check engine JAGUAR XF 2009 1.G AJ133 5.0L Engine Manual
[x] Cancel search | Manufacturer: JAGUAR, Model Year: 2009, Model line: XF, Model: JAGUAR XF 2009 1.GPages: 36, PDF Size: 0.38 MB
Page 9 of 36
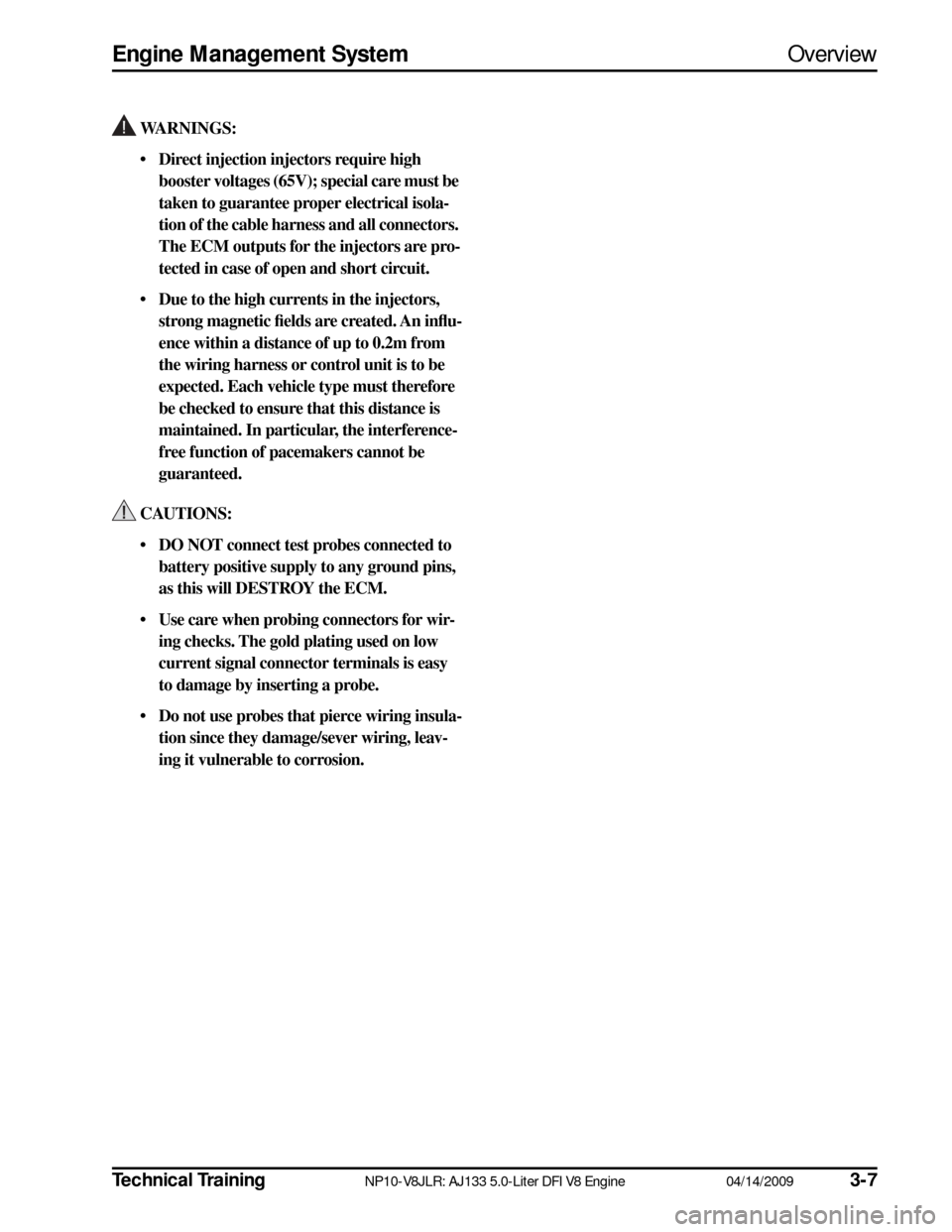
Technical Training
NP10-V8JLR: AJ133 5.0-Liter DFI V8 Engine 04/14/2009
3-7
Engine Management System
Overview
WARNINGS:
• Direct injection injectors require high booster voltages (65V); special care must be
taken to guarantee proper electrical isola-
tion of the cable harness and all connectors.
The ECM outputs for the injectors are pro-
tected in case of open and short circuit.
• Due to the high currents in the injectors, strong magnetic fields are created. An influ-
ence within a distance of up to 0.2m from
the wiring harness or control unit is to be
expected. Each vehicle type must therefore
be checked to ensure that this distance is
maintained. In particular, the interference-
free function of pacemakers cannot be
guaranteed.
CAUTIONS:
• DO NOT connect test probes connected to battery positive supply to any ground pins,
as this will DESTROY the ECM.
• Use care when probing connectors for wir- ing checks. The gold plating used on low
current signal connector terminals is easy
to damage by inserting a probe.
• Do not use probes that pierce wiring insula- tion since they damage/sever wiring, leav-
ing it vulnerable to corrosion.
Page 14 of 36
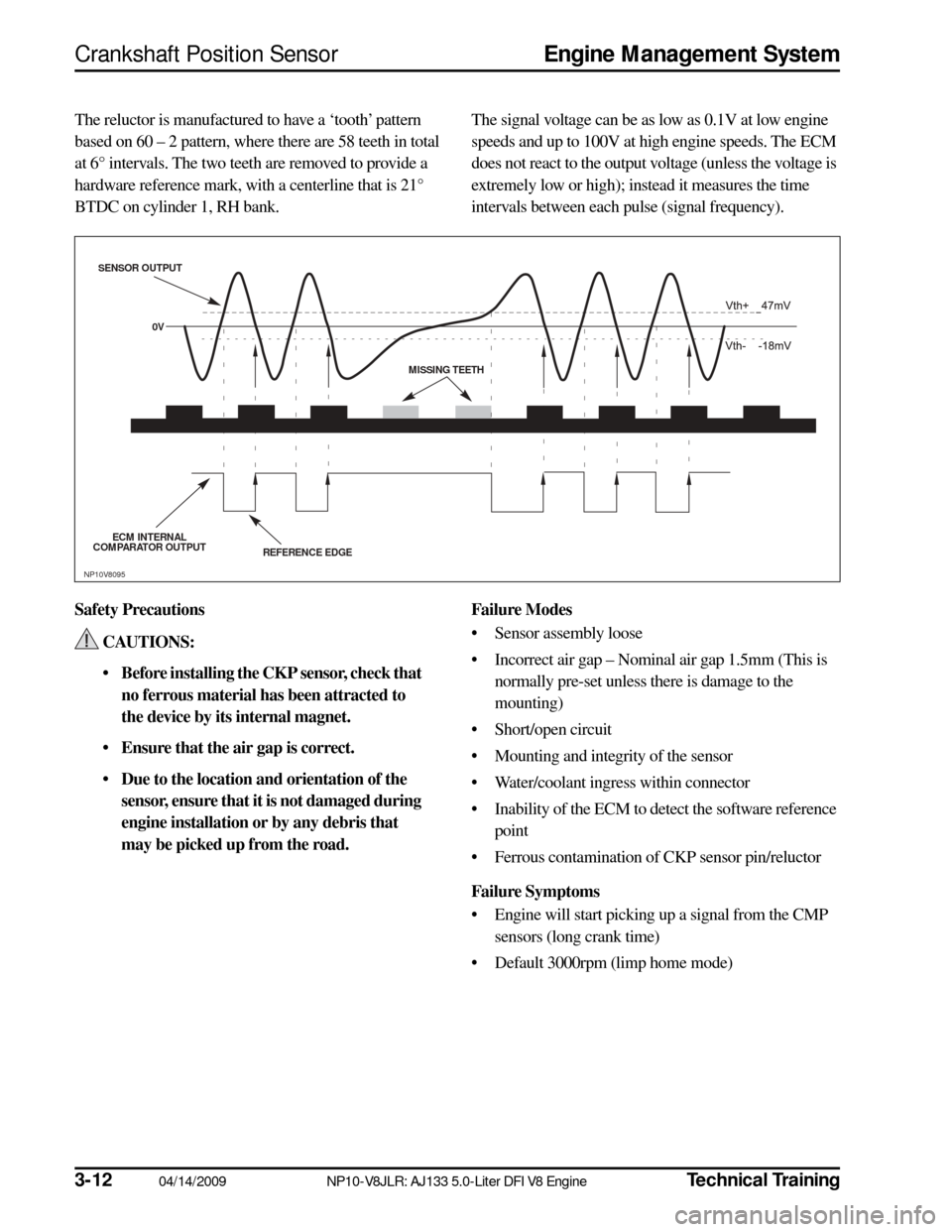
3-12
04/14/2009 NP10-V8JLR: AJ133 5.0-Liter DFI V8 Engine
Technical Training
Crankshaft Position Sensor
Engine Management System
The reluctor is manufactured to have a ‘tooth’ pattern
based on 60 – 2 pattern, where there are 58 teeth in total
at 6° intervals. The two teeth are removed to provide a
hardware reference mark, with a centerline that is 21°
BTDC on cylinder 1, RH bank. The signal voltage can be as low as 0.1V at low engine
speeds and up to 100V at high engine speeds. The ECM
does not react to the output voltage (unless the voltage is
extremely low or high); instead it measures the time
intervals between each pulse (signal frequency).
Safety Precautions CAUTIONS:
• Before installing the CKP sensor, check that no ferrous material has been attracted to
the device by its internal magnet.
• Ensure that the air gap is correct.
• Due to the location and orientation of the sensor, ensure that it is not damaged during
engine installation or by any debris that
may be picked up from the road. Failure Modes
• Sensor assembly loose
• Incorrect air gap – Nominal air gap 1.5mm (This is normally pre-set unless there is damage to the
mounting)
• Short/open circuit
• Mounting and integrity of the sensor
• Water/coolant ingress within connector
• Inability of the ECM to detect the software reference point
• Ferrous contamination of CKP sensor pin/reluctor
Failure Symptoms
• Engine will start picking up a signal from the CMP sensors (long crank time)
• Default 3000rpm (limp home mode)
REFERENCE EDGE
S
ENS OR OUTPUT
ECM INTERNAL
COMPARATOR OUTPUT 0V
MISSING TEETH
NP10V8095
Page 17 of 36
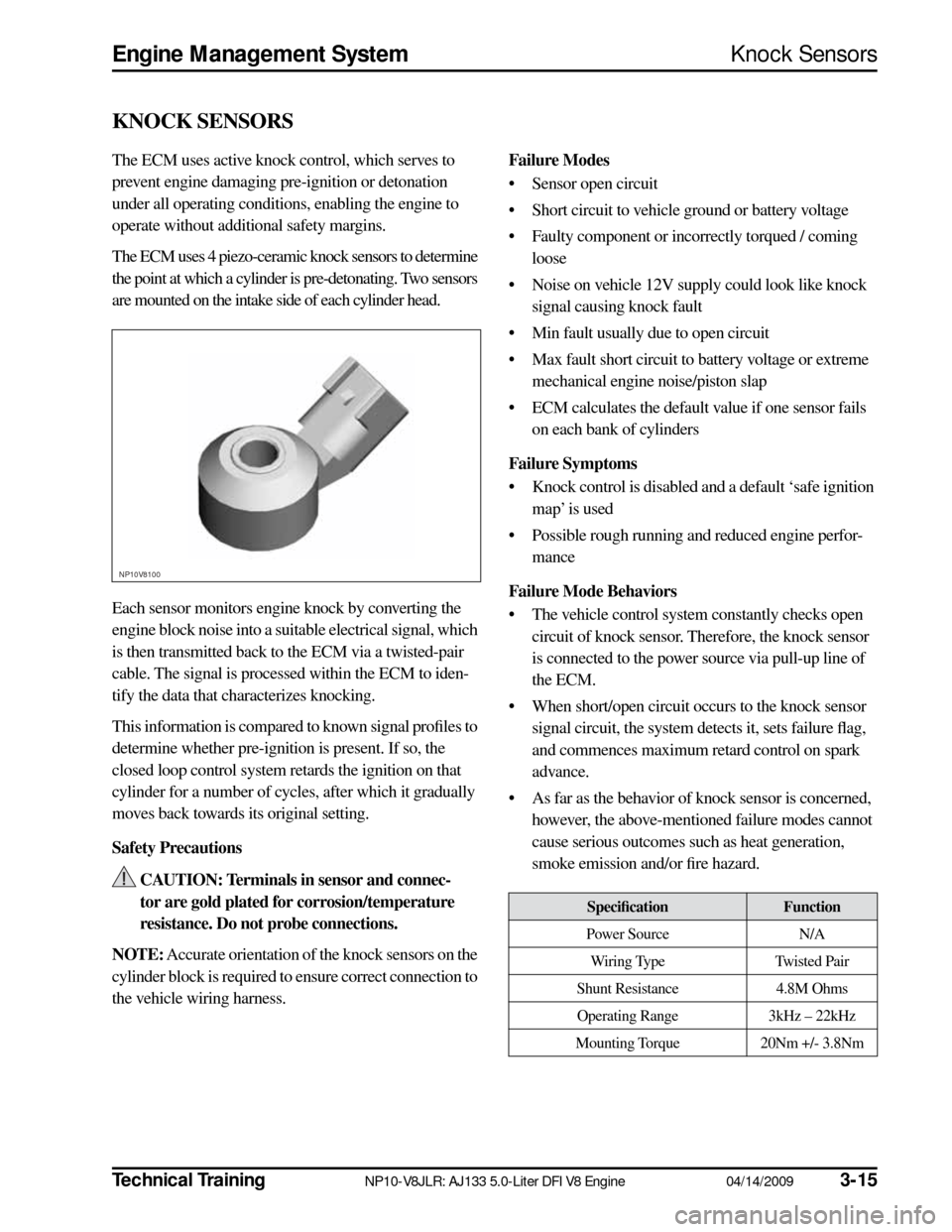
Technical Training
NP10-V8JLR: AJ133 5.0-Liter DFI V8 Engine 04/14/2009
3-15
Engine Management System
Knock Sensors
KNOCK SENSORS
The ECM uses active knock control, which serves to
prevent engine damaging pre-ignition or detonation
under all operating conditions, enabling the engine to
operate without additional safety margins.
The ECM uses 4 piezo-ceramic knock sensors to determine
the point at which a cylinder is pre-detonating. Two sensors
are mounted on the intake side of each cylinder head.
Each sensor monitors engine knock by converting the
engine block noise into a suitable electrical signal, which
is then transmitted back to the ECM via a twisted-pair
cable. The signal is processed within the ECM to iden-
tify the data that characterizes knocking.
This information is compared to known signal profiles to
determine whether pre-ignition is present. If so, the
closed loop control system retards the ignition on that
cylinder for a number of cycles, after which it gradually
moves back towards its original setting.
Safety Precautions CAUTION: Terminals in sensor and connec-
tor are gold plated for corrosion/temperature
resistance. Do not probe connections.
NOTE:
Accurate orientation of the knock sensors on the
cylinder block is required to ensure correct connection to
the vehicle wiring harness.
Failure Modes
• Sensor open circuit
• Short circuit to vehicle ground or battery voltage
• Faulty component or incorrectly torqued / coming loose
• Noise on vehicle 12V supply could look like knock signal causing knock fault
• Min fault usually due to open circuit
• Max fault short circuit to battery voltage or extreme mechanical engine noise/piston slap
• ECM calculates the default value if one sensor fails on each bank of cylinders
Failure Symptoms
• Knock control is disabled and a default ‘safe ignition map’ is used
• Possible rough running and reduced engine perfor- mance
Failure Mode Behaviors
• The vehicle control system constantly checks open circuit of knock sensor. Therefore, the knock sensor
is connected to the power source via pull-up line of
the ECM.
• When short/open circuit occurs to the knock sensor signal circuit, the system detects it, sets failure flag,
and commences maximum retard control on spark
advance.
• As far as the behavior of knock sensor is concerned, however, the above-mentioned failure modes cannot
cause serious outcomes such as heat generation,
smoke emission and/or fire hazard.
NP10V8100
Specification
Function
Power Source N/A
Wiring Type Twisted Pair
Shunt Resistance 4.8M Ohms
Operating Range 3kHz – 22kHz
Mounting Torque 20Nm +/- 3.8Nm
Page 23 of 36
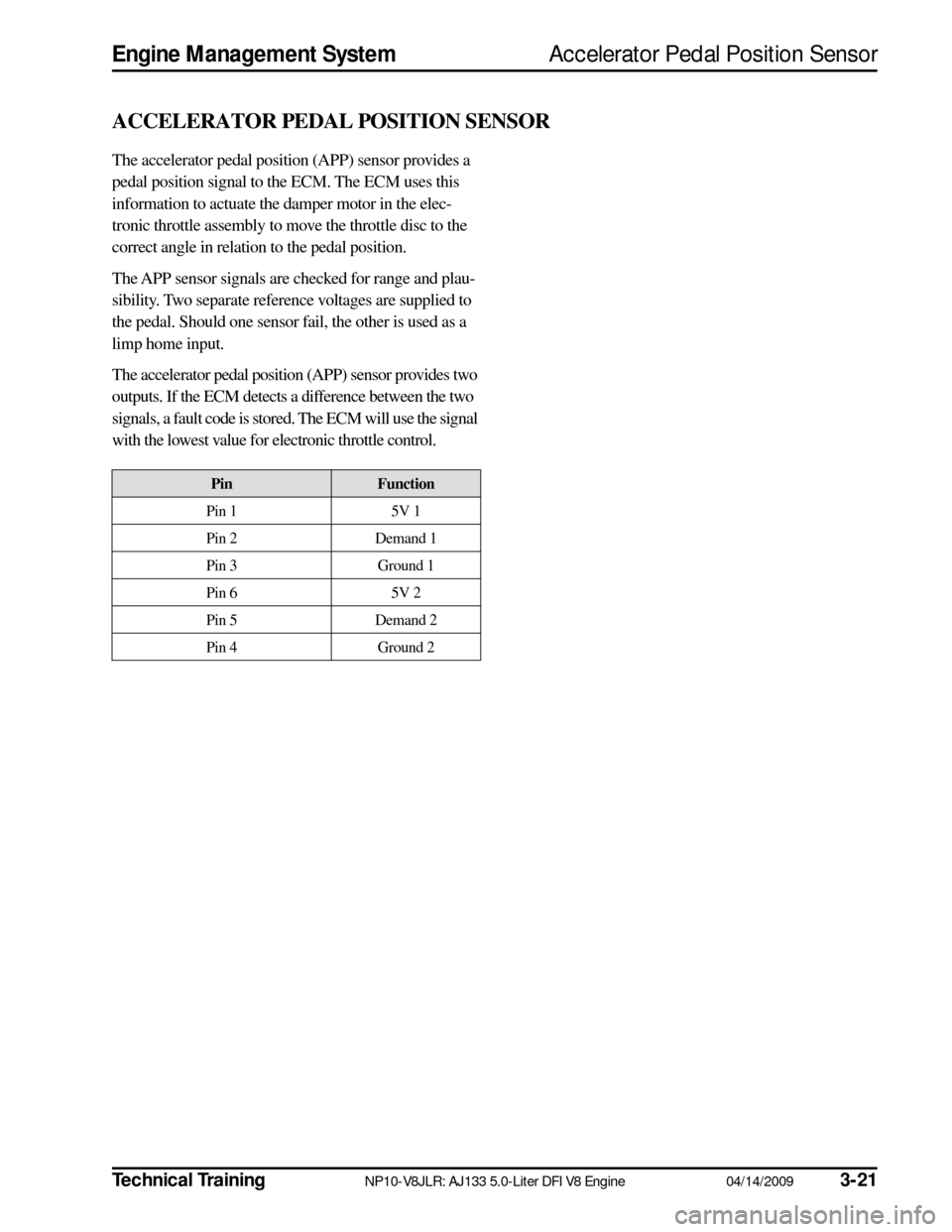
Technical TrainingNP10-V8JLR: AJ133 5.0-Liter DFI V8 Engine04/14/20093-21
Engine Management SystemAccelerator Pedal Position Sensor
ACCELERATOR PEDAL POSITION SENSOR
The accelerator pedal position (APP) sensor provides a
pedal position signal to the ECM. The ECM uses this
information to actuate the damper motor in the elec-
tronic throttle assembly to move the throttle disc to the
correct angle in relation to the pedal position.
The APP sensor signals are checked for range and plau-
sibility. Two separate reference voltages are supplied to
the pedal. Should one sensor fail, the other is used as a
limp home input.
The accelerator pedal position (APP) sensor provides two
outputs. If the ECM detects a difference between the two
signals, a fault code is stored. The ECM will use the signal
with the lowest value for electronic throttle control.
PinFunction
Pin 1 5V 1
Pin 2 Demand 1
Pin 3 Ground 1
Pin 6 5V 2
Pin 5 Demand 2
Pin 4 Ground 2
Page 30 of 36
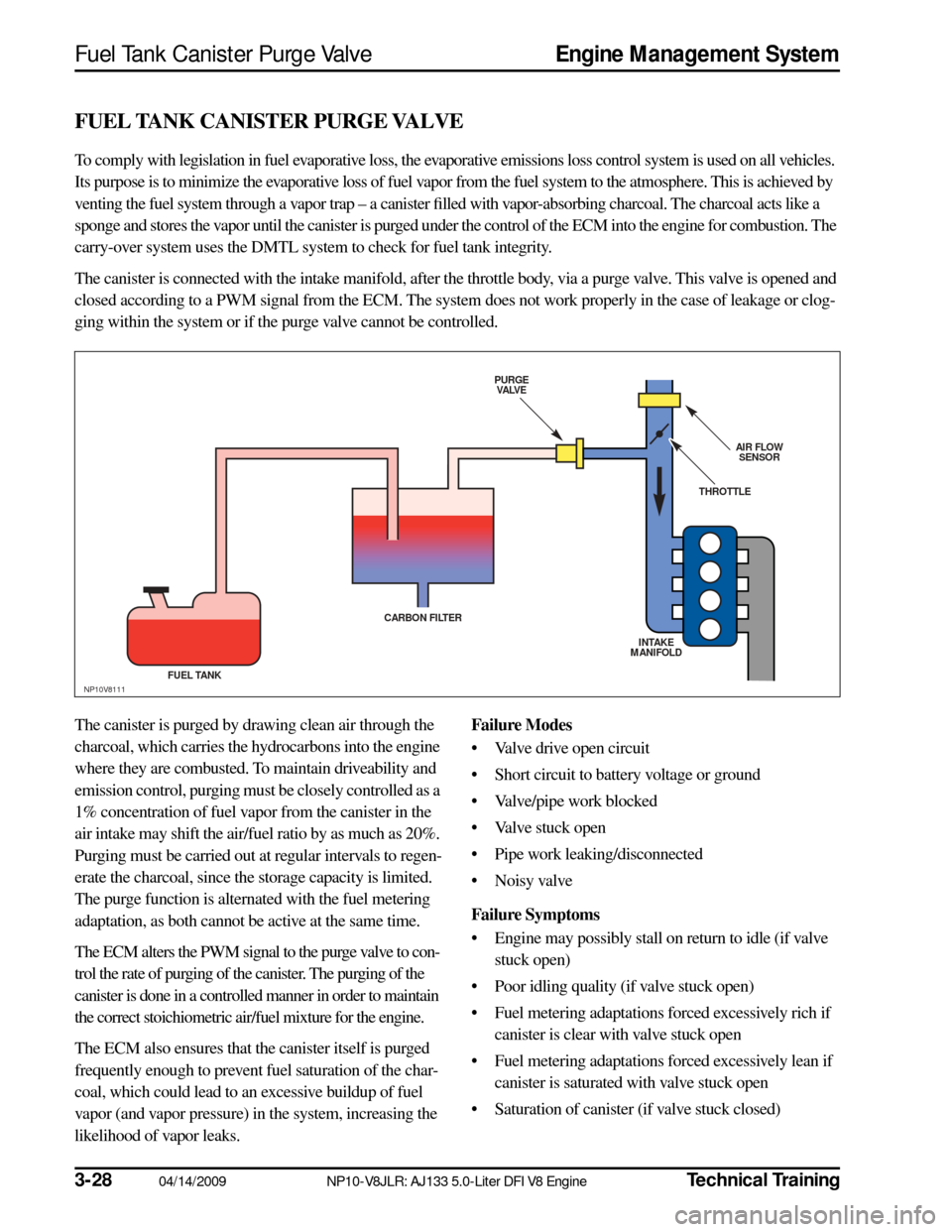
3-2804/14/2009NP10-V8JLR: AJ133 5.0-Liter DFI V8 EngineTechnical Training
Fuel Tank Canister Purge ValveEngine Management System
FUEL TANK CANISTER PURGE VALVE
To comply with legislation in fuel evaporative loss, the evaporative emissions loss control system is used on all vehicles.
Its purpose is to minimize the evaporative loss of fuel vapor from the fuel system to the atmosphere. This is achieved by
venting the fuel system through a vapor trap – a canister filled with vapor-absorbing charcoal. The charcoal acts like a
sponge and stores the vapor until the canister is purged under the control of the ECM into the engine for combustion. The
carry-over system uses the DMTL system to check for fuel tank integrity.
The canister is connected with the intake manifold, after the throttle body, via a purge valve. This valve is opened and
closed according to a PWM signal from the ECM. The system does not work properly in the case of leakage or clog-
ging within the system or if the purge valve cannot be controlled.
The canister is purged by drawing clean air through the
charcoal, which carries the hydrocarbons into the engine
where they are combusted. To maintain driveability and
emission control, purging must be closely controlled as a
1% concentration of fuel vapor from the canister in the
air intake may shift the air/fuel ratio by as much as 20%.
Purging must be carried out at regular intervals to regen-
erate the charcoal, since the storage capacity is limited.
The purge function is alternated with the fuel metering
adaptation, as both cannot be active at the same time.
The ECM alters the PWM signal to the purge valve to con-
trol the rate of purging of the canister. The purging of the
canister is done in a controlled manner in order to maintain
the correct stoichiometric air/fuel mixture for the engine.
The ECM also ensures that the canister itself is purged
frequently enough to prevent fuel saturation of the char-
coal, which could lead to an excessive buildup of fuel
vapor (and vapor pressure) in the system, increasing the
likelihood of vapor leaks. Failure Modes
• Valve drive open circuit
• Short circuit to battery voltage or ground
• Valve/pipe work blocked
• Valve stuck open
• Pipe work leaking/disconnected
• Noisy valve
Failure Symptoms
• Engine may possibly stall on return to idle (if valve
stuck open)
• Poor idling quality (if valve stuck open)
• Fuel metering adaptations forced excessively rich if canister is clear with valve stuck open
• Fuel metering adaptations forced excessively lean if canister is saturated with valve stuck open
• Saturation of canister (if valve stuck closed)
PURGE VALVE
AIR FLOWS ENS OR
THROTTLE
FUEL TANK CARBON FILTER
INTAKE
MANIFOLD
NP10V8111
Page 32 of 36
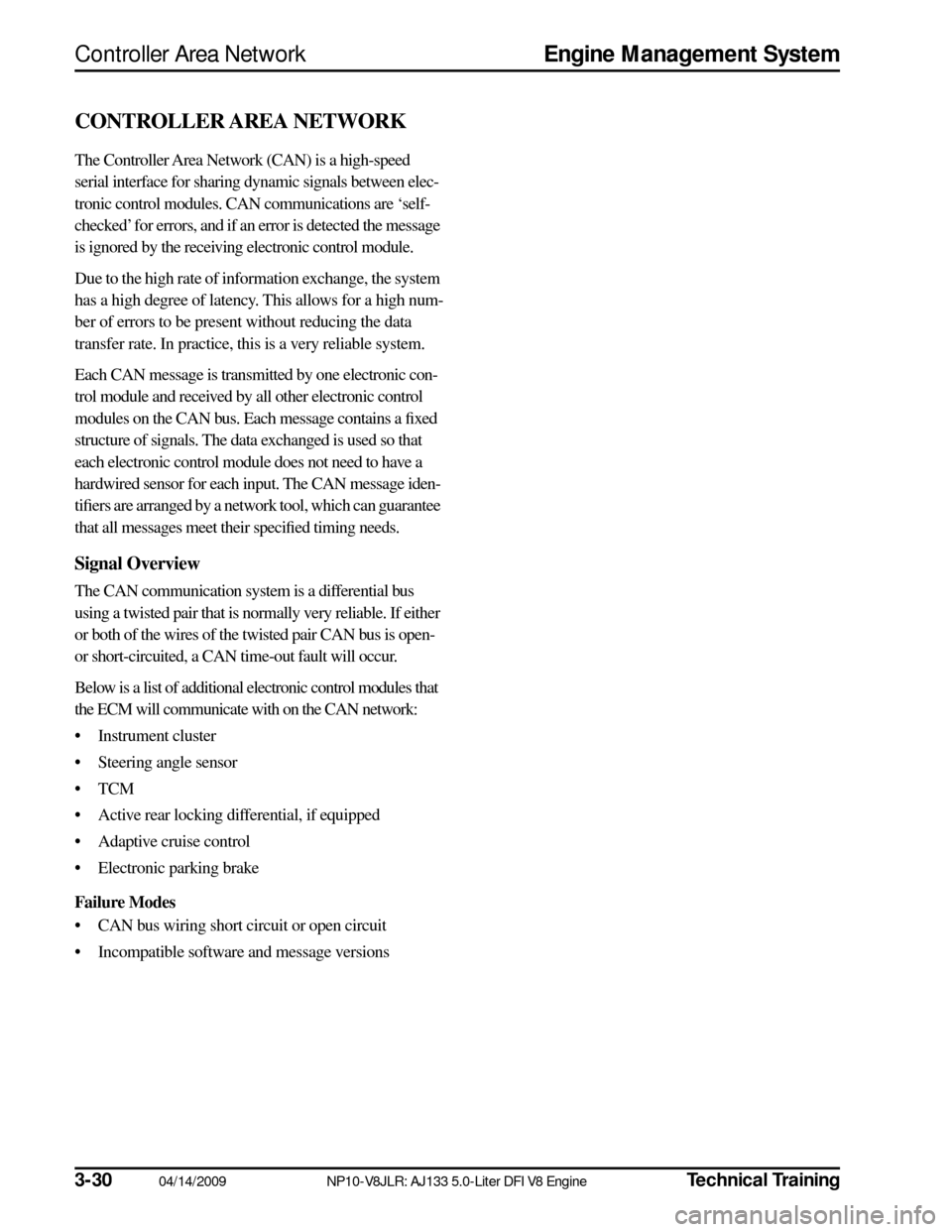
3-3004/14/2009NP10-V8JLR: AJ133 5.0-Liter DFI V8 EngineTechnical Training
Controller Area Network Engine Management System
CONTROLLER AREA NETWORK
The Controller Area Network (CAN) is a high-speed
serial interface for sharing dynamic signals between elec-
tronic control modules. CAN communications are ‘self-
checked’ for errors, and if an error is detected the message
is ignored by the receiving electronic control module.
Due to the high rate of information exchange, the system
has a high degree of latency. This allows for a high num-
ber of errors to be present without reducing the data
transfer rate. In practice, this is a very reliable system.
Each CAN message is transmitted by one electronic con-
trol module and received by all other electronic control
modules on the CAN bus. Each message contains a fixed
structure of signals. The data exchanged is used so that
each electronic control module does not need to have a
hardwired sensor for each input. The CAN message iden-
tifiers are arranged by a network tool, which can guarantee
that all messages meet their specified timing needs.
Signal Overview
The CAN communication system is a differential bus
using a twisted pair that is normally very reliable. If either
or both of the wires of the twisted pair CAN bus is open-
or short-circuited, a CAN time-out fault will occur.
Below is a list of additional electronic control modules that
the ECM will communicate with on the CAN network:
• Instrument cluster
• Steering angle sensor
•TCM
• Active rear locking differential, if equipped
• Adaptive cruise control
• Electronic parking brake
Failure Modes
• CAN bus wiring short circuit or open circuit
• Incompatible software and message versions