................203
Components .........................................................203
Removal and Installation ......................................204
REMOVAL ........................................................
.204
INSPECTION AFTER REMOVAL ......................208
INSTALLATION ..................................................208
INSPECTION AFTER INSTALLATION ..............214
CAMSHAFT .............................................................215
Components .........................................................215
Removal and Installation ......................................215
REMOVAL ........................................................
.215
INSPECTION AFTER REMOVAL ......................216
INSTALLATION ..................................................219
INSPECTION AFTER INSTALLATION ..............221
INSPECTION AFTER INSTALLATION ..............222
Valve Clearance ....................................................222
INSPECTION .....................................................222
ADJUSTMENT ..................................................225
OIL SEAL ................................................................229
Removal and Installation of Valve Oil Seal ...........229
REMOVAL ........................................................
.229
INSTALLATION ..................................................229
Removal and Installation of Front Oil Seal ...........230
REMOVAL ........................................................
.230
INSTALLATION ..................................................230
Removal and Installation of Rear Oil Seal ............231
REMOVAL ........................................................
.231
INSTALLATION ..................................................231
CYLINDER HEAD .................................................. .233
On-Vehicle Service ...............................................233
CHECKING COMPRESSION PRESSURE .......233
Components .........................................................234
Removal and Installation ......................................234
REMOVAL ........................................................
.234
INSPECTION AFTER REMOVAL ......................235
INSTALLATION ..................................................235
Disassembly and Assembly ..................................237
COMPONENTS .................................................237
DISASSEMBLY .................................................237
ASSEMBLY ......................................................
.238
Inspection after Disassembly ................................239
VALVE DIMENSIONS ........................................239
VALVE GUIDE CLEARANCE ............................240
VALVE GUIDE REPLACEMENT .......................240
VALVE SEAT CONTACT ...................................242
VALVE SEAT REPLACEMENT .........................242
VALVE SPRING SQUARENESS .......................243
VALVE SPRING DIMENSIONS AND VALVE
SPRING PRESSURE LOAD .............................243ENGINE ASSEMBLY ...............................................244
Components ..........................................................244
Removal and Installation .......................................244
REMOVAL ..........................................................245
INSTALLATION ..................................................247
INSPECTION AFTER INSTALLATION ..............247
CYLINDER BLOCK .................................................249
Components ..........................................................249
Disassembly and Assembly ..................................250
DISASSEMBLY ..................................................250
ASSEMBLY ........................................................254
How to Select Piston and Bearing ........................259
DESCRIPTION ..................................................259
HOW TO SELECT PISTON ...............................260
HOW TO SELECT CONNECTING ROD BEAR-
ING .....................................................................261
HOW TO SELECT MAIN BEARING ..................262
Inspection after Disassembly ................................266
CRANKSHAFT END PLAY ................................266
CONNECTING ROD SIDE CLEARANCE .........266
PISTON TO PISTON PIN OIL CLEARANCE .....266
PISTON RING SIDE CLEARANCE ...................267
PISTON RING END GAP ..................................267
CONNECTING ROD BEND AND TORSION .....268
CONNECTING ROD BIG END DIAMETER ......268
CONNECTING ROD BUSHING OIL CLEAR-
ANCE .................................................................268
CYLINDER BLOCK DISTORTION ....................269
MAIN BEARING HOUSING INNER DIAMETER .270
PISTON TO CYLINDER BORE CLEARANCE ..270
CRANKSHAFT MAIN JOURNAL DIAMETER ...271
CRANKSHAFT PIN JOURNAL DIAMETER ......272
CRANKSHAFT OUT-OF-ROUND AND TAPER .272
CRANKSHAFT RUNOUT ..................................272
CONNECTING ROD BEARING OIL CLEAR-
ANCE .................................................................273
MAIN BEARING OIL CLEARANCE ...................274
CRUSH HEIGHT OF MAIN BEARING ..............275
CRUSH HEIGHT OF CONNECTING ROD
BEARING ...........................................................275
DRIVE PLATE ....................................................275
SERVICE DATA AND SPECIFICATIONS (SDS) ....276
Standard and Limit ................................................276
GENERAL SPECIFICATIONS ...........................276
DRIVE BELTS ....................................................276
INTAKE MANIFOLD AND EXHAUST MANI-
FOLD .................................................................276
SPARK PLUG ....................................................277
CAMSHAFT AND CAMSHAFT BEARING .........277
CYLINDER HEAD ..............................................279
CYLINDER BLOCK ............................................282
PISTON, PISTON RING AND PISTON PIN ......283
CONNECTING ROD ..........................................284
CRANKSHAFT ...................................................285
MAIN BEARING .................................................287
CONNECTING ROD BEARING .........................288
Page 3071 of 5621
![INFINITI M35 2006 Factory Service Manual EM-8
[VQ35DE]
PREPARATION
Revision: 2006 January2006 M35/M45
PREPARATIONPFP:00002
Special Service ToolsNBS004MO
The actual shapes of Kent-Moore tools may differ from those of special service tools ill INFINITI M35 2006 Factory Service Manual EM-8
[VQ35DE]
PREPARATION
Revision: 2006 January2006 M35/M45
PREPARATIONPFP:00002
Special Service ToolsNBS004MO
The actual shapes of Kent-Moore tools may differ from those of special service tools ill](/img/42/57023/w960_57023-3070.png)
EM-8
[VQ35DE]
PREPARATION
Revision: 2006 January2006 M35/M45
PREPARATIONPFP:00002
Special Service ToolsNBS004MO
The actual shapes of Kent-Moore tools may differ from those of special service tools illustrated here.
Tool number
(Kent-Moore No.)
Tool nameDescription
KV10116200
(J26336-A)
Valve spring compressor
1. KV10115900
(J26336-20)
Attachment
2.KV10109220
(—)
AdapterDisassembling valve mechanism
Part (1) is a component of KV10116200
(J26336-A), but Part (2) is not so.
KV10107902
(J38959)
Valve oil seal pullerReplacing valve oil seal
KV10115600
(J-38958)
Valve oil seal driftInstalling valve oil seal
Use side A.
a: 20 (0.79) dia. d: 8 (0.31) dia.
b: 13 (0.51) dia. e: 10.7 (0.421)
c: 10.3 (0.406) dia. f: 5 (0.20)
Unit: mm (in)
EM03470000
(J8037)
Piston ring compressorInstalling piston assembly into cylinder bore
ST16610001
(J23907)
Pilot bushing pullerRemoving pilot converter
KV10111100
(J37228)
Seal cutterRemoving oil pan (lower and upper), front
and rear timing chain case, etc.
PBIC1650E
NT011
S-NT603
NT044
NT045
NT046
Page 3073 of 5621
![INFINITI M35 2006 Factory Service Manual EM-10
[VQ35DE]
PREPARATION
Revision: 2006 January2006 M35/M45
Commercial Service ToolsNBS004MP
(Kent-Moore No.)
Tool nameDescription
(—)
Power toolLoosening nuts and bolts
(BT3373-F)
Belt tension ga INFINITI M35 2006 Factory Service Manual EM-10
[VQ35DE]
PREPARATION
Revision: 2006 January2006 M35/M45
Commercial Service ToolsNBS004MP
(Kent-Moore No.)
Tool nameDescription
(—)
Power toolLoosening nuts and bolts
(BT3373-F)
Belt tension ga](/img/42/57023/w960_57023-3072.png)
EM-10
[VQ35DE]
PREPARATION
Revision: 2006 January2006 M35/M45
Commercial Service ToolsNBS004MP
(Kent-Moore No.)
Tool nameDescription
(—)
Power toolLoosening nuts and bolts
(BT3373-F)
Belt tension gaugeChecking drive belt tension
(—)
TORX socketRemoving and installing drive plate
Size: T55
(—)
Manual lift table caddyRemoving and installing engine
(J24239-01)
Cylinder head bolt wrenchLoosening and tightening cylinder head bolt,
and used with the angle wrench [SST:
KV10112100 (BT8653-A)]
a: 13 (0.51) dia.
b: 12 (0.47)
c: 10 (0.39)
Unit: mm (in)
(—)
1.Compression gauge
2.AdapterChecking compression pressure
(—)
Spark plug wrenchRemoving and installing spark plug
PBIC0190E
AMA126
PBIC1113E
ZZA1210D
NT583
ZZA0008D
NT047
Page 3078 of 5621
![INFINITI M35 2006 Factory Service Manual DRIVE BELTS
EM-15
[VQ35DE]
C
D
E
F
G
H
I
J
K
L
MA
EM
Revision: 2006 January2006 M35/M45
DRIVE BELTSPFP:02117
Checking Drive BeltsNBS004MU
WAR NING :
Be sure to perform when engine is stopped.
1. Inspe INFINITI M35 2006 Factory Service Manual DRIVE BELTS
EM-15
[VQ35DE]
C
D
E
F
G
H
I
J
K
L
MA
EM
Revision: 2006 January2006 M35/M45
DRIVE BELTSPFP:02117
Checking Drive BeltsNBS004MU
WAR NING :
Be sure to perform when engine is stopped.
1. Inspe](/img/42/57023/w960_57023-3077.png)
DRIVE BELTS
EM-15
[VQ35DE]
C
D
E
F
G
H
I
J
K
L
MA
EM
Revision: 2006 January2006 M35/M45
DRIVE BELTSPFP:02117
Checking Drive BeltsNBS004MU
WAR NING :
Be sure to perform when engine is stopped.
1. Inspect belts for cracks, fraying, wear and oil. If necessary, replace.
2. Inspect drive belt deflection or tension at a point on belt midway
between pulleys.
Inspection should be done only when engine is cold, or over
30 minutes after engine is stopped.
Measure the belt tension with belt tension gauge (Commercial
service tool: BT3373-F or equivalent) at points marked
shown in the figure.
When measuring the deflection, apply 98 N (10 kg, 22 lb) at
the marked point.
Adjust if the belt deflection exceeds the limit or if the belt ten-
sion is not within specifications.
CAUTION:
When checking the belt deflection or the tension immediately after installation, first adjust it to
the specified value. Then, after turning crankshaft two turns or more, re-adjust to the specified
value to avoid variation in deflection between pulleys.
Tighten idler pulley lock nut by hand and measure the deflection or the tension without loose-
ness.
Belt Deflection and Tension
*: If belt tension gauge cannot be installed at check points shown, check drive belt tension at different location on belt.
Tension AdjustmentNBS004MV
CAUTION:
When belt is replaced with a new one, adjust it to value for “New belt” to accommodate for insuffi-
cient adaptability with pulley grooves.
When deflection or tension of belt being used exceeds “Limit”, adjust it to value for “After adjust-
ment”.
When checking belt deflection or tension immediately after installation, first adjust it to the speci-
fied value. Then, after turning crankshaft two turns or more, re-adjust to the specified value to
avoid variation in deflection between pulleys.
When installing belt, make sure that it is correctly engaged with pulley grooves.
Keep engine oil, working fluid and engine coolant away from belt and pulley grooves.
Do not twist or bend belt excessively.
KBIA1731J
ItemsDeflection adjustment Unit: mm (in) Tension adjustment* Unit: N (kg, lb)
Used belt
New beltUsed belt
New belt
Limit After adjustment Limit After adjustment
Alternator and
power steering
oil pump belt7 (0.28)4 - 5
(0.16 - 0.20)3.5 - 4.5
(0.138 - 0.177)294 (30, 66)730 - 818
(74.5 - 83.5,
164 - 184)838 - 926
(85.5 - 94.5,
188 - 208)
A/C compressor
belt12 (0.47)9 - 10
(0.35 - 0.39)8 - 9
(0.31 - 0.35)196 (20, 44)348 - 436
(35.5 - 44.5,
78 - 98)470 - 559
(48 - 57,
106 - 126)
Applied pushing
force98 N (10 kg, 22 lb) —
PortionBelt tightening method for adjustment
Alternator and power steering oil pump belt Adjusting bolt on idler pulley
A/C compressor belt Adjusting bolt on idler pulley
Page 3091 of 5621
![INFINITI M35 2006 Factory Service Manual EM-28
[VQ35DE]
EXHAUST MANIFOLD
Revision: 2006 January2006 M35/M45
Exhaust Manifold Gasket
Install in direction shown below. (Follow same procedure for
both banks.)
Locate thick side of port c INFINITI M35 2006 Factory Service Manual EM-28
[VQ35DE]
EXHAUST MANIFOLD
Revision: 2006 January2006 M35/M45
Exhaust Manifold Gasket
Install in direction shown below. (Follow same procedure for
both banks.)
Locate thick side of port c](/img/42/57023/w960_57023-3090.png)
EM-28
[VQ35DE]
EXHAUST MANIFOLD
Revision: 2006 January2006 M35/M45
Exhaust Manifold Gasket
Install in direction shown below. (Follow same procedure for
both banks.)
Locate thick side of port connecting part on right side from tech-
nician’s view.
Locate round press in thick side of port connecting part above
center level line of port.
Exhaust Manifold
If stud bolts were removed, install them and tighten to the specified torque below.
Install exhaust manifold and tighten mounting bolts in numerical
order as shown in the figure.
NOTE:
Tighten nuts No. 1 and 2 in two steps. The numerical order No. 7
and 8 shows second step.
Air Fuel Ratio Sensor
CAUTION:
Before installing a new air fuel ratio sensor, clean exhaust system threads using heated oxygen
sensor thread cleaner tool (Commercial Service Tool: J-43897-18 or J-43897-12) and apply anti-
seize lubricant.
Do not over torque air fuel ratio sensor. Doing so may cause damage to air fuel ratio sensor,
resulting in the “MIL” coming on.
KBIA1051E
: 14.7 Nꞏm (1.5 kg-m, 11 ft-lb)
PBIC2042E
Page 3164 of 5621
![INFINITI M35 2006 Factory Service Manual CYLINDER HEAD
EM-101
[VQ35DE]
C
D
E
F
G
H
I
J
K
L
MA
EM
Revision: 2006 January2006 M35/M45
CYLINDER HEADPFP:11041
On-Vehicle ServiceNBS004NR
CHECKING COMPRESSION PRESSURE
1. Warm up engine thoroughly. INFINITI M35 2006 Factory Service Manual CYLINDER HEAD
EM-101
[VQ35DE]
C
D
E
F
G
H
I
J
K
L
MA
EM
Revision: 2006 January2006 M35/M45
CYLINDER HEADPFP:11041
On-Vehicle ServiceNBS004NR
CHECKING COMPRESSION PRESSURE
1. Warm up engine thoroughly.](/img/42/57023/w960_57023-3163.png)
CYLINDER HEAD
EM-101
[VQ35DE]
C
D
E
F
G
H
I
J
K
L
MA
EM
Revision: 2006 January2006 M35/M45
CYLINDER HEADPFP:11041
On-Vehicle ServiceNBS004NR
CHECKING COMPRESSION PRESSURE
1. Warm up engine thoroughly. Then, stop it.
2. Release fuel pressure. Refer to EC-98, "
FUEL PRESSURE RELEASE" .
3. Disconnect fuel pump fuse to avoid fuel injection during mea-
surement.
4. Remove engine cover with power tool. Refer to EM-19, "
INTAKE MANIFOLD COLLECTOR" .
5. Remove ignition coil and spark plug from each cylinder. Refer to EM-42, "
IGNITION COIL" and EM-43,
"SPARK PLUG (PLATINUM-TIPPED TYPE)" .
6. Connect engine tachometer (not required in use of CONSULT-ll).
7. Install compression gauge with an adapter (commercial service
tool) onto spark plug hole.
Use the adapter whose picking up end inserted to spark plug
hole is smaller than 20 mm (0.79 in) in diameter. Otherwise, it
may be caught by cylinder head during removal.
8. With accelerator pedal fully depressed, turn ignition switch to “START” for cranking. When the gauge
pointer stabilizes, read the compression pressure and the engine rpm. Perform these steps to check each
cylinder.
Compression pressure:
Unit: kPa (kg/cm2 , psi) /rpm
CAUTION:
Always use a fully changed battery to obtain the specified engine speed.
SBIA0466E
PBIC0900E
SBIA0533E
Standard Minimum Deference limit between cylinders
1,275 (13.0, 185) / 300 981 (10.0, 142) / 300 98 (1.0, 14) / 300
Page 3166 of 5621
![INFINITI M35 2006 Factory Service Manual CYLINDER HEAD
EM-103
[VQ35DE]
C
D
E
F
G
H
I
J
K
L
MA
EM
Revision: 2006 January2006 M35/M45
2. Temporarily fit front suspension member to support engine. Refer to FSU-6, "FRONT SUSPENSIO INFINITI M35 2006 Factory Service Manual CYLINDER HEAD
EM-103
[VQ35DE]
C
D
E
F
G
H
I
J
K
L
MA
EM
Revision: 2006 January2006 M35/M45
2. Temporarily fit front suspension member to support engine. Refer to FSU-6, "FRONT SUSPENSIO](/img/42/57023/w960_57023-3165.png)
CYLINDER HEAD
EM-103
[VQ35DE]
C
D
E
F
G
H
I
J
K
L
MA
EM
Revision: 2006 January2006 M35/M45
2. Temporarily fit front suspension member to support engine. Refer to FSU-6, "FRONT SUSPENSION
ASSEMBLY" (2WD) or FSU-23, "FRONT SUSPENSION ASSEMBLY" (AWD).
CAUTION:
Temporary fitting means the status that engine is adequately stable though the hoist is released
from hanging.
NOTE:
At the time of the start of this procedure front suspension member is removed, and cylinder head is
hanged by hoist with the engine slinger installed.
3. Release the hoist from hanging, then remove the engine slinger.
4. Remove the following parts:
Fuel tube and fuel injector assembly; Refer to EM-45, "FUEL INJECTOR AND FUEL TUBE" .
Intake manifold; Refer to EM-24, "INTAKE MANIFOLD" .
Exhaust manifold; Refer to EM-26, "EXHAUST MANIFOLD" .
Water inlet and thermostat assembly; Refer to CO-29, "WATER INLET AND THERMOSTAT ASSEM-
BLY" .
Water outlet, water pipe and heater pipe; Refer to CO-31, "WATER OUTLET AND WATER PIPING" .
5. Remove cylinder head bolts in reverse order as shown in the fig-
ure with cylinder head bolt wrench (commercial service tool) and
power tool to remove cylinder heads (right and left banks).
6. Remove cylinder head gaskets.
INSPECTION AFTER REMOVAL
Cylinder Head Bolts Outer Diameter
Cylinder head bolts are tightened by plastic zone tightening
method. Whenever the size difference between “d1” and “d2”
exceeds the limit, replace them with new one.
If reduction of outer diameter appears in a position other than
“d2”, use it as “d2” point.
PBIC2057E
Limit (“d1” – “d2”) : 0.11 mm (0.0043 in)
PBIC2480E
Page 3167 of 5621
![INFINITI M35 2006 Factory Service Manual EM-104
[VQ35DE]
CYLINDER HEAD
Revision: 2006 January2006 M35/M45
Cylinder Head Distortion
NOTE:
When performing this inspection, cylinder block distortion should be also checking. Refer to EM-143, INFINITI M35 2006 Factory Service Manual EM-104
[VQ35DE]
CYLINDER HEAD
Revision: 2006 January2006 M35/M45
Cylinder Head Distortion
NOTE:
When performing this inspection, cylinder block distortion should be also checking. Refer to EM-143,](/img/42/57023/w960_57023-3166.png)
EM-104
[VQ35DE]
CYLINDER HEAD
Revision: 2006 January2006 M35/M45
Cylinder Head Distortion
NOTE:
When performing this inspection, cylinder block distortion should be also checking. Refer to EM-143, "
CYLIN-
DER BLOCK DISTORTION" .
1. Using a scraper, wipe off oil, scale, gasket, sealant and carbon deposits from surface of cylinder head.
CAUTION:
Do not allow gasket fragments to enter engine oil or engine coolant passages.
2. At each of several locations on bottom surface of cylinder head,
measure the distortion in six directions.
If it exceeds the limit, replace cylinder head.
INSTALLATION
1. Install new cylinder head gaskets.
2. Turn crankshaft until No. 1 piston is set at TDC.
Crankshaft key should line up with the right bank cylinder cen-
ter line as shown in the figure.
3. Install cylinder head follow the steps below to tighten cylinder
head bolts in numerical order as shown in the figure with cylin-
der head bolts wrench (commercial service tool).
CAUTION:
If cylinder head bolts re-used, check their outer diameters
before installation. Refer toEM-103, "
Cylinder Head Bolts
Outer Diameter" .
a. Apply new engine oil to threads and seat surfaces of cylinder
head bolts.
b. Tighten all cylinder head bolts.
c. Completely loosen all cylinder head bolts.
CAUTION:
In step “c”, loosen bolts in reverse order of that indicated in
the figure.
d. Tighten all cylinder head bolts.Limit : 0.1 mm (0.004 in)
SEM861E
SEM532G
: 98.1 Nꞏm (10 kg-m, 72 ft-lb)
: 0 Nꞏm (0 kg-m, 0 ft-lb)
: 39.2 Nꞏm (4.0 kg-m, 29 ft-lb)
PBIC2057E
Page 3169 of 5621
![INFINITI M35 2006 Factory Service Manual EM-106
[VQ35DE]
CYLINDER HEAD
Revision: 2006 January2006 M35/M45
Disassembly and AssemblyNBS004NU
COMPONENTS
DISASSEMBLY
1. Remove spark plug with spark plug wrench (commercial service tool).
2. Remov INFINITI M35 2006 Factory Service Manual EM-106
[VQ35DE]
CYLINDER HEAD
Revision: 2006 January2006 M35/M45
Disassembly and AssemblyNBS004NU
COMPONENTS
DISASSEMBLY
1. Remove spark plug with spark plug wrench (commercial service tool).
2. Remov](/img/42/57023/w960_57023-3168.png)
EM-106
[VQ35DE]
CYLINDER HEAD
Revision: 2006 January2006 M35/M45
Disassembly and AssemblyNBS004NU
COMPONENTS
DISASSEMBLY
1. Remove spark plug with spark plug wrench (commercial service tool).
2. Remove valve lifter.
Identify installation positions, and store them without mixing them up.
3. Remove valve collet.
Compress valve spring with the valve spring compressor, the
attachment and the adapter (SST). Remove valve collet with
a magnet hand.
CAUTION:
When working, take care not to damage valve lifter holes.
4. Remove valve spring retainer, valve spring and valve spring seat.
5. Push valve stem to combustion chamber side, and remove valve.
Identify installation positions, and store them without mixing them up.
1. Valve lifter 2. Valve collet 3. Valve spring retainer
4. Valve spring 5. Valve oil seal 6. Valve spring seat
7. Valve guide 8. Spark plug 9. Spark plug tube
10. Cylinder head (right bank) 11. Valve seat 12. Valve (EXH)
13. Valve (INT) 14. Cylinder head (left bank)
PBIC2637E
PBIC1803E
Page 3171 of 5621
![INFINITI M35 2006 Factory Service Manual EM-108
[VQ35DE]
CYLINDER HEAD
Revision: 2006 January2006 M35/M45
8. Install valve collet.
Compress valve spring with the valve spring compressor, the
attachment and the adapter (SST). Install va INFINITI M35 2006 Factory Service Manual EM-108
[VQ35DE]
CYLINDER HEAD
Revision: 2006 January2006 M35/M45
8. Install valve collet.
Compress valve spring with the valve spring compressor, the
attachment and the adapter (SST). Install va](/img/42/57023/w960_57023-3170.png)
EM-108
[VQ35DE]
CYLINDER HEAD
Revision: 2006 January2006 M35/M45
8. Install valve collet.
Compress valve spring with the valve spring compressor, the
attachment and the adapter (SST). Install valve collet with a
magnet hand.
CAUTION:
When working, take care not to damage valve lifter holes.
Tap valve stem edge lightly with plastic hammer after installa-
tion to check its installed condition.
9. Install valve lifter.
Install it in the original position.
10. Install spark plug tube.
Press-fit spark plug tube as follows:
a. Remove old locking sealant adhering to cylinder head mounting hole.
b. Apply sealant to area within approximately 12 mm (0.47 in) from edge of spark plug tube press-fit side.
Use Genuine High Strength Locking Sealant or equivalent. Refer to GI-48, "
RECOMMENDED
CHEMICAL PRODUCTS AND SEALANTS" .
c. Using drift, press-fit spark plug tube so that its height “H” is as
specified in the figure.
CAUTION:
When press-fitting, take care not to deform spark plug
tube.
After press-fitting, wipe off liquid gasket protruding onto
cylinder-head upper face.
11. Install spark plug with spark plug wrench (commercial service tool).
Inspection after DisassemblyNBS004NV
VALVE DIMENSIONS
Check the dimensions of each valve. For the dimensions, refer to EM-154, "Valve Dimensions" .
If dimensions are out of the standard, replace valve and check valve seat contact. Refer to EM-110,
"VA LV E S E AT C O N TA C T" .
VALVE GUIDE CLEARANCE
Valve Stem Diameter
Measure the diameter of valve stem with micrometer.
Valve Guide Inner Diameter
Measure the inner diameter of valve guide with bore gauge.
PBIC1803E
Standard press-fit height “H”:
: 38.1 - 39.1 mm (1.500 - 1.539 in)
PBIC2638E
Standard
Intake : 5.965 - 5.980 mm (0.2348 - 0.2354 in)
Exhaust : 5.955 - 5.970 mm (0.2344 - 0.2350 in)
SEM938C