wiring INFINITI QX4 2005 Factory User Guide
[x] Cancel search | Manufacturer: INFINITI, Model Year: 2005, Model line: QX4, Model: INFINITI QX4 2005Pages: 3419, PDF Size: 80.18 MB
Page 75 of 3419
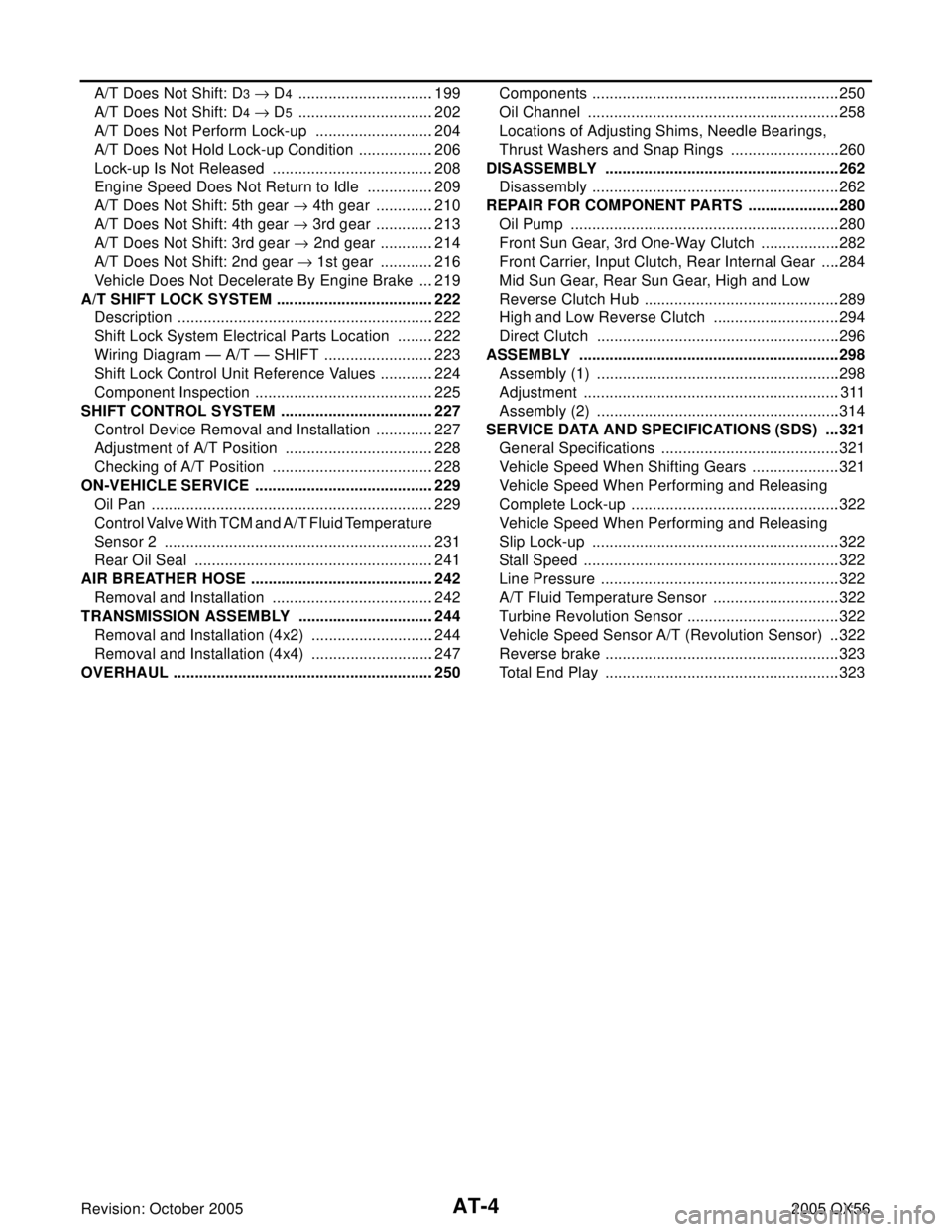
AT-4Revision: October 20052005 QX56 A/T Does Not Shift: D
3 → D4 ................................199
A/T Does Not Shift: D
4 → D5 ................................202
A/T Does Not Perform Lock-up ............................204
A/T Does Not Hold Lock-up Condition ..................206
Lock-up Is Not Released ......................................208
Engine Speed Does Not Return to Idle ................209
A/T Does Not Shift: 5th gear → 4th gear ..............210
A/T Does Not Shift: 4th gear → 3rd gear ..............213
A/T Does Not Shift: 3rd gear → 2nd gear .............214
A/T Does Not Shift: 2nd gear → 1st gear .............216
Vehicle Does Not Decelerate By Engine Brake ....219
A/T SHIFT LOCK SYSTEM .....................................222
Description ............................................................222
Shift Lock System Electrical Parts Location .........222
Wiring Diagram — A/T — SHIFT ..........................223
Shift Lock Control Unit Reference Values .............224
Component Inspection ..........................................225
SHIFT CONTROL SYSTEM ....................................227
Control Device Removal and Installation ..............227
Adjustment of A/T Position ...................................228
Checking of A/T Position ......................................228
ON-VEHICLE SERVICE ..........................................229
Oil Pan ..................................................................229
Control Valve With TCM and A/T Fluid Temperature
Sensor 2 ...............................................................231
Rear Oil Seal ........................................................241
AIR BREATHER HOSE ...........................................242
Removal and Installation ......................................242
TRANSMISSION ASSEMBLY ................................244
Removal and Installation (4x2) .............................244
Removal and Installation (4x4) .............................247
OVERHAUL .............................................................250Components .......................................................... 250
Oil Channel ........................................................... 258
Locations of Adjusting Shims, Needle Bearings,
Thrust Washers and Snap Rings .......................... 260
DISASSEMBLY ....................................................... 262
Disassembly .......................................................... 262
REPAIR FOR COMPONENT PARTS ...................... 280
Oil Pump ............................................................... 280
Front Sun Gear, 3rd One-Way Clutch ................... 282
Front Carrier, Input Clutch, Rear Internal Gear ..... 284
Mid Sun Gear, Rear Sun Gear, High and Low
Reverse Clutch Hub .............................................. 289
High and Low Reverse Clutch .............................. 294
Direct Clutch ......................................................... 296
ASSEMBLY ............................................................. 298
Assembly (1) ......................................................... 298
Adjustment ............................................................311
Assembly (2) ......................................................... 314
SERVICE DATA AND SPECIFICATIONS (SDS) .... 321
General Specifications .......................................... 321
Vehicle Speed When Shifting Gears ..................... 321
Vehicle Speed When Performing and Releasing
Complete Lock-up ................................................. 322
Vehicle Speed When Performing and Releasing
Slip Lock-up .......................................................... 322
Stall Speed ............................................................ 322
Line Pressure ........................................................ 322
A/T Fluid Temperature Sensor .............................. 322
Turbine Revolution Sensor .................................... 322
Vehicle Speed Sensor A/T (Revolution Sensor) ... 322
Reverse brake ....................................................... 323
Total End Play ....................................................... 323
Page 78 of 3419
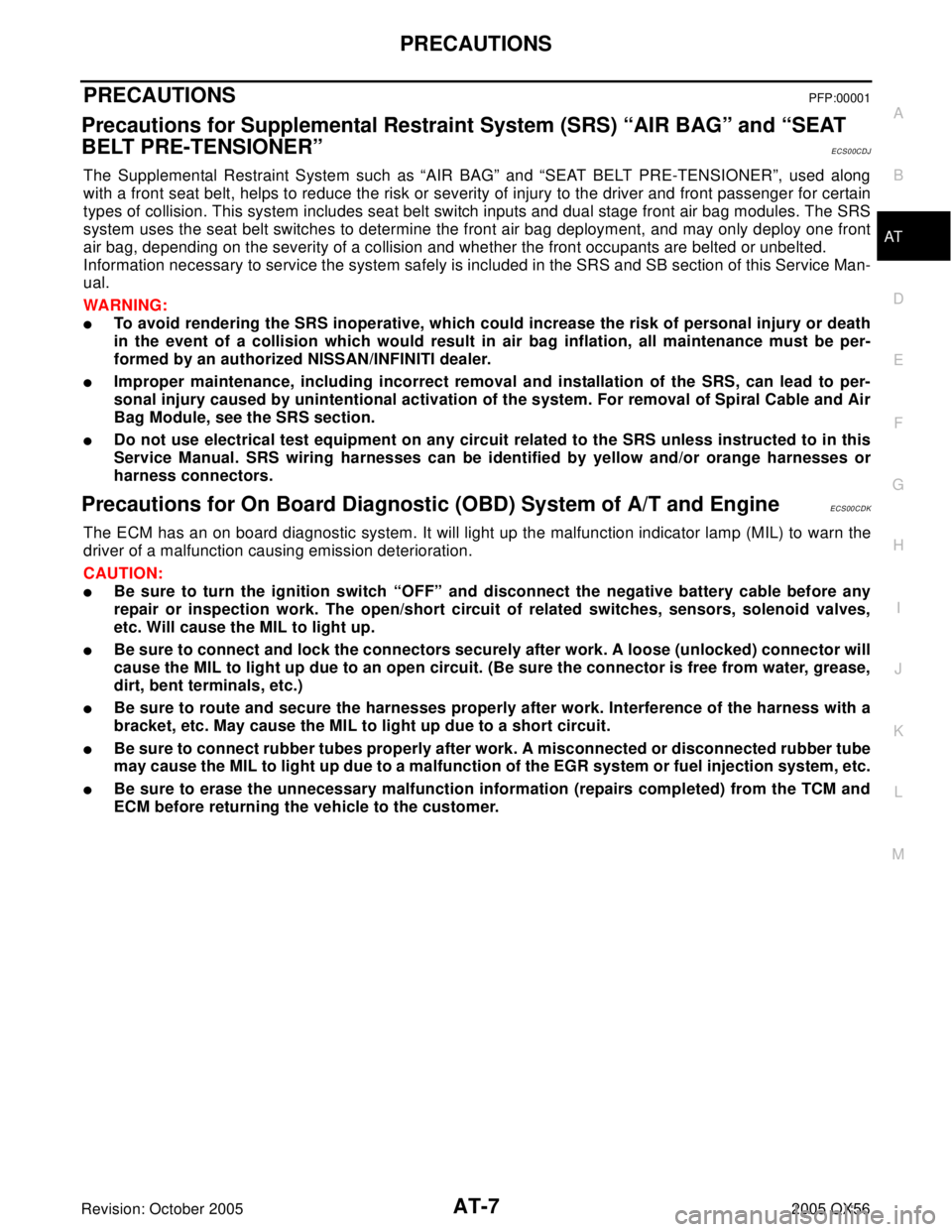
PRECAUTIONS
AT-7
D
E
F
G
H
I
J
K
L
MA
B
AT
Revision: October 20052005 QX56
PRECAUTIONSPFP:00001
Precautions for Supplemental Restraint System (SRS) “AIR BAG” and “SEAT
BELT PRE-TENSIONER”
ECS00CDJ
The Supplemental Restraint System such as “AIR BAG” and “SEAT BELT PRE-TENSIONER”, used along
with a front seat belt, helps to reduce the risk or severity of injury to the driver and front passenger for certain
types of collision. This system includes seat belt switch inputs and dual stage front air bag modules. The SRS
system uses the seat belt switches to determine the front air bag deployment, and may only deploy one front
air bag, depending on the severity of a collision and whether the front occupants are belted or unbelted.
Information necessary to service the system safely is included in the SRS and SB section of this Service Man-
ual.
WA RN ING:
To avoid rendering the SRS inoperative, which could increase the risk of personal injury or death
in the event of a collision which would result in air bag inflation, all maintenance must be per-
formed by an authorized NISSAN/INFINITI dealer.
Improper maintenance, including incorrect removal and installation of the SRS, can lead to per-
sonal injury caused by unintentional activation of the system. For removal of Spiral Cable and Air
Bag Module, see the SRS section.
Do not use electrical test equipment on any circuit related to the SRS unless instructed to in this
Service Manual. SRS wiring harnesses can be identified by yellow and/or orange harnesses or
harness connectors.
Precautions for On Board Diagnostic (OBD) System of A/T and EngineECS00CDK
The ECM has an on board diagnostic system. It will light up the malfunction indicator lamp (MIL) to warn the
driver of a malfunction causing emission deterioration.
CAUTION:
Be sure to turn the ignition switch “OFF” and disconnect the negative battery cable before any
repair or inspection work. The open/short circuit of related switches, sensors, solenoid valves,
etc. Will cause the MIL to light up.
Be sure to connect and lock the connectors securely after work. A loose (unlocked) connector will
cause the MIL to light up due to an open circuit. (Be sure the connector is free from water, grease,
dirt, bent terminals, etc.)
Be sure to route and secure the harnesses properly after work. Interference of the harness with a
bracket, etc. May cause the MIL to light up due to a short circuit.
Be sure to connect rubber tubes properly after work. A misconnected or disconnected rubber tube
may cause the MIL to light up due to a malfunction of the EGR system or fuel injection system, etc.
Be sure to erase the unnecessary malfunction information (repairs completed) from the TCM and
ECM before returning the vehicle to the customer.
Page 80 of 3419
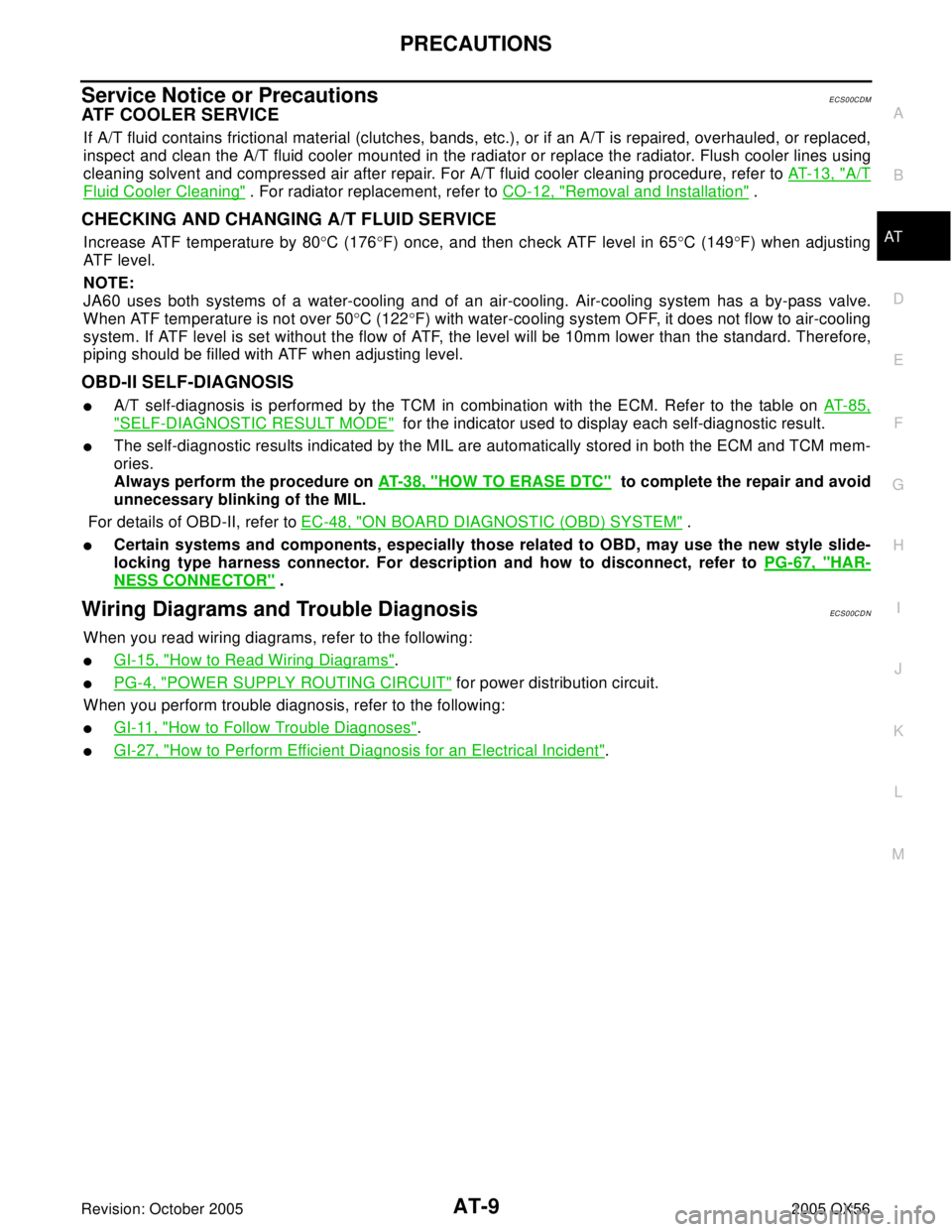
PRECAUTIONS
AT-9
D
E
F
G
H
I
J
K
L
MA
B
AT
Revision: October 20052005 QX56
Service Notice or PrecautionsECS00CDM
ATF COOLER SERVICE
If A/T fluid contains frictional material (clutches, bands, etc.), or if an A/T is repaired, overhauled, or replaced,
inspect and clean the A/T fluid cooler mounted in the radiator or replace the radiator. Flush cooler lines using
cleaning solvent and compressed air after repair. For A/T fluid cooler cleaning procedure, refer to AT-13, "
A/T
Fluid Cooler Cleaning" . For radiator replacement, refer to CO-12, "Removal and Installation" .
CHECKING AND CHANGING A/T FLUID SERVICE
Increase ATF temperature by 80°C (176°F) once, and then check ATF level in 65°C (149°F) when adjusting
ATF level.
NOTE:
JA60 uses both systems of a water-cooling and of an air-cooling. Air-cooling system has a by-pass valve.
When ATF temperature is not over 50°C (122°F) with water-cooling system OFF, it does not flow to air-cooling
system. If ATF level is set without the flow of ATF, the level will be 10mm lower than the standard. Therefore,
piping should be filled with ATF when adjusting level.
OBD-II SELF-DIAGNOSIS
A/T self-diagnosis is performed by the TCM in combination with the ECM. Refer to the table on AT-85,
"SELF-DIAGNOSTIC RESULT MODE" for the indicator used to display each self-diagnostic result.
The self-diagnostic results indicated by the MIL are automatically stored in both the ECM and TCM mem-
ories.
Always perform the procedure on AT-3 8, "
HOW TO ERASE DTC" to complete the repair and avoid
unnecessary blinking of the MIL.
For details of OBD-II, refer to EC-48, "
ON BOARD DIAGNOSTIC (OBD) SYSTEM" .
Certain systems and components, especially those related to OBD, may use the new style slide-
locking type harness connector. For description and how to disconnect, refer to PG-67, "
HAR-
NESS CONNECTOR" .
Wiring Diagrams and Trouble DiagnosisECS0 0CD N
When you read wiring diagrams, refer to the following:
GI-15, "How to Read Wiring Diagrams".
PG-4, "POWER SUPPLY ROUTING CIRCUIT" for power distribution circuit.
When you perform trouble diagnosis, refer to the following:
GI-11, "How to Follow Trouble Diagnoses".
GI-27, "How to Perform Efficient Diagnosis for an Electrical Incident".
Page 101 of 3419
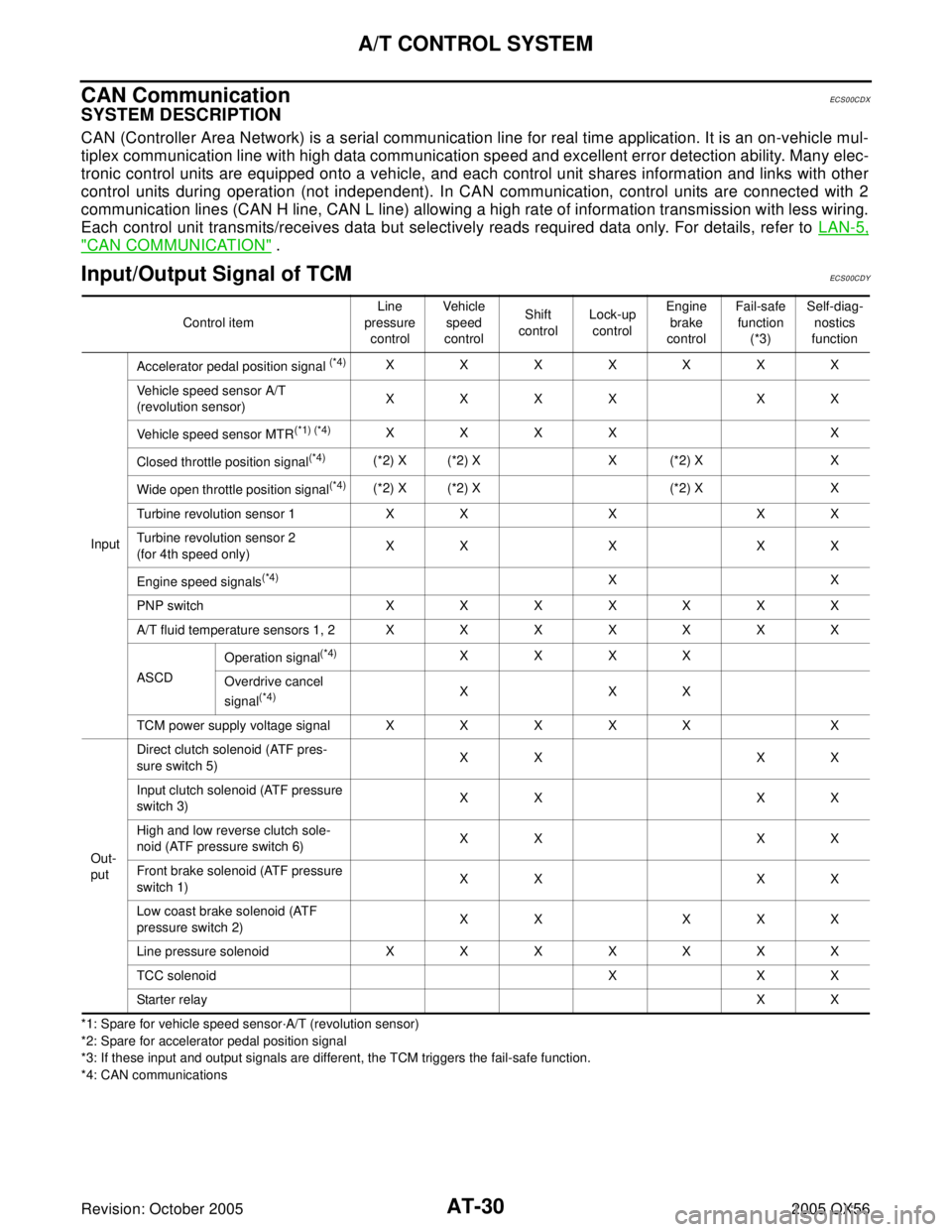
AT-30
A/T CONTROL SYSTEM
Revision: October 20052005 QX56
CAN CommunicationECS00CDX
SYSTEM DESCRIPTION
CAN (Controller Area Network) is a serial communication line for real time application. It is an on-vehicle mul-
tiplex communication line with high data communication speed and excellent error detection ability. Many elec-
tronic control units are equipped onto a vehicle, and each control unit shares information and links with other
control units during operation (not independent). In CAN communication, control units are connected with 2
communication lines (CAN H line, CAN L line) allowing a high rate of information transmission with less wiring.
Each control unit transmits/receives data but selectively reads required data only. For details, refer to LAN-5,
"CAN COMMUNICATION" .
Input/Output Signal of TCMECS00CDY
*1: Spare for vehicle speed sensor·A/T (revolution sensor)
*2: Spare for accelerator pedal position signal
*3: If these input and output signals are different, the TCM triggers the fail-safe function.
*4: CAN communicationsControl itemLine
pressure
controlVehicle
speed
controlShift
controlLock-up
controlEngine
brake
controlFail-safe
function
(*3)Self-diag-
nostics
function
InputAccelerator pedal position signal
(*4)XXXXXXX
Vehicle speed sensor A/T
(revolution sensor)XXXX XX
Vehicle speed sensor MTR
(*1) (*4)XXXX X
Closed throttle position signal
(*4)(*2) X (*2) X X (*2) X X
Wide open throttle position signal
(*4)(*2) X (*2) X (*2) X X
Turbine revolution sensor 1 X X X X X
Turbine revolution sensor 2
(for 4th speed only)XX X XX
Engine speed signals
(*4)XX
PNP switch XXXXXXX
A/T fluid temperature sensors 1, 2 X X X X X X X
ASCDOperation signal
(*4)XXXX
Overdrive cancel
signal
(*4)XXX
TCM power supply voltage signal X X X X X X
Out-
putDirect clutch solenoid (ATF pres-
sure switch 5)XX XX
Input clutch solenoid (ATF pressure
switch 3)XX XX
High and low reverse clutch sole-
noid (ATF pressure switch 6)XX XX
Front brake solenoid (ATF pressure
switch 1)XX XX
Low coast brake solenoid (ATF
pressure switch 2)XX XXX
Line pressure solenoid X X X X X X X
TCC solenoid X X X
Starte r re la yXX
Page 114 of 3419
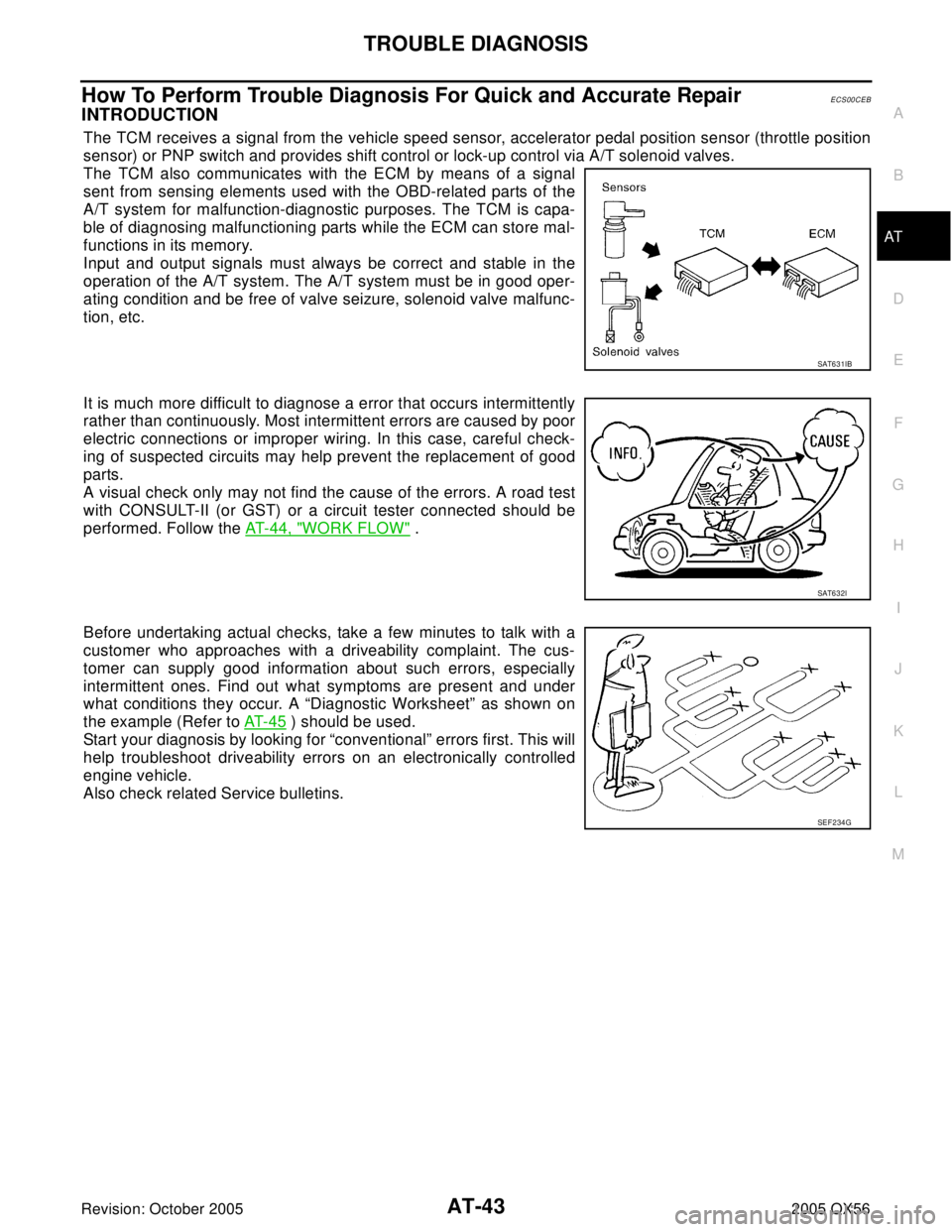
TROUBLE DIAGNOSIS
AT-43
D
E
F
G
H
I
J
K
L
MA
B
AT
Revision: October 20052005 QX56
How To Perform Trouble Diagnosis For Quick and Accurate RepairECS00CEB
INTRODUCTION
The TCM receives a signal from the vehicle speed sensor, accelerator pedal position sensor (throttle position
sensor) or PNP switch and provides shift control or lock-up control via A/T solenoid valves.
The TCM also communicates with the ECM by means of a signal
sent from sensing elements used with the OBD-related parts of the
A/T system for malfunction-diagnostic purposes. The TCM is capa-
ble of diagnosing malfunctioning parts while the ECM can store mal-
functions in its memory.
Input and output signals must always be correct and stable in the
operation of the A/T system. The A/T system must be in good oper-
ating condition and be free of valve seizure, solenoid valve malfunc-
tion, etc.
It is much more difficult to diagnose a error that occurs intermittently
rather than continuously. Most intermittent errors are caused by poor
electric connections or improper wiring. In this case, careful check-
ing of suspected circuits may help prevent the replacement of good
parts.
A visual check only may not find the cause of the errors. A road test
with CONSULT-II (or GST) or a circuit tester connected should be
performed. Follow the AT-44, "
WORK FLOW" .
Before undertaking actual checks, take a few minutes to talk with a
customer who approaches with a driveability complaint. The cus-
tomer can supply good information about such errors, especially
intermittent ones. Find out what symptoms are present and under
what conditions they occur. A “Diagnostic Worksheet” as shown on
the example (Refer to AT- 4 5
) should be used.
Start your diagnosis by looking for “conventional” errors first. This will
help troubleshoot driveability errors on an electronically controlled
engine vehicle.
Also check related Service bulletins.
SAT6 3 1IB
SAT6 3 2I
SEF 2 34 G
Page 166 of 3419
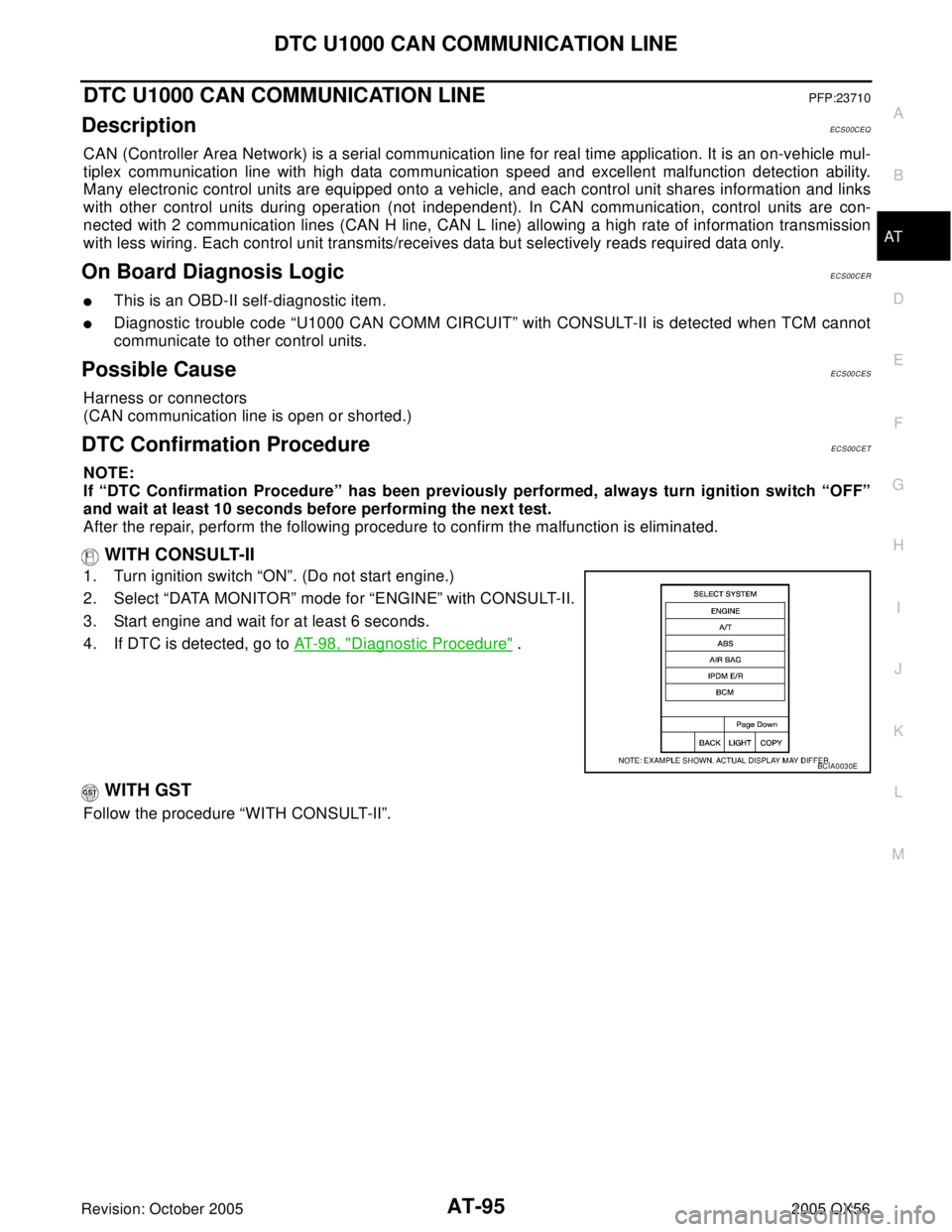
DTC U1000 CAN COMMUNICATION LINE
AT-95
D
E
F
G
H
I
J
K
L
MA
B
AT
Revision: October 20052005 QX56
DTC U1000 CAN COMMUNICATION LINEPFP:23710
DescriptionECS00CEQ
CAN (Controller Area Network) is a serial communication line for real time application. It is an on-vehicle mul-
tiplex communication line with high data communication speed and excellent malfunction detection ability.
Many electronic control units are equipped onto a vehicle, and each control unit shares information and links
with other control units during operation (not independent). In CAN communication, control units are con-
nected with 2 communication lines (CAN H line, CAN L line) allowing a high rate of information transmission
with less wiring. Each control unit transmits/receives data but selectively reads required data only.
On Board Diagnosis LogicECS00CER
This is an OBD-II self-diagnostic item.
Diagnostic trouble code “U1000 CAN COMM CIRCUIT” with CONSULT-II is detected when TCM cannot
communicate to other control units.
Possible CauseECS00CES
Harness or connectors
(CAN communication line is open or shorted.)
DTC Confirmation ProcedureECS00CET
NOTE:
If “DTC Confirmation Procedure” has been previously performed, always turn ignition switch “OFF”
and wait at least 10 seconds before performing the next test.
After the repair, perform the following procedure to confirm the malfunction is eliminated.
WITH CONSULT-II
1. Turn ignition switch “ON”. (Do not start engine.)
2. Select “DATA MONITOR” mode for “ENGINE” with CONSULT-II.
3. Start engine and wait for at least 6 seconds.
4. If DTC is detected, go to AT - 9 8 , "
Diagnostic Procedure" .
WITH GST
Follow the procedure “WITH CONSULT-II”.
BCIA0030E
Page 167 of 3419
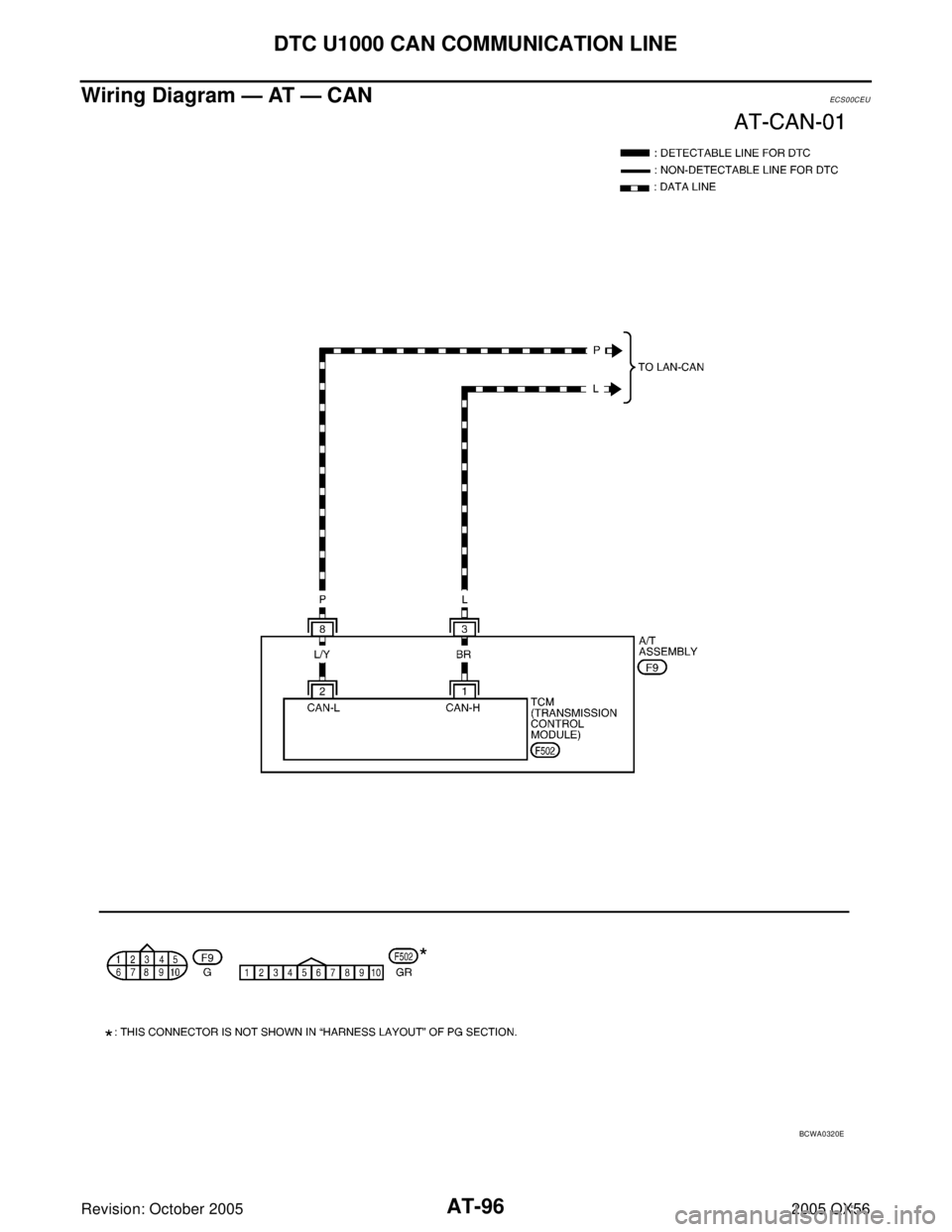
AT-96
DTC U1000 CAN COMMUNICATION LINE
Revision: October 20052005 QX56
Wiring Diagram — AT — CANECS00CEU
BCWA0320E
Page 171 of 3419
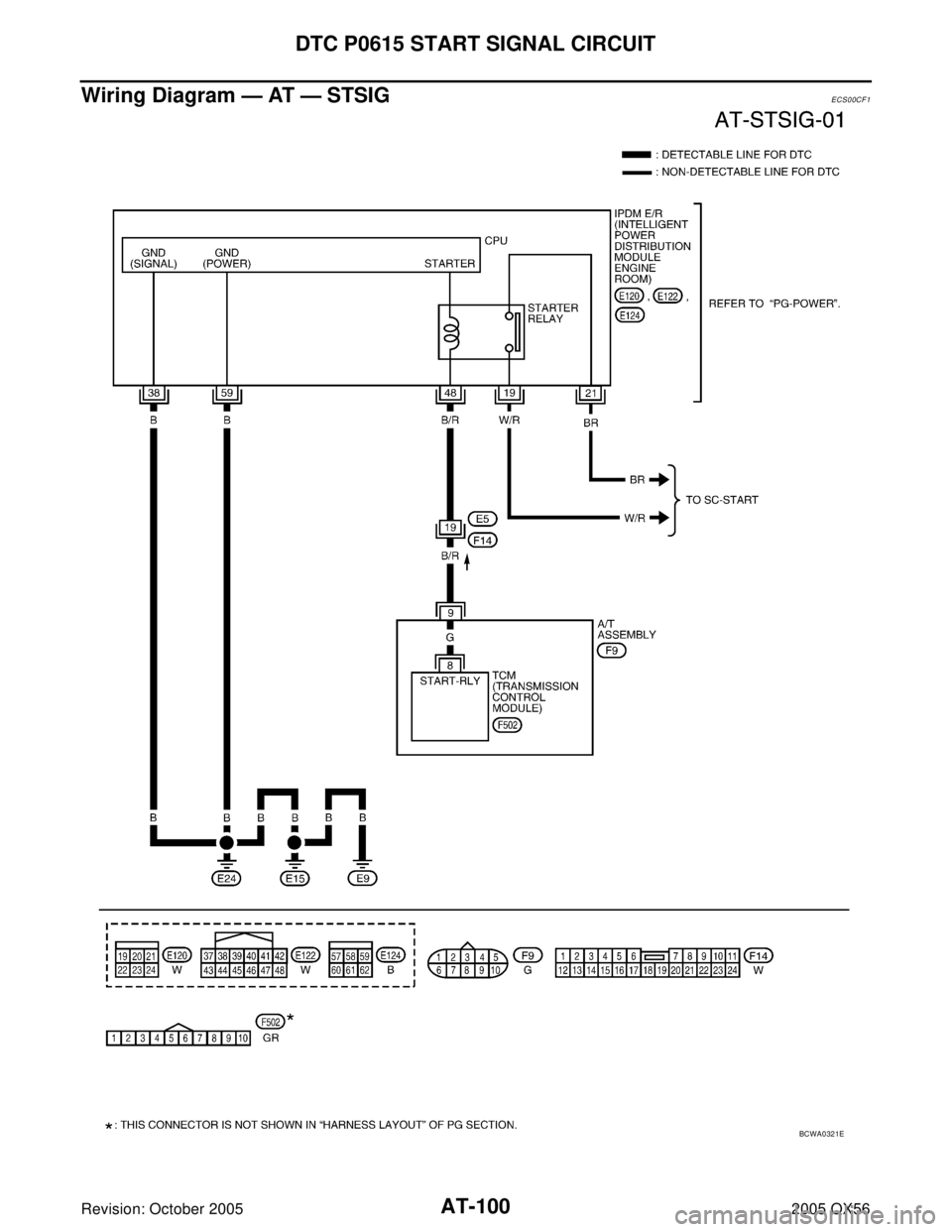
AT-100
DTC P0615 START SIGNAL CIRCUIT
Revision: October 20052005 QX56
Wiring Diagram — AT — STSIGECS00CF1
BCWA0321E
Page 176 of 3419
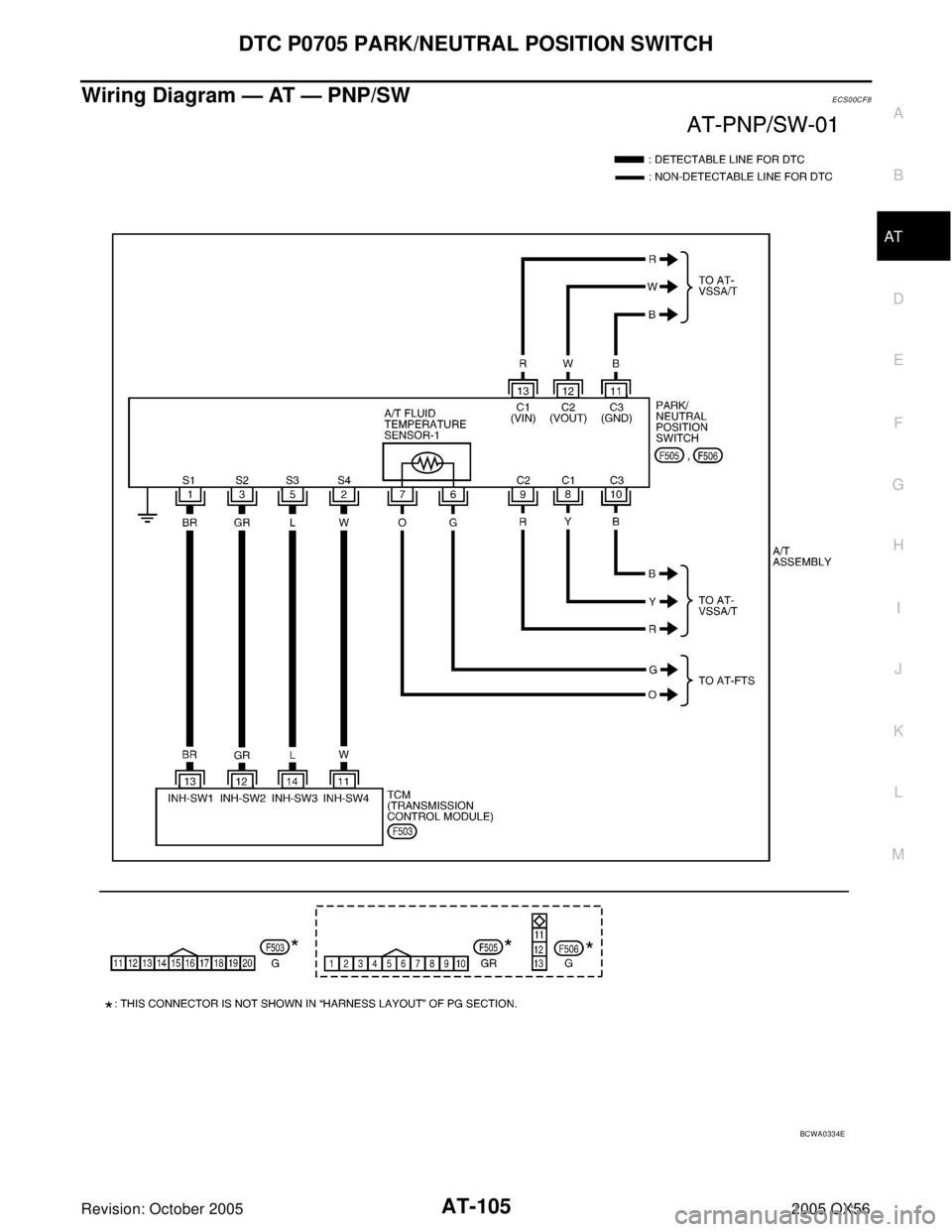
DTC P0705 PARK/NEUTRAL POSITION SWITCH
AT-105
D
E
F
G
H
I
J
K
L
MA
B
AT
Revision: October 20052005 QX56
Wiring Diagram — AT — PNP/SWECS00CF8
BCWA0334E
Page 181 of 3419
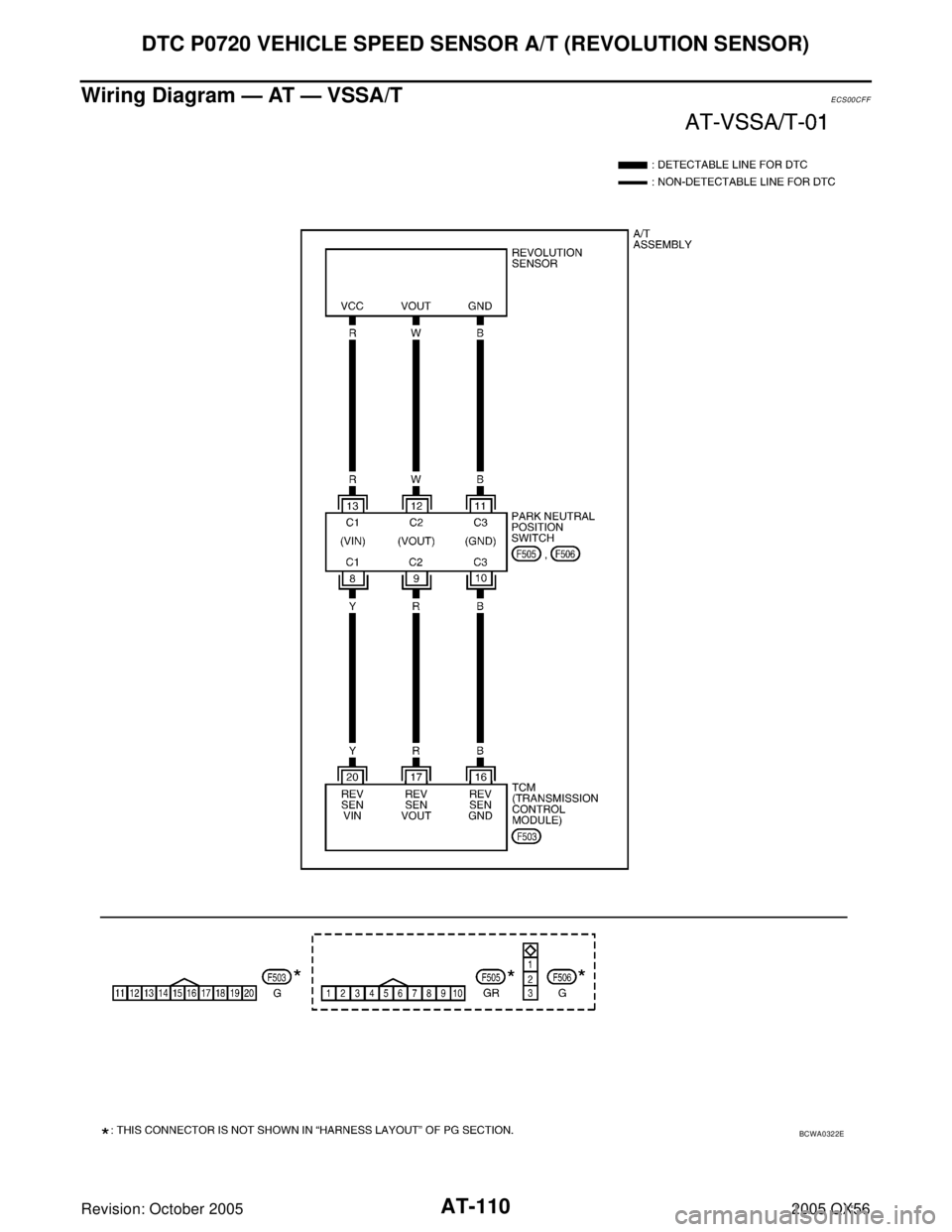
AT-110
DTC P0720 VEHICLE SPEED SENSOR A/T (REVOLUTION SENSOR)
Revision: October 20052005 QX56
Wiring Diagram — AT — VSSA/TECS00CFF
BCWA0322E