air condition INFINITI QX4 2005 Factory Service Manual
[x] Cancel search | Manufacturer: INFINITI, Model Year: 2005, Model line: QX4, Model: INFINITI QX4 2005Pages: 3419, PDF Size: 80.18 MB
Page 1131 of 3419
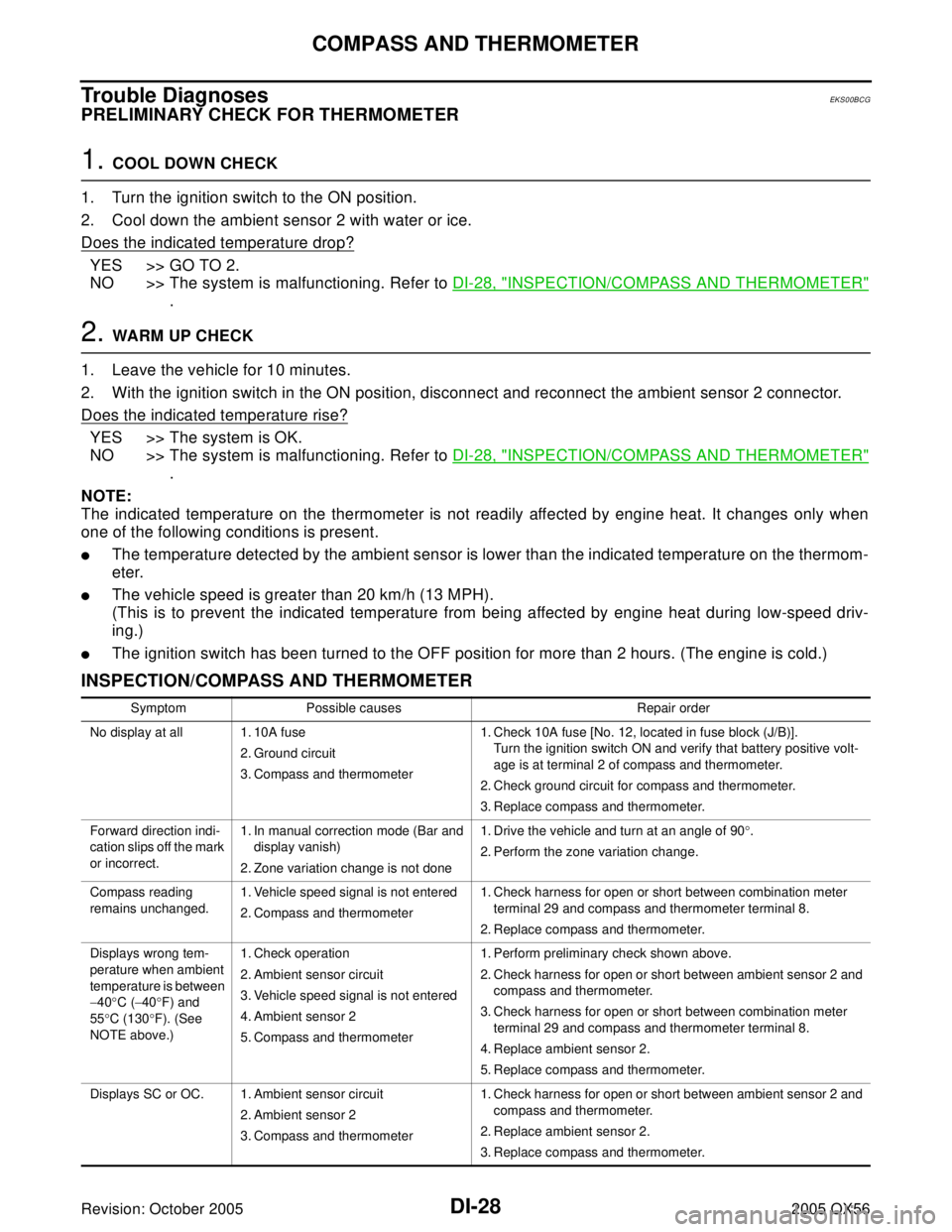
DI-28
COMPASS AND THERMOMETER
Revision: October 20052005 QX56
Trouble DiagnosesEKS00BCG
PRELIMINARY CHECK FOR THERMOMETER
1. COOL DOWN CHECK
1. Turn the ignition switch to the ON position.
2. Cool down the ambient sensor 2 with water or ice.
Does the indicated temperature drop?
YES >> GO TO 2.
NO >> The system is malfunctioning. Refer to DI-28, "
INSPECTION/COMPASS AND THERMOMETER"
.
2. WARM UP CHECK
1. Leave the vehicle for 10 minutes.
2. With the ignition switch in the ON position, disconnect and reconnect the ambient sensor 2 connector.
Does the indicated temperature rise?
YES >> The system is OK.
NO >> The system is malfunctioning. Refer to DI-28, "
INSPECTION/COMPASS AND THERMOMETER"
.
NOTE:
The indicated temperature on the thermometer is not readily affected by engine heat. It changes only when
one of the following conditions is present.
The temperature detected by the ambient sensor is lower than the indicated temperature on the thermom-
eter.
The vehicle speed is greater than 20 km/h (13 MPH).
(This is to prevent the indicated temperature from being affected by engine heat during low-speed driv-
ing.)
The ignition switch has been turned to the OFF position for more than 2 hours. (The engine is cold.)
INSPECTION/COMPASS AND THERMOMETER
Symptom Possible causes Repair order
No display at all 1. 10A fuse
2. Ground circuit
3. Compass and thermometer1. Check 10A fuse [No. 12, located in fuse block (J/B)].
Turn the ignition switch ON and verify that battery positive volt-
age is at terminal 2 of compass and thermometer.
2. Check ground circuit for compass and thermometer.
3. Replace compass and thermometer.
Forward direction indi-
cation slips off the mark
or incorrect.1. In manual correction mode (Bar and
display vanish)
2. Zone variation change is not done1. Drive the vehicle and turn at an angle of 90°.
2. Perform the zone variation change.
Compass reading
remains unchanged.1. Vehicle speed signal is not entered
2. Compass and thermometer1. Check harness for open or short between combination meter
terminal 29 and compass and thermometer terminal 8.
2. Replace compass and thermometer.
Displays wrong tem-
perature when ambient
temperature is between
−40°C (−40°F) and
55°C (130°F). (See
NOTE above.)1. Check operation
2. Ambient sensor circuit
3. Vehicle speed signal is not entered
4. Ambient sensor 2
5. Compass and thermometer1. Perform preliminary check shown above.
2. Check harness for open or short between ambient sensor 2 and
compass and thermometer.
3. Check harness for open or short between combination meter
terminal 29 and compass and thermometer terminal 8.
4. Replace ambient sensor 2.
5. Replace compass and thermometer.
Displays SC or OC. 1. Ambient sensor circuit
2. Ambient sensor 2
3. Compass and thermometer1. Check harness for open or short between ambient sensor 2 and
compass and thermometer.
2. Replace ambient sensor 2.
3. Replace compass and thermometer.
Page 1140 of 3419
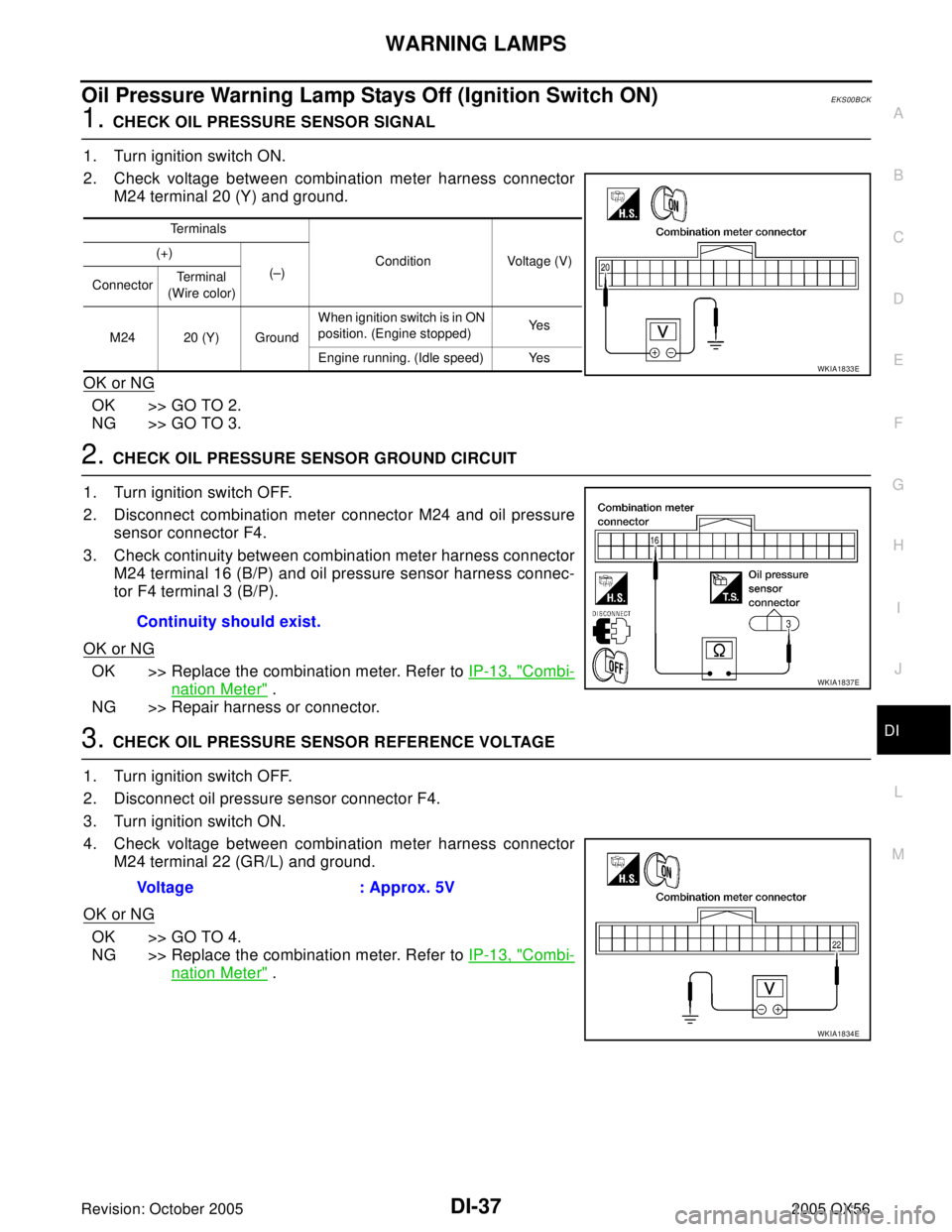
WARNING LAMPS
DI-37
C
D
E
F
G
H
I
J
L
MA
B
DI
Revision: October 20052005 QX56
Oil Pressure Warning Lamp Stays Off (Ignition Switch ON)EKS00BCK
1. CHECK OIL PRESSURE SENSOR SIGNAL
1. Turn ignition switch ON.
2. Check voltage between combination meter harness connector
M24 terminal 20 (Y) and ground.
OK or NG
OK >> GO TO 2.
NG >> GO TO 3.
2. CHECK OIL PRESSURE SENSOR GROUND CIRCUIT
1. Turn ignition switch OFF.
2. Disconnect combination meter connector M24 and oil pressure
sensor connector F4.
3. Check continuity between combination meter harness connector
M24 terminal 16 (B/P) and oil pressure sensor harness connec-
tor F4 terminal 3 (B/P).
OK or NG
OK >> Replace the combination meter. Refer to IP-13, "Combi-
nation Meter" .
NG >> Repair harness or connector.
3. CHECK OIL PRESSURE SENSOR REFERENCE VOLTAGE
1. Turn ignition switch OFF.
2. Disconnect oil pressure sensor connector F4.
3. Turn ignition switch ON.
4. Check voltage between combination meter harness connector
M24 terminal 22 (GR/L) and ground.
OK or NG
OK >> GO TO 4.
NG >> Replace the combination meter. Refer to IP-13, "
Combi-
nation Meter" .
Te r m i n a l s
Condition Voltage (V) (+)
(–)
ConnectorTe r m i n a l
(Wire color)
M24 20 (Y) GroundWhen ignition switch is in ON
position. (Engine stopped)Ye s
Engine running. (Idle speed) Yes
WKIA1833E
Continuity should exist.
WKIA1837E
Voltage : Approx. 5V
WKIA1834E
Page 1150 of 3419
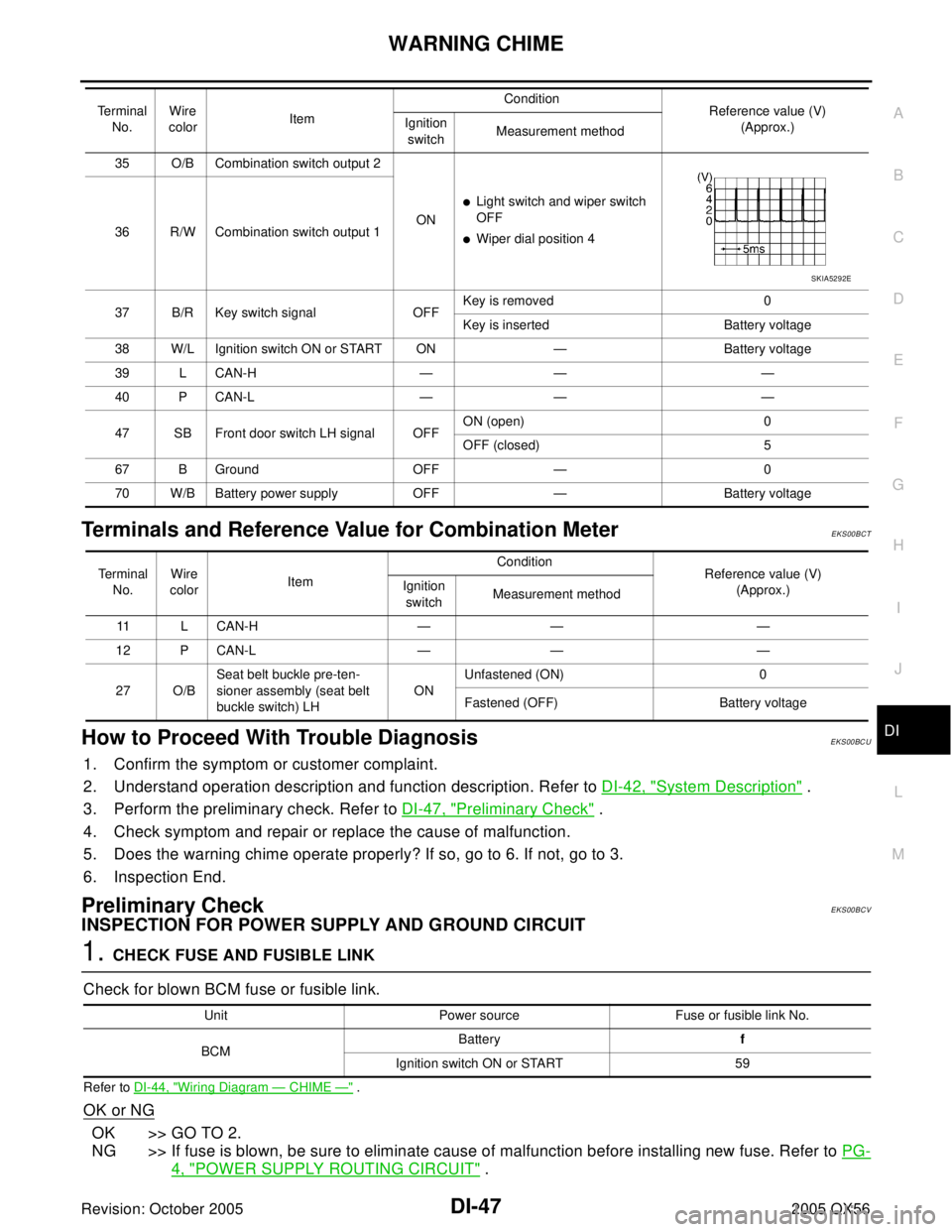
WARNING CHIME
DI-47
C
D
E
F
G
H
I
J
L
MA
B
DI
Revision: October 20052005 QX56
Terminals and Reference Value for Combination MeterEKS00BCT
How to Proceed With Trouble DiagnosisEKS00BCU
1. Confirm the symptom or customer complaint.
2. Understand operation description and function description. Refer to DI-42, "
System Description" .
3. Perform the preliminary check. Refer to DI-47, "
Preliminary Check" .
4. Check symptom and repair or replace the cause of malfunction.
5. Does the warning chime operate properly? If so, go to 6. If not, go to 3.
6. Inspection End.
Preliminary CheckEKS00BCV
INSPECTION FOR POWER SUPPLY AND GROUND CIRCUIT
1. CHECK FUSE AND FUSIBLE LINK
Check for blown BCM fuse or fusible link.
Refer to DI-44, "Wiring Diagram — CHIME —" .
OK or NG
OK >> GO TO 2.
NG >> If fuse is blown, be sure to eliminate cause of malfunction before installing new fuse. Refer to PG-
4, "POWER SUPPLY ROUTING CIRCUIT" .
35 O/B Combination switch output 2
ON
Light switch and wiper switch
OFF
Wiper dial position 4 36 R/W Combination switch output 1
37 B/R Key switch signal OFFKey is removed 0
Key is inserted Battery voltage
38 W/L Ignition switch ON or START ON — Battery voltage
39 L CAN-H — — —
40 P CAN-L — — —
47 SB Front door switch LH signal OFFON (open) 0
OFF (closed) 5
67 B Ground OFF — 0
70 W/B Battery power supply OFF — Battery voltage Te r m i n a l
No.Wire
colorItem Condition
Reference value (V)
(Approx.) Ignition
switchMeasurement method
SKIA5292E
Te r m i n a l
No.Wire
colorItem Condition
Reference value (V)
(Approx.) Ignition
switchMeasurement method
11 L C A N - H — — —
12 P CAN-L — — —
27 O/BSeat belt buckle pre-ten-
sioner assembly (seat belt
buckle switch) LH ONUnfastened (ON) 0
Fastened (OFF) Battery voltage
Unit Power source Fuse or fusible link No.
BCMBatteryf
Ignition switch ON or START 59
Page 1166 of 3419
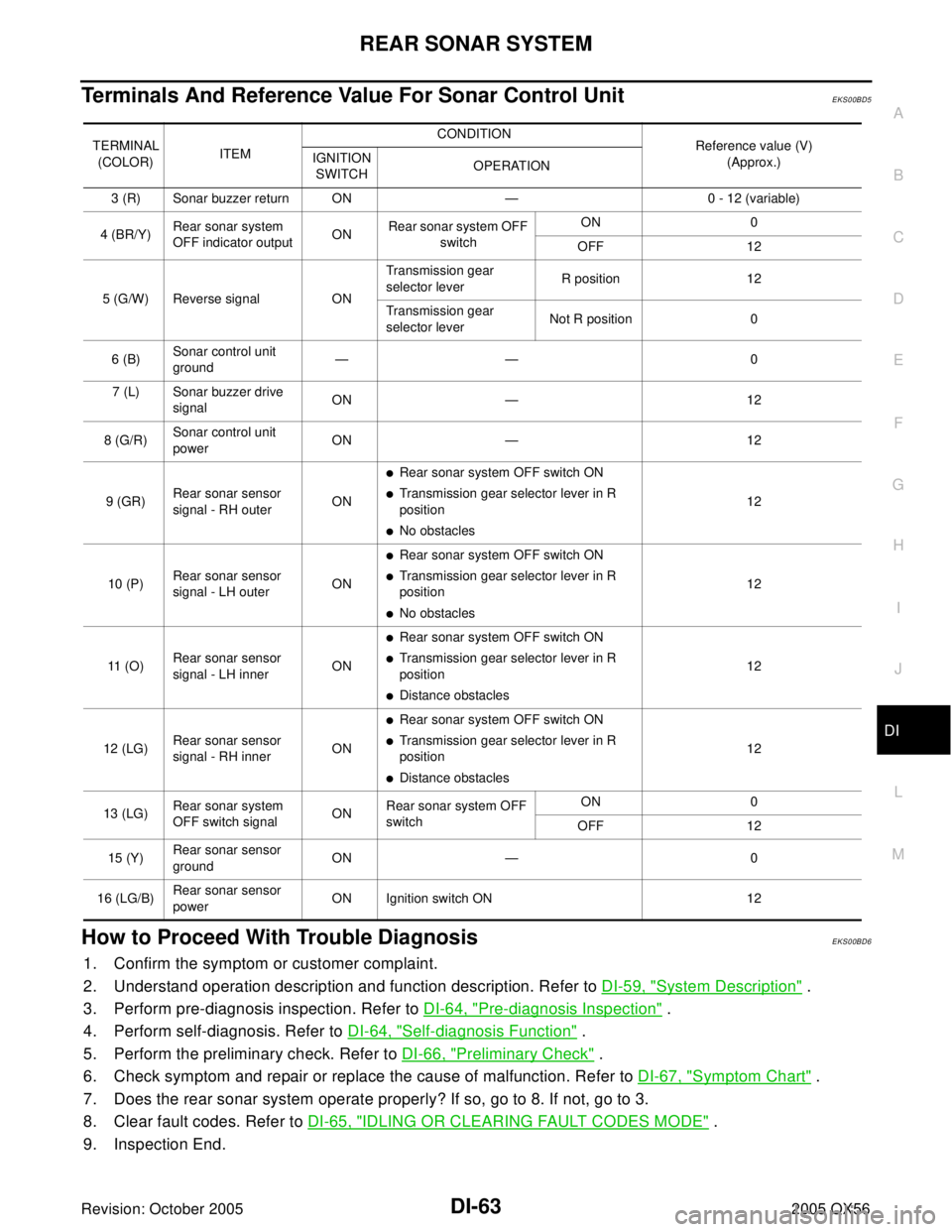
REAR SONAR SYSTEM
DI-63
C
D
E
F
G
H
I
J
L
MA
B
DI
Revision: October 20052005 QX56
Terminals And Reference Value For Sonar Control UnitEKS00BD5
How to Proceed With Trouble DiagnosisEKS00BD6
1. Confirm the symptom or customer complaint.
2. Understand operation description and function description. Refer to DI-59, "
System Description" .
3. Perform pre-diagnosis inspection. Refer to DI-64, "
Pre-diagnosis Inspection" .
4. Perform self-diagnosis. Refer to DI-64, "
Self-diagnosis Function" .
5. Perform the preliminary check. Refer to DI-66, "
Preliminary Check" .
6. Check symptom and repair or replace the cause of malfunction. Refer to DI-67, "
Symptom Chart" .
7. Does the rear sonar system operate properly? If so, go to 8. If not, go to 3.
8. Clear fault codes. Refer to DI-65, "
IDLING OR CLEARING FAULT CODES MODE" .
9. Inspection End.
TERMINAL
(COLOR)ITEMCONDITION
Reference value (V)
(Approx.) IGNITION
SWITCHOPERATION
3 (R) Sonar buzzer return ON — 0 - 12 (variable)
4 (BR/Y)Rear sonar system
OFF indicator outputONRear sonar system OFF
switch ON 0
OFF 12
5 (G/W) Reverse signal ONTransmission gear
selector leverR position 12
Transmission gear
selector leverNot R position 0
6 (B)Sonar control unit
ground —— 0
7 (L) Sonar buzzer drive
signalON — 12
8 (G/R)Sonar control unit
powerON — 12
9 (GR)Rear sonar sensor
signal - RH outerON
Rear sonar system OFF switch ON
Transmission gear selector lever in R
position
No obstacles12
10 (P)Rear sonar sensor
signal - LH outerON
Rear sonar system OFF switch ON
Transmission gear selector lever in R
position
No obstacles12
11 ( O )Rear sonar sensor
signal - LH innerON
Rear sonar system OFF switch ON
Transmission gear selector lever in R
position
Distance obstacles12
12 (LG)Rear sonar sensor
signal - RH innerON
Rear sonar system OFF switch ON
Transmission gear selector lever in R
position
Distance obstacles12
13 (LG)Rear sonar system
OFF switch signalONRear sonar system OFF
switchON 0
OFF 12
15 (Y)Rear sonar sensor
groundON — 0
16 (LG/B)Rear sonar sensor
powerON Ignition switch ON 12
Page 1170 of 3419
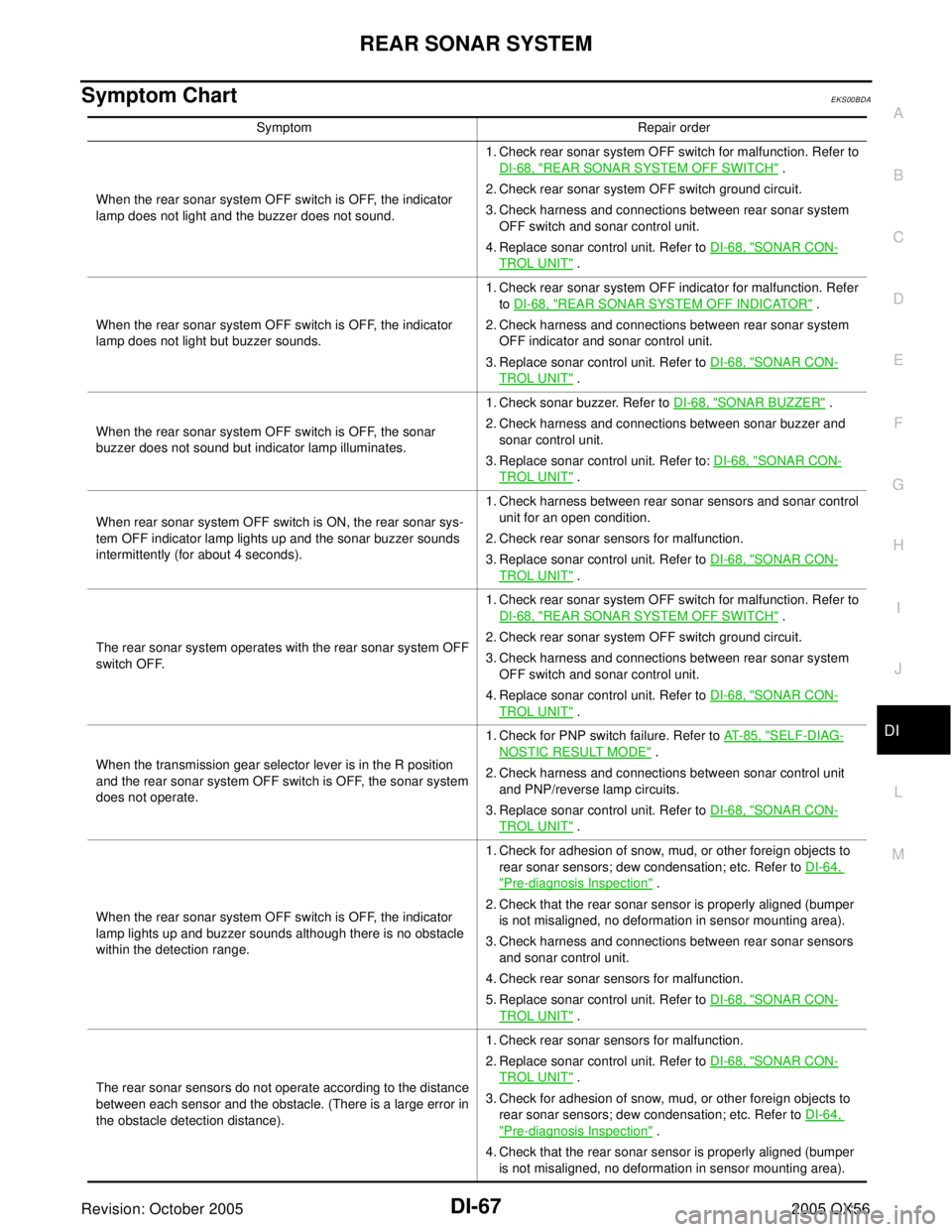
REAR SONAR SYSTEM
DI-67
C
D
E
F
G
H
I
J
L
MA
B
DI
Revision: October 20052005 QX56
Symptom Chart EKS00BDA
Symptom Repair order
When the rear sonar system OFF switch is OFF, the indicator
lamp does not light and the buzzer does not sound.1. Check rear sonar system OFF switch for malfunction. Refer to
DI-68, "
REAR SONAR SYSTEM OFF SWITCH" .
2. Check rear sonar system OFF switch ground circuit.
3. Check harness and connections between rear sonar system
OFF switch and sonar control unit.
4. Replace sonar control unit. Refer to DI-68, "
SONAR CON-
TROL UNIT" .
When the rear sonar system OFF switch is OFF, the indicator
lamp does not light but buzzer sounds.1. Check rear sonar system OFF indicator for malfunction. Refer
to DI-68, "
REAR SONAR SYSTEM OFF INDICATOR" .
2. Check harness and connections between rear sonar system
OFF indicator and sonar control unit.
3. Replace sonar control unit. Refer to DI-68, "
SONAR CON-
TROL UNIT" .
When the rear sonar system OFF switch is OFF, the sonar
buzzer does not sound but indicator lamp illuminates.1. Check sonar buzzer. Refer to DI-68, "
SONAR BUZZER" .
2. Check harness and connections between sonar buzzer and
sonar control unit.
3. Replace sonar control unit. Refer to: DI-68, "
SONAR CON-
TROL UNIT" .
When rear sonar system OFF switch is ON, the rear sonar sys-
tem OFF indicator lamp lights up and the sonar buzzer sounds
intermittently (for about 4 seconds).1. Check harness between rear sonar sensors and sonar control
unit for an open condition.
2. Check rear sonar sensors for malfunction.
3. Replace sonar control unit. Refer to DI-68, "
SONAR CON-
TROL UNIT" .
The rear sonar system operates with the rear sonar system OFF
switch OFF.1. Check rear sonar system OFF switch for malfunction. Refer to
DI-68, "
REAR SONAR SYSTEM OFF SWITCH" .
2. Check rear sonar system OFF switch ground circuit.
3. Check harness and connections between rear sonar system
OFF switch and sonar control unit.
4. Replace sonar control unit. Refer to DI-68, "
SONAR CON-
TROL UNIT" .
When the transmission gear selector lever is in the R position
and the rear sonar system OFF switch is OFF, the sonar system
does not operate.1. Check for PNP switch failure. Refer to AT - 8 5 , "
SELF-DIAG-
NOSTIC RESULT MODE" .
2. Check harness and connections between sonar control unit
and PNP/reverse lamp circuits.
3. Replace sonar control unit. Refer to DI-68, "
SONAR CON-
TROL UNIT" .
When the rear sonar system OFF switch is OFF, the indicator
lamp lights up and buzzer sounds although there is no obstacle
within the detection range.1. Check for adhesion of snow, mud, or other foreign objects to
rear sonar sensors; dew condensation; etc. Refer to DI-64,
"Pre-diagnosis Inspection" .
2. Check that the rear sonar sensor is properly aligned (bumper
is not misaligned, no deformation in sensor mounting area).
3. Check harness and connections between rear sonar sensors
and sonar control unit.
4. Check rear sonar sensors for malfunction.
5. Replace sonar control unit. Refer to DI-68, "
SONAR CON-
TROL UNIT" .
The rear sonar sensors do not operate according to the distance
between each sensor and the obstacle. (There is a large error in
the obstacle detection distance).1. Check rear sonar sensors for malfunction.
2. Replace sonar control unit. Refer to DI-68, "
SONAR CON-
TROL UNIT" .
3. Check for adhesion of snow, mud, or other foreign objects to
rear sonar sensors; dew condensation; etc. Refer to DI-64,
"Pre-diagnosis Inspection" .
4. Check that the rear sonar sensor is properly aligned (bumper
is not misaligned, no deformation in sensor mounting area).
Page 1192 of 3419
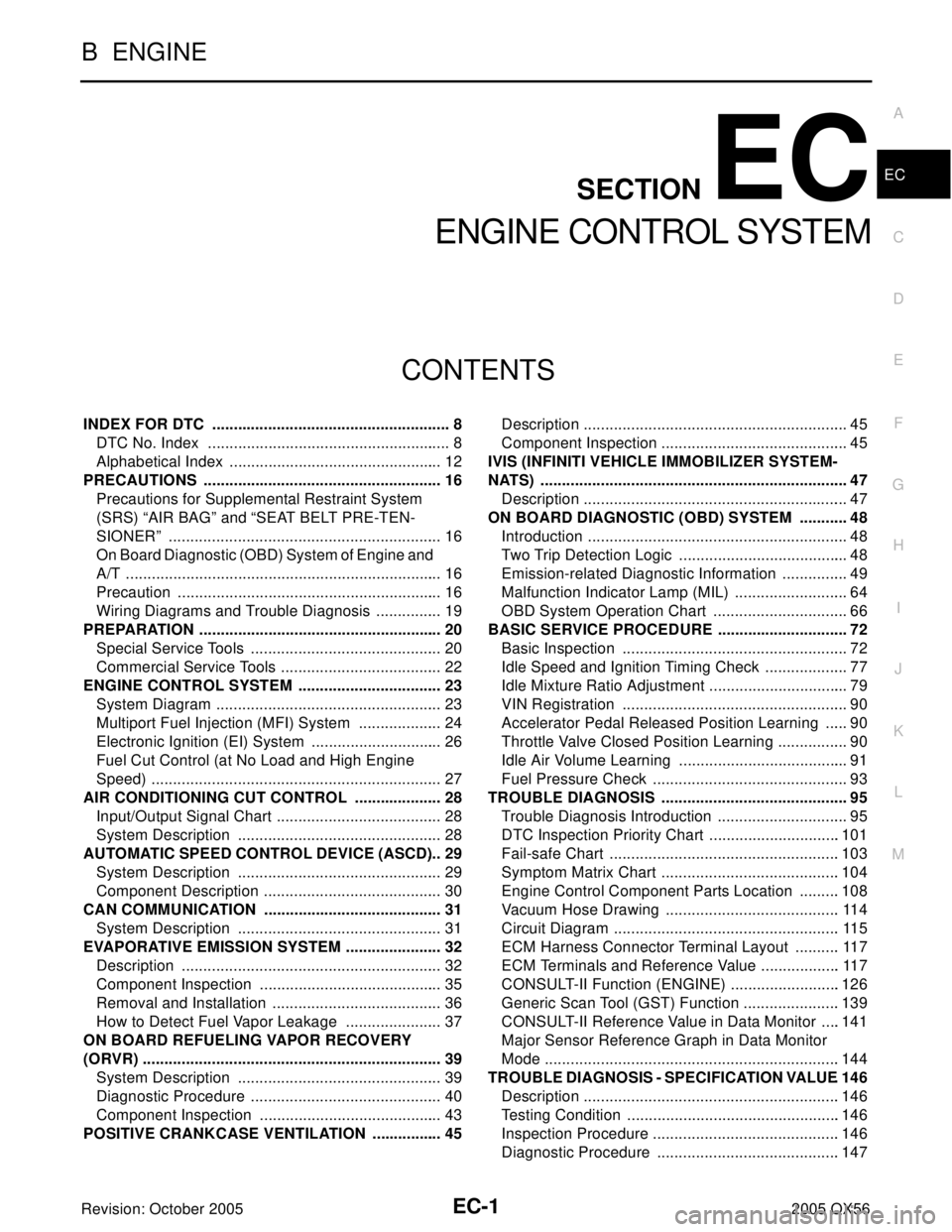
EC-1
ENGINE CONTROL SYSTEM
B ENGINE
CONTENTS
C
D
E
F
G
H
I
J
K
L
M
SECTION EC
A
EC
Revision: October 20052005 QX56 INDEX FOR DTC ........................................................ 8
DTC No. Index ......................................................... 8
Alphabetical Index .................................................. 12
PRECAUTIONS ........................................................ 16
Precautions for Supplemental Restraint System
(SRS) “AIR BAG” and “SEAT BELT PRE-TEN-
SIONER” ................................................................ 16
On Board Diagnostic (OBD) System of Engine and
A/T .......................................................................... 16
Precaution .............................................................. 16
Wiring Diagrams and Trouble Diagnosis ................ 19
PREPARATION ......................................................... 20
Special Service Tools ............................................. 20
Commercial Service Tools ...................................... 22
ENGINE CONTROL SYSTEM .................................. 23
System Diagram ..................................................... 23
Multiport Fuel Injection (MFI) System .................... 24
Electronic Ignition (EI) System ............................... 26
Fuel Cut Control (at No Load and High Engine
Speed) .................................................................... 27
AIR CONDITIONING CUT CONTROL ..................... 28
Input/Output Signal Chart ....................................... 28
System Description ................................................ 28
AUTOMATIC SPEED CONTROL DEVICE (ASCD) ... 29
System Description ................................................ 29
Component Description .......................................... 30
CAN COMMUNICATION .......................................... 31
System Description ................................................ 31
EVAPORATIVE EMISSION SYSTEM ....................... 32
Description ............................................................. 32
Component Inspection ........................................... 35
Removal and Installation ........................................ 36
How to Detect Fuel Vapor Leakage ....................... 37
ON BOARD REFUELING VAPOR RECOVERY
(ORVR) ...................................................................... 39
System Description ................................................ 39
Diagnostic Procedure ............................................. 40
Component Inspection ........................................... 43
POSITIVE CRANKCASE VENTILATION ................. 45Description .............................................................. 45
Component Inspection ............................................ 45
IVIS (INFINITI VEHICLE IMMOBILIZER SYSTEM-
NATS) ........................................................................ 47
Description .............................................................. 47
ON BOARD DIAGNOSTIC (OBD) SYSTEM ............ 48
Introduction ............................................................. 48
Two Trip Detection Logic ........................................ 48
Emission-related Diagnostic Information ................ 49
Malfunction Indicator Lamp (MIL) ........................... 64
OBD System Operation Chart ................................ 66
BASIC SERVICE PROCEDURE ............................... 72
Basic Inspection ..................................................... 72
Idle Speed and Ignition Timing Check .................... 77
Idle Mixture Ratio Adjustment ................................. 79
VIN Registration ..................................................... 90
Accelerator Pedal Released Position Learning ...... 90
Throttle Valve Closed Position Learning ................. 90
Idle Air Volume Learning ........................................ 91
Fuel Pressure Check .............................................. 93
TROUBLE DIAGNOSIS ............................................ 95
Trouble Diagnosis Introduction ............................... 95
DTC Inspection Priority Chart ...............................101
Fail-safe Chart ......................................................103
Symptom Matrix Chart ..........................................104
Engine Control Component Parts Location ..........108
Vacuum Hose Drawing .........................................114
Circuit Diagram .....................................................115
ECM Harness Connector Terminal Layout ...........117
ECM Terminals and Reference Value ...................117
CONSULT-II Function (ENGINE) ..........................126
Generic Scan Tool (GST) Function .......................139
CONSULT-II Reference Value in Data Monitor .....141
Major Sensor Reference Graph in Data Monitor
Mode .....................................................................144
TROUBLE DIAGNOSIS - SPECIFICATION VALUE .146
Description ............................................................146
Testing Condition ..................................................146
Inspection Procedure ............................................146
Diagnostic Procedure ...........................................147
Page 1215 of 3419
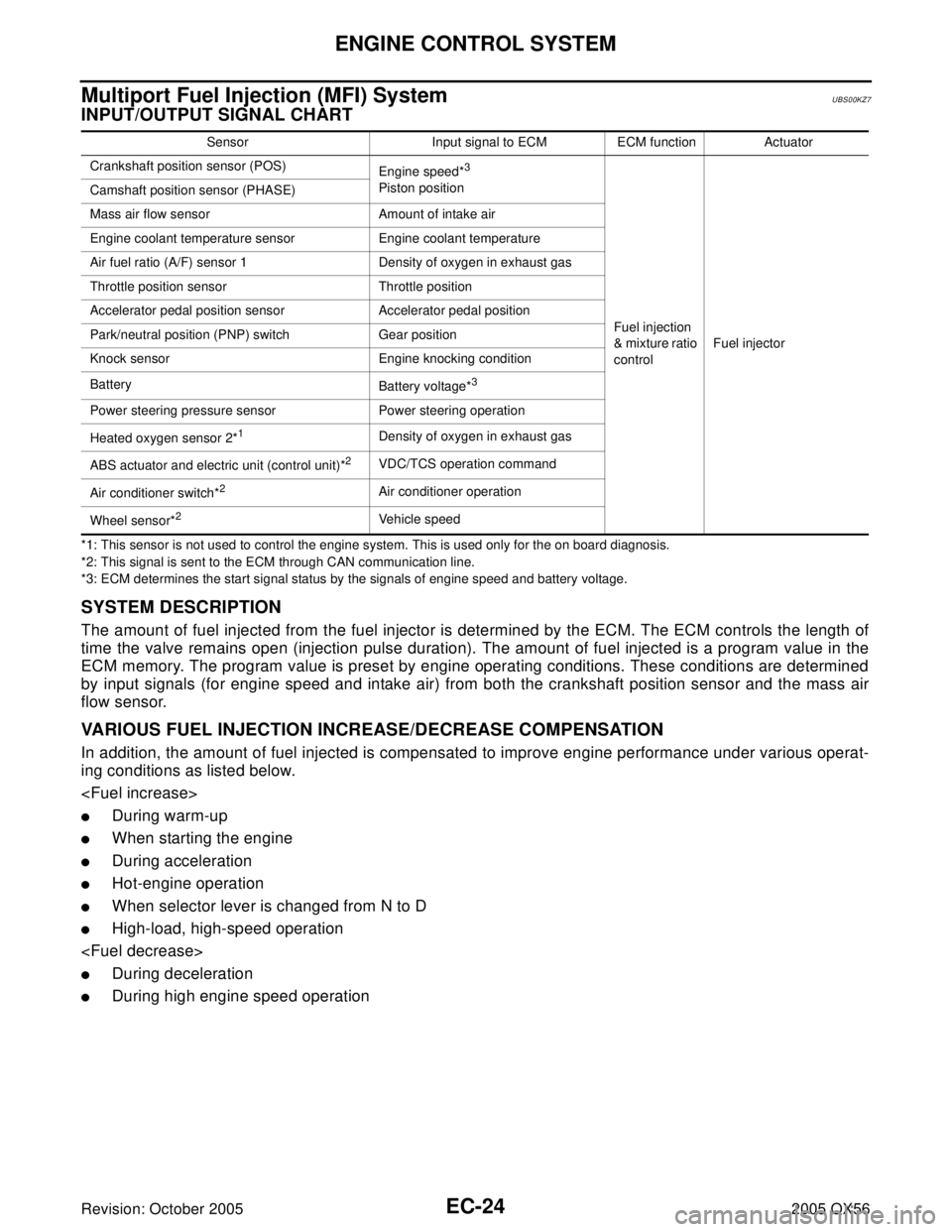
EC-24Revision: October 2005
ENGINE CONTROL SYSTEM
2005 QX56
Multiport Fuel Injection (MFI) SystemUBS00KZ7
INPUT/OUTPUT SIGNAL CHART
*1: This sensor is not used to control the engine system. This is used only for the on board diagnosis.
*2: This signal is sent to the ECM through CAN communication line.
*3: ECM determines the start signal status by the signals of engine speed and battery voltage.
SYSTEM DESCRIPTION
The amount of fuel injected from the fuel injector is determined by the ECM. The ECM controls the length of
time the valve remains open (injection pulse duration). The amount of fuel injected is a program value in the
ECM memory. The program value is preset by engine operating conditions. These conditions are determined
by input signals (for engine speed and intake air) from both the crankshaft position sensor and the mass air
flow sensor.
VARIOUS FUEL INJECTION INCREASE/DECREASE COMPENSATION
In addition, the amount of fuel injected is compensated to improve engine performance under various operat-
ing conditions as listed below.
During warm-up
When starting the engine
During acceleration
Hot-engine operation
When selector lever is changed from N to D
High-load, high-speed operation
During deceleration
During high engine speed operation
Sensor Input signal to ECM ECM function Actuator
Crankshaft position sensor (POS)
Engine speed*
3
Piston position
Fuel injection
& mixture ratio
controlFuel injector Camshaft position sensor (PHASE)
Mass air flow sensor Amount of intake air
Engine coolant temperature sensor Engine coolant temperature
Air fuel ratio (A/F) sensor 1 Density of oxygen in exhaust gas
Throttle position sensor Throttle position
Accelerator pedal position sensor Accelerator pedal position
Park/neutral position (PNP) switch Gear position
Knock sensor Engine knocking condition
Battery
Battery voltage*
3
Power steering pressure sensor Power steering operation
Heated oxygen sensor 2*
1Density of oxygen in exhaust gas
ABS actuator and electric unit (control unit)*
2VDC/TCS operation command
Air conditioner switch*
2Air conditioner operation
Wheel sensor*
2Vehicle speed
Page 1216 of 3419
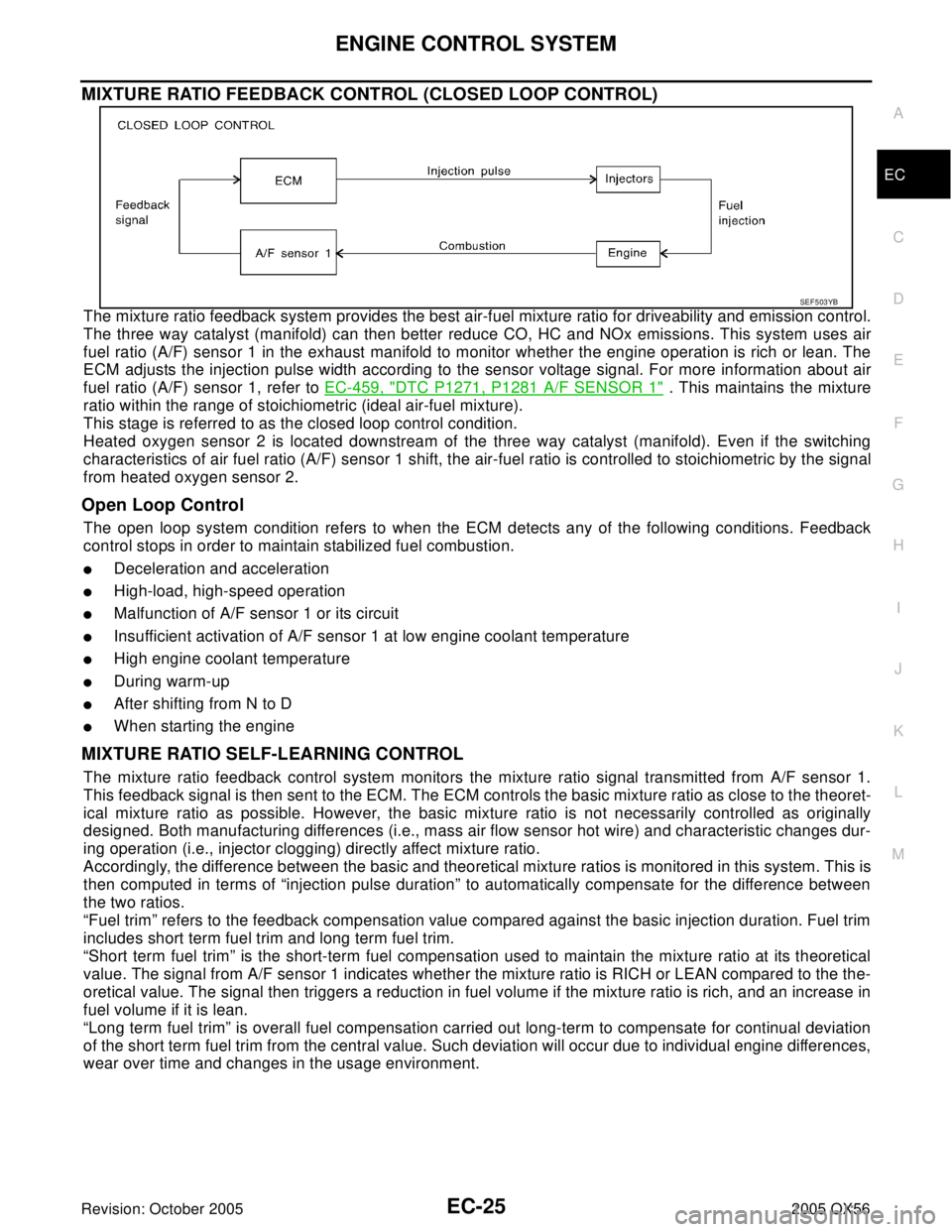
ENGINE CONTROL SYSTEM
EC-25
C
D
E
F
G
H
I
J
K
L
MA
EC
Revision: October 20052005 QX56
MIXTURE RATIO FEEDBACK CONTROL (CLOSED LOOP CONTROL)
The mixture ratio feedback system provides the best air-fuel mixture ratio for driveability and emission control.
The three way catalyst (manifold) can then better reduce CO, HC and NOx emissions. This system uses air
fuel ratio (A/F) sensor 1 in the exhaust manifold to monitor whether the engine operation is rich or lean. The
ECM adjusts the injection pulse width according to the sensor voltage signal. For more information about air
fuel ratio (A/F) sensor 1, refer to EC-459, "
DTC P1271, P1281 A/F SENSOR 1" . This maintains the mixture
ratio within the range of stoichiometric (ideal air-fuel mixture).
This stage is referred to as the closed loop control condition.
Heated oxygen sensor 2 is located downstream of the three way catalyst (manifold). Even if the switching
characteristics of air fuel ratio (A/F) sensor 1 shift, the air-fuel ratio is controlled to stoichiometric by the signal
from heated oxygen sensor 2.
Open Loop Control
The open loop system condition refers to when the ECM detects any of the following conditions. Feedback
control stops in order to maintain stabilized fuel combustion.
Deceleration and acceleration
High-load, high-speed operation
Malfunction of A/F sensor 1 or its circuit
Insufficient activation of A/F sensor 1 at low engine coolant temperature
High engine coolant temperature
During warm-up
After shifting from N to D
When starting the engine
MIXTURE RATIO SELF-LEARNING CONTROL
The mixture ratio feedback control system monitors the mixture ratio signal transmitted from A/F sensor 1.
This feedback signal is then sent to the ECM. The ECM controls the basic mixture ratio as close to the theoret-
ical mixture ratio as possible. However, the basic mixture ratio is not necessarily controlled as originally
designed. Both manufacturing differences (i.e., mass air flow sensor hot wire) and characteristic changes dur-
ing operation (i.e., injector clogging) directly affect mixture ratio.
Accordingly, the difference between the basic and theoretical mixture ratios is monitored in this system. This is
then computed in terms of “injection pulse duration” to automatically compensate for the difference between
the two ratios.
“Fuel trim” refers to the feedback compensation value compared against the basic injection duration. Fuel trim
includes short term fuel trim and long term fuel trim.
“Short term fuel trim” is the short-term fuel compensation used to maintain the mixture ratio at its theoretical
value. The signal from A/F sensor 1 indicates whether the mixture ratio is RICH or LEAN compared to the the-
oretical value. The signal then triggers a reduction in fuel volume if the mixture ratio is rich, and an increase in
fuel volume if it is lean.
“Long term fuel trim” is overall fuel compensation carried out long-term to compensate for continual deviation
of the short term fuel trim from the central value. Such deviation will occur due to individual engine differences,
wear over time and changes in the usage environment.
SEF 5 03 YB
Page 1217 of 3419
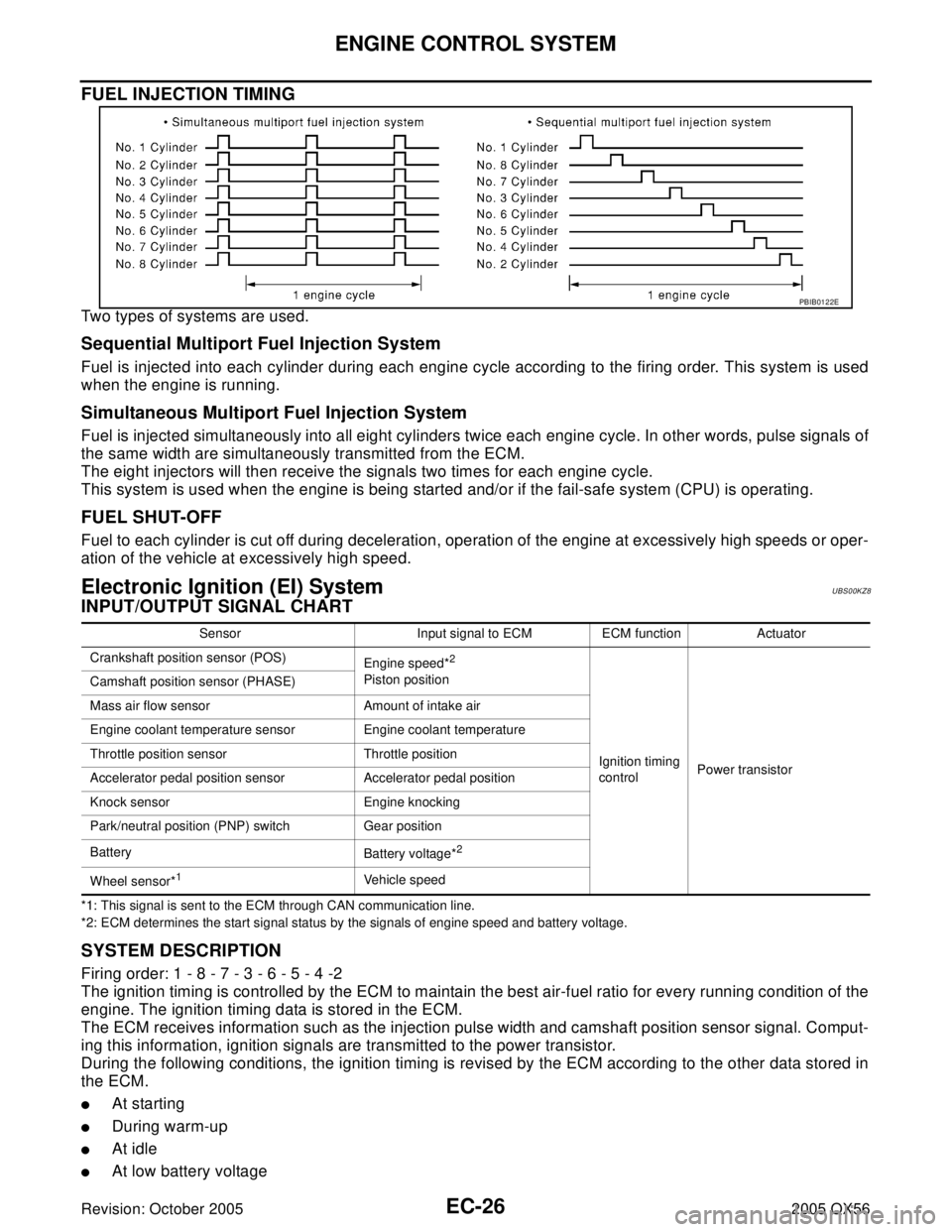
EC-26Revision: October 2005
ENGINE CONTROL SYSTEM
2005 QX56
FUEL INJECTION TIMING
Two types of systems are used.
Sequential Multiport Fuel Injection System
Fuel is injected into each cylinder during each engine cycle according to the firing order. This system is used
when the engine is running.
Simultaneous Multiport Fuel Injection System
Fuel is injected simultaneously into all eight cylinders twice each engine cycle. In other words, pulse signals of
the same width are simultaneously transmitted from the ECM.
The eight injectors will then receive the signals two times for each engine cycle.
This system is used when the engine is being started and/or if the fail-safe system (CPU) is operating.
FUEL SHUT-OFF
Fuel to each cylinder is cut off during deceleration, operation of the engine at excessively high speeds or oper-
ation of the vehicle at excessively high speed.
Electronic Ignition (EI) SystemUBS00KZ8
INPUT/OUTPUT SIGNAL CHART
*1: This signal is sent to the ECM through CAN communication line.
*2: ECM determines the start signal status by the signals of engine speed and battery voltage.
SYSTEM DESCRIPTION
Firing order: 1 - 8 - 7 - 3 - 6 - 5 - 4 -2
The ignition timing is controlled by the ECM to maintain the best air-fuel ratio for every running condition of the
engine. The ignition timing data is stored in the ECM.
The ECM receives information such as the injection pulse width and camshaft position sensor signal. Comput-
ing this information, ignition signals are transmitted to the power transistor.
During the following conditions, the ignition timing is revised by the ECM according to the other data stored in
the ECM.
At starting
During warm-up
At idle
At low battery voltage
PBIB0122E
Sensor Input signal to ECM ECM function Actuator
Crankshaft position sensor (POS)
Engine speed*
2
Piston position
Ignition timing
controlPower transistor Camshaft position sensor (PHASE)
Mass air flow sensor Amount of intake air
Engine coolant temperature sensor Engine coolant temperature
Throttle position sensor Throttle position
Accelerator pedal position sensor Accelerator pedal position
Knock sensor Engine knocking
Park/neutral position (PNP) switch Gear position
Battery
Battery voltage*
2
Wheel sensor*1Vehicle speed
Page 1219 of 3419
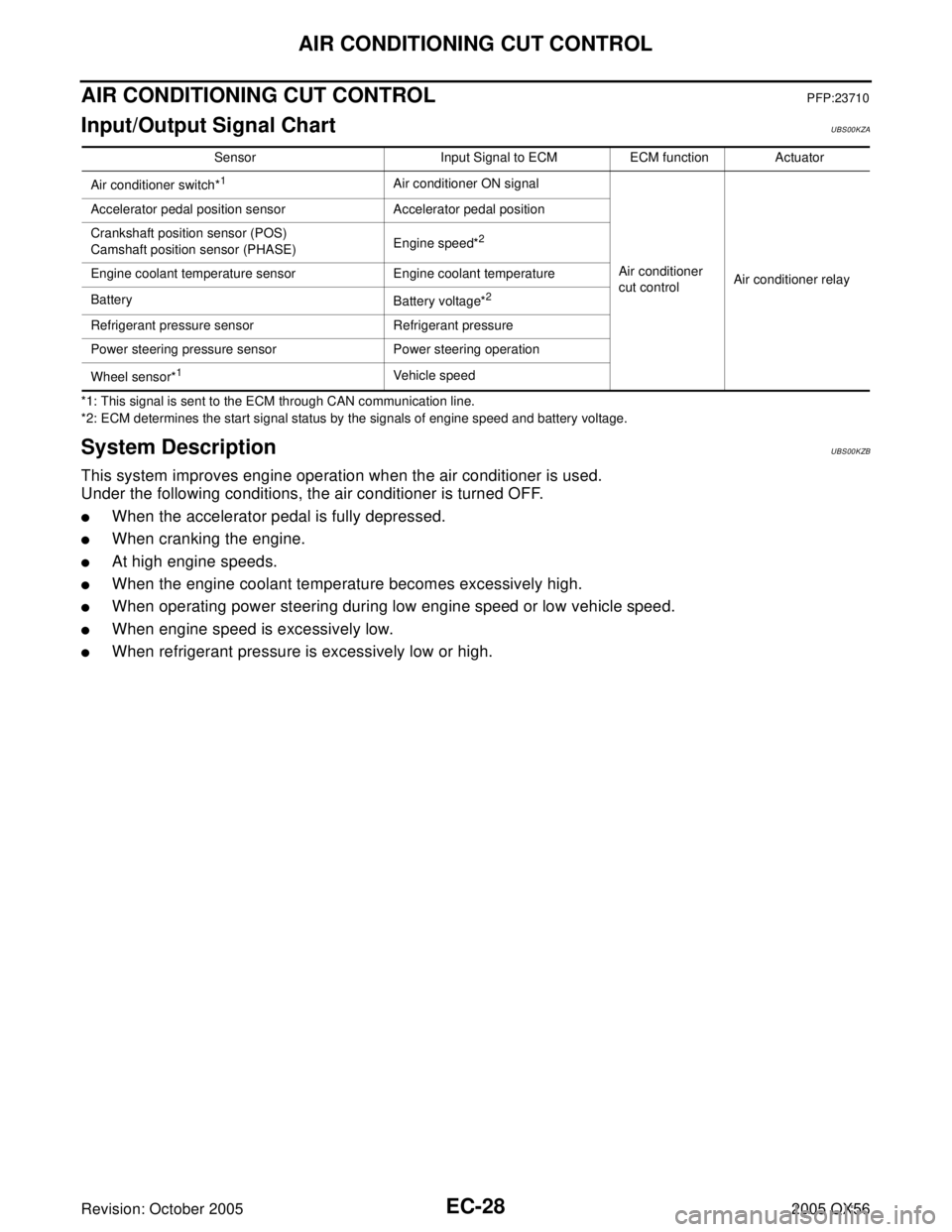
EC-28Revision: October 2005
AIR CONDITIONING CUT CONTROL
2005 QX56
AIR CONDITIONING CUT CONTROLPFP:23710
Input/Output Signal ChartUBS00KZA
*1: This signal is sent to the ECM through CAN communication line.
*2: ECM determines the start signal status by the signals of engine speed and battery voltage.
System DescriptionUBS00KZB
This system improves engine operation when the air conditioner is used.
Under the following conditions, the air conditioner is turned OFF.
When the accelerator pedal is fully depressed.
When cranking the engine.
At high engine speeds.
When the engine coolant temperature becomes excessively high.
When operating power steering during low engine speed or low vehicle speed.
When engine speed is excessively low.
When refrigerant pressure is excessively low or high.
Sensor Input Signal to ECM ECM function Actuator
Air conditioner switch*
1Air conditioner ON signal
Air conditioner
cut controlAir conditioner relay Accelerator pedal position sensor Accelerator pedal position
Crankshaft position sensor (POS)
Camshaft position sensor (PHASE)Engine speed*
2
Engine coolant temperature sensor Engine coolant temperature
Battery
Battery voltage*
2
Refrigerant pressure sensor Refrigerant pressure
Power steering pressure sensor Power steering operation
Wheel sensor*
1Vehicle speed