Engine JAGUAR XFR 2010 1.G Workshop Manual
[x] Cancel search | Manufacturer: JAGUAR, Model Year: 2010, Model line: XFR, Model: JAGUAR XFR 2010 1.GPages: 3039, PDF Size: 58.49 MB
Page 1418 of 3039
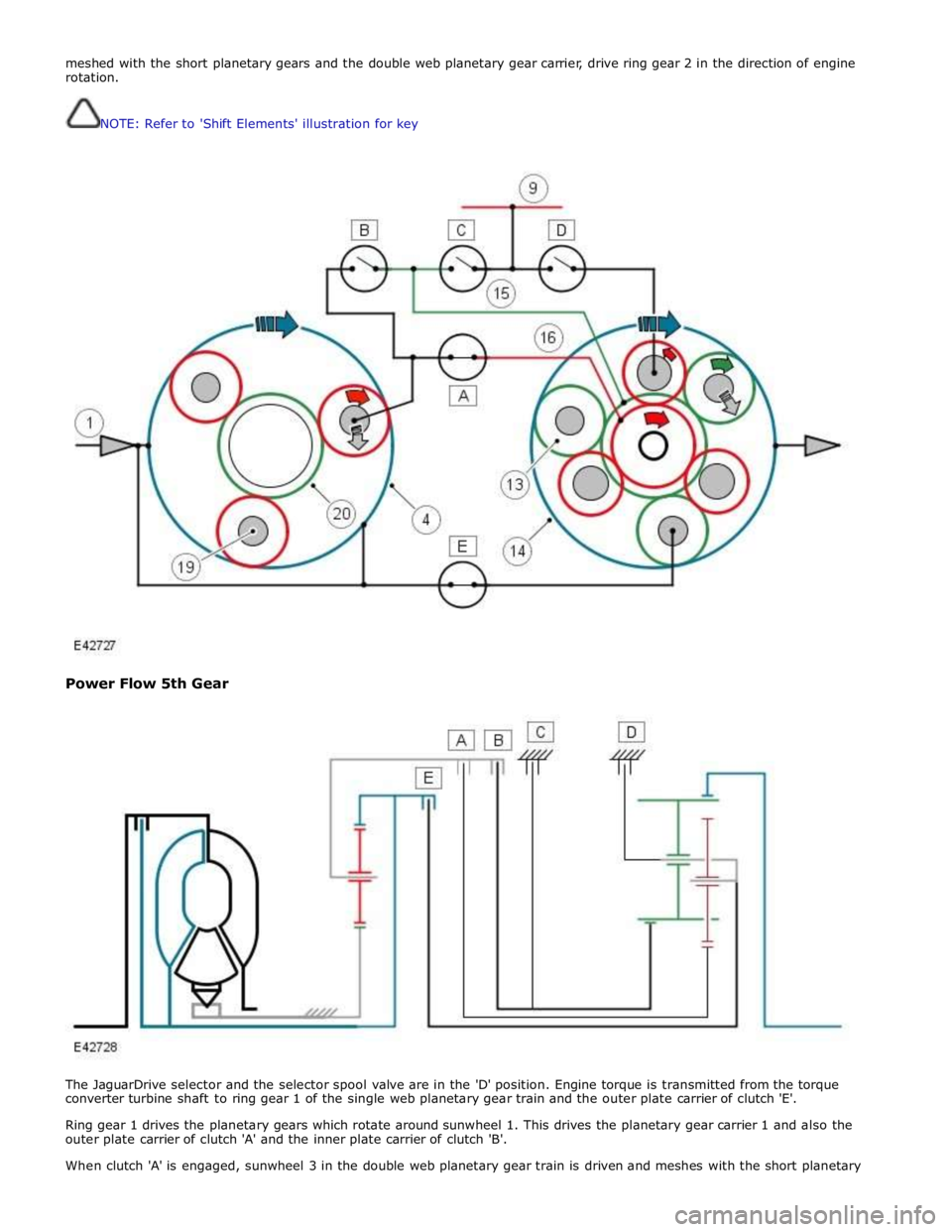
meshed with the short planetary gears and the double web planetary gear carrier, drive ring gear 2 in the direction of engine
rotation.
NOTE: Refer to 'Shift Elements' illustration for key
Power Flow 5th Gear
The JaguarDrive selector and the selector spool valve are in the 'D' position. Engine torque is transmitted from the torque
converter turbine shaft to ring gear 1 of the single web planetary gear train and the outer plate carrier of clutch 'E'.
Ring gear 1 drives the planetary gears which rotate around sunwheel 1. This drives the planetary gear carrier 1 and also the
outer plate carrier of clutch 'A' and the inner plate carrier of clutch 'B'.
When clutch 'A' is engaged, sunwheel 3 in the double web planetary gear train is driven and meshes with the short planetary
Page 1419 of 3039
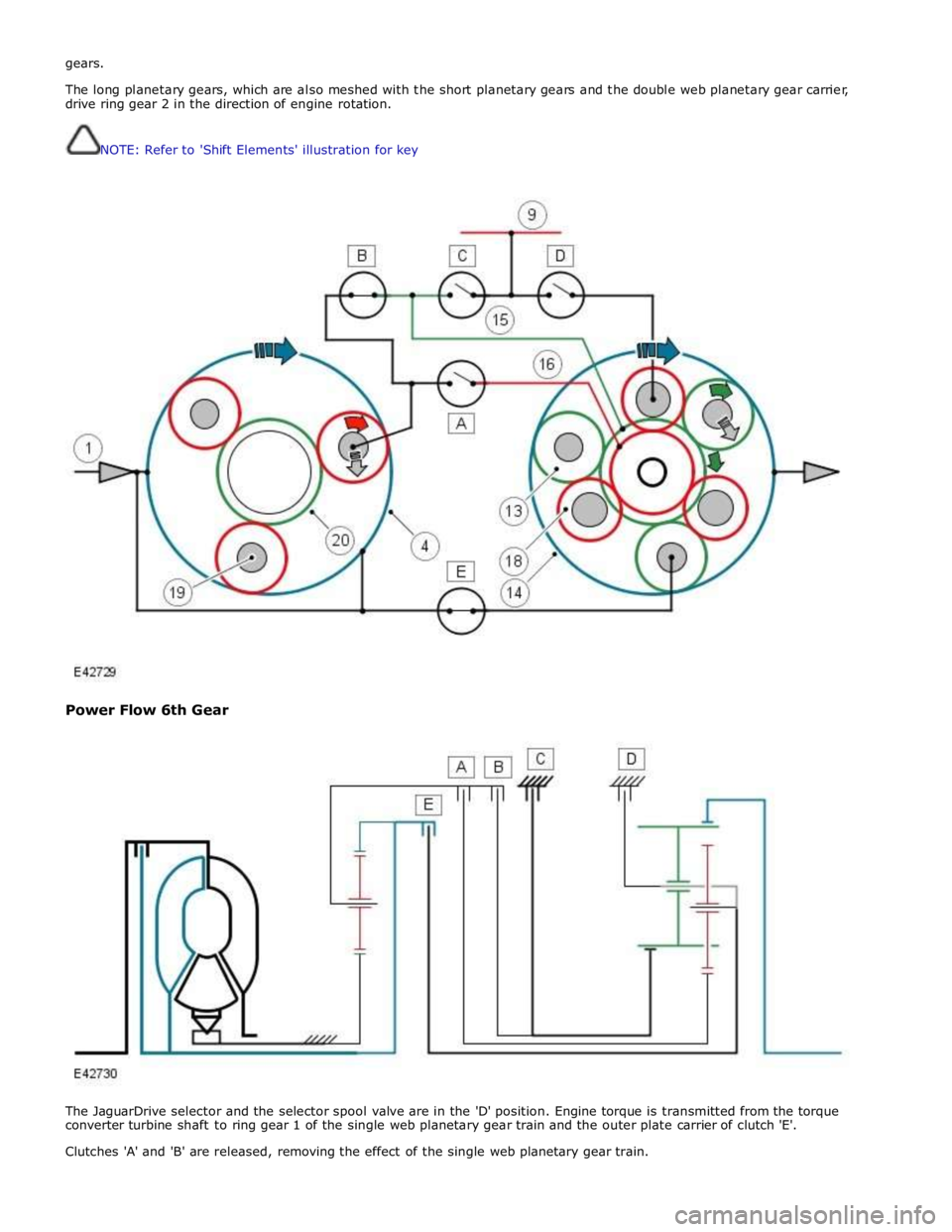
gears.
The long planetary gears, which are also meshed with the short planetary gears and the double web planetary gear carrier,
drive ring gear 2 in the direction of engine rotation.
NOTE: Refer to 'Shift Elements' illustration for key
Power Flow 6th Gear
The JaguarDrive selector and the selector spool valve are in the 'D' position. Engine torque is transmitted from the torque
converter turbine shaft to ring gear 1 of the single web planetary gear train and the outer plate carrier of clutch 'E'.
Clutches 'A' and 'B' are released, removing the effect of the single web planetary gear train.
Page 1420 of 3039
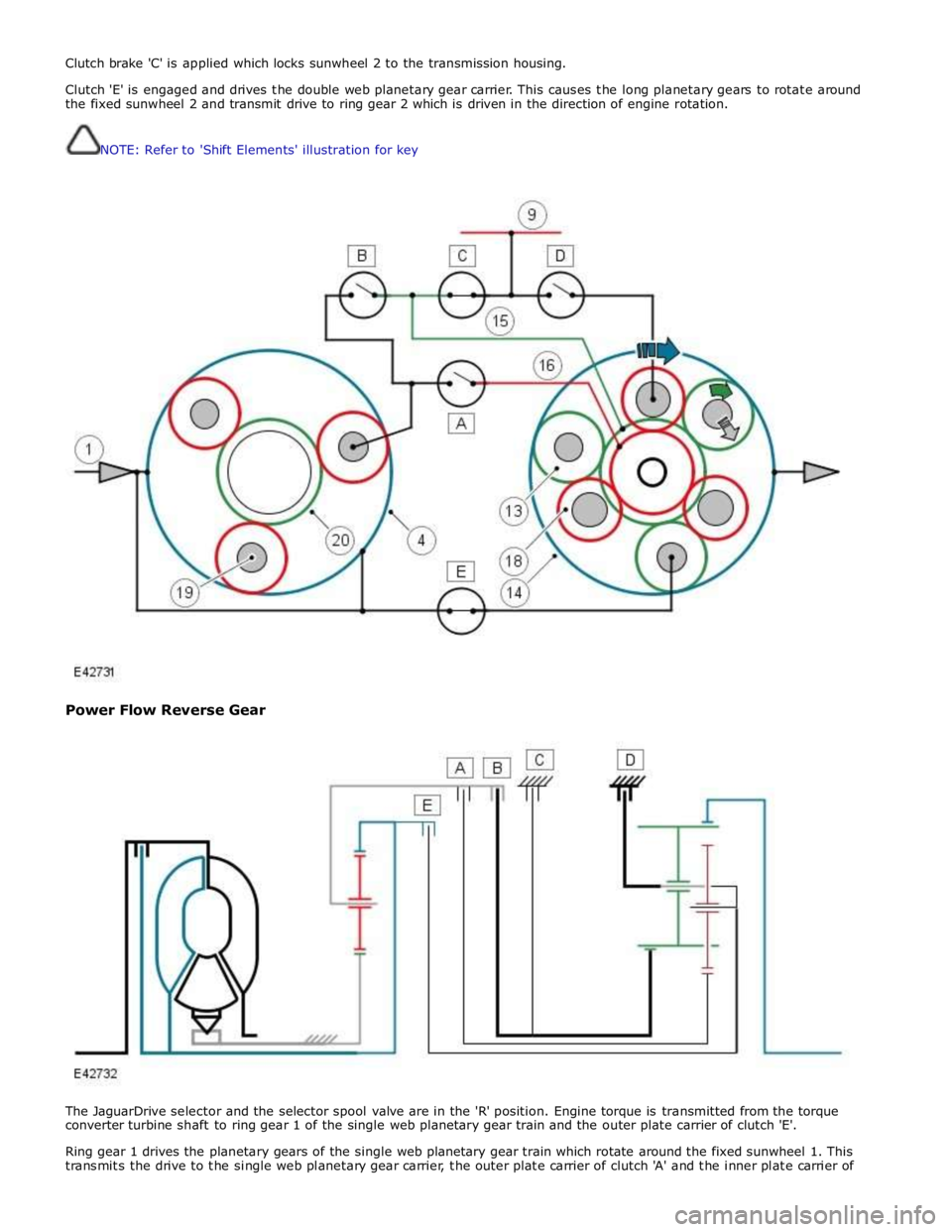
Clutch brake 'C' is applied which locks sunwheel 2 to the transmission housing.
Clutch 'E' is engaged and drives the double web planetary gear carrier. This causes the long planetary gears to rotate around
the fixed sunwheel 2 and transmit drive to ring gear 2 which is driven in the direction of engine rotation.
NOTE: Refer to 'Shift Elements' illustration for key
Power Flow Reverse Gear
The JaguarDrive selector and the selector spool valve are in the 'R' position. Engine torque is transmitted from the torque
converter turbine shaft to ring gear 1 of the single web planetary gear train and the outer plate carrier of clutch 'E'.
Ring gear 1 drives the planetary gears of the single web planetary gear train which rotate around the fixed sunwheel 1. This
transmits the drive to the single web planetary gear carrier, the outer plate carrier of clutch 'A' and the inner plate carrier of
Page 1421 of 3039
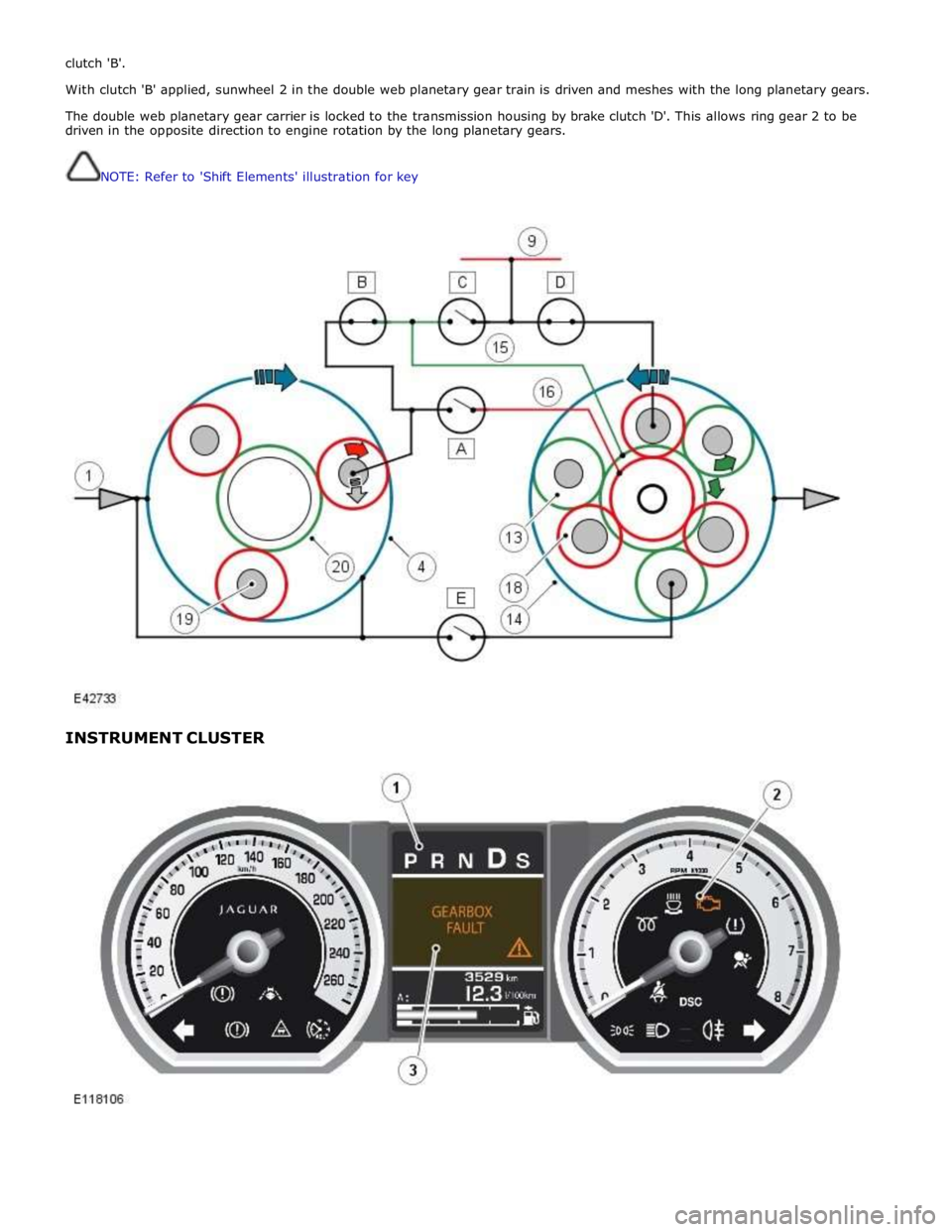
clutch 'B'.
With clutch 'B' applied, sunwheel 2 in the double web planetary gear train is driven and meshes with the long planetary gears.
The double web planetary gear carrier is locked to the transmission housing by brake clutch 'D'. This allows ring gear 2 to be
driven in the opposite direction to engine rotation by the long planetary gears.
NOTE: Refer to 'Shift Elements' illustration for key
INSTRUMENT CLUSTER
Page 1422 of 3039
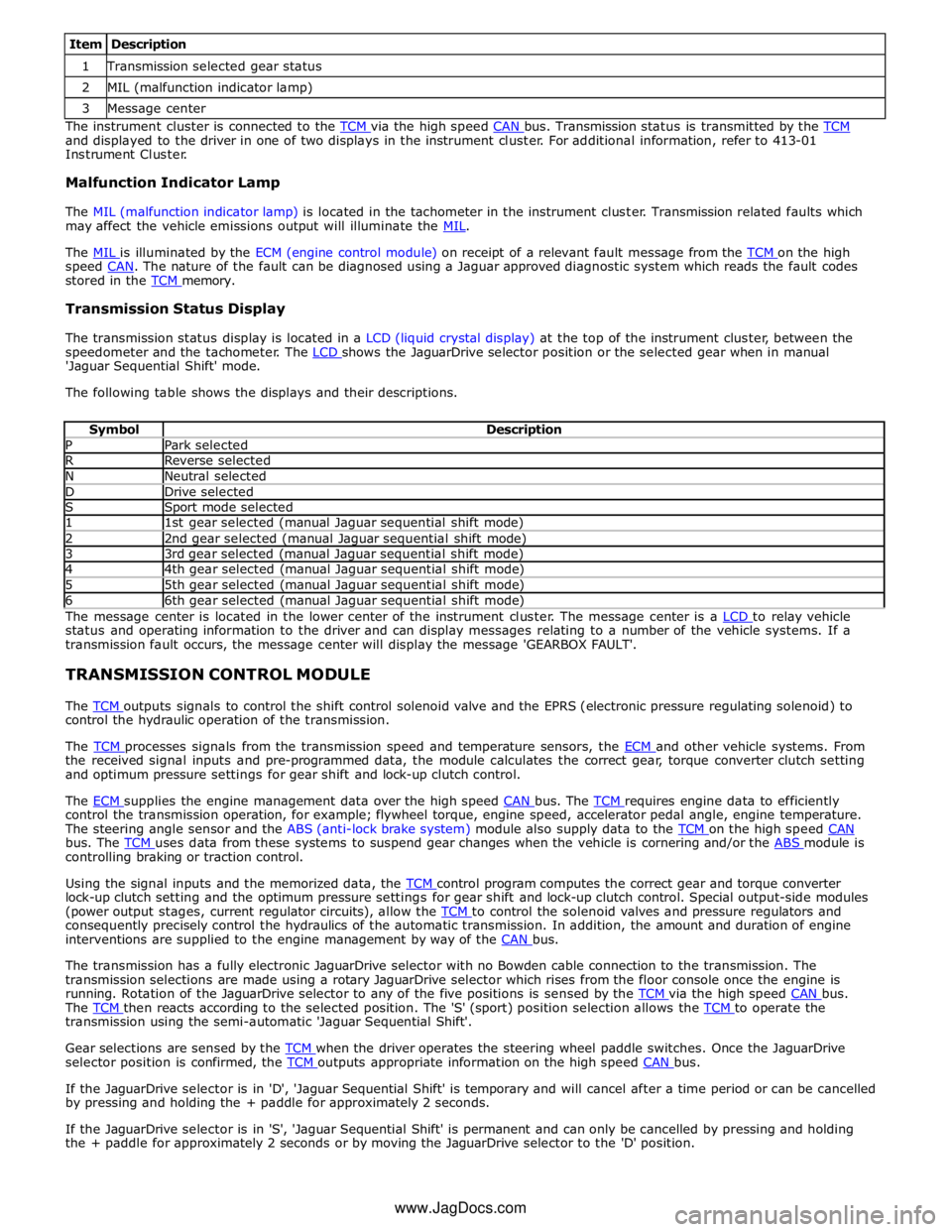
1 Transmission selected gear status 2 MIL (malfunction indicator lamp) 3 Message center The instrument cluster is connected to the TCM via the high speed CAN bus. Transmission status is transmitted by the TCM and displayed to the driver in one of two displays in the instrument cluster. For additional information, refer to 413-01
Instrument Cluster.
Malfunction Indicator Lamp
The MIL (malfunction indicator lamp) is located in the tachometer in the instrument cluster. Transmission related faults which
may affect the vehicle emissions output will illuminate the MIL.
The MIL is illuminated by the ECM (engine control module) on receipt of a relevant fault message from the TCM on the high speed CAN. The nature of the fault can be diagnosed using a Jaguar approved diagnostic system which reads the fault codes stored in the TCM memory.
Transmission Status Display
The transmission status display is located in a LCD (liquid crystal display) at the top of the instrument cluster, between the
speedometer and the tachometer. The LCD shows the JaguarDrive selector position or the selected gear when in manual 'Jaguar Sequential Shift' mode.
The following table shows the displays and their descriptions.
Symbol Description P Park selected R Reverse selected N Neutral selected D Drive selected S Sport mode selected 1 1st gear selected (manual Jaguar sequential shift mode) 2 2nd gear selected (manual Jaguar sequential shift mode) 3 3rd gear selected (manual Jaguar sequential shift mode) 4 4th gear selected (manual Jaguar sequential shift mode) 5 5th gear selected (manual Jaguar sequential shift mode) 6 6th gear selected (manual Jaguar sequential shift mode) The message center is located in the lower center of the instrument cluster. The message center is a LCD to relay vehicle status and operating information to the driver and can display messages relating to a number of the vehicle systems. If a
transmission fault occurs, the message center will display the message 'GEARBOX FAULT'.
TRANSMISSION CONTROL MODULE
The TCM outputs signals to control the shift control solenoid valve and the EPRS (electronic pressure regulating solenoid) to control the hydraulic operation of the transmission.
The TCM processes signals from the transmission speed and temperature sensors, the ECM and other vehicle systems. From the received signal inputs and pre-programmed data, the module calculates the correct gear, torque converter clutch setting
and optimum pressure settings for gear shift and lock-up clutch control.
The ECM supplies the engine management data over the high speed CAN bus. The TCM requires engine data to efficiently control the transmission operation, for example; flywheel torque, engine speed, accelerator pedal angle, engine temperature.
The steering angle sensor and the ABS (anti-lock brake system) module also supply data to the TCM on the high speed CAN bus. The TCM uses data from these systems to suspend gear changes when the vehicle is cornering and/or the ABS module is controlling braking or traction control.
Using the signal inputs and the memorized data, the TCM control program computes the correct gear and torque converter lock-up clutch setting and the optimum pressure settings for gear shift and lock-up clutch control. Special output-side modules
(power output stages, current regulator circuits), allow the TCM to control the solenoid valves and pressure regulators and consequently precisely control the hydraulics of the automatic transmission. In addition, the amount and duration of engine
interventions are supplied to the engine management by way of the CAN bus.
The transmission has a fully electronic JaguarDrive selector with no Bowden cable connection to the transmission. The
transmission selections are made using a rotary JaguarDrive selector which rises from the floor console once the engine is
running. Rotation of the JaguarDrive selector to any of the five positions is sensed by the TCM via the high speed CAN bus. The TCM then reacts according to the selected position. The 'S' (sport) position selection allows the TCM to operate the transmission using the semi-automatic 'Jaguar Sequential Shift'.
Gear selections are sensed by the TCM when the driver operates the steering wheel paddle switches. Once the JaguarDrive selector position is confirmed, the TCM outputs appropriate information on the high speed CAN bus.
If the JaguarDrive selector is in 'D', 'Jaguar Sequential Shift' is temporary and will cancel after a time period or can be cancelled
by pressing and holding the + paddle for approximately 2 seconds.
If the JaguarDrive selector is in 'S', 'Jaguar Sequential Shift' is permanent and can only be cancelled by pressing and holding
the + paddle for approximately 2 seconds or by moving the JaguarDrive selector to the 'D' position.
www.JagDocs.com
Page 1423 of 3039
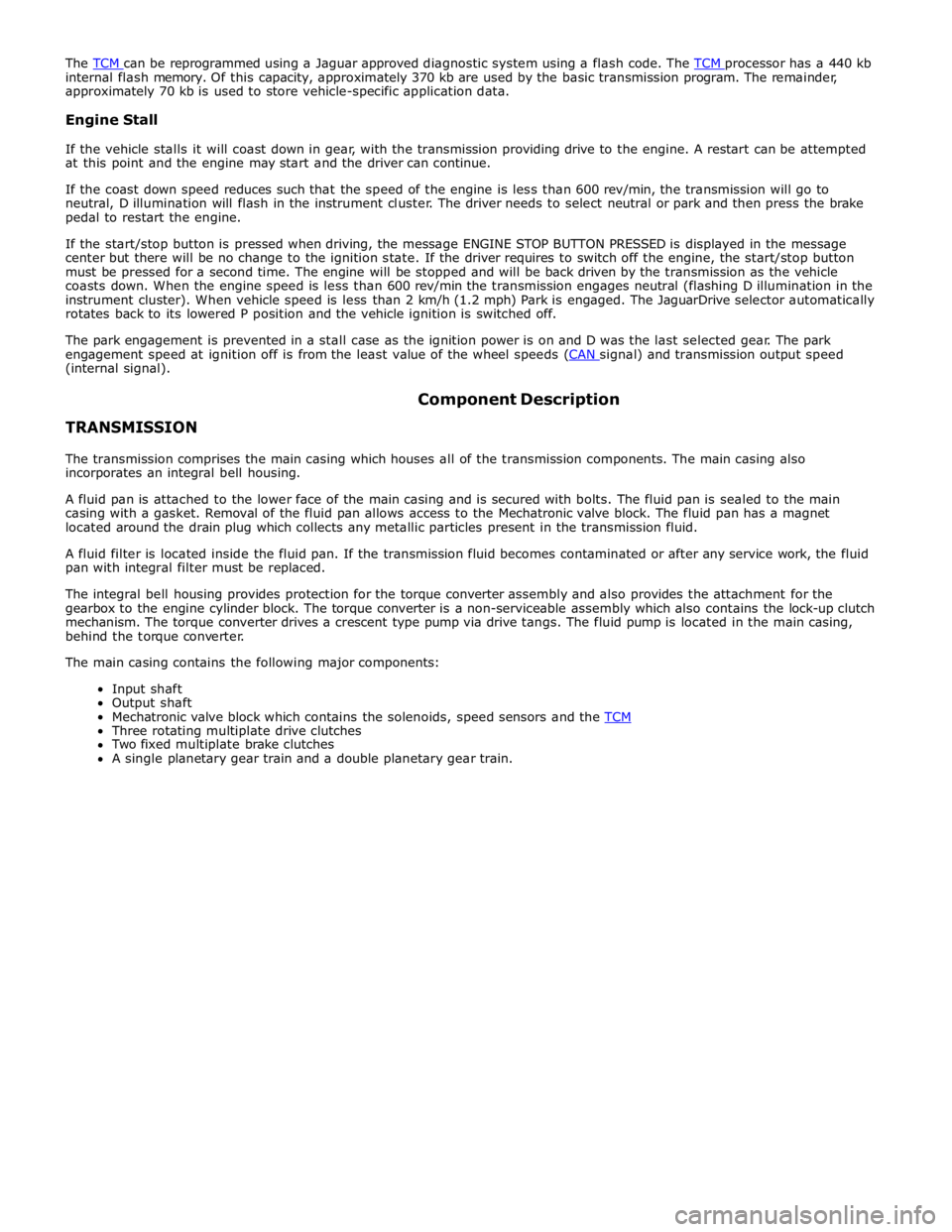
The TCM can be reprogrammed using a Jaguar approved diagnostic system using a flash code. The TCM processor has a 440 kb internal flash memory. Of this capacity, approximately 370 kb are used by the basic transmission program. The remainder,
approximately 70 kb is used to store vehicle-specific application data.
Engine Stall
If the vehicle stalls it will coast down in gear, with the transmission providing drive to the engine. A restart can be attempted
at this point and the engine may start and the driver can continue.
If the coast down speed reduces such that the speed of the engine is less than 600 rev/min, the transmission will go to
neutral, D illumination will flash in the instrument cluster. The driver needs to select neutral or park and then press the brake
pedal to restart the engine.
If the start/stop button is pressed when driving, the message ENGINE STOP BUTTON PRESSED is displayed in the message
center but there will be no change to the ignition state. If the driver requires to switch off the engine, the start/stop button
must be pressed for a second time. The engine will be stopped and will be back driven by the transmission as the vehicle
coasts down. When the engine speed is less than 600 rev/min the transmission engages neutral (flashing D illumination in the
instrument cluster). When vehicle speed is less than 2 km/h (1.2 mph) Park is engaged. The JaguarDrive selector automatically
rotates back to its lowered P position and the vehicle ignition is switched off.
The park engagement is prevented in a stall case as the ignition power is on and D was the last selected gear. The park
engagement speed at ignition off is from the least value of the wheel speeds (CAN signal) and transmission output speed (internal signal).
TRANSMISSION Component Description
The transmission comprises the main casing which houses all of the transmission components. The main casing also
incorporates an integral bell housing.
A fluid pan is attached to the lower face of the main casing and is secured with bolts. The fluid pan is sealed to the main
casing with a gasket. Removal of the fluid pan allows access to the Mechatronic valve block. The fluid pan has a magnet
located around the drain plug which collects any metallic particles present in the transmission fluid.
A fluid filter is located inside the fluid pan. If the transmission fluid becomes contaminated or after any service work, the fluid
pan with integral filter must be replaced.
The integral bell housing provides protection for the torque converter assembly and also provides the attachment for the
gearbox to the engine cylinder block. The torque converter is a non-serviceable assembly which also contains the lock-up clutch
mechanism. The torque converter drives a crescent type pump via drive tangs. The fluid pump is located in the main casing,
behind the torque converter.
The main casing contains the following major components:
Input shaft
Output shaft
Mechatronic valve block which contains the solenoids, speed sensors and the TCM Three rotating multiplate drive clutches
Two fixed multiplate brake clutches
A single planetary gear train and a double planetary gear train.
Page 1426 of 3039
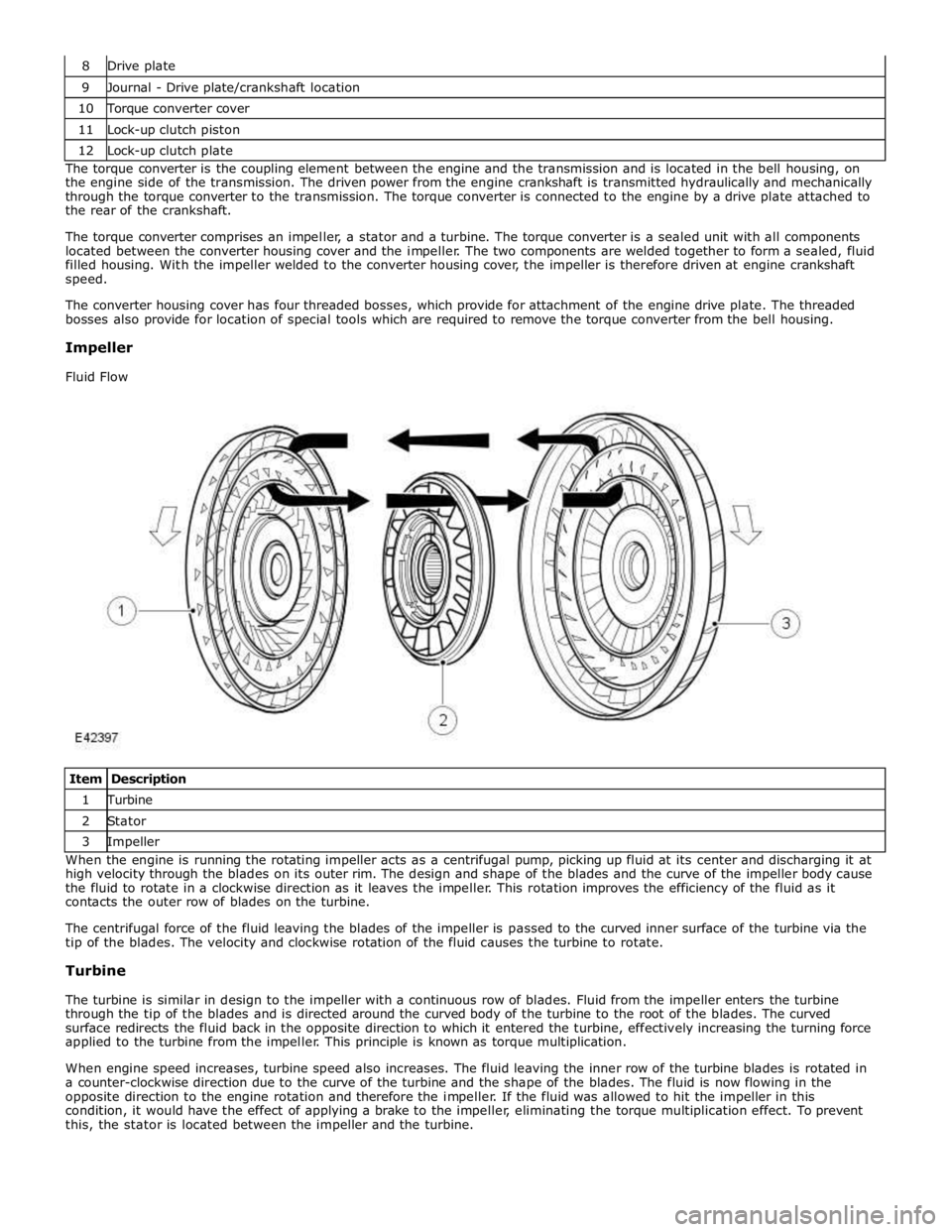
9 Journal - Drive plate/crankshaft location 10 Torque converter cover 11 Lock-up clutch piston 12 Lock-up clutch plate The torque converter is the coupling element between the engine and the transmission and is located in the bell housing, on
the engine side of the transmission. The driven power from the engine crankshaft is transmitted hydraulically and mechanically
through the torque converter to the transmission. The torque converter is connected to the engine by a drive plate attached to
the rear of the crankshaft.
The torque converter comprises an impeller, a stator and a turbine. The torque converter is a sealed unit with all components
located between the converter housing cover and the impeller. The two components are welded together to form a sealed, fluid
filled housing. With the impeller welded to the converter housing cover, the impeller is therefore driven at engine crankshaft
speed.
The converter housing cover has four threaded bosses, which provide for attachment of the engine drive plate. The threaded
bosses also provide for location of special tools which are required to remove the torque converter from the bell housing.
Impeller
Fluid Flow
Item Description 1 Turbine 2 Stator 3 Impeller When the engine is running the rotating impeller acts as a centrifugal pump, picking up fluid at its center and discharging it at
high velocity through the blades on its outer rim. The design and shape of the blades and the curve of the impeller body cause
the fluid to rotate in a clockwise direction as it leaves the impeller. This rotation improves the efficiency of the fluid as it
contacts the outer row of blades on the turbine.
The centrifugal force of the fluid leaving the blades of the impeller is passed to the curved inner surface of the turbine via the
tip of the blades. The velocity and clockwise rotation of the fluid causes the turbine to rotate.
Turbine
The turbine is similar in design to the impeller with a continuous row of blades. Fluid from the impeller enters the turbine
through the tip of the blades and is directed around the curved body of the turbine to the root of the blades. The curved
surface redirects the fluid back in the opposite direction to which it entered the turbine, effectively increasing the turning force
applied to the turbine from the impeller. This principle is known as torque multiplication.
When engine speed increases, turbine speed also increases. The fluid leaving the inner row of the turbine blades is rotated in
a counter-clockwise direction due to the curve of the turbine and the shape of the blades. The fluid is now flowing in the
opposite direction to the engine rotation and therefore the impeller. If the fluid was allowed to hit the impeller in this
condition, it would have the effect of applying a brake to the impeller, eliminating the torque multiplication effect. To prevent
this, the stator is located between the impeller and the turbine.
Page 1427 of 3039
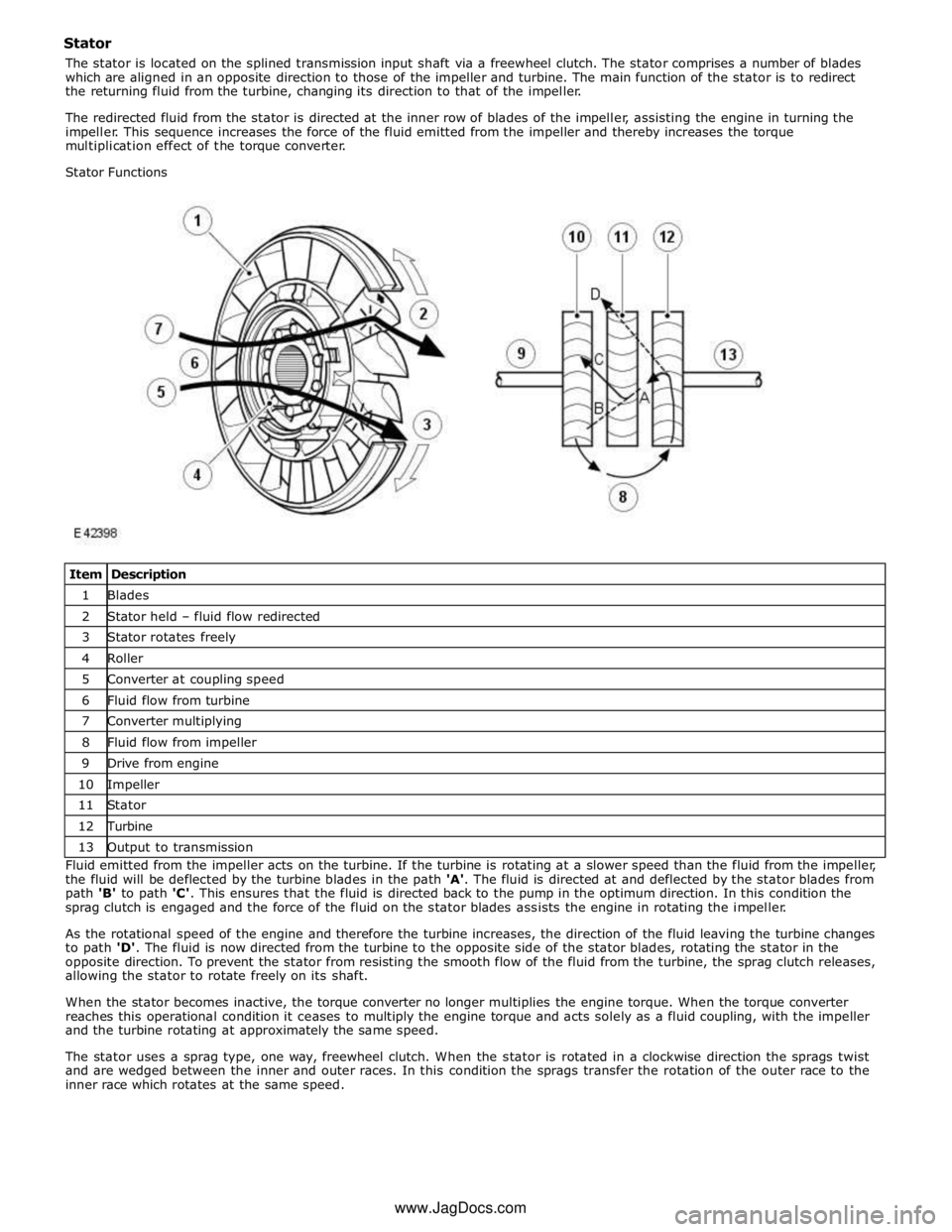
1 Blades 2 Stator held – fluid flow redirected 3 Stator rotates freely 4 Roller 5 Converter at coupling speed 6 Fluid flow from turbine 7 Converter multiplying 8 Fluid flow from impeller 9 Drive from engine 10 Impeller 11 Stator 12 Turbine 13 Output to transmission Fluid emitted from the impeller acts on the turbine. If the turbine is rotating at a slower speed than the fluid from the impeller,
the fluid will be deflected by the turbine blades in the path 'A'. The fluid is directed at and deflected by the stator blades from
path 'B' to path 'C'. This ensures that the fluid is directed back to the pump in the optimum direction. In this condition the
sprag clutch is engaged and the force of the fluid on the stator blades assists the engine in rotating the impeller.
As the rotational speed of the engine and therefore the turbine increases, the direction of the fluid leaving the turbine changes
to path 'D'. The fluid is now directed from the turbine to the opposite side of the stator blades, rotating the stator in the
opposite direction. To prevent the stator from resisting the smooth flow of the fluid from the turbine, the sprag clutch releases,
allowing the stator to rotate freely on its shaft.
When the stator becomes inactive, the torque converter no longer multiplies the engine torque. When the torque converter
reaches this operational condition it ceases to multiply the engine torque and acts solely as a fluid coupling, with the impeller
and the turbine rotating at approximately the same speed.
The stator uses a sprag type, one way, freewheel clutch. When the stator is rotated in a clockwise direction the sprags twist
and are wedged between the inner and outer races. In this condition the sprags transfer the rotation of the outer race to the
inner race which rotates at the same speed. www.JagDocs.com
Page 1429 of 3039
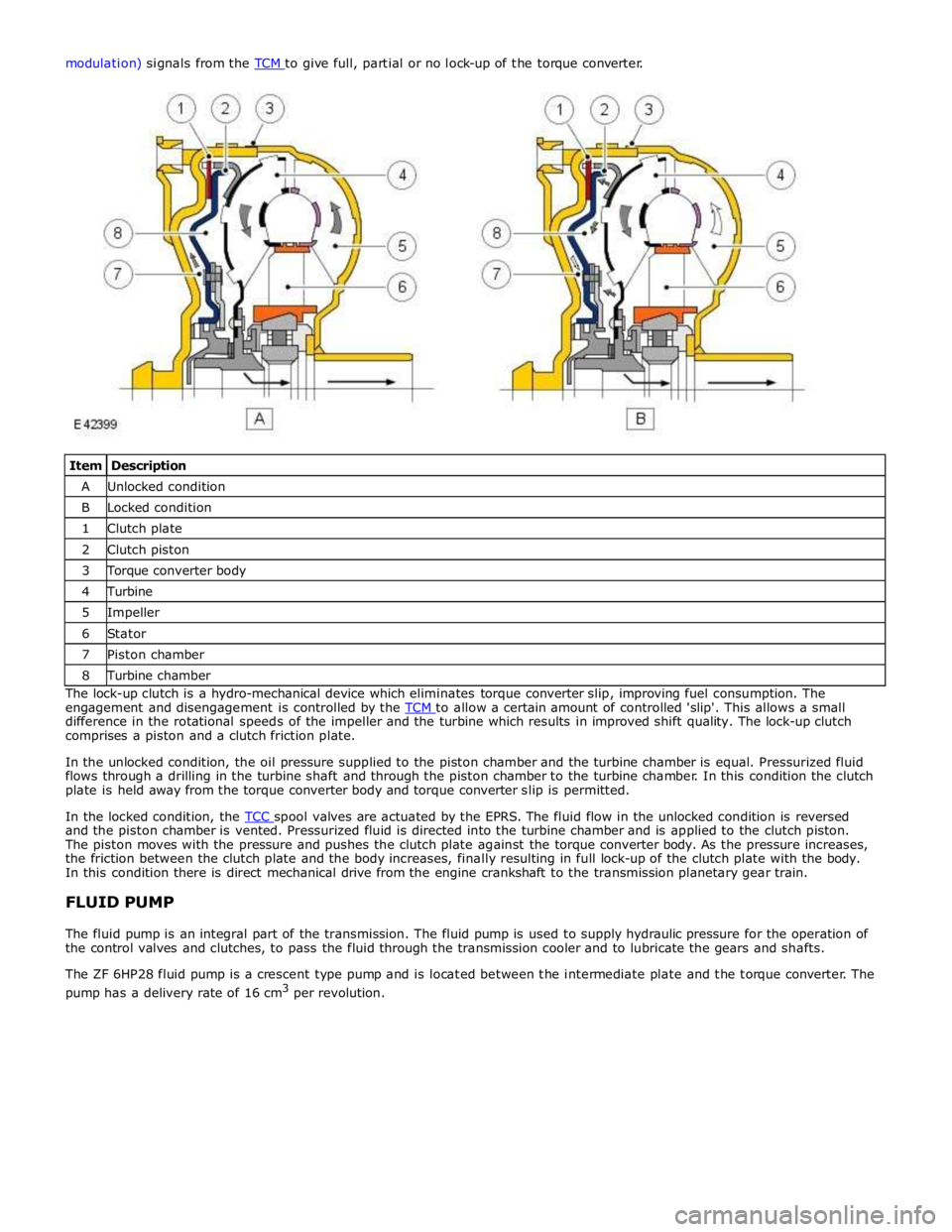
Item Description A Unlocked condition B Locked condition 1 Clutch plate 2 Clutch piston 3 Torque converter body 4 Turbine 5 Impeller 6 Stator 7 Piston chamber 8 Turbine chamber The lock-up clutch is a hydro-mechanical device which eliminates torque converter slip, improving fuel consumption. The
engagement and disengagement is controlled by the TCM to allow a certain amount of controlled 'slip'. This allows a small difference in the rotational speeds of the impeller and the turbine which results in improved shift quality. The lock-up clutch
comprises a piston and a clutch friction plate.
In the unlocked condition, the oil pressure supplied to the piston chamber and the turbine chamber is equal. Pressurized fluid
flows through a drilling in the turbine shaft and through the piston chamber to the turbine chamber. In this condition the clutch
plate is held away from the torque converter body and torque converter slip is permitted.
In the locked condition, the TCC spool valves are actuated by the EPRS. The fluid flow in the unlocked condition is reversed and the piston chamber is vented. Pressurized fluid is directed into the turbine chamber and is applied to the clutch piston.
The piston moves with the pressure and pushes the clutch plate against the torque converter body. As the pressure increases,
the friction between the clutch plate and the body increases, finally resulting in full lock-up of the clutch plate with the body.
In this condition there is direct mechanical drive from the engine crankshaft to the transmission planetary gear train.
FLUID PUMP
The fluid pump is an integral part of the transmission. The fluid pump is used to supply hydraulic pressure for the operation of
the control valves and clutches, to pass the fluid through the transmission cooler and to lubricate the gears and shafts.
The ZF 6HP28 fluid pump is a crescent type pump and is located between the intermediate plate and the torque converter. The
pump has a delivery rate of 16 cm3
per revolution.
Page 1431 of 3039
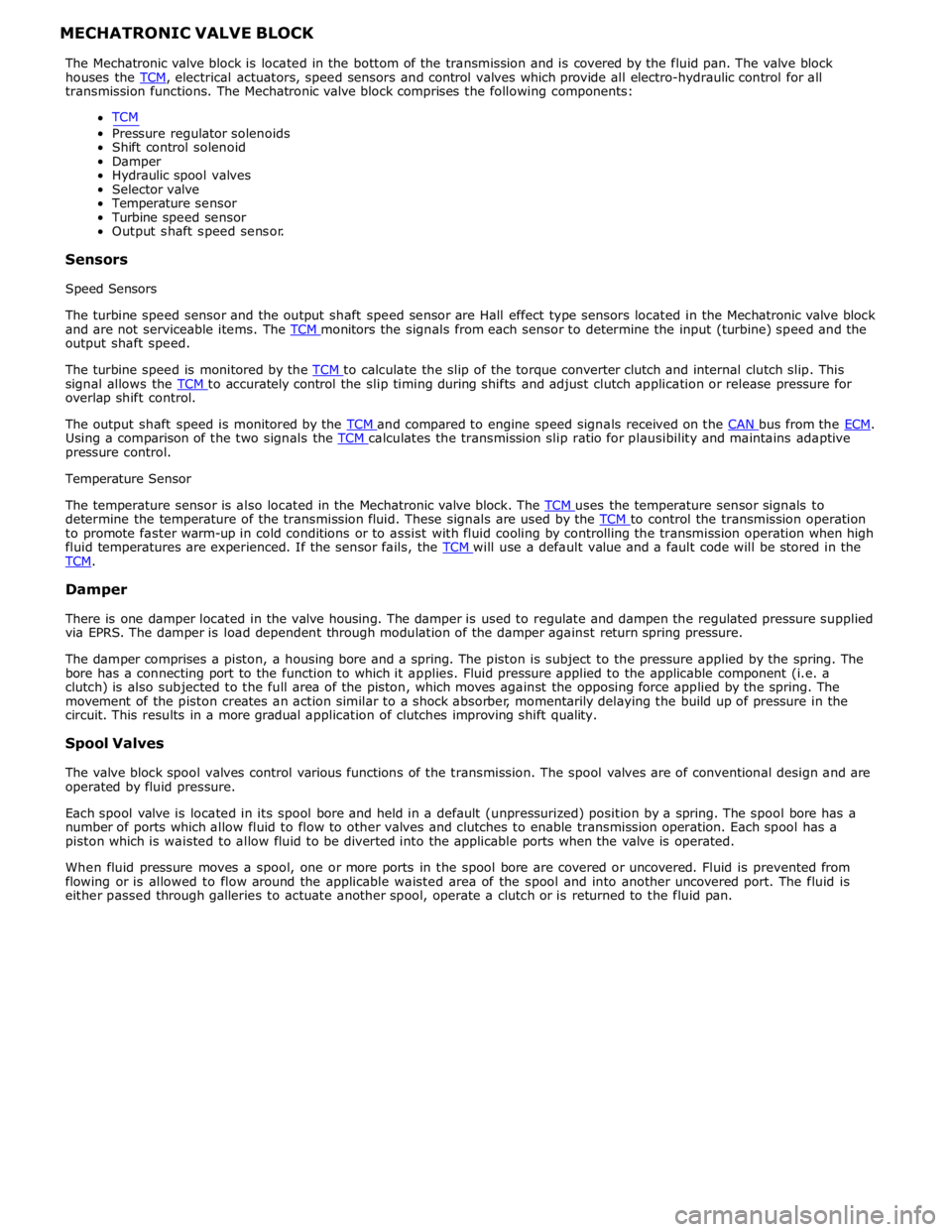
transmission functions. The Mechatronic valve block comprises the following components:
TCM
Pressure regulator solenoids
Shift control solenoid
Damper
Hydraulic spool valves
Selector valve
Temperature sensor
Turbine speed sensor
Output shaft speed sensor.
Sensors
Speed Sensors
The turbine speed sensor and the output shaft speed sensor are Hall effect type sensors located in the Mechatronic valve block
and are not serviceable items. The TCM monitors the signals from each sensor to determine the input (turbine) speed and the output shaft speed.
The turbine speed is monitored by the TCM to calculate the slip of the torque converter clutch and internal clutch slip. This signal allows the TCM to accurately control the slip timing during shifts and adjust clutch application or release pressure for overlap shift control.
The output shaft speed is monitored by the TCM and compared to engine speed signals received on the CAN bus from the ECM. Using a comparison of the two signals the TCM calculates the transmission slip ratio for plausibility and maintains adaptive pressure control.
Temperature Sensor
The temperature sensor is also located in the Mechatronic valve block. The TCM uses the temperature sensor signals to determine the temperature of the transmission fluid. These signals are used by the TCM to control the transmission operation to promote faster warm-up in cold conditions or to assist with fluid cooling by controlling the transmission operation when high
fluid temperatures are experienced. If the sensor fails, the TCM will use a default value and a fault code will be stored in the TCM.
Damper
There is one damper located in the valve housing. The damper is used to regulate and dampen the regulated pressure supplied
via EPRS. The damper is load dependent through modulation of the damper against return spring pressure.
The damper comprises a piston, a housing bore and a spring. The piston is subject to the pressure applied by the spring. The
bore has a connecting port to the function to which it applies. Fluid pressure applied to the applicable component (i.e. a
clutch) is also subjected to the full area of the piston, which moves against the opposing force applied by the spring. The
movement of the piston creates an action similar to a shock absorber, momentarily delaying the build up of pressure in the
circuit. This results in a more gradual application of clutches improving shift quality.
Spool Valves
The valve block spool valves control various functions of the transmission. The spool valves are of conventional design and are
operated by fluid pressure.
Each spool valve is located in its spool bore and held in a default (unpressurized) position by a spring. The spool bore has a
number of ports which allow fluid to flow to other valves and clutches to enable transmission operation. Each spool has a
piston which is waisted to allow fluid to be diverted into the applicable ports when the valve is operated.
When fluid pressure moves a spool, one or more ports in the spool bore are covered or uncovered. Fluid is prevented from
flowing or is allowed to flow around the applicable waisted area of the spool and into another uncovered port. The fluid is
either passed through galleries to actuate another spool, operate a clutch or is returned to the fluid pan.