height adjustment INFINITI QX56 2009 Factory User Guide
[x] Cancel search | Manufacturer: INFINITI, Model Year: 2009, Model line: QX56, Model: INFINITI QX56 2009Pages: 4171, PDF Size: 84.65 MB
Page 1283 of 4171
![INFINITI QX56 2009 Factory User Guide
FRONT FINAL DRIVEDLN-227
< DISASSEMBLY AND ASSEMBLY > [FRONT FINAL DRIVE: M205]
C
EF
G H
I
J
K L
M A
B
DLN
N
O P
2. Using feeler gauges, measure the clearance between the side gear back and different INFINITI QX56 2009 Factory User Guide
FRONT FINAL DRIVEDLN-227
< DISASSEMBLY AND ASSEMBLY > [FRONT FINAL DRIVE: M205]
C
EF
G H
I
J
K L
M A
B
DLN
N
O P
2. Using feeler gauges, measure the clearance between the side gear back and different](/img/42/57031/w960_57031-1282.png)
FRONT FINAL DRIVEDLN-227
< DISASSEMBLY AND ASSEMBLY > [FRONT FINAL DRIVE: M205]
C
EF
G H
I
J
K L
M A
B
DLN
N
O P
2. Using feeler gauges, measure the clearance between the side gear back and differential case at three different points, while
rotating the side gear. Average the three readings to calculate
the clearance. (Measure the clearanc e of the other side as well.)
If the side gear back clearance is outside of the specification, use a thicker or thinner side gear thrust washer to adjust.
Refer to DLN-234, "Inspection and Adjustment"
.
CAUTION:
Insert feeler gauges with the same thickness on both
sides to prevent side gear from tilting.
Each gear should rotate smoothly without excessive
resistance during differential motion.
Select a side gear thrust washer for right and left individually.
NOTE:
Side gear back clearance is clearance between side gear and differential case for adjusting side gear
backlash.
Drive Pinion Height
Drive gear and drive pinion are supplied in matched sets only.
Matching numbers on both drive pinion and drive gear are etched
for verification. If a new gear set is being used, verify the numbers
of each drive pinion and drive gear before proceeding with assem-
bly.
The mounting distance from the centerline of the drive gear to the back face of the drive pinion for the M205
final drive assembly is 103.5 mm (4.0748 inches).
On the button end of each drive pinion, there is etched a plus (+) number, a minus (-) number, or a zero (0),
which indicates the best running position for each partic ular gear set. This dimension is controlled by a
selective drive pinion height adjusting washer between t he drive pinion rear bearing inner race and drive pin-
ion.
For example: If a drive pinion is etched m+8 (+3), it would require 0.08 mm (0.003 inch) less drive pinion
height adjusting washer than a drive pinion etched “0”. This means decreasing drive pinion height adjusting
washer thickness; increases the m ounting distance of the drive pinion to 103.6 mm (4.0778 inches). If a
drive pinion is etched m-8 (-3), it would require adding 0.08 mm (0.003 inch) more to the drive pinion height
adjusting washer than would be required if the drive pinion were etched “0”. By adding 0.08 mm (0.003 inch),
the mounting distance of the drive pinion was decreased to 103.4 mm (4.0718 inches) which is just what a
m-8 (-3) etching indicated.
To change the drive pinion height, use different drive pinion height adjusting washers which come in different thickness.
Use the following tables as a guide for selecting the correct drive pinion height adjusting washer thickness to
add or subtract from the old drive pinion height adjusting washer. Side gear back
clearance
: Refer to
DLN-234, "Inspection
and Adjustment"
If the side gear back clearance is greater than
specification:
Use a thicker side gear thrust washer.
If the side gear back clearance is less than spec-
ification: Use a thinner side gear thrust washer.
PDIA0576E
SDIA2241E
Revision: December 20092009 QX56
Page 1290 of 4171
![INFINITI QX56 2009 Factory User Guide
DLN-234
< SERVICE DATA AND SPECIFICATIONS (SDS) [FRONT FINAL DRIVE: M205]
SERVICE DATA AND SPECIFICATIONS (SDS)
SERVICE DATA AND SPECIFICATIONS (SDS)
SERVICE DATA AND SPECIFICATIONS (SDS)
General Spe INFINITI QX56 2009 Factory User Guide
DLN-234
< SERVICE DATA AND SPECIFICATIONS (SDS) [FRONT FINAL DRIVE: M205]
SERVICE DATA AND SPECIFICATIONS (SDS)
SERVICE DATA AND SPECIFICATIONS (SDS)
SERVICE DATA AND SPECIFICATIONS (SDS)
General Spe](/img/42/57031/w960_57031-1289.png)
DLN-234
< SERVICE DATA AND SPECIFICATIONS (SDS) [FRONT FINAL DRIVE: M205]
SERVICE DATA AND SPECIFICATIONS (SDS)
SERVICE DATA AND SPECIFICATIONS (SDS)
SERVICE DATA AND SPECIFICATIONS (SDS)
General SpecificationINFOID:0000000004193547
Inspection and AdjustmentINFOID:0000000004193548
DRIVE GEAR RUNOUT
Unit: mm (in)
SIDE GEAR CLEARANCE
Unit: mm (in)
PRELOAD TORQUE
Unit: N·m (kg-m, in-lb)
BACKLASH
Unit: mm (in)
COMPANION FLANGE RUNOUT
Unit: mm (in)
SELECTIVE PARTS
Drive Pinion Height Adjusting Washer
Applied model4WD
VK56DE
A/T
Final drive model M205
Gear ratio 3.357
Number of teeth (Drive gear/Drive pinion) 47/14
Differential gear oil capacity (Approx.) 1.6 (3 3/8 US pt, 2 7/8 Imp pt)
Number of pinion gears 2
Drive pinion adjustment spacer type Collapsible
Item Limit
Drive gear back face 0.08 (0.0031) or less
Item Standard
Side gear back clearance (Clearance between side gear and dif-
ferential case for adjusting side gear backlash) 0.20 (0.0079) or less
(Each gear should rotate smoothly without excessive resistance during differential motion.)
Item Standard
Drive pinion bearing preload torque 2.3 - 3.4 (0.24 - 0.34, 21 - 30)
Total preload torque
(Total preload torque = drive pinion bearing preload torque + side
bearing preload torque). 2.98 - 4.76 (0.31 - 0.48, 27 - 42)
Item Standard
Drive gear to drive pinion backlash 0.12 - 0.20 (0.0050 - 0.0078)
Item Limit
Companion flange face 0.10 (0.0039) or less
Companion flange inner side 0.13 (0.0051) or less
Revision: December 20092009 QX56
Page 1310 of 4171
![INFINITI QX56 2009 Factory User Guide
DLN-254
< DISASSEMBLY AND ASSEMBLY >[REAR FINAL DRIVE: R230]
REAR FINAL DRIVE
ASSEMBLY INSPECTION AND ADJUSTMENT
Drain the differential gear oil before inspection and adjustment. Refer to
DLN-244, INFINITI QX56 2009 Factory User Guide
DLN-254
< DISASSEMBLY AND ASSEMBLY >[REAR FINAL DRIVE: R230]
REAR FINAL DRIVE
ASSEMBLY INSPECTION AND ADJUSTMENT
Drain the differential gear oil before inspection and adjustment. Refer to
DLN-244,](/img/42/57031/w960_57031-1309.png)
DLN-254
< DISASSEMBLY AND ASSEMBLY >[REAR FINAL DRIVE: R230]
REAR FINAL DRIVE
ASSEMBLY INSPECTION AND ADJUSTMENT
Drain the differential gear oil before inspection and adjustment. Refer to
DLN-244, "Changing Differential
Gear Oil".
Remove and install the carrier cover as neces sary for inspection and adjustment. Refer to DLN-249,
"Removal and Installation".
Total Preload Torque
1. Remove the side flanges if necessary. Refer to DLN-247, "Removal and Installation".
CAUTION:
The side flanges must removed in or der to measure total preload torque.
2. Rotate the drive pinion back and forth 2 to 3 times to check for unusual noise and rotation malfunction.
3. Rotate the drive pinion at least 20 times to check for smooth operation of the bearings.
4. Measure the total preload torque using Tool.
NOTE:
Total preload torque = Drive pinion bearing preload torque +
Side bearing preload torque
If the measured value is out of the specification, check and adjust each part. Adjust the drive pinion
bearing preload torque first, then adjust the side bearing preload torque.
CAUTION:
Select a side bearing adjusting wash er for right and left individually.
Drive Gear Runout
1. Drive pinion lock nut 2. Companion flange 3. Front oil seal
4. Drive pinion front bearing 5. Collapsible spacer 6. Drive pinion rear bearing
7. Drive pinion height adjusting washer 8. Drive pinion 9. Gear carrier
10. Drive gear 11. Pinion mate shaft 12. Lock pin
13. Pinion mate gear 14. Pinion mate thrust washer 15. Side gear
16. Side gear thrust washer 17. Differential case 18. Side bearing
19. Side bearing adjusting washer 20. Bearing cap 21. Carrier cover
22. Filler plug 23. Drain plug 24. Side oil seal
Tool number : ST3127S000 (J-25765-A)
Total preload torque
: Refer to DLN-270, "Inspection and Adjustment"
SPD884
If the total preload torque is greater than specification
On drive pinion bearings: R eplace the collapsible spacer.
On side bearings: Use thinner side b earing adjusting washers by the same
amount on each side. Refer to DLN-270, "Inspection and Adjust-
ment".
If the total preload torque is less than specification On drive pinion bearings: Tighten the drive pinion lock nut.
On side bearings: Use thicker side b earing adjusting washers by the same
amount on each side. Refer to DLN-270, "Inspection and Ad-
justment".
Revision: December 20092009 QX56
Page 1311 of 4171
![INFINITI QX56 2009 Factory User Guide
REAR FINAL DRIVEDLN-255
< DISASSEMBLY AND ASSEMBLY > [REAR FINAL DRIVE: R230]
C
EF
G H
I
J
K L
M A
B
DLN
N
O P
1. Fit a dial indicator to the drive gear back face.
2. Rotate the drive gear to measure INFINITI QX56 2009 Factory User Guide
REAR FINAL DRIVEDLN-255
< DISASSEMBLY AND ASSEMBLY > [REAR FINAL DRIVE: R230]
C
EF
G H
I
J
K L
M A
B
DLN
N
O P
1. Fit a dial indicator to the drive gear back face.
2. Rotate the drive gear to measure](/img/42/57031/w960_57031-1310.png)
REAR FINAL DRIVEDLN-255
< DISASSEMBLY AND ASSEMBLY > [REAR FINAL DRIVE: R230]
C
EF
G H
I
J
K L
M A
B
DLN
N
O P
1. Fit a dial indicator to the drive gear back face.
2. Rotate the drive gear to measure runout.
If the runout is outside of the limit , check the condition of the drive
gear assembly. Foreign material may be caught between the drive
gear and differential case, or the differential case or drive gear may
be deformed.
CAUTION:
Replace drive gear and drive pinion as a set.
Tooth Contact
1. Apply red lead to the drive gear. NOTE:
Apply red lead to both faces of thr ee to four gears, at four loca-
tions evenly spaced on the drive gear.
2. Rotate the drive gear back and forth several times. Then check for correct drive pinion to drive gear tooth contact as shown.
CAUTION:
Check tooth contact on dri ve side and reverse side.
3. If the tooth contact is improper ly adjusted, follow the procedure
below to adjust the pinion height (dimension X). Runout limit : Refer to
DLN-270, "Inspection
and Adjustment"
SPD886
SPD357
SDIA0570E
SDIA0517E
Revision: December 20092009 QX56
Page 1312 of 4171
![INFINITI QX56 2009 Factory User Guide
DLN-256
< DISASSEMBLY AND ASSEMBLY >[REAR FINAL DRIVE: R230]
REAR FINAL DRIVE
If the tooth contact is near the face (face contact), or near the heel
(heel contact), use a thicker drive pinion heigh INFINITI QX56 2009 Factory User Guide
DLN-256
< DISASSEMBLY AND ASSEMBLY >[REAR FINAL DRIVE: R230]
REAR FINAL DRIVE
If the tooth contact is near the face (face contact), or near the heel
(heel contact), use a thicker drive pinion heigh](/img/42/57031/w960_57031-1311.png)
DLN-256
< DISASSEMBLY AND ASSEMBLY >[REAR FINAL DRIVE: R230]
REAR FINAL DRIVE
If the tooth contact is near the face (face contact), or near the heel
(heel contact), use a thicker drive pinion height adjusting washers
to move the drive pinion closer to the drive gear.
Refer to DLN-270, "Inspection and Adjustment"
.
If the tooth contact is near the flank (flank contact), or near the toe (toe contact), use a thinner drive pinion height adjusting washers to
move the drive pinion farther from the drive gear.
Refer to DLN-270, "Inspection and Adjustment"
.
Backlash
1. Fit a dial indicator to the drive gear face to measure the back-
lash.
If the backlash is outside of the specification, change the thickness of the side bearing adjusting washers.
CAUTION:
Do not change the total thickness of side bearing adjusting washers as it will change the side bearing
preload torque.
Companion Flange Runout
PDIA0440E
PDIA0441E
Backlash : Refer to DLN-270, "Inspection and
Adjustment"
If the backlash is greater than specification:
Make side bearing adjusting washer thicker on drive
gear back side, and side bearing adjusting washer
thinner on drive gear toot h side by the same amount.
Refer to DLN-270, "Inspection and Adjustment"
.
If the backlash is less than specification: Make side bearing adjusting washer thinner on drive
gear back side, and side bearing adjusting washer
thicker on drive gear tooth side by the same amount.
Refer to DLN-270, "Inspection and Adjustment"
.
SPD513
Revision: December 20092009 QX56
Page 1320 of 4171
![INFINITI QX56 2009 Factory User Guide
DLN-264
< DISASSEMBLY AND ASSEMBLY >[REAR FINAL DRIVE: R230]
REAR FINAL DRIVE
7. If the pulling force is outside the specification, use a thicker or
thinner side bearing adjusting washer to adjust. R INFINITI QX56 2009 Factory User Guide
DLN-264
< DISASSEMBLY AND ASSEMBLY >[REAR FINAL DRIVE: R230]
REAR FINAL DRIVE
7. If the pulling force is outside the specification, use a thicker or
thinner side bearing adjusting washer to adjust. R](/img/42/57031/w960_57031-1319.png)
DLN-264
< DISASSEMBLY AND ASSEMBLY >[REAR FINAL DRIVE: R230]
REAR FINAL DRIVE
7. If the pulling force is outside the specification, use a thicker or
thinner side bearing adjusting washer to adjust. Refer to DLN-
270, "Inspection and Adjustment".
CAUTION:
Select a side bearing adjust ing washer for right and left
individually.
8. Record the total amount of washer thickness required for the correct side bearing preload torque.
ASSEMBLY
Drive Pinion Assembly
1. Install the drive pinion front and rear bearing outer races using
Tools.
CAUTION:
Do not reuse drive pinion fron t and rear bearing outer race.
2. Select a drive pinion height adjusting washer. Refer to DLN-270, "Inspection and Adjustment"
.
3. Install the selected drive pinion height adjusting washer to the drive pinion. Press the drive pinion rear bearing inner race to it
using Tool.
CAUTION:
Install the drive pinion hei ght adjusting washer in the
proper direction as shown.
Do not reuse drive pinion rear bearing inner race. If the pulling force is
less than the specification:
Use a thicker side bear ing adjusting washer.
If the pulling force is gr eater than the specification:
Use a thinner side bear ing adjusting washer.
SPD772
Tool number A: ST15310000 ( — )
B: ST35325000 ( — )
C: ST30621000 ( — )
SPD992
Tool number : ST30022000 ( — )
SPD377
Revision: December 20092009 QX56
Page 1708 of 4171
![INFINITI QX56 2009 Factory User Guide
P2A00, P2A03 A/F SENSOR 1EC-381
< COMPONENT DIAGNOSIS > [VK56DE]
C
D
E
F
G H
I
J
K L
M A
EC
NP
O
5. Also check harness for short to power.
OK or NG
OK >> GO TO 9.
NG >> Repair open circuit or short t INFINITI QX56 2009 Factory User Guide
P2A00, P2A03 A/F SENSOR 1EC-381
< COMPONENT DIAGNOSIS > [VK56DE]
C
D
E
F
G H
I
J
K L
M A
EC
NP
O
5. Also check harness for short to power.
OK or NG
OK >> GO TO 9.
NG >> Repair open circuit or short t](/img/42/57031/w960_57031-1707.png)
P2A00, P2A03 A/F SENSOR 1EC-381
< COMPONENT DIAGNOSIS > [VK56DE]
C
D
E
F
G H
I
J
K L
M A
EC
NP
O
5. Also check harness for short to power.
OK or NG
OK >> GO TO 9.
NG >> Repair open circuit or short to ground or short to power in harness or connectors.
9.CHECK A/F SENSOR 1 HEATER
Refer to EC-96, "Component Inspection"
.
OK or NG
OK >> GO TO 10.
NG >> GO TO 11.
10.CHECK INTERMITTENT INCIDENT
Perform GI-35, "How to Check Terminal"
and GI-38, "Intermittent Incident".
OK or NG
OK >> GO TO 11.
NG >> Repair or replace.
11 .REPLACE AIR FUEL RATIO (A/F) SENSOR 1
Replace malfunctioning air f uel ratio (A/F) sensor 1.
CAUTION:
Discard any A/F sensor which has been dropped from a height of more than 0.5 m (19.7 in) onto a
hard surface such as a concrete floor; use a new one.
Before installing new A/F senso r, clean exhaust system threads using Oxygen Sensor Thread
Cleaner tool J-43897-18 or J-43897-12 and approved anti-seize lubricant.
>> GO TO 12.
12.CONFIRM A/F ADJUSTMENT DATA
1. Turn ignition switch OFF and then ON.
2. Select “A/F ADJ-B1” and “” in “DATA MONITOR” mode with CONSULT-lll.
3. Make sure that “0.000” is displayed on CONSULT-lll screen.
OK or NG
OK >> INSPECTION END
NG >> GO TO 13.
13.CLEAR THE SELF-LEARNING DATA
With CONSULT-lll
1. Start engine and warm it up to normal operating temperature.
2. Select “SELF-LEARNING CONT” in “WORK SUPPORT” mode with CONSULT-lll.
3. Clear the self-learning control coefficient by touching “CLEAR”.
Without CONSULT-lll
1. Start engine and warm it up to normal operating temperature.
2. Turn ignition switch OFF.
Bank 1 Bank 2
A/F sensor 1 terminal ECM terminal A/F sensor 1 terminal ECM terminal 135116
256275
Continuity should not exist.
Revision: December 20092009 QX56
Page 2093 of 4171
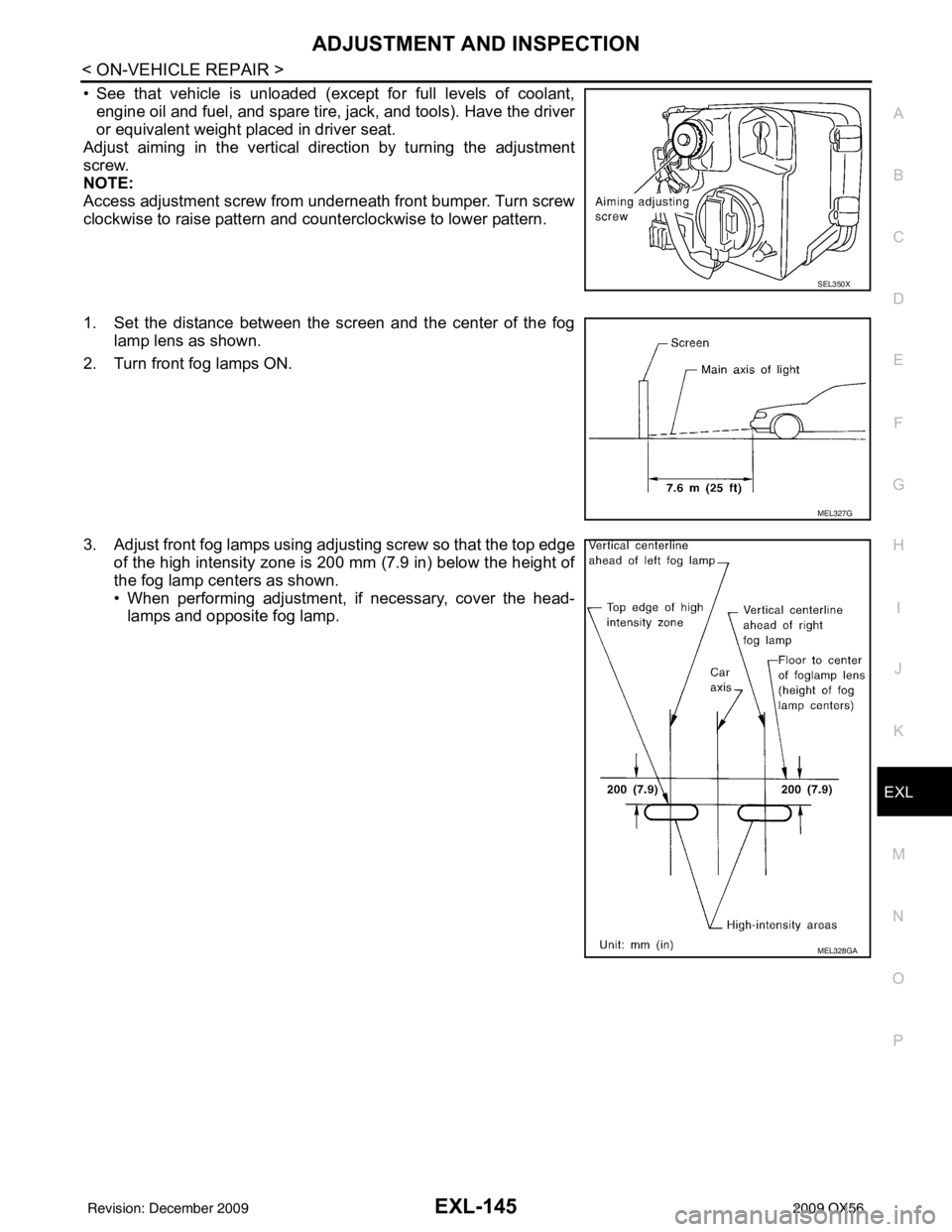
ADJUSTMENT AND INSPECTIONEXL-145
< ON-VEHICLE REPAIR >
C
DE
F
G H
I
J
K
M A
B
EXL
N
O P
• See that vehicle is unloaded (except for full levels of coolant, engine oil and fuel, and spare tire, jack, and tools). Have the driver
or equivalent weight placed in driver seat.
Adjust aiming in the vertical direction by turning the adjustment
screw.
NOTE:
Access adjustment screw from underneath front bumper. Turn screw
clockwise to raise pattern and c ounterclockwise to lower pattern.
1. Set the distance between the screen and the center of the fog lamp lens as shown.
2. Turn front fog lamps ON.
3. Adjust front fog lamps using adjusting screw so that the top edge of the high intensity zone is 200 mm (7.9 in) below the height of
the fog lamp centers as shown.
• When performing adjustment, if necessary, cover the head-lamps and opposite fog lamp.
SEL350X
MEL327G
MEL328GA
Revision: December 20092009 QX56
Page 2176 of 4171
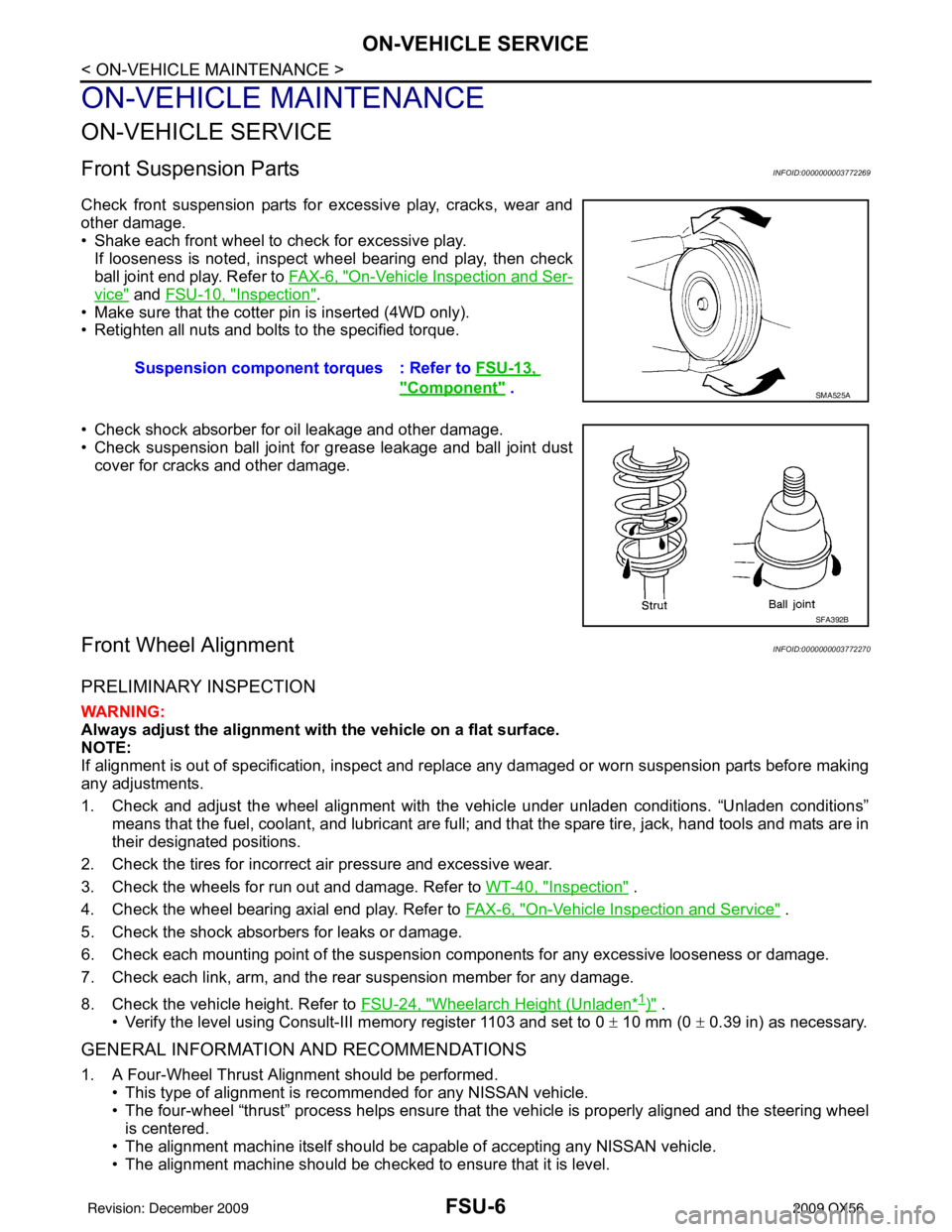
FSU-6
< ON-VEHICLE MAINTENANCE >
ON-VEHICLE SERVICE
ON-VEHICLE MAINTENANCE
ON-VEHICLE SERVICE
Front Suspension PartsINFOID:0000000003772269
Check front suspension parts for excessive play, cracks, wear and
other damage.
• Shake each front wheel to check for excessive play.If looseness is noted, inspect wheel bearing end play, then check
ball joint end play. Refer to FA X - 6 , "
On-Vehicle Inspection and Ser-
vice" and FSU-10, "Inspection".
• Make sure that the cotter pin is inserted (4WD only).
• Retighten all nuts and bolts to the specified torque.
• Check shock absorber for oil leakage and other damage.
• Check suspension ball joint for grease leakage and ball joint dust cover for cracks and other damage.
Front Wheel AlignmentINFOID:0000000003772270
PRELIMINARY INSPECTION
WARNING:
Always adjust the alignment with the vehicle on a flat surface.
NOTE:
If alignment is out of specificat ion, inspect and replace any damaged or worn suspension parts before making
any adjustments.
1. Check and adjust the wheel alignment with the vehicle under unladen conditions. “Unladen conditions”
means that the fuel, coolant, and lubricant are full; and that the spare tire, jack, hand tools and mats are in
their designated positions.
2. Check the tires for incorrect air pressure and excessive wear.
3. Check the wheels for run out and damage. Refer to WT-40, "
Inspection" .
4. Check the wheel bearing axial end play. Refer to FA X - 6 , "
On-Vehicle Inspection and Service" .
5. Check the shock absorbers for leaks or damage.
6. Check each mounting point of the suspension components for any excessive looseness or damage.
7. Check each link, arm, and the rear suspension member for any damage.
8. Check the vehicle height. Refer to FSU-24, "
Wheelarch Height (Unladen*1)" .
• Verify the level using Consult-III memory register 1103 and set to 0 ± 10 mm (0 ± 0.39 in) as necessary.
GENERAL INFORMATION AND RECOMMENDATIONS
1. A Four-Wheel Thrust Alignment should be performed.
• This type of alignment is recommended for any NISSAN vehicle.
• The four-wheel “thrust” process helps ensure that the vehicle is properly aligned and the steering wheel
is centered.
• The alignment machine itself should be ca pable of accepting any NISSAN vehicle.
• The alignment machine should be checked to ensure that it is level. Suspension component
torques : Refer to FSU-13,
"Component" . SMA525A
SFA392B
Revision: December 20092009 QX56
Page 3144 of 4171
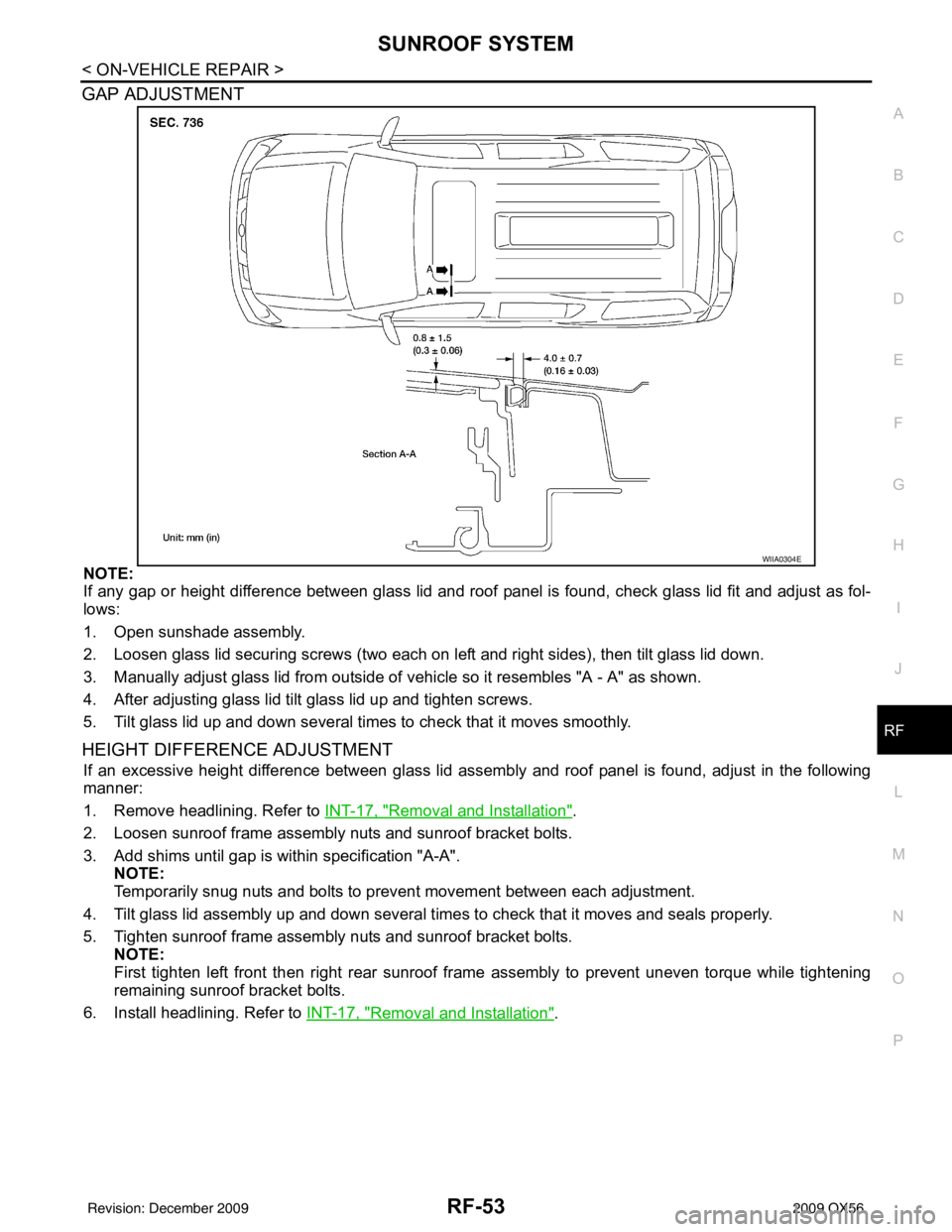
SUNROOF SYSTEMRF-53
< ON-VEHICLE REPAIR >
C
DE
F
G H
I
J
L
M A
B
RF
N
O P
GAP ADJUSTMENT
NOTE:
If any gap or height difference between glass lid and roof panel is found, check glass lid fit and adjust as fol-
lows:
1. Open sunshade assembly.
2. Loosen glass lid securing screws (two each on left and right sides), then tilt glass lid down.
3. Manually adjust glass lid from outside of v ehicle so it resembles "A - A" as shown.
4. After adjusting glass lid tilt glass lid up and tighten screws.
5. Tilt glass lid up and down several times to check that it moves smoothly.
HEIGHT DIFFERE NCE ADJUSTMENT
If an excessive height difference between glass lid assemb ly and roof panel is found, adjust in the following
manner:
1. Remove headlining. Refer to INT-17, "
Removal and Installation".
2. Loosen sunroof frame assembly nuts and sunroof bracket bolts.
3. Add shims until gap is within specification "A-A". NOTE:
Temporarily snug nuts and bolts to prevent movement between each adjustment.
4. Tilt glass lid assembly up and down several times to check that it moves and seals properly.
5. Tighten sunroof frame assembly nuts and sunroof bracket bolts. NOTE:
First tighten left front then right rear sunroof frame assembly to prevent uneven torque while tightening
remaining sunroof bracket bolts.
6. Install headlining. Refer to INT-17, "
Removal and Installation".
WIIA0304E
Revision: December 20092009 QX56