height adjustment INFINITI QX56 2007 Factory Service Manual
[x] Cancel search | Manufacturer: INFINITI, Model Year: 2007, Model line: QX56, Model: INFINITI QX56 2007Pages: 3061, PDF Size: 64.56 MB
Page 25 of 3061
![INFINITI QX56 2007 Factory Service Manual ACS-12
< SERVICE INFORMATION >[ICC]
LASER BEAM AIMING ADJUSTMENT
LASER BEAM AIMING ADJUSTMENT
Outline of Laser Beam Aiming Adjustment ProcedureINFOID:0000000003533782
CAUTION:
• The laser beam aimin INFINITI QX56 2007 Factory Service Manual ACS-12
< SERVICE INFORMATION >[ICC]
LASER BEAM AIMING ADJUSTMENT
LASER BEAM AIMING ADJUSTMENT
Outline of Laser Beam Aiming Adjustment ProcedureINFOID:0000000003533782
CAUTION:
• The laser beam aimin](/img/42/57029/w960_57029-24.png)
ACS-12
< SERVICE INFORMATION >[ICC]
LASER BEAM AIMING ADJUSTMENT
LASER BEAM AIMING ADJUSTMENT
Outline of Laser Beam Aiming Adjustment ProcedureINFOID:0000000003533782
CAUTION:
• The laser beam aiming adjustment cannot be performed without CONSULT-II.
• The laser beam aiming adjustment must be performed every time the ICC sensor is removed,
installed or has been moved as a result of a collision.
1. Prepare the vehicle and the work area.
2. Set up the ICC target board. For details, refer to Technical Service Bulletin.
3. Adjust the sensor following the procedure on CONSULT-II.
4. Check system operation after the adjustment.
PreparationINFOID:0000000003533783
• Place the vehicle on level ground. Shift the transmission into "P" position and release the parking brake.
• Adjust the tire pressure to the specified value.
• See that there is no load in the vehicle. Coolant, engine oil and fuel should be filled to correct level.
• Check that the vehicle suspension has been adjusted to the standard height by the load leveling rear air sus-
pension system. Refer to RSU-10, "
Basic Inspection" .
• Clean the sensor with a soft cloth.
Setting up the ICC Target BoardINFOID:0000000003533784
CAUTION:
Accuracy in setting up the ICC target board is essential for the laser beam aiming adjustment. For
details, refer to Technical Service Bulletin.
ADJUSTING HEIGHT OF THE TARGET
1. Attach a triangle scale as shown.Tool number : KV99110100 (J-45718)
LKIA0632E
WKIA1849E
Page 26 of 3061
![INFINITI QX56 2007 Factory Service Manual LASER BEAM AIMING ADJUSTMENT
ACS-13
< SERVICE INFORMATION >[ICC]
C
D
E
F
G
H
I
J
L
MA
B
ACS
N
O
P
2. Adjust the height of the target stand so that the point of the trian-
gle aims above the center of INFINITI QX56 2007 Factory Service Manual LASER BEAM AIMING ADJUSTMENT
ACS-13
< SERVICE INFORMATION >[ICC]
C
D
E
F
G
H
I
J
L
MA
B
ACS
N
O
P
2. Adjust the height of the target stand so that the point of the trian-
gle aims above the center of](/img/42/57029/w960_57029-25.png)
LASER BEAM AIMING ADJUSTMENT
ACS-13
< SERVICE INFORMATION >[ICC]
C
D
E
F
G
H
I
J
L
MA
B
ACS
N
O
P
2. Adjust the height of the target stand so that the point of the trian-
gle aims above the center of the ICC sensor.
ADJUSTING THE POSITION OF THE TARGET BOARD STRING
1. Attach a scale or straightedge (at least 350 mm [14 in] or
longer).
2. Suspend a string with a weight on the end 218 mm
(8.6 in) to the left side of the target board center.
POSITIONING THE TARGET
1. Suspend a string with weights on each end over the centerline of the vehicle. The string should lay over
the center of the front and back bumpers. Mark these centerpoints on the ground at each weight.
2. Connect the two center points using a string. Extend the string
an additional 5 m (16 ft) beyond the front centerpoint and mark
the floor. Position the target board weight on this mark.
3. Relocate the suspended string from the left side of the target board to the center of the target board. Mark
this point on the ground.
WKIA2039E
SKIA1211E
WKIA2040E
WKIA1851E
Page 722 of 3061
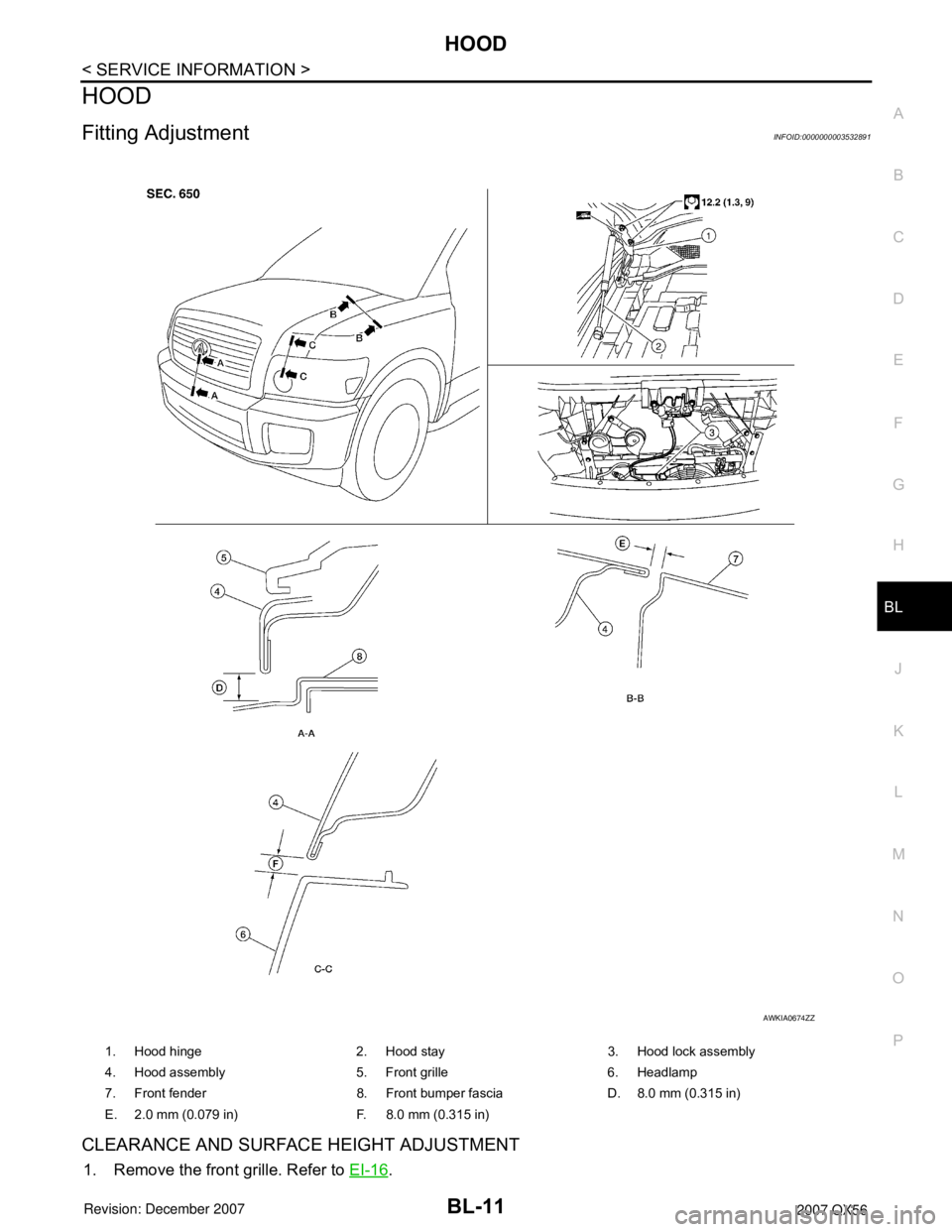
HOOD
BL-11
< SERVICE INFORMATION >
C
D
E
F
G
H
J
K
L
MA
B
BL
N
O
P
HOOD
Fitting AdjustmentINFOID:0000000003532891
CLEARANCE AND SURFACE HEIGHT ADJUSTMENT
1. Remove the front grille. Refer to EI-16.
1. Hood hinge 2. Hood stay 3. Hood lock assembly
4. Hood assembly 5. Front grille 6. Headlamp
7. Front fender 8. Front bumper fascia D. 8.0 mm (0.315 in)
E. 2.0 mm (0.079 in) F. 8.0 mm (0.315 in)
AWKIA0674ZZ
Page 723 of 3061
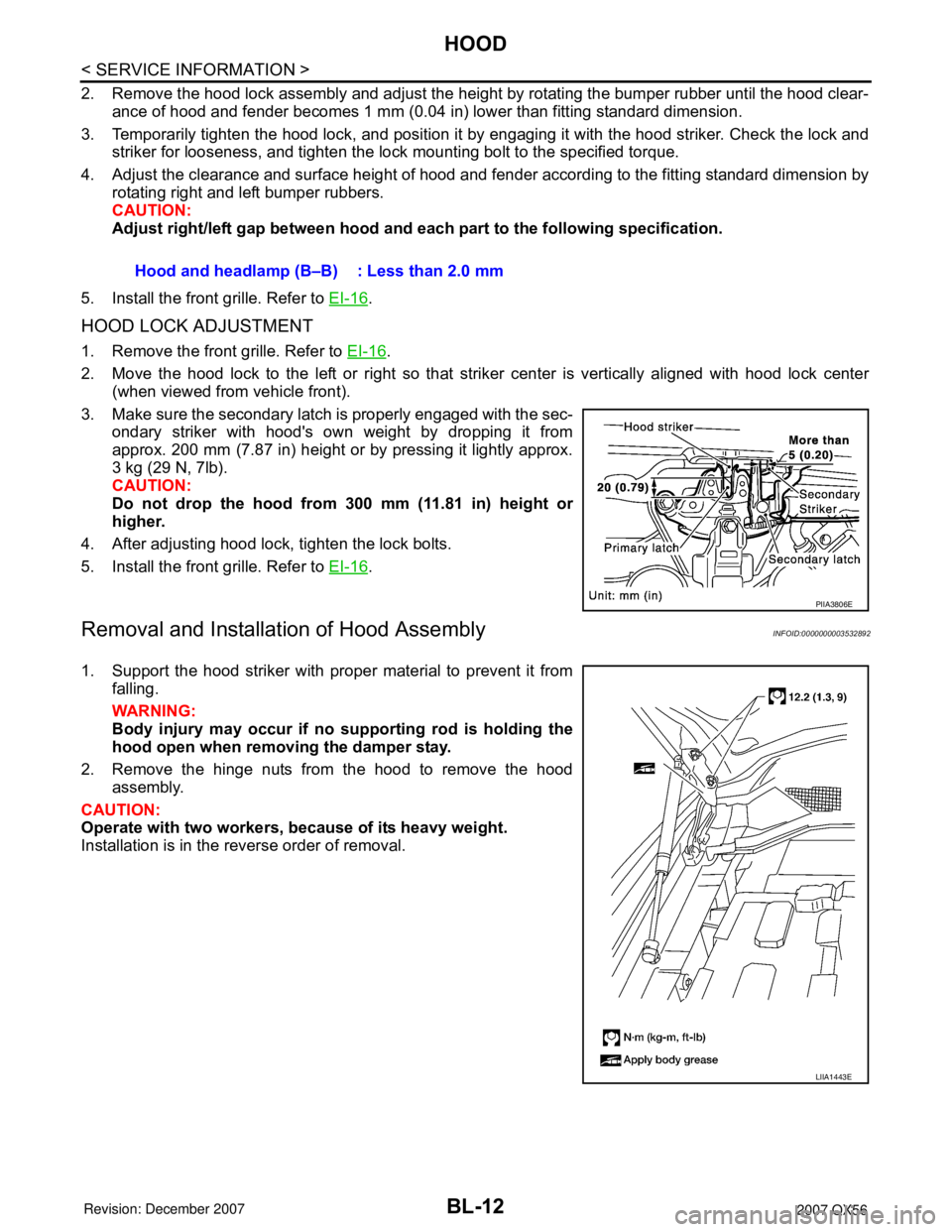
BL-12
< SERVICE INFORMATION >
HOOD
2. Remove the hood lock assembly and adjust the height by rotating the bumper rubber until the hood clear-
ance of hood and fender becomes 1 mm (0.04 in) lower than fitting standard dimension.
3. Temporarily tighten the hood lock, and position it by engaging it with the hood striker. Check the lock and
striker for looseness, and tighten the lock mounting bolt to the specified torque.
4. Adjust the clearance and surface height of hood and fender according to the fitting standard dimension by
rotating right and left bumper rubbers.
CAUTION:
Adjust right/left gap between hood and each part to the following specification.
5. Install the front grille. Refer to EI-16
.
HOOD LOCK ADJUSTMENT
1. Remove the front grille. Refer to EI-16.
2. Move the hood lock to the left or right so that striker center is vertically aligned with hood lock center
(when viewed from vehicle front).
3. Make sure the secondary latch is properly engaged with the sec-
ondary striker with hood's own weight by dropping it from
approx. 200 mm (7.87 in) height or by pressing it lightly approx.
3 kg (29 N, 7lb).
CAUTION:
Do not drop the hood from 300 mm (11.81 in) height or
higher.
4. After adjusting hood lock, tighten the lock bolts.
5. Install the front grille. Refer to EI-16
.
Removal and Installation of Hood AssemblyINFOID:0000000003532892
1. Support the hood striker with proper material to prevent it from
falling.
WARNING:
Body injury may occur if no supporting rod is holding the
hood open when removing the damper stay.
2. Remove the hinge nuts from the hood to remove the hood
assembly.
CAUTION:
Operate with two workers, because of its heavy weight.
Installation is in the reverse order of removal.Hood and headlamp (B–B) : Less than 2.0 mm
PIIA3806E
LIIA1443E
Page 725 of 3061
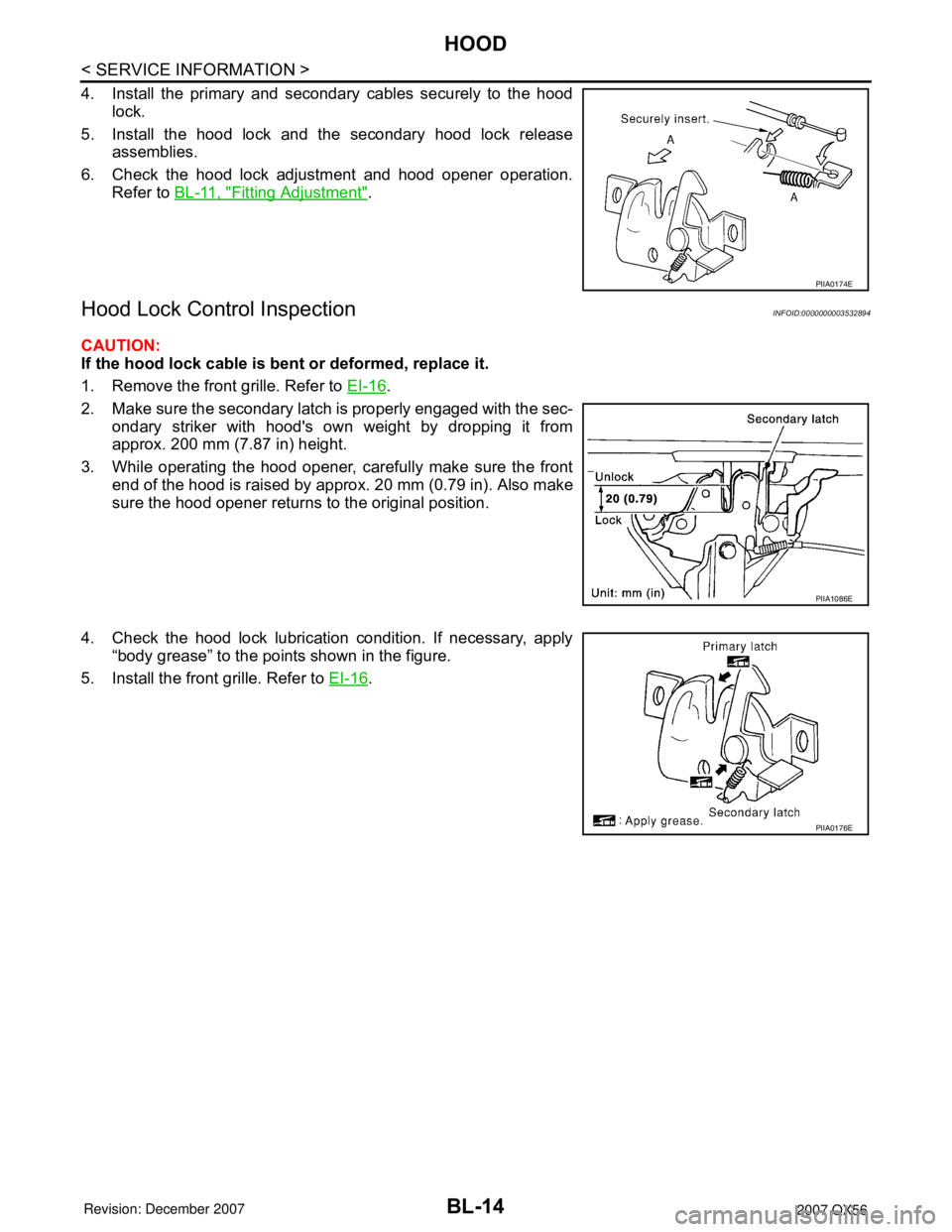
BL-14
< SERVICE INFORMATION >
HOOD
4. Install the primary and secondary cables securely to the hood
lock.
5. Install the hood lock and the secondary hood lock release
assemblies.
6. Check the hood lock adjustment and hood opener operation.
Refer to BL-11, "
Fitting Adjustment".
Hood Lock Control InspectionINFOID:0000000003532894
CAUTION:
If the hood lock cable is bent or deformed, replace it.
1. Remove the front grille. Refer to EI-16
.
2. Make sure the secondary latch is properly engaged with the sec-
ondary striker with hood's own weight by dropping it from
approx. 200 mm (7.87 in) height.
3. While operating the hood opener, carefully make sure the front
end of the hood is raised by approx. 20 mm (0.79 in). Also make
sure the hood opener returns to the original position.
4. Check the hood lock lubrication condition. If necessary, apply
“body grease” to the points shown in the figure.
5. Install the front grille. Refer to EI-16
.
PIIA0174E
PIIA1086E
PIIA0176E
Page 817 of 3061

BL-106
< SERVICE INFORMATION >
DOOR
DOOR
Fitting AdjustmentINFOID:0000000003532977
Front door
Longitudinal clearance and surface height adjustment at front end
1. Remove the fender. Refer to EI-19.
2. Loosen the hinge bolts. Raise the front door at rear end to adjust.
3. Install the fender. Refer to EI-19
.
Rear door
Longitudinal clearance and surface height adjustment at front end
1. Loosen the bolts. Open the rear door, and raise the rear door at rear end to adjust.
Striker adjustment
D. 4.5 ± 1.0 mm (0.177 ± 0.039 in)
AWKIA0675ZZ
Page 903 of 3061
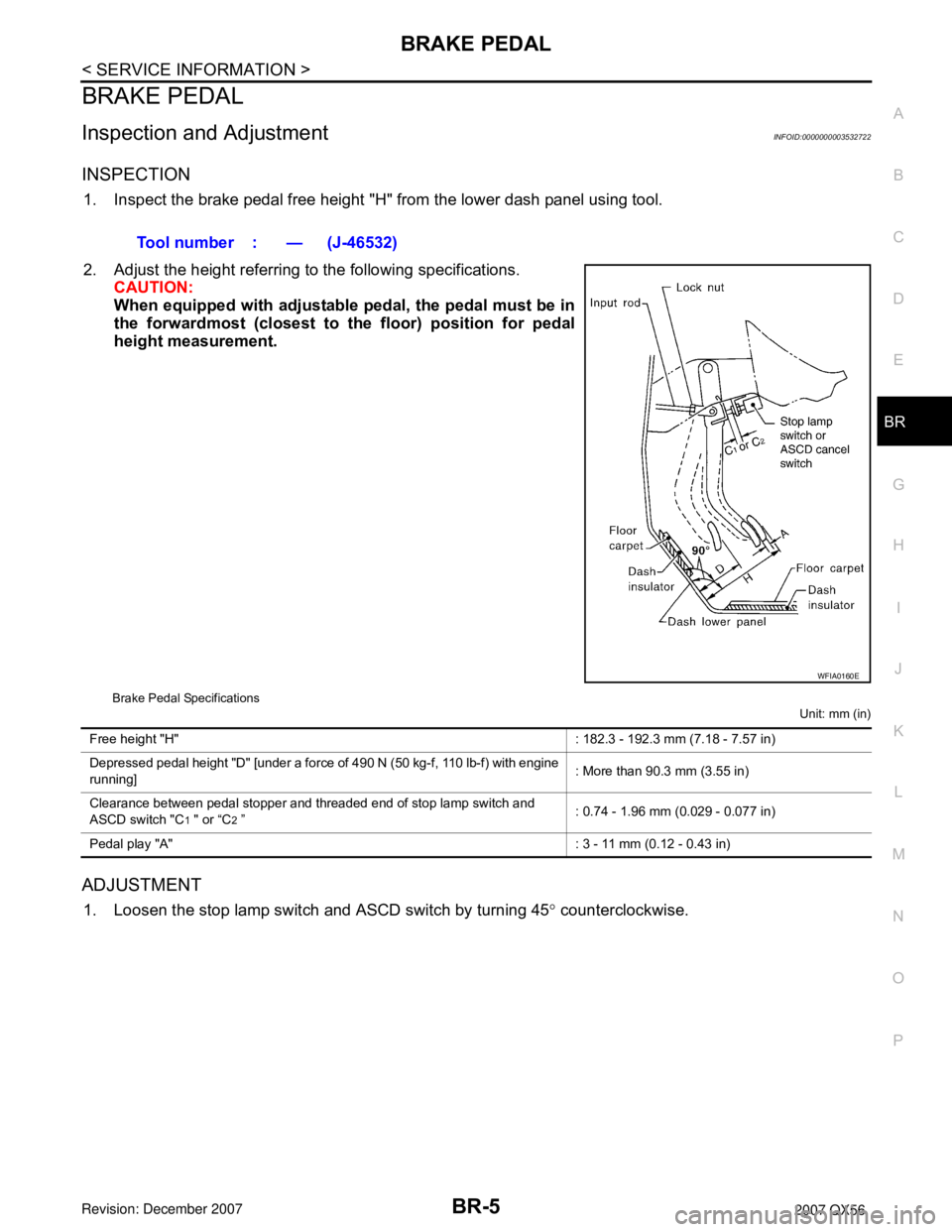
BRAKE PEDAL
BR-5
< SERVICE INFORMATION >
C
D
E
G
H
I
J
K
L
MA
B
BR
N
O
P
BRAKE PEDAL
Inspection and AdjustmentINFOID:0000000003532722
INSPECTION
1. Inspect the brake pedal free height "H" from the lower dash panel using tool.
2. Adjust the height referring to the following specifications.
CAUTION:
When equipped with adjustable pedal, the pedal must be in
the forwardmost (closest to the floor) position for pedal
height measurement.
Brake Pedal Specifications
Unit: mm (in)
ADJUSTMENT
1. Loosen the stop lamp switch and ASCD switch by turning 45° counterclockwise. Tool number : — (J-46532)
WFIA0160E
Free height "H" : 182.3 - 192.3 mm (7.18 - 7.57 in)
Depressed pedal height "D" [under a force of 490 N (50 kg-f, 110 lb-f) with engine
running]: More than 90.3 mm (3.55 in)
Clearance between pedal stopper and threaded end of stop lamp switch and
ASCD switch "C
1 " or “C2 ”: 0.74 - 1.96 mm (0.029 - 0.077 in)
Pedal play "A" : 3 - 11 mm (0.12 - 0.43 in)
Page 1679 of 3061
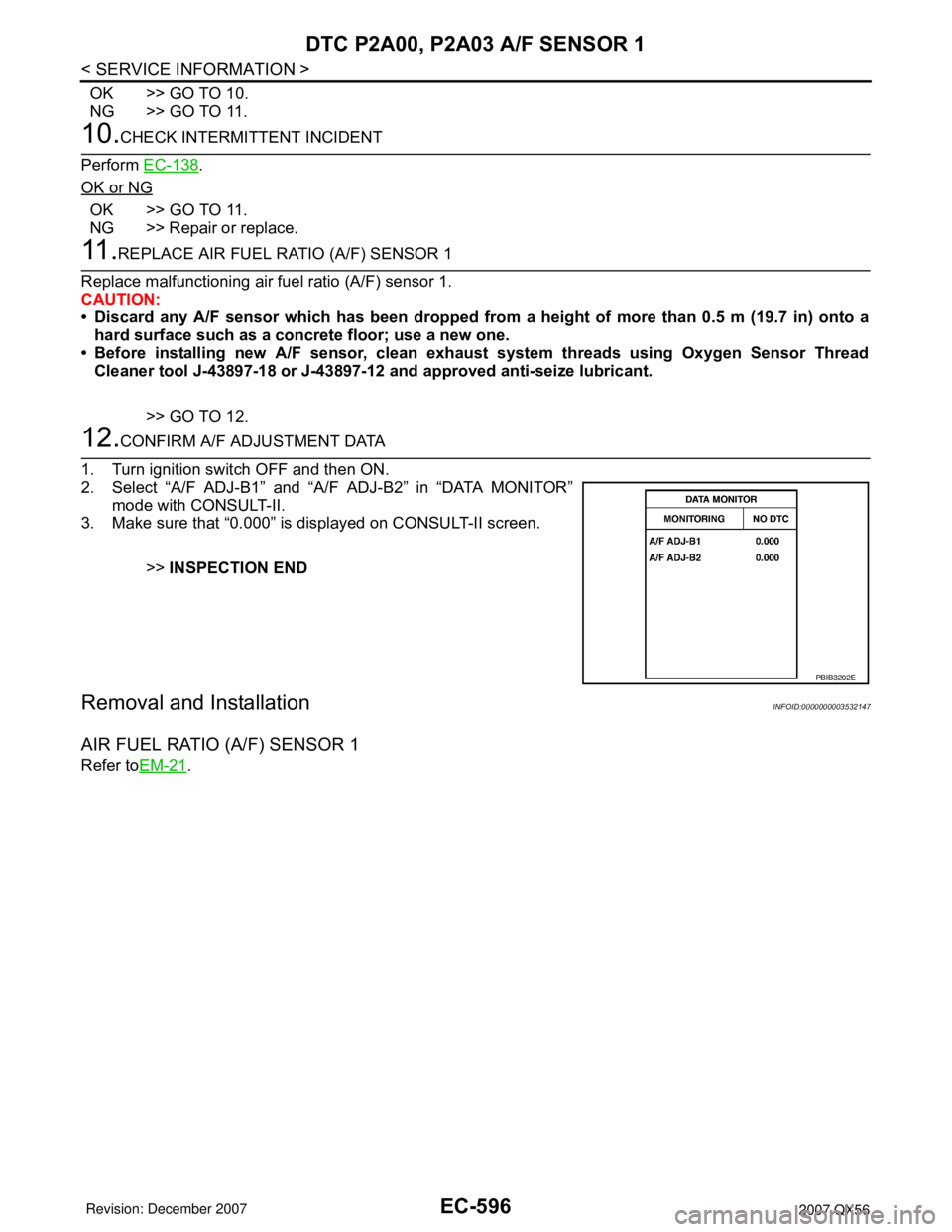
EC-596
< SERVICE INFORMATION >
DTC P2A00, P2A03 A/F SENSOR 1
OK >> GO TO 10.
NG >> GO TO 11.
10.CHECK INTERMITTENT INCIDENT
Perform EC-138
.
OK or NG
OK >> GO TO 11.
NG >> Repair or replace.
11 .REPLACE AIR FUEL RATIO (A/F) SENSOR 1
Replace malfunctioning air fuel ratio (A/F) sensor 1.
CAUTION:
• Discard any A/F sensor which has been dropped from a height of more than 0.5 m (19.7 in) onto a
hard surface such as a concrete floor; use a new one.
• Before installing new A/F sensor, clean exhaust system threads using Oxygen Sensor Thread
Cleaner tool J-43897-18 or J-43897-12 and approved anti-seize lubricant.
>> GO TO 12.
12.CONFIRM A/F ADJUSTMENT DATA
1. Turn ignition switch OFF and then ON.
2. Select “A/F ADJ-B1” and “A/F ADJ-B2” in “DATA MONITOR”
mode with CONSULT-II.
3. Make sure that “0.000” is displayed on CONSULT-II screen.
>>INSPECTION END
Removal and InstallationINFOID:0000000003532147
AIR FUEL RATIO (A/F) SENSOR 1
Refer toEM-21.
PBIB3202E
Page 1913 of 3061
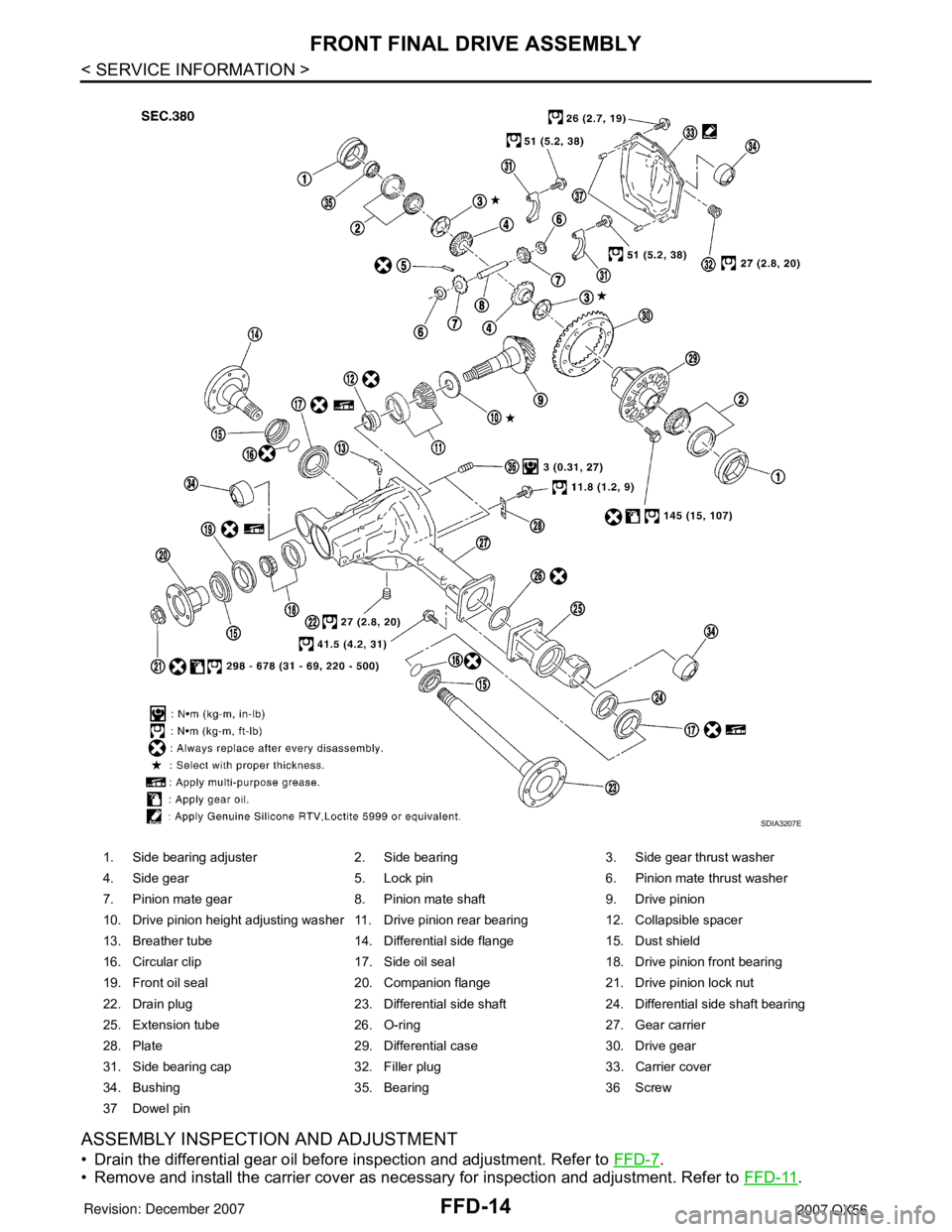
FFD-14
< SERVICE INFORMATION >
FRONT FINAL DRIVE ASSEMBLY
ASSEMBLY INSPECTION AND ADJUSTMENT
• Drain the differential gear oil before inspection and adjustment. Refer to FFD-7.
• Remove and install the carrier cover as necessary for inspection and adjustment. Refer to FFD-11
.
1. Side bearing adjuster 2. Side bearing 3. Side gear thrust washer
4. Side gear 5. Lock pin 6. Pinion mate thrust washer
7. Pinion mate gear 8. Pinion mate shaft 9. Drive pinion
10. Drive pinion height adjusting washer 11. Drive pinion rear bearing 12. Collapsible spacer
13. Breather tube 14. Differential side flange 15. Dust shield
16. Circular clip 17. Side oil seal 18. Drive pinion front bearing
19. Front oil seal 20. Companion flange 21. Drive pinion lock nut
22. Drain plug 23. Differential side shaft 24. Differential side shaft bearing
25. Extension tube 26. O-ring 27. Gear carrier
28. Plate 29. Differential case 30. Drive gear
31. Side bearing cap 32. Filler plug 33. Carrier cover
34. Bushing 35. Bearing 36 Screw
37 Dowel pin
SDIA3207E
Page 1915 of 3061
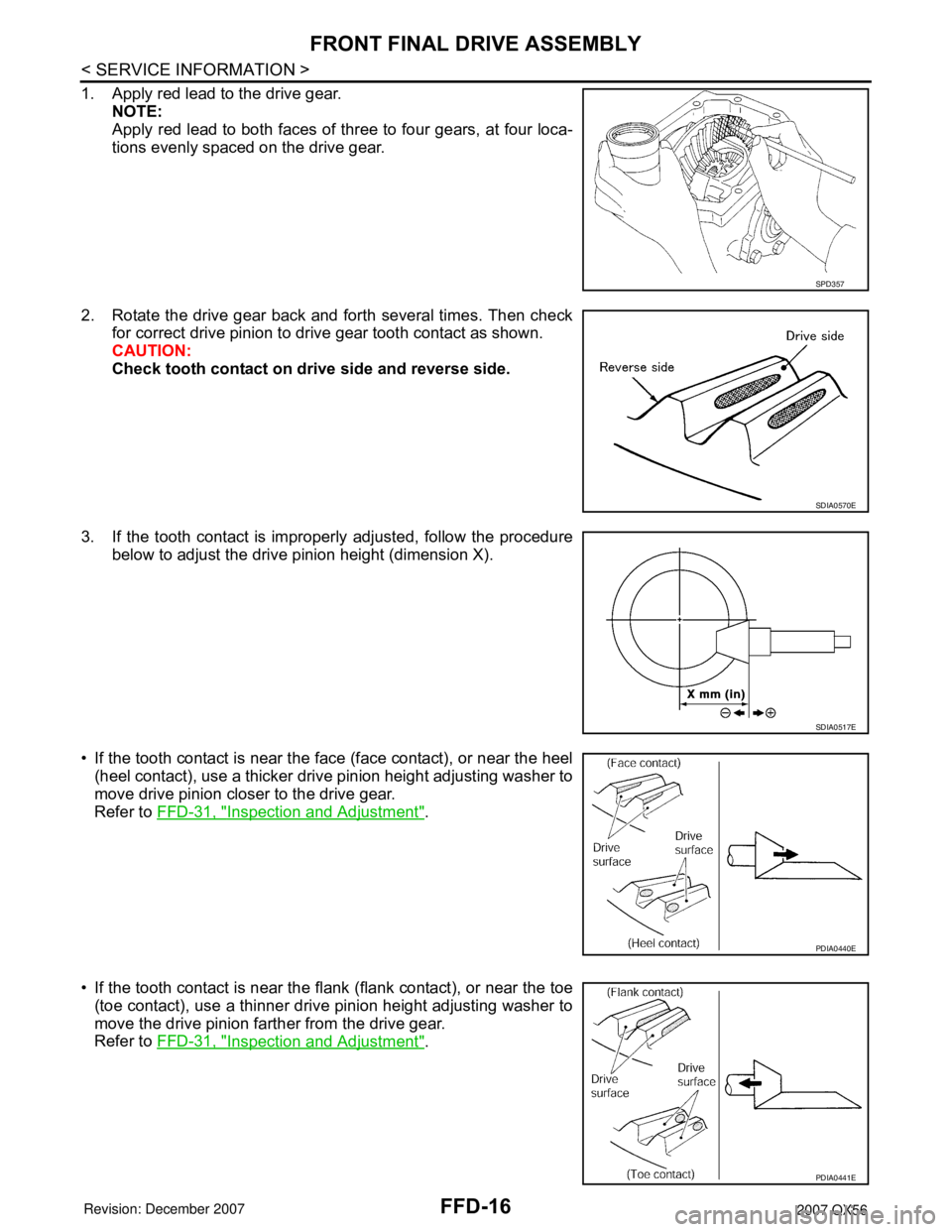
FFD-16
< SERVICE INFORMATION >
FRONT FINAL DRIVE ASSEMBLY
1. Apply red lead to the drive gear.
NOTE:
Apply red lead to both faces of three to four gears, at four loca-
tions evenly spaced on the drive gear.
2. Rotate the drive gear back and forth several times. Then check
for correct drive pinion to drive gear tooth contact as shown.
CAUTION:
Check tooth contact on drive side and reverse side.
3. If the tooth contact is improperly adjusted, follow the procedure
below to adjust the drive pinion height (dimension X).
• If the tooth contact is near the face (face contact), or near the heel
(heel contact), use a thicker drive pinion height adjusting washer to
move drive pinion closer to the drive gear.
Refer to FFD-31, "
Inspection and Adjustment".
• If the tooth contact is near the flank (flank contact), or near the toe
(toe contact), use a thinner drive pinion height adjusting washer to
move the drive pinion farther from the drive gear.
Refer to FFD-31, "
Inspection and Adjustment".
SPD357
SDIA0570E
SDIA0517E
PDIA0440E
PDIA0441E