ISUZU AXIOM 2002 Service Repair Manual
Manufacturer: ISUZU, Model Year: 2002, Model line: AXIOM, Model: ISUZU AXIOM 2002Pages: 2100, PDF Size: 19.35 MB
Page 561 of 2100
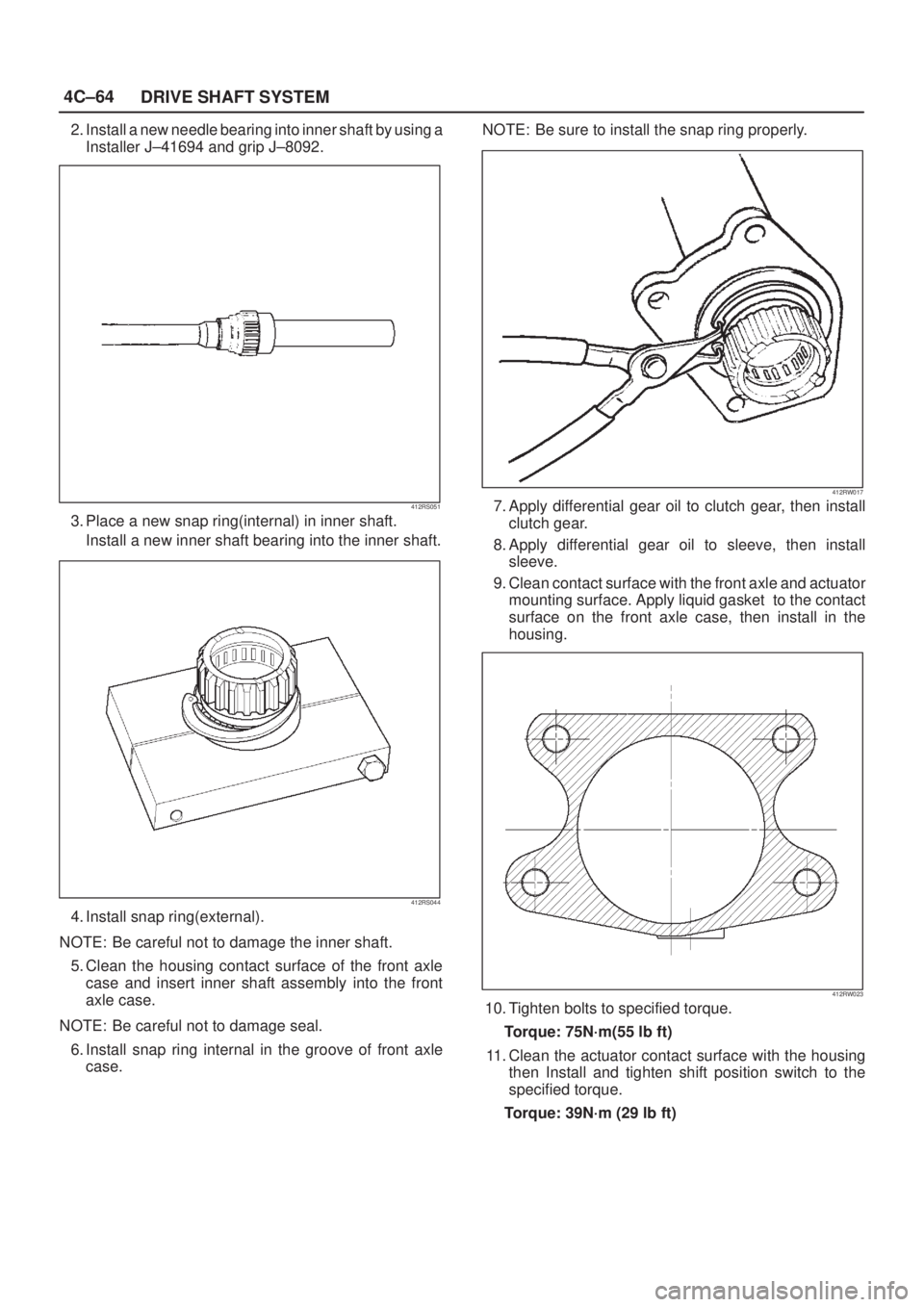
4C±64
DRIVE SHAFT SYSTEM
2. Install a new needle bearing into inner shaft by using a
Installer J±41694 and grip J±8092.
412RS051
3. Place a new snap ring(internal) in inner shaft.
Install a new inner shaft bearing into the inner shaft.
412RS044
4. Install snap ring(external).
NOTE: Be careful not to damage the inner shaft.
5. Clean the housing contact surface of the front axle
case and insert inner shaft assembly into the front
axle case.
NOTE: Be careful not to damage seal.
6. Install snap ring internal in the groove of front axle
case.NOTE: Be sure to install the snap ring properly.
412RW017
7. Apply differential gear oil to clutch gear, then install
clutch gear.
8. Apply differential gear oil to sleeve, then install
sleeve.
9. Clean contact surface with the front axle and actuator
mounting surface. Apply liquid gasket to the contact
surface on the front axle case, then install in the
housing.
412RW023
10. Tighten bolts to specified torque.
Torque: 75N´m(55 lb ft)
11. Clean the actuator contact surface with the housing
then Install and tighten shift position switch to the
specified torque.
Torque: 39N´m (29 lb ft)
Page 562 of 2100
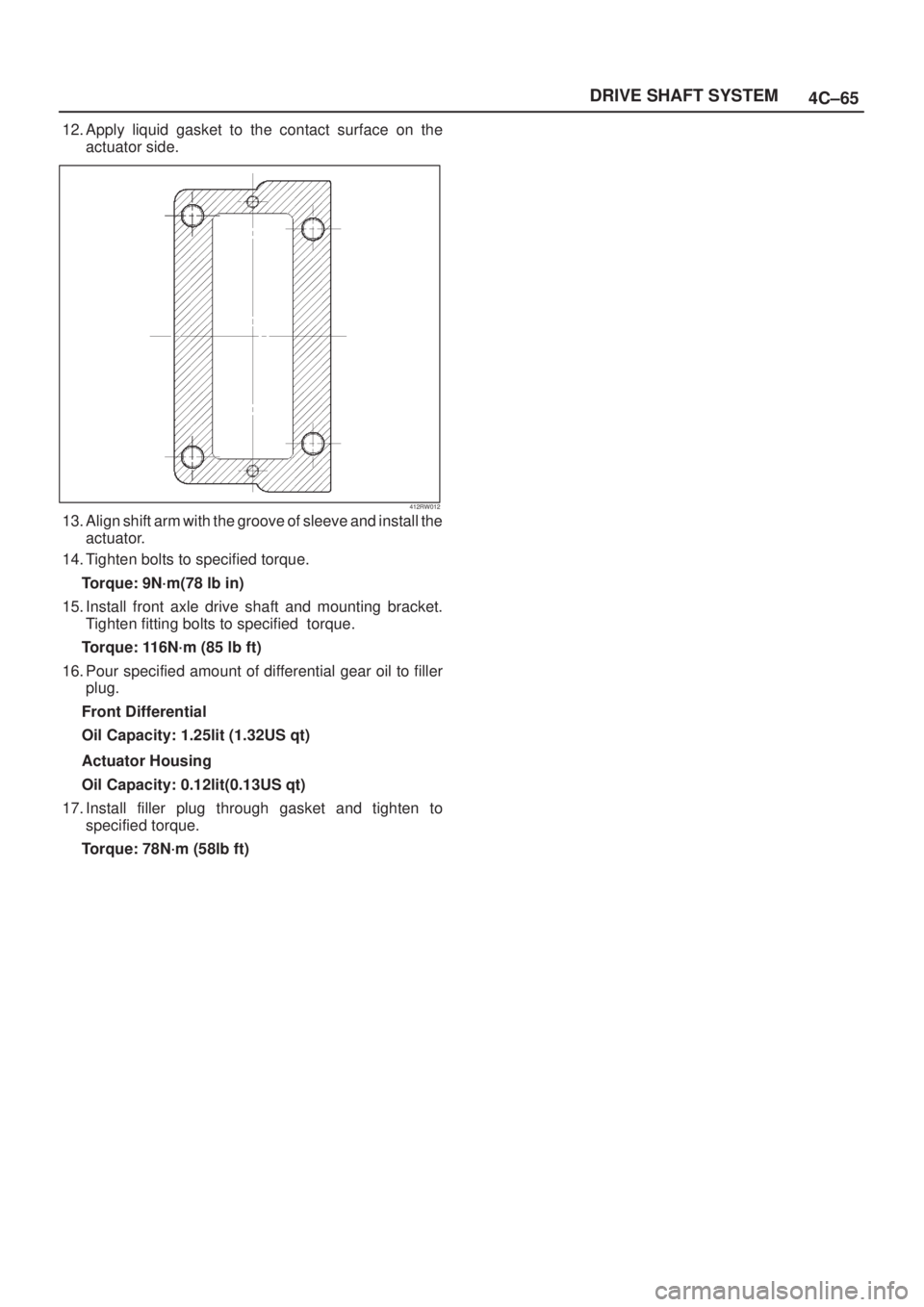
4C±65 DRIVE SHAFT SYSTEM
12. Apply liquid gasket to the contact surface on the
actuator side.
412RW012
13. Align shift arm with the groove of sleeve and install the
actuator.
14. Tighten bolts to specified torque.
Torque: 9N´m(78 lb in)
15. Install front axle drive shaft and mounting bracket.
Tighten fitting bolts to specified torque.
Torque: 116N´m (85 lb ft)
16. Pour specified amount of differential gear oil to filler
plug.
Front Differential
Oil Capacity: 1.25lit (1.32US qt)
Actuator Housing
Oil Capacity: 0.12lit(0.13US qt)
17. Install filler plug through gasket and tighten to
specified torque.
Torque: 78N´m (58lb ft)
Page 563 of 2100
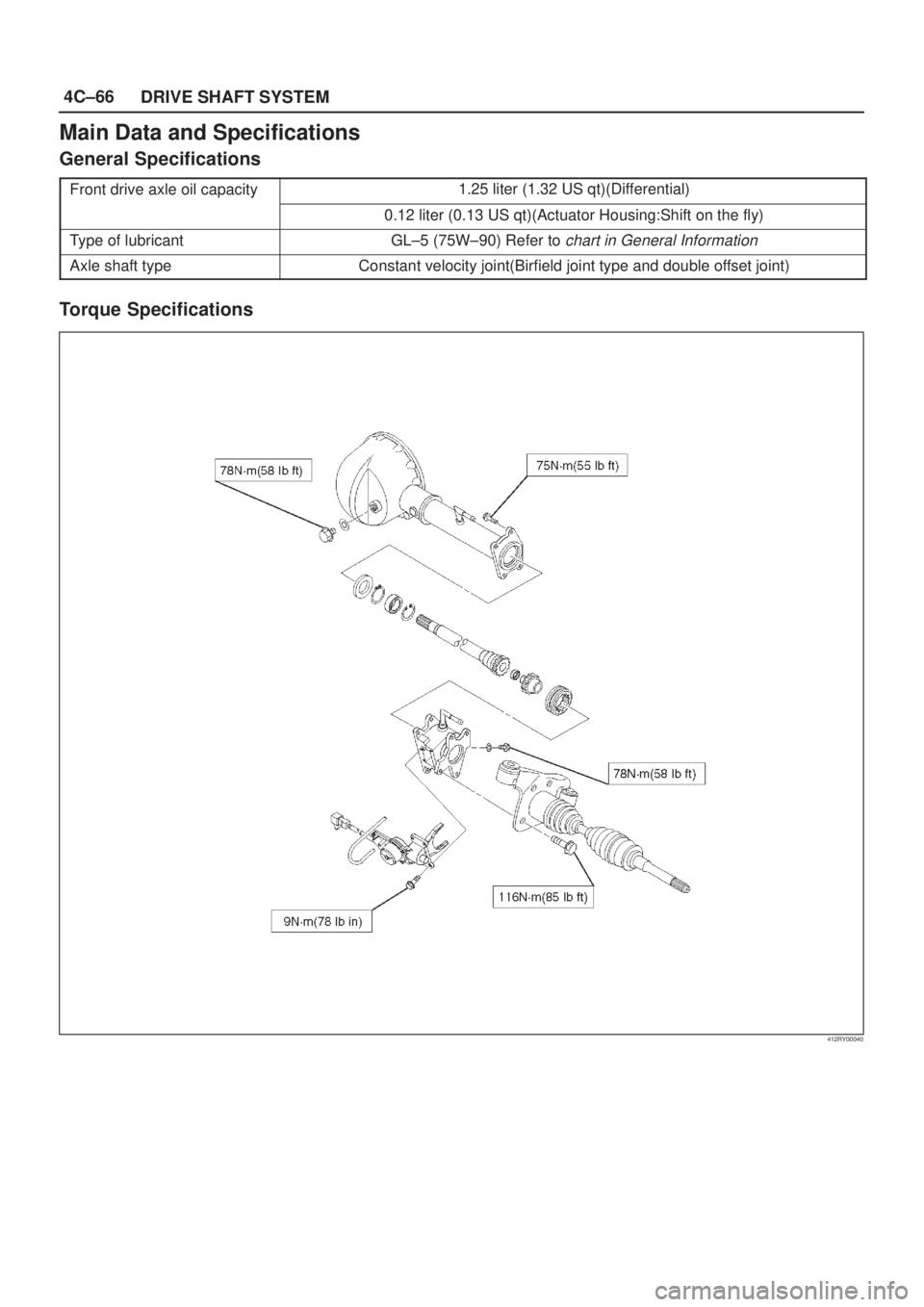
4C±66
DRIVE SHAFT SYSTEM
Main Data and Specifications
General Specifications
Front drive axle oil capacity1.25 liter (1.32 US qt)(Differential)
0.12 liter (0.13 US qt)(Actuator Housing:Shift on the fly)
Type of lubricantGL±5 (75W±90) Refer to chart in General Information
Axle shaft typeConstant velocity joint(Birfield joint type and double offset joint)
Torque Specifications
412RY00040
Page 564 of 2100
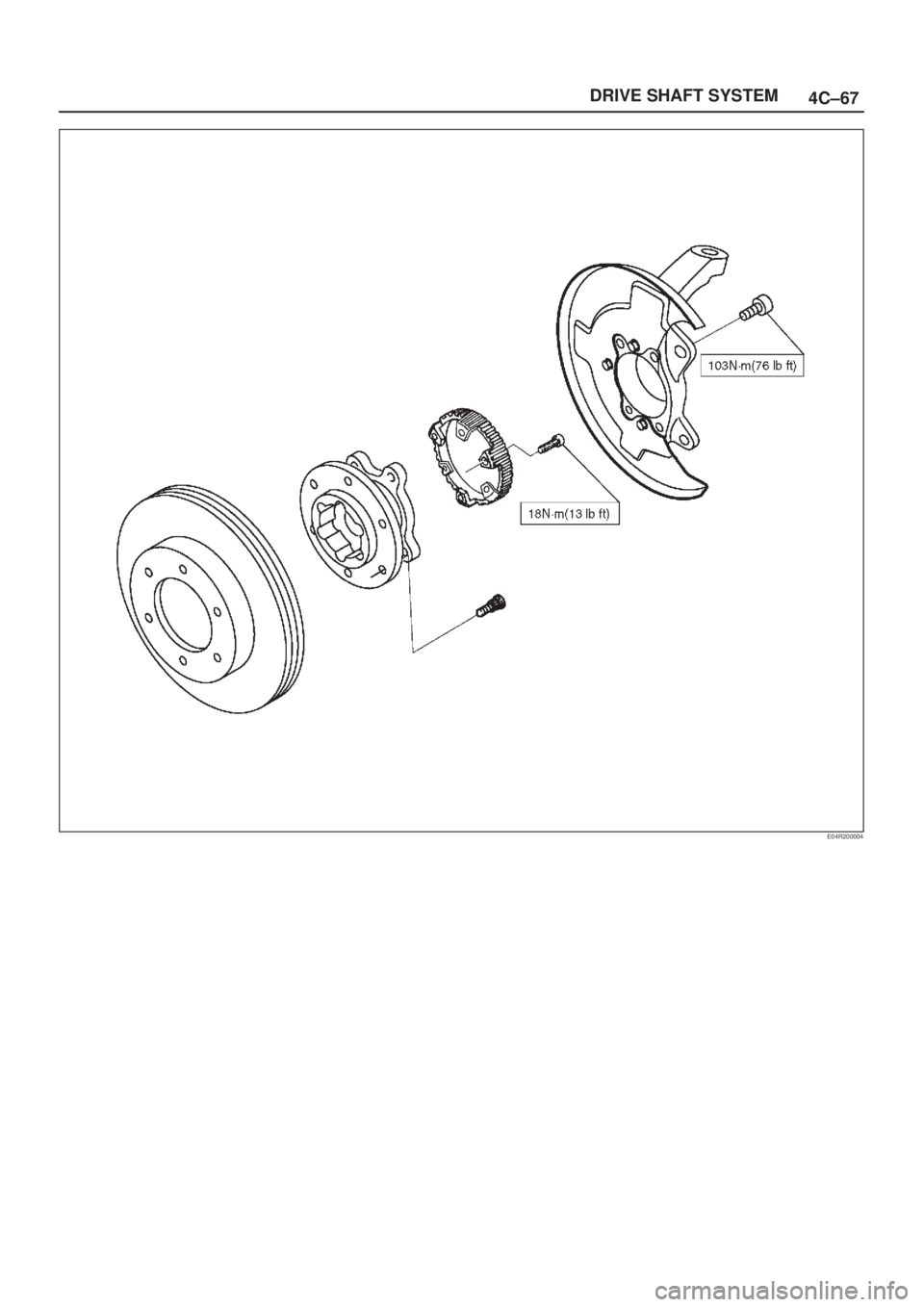
4C±67 DRIVE SHAFT SYSTEM
E04R200004
Page 565 of 2100
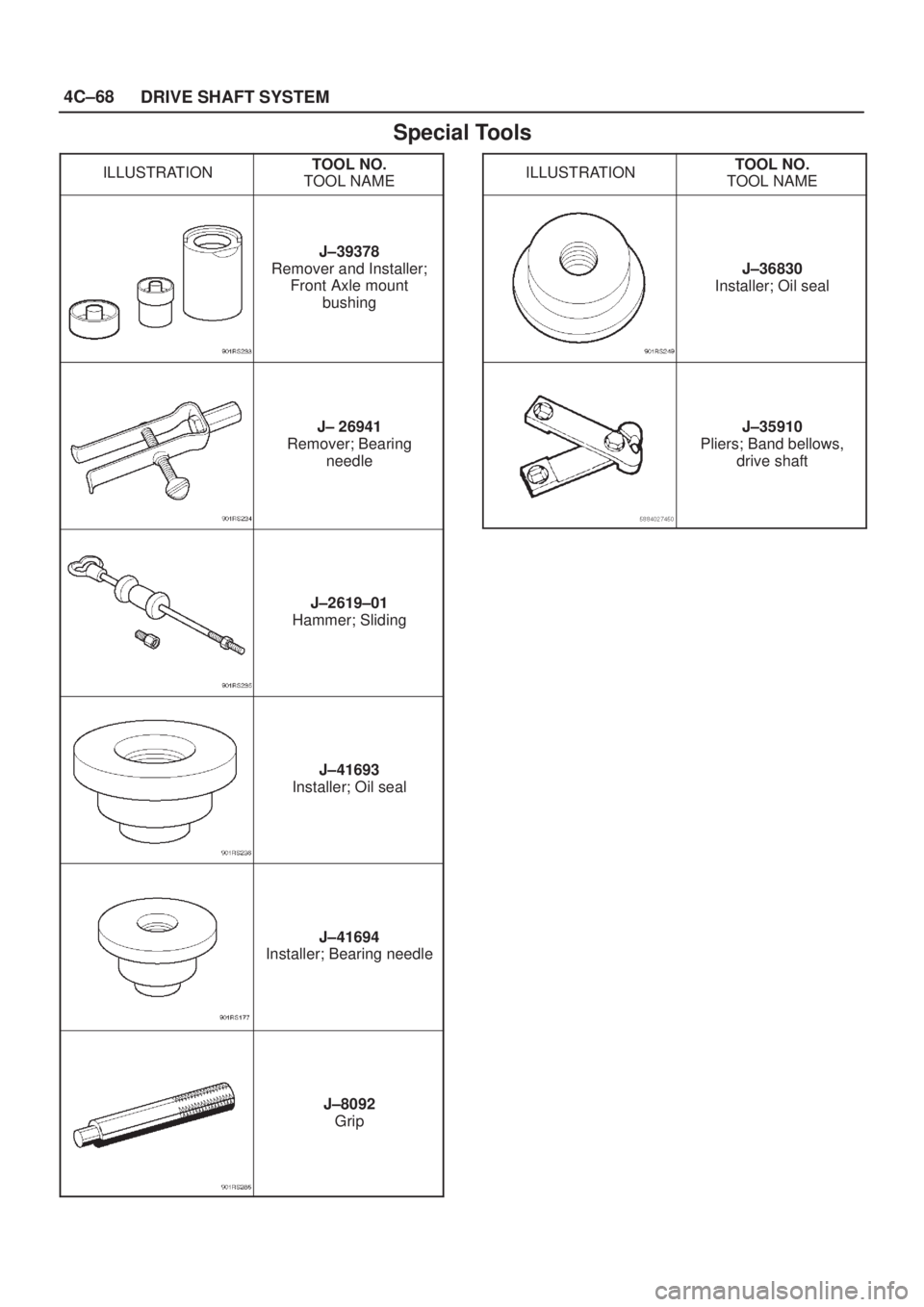
4C±68
DRIVE SHAFT SYSTEM
Special Tools
ILLUSTRATIONTOOL NO.
TOOL NAME
J±39378
Remover and Installer;
Front Axle mount
bushing
J± 26941
Remover; Bearing
needle
J±2619±01
Hammer; Sliding
J±41693
Installer; Oil seal
J±41694
Installer; Bearing needle
J±8092
Grip
ILLUSTRATIONTOOL NO.
TOOL NAME
J±36830
Installer; Oil seal
J±35910
Pliers; Band bellows,
drive shaft
Page 566 of 2100
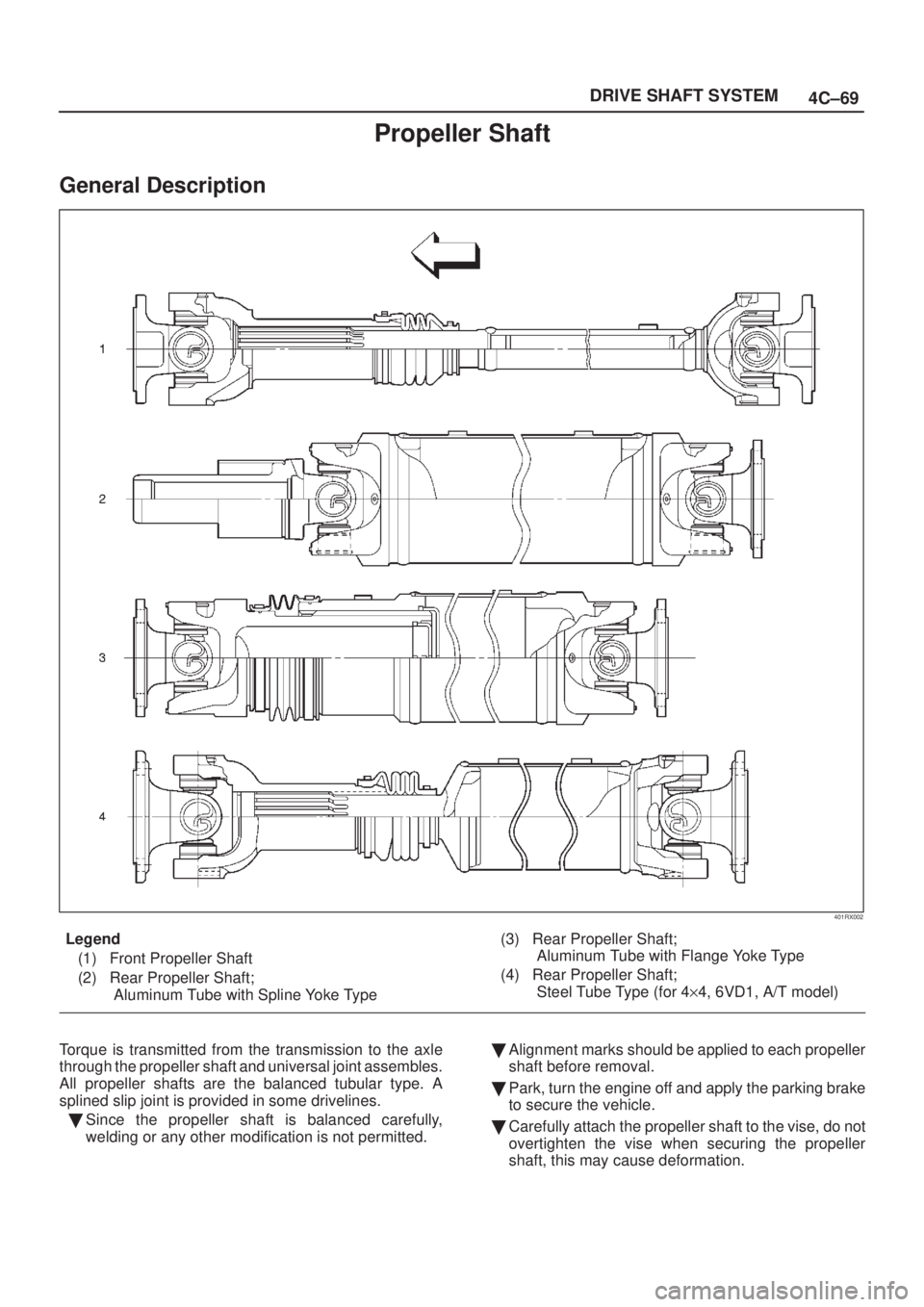
4C±69 DRIVE SHAFT SYSTEM
Propeller Shaft
General Description
401RX002
Legend
(1) Front Propeller Shaft
(2) Rear Propeller Shaft;
Aluminum Tube with Spline Yoke Type(3) Rear Propeller Shaft;
Aluminum Tube with Flange Yoke Type
(4) Rear Propeller Shaft;
Steel Tube Type (for 4y4, 6VD1, A/T model)
Torque is transmitted from the transmission to the axle
through the propeller shaft and universal joint assembles.
All propeller shafts are the balanced tubular type. A
splined slip joint is provided in some drivelines.
Since the propeller shaft is balanced carefully,
welding or any other modification is not permitted.Alignment marks should be applied to each propeller
shaft before removal.
Park, turn the engine off and apply the parking brake
to secure the vehicle.
Carefully attach the propeller shaft to the vise, do not
overtighten the vise when securing the propeller
shaft, this may cause deformation.
Page 567 of 2100
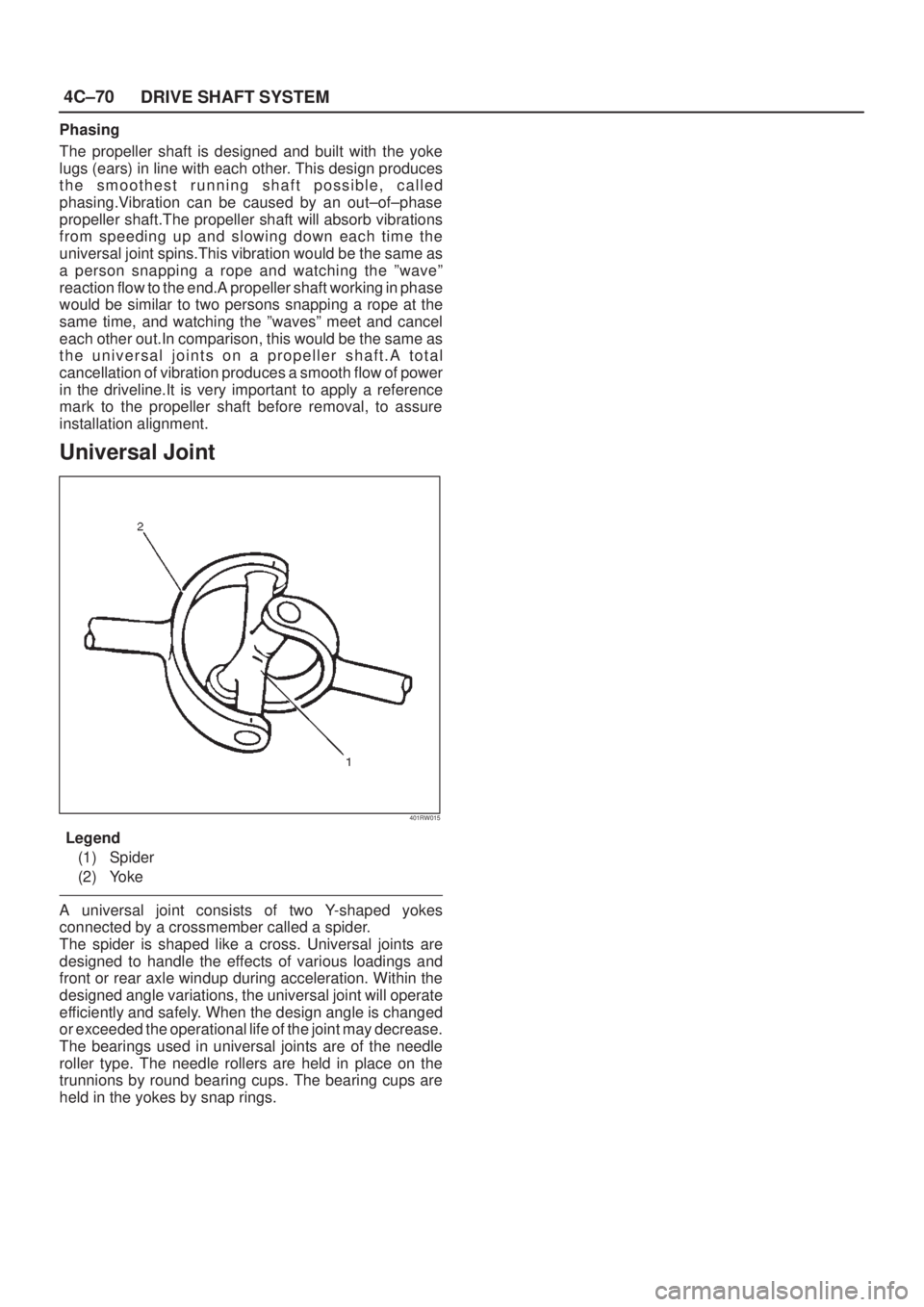
4C±70
DRIVE SHAFT SYSTEM
Phasing
The propeller shaft is designed and built with the yoke
lugs (ears) in line with each other. This design produces
the smoothest running shaft possible, called
phasing.Vibration can be caused by an out±of±phase
propeller shaft.The propeller shaft will absorb vibrations
from speeding up and slowing down each time the
universal joint spins.This vibration would be the same as
a person snapping a rope and watching the ºwaveº
reaction flow to the end.A propeller shaft working in phase
would be similar to two persons snapping a rope at the
same time, and watching the ºwavesº meet and cancel
each other out.In comparison, this would be the same as
the universal joints on a propeller shaft.A total
cancellation of vibration produces a smooth flow of power
in the driveline.It is very important to apply a reference
mark to the propeller shaft before removal, to assure
installation alignment.
Universal Joint
401RW015
Legend
(1) Spider
(2) Yoke
A universal joint consists of two Y-shaped yokes
connected by a crossmember called a spider.
The spider is shaped like a cross. Universal joints are
designed to handle the effects of various loadings and
front or rear axle windup during acceleration. Within the
designed angle variations, the universal joint will operate
efficiently and safely. When the design angle is changed
or exceeded the operational life of the joint may decrease.
The bearings used in universal joints are of the needle
roller type. The needle rollers are held in place on the
trunnions by round bearing cups. The bearing cups are
held in the yokes by snap rings.
Page 568 of 2100
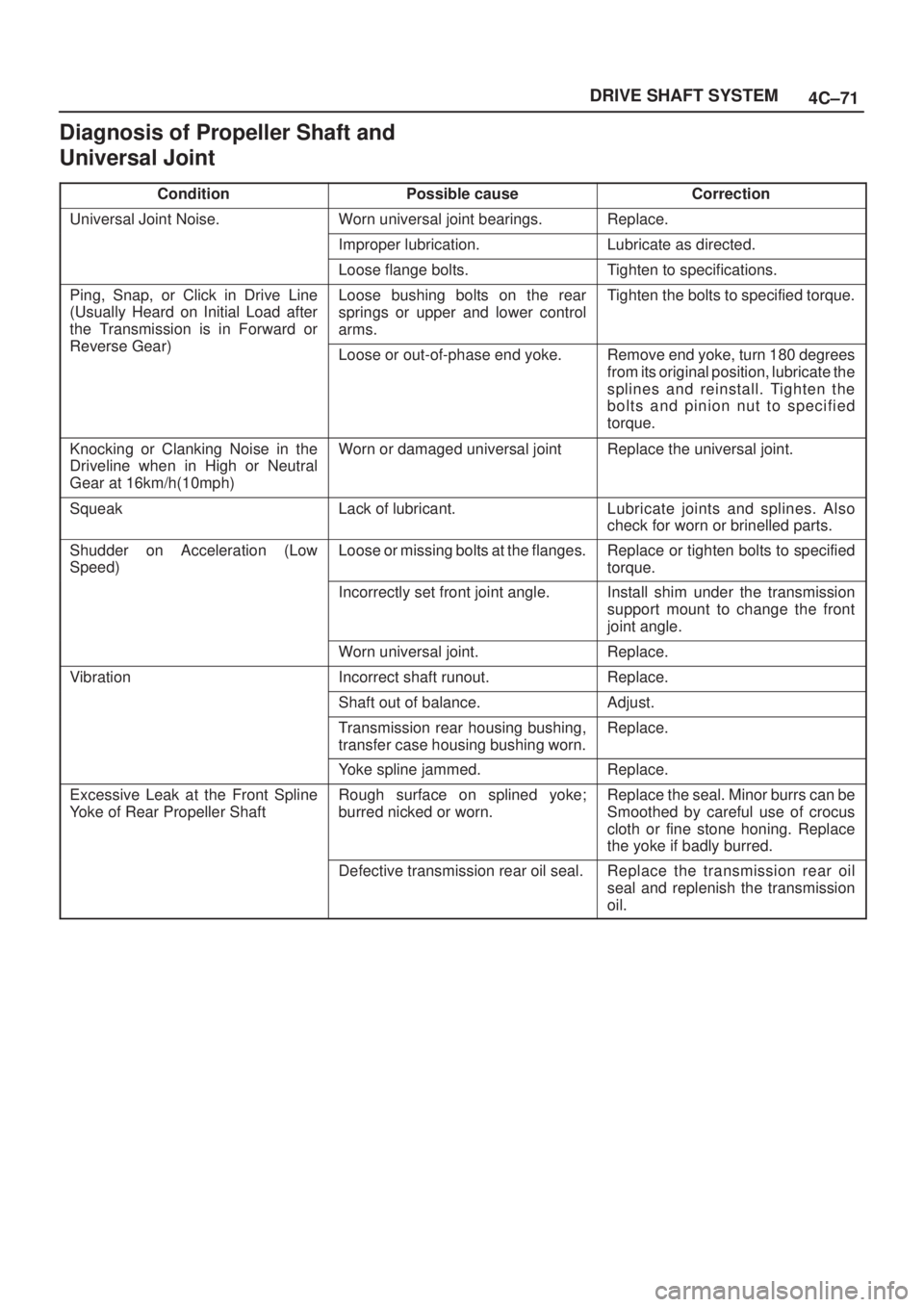
4C±71 DRIVE SHAFT SYSTEM
Diagnosis of Propeller Shaft and
Universal Joint
ConditionPossible causeCorrection
Universal Joint Noise.Worn universal joint bearings.Replace.
Improper lubrication.Lubricate as directed.
Loose flange bolts.Tighten to specifications.
Ping, Snap, or Click in Drive Line
(Usually Heard on Initial Load after
the Transmission is in Forward or
Reverse Gear)
Loose bushing bolts on the rear
springs or upper and lower control
arms.Tighten the bolts to specified torque.
Reverse Gear)Loose or out-of-phase end yoke.Remove end yoke, turn 180 degrees
from its original position, lubricate the
splines and reinstall. Tighten the
bolts and pinion nut to specified
torque.
Knocking or Clanking Noise in the
Driveline when in High or Neutral
Gear at 16km/h(10mph)Worn or damaged universal jointReplace the universal joint.
SqueakLack of lubricant.Lubricate joints and splines. Also
check for worn or brinelled parts.
Shudder on Acceleration (Low
Speed)Loose or missing bolts at the flanges.Replace or tighten bolts to specified
torque.
Incorrectly set front joint angle.Install shim under the transmission
support mount to change the front
joint angle.
Worn universal joint.Replace.
VibrationIncorrect shaft runout.Replace.
Shaft out of balance.Adjust.
Transmission rear housing bushing,
transfer case housing bushing worn.Replace.
Yoke spline jammed.Replace.
Excessive Leak at the Front Spline
Yoke of Rear Propeller ShaftRough surface on splined yoke;
burred nicked or worn.Replace the seal. Minor burrs can be
Smoothed by careful use of crocus
cloth or fine stone honing. Replace
the yoke if badly burred.
Defective transmission rear oil seal.Replace the transmission rear oil
seal and replenish the transmission
oil.
Page 569 of 2100
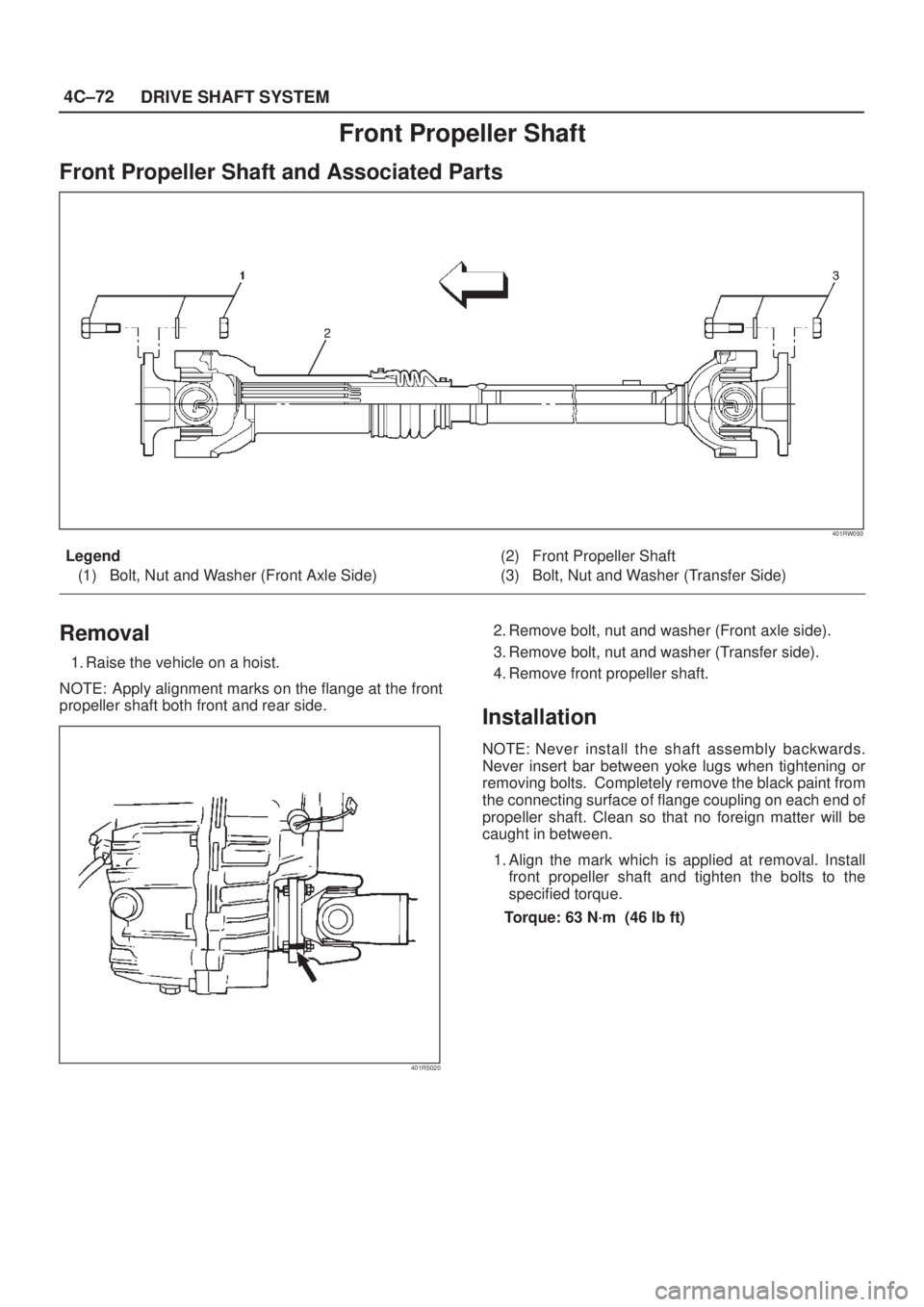
4C±72
DRIVE SHAFT SYSTEM
Front Propeller Shaft
Front Propeller Shaft and Associated Parts
401RW093
Legend
(1) Bolt, Nut and Washer (Front Axle Side)(2) Front Propeller Shaft
(3) Bolt, Nut and Washer (Transfer Side)
Removal
1. Raise the vehicle on a hoist.
NOTE: Apply alignment marks on the flange at the front
propeller shaft both front and rear side.
401RS020
2. Remove bolt, nut and washer (Front axle side).
3. Remove bolt, nut and washer (Transfer side).
4. Remove front propeller shaft.
Installation
NOTE: Never install the shaft assembly backwards.
Never insert bar between yoke lugs when tightening or
removing bolts. Completely remove the black paint from
the connecting surface of flange coupling on each end of
propeller shaft. Clean so that no foreign matter will be
caught in between.
1. Align the mark which is applied at removal. Install
front propeller shaft and tighten the bolts to the
specified torque.
Torque: 63 N´m (46 lb ft)
Page 570 of 2100
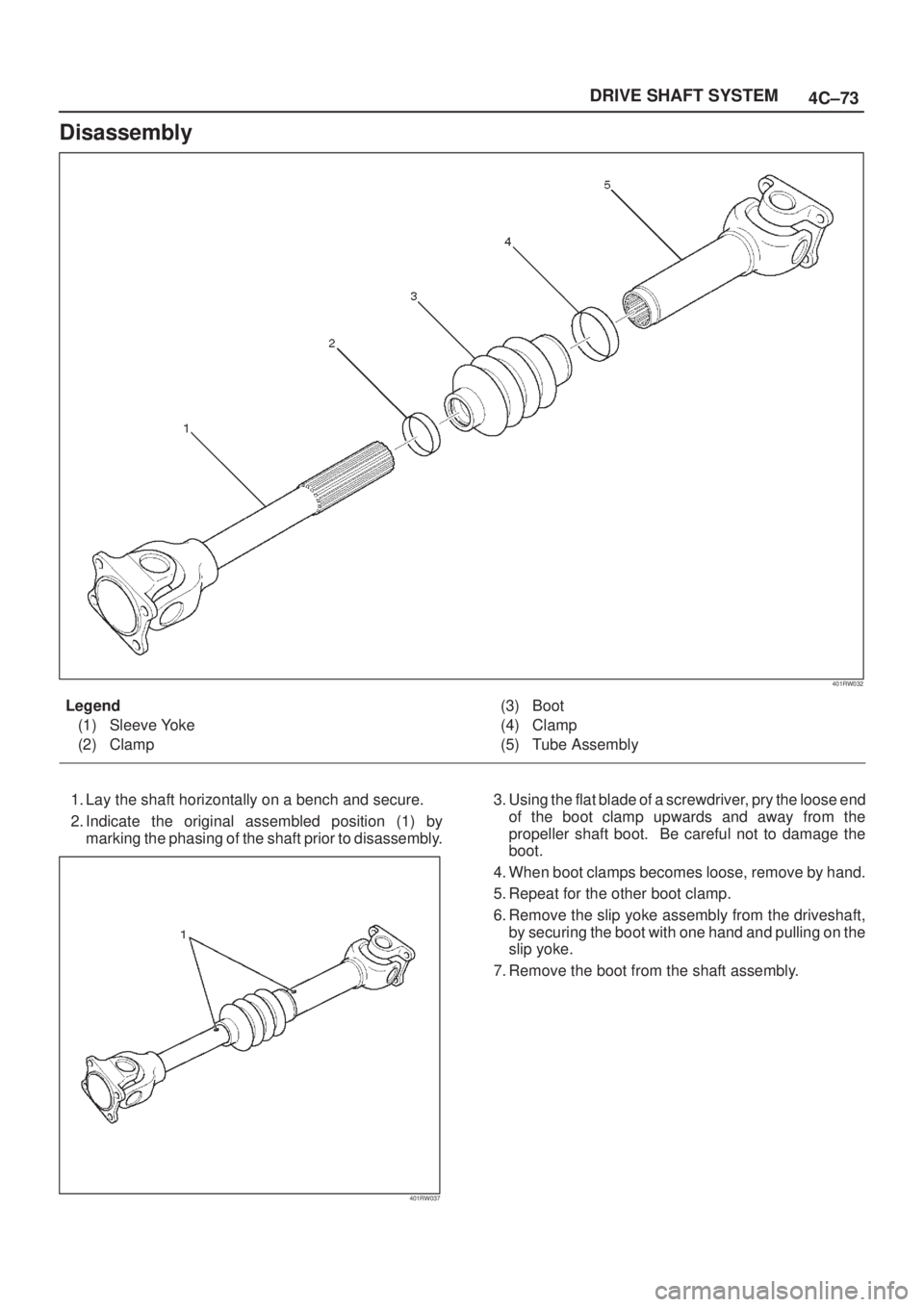
4C±73 DRIVE SHAFT SYSTEM
Disassembly
401RW032
Legend
(1) Sleeve Yoke
(2) Clamp(3) Boot
(4) Clamp
(5) Tube Assembly
1. Lay the shaft horizontally on a bench and secure.
2. Indicate the original assembled position (1) by
marking the phasing of the shaft prior to disassembly.
401RW037
3. Using the flat blade of a screwdriver, pry the loose end
of the boot clamp upwards and away from the
propeller shaft boot. Be careful not to damage the
boot.
4. When boot clamps becomes loose, remove by hand.
5. Repeat for the other boot clamp.
6. Remove the slip yoke assembly from the driveshaft,
by securing the boot with one hand and pulling on the
slip yoke.
7. Remove the boot from the shaft assembly.