height INFINITI QX56 2009 Factory Owner's Guide
[x] Cancel search | Manufacturer: INFINITI, Model Year: 2009, Model line: QX56, Model: INFINITI QX56 2009Pages: 4171, PDF Size: 84.65 MB
Page 1472 of 4171
![INFINITI QX56 2009 Factory Owners Guide
P0132, P0152 A/F SENSOR 1EC-145
< COMPONENT DIAGNOSIS > [VK56DE]
C
D
E
F
G H
I
J
K L
M A
EC
NP
O
Check the following.
Harness connectors E5, F14
IPDM E/R harness connector E119
15A fuse
Harne INFINITI QX56 2009 Factory Owners Guide
P0132, P0152 A/F SENSOR 1EC-145
< COMPONENT DIAGNOSIS > [VK56DE]
C
D
E
F
G H
I
J
K L
M A
EC
NP
O
Check the following.
Harness connectors E5, F14
IPDM E/R harness connector E119
15A fuse
Harne](/img/42/57031/w960_57031-1471.png)
P0132, P0152 A/F SENSOR 1EC-145
< COMPONENT DIAGNOSIS > [VK56DE]
C
D
E
F
G H
I
J
K L
M A
EC
NP
O
Check the following.
Harness connectors E5, F14
IPDM E/R harness connector E119
15A fuse
Harness for open or short between A/F sensor 1 and fuse
>> Repair or replace harness or connectors.
4.CHECK A/F SENSOR 1 INPUT SIGNAL CIRCUIT FOR OPEN AND SHORT
1. Turn ignition switch OFF.
2. Disconnect ECM harness connector.
3. Check harness continuity between A/F sensor 1 terminal and ECM terminal as follows. Refer to Wiring Diagram.
4. Check harness continuity between the following terminals and ground. Refer to Wiring Diagram.
5. Also check harness for short to power.
OK or NG
OK >> GO TO 5.
NG >> Repair open circuit or short to ground or short to power in harness or connectors.
5.CHECK INTERMITTENT INCIDENT
Refer to GI-35, "How to Check Terminal"
and GI-38, "Intermittent Incident".
OK or NG
OK >> GO TO 6.
NG >> Repair or replace.
6.REPLACE AIR FUEL RATIO (A/F) SENSOR 1
Replace malfunctioning air f uel ratio (A/F) sensor 1.
CAUTION:
Discard any air fuel ratio (A/F) sensor which has b een dropped from a height of more than 0.5 m
(19.7 in) onto a hard surface such as a concrete floor; use a new one.
Before installing new air fuel ra tio (A/F) sensor, clean exhaust syst em threads (using Oxygen Sensor
Thread Cleaner tool J-43897-18 or J-43897-12) and approved anti-seize lubricant.
>> INSPECTION END
A/F sensor 1 terminal ECM terminal
Bank1 135
256
Bank 2 116
275
Continuity should exist.
Bank 1 Bank 2
A/F sensor 1 terminal ECM terminal A/F sensor 1 terminal ECM terminal 135116
256275
Continuity should not exist.
Revision: December 20092009 QX56
Page 1478 of 4171
![INFINITI QX56 2009 Factory Owners Guide
P0133, P0153 A/F SENSOR 1EC-151
< COMPONENT DIAGNOSIS > [VK56DE]
C
D
E
F
G H
I
J
K L
M A
EC
NP
O
Discard any air fuel ratio (A/F) sensor which has b
een dropped from a height of more than 0.5 m
(19 INFINITI QX56 2009 Factory Owners Guide
P0133, P0153 A/F SENSOR 1EC-151
< COMPONENT DIAGNOSIS > [VK56DE]
C
D
E
F
G H
I
J
K L
M A
EC
NP
O
Discard any air fuel ratio (A/F) sensor which has b
een dropped from a height of more than 0.5 m
(19](/img/42/57031/w960_57031-1477.png)
P0133, P0153 A/F SENSOR 1EC-151
< COMPONENT DIAGNOSIS > [VK56DE]
C
D
E
F
G H
I
J
K L
M A
EC
NP
O
Discard any air fuel ratio (A/F) sensor which has b
een dropped from a height of more than 0.5 m
(19.7 in) onto a hard surface such as a concrete floor; use a new one.
Before installing new air fuel ra tio (A/F) sensor, clean exhaust syst em threads (using Oxygen Sensor
Thread Cleaner tool J-43897-18 or J-43897-12) and approved anti-seize lubricant.
>> INSPECTION END
Revision: December 20092009 QX56
Page 1483 of 4171
![INFINITI QX56 2009 Factory Owners Guide
EC-156
< COMPONENT DIAGNOSIS >[VK56DE]
P0137, P0157 HO2S2
7. Check “HO2S2 (B1)/(B2)” at idle speed when adjusting “FUEL INJECTION” to
±25%.
“HO2S2 (B1)/(B2)” should be above 0.58V at l INFINITI QX56 2009 Factory Owners Guide
EC-156
< COMPONENT DIAGNOSIS >[VK56DE]
P0137, P0157 HO2S2
7. Check “HO2S2 (B1)/(B2)” at idle speed when adjusting “FUEL INJECTION” to
±25%.
“HO2S2 (B1)/(B2)” should be above 0.58V at l](/img/42/57031/w960_57031-1482.png)
EC-156
< COMPONENT DIAGNOSIS >[VK56DE]
P0137, P0157 HO2S2
7. Check “HO2S2 (B1)/(B2)” at idle speed when adjusting “FUEL INJECTION” to
±25%.
“HO2S2 (B1)/(B2)” should be above 0.58V at least once when the “FUEL INJECTION” is +25%.
“HO2S2 (B1)/(B2)” should be below 0.18V at least once when the “FUEL INJECTION” is −25%.
CAUTION:
Discard any heated oxygen sensor which has been dropped from a height of more than 0.5 m (19.7
in) onto a hard surface such as a concrete floor; use a new one.
Before installing new oxygen sensor, clean exh aust system threads using Oxygen Sensor Thread
Cleaner tool J-43897-18 or J-43897-12 and approved anti-seize lubricant.
Without CONSULT-III
1. Start engine and warm it up to the normal operating temperature.
2. Turn ignition switch OFF and wait at least 10 seconds.
3. Start engine and keep the engine speed between 3,500 and 4,000 rpm for at least 1 minute under no load.
4. Let engine idle for 1 minute.
5. Set voltmeter probes between ECM terminal 55 [HO2S2 (B1) signal] or 74\
[HO2S2 (B2) signal] and
ground.
6. Check the voltage when revving up to 4,000 rpm under no load at least 10 times.
(Depress and release accelerator pedal as soon as possible.)
The voltage should be above 0.58V and below 0.18V at least
once during this procedure.
If the voltage can be confirmed at step 6, step 7 is not nec-
essary.
7. Keep vehicle at idling for 10 minutes, then check voltage. Or check the voltage when coasting from 80 km/h (50 MPH) in D
position.
The voltage should be aboce 0.58V and below 0.18V at least
once during this procedure.
8. If NG, replace heated oxygen sensor 2.
CAUTION:
Discard any heated oxygen sensor which has been dropped from a height of more than 0.5 m (19.7
in) onto a hard surface such as a concrete floor; use a new one.
Before installing new oxygen sensor, clean exh aust system threads using Oxygen Sensor Thread
Cleaner tool J-43897-18 or J-43897-12 and approved anti-seize lubricant.
JMBIA0605GB
PBIB2054E
Revision: December 20092009 QX56
Page 1490 of 4171
![INFINITI QX56 2009 Factory Owners Guide
P0138, P0158 HO2S2EC-163
< COMPONENT DIAGNOSIS > [VK56DE]
C
D
E
F
G H
I
J
K L
M A
EC
NP
O
6. Select “FUEL INJECTION” in “ACTIVE TEST” mode,
and select “HO2S2 (B1)/(B2)” as the monitor it INFINITI QX56 2009 Factory Owners Guide
P0138, P0158 HO2S2EC-163
< COMPONENT DIAGNOSIS > [VK56DE]
C
D
E
F
G H
I
J
K L
M A
EC
NP
O
6. Select “FUEL INJECTION” in “ACTIVE TEST” mode,
and select “HO2S2 (B1)/(B2)” as the monitor it](/img/42/57031/w960_57031-1489.png)
P0138, P0158 HO2S2EC-163
< COMPONENT DIAGNOSIS > [VK56DE]
C
D
E
F
G H
I
J
K L
M A
EC
NP
O
6. Select “FUEL INJECTION” in “ACTIVE TEST” mode,
and select “HO2S2 (B1)/(B2)” as the monitor item
with CONSULT-III.
7. Check “HO2S2 (B1)/(B2)” at idle speed when adjusting “FUEL INJECTION” to ±25%.
“HO2S2 (B1)/(B2)” should be above 0.58V at least once when the “FUEL INJECTION” is +25%.
“HO2S2 (B1)/(B2)” should be below 0.18V at least once when the “FUEL INJECTION” is −25%.
CAUTION:
Discard any heated oxygen sensor which has been dr opped from a height of more than 0.5 m (19.7
in) onto a hard surface such as a concrete floor; use a new one.
Before installing new oxygen sensor, clean exh aust system threads using Oxygen Sensor Thread
Cleaner tool J-43897-18 or J-43897-12 and approved anti-seize lubricant.
Without CONSULT-III
1. Start engine and warm it up to the normal operating temperature.
2. Turn ignition switch OFF and wait at least 10 seconds.
3. Start engine and keep the engine speed between 3,500 and 4,000 rpm for at least 1 minute under no load.
4. Let engine idle for 1 minute.
5. Set voltmeter probes between ECM terminal 55 [HO2S2 (B1) signal] or 74 [HO2S2 (B2) signal] and ground.
6. Check the voltage when revving up to 4,000 rpm under no load at least 10 times.
(Depress and release accelerator pedal as soon as possible.)
The voltage should be above 0.58V and below 0.18V at least
once during this procedure.
If the voltage can be confirmed at step 6, step 7 is not nec-
essary.
7. Keep vehicle at idling for 10 minutes, then check voltage. Or check the voltage when coasting from 80 km/h (50 MPH) in D
position.
The voltage should be aboce 0.58V and below 0.18V at least
once during this procedure.
8. If NG, replace heated oxygen sensor 2.
CAUTION:
Discard any heated oxygen sensor which has been dr opped from a height of more than 0.5 m (19.7
in) onto a hard surface such as a concrete floor; use a new one.
Before installing new oxygen sensor, clean exh aust system threads using Oxygen Sensor Thread
Cleaner tool J-43897-18 or J-43897-12 and approved anti-seize lubricant.
JMBIA0605GB
PBIB2054E
Revision: December 20092009 QX56
Page 1495 of 4171
![INFINITI QX56 2009 Factory Owners Guide
EC-168
< COMPONENT DIAGNOSIS >[VK56DE]
P0139, P0159 HO2S2
7. Check “HO2S2 (B1)/(B2)” at idle speed when adjusting “FUEL INJECTION” to
±25%.
“HO2S2 (B1)/(B2)” should be above 0.58V at l INFINITI QX56 2009 Factory Owners Guide
EC-168
< COMPONENT DIAGNOSIS >[VK56DE]
P0139, P0159 HO2S2
7. Check “HO2S2 (B1)/(B2)” at idle speed when adjusting “FUEL INJECTION” to
±25%.
“HO2S2 (B1)/(B2)” should be above 0.58V at l](/img/42/57031/w960_57031-1494.png)
EC-168
< COMPONENT DIAGNOSIS >[VK56DE]
P0139, P0159 HO2S2
7. Check “HO2S2 (B1)/(B2)” at idle speed when adjusting “FUEL INJECTION” to
±25%.
“HO2S2 (B1)/(B2)” should be above 0.58V at least once when the “FUEL INJECTION” is +25%.
“HO2S2 (B1)/(B2)” should be below 0.18V at least once when the “FUEL INJECTION” is −25%.
CAUTION:
Discard any heated oxygen sensor which has been dropped from a height of more than 0.5 m (19.7
in) onto a hard surface such as a concrete floor; use a new one.
Before installing new oxygen sensor, clean exh aust system threads using Oxygen Sensor Thread
Cleaner tool J-43897-18 or J-43897-12 and approved anti-seize lubricant.
Without CONSULT-III
1. Start engine and warm it up to the normal operating temperature.
2. Turn ignition switch OFF and wait at least 10 seconds.
3. Start engine and keep the engine speed between 3,500 and 4,000 rpm for at least 1 minute under no load.
4. Let engine idle for 1 minute.
5. Set voltmeter probes between ECM terminal 55 [HO2S2 (B1) signal] or 74\
[HO2S2 (B2) signal] and
ground.
6. Check the voltage when revving up to 4,000 rpm under no load at least 10 times.
(Depress and release accelerator pedal as soon as possible.)
The voltage should be above 0.58V and below 0.18V at least
once during this procedure.
If the voltage can be confirmed at step 6, step 7 is not nec-
essary.
7. Keep vehicle at idling for 10 minutes, then check voltage. Or check the voltage when coasting from 80 km/h (50 MPH) in D
position.
The voltage should be aboce 0.58V and below 0.18V at least
once during this procedure.
8. If NG, replace heated oxygen sensor 2.
CAUTION:
Discard any heated oxygen sensor which has been dropped from a height of more than 0.5 m (19.7
in) onto a hard surface such as a concrete floor; use a new one.
Before installing new oxygen sensor, clean exh aust system threads using Oxygen Sensor Thread
Cleaner tool J-43897-18 or J-43897-12 and approved anti-seize lubricant.
JMBIA0605GB
PBIB2054E
Revision: December 20092009 QX56
Page 1521 of 4171
![INFINITI QX56 2009 Factory Owners Guide
EC-194
< COMPONENT DIAGNOSIS >[VK56DE]
P0300, P0301, P0302, P
0303, P0304, P0305, P0306, P0307, P0308 MISFIRE
6. Also check harness for short to power.
OK or NG
OK >> GO TO 14.
NG >> Repair open cir INFINITI QX56 2009 Factory Owners Guide
EC-194
< COMPONENT DIAGNOSIS >[VK56DE]
P0300, P0301, P0302, P
0303, P0304, P0305, P0306, P0307, P0308 MISFIRE
6. Also check harness for short to power.
OK or NG
OK >> GO TO 14.
NG >> Repair open cir](/img/42/57031/w960_57031-1520.png)
EC-194
< COMPONENT DIAGNOSIS >[VK56DE]
P0300, P0301, P0302, P
0303, P0304, P0305, P0306, P0307, P0308 MISFIRE
6. Also check harness for short to power.
OK or NG
OK >> GO TO 14.
NG >> Repair open circuit or short to ground or short to power in harness or connectors.
14.CHECK A/F SENSOR 1 HEATER
Refer to EC-96, "Component Inspection"
.
OK or NG
OK >> GO TO 16.
NG >> GO TO 15.
15.REPLACE AIR FUEL RATIO (A/F) SENSOR 1
Replace malfunctioning air fuel ratio (A/F) sensor 1.
CAUTION:
Discard any air fuel ratio (A/F) sensor which has b een dropped from a height of more than 0.5 m
(19.7 in) onto a hard surface such as a concrete floor; use a new one.
Before installing new ai r fuel ratio (A/F) sensor, clean exhaust system threads (using Oxygen Sensor
Thread Cleaner tool J-43897-18 or J-43897-12) and approved anti-seize lubricant.
>> INSPECTION END
16.CHECK MASS AIR FLOW SENSOR
With CONSULT-III
Check mass air flow sensor signal in “DATA MONITOR” mode with CONSULT-III.
With GST
Check mass air flow sensor signal in Service $01 with GST.
OK or NG
OK >> GO TO 17.
NG >> Check connectors for rusted terminals or loose connections in the mass air flow sensor circuit or
ground. Refer to EC-103
.
17.CHECK SYMPTOM MATRIX CHART
Check items on the rough idle symptom in EC-475, "Symptom Matrix Chart"
.
OK or NG
OK >> GO TO 18.
NG >> Repair or replace.
18.ERASE THE 1ST TRIP DTC
Some tests may cause a 1st trip DTC to be set.
Erase the 1st trip DTC from the ECM memo ry after performing the tests. Refer to EC-456, "DTC Index"
.
>> GO TO 19.
19.CHECK INTERMITTENT INCIDENT
Refer to GI-35, "How to Check Terminal"
and GI-38, "Intermittent Incident".
>> INSPECTION END
Continuity should not exist.
3.0 - 9.0 g·m/sec: at idling
9.0 - 28.0 g·m/sec: at 2,500 rpm
3.0 - 9.0 g·m/sec: at idling
9.0 - 28.0 g·m/sec: at 2,500 rpm
Revision: December 20092009 QX56
Page 1708 of 4171
![INFINITI QX56 2009 Factory Owners Guide
P2A00, P2A03 A/F SENSOR 1EC-381
< COMPONENT DIAGNOSIS > [VK56DE]
C
D
E
F
G H
I
J
K L
M A
EC
NP
O
5. Also check harness for short to power.
OK or NG
OK >> GO TO 9.
NG >> Repair open circuit or short t INFINITI QX56 2009 Factory Owners Guide
P2A00, P2A03 A/F SENSOR 1EC-381
< COMPONENT DIAGNOSIS > [VK56DE]
C
D
E
F
G H
I
J
K L
M A
EC
NP
O
5. Also check harness for short to power.
OK or NG
OK >> GO TO 9.
NG >> Repair open circuit or short t](/img/42/57031/w960_57031-1707.png)
P2A00, P2A03 A/F SENSOR 1EC-381
< COMPONENT DIAGNOSIS > [VK56DE]
C
D
E
F
G H
I
J
K L
M A
EC
NP
O
5. Also check harness for short to power.
OK or NG
OK >> GO TO 9.
NG >> Repair open circuit or short to ground or short to power in harness or connectors.
9.CHECK A/F SENSOR 1 HEATER
Refer to EC-96, "Component Inspection"
.
OK or NG
OK >> GO TO 10.
NG >> GO TO 11.
10.CHECK INTERMITTENT INCIDENT
Perform GI-35, "How to Check Terminal"
and GI-38, "Intermittent Incident".
OK or NG
OK >> GO TO 11.
NG >> Repair or replace.
11 .REPLACE AIR FUEL RATIO (A/F) SENSOR 1
Replace malfunctioning air f uel ratio (A/F) sensor 1.
CAUTION:
Discard any A/F sensor which has been dropped from a height of more than 0.5 m (19.7 in) onto a
hard surface such as a concrete floor; use a new one.
Before installing new A/F senso r, clean exhaust system threads using Oxygen Sensor Thread
Cleaner tool J-43897-18 or J-43897-12 and approved anti-seize lubricant.
>> GO TO 12.
12.CONFIRM A/F ADJUSTMENT DATA
1. Turn ignition switch OFF and then ON.
2. Select “A/F ADJ-B1” and “” in “DATA MONITOR” mode with CONSULT-lll.
3. Make sure that “0.000” is displayed on CONSULT-lll screen.
OK or NG
OK >> INSPECTION END
NG >> GO TO 13.
13.CLEAR THE SELF-LEARNING DATA
With CONSULT-lll
1. Start engine and warm it up to normal operating temperature.
2. Select “SELF-LEARNING CONT” in “WORK SUPPORT” mode with CONSULT-lll.
3. Clear the self-learning control coefficient by touching “CLEAR”.
Without CONSULT-lll
1. Start engine and warm it up to normal operating temperature.
2. Turn ignition switch OFF.
Bank 1 Bank 2
A/F sensor 1 terminal ECM terminal A/F sensor 1 terminal ECM terminal 135116
256275
Continuity should not exist.
Revision: December 20092009 QX56
Page 1854 of 4171
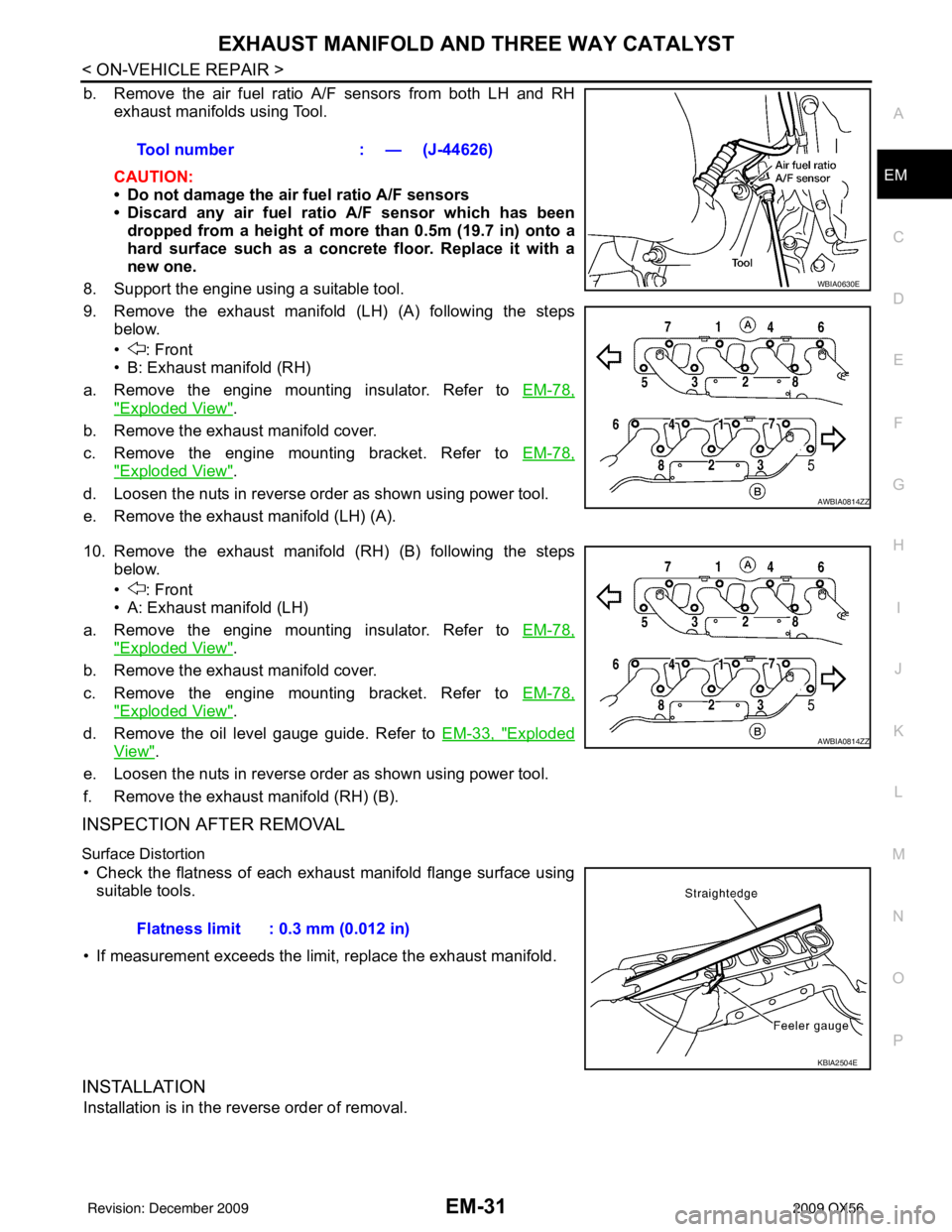
EXHAUST MANIFOLD AND THREE WAY CATALYST
EM-31
< ON-VEHICLE REPAIR >
C
D E
F
G H
I
J
K L
M A
EM
NP
O
b. Remove the air fuel ratio A/F sensors from both LH and RH
exhaust manifolds using Tool.
CAUTION:
• Do not damage the air fuel ratio A/F sensors
• Discard any air fuel rati o A/F sensor which has been
dropped from a height of more than 0.5m (19.7 in) onto a
hard surface such as a concrete floor. Replace it with a
new one.
8. Support the engine using a suitable tool.
9. Remove the exhaust manifold (LH) (A) following the steps below.
• : Front
• B: Exhaust manifold (RH)
a. Remove the engine mounting insulator. Refer to EM-78,
"Exploded View".
b. Remove the exhaust manifold cover.
c. Remove the engine mounting bracket. Refer to EM-78,
"Exploded View".
d. Loosen the nuts in reverse order as shown using power tool.
e. Remove the exhaust manifold (LH) (A).
10. Remove the exhaust manifold (RH) (B) following the steps below.
• : Front
• A: Exhaust manifold (LH)
a. Remove the engine mounting insulator. Refer to EM-78,
"Exploded View".
b. Remove the exhaust manifold cover.
c. Remove the engine mounting bracket. Refer to EM-78,
"Exploded View".
d. Remove the oil level gauge guide. Refer to EM-33, "
Exploded
View".
e. Loosen the nuts in reverse order as shown using power tool.
f. Remove the exhaust manifold (RH) (B).
INSPECTION AFTER REMOVAL
Surface Distortion
• Check the flatness of each exhaust manifold flange surface using suitable tools.
• If measurement exceeds the limit, replace the exhaust manifold.
INSTALLATION
Installation is in the reverse order of removal. Tool number
: — (J-44626)
WBIA0630E
AWBIA0814ZZ
AWBIA0814ZZ
Flatness limit : 0.3 mm (0.012 in)
KBIA2504E
Revision: December 20092009 QX56
Page 1880 of 4171
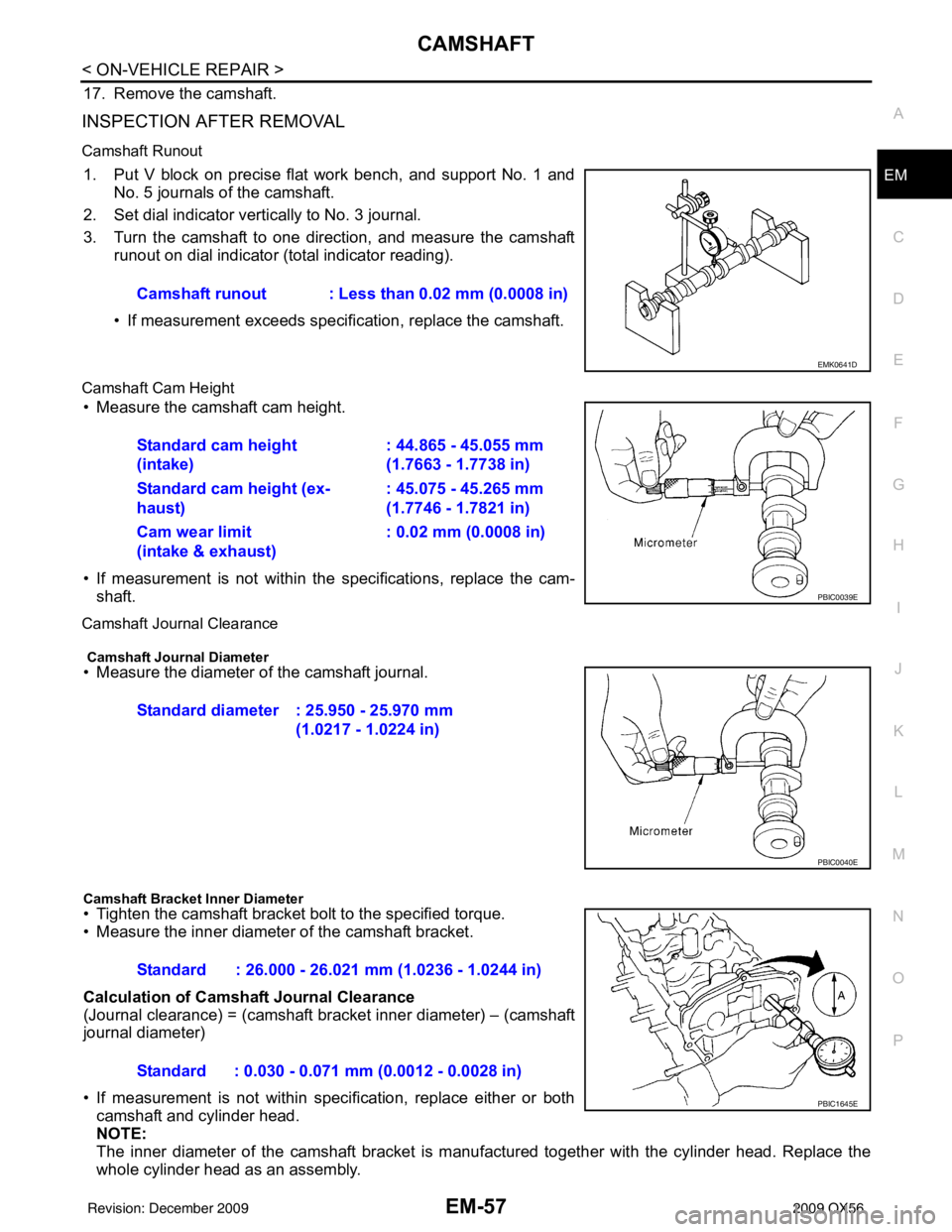
CAMSHAFTEM-57
< ON-VEHICLE REPAIR >
C
DE
F
G H
I
J
K L
M A
EM
NP
O
17. Remove the camshaft.
INSPECTION AFTER REMOVAL
Camshaft Runout
1. Put V block on precise flat work bench, and support No. 1 and
No. 5 journals of the camshaft.
2. Set dial indicator vertically to No. 3 journal.
3. Turn the camshaft to one direction, and measure the camshaft runout on dial indicator (total indicator reading).
• If measurement exceeds specif ication, replace the camshaft.
Camshaft Cam Height
• Measure the camshaft cam height.
• If measurement is not within the specifications, replace the cam-
shaft.
Camshaft Journal Clearance
Camshaft Journal Diameter
• Measure the diameter of the camshaft journal.
Camshaft Bracket Inner Diameter• Tighten the camshaft bracket bolt to the specified torque.
• Measure the inner diameter of the camshaft bracket.
Calculation of Camshaft Journal Clearance
(Journal clearance) = (camshaft bracket inner diameter) – (camshaft
journal diameter)
• If measurement is not within specification, replace either or both camshaft and cylinder head.
NOTE:
The inner diameter of the camshaft bracket is m anufactured together with the cylinder head. Replace the
whole cylinder head as an assembly. Camshaft runout : Less than 0.02 mm (0.0008 in)
EMK0641D
Standard cam height
(intake)
: 44.865 - 45.055 mm
(1.7663 - 1.7738 in)
Standard cam height (ex-
haust) : 45.075 - 45.265 mm
(1.7746 - 1.7821 in)
Cam wear limit
(intake & exhaust) : 0.02 mm (0.0008 in)
PBIC0039E
Standard diameter : 25.950 - 25.970 mm
(1.0217 - 1.0224 in)
PBIC0040E
Standard : 26.000 - 26.021 mm (1.0236 - 1.0244 in)
Standard : 0.030 - 0.071 mm (0.0012 - 0.0028 in)
PBIC1645E
Revision: December 20092009 QX56
Page 1887 of 4171
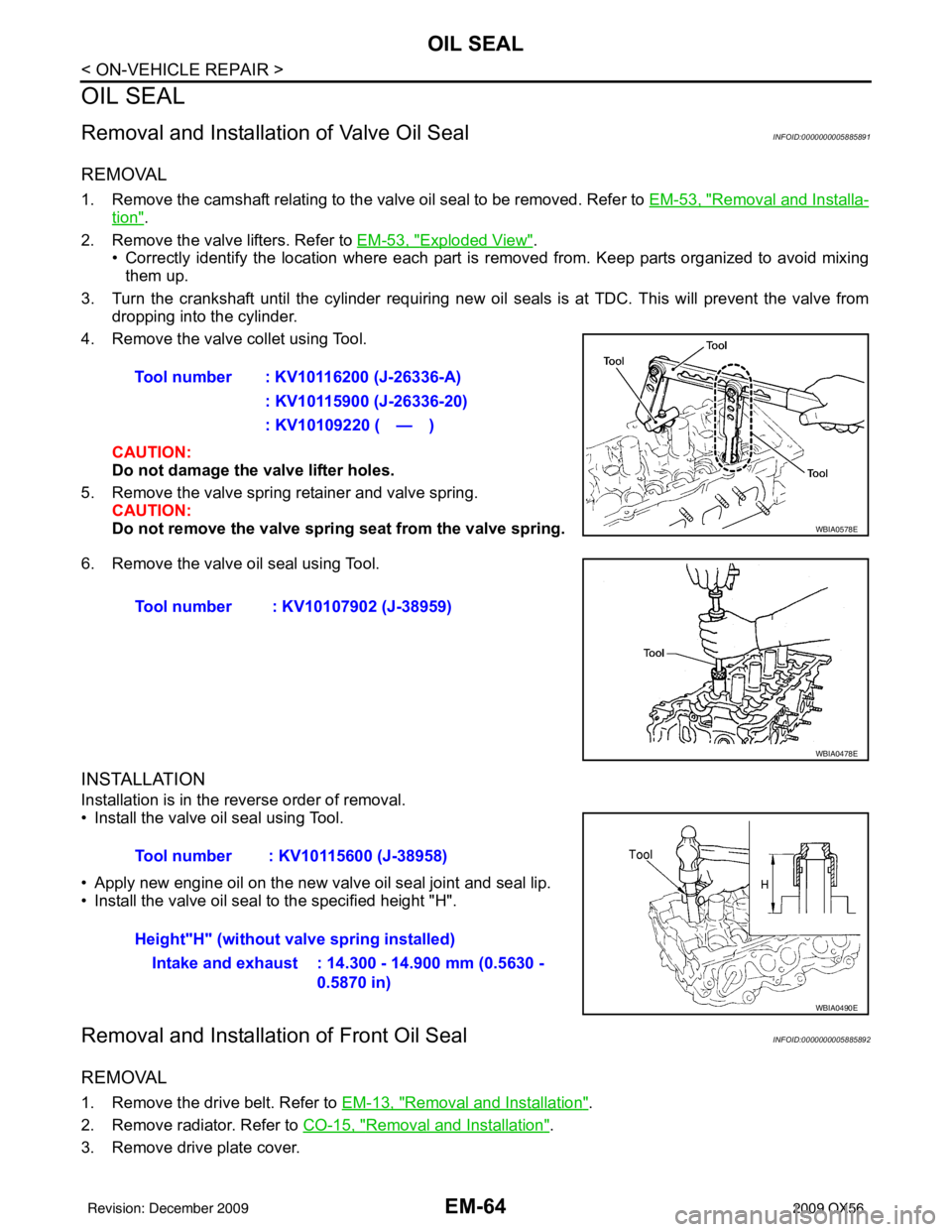
EM-64
< ON-VEHICLE REPAIR >
OIL SEAL
OIL SEAL
Removal and Installation of Valve Oil SealINFOID:0000000005885891
REMOVAL
1. Remove the camshaft relating to the valve oil seal to be removed. Refer to EM-53, "Removal and Installa-
tion".
2. Remove the valve lifters. Refer to EM-53, "
Exploded View".
• Correctly identify the location where each part is removed from. Keep parts organized to avoid mixing
them up.
3. Turn the crankshaft until the cylinder requiring new oil seals is at TDC. This will prevent the valve from
dropping into the cylinder.
4. Remove the valve collet using Tool.
CAUTION:
Do not damage the valve lifter holes.
5. Remove the valve spring retainer and valve spring. CAUTION:
Do not remove the valve spring seat from the valve spring.
6. Remove the valve oil seal using Tool.
INSTALLATION
Installation is in the reverse order of removal.
• Install the valve oil seal using Tool.
• Apply new engine oil on the new valve oil seal joint and seal lip.
• Install the valve oil seal to the specified height "H".
Removal and Installation of Front Oil SealINFOID:0000000005885892
REMOVAL
1. Remove the drive belt. Refer to EM-13, "Removal and Installation".
2. Remove radiator. Refer to CO-15, "
Removal and Installation".
3. Remove drive plate cover. Tool number : KV10116200 (J-26336-A)
: KV10115900 (J-26336-20)
: KV10109220 ( — )
WBIA0578E
Tool number : KV10107902 (J-38959)
WBIA0478E
Tool number : KV10115600 (J-38958)
Height"H" (without valve spring installed)Intake and exhaust : 14.300 - 14.900 mm (0.5630 - 0.5870 in)
WBIA0490E
Revision: December 20092009 QX56