change time INFINITI M35 2006 Factory Service Manual
[x] Cancel search | Manufacturer: INFINITI, Model Year: 2006, Model line: M35, Model: INFINITI M35 2006Pages: 5621, PDF Size: 65.56 MB
Page 26 of 5621
![INFINITI M35 2006 Factory Service Manual LASER BEAM AIMING ADJUSTMENT
ACS-17
[ICC]
C
D
E
F
G
H
I
J
L
MA
B
ACS
Revision: 2006 January2006 M35/M45
6. Touch “LASER BEAM ADJUST”.
7. Touch “START”.
CAUTION:
If the adjustment screen does n INFINITI M35 2006 Factory Service Manual LASER BEAM AIMING ADJUSTMENT
ACS-17
[ICC]
C
D
E
F
G
H
I
J
L
MA
B
ACS
Revision: 2006 January2006 M35/M45
6. Touch “LASER BEAM ADJUST”.
7. Touch “START”.
CAUTION:
If the adjustment screen does n](/img/42/57023/w960_57023-25.png)
LASER BEAM AIMING ADJUSTMENT
ACS-17
[ICC]
C
D
E
F
G
H
I
J
L
MA
B
ACS
Revision: 2006 January2006 M35/M45
6. Touch “LASER BEAM ADJUST”.
7. Touch “START”.
CAUTION:
If the adjustment screen does not appear on the CONSULT-
II screen in 10 seconds. After touching “LASER BEAM
ADJUST” screen, the following causes may be considered:
Target is not set accurately.
There is not enough space beside the target.
The range of laser beam aiming exceeds for improper
installation position.
–Deformation of vehicle body.
–Deformation of unit.
–Deformation of bracket.
The area is not suitable for the adjustment work.
ICC sensor integrated unit is not clean.
8. After the CONSULT-II displays “ADJUST THE VERTICAL OF
LASER BEAM AIMING” turn the up-down direction adjusting
screw until “U/D CORRECT” value is set in the range of
4.
CAUTION:
Turn the screw slowly. The value change on display is
slower than actual movement of the ICC sensor integrated
unit. Wait for 2 seconds every time the screw is turned half
a rotation.
NOTE:
Turning the screw clockwise to laser beam is downward and
counterclockwise to laser beam is upward.
9. When “U/D CORRECT” value indicates
4, confirm that the margin of value remains within 4 at least for
2 seconds with no equipment or hand touching the ICC sensor integrated unit.
SKIA6191E
PKIB8359E
PKIB8360E
PKIB8361E
Page 114 of 5621
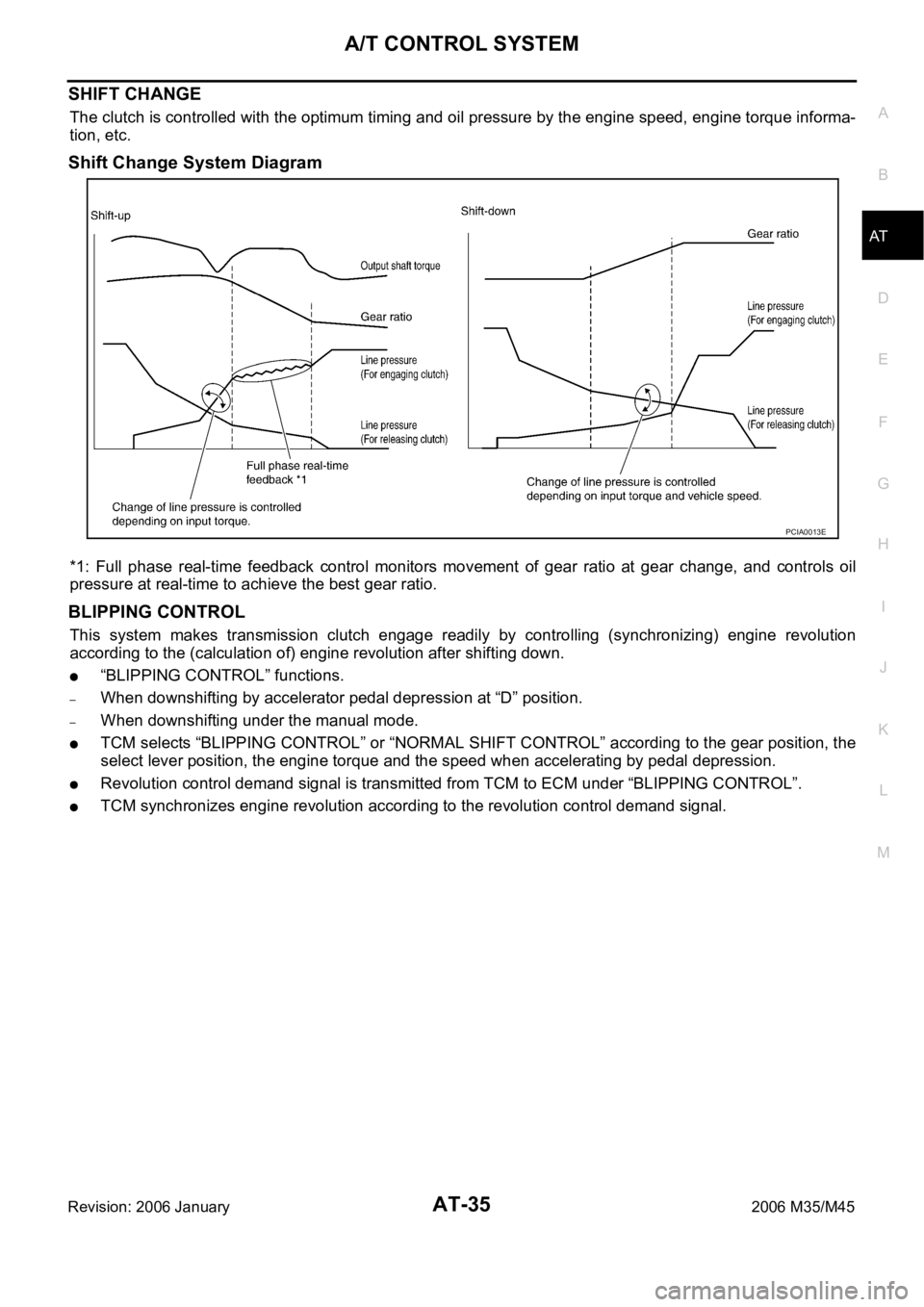
A/T CONTROL SYSTEM
AT-35
D
E
F
G
H
I
J
K
L
MA
B
AT
Revision: 2006 January2006 M35/M45
SHIFT CHANGE
The clutch is controlled with the optimum timing and oil pressure by the engine speed, engine torque informa-
tion, etc.
Shift Change System Diagram
*1: Full phase real-time feedback control monitors movement of gear ratio at gear change, and controls oil
pressure at real-time to achieve the best gear ratio.
BLIPPING CONTROL
This system makes transmission clutch engage readily by controlling (synchronizing) engine revolution
according to the (calculation of) engine revolution after shifting down.
“BLIPPING CONTROL” functions.
–When downshifting by accelerator pedal depression at “D” position.
–When downshifting under the manual mode.
TCM selects “BLIPPING CONTROL” or “NORMAL SHIFT CONTROL” according to the gear position, the
select lever position, the engine torque and the speed when accelerating by pedal depression.
Revolution control demand signal is transmitted from TCM to ECM under “BLIPPING CONTROL”.
TCM synchronizes engine revolution according to the revolution control demand signal.
PCIA0013E
Page 169 of 5621
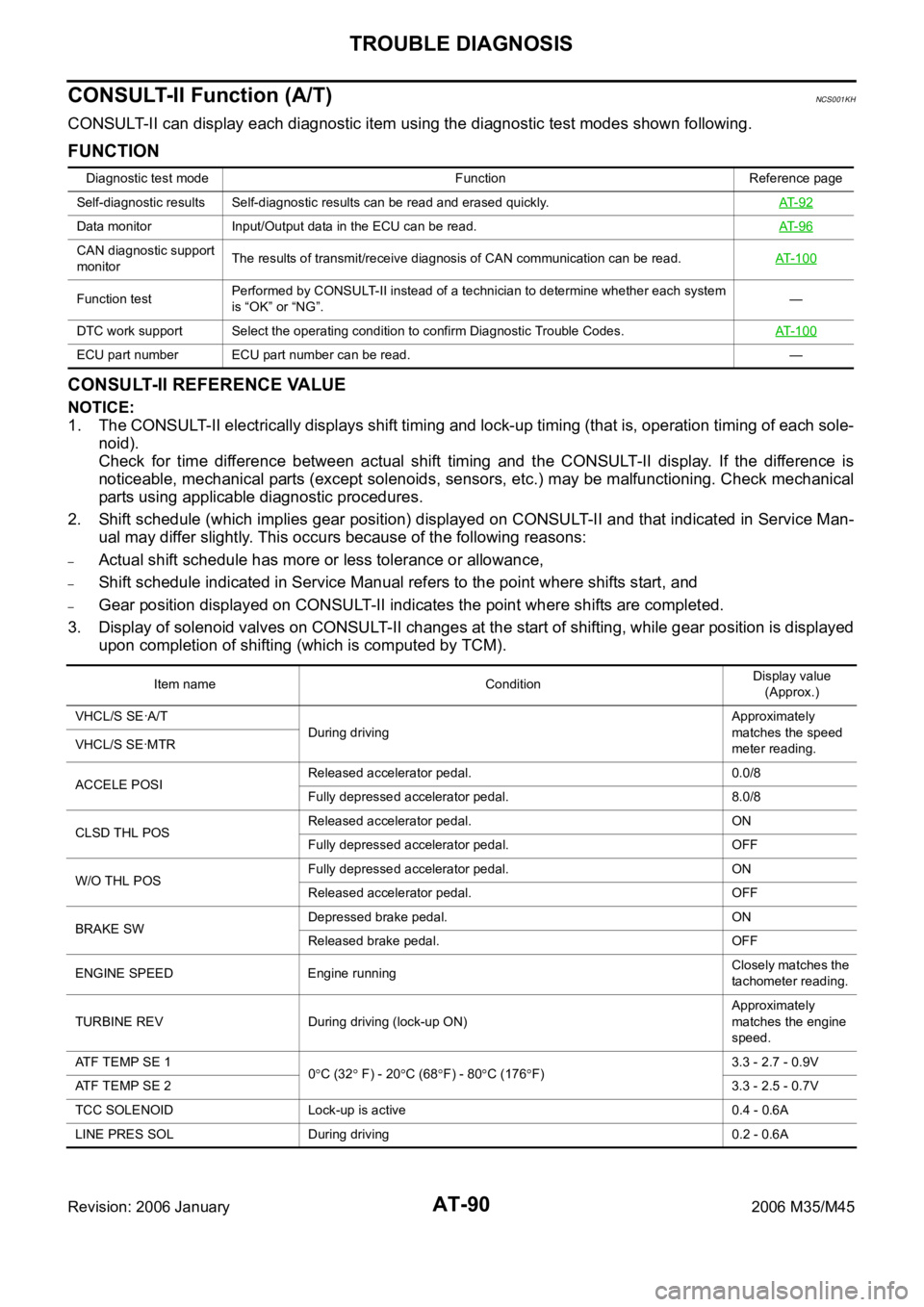
AT-90
TROUBLE DIAGNOSIS
Revision: 2006 January2006 M35/M45
CONSULT-II Function (A/T)NCS001KH
CONSULT-II can display each diagnostic item using the diagnostic test modes shown following.
FUNCTION
CONSULT-II REFERENCE VALUE
NOTICE:
1. The CONSULT-II electrically displays shift timing and lock-up timing (that is, operation timing of each sole-
noid).
Check for time difference between actual shift timing and the CONSULT-II display. If the difference is
noticeable, mechanical parts (except solenoids, sensors, etc.) may be malfunctioning. Check mechanical
parts using applicable diagnostic procedures.
2. Shift schedule (which implies gear position) displayed on CONSULT-II and that indicated in Service Man-
ual may differ slightly. This occurs because of the following reasons:
–Actual shift schedule has more or less tolerance or allowance,
–Shift schedule indicated in Service Manual refers to the point where shifts start, and
–Gear position displayed on CONSULT-II indicates the point where shifts are completed.
3. Display of solenoid valves on CONSULT-II changes at the start of shifting, while gear position is displayed
upon completion of shifting (which is computed by TCM).
Diagnostic test mode Function Reference page
Self-diagnostic results Self-diagnostic results can be read and erased quickly.AT- 9 2
Data monitor Input/Output data in the ECU can be read.AT- 9 6
CAN diagnostic support
monitorThe results of transmit/receive diagnosis of CAN communication can be read.AT- 1 0 0
Function testPerformed by CONSULT-II instead of a technician to determine whether each system
is “OK” or “NG”.—
DTC work support Select the operating condition to confirm Diagnostic Trouble Codes.AT- 1 0 0
ECU part number ECU part number can be read. —
Item name Condition Display value
(Approx.)
VHCL/S SEꞏA/T
During drivingApproximately
matches the speed
meter reading. VHCL/S SEꞏMTR
ACCELE POSIReleased accelerator pedal. 0.0/8
Fully depressed accelerator pedal. 8.0/8
CLSD THL POSReleased accelerator pedal. ON
Fully depressed accelerator pedal. OFF
W/O THL POSFully depressed accelerator pedal. ON
Released accelerator pedal. OFF
BRAKE SWDepressed brake pedal. ON
Released brake pedal. OFF
ENGINE SPEED Engine runningClosely matches the
tachometer reading.
TURBINE REV During driving (lock-up ON)Approximately
matches the engine
speed.
ATF TEMP SE 1
0
C (32 F) - 20C (68F) - 80C (176F)3.3 - 2.7 - 0.9V
ATF TEMP SE 23.3 - 2.5 - 0.7V
TCC SOLENOID Lock-up is active 0.4 - 0.6A
LINE PRES SOL During driving 0.2 - 0.6A
Page 470 of 5621
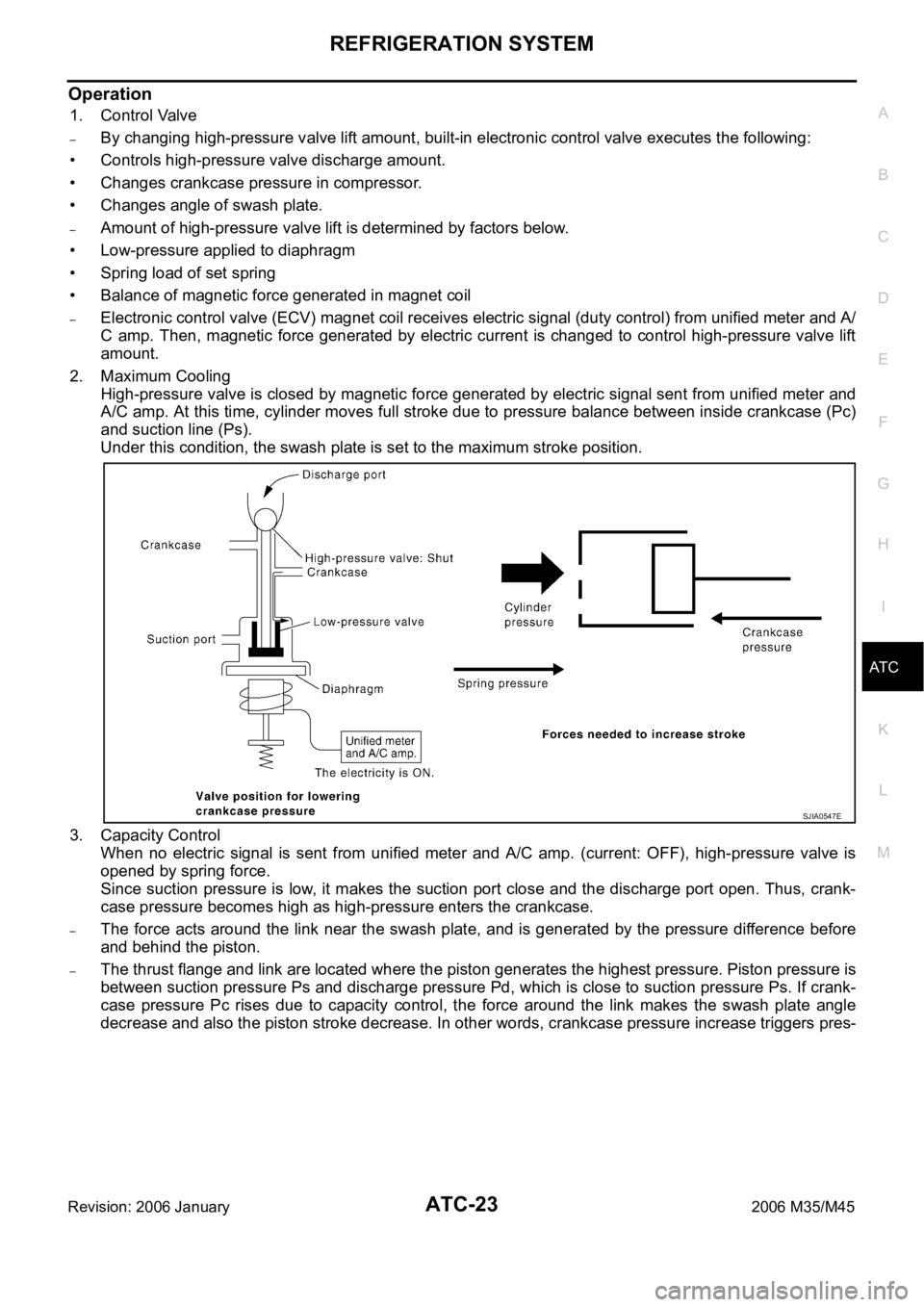
REFRIGERATION SYSTEM
ATC-23
C
D
E
F
G
H
I
K
L
MA
B
AT C
Revision: 2006 January2006 M35/M45
Operation
1. Control Valve
–By changing high-pressure valve lift amount, built-in electronic control valve executes the following:
• Controls high-pressure valve discharge amount.
• Changes crankcase pressure in compressor.
• Changes angle of swash plate.
–Amount of high-pressure valve lift is determined by factors below.
• Low-pressure applied to diaphragm
• Spring load of set spring
• Balance of magnetic force generated in magnet coil
–Electronic control valve (ECV) magnet coil receives electric signal (duty control) from unified meter and A/
C amp. Then, magnetic force generated by electric current is changed to control high-pressure valve lift
amount.
2. Maximum Cooling
High-pressure valve is closed by magnetic force generated by electric signal sent from unified meter and
A/C amp. At this time, cylinder moves full stroke due to pressure balance between inside crankcase (Pc)
and suction line (Ps).
Under this condition, the swash plate is set to the maximum stroke position.
3. Capacity Control
When no electric signal is sent from unified meter and A/C amp. (current: OFF), high-pressure valve is
opened by spring force.
Since suction pressure is low, it makes the suction port close and the discharge port open. Thus, crank-
case pressure becomes high as high-pressure enters the crankcase.
–The force acts around the link near the swash plate, and is generated by the pressure difference before
and behind the piston.
–The thrust flange and link are located where the piston generates the highest pressure. Piston pressure is
between suction pressure Ps and discharge pressure Pd, which is close to suction pressure Ps. If crank-
case pressure Pc rises due to capacity control, the force around the link makes the swash plate angle
decrease and also the piston stroke decrease. In other words, crankcase pressure increase triggers pres-
SJIA0547E
Page 505 of 5621
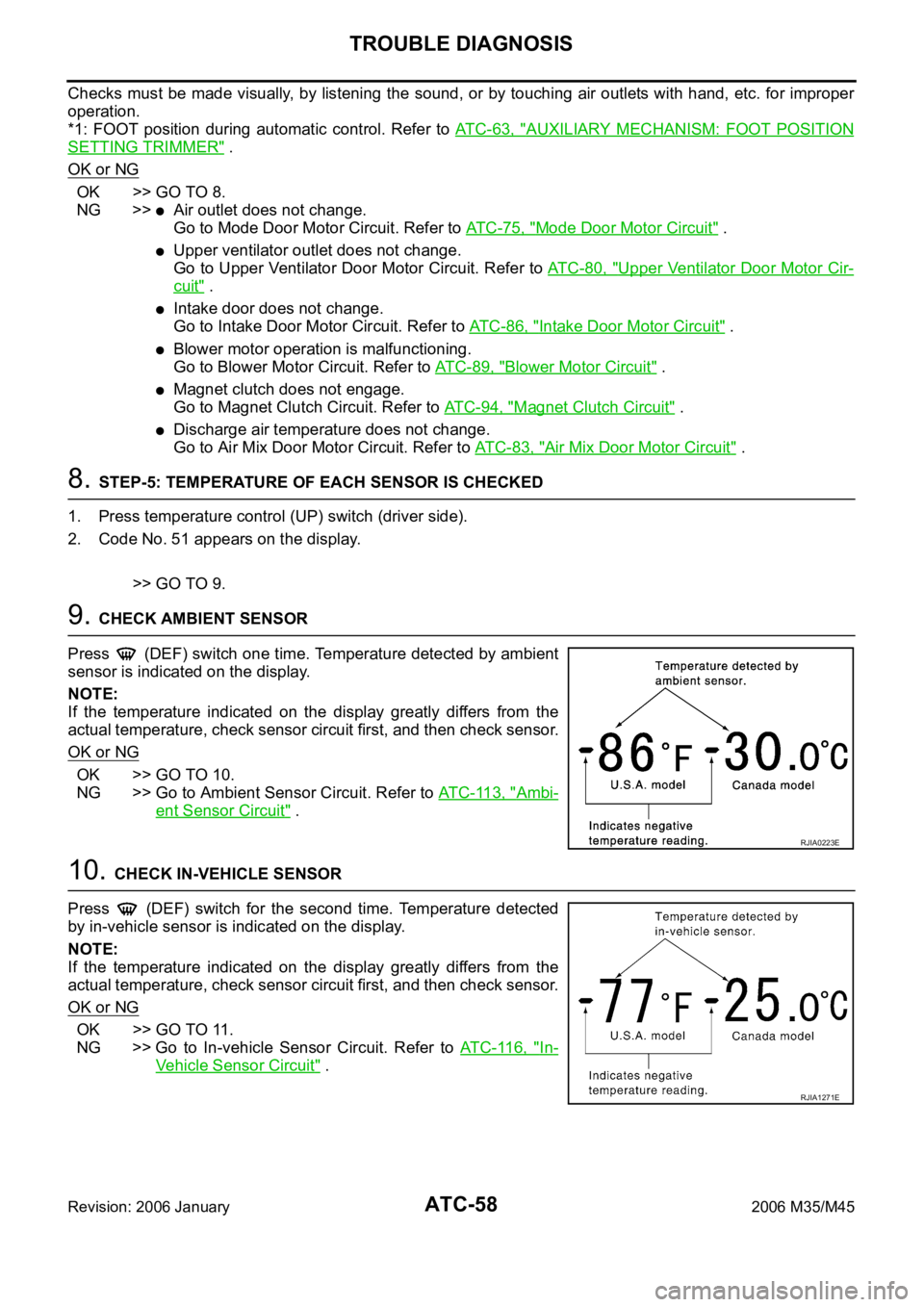
ATC-58
TROUBLE DIAGNOSIS
Revision: 2006 January2006 M35/M45
Checks must be made visually, by listening the sound, or by touching air outlets with hand, etc. for improper
operation.
*1: FOOT position during automatic control. Refer to AT C - 6 3 , "
AUXILIARY MECHANISM: FOOT POSITION
SETTING TRIMMER" .
OK or NG
OK >> GO TO 8.
NG >>
Air outlet does not change.
Go to Mode Door Motor Circuit. Refer to AT C - 7 5 , "
Mode Door Motor Circuit" .
Upper ventilator outlet does not change.
Go to Upper Ventilator Door Motor Circuit. Refer to AT C - 8 0 , "
Upper Ventilator Door Motor Cir-
cuit" .
Intake door does not change.
Go to Intake Door Motor Circuit. Refer to AT C - 8 6 , "
Intake Door Motor Circuit" .
Blower motor operation is malfunctioning.
Go to Blower Motor Circuit. Refer to AT C - 8 9 , "
Blower Motor Circuit" .
Magnet clutch does not engage.
Go to Magnet Clutch Circuit. Refer to ATC-94, "
Magnet Clutch Circuit" .
Discharge air temperature does not change.
Go to Air Mix Door Motor Circuit. Refer to AT C - 8 3 , "
Air Mix Door Motor Circuit" .
8. STEP-5: TEMPERATURE OF EACH SENSOR IS CHECKED
1. Press temperature control (UP) switch (driver side).
2. Code No. 51 appears on the display.
>> GO TO 9.
9. CHECK AMBIENT SENSOR
Press (DEF) switch one time. Temperature detected by ambient
sensor is indicated on the display.
NOTE:
If the temperature indicated on the display greatly differs from the
actual temperature, check sensor circuit first, and then check sensor.
OK or NG
OK >> GO TO 10.
NG >> Go to Ambient Sensor Circuit. Refer to AT C - 11 3 , "
Ambi-
ent Sensor Circuit" .
10. CHECK IN-VEHICLE SENSOR
Press (DEF) switch for the second time. Temperature detected
by in-vehicle sensor is indicated on the display.
NOTE:
If the temperature indicated on the display greatly differs from the
actual temperature, check sensor circuit first, and then check sensor.
OK or NG
OK >> GO TO 11.
NG >> Go to In-vehicle Sensor Circuit. Refer to AT C - 11 6 , "
In-
Vehicle Sensor Circuit" .
RJIA0223E
RJIA1271E
Page 509 of 5621
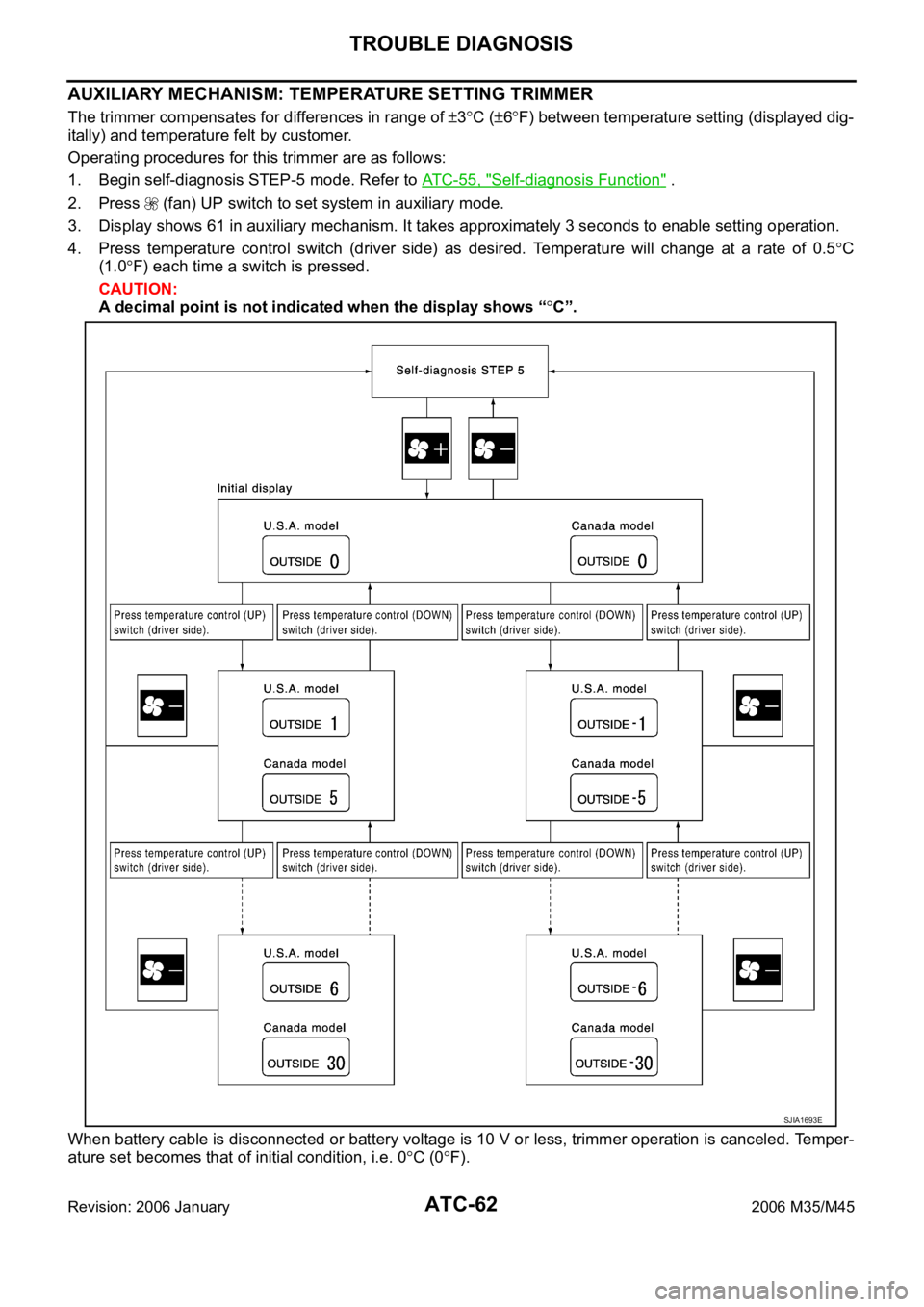
ATC-62
TROUBLE DIAGNOSIS
Revision: 2006 January2006 M35/M45
AUXILIARY MECHANISM: TEMPERATURE SETTING TRIMMER
The trimmer compensates for differences in range of 3C (6F) between temperature setting (displayed dig-
itally) and temperature felt by customer.
Operating procedures for this trimmer are as follows:
1. Begin self-diagnosis STEP-5 mode. Refer to ATC-55, "
Self-diagnosis Function" .
2. Press (fan) UP switch to set system in auxiliary mode.
3. Display shows 61 in auxiliary mechanism. It takes approximately 3 seconds to enable setting operation.
4. Press temperature control switch (driver side) as desired. Temperature will change at a rate of 0.5
C
(1.0
F) each time a switch is pressed.
CAUTION:
A decimal point is not indicated when the display shows “
C”.
When battery cable is disconnected or battery voltage is 10 V or less, trimmer operation is canceled. Temper-
ature set becomes that of initial condition, i.e. 0
C (0F).
SJIA1693E
Page 552 of 5621
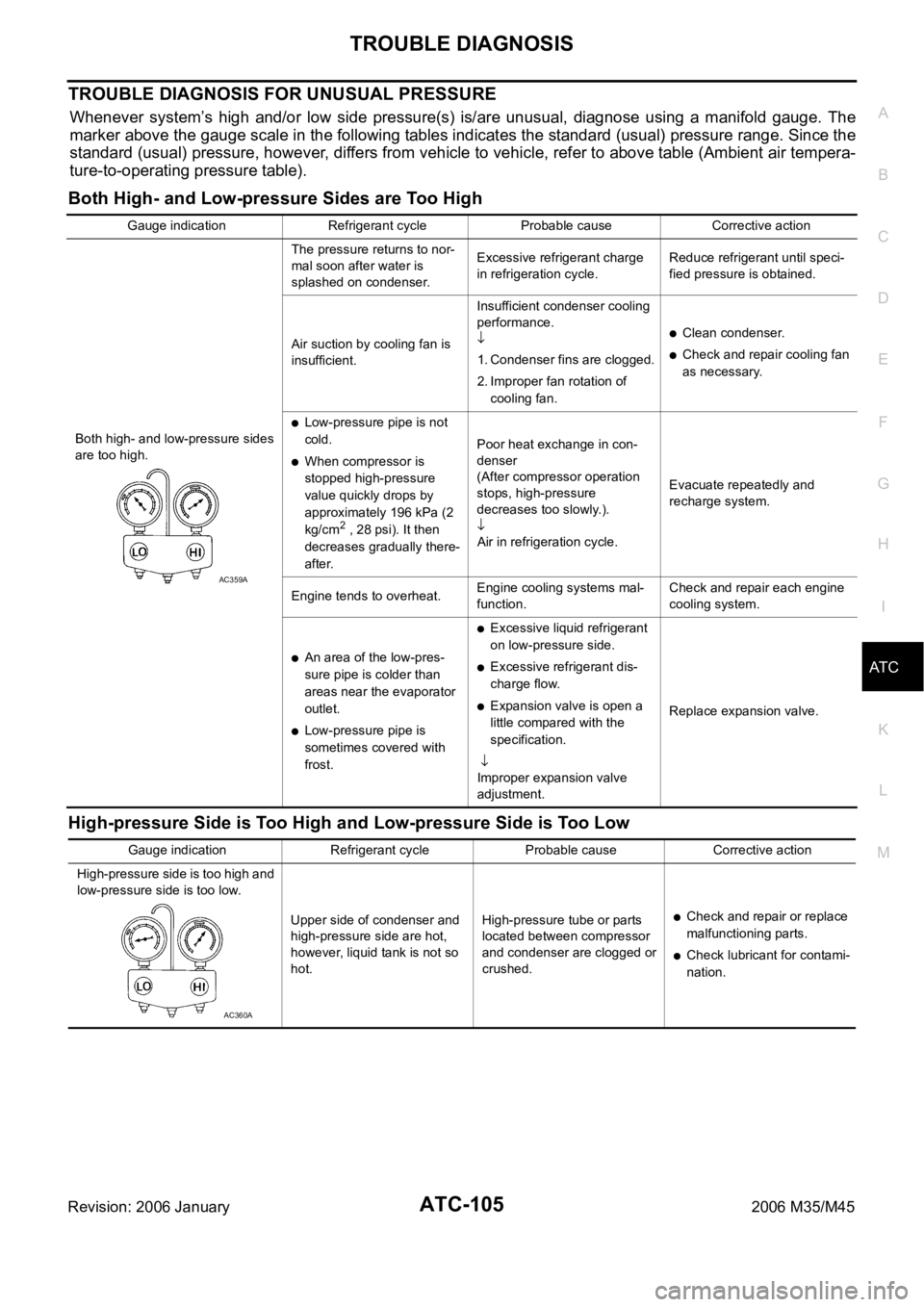
TROUBLE DIAGNOSIS
ATC-105
C
D
E
F
G
H
I
K
L
MA
B
AT C
Revision: 2006 January2006 M35/M45
TROUBLE DIAGNOSIS FOR UNUSUAL PRESSURE
Whenever system’s high and/or low side pressure(s) is/are unusual, diagnose using a manifold gauge. The
marker above the gauge scale in the following tables indicates the standard (usual) pressure range. Since the
standard (usual) pressure, however, differs from vehicle to vehicle, refer to above table (Ambient air tempera-
ture-to-operating pressure table).
Both High- and Low-pressure Sides are Too High
High-pressure Side is Too High and Low-pressure Side is Too Low
Gauge indication Refrigerant cycle Probable cause Corrective action
Both high- and low-pressure sides
are too high.The pressure returns to nor-
mal soon after water is
splashed on condenser.Excessive refrigerant charge
in refrigeration cycle.Reduce refrigerant until speci-
fied pressure is obtained.
Air suction by cooling fan is
insufficient.Insufficient condenser cooling
performance.
1. Condenser fins are clogged.
2. Improper fan rotation of
cooling fan.
Clean condenser.
Check and repair cooling fan
as necessary.
Low-pressure pipe is not
cold.
When compressor is
stopped high-pressure
value quickly drops by
approximately 196 kPa (2
kg/cm
2 , 28 psi). It then
decreases gradually there-
after.Poor heat exchange in con-
denser
(After compressor operation
stops, high-pressure
decreases too slowly.).Air in refrigeration cycle.Evacuate repeatedly and
recharge system.
Engine tends to overheat.Engine cooling systems mal-
function.Check and repair each engine
cooling system.
An area of the low-pres-
sure pipe is colder than
areas near the evaporator
outlet.
Low-pressure pipe is
sometimes covered with
frost.
Excessive liquid refrigerant
on low-pressure side.
Excessive refrigerant dis-
charge flow.
Expansion valve is open a
little compared with the
specification.
Improper expansion valve
adjustment.Replace expansion valve.
AC359A
Gauge indication Refrigerant cycle Probable cause Corrective action
High-pressure side is too high and
low-pressure side is too low.
Upper side of condenser and
high-pressure side are hot,
however, liquid tank is not so
hot.High-pressure tube or parts
located between compressor
and condenser are clogged or
crushed.
Check and repair or replace
malfunctioning parts.
Check lubricant for contami-
nation.
AC360A
Page 566 of 5621
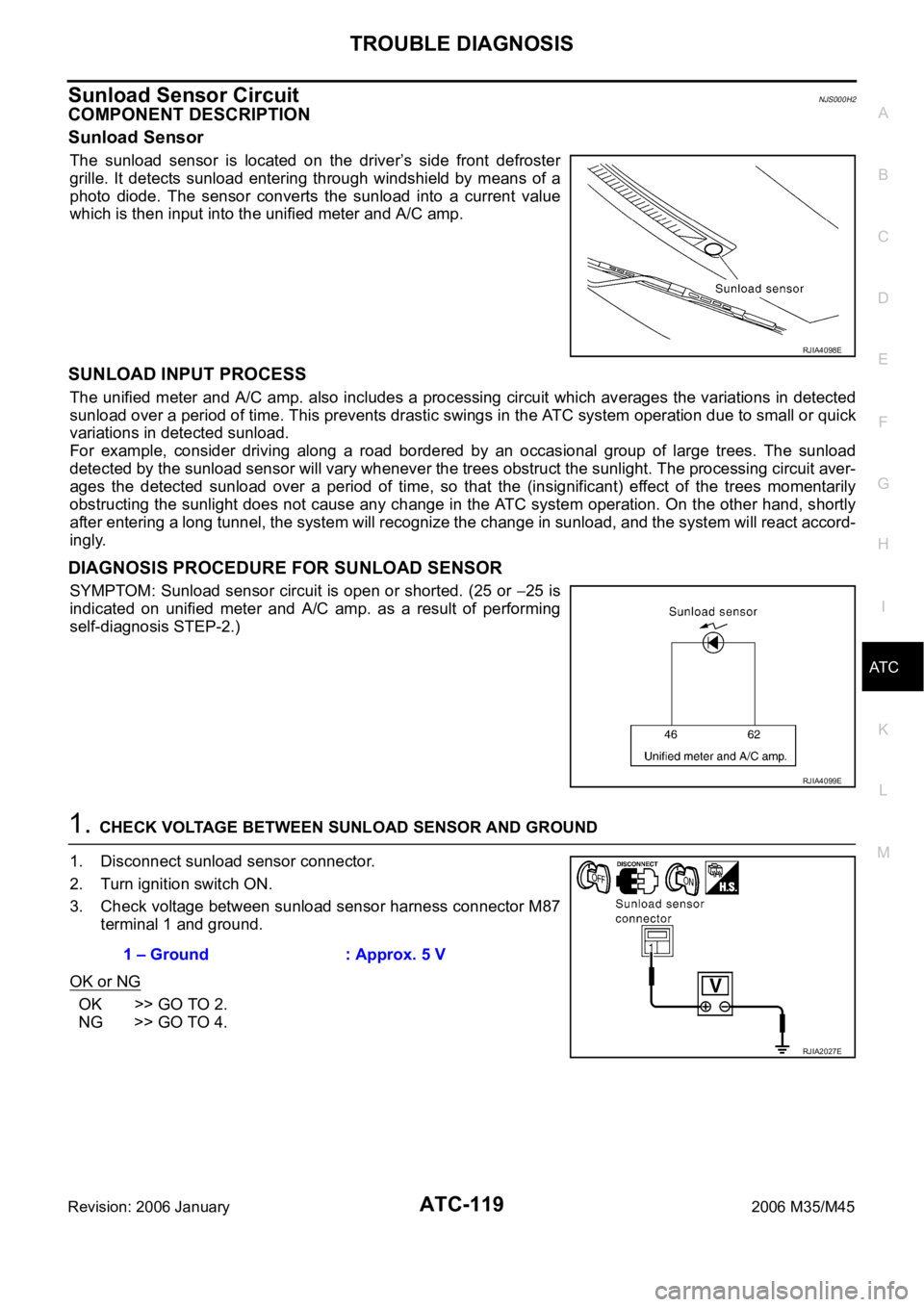
TROUBLE DIAGNOSIS
ATC-119
C
D
E
F
G
H
I
K
L
MA
B
AT C
Revision: 2006 January2006 M35/M45
Sunload Sensor CircuitNJS000H2
COMPONENT DESCRIPTION
Sunload Sensor
The sunload sensor is located on the driver’s side front defroster
grille. It detects sunload entering through windshield by means of a
photo diode. The sensor converts the sunload into a current value
which is then input into the unified meter and A/C amp.
SUNLOAD INPUT PROCESS
The unified meter and A/C amp. also includes a processing circuit which averages the variations in detected
sunload over a period of time. This prevents drastic swings in the ATC system operation due to small or quick
variations in detected sunload.
For example, consider driving along a road bordered by an occasional group of large trees. The sunload
detected by the sunload sensor will vary whenever the trees obstruct the sunlight. The processing circuit aver-
ages the detected sunload over a period of time, so that the (insignificant) effect of the trees momentarily
obstructing the sunlight does not cause any change in the ATC system operation. On the other hand, shortly
after entering a long tunnel, the system will recognize the change in sunload, and the system will react accord-
ingly.
DIAGNOSIS PROCEDURE FOR SUNLOAD SENSOR
SYMPTOM: Sunload sensor circuit is open or shorted. (25 or 25 is
indicated on unified meter and A/C amp. as a result of performing
self-diagnosis STEP-2.)
1. CHECK VOLTAGE BETWEEN SUNLOAD SENSOR AND GROUND
1. Disconnect sunload sensor connector.
2. Turn ignition switch ON.
3. Check voltage between sunload sensor harness connector M87
terminal 1 and ground.
OK or NG
OK >> GO TO 2.
NG >> GO TO 4.
RJIA4098E
RJIA4099E
1 – Ground : Approx. 5 V
RJIA2027E
Page 630 of 5621
![INFINITI M35 2006 Factory Service Manual SYSTEM DESCRIPTION
AV-9
[WITHOUT MOBILE ENTERTAINMENT SYSTEM]
C
D
E
F
G
H
I
J
L
MA
B
AV
Revision: 2006 January2006 M35/M45
indicated on the screen as a vehicle mark. More accurate data is judged and u INFINITI M35 2006 Factory Service Manual SYSTEM DESCRIPTION
AV-9
[WITHOUT MOBILE ENTERTAINMENT SYSTEM]
C
D
E
F
G
H
I
J
L
MA
B
AV
Revision: 2006 January2006 M35/M45
indicated on the screen as a vehicle mark. More accurate data is judged and u](/img/42/57023/w960_57023-629.png)
SYSTEM DESCRIPTION
AV-9
[WITHOUT MOBILE ENTERTAINMENT SYSTEM]
C
D
E
F
G
H
I
J
L
MA
B
AV
Revision: 2006 January2006 M35/M45
indicated on the screen as a vehicle mark. More accurate data is judged and used by comparing vehicle posi-
tion detection results found by the GPS with the result by map-matching.
The current vehicle position will be calculated by detecting the dis-
tance the vehicle moved from the previous calculation point and its
direction.
Travel distance
Travel distance calculations are based on the vehicle speed
sensor input signal. Therefore, the calculation may become
incorrect as the tires wear down. To prevent this, an automatic
distance correction function has been adopted.
Travel direction
Change in the travel direction of the vehicle is calculated by a
gyroscope (angular velocity sensor) and a GPS antenna (GPS
information). They have both advantages and disadvantages.
More accurate traveling direction is detected because priorities are set for the signals from these two
devices according to the situation.
Map-Matching
Map-matching compares a current location detected by the method
in the “Location Detection Principle” with a road map data from Map
DVD-ROM stored in DVD-ROM drive.
NOTE:
The road map data is based on data stored in the map DVD-ROM.
The vehicle position may not be corrected under the following circumstances and after driving for a certain
time when GPS information is difficult to receive. In this case, the vehicle mark on the display must be cor-
rected manually.
In map-matching, alternative routes to reach the destination will
be shown and prioritized, after the road on which the vehicle is
currently driven has been judged and the vehicle mark has been
repositioned.
If there is an error in distance and/or direction, alternative routes
will be shown in different order of priority, and the incorrect road
can be avoided.
If two roads are running in parallel, they are of the same priority.
Therefore, the vehicle mark may appear on either of them alter-
nately, depending on maneuvering of the steering wheel and
configuration of the road.
SEL684V
Type Advantage Disadvantage
Gyroscope
(angular velocity sensor)Can detect the vehicle's turning angle quite
accurately.Direction errors may accumulate when vehicle is
driven for long distances without stopping.
GPS antenna
(GPS information)Can detect the vehicle's travel direction
(North/South/East/West).Correct direction cannot be detected when vehi-
cle speed is low.
SEL685V
SEL686V
Page 631 of 5621
![INFINITI M35 2006 Factory Service Manual AV-10
[WITHOUT MOBILE ENTERTAINMENT SYSTEM]
SYSTEM DESCRIPTION
Revision: 2006 January2006 M35/M45
Map-matching does not function correctly when a road on which
the vehicle is driving is new and not INFINITI M35 2006 Factory Service Manual AV-10
[WITHOUT MOBILE ENTERTAINMENT SYSTEM]
SYSTEM DESCRIPTION
Revision: 2006 January2006 M35/M45
Map-matching does not function correctly when a road on which
the vehicle is driving is new and not](/img/42/57023/w960_57023-630.png)
AV-10
[WITHOUT MOBILE ENTERTAINMENT SYSTEM]
SYSTEM DESCRIPTION
Revision: 2006 January2006 M35/M45
Map-matching does not function correctly when a road on which
the vehicle is driving is new and not recorded in the map DVD-
ROM, or when road pattern stored in the map data and the
actual road pattern are different due to repair.
When driving on a road not present in the map, the map-match-
ing function may find another road and position the vehicle mark
on it. Then, when the correct road is detected, the vehicle mark
may change to it.
Effective range for comparing the vehicle position and travel
direction calculated by the distance and direction with the road
data read from the map DVD-ROM is limited. Therefore, when
there is an excessive gap between current vehicle position and
the position on the map, correction by map-matching is not possible.
GPS (Global Positioning System)
GPS (Global Positioning System) was developed for and is con-
trolled by the US Department of Defense. The system utilizes GPS
satellites (NAVSTAR), sending out radio waves while flying on an
orbit around the earth at an altitude of approximately 21,000 km
(13,100miles).
The GPS receiver calculates the vehicle's position in three dimen-
sions (latitude/longitude/altitude) according to the time lag of the
radio waves received from four or more GPS satellites (three-dimen-
sional positioning). If radio waves were received only from three
GPS satellites, the GPS receiver calculates the vehicle's position in
two dimensions (latitude/longitude), utilizing the altitude data calcu-
lated previously with radio waves from four or more GPS satellites
(two-dimensional positioning).
Position correction by GPS is not available while the vehicle is stopped.
Accuracy of GPS will deteriorate under the following conditions:
In two-dimensional positioning, GPS accuracy will deteriorate when altitude of the vehicle position
changes.
The accuracy can be even lower depending on the arrangement of the GPS satellites utilized for the posi-
tioning.
Position detection is not possible when vehicle is in an area where radio waves from the GPS satellite do
not reach, such as in a tunnel, parking lot in a building, and under an elevated highway. Radio waves from
the GPS satellites may not be received when some object is located over the GPS antenna.
NOTE:
Even a high-precision three dimensional positioning, the detection result has an error about 10 m (30 ft).
Because the signals of GPS satellite is controlled by the Tracking and Control Center in the United States,
the accuracy may be degraded lower intentionally or the radio waves may stop.
HANDS-FREE PHONE
AV (NAVI) control unit has Bluetooth module. It can perform wireless hands-free telephone calls using a
cellular phone in vehicle compartment.
5 or more portable phones can be registered into the AV (NAVI) control unit.
REAR VIEW MONITOR
The small CCD camera is equipped into the rear end of the vehicle. The rear view monitor that displays
the area behind the vehicle while backing up is equipped.
Guiding lines indicating side and rear clearances are provided in the rear view monitor image, which
allows the driver to more easily judge distances between the vehicle and objects in the display. The possi-
ble route lines that indicate the possible route according to the steering angle are provided to help backing
up when parking.
Image quality of the rear view image and of the navigation screen can be adjusted separately.
SKIA0613E
SEL526V