service INFINITI M35 2006 Factory Service Manual
[x] Cancel search | Manufacturer: INFINITI, Model Year: 2006, Model line: M35, Model: INFINITI M35 2006Pages: 5621, PDF Size: 65.56 MB
Page 3367 of 5621
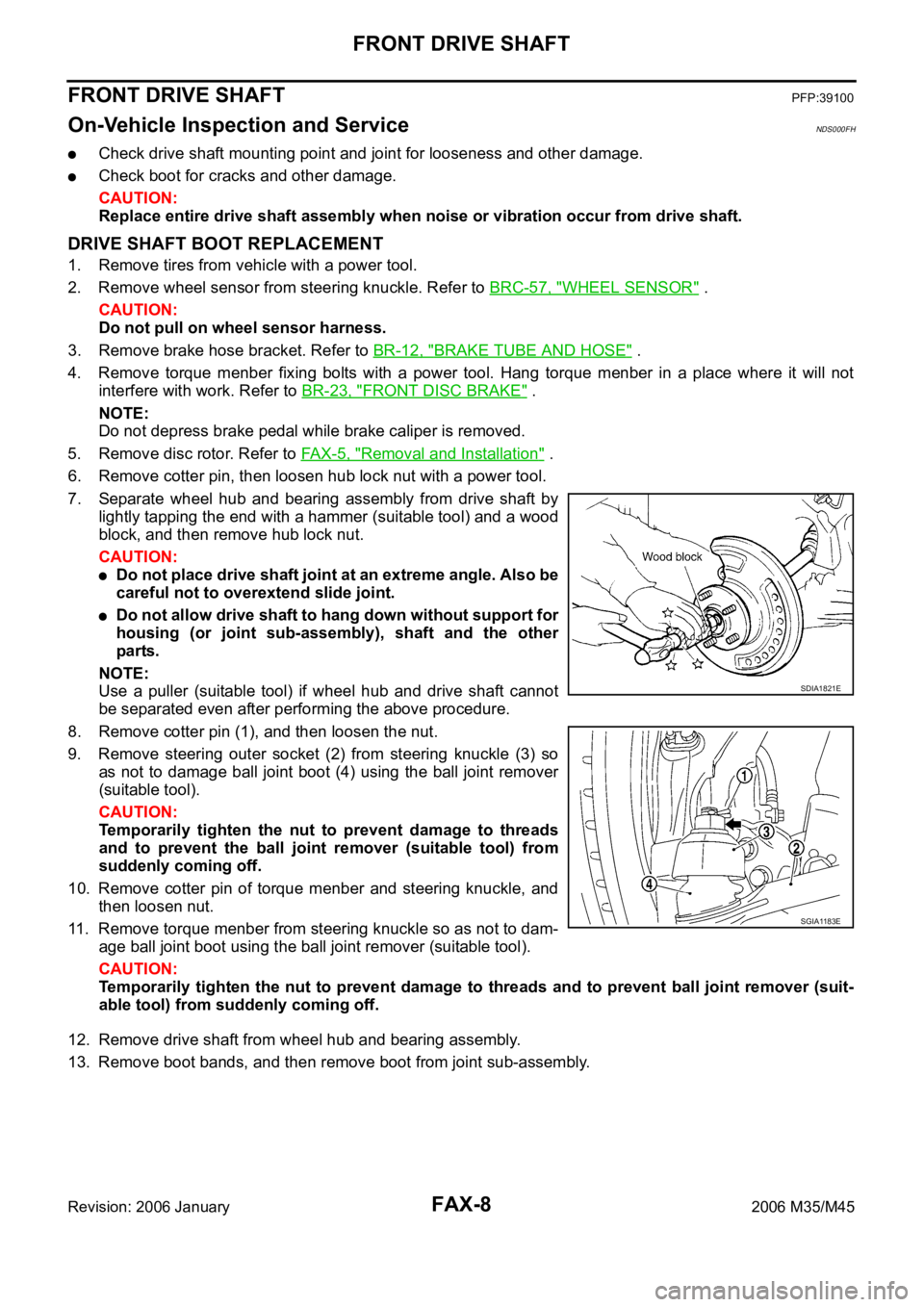
FAX-8
FRONT DRIVE SHAFT
Revision: 2006 January2006 M35/M45
FRONT DRIVE SHAFTPFP:39100
On-Vehicle Inspection and ServiceNDS000FH
Check drive shaft mounting point and joint for looseness and other damage.
Check boot for cracks and other damage.
CAUTION:
Replace entire drive shaft assembly when noise or vibration occur from drive shaft.
DRIVE SHAFT BOOT REPLACEMENT
1. Remove tires from vehicle with a power tool.
2. Remove wheel sensor from steering knuckle. Refer to BRC-57, "
WHEEL SENSOR" .
CAUTION:
Do not pull on wheel sensor harness.
3. Remove brake hose bracket. Refer to BR-12, "
BRAKE TUBE AND HOSE" .
4. Remove torque menber fixing bolts with a power tool. Hang torque menber in a place where it will not
interfere with work. Refer to BR-23, "
FRONT DISC BRAKE" .
NOTE:
Do not depress brake pedal while brake caliper is removed.
5. Remove disc rotor. Refer to FA X - 5 , "
Removal and Installation" .
6. Remove cotter pin, then loosen hub lock nut with a power tool.
7. Separate wheel hub and bearing assembly from drive shaft by
lightly tapping the end with a hammer (suitable tool) and a wood
block, and then remove hub lock nut.
CAUTION:
Do not place drive shaft joint at an extreme angle. Also be
careful not to overextend slide joint.
Do not allow drive shaft to hang down without support for
housing (or joint sub-assembly), shaft and the other
parts.
NOTE:
Use a puller (suitable tool) if wheel hub and drive shaft cannot
be separated even after performing the above procedure.
8. Remove cotter pin (1), and then loosen the nut.
9. Remove steering outer socket (2) from steering knuckle (3) so
as not to damage ball joint boot (4) using the ball joint remover
(suitable tool).
CAUTION:
Temporarily tighten the nut to prevent damage to threads
and to prevent the ball joint remover (suitable tool) from
suddenly coming off.
10. Remove cotter pin of torque menber and steering knuckle, and
then loosen nut.
11. Remove torque menber from steering knuckle so as not to dam-
age ball joint boot using the ball joint remover (suitable tool).
CAUTION:
Temporarily tighten the nut to prevent damage to threads and to prevent ball joint remover (suit-
able tool) from suddenly coming off.
12. Remove drive shaft from wheel hub and bearing assembly.
13. Remove boot bands, and then remove boot from joint sub-assembly.
SDIA1821E
SGIA1183E
Page 3375 of 5621
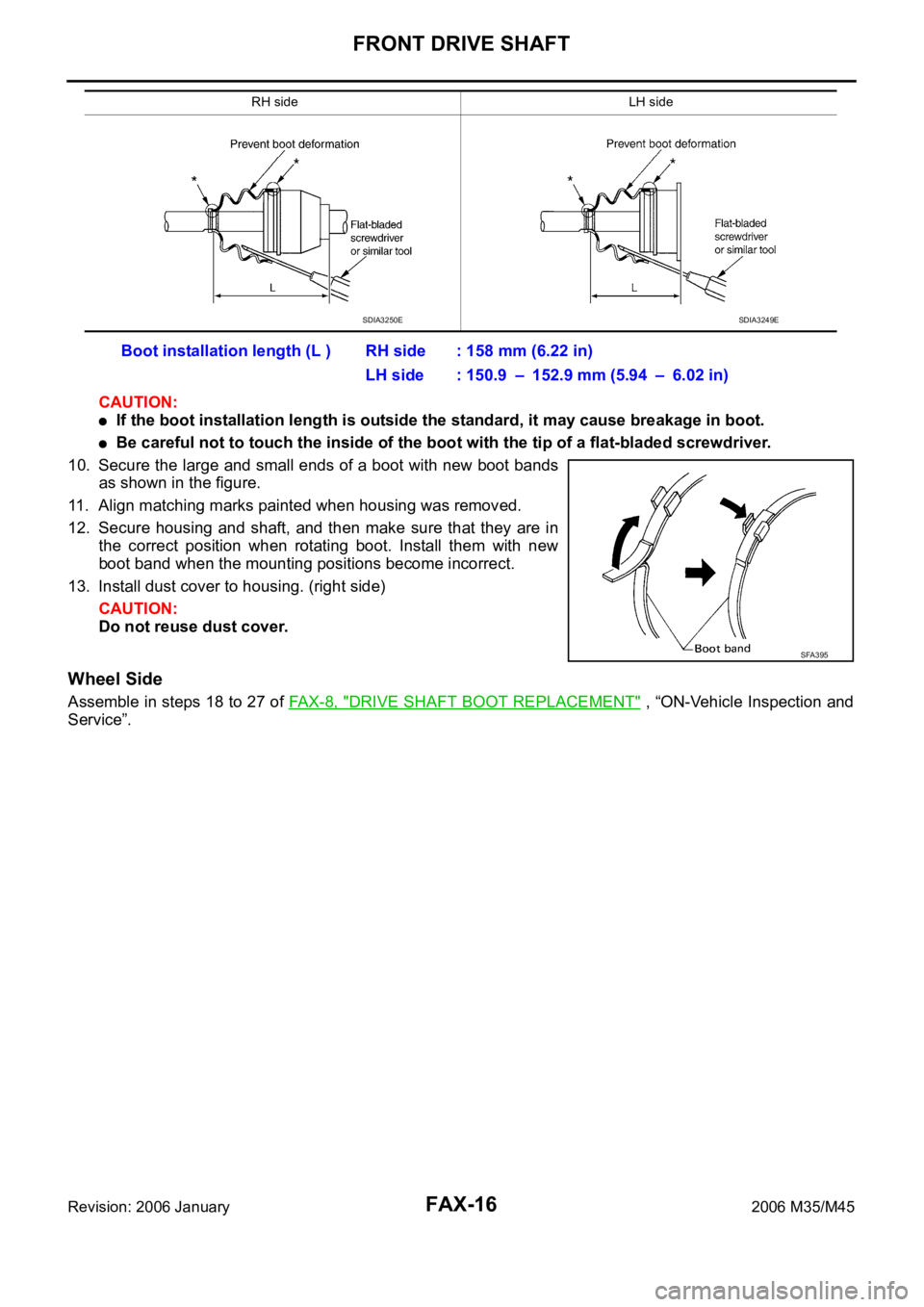
FAX-16
FRONT DRIVE SHAFT
Revision: 2006 January2006 M35/M45
CAUTION:
If the boot installation length is outside the standard, it may cause breakage in boot.
Be careful not to touch the inside of the boot with the tip of a flat-bladed screwdriver.
10. Secure the large and small ends of a boot with new boot bands
as shown in the figure.
11. Align matching marks painted when housing was removed.
12. Secure housing and shaft, and then make sure that they are in
the correct position when rotating boot. Install them with new
boot band when the mounting positions become incorrect.
13. Install dust cover to housing. (right side)
CAUTION:
Do not reuse dust cover.
Wheel Side
Assemble in steps 18 to 27 of FA X - 8 , "DRIVE SHAFT BOOT REPLACEMENT" , “ON-Vehicle Inspection and
Service”.
RH side LH side
Boot installation length (L ) RH side : 158 mm (6.22 in)
LH side : 150.9 – 152.9 mm (5.94 – 6.02 in)
SDIA3250ESDIA3249E
SFA395
Page 3376 of 5621
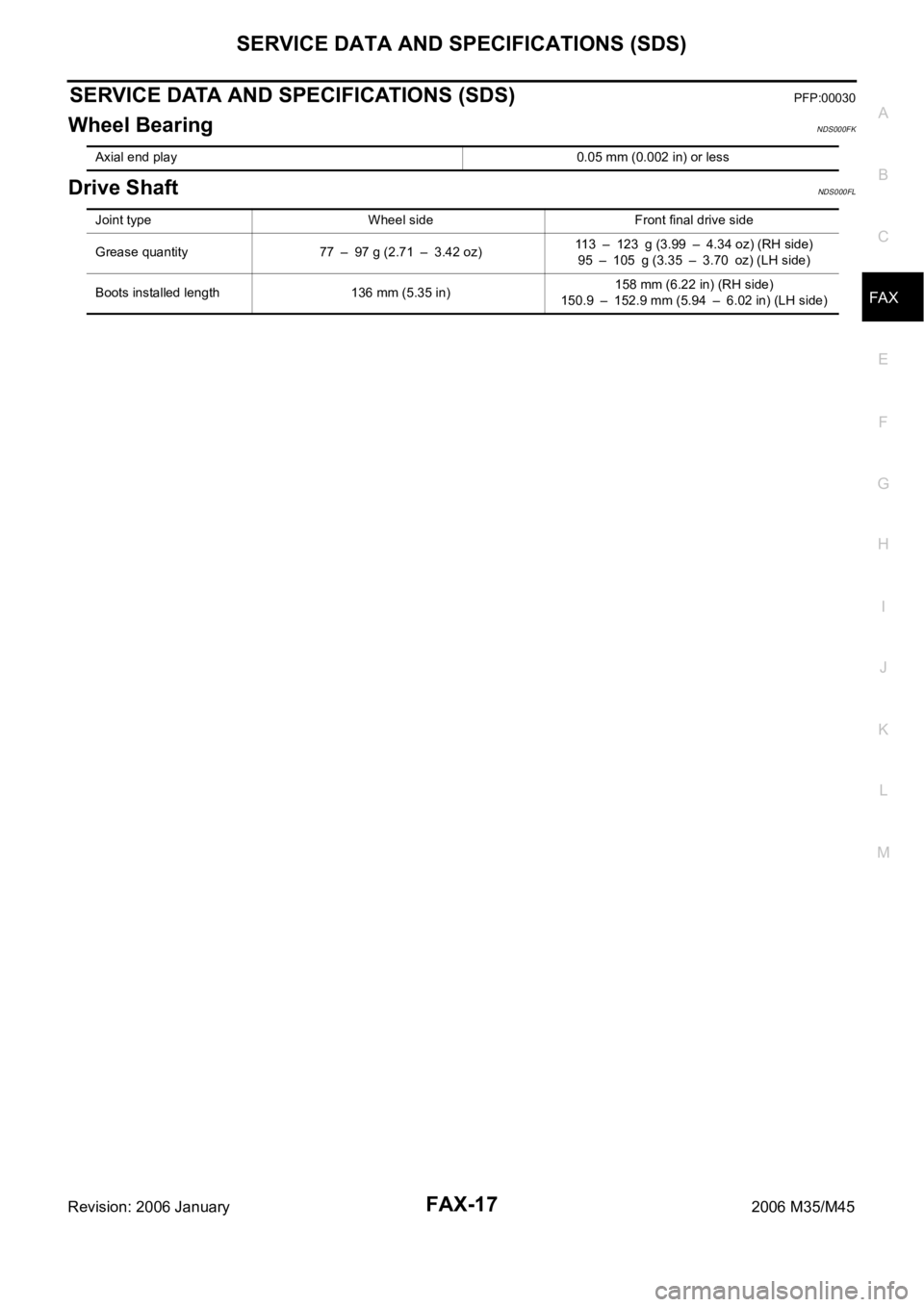
SERVICE DATA AND SPECIFICATIONS (SDS)
FAX-17
C
E
F
G
H
I
J
K
L
MA
B
FA X
Revision: 2006 January2006 M35/M45
SERVICE DATA AND SPECIFICATIONS (SDS)PFP:00030
Wheel BearingNDS000FK
Drive ShaftNDS000FL
Axial end play 0.05 mm (0.002 in) or less
Joint type Wheel side Front final drive side
Grease quantity 77 – 97 g (2.71 – 3.42 oz)113 – 123 g (3.99 – 4.34 oz) (RH side)
95 – 105 g (3.35 – 3.70 oz) (LH side)
Boots installed length 136 mm (5.35 in)158 mm (6.22 in) (RH side)
150.9 – 152.9 mm (5.94 – 6.02 in) (LH side)
Page 3377 of 5621
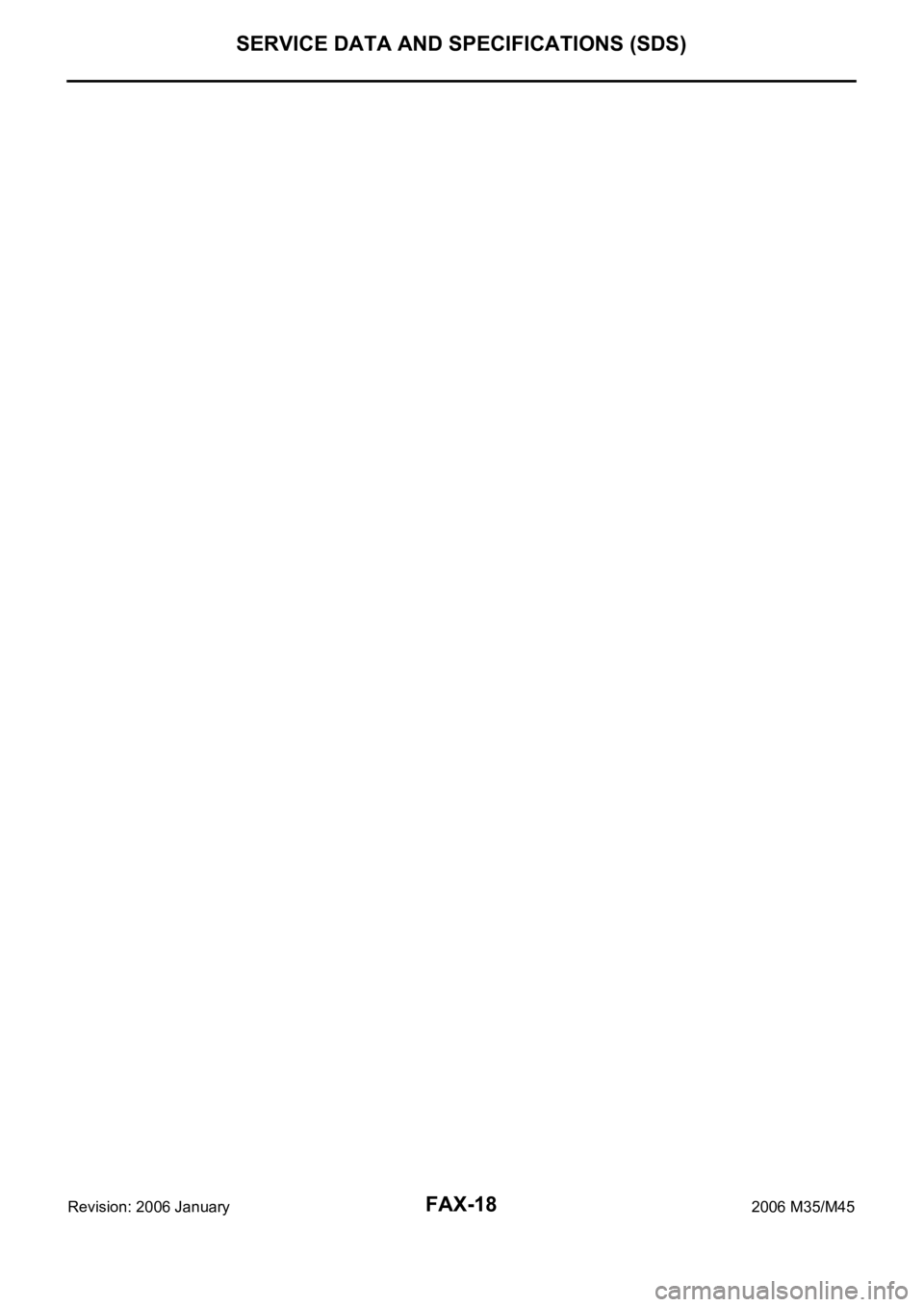
FAX-18
SERVICE DATA AND SPECIFICATIONS (SDS)
Revision: 2006 January2006 M35/M45
Page 3378 of 5621

FFD-1
FRONT FINAL DRIVE
D DRIVELINE/AXLE
CONTENTS
C
E
F
G
H
I
J
K
L
M
SECTION FFD
A
B
FFD
Revision: 2006 January2006 M35/M45
FRONT FINAL DRIVE
PRECAUTIONS .......................................................... 2
Precautions Necessary for Steering Wheel Rotation
after Battery Disconnect ........................................... 2
OPERATION PROCEDURE ................................. 2
Service Notice or Precautions .................................. 2
PREPARATION ........................................................... 3
Special Service Tools ............................................... 3
Commercial Service Tools ........................................ 5
NOISE, VIBRATION AND HARSHNESS (NVH)
TROUBLESHOOTING ................................................ 6
NVH Troubleshooting Chart ..................................... 6
DESCRIPTION ............................................................ 7
Cross-Sectional View ............................................... 7
DIFFERENTIAL GEAR OIL ........................................ 8
Changing Differential Gear Oil ................................. 8
DRAINING ............................................................. 8
FILLING ................................................................. 8
Checking Differential Gear Oil .................................. 8
OIL LEAKAGE AND OIL LEVEL ........................... 8
FRONT OIL SEAL .................................................
..... 9
Removal and Installation .......................................... 9
REMOVAL ........................................................
..... 9
INSTALLATION ................................................... 10SIDE OIL SEAL ......................................................... 11
Removal and Installation ........................................ 11
REMOVAL ........................................................
... 11
INSTALLATION ................................................... 11
FRONT FINAL DRIVE ASSEMBLY .......................... 13
Removal and Installation ........................................ 13
COMPONENTS ................................................... 13
REMOVAL ........................................................
... 13
INSTALLATION ................................................... 14
Disassembly and Assembly .................................... 15
COMPONENTS ................................................... 15
ASSEMBLY INSPECTION AND ADJUSTMENT ... 16
DISASSEMBLY ................................................... 20
INSPECTION AFTER DISASSEMBLY ................ 24
ADJUSTMENT AND SELECTION OF ADJUST-
ING WASHERS (SHIMS) .................................... 25
ASSEMBLY ......................................................... 28
SERVICE DATA AND SPECIFICATIONS (SDS) ...... 35
General Specifications ......................................... ... 35
Inspection and Adjustment ..................................... 35
DRIVE GEAR RUNOUT ...................................... 35
DIFFERENTIAL SIDE GEAR CLEARANCE ....... 35
PRELOAD TORQUE ........................................... 35
BACKLASH ......................................................... 35
COMPANION FLANGE RUNOUT ....................... 35
SELECTIVE PARTS ............................................ 35
Page 3379 of 5621
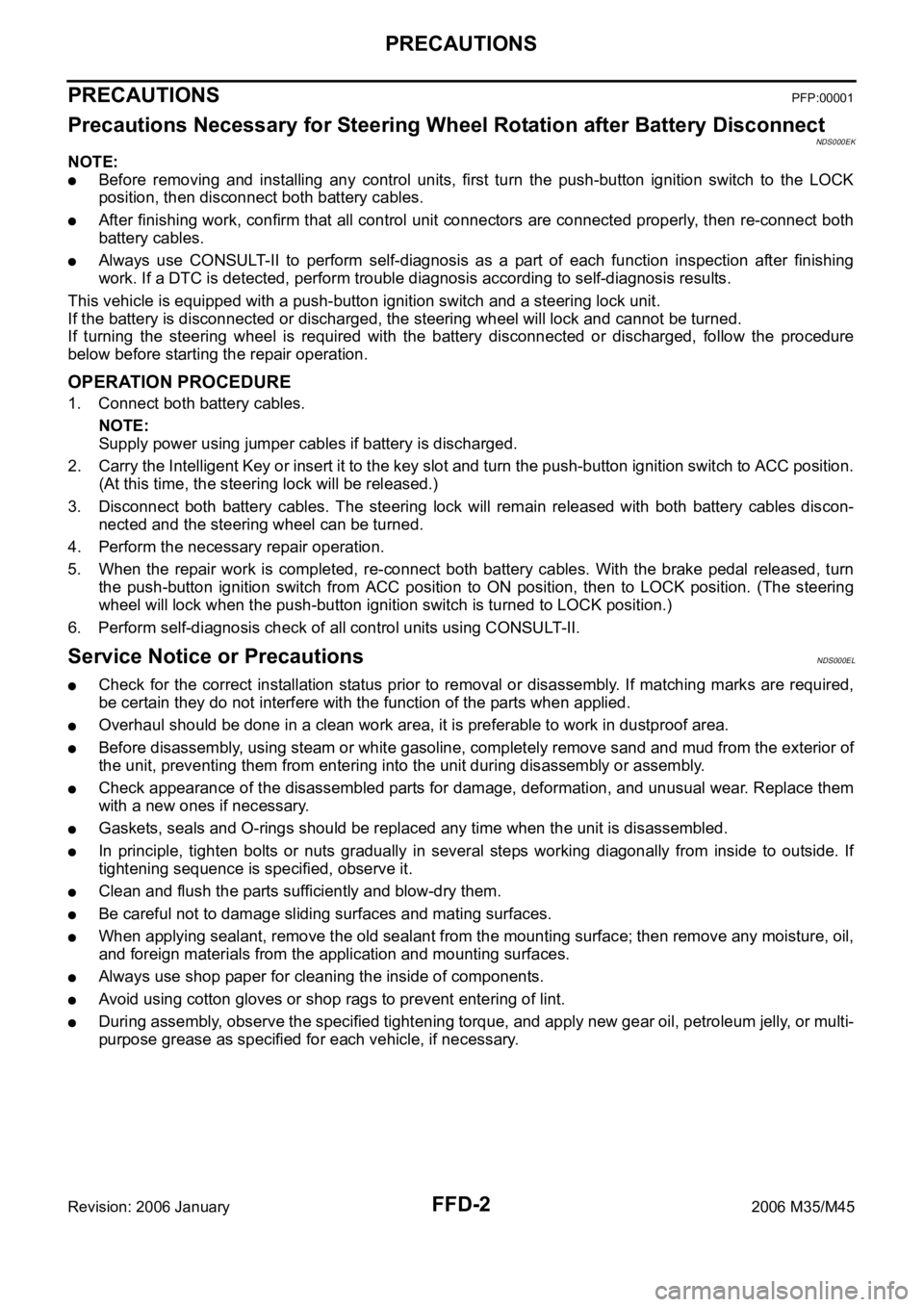
FFD-2
PRECAUTIONS
Revision: 2006 January2006 M35/M45
PRECAUTIONSPFP:00001
Precautions Necessary for Steering Wheel Rotation after Battery DisconnectNDS000EK
NOTE:
Before removing and installing any control units, first turn the push-button ignition switch to the LOCK
position, then disconnect both battery cables.
After finishing work, confirm that all control unit connectors are connected properly, then re-connect both
battery cables.
Always use CONSULT-II to perform self-diagnosis as a part of each function inspection after finishing
work. If a DTC is detected, perform trouble diagnosis according to self-diagnosis results.
This vehicle is equipped with a push-button ignition switch and a steering lock unit.
If the battery is disconnected or discharged, the steering wheel will lock and cannot be turned.
If turning the steering wheel is required with the battery disconnected or discharged, follow the procedure
below before starting the repair operation.
OPERATION PROCEDURE
1. Connect both battery cables.
NOTE:
Supply power using jumper cables if battery is discharged.
2. Carry the Intelligent Key or insert it to the key slot and turn the push-button ignition switch to ACC position.
(At this time, the steering lock will be released.)
3. Disconnect both battery cables. The steering lock will remain released with both battery cables discon-
nected and the steering wheel can be turned.
4. Perform the necessary repair operation.
5. When the repair work is completed, re-connect both battery cables. With the brake pedal released, turn
the push-button ignition switch from ACC position to ON position, then to LOCK position. (The steering
wheel will lock when the push-button ignition switch is turned to LOCK position.)
6. Perform self-diagnosis check of all control units using CONSULT-II.
Service Notice or PrecautionsNDS000EL
Check for the correct installation status prior to removal or disassembly. If matching marks are required,
be certain they do not interfere with the function of the parts when applied.
Overhaul should be done in a clean work area, it is preferable to work in dustproof area.
Before disassembly, using steam or white gasoline, completely remove sand and mud from the exterior of
the unit, preventing them from entering into the unit during disassembly or assembly.
Check appearance of the disassembled parts for damage, deformation, and unusual wear. Replace them
with a new ones if necessary.
Gaskets, seals and O-rings should be replaced any time when the unit is disassembled.
In principle, tighten bolts or nuts gradually in several steps working diagonally from inside to outside. If
tightening sequence is specified, observe it.
Clean and flush the parts sufficiently and blow-dry them.
Be careful not to damage sliding surfaces and mating surfaces.
When applying sealant, remove the old sealant from the mounting surface; then remove any moisture, oil,
and foreign materials from the application and mounting surfaces.
Always use shop paper for cleaning the inside of components.
Avoid using cotton gloves or shop rags to prevent entering of lint.
During assembly, observe the specified tightening torque, and apply new gear oil, petroleum jelly, or multi-
purpose grease as specified for each vehicle, if necessary.
Page 3380 of 5621
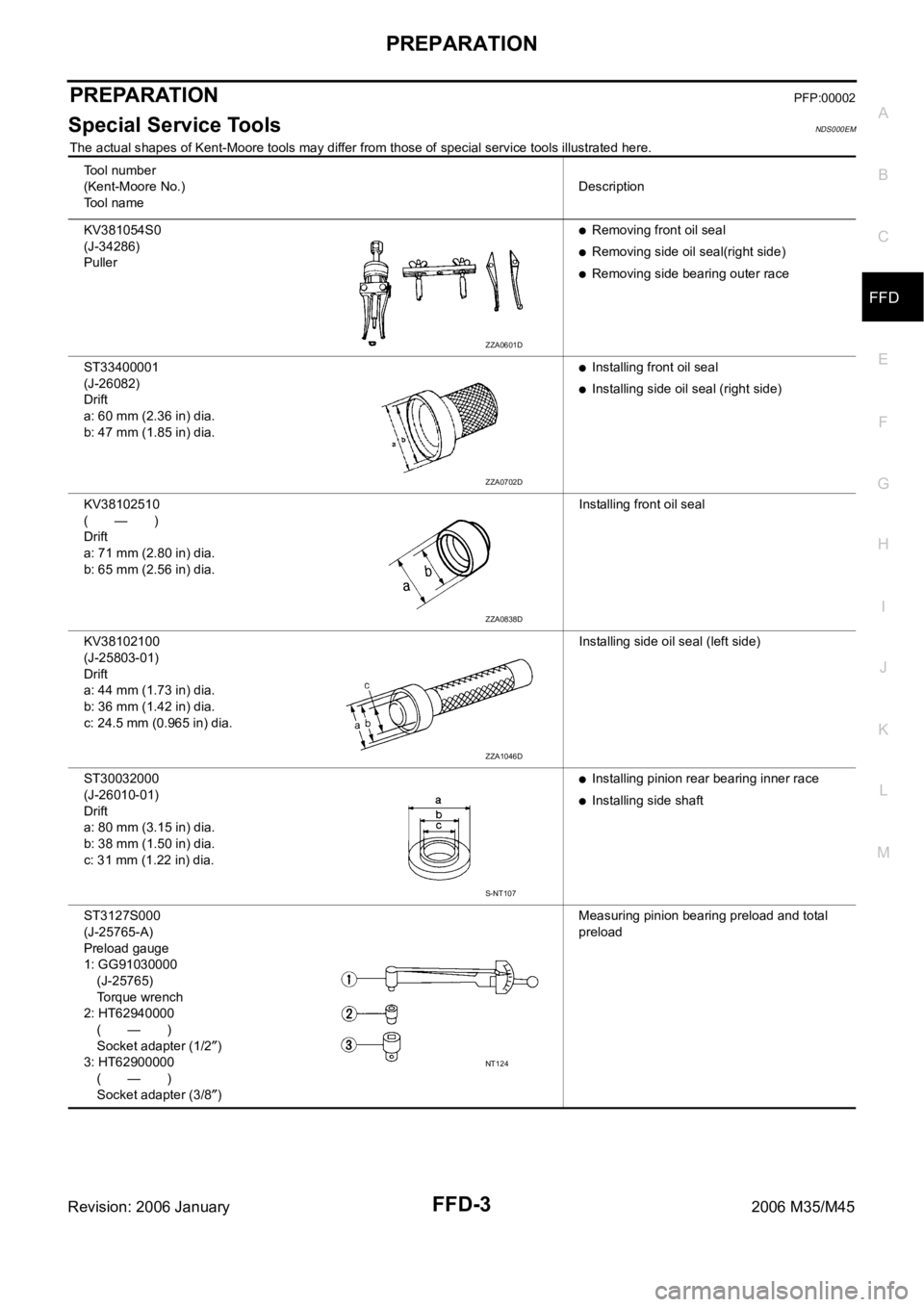
PREPARATION
FFD-3
C
E
F
G
H
I
J
K
L
MA
B
FFD
Revision: 2006 January2006 M35/M45
PREPARATIONPFP:00002
Special Service ToolsNDS000EM
The actual shapes of Kent-Moore tools may differ from those of special service tools illustrated here.
To o l n u m b e r
(Kent-Moore No.)
To o l n a m eDescription
KV381054S0
(J-34286)
Puller
Removing front oil seal
Removing side oil seal(right side)
Removing side bearing outer race
ST33400001
(J-26082)
Drift
a: 60 mm (2.36 in) dia.
b: 47 mm (1.85 in) dia.
Installing front oil seal
Installing side oil seal (right side)
KV38102510
(—)
Drift
a: 71 mm (2.80 in) dia.
b: 65 mm (2.56 in) dia.Installing front oil seal
KV38102100
(J-25803-01)
Drift
a: 44 mm (1.73 in) dia.
b: 36 mm (1.42 in) dia.
c: 24.5 mm (0.965 in) dia.Installing side oil seal (left side)
ST30032000
(J-26010-01)
Drift
a: 80 mm (3.15 in) dia.
b: 38 mm (1.50 in) dia.
c: 31 mm (1.22 in) dia.
Installing pinion rear bearing inner race
Installing side shaft
ST3127S000
(J-25765-A)
Preload gauge
1: GG91030000
(J-25765)
Torque wrench
2: HT62940000
(—)
Socket adapter (1/2
)
3: HT62900000
(—)
Socket adapter (3/8
)Measuring pinion bearing preload and total
preload
ZZA0601D
ZZA0702D
ZZA0838D
ZZA1046D
S-NT107
NT124
Page 3382 of 5621
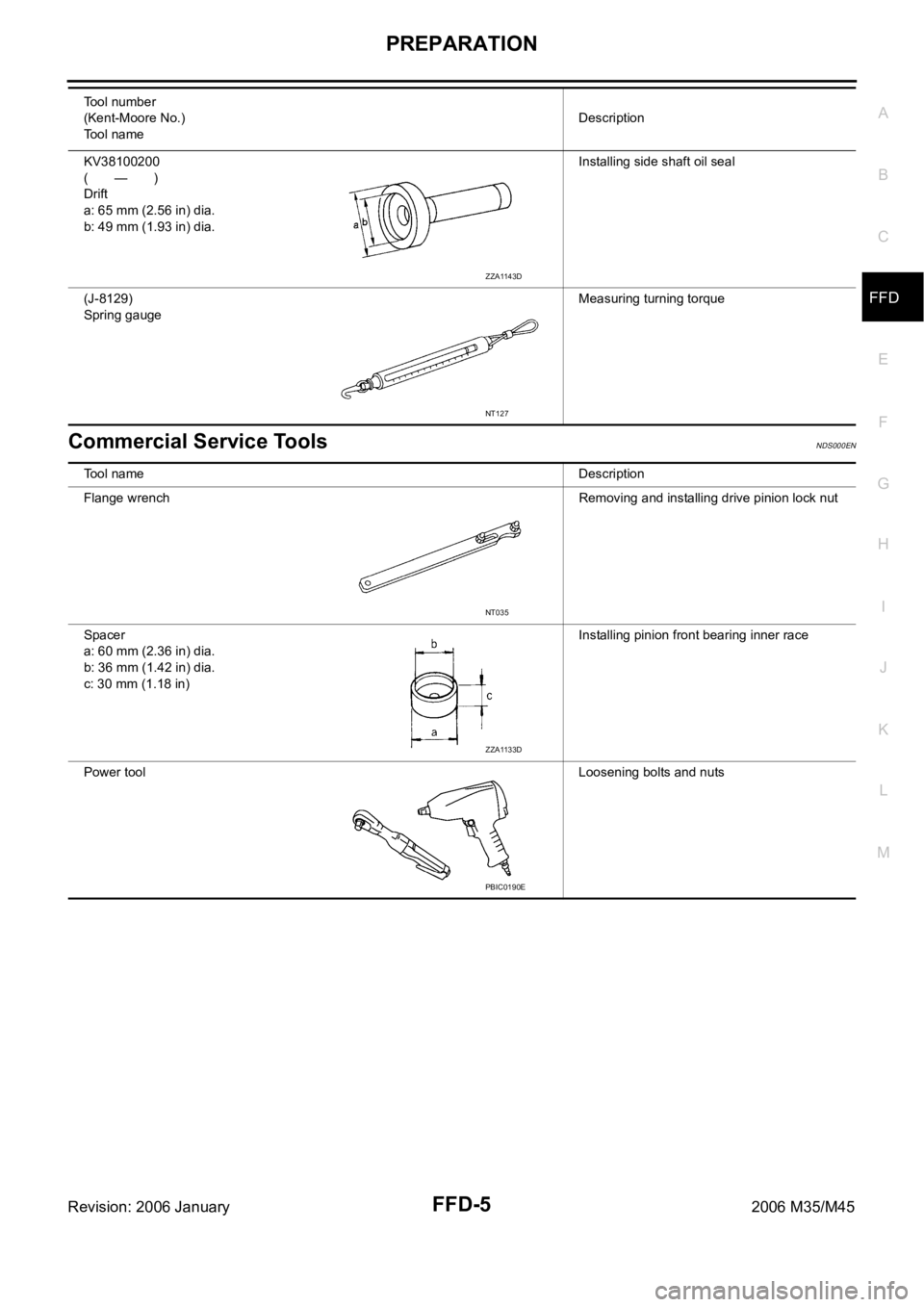
PREPARATION
FFD-5
C
E
F
G
H
I
J
K
L
MA
B
FFD
Revision: 2006 January2006 M35/M45
Commercial Service ToolsNDS000EN
KV38100200
(—)
Drift
a: 65 mm (2.56 in) dia.
b: 49 mm (1.93 in) dia.Installing side shaft oil seal
(J-8129)
Spring gaugeMeasuring turning torque Tool number
(Kent-Moore No.)
Tool nameDescription
ZZA1143D
NT127
Tool nameDescription
Flange wrench Removing and installing drive pinion lock nut
Spacer
a: 60 mm (2.36 in) dia.
b: 36 mm (1.42 in) dia.
c: 30 mm (1.18 in)Installing pinion front bearing inner race
Power toolLoosening bolts and nuts
NT035
ZZA1133D
PBIC0190E
Page 3412 of 5621
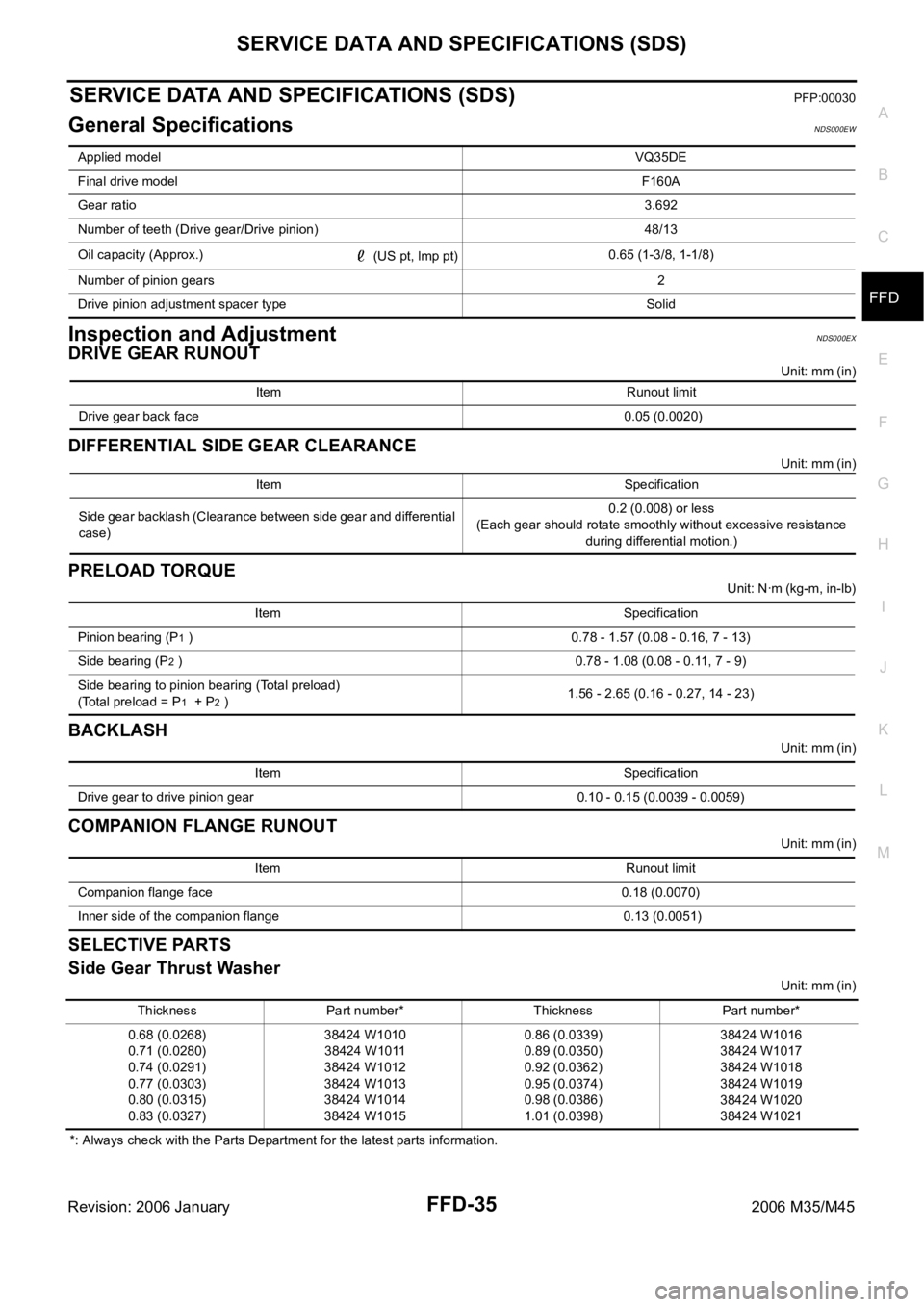
SERVICE DATA AND SPECIFICATIONS (SDS)
FFD-35
C
E
F
G
H
I
J
K
L
MA
B
FFD
Revision: 2006 January2006 M35/M45
SERVICE DATA AND SPECIFICATIONS (SDS)PFP:00030
General SpecificationsNDS000EW
Inspection and AdjustmentNDS000EX
DRIVE GEAR RUNOUT
Unit: mm (in)
DIFFERENTIAL SIDE GEAR CLEARANCE
Unit: mm (in)
PRELOAD TORQUE
Unit: Nꞏm (kg-m, in-lb)
BACKLASH
Unit: mm (in)
COMPANION FLANGE RUNOUT
Unit: mm (in)
SELECTIVE PARTS
Side Gear Thrust Washer
Unit: mm (in)
*: Always check with the Parts Department for the latest parts information. Applied modelVQ35DE
Final drive modelF160A
Gear ratio3.692
Number of teeth (Drive gear/Drive pinion) 48/13
Oil capacity (Approx.)
(US pt, lmp pt)0.65 (1-3/8, 1-1/8)
Number of pinion gears2
Drive pinion adjustment spacer type Solid
Item Runout limit
Drive gear back face 0.05 (0.0020)
Item Specification
Side gear backlash (Clearance between side gear and differential
case)0.2 (0.008) or less
(Each gear should rotate smoothly without excessive resistance
during differential motion.)
Item Specification
Pinion bearing (P
1 ) 0.78 - 1.57 (0.08 - 0.16, 7 - 13)
Side bearing (P
2 ) 0.78 - 1.08 (0.08 - 0.11, 7 - 9)
Side bearing to pinion bearing (Total preload)
(Total preload = P
1 + P2 )1.56 - 2.65 (0.16 - 0.27, 14 - 23)
Item Specification
Drive gear to drive pinion gear 0.10 - 0.15 (0.0039 - 0.0059)
Item Runout limit
Companion flange face 0.18 (0.0070)
Inner side of the companion flange 0.13 (0.0051)
Thickness Part number* Thickness Part number*
0.68 (0.0268)
0.71 (0.0280)
0.74 (0.0291)
0.77 (0.0303)
0.80 (0.0315)
0.83 (0.0327)38424 W1010
38424 W1011
38424 W1012
38424 W1013
38424 W1014
38424 W10150.86 (0.0339)
0.89 (0.0350)
0.92 (0.0362)
0.95 (0.0374)
0.98 (0.0386)
1.01 (0.0398)38424 W1016
38424 W1017
38424 W1018
38424 W1019
38424 W1020
38424 W1021
Page 3413 of 5621
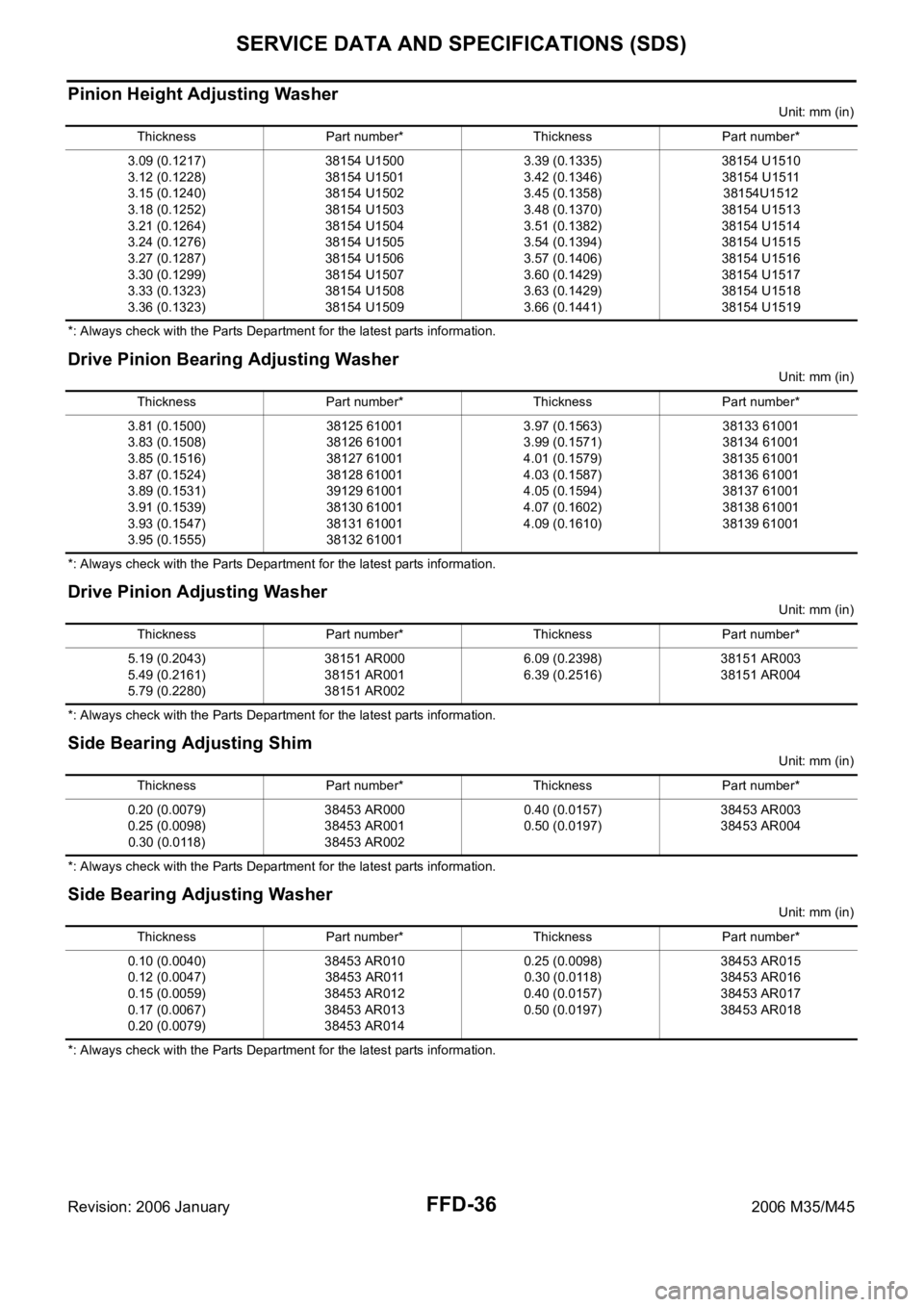
FFD-36
SERVICE DATA AND SPECIFICATIONS (SDS)
Revision: 2006 January2006 M35/M45
Pinion Height Adjusting Washer
Unit: mm (in)
*: Always check with the Parts Department for the latest parts information.
Drive Pinion Bearing Adjusting Washer
Unit: mm (in)
*: Always check with the Parts Department for the latest parts information.
Drive Pinion Adjusting Washer
Unit: mm (in)
*: Always check with the Parts Department for the latest parts information.
Side Bearing Adjusting Shim
Unit: mm (in)
*: Always check with the Parts Department for the latest parts information.
Side Bearing Adjusting Washer
Unit: mm (in)
*: Always check with the Parts Department for the latest parts information. Thickness Part number* Thickness Part number*
3.09 (0.1217)
3.12 (0.1228)
3.15 (0.1240)
3.18 (0.1252)
3.21 (0.1264)
3.24 (0.1276)
3.27 (0.1287)
3.30 (0.1299)
3.33 (0.1323)
3.36 (0.1323)38154 U1500
38154 U1501
38154 U1502
38154 U1503
38154 U1504
38154 U1505
38154 U1506
38154 U1507
38154 U1508
38154 U15093.39 (0.1335)
3.42 (0.1346)
3.45 (0.1358)
3.48 (0.1370)
3.51 (0.1382)
3.54 (0.1394)
3.57 (0.1406)
3.60 (0.1429)
3.63 (0.1429)
3.66 (0.1441)38154 U1510
38154 U1511
38154U1512
38154 U1513
38154 U1514
38154 U1515
38154 U1516
38154 U1517
38154 U1518
38154 U1519
Thickness Part number* Thickness Part number*
3.81 (0.1500)
3.83 (0.1508)
3.85 (0.1516)
3.87 (0.1524)
3.89 (0.1531)
3.91 (0.1539)
3.93 (0.1547)
3.95 (0.1555)38125 61001
38126 61001
38127 61001
38128 61001
39129 61001
38130 61001
38131 61001
38132 610013.97 (0.1563)
3.99 (0.1571)
4.01 (0.1579)
4.03 (0.1587)
4.05 (0.1594)
4.07 (0.1602)
4.09 (0.1610)38133 61001
38134 61001
38135 61001
38136 61001
38137 61001
38138 61001
38139 61001
Thickness Part number* Thickness Part number*
5.19 (0.2043)
5.49 (0.2161)
5.79 (0.2280)38151 AR000
38151 AR001
38151 AR0026.09 (0.2398)
6.39 (0.2516)38151 AR003
38151 AR004
Thickness Part number* Thickness Part number*
0.20 (0.0079)
0.25 (0.0098)
0.30 (0.0118)38453 AR000
38453 AR001
38453 AR0020.40 (0.0157)
0.50 (0.0197)38453 AR003
38453 AR004
Thickness Part number* Thickness Part number*
0.10 (0.0040)
0.12 (0.0047)
0.15 (0.0059)
0.17 (0.0067)
0.20 (0.0079)38453 AR010
38453 AR011
38453 AR012
38453 AR013
38453 AR0140.25 (0.0098)
0.30 (0.0118)
0.40 (0.0157)
0.50 (0.0197)38453 AR015
38453 AR016
38453 AR017
38453 AR018