engine oil INFINITI QX56 2007 Factory Service Manual
[x] Cancel search | Manufacturer: INFINITI, Model Year: 2007, Model line: QX56, Model: INFINITI QX56 2007Pages: 3061, PDF Size: 64.56 MB
Page 4 of 3061

QUICK REFERENCE CHART: QX562007
QUICK REFERENCE CHART: QX56PFP:00000
Engine Tune-Up DataELS0028Z
Cylinder arrangementV-8
Displacement cm
3 (cu in) 5,552 (338.80)
Bore and stroke mm (in) 98 x 92 (3.86 x 3.62)
Valve arrangement DOHC
Firing order 1-8-7-3-6-5-4-2
Number of piston rings Compression 2
Oil 1
Number of main bearings 5
Compression ratio 9.8:1
Compression pressure
kPa (kg/cm
2 , psi)/rpm Standard 1,520 (15.5, 220)/200
Minimum 1,324 (13.5, 192)/200
Differential limit between cylinders 98 (1.0, 14)/200
Cylinder number
Va l v e t i m i n g Unit: degree
abcde f
244 ° 232° -8° 60° 10° 54°
SEM957C
PBIC0187E
Page 5 of 3061
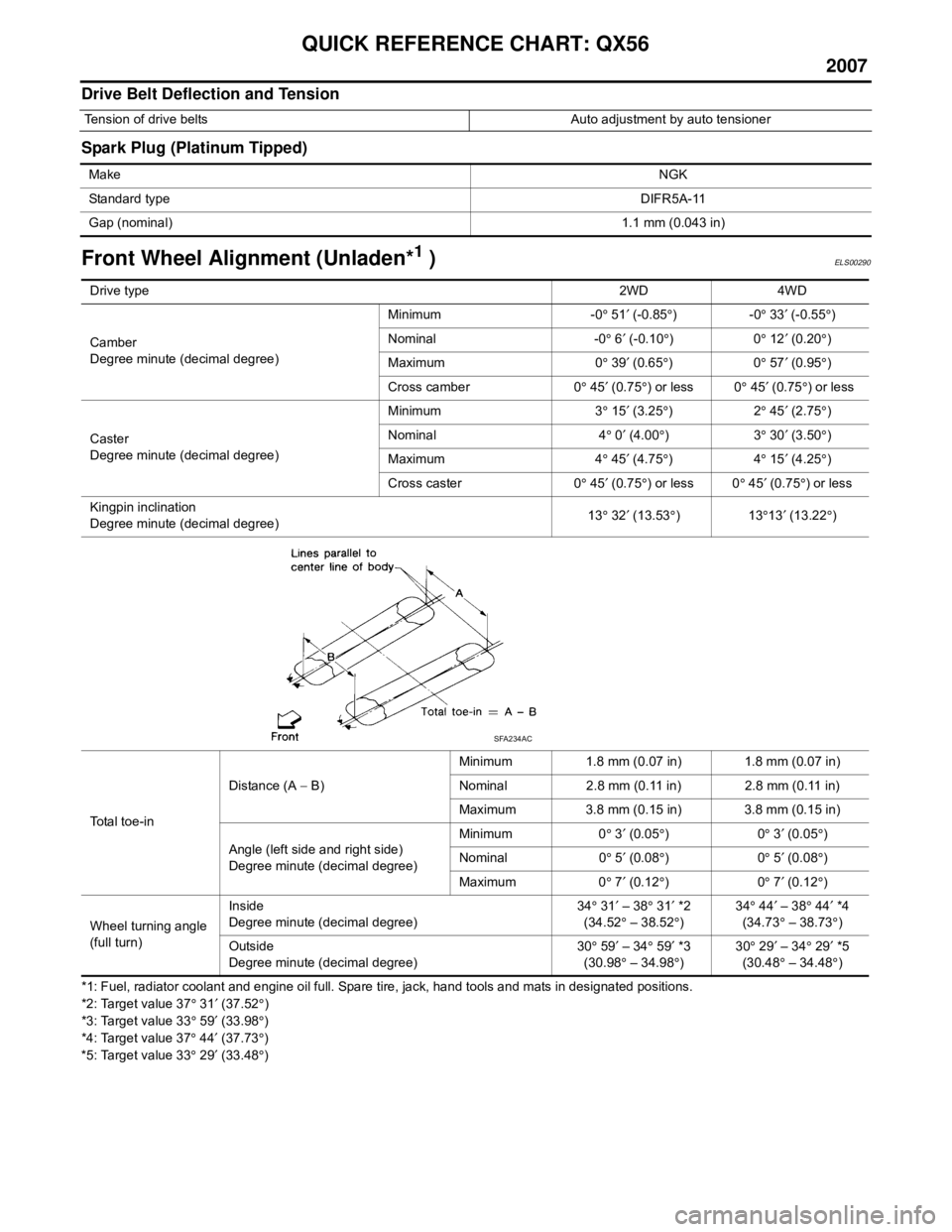
2007
QUICK REFERENCE CHART: QX56
Drive Belt Deflection and Tension
Spark Plug (Platinum Tipped)
Front Wheel Alignment (Unladen*1 )ELS00290
*1: Fuel, radiator coolant and engine oil full. Spare tire, jack, hand tools and mats in designated positions.
*2: Target value 37° 31 ′ (37.52 °)
*3: Target value 33 ° 59 ′ (33.98 °)
*4: Target value 37 ° 44 ′ (37.73 °)
*5: Target value 33 ° 29 ′ (33.48 °)
Tension of drive belts Auto adjustment by auto tensioner
Make NGK
Standard type DIFR5A-11
Gap (nominal) 1.1 mm (0.043 in)
Drive type2WD 4WD
Camber
Degree minute (decimal degree) Minimum -0
° 51 ′ (-0.85 °)-0 ° 33 ′ (-0.55 °)
Nominal -0 ° 6 ′ (-0.10 °)0 ° 12 ′ (0.20 °)
Maximum 0 ° 39 ′ (0.65 °)0 ° 57 ′ (0.95 °)
Cross camber 0 ° 45 ′ (0.75 °) or less 0 ° 45 ′ (0.75 °) or less
Caster
Degree minute (decimal degree) Minimum 3
° 15 ′ (3.25 °)2 ° 45 ′ (2.75 °)
Nominal 4 ° 0 ′ (4.00 °)3 ° 30 ′ (3.50 °)
Maximum 4 ° 45 ′ (4.75 °)4 ° 15 ′ (4.25 °)
Cross caster 0 ° 45 ′ (0.75 °) or less 0 ° 45 ′ (0.75 °) or less
Kingpin inclination
Degree minute (decimal degree) 13
° 32 ′ (13.53 °)13 °13 ′ (13.22 °)
Total toe-in Distance (A
− B) Minimum 1.8 mm (0.07 in) 1.8 mm (0.07 in)
Nominal 2.8 mm (0.11 in) 2.8 mm (0.11 in)
Maximum 3.8 mm (0.15 in) 3.8 mm (0.15 in)
Angle (left side and right side)
Degree minute (decimal degree) Minimum 0
° 3 ′ (0.05 °)0 ° 3 ′ (0.05 °)
Nominal 0 ° 5 ′ (0.08 °)0 ° 5 ′ (0.08 °)
Maximum 0 ° 7 ′ (0.12 °)0 ° 7 ′ (0.12 °)
Wheel turning angle
(full turn) Inside
Degree minute (decimal degree)
34
° 31 ′ – 38 ° 31 ′ *2
(34.52 ° – 38.52 °) 34
° 44 ′ – 38 ° 44 ′ *4
(34.73 ° – 38.73 °)
Outside
Degree minute (decimal degree) 30
° 59 ′ – 34 ° 59 ′ *3
(30.98 ° – 34.98 °) 30
° 29 ′ – 34 ° 29 ′ *5
(30.48 ° – 34.48 °)
SFA234AC
Page 8 of 3061
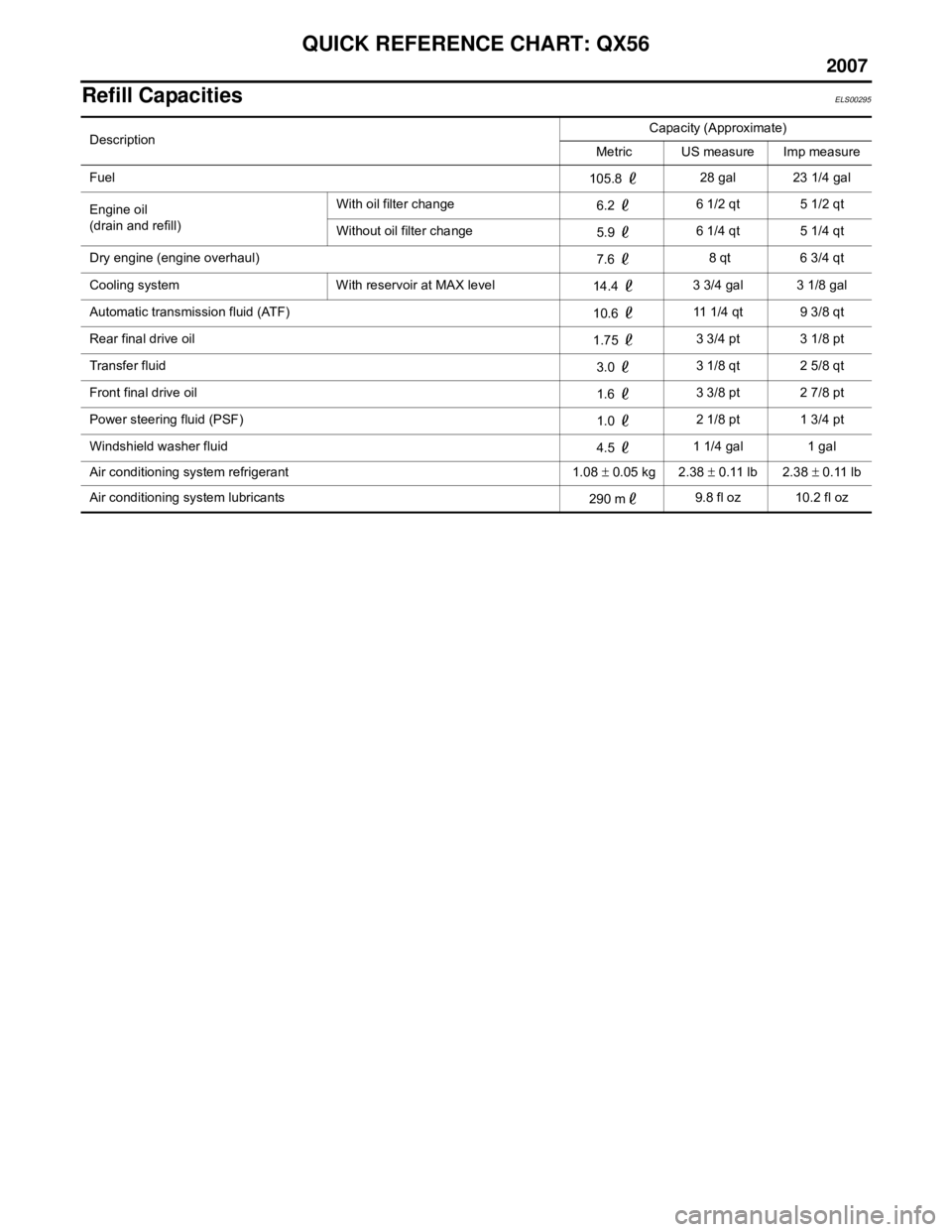
QUICK REFERENCE CHART: QX56
2007
Refill CapacitiesELS00295
DescriptionCapacity (Approximate)
Metric US measure Imp measure
Fuel 105.8 28 gal 23 1/4 gal
Engine oil
(drain and refill) With oil filter change
6.2 6 1/2 qt 5 1/2 qt
Without oil filter change 5.9 6 1/4 qt 5 1/4 qt
Dry engine (engine overhaul) 7.6 8 qt 6 3/4 qt
Cooling system With reservoir at MAX level 14.4 3 3/4 gal 3 1/8 gal
Automatic transmission fluid (ATF) 10.6 11 1/4 qt 9 3/8 qt
Rear final drive oil 1.75 3 3/4 pt 3 1/8 pt
Transfer fluid 3.0 3 1/8 qt 2 5/8 qt
Front final drive oil 1.6 3 3/8 pt 2 7/8 pt
Power steering fluid (PSF) 1.0 2 1/8 pt 1 3/4 pt
Windshield washer fluid 4.5 1 1/4 gal 1 gal
Air conditioning system refrigerant 1.08 ± 0.05 kg 2.38 ± 0.11 lb 2.38 ± 0.11 lb
Air conditioning system lubricants 290 m9.8 fl oz 10.2 fl oz
Page 25 of 3061
![INFINITI QX56 2007 Factory Service Manual ACS-12
< SERVICE INFORMATION >[ICC]
LASER BEAM AIMING ADJUSTMENT
LASER BEAM AIMING ADJUSTMENT
Outline of Laser Beam Aiming Adjustment ProcedureINFOID:0000000003533782
CAUTION:
• The laser beam aimin INFINITI QX56 2007 Factory Service Manual ACS-12
< SERVICE INFORMATION >[ICC]
LASER BEAM AIMING ADJUSTMENT
LASER BEAM AIMING ADJUSTMENT
Outline of Laser Beam Aiming Adjustment ProcedureINFOID:0000000003533782
CAUTION:
• The laser beam aimin](/img/42/57029/w960_57029-24.png)
ACS-12
< SERVICE INFORMATION >[ICC]
LASER BEAM AIMING ADJUSTMENT
LASER BEAM AIMING ADJUSTMENT
Outline of Laser Beam Aiming Adjustment ProcedureINFOID:0000000003533782
CAUTION:
• The laser beam aiming adjustment cannot be performed without CONSULT-II.
• The laser beam aiming adjustment must be performed every time the ICC sensor is removed,
installed or has been moved as a result of a collision.
1. Prepare the vehicle and the work area.
2. Set up the ICC target board. For details, refer to Technical Service Bulletin.
3. Adjust the sensor following the procedure on CONSULT-II.
4. Check system operation after the adjustment.
PreparationINFOID:0000000003533783
• Place the vehicle on level ground. Shift the transmission into "P" position and release the parking brake.
• Adjust the tire pressure to the specified value.
• See that there is no load in the vehicle. Coolant, engine oil and fuel should be filled to correct level.
• Check that the vehicle suspension has been adjusted to the standard height by the load leveling rear air sus-
pension system. Refer to RSU-10, "
Basic Inspection" .
• Clean the sensor with a soft cloth.
Setting up the ICC Target BoardINFOID:0000000003533784
CAUTION:
Accuracy in setting up the ICC target board is essential for the laser beam aiming adjustment. For
details, refer to Technical Service Bulletin.
ADJUSTING HEIGHT OF THE TARGET
1. Attach a triangle scale as shown.Tool number : KV99110100 (J-45718)
LKIA0632E
WKIA1849E
Page 74 of 3061
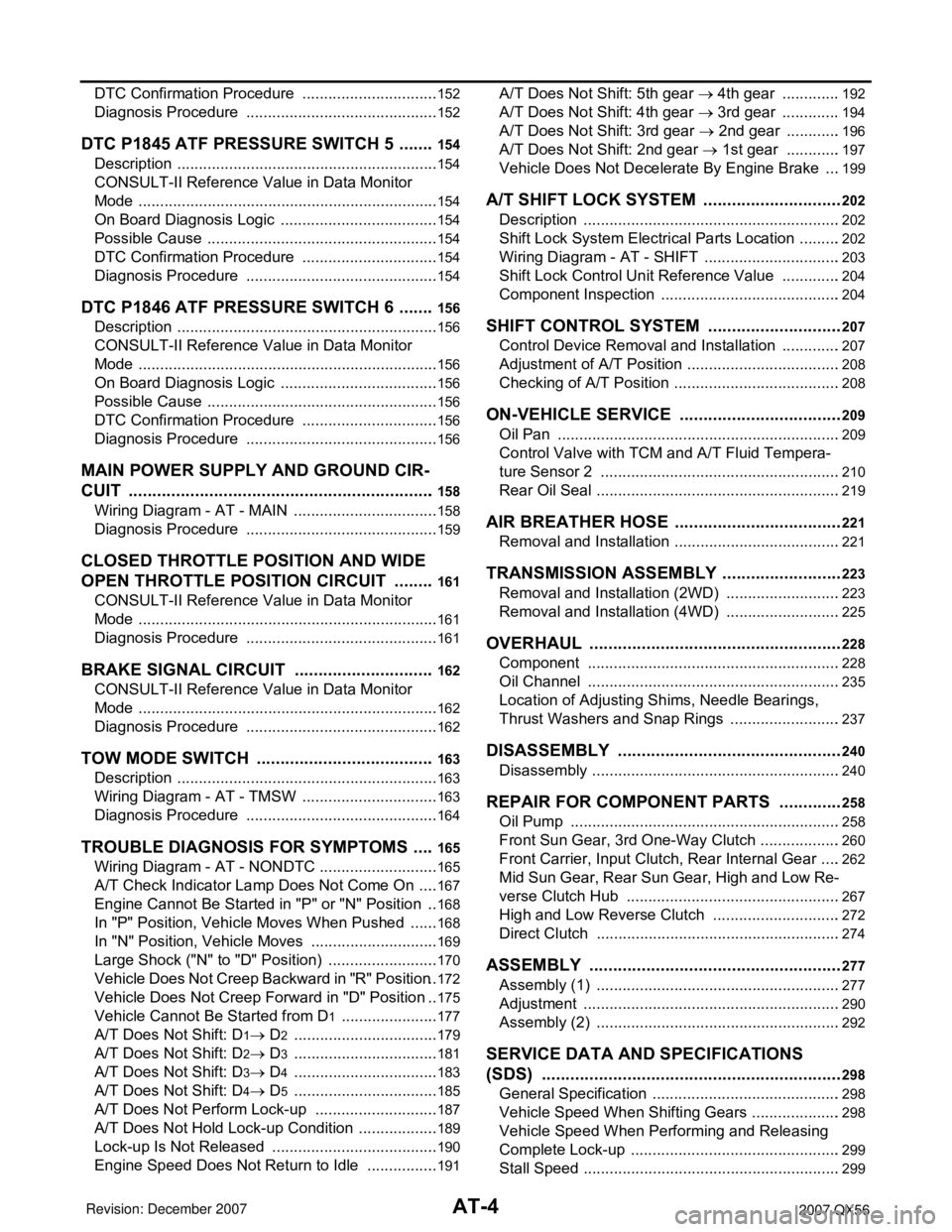
AT-4
DTC Confirmation Procedure ................................152
Diagnosis Procedure .............................................152
DTC P1845 ATF PRESSURE SWITCH 5 ........154
Description .............................................................154
CONSULT-II Reference Value in Data Monitor
Mode ......................................................................
154
On Board Diagnosis Logic .....................................154
Possible Cause ......................................................154
DTC Confirmation Procedure ................................154
Diagnosis Procedure .............................................154
DTC P1846 ATF PRESSURE SWITCH 6 ........156
Description .............................................................156
CONSULT-II Reference Value in Data Monitor
Mode ......................................................................
156
On Board Diagnosis Logic .....................................156
Possible Cause ......................................................156
DTC Confirmation Procedure ................................156
Diagnosis Procedure .............................................156
MAIN POWER SUPPLY AND GROUND CIR-
CUIT .................................................................
158
Wiring Diagram - AT - MAIN ..................................158
Diagnosis Procedure .............................................159
CLOSED THROTTLE POSITION AND WIDE
OPEN THROTTLE POSITION CIRCUIT .........
161
CONSULT-II Reference Value in Data Monitor
Mode ......................................................................
161
Diagnosis Procedure .............................................161
BRAKE SIGNAL CIRCUIT ..............................162
CONSULT-II Reference Value in Data Monitor
Mode ......................................................................
162
Diagnosis Procedure .............................................162
TOW MODE SWITCH ......................................163
Description .............................................................163
Wiring Diagram - AT - TMSW ................................163
Diagnosis Procedure .............................................164
TROUBLE DIAGNOSIS FOR SYMPTOMS .....165
Wiring Diagram - AT - NONDTC ............................165
A/T Check Indicator Lamp Does Not Come On .....167
Engine Cannot Be Started in "P" or "N" Position ...168
In "P" Position, Vehicle Moves When Pushed .......168
In "N" Position, Vehicle Moves ..............................169
Large Shock ("N" to "D" Position) ..........................170
Vehicle Does Not Creep Backward in "R" Position ..172
Vehicle Does Not Creep Forward in "D" Position ..175
Vehicle Cannot Be Started from D1 .......................177
A/T Does Not Shift: D1→ D2 ..................................179
A/T Does Not Shift: D2→ D3 ..................................181
A/T Does Not Shift: D3→ D4 ..................................183
A/T Does Not Shift: D4→ D5 ..................................185
A/T Does Not Perform Lock-up .............................187
A/T Does Not Hold Lock-up Condition ...................189
Lock-up Is Not Released .......................................190
Engine Speed Does Not Return to Idle .................191
A/T Does Not Shift: 5th gear → 4th gear ..............192
A/T Does Not Shift: 4th gear → 3rd gear ..............194
A/T Does Not Shift: 3rd gear → 2nd gear .............196
A/T Does Not Shift: 2nd gear → 1st gear .............197
Vehicle Does Not Decelerate By Engine Brake ....199
A/T SHIFT LOCK SYSTEM ..............................202
Description ............................................................202
Shift Lock System Electrical Parts Location ..........202
Wiring Diagram - AT - SHIFT ................................203
Shift Lock Control Unit Reference Value ..............204
Component Inspection ..........................................204
SHIFT CONTROL SYSTEM .............................207
Control Device Removal and Installation ..............207
Adjustment of A/T Position ....................................208
Checking of A/T Position .......................................208
ON-VEHICLE SERVICE ...................................209
Oil Pan ..................................................................209
Control Valve with TCM and A/T Fluid Tempera-
ture Sensor 2 ........................................................
210
Rear Oil Seal .........................................................219
AIR BREATHER HOSE ....................................221
Removal and Installation .......................................221
TRANSMISSION ASSEMBLY ..........................223
Removal and Installation (2WD) ...........................223
Removal and Installation (4WD) ...........................225
OVERHAUL ......................................................228
Component ...........................................................228
Oil Channel ...........................................................235
Location of Adjusting Shims, Needle Bearings,
Thrust Washers and Snap Rings ..........................
237
DISASSEMBLY ................................................240
Disassembly ..........................................................240
REPAIR FOR COMPONENT PARTS ..............258
Oil Pump ...............................................................258
Front Sun Gear, 3rd One-Way Clutch ...................260
Front Carrier, Input Clutch, Rear Internal Gear .....262
Mid Sun Gear, Rear Sun Gear, High and Low Re-
verse Clutch Hub ..................................................
267
High and Low Reverse Clutch ..............................272
Direct Clutch .........................................................274
ASSEMBLY ......................................................277
Assembly (1) .........................................................277
Adjustment ............................................................290
Assembly (2) .........................................................292
SERVICE DATA AND SPECIFICATIONS
(SDS) ................................................................
298
General Specification ............................................298
Vehicle Speed When Shifting Gears .....................298
Vehicle Speed When Performing and Releasing
Complete Lock-up .................................................
299
Stall Speed ............................................................299
Page 83 of 3061
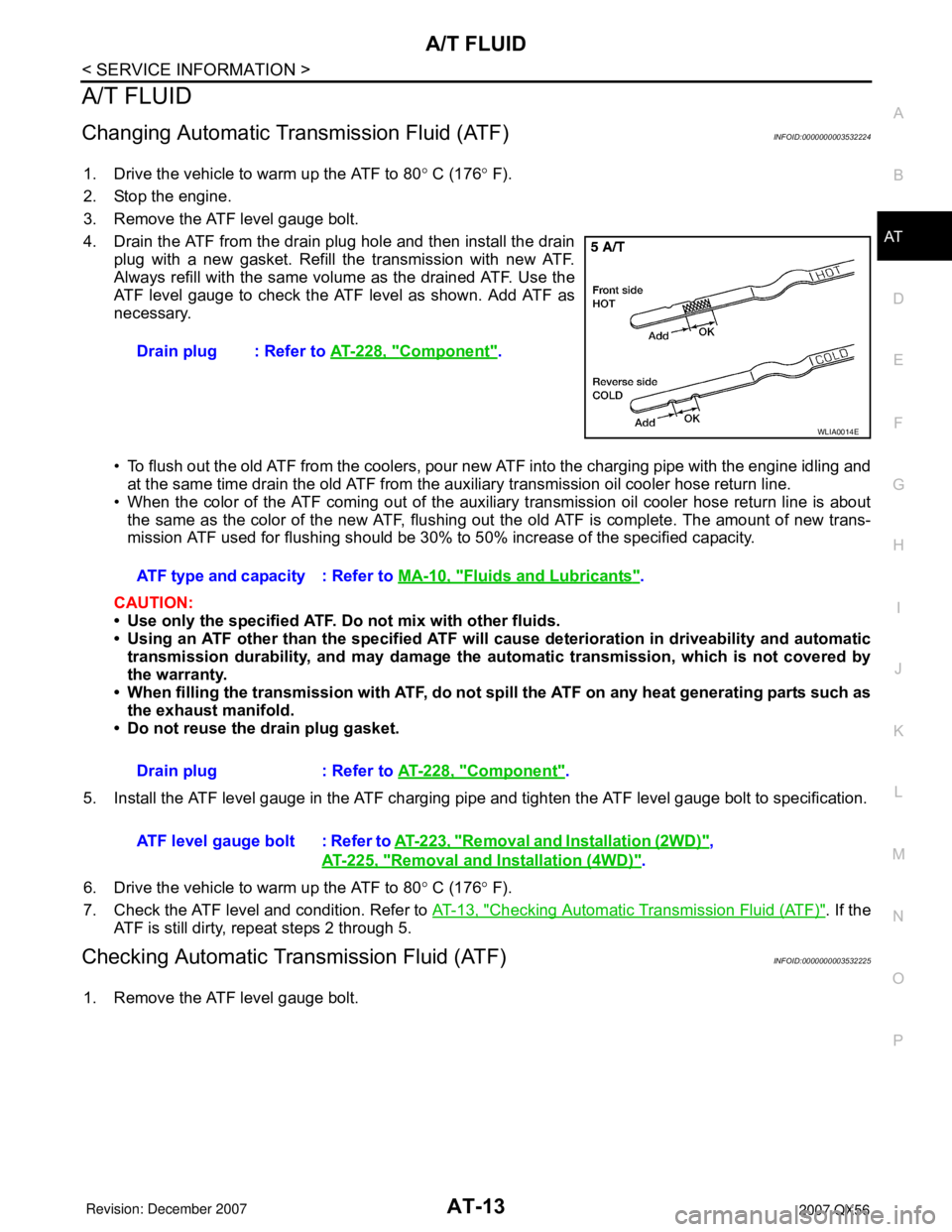
A/T FLUID
AT-13
< SERVICE INFORMATION >
D
E
F
G
H
I
J
K
L
MA
B
AT
N
O
P
A/T FLUID
Changing Automatic Transmission Fluid (ATF)INFOID:0000000003532224
1. Drive the vehicle to warm up the ATF to 80° C (176° F).
2. Stop the engine.
3. Remove the ATF level gauge bolt.
4. Drain the ATF from the drain plug hole and then install the drain
plug with a new gasket. Refill the transmission with new ATF.
Always refill with the same volume as the drained ATF. Use the
ATF level gauge to check the ATF level as shown. Add ATF as
necessary.
• To flush out the old ATF from the coolers, pour new ATF into the charging pipe with the engine idling and
at the same time drain the old ATF from the auxiliary transmission oil cooler hose return line.
• When the color of the ATF coming out of the auxiliary transmission oil cooler hose return line is about
the same as the color of the new ATF, flushing out the old ATF is complete. The amount of new trans-
mission ATF used for flushing should be 30% to 50% increase of the specified capacity.
CAUTION:
• Use only the specified ATF. Do not mix with other fluids.
• Using an ATF other than the specified ATF will cause deterioration in driveability and automatic
transmission durability, and may damage the automatic transmission, which is not covered by
the warranty.
• When filling the transmission with ATF, do not spill the ATF on any heat generating parts such as
the exhaust manifold.
• Do not reuse the drain plug gasket.
5. Install the ATF level gauge in the ATF charging pipe and tighten the ATF level gauge bolt to specification.
6. Drive the vehicle to warm up the ATF to 80° C (176° F).
7. Check the ATF level and condition. Refer to AT-13, "
Checking Automatic Transmission Fluid (ATF)". If the
ATF is still dirty, repeat steps 2 through 5.
Checking Automatic Transmission Fluid (ATF)INFOID:0000000003532225
1. Remove the ATF level gauge bolt.Drain plug : Refer to AT-228, "
Component".
WLIA0014E
ATF type and capacity : Refer to MA-10, "Fluids and Lubricants".
Drain plug : Refer to AT-228, "
Component".
ATF level gauge bolt : Refer to AT-223, "
Removal and Installation (2WD)",
AT-225, "
Removal and Installation (4WD)".
Page 104 of 3061
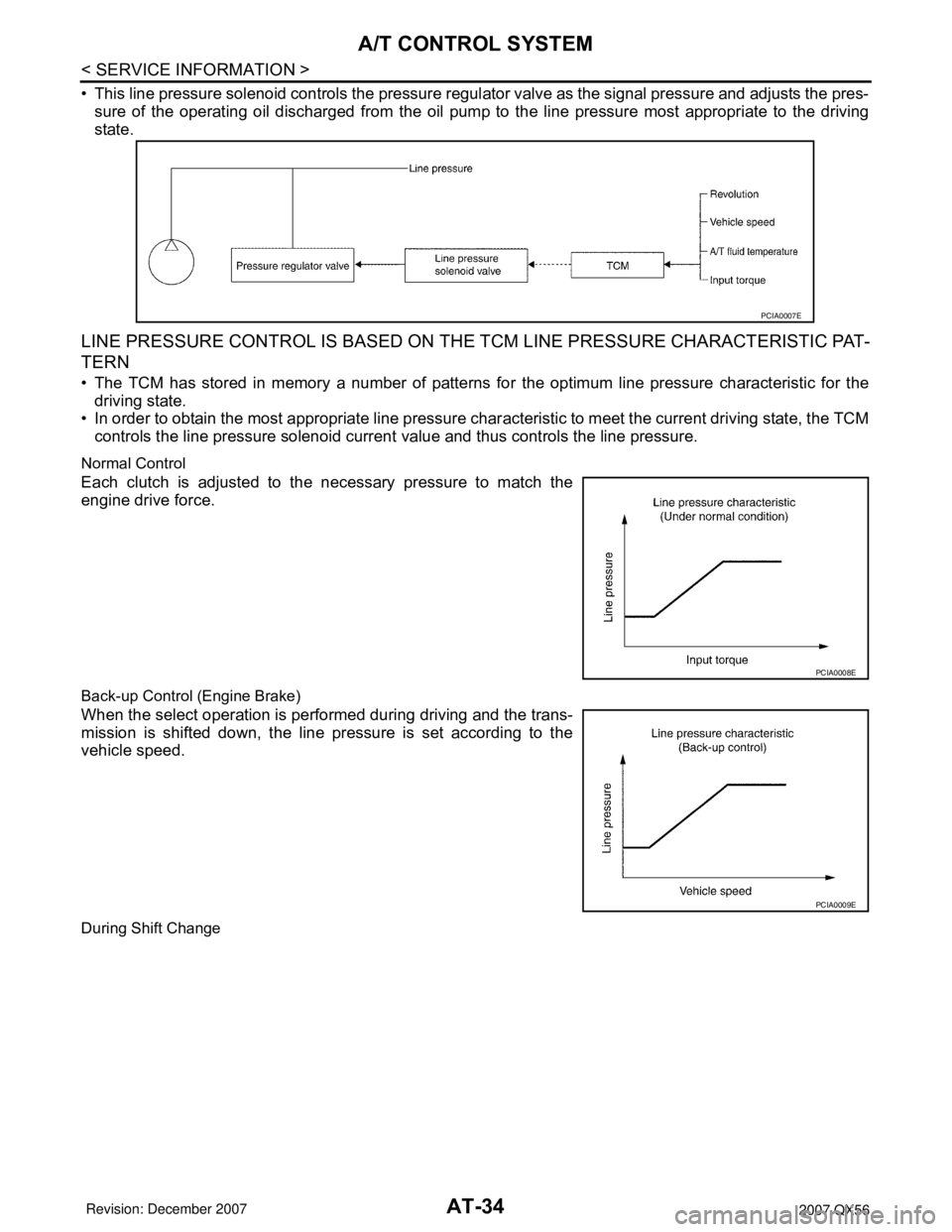
AT-34
< SERVICE INFORMATION >
A/T CONTROL SYSTEM
• This line pressure solenoid controls the pressure regulator valve as the signal pressure and adjusts the pres-
sure of the operating oil discharged from the oil pump to the line pressure most appropriate to the driving
state.
LINE PRESSURE CONTROL IS BASED ON THE TCM LINE PRESSURE CHARACTERISTIC PAT-
TERN
• The TCM has stored in memory a number of patterns for the optimum line pressure characteristic for the
driving state.
• In order to obtain the most appropriate line pressure characteristic to meet the current driving state, the TCM
controls the line pressure solenoid current value and thus controls the line pressure.
Normal Control
Each clutch is adjusted to the necessary pressure to match the
engine drive force.
Back-up Control (Engine Brake)
When the select operation is performed during driving and the trans-
mission is shifted down, the line pressure is set according to the
vehicle speed.
During Shift Change
PCIA0007E
PCIA0008E
PCIA0009E
Page 105 of 3061
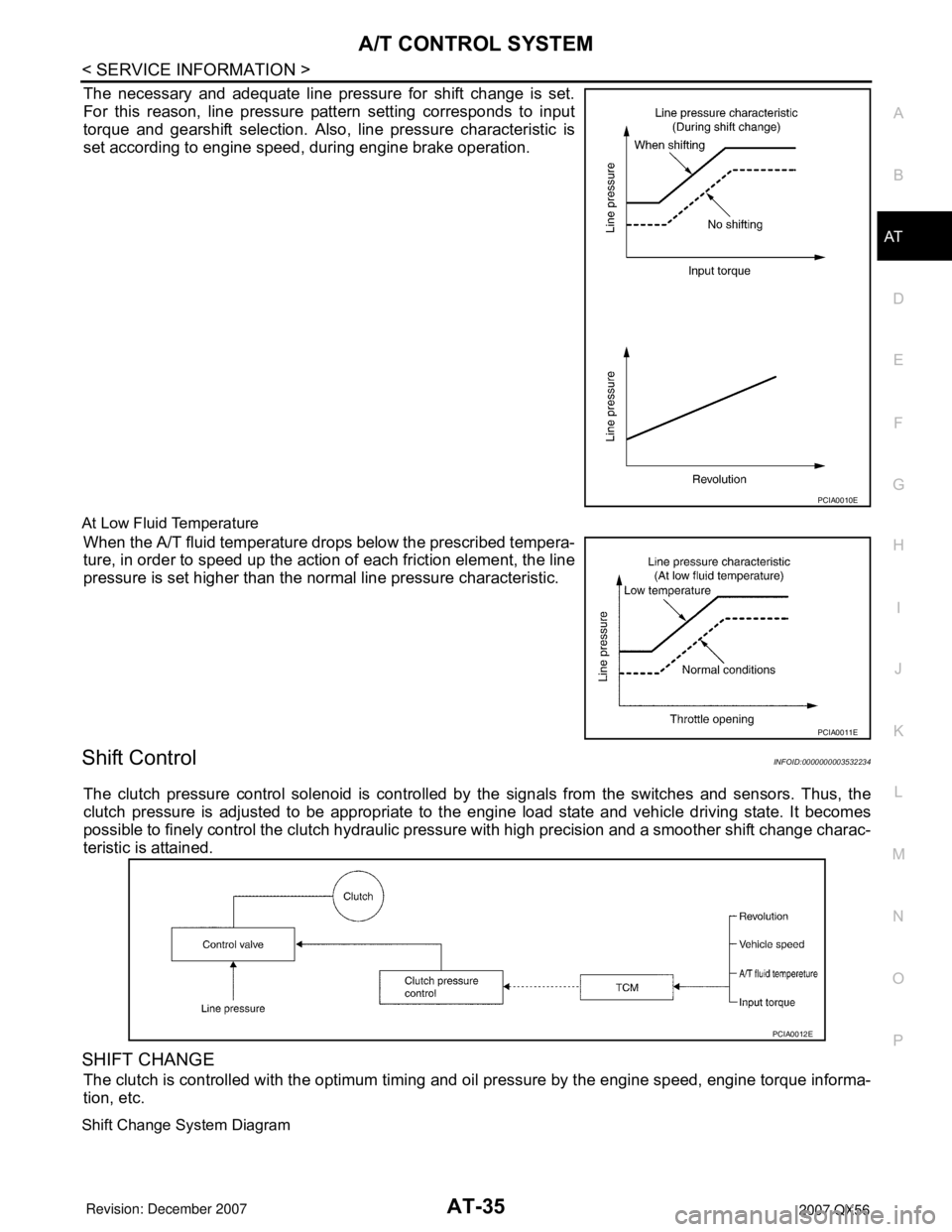
A/T CONTROL SYSTEM
AT-35
< SERVICE INFORMATION >
D
E
F
G
H
I
J
K
L
MA
B
AT
N
O
P
The necessary and adequate line pressure for shift change is set.
For this reason, line pressure pattern setting corresponds to input
torque and gearshift selection. Also, line pressure characteristic is
set according to engine speed, during engine brake operation.
At Low Fluid Temperature
When the A/T fluid temperature drops below the prescribed tempera-
ture, in order to speed up the action of each friction element, the line
pressure is set higher than the normal line pressure characteristic.
Shift ControlINFOID:0000000003532234
The clutch pressure control solenoid is controlled by the signals from the switches and sensors. Thus, the
clutch pressure is adjusted to be appropriate to the engine load state and vehicle driving state. It becomes
possible to finely control the clutch hydraulic pressure with high precision and a smoother shift change charac-
teristic is attained.
SHIFT CHANGE
The clutch is controlled with the optimum timing and oil pressure by the engine speed, engine torque informa-
tion, etc.
Shift Change System Diagram
PCIA0010E
PCIA0011E
PCIA0012E
Page 107 of 3061
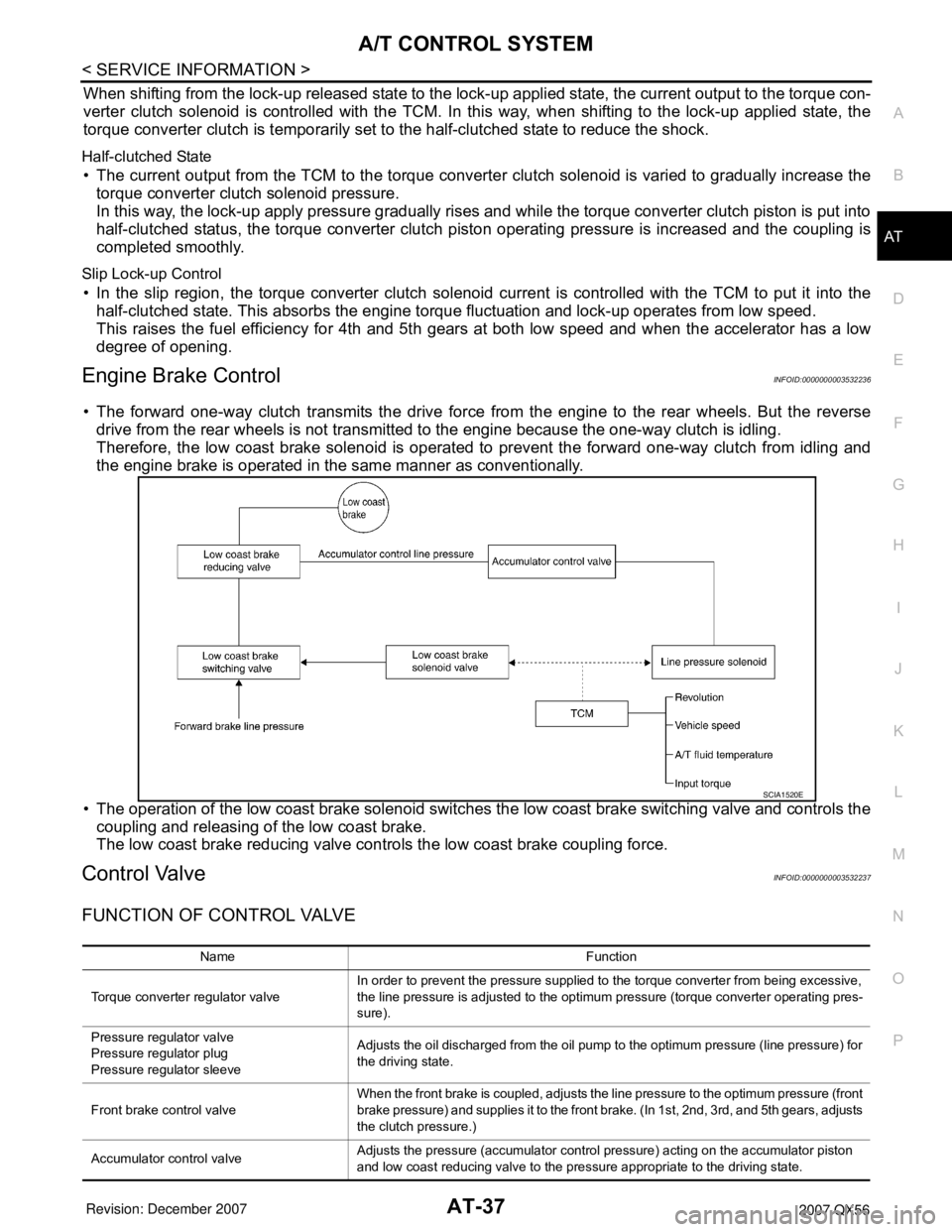
A/T CONTROL SYSTEM
AT-37
< SERVICE INFORMATION >
D
E
F
G
H
I
J
K
L
MA
B
AT
N
O
P
When shifting from the lock-up released state to the lock-up applied state, the current output to the torque con-
verter clutch solenoid is controlled with the TCM. In this way, when shifting to the lock-up applied state, the
torque converter clutch is temporarily set to the half-clutched state to reduce the shock.
Half-clutched State
• The current output from the TCM to the torque converter clutch solenoid is varied to gradually increase the
torque converter clutch solenoid pressure.
In this way, the lock-up apply pressure gradually rises and while the torque converter clutch piston is put into
half-clutched status, the torque converter clutch piston operating pressure is increased and the coupling is
completed smoothly.
Slip Lock-up Control
• In the slip region, the torque converter clutch solenoid current is controlled with the TCM to put it into the
half-clutched state. This absorbs the engine torque fluctuation and lock-up operates from low speed.
This raises the fuel efficiency for 4th and 5th gears at both low speed and when the accelerator has a low
degree of opening.
Engine Brake ControlINFOID:0000000003532236
• The forward one-way clutch transmits the drive force from the engine to the rear wheels. But the reverse
drive from the rear wheels is not transmitted to the engine because the one-way clutch is idling.
Therefore, the low coast brake solenoid is operated to prevent the forward one-way clutch from idling and
the engine brake is operated in the same manner as conventionally.
• The operation of the low coast brake solenoid switches the low coast brake switching valve and controls the
coupling and releasing of the low coast brake.
The low coast brake reducing valve controls the low coast brake coupling force.
Control ValveINFOID:0000000003532237
FUNCTION OF CONTROL VALVE
SCIA1520E
Name Function
Torque converter regulator valveIn order to prevent the pressure supplied to the torque converter from being excessive,
the line pressure is adjusted to the optimum pressure (torque converter operating pres-
sure).
Pressure regulator valve
Pressure regulator plug
Pressure regulator sleeveAdjusts the oil discharged from the oil pump to the optimum pressure (line pressure) for
the driving state.
Front brake control valveWhen the front brake is coupled, adjusts the line pressure to the optimum pressure (front
brake pressure) and supplies it to the front brake. (In 1st, 2nd, 3rd, and 5th gears, adjusts
the clutch pressure.)
Accumulator control valveAdjusts the pressure (accumulator control pressure) acting on the accumulator piston
and low coast reducing valve to the pressure appropriate to the driving state.
Page 108 of 3061
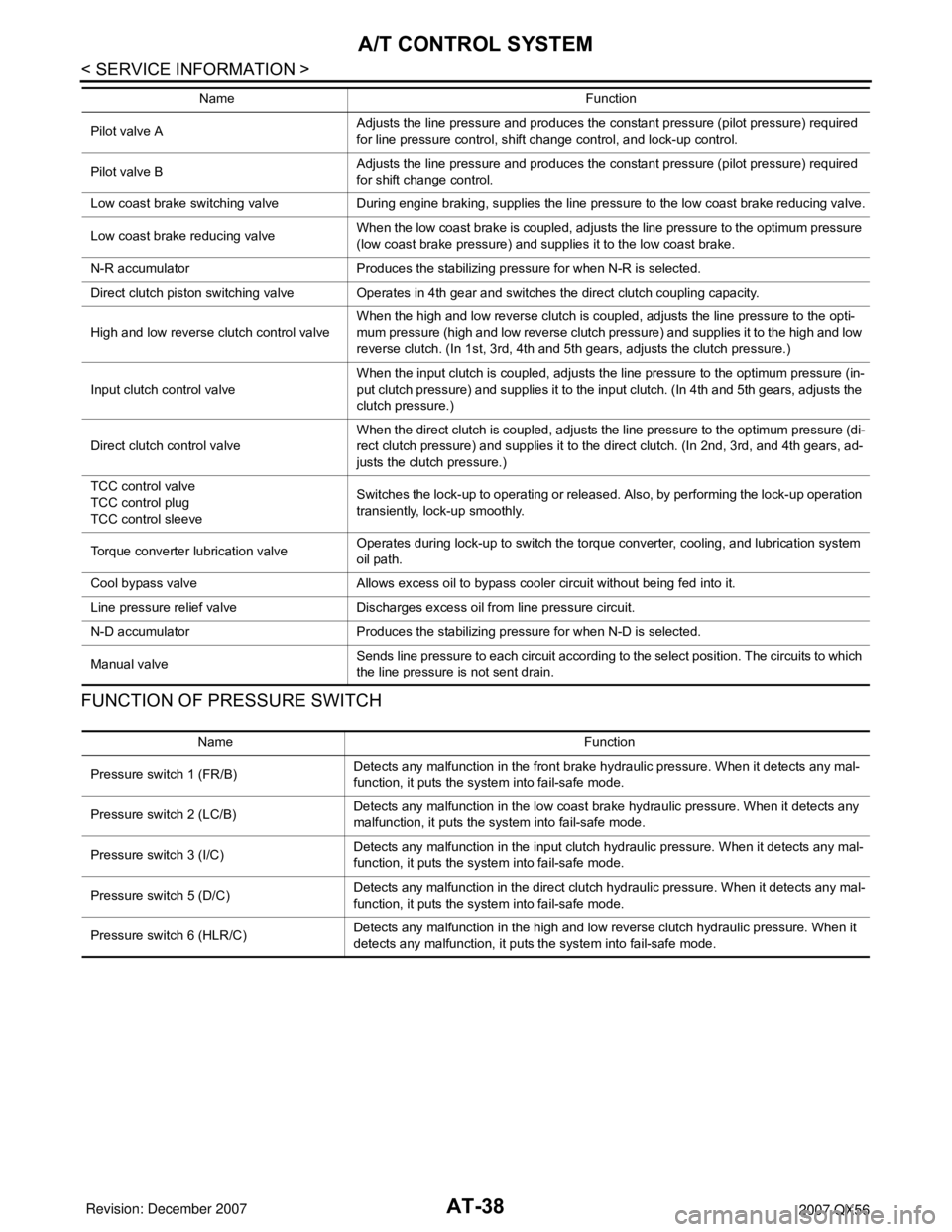
AT-38
< SERVICE INFORMATION >
A/T CONTROL SYSTEM
FUNCTION OF PRESSURE SWITCH
Pilot valve AAdjusts the line pressure and produces the constant pressure (pilot pressure) required
for line pressure control, shift change control, and lock-up control.
Pilot valve BAdjusts the line pressure and produces the constant pressure (pilot pressure) required
for shift change control.
Low coast brake switching valve During engine braking, supplies the line pressure to the low coast brake reducing valve.
Low coast brake reducing valveWhen the low coast brake is coupled, adjusts the line pressure to the optimum pressure
(low coast brake pressure) and supplies it to the low coast brake.
N-R accumulator Produces the stabilizing pressure for when N-R is selected.
Direct clutch piston switching valve Operates in 4th gear and switches the direct clutch coupling capacity.
High and low reverse clutch control valveWhen the high and low reverse clutch is coupled, adjusts the line pressure to the opti-
mum pressure (high and low reverse clutch pressure) and supplies it to the high and low
reverse clutch. (In 1st, 3rd, 4th and 5th gears, adjusts the clutch pressure.)
Input clutch control valveWhen the input clutch is coupled, adjusts the line pressure to the optimum pressure (in-
put clutch pressure) and supplies it to the input clutch. (In 4th and 5th gears, adjusts the
clutch pressure.)
Direct clutch control valveWhen the direct clutch is coupled, adjusts the line pressure to the optimum pressure (di-
rect clutch pressure) and supplies it to the direct clutch. (In 2nd, 3rd, and 4th gears, ad-
justs the clutch pressure.)
TCC control valve
TCC control plug
TCC control sleeveSwitches the lock-up to operating or released. Also, by performing the lock-up operation
transiently, lock-up smoothly.
Torque converter lubrication valveOperates during lock-up to switch the torque converter, cooling, and lubrication system
oil path.
Cool bypass valve Allows excess oil to bypass cooler circuit without being fed into it.
Line pressure relief valve Discharges excess oil from line pressure circuit.
N-D accumulator Produces the stabilizing pressure for when N-D is selected.
Manual valveSends line pressure to each circuit according to the select position. The circuits to which
the line pressure is not sent drain. Name Function
Name Function
Pressure switch 1 (FR/B)Detects any malfunction in the front brake hydraulic pressure. When it detects any mal-
function, it puts the system into fail-safe mode.
Pressure switch 2 (LC/B)Detects any malfunction in the low coast brake hydraulic pressure. When it detects any
malfunction, it puts the system into fail-safe mode.
Pressure switch 3 (I/C)Detects any malfunction in the input clutch hydraulic pressure. When it detects any mal-
function, it puts the system into fail-safe mode.
Pressure switch 5 (D/C)Detects any malfunction in the direct clutch hydraulic pressure. When it detects any mal-
function, it puts the system into fail-safe mode.
Pressure switch 6 (HLR/C)Detects any malfunction in the high and low reverse clutch hydraulic pressure. When it
detects any malfunction, it puts the system into fail-safe mode.