ISUZU AXIOM 2002 Service Repair Manual
Manufacturer: ISUZU, Model Year: 2002, Model line: AXIOM, Model: ISUZU AXIOM 2002Pages: 2100, PDF Size: 19.35 MB
Page 991 of 2100
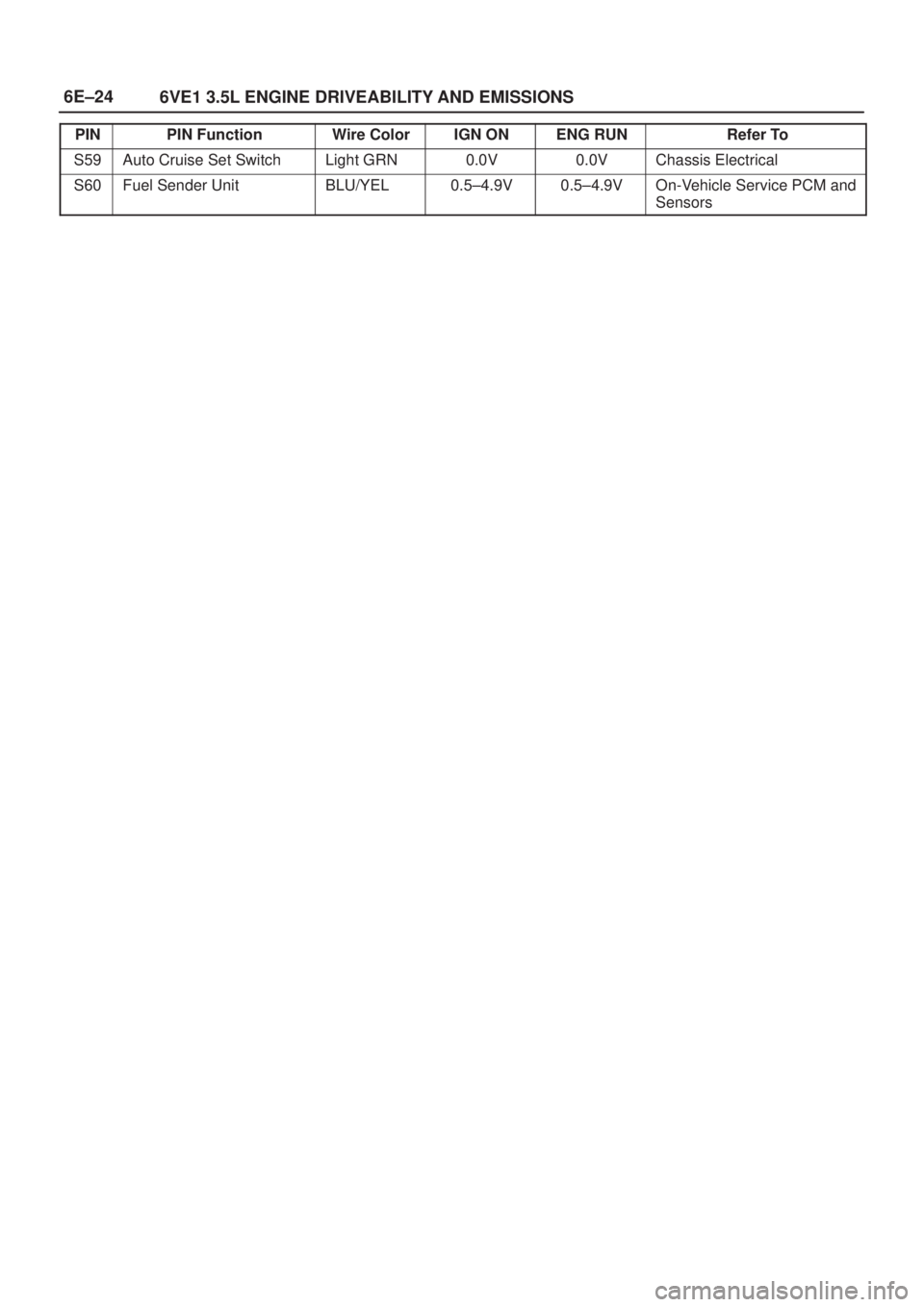
6E±24
6VE1 3.5L ENGINE DRIVEABILITY AND EMISSIONS
PINRefer To ENG RUN IGN ON Wire Color PIN Function
S59Auto Cruise Set SwitchLight GRN0.0V0.0VChassis Electrical
S60Fuel Sender UnitBLU/YEL0.5±4.9V0.5±4.9VOn-Vehicle Service PCM and
Sensors
Page 992 of 2100
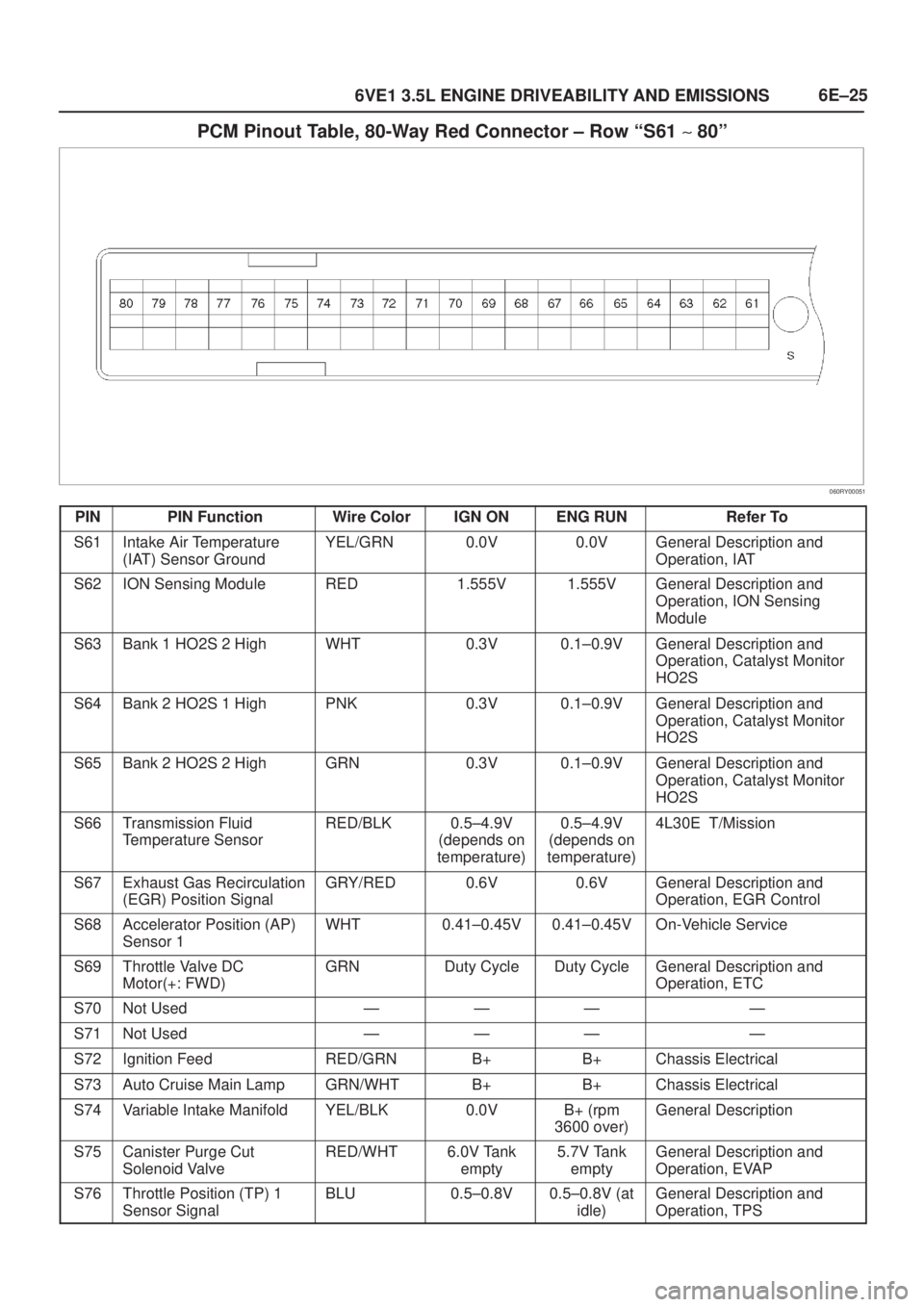
6E±25
6VE1 3.5L ENGINE DRIVEABILITY AND EMISSIONS
PCM Pinout Table, 80-Way Red Connector ± Row ªS61 ~ 80º
060RY00051
PINPIN FunctionWire ColorIGN ONENG RUNRefer To
S61Intake Air Temperature
(IAT) Sensor GroundYEL/GRN0.0V0.0VGeneral Description and
Operation, IAT
S62ION Sensing ModuleRED1.555V1.555VGeneral Description and
Operation, ION Sensing
Module
S63Bank 1 HO2S 2 HighWHT0.3V0.1±0.9VGeneral Description and
Operation, Catalyst Monitor
HO2S
S64Bank 2 HO2S 1 HighPNK0.3V0.1±0.9VGeneral Description and
Operation, Catalyst Monitor
HO2S
S65Bank 2 HO2S 2 HighGRN0.3V0.1±0.9VGeneral Description and
Operation, Catalyst Monitor
HO2S
S66Transmission Fluid
Temperature SensorRED/BLK0.5±4.9V
(depends on
temperature)0.5±4.9V
(depends on
temperature)4L30E T/Mission
S67Exhaust Gas Recirculation
(EGR) Position SignalGRY/RED0.6V0.6VGeneral Description and
Operation, EGR Control
S68Accelerator Position (AP)
Sensor 1WHT0.41±0.45V0.41±0.45VOn-Vehicle Service
S69Throttle Valve DC
Motor(+: FWD)GRNDuty CycleDuty CycleGeneral Description and
Operation, ETC
S70Not UsedÐÐÐÐ
S71Not UsedÐÐÐÐ
S72Ignition FeedRED/GRNB+B+Chassis Electrical
S73Auto Cruise Main LampGRN/WHTB+B+Chassis Electrical
S74Variable Intake ManifoldYEL/BLK0.0VB+ (rpm
3600 over)General Description
S75Canister Purge Cut
Solenoid ValveRED/WHT6.0V Tank
empty5.7V Tank
emptyGeneral Description and
Operation, EVAP
S76Throttle Position (TP) 1
Sensor SignalBLU0.5±0.8V0.5±0.8V (at
idle)General Description and
Operation, TPS
Page 993 of 2100
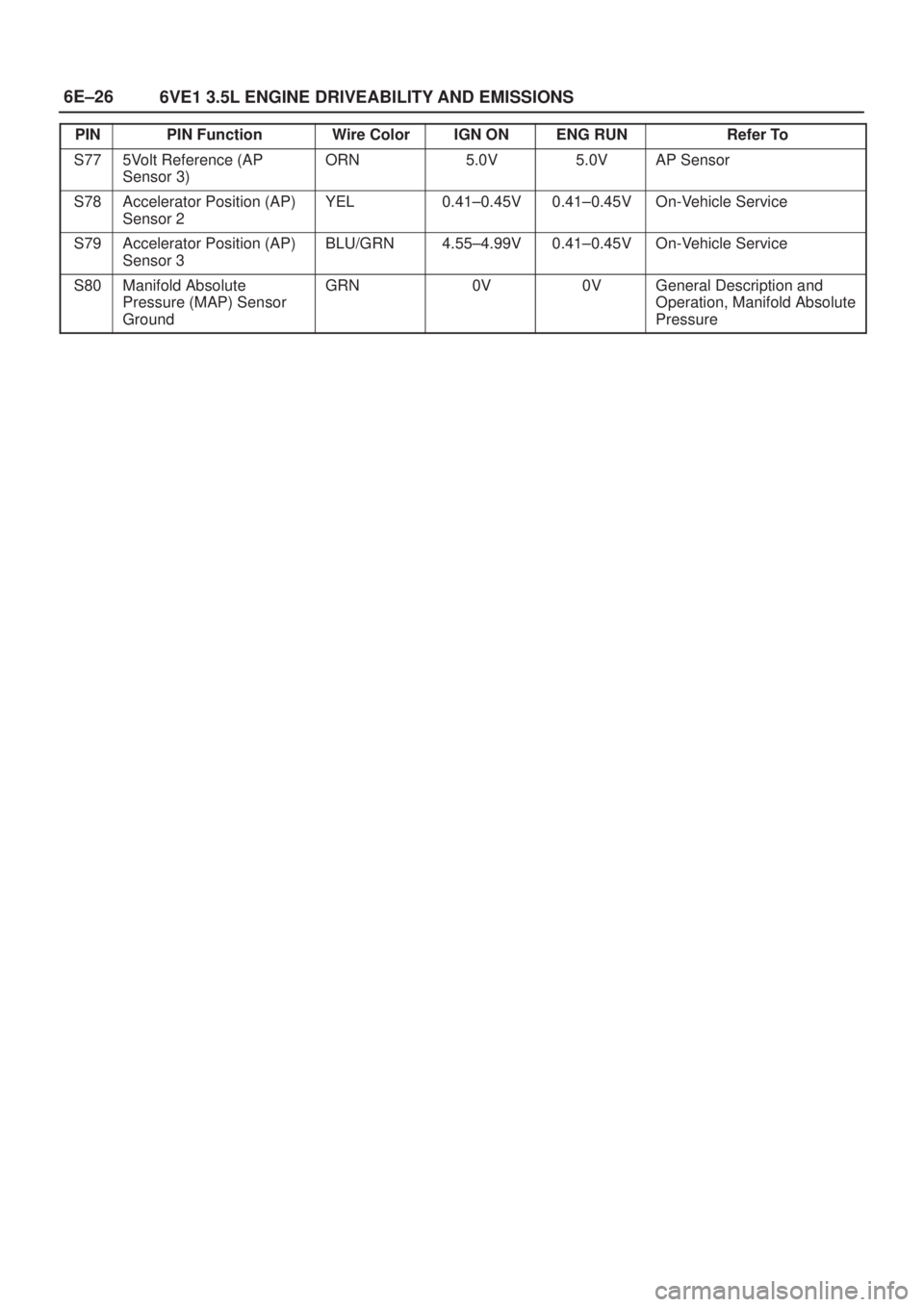
6E±26
6VE1 3.5L ENGINE DRIVEABILITY AND EMISSIONS
PINRefer To ENG RUN IGN ON Wire Color PIN Function
S775Volt Reference (AP
Sensor 3)ORN5.0V5.0VAP Sensor
S78Accelerator Position (AP)
Sensor 2YEL0.41±0.45V0.41±0.45VOn-Vehicle Service
S79Accelerator Position (AP)
Sensor 3BLU/GRN4.55±4.99V0.41±0.45VOn-Vehicle Service
S80Manifold Absolute
Pressure (MAP) Sensor
GroundGRN0V0VGeneral Description and
Operation, Manifold Absolute
Pressure
Page 994 of 2100
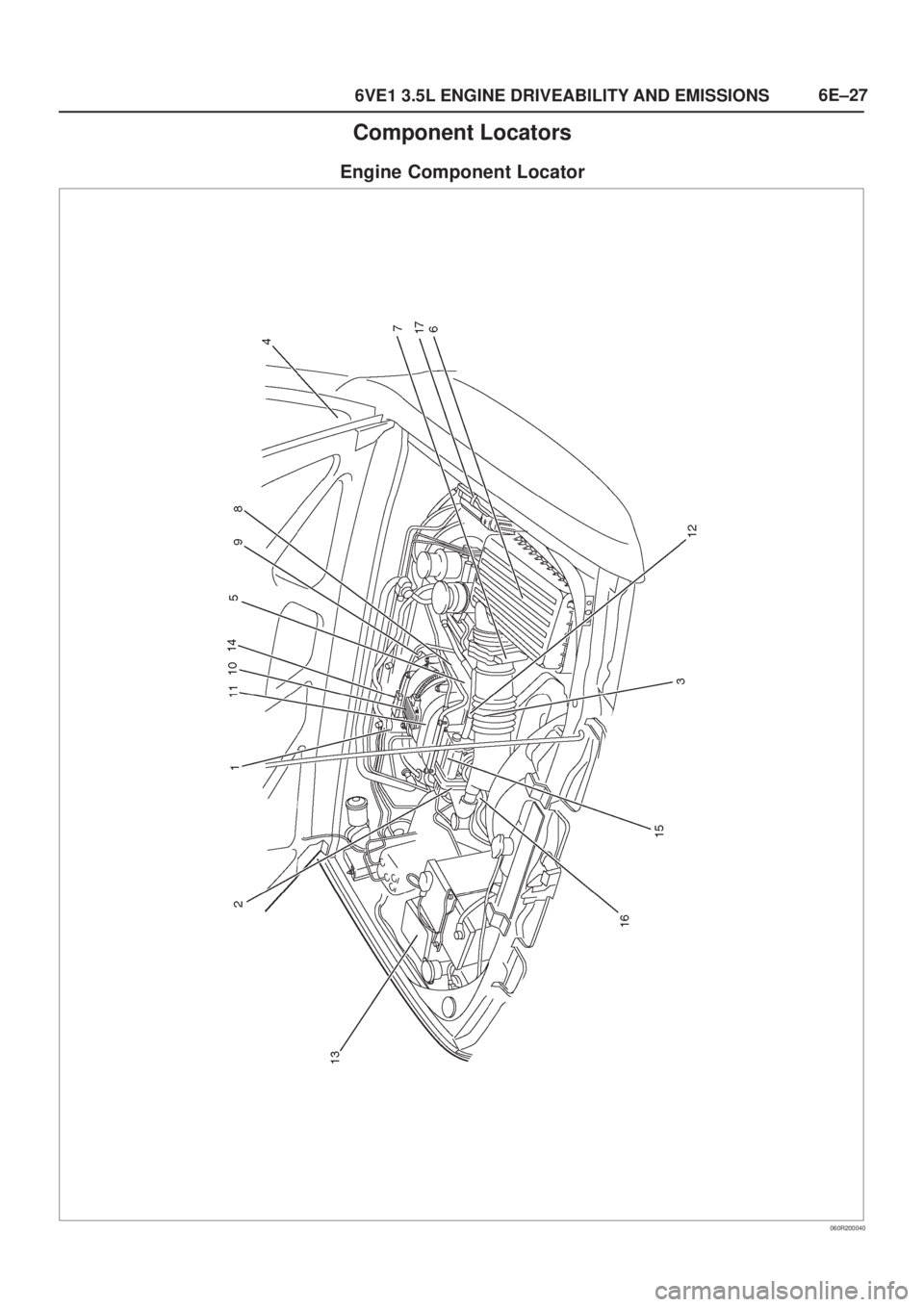
6E±27
6VE1 3.5L ENGINE DRIVEABILITY AND EMISSIONS
Component Locators
Engine Component Locator
060R200040
Page 995 of 2100
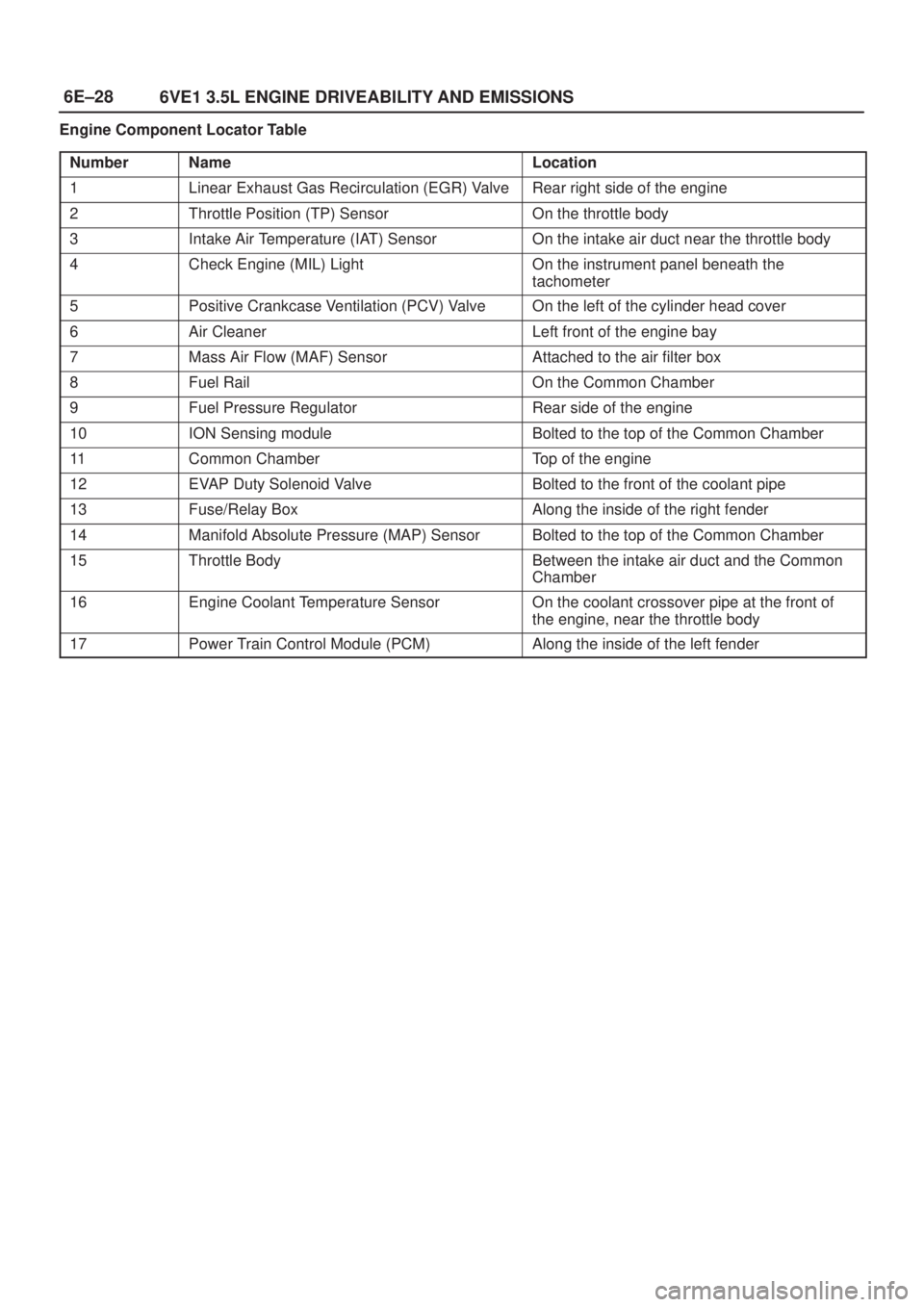
6E±28
6VE1 3.5L ENGINE DRIVEABILITY AND EMISSIONS
Engine Component Locator Table
Number
NameLocation
1Linear Exhaust Gas Recirculation (EGR) ValveRear right side of the engine
2Throttle Position (TP) SensorOn the throttle body
3Intake Air Temperature (IAT) SensorOn the intake air duct near the throttle body
4Check Engine (MIL) LightOn the instrument panel beneath the
tachometer
5Positive Crankcase Ventilation (PCV) ValveOn the left of the cylinder head cover
6Air CleanerLeft front of the engine bay
7Mass Air Flow (MAF) SensorAttached to the air filter box
8Fuel RailOn the Common Chamber
9Fuel Pressure RegulatorRear side of the engine
10ION Sensing moduleBolted to the top of the Common Chamber
11Common ChamberTop of the engine
12EVAP Duty Solenoid ValveBolted to the front of the coolant pipe
13Fuse/Relay BoxAlong the inside of the right fender
14Manifold Absolute Pressure (MAP) SensorBolted to the top of the Common Chamber
15Throttle BodyBetween the intake air duct and the Common
Chamber
16Engine Coolant Temperature SensorOn the coolant crossover pipe at the front of
the engine, near the throttle body
17Power Train Control Module (PCM)Along the inside of the left fender
Page 996 of 2100
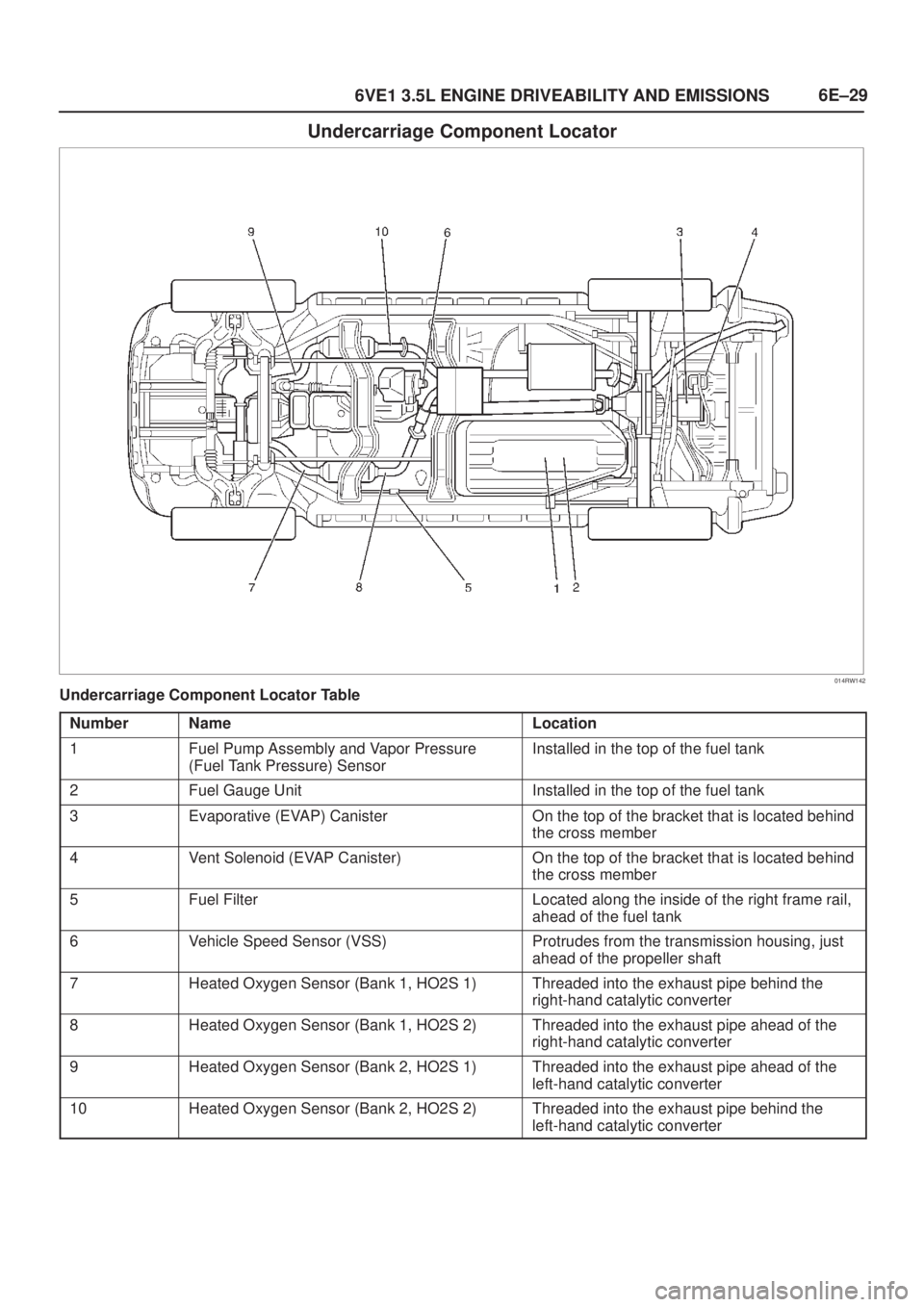
6E±29
6VE1 3.5L ENGINE DRIVEABILITY AND EMISSIONS
Undercarriage Component Locator
014RW142
Undercarriage Component Locator Table
Number
NameLocation
1Fuel Pump Assembly and Vapor Pressure
(Fuel Tank Pressure) SensorInstalled in the top of the fuel tank
2Fuel Gauge UnitInstalled in the top of the fuel tank
3Evaporative (EVAP) CanisterOn the top of the bracket that is located behind
the cross member
4Vent Solenoid (EVAP Canister)On the top of the bracket that is located behind
the cross member
5Fuel FilterLocated along the inside of the right frame rail,
ahead of the fuel tank
6Vehicle Speed Sensor (VSS)Protrudes from the transmission housing, just
ahead of the propeller shaft
7Heated Oxygen Sensor (Bank 1, HO2S 1)Threaded into the exhaust pipe behind the
right-hand catalytic converter
8Heated Oxygen Sensor (Bank 1, HO2S 2)Threaded into the exhaust pipe ahead of the
right-hand catalytic converter
9Heated Oxygen Sensor (Bank 2, HO2S 1)Threaded into the exhaust pipe ahead of the
left-hand catalytic converter
10Heated Oxygen Sensor (Bank 2, HO2S 2)Threaded into the exhaust pipe behind the
left-hand catalytic converter
Page 997 of 2100

6E±30
6VE1 3.5L ENGINE DRIVEABILITY AND EMISSIONS
Fuse and Relay Panel (Underhood Electrical Center)
060R200085
Page 998 of 2100
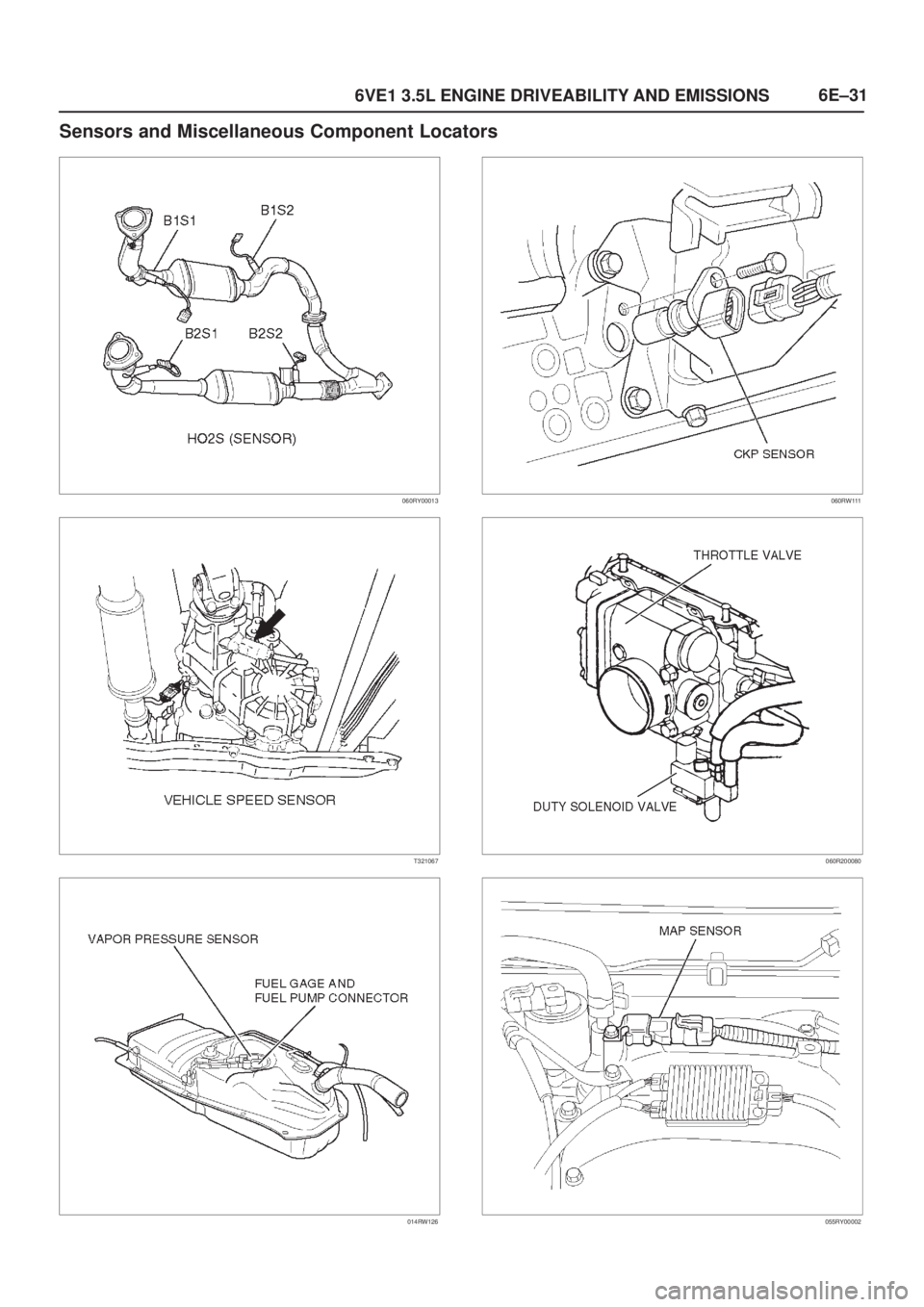
6E±31
6VE1 3.5L ENGINE DRIVEABILITY AND EMISSIONS
Sensors and Miscellaneous Component Locators
060RY00013
T321067
014RW126
060RW111
060R200080
055RY00002
Page 999 of 2100
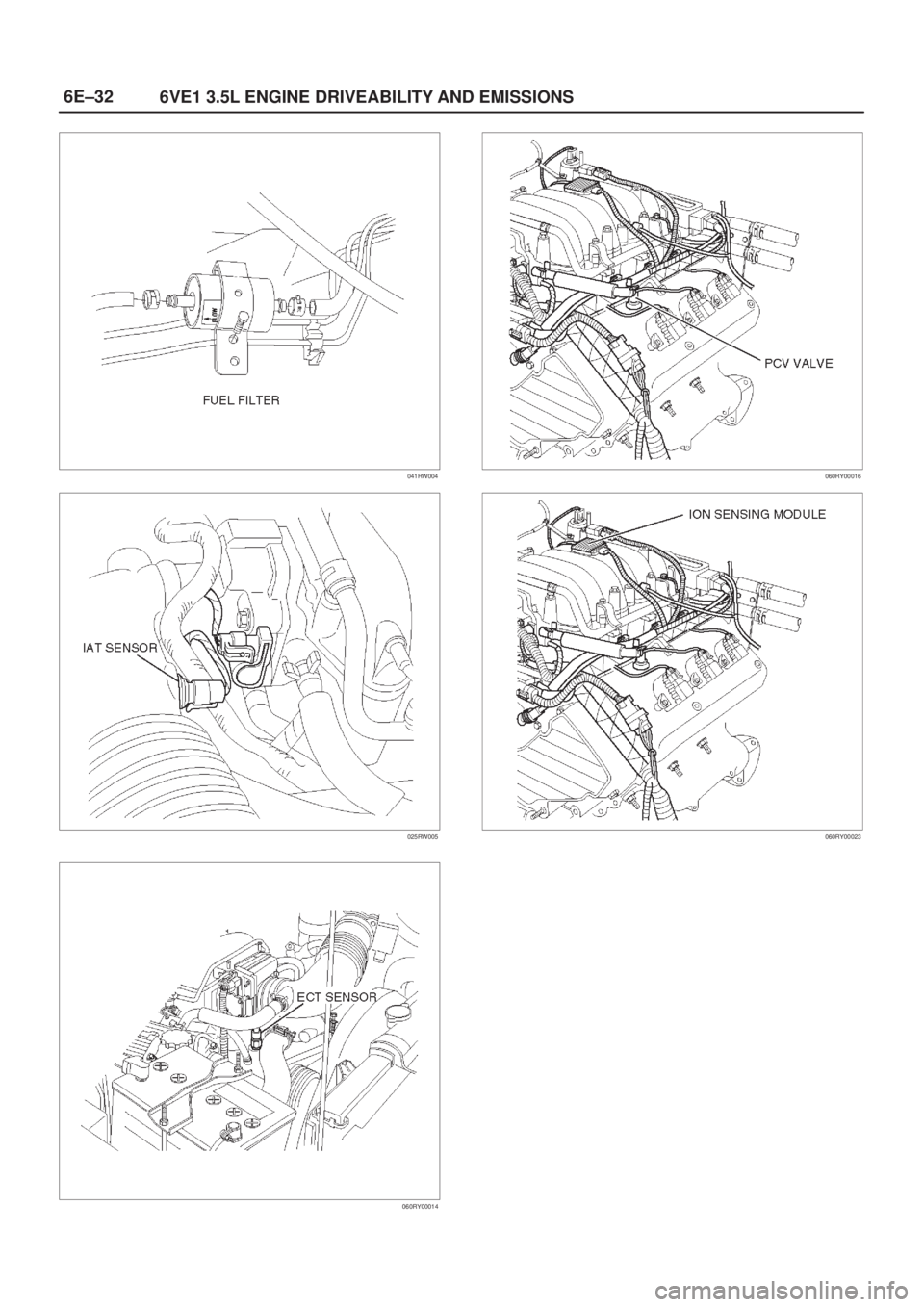
6E±32
6VE1 3.5L ENGINE DRIVEABILITY AND EMISSIONS
041RW004
025RW005
060RY00014
060RY00016
060RY00023
Page 1000 of 2100
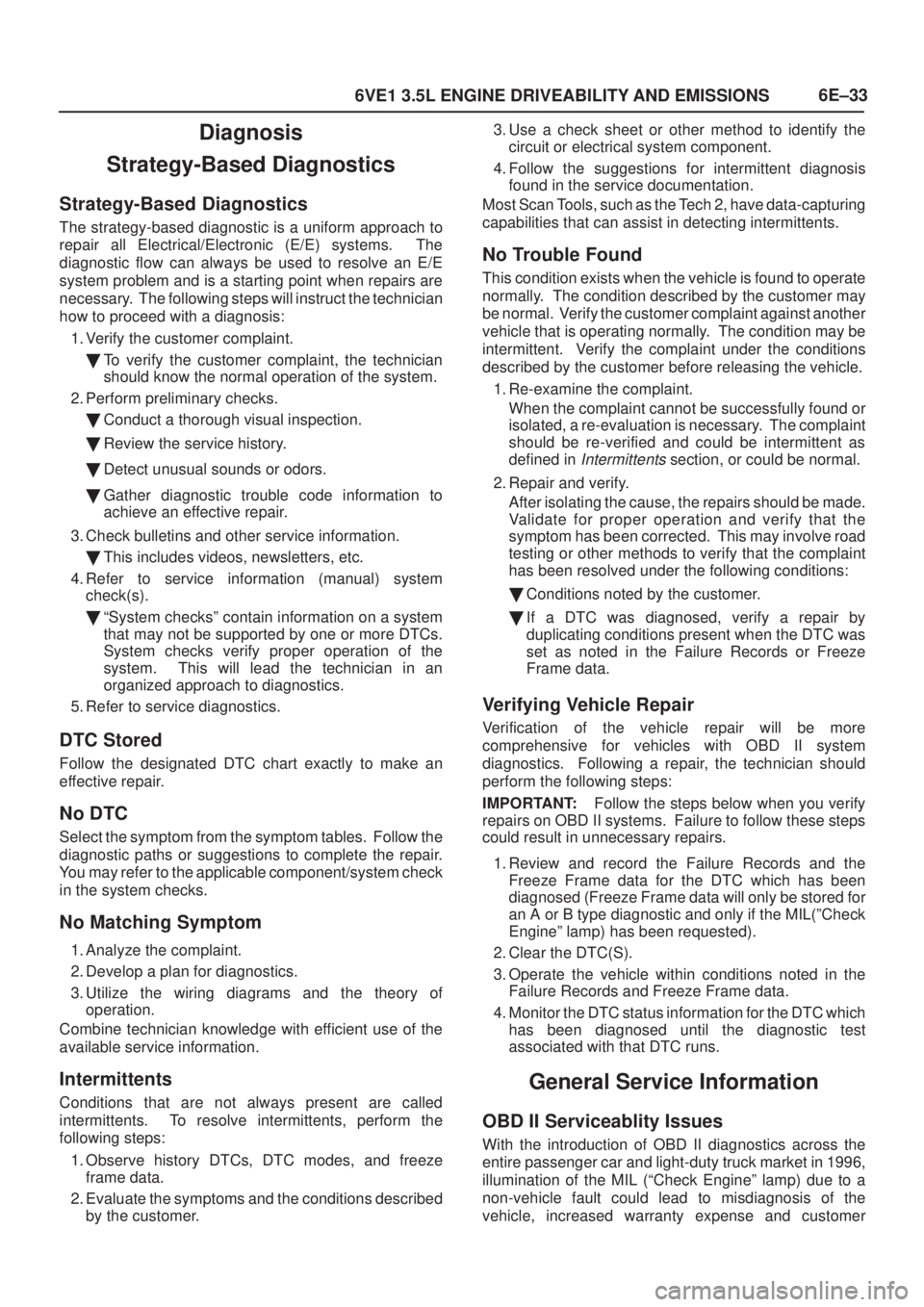
6E±33
6VE1 3.5L ENGINE DRIVEABILITY AND EMISSIONS
Diagnosis
Strategy-Based Diagnostics
Strategy-Based Diagnostics
The strategy-based diagnostic is a uniform approach to
repair all Electrical/Electronic (E/E) systems. The
diagnostic flow can always be used to resolve an E/E
system problem and is a starting point when repairs are
necessary. The following steps will instruct the technician
how to proceed with a diagnosis:
1. Verify the customer complaint.
To verify the customer complaint, the technician
should know the normal operation of the system.
2. Perform preliminary checks.
Conduct a thorough visual inspection.
Review the service history.
Detect unusual sounds or odors.
Gather diagnostic trouble code information to
achieve an effective repair.
3. Check bulletins and other service information.
This includes videos, newsletters, etc.
4. Refer to service information (manual) system
check(s).
ªSystem checksº contain information on a system
that may not be supported by one or more DTCs.
System checks verify proper operation of the
system. This will lead the technician in an
organized approach to diagnostics.
5. Refer to service diagnostics.
DTC Stored
Follow the designated DTC chart exactly to make an
effective repair.
No DTC
Select the symptom from the symptom tables. Follow the
diagnostic paths or suggestions to complete the repair.
You may refer to the applicable component/system check
in the system checks.
No Matching Symptom
1. Analyze the complaint.
2. Develop a plan for diagnostics.
3. Utilize the wiring diagrams and the theory of
operation.
Combine technician knowledge with efficient use of the
available service information.
Intermittents
Conditions that are not always present are called
intermittents. To resolve intermittents, perform the
following steps:
1. Observe history DTCs, DTC modes, and freeze
frame data.
2. Evaluate the symptoms and the conditions described
by the customer.3. Use a check sheet or other method to identify the
circuit or electrical system component.
4. Follow the suggestions for intermittent diagnosis
found in the service documentation.
Most Scan Tools, such as the Tech 2, have data-capturing
capabilities that can assist in detecting intermittents.
No Trouble Found
This condition exists when the vehicle is found to operate
normally. The condition described by the customer may
be normal. Verify the customer complaint against another
vehicle that is operating normally. The condition may be
intermittent. Verify the complaint under the conditions
described by the customer before releasing the vehicle.
1. Re-examine the complaint.
When the complaint cannot be successfully found or
isolated, a re-evaluation is necessary. The complaint
should be re-verified and could be intermittent as
defined in
Intermittents section, or could be normal.
2. Repair and verify.
After isolating the cause, the repairs should be made.
Validate for proper operation and verify that the
symptom has been corrected. This may involve road
testing or other methods to verify that the complaint
has been resolved under the following conditions:
Conditions noted by the customer.
If a DTC was diagnosed, verify a repair by
duplicating conditions present when the DTC was
set as noted in the Failure Records or Freeze
Frame data.
Verifying Vehicle Repair
Verification of the vehicle repair will be more
comprehensive for vehicles with OBD II system
diagnostics. Following a repair, the technician should
perform the following steps:
IMPORTANT:Follow the steps below when you verify
repairs on OBD II systems. Failure to follow these steps
could result in unnecessary repairs.
1. Review and record the Failure Records and the
Freeze Frame data for the DTC which has been
diagnosed (Freeze Frame data will only be stored for
an A or B type diagnostic and only if the MIL(ºCheck
Engineº lamp) has been requested).
2. Clear the DTC(S).
3. Operate the vehicle within conditions noted in the
Failure Records and Freeze Frame data.
4. Monitor the DTC status information for the DTC which
has been diagnosed until the diagnostic test
associated with that DTC runs.
General Service Information
OBD II Serviceablity Issues
With the introduction of OBD II diagnostics across the
entire passenger car and light-duty truck market in 1996,
illumination of the MIL (ªCheck Engineº lamp) due to a
non-vehicle fault could lead to misdiagnosis of the
vehicle, increased warranty expense and customer