oil level ISUZU TF SERIES 2004 Service Manual
[x] Cancel search | Manufacturer: ISUZU, Model Year: 2004, Model line: TF SERIES, Model: ISUZU TF SERIES 2004Pages: 4264, PDF Size: 72.63 MB
Page 2440 of 4264
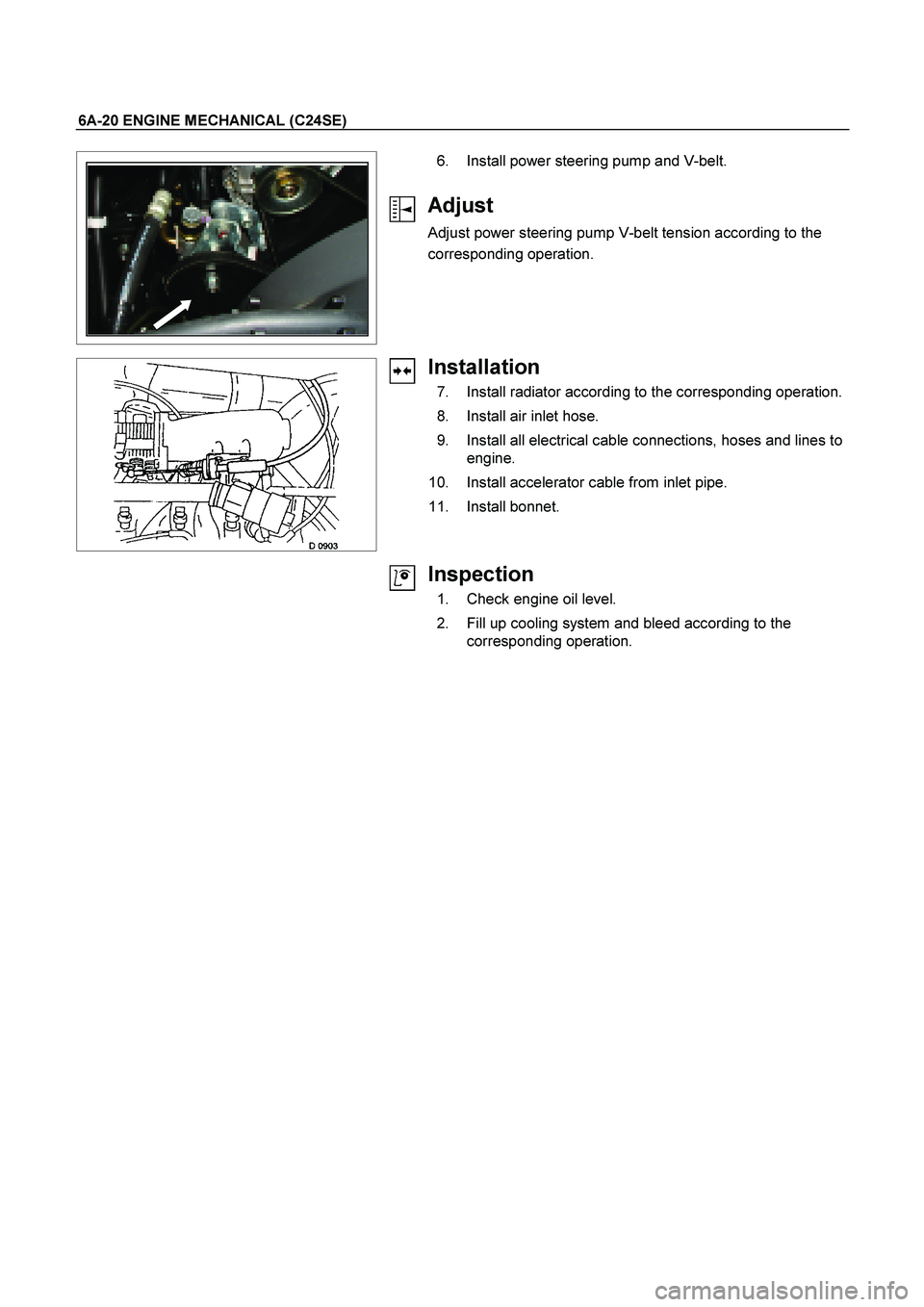
6A-20 ENGINE MECHANICAL (C24SE)
6. Install power steering pump and V-belt.
Adjust
Adjust power steering pump V-belt tension according to the
corresponding operation.
Installation
7. Install radiator according to the corresponding operation.
8. Install air inlet hose.
9. Install all electrical cable connections, hoses and lines to
engine.
10. Install accelerator cable from inlet pipe.
11. Install bonnet.
Inspection
1. Check engine oil level.
2. Fill up cooling system and bleed according to the
corresponding operation.
Page 2490 of 4264
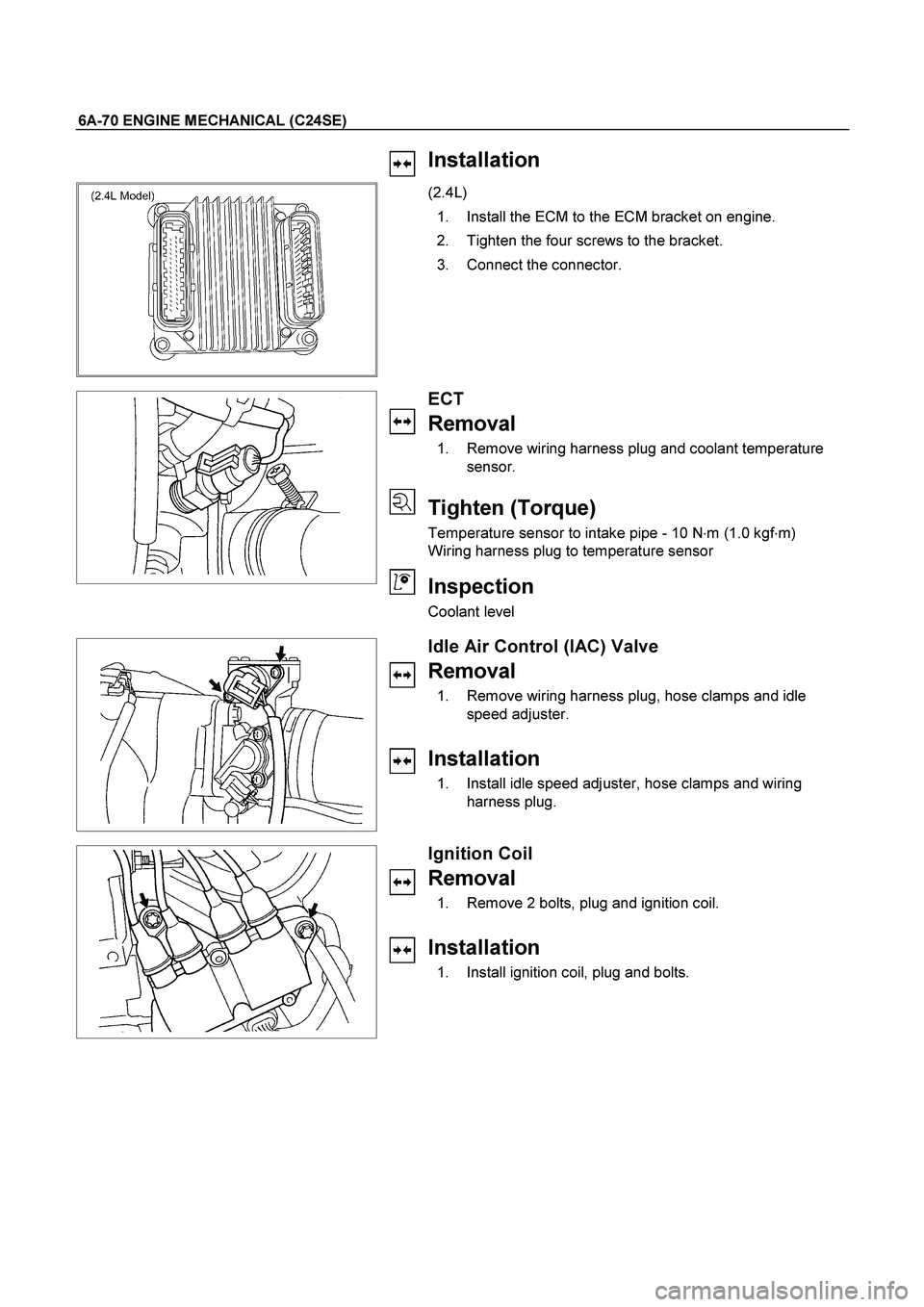
6A-70 ENGINE MECHANICAL (C24SE)
Installation
(2.4L)
1. Install the ECM to the ECM bracket on engine.
2. Tighten the four screws to the bracket.
3. Connect the connector.
ECT
Removal
1. Remove wiring harness plug and coolant temperature
sensor.
Tighten (Torque)
Temperature sensor to intake pipe - 10 N
m (1.0 kgf
m)
Wiring harness plug to temperature sensor
Inspection
Coolant level
Idle Air Control (IAC) Valve
Removal
1. Remove wiring harness plug, hose clamps and idle
speed adjuster.
Installation
1. Install idle speed adjuster, hose clamps and wiring
harness plug.
Ignition Coil
Removal
1. Remove 2 bolts, plug and ignition coil.
Installation
1. Install ignition coil, plug and bolts.
Page 2515 of 4264
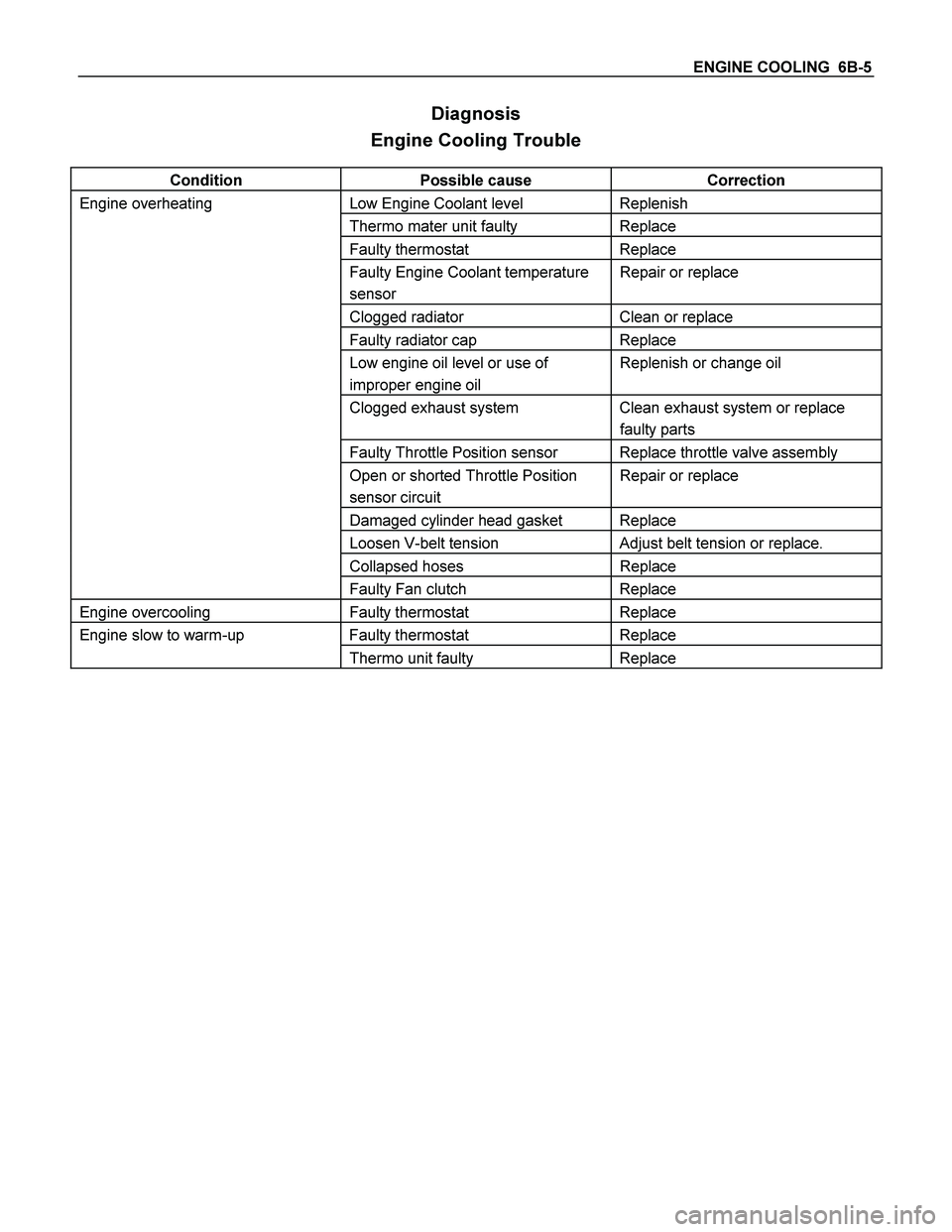
ENGINE COOLING 6B-5
Diagnosis
Engine Cooling Trouble
Condition Possible cause Correction
Engine overheating Low Engine Coolant level Replenish
Thermo mater unit faulty Replace
Faulty thermostat Replace
Faulty Engine Coolant temperature
sensor Repair or replace
Clogged radiator Clean or replace
Faulty radiator cap Replace
Low engine oil level or use of
improper engine oil Replenish or change oil
Clogged exhaust system Clean exhaust system or replace
faulty parts
Faulty Throttle Position sensor Replace throttle valve assembly
Open or shorted Throttle Position
sensor circuit Repair or replace
Damaged cylinder head gasket Replace
Loosen V-belt tension Adjust belt tension or replace.
Collapsed hoses Replace
Faulty Fan clutch Replace
Engine overcooling Faulty thermostat Replace
Engine slow to warm-up Faulty thermostat Replace
Thermo unit faulty Replace
Page 2516 of 4264
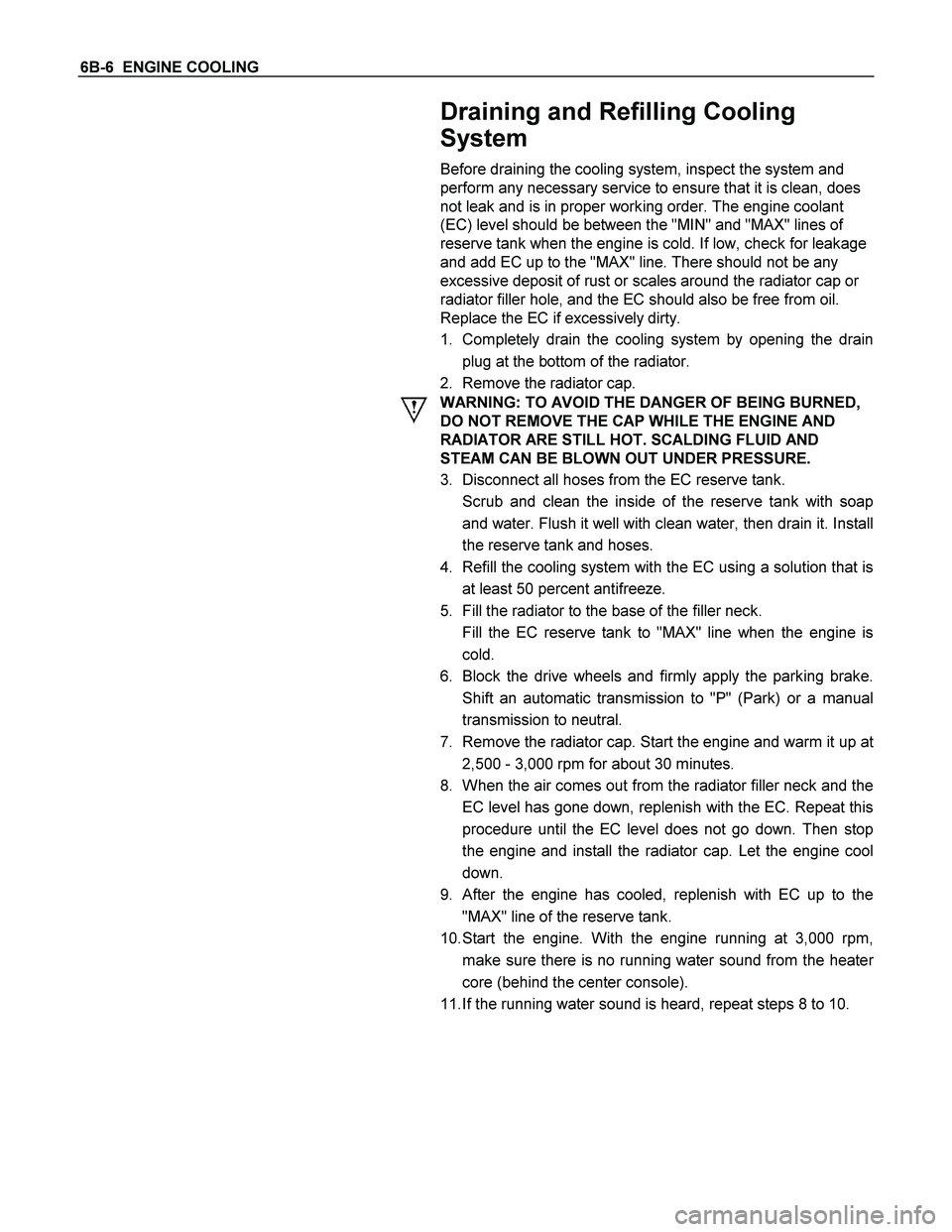
6B-6 ENGINE COOLING
Draining and Refilling Cooling
System
Before draining the cooling system, inspect the system and
perform any necessary service to ensure that it is clean, does
not leak and is in proper working order. The engine coolant
(EC) level should be between the "MIN" and "MAX" lines of
reserve tank when the engine is cold. If low, check for leakage
and add EC up to the "MAX" line. There should not be any
excessive deposit of rust or scales around the radiator cap or
radiator filler hole, and the EC should also be free from oil.
Replace the EC if excessively dirty.
1. Completely drain the cooling system by opening the drain
plug at the bottom of the radiator.
2. Remove the radiator cap.
WARNING: TO AVOID THE DANGER OF BEING BURNED,
DO NOT REMOVE THE CAP WHILE THE ENGINE AND
RADIATOR ARE STILL HOT. SCALDING FLUID AND
STEAM CAN BE BLOWN OUT UNDER PRESSURE.
3. Disconnect all hoses from the EC reserve tank.
Scrub and clean the inside of the reserve tank with soap
and water. Flush it well with clean water, then drain it. Install
the reserve tank and hoses.
4. Refill the cooling system with the EC using a solution that is
at least 50 percent antifreeze.
5. Fill the radiator to the base of the filler neck.
Fill the EC reserve tank to "MAX" line when the engine is
cold.
6. Block the drive wheels and firmly apply the parking brake.
Shift an automatic transmission to "P" (Park) or a manual
transmission to neutral.
7. Remove the radiator cap. Start the engine and warm it up a
t
2,500 - 3,000 rpm for about 30 minutes.
8. When the air comes out from the radiator filler neck and the
EC level has gone down, replenish with the EC. Repeat this
procedure until the EC level does not go down. Then stop
the engine and install the radiator cap. Let the engine cool
down.
9. After the engine has cooled, replenish with EC up to the
"MAX" line of the reserve tank.
10. Start the engine. With the engine running at 3,000 rpm,
make sure there is no running water sound from the heate
r
core (behind the center console).
11. If the running water sound is heard, repeat steps 8 to 10.
Page 2974 of 4264
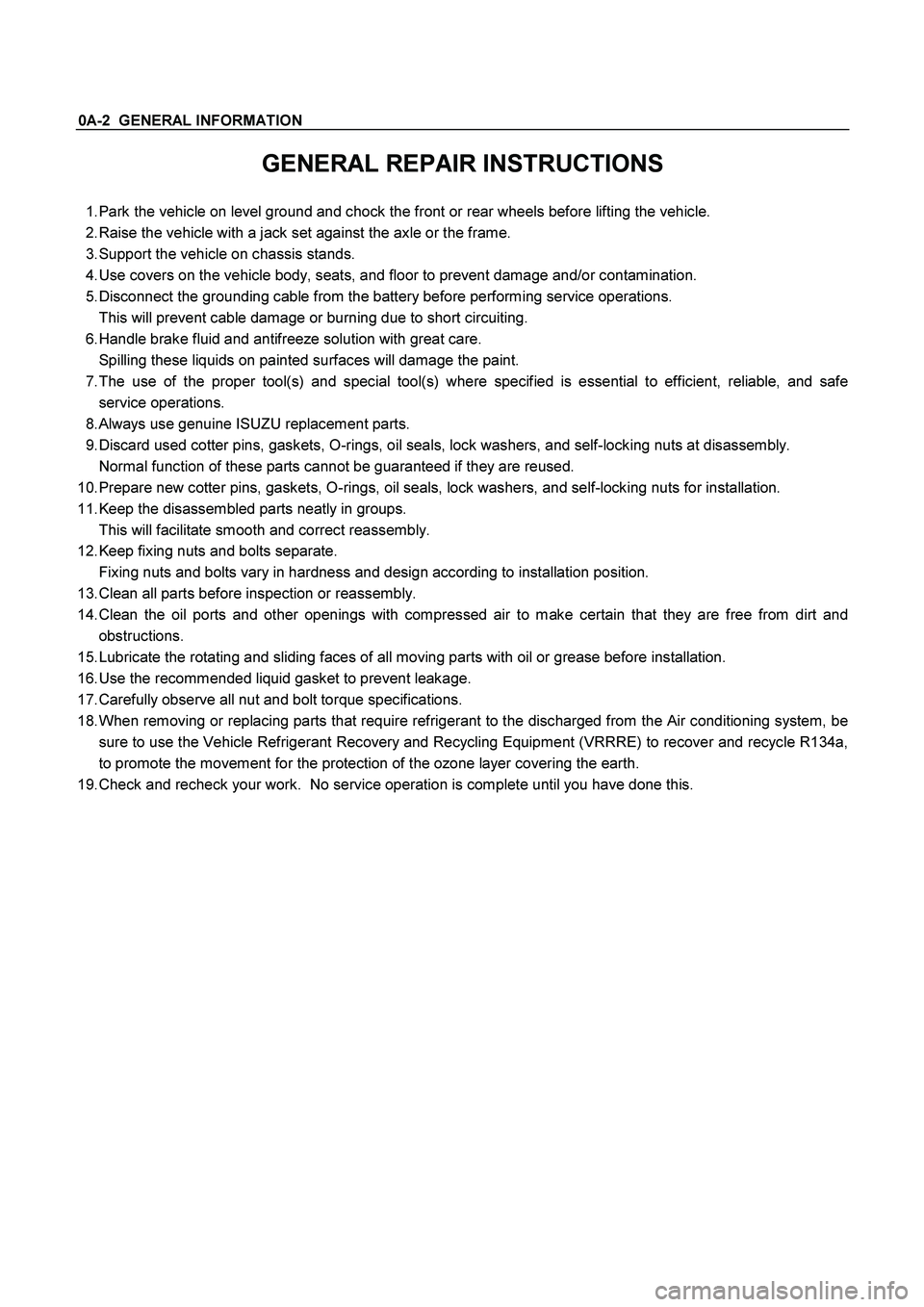
0A-2 GENERAL INFORMATION
GENERAL REPAIR INSTRUCTIONS
1. Park the vehicle on level ground and chock the front or rear wheels before lifting the vehicle.
2. Raise the vehicle with a jack set against the axle or the frame.
3. Support the vehicle on chassis stands.
4. Use covers on the vehicle body, seats, and floor to prevent damage and/or contamination.
5. Disconnect the grounding cable from the battery before performing service operations.
This will prevent cable damage or burning due to short circuiting.
6. Handle brake fluid and antifreeze solution with great care.
Spilling these liquids on painted surfaces will damage the paint.
7. The use of the proper tool(s) and special tool(s) where specified is essential to efficient, reliable, and safe
service operations.
8. Always use genuine ISUZU replacement parts.
9. Discard used cotter pins, gaskets, O-rings, oil seals, lock washers, and self-locking nuts at disassembly.
Normal function of these parts cannot be guaranteed if they are reused.
10. Prepare new cotter pins, gaskets, O-rings, oil seals, lock washers, and self-locking nuts for installation.
11. Keep the disassembled parts neatly in groups.
This will facilitate smooth and correct reassembly.
12. Keep fixing nuts and bolts separate.
Fixing nuts and bolts vary in hardness and design according to installation position.
13. Clean all parts before inspection or reassembly.
14. Clean the oil ports and other openings with compressed air to make certain that they are free from dirt and
obstructions.
15. Lubricate the rotating and sliding faces of all moving parts with oil or grease before installation.
16. Use the recommended liquid gasket to prevent leakage.
17. Carefully observe all nut and bolt torque specifications.
18. When removing or replacing parts that require refrigerant to the discharged from the Air conditioning system, be
sure to use the Vehicle Refrigerant Recovery and Recycling Equipment (VRRRE) to recover and recycle R134a,
to promote the movement for the protection of the ozone layer covering the earth.
19. Check and recheck your work. No service operation is complete until you have done this.
Page 2990 of 4264
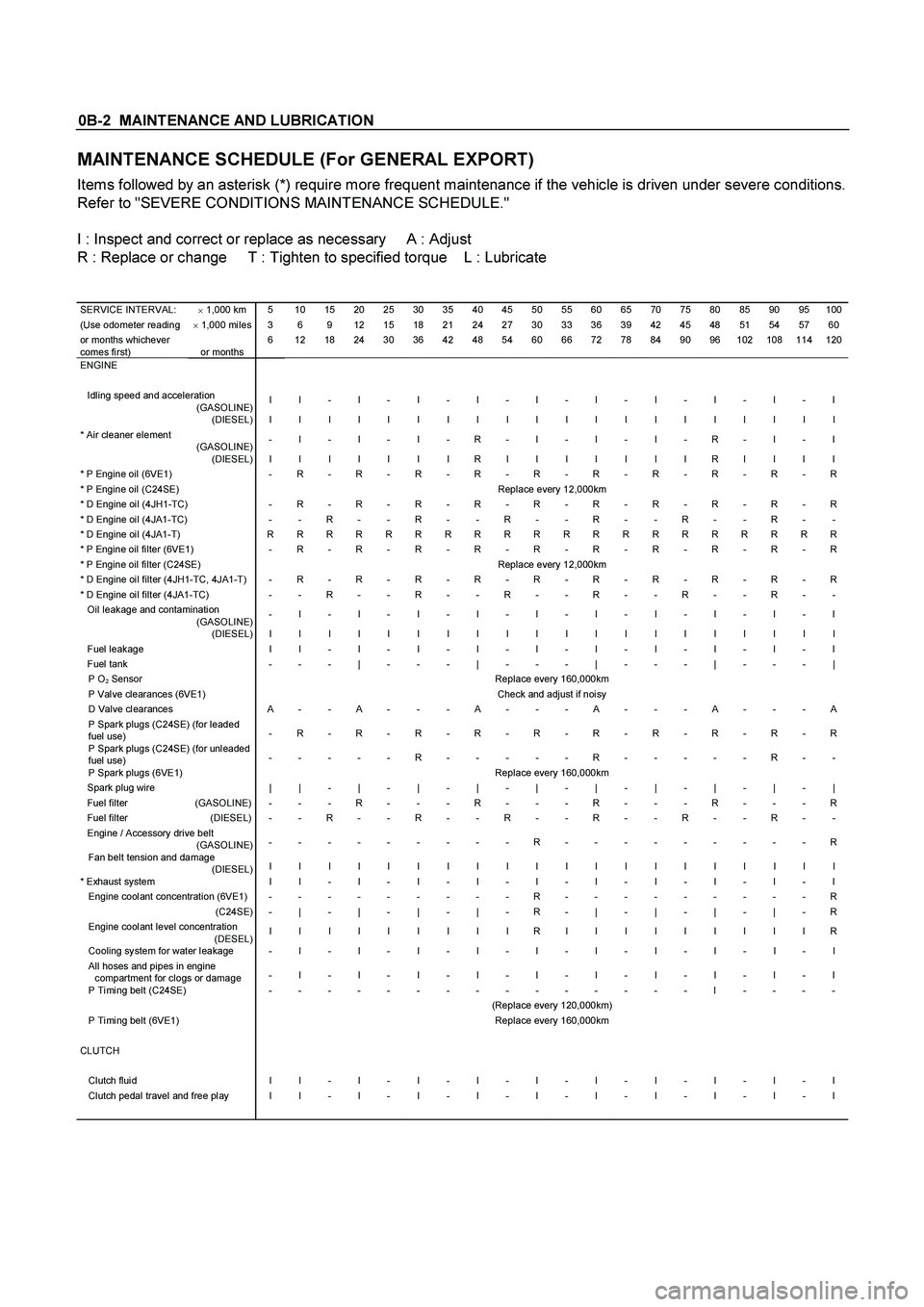
0B-2 MAINTENANCE AND LUBRICATION
MAINTENANCE SCHEDULE (For GENERAL EXPORT)
Items followed by an asterisk (*) require more frequent maintenance if the vehicle is driven under severe conditions.
Refer to "SEVERE CONDITIONS MAINTENANCE SCHEDULE."
I : Inspect and correct or replace as necessary A : Adjust
R : Replace or change T : Tighten to specified torque L : Lubricate
SERVICE INTERVAL:
1,000 km 5 10 15 20 25 30 35 40 45 50 55 60 65 70 75 80 85 90 95 100(Use odometer reading 1,000 miles 3 6 9 12 15 18 21 24 27 30 33 36 39 42 45 48 51 54 57 60or months whichever
comes fi rst)
or months 6 12 18 24 30 36 42 48 54 60 66 72 78 84 90 96 102 108 114 120
ENGINE Idling speed and acceleration
(GASOLINE) I I - I - I - I - I - I - I - I - I - I
(DIESEL) I I I I I I I I I I I I I I I I I I I I * Air cleaner element
(GASOLINE) - I - I - I - R - I - I - I - R - I - I
(DIESEL) I I I I I I I R I I I I I I I R I I I I * P Engine oil (6VE1) - R - R - R - R - R - R - R - R - R - R * P Engine oil (C24SE) Replace every 12,000km * D Engine oil (4JH1-TC) - R - R - R - R - R - R - R - R - R - R * D Engine oil (4JA1-TC) - - R - - R - - R - - R - - R - - R - - * D Engine oil (4JA1-T) RR R R RR RRRRRRRR R R R RRR * P Engine oil filter (6VE1) - R - R - R - R - R - R - R - R - R - R * P Engine oil filter (C24SE) Replace every 12,000km * D Engine oil filter (4JH1-TC, 4JA1-T) - R - R - R - R - R - R - R - R - R - R * D Engine oil filter (4JA1-TC) - - R - - R - - R - - R - - R - - R - - Oil leakage and contamination
(GASOLINE) - I - I - I - I - I - I - I - I - I - I
(DIESEL) I I I I I I I I I I I I I I I I I I I I Fuel leakage I I - I - I - I - I - I - I - I - I - I Fuel tank - - - | - - - | - - - | - - - | - - - | P O2 Sensor Replace every 160,000km P Valve clearances (6VE1) Check and adjust if noisy D Valve clearances A - - A - - - A - - - A - - - A - - - A P Spark plugs (C24SE) (for leaded
fuel use) - R - R - R - R - R - R - R - R - R - R
P Spark plugs (C24SE) (for unleaded
fuel use) - - - - - R - - - - - R - - - - - R - -
P Spark plugs (6VE1) Replace every 160,000km Spark plug wire | | - | - | - | - | - | - | - | - | - | Fuel filter (GASOLINE) - - - R - - - R - - - R - - - R - - - R Fuel filter (DIESEL) - - R - - R - - R - - R - - R - - R - - Engi ne / Accessory dri ve belt
(GASOLINE) - - - - - - - - - R - - - - - - - - - R
Fan belt tension and damage
(DIESEL) I I I I I I I I I I I I I I I I I I I I
* Exhaust system I I - I - I - I - I - I - I - I - I - I Engine coolant concentration (6VE1) - - - - - - - - - R - - - - - - - - - R (C24SE) - | - | - | - | - R - | - | - | - | - R Engine coolant level concentration
(DESEL) I I I I I I I I I R I I I I I I I I I R
Cooli ng sy stem for water l eakage - I - I - I - I - I - I - I - I - I - I All hoses and pipes in engine
compartment for clogs or damage - I - I - I - I - I - I - I - I - I - I
P Timing belt (C24SE) - - - - - - - - - - - - - - - I - - - - (Replace every 120,000km) P Timing belt (6VE1) Replace every 160,000km CLUTCH Cl utch fl ui d I I - I - I - I - I - I - I - I - I - I Clutch pedal travel and free play I I - I - I - I - I - I - I - I - I - I
Page 3057 of 4264
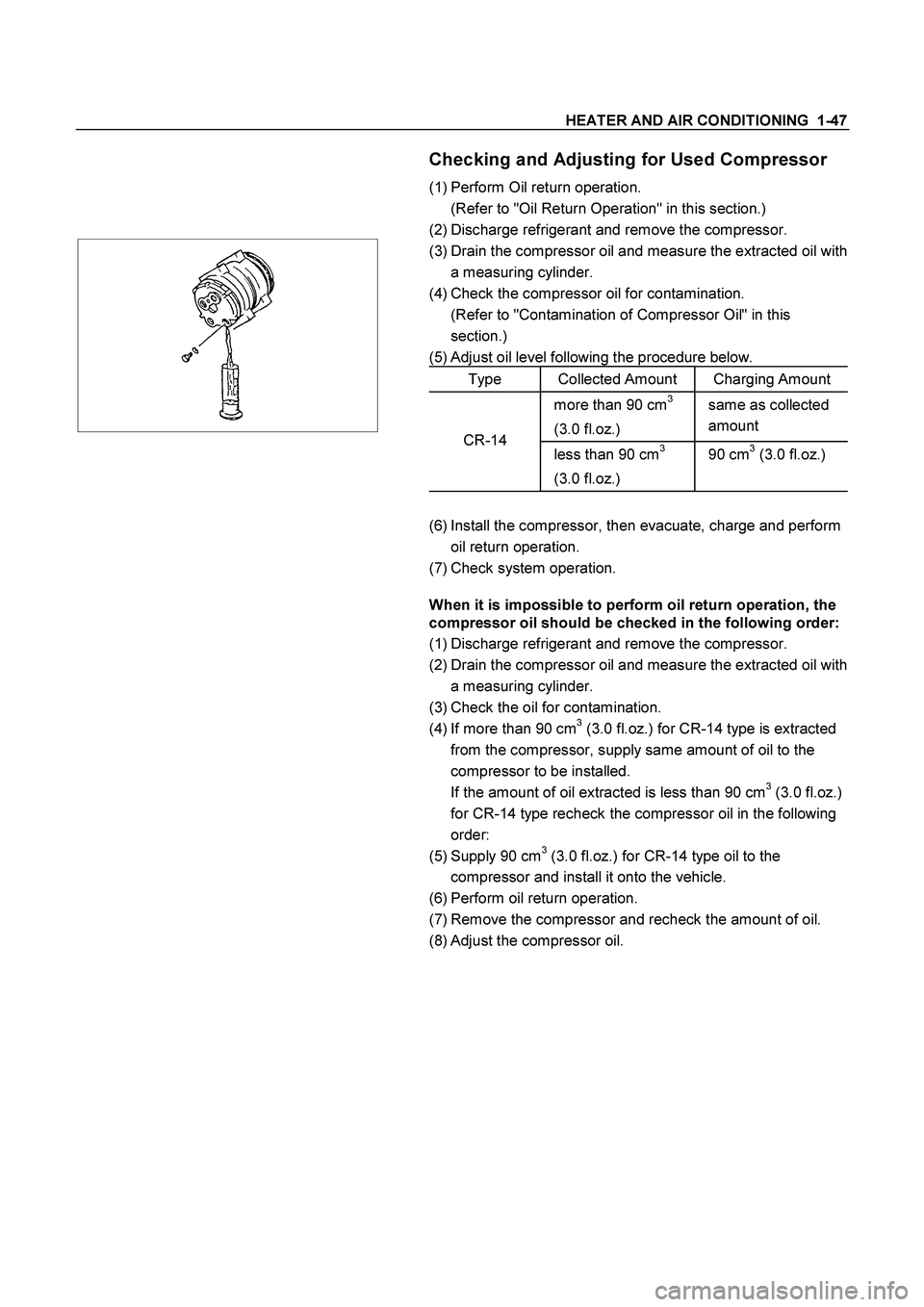
HEATER AND AIR CONDITIONING 1-47
Checking and Adjusting for Used Compressor
(1) Perform Oil return operation.
(Refer to "Oil Return Operation" in this section.)
(2) Discharge refrigerant and remove the compressor.
(3) Drain the compressor oil and measure the extracted oil with
a measuring cylinder.
(4) Check the compressor oil for contamination.
(Refer to "Contamination of Compressor Oil" in this
section.)
(5) Adjust oil level following the procedure below.
Type Collected Amount Charging Amount
more than 90 cm3
(3.0 fl.oz.) same as collected
amount
less than 90 cm3
(3.0 fl.oz.) 90 cm3 (3.0 fl.oz.) CR-14
(6) Install the compressor, then evacuate, charge and perform
oil return operation.
(7) Check system operation.
When it is impossible to perform oil return operation, the
compressor oil should be checked in the following order:
(1) Discharge refrigerant and remove the compressor.
(2) Drain the compressor oil and measure the extracted oil with
a measuring cylinder.
(3) Check the oil for contamination.
(4) If more than 90 cm
3 (3.0 fl.oz.) for CR-14 type is extracted
from the compressor, supply same amount of oil to the
compressor to be installed.
If the amount of oil extracted is less than 90 cm
3 (3.0 fl.oz.)
for CR-14 type recheck the compressor oil in the following
order:
(5) Supply 90 cm
3 (3.0 fl.oz.) for CR-14 type oil to the
compressor and install it onto the vehicle.
(6) Perform oil return operation.
(7) Remove the compressor and recheck the amount of oil.
(8) Adjust the compressor oil.
Page 3058 of 4264
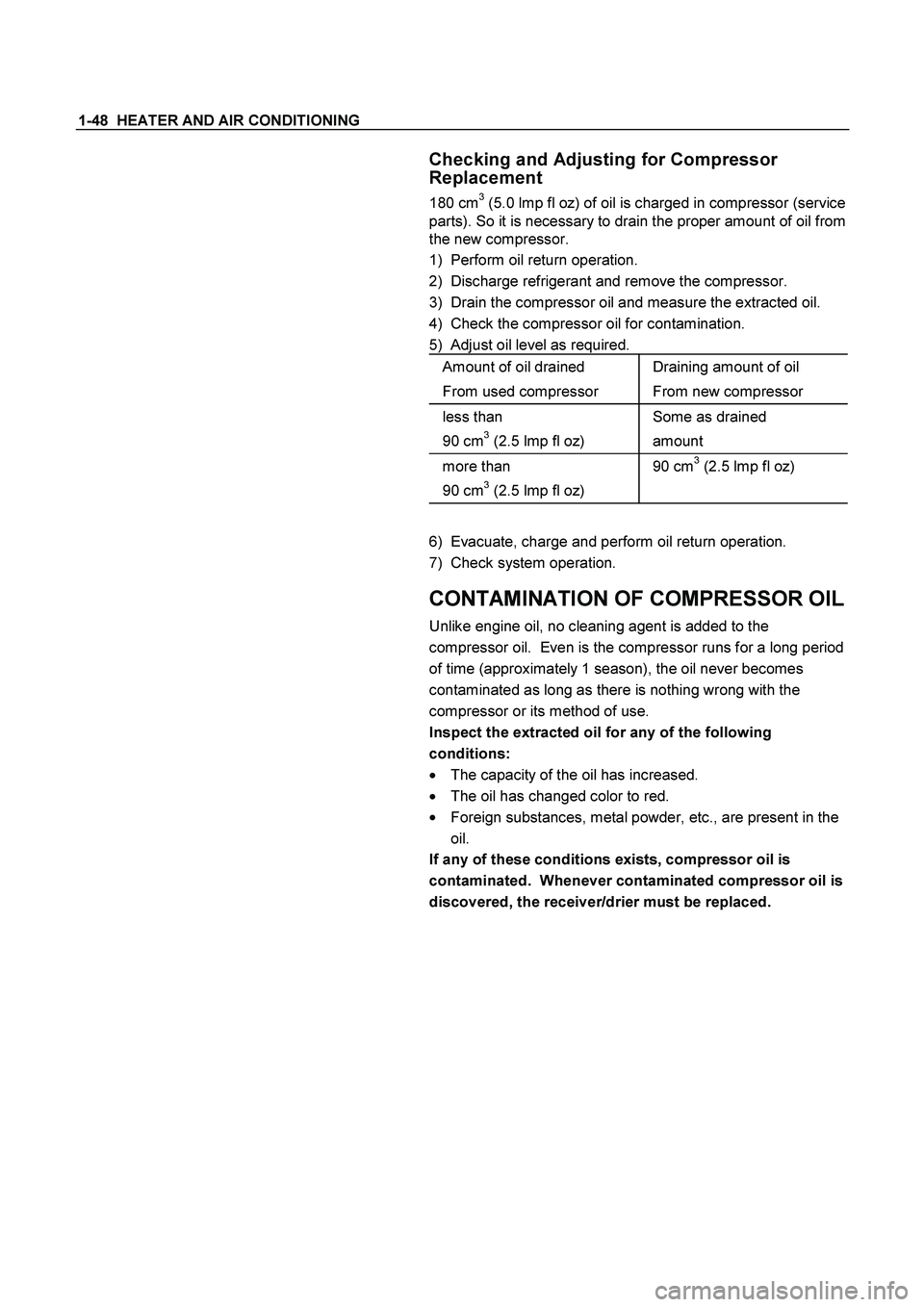
1-48 HEATER AND AIR CONDITIONING
Checking and Adjusting for Compressor
Replacement
180 cm3 (5.0 lmp fl oz) of oil is charged in compressor (service
parts). So it is necessary to drain the proper amount of oil from
the new compressor.
1) Perform oil return operation.
2) Discharge refrigerant and remove the compressor.
3) Drain the compressor oil and measure the extracted oil.
4) Check the compressor oil for contamination.
5) Adjust oil level as required.
Amount of oil drained
From used compressor Draining amount of oil
From new compressor
less than
90 cm
3 (2.5 lmp fl oz) Some as drained
amount
more than
90 cm
3 (2.5 lmp fl oz) 90 cm
3 (2.5 lmp fl oz)
6) Evacuate, charge and perform oil return operation.
7) Check system operation.
CONTAMINATION OF COMPRESSOR OIL
Unlike engine oil, no cleaning agent is added to the
compressor oil. Even is the compressor runs for a long period
of time (approximately 1 season), the oil never becomes
contaminated as long as there is nothing wrong with the
compressor or its method of use.
Inspect the extracted oil for any of the following
conditions:
The capacity of the oil has increased.
The oil has changed color to red.
Foreign substances, metal powder, etc., are present in the
oil.
If any of these conditions exists, compressor oil is
contaminated. Whenever contaminated compressor oil is
discovered, the receiver/drier must be replaced.
Page 3224 of 4264
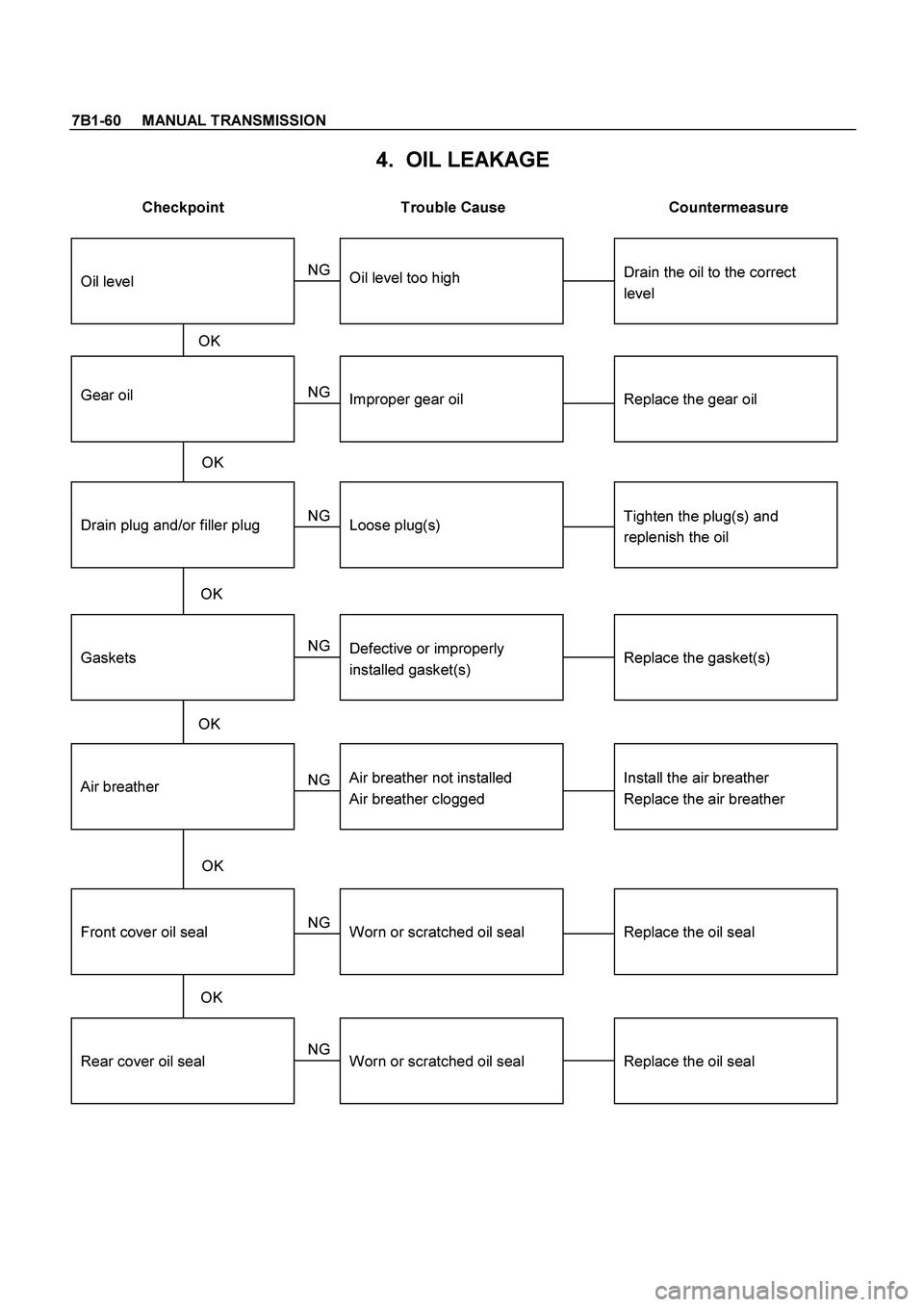
7B1-60 MANUAL TRANSMISSION
4. OIL LEAKAGE
Checkpoint Trouble Cause Countermeasure
Gear oilReplace the gear oilImproper gear oil
Drain plug and/or filler plugTighten the plug(s) and
replenish the oil
Drain the oil to the correct
level
Loose plug(s)
Oil level too high
OKNG NG NG
OK OKOil level
Rear cover oil seal
Air breather
Replace the oil seal
Install the air breather
Replace the air breather
Worn or scratched oil seal
Air breather not installed
Air breather clogged
Front cover oil sealReplace the oil seal
Replace the gasket(s)
Worn or scratched oil seal
Defective or improperly
installed gasket(s)
OK
NG NG NG NG
OK OKGaskets
Page 3281 of 4264
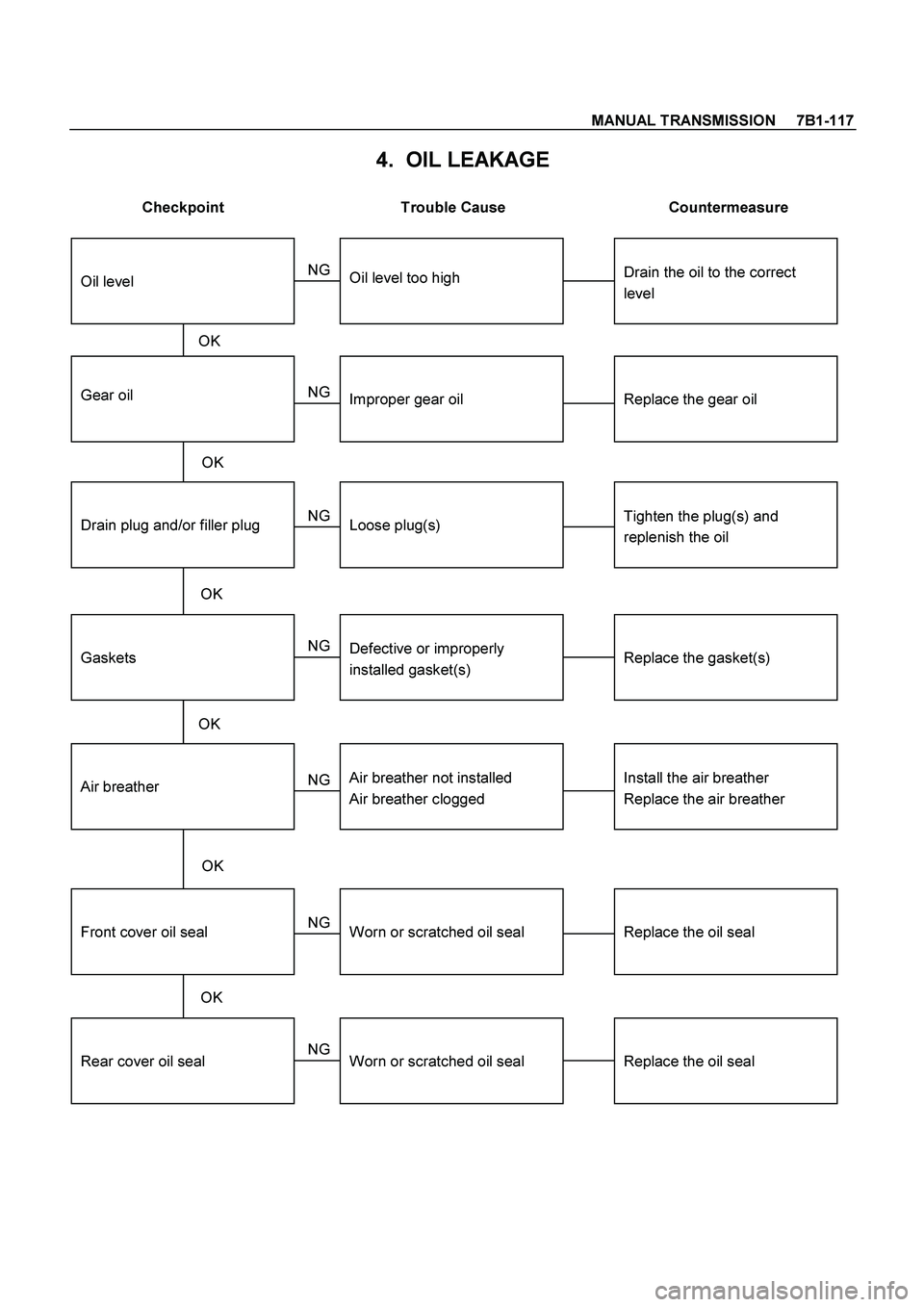
MANUAL TRANSMISSION 7B1-117
4. OIL LEAKAGE
Checkpoint Trouble Cause Countermeasure
Gear oilReplace the gear oilImproper gear oil
Drain plug and/or filler plugTighten the plug(s) and
replenish the oil
Drain the oil to the correct
level
Loose plug(s)
Oil level too high
OKNG NG NG
OK OKOil level
Rear cover oil seal
Air breather
Replace the oil seal
Install the air breather
Replace the air breather
Worn or scratched oil seal
Air breather not installed
Air breather clogged
Front cover oil sealReplace the oil seal
Replace the gasket(s)
Worn or scratched oil seal
Defective or improperly
installed gasket(s)
OK
NG NG NG NG
OK OKGaskets