wiring ISUZU TF SERIES 2004 Workshop Manual
[x] Cancel search | Manufacturer: ISUZU, Model Year: 2004, Model line: TF SERIES, Model: ISUZU TF SERIES 2004Pages: 4264, PDF Size: 72.63 MB
Page 3752 of 4264
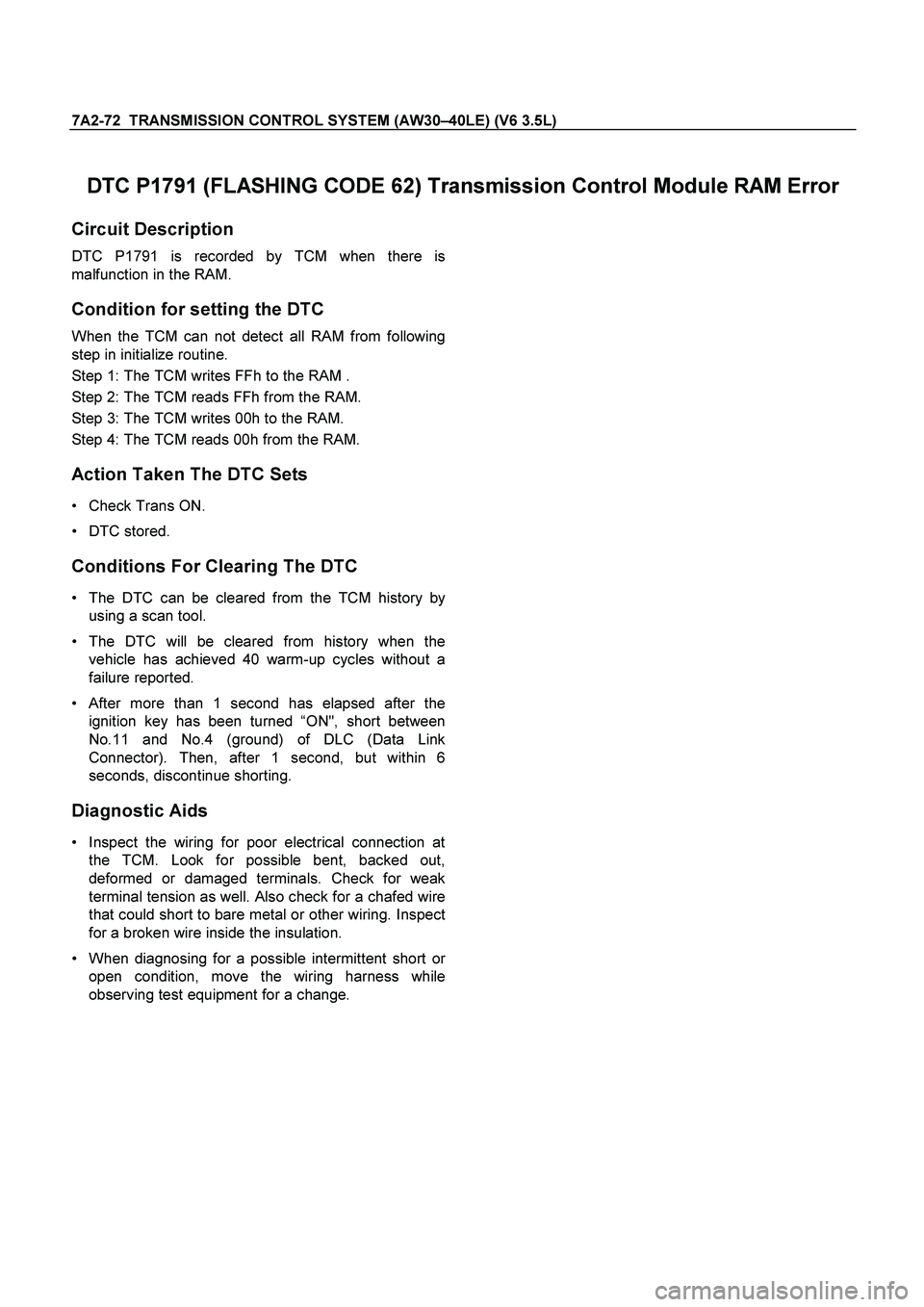
7A2-72 TRANSMISSION CONTROL SYSTEM (AW30–40LE) (V6 3.5L)
DTC P1791 (FLASHING CODE 62) Transmission Control Module RAM Error
Circuit Description
DTC P1791 is recorded by TCM when there is
malfunction in the RAM.
Condition for setting the DTC
When the TCM can not detect all RAM from following
step in initialize routine.
Step 1: The TCM writes FFh to the RAM .
Step 2: The TCM reads FFh from the RAM.
Step 3: The TCM writes 00h to the RAM.
Step 4: The TCM reads 00h from the RAM.
Action Taken The DTC Sets
Check Trans ON.
DTC stored.
Conditions For Clearing The DTC
The DTC can be cleared from the TCM history by
using a scan tool.
The DTC will be cleared from history when the
vehicle has achieved 40 warm-up cycles without a
failure reported.
After more than 1 second has elapsed after the
ignition key has been turned “ON", short between
No.11 and No.4 (ground) of DLC (Data Link
Connector). Then, after 1 second, but within 6
seconds, discontinue shorting.
Diagnostic Aids
Inspect the wiring for poor electrical connection at
the TCM. Look for possible bent, backed out,
deformed or damaged terminals. Check for weak
terminal tension as well. Also check for a chafed wire
that could short to bare metal or other wiring. Inspect
for a broken wire inside the insulation.
When diagnosing for a possible intermittent short o
r
open condition, move the wiring harness while
observing test equipment for a change.
Page 3755 of 4264
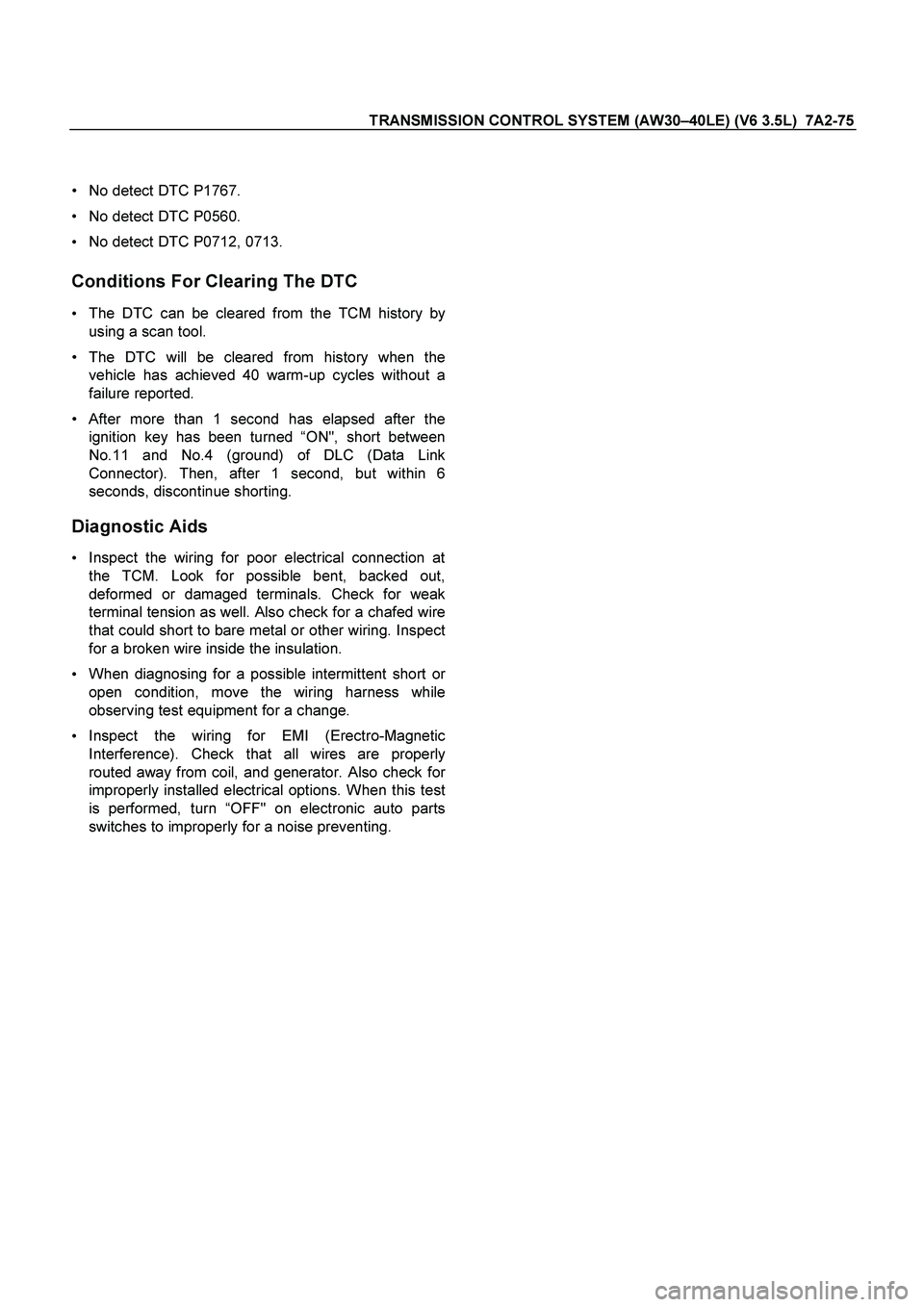
TRANSMISSION CONTROL SYSTEM (AW30–40LE) (V6 3.5L) 7A2-75
No detect DTC P1767.
No detect DTC P0560.
No detect DTC P0712, 0713.
Conditions For Clearing The DTC
The DTC can be cleared from the TCM history by
using a scan tool.
The DTC will be cleared from history when the
vehicle has achieved 40 warm-up cycles without a
failure reported.
After more than 1 second has elapsed after the
ignition key has been turned “ON", short between
No.11 and No.4 (ground) of DLC (Data Link
Connector). Then, after 1 second, but within 6
seconds, discontinue shorting.
Diagnostic Aids
Inspect the wiring for poor electrical connection at
the TCM. Look for possible bent, backed out,
deformed or damaged terminals. Check for weak
terminal tension as well. Also check for a chafed wire
that could short to bare metal or other wiring. Inspect
for a broken wire inside the insulation.
When diagnosing for a possible intermittent short o
r
open condition, move the wiring harness while
observing test equipment for a change.
Inspect the wiring for EMI (Erectro-Magnetic
Interference). Check that all wires are properly
routed away from coil, and generator. Also check fo
r
improperly installed electrical options. When this test
is performed, turn “OFF" on electronic auto parts
switches to improperly for a noise preventing.
Page 3758 of 4264
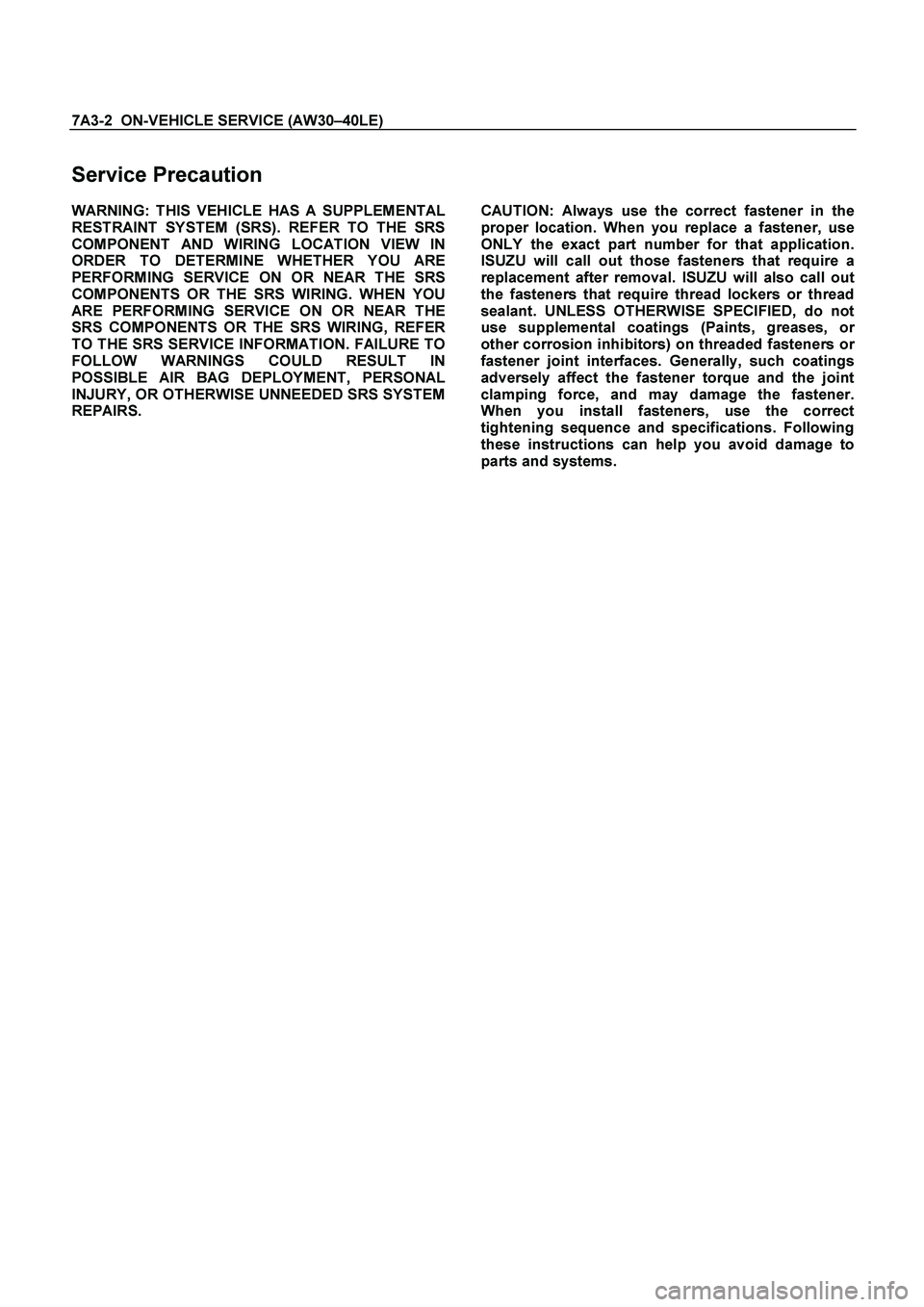
7A3-2 ON-VEHICLE SERVICE (AW30 –40LE)
Service Precaution
WARNING: THIS VEHICLE HAS A SUPPLEMENTAL
RESTRAINT SYSTEM (SRS). REFER TO THE SRS
COMPONENT AND WIRING LOCATION VIEW IN
ORDER TO DETERMINE WHETHER YOU ARE
PERFORMING SERVICE ON OR NEAR THE SRS
COMPONENTS OR THE SRS WIRING. WHEN YOU
ARE PERFORMING SERVICE ON OR NEAR THE
SRS COMPONENTS OR THE SRS WIRING, REFE
R
TO THE SRS SERVICE INFORMATION. FAILURE TO
FOLLOW WARNINGS COULD RESULT IN
POSSIBLE AIR BAG DEPLOYMENT, PERSONAL
INJURY, OR OTHERWISE UNNEEDED SRS SYSTEM
REPAIRS.
CAUTION: Always use the correct fastener in the
proper location. When you replace a fastener, use
ONLY the exact part number for that application.
ISUZU will call out those fasteners that require a
replacement after removal. ISUZU will also call out
the fasteners that require thread lockers or thread
sealant. UNLESS OTHERWISE SPECIFIED, do not
use supplemental coatings (Paints, greases, o
r
other corrosion inhibitors) on threaded fasteners o
r
fastener joint interfaces. Generally, such coatings
adversely affect the fastener torque and the joint
clamping force, and may damage the fastener.
When you install fasteners, use the correct
tightening sequence and specifications. Following
these instructions can help you avoid damage to
parts and systems.
Page 3792 of 4264
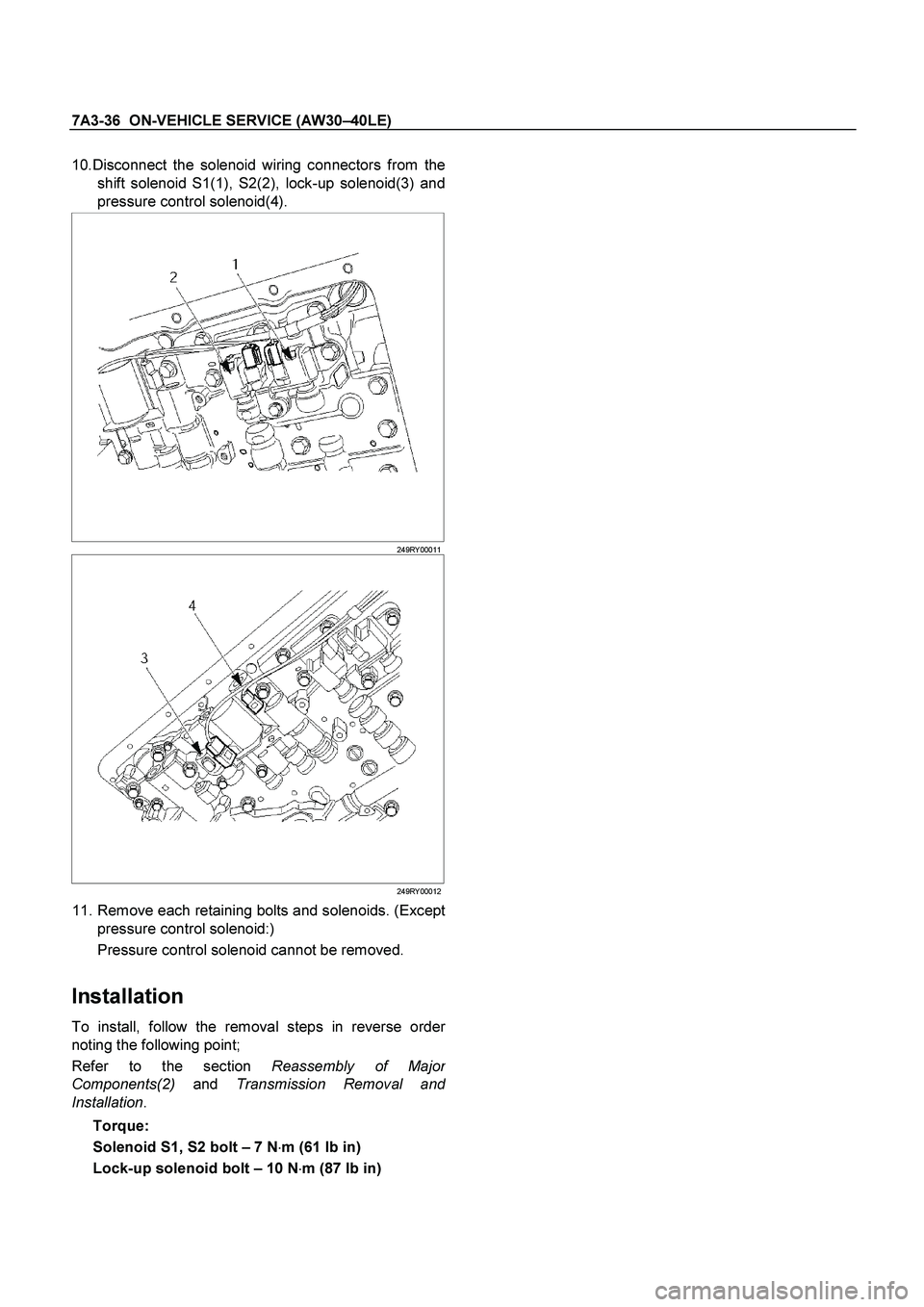
7A3-36 ON-VEHICLE SERVICE (AW30 –40LE)
10.Disconnect the solenoid wiring connectors from the
shift solenoid S1(1), S2(2), lock-up solenoid(3) and
pressure control solenoid(4).
249RY 00011
249RY 00012
11. Remove each retaining bolts and solenoids. (Except
pressure control solenoid:)
Pressure control solenoid cannot be removed.
Installation
To install, follow the removal steps in reverse order
noting the following point;
Refer to the section Reassembly of Majo
r
Components(2) and Transmission Removal an
d
Installation .
Torque:
Solenoid S1, S2 bolt – 7 N m (61 Ib in)
Lock-up solenoid bolt – 10 N m (87 Ib in)
Page 3794 of 4264
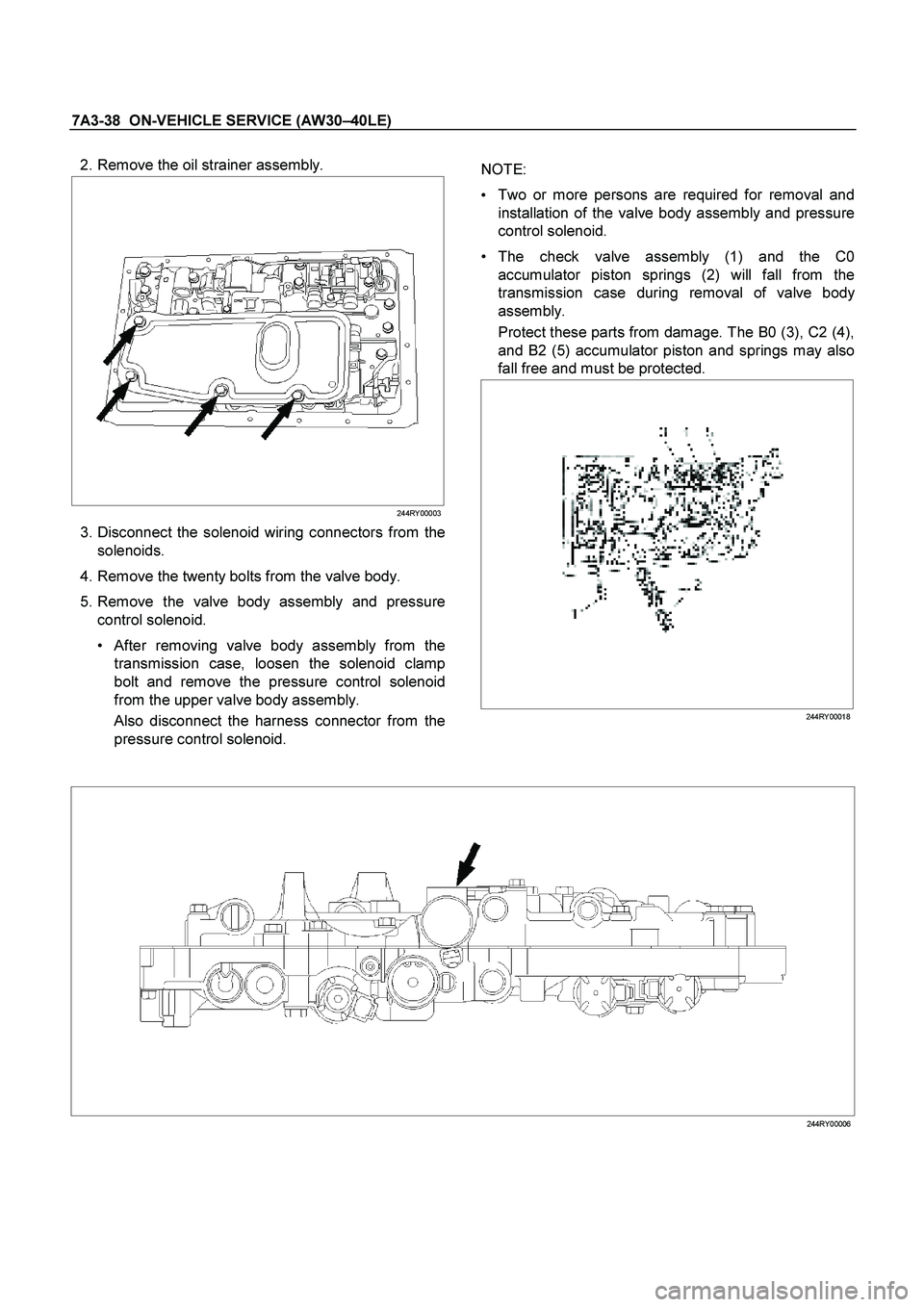
7A3-38 ON-VEHICLE SERVICE (AW30 –40LE)
2. Remove the oil strainer assembly.
244RY 00003
3. Disconnect the solenoid wiring connectors from the
solenoids.
4. Remove the twenty bolts from the valve body.
5. Remove the valve body assembly and pressure control solenoid.
After removing valve body assembly from the
transmission case, loosen the solenoid clamp
bolt and remove the pressure control solenoid
from the upper valve body assembly.
Also disconnect the harness connector from the
pressure control solenoid.
NOTE:
Two or more persons are required for removal and
installation of the valve body assembly and pressure
control solenoid.
The check valve assembly (1) and the C0
accumulator piston springs (2) will fall from the
transmission case during removal of valve bod
y
assembly.
Protect these parts from damage. The B0 (3), C2 (4),
and B2 (5) accumulator piston and springs may also
fall free and must be protected.
244RY00018
244RY00006
Page 3815 of 4264
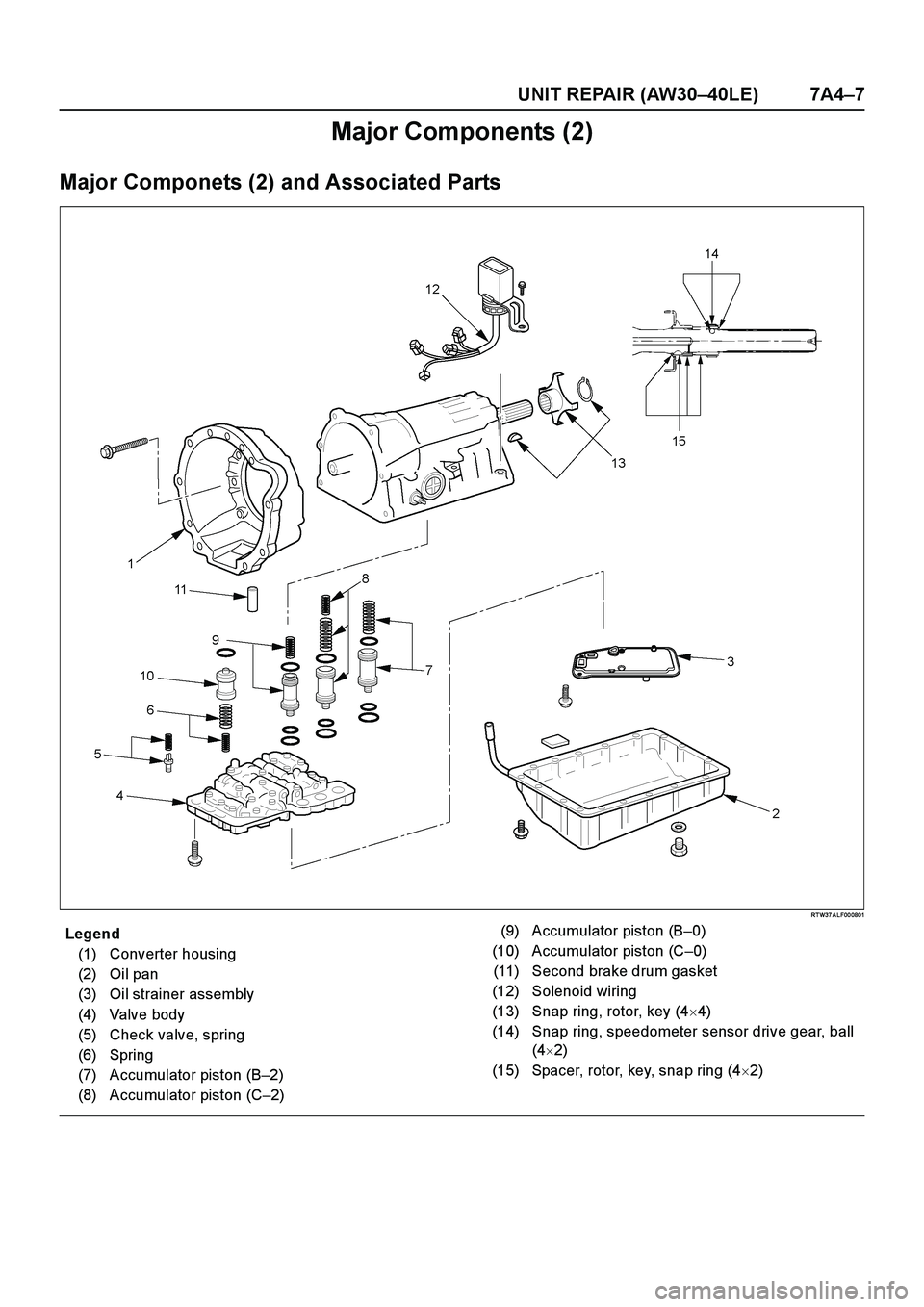
UNIT REPAIR (AW30–40LE) 7A4–7
Major Components (2)
Major Componets (2) and Associated Parts
RT W37 A LF00 0801
E nd O FCallo ut
Legend
(1) Converter housing
(2) Oil pan
(3) Oil strainer assembly
(4) Valve body
(5) Check valve, spring
(6) Spring
(7) Accumulator piston (B–2)
(8) Accumulator piston (C–2)(9) Accumulator piston (B–0)
(10) Accumulator piston (C–0)
(11) Second brake drum gasket
(12) Solenoid wiring
(13) Snap ring, rotor, key (44)
(14) Snap ring, speedometer sensor drive gear, ball
(42)
(15) Spacer, rotor, key, snap ring (42)
Page 3818 of 4264
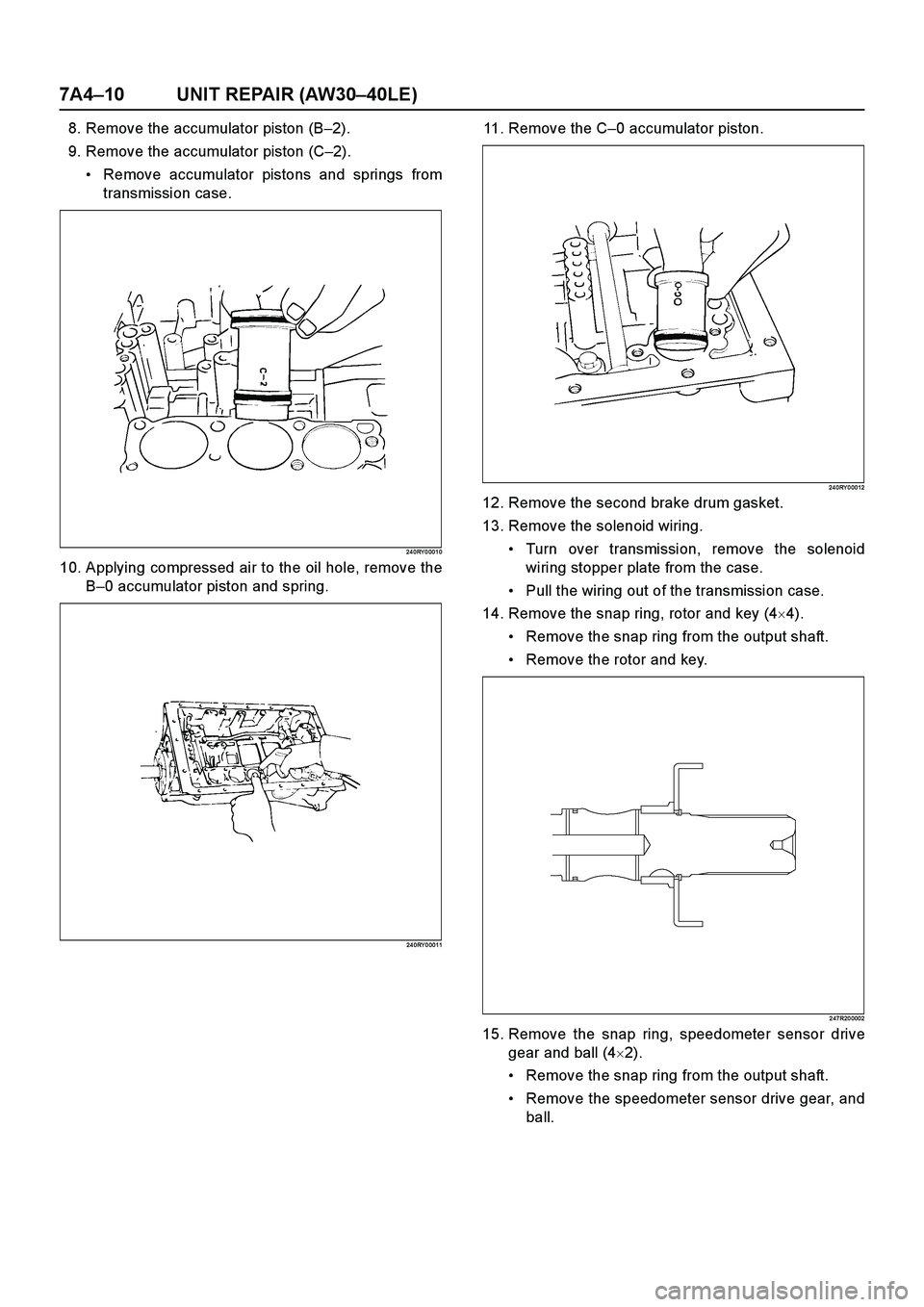
7A4–10 UNIT REPAIR (AW30–40LE)
8. Remove the accumulator piston (B–2).
9. Remove the accumulator piston (C–2).
Remove accumulator pistons and springs from
transmission case.
24 0RY 0 001 0
10. Applying compressed air to the oil hole, remove the
B–0 accumulator piston and spring.
24 0RY 0 0011
11. Remove the C–0 accumulator piston.
24 0RY 0 0012
12. Remove the second brake drum gasket.
13. Remove the solenoid wiring.
Turn over transmission, remove the solenoid
wiring stopper plate from the case.
Pull the wiring out of the transmission case.
14. Remove the snap ring, rotor and key (44).
Remove the snap ring from the output shaft.
Remove the rotor and key.
2 47R20 0002
15. Remove the snap ring, speedometer sensor drive
gear and ball (42).
Remove the snap ring from the output shaft.
Remove the speedometer sensor drive gear, and
ball.
Page 3822 of 4264
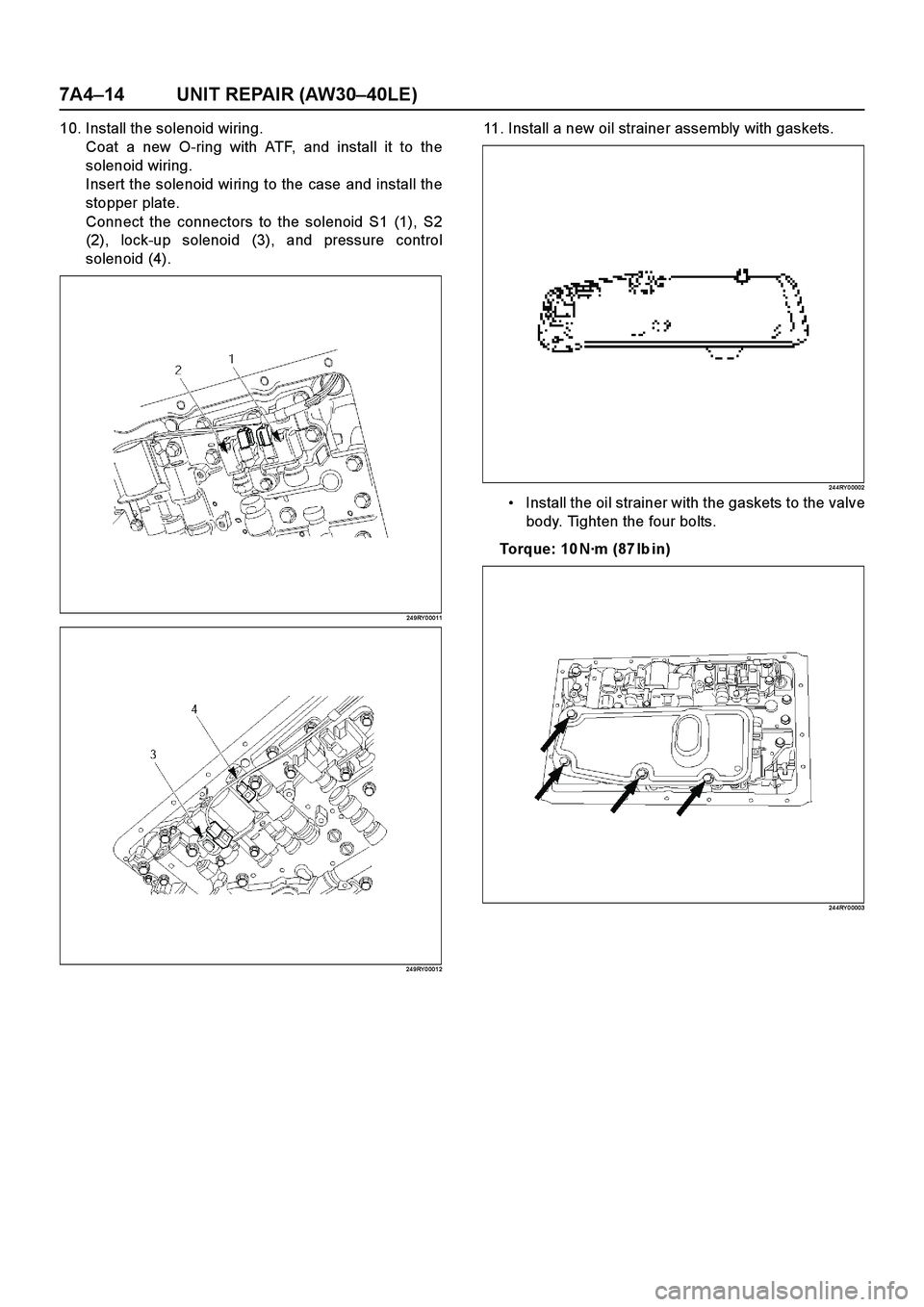
7A4–14 UNIT REPAIR (AW30–40LE)
10. Install the solenoid wiring.
Coat a new O-ring with ATF, and install it to the
solenoid wiring.
Insert the solenoid wiring to the case and install the
stopper plate.
Connect the connectors to the solenoid S1 (1), S2
(2), lock-up solenoid (3), and pressure control
solenoid (4).
24 9RY 0 0011
24 9RY 0 001 2
11. Install a new oil strainer assembly with gaskets.
24 4RY 0 0002
Install the oil strainer with the gaskets to the valve
body. Tighten the four bolts.
Torque: 10 N·m (87lbin)
24 4RY 0 0003
Page 4008 of 4264
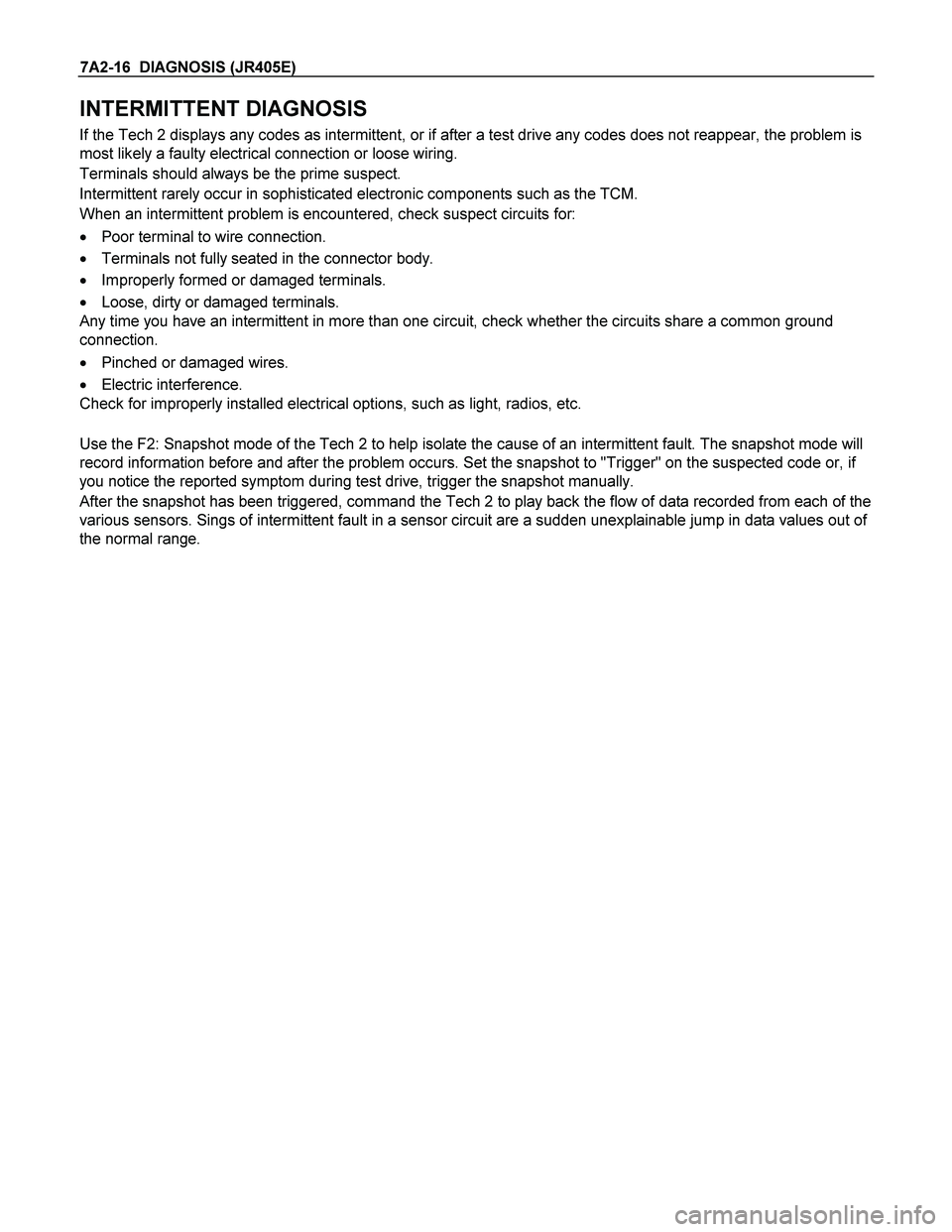
7A2-16 DIAGNOSIS (JR405E)
INTERMITTENT DIAGNOSIS
If the Tech 2 displays any codes as intermittent, or if after a test drive any codes does not reappear, the problem is
most likely a faulty electrical connection or loose wiring.
Terminals should always be the prime suspect.
Intermittent rarely occur in sophisticated electronic components such as the TCM.
When an intermittent problem is encountered, check suspect circuits for:
Poor terminal to wire connection.
Terminals not fully seated in the connector body.
Improperly formed or damaged terminals.
Loose, dirty or damaged terminals.
Any time you have an intermittent in more than one circuit, check whether the circuits share a common ground
connection.
Pinched or damaged wires.
Electric interference.
Check for improperly installed electrical options, such as light, radios, etc.
Use the F2: Snapshot mode of the Tech 2 to help isolate the cause of an intermittent fault. The snapshot mode will
record information before and after the problem occurs. Set the snapshot to "Trigger" on the suspected code or, if
you notice the reported symptom during test drive, trigger the snapshot manually.
After the snapshot has been triggered, command the Tech 2 to play back the flow of data recorded from each of the
various sensors. Sings of intermittent fault in a sensor circuit are a sudden unexplainable jump in data values out of
the normal range.
Page 4146 of 4264
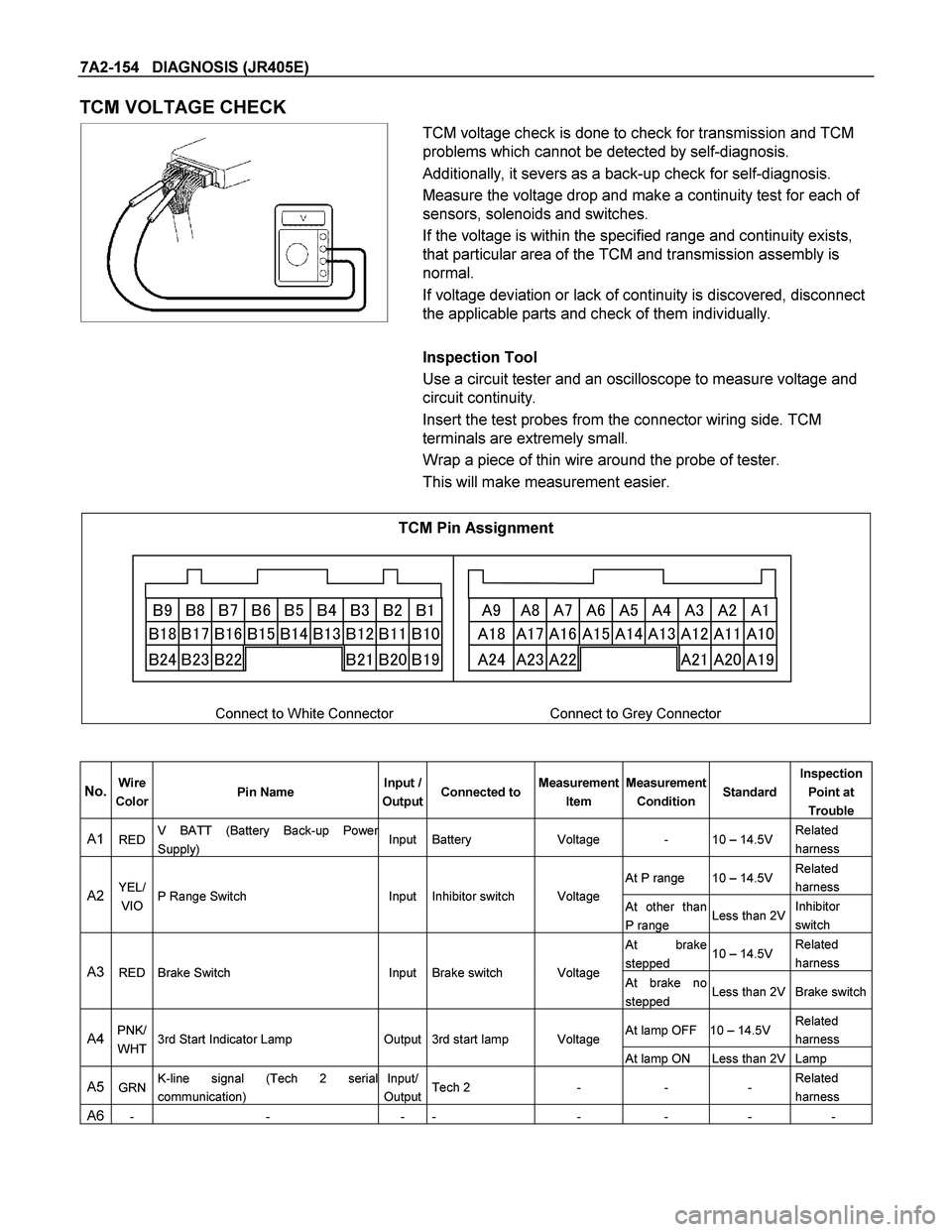
7A2-154 DIAGNOSIS (JR405E)
TCM VOLTAGE CHECK
TCM voltage check is done to check for transmission and TCM
problems which cannot be detected by self-diagnosis.
Additionally, it severs as a back-up check for self-diagnosis.
Measure the voltage drop and make a continuity test for each of
sensors, solenoids and switches.
If the voltage is within the specified range and continuity exists,
that particular area of the TCM and transmission assembly is
normal.
If voltage deviation or lack of continuity is discovered, disconnect
the applicable parts and check of them individually.
Inspection Tool
Use a circuit tester and an oscilloscope to measure voltage and
circuit continuity.
Insert the test probes from the connector wiring side. TCM
terminals are extremely small.
Wrap a piece of thin wire around the probe of tester.
This will make measurement easier.
TCM Pin Assignment
Connect to White Connector Connect to Grey Connector
No. Wire
Color Pin Name Input /
OutputConnected toMeasurement
Item Measurement
Condition StandardInspection
Point at
Trouble
A1 RED V BATT (Battery Back-up Power
Supply) Input Battery Voltage - 10 – 14.5V Related
harness
At P range 10 – 14.5V Related
harness
A2 YEL/
VIO P Range Switch Input Inhibitor switch Voltage
At other than
P range Less than 2VInhibitor
switch
At brake
stepped 10 – 14.5V Related
harness
A3 RED Brake Switch Input Brake switch Voltage At brake no
stepped Less than 2V Brake switch
At lamp OFF 10 – 14.5V Related
harness A4 PNK/
WHT 3rd Start Indicator Lamp Output 3rd start lamp Voltage
At lamp ON Less than 2V Lamp
A5 GRN K-line signal (Tech 2 serial
communication) Input/
OutputTech 2 - - - Related
harness
A6 - - - - - - - -