radiator INFINITI M35 2006 Factory Service Manual
[x] Cancel search | Manufacturer: INFINITI, Model Year: 2006, Model line: M35, Model: INFINITI M35 2006Pages: 5621, PDF Size: 65.56 MB
Page 2 of 5621
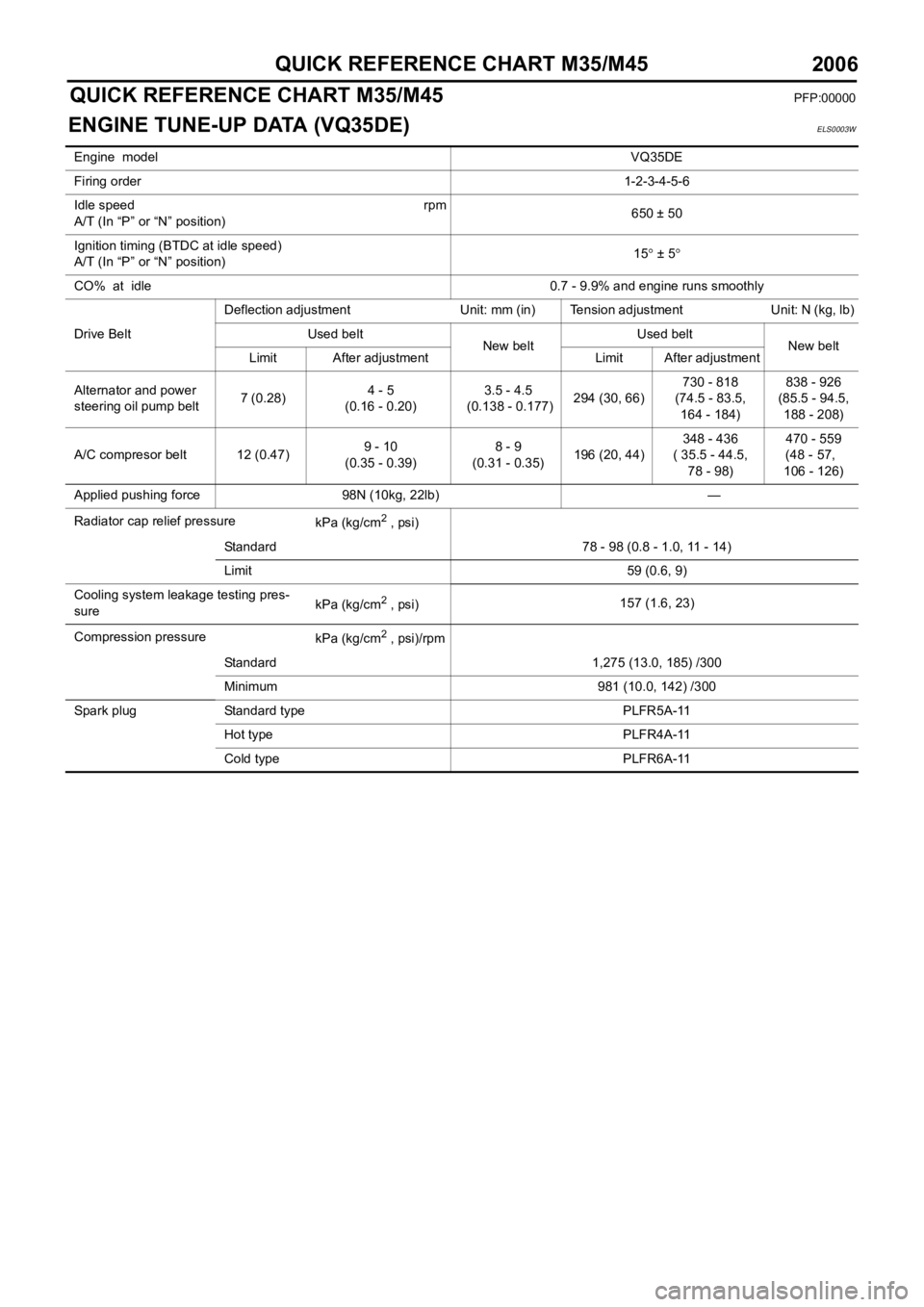
QUICK REFERENCE CHART M35/M45
QUICK REFERENCE CHART M35/M45PFP:00000
ENGINE TUNE-UP DATA (VQ35DE)ELS0003W
Engine modelVQ35DE
Firing order1-2-3-4-5-6
Idle speed
A/T (In “P” or “N” position)rpm
650 ± 50
Ignition timing (BTDC at idle speed)
A/T (In “P” or “N” position)15
± 5
CO% at idle 0.7 - 9.9% and engine runs smoothly
Drive BeltDeflection adjustment Unit: mm (in) Tension adjustment Unit: N (kg, lb)
Used belt
New beltUsed belt
New belt
Limit After adjustment Limit After adjustment
Alternator and power
steering oil pump belt7 (0.28)4 - 5
(0.16 - 0.20)3.5 - 4.5
(0.138 - 0.177)294 (30, 66)730 - 818
(74.5 - 83.5,
164 - 184)838 - 926
(85.5 - 94.5,
188 - 208)
A/C compresor belt 12 (0.47)9 - 10
(0.35 - 0.39)8 - 9
(0.31 - 0.35)196 (20, 44)348 - 436
( 35.5 - 44.5,
78 - 98)470 - 559
( 4 8 - 5 7 ,
106 - 126)
Applied pushing force 98N (10kg, 22lb) —
Radiator cap relief pressure
kPa (kg/cm
2 , psi)
Standard 78 - 98 (0.8 - 1.0, 11 - 14)
Limit 59 (0.6, 9)
Cooling system leakage testing pres-
surekPa (kg/cm
2 , psi)157 (1.6, 23)
Compression pressure
kPa (kg/cm
2 , psi)/rpm
Standard 1,275 (13.0, 185) /300
Minimum 981 (10.0, 142) /300
Spark plug Standard type PLFR5A-11
Hot type PLFR4A-11
Cold type PLFR6A-11
2006
Page 3 of 5621
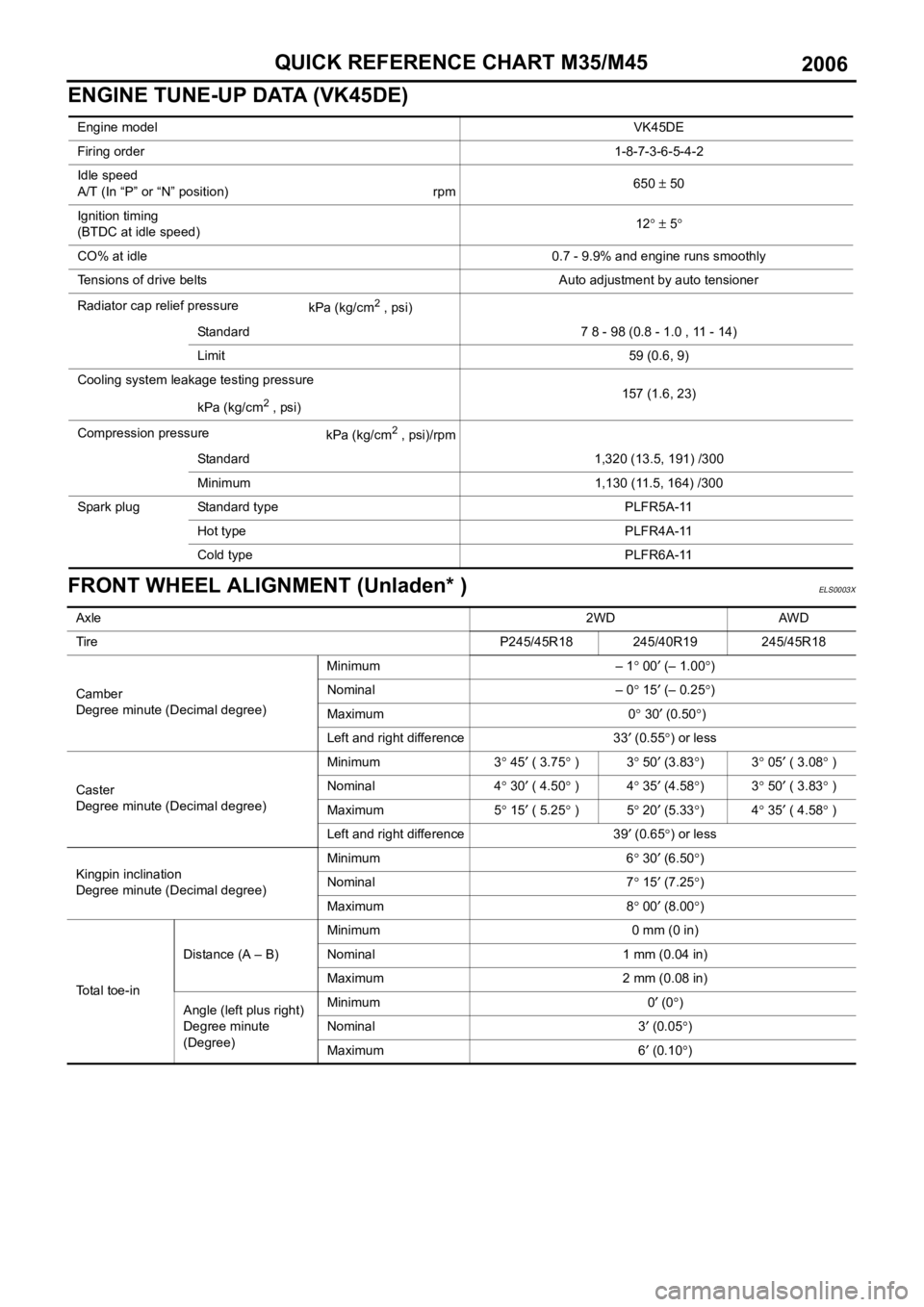
QUICK REFERENCE CHART M35/M45
ENGINE TUNE-UP DATA (VK45DE)
FRONT WHEEL ALIGNMENT (Unladen* )
ELS0003X
Engine modelVK45DE
Firing order1-8-7-3-6-5-4-2
Idle speed
A/T (In “P” or “N” position) rpm650
50
Ignition timing
(BTDC at idle speed)12
5
CO% at idle 0.7 - 9.9% and engine runs smoothly
Tensions of drive belts Auto adjustment by auto tensioner
Radiator cap relief pressure
kPa (kg/cm
2 , psi)
7 8 - 98 (0.8 - 1.0 , 11 - 14) Standard
Limit 59 (0.6, 9)
Cooling system leakage testing pressure
157 (1.6, 23)
kPa (kg/cm
2 , psi)
Compression pressure
kPa (kg/cm
2 , psi)/rpm
1,320 (13.5, 191) /300 Standard
Minimum 1,130 (11.5, 164) /300
Spark plug Standard type PLFR5A-11
Hot type PLFR4A-11
Cold type PLFR6A-11
Axle2WD AWD
Tire P245/45R18 245/40R19 245/45R18
Camber
Degree minute (Decimal degree)Minimum – 1
00 (– 1.00)
Nominal – 0
15 (– 0.25)
Maximum 0
30 (0.50)
Left and right difference 33
(0.55) or less
Caster
Degree minute (Decimal degree)Minimum 3
45 ( 3.75 ) 3 50 (3.83)3 05 ( 3.08 )
Nominal 4
30 ( 4.50 ) 4 35 (4.58)3 50 ( 3.83 )
Maximum 5
15 ( 5.25 ) 5 20 (5.33)4 35 ( 4.58 )
Left and right difference 39
(0.65) or less
Kingpin inclination
Degree minute (Decimal degree)Minimum 6
30 (6.50)
Nominal 7
15 (7.25)
Maximum 8
00 (8.00)
Total toe-inDistance (A – B)Minimum 0 mm (0 in)
Nominal 1 mm (0.04 in)
Maximum 2 mm (0.08 in)
Angle (left plus right)
Degree minute
(Degree)Minimum 0
(0)
Nominal 3
(0.05)
Maximum 6
(0.10)
2006
Page 88 of 5621
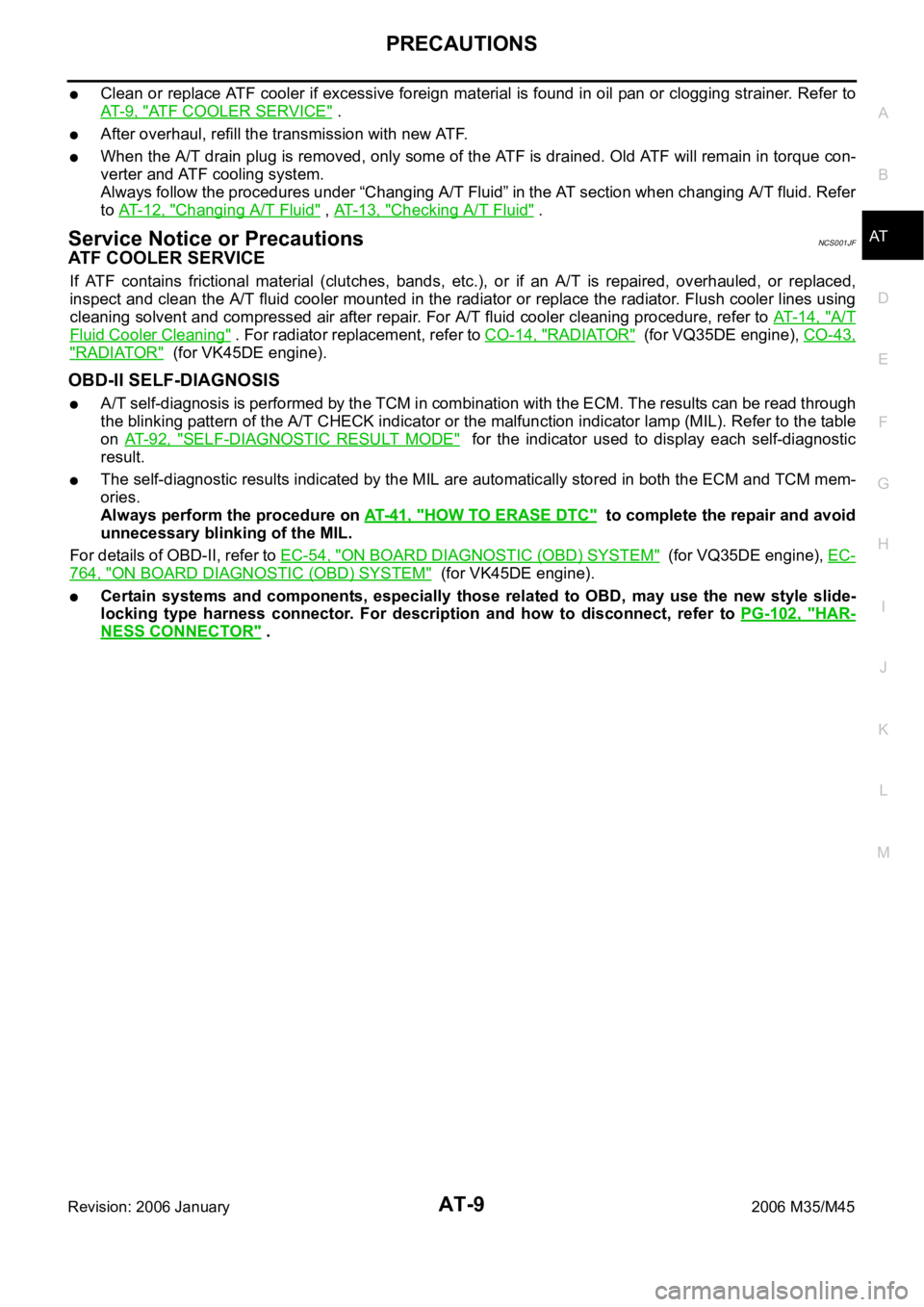
PRECAUTIONS
AT-9
D
E
F
G
H
I
J
K
L
MA
B
AT
Revision: 2006 January2006 M35/M45
Clean or replace ATF cooler if excessive foreign material is found in oil pan or clogging strainer. Refer to
AT- 9 , "
ATF COOLER SERVICE" .
After overhaul, refill the transmission with new ATF.
When the A/T drain plug is removed, only some of the ATF is drained. Old ATF will remain in torque con-
verter and ATF cooling system.
Always follow the procedures under “Changing A/T Fluid” in the AT section when changing A/T fluid. Refer
to AT- 1 2 , "
Changing A/T Fluid" , AT- 1 3 , "Checking A/T Fluid" .
Service Notice or PrecautionsNCS001JF
ATF COOLER SERVICE
If ATF contains frictional material (clutches, bands, etc.), or if an A/T is repaired, overhauled, or replaced,
inspect and clean the A/T fluid cooler mounted in the radiator or replace the radiator. Flush cooler lines using
cleaning solvent and compressed air after repair. For A/T fluid cooler cleaning procedure, refer to AT- 1 4 , "
A/T
Fluid Cooler Cleaning" . For radiator replacement, refer to CO-14, "RADIATOR" (for VQ35DE engine), CO-43,
"RADIATOR" (for VK45DE engine).
OBD-II SELF-DIAGNOSIS
A/T self-diagnosis is performed by the TCM in combination with the ECM. The results can be read through
the blinking pattern of the A/T CHECK indicator or the malfunction indicator lamp (MIL). Refer to the table
on AT- 9 2 , "
SELF-DIAGNOSTIC RESULT MODE" for the indicator used to display each self-diagnostic
result.
The self-diagnostic results indicated by the MIL are automatically stored in both the ECM and TCM mem-
ories.
Always perform the procedure on AT- 4 1 , "
HOW TO ERASE DTC" to complete the repair and avoid
unnecessary blinking of the MIL.
For details of OBD-II, refer to EC-54, "
ON BOARD DIAGNOSTIC (OBD) SYSTEM" (for VQ35DE engine), EC-
764, "ON BOARD DIAGNOSTIC (OBD) SYSTEM" (for VK45DE engine).
Certain systems and components, especially those related to OBD, may use the new style slide-
locking type harness connector. For description and how to disconnect, refer to PG-102, "
HAR-
NESS CONNECTOR" .
Page 91 of 5621
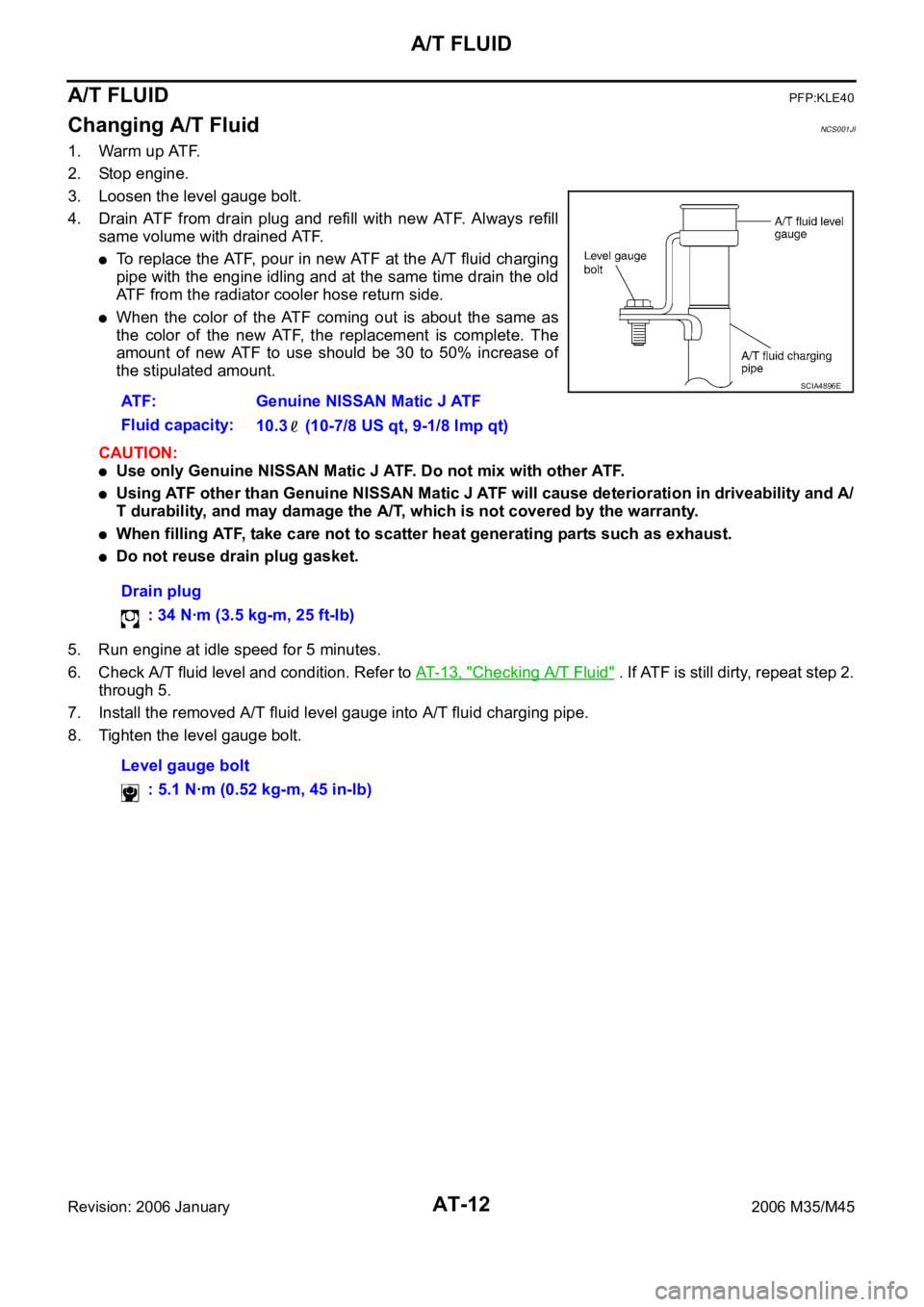
AT-12
A/T FLUID
Revision: 2006 January2006 M35/M45
A/T FLUIDPFP:KLE40
Changing A/T FluidNCS001JI
1. Warm up ATF.
2. Stop engine.
3. Loosen the level gauge bolt.
4. Drain ATF from drain plug and refill with new ATF. Always refill
same volume with drained ATF.
To replace the ATF, pour in new ATF at the A/T fluid charging
pipe with the engine idling and at the same time drain the old
ATF from the radiator cooler hose return side.
When the color of the ATF coming out is about the same as
the color of the new ATF, the replacement is complete. The
amount of new ATF to use should be 30 to 50% increase of
the stipulated amount.
CAUTION:
Use only Genuine NISSAN Matic J ATF. Do not mix with other ATF.
Using ATF other than Genuine NISSAN Matic J ATF will cause deterioration in driveability and A/
T durability, and may damage the A/T, which is not covered by the warranty.
When filling ATF, take care not to scatter heat generating parts such as exhaust.
Do not reuse drain plug gasket.
5. Run engine at idle speed for 5 minutes.
6. Check A/T fluid level and condition. Refer to AT- 1 3 , "
Checking A/T Fluid" . If ATF is still dirty, repeat step 2.
through 5.
7. Install the removed A/T fluid level gauge into A/T fluid charging pipe.
8. Tighten the level gauge bolt.ATF: Genuine NISSAN Matic J ATF
Fluid capacity:
10.3 (10-7/8 US qt, 9-1/8 lmp qt)
Drain plug
: 34 Nꞏm (3.5 kg-m, 25 ft-lb)
Level gauge bolt
: 5.1 Nꞏm (0.52 kg-m, 45 in-lb)
SCIA4896E
Page 93 of 5621
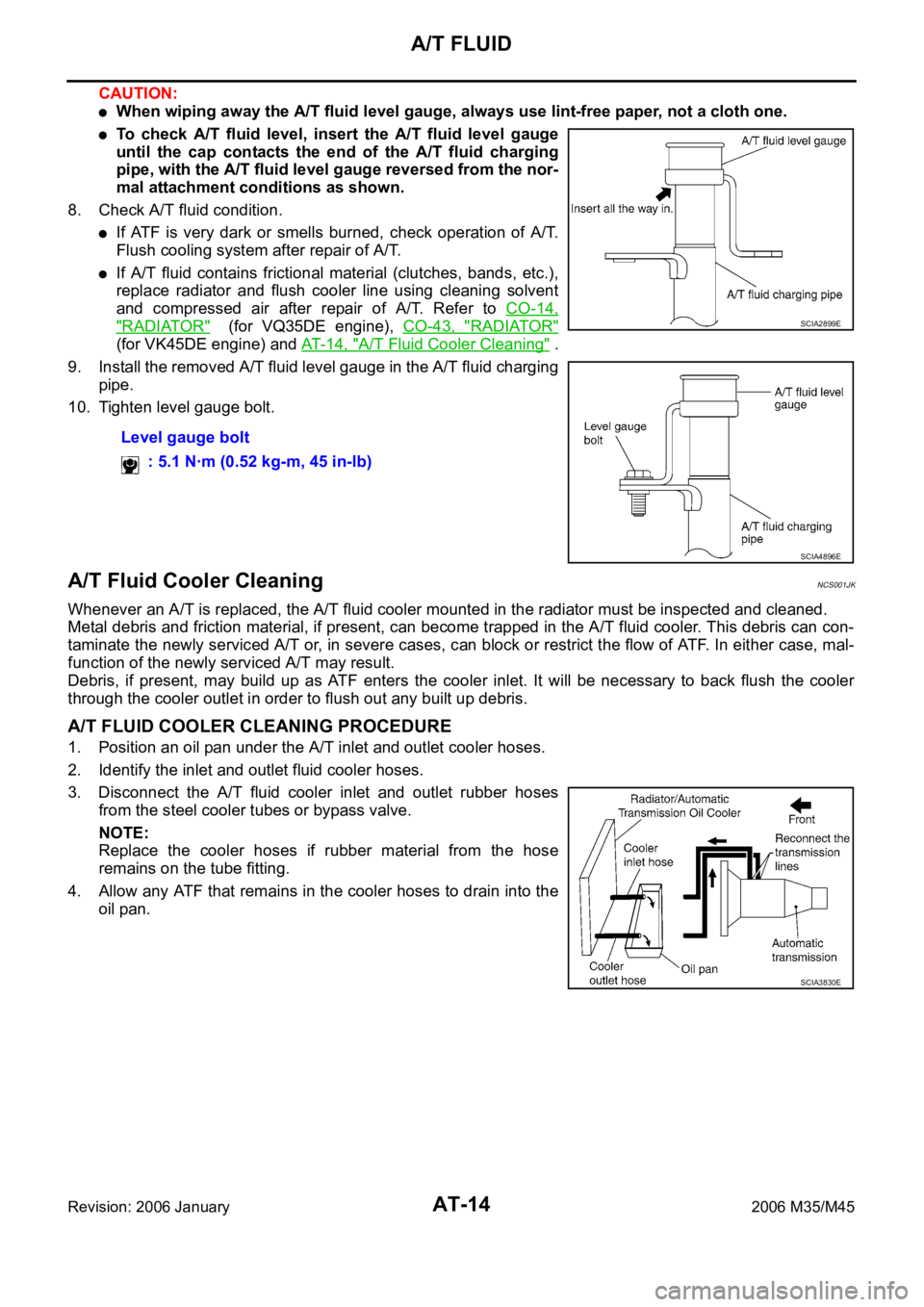
AT-14
A/T FLUID
Revision: 2006 January2006 M35/M45
CAUTION:
When wiping away the A/T fluid level gauge, always use lint-free paper, not a cloth one.
To check A/T fluid level, insert the A/T fluid level gauge
until the cap contacts the end of the A/T fluid charging
pipe, with the A/T fluid level gauge reversed from the nor-
mal attachment conditions as shown.
8. Check A/T fluid condition.
If ATF is very dark or smells burned, check operation of A/T.
Flush cooling system after repair of A/T.
If A/T fluid contains frictional material (clutches, bands, etc.),
replace radiator and flush cooler line using cleaning solvent
and compressed air after repair of A/T. Refer to CO-14,
"RADIATOR" (for VQ35DE engine), CO-43, "RADIATOR"
(for VK45DE engine) and AT- 1 4 , "A/T Fluid Cooler Cleaning" .
9. Install the removed A/T fluid level gauge in the A/T fluid charging
pipe.
10. Tighten level gauge bolt.
A/T Fluid Cooler CleaningNCS001JK
Whenever an A/T is replaced, the A/T fluid cooler mounted in the radiator must be inspected and cleaned.
Metal debris and friction material, if present, can become trapped in the A/T fluid cooler. This debris can con-
taminate the newly serviced A/T or, in severe cases, can block or restrict the flow of ATF. In either case, mal-
function of the newly serviced A/T may result.
Debris, if present, may build up as ATF enters the cooler inlet. It will be necessary to back flush the cooler
through the cooler outlet in order to flush out any built up debris.
A/T FLUID COOLER CLEANING PROCEDURE
1. Position an oil pan under the A/T inlet and outlet cooler hoses.
2. Identify the inlet and outlet fluid cooler hoses.
3. Disconnect the A/T fluid cooler inlet and outlet rubber hoses
from the steel cooler tubes or bypass valve.
NOTE:
Replace the cooler hoses if rubber material from the hose
remains on the tube fitting.
4. Allow any ATF that remains in the cooler hoses to drain into the
oil pan.Level gauge bolt
: 5.1 Nꞏm (0.52 kg-m, 45 in-lb)
SCIA2899E
SCIA4896E
SCIA3830E
Page 95 of 5621
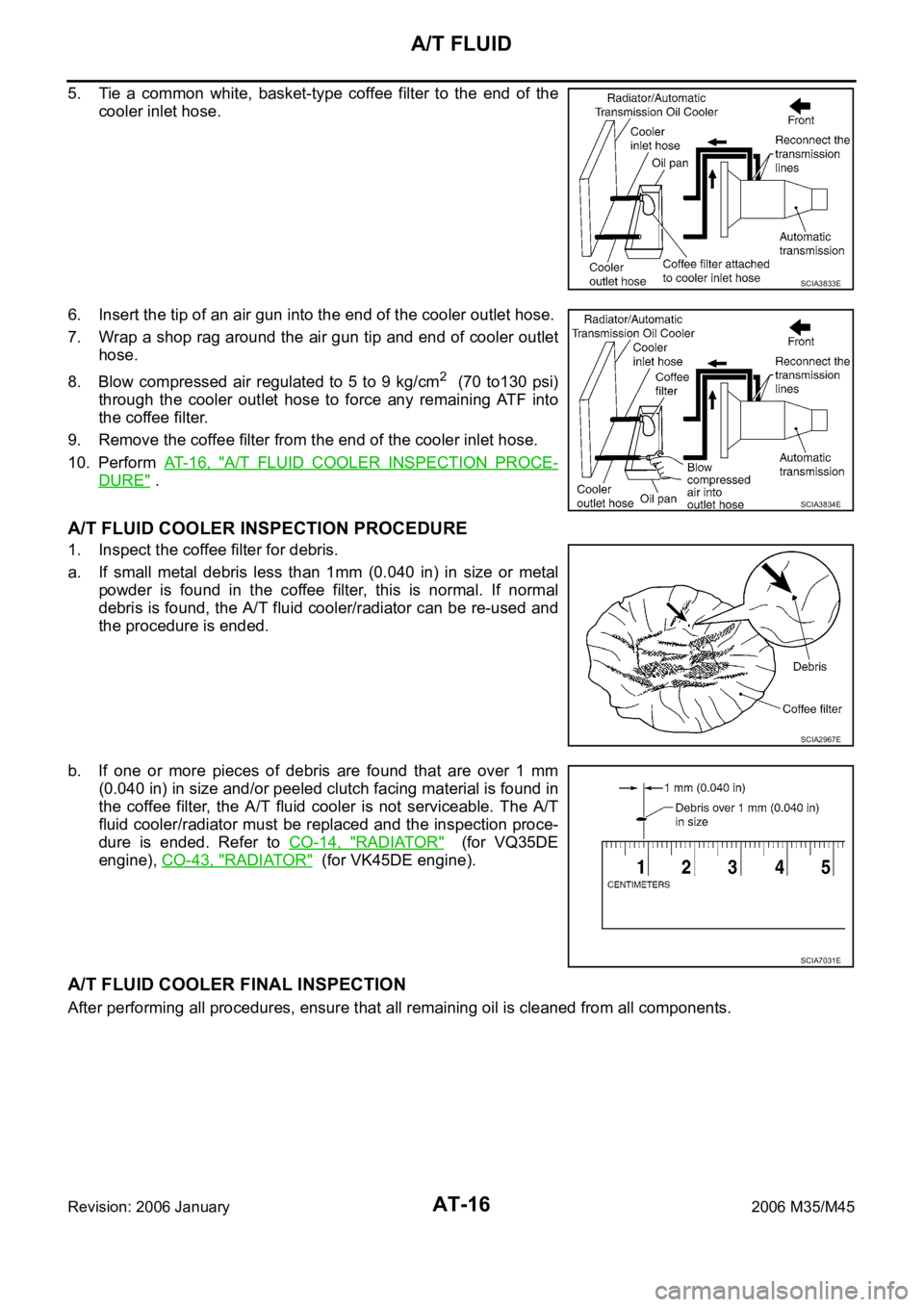
AT-16
A/T FLUID
Revision: 2006 January2006 M35/M45
5. Tie a common white, basket-type coffee filter to the end of the
cooler inlet hose.
6. Insert the tip of an air gun into the end of the cooler outlet hose.
7. Wrap a shop rag around the air gun tip and end of cooler outlet
hose.
8. Blow compressed air regulated to 5 to 9 kg/cm
2 (70 to130 psi)
through the cooler outlet hose to force any remaining ATF into
the coffee filter.
9. Remove the coffee filter from the end of the cooler inlet hose.
10. Perform AT- 1 6 , "
A/T FLUID COOLER INSPECTION PROCE-
DURE" .
A/T FLUID COOLER INSPECTION PROCEDURE
1. Inspect the coffee filter for debris.
a. If small metal debris less than 1mm (0.040 in) in size or metal
powder is found in the coffee filter, this is normal. If normal
debris is found, the A/T fluid cooler/radiator can be re-used and
the procedure is ended.
b. If one or more pieces of debris are found that are over 1 mm
(0.040 in) in size and/or peeled clutch facing material is found in
the coffee filter, the A/T fluid cooler is not serviceable. The A/T
fluid cooler/radiator must be replaced and the inspection proce-
dure is ended. Refer to CO-14, "
RADIATOR" (for VQ35DE
engine), CO-43, "
RADIATOR" (for VK45DE engine).
A/T FLUID COOLER FINAL INSPECTION
After performing all procedures, ensure that all remaining oil is cleaned from all components.
SCIA3833E
SCIA3834E
SCIA2967E
SCIA7031E
Page 556 of 5621
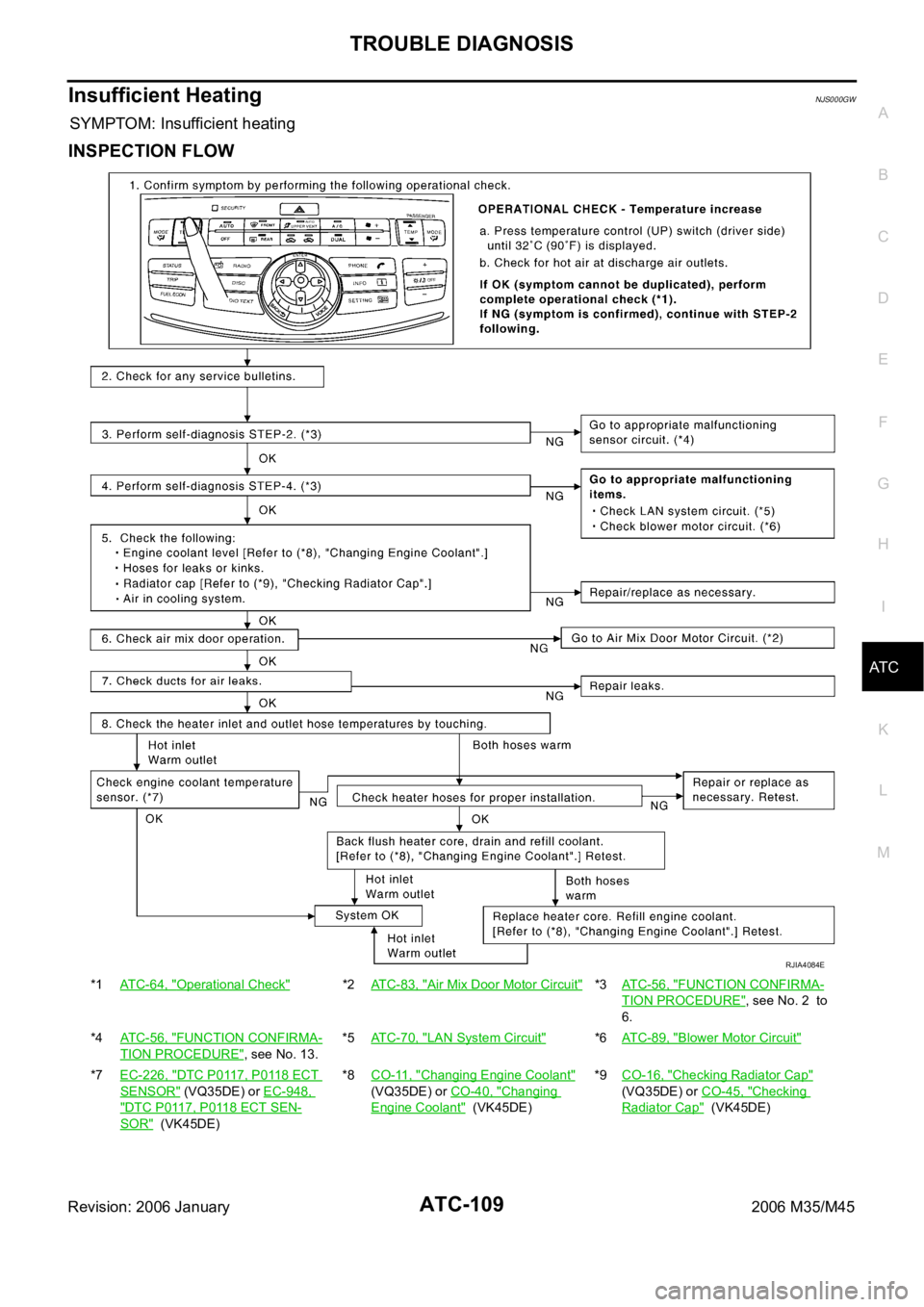
TROUBLE DIAGNOSIS
ATC-109
C
D
E
F
G
H
I
K
L
MA
B
AT C
Revision: 2006 January2006 M35/M45
Insufficient HeatingNJS000GW
SYMPTOM: Insufficient heating
INSPECTION FLOW
*1ATC-64, "Operational Check"*2ATC-83, "Air Mix Door Motor Circuit"*3AT C - 5 6 , "FUNCTION CONFIRMA-
TION PROCEDURE", see No. 2 to
6.
*4ATC-56, "
FUNCTION CONFIRMA-
TION PROCEDURE", see No. 13.*5ATC-70, "
LAN System Circuit"*6AT C - 8 9 , "Blower Motor Circuit"
*7EC-226, "DTC P0117, P0118 ECT
SENSOR" (VQ35DE) or EC-948,
"DTC P0117, P0118 ECT SEN-
SOR" (VK45DE)*8CO-11, "
Changing Engine Coolant"
(VQ35DE) or CO-40, "
Changing
Engine Coolant" (VK45DE)*9CO-16, "
Checking Radiator Cap"
(VQ35DE) or CO-45, "
Checking
Radiator Cap" (VK45DE)
RJIA4084E
Page 560 of 5621
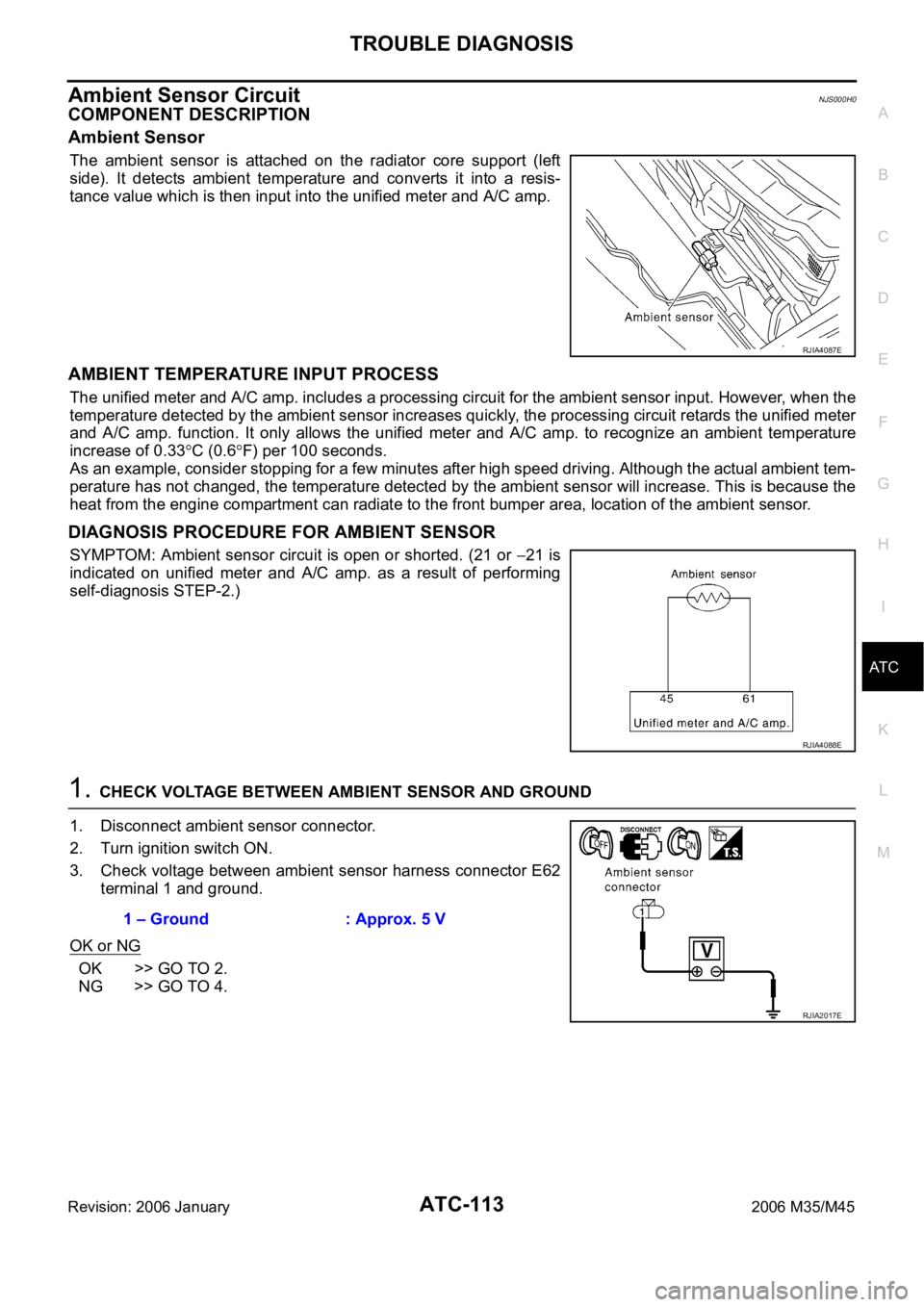
TROUBLE DIAGNOSIS
ATC-113
C
D
E
F
G
H
I
K
L
MA
B
AT C
Revision: 2006 January2006 M35/M45
Ambient Sensor CircuitNJS000H0
COMPONENT DESCRIPTION
Ambient Sensor
The ambient sensor is attached on the radiator core support (left
side). It detects ambient temperature and converts it into a resis-
tance value which is then input into the unified meter and A/C amp.
AMBIENT TEMPERATURE INPUT PROCESS
The unified meter and A/C amp. includes a processing circuit for the ambient sensor input. However, when the
temperature detected by the ambient sensor increases quickly, the processing circuit retards the unified meter
and A/C amp. function. It only allows the unified meter and A/C amp. to recognize an ambient temperature
increase of 0.33
C (0.6F) per 100 seconds.
As an example, consider stopping for a few minutes after high speed driving. Although the actual ambient tem-
perature has not changed, the temperature detected by the ambient sensor will increase. This is because the
heat from the engine compartment can radiate to the front bumper area, location of the ambient sensor.
DIAGNOSIS PROCEDURE FOR AMBIENT SENSOR
SYMPTOM: Ambient sensor circuit is open or shorted. (21 or 21 is
indicated on unified meter and A/C amp. as a result of performing
self-diagnosis STEP-2.)
1. CHECK VOLTAGE BETWEEN AMBIENT SENSOR AND GROUND
1. Disconnect ambient sensor connector.
2. Turn ignition switch ON.
3. Check voltage between ambient sensor harness connector E62
terminal 1 and ground.
OK or NG
OK >> GO TO 2.
NG >> GO TO 4.
RJIA4087E
RJIA4088E
1 – Ground : Approx. 5 V
RJIA2017E
Page 584 of 5621
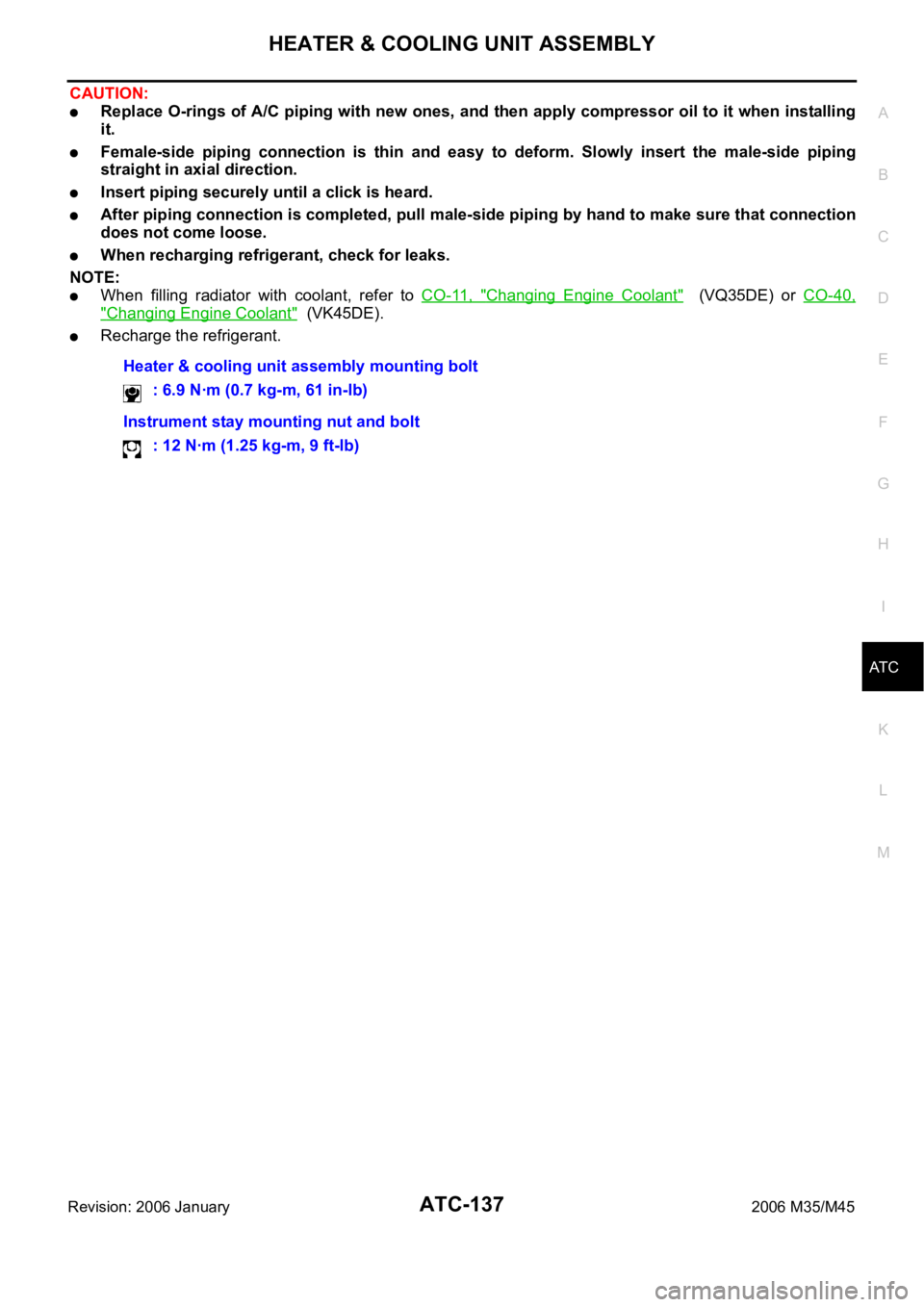
HEATER & COOLING UNIT ASSEMBLY
ATC-137
C
D
E
F
G
H
I
K
L
MA
B
AT C
Revision: 2006 January2006 M35/M45
CAUTION:
Replace O-rings of A/C piping with new ones, and then apply compressor oil to it when installing
it.
Female-side piping connection is thin and easy to deform. Slowly insert the male-side piping
straight in axial direction.
Insert piping securely until a click is heard.
After piping connection is completed, pull male-side piping by hand to make sure that connection
does not come loose.
When recharging refrigerant, check for leaks.
NOTE:
When filling radiator with coolant, refer to CO-11, "Changing Engine Coolant" (VQ35DE) or CO-40,
"Changing Engine Coolant" (VK45DE).
Recharge the refrigerant.
Heater & cooling unit assembly mounting bolt
: 6.9 Nꞏm (0.7 kg-m, 61 in-lb)
Instrument stay mounting nut and bolt
: 12 Nꞏm (1.25 kg-m, 9 ft-lb)
Page 612 of 5621
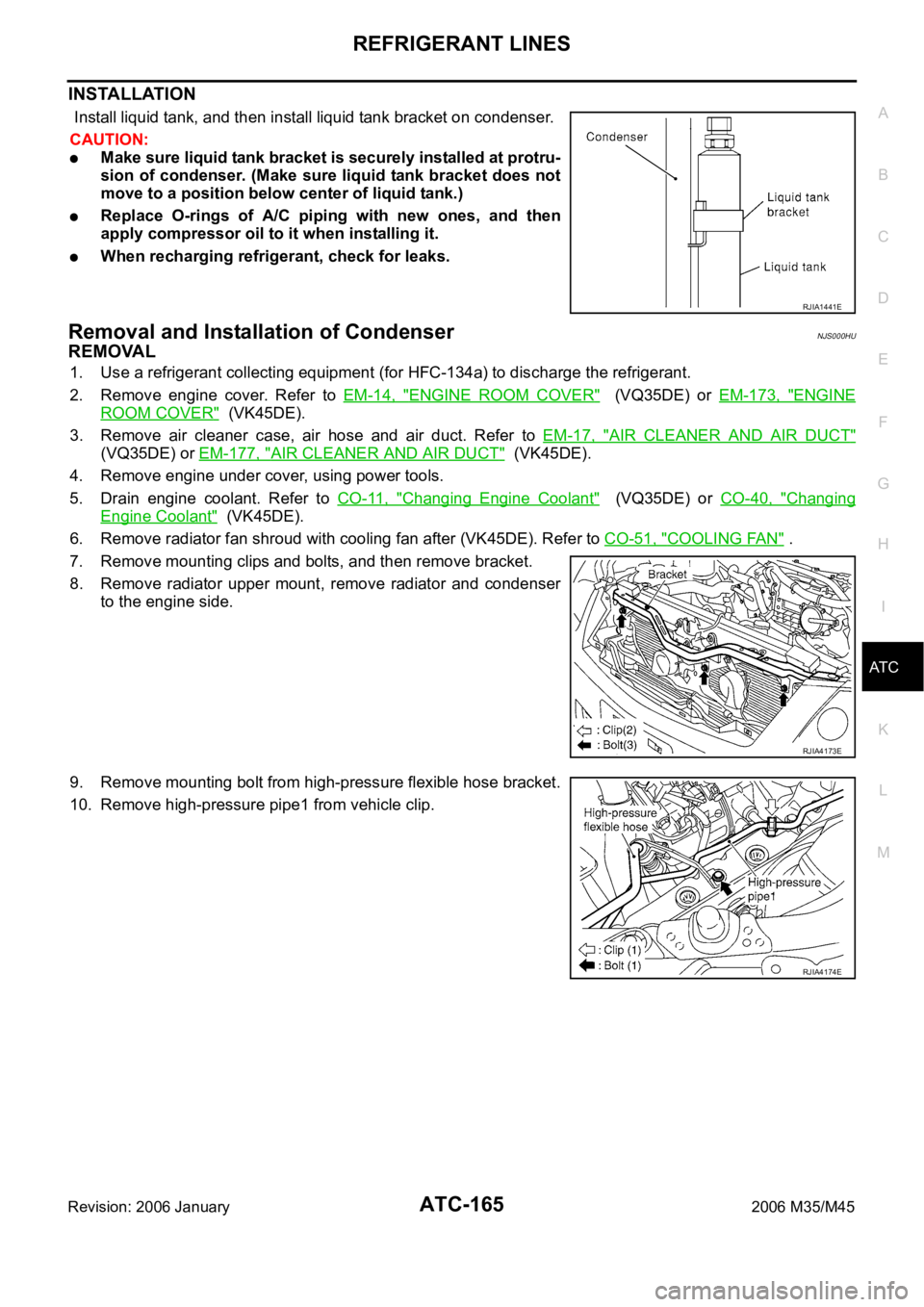
REFRIGERANT LINES
ATC-165
C
D
E
F
G
H
I
K
L
MA
B
AT C
Revision: 2006 January2006 M35/M45
INSTALLATION
Install liquid tank, and then install liquid tank bracket on condenser.
CAUTION:
Make sure liquid tank bracket is securely installed at protru-
sion of condenser. (Make sure liquid tank bracket does not
move to a position below center of liquid tank.)
Replace O-rings of A/C piping with new ones, and then
apply compressor oil to it when installing it.
When recharging refrigerant, check for leaks.
Removal and Installation of CondenserNJS000HU
REMOVAL
1. Use a refrigerant collecting equipment (for HFC-134a) to discharge the refrigerant.
2. Remove engine cover. Refer to EM-14, "
ENGINE ROOM COVER" (VQ35DE) or EM-173, "ENGINE
ROOM COVER" (VK45DE).
3. Remove air cleaner case, air hose and air duct. Refer to EM-17, "
AIR CLEANER AND AIR DUCT"
(VQ35DE) or EM-177, "AIR CLEANER AND AIR DUCT" (VK45DE).
4. Remove engine under cover, using power tools.
5. Drain engine coolant. Refer to CO-11, "
Changing Engine Coolant" (VQ35DE) or CO-40, "Changing
Engine Coolant" (VK45DE).
6. Remove radiator fan shroud with cooling fan after (VK45DE). Refer to CO-51, "
COOLING FAN" .
7. Remove mounting clips and bolts, and then remove bracket.
8. Remove radiator upper mount, remove radiator and condenser
to the engine side.
9. Remove mounting bolt from high-pressure flexible hose bracket.
10. Remove high-pressure pipe1 from vehicle clip.
RJIA1441E
RJIA4173E
RJIA4174E