torque JAGUAR XF 2009 1.G AJ133 5.0L Engine Manual
[x] Cancel search | Manufacturer: JAGUAR, Model Year: 2009, Model line: XF, Model: JAGUAR XF 2009 1.GPages: 36, PDF Size: 0.38 MB
Page 4 of 36
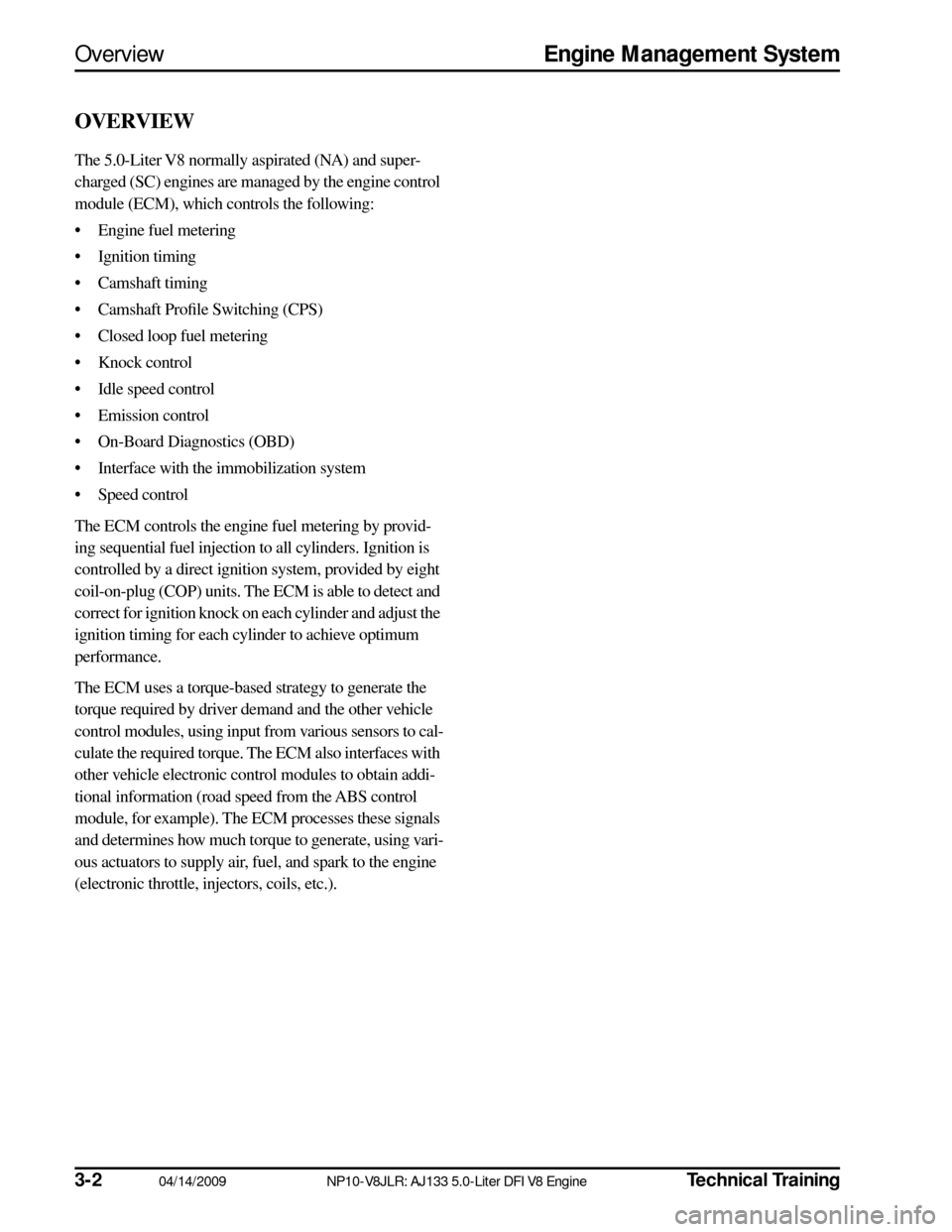
3-2
04/14/2009 NP10-V8JLR: AJ133 5.0-Liter DFI V8 Engine
Technical Training
Overview
Engine Management System
OVERVIEW
The 5.0-Liter V8 normally aspirated (NA) and super-
charged (SC) engines are managed by the engine control
module (ECM), which controls the following:
• Engine fuel metering
• Ignition timing
• Camshaft timing
• Camshaft Profile Switching (CPS)
• Closed loop fuel metering
• Knock control
• Idle speed control
• Emission control
• On-Board Diagnostics (OBD)
• Interface with the immobilization system
• Speed control
The ECM controls the engine fuel metering by provid-
ing sequential fuel injection to all cylinders. Ignition is
controlled by a direct ignition system, provided by eight
coil-on-plug (COP) units. The ECM is able to detect and
correct for ignition knock on each cylinder and adjust the
ignition timing for each cylinder to achieve optimum
performance.
The ECM uses a torque-based strategy to generate the
torque required by driver demand and the other vehicle
control modules, using input from various sensors to cal-
culate the required torque. The ECM also interfaces with
other vehicle electronic control modules to obtain addi-
tional information (road speed from the ABS control
module, for example). The ECM processes these signals
and determines how much torque to generate, using vari-
ous actuators to supply air, fuel, and spark to the engine
(electronic throttle, injectors, coils, etc.).
Page 13 of 36
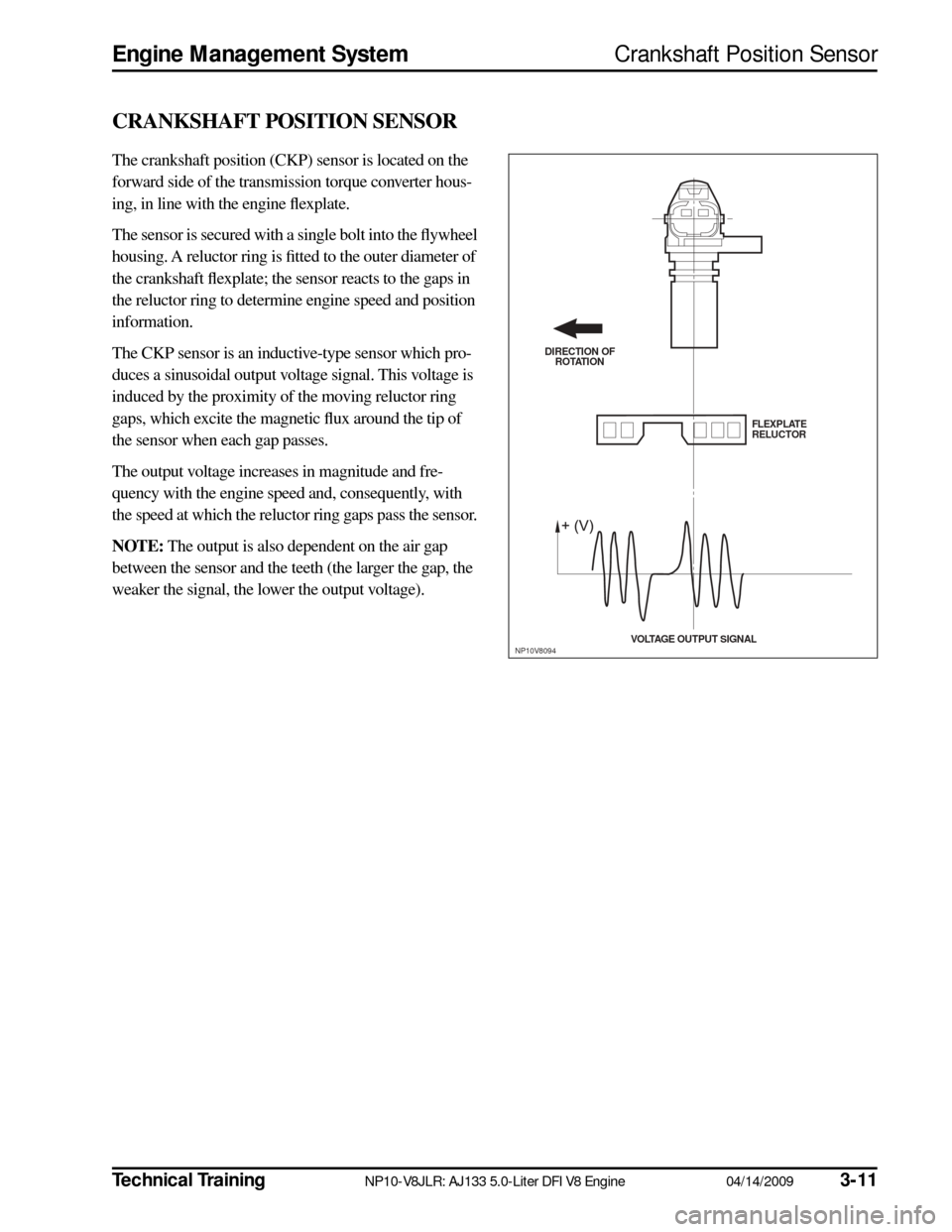
Technical Training
NP10-V8JLR: AJ133 5.0-Liter DFI V8 Engine 04/14/2009
3-11
Engine Management System
Crankshaft Position Sensor
CRANKSHAFT POSITION SENSOR
The crankshaft position (CKP) sensor is located on the
forward side of the transmission torque converter hous-
ing, in line with the engine flexplate.
The sensor is secured with a single bolt into the flywheel
housing. A reluctor ring is fitted to the outer diameter of
the crankshaft flexplate; the sensor reacts to the gaps in
the reluctor ring to determine engine speed and position
information.
The CKP sensor is an inductive-type sensor which pro-
duces a sinusoidal output voltage signal. This voltage is
induced by the proximity of the moving reluctor ring
gaps, which excite the magnetic flux around the tip of
the sensor when each gap passes.
The output voltage increases in magnitude and fre-
quency with the engine speed and, consequently, with
the speed at which the reluctor ring gaps pass the sensor.
NOTE:
The output is also dependent on the air gap
between the sensor and the teeth (the larger the gap, the
weaker the signal, the lower the output voltage).
DIRECTION OF ROTATION
FLEXPLATE
RELUCTOR
VOLTAGE OUTPUT S IGNAL
NP10V8094
Page 17 of 36
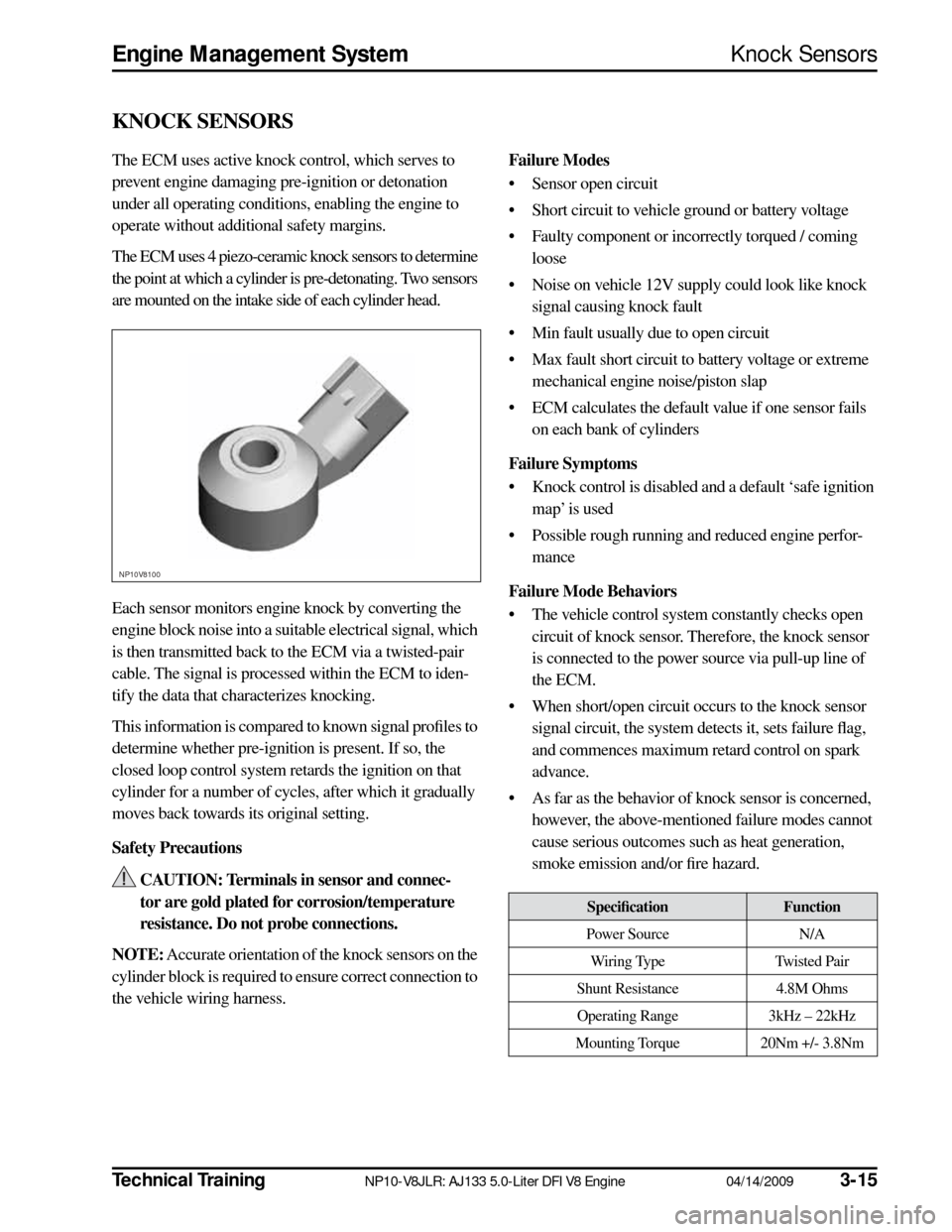
Technical Training
NP10-V8JLR: AJ133 5.0-Liter DFI V8 Engine 04/14/2009
3-15
Engine Management System
Knock Sensors
KNOCK SENSORS
The ECM uses active knock control, which serves to
prevent engine damaging pre-ignition or detonation
under all operating conditions, enabling the engine to
operate without additional safety margins.
The ECM uses 4 piezo-ceramic knock sensors to determine
the point at which a cylinder is pre-detonating. Two sensors
are mounted on the intake side of each cylinder head.
Each sensor monitors engine knock by converting the
engine block noise into a suitable electrical signal, which
is then transmitted back to the ECM via a twisted-pair
cable. The signal is processed within the ECM to iden-
tify the data that characterizes knocking.
This information is compared to known signal profiles to
determine whether pre-ignition is present. If so, the
closed loop control system retards the ignition on that
cylinder for a number of cycles, after which it gradually
moves back towards its original setting.
Safety Precautions CAUTION: Terminals in sensor and connec-
tor are gold plated for corrosion/temperature
resistance. Do not probe connections.
NOTE:
Accurate orientation of the knock sensors on the
cylinder block is required to ensure correct connection to
the vehicle wiring harness.
Failure Modes
• Sensor open circuit
• Short circuit to vehicle ground or battery voltage
• Faulty component or incorrectly torqued / coming loose
• Noise on vehicle 12V supply could look like knock signal causing knock fault
• Min fault usually due to open circuit
• Max fault short circuit to battery voltage or extreme mechanical engine noise/piston slap
• ECM calculates the default value if one sensor fails on each bank of cylinders
Failure Symptoms
• Knock control is disabled and a default ‘safe ignition map’ is used
• Possible rough running and reduced engine perfor- mance
Failure Mode Behaviors
• The vehicle control system constantly checks open circuit of knock sensor. Therefore, the knock sensor
is connected to the power source via pull-up line of
the ECM.
• When short/open circuit occurs to the knock sensor signal circuit, the system detects it, sets failure flag,
and commences maximum retard control on spark
advance.
• As far as the behavior of knock sensor is concerned, however, the above-mentioned failure modes cannot
cause serious outcomes such as heat generation,
smoke emission and/or fire hazard.
NP10V8100
Specification
Function
Power Source N/A
Wiring Type Twisted Pair
Shunt Resistance 4.8M Ohms
Operating Range 3kHz – 22kHz
Mounting Torque 20Nm +/- 3.8Nm
Page 21 of 36
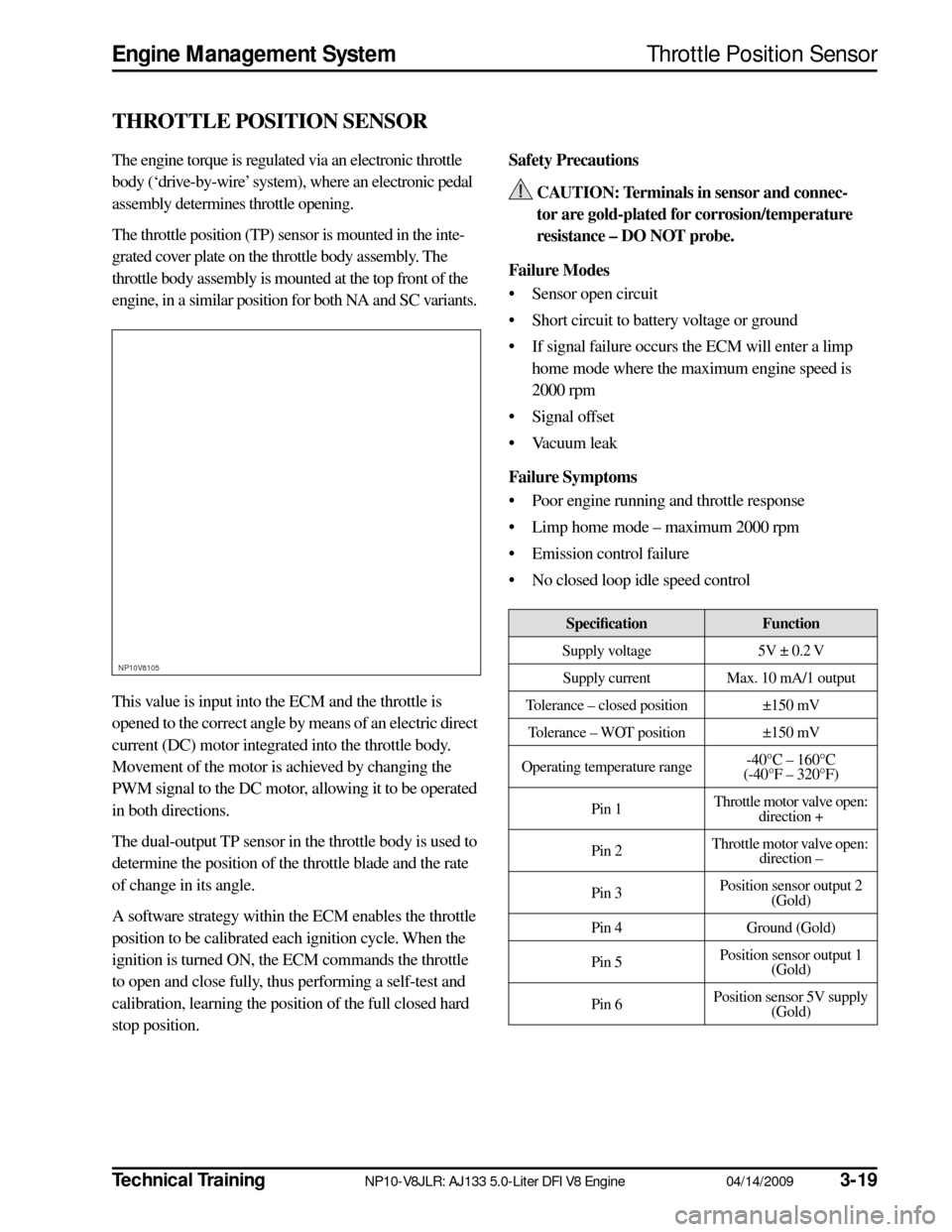
Technical TrainingNP10-V8JLR: AJ133 5.0-Liter DFI V8 Engine04/14/20093-19
Engine Management SystemThrottle Position Sensor
THROTTLE POSITION SENSOR
The engine torque is regulated via an electronic throttle
body (‘drive-by-wire’ system), where an electronic pedal
assembly determines throttle opening.
The throttle position (TP) sensor is mounted in the inte-
grated cover plate on the throttle body assembly. The
throttle body assembly is mounted at the top front of the
engine, in a similar position for both NA and SC variants.
This value is input into the ECM and the throttle is
opened to the correct angle by means of an electric direct
current (DC) motor integrated into the throttle body.
Movement of the motor is achieved by changing the
PWM signal to the DC motor, allowing it to be operated
in both directions.
The dual-output TP sensor in the throttle body is used to
determine the position of the throttle blade and the rate
of change in its angle.
A software strategy within the ECM enables the throttle
position to be calibrated each ignition cycle. When the
ignition is turned ON, the ECM commands the throttle
to open and close fully, thus performing a self-test and
calibration, learning the position of the full closed hard
stop position.Safety Precautions
CAUTION: Terminals in sensor and connec-
tor are gold-plated for corrosion/temperature
resistance – DO NOT probe.
Failure Modes
• Sensor open circuit
• Short circuit to battery voltage or ground
• If signal failure occurs the ECM will enter a limp home mode where the maximum engine speed is
2000 rpm
• Signal offset
• Vacuum leak
Failure Symptoms
• Poor engine running and throttle response
• Limp home mode – maximum 2000 rpm
• Emission control failure
• No closed loop idle speed control
NP10V8105
SpecificationFunction
Supply voltage 5V ± 0.2 V
Supply current Max. 10 mA/1 output
Tolerance – closed position ±150 mV Tolerance – WOT position ±150 mV
Operating temperature range -40°C – 160°C
(-40°F – 320°F)
Pin 1 Throttle motor valve open:
direction +
Pin 2 Throttle motor valve open:
direction –
Pin 3 Position sensor output 2
(Gold)
Pin 4 Ground (Gold)
Pin 5 Position sensor output 1
(Gold)
Pin 6 Position sensor 5V supply
(Gold)
Page 27 of 36
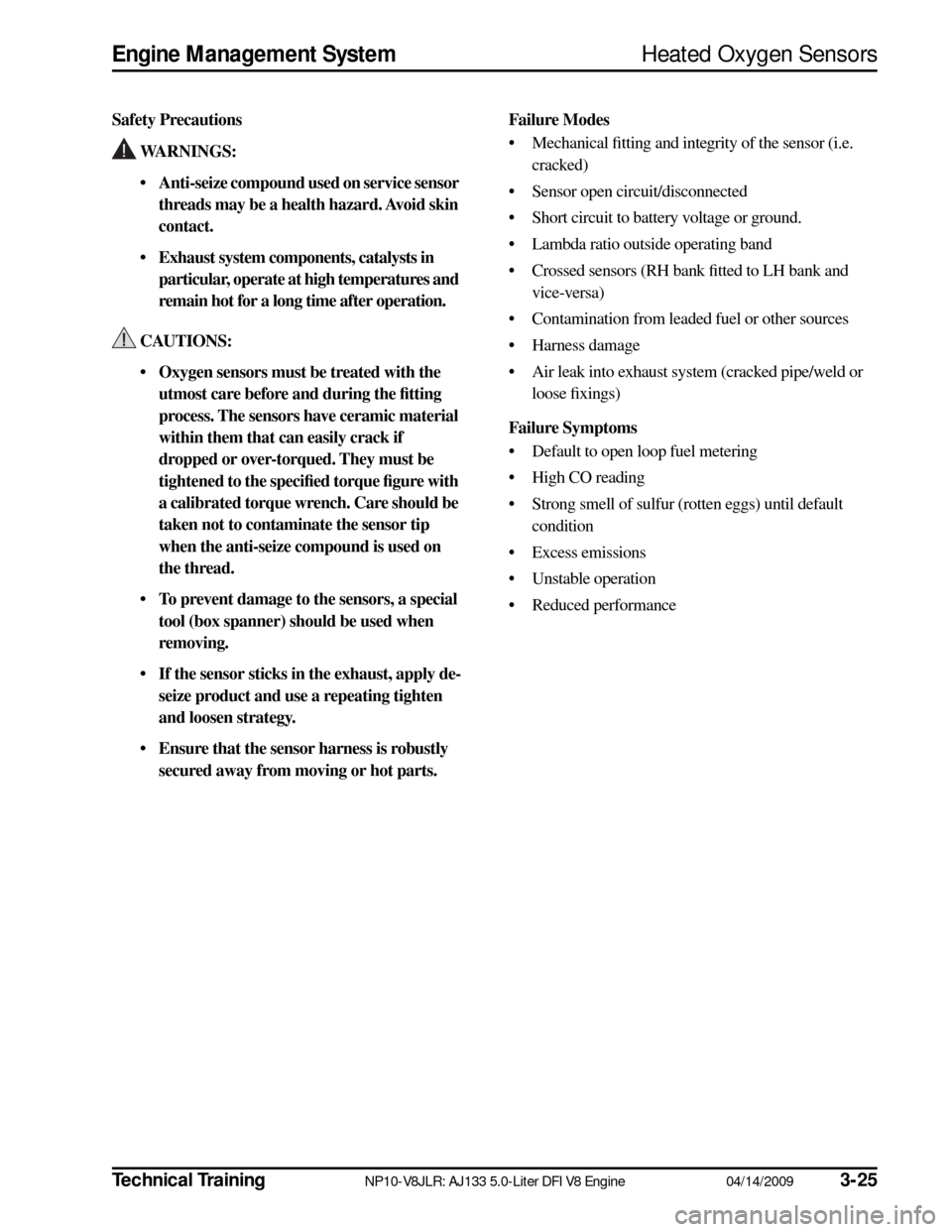
Technical TrainingNP10-V8JLR: AJ133 5.0-Liter DFI V8 Engine04/14/20093-25
Engine Management SystemHeated Oxygen Sensors
Safety Precautions
WARNINGS:
• Anti-seize compound used on service sensor threads may be a health hazard. Avoid skin
contact.
• Exhaust system components, catalysts in particular, operate at high temperatures and
remain hot for a long time after operation.
CAUTIONS:
• Oxygen sensors must be treated with the utmost care before and during the fitting
process. The sensors have ceramic material
within them that can easily crack if
dropped or over-torqued. They must be
tightened to the specified torque figure with
a calibrated torque wrench. Care should be
taken not to contaminate the sensor tip
when the anti-seize compound is used on
the thread.
• To prevent damage to the sensors, a special tool (box spanner) should be used when
removing.
• If the sensor sticks in the exhaust, apply de- seize product and use a repeating tighten
and loosen strategy.
• Ensure that the sensor harness is robustly secured away from moving or hot parts. Failure Modes
• Mechanical fitting and integrity of the sensor (i.e.
cracked)
• Sensor open circuit/disconnected
• Short circuit to battery voltage or ground.
• Lambda ratio outside operating band
• Crossed sensors (RH bank fitted to LH bank and vice-versa)
• Contamination from leaded fuel or other sources
• Harness damage
• Air leak into exhaust system (cracked pipe/weld or loose fixings)
Failure Symptoms
• Default to open loop fuel metering
• High CO reading
• Strong smell of sulfur (rotten eggs) until default condition
• Excess emissions
• Unstable operation
• Reduced performance