Electrical INFINITI QX56 2008 Factory Workshop Manual
[x] Cancel search | Manufacturer: INFINITI, Model Year: 2008, Model line: QX56, Model: INFINITI QX56 2008Pages: 4083, PDF Size: 81.73 MB
Page 1169 of 4083
![INFINITI QX56 2008 Factory Workshop Manual TRANSFER ASSEMBLYDLN-139
< REMOVAL AND INSTALLATION > [ATX14B]
C
EF
G H
I
J
K L
M A
B
DLN
N
O P
REMOVAL AND INSTALLATION
TRANSFER ASSEMBLY
Removal and InstallationINFOID:0000000001604419
REMOVAL
1. Se INFINITI QX56 2008 Factory Workshop Manual TRANSFER ASSEMBLYDLN-139
< REMOVAL AND INSTALLATION > [ATX14B]
C
EF
G H
I
J
K L
M A
B
DLN
N
O P
REMOVAL AND INSTALLATION
TRANSFER ASSEMBLY
Removal and InstallationINFOID:0000000001604419
REMOVAL
1. Se](/img/42/57030/w960_57030-1168.png)
TRANSFER ASSEMBLYDLN-139
< REMOVAL AND INSTALLATION > [ATX14B]
C
EF
G H
I
J
K L
M A
B
DLN
N
O P
REMOVAL AND INSTALLATION
TRANSFER ASSEMBLY
Removal and InstallationINFOID:0000000001604419
REMOVAL
1. Set transfer state as 2WD when 4WD shift switch is at 2WD.
2. Remove the undercovers using power tool.
3. Drain the transfer fluid. Refer to DLN-127, "
Replacement".
4. Remove the center exhaust tube and main muffler. Refer to EX-6, "
Removal and Installation".
5. Remove the front and rear propeller shafts. Refer to DLN-184, "
Removal and Installation" (front), DLN-
184, "Removal and Installation" (rear).
CAUTION:
Do not damage spline, sleeve yoke and rear oi l seal when removing rear propeller shaft.
NOTE:
Insert a plug into the rear oil seal after removing the rear propeller shaft.
6. Remove the A/T nuts from the A/T crossmember. Refer to TM-216, "
Removal and Installation (4WD)".
7. Position two suitable jacks under the A/T and transfer assembly.
8. Remove the crossmember. Refer to TM-216, "
Removal and Installation (4WD)".
WARNING:
Support A/T and transfer assembly using two suitable jacks while removing crossmember.
9. Disconnect the electrical connectors from the following: • ATP switch
• Neutral 4LO switch
• Wait detection switch
• Transfer motor
• Transfer control device
• Transfer terminal cord assembly
10. Disconnect each air breather hose from the following. Refer to DLN-135, "
Removal and Installation".
• Actuator
• Breather tube (transfer)
• Transfer motor
11. Remove the transfer control dev ice from the extension housing.
12. Remove the transfer to A/T and A/T to transfer bolts.
13. Remove the transfer assembly. WARNING:
Support transfer assembly with su itable jack while removing it.
CAUTION:
Do not damage rear oil seal (A/T).
INSTALLATION
Installation is in the reverse order of removal.
• Tighten the bolts to specification.
• Fill the transfer with new fluid and check for fluid leakage and fluid level. Refer to DLN-127, "
Replacement".
• Start the engine for one minute. Then stop the engine and recheck the transfer fluid. Refer to DLN-127, "
Inspection".
Transfer bolt torque : 36 N·m (3.7 kg-m, 27 ft-lb)
SMT872C
Revision: March 2010
2008 QX56
Page 1209 of 4083
![INFINITI QX56 2008 Factory Workshop Manual PRECAUTIONSDLN-179
< PRECAUTION > [PROPELLER SHAFT: 2F1310]
C
EF
G H
I
J
K L
M A
B
DLN
N
O P
PRECAUTION
PRECAUTIONS
Precaution for Supplemental Restraint System (SRS) "AIR BAG" and "SEAT BELT
PRE-TE INFINITI QX56 2008 Factory Workshop Manual PRECAUTIONSDLN-179
< PRECAUTION > [PROPELLER SHAFT: 2F1310]
C
EF
G H
I
J
K L
M A
B
DLN
N
O P
PRECAUTION
PRECAUTIONS
Precaution for Supplemental Restraint System (SRS) "AIR BAG" and "SEAT BELT
PRE-TE](/img/42/57030/w960_57030-1208.png)
PRECAUTIONSDLN-179
< PRECAUTION > [PROPELLER SHAFT: 2F1310]
C
EF
G H
I
J
K L
M A
B
DLN
N
O P
PRECAUTION
PRECAUTIONS
Precaution for Supplemental Restraint System (SRS) "AIR BAG" and "SEAT BELT
PRE-TENSIONER"
INFOID:0000000004884144
The Supplemental Restraint System such as “AIR BAG” and “SEAT BELT PRE-TENSIONER”, used along
with a front seat belt, helps to reduce the risk or severi ty of injury to the driver and front passenger for certain
types of collision. This system includes seat belt switch inputs and dual stage front air bag modules. The SRS
system uses the seat belt switches to determine the front air bag deployment, and may only deploy one front
air bag, depending on the severity of a collision and w hether the front occupants are belted or unbelted.
Information necessary to service the system safely is included in the SR and SB section of this Service Man-
ual.
WARNING:
• To avoid rendering the SRS inoper ative, which could increase the risk of personal injury or death in
the event of a collision which would result in air bag inflation, all maintenance must be performed by
an authorized NISSAN/INFINITI dealer.
• Improper maintenance, including in correct removal and installation of the SRS, can lead to personal
injury caused by unintentional act ivation of the system. For removal of Spiral Cable and Air Bag
Module, see the SR section.
• Do not use electrical test equipm ent on any circuit related to the SRS unless instructed to in this
Service Manual. SRS wiring harnesses can be identi fied by yellow and/or orange harnesses or har-
ness connectors.
PRECAUTIONS WHEN USING POWER TOOLS (AIR OR ELECTRIC) AND HAMMERS
WARNING:
• When working near the Airbag Diagnosis Sensor Un it or other Airbag System sensors with the Igni-
tion ON or engine running, DO NOT use air or el ectric power tools or strike near the sensor(s) with a
hammer. Heavy vibration could activate the sensor( s) and deploy the air bag(s), possibly causing
serious injury.
• When using air or electric power tools or hammers, always switch the Ignition OFF, disconnect the battery, and wait at least 3 minutes before performing any service.
Precaution Necessary for Steering Wheel Rotation After Battery Disconnect
INFOID:0000000004884143
NOTE:
• This Procedure is applied only to models with Intelligent Key system and NATS (NISSAN ANTI-THEFT SYS-
TEM).
• Remove and install all control units after disconnecti ng both battery cables with the ignition knob in the
″ LOCK ″ position.
• Always use CONSULT-III to perform self-diagnosis as a part of each function inspection after finishing work.
If DTC is detected, perform trouble diagnosis according to self-diagnostic results.
For models equipped with the Intelligent Key system and NATS , an electrically controlled steering lock mech-
anism is adopted on the key cylinder.
For this reason, if the battery is disconnected or if the battery is discharged, the steering wheel will lock and
steering wheel rotation will become impossible.
If steering wheel rotation is required when battery power is interrupted, follow the procedure below before
starting the repair operation.
OPERATION PROCEDURE
1. Connect both battery cables. NOTE:
Supply power using jumper cables if battery is discharged.
2. Use the Intelligent Key or mechanical key to turn the ignition switch to the ″ACC ″ position. At this time, the
steering lock will be released.
3. Disconnect both battery cables. The steering lock will remain released and the steering wheel can be
rotated.
4. Perform the necessary repair operation.
Revision: March 2010 2008 QX56
Page 1219 of 4083
![INFINITI QX56 2008 Factory Workshop Manual PRECAUTIONSDLN-189
< PRECAUTION > [PROPELLER SHAFT: 2S1410]
C
EF
G H
I
J
K L
M A
B
DLN
N
O P
PRECAUTION
PRECAUTIONS
Precaution for Supplemental Restraint System (SRS) "AIR BAG" and "SEAT BELT
PRE-TE INFINITI QX56 2008 Factory Workshop Manual PRECAUTIONSDLN-189
< PRECAUTION > [PROPELLER SHAFT: 2S1410]
C
EF
G H
I
J
K L
M A
B
DLN
N
O P
PRECAUTION
PRECAUTIONS
Precaution for Supplemental Restraint System (SRS) "AIR BAG" and "SEAT BELT
PRE-TE](/img/42/57030/w960_57030-1218.png)
PRECAUTIONSDLN-189
< PRECAUTION > [PROPELLER SHAFT: 2S1410]
C
EF
G H
I
J
K L
M A
B
DLN
N
O P
PRECAUTION
PRECAUTIONS
Precaution for Supplemental Restraint System (SRS) "AIR BAG" and "SEAT BELT
PRE-TENSIONER"
INFOID:0000000004884146
The Supplemental Restraint System such as “AIR BAG” and “SEAT BELT PRE-TENSIONER”, used along
with a front seat belt, helps to reduce the risk or severi ty of injury to the driver and front passenger for certain
types of collision. This system includes seat belt switch inputs and dual stage front air bag modules. The SRS
system uses the seat belt switches to determine the front air bag deployment, and may only deploy one front
air bag, depending on the severity of a collision and w hether the front occupants are belted or unbelted.
Information necessary to service the system safely is included in the SR and SB section of this Service Man-
ual.
WARNING:
• To avoid rendering the SRS inoper ative, which could increase the risk of personal injury or death in
the event of a collision which would result in air bag inflation, all maintenance must be performed by
an authorized NISSAN/INFINITI dealer.
• Improper maintenance, including in correct removal and installation of the SRS, can lead to personal
injury caused by unintentional act ivation of the system. For removal of Spiral Cable and Air Bag
Module, see the SR section.
• Do not use electrical test equipm ent on any circuit related to the SRS unless instructed to in this
Service Manual. SRS wiring harnesses can be identi fied by yellow and/or orange harnesses or har-
ness connectors.
PRECAUTIONS WHEN USING POWER TOOLS (AIR OR ELECTRIC) AND HAMMERS
WARNING:
• When working near the Airbag Diagnosis Sensor Un it or other Airbag System sensors with the Igni-
tion ON or engine running, DO NOT use air or el ectric power tools or strike near the sensor(s) with a
hammer. Heavy vibration could activate the sensor( s) and deploy the air bag(s), possibly causing
serious injury.
• When using air or electric power tools or hammers, always switch the Ignition OFF, disconnect the battery, and wait at least 3 minutes before performing any service.
Precaution Necessary for Steering Wheel Rotation After Battery Disconnect
INFOID:0000000004884145
NOTE:
• This Procedure is applied only to models with Intelligent Key system and NATS (NISSAN ANTI-THEFT SYS-
TEM).
• Remove and install all control units after disconnecti ng both battery cables with the ignition knob in the
″ LOCK ″ position.
• Always use CONSULT-III to perform self-diagnosis as a part of each function inspection after finishing work.
If DTC is detected, perform trouble diagnosis according to self-diagnostic results.
For models equipped with the Intelligent Key system and NATS , an electrically controlled steering lock mech-
anism is adopted on the key cylinder.
For this reason, if the battery is disconnected or if the battery is discharged, the steering wheel will lock and
steering wheel rotation will become impossible.
If steering wheel rotation is required when battery power is interrupted, follow the procedure below before
starting the repair operation.
OPERATION PROCEDURE
1. Connect both battery cables. NOTE:
Supply power using jumper cables if battery is discharged.
2. Use the Intelligent Key or mechanical key to turn the ignition switch to the ″ACC ″ position. At this time, the
steering lock will be released.
3. Disconnect both battery cables. The steering lock will remain released and the steering wheel can be
rotated.
4. Perform the necessary repair operation.
Revision: March 2010 2008 QX56
Page 1231 of 4083
![INFINITI QX56 2008 Factory Workshop Manual PRECAUTIONSDLN-201
< PRECAUTION > [FRONT FINAL DRIVE: M205]
C
EF
G H
I
J
K L
M A
B
DLN
N
O P
PRECAUTION
PRECAUTIONS
Precaution for Supplemental Restraint System (SRS) "AIR BAG" and "SEAT BELT
PRE-TE INFINITI QX56 2008 Factory Workshop Manual PRECAUTIONSDLN-201
< PRECAUTION > [FRONT FINAL DRIVE: M205]
C
EF
G H
I
J
K L
M A
B
DLN
N
O P
PRECAUTION
PRECAUTIONS
Precaution for Supplemental Restraint System (SRS) "AIR BAG" and "SEAT BELT
PRE-TE](/img/42/57030/w960_57030-1230.png)
PRECAUTIONSDLN-201
< PRECAUTION > [FRONT FINAL DRIVE: M205]
C
EF
G H
I
J
K L
M A
B
DLN
N
O P
PRECAUTION
PRECAUTIONS
Precaution for Supplemental Restraint System (SRS) "AIR BAG" and "SEAT BELT
PRE-TENSIONER"
INFOID:0000000004857592
The Supplemental Restraint System such as “AIR BAG” and “SEAT BELT PRE-TENSIONER”, used along
with a front seat belt, helps to reduce the risk or severi ty of injury to the driver and front passenger for certain
types of collision. This system includes seat belt switch inputs and dual stage front air bag modules. The SRS
system uses the seat belt switches to determine the front air bag deployment, and may only deploy one front
air bag, depending on the severity of a collision and w hether the front occupants are belted or unbelted.
Information necessary to service the system safely is included in the SR and SB section of this Service Man-
ual.
WARNING:
• To avoid rendering the SRS inoper ative, which could increase the risk of personal injury or death in
the event of a collision which would result in air bag inflation, all maintenance must be performed by
an authorized NISSAN/INFINITI dealer.
• Improper maintenance, including in correct removal and installation of the SRS, can lead to personal
injury caused by unintentional act ivation of the system. For removal of Spiral Cable and Air Bag
Module, see the SR section.
• Do not use electrical test equipm ent on any circuit related to the SRS unless instructed to in this
Service Manual. SRS wiring harnesses can be identi fied by yellow and/or orange harnesses or har-
ness connectors.
PRECAUTIONS WHEN USING POWER TOOLS (AIR OR ELECTRIC) AND HAMMERS
WARNING:
• When working near the Airbag Diagnosis Sensor Un it or other Airbag System sensors with the Igni-
tion ON or engine running, DO NOT use air or el ectric power tools or strike near the sensor(s) with a
hammer. Heavy vibration could activate the sensor( s) and deploy the air bag(s), possibly causing
serious injury.
• When using air or electric power tools or hammers, always switch the Ignition OFF, disconnect the battery, and wait at least 3 minutes before performing any service.
Precaution Necessary for Steering Wheel Rotation After Battery Disconnect
INFOID:0000000004857591
NOTE:
• This Procedure is applied only to models with Intelligent Key system and NATS (NISSAN ANTI-THEFT SYS-
TEM).
• Remove and install all control units after disconnecti ng both battery cables with the ignition knob in the
″ LOCK ″ position.
• Always use CONSULT-III to perform self-diagnosis as a part of each function inspection after finishing work.
If DTC is detected, perform trouble diagnosis according to self-diagnostic results.
For models equipped with the Intelligent Key system and NATS , an electrically controlled steering lock mech-
anism is adopted on the key cylinder.
For this reason, if the battery is disconnected or if the battery is discharged, the steering wheel will lock and
steering wheel rotation will become impossible.
If steering wheel rotation is required when battery power is interrupted, follow the procedure below before
starting the repair operation.
OPERATION PROCEDURE
1. Connect both battery cables. NOTE:
Supply power using jumper cables if battery is discharged.
2. Use the Intelligent Key or mechanical key to turn the ignition switch to the ″ACC ″ position. At this time, the
steering lock will be released.
3. Disconnect both battery cables. The steering lock will remain released and the steering wheel can be
rotated.
4. Perform the necessary repair operation.
Revision: March 2010 2008 QX56
Page 1263 of 4083
![INFINITI QX56 2008 Factory Workshop Manual PRECAUTIONSDLN-233
< PRECAUTION > [REAR FINAL DRIVE: R230]
C
EF
G H
I
J
K L
M A
B
DLN
N
O P
PRECAUTION
PRECAUTIONS
Precaution for Supplemental Restraint System (SRS) "AIR BAG" and "SEAT BELT
PRE-TEN INFINITI QX56 2008 Factory Workshop Manual PRECAUTIONSDLN-233
< PRECAUTION > [REAR FINAL DRIVE: R230]
C
EF
G H
I
J
K L
M A
B
DLN
N
O P
PRECAUTION
PRECAUTIONS
Precaution for Supplemental Restraint System (SRS) "AIR BAG" and "SEAT BELT
PRE-TEN](/img/42/57030/w960_57030-1262.png)
PRECAUTIONSDLN-233
< PRECAUTION > [REAR FINAL DRIVE: R230]
C
EF
G H
I
J
K L
M A
B
DLN
N
O P
PRECAUTION
PRECAUTIONS
Precaution for Supplemental Restraint System (SRS) "AIR BAG" and "SEAT BELT
PRE-TENSIONER"
INFOID:0000000004857594
The Supplemental Restraint System such as “AIR BAG” and “SEAT BELT PRE-TENSIONER”, used along
with a front seat belt, helps to reduce the risk or severi ty of injury to the driver and front passenger for certain
types of collision. This system includes seat belt switch inputs and dual stage front air bag modules. The SRS
system uses the seat belt switches to determine the front air bag deployment, and may only deploy one front
air bag, depending on the severity of a collision and w hether the front occupants are belted or unbelted.
Information necessary to service the system safely is included in the SR and SB section of this Service Man-
ual.
WARNING:
• To avoid rendering the SRS inoper ative, which could increase the risk of personal injury or death in
the event of a collision which would result in air bag inflation, all maintenance must be performed by
an authorized NISSAN/INFINITI dealer.
• Improper maintenance, including in correct removal and installation of the SRS, can lead to personal
injury caused by unintentional act ivation of the system. For removal of Spiral Cable and Air Bag
Module, see the SR section.
• Do not use electrical test equipm ent on any circuit related to the SRS unless instructed to in this
Service Manual. SRS wiring harnesses can be identi fied by yellow and/or orange harnesses or har-
ness connectors.
PRECAUTIONS WHEN USING POWER TOOLS (AIR OR ELECTRIC) AND HAMMERS
WARNING:
• When working near the Airbag Diagnosis Sensor Un it or other Airbag System sensors with the Igni-
tion ON or engine running, DO NOT use air or el ectric power tools or strike near the sensor(s) with a
hammer. Heavy vibration could activate the sensor( s) and deploy the air bag(s), possibly causing
serious injury.
• When using air or electric power tools or hammers, always switch the Ignition OFF, disconnect the battery, and wait at least 3 minutes before performing any service.
Precaution Necessary for Steering Wheel Rotation After Battery Disconnect
INFOID:0000000004857593
NOTE:
• This Procedure is applied only to models with Intelligent Key system and NATS (NISSAN ANTI-THEFT SYS-
TEM).
• Remove and install all control units after disconnecti ng both battery cables with the ignition knob in the
″ LOCK ″ position.
• Always use CONSULT-III to perform self-diagnosis as a part of each function inspection after finishing work.
If DTC is detected, perform trouble diagnosis according to self-diagnostic results.
For models equipped with the Intelligent Key system and NATS , an electrically controlled steering lock mech-
anism is adopted on the key cylinder.
For this reason, if the battery is disconnected or if the battery is discharged, the steering wheel will lock and
steering wheel rotation will become impossible.
If steering wheel rotation is required when battery power is interrupted, follow the procedure below before
starting the repair operation.
OPERATION PROCEDURE
1. Connect both battery cables. NOTE:
Supply power using jumper cables if battery is discharged.
2. Use the Intelligent Key or mechanical key to turn the ignition switch to the ″ACC ″ position. At this time, the
steering lock will be released.
3. Disconnect both battery cables. The steering lock will remain released and the steering wheel can be
rotated.
4. Perform the necessary repair operation.
Revision: March 2010 2008 QX56
Page 1305 of 4083
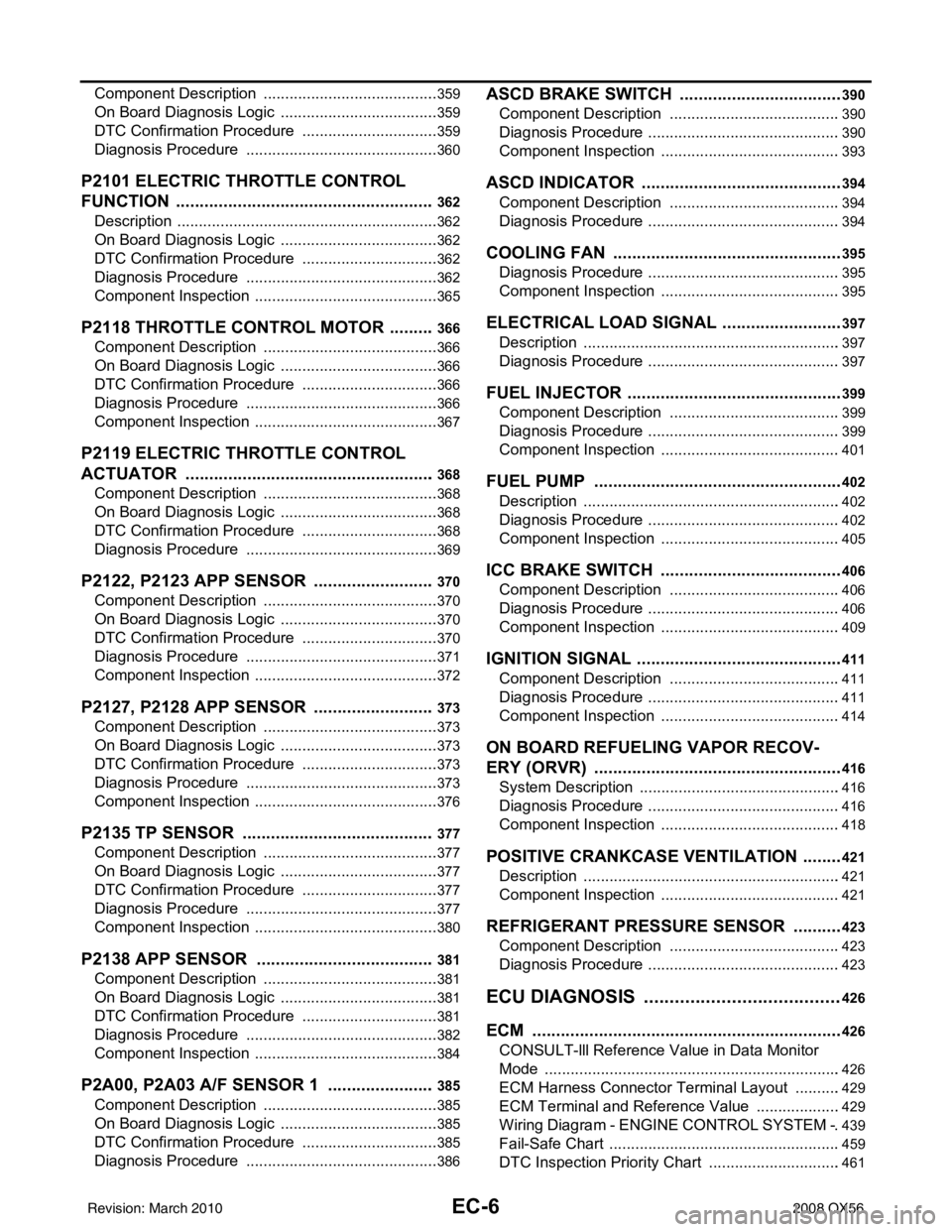
EC-6
Component Description .........................................359
On Board Diagnosis Logic .....................................359
DTC Confirmation Procedure ................................359
Diagnosis Procedure .............................................360
P2101 ELECTRIC THROTTLE CONTROL
FUNCTION .......................................................
362
Description ........................................................... ..362
On Board Diagnosis Logic .....................................362
DTC Confirmation Procedure ................................362
Diagnosis Procedure .............................................362
Component Inspection ...........................................365
P2118 THROTTLE CONTROL MOTOR ..........366
Component Description ....................................... ..366
On Board Diagnosis Logic .....................................366
DTC Confirmation Procedure ................................366
Diagnosis Procedure .............................................366
Component Inspection ...........................................367
P2119 ELECTRIC THROTTLE CONTROL
ACTUATOR .....................................................
368
Component Description ....................................... ..368
On Board Diagnosis Logic .....................................368
DTC Confirmation Procedure ................................368
Diagnosis Procedure .............................................369
P2122, P2123 APP SENSOR ..........................370
Component Description ....................................... ..370
On Board Diagnosis Logic .....................................370
DTC Confirmation Procedure ................................370
Diagnosis Procedure .............................................371
Component Inspection ...........................................372
P2127, P2128 APP SENSOR ..........................373
Component Description ....................................... ..373
On Board Diagnosis Logic .....................................373
DTC Confirmation Procedure ................................373
Diagnosis Procedure .............................................373
Component Inspection ...........................................376
P2135 TP SENSOR .........................................377
Component Description ....................................... ..377
On Board Diagnosis Logic .....................................377
DTC Confirmation Procedure ................................377
Diagnosis Procedure .............................................377
Component Inspection ...........................................380
P2138 APP SENSOR ......................................381
Component Description ....................................... ..381
On Board Diagnosis Logic .....................................381
DTC Confirmation Procedure ................................381
Diagnosis Procedure .............................................382
Component Inspection ...........................................384
P2A00, P2A03 A/F SENSOR 1 .......................385
Component Description ....................................... ..385
On Board Diagnosis Logic .....................................385
DTC Confirmation Procedure ................................385
Diagnosis Procedure .............................................386
ASCD BRAKE SWITCH ...................................390
Component Description ....................................... .390
Diagnosis Procedure .............................................390
Component Inspection ..........................................393
ASCD INDICATOR ...........................................394
Component Description ....................................... .394
Diagnosis Procedure .............................................394
COOLING FAN .................................................395
Diagnosis Procedure ............................................ .395
Component Inspection ..........................................395
ELECTRICAL LOAD SIGNAL ..........................397
Description ........................................................... .397
Diagnosis Procedure .............................................397
FUEL INJECTOR ..............................................399
Component Description ....................................... .399
Diagnosis Procedure .............................................399
Component Inspection ..........................................401
FUEL PUMP .....................................................402
Description ........................................................... .402
Diagnosis Procedure .............................................402
Component Inspection ..........................................405
ICC BRAKE SWITCH ..................................... ..406
Component Description ....................................... .406
Diagnosis Procedure .............................................406
Component Inspection ..........................................409
IGNITION SIGNAL ............................................411
Component Description ....................................... .411
Diagnosis Procedure .............................................411
Component Inspection ..........................................414
ON BOARD REFUELING VAPOR RECOV-
ERY (ORVR) .....................................................
416
System Description .............................................. .416
Diagnosis Procedure .............................................416
Component Inspection ..........................................418
POSITIVE CRANKCASE VENTILATION .........421
Description ........................................................... .421
Component Inspection ..........................................421
REFRIGERANT PRESSURE SENSOR ...........423
Component Description ....................................... .423
Diagnosis Procedure .............................................423
ECU DIAGNOSIS ......................................426
ECM ................................................................ ..426
CONSULT-lll Reference Value in Data Monitor
Mode .................................................................... .
426
ECM Harness Connector Terminal Layout ...........429
ECM Terminal and Reference Value ....................429
Wiring Diagram - ENGINE CONTROL SYSTEM - .439
Fail-Safe Chart ......................................................459
DTC Inspection Priority Chart ...............................461
Revision: March 2010 2008 QX56
Page 1312 of 4083
![INFINITI QX56 2008 Factory Workshop Manual INSPECTION AND ADJUSTMENTEC-13
< BASIC INSPECTION > [VK56DE]
C
D
E
F
G H
I
J
K L
M A
EC
NP
O
INSPECTION AND ADJUSTMENT
Basic InspectionINFOID:0000000001351329
1.INSPECTION START
1. Check service recor INFINITI QX56 2008 Factory Workshop Manual INSPECTION AND ADJUSTMENTEC-13
< BASIC INSPECTION > [VK56DE]
C
D
E
F
G H
I
J
K L
M A
EC
NP
O
INSPECTION AND ADJUSTMENT
Basic InspectionINFOID:0000000001351329
1.INSPECTION START
1. Check service recor](/img/42/57030/w960_57030-1311.png)
INSPECTION AND ADJUSTMENTEC-13
< BASIC INSPECTION > [VK56DE]
C
D
E
F
G H
I
J
K L
M A
EC
NP
O
INSPECTION AND ADJUSTMENT
Basic InspectionINFOID:0000000001351329
1.INSPECTION START
1. Check service records for any recent repairs that may indicate a related malfunction, or a current need for scheduled maintenance.
2. Open engine hood and check the following:
- Harness connectors for improper connections
- Wiring harness for improper connections, pinches and cut
- Vacuum hoses for splits, kinks and improper connections
- Hoses and ducts for leaks
- Air cleaner clogging
- Gasket
3. Confirm that electrical or mechanical loads are not applied.
- Headlamp switch is OFF.
- Air conditioner switch is OFF.
- Rear window defogger switch is OFF.
- Steering wheel is in the straight-ahead position, etc.
4. Start engine and warm it up until engine coolant temperature indicator points the middle of gauge.
Ensure engine stays below 1,000 rpm.
5. Run engine at about 2,000 rpm for about 2 minutes under no load.
6. Make sure that no DTC is displayed with CONSULT-III or GST.
OK or NG
OK >> GO TO 3.
NG >> GO TO 2.
2.REPAIR OR REPLACE
Repair or replace components as necessary according to corresponding Diagnostic Procedure.
>> GO TO 3.
3.CHECK TARGET IDLE SPEED
With CONSULT-III
1. Run engine at about 2,000 rpm for about 2 minutes under no load.
SEF983U
SEF976U
SEF977U
Revision: March 2010 2008 QX56
Page 1341 of 4083
![INFINITI QX56 2008 Factory Workshop Manual EC-42
< FUNCTION DIAGNOSIS >[VK56DE]
ON BOARD DIAGNOSTIC (OBD) SYSTEM
Therefore, when electrical controlled throttle and part
of ECM related diagnoses are continuously detected as
NG for 5 trips, ECM INFINITI QX56 2008 Factory Workshop Manual EC-42
< FUNCTION DIAGNOSIS >[VK56DE]
ON BOARD DIAGNOSTIC (OBD) SYSTEM
Therefore, when electrical controlled throttle and part
of ECM related diagnoses are continuously detected as
NG for 5 trips, ECM](/img/42/57030/w960_57030-1340.png)
EC-42
< FUNCTION DIAGNOSIS >[VK56DE]
ON BOARD DIAGNOSTIC (OBD) SYSTEM
Therefore, when electrical controlled throttle and part
of ECM related diagnoses are continuously detected as
NG for 5 trips, ECM warns the driver that engine cont rol system malfunctions and MIL circuit is open by means
of operating fail-safe function.
The fail-safe function also operates when above diagnos es except MIL circuit are detected and demands the
driver to repair the malfunction.
Emission-related Diagnostic InformationINFOID:0000000001351325
DTC AND 1ST TRIP DTC
The 1st trip DTC (whose number is the same as the DT C number) is displayed for the latest self-diagnostic
result obtained. If the ECM memory was cleared previous ly, and the 1st trip DTC did not reoccur, the 1st trip
DTC will not be displayed.
If a malfunction is detected during the 1st trip, the 1st trip DTC is stored in the ECM memory. The MIL will not
light up (two trip detection logic). If the same malfunction is not detected in the 2nd trip (meeting the required
driving pattern), the 1st trip DTC is cleared from the ECM memory. If the same malfunction is detected in the
2nd trip, both the 1st trip DTC and DTC are stored in t he ECM memory and the MIL lights up. In other words,
the DTC is stored in the ECM memory and the MIL light s up when the same malfunction occurs in two consec-
utive trips. If a 1st trip DTC is stored and a non-diagnostic operation is performed between the 1st and 2nd
trips, only the 1st trip DTC will continue to be stored. Fo r malfunctions that blink or light up the MIL during the
1st trip, the DTC and 1st trip DTC are stored in the ECM memory.
Procedures for clearing the DTC and the 1st trip DT C from the ECM memory are described in "HOW TO
ERASE EMISSION-RELATED DI AGNOSTIC INFORMATION".
For malfunctions in which 1st trip DTCs are displa yed, refer to "EMISSION-RELATED DIAGNOSTIC INFOR-
MATION ITEMS". These items are required by legal regulations to continuously monitor the system/compo-
nent. In addition, the items monitored non-cont inuously are also displayed on CONSULT-III.
1st trip DTC is specified in Service $07 of SAE J1979. 1st trip DTC detection occurs without lighting up the MIL
and therefore does not warn the driver of a malfunction. However, 1st trip DTC detection will not prevent the
vehicle from being tested, for example during Inspection/Maintenance (I/M) tests.
When a 1st trip DTC is detected, check, print out or write down and erase (1st trip) DTC and Freeze Frame
data as specified in Work Flow procedure Step 2, refer to EC-8, "
Trouble Diagnosis Introduction". Then per-
form DTC Confirmation Procedure or Overall Function Check to try to duplicate the malfunction. If the mal-
function is duplicated, the item requires repair.
How to Read DTC and 1st Trip DTC
DTC and 1st trip DTC can be read by the following methods.
With CONSULT-III
With GST
CONSULT-III or GST (Generic Scan Tool ) Examples: P0340, P0850, P1148, etc.
These DTCs are prescribed by SAE J2012.
(CONSULT-III also displays the malfunctioning component or system.)
No Tools
The number of blinks of the MIL in the Diagnostic Test Mode II (Self-Diagnostic Results) indicates the DTC.
Example: 0340, 0850, 1148, etc.
These DTCs are controlled by NISSAN.
• 1st trip DTC No. is the same as DTC No.
• Output of a DTC indicates a malfunct ion. However, GST or the Diagnostic Test Mode II do not indi-
cate whether the malfunction is still occurring or h as occurred in the past and has returned to nor-
mal. CONSULT-III can identify ma lfunction status as shown below. Therefore, using CONSULT-III (if
available) is recommended.
DTC or 1st trip DTC of a malfunction is display ed in SELF-DIAGNOSTIC RESULTS mode of CONSULT-III.
Time data indicates how many times the vehicle was driven after the last detection of a DTC.
If the DTC is being detected currently, the time data will be [0].
If a 1st trip DTC is stored in t he ECM, the time data will be [1t].
FREEZE FRAME DATA AND 1ST TRIP FREEZE FRAME DATA
The ECM records the driving conditions such as fuel system status, calculated load value, engine coolant tem-
perature, short term fuel trim, long term fuel trim, engine speed, vehicle speed, absolute throttle position, base
fuel schedule and intake air temperature at the moment a malfunction is detected.
Engine operating condition in fail-safe mode Engine speed will not rise more than 2,500 rpm due to the fuel cut
Revision: March 2010 2008 QX56
Page 1355 of 4083
![INFINITI QX56 2008 Factory Workshop Manual EC-56
< FUNCTION DIAGNOSIS >[VK56DE]
ON BOARD DIAGNOSTIC (OBD) SYSTEM
When there is an open circuit on MIL circuit, the ECM c
annot warn the driver by lighting up MIL when there is
malfunction on engi INFINITI QX56 2008 Factory Workshop Manual EC-56
< FUNCTION DIAGNOSIS >[VK56DE]
ON BOARD DIAGNOSTIC (OBD) SYSTEM
When there is an open circuit on MIL circuit, the ECM c
annot warn the driver by lighting up MIL when there is
malfunction on engi](/img/42/57030/w960_57030-1354.png)
EC-56
< FUNCTION DIAGNOSIS >[VK56DE]
ON BOARD DIAGNOSTIC (OBD) SYSTEM
When there is an open circuit on MIL circuit, the ECM c
annot warn the driver by lighting up MIL when there is
malfunction on engine control system.
Therefore, when electrical controlled throttle and part of ECM related diagnoses are continuously detected as
NG for 5 trips, ECM warns the driver that engine cont rol system malfunctions and MIL circuit is open by means
of operating fail-safe function.
The fail-safe function also operates when above diagnos es except MIL circuit are detected and demands the
driver to repair the malfunction.
MIL Flashing Without DTC
When any SRT codes are not set, MIL may fl ash without DTC. For the details, refer to EC-462, "DTC Index".
HOW TO SWITCH DIAGNOSTIC TEST MODE
NOTE:
•It is better to count the ti me accurately with a clock.
• It is impossible to switch the di agnostic mode when an accelerator pedal position sensor circuit has
a malfunction.
• Always ECM returns to Diagnostic Test Mode I after ignition switch is turned OFF.
How to Set Diagnostic Test Mode II (Self-diagnostic Results)
1. Confirm that accelerator pedal is fully releas ed, turn ignition switch ON and wait 3 seconds.
2. Repeat the following procedure quickly five times within 5 seconds.
a. Fully depress the accelerator pedal.
b. Fully release the accelerator pedal.
3. Wait 7 seconds, fully depress the accelerator pedal and keep it for approx. 10 seconds until the MIL starts blinking.
NOTE:
Do not release the accelerator pedal for 10 seconds if MIL may start blinking on the halfway of this
10 seconds. This blinking is displaying SRT status and is continued for another 10 seconds. For
the details, refer to EC-462, "
DTC Index".
Diagnostic Test
ModeKEY and ENG.
Status Function
Explanation of Function
Mode I Ignition switch in
ON position
Engine stopped BULB CHECK
This function checks the MIL bulb for damage (blown, open
circuit, etc.).
If the MIL does not come on, check MIL circuit.
Engine running MALFUNCTION WARNING This is a usual driving condition. When a malfunction is de-
tected twice in two consecutive driving cycles (two trip de-
tection logic), the MIL will light up to inform the driver that a
malfunction has been detected.
The following malfunctions will light up or blink the MIL in
the 1st trip.
• Misfire (Possible three way catalyst damage)
• One trip detection diagnoses
Mode II Ignition switch in
ON position
Engine stopped SELF-DIAGNOSTIC
RESULTS
This function allows DTCs an
d 1st trip DTCs to be read.
Engine operating condition in fail-safe mode Engine speed will not rise more than 2,500 rpm due to the fuel cut
Revision: March 2010 2008 QX56
Page 1367 of 4083
![INFINITI QX56 2008 Factory Workshop Manual EC-68
< FUNCTION DIAGNOSIS >[VK56DE]
ON BOARD DIAGNOSTIC (OBD) SYSTEM
TP SEN 1-B1 [V]
××
• The throttle position sensor signal volt-
age is displayed. • TP SEN 2-B1 signal is converted by
ECM i INFINITI QX56 2008 Factory Workshop Manual EC-68
< FUNCTION DIAGNOSIS >[VK56DE]
ON BOARD DIAGNOSTIC (OBD) SYSTEM
TP SEN 1-B1 [V]
××
• The throttle position sensor signal volt-
age is displayed. • TP SEN 2-B1 signal is converted by
ECM i](/img/42/57030/w960_57030-1366.png)
EC-68
< FUNCTION DIAGNOSIS >[VK56DE]
ON BOARD DIAGNOSTIC (OBD) SYSTEM
TP SEN 1-B1 [V]
××
• The throttle position sensor signal volt-
age is displayed. • TP SEN 2-B1 signal is converted by
ECM internally. Thus, it differs from
ECM terminal voltage signal.
TP SEN 2-B1 [V]
×
FUEL T/TMP SE
[ ° C] or [ °F] × • The fuel temperature (determined by the
signal voltage of the fuel tank tempera-
ture sensor) is displayed.
INT/A TEMP SE
[ ° C] or [ °F] ×× • The intake air temperature (determined
by the signal voltage of the intake air
temperature sensor) is indicated.
EVAP SYS PRES
[V] ×
• The signal voltage of EVAP control sys-
tem pressure sensor is displayed.
FUEL LEVEL SE [V] ו The signal voltage of the fuel level sen-
sor is displayed.
START SIGNAL
[ON/OFF] ×ו Indicates start signal status [ON/OFF]
computed by the ECM according to the
signals of engine speed and battery volt-
age. • After starting the engine, [OFF] is dis-
played regardless of the starter signal.
CLSD THL POS
[ON/OFF] ×ו Indicates idle position [ON/OFF] comput-
ed by ECM according to the accelerator
pedal position sensor signal.
AIR COND SIG
[ON/OFF] ×ו Indicates [ON/OFF] condition of the air
conditioner switch as determined by the
air conditioner signal.
P/N POSI SW
[ON/OFF] ××
• Indicates [ON/OFF] condition from the
park/neutral position (PNP) signal.
PW/ST SIGNAL
[ON/OFF] ×ו [ON/OFF] condition of the power steering
system (determined by the signal voltage
of the power steering pressure sensor
signal) is indicated.
LOAD SIGNAL [ON/
OFF] ×ו Indicates [ON/OFF] condition from the
electrical load signal.
ON: Rear window defogger switch is ON
and/or lighting switch is in 2nd position.
OFF: Both rear window defogger switch
and lighting switch are OFF.
IGNITION SW
[ON/OFF] ו Indicates [ON/OFF] condition from igni-
tion switch signal.
HEATER FAN SW
[ON/OFF] ×
• Indicates [ON/OFF] condition from heat-
er fan switch signal.
BRAKE SW
[ON/OFF] ו Indicates [ON/OFF] condition from the
stop lamp switch signal.
INJ PULSE-B1
[msec] ×
• Indicates the actual fuel injection pulse
width compensated by ECM according to
the input signals. • When the engine is stopped, a certain
computed value is indicated.
INJ PULSE-B2
[msec]
IGN TIMING [BT-
DC] ו
Ind
ic
ates the ignition timing computed by
ECM according to the input signals. • When the engine is stopped, a certain
value is indicated.
CAL/LD VALUE [%] • “Calculated load value” indicates the val-
ue of the current air flow divided by peak
air flow.
MASS AIRFLOW
[g·m/s] • Indicates the mass air flow computed by
ECM according to the signal voltage of
the mass air flow sensor.
Monitored item
[Unit] ECM IN-
PUT SIG-
NALS MAIN
SIGNALS Description
Remarks
Revision: March 2010 2008 QX56