service INFINITI M35 2006 Factory Service Manual
[x] Cancel search | Manufacturer: INFINITI, Model Year: 2006, Model line: M35, Model: INFINITI M35 2006Pages: 5621, PDF Size: 65.56 MB
Page 3350 of 5621
![INFINITI M35 2006 Factory Service Manual SERVICE DATA AND SPECIFICATIONS (SDS)
EM-287
[VK45DE]
C
D
E
F
G
H
I
J
K
L
MA
EM
Revision: 2006 January2006 M35/M45
MAIN BEARING
Unit: mm (in)
Undersize
Unit: mm (in) Grade number Thickness Identifica INFINITI M35 2006 Factory Service Manual SERVICE DATA AND SPECIFICATIONS (SDS)
EM-287
[VK45DE]
C
D
E
F
G
H
I
J
K
L
MA
EM
Revision: 2006 January2006 M35/M45
MAIN BEARING
Unit: mm (in)
Undersize
Unit: mm (in) Grade number Thickness Identifica](/img/42/57023/w960_57023-3349.png)
SERVICE DATA AND SPECIFICATIONS (SDS)
EM-287
[VK45DE]
C
D
E
F
G
H
I
J
K
L
MA
EM
Revision: 2006 January2006 M35/M45
MAIN BEARING
Unit: mm (in)
Undersize
Unit: mm (in) Grade number Thickness Identification color Remarks
0 2.483 - 2.486 (0.0978 - 0.0979) Black
Grade and color are the same
for upper and lower bearings. 1 2.486 - 2.489 (0.0979 - 0.0980) Brown
2 2.489 - 2.492 (0.0980 - 0.0981) Green
3 2.492 - 2.495 (0.0981 - 0.0982) Yellow
4 2.495 - 2.498 (0.0982 - 0.0983) Blue
5 2.498 - 2.501 (0.0983 - 0.0985) Pink
6 2.501 - 2.504 (0.0985 - 0.0986) Purple
7 2.504 - 2.507 (0.0986 - 0.0987) White
8 2.507 - 2.510 (0.0987 - 0.0988) Red
01UPR 2.483 - 2.486 (0.0978 - 0.0979) Black
Grade and color are different
for upper and lower bearings. LWR 2.486 - 2.489 (0.0979 - 0.0980) Brown
12UPR 2.486 - 2.489 (0.0979 - 0.0980) Brown
LWR 2.489 - 2.492 (0.0980 - 0.0981) Green
23UPR 2.489 - 2.492 (0.0980 - 0.0981) Green
LWR 2.492 - 2.495 (0.0981 - 0.0982) Yellow
34UPR 2.492 - 2.495 (0.0981 - 0.0982) Yellow
LWR 2.495 - 2.498 (0.0982 - 0.0983) Blue
45UPR 2.495 - 2.498 (0.0982 - 0.0983) Blue
LWR 2.498 - 2.501 (0.0983 - 0.0985) Pink
56UPR 2.498 - 2.501 (0.0983 - 0.0985) Pink
LWR 2.501 - 2.504 (0.0985 - 0.0986) Purple
67UPR 2.501 - 2.504 (0.0985 - 0.0986) Purple
LWR 2.504 - 2.507 (0.0986 - 0.0987) White
78UPR 2.504 - 2.507 (0.0986 - 0.0987) White
LWR 2.507 - 2.510 (0.0987 - 0.0988) Red
PBIC0189E
Undersize Thickness Main journal diameter
0.25 (0.0098) 2.618 - 2.626 (0.1031 - 0.1034) Grind so that bearing clearance is the specified value.
Page 3351 of 5621
![INFINITI M35 2006 Factory Service Manual EM-288
[VK45DE]
SERVICE DATA AND SPECIFICATIONS (SDS)
Revision: 2006 January2006 M35/M45
Main Bearing Oil Clearance
Unit: mm (in)
CONNECTING ROD BEARING
Unit: mm (in)
Undersize
Unit: mm (in)
Connectin INFINITI M35 2006 Factory Service Manual EM-288
[VK45DE]
SERVICE DATA AND SPECIFICATIONS (SDS)
Revision: 2006 January2006 M35/M45
Main Bearing Oil Clearance
Unit: mm (in)
CONNECTING ROD BEARING
Unit: mm (in)
Undersize
Unit: mm (in)
Connectin](/img/42/57023/w960_57023-3350.png)
EM-288
[VK45DE]
SERVICE DATA AND SPECIFICATIONS (SDS)
Revision: 2006 January2006 M35/M45
Main Bearing Oil Clearance
Unit: mm (in)
CONNECTING ROD BEARING
Unit: mm (in)
Undersize
Unit: mm (in)
Connecting Rod Bearing Oil Clearance
Unit: mm (in) Main bearing oil clearanceStandardNo.1 and 5 0.001 - 0.011 (0.00004 - 0.0004)
No.2, 3 and 4 0.007 - 0.017 (0.0003 - 0.0007)
LimitNo.1 and 5 0.021 (0.0008)
No.2, 3 and 4 0.027 (0.0011)
Grade number Thickness Identification color (mark)
0 1.500 - 1.503 (0.0591 - 0.0592) No color
1 1.503 - 1.506 (0.0592 - 0.0593) Brown
2 1.506 - 1.509 (0.0593 - 0.0594) Green
Undersize Thickness Pin journal diameter
0.25 (0.0098) 1.626 - 1.634 (0.0640 - 0.0643) Grind so that bearing clearance is the specified value.
Connecting rod bearing oil clearanceStandard 0.020 - 0.045 (0.0008 - 0.0018)
Limit 0.055 (0.0022)
Page 3352 of 5621
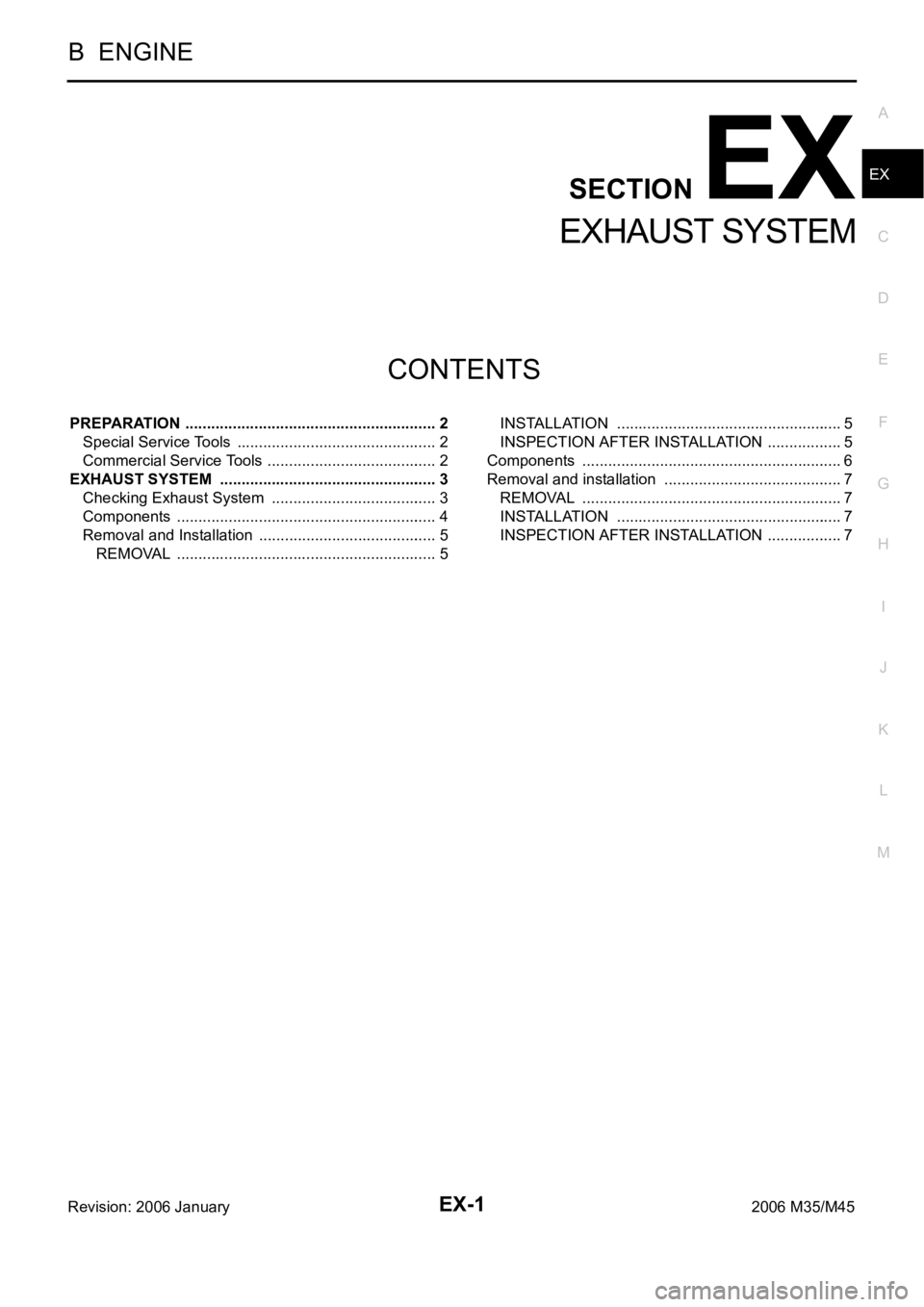
EX-1
EXHAUST SYSTEM
B ENGINE
CONTENTS
C
D
E
F
G
H
I
J
K
L
M
SECTION EX
A
EX
Revision: 2006 January2006 M35/M45
EXHAUST SYSTEM
PREPARATION ........................................................... 2
Special Service Tools ............................................... 2
Commercial Service Tools ........................................ 2
EXHAUST SYSTEM ................................................... 3
Checking Exhaust System ....................................... 3
Components ............................................................. 4
Removal and Installation .......................................... 5
REMOVAL ........................................................
..... 5INSTALLATION ..................................................... 5
INSPECTION AFTER INSTALLATION .................. 5
Components ............................................................. 6
Removal and installation .......................................... 7
REMOVAL ........................................................
..... 7
INSTALLATION ..................................................... 7
INSPECTION AFTER INSTALLATION .................. 7
Page 3353 of 5621
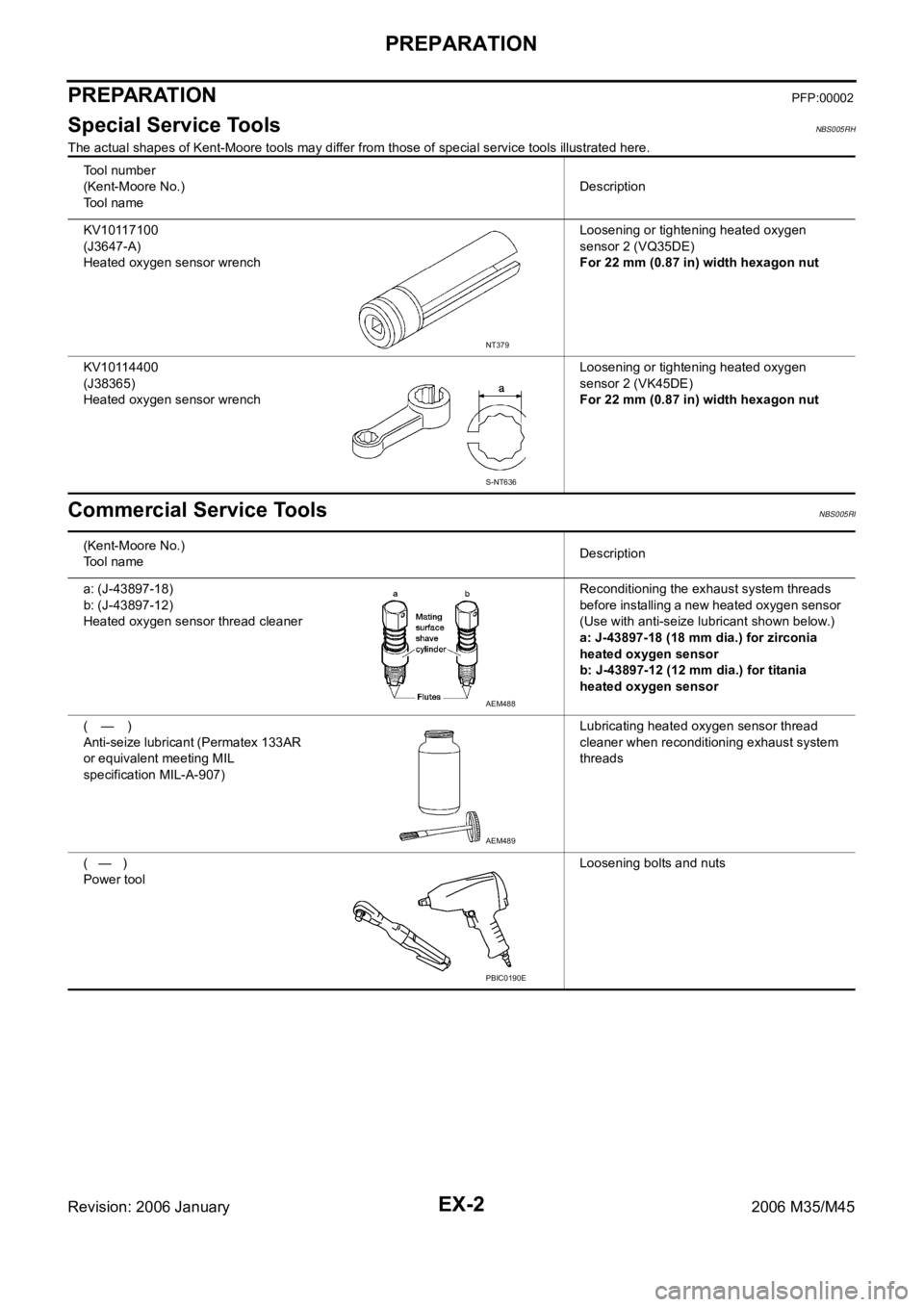
EX-2
PREPARATION
Revision: 2006 January2006 M35/M45
PREPARATIONPFP:00002
Special Service ToolsNBS005RH
The actual shapes of Kent-Moore tools may differ from those of special service tools illustrated here.
Commercial Service ToolsNBS005RI
Tool number
(Kent-Moore No.)
Tool nameDescription
KV10117100
(J3647-A)
Heated oxygen sensor wrenchLoosening or tightening heated oxygen
sensor 2 (VQ35DE)
For 22 mm (0.87 in) width hexagon nut
KV10114400
(J38365)
Heated oxygen sensor wrenchLoosening or tightening heated oxygen
sensor 2 (VK45DE)
For 22 mm (0.87 in) width hexagon nut
NT379
S-NT636
(Kent-Moore No.)
Tool nameDescription
a: (J-43897-18)
b: (J-43897-12)
Heated oxygen sensor thread cleanerReconditioning the exhaust system threads
before installing a new heated oxygen sensor
(Use with anti-seize lubricant shown below.)
a: J-43897-18 (18 mm dia.) for zirconia
heated oxygen sensor
b: J-43897-12 (12 mm dia.) for titania
heated oxygen sensor
(—)
Anti-seize lubricant (Permatex 133AR
or equivalent meeting MIL
specification MIL-A-907)Lubricating heated oxygen sensor thread
cleaner when reconditioning exhaust system
threads
( — )
Power toolLoosening bolts and nuts
AEM488
AEM489
PBIC0190E
Page 3356 of 5621
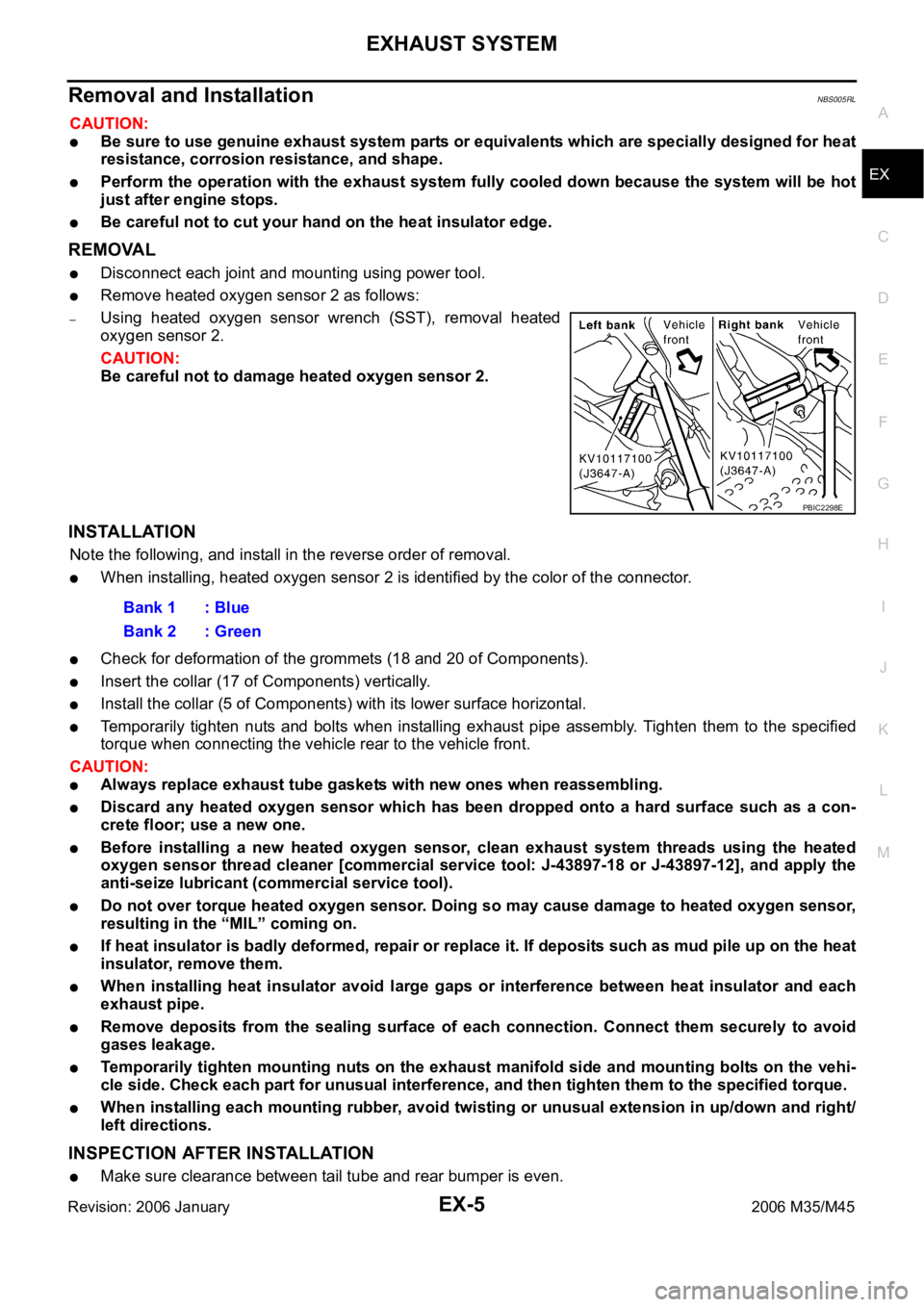
EXHAUST SYSTEM
EX-5
C
D
E
F
G
H
I
J
K
L
MA
EX
Revision: 2006 January2006 M35/M45
Removal and InstallationNBS005RL
CAUTION:
Be sure to use genuine exhaust system parts or equivalents which are specially designed for heat
resistance, corrosion resistance, and shape.
Perform the operation with the exhaust system fully cooled down because the system will be hot
just after engine stops.
Be careful not to cut your hand on the heat insulator edge.
REMOVAL
Disconnect each joint and mounting using power tool.
Remove heated oxygen sensor 2 as follows:
–Using heated oxygen sensor wrench (SST), removal heated
oxygen sensor 2.
CAUTION:
Be careful not to damage heated oxygen sensor 2.
INSTALLATION
Note the following, and install in the reverse order of removal.
When installing, heated oxygen sensor 2 is identified by the color of the connector.
Check for deformation of the grommets (18 and 20 of Components).
Insert the collar (17 of Components) vertically.
Install the collar (5 of Components) with its lower surface horizontal.
Temporarily tighten nuts and bolts when installing exhaust pipe assembly. Tighten them to the specified
torque when connecting the vehicle rear to the vehicle front.
CAUTION:
Always replace exhaust tube gaskets with new ones when reassembling.
Discard any heated oxygen sensor which has been dropped onto a hard surface such as a con-
crete floor; use a new one.
Before installing a new heated oxygen sensor, clean exhaust system threads using the heated
oxygen sensor thread cleaner [commercial service tool: J-43897-18 or J-43897-12], and apply the
anti-seize lubricant (commercial service tool).
Do not over torque heated oxygen sensor. Doing so may cause damage to heated oxygen sensor,
resulting in the “MIL” coming on.
If heat insulator is badly deformed, repair or replace it. If deposits such as mud pile up on the heat
insulator, remove them.
When installing heat insulator avoid large gaps or interference between heat insulator and each
exhaust pipe.
Remove deposits from the sealing surface of each connection. Connect them securely to avoid
gases leakage.
Temporarily tighten mounting nuts on the exhaust manifold side and mounting bolts on the vehi-
cle side. Check each part for unusual interference, and then tighten them to the specified torque.
When installing each mounting rubber, avoid twisting or unusual extension in up/down and right/
left directions.
INSPECTION AFTER INSTALLATION
Make sure clearance between tail tube and rear bumper is even.
PBIC2298E
Bank 1 : Blue
Bank 2 : Green
Page 3358 of 5621
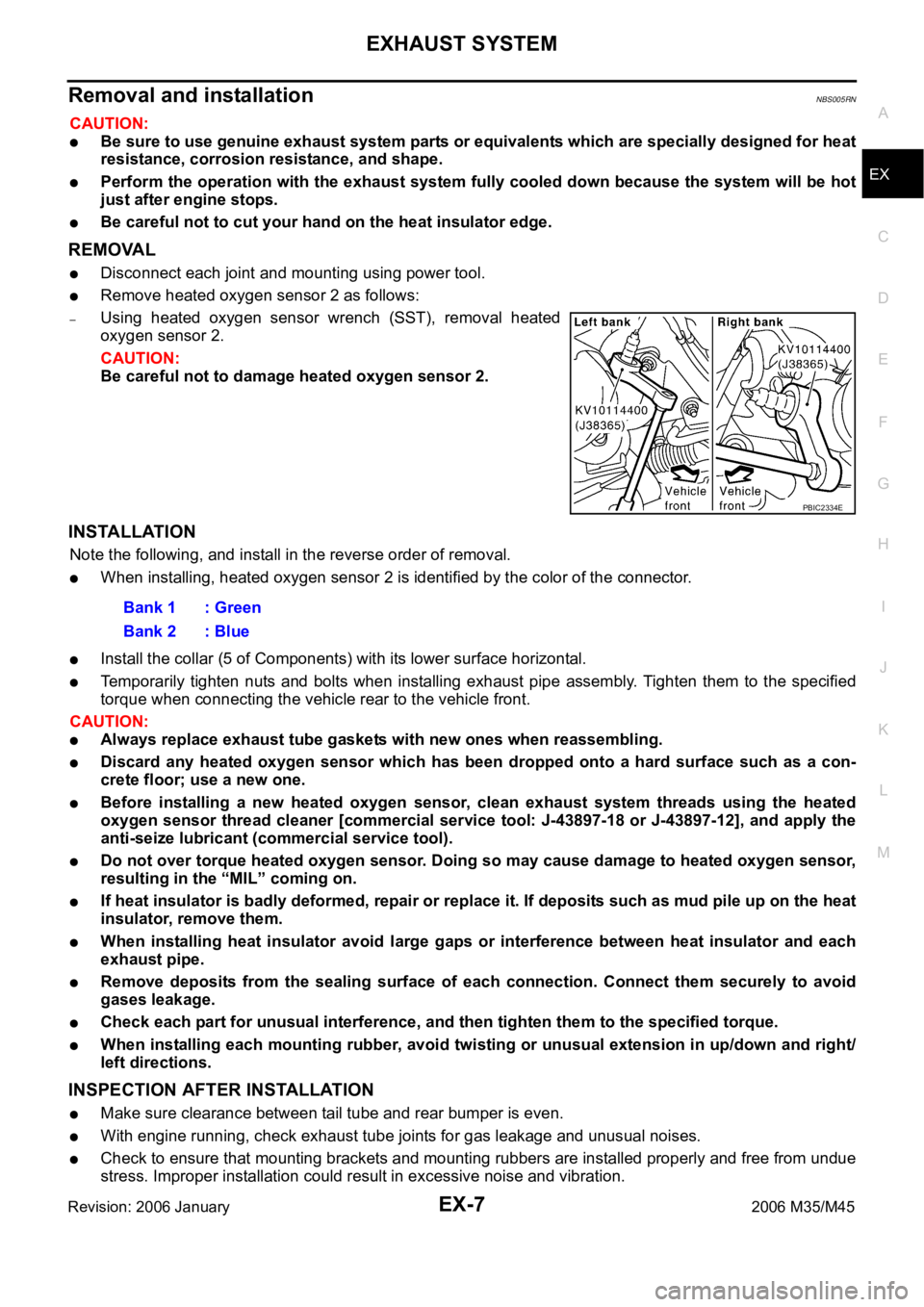
EXHAUST SYSTEM
EX-7
C
D
E
F
G
H
I
J
K
L
MA
EX
Revision: 2006 January2006 M35/M45
Removal and installationNBS005RN
CAUTION:
Be sure to use genuine exhaust system parts or equivalents which are specially designed for heat
resistance, corrosion resistance, and shape.
Perform the operation with the exhaust system fully cooled down because the system will be hot
just after engine stops.
Be careful not to cut your hand on the heat insulator edge.
REMOVAL
Disconnect each joint and mounting using power tool.
Remove heated oxygen sensor 2 as follows:
–Using heated oxygen sensor wrench (SST), removal heated
oxygen sensor 2.
CAUTION:
Be careful not to damage heated oxygen sensor 2.
INSTALLATION
Note the following, and install in the reverse order of removal.
When installing, heated oxygen sensor 2 is identified by the color of the connector.
Install the collar (5 of Components) with its lower surface horizontal.
Temporarily tighten nuts and bolts when installing exhaust pipe assembly. Tighten them to the specified
torque when connecting the vehicle rear to the vehicle front.
CAUTION:
Always replace exhaust tube gaskets with new ones when reassembling.
Discard any heated oxygen sensor which has been dropped onto a hard surface such as a con-
crete floor; use a new one.
Before installing a new heated oxygen sensor, clean exhaust system threads using the heated
oxygen sensor thread cleaner [commercial service tool: J-43897-18 or J-43897-12], and apply the
anti-seize lubricant (commercial service tool).
Do not over torque heated oxygen sensor. Doing so may cause damage to heated oxygen sensor,
resulting in the “MIL” coming on.
If heat insulator is badly deformed, repair or replace it. If deposits such as mud pile up on the heat
insulator, remove them.
When installing heat insulator avoid large gaps or interference between heat insulator and each
exhaust pipe.
Remove deposits from the sealing surface of each connection. Connect them securely to avoid
gases leakage.
Check each part for unusual interference, and then tighten them to the specified torque.
When installing each mounting rubber, avoid twisting or unusual extension in up/down and right/
left directions.
INSPECTION AFTER INSTALLATION
Make sure clearance between tail tube and rear bumper is even.
With engine running, check exhaust tube joints for gas leakage and unusual noises.
Check to ensure that mounting brackets and mounting rubbers are installed properly and free from undue
stress. Improper installation could result in excessive noise and vibration.
PBIC2334E
Bank 1 : Green
Bank 2 : Blue
Page 3360 of 5621
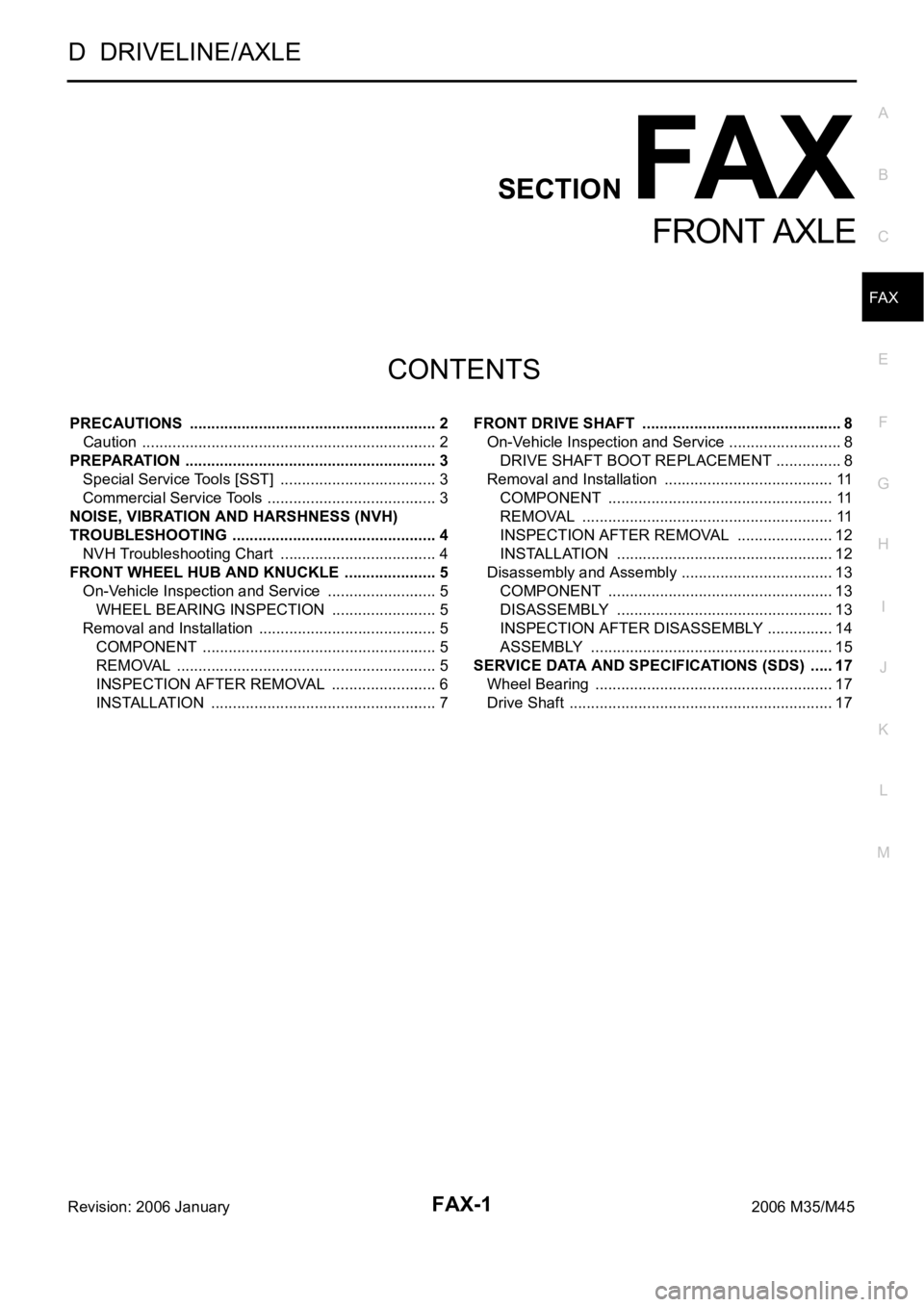
FAX-1
FRONT AXLE
D DRIVELINE/AXLE
CONTENTS
C
E
F
G
H
I
J
K
L
M
SECTION FA X
A
B
FA X
Revision: 2006 January2006 M35/M45
FRONT AXLE
PRECAUTIONS .......................................................... 2
Caution ..................................................................... 2
PREPARATION ........................................................... 3
Special Service Tools [SST] ..................................... 3
Commercial Service Tools ........................................ 3
NOISE, VIBRATION AND HARSHNESS (NVH)
TROUBLESHOOTING ................................................ 4
NVH Troubleshooting Chart ..................................... 4
FRONT WHEEL HUB AND KNUCKLE ...................... 5
On-Vehicle Inspection and Service .......................... 5
WHEEL BEARING INSPECTION ......................... 5
Removal and Installation .......................................... 5
COMPONENT ....................................................... 5
REMOVAL ........................................................
..... 5
INSPECTION AFTER REMOVAL ......................... 6
INSTALLATION ..................................................... 7FRONT DRIVE SHAFT ............................................... 8
On-Vehicle Inspection and Service ........................... 8
DRIVE SHAFT BOOT REPLACEMENT ................ 8
Removal and Installation ........................................ 11
COMPONENT ..................................................... 11
REMOVAL ........................................................
... 11
INSPECTION AFTER REMOVAL ....................... 12
INSTALLATION ................................................... 12
Disassembly and Assembly .................................... 13
COMPONENT ..................................................... 13
DISASSEMBLY ................................................... 13
INSPECTION AFTER DISASSEMBLY ................ 14
ASSEMBLY ......................................................... 15
SERVICE DATA AND SPECIFICATIONS (SDS) ...... 17
Wheel Bearing ........................................................ 17
Drive Shaft .............................................................. 17
Page 3361 of 5621
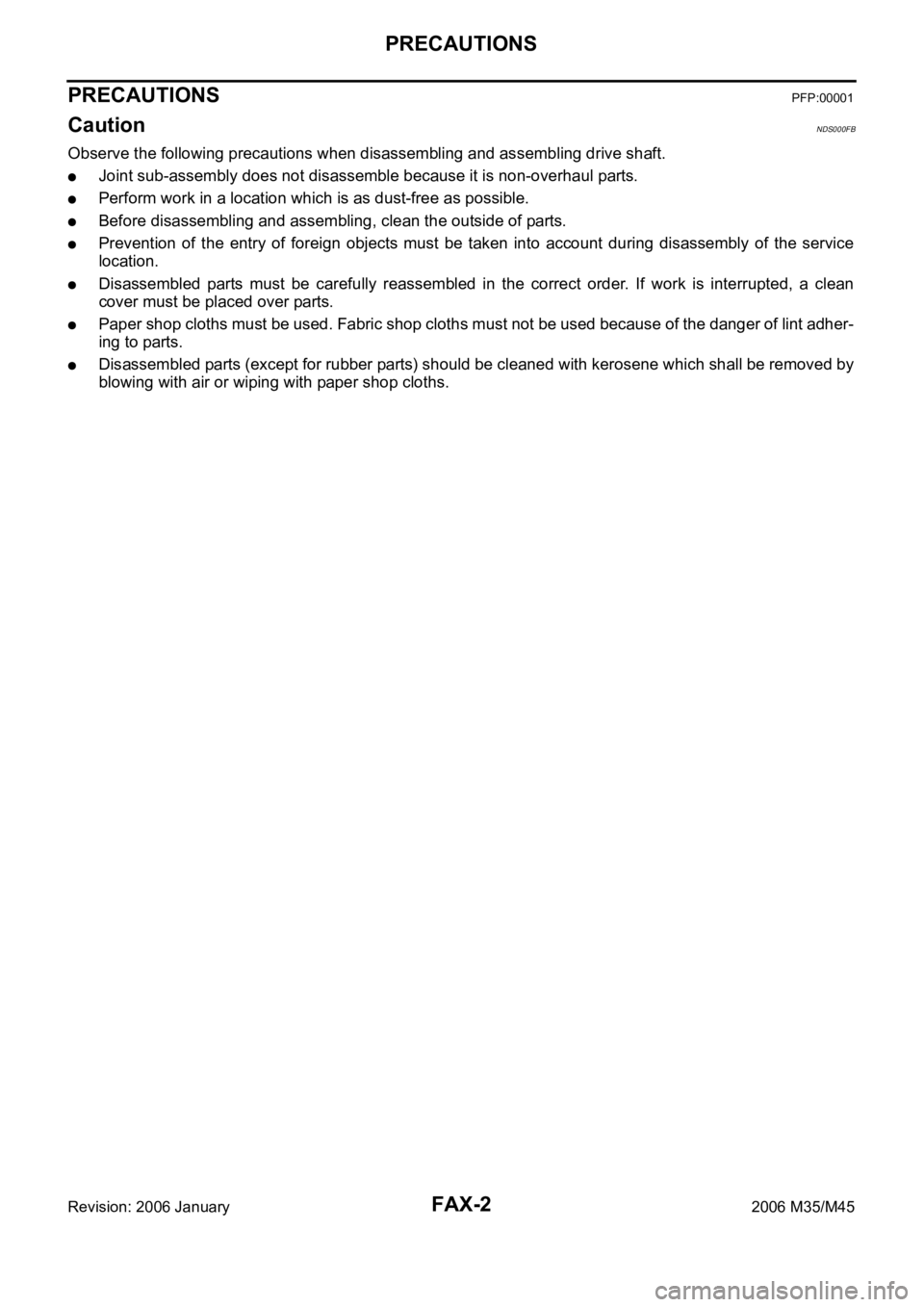
FAX-2
PRECAUTIONS
Revision: 2006 January2006 M35/M45
PRECAUTIONSPFP:00001
CautionNDS000FB
Observe the following precautions when disassembling and assembling drive shaft.
Joint sub-assembly does not disassemble because it is non-overhaul parts.
Perform work in a location which is as dust-free as possible.
Before disassembling and assembling, clean the outside of parts.
Prevention of the entry of foreign objects must be taken into account during disassembly of the service
location.
Disassembled parts must be carefully reassembled in the correct order. If work is interrupted, a clean
cover must be placed over parts.
Paper shop cloths must be used. Fabric shop cloths must not be used because of the danger of lint adher-
ing to parts.
Disassembled parts (except for rubber parts) should be cleaned with kerosene which shall be removed by
blowing with air or wiping with paper shop cloths.
Page 3362 of 5621
![INFINITI M35 2006 Factory Service Manual PREPARATION
FAX-3
C
E
F
G
H
I
J
K
L
MA
B
FA X
Revision: 2006 January2006 M35/M45
PREPARATIONPFP:00002
Special Service Tools [SST]NDS000FC
The actual shapes of Kent-Moore tools may differ from those of INFINITI M35 2006 Factory Service Manual PREPARATION
FAX-3
C
E
F
G
H
I
J
K
L
MA
B
FA X
Revision: 2006 January2006 M35/M45
PREPARATIONPFP:00002
Special Service Tools [SST]NDS000FC
The actual shapes of Kent-Moore tools may differ from those of](/img/42/57023/w960_57023-3361.png)
PREPARATION
FAX-3
C
E
F
G
H
I
J
K
L
MA
B
FA X
Revision: 2006 January2006 M35/M45
PREPARATIONPFP:00002
Special Service Tools [SST]NDS000FC
The actual shapes of Kent-Moore tools may differ from those of special service tools illustrated here.
Commercial Service ToolsNDS000FD
Tool number
(Kent-Moore No.)
Tool nameDescription
KV40107300
(–)
Boot band crimping toolInstalling boot band
KV40107500
(–)
Drive shaft attachmentRemoving drive shaft
KV38107900
(–)
Protector
a: 32 mm (1.26 in) dia.Installing drive shaft
KV38100500
(–)
Drift
a: 80 mm (3.15 in) dia.
b: 60 mm (2.36 in) dia.Installing drive shaft plug
KV38102200
(–)
Drift
a: 90 mm (3.54 in) dia.
b: 31 mm (1.22 in) dia.Installing drive shaft plug
ZZA1229D
ZZA1230D
ZZA0835D
ZZA0701D
ZZA0920D
Tool name Description
Power tool
Removing wheel nuts
Removing torque member fixing bolts
Removing hub lock nut
PBIC0190E
Page 3364 of 5621

FRONT WHEEL HUB AND KNUCKLE
FAX-5
C
E
F
G
H
I
J
K
L
MA
B
FA X
Revision: 2006 January2006 M35/M45
FRONT WHEEL HUB AND KNUCKLEPFP:40202
On-Vehicle Inspection and ServiceNDS000FF
Make sure that the mounting conditions (looseness, backlash) of each component and component conditions
(wear, damage) are normal.
WHEEL BEARING INSPECTION
Move wheel hub and bearing assembly in the axial direction by hand. Make sure there is no looseness of
wheel bearing.
Rotate wheel hub and make sure that is no unusual noise or other irregular conditions. If there is any of
irregular conditions, replace wheel hub and bearing assembly
Removal and InstallationNDS000FG
COMPONENT
Refer to GI section for symbol marks in the figure. Refer to GI-9, "HOW TO USE THIS MANUAL" .
REMOVAL
Wheel Hub and Bearing Assembly
1. Remove tires from vehicle with a power tool.
2. Remove wheel sensor from steering knuckle. Refer to BRC-57, "
WHEEL SENSOR" .
CAUTION:
Do not pull on wheel sensor harness.
3. Remove brake hose bracket. Refer to BR-12, "
BRAKE TUBE AND HOSE" .
4. Remove torque member fixing bolts with a power tool. Hang torque member in a place where it will not
interfere with work. Refer to BR-23, "
FRONT DISC BRAKE" .
CAUTION:
Do not depress brake pedal while brake caliper is removed.Axial end play : 0.05 mm (0.002 in) or less
1. Steering knuckle 2. Cotter pin 3. Splash guard
4. Wheel hub and bearing assembly 5. Washer A. AWD models
SDIA3256E