oil change ISUZU TF SERIES 2004 Owner's Manual
[x] Cancel search | Manufacturer: ISUZU, Model Year: 2004, Model line: TF SERIES, Model: ISUZU TF SERIES 2004Pages: 4264, PDF Size: 72.63 MB
Page 2210 of 4264
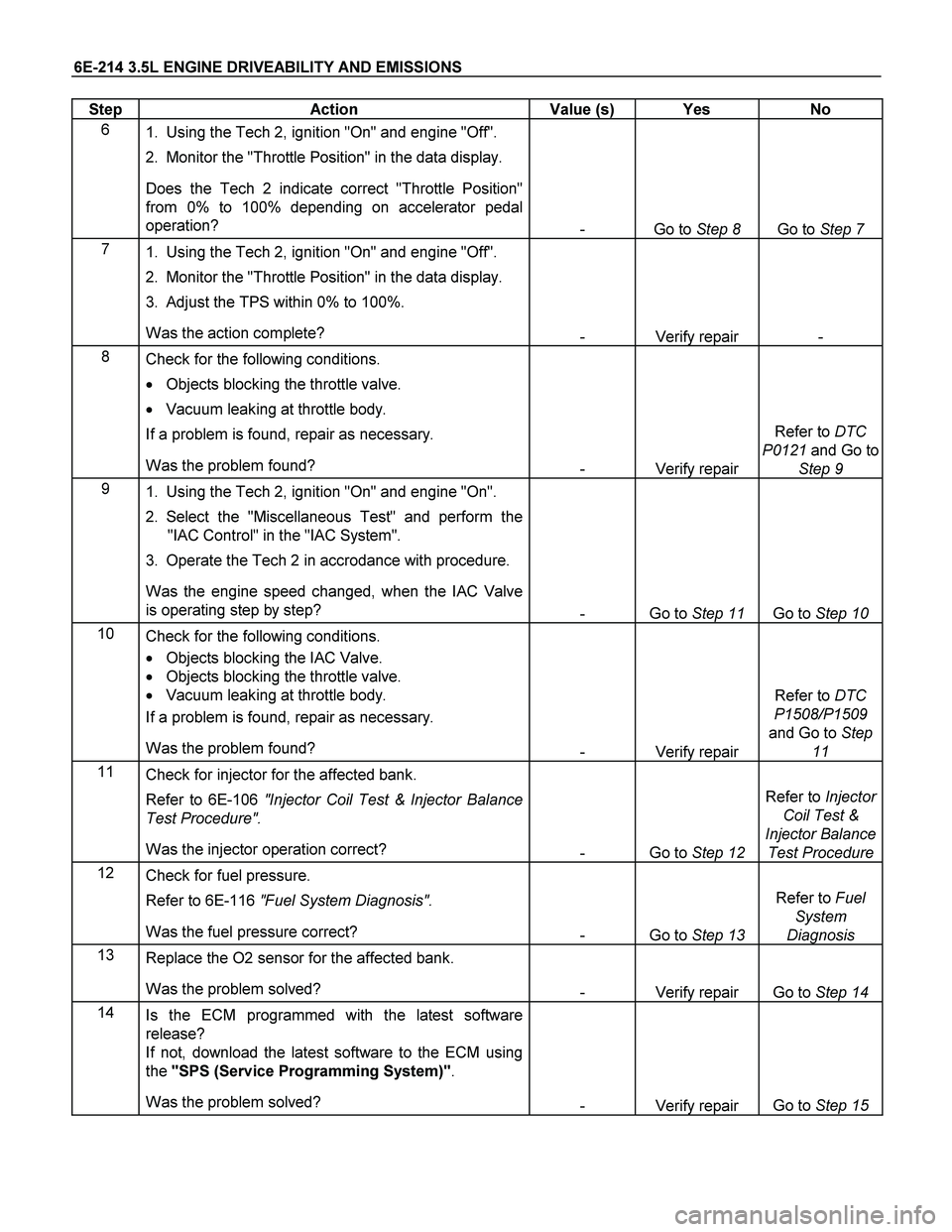
6E-214 3.5L ENGINE DRIVEABILITY AND EMISSIONS
Step Action Value (s) Yes No
6
1. Using the Tech 2, ignition "On" and engine "Off".
2. Monitor the "Throttle Position" in the data display.
Does the Tech 2 indicate correct "Throttle Position"
from 0% to 100% depending on accelerator pedal
operation?
- Go to Step 8 Go to Step 7
7
1. Using the Tech 2, ignition "On" and engine "Off".
2. Monitor the "Throttle Position" in the data display.
3. Adjust the TPS within 0% to 100%.
Was the action complete?
- Verify repair -
8
Check for the following conditions.
Objects blocking the throttle valve.
Vacuum leaking at throttle body.
If a problem is found, repair as necessary.
Was the problem found?
- Verify repair Refer to DTC
P0121 and Go to
Step 9
9
1. Using the Tech 2, ignition "On" and engine "On".
2. Select the "Miscellaneous Test" and perform the
"IAC Control" in the "IAC System".
3. Operate the Tech 2 in accrodance with procedure.
Was the engine speed changed, when the IAC Valve
is operating step by step?
- Go to Step 11 Go to Step 10
10
Check for the following conditions.
Objects blocking the IAC Valve.
Objects blocking the throttle valve.
Vacuum leaking at throttle body.
If a problem is found, repair as necessary.
Was the problem found?
- Verify repair Refer to DTC
P1508/P1509
and Go to Step
11
11
Check for injector for the affected bank.
Refer to 6E-106 "Injector Coil Test & Injector Balance
Test Procedure".
Was the injector operation correct?
- Go to Step 12 Refer to Injector
Coil Test &
Injector Balance
Test Procedure
12
Check for fuel pressure.
Refer to 6E-116 "Fuel System Diagnosis".
Was the fuel pressure correct?
- Go to Step 13 Refer to Fuel
System
Diagnosis
13
Replace the O2 sensor for the affected bank.
Was the problem solved?
- Verify repair Go to Step 14
14
Is the ECM programmed with the latest software
release?
If not, download the latest software to the ECM using
the "SPS (Service Programming System)".
Was the problem solved?
- Verify repair Go to Step 15
Page 2215 of 4264
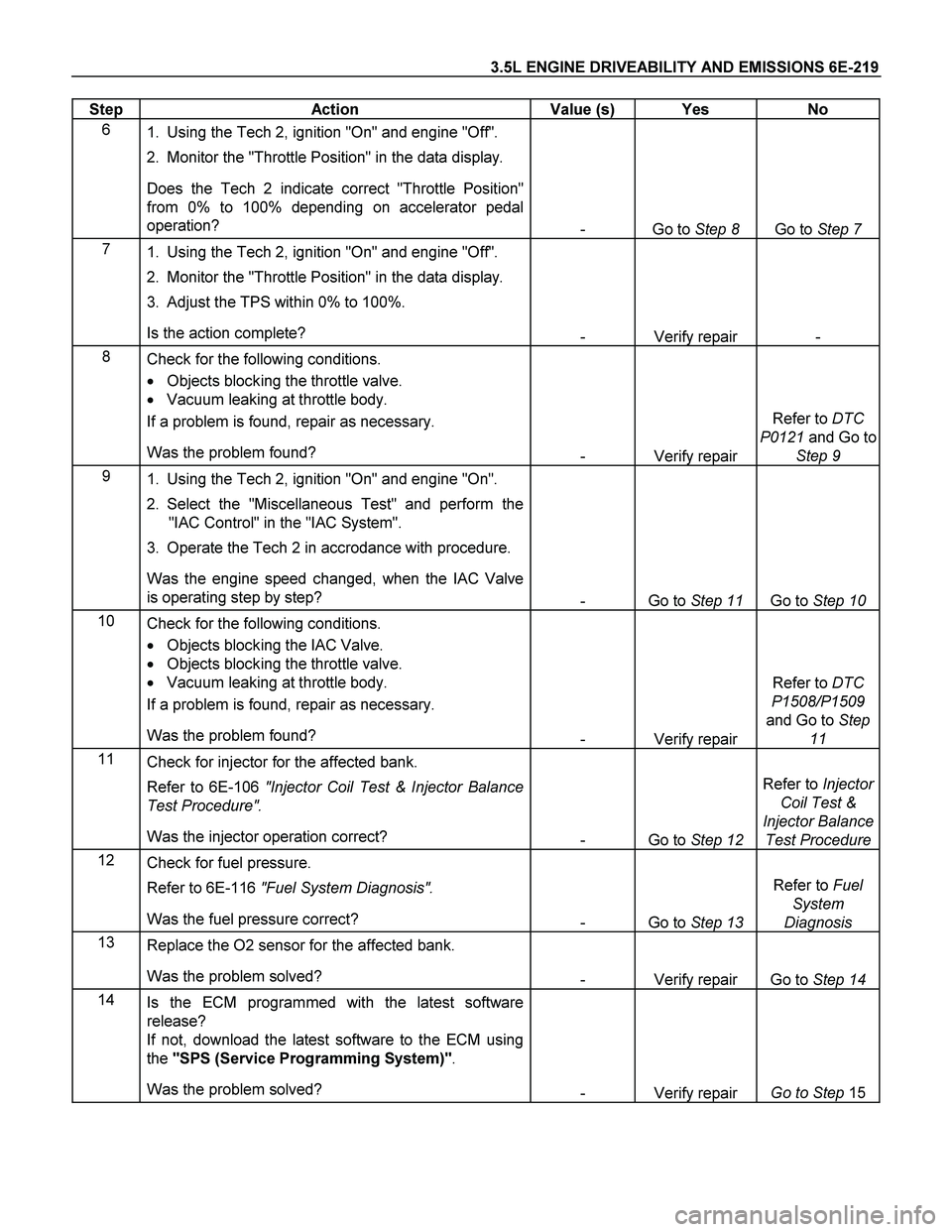
3.5L ENGINE DRIVEABILITY AND EMISSIONS 6E-219
Step Action Value (s) Yes No
6
1. Using the Tech 2, ignition "On" and engine "Off".
2. Monitor the "Throttle Position" in the data display.
Does the Tech 2 indicate correct "Throttle Position"
from 0% to 100% depending on accelerator pedal
operation?
- Go to Step 8 Go to Step 7
7
1. Using the Tech 2, ignition "On" and engine "Off".
2. Monitor the "Throttle Position" in the data display.
3. Adjust the TPS within 0% to 100%.
Is the action complete?
- Verify repair -
8
Check for the following conditions.
Objects blocking the throttle valve.
Vacuum leaking at throttle body.
If a problem is found, repair as necessary.
Was the problem found?
- Verify repair Refer to DTC
P0121 and Go to
Step 9
9
1. Using the Tech 2, ignition "On" and engine "On".
2. Select the "Miscellaneous Test" and perform the
"IAC Control" in the "IAC System".
3. Operate the Tech 2 in accrodance with procedure.
Was the engine speed changed, when the IAC Valve
is operating step by step?
-
Go to Step 11
Go to Step 10
10
Check for the following conditions.
Objects blocking the IAC Valve.
Objects blocking the throttle valve.
Vacuum leaking at throttle body.
If a problem is found, repair as necessary.
Was the problem found?
- Verify repair Refer to DTC
P1508/P1509
and Go to Step
11
11
Check for injector for the affected bank.
Refer to 6E-106 "Injector Coil Test & Injector Balance
Test Procedure".
Was the injector operation correct?
- Go to Step 12 Refer to Injector
Coil Test &
Injector Balance
Test Procedure
12
Check for fuel pressure.
Refer to 6E-116 "Fuel System Diagnosis".
Was the fuel pressure correct?
- Go to Step 13 Refer to Fuel
System
Diagnosis
13
Replace the O2 sensor for the affected bank.
Was the problem solved?
- Verify repair Go to Step 14
14
Is the ECM programmed with the latest software
release?
If not, download the latest software to the ECM using
the "SPS (Service Programming System)".
Was the problem solved?
- Verify repair Go to Step 15
Page 2220 of 4264
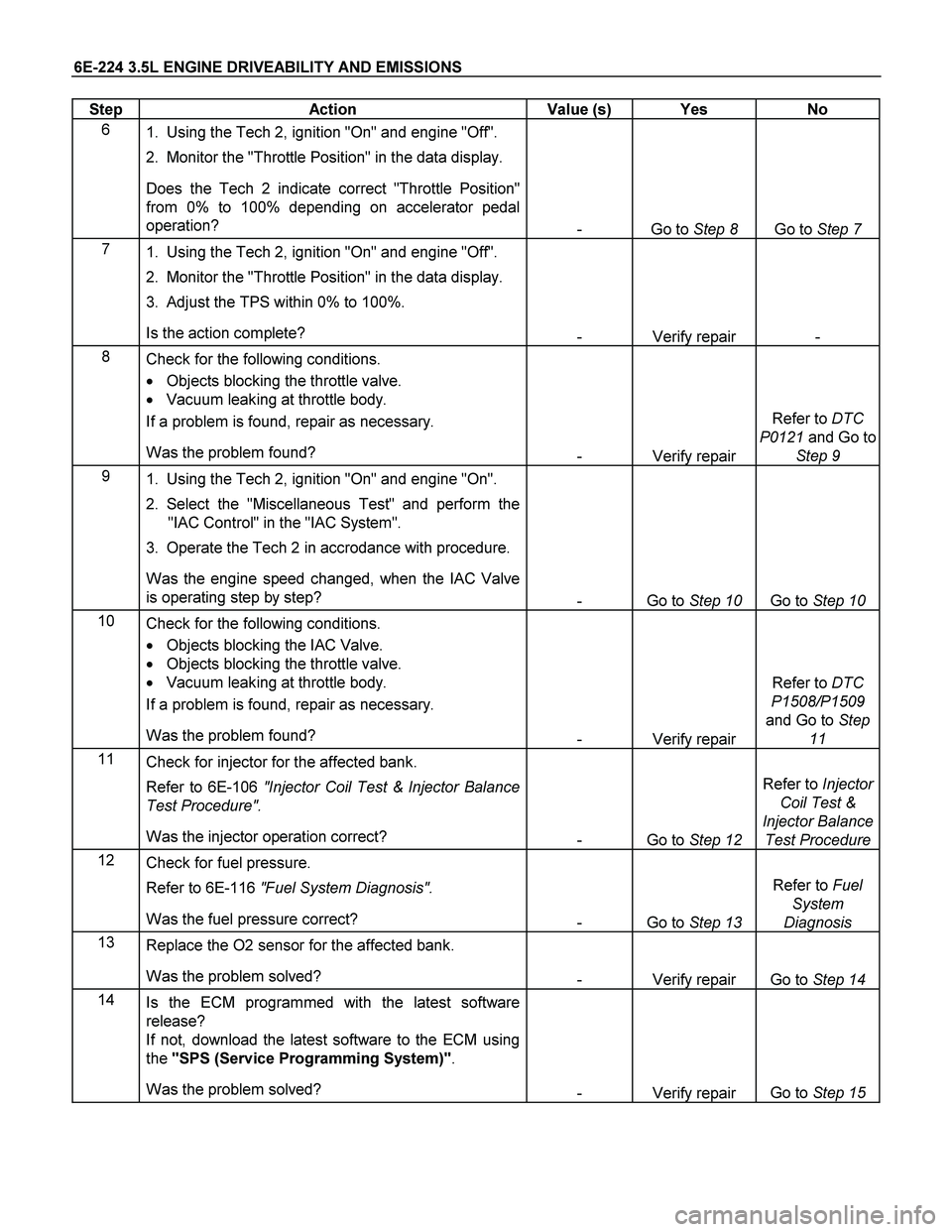
6E-224 3.5L ENGINE DRIVEABILITY AND EMISSIONS
Step Action Value (s) Yes No
6
1. Using the Tech 2, ignition "On" and engine "Off".
2. Monitor the "Throttle Position" in the data display.
Does the Tech 2 indicate correct "Throttle Position"
from 0% to 100% depending on accelerator pedal
operation?
- Go to Step 8 Go to Step 7
7
1. Using the Tech 2, ignition "On" and engine "Off".
2. Monitor the "Throttle Position" in the data display.
3. Adjust the TPS within 0% to 100%.
Is the action complete?
- Verify repair -
8
Check for the following conditions.
Objects blocking the throttle valve.
Vacuum leaking at throttle body.
If a problem is found, repair as necessary.
Was the problem found?
- Verify repair Refer to DTC
P0121 and Go to
Step 9
9
1. Using the Tech 2, ignition "On" and engine "On".
2. Select the "Miscellaneous Test" and perform the
"IAC Control" in the "IAC System".
3. Operate the Tech 2 in accrodance with procedure.
Was the engine speed changed, when the IAC Valve
is operating step by step?
-
Go to Step 10
Go to Step 10
10
Check for the following conditions.
Objects blocking the IAC Valve.
Objects blocking the throttle valve.
Vacuum leaking at throttle body.
If a problem is found, repair as necessary.
Was the problem found?
- Verify repair Refer to DTC
P1508/P1509
and Go to Step
11
11
Check for injector for the affected bank.
Refer to 6E-106 "Injector Coil Test & Injector Balance
Test Procedure".
Was the injector operation correct?
- Go to Step 12 Refer to Injector
Coil Test &
Injector Balance
Test Procedure
12
Check for fuel pressure.
Refer to 6E-116 "Fuel System Diagnosis".
Was the fuel pressure correct?
- Go to Step 13 Refer to Fuel
System
Diagnosis
13
Replace the O2 sensor for the affected bank.
Was the problem solved?
- Verify repair Go to Step 14
14
Is the ECM programmed with the latest software
release?
If not, download the latest software to the ECM using
the "SPS (Service Programming System)".
Was the problem solved?
- Verify repair Go to Step 15
Page 2246 of 4264
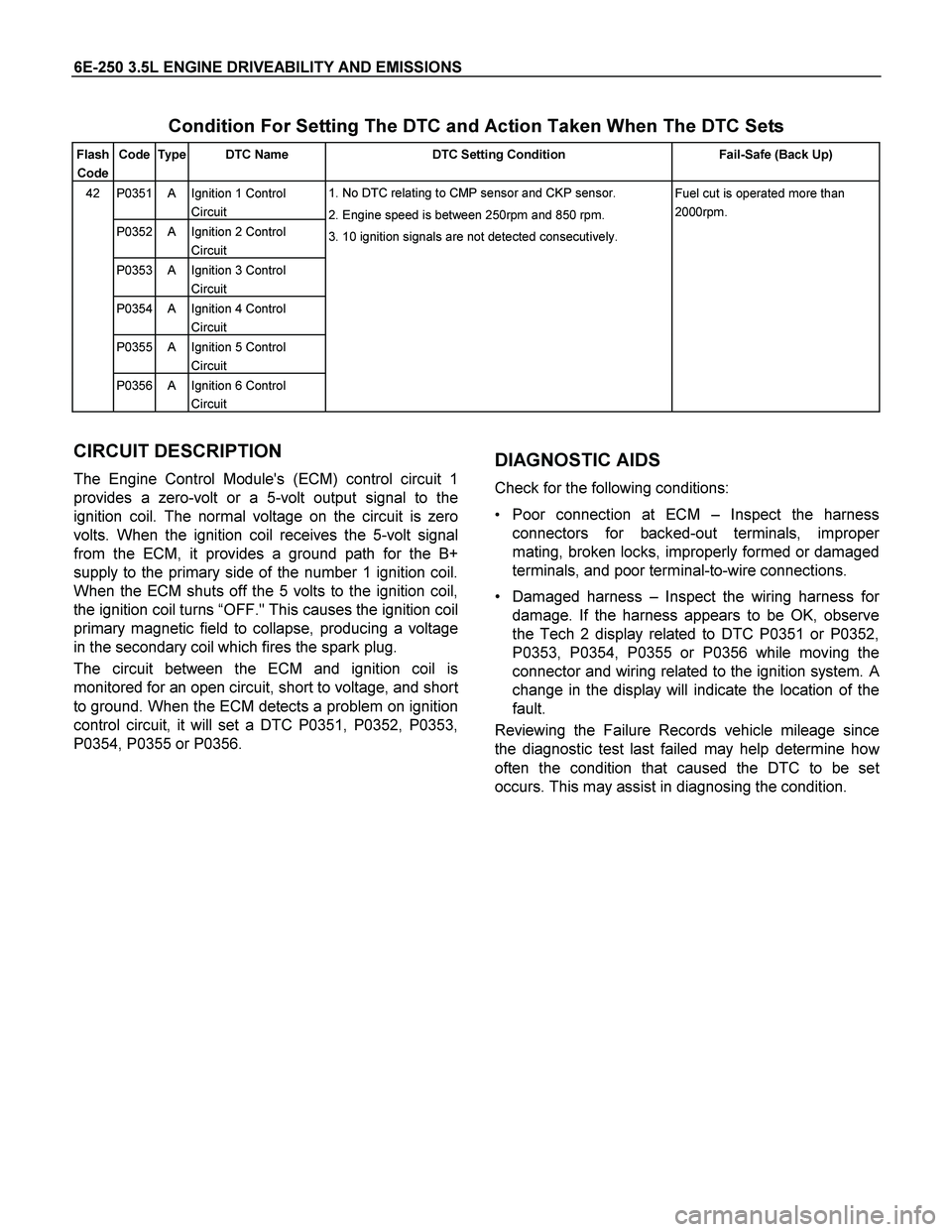
6E-250 3.5L ENGINE DRIVEABILITY AND EMISSIONS
Condition For Setting The DTC and Action Taken When The DTC Sets
Flash
Code Code Type DTC Name DTC Setting Condition Fail-Safe (Back Up)
P0351 A Ignition 1 Control
Circuit
P0352 A Ignition 2 Control
Circuit
P0353 A Ignition 3 Control
Circuit
P0354 A Ignition 4 Control
Circuit
P0355 A Ignition 5 Control
Circuit
42
P0356 A Ignition 6 Control
Circuit 1. No DTC relating to CMP sensor and CKP sensor.
2. Engine speed is between 250rpm and 850 rpm.
3. 10 ignition signals are not detected consecutively. Fuel cut is operated more than
2000rpm.
CIRCUIT DESCRIPTION
The Engine Control Module's (ECM) control circuit 1
provides a zero-volt or a 5-volt output signal to the
ignition coil. The normal voltage on the circuit is zero
volts. When the ignition coil receives the 5-volt signal
from the ECM, it provides a ground path for the B+
supply to the primary side of the number 1 ignition coil.
When the ECM shuts off the 5 volts to the ignition coil,
the ignition coil turns “OFF." This causes the ignition coil
primary magnetic field to collapse, producing a voltage
in the secondary coil which fires the spark plug.
The circuit between the ECM and ignition coil is
monitored for an open circuit, short to voltage, and shor
t
to ground. When the ECM detects a problem on ignition
control circuit, it will set a DTC P0351, P0352, P0353,
P0354, P0355 or P0356.
DIAGNOSTIC AIDS
Check for the following conditions:
Poor connection at ECM – Inspect the harness
connectors for backed-out terminals, imprope
r
mating, broken locks, improperly formed or damaged
terminals, and poor terminal-to-wire connections.
Damaged harness –Inspect the wiring harness fo
r
damage. If the harness appears to be OK, observe
the Tech 2 display related to DTC P0351 or P0352,
P0353, P0354, P0355 or P0356 while moving the
connector and wiring related to the ignition system.
A
change in the display will indicate the location of the
fault.
Reviewing the Failure Records vehicle mileage since
the diagnostic test last failed may help determine ho
w
often the condition that caused the DTC to be set
occurs. This may assist in diagnosing the condition.
Page 2293 of 4264
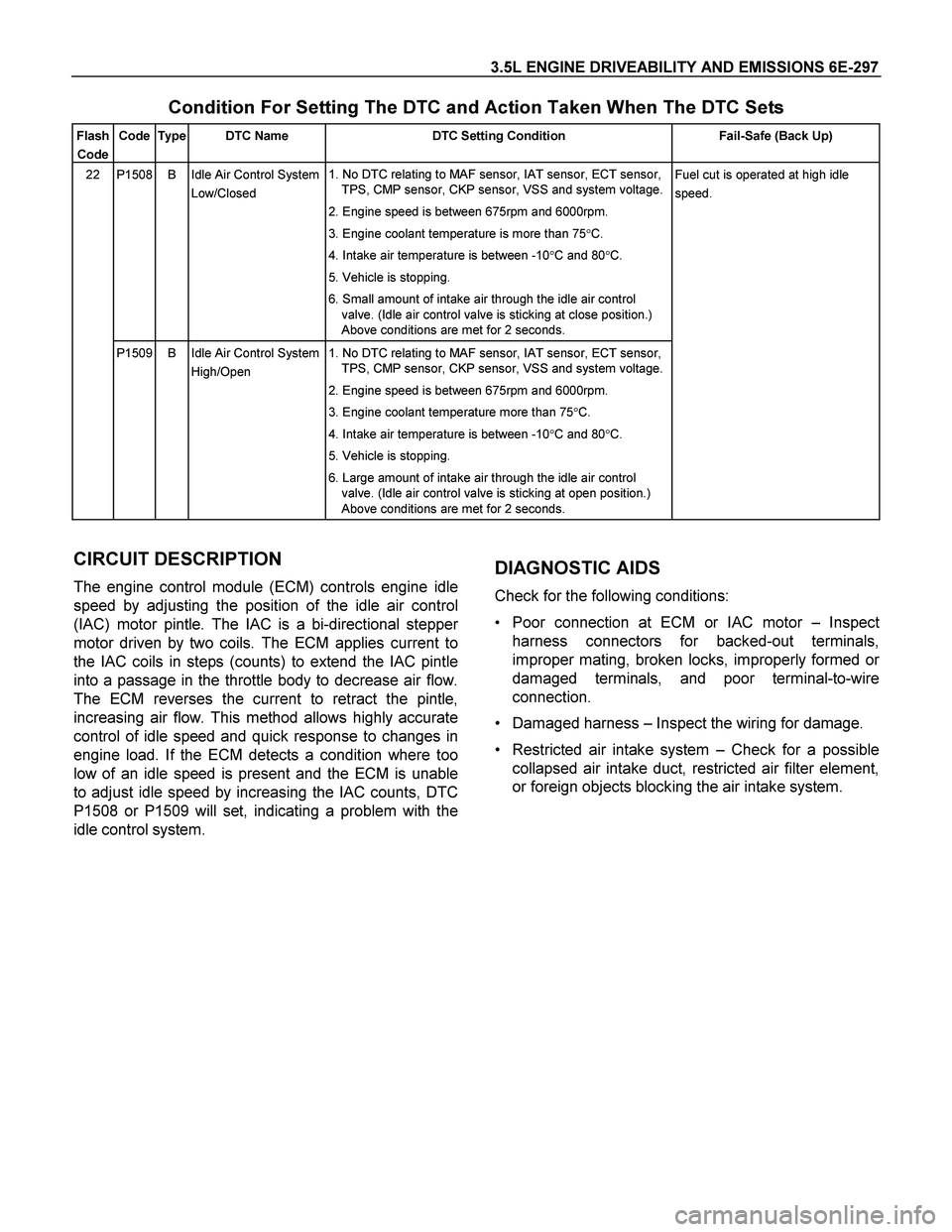
3.5L ENGINE DRIVEABILITY AND EMISSIONS 6E-297
Condition For Setting The DTC and Action Taken When The DTC Sets
Flash
Code Code Type DTC Name DTC Setting Condition Fail-Safe (Back Up)
P1508 B Idle Air Control System
Low/Closed 1. No DTC relating to MAF sensor, IAT sensor, ECT sensor,
TPS, CMP sensor, CKP sensor, VSS and system voltage.
2. Engine speed is between 675rpm and 6000rpm.
3. Engine coolant temperature is more than 75C.
4. Intake air temperature is between -10C and 80C.
5. Vehicle is stopping.
6. Small amount of intake air through the idle air control
valve. (Idle air control valve is sticking at close position.)
Above conditions are met for 2 seconds. 22
P1509 B Idle Air Control System
High/Open 1. No DTC relating to MAF sensor, IAT sensor, ECT sensor,
TPS, CMP sensor, CKP sensor, VSS and system voltage.
2. Engine speed is between 675rpm and 6000rpm.
3. Engine coolant temperature more than 75C.
4. Intake air temperature is between -10C and 80C.
5. Vehicle is stopping.
6. Large amount of intake air through the idle air control
valve. (Idle air control valve is sticking at open position.)
Above conditions are met for 2 seconds. Fuel cut is operated at high idle
speed.
CIRCUIT DESCRIPTION
The engine control module (ECM) controls engine idle
speed by adjusting the position of the idle air control
(IAC) motor pintle. The IAC is a bi-directional steppe
r
motor driven by two coils. The ECM applies current to
the IAC coils in steps (counts) to extend the IAC pintle
into a passage in the throttle body to decrease air flow.
The ECM reverses the current to retract the pintle,
increasing air flow. This method allows highly accurate
control of idle speed and quick response to changes in
engine load. If the ECM detects a condition where too
low of an idle speed is present and the ECM is unable
to adjust idle speed by increasing the IAC counts, DTC
P1508 or P1509 will set, indicating a problem with the
idle control system.
DIAGNOSTIC AIDS
Check for the following conditions:
Poor connection at ECM or IAC motor –Inspec
t
harness connectors for backed-out terminals,
improper mating, broken locks, improperly formed o
r
damaged terminals, and poor terminal-to-wire
connection.
Damaged harness – Inspect the wiring for damage.
Restricted air intake system – Check for a possible
collapsed air intake duct, restricted air filter element,
or foreign objects blocking the air intake system.
Page 2300 of 4264
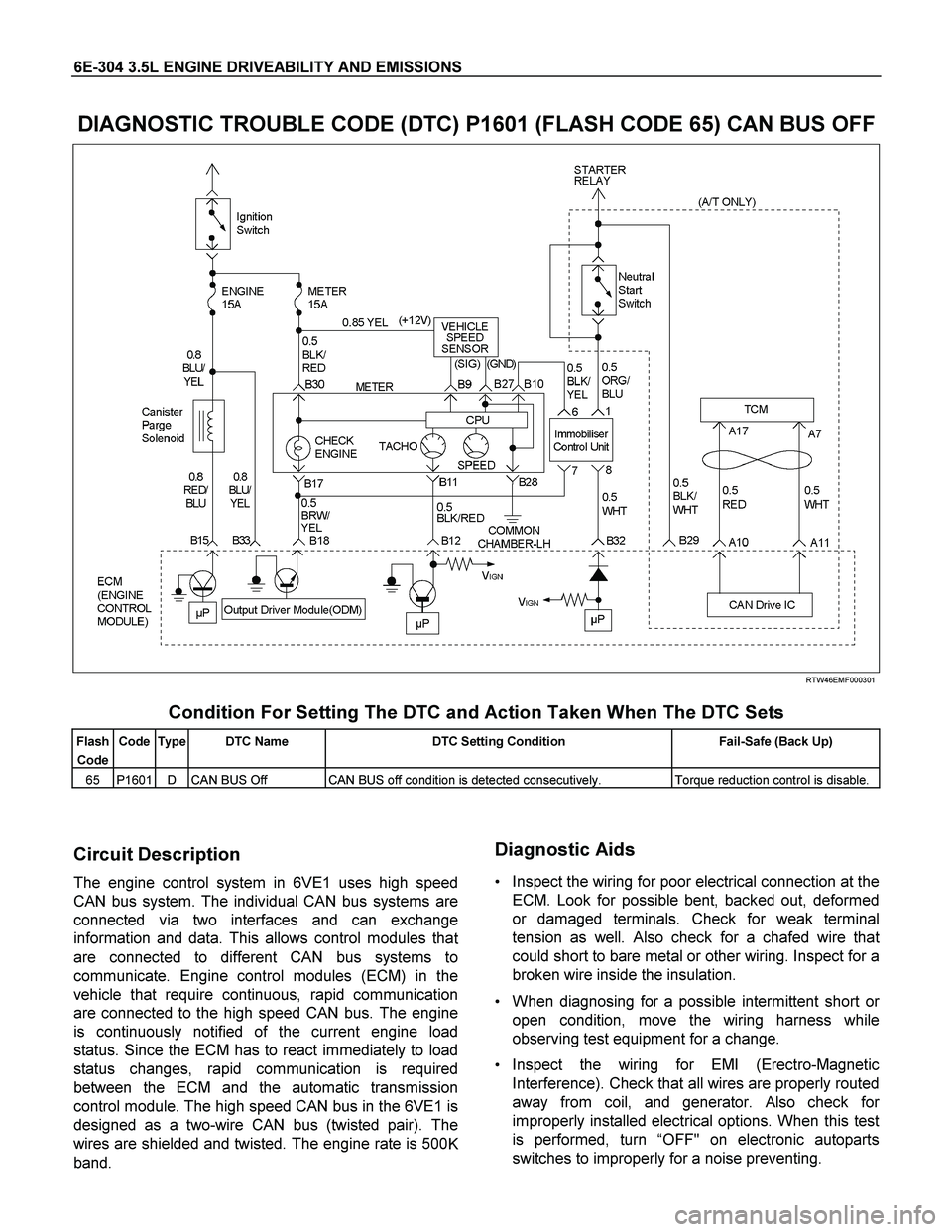
6E-304 3.5L ENGINE DRIVEABILITY AND EMISSIONS
DIAGNOSTIC TROUBLE CODE (DTC) P1601 (FLASH CODE 65) CAN BUS OFF
RTW46EMF000301
Condition For Setting The DTC and Action Taken When The DTC Sets
Flash
Code Code Type DTC Name DTC Setting Condition Fail-Safe (Back Up)
65 P1601 D CAN BUS Off CAN BUS off condition is detected consecutively. Torque reduction control is disable.
Circuit Description
The engine control system in 6VE1 uses high speed
CAN bus system. The individual CAN bus systems are
connected via two interfaces and can exchange
information and data. This allows control modules tha
t
are connected to different CAN bus systems to
communicate. Engine control modules (ECM) in the
vehicle that require continuous, rapid communication
are connected to the high speed CAN bus. The engine
is continuously notified of the current engine load
status. Since the ECM has to react immediately to load
status changes, rapid communication is required
between the ECM and the automatic transmission
control module. The high speed CAN bus in the 6VE1 is
designed as a two-wire CAN bus (twisted pair). The
wires are shielded and twisted. The engine rate is 500
K
band.
Diagnostic Aids
Inspect the wiring for poor electrical connection at the
ECM. Look for possible bent, backed out, deformed
or damaged terminals. Check for weak terminal
tension as well. Also check for a chafed wire tha
t
could short to bare metal or other wiring. Inspect for a
broken wire inside the insulation.
When diagnosing for a possible intermittent short o
r
open condition, move the wiring harness while
observing test equipment for a change.
Inspect the wiring for EMI (Erectro-Magnetic
Interference). Check that all wires are properly routed
away from coil, and generator. Also check fo
r
improperly installed electrical options. When this test
is performed, turn “OFF" on electronic autoparts
switches to improperly for a noise preventing.
Page 2306 of 4264
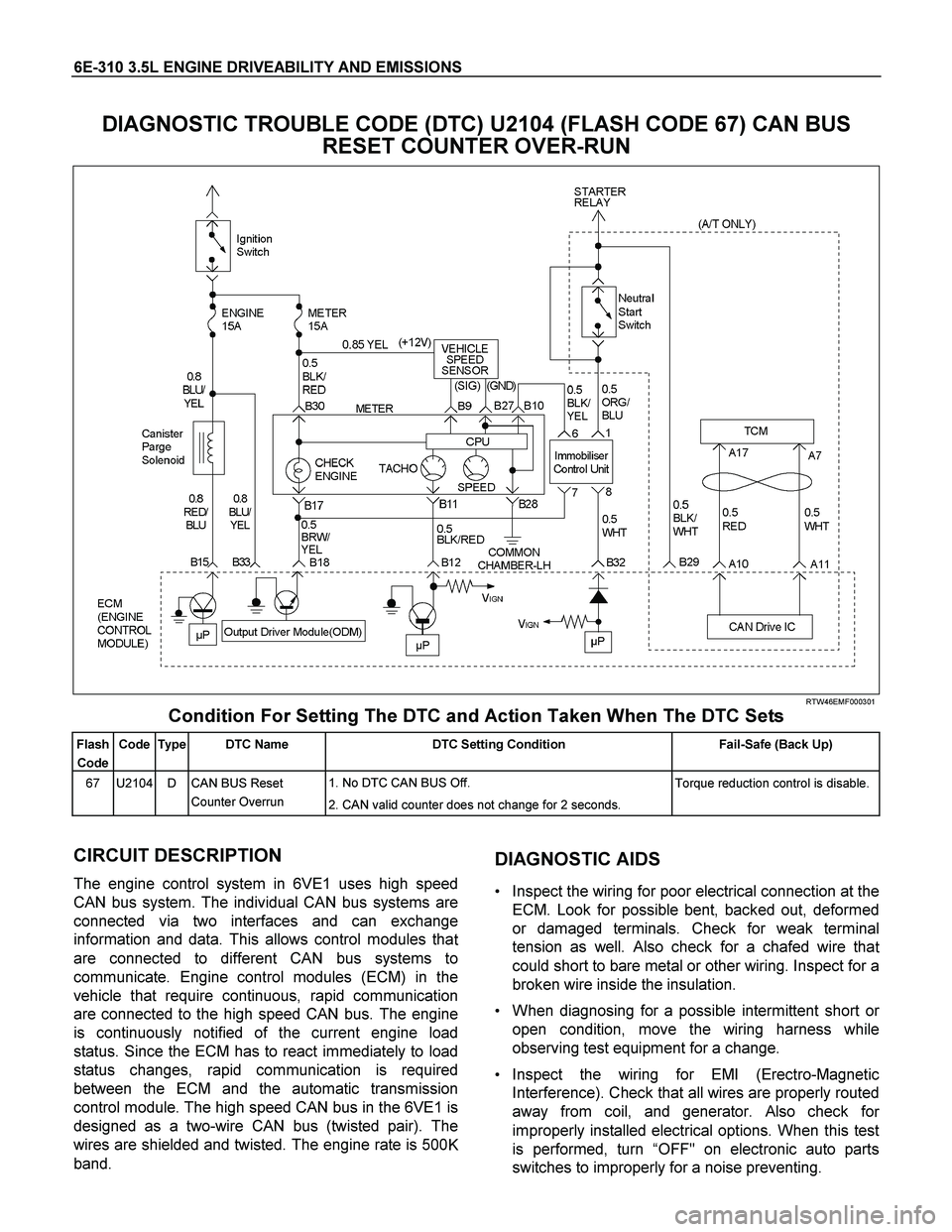
6E-310 3.5L ENGINE DRIVEABILITY AND EMISSIONS
DIAGNOSTIC TROUBLE CODE (DTC) U2104 (FLASH CODE 67) CAN BUS
RESET COUNTER OVER-RUN
RTW46EMF000301
Condition For Setting The DTC and Action Taken When The DTC Sets
Flash
Code Code Type DTC Name DTC Setting Condition Fail-Safe (Back Up)
67 U2104 D CAN BUS Reset
Counter Overrun 1. No DTC CAN BUS Off.
2. CAN valid counter does not change for 2 seconds. Torque reduction control is disable.
CIRCUIT DESCRIPTION
The engine control system in 6VE1 uses high speed
CAN bus system. The individual CAN bus systems are
connected via two interfaces and can exchange
information and data. This allows control modules tha
t
are connected to different CAN bus systems to
communicate. Engine control modules (ECM) in the
vehicle that require continuous, rapid communication
are connected to the high speed CAN bus. The engine
is continuously notified of the current engine load
status. Since the ECM has to react immediately to load
status changes, rapid communication is required
between the ECM and the automatic transmission
control module. The high speed CAN bus in the 6VE1 is
designed as a two-wire CAN bus (twisted pair). The
wires are shielded and twisted. The engine rate is 500
K
band.
DIAGNOSTIC AIDS
Inspect the wiring for poor electrical connection at the
ECM. Look for possible bent, backed out, deformed
or damaged terminals. Check for weak terminal
tension as well. Also check for a chafed wire tha
t
could short to bare metal or other wiring. Inspect for a
broken wire inside the insulation.
When diagnosing for a possible intermittent short o
r
open condition, move the wiring harness while
observing test equipment for a change.
Inspect the wiring for EMI (Erectro-Magnetic
Interference). Check that all wires are properly routed
away from coil, and generator. Also check fo
r
improperly installed electrical options. When this test
is performed, turn “OFF" on electronic auto parts
switches to improperly for a noise preventing.
Page 2371 of 4264
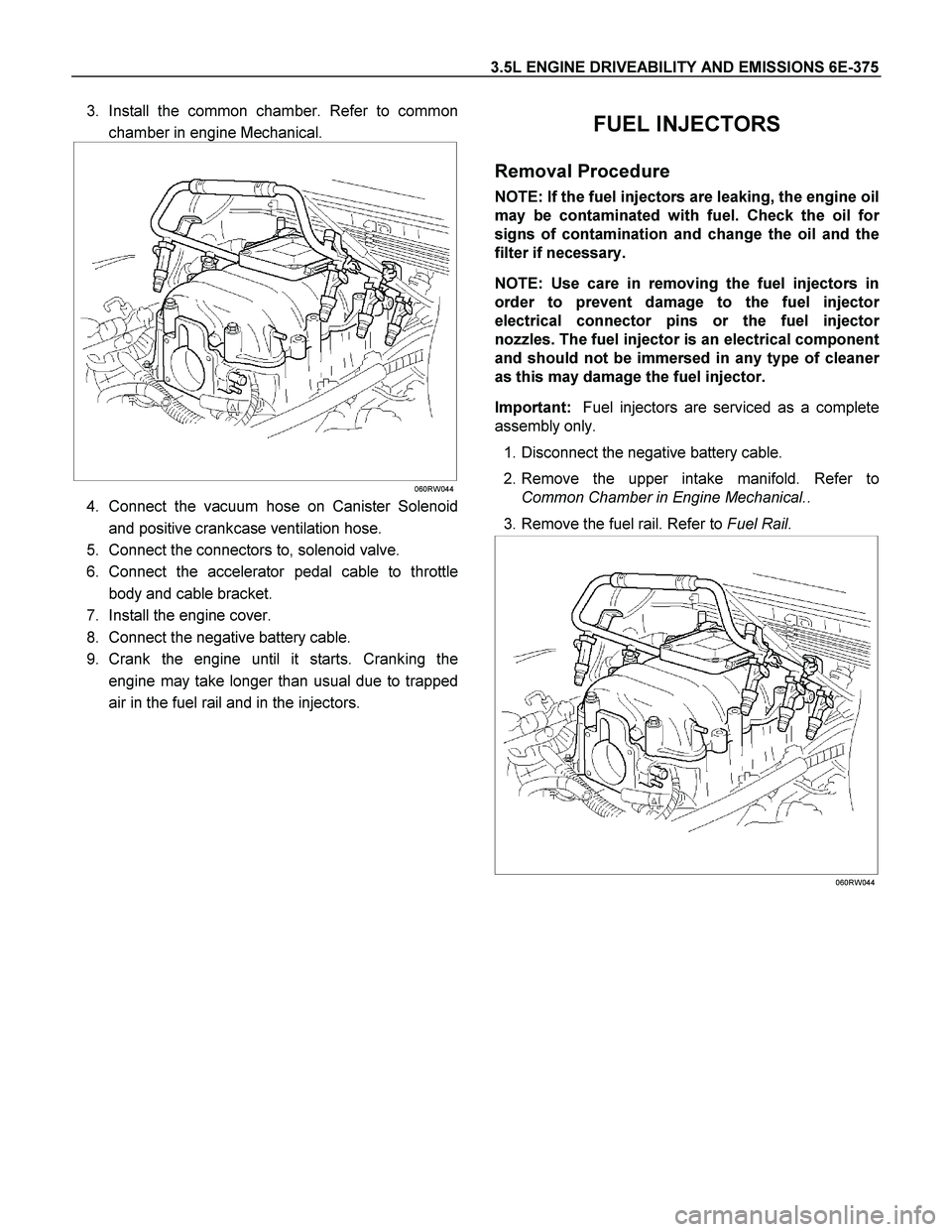
3.5L ENGINE DRIVEABILITY AND EMISSIONS 6E-375
3. Install the common chamber. Refer to common
chamber in engine Mechanical.
060RW044
4. Connect the vacuum hose on Canister Solenoid
and positive crankcase ventilation hose.
5. Connect the connectors to, solenoid valve.
6. Connect the accelerator pedal cable to throttle
body and cable bracket.
7. Install the engine cover.
8. Connect the negative battery cable.
9. Crank the engine until it starts. Cranking the
engine may take longer than usual due to trapped
air in the fuel rail and in the injectors.
FUEL INJECTORS
Removal Procedure
NOTE: If the fuel injectors are leaking, the engine oil
may be contaminated with fuel. Check the oil fo
r
signs of contamination and change the oil and the
filter if necessary.
NOTE: Use care in removing the fuel injectors in
order to prevent damage to the fuel injecto
r
electrical connector pins or the fuel injector
nozzles. The fuel injector is an electrical component
and should not be immersed in any type of cleane
r
as this may damage the fuel injector.
Important: Fuel injectors are serviced as a complete
assembly only.
1. Disconnect the negative battery cable.
2. Remove the upper intake manifold. Refer to
Common Chamber in Engine Mechanical..
3. Remove the fuel rail. Refer to Fuel Rail.
060RW044
Page 2414 of 4264
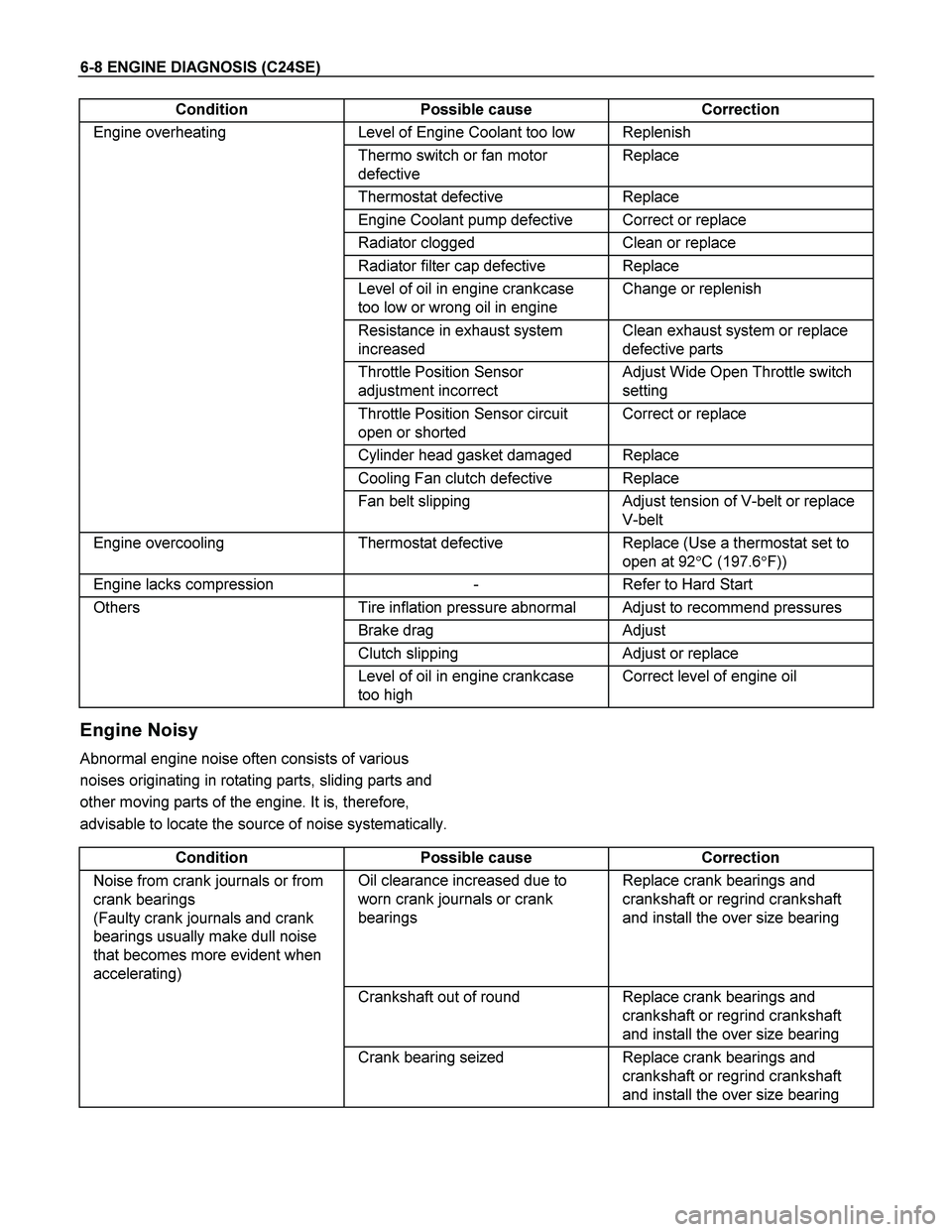
6-8 ENGINE DIAGNOSIS (C24SE)
Condition Possible cause Correction
Engine overheating Level of Engine Coolant too low Replenish
Thermo switch or fan motor
defective Replace
Thermostat defective Replace
Engine Coolant pump defective Correct or replace
Radiator clogged Clean or replace
Radiator filter cap defective Replace
Level of oil in engine crankcase
too low or wrong oil in engine Change or replenish
Resistance in exhaust system
increased Clean exhaust system or replace
defective parts
Throttle Position Sensor
adjustment incorrect Adjust Wide Open Throttle switch
setting
Throttle Position Sensor circuit
open or shorted Correct or replace
Cylinder head gasket damaged Replace
Cooling Fan clutch defective Replace
Fan belt slipping Adjust tension of V-belt or replace
V-belt
Engine overcooling Thermostat defective Replace (Use a thermostat set to
open at 92C (197.6F))
Engine lacks compression - Refer to Hard Start
Others Tire inflation pressure abnormal Adjust to recommend pressures
Brake drag Adjust
Clutch slipping Adjust or replace
Level of oil in engine crankcase
too high Correct level of engine oil
Engine Noisy
Abnormal engine noise often consists of various
noises originating in rotating parts, sliding parts and
other moving parts of the engine. It is, therefore,
advisable to locate the source of noise systematically.
Condition Possible cause Correction
Noise from crank journals or from
crank bearings
(Faulty crank journals and crank
bearings usually make dull noise
that becomes more evident when
accelerating) Oil clearance increased due to
worn crank journals or crank
bearings Replace crank bearings and
crankshaft or regrind crankshaft
and install the over size bearing
Crankshaft out of round Replace crank bearings and
crankshaft or regrind crankshaft
and install the over size bearing
Crank bearing seized Replace crank bearings and
crankshaft or regrind crankshaft
and install the over size bearing
Page 2419 of 4264
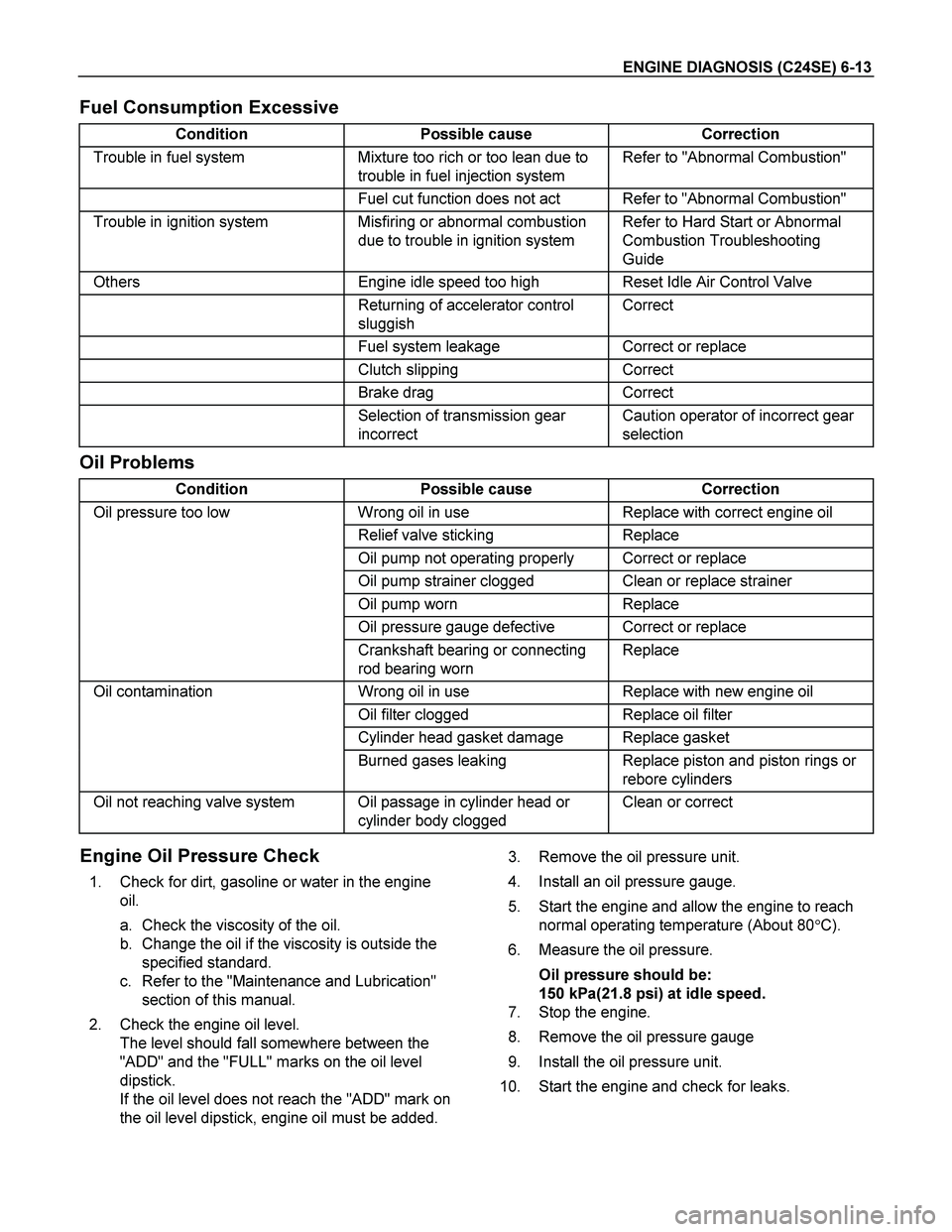
ENGINE DIAGNOSIS (C24SE) 6-13
Fuel Consumption Excessive
Condition Possible cause Correction
Trouble in fuel system Mixture too rich or too lean due to
trouble in fuel injection system Refer to "Abnormal Combustion"
Fuel cut function does not act Refer to "Abnormal Combustion"
Trouble in ignition system Misfiring or abnormal combustion
due to trouble in ignition system Refer to Hard Start or Abnormal
Combustion Troubleshooting
Guide
Others Engine idle speed too high Reset Idle Air Control Valve
Returning of accelerator control
sluggish Correct
Fuel system leakage Correct or replace
Clutch slipping Correct
Brake drag Correct
Selection of transmission gear
incorrect Caution operator of incorrect gear
selection
Oil Problems
Condition Possible cause Correction
Oil pressure too low Wrong oil in use Replace with correct engine oil
Relief valve sticking Replace
Oil pump not operating properly Correct or replace
Oil pump strainer clogged Clean or replace strainer
Oil pump worn Replace
Oil pressure gauge defective Correct or replace
Crankshaft bearing or connecting
rod bearing worn Replace
Oil contamination Wrong oil in use Replace with new engine oil
Oil filter clogged Replace oil filter
Cylinder head gasket damage Replace gasket
Burned gases leaking Replace piston and piston rings or
rebore cylinders
Oil not reaching valve system Oil passage in cylinder head or
cylinder body clogged Clean or correct
Engine Oil Pressure Check
1. Check for dirt, gasoline or water in the engine
oil.
a. Check the viscosity of the oil.
b. Change the oil if the viscosity is outside the
specified standard.
c. Refer to the "Maintenance and Lubrication"
section of this manual.
2. Check the engine oil level.
The level should fall somewhere between the
"ADD" and the "FULL" marks on the oil level
dipstick.
If the oil level does not reach the "ADD" mark on
the oil level dipstick, engine oil must be added. 3. Remove the oil pressure unit.
4. Install an oil pressure gauge.
5. Start the engine and allow the engine to reach
normal operating temperature (About 80C).
6. Measure the oil pressure.
Oil pressure should be:
150 kPa(21.8 psi) at idle speed.
7. Stop the engine.
8. Remove the oil pressure gauge
9. Install the oil pressure unit.
10. Start the engine and check for leaks.