key JAGUAR XJ6 1997 2.G User Guide
[x] Cancel search | Manufacturer: JAGUAR, Model Year: 1997, Model line: XJ6, Model: JAGUAR XJ6 1997 2.GPages: 227, PDF Size: 7.2 MB
Page 109 of 227
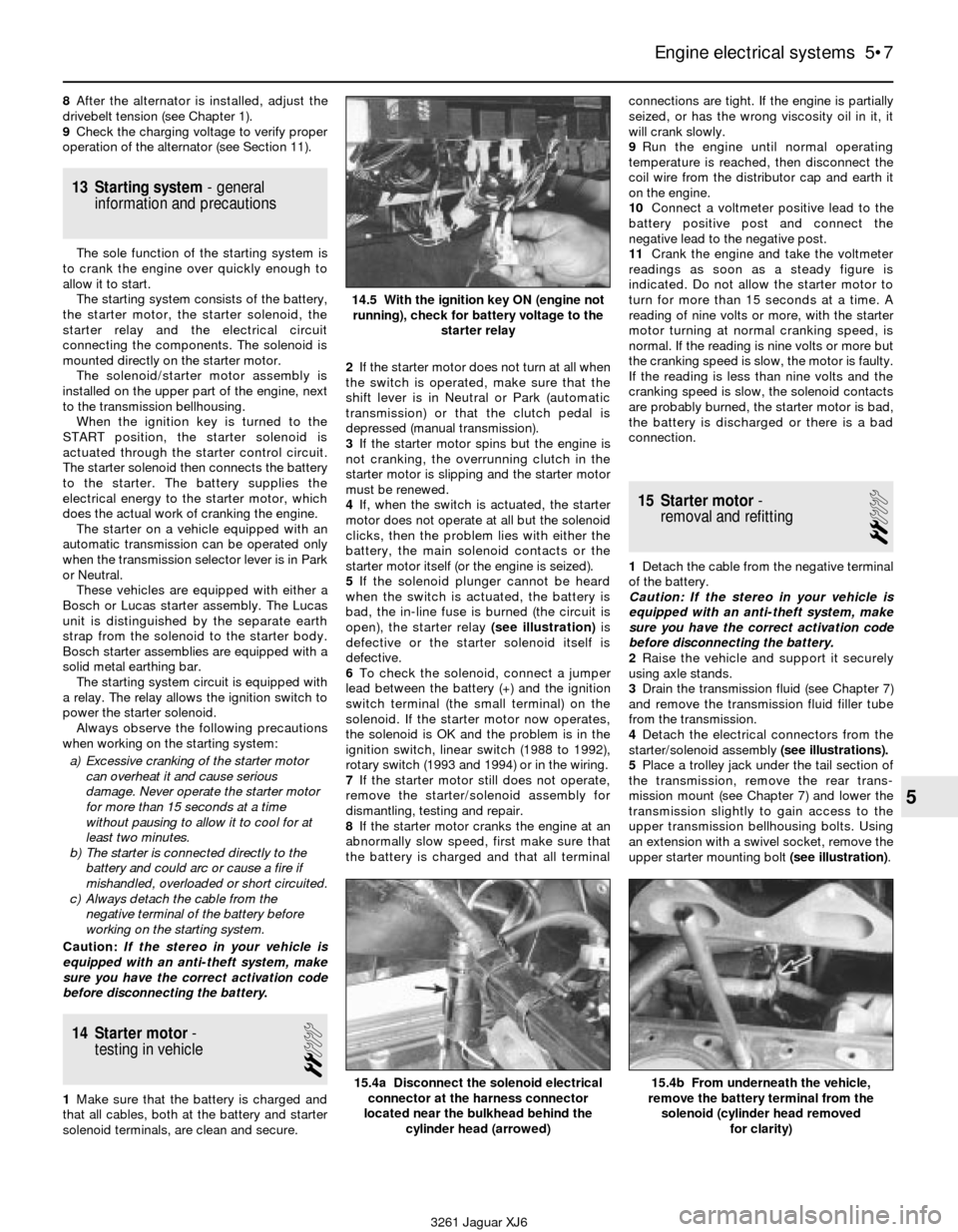
8After the alternator is installed, adjust the
drivebelt tension (see Chapter 1).
9Check the charging voltage to verify proper
operation of the alternator (see Section 11).
13 Starting system- general
information and precautions
The sole function of the starting system is
to crank the engine over quickly enough to
allow it to start.
The starting system consists of the battery,
the starter motor, the starter solenoid, the
starter relay and the electrical circuit
connecting the components. The solenoid is
mounted directly on the starter motor.
The solenoid/starter motor assembly is
installed on the upper part of the engine, next
to the transmission bellhousing.
When the ignition key is turned to the
START position, the starter solenoid is
actuated through the starter control circuit.
The starter solenoid then connects the battery
to the starter. The battery supplies the
electrical energy to the starter motor, which
does the actual work of cranking the engine.
The starter on a vehicle equipped with an
automatic transmission can be operated only
when the transmission selector lever is in Park
or Neutral.
These vehicles are equipped with either a
Bosch or Lucas starter assembly. The Lucas
unit is distinguished by the separate earth
strap from the solenoid to the starter body.
Bosch starter assemblies are equipped with a
solid metal earthing bar.
The starting system circuit is equipped with
a relay. The relay allows the ignition switch to
power the starter solenoid.
Always observe the following precautions
when working on the starting system:
a) Excessive cranking of the starter motor
can overheat it and cause serious
damage. Never operate the starter motor
for more than 15 seconds at a time
without pausing to allow it to cool for at
least two minutes.
b) The starter is connected directly to the
battery and could arc or cause a fire if
mishandled, overloaded or short circuited.
c) Always detach the cable from the
negative terminal of the battery before
working on the starting system.
Caution:If the stereo in your vehicle is
equipped with an anti-theft system, make
sure you have the correct activation code
before disconnecting the battery.
14 Starter motor-
testing in vehicle
2
1Make sure that the battery is charged and
that all cables, both at the battery and starter
solenoid terminals, are clean and secure.2If the starter motor does not turn at all when
the switch is operated, make sure that the
shift lever is in Neutral or Park (automatic
transmission) or that the clutch pedal is
depressed (manual transmission).
3If the starter motor spins but the engine is
not cranking, the overrunning clutch in the
starter motor is slipping and the starter motor
must be renewed.
4If, when the switch is actuated, the starter
motor does not operate at all but the solenoid
clicks, then the problem lies with either the
battery, the main solenoid contacts or the
starter motor itself (or the engine is seized).
5If the solenoid plunger cannot be heard
when the switch is actuated, the battery is
bad, the in-line fuse is burned (the circuit is
open), the starter relay (see illustration)is
defective or the starter solenoid itself is
defective.
6To check the solenoid, connect a jumper
lead between the battery (+) and the ignition
switch terminal (the small terminal) on the
solenoid. If the starter motor now operates,
the solenoid is OK and the problem is in the
ignition switch, linear switch (1988 to 1992),
rotary switch (1993 and 1994) or in the wiring.
7If the starter motor still does not operate,
remove the starter/solenoid assembly for
dismantling, testing and repair.
8If the starter motor cranks the engine at an
abnormally slow speed, first make sure that
the battery is charged and that all terminalconnections are tight. If the engine is partially
seized, or has the wrong viscosity oil in it, it
will crank slowly.
9Run the engine until normal operating
temperature is reached, then disconnect the
coil wire from the distributor cap and earth it
on the engine.
10Connect a voltmeter positive lead to the
battery positive post and connect the
negative lead to the negative post.
11Crank the engine and take the voltmeter
readings as soon as a steady figure is
indicated. Do not allow the starter motor to
turn for more than 15 seconds at a time. A
reading of nine volts or more, with the starter
motor turning at normal cranking speed, is
normal. If the reading is nine volts or more but
the cranking speed is slow, the motor is faulty.
If the reading is less than nine volts and the
cranking speed is slow, the solenoid contacts
are probably burned, the starter motor is bad,
the battery is discharged or there is a bad
connection.
15 Starter motor-
removal and refitting
2
1Detach the cable from the negative terminal
of the battery.
Caution: If the stereo in your vehicle is
equipped with an anti-theft system, make
sure you have the correct activation code
before disconnecting the battery.
2Raise the vehicle and support it securely
using axle stands.
3Drain the transmission fluid (see Chapter 7)
and remove the transmission fluid filler tube
from the transmission.
4Detach the electrical connectors from the
starter/solenoid assembly (see illustrations).
5Place a trolley jack under the tail section of
the transmission, remove the rear trans-
mission mount (see Chapter 7) and lower the
transmission slightly to gain access to the
upper transmission bellhousing bolts. Using
an extension with a swivel socket, remove the
upper starter mounting bolt (see illustration).
Engine electrical systems 5•7
5
14.5 With the ignition key ON (engine not
running), check for battery voltage to the
starter relay
15.4a Disconnect the solenoid electrical
connector at the harness connector
located near the bulkhead behind the
cylinder head (arrowed)15.4b From underneath the vehicle,
remove the battery terminal from the
solenoid (cylinder head removed
for clarity)
3261 Jaguar XJ6
Page 112 of 227
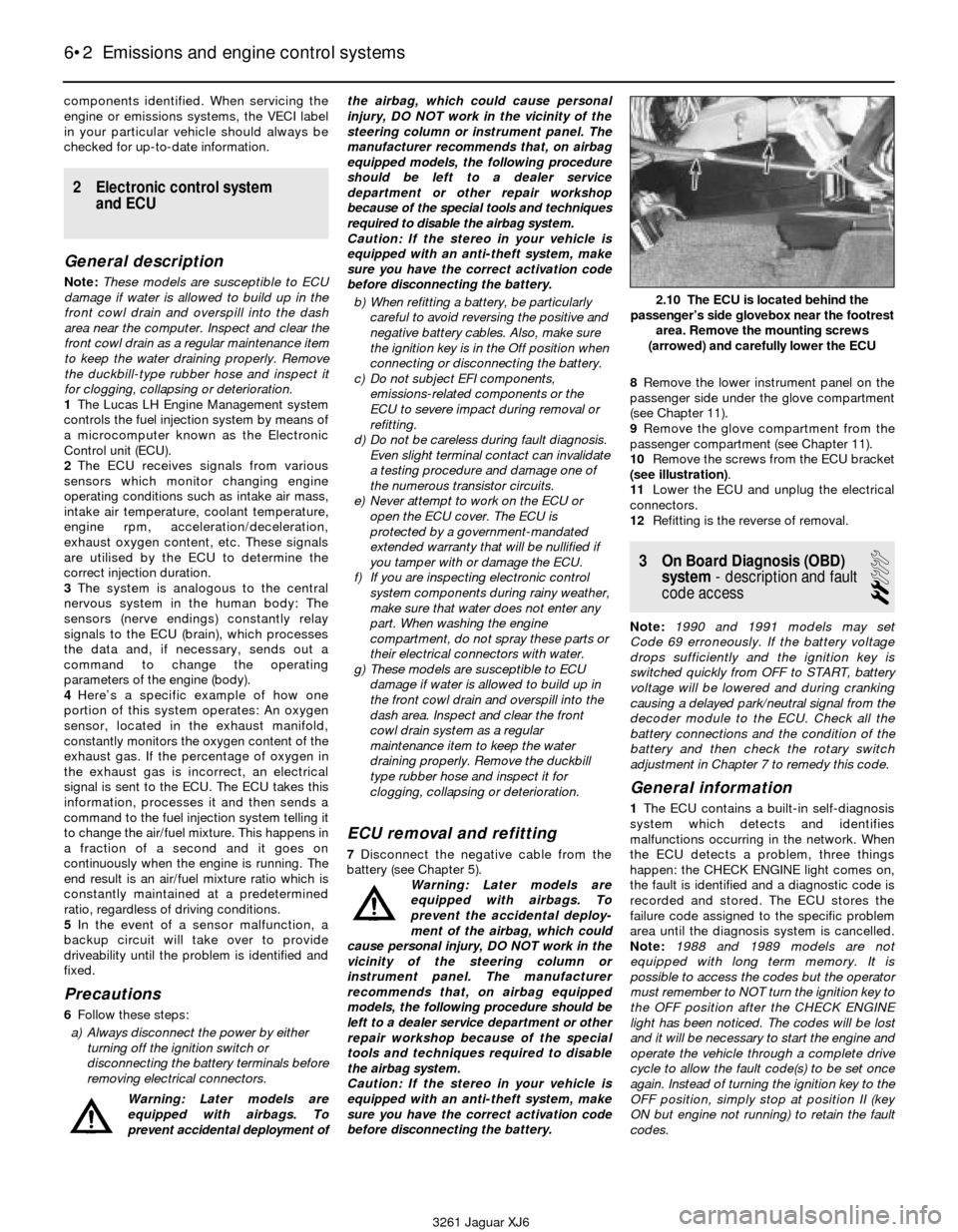
components identified. When servicing the
engine or emissions systems, the VECI label
in your particular vehicle should always be
checked for up-to-date information.
2 Electronic control system
and ECU
General description
Note: These models are susceptible to ECU
damage if water is allowed to build up in the
front cowl drain and overspill into the dash
area near the computer. Inspect and clear the
front cowl drain as a regular maintenance item
to keep the water draining properly. Remove
the duckbill-type rubber hose and inspect it
for clogging, collapsing or deterioration.
1The Lucas LH Engine Management system
controls the fuel injection system by means of
a microcomputer known as the Electronic
Control unit (ECU).
2The ECU receives signals from various
sensors which monitor changing engine
operating conditions such as intake air mass,
intake air temperature, coolant temperature,
engine rpm, acceleration/deceleration,
exhaust oxygen content, etc. These signals
are utilised by the ECU to determine the
correct injection duration.
3The system is analogous to the central
nervous system in the human body: The
sensors (nerve endings) constantly relay
signals to the ECU (brain), which processes
the data and, if necessary, sends out a
command to change the operating
parameters of the engine (body).
4Here’s a specific example of how one
portion of this system operates: An oxygen
sensor, located in the exhaust manifold,
constantly monitors the oxygen content of the
exhaust gas. If the percentage of oxygen in
the exhaust gas is incorrect, an electrical
signal is sent to the ECU. The ECU takes this
information, processes it and then sends a
command to the fuel injection system telling it
to change the air/fuel mixture. This happens in
a fraction of a second and it goes on
continuously when the engine is running. The
end result is an air/fuel mixture ratio which is
constantly maintained at a predetermined
ratio, regardless of driving conditions.
5In the event of a sensor malfunction, a
backup circuit will take over to provide
driveability until the problem is identified and
fixed.
Precautions
6Follow these steps:
a) Always disconnect the power by either
turning off the ignition switch or
disconnecting the battery terminals before
removing electrical connectors.
Warning: Later models are
equipped with airbags. To
prevent accidental deployment ofthe airbag, which could cause personal
injury, DO NOT work in the vicinity of the
steering column or instrument panel. The
manufacturer recommends that, on airbag
equipped models, the following procedure
should be left to a dealer service
department or other repair workshop
because of the special tools and techniques
required to disable the airbag system.
Caution: If the stereo in your vehicle is
equipped with an anti-theft system, make
sure you have the correct activation code
before disconnecting the battery.
b) When refitting a battery, be particularly
careful to avoid reversing the positive and
negative battery cables. Also, make sure
the ignition key is in the Off position when
connecting or disconnecting the battery.
c) Do not subject EFI components,
emissions-related components or the
ECU to severe impact during removal or
refitting.
d) Do not be careless during fault diagnosis.
Even slight terminal contact can invalidate
a testing procedure and damage one of
the numerous transistor circuits.
e) Never attempt to work on the ECU or
open the ECU cover. The ECU is
protected by a government-mandated
extended warranty that will be nullified if
you tamper with or damage the ECU.
f) If you are inspecting electronic control
system components during rainy weather,
make sure that water does not enter any
part. When washing the engine
compartment, do not spray these parts or
their electrical connectors with water.
g) These models are susceptible to ECU
damage if water is allowed to build up in
the front cowl drain and overspill into the
dash area. Inspect and clear the front
cowl drain system as a regular
maintenance item to keep the water
draining properly. Remove the duckbill
type rubber hose and inspect it for
clogging, collapsing or deterioration.
ECU removal and refitting
7Disconnect the negative cable from the
battery (see Chapter 5).
Warning: Later models are
equipped with airbags. To
prevent the accidental deploy-
ment of the airbag, which could
cause personal injury, DO NOT work in the
vicinity of the steering column or
instrument panel. The manufacturer
recommends that, on airbag equipped
models, the following procedure should be
left to a dealer service department or other
repair workshop because of the special
tools and techniques required to disable
the airbag system.
Caution: If the stereo in your vehicle is
equipped with an anti-theft system, make
sure you have the correct activation code
before disconnecting the battery.8Remove the lower instrument panel on the
passenger side under the glove compartment
(see Chapter 11).
9Remove the glove compartment from the
passenger compartment (see Chapter 11).
10Remove the screws from the ECU bracket
(see illustration).
11Lower the ECU and unplug the electrical
connectors.
12Refitting is the reverse of removal.
3 On Board Diagnosis (OBD)
system- description and fault
code access
2
Note: 1990 and 1991 models may set
Code 69 erroneously. If the battery voltage
drops sufficiently and the ignition key is
switched quickly from OFF to START, battery
voltage will be lowered and during cranking
causing a delayed park/neutral signal from the
decoder module to the ECU. Check all the
battery connections and the condition of the
battery and then check the rotary switch
adjustment in Chapter 7 to remedy this code.
General information
1The ECU contains a built-in self-diagnosis
system which detects and identifies
malfunctions occurring in the network. When
the ECU detects a problem, three things
happen: the CHECK ENGINE light comes on,
the fault is identified and a diagnostic code is
recorded and stored. The ECU stores the
failure code assigned to the specific problem
area until the diagnosis system is cancelled.
Note: 1988 and 1989 models are not
equipped with long term memory. It is
possible to access the codes but the operator
must remember to NOT turn the ignition key to
the OFF position after the CHECK ENGINE
light has been noticed. The codes will be lost
and it will be necessary to start the engine and
operate the vehicle through a complete drive
cycle to allow the fault code(s) to be set once
again. Instead of turning the ignition key to the
OFF position, simply stop at position II (key
ON but engine not running) to retain the fault
codes.
6•2 Emissions and engine control systems
3261 Jaguar XJ6
2.10 The ECU is located behind the
passenger’s side glovebox near the footrest
area. Remove the mounting screws
(arrowed) and carefully lower the ECU
Page 113 of 227
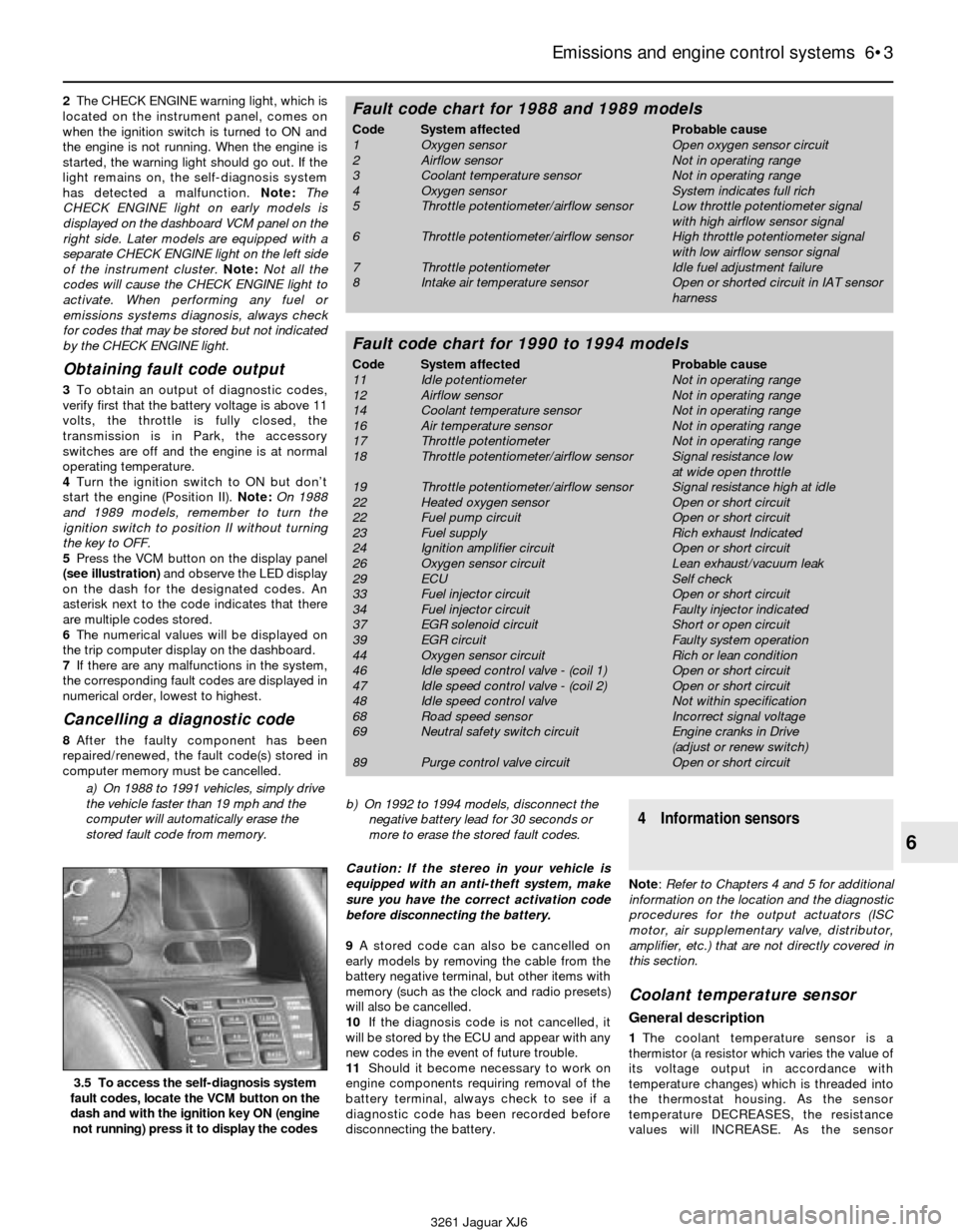
2The CHECK ENGINE warning light, which is
located on the instrument panel, comes on
when the ignition switch is turned to ON and
the engine is not running. When the engine is
started, the warning light should go out. If the
light remains on, the self-diagnosis system
has detected a malfunction. Note: The
CHECK ENGINE light on early models is
displayed on the dashboard VCM panel on the
right side. Later models are equipped with a
separate CHECK ENGINE light on the left side
of the instrument cluster.Note:Not all the
codes will cause the CHECK ENGINE light to
activate. When performing any fuel or
emissions systems diagnosis, always check
for codes that may be stored but not indicated
by the CHECK ENGINE light.
Obtaining fault code output
3To obtain an output of diagnostic codes,
verify first that the battery voltage is above 11
volts, the throttle is fully closed, the
transmission is in Park, the accessory
switches are off and the engine is at normal
operating temperature.
4Turn the ignition switch to ON but don’t
start the engine (Position II). Note:On 1988
and 1989 models, remember to turn the
ignition switch to position II without turning
the key to OFF.
5Press the VCM button on the display panel
(see illustration)and observe the LED display
on the dash for the designated codes. An
asterisk next to the code indicates that there
are multiple codes stored.
6The numerical values will be displayed on
the trip computer display on the dashboard.
7If there are any malfunctions in the system,
the corresponding fault codes are displayed in
numerical order, lowest to highest.
Cancelling a diagnostic code
8After the faulty component has been
repaired/renewed, the fault code(s) stored in
computer memory must be cancelled.
a) On 1988 to 1991 vehicles, simply drive
the vehicle faster than 19 mph and the
computer will automatically erase the
stored fault code from memory.b) On 1992 to 1994 models, disconnect the
negative battery lead for 30 seconds or
more to erase the stored fault codes.
Caution: If the stereo in your vehicle is
equipped with an anti-theft system, make
sure you have the correct activation code
before disconnecting the battery.
9A stored code can also be cancelled on
early models by removing the cable from the
battery negative terminal, but other items with
memory (such as the clock and radio presets)
will also be cancelled.
10If the diagnosis code is not cancelled, it
will be stored by the ECU and appear with any
new codes in the event of future trouble.
11Should it become necessary to work on
engine components requiring removal of the
battery terminal, always check to see if a
diagnostic code has been recorded before
disconnecting the battery.
4 Information sensors
Note: Refer to Chapters 4 and 5 for additional
information on the location and the diagnostic
procedures for the output actuators (ISC
motor, air supplementary valve, distributor,
amplifier, etc.) that are not directly covered in
this section.
Coolant temperature sensor
General description
1The coolant temperature sensor is a
thermistor (a resistor which varies the value of
its voltage output in accordance with
temperature changes) which is threaded into
the thermostat housing. As the sensor
temperature DECREASES, the resistance
values will INCREASE. As the sensor
Emissions and engine control systems 6•3
6
3.5 To access the self-diagnosis system
fault codes, locate the VCM button on the
dash and with the ignition key ON (engine
not running) press it to display the codes
3261 Jaguar XJ6
Fault code chart for 1988 and 1989 models
Code System affected Probable cause
1 Oxygen sensor Open oxygen sensor circuit
2 Airflow sensor Not in operating range
3 Coolant temperature sensor Not in operating range
4 Oxygen sensor System indicates full rich
5 Throttle potentiometer/airflow sensor Low throttle potentiometer signal
with high airflow sensor signal
6 Throttle potentiometer/airflow sensor High throttle potentiometer signal
with low airflow sensor signal
7 Throttle potentiometer Idle fuel adjustment failure
8 Intake air temperature sensor Open or shorted circuit in IAT sensor
harness
Fault code chart for 1990 to 1994 models
Code System affected Probable cause
11 Idle potentiometer Not in operating range
12 Airflow sensor Not in operating range
14 Coolant temperature sensor Not in operating range
16 Air temperature sensor Not in operating range
17 Throttle potentiometer Not in operating range
18 Throttle potentiometer/airflow sensor Signal resistance low
at wide open throttle
19 Throttle potentiometer/airflow sensor Signal resistance high at idle
22 Heated oxygen sensor Open or short circuit
22 Fuel pump circuit Open or short circuit
23 Fuel supply Rich exhaust Indicated
24 Ignition amplifier circuit Open or short circuit
26 Oxygen sensor circuit Lean exhaust/vacuum leak
29 ECU Self check
33 Fuel injector circuit Open or short circuit
34 Fuel injector circuit Faulty injector indicated
37 EGR solenoid circuit Short or open circuit
39 EGR circuit Faulty system operation
44 Oxygen sensor circuit Rich or lean condition
46 Idle speed control valve - (coil 1) Open or short circuit
47 Idle speed control valve - (coil 2) Open or short circuit
48 Idle speed control valve Not within specification
68 Road speed sensor Incorrect signal voltage
69 Neutral safety switch circuit Engine cranks in Drive
(adjust or renew switch)
89 Purge control valve circuit Open or short circuit
Page 114 of 227
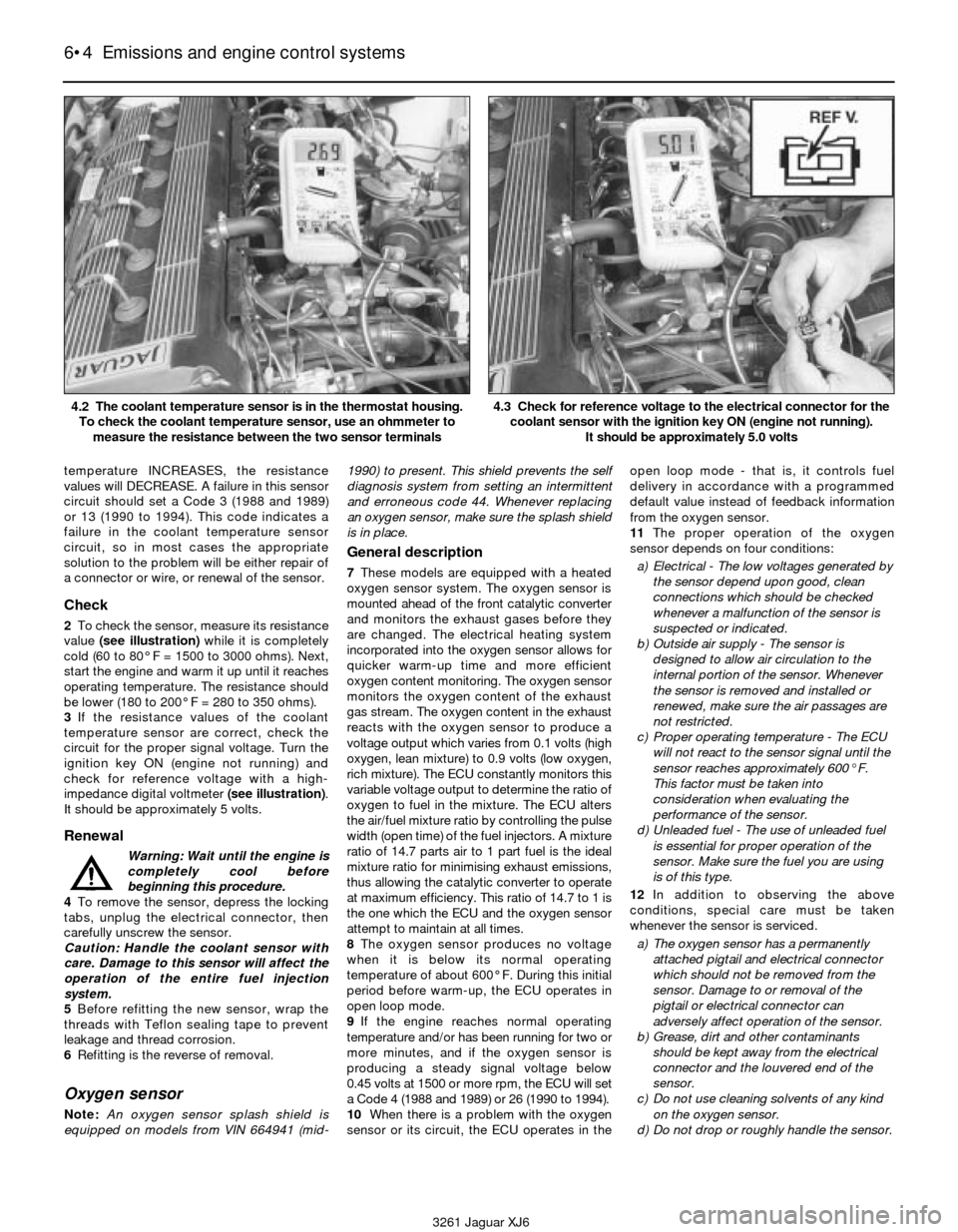
temperature INCREASES, the resistance
values will DECREASE. A failure in this sensor
circuit should set a Code 3 (1988 and 1989)
or 13 (1990 to 1994). This code indicates a
failure in the coolant temperature sensor
circuit, so in most cases the appropriate
solution to the problem will be either repair of
a connector or wire, or renewal of the sensor.
Check
2To check the sensor, measure its resistance
value (see illustration)while it is completely
cold (60 to 80° F = 1500 to 3000 ohms). Next,
start the engine and warm it up until it reaches
operating temperature. The resistance should
be lower (180 to 200° F = 280 to 350 ohms).
3If the resistance values of the coolant
temperature sensor are correct, check the
circuit for the proper signal voltage. Turn the
ignition key ON (engine not running) and
check for reference voltage with a high-
impedance digital voltmeter (see illustration).
It should be approximately 5 volts.
Renewal
Warning: Wait until the engine is
completely cool before
beginning this procedure.
4To remove the sensor, depress the locking
tabs, unplug the electrical connector, then
carefully unscrew the sensor.
Caution: Handle the coolant sensor with
care. Damage to this sensor will affect the
operation of the entire fuel injection
system.
5Before refitting the new sensor, wrap the
threads with Teflon sealing tape to prevent
leakage and thread corrosion.
6Refitting is the reverse of removal.
Oxygen sensor
Note:An oxygen sensor splash shield is
equipped on models from VIN 664941 (mid-1990) to present. This shield prevents the self
diagnosis system from setting an intermittent
and erroneous code 44. Whenever replacing
an oxygen sensor, make sure the splash shield
is in place.
General description
7These models are equipped with a heated
oxygen sensor system. The oxygen sensor is
mounted ahead of the front catalytic converter
and monitors the exhaust gases before they
are changed. The electrical heating system
incorporated into the oxygen sensor allows for
quicker warm-up time and more efficient
oxygen content monitoring. The oxygen sensor
monitors the oxygen content of the exhaust
gas stream. The oxygen content in the exhaust
reacts with the oxygen sensor to produce a
voltage output which varies from 0.1 volts (high
oxygen, lean mixture) to 0.9 volts (low oxygen,
rich mixture). The ECU constantly monitors this
variable voltage output to determine the ratio of
oxygen to fuel in the mixture. The ECU alters
the air/fuel mixture ratio by controlling the pulse
width (open time) of the fuel injectors. A mixture
ratio of 14.7 parts air to 1 part fuel is the ideal
mixture ratio for minimising exhaust emissions,
thus allowing the catalytic converter to operate
at maximum efficiency. This ratio of 14.7 to 1 is
the one which the ECU and the oxygen sensor
attempt to maintain at all times.
8The oxygen sensor produces no voltage
when it is below its normal operating
temperature of about 600° F. During this initial
period before warm-up, the ECU operates in
open loop mode.
9If the engine reaches normal operating
temperature and/or has been running for two or
more minutes, and if the oxygen sensor is
producing a steady signal voltage below
0.45 volts at 1500 or more rpm, the ECU will set
a Code 4 (1988 and 1989) or 26 (1990 to 1994).
10When there is a problem with the oxygen
sensor or its circuit, the ECU operates in theopen loop mode - that is, it controls fuel
delivery in accordance with a programmed
default value instead of feedback information
from the oxygen sensor.
11The proper operation of the oxygen
sensor depends on four conditions:
a) Electrical - The low voltages generated by
the sensor depend upon good, clean
connections which should be checked
whenever a malfunction of the sensor is
suspected or indicated.
b) Outside air supply - The sensor is
designed to allow air circulation to the
internal portion of the sensor. Whenever
the sensor is removed and installed or
renewed, make sure the air passages are
not restricted.
c) Proper operating temperature - The ECU
will not react to the sensor signal until the
sensor reaches approximately 600° F.
This factor must be taken into
consideration when evaluating the
performance of the sensor.
d) Unleaded fuel - The use of unleaded fuel
is essential for proper operation of the
sensor. Make sure the fuel you are using
is of this type.
12In addition to observing the above
conditions, special care must be taken
whenever the sensor is serviced.
a) The oxygen sensor has a permanently
attached pigtail and electrical connector
which should not be removed from the
sensor. Damage to or removal of the
pigtail or electrical connector can
adversely affect operation of the sensor.
b) Grease, dirt and other contaminants
should be kept away from the electrical
connector and the louvered end of the
sensor.
c) Do not use cleaning solvents of any kind
on the oxygen sensor.
d) Do not drop or roughly handle the sensor.
6•4 Emissions and engine control systems
3261 Jaguar XJ6 4.2 The coolant temperature sensor is in the thermostat housing.
To check the coolant temperature sensor, use an ohmmeter to
measure the resistance between the two sensor terminals
4.3 Check for reference voltage to the electrical connector for the
coolant sensor with the ignition key ON (engine not running).
It should be approximately 5.0 volts
Page 115 of 227
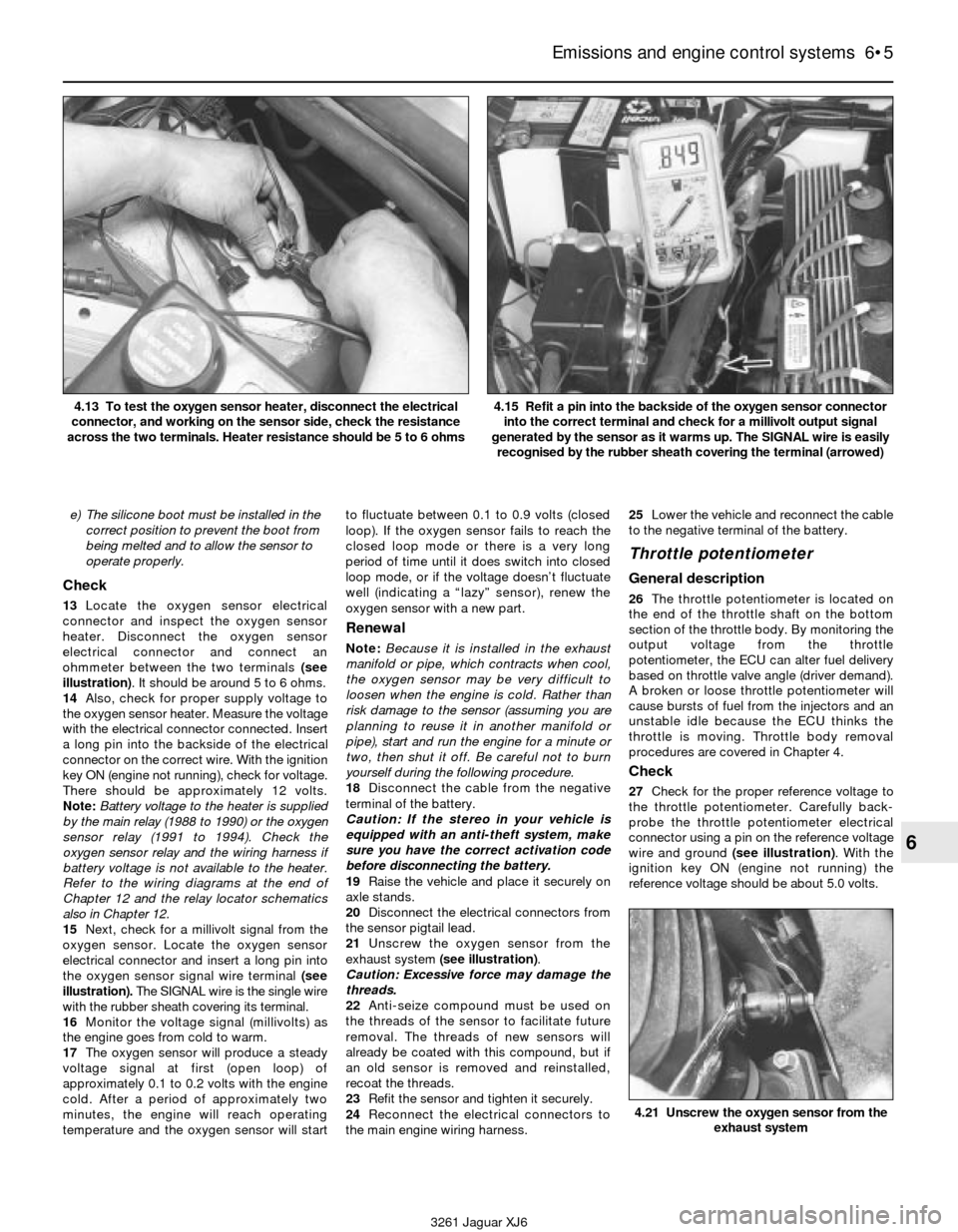
e) The silicone boot must be installed in the
correct position to prevent the boot from
being melted and to allow the sensor to
operate properly.
Check
13Locate the oxygen sensor electrical
connector and inspect the oxygen sensor
heater. Disconnect the oxygen sensor
electrical connector and connect an
ohmmeter between the two terminals (see
illustration). It should be around 5 to 6 ohms.
14Also, check for proper supply voltage to
the oxygen sensor heater. Measure the voltage
with the electrical connector connected. Insert
a long pin into the backside of the electrical
connector on the correct wire. With the ignition
key ON (engine not running), check for voltage.
There should be approximately 12 volts.
Note:Battery voltage to the heater is supplied
by the main relay (1988 to 1990) or the oxygen
sensor relay (1991 to 1994). Check the
oxygen sensor relay and the wiring harness if
battery voltage is not available to the heater.
Refer to the wiring diagrams at the end of
Chapter 12 and the relay locator schematics
also in Chapter 12.
15Next, check for a millivolt signal from the
oxygen sensor. Locate the oxygen sensor
electrical connector and insert a long pin into
the oxygen sensor signal wire terminal (see
illustration). The SIGNAL wire is the single wire
with the rubber sheath covering its terminal.
16Monitor the voltage signal (millivolts) as
the engine goes from cold to warm.
17The oxygen sensor will produce a steady
voltage signal at first (open loop) of
approximately 0.1 to 0.2 volts with the engine
cold. After a period of approximately two
minutes, the engine will reach operating
temperature and the oxygen sensor will startto fluctuate between 0.1 to 0.9 volts (closed
loop). If the oxygen sensor fails to reach the
closed loop mode or there is a very long
period of time until it does switch into closed
loop mode, or if the voltage doesn’t fluctuate
well (indicating a “lazy” sensor), renew the
oxygen sensor with a new part.
Renewal
Note:Because it is installed in the exhaust
manifold or pipe, which contracts when cool,
the oxygen sensor may be very difficult to
loosen when the engine is cold. Rather than
risk damage to the sensor (assuming you are
planning to reuse it in another manifold or
pipe), start and run the engine for a minute or
two, then shut it off. Be careful not to burn
yourself during the following procedure.
18Disconnect the cable from the negative
terminal of the battery.
Caution: If the stereo in your vehicle is
equipped with an anti-theft system, make
sure you have the correct activation code
before disconnecting the battery.
19Raise the vehicle and place it securely on
axle stands.
20Disconnect the electrical connectors from
the sensor pigtail lead.
21Unscrew the oxygen sensor from the
exhaust system (see illustration).
Caution: Excessive force may damage the
threads.
22Anti-seize compound must be used on
the threads of the sensor to facilitate future
removal. The threads of new sensors will
already be coated with this compound, but if
an old sensor is removed and reinstalled,
recoat the threads.
23Refit the sensor and tighten it securely.
24Reconnect the electrical connectors to
the main engine wiring harness.25Lower the vehicle and reconnect the cable
to the negative terminal of the battery.
Throttle potentiometer
General description
26The throttle potentiometer is located on
the end of the throttle shaft on the bottom
section of the throttle body. By monitoring the
output voltage from the throttle
potentiometer, the ECU can alter fuel delivery
based on throttle valve angle (driver demand).
A broken or loose throttle potentiometer will
cause bursts of fuel from the injectors and an
unstable idle because the ECU thinks the
throttle is moving. Throttle body removal
procedures are covered in Chapter 4.
Check
27Check for the proper reference voltage to
the throttle potentiometer. Carefully back-
probe the throttle potentiometer electrical
connector using a pin on the reference voltage
wire and ground (see illustration). With the
ignition key ON (engine not running) the
reference voltage should be about 5.0 volts.
Emissions and engine control systems 6•5
6
4.21 Unscrew the oxygen sensor from the
exhaust system
3261 Jaguar XJ6 4.13 To test the oxygen sensor heater, disconnect the electrical
connector, and working on the sensor side, check the resistance
across the two terminals. Heater resistance should be 5 to 6 ohms
4.15 Refit a pin into the backside of the oxygen sensor connector
into the correct terminal and check for a millivolt output signal
generated by the sensor as it warms up. The SIGNAL wire is easily
recognised by the rubber sheath covering the terminal (arrowed)
Page 116 of 227
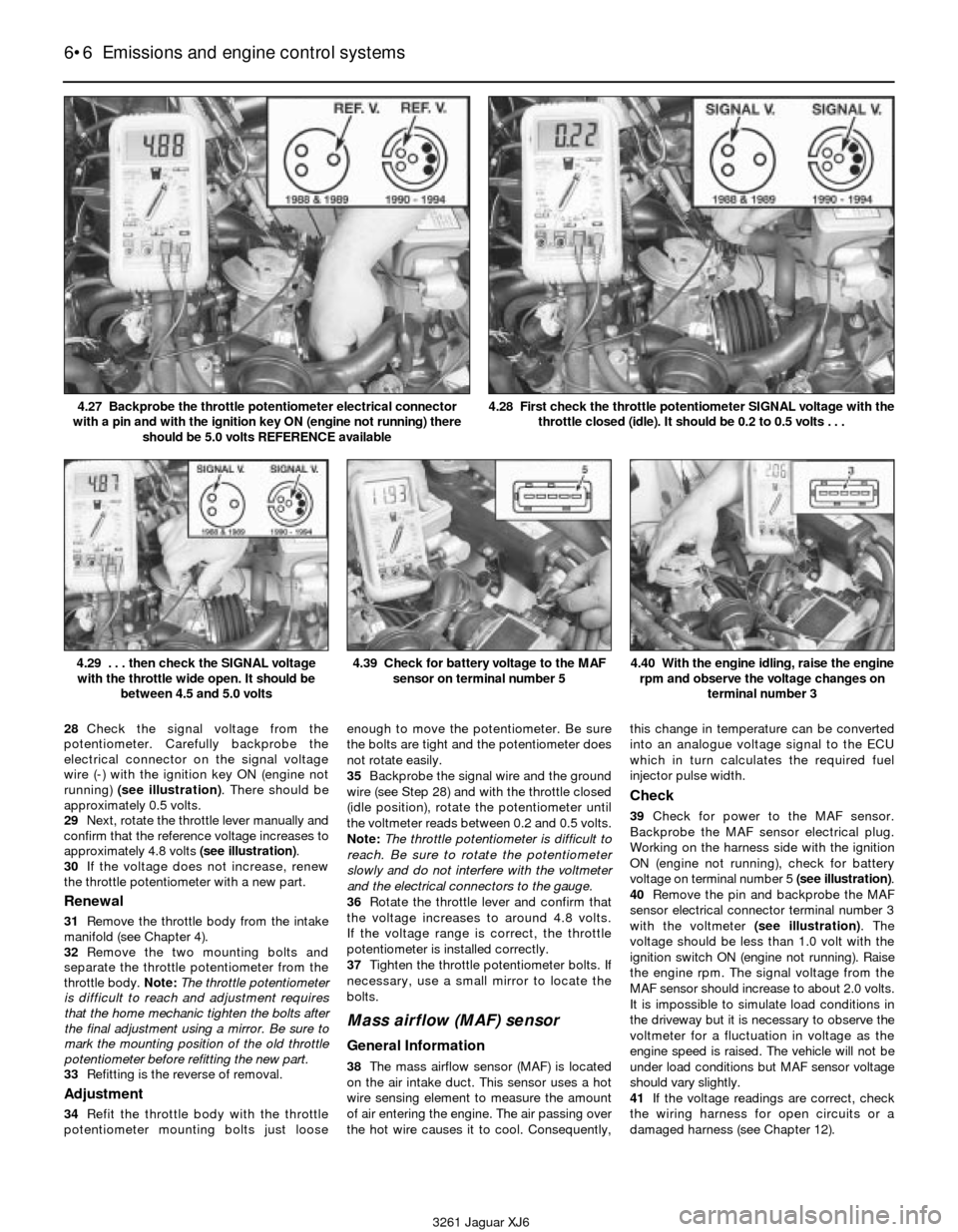
28Check the signal voltage from the
potentiometer. Carefully backprobe the
electrical connector on the signal voltage
wire (-) with the ignition key ON (engine not
running) (see illustration). There should be
approximately 0.5 volts.
29Next, rotate the throttle lever manually and
confirm that the reference voltage increases to
approximately 4.8 volts (see illustration).
30If the voltage does not increase, renew
the throttle potentiometer with a new part.
Renewal
31Remove the throttle body from the intake
manifold (see Chapter 4).
32Remove the two mounting bolts and
separate the throttle potentiometer from the
throttle body. Note:The throttle potentiometer
is difficult to reach and adjustment requires
that the home mechanic tighten the bolts after
the final adjustment using a mirror. Be sure to
mark the mounting position of the old throttle
potentiometer before refitting the new part.
33Refitting is the reverse of removal.
Adjustment
34Refit the throttle body with the throttle
potentiometer mounting bolts just looseenough to move the potentiometer. Be sure
the bolts are tight and the potentiometer does
not rotate easily.
35Backprobe the signal wire and the ground
wire (see Step 28) and with the throttle closed
(idle position), rotate the potentiometer until
the voltmeter reads between 0.2 and 0.5 volts.
Note:The throttle potentiometer is difficult to
reach. Be sure to rotate the potentiometer
slowly and do not interfere with the voltmeter
and the electrical connectors to the gauge.
36Rotate the throttle lever and confirm that
the voltage increases to around 4.8 volts.
If the voltage range is correct, the throttle
potentiometer is installed correctly.
37Tighten the throttle potentiometer bolts. If
necessary, use a small mirror to locate the
bolts.
Mass airflow (MAF) sensor
General Information
38The mass airflow sensor (MAF) is located
on the air intake duct. This sensor uses a hot
wire sensing element to measure the amount
of air entering the engine. The air passing over
the hot wire causes it to cool. Consequently,this change in temperature can be converted
into an analogue voltage signal to the ECU
which in turn calculates the required fuel
injector pulse width.
Check
39Check for power to the MAF sensor.
Backprobe the MAF sensor electrical plug.
Working on the harness side with the ignition
ON (engine not running), check for battery
voltage on terminal number 5 (see illustration).
40Remove the pin and backprobe the MAF
sensor electrical connector terminal number 3
with the voltmeter (see illustration). The
voltage should be less than 1.0 volt with the
ignition switch ON (engine not running). Raise
the engine rpm. The signal voltage from the
MAF sensor should increase to about 2.0 volts.
It is impossible to simulate load conditions in
the driveway but it is necessary to observe the
voltmeter for a fluctuation in voltage as the
engine speed is raised. The vehicle will not be
under load conditions but MAF sensor voltage
should vary slightly.
41If the voltage readings are correct, check
the wiring harness for open circuits or a
damaged harness (see Chapter 12).
6•6 Emissions and engine control systems
4.29 . . . then check the SIGNAL voltage
with the throttle wide open. It should be
between 4.5 and 5.0 volts4.39 Check for battery voltage to the MAF
sensor on terminal number 54.40 With the engine idling, raise the engine
rpm and observe the voltage changes on
terminal number 3
3261 Jaguar XJ6 4.27 Backprobe the throttle potentiometer electrical connector
with a pin and with the ignition key ON (engine not running) there
should be 5.0 volts REFERENCE available
4.28 First check the throttle potentiometer SIGNAL voltage with the
throttle closed (idle). It should be 0.2 to 0.5 volts . . .
Page 117 of 227
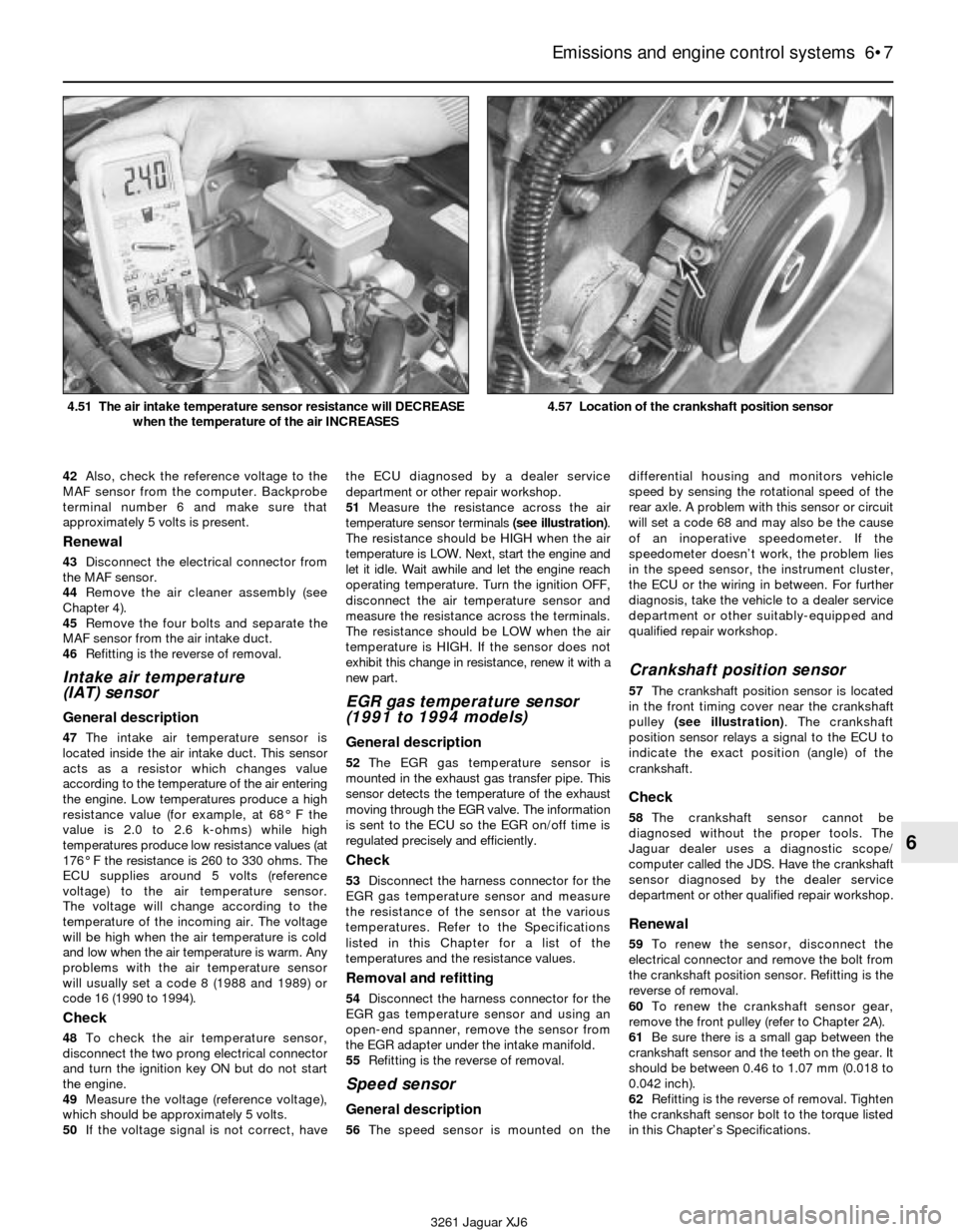
42Also, check the reference voltage to the
MAF sensor from the computer. Backprobe
terminal number 6 and make sure that
approximately 5 volts is present.
Renewal
43Disconnect the electrical connector from
the MAF sensor.
44Remove the air cleaner assembly (see
Chapter 4).
45Remove the four bolts and separate the
MAF sensor from the air intake duct.
46Refitting is the reverse of removal.
Intake air temperature
(IAT) sensor
General description
47The intake air temperature sensor is
located inside the air intake duct. This sensor
acts as a resistor which changes value
according to the temperature of the air entering
the engine. Low temperatures produce a high
resistance value (for example, at 68° F the
value is 2.0 to 2.6 k-ohms) while high
temperatures produce low resistance values (at
176° F the resistance is 260 to 330 ohms. The
ECU supplies around 5 volts (reference
voltage) to the air temperature sensor.
The voltage will change according to the
temperature of the incoming air. The voltage
will be high when the air temperature is cold
and low when the air temperature is warm. Any
problems with the air temperature sensor
will usually set a code 8 (1988 and 1989) or
code 16 (1990 to 1994).
Check
48To check the air temperature sensor,
disconnect the two prong electrical connector
and turn the ignition key ON but do not start
the engine.
49Measure the voltage (reference voltage),
which should be approximately 5 volts.
50If the voltage signal is not correct, havethe ECU diagnosed by a dealer service
department or other repair workshop.
51Measure the resistance across the air
temperature sensor terminals (see illustration).
The resistance should be HIGH when the air
temperature is LOW. Next, start the engine and
let it idle. Wait awhile and let the engine reach
operating temperature. Turn the ignition OFF,
disconnect the air temperature sensor and
measure the resistance across the terminals.
The resistance should be LOW when the air
temperature is HIGH. If the sensor does not
exhibit this change in resistance, renew it with a
new part.
EGR gas temperature sensor
(1991 to 1994 models)
General description
52The EGR gas temperature sensor is
mounted in the exhaust gas transfer pipe. This
sensor detects the temperature of the exhaust
moving through the EGR valve. The information
is sent to the ECU so the EGR on/off time is
regulated precisely and efficiently.
Check
53Disconnect the harness connector for the
EGR gas temperature sensor and measure
the resistance of the sensor at the various
temperatures. Refer to the Specifications
listed in this Chapter for a list of the
temperatures and the resistance values.
Removal and refitting
54Disconnect the harness connector for the
EGR gas temperature sensor and using an
open-end spanner, remove the sensor from
the EGR adapter under the intake manifold.
55Refitting is the reverse of removal.
Speed sensor
General description
56The speed sensor is mounted on thedifferential housing and monitors vehicle
speed by sensing the rotational speed of the
rear axle. A problem with this sensor or circuit
will set a code 68 and may also be the cause
of an inoperative speedometer. If the
speedometer doesn’t work, the problem lies
in the speed sensor, the instrument cluster,
the ECU or the wiring in between. For further
diagnosis, take the vehicle to a dealer service
department or other suitably-equipped and
qualified repair workshop.
Crankshaft position sensor
57The crankshaft position sensor is located
in the front timing cover near the crankshaft
pulley (see illustration). The crankshaft
position sensor relays a signal to the ECU to
indicate the exact position (angle) of the
crankshaft.
Check
58The crankshaft sensor cannot be
diagnosed without the proper tools. The
Jaguar dealer uses a diagnostic scope/
computer called the JDS. Have the crankshaft
sensor diagnosed by the dealer service
department or other qualified repair workshop.
Renewal
59To renew the sensor, disconnect the
electrical connector and remove the bolt from
the crankshaft position sensor. Refitting is the
reverse of removal.
60To renew the crankshaft sensor gear,
remove the front pulley (refer to Chapter 2A).
61Be sure there is a small gap between the
crankshaft sensor and the teeth on the gear. It
should be between 0.46 to 1.07 mm (0.018 to
0.042 inch).
62Refitting is the reverse of removal. Tighten
the crankshaft sensor bolt to the torque listed
in this Chapter’s Specifications.
Emissions and engine control systems 6•7
6
3261 Jaguar XJ6 4.51 The air intake temperature sensor resistance will DECREASE
when the temperature of the air INCREASES
4.57 Location of the crankshaft position sensor
Page 163 of 227
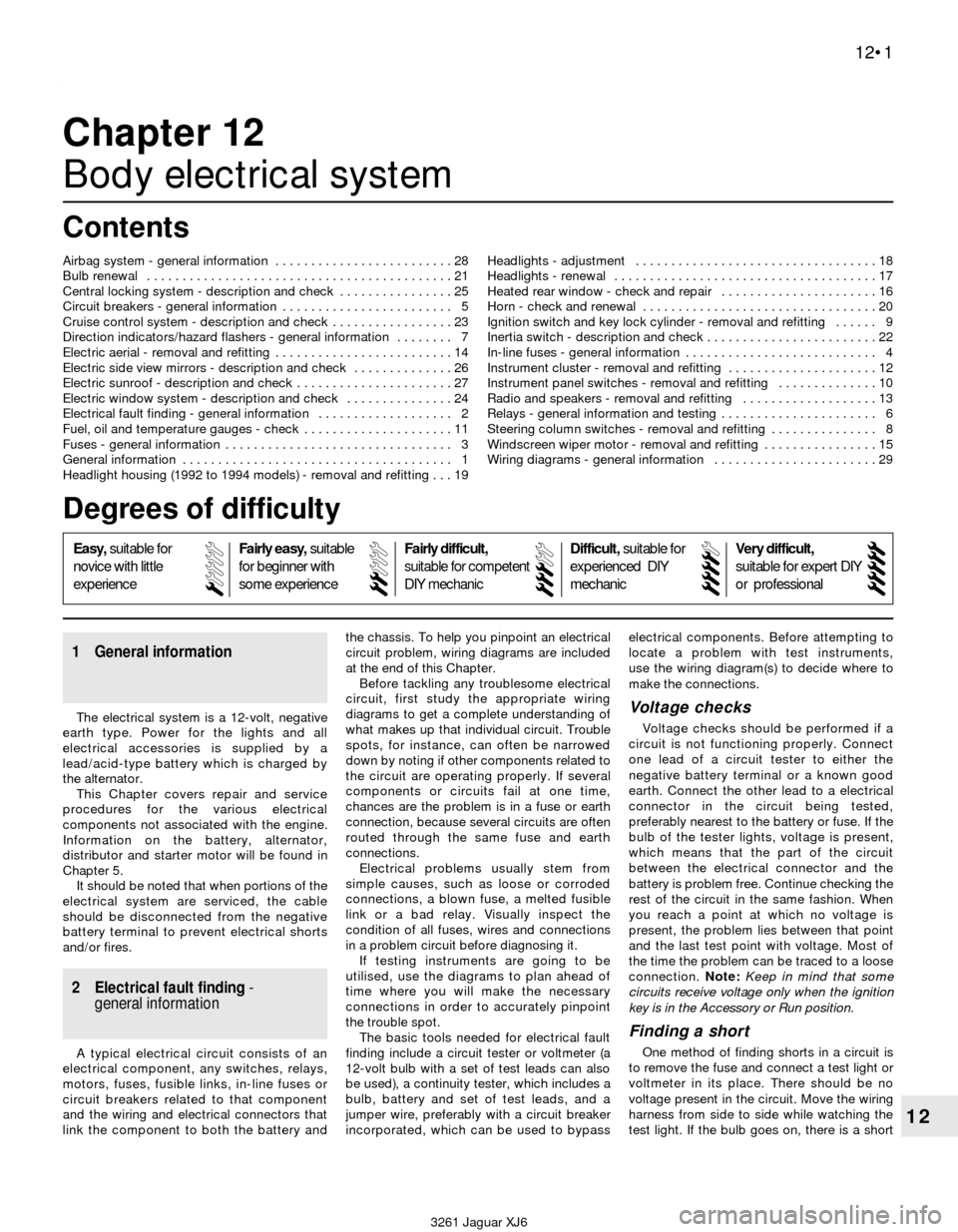
3261 Jaguar XJ6
12
Chapter 12
Body electrical system
1 General information
The electrical system is a 12-volt, negative
earth type. Power for the lights and all
electrical accessories is supplied by a
lead/acid-type battery which is charged by
the alternator.
This Chapter covers repair and service
procedures for the various electrical
components not associated with the engine.
Information on the battery, alternator,
distributor and starter motor will be found in
Chapter 5.
It should be noted that when portions of the
electrical system are serviced, the cable
should be disconnected from the negative
battery terminal to prevent electrical shorts
and/or fires.
2 Electrical fault finding-
general information
A typical electrical circuit consists of an
electrical component, any switches, relays,
motors, fuses, fusible links, in-line fuses or
circuit breakers related to that component
and the wiring and electrical connectors that
link the component to both the battery andthe chassis. To help you pinpoint an electrical
circuit problem, wiring diagrams are included
at the end of this Chapter.
Before tackling any troublesome electrical
circuit, first study the appropriate wiring
diagrams to get a complete understanding of
what makes up that individual circuit. Trouble
spots, for instance, can often be narrowed
down by noting if other components related to
the circuit are operating properly. If several
components or circuits fail at one time,
chances are the problem is in a fuse or earth
connection, because several circuits are often
routed through the same fuse and earth
connections.
Electrical problems usually stem from
simple causes, such as loose or corroded
connections, a blown fuse, a melted fusible
link or a bad relay. Visually inspect the
condition of all fuses, wires and connections
in a problem circuit before diagnosing it.
If testing instruments are going to be
utilised, use the diagrams to plan ahead of
time where you will make the necessary
connections in order to accurately pinpoint
the trouble spot.
The basic tools needed for electrical fault
finding include a circuit tester or voltmeter (a
12-volt bulb with a set of test leads can also
be used), a continuity tester, which includes a
bulb, battery and set of test leads, and a
jumper wire, preferably with a circuit breaker
incorporated, which can be used to bypasselectrical components. Before attempting to
locate a problem with test instruments,
use the wiring diagram(s) to decide where to
make the connections.
Voltage checks
Voltage checks should be performed if a
circuit is not functioning properly. Connect
one lead of a circuit tester to either the
negative battery terminal or a known good
earth. Connect the other lead to a electrical
connector in the circuit being tested,
preferably nearest to the battery or fuse. If the
bulb of the tester lights, voltage is present,
which means that the part of the circuit
between the electrical connector and the
battery is problem free. Continue checking the
rest of the circuit in the same fashion. When
you reach a point at which no voltage is
present, the problem lies between that point
and the last test point with voltage. Most of
the time the problem can be traced to a loose
connection. Note:Keep in mind that some
circuits receive voltage only when the ignition
key is in the Accessory or Run position.
Finding a short
One method of finding shorts in a circuit is
to remove the fuse and connect a test light or
voltmeter in its place. There should be no
voltage present in the circuit. Move the wiring
harness from side to side while watching the
test light. If the bulb goes on, there is a short Airbag system - general information . . . . . . . . . . . . . . . . . . . . . . . . . 28
Bulb renewal . . . . . . . . . . . . . . . . . . . . . . . . . . . . . . . . . . . . . . . . . . . 21
Central locking system - description and check . . . . . . . . . . . . . . . . 25
Circuit breakers - general information . . . . . . . . . . . . . . . . . . . . . . . . 5
Cruise control system - description and check . . . . . . . . . . . . . . . . . 23
Direction indicators/hazard flashers - general information . . . . . . . . 7
Electric aerial - removal and refitting . . . . . . . . . . . . . . . . . . . . . . . . . 14
Electric side view mirrors - description and check . . . . . . . . . . . . . . 26
Electric sunroof - description and check . . . . . . . . . . . . . . . . . . . . . . 27
Electric window system - description and check . . . . . . . . . . . . . . . 24
Electrical fault finding - general information . . . . . . . . . . . . . . . . . . . 2
Fuel, oil and temperature gauges - check . . . . . . . . . . . . . . . . . . . . . 11
Fuses - general information . . . . . . . . . . . . . . . . . . . . . . . . . . . . . . . . 3
General information . . . . . . . . . . . . . . . . . . . . . . . . . . . . . . . . . . . . . . 1
Headlight housing (1992 to 1994 models) - removal and refitting . . . 19Headlights - adjustment . . . . . . . . . . . . . . . . . . . . . . . . . . . . . . . . . . 18
Headlights - renewal . . . . . . . . . . . . . . . . . . . . . . . . . . . . . . . . . . . . . 17
Heated rear window - check and repair . . . . . . . . . . . . . . . . . . . . . . 16
Horn - check and renewal . . . . . . . . . . . . . . . . . . . . . . . . . . . . . . . . . 20
Ignition switch and key lock cylinder - removal and refitting . . . . . . 9
Inertia switch - description and check . . . . . . . . . . . . . . . . . . . . . . . . 22
In-line fuses - general information . . . . . . . . . . . . . . . . . . . . . . . . . . . 4
Instrument cluster - removal and refitting . . . . . . . . . . . . . . . . . . . . . 12
Instrument panel switches - removal and refitting . . . . . . . . . . . . . . 10
Radio and speakers - removal and refitting . . . . . . . . . . . . . . . . . . . 13
Relays - general information and testing . . . . . . . . . . . . . . . . . . . . . . 6
Steering column switches - removal and refitting . . . . . . . . . . . . . . . 8
Windscreen wiper motor - removal and refitting . . . . . . . . . . . . . . . . 15
Wiring diagrams - general information . . . . . . . . . . . . . . . . . . . . . . . 29
12•1
Contents
Easy,suitable for
novice with little
experienceFairly easy,suitable
for beginner with
some experienceFairly difficult,
suitable for competent
DIY mechanic
Difficult,suitable for
experienced DIY
mechanicVery difficult,
suitable for expert DIY
or professional
Degrees of difficulty
54321
Page 168 of 227
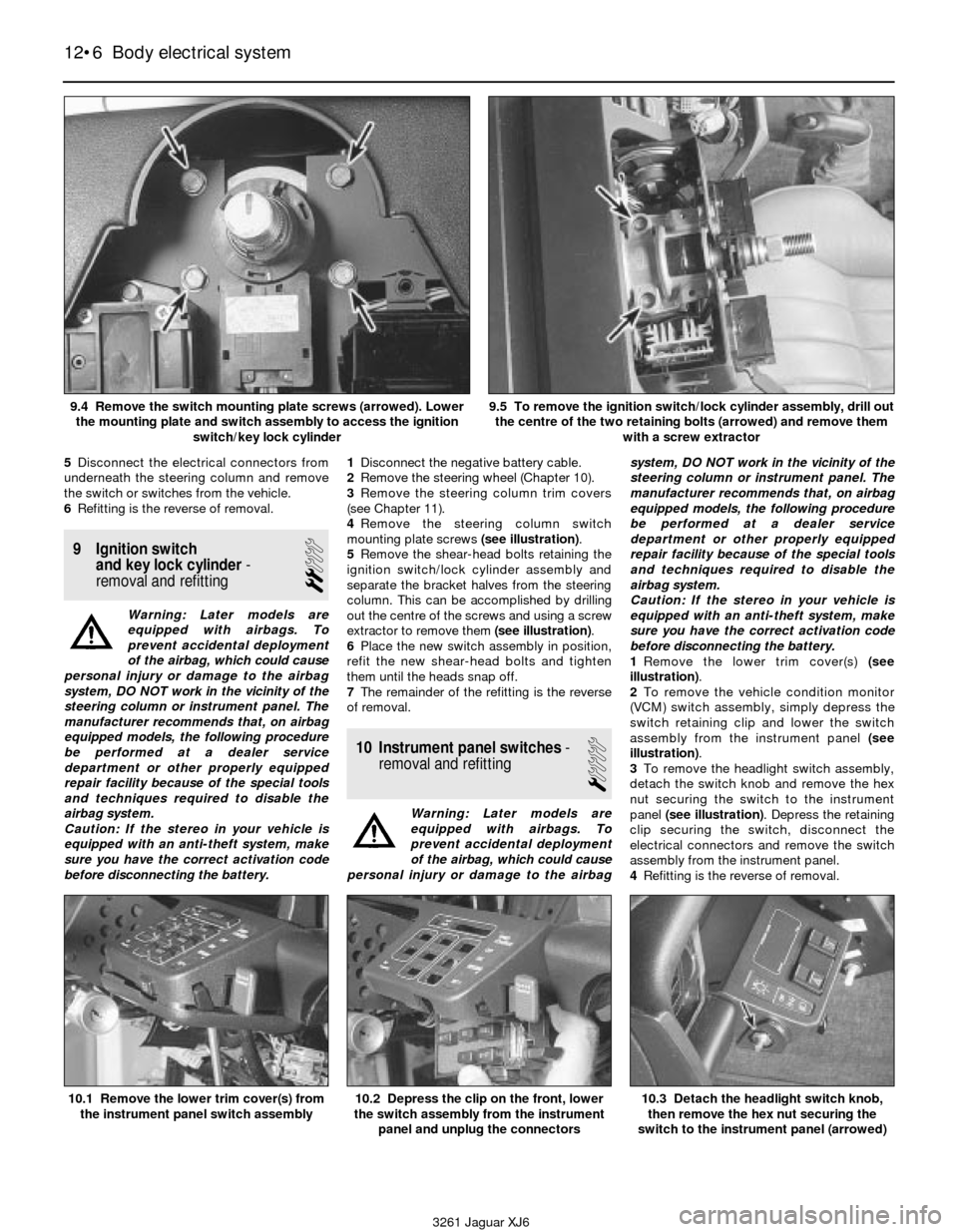
5Disconnect the electrical connectors from
underneath the steering column and remove
the switch or switches from the vehicle.
6Refitting is the reverse of removal.
9 Ignition switch
and key lock cylinder-
removal and refitting
2
Warning: Later models are
equipped with airbags. To
prevent accidental deployment
of the airbag, which could cause
personal injury or damage to the airbag
system, DO NOT work in the vicinity of the
steering column or instrument panel. The
manufacturer recommends that, on airbag
equipped models, the following procedure
be performed at a dealer service
department or other properly equipped
repair facility because of the special tools
and techniques required to disable the
airbag system.
Caution: If the stereo in your vehicle is
equipped with an anti-theft system, make
sure you have the correct activation code
before disconnecting the battery.1Disconnect the negative battery cable.
2Remove the steering wheel (Chapter 10).
3Remove the steering column trim covers
(see Chapter 11).
4Remove the steering column switch
mounting plate screws (see illustration).
5Remove the shear-head bolts retaining the
ignition switch/lock cylinder assembly and
separate the bracket halves from the steering
column. This can be accomplished by drilling
out the centre of the screws and using a screw
extractor to remove them (see illustration).
6Place the new switch assembly in position,
refit the new shear-head bolts and tighten
them until the heads snap off.
7The remainder of the refitting is the reverse
of removal.
10 Instrument panel switches-
removal and refitting
1
Warning: Later models are
equipped with airbags. To
prevent accidental deployment
of the airbag, which could cause
personal injury or damage to the airbagsystem, DO NOT work in the vicinity of the
steering column or instrument panel. The
manufacturer recommends that, on airbag
equipped models, the following procedure
be performed at a dealer service
department or other properly equipped
repair facility because of the special tools
and techniques required to disable the
airbag system.
Caution: If the stereo in your vehicle is
equipped with an anti-theft system, make
sure you have the correct activation code
before disconnecting the battery.
1Remove the lower trim cover(s) (see
illustration).
2To remove the vehicle condition monitor
(VCM) switch assembly, simply depress the
switch retaining clip and lower the switch
assembly from the instrument panel (see
illustration).
3To remove the headlight switch assembly,
detach the switch knob and remove the hex
nut securing the switch to the instrument
panel (see illustration). Depress the retaining
clip securing the switch, disconnect the
electrical connectors and remove the switch
assembly from the instrument panel.
4Refitting is the reverse of removal.
12•6 Body electrical system
10.1 Remove the lower trim cover(s) from
the instrument panel switch assembly10.2 Depress the clip on the front, lower
the switch assembly from the instrument
panel and unplug the connectors10.3 Detach the headlight switch knob,
then remove the hex nut securing the
switch to the instrument panel (arrowed)
3261 Jaguar XJ6 9.4 Remove the switch mounting plate screws (arrowed). Lower
the mounting plate and switch assembly to access the ignition
switch/key lock cylinder
9.5 To remove the ignition switch/lock cylinder assembly, drill out
the centre of the two retaining bolts (arrowed) and remove them
with a screw extractor
Page 170 of 227
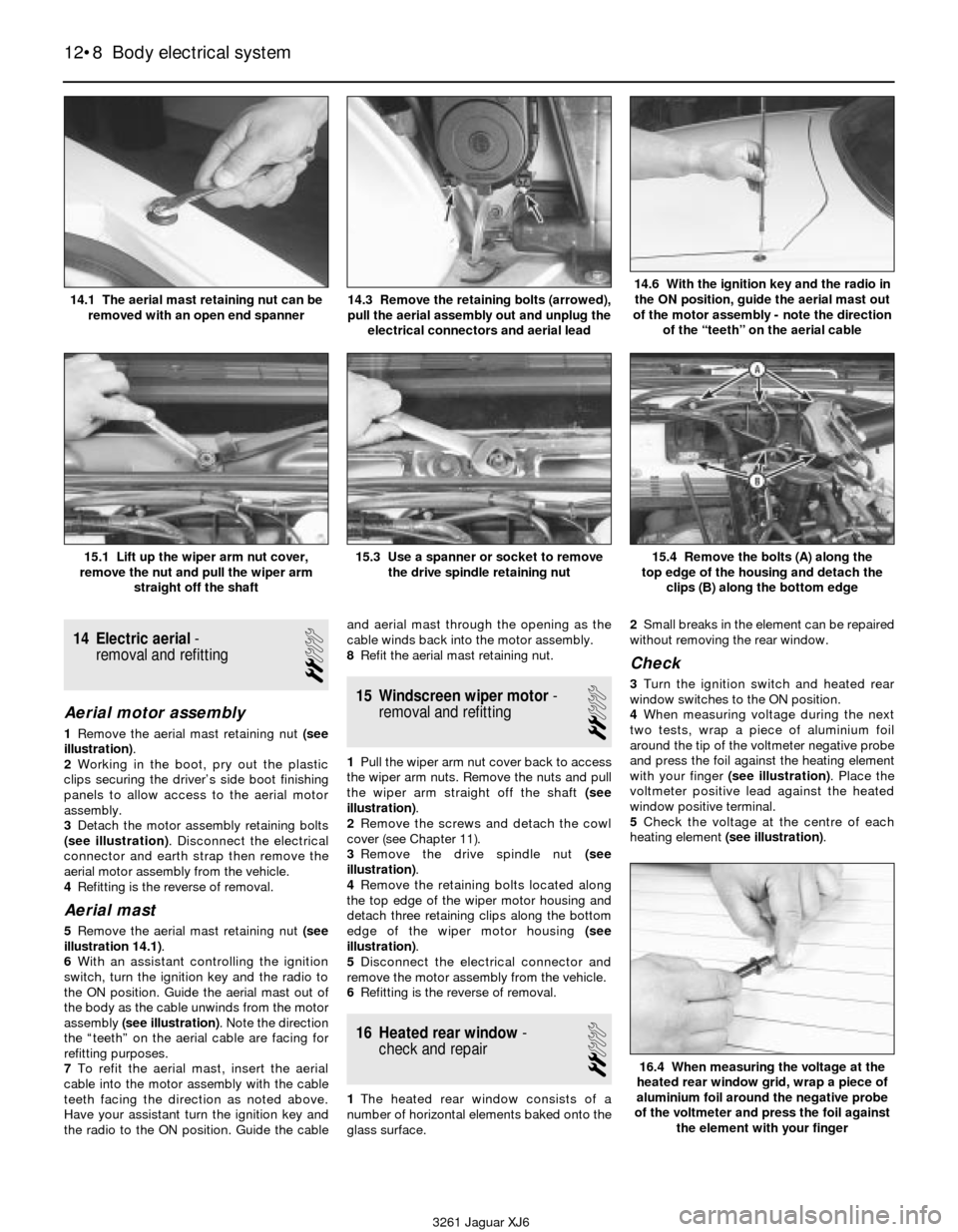
14 Electric aerial-
removal and refitting
2
Aerial motor assembly
1Remove the aerial mast retaining nut (see
illustration).
2Working in the boot, pry out the plastic
clips securing the driver’s side boot finishing
panels to allow access to the aerial motor
assembly.
3Detach the motor assembly retaining bolts
(see illustration). Disconnect the electrical
connector and earth strap then remove the
aerial motor assembly from the vehicle.
4Refitting is the reverse of removal.
Aerial mast
5Remove the aerial mast retaining nut (see
illustration 14.1).
6With an assistant controlling the ignition
switch, turn the ignition key and the radio to
the ON position. Guide the aerial mast out of
the body as the cable unwinds from the motor
assembly (see illustration). Note the direction
the “teeth” on the aerial cable are facing for
refitting purposes.
7To refit the aerial mast, insert the aerial
cable into the motor assembly with the cable
teeth facing the direction as noted above.
Have your assistant turn the ignition key and
the radio to the ON position. Guide the cableand aerial mast through the opening as the
cable winds back into the motor assembly.
8Refit the aerial mast retaining nut.
15 Windscreen wiper motor-
removal and refitting
2
1Pull the wiper arm nut cover back to access
the wiper arm nuts. Remove the nuts and pull
the wiper arm straight off the shaft (see
illustration).
2Remove the screws and detach the cowl
cover (see Chapter 11).
3Remove the drive spindle nut (see
illustration).
4Remove the retaining bolts located along
the top edge of the wiper motor housing and
detach three retaining clips along the bottom
edge of the wiper motor housing (see
illustration).
5Disconnect the electrical connector and
remove the motor assembly from the vehicle.
6Refitting is the reverse of removal.
16 Heated rear window-
check and repair
2
1The heated rear window consists of a
number of horizontal elements baked onto the
glass surface.2Small breaks in the element can be repaired
without removing the rear window.
Check
3Turn the ignition switch and heated rear
window switches to the ON position.
4When measuring voltage during the next
two tests, wrap a piece of aluminium foil
around the tip of the voltmeter negative probe
and press the foil against the heating element
with your finger (see illustration). Place the
voltmeter positive lead against the heated
window positive terminal.
5Check the voltage at the centre of each
heating element (see illustration).
12•8 Body electrical system
14.1 The aerial mast retaining nut can be
removed with an open end spanner14.3 Remove the retaining bolts (arrowed),
pull the aerial assembly out and unplug the
electrical connectors and aerial lead14.6 With the ignition key and the radio in
the ON position, guide the aerial mast out
of the motor assembly - note the direction
of the “teeth” on the aerial cable
15.1 Lift up the wiper arm nut cover,
remove the nut and pull the wiper arm
straight off the shaft15.3 Use a spanner or socket to remove
the drive spindle retaining nut15.4 Remove the bolts (A) along the
top edge of the housing and detach the
clips (B) along the bottom edge
3261 Jaguar XJ6
16.4 When measuring the voltage at the
heated rear window grid, wrap a piece of
aluminium foil around the negative probe
of the voltmeter and press the foil against
the element with your finger