engine JEEP CJ 1953 Repair Manual
[x] Cancel search | Manufacturer: JEEP, Model Year: 1953, Model line: CJ, Model: JEEP CJ 1953Pages: 376, PDF Size: 19.96 MB
Page 64 of 376
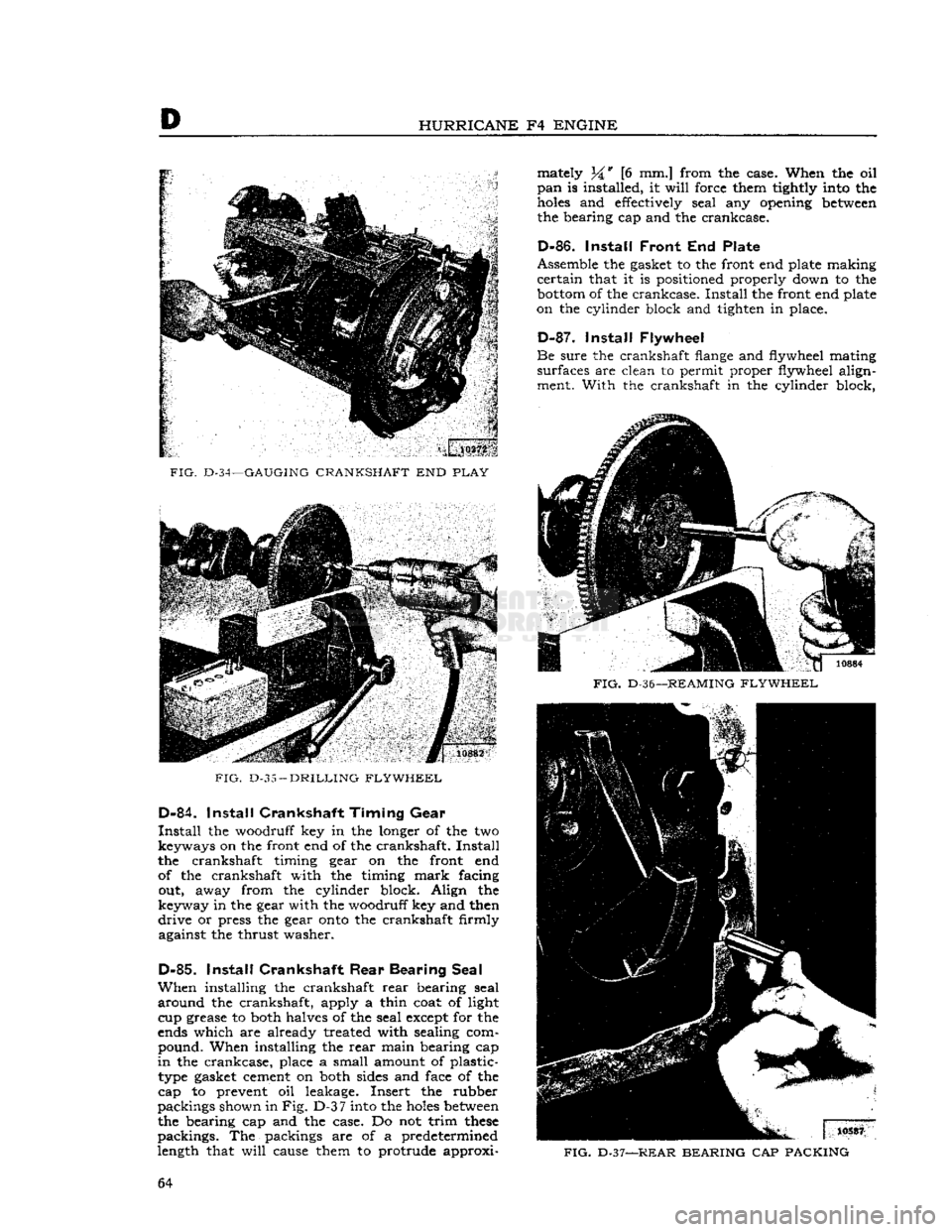
D
HURRICANE
F4
ENGINE
FIG.
D-34—GAUGING
CRANKSHAFT
END
PLAY
FIG.
D-35
—
DRILLING FLYWHEEL
D-84.
Install
Crankshaft Timing
Gear
Install
the woodruff key in the longer of the two keyways on the front end of the crankshaft.
Install
the crankshaft timing gear on the front end of the crankshaft with the timing
mark
facing out, away from the cylinder block. Align the
keyway in the gear with the woodruff key and then
drive
or press the gear
onto
the crankshaft firmly against the thrust washer.
D-85.
Install
Crankshaft
Rear
Bearing Seal
When
installing the crankshaft
rear
bearing seal
around
the crankshaft, apply a thin coat of light cup grease to both halves of the seal except for the
ends which are already treated with sealing com pound. When installing the
rear
main bearing cap
in
the crankcase, place a small amount of plastic- type gasket cement on both sides and face of the
cap to prevent oil leakage. Insert the rubber
packings shown in
Fig. D-3
7
into the
holes
between
the bearing cap and the case. Do not trim
these
packings. The packings are of a predetermined
length that
will
cause them to protrude approxi mately 34* [6 mm.] from the case. When the oil
pan
is installed, it
will
force them tightly into the
holes
and effectively seal any opening
between
the bearing cap and the crankcase.
D-86.
Install
Front
End Plate
Assemble the gasket to the front end plate making
certain
that it is positioned properly down to the
bottom
of the crankcase.
Install
the front end plate
on the cylinder block and tighten in place.
D-87.
Install
Flywheel
Be
sure the crankshaft flange and flywheel mating
surfaces are clean to permit proper flywheel align ment. With the crankshaft in the cylinder block,
FIG.
D-36—
REAMING FLYWHEEL
FIG.
D-37—REAR
BEARING
CAP
PACKING
64
Page 65 of 376
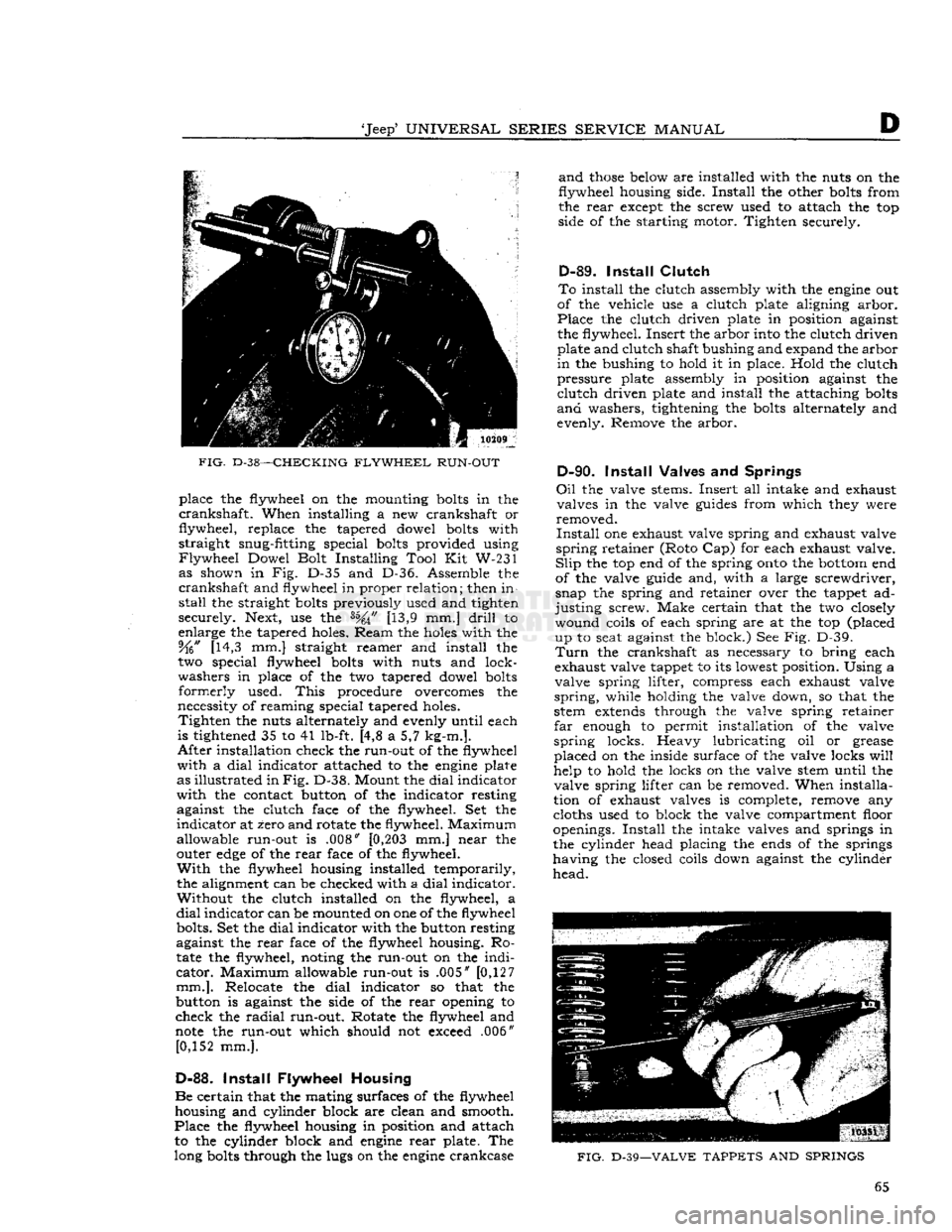
'Jeep'
UNIVERSAL
SERIES
SERVICE
MANUAL
D
FIG.
D-38—CHECKING
FLYWHEEL
RUN-OUT
place the flywheel on the mounting
bolts
in the
crankshaft.
When installing a new crankshaft or
flywheel, replace the tapered dowel
bolts
with
straight snug-fitting special
bolts
provided using
Flywheel
Dowel Bolt Installing Tool Kit W-231 as shown in Fig. D-35 and D-36. Assemble the
crankshaft
and flywheel in proper relation; then in
stall
the straight
bolts
previously used and tighten
securely. Next, use the [13,9 mm.]
drill
to
enlarge the tapered holes. Ream the
holes
with the 5fo" [14,3 mm.] straight reamer and install the
two special flywheel
bolts
with nuts and lock
washers in place of the two tapered dowel
bolts
formerly
used.
This
procedure overcomes the
necessity of reaming special tapered holes.
Tighten
the nuts alternately and evenly until each
is tightened 35 to 41 lb-ft. [4,8 a 5,7 kg-m.].
After
installation check the run-out of the flywheel
with
a
dial
indicator attached to the
engine
plate
as illustrated in
Fig.
D-38. Mount the
dial
indicator
with
the contact button of the indicator resting against the clutch face of the flywheel. Set the
indicator
at zero and rotate the flywheel. Maximum
allowable run-out is .008"
[0,203
mm.] near the
outer
edge
of the
rear
face of the flywheel.
With
the flywheel housing installed temporarily,
the alignment can be checked with a
dial
indicator. Without the clutch installed on the flywheel, a
dial
indicator can be mounted on one of the flywheel bolts. Set the
dial
indicator with the button resting
against the
rear
face of the flywheel housing. Ro
tate
the flywheel, noting the run-out on the
indi
cator.
Maximum allowable run-out is .005" [0,127
mm.].
Relocate the
dial
indicator so that the
button is against the side of the
rear
opening to
check the
radial
run-out. Rotate the flywheel and
note
the run-out which should not exceed .006" [0,152 mm.].
D-88.
Install
Flywheel Housing
Be
certain that the mating surfaces of the flywheel housing and cylinder block are clean and smooth.
Place
the flywheel housing in position and attach to the cylinder block and
engine
rear
plate. The
long
bolts
through the lugs on the
engine
crankcase
and
those
below are installed with the nuts on the
flywheel housing side.
Install
the other
bolts
from
the
rear
except the screw used to attach the top
side of the starting motor. Tighten securely.
D-89.
Install
Clutch
To
install the clutch assembly with the
engine
out
of the vehicle use a clutch plate aligning arbor.
Place
the clutch driven plate in position against
the flywheel. Insert the arbor into the clutch driven plate and clutch shaft bushing and expand the arbor
in
the bushing to hold it in place. Hold the clutch
pressure plate assembly in position against the
clutch
driven plate and install the attaching
bolts
and
washers, tightening the
bolts
alternately and
evenly. Remove the arbor.
D-90.
Install
Valves and Springs
Oil
the valve stems. Insert all intake and exhaust valves in the valve
guides
from which they were
removed.
Install
one exhaust valve spring and exhaust valve
spring
retainer (Roto Cap) for each exhaust valve.
Slip
the top end of the spring
onto
the
bottom
end
of the valve guide and, with a large screwdriver,
snap the spring and retainer over the tappet ad
justing
screw. Make certain that the two closely wound coils of each spring are at the top (placed up to seat against the block.) See Fig. D-39.
Turn
the crankshaft as necessary to bring each
exhaust valve tappet to its lowest position. Using a
valve spring lifter, compress each exhaust valve
spring,
while holding the valve down, so that the
stem
extends
through the valve spring retainer
far
enough to permit installation of the valve
spring
locks. Heavy lubricating oil or grease
placed on the inside surface of the valve locks
will
help to hold the locks on the valve stem until the valve spring lifter can be removed. When installa
tion of exhaust valves is complete, remove any
cloths used to block the valve compartment floor
openings.
Install
the intake valves and springs in the cylinder head placing the ends of the springs
having the closed coils down against the cylinder
head.
FIG.
D-39—VALVE
TAPPETS
AND
SPRINGS
65
Page 66 of 376
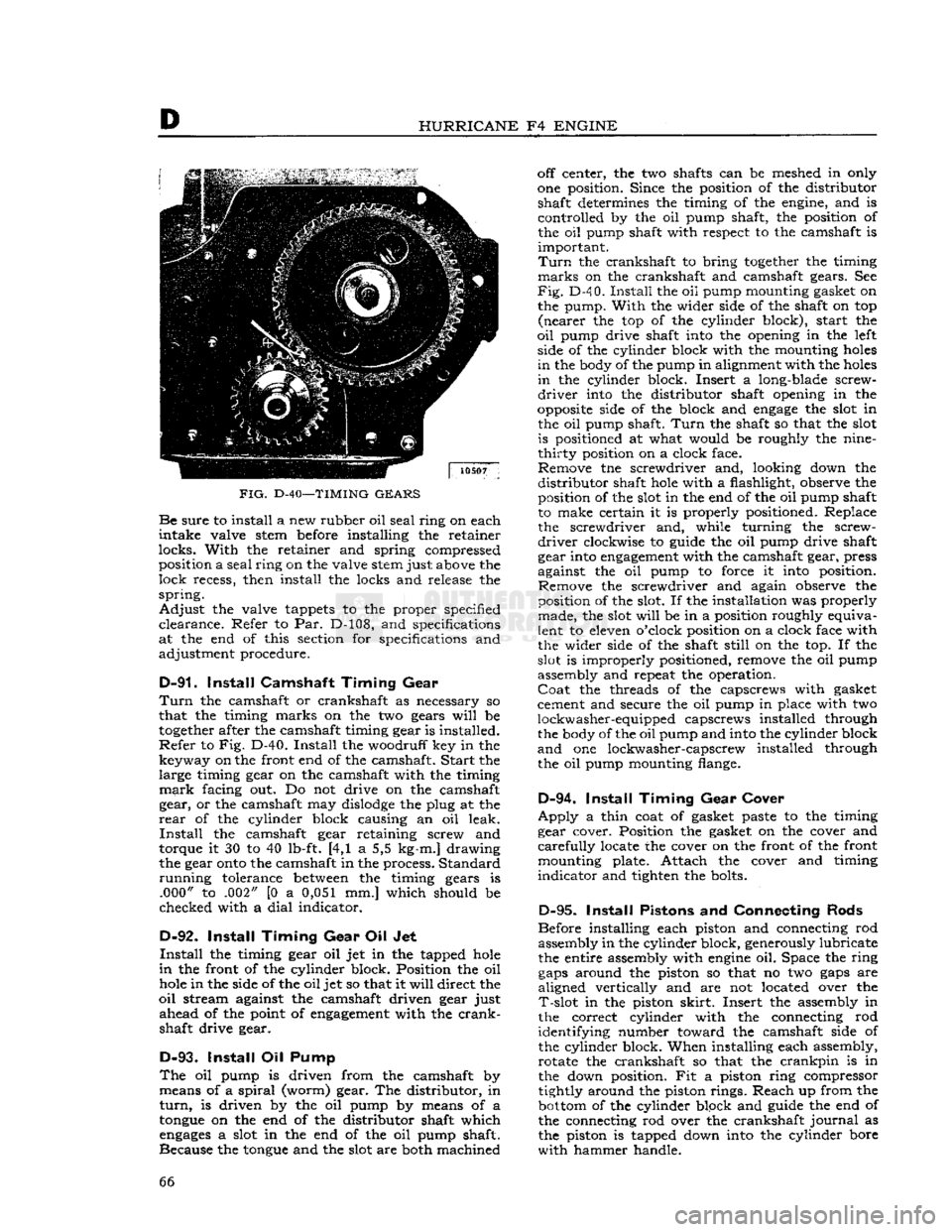
D
HURRICANE
F4
ENGINE
FIG.
D-40—TIMING
GEARS Be
sure
to install a new rubber oil
seal
ring on each
intake
valve stem before installing the retainer
locks.
With
the retainer and spring compressed position a
seal
ring
on the valve stem just above the
lock
recess, then install the locks and release the
spring.
Adjust
the valve tappets to the proper specified
clearance.
Refer to Par. D-108, and specifications
at the end of this section for specifications and
adjustment procedure.
D-91.
Install
Camshaft
Timing
Gear
Turn
the camshaft or crankshaft as necessary so
that the timing marks on the two gears
will
be
together
after the camshaft timing gear is installed.
Refer
to Fig. D-40.
Install
the woodruff key in the key way on the front end of the camshaft.
Start
the large timing gear on the camshaft with the timing
mark
facing out. Do not drive on the camshaft gear, or the camshaft may
dislodge
the plug at the
rear
of the cylinder block causing an oil leak.
Install
the camshaft gear retaining screw and
torque it 30 to 40 lb-ft. [4,1 a 5,5 kg-m.] drawing
the gear
onto
the camshaft in the process. Standard
running
tolerance
between
the timing gears is .000" to .002" [0 a 0,051 mm.] which should be
checked with a
dial
indicator.
D-92.
Install
Timing
Gear
Oil Jet
Install
the timing gear oil jet in the tapped
hole
in
the front of the cylinder block. Position the oil
hole
in the side of the oil jet so that it
will
direct the
oil
stream against the camshaft driven gear just
ahead
of the point of
engagement
with the
crank
shaft drive gear.
D-93.
Install
Oil Pump
The
oil pump is driven from the camshaft by means of a
spiral
(worm) gear. The distributor, in
turn,
is driven by the oil pump by means of a
tongue
on the end of the distributor shaft which
engages
a slot in the end of the oil pump shaft.
Because the
tongue
and the slot are both machined off center, the two shafts can be meshed in only
one position. Since the position of the distributor shaft determines the timing of the engine, and is
controlled by the oil pump shaft, the position of the oil pump shaft with respect to the camshaft is
important.
Turn
the crankshaft to bring
together
the timing
marks
on the crankshaft and camshaft gears. See
Fig.
D-4 0.
Install
the oil pump mounting gasket on
the pump.
With
the wider side of the shaft on top
(nearer
the top of the cylinder block), start the
oil
pump drive shaft into the opening in the left side of the cylinder block with the mounting
holes
in
the body of the pump in alignment with the
holes
in
the cylinder block. Insert a long-blade screw
driver
into the distributor shaft opening in the
opposite
side of the block and
engage
the slot in the oil pump shaft.
Turn
the shaft so that the slot is positioned at what would be roughly the nine-
thirty
position on a clock face. Remove tne screwdriver and, looking down the
distributor
shaft
hole
with a flashlight, observe the position of the slot in the end of the oil pump shaft
to make certain it is properly positioned. Replace the screwdriver and, while turning the screw
driver
clockwise to guide the oil pump drive shaft
gear into
engagement
with the camshaft gear, press
against the oil pump to force it into position. Remove the screwdriver and again observe the
position of the slot. If the installation was properly made, the slot
will
be in a position roughly equiva
lent to eleven o'clock position on a clock face with
the wider side of the shaft
still
on the top. If the
slot is improperly positioned, remove the oil pump
assembly and repeat the operation.
Coat
the threads of the capscrews with gasket
cement and secure the oil pump in place with two
lockwasher-equipped capscrews installed through the body of the oil pump and into the cylinder block
and
one lockwasher-capscrew installed through
the oil pump mounting flange.
D-94.
Install
Timing
Gear
Cover
Apply
a thin coat of gasket paste to the timing
gear cover. Position the gasket on the cover and
carefully
locate the cover on the front of the front mounting plate. Attach the cover and timing
indicator
and tighten the bolts.
D-95.
Install
Pistons and Connecting Rods
Before installing each piston and connecting rod assembly in the cylinder block, generously lubricate
the entire assembly with
engine
oil. Space the ring
gaps
around the piston so that no two
gaps
are
aligned vertically and are not located over the
T-slot
in the piston
skirt.
Insert the assembly in
the correct cylinder with the connecting rod
identifying number toward the camshaft side of
the cylinder block. When installing each assembly, rotate the crankshaft so that the
crankpin
is in
the down position. Fit a piston ring compressor
tightly around the piston rings. Reach up from the
bottom
of the cylinder block and guide the end of
the connecting rod over the crankshaft
journal
as
the piston is tapped down into the cylinder bore
with
hammer handle. 66
Page 67 of 376
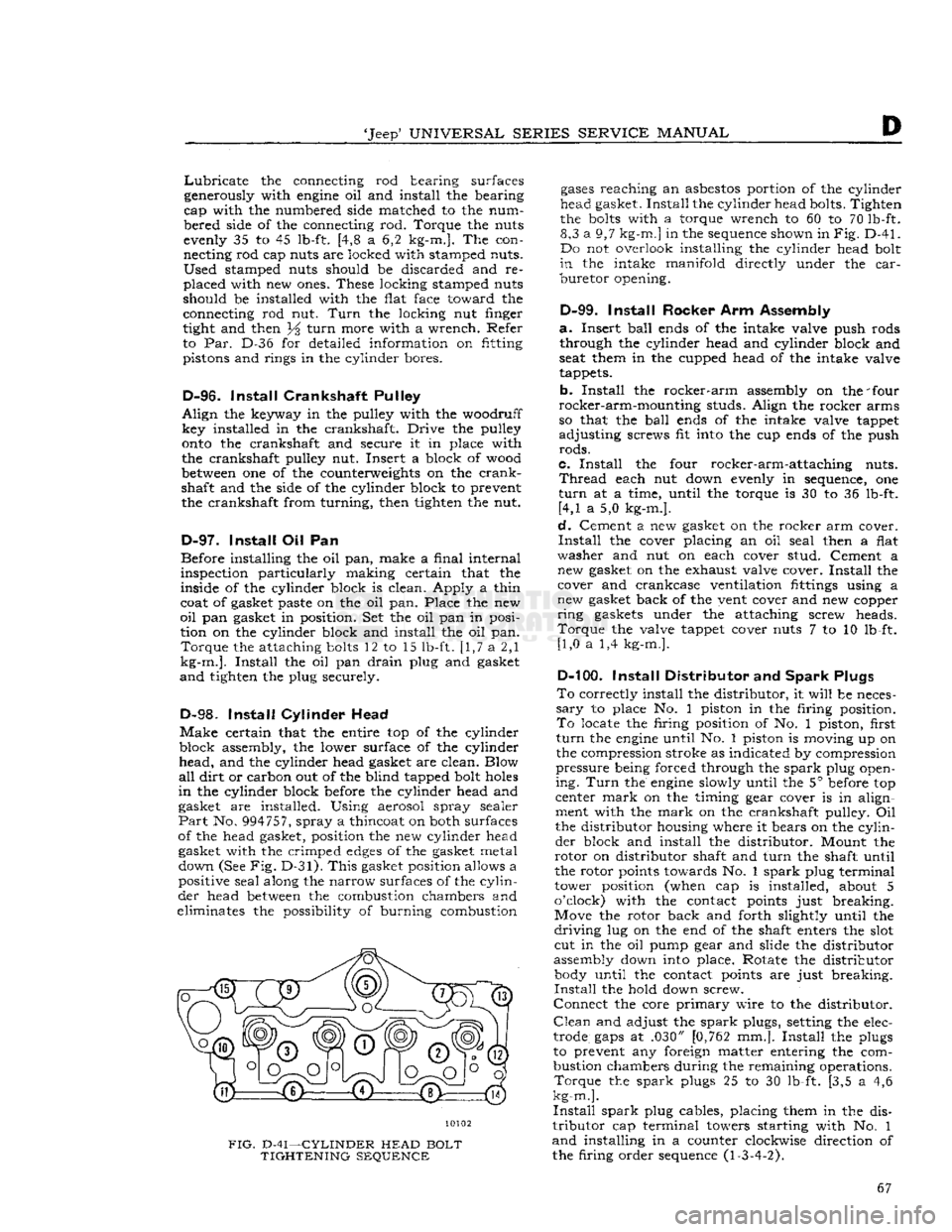
'Jeep'
UNIVERSAL
SERIES SERVICE
MANUAL
D
Lubricate
the connecting rod bearing surfaces
generously with
engine
oil and install the bearing
cap with the numbered side matched to the num
bered side of the connecting rod. Torque the nuts
evenly 35 to 45 lb-ft. [4,8 a 6,2 kg-m.]. The con
necting rod cap nuts are locked with stamped nuts.
Used
stamped nuts should be discarded and re
placed with new
ones.
These locking stamped nuts
should be installed with the flat face toward the
connecting rod nut.
Turn
the locking nut finger
tight and then 34
turn
more with a wrench. Refer
to Par. D-36 for detailed information on fitting pistons and rings in the cylinder bores.
D-96.
Install
Crankshaft
Pulley
Align
the keyway in the pulley with the woodruff key installed in the crankshaft. Drive the pulley
onto
the crankshaft and secure it in place with
the crankshaft pulley nut. Insert a block of wood
between
one of the counterweights on the
crank
shaft and the side of the cylinder block to prevent the crankshaft from turning, then tighten the nut.
D-97.
Install
Oil Pan
Before installing the oil pan, make a final internal
inspection particularly making certain that the
inside of the cylinder block is clean. Apply a thin
coat of gasket paste on the oil pan. Place the new
oil
pan gasket in position. Set the oil pan in posi
tion on the cylinder block and install the oil pan.
Torque
the attaching
bolts
12 to 15 lb-ft. [1,7 a 2,1
kg-m.].
Install
the oil pan
drain
plug and gasket
and
tighten the plug securely.
D-98.
Install
Cylinder
Head
Make
certain that the entire top of the cylinder
block
assembly, the lower surface of the cylinder
head,
and the cylinder head gasket are clean. Blow
all
dirt
or carbon out of the blind tapped bolt
holes
in
the cylinder block before the cylinder head and gasket are installed. Using aerosol spray sealer
Part
No. 994757, spray a thincoat on both surfaces
of the head gasket, position the new cylinder head gasket with the crimped
edges
of the gasket metal down (See Fig. D-31).
This
gasket position allows a
positive seal along the narrow surfaces of the
cylin
der
head
between
the combustion chambers and
eliminates the possibility of burning combustion
10102
FIG.
D-41—CYLINDER
HEAD
BOLT
TIGHTENING
SEQUENCE
gases
reaching
an
asbestos
portion of the cylinder
head gasket.
Install
the cylinder head bolts. Tighten
the
bolts
with a torque wrench to 60 to 70 lb-ft. 8,3 a 9,7
kg-m.]
in the sequence shown in
Fig.
D-41.
Do not overlook installing the cylinder head bolt
in
the intake
manifold
directly under the
car
buretor
opening.
D-99.
Install
Rocker Arm Assembly
a.
Insert
ball
ends of the intake valve push rods through the cylinder head and cylinder block and
seat them in the cupped head of the intake valve
tappets.
b.
Install
the
rocker-arm
assembly on the 'four
rocker-arm-mounting
studs. Align the rocker arms
so that the
ball
ends of the intake valve tappet
adjusting
screws fit into the cup ends of the push
rods.
c.
Install
the four rocker-arm-attaching nuts.
Thread
each nut down evenly in sequence, one
turn
at a time, until the torque is 30 to 36 lb-ft. [4,1 a 5,0 kg-m.].
d.
Cement a new gasket on the rocker arm cover.
Install
the cover placing an oil seal then a flat
washer
and nut on each cover stud. Cement a new gasket on the exhaust valve cover.
Install
the cover and crankcase ventilation fittings using a
new gasket back of the vent cover and new copper
ring
gaskets under the attaching screw heads.
Torque
the valve tappet cover nuts 7 to 10 lb-ft. [1,0 a 1,4 kg-m.].
D-100.
Install
Distributor and
Spark
Plugs
To
correctly install the distributor, it
will
be neces
sary
to place No. 1 piston in the firing position.
To
locate the firing position of No. 1 piston, first
turn
the
engine
until No. 1 piston is moving up on
the compression stroke as indicated by compression
pressure
being forced through the
spark
plug open
ing.
Turn
the
engine
slowly until the 5° before top
center
mark
on the timing gear cover is in align
ment with the
mark
on the crankshaft pulley. Oil
the distributor housing where it bears on the
cylin
der
block and install the distributor. Mount the
rotor
on distributor shaft and
turn
the shaft until
the rotor points towards No. 1
spark
plug terminal
tower position (when cap is installed, about 5
o'clock) with the contact points just breaking.
Move the rotor back and forth slightly until the
driving
lug on the end of the shaft enters the slot cut in the oil pump gear and slide the distributor
assembly down into place. Rotate the distributor body until the contact points are just breaking.
Install
the hold down screw.
Connect
the core
primary
wire to the distributor.
Clean
and adjust the
spark
plugs, setting the elec
trode
gaps
at .030" [0,762 mm.].
Install
the plugs
to prevent any foreign matter entering the com
bustion chambers during the remaining operations.
Torque
the
spark
plugs 25 to 30 lb-ft. [3,5 a 4,6
kg-m.].
Install
spark
plug cables, placing them in the dis
tributor
cap terminal towers starting with No. 1
and
installing in a counter clockwise direction of
the firing order sequence (1-3-4-2). 67
Page 68 of 376
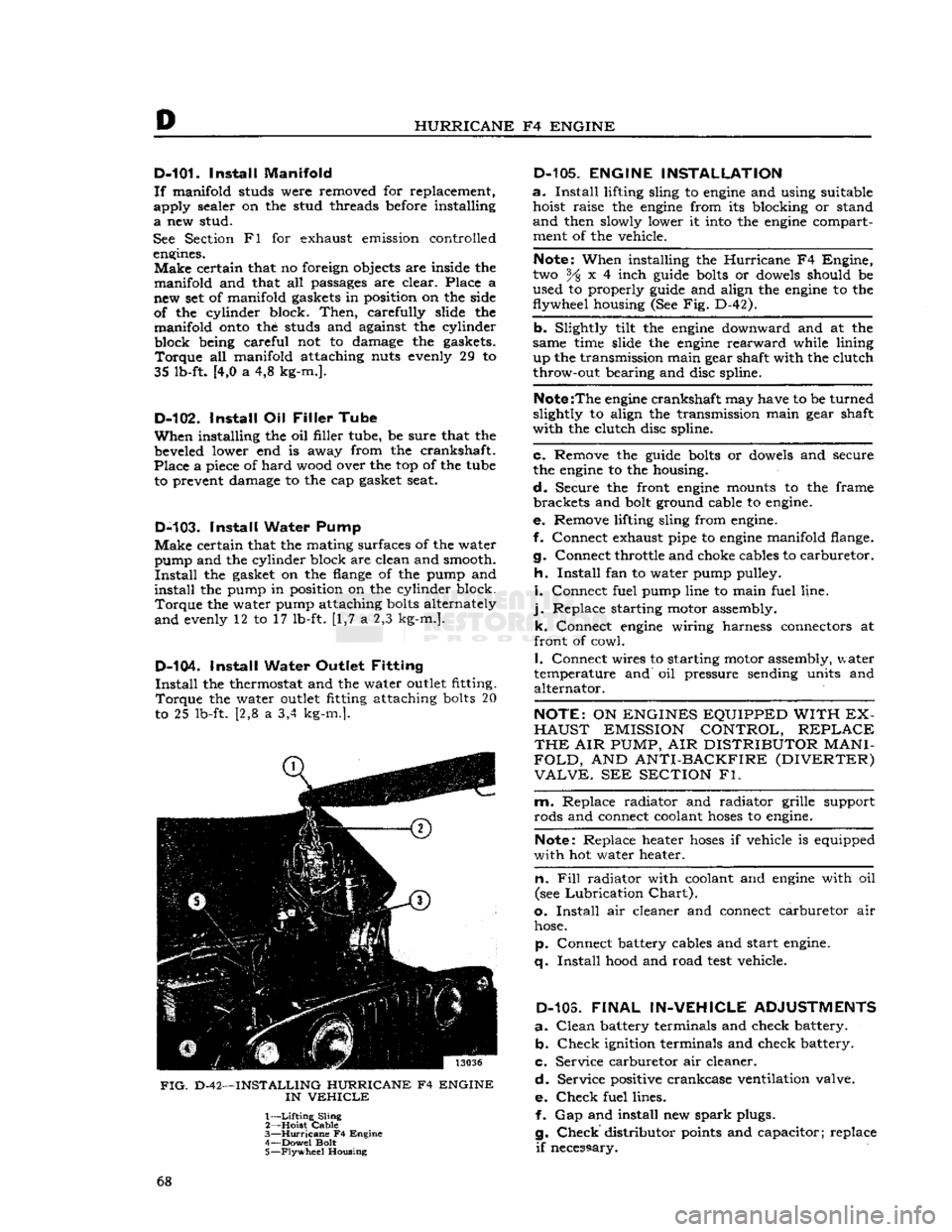
D
HURRICANE
F4
ENGINE
D-101.
Install
Manifold
If
manifold studs were removed for replacement,
apply sealer on the stud threads
before
installing
a
new stud.
See Section Fl for exhaust emission controlled
engines.
Make
certain that no foreign objects are inside the manifold and that all
passages
are clear. Place a
new set of manifold
gaskets
in position on the side
of the cylinder block.
Then,
carefully slide the manifold
onto
the studs and against the cylinder block being careful not to damage the gaskets.
Torque
all manifold attaching nuts evenly 29 to
35 lb-ft. [4,0 a 4,8 kg-m.].
D-102.
Install
Oil
Filler
Tube
When
installing the oil filler tube, be sure that the
beveled lower end is away from the crankshaft.
Place a
piece
of
hard
wood
over the top of the
tube
to prevent damage to the cap gasket seat.
D-103.
Install
Water Pump
Make
certain that the mating surfaces of the water pump and the cylinder block are clean and smooth.
Install
the gasket on the
flange
of the pump and
install
the pump in position on the cylinder block.
Torque
the water pump attaching
bolts
alternately
and
evenly 12 to 17 lb-ft. [1,7 a 2,3 kg-m.].
D-104.
Install
Water Outlet Fitting
Install
the thermostat and the water
outlet
fitting.
Torque
the water
outlet
fitting attaching
bolts
20
to 25 lb-ft. [2,8 a 3,4 kg-m.].
FIG.
D-42—INSTALLING HURRICANE F4 ENGINE
IN
VEHICLE
1—
Lifting
Sling
2— Hoist
Cable
3—
Hurricane
F4 Engine
4— Dowel Bolt
5—
Flywheel
Housing
D-105.
ENGINE INSTALLATION
a.
Install
lifting sling to
engine
and using suitable hoist raise the
engine
from its blocking or stand
and
then slowly lower it
into
the
engine
compartment of the vehicle.
Note:
When installing the
Hurricane
F4 Engine,
two % x 4 inch
guide
bolts
or
dowels
should be
used to properly
guide
and align the
engine
to the
flywheel housing (See Fig. D-42).
b. Slightly tilt the
engine
downward and at the
same time slide the
engine
rearward
while lining up the transmission main gear shaft with the clutch
throw-out bearing and disc spline.
Note
:The
engine
crankshaft may have to be turned
slightly to align the transmission main gear shaft
with the clutch disc spline.
c. Remove the
guide
bolts
or
dowels
and secure
the
engine
to the housing.
d.
Secure the front
engine
mounts to the frame brackets and
bolt
ground cable to
engine.
e. Remove lifting sling from
engine.
f. Connect exhaust pipe to
engine
manifold flange.
g. Connect throttle and choke cables to carburetor.
h.
Install
fan to water pump pulley.
i.
Connect fuel pump line to main fuel line,
j.
Replace starting motor assembly. k. Connect
engine
wiring harness connectors at
front of cowl.
I.
Connect wires to starting motor assembly, water
temperature and oil pressure sending units and alternator.
NOTE:
ON
ENGINES EQUIPPED WITH EX
HAUST
EMISSION CONTROL,
REPLACE
THE
AIR
PUMP,
AIR
DISTRIBUTOR
MANI
FOLD,
AND
ANTI-BACKFIRE (DIVERTER)
VALVE.
SEE
SECTION
Fl.
m. Replace radiator and radiator grille support
rods and connect coolant
hoses
to
engine.
Note:
Replace heater
hoses
if vehicle is equipped
with hot water heater.
n. Fill
radiator with coolant and
engine
with oil
(see
Lubrication
Chart).
o.
Install
air cleaner and connect carburetor air
hose.
p. Connect battery cables and start
engine,
q.
Install
hood
and road
test
vehicle.
D-103.
FINAL
IN-VEHICLE
ADJUSTMENTS
a.
Clean
battery terminals and check battery. b.
Check
ignition terminals and check battery.
c. Service carburetor air cleaner.
d.
Service positive crankcase ventilation valve.
e.
Check
fuel lines. f. Gap and install new
spark
plugs.
g.
Check
distributor
points
and capacitor; replace
if
necessary. 68
Page 69 of 376
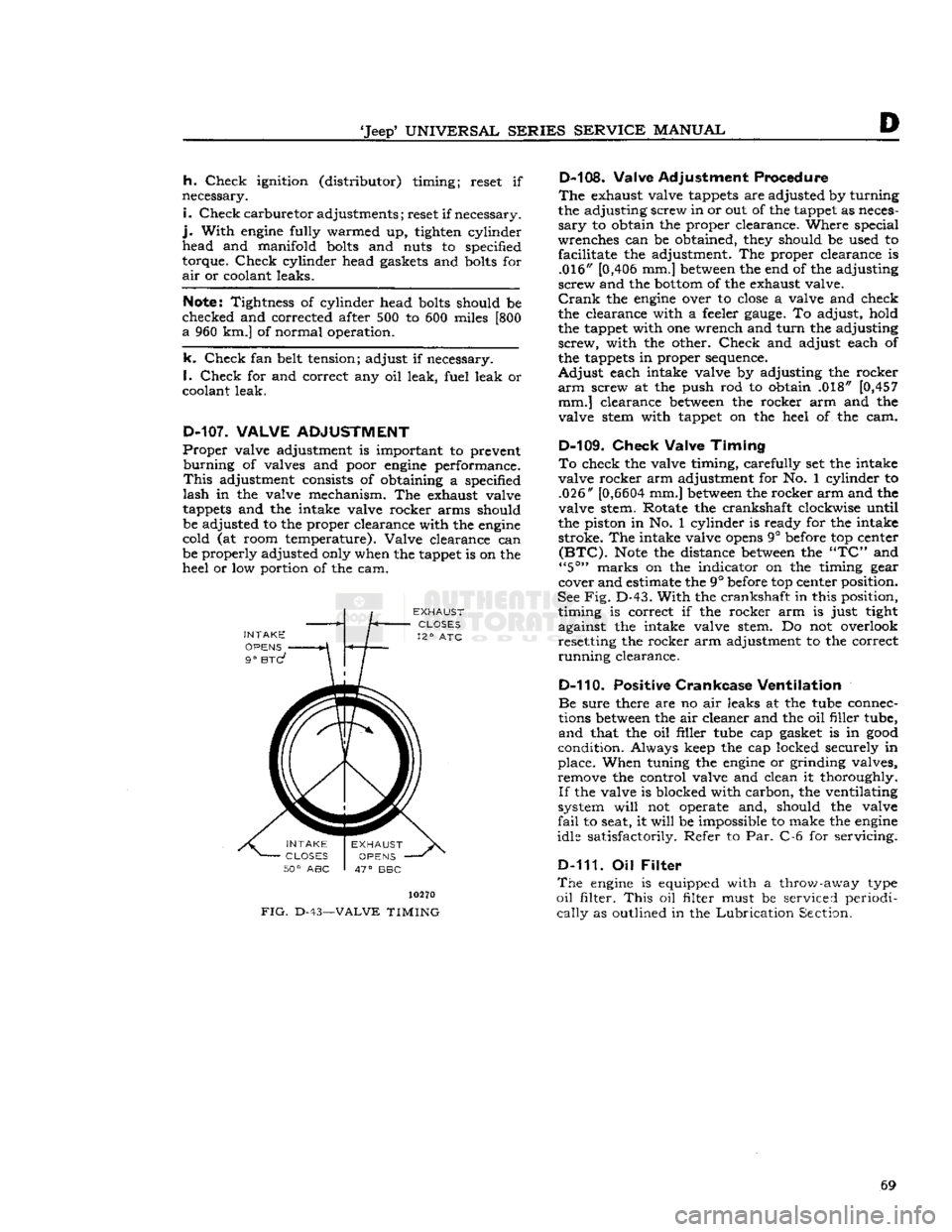
'Jeep9
UNIVERSAL
SERIES
SERVICE
MANUAL
h.
Check
ignition (distributor) timing; reset if
necessary.
i.
Check
carburetor
adjustments; reset if necessary,
j.
With
engine
fully warmed up, tighten cylinder
head and manifold
bolts
and nuts to specified
torque.
Check
cylinder head gaskets and
bolts
for
air
or coolant leaks.
Note:
Tightness of cylinder head
bolts
should be
checked and corrected after 500 to 600 miles [800
a
960 km.] of normal operation.
k.
Check
fan belt tension; adjust if necessary.
I.
Check
for and correct any oil leak, fuel leak or
coolant leak.
D-107.
VALVE
ADJUSTMENT
Proper
valve adjustment is important to prevent
burning
of valves and poor
engine
performance.
This
adjustment consists of obtaining a specified
lash
in the valve mechanism. The exhaust valve
tappets and the intake valve rocker arms should be adjusted to the proper clearance with the
engine
cold (at room temperature). Valve clearance can
be properly adjusted only when the tappet is on the
heel or low portion of the cam.
INTAKE
OPENS
9°
BTC?
FIG.
D-43-
10270
-VALVE
TIMING
D-108. Valve Adjustment Procedure
The
exhaust valve tappets are adjusted by turning
the adjusting screw in or out of the tappet as neces
sary
to obtain the proper clearance. Where special
wrenches can be obtained, they should be used to facilitate the adjustment. The proper clearance is .016" [0,406 mm.]
between
the end of the adjusting
screw and the
bottom
of the exhaust valve.
Crank
the
engine
over to
close
a valve and check
the clearance with a feeler
gauge.
To adjust, hold
the tappet with one wrench and
turn
the adjusting
screw,
with the other.
Check
and adjust each of
the tappets in proper sequence.
Adjust
each intake valve by adjusting the rocker
arm
screw at the push rod to obtain .018" [0,457 mm.] clearance
between
the rocker arm and the
valve stem with tappet on the heel of the cam.
D-109.
Check
Valve
Timing
To
check the valve timing, carefully set the intake
valve rocker arm adjustment for No. 1 cylinder to .026"
[0,6604
mm.]
between
the rocker arm and the
valve stem. Rotate the crankshaft clockwise until
the piston in No. 1 cylinder is ready for the intake stroke. The intake valve
opens
9° before top center
(BTC).
Note
the distance
between
the
"TC"
and
"5°"
marks on the indicator on the timing gear
cover and estimate the 9° before top center position.
See
Fig.
D-43.
With
the crankshaft in this position, timing is correct if the rocker arm is just tight
against the intake valve stem. Do not overlook resetting the rocker arm adjustment to the correct
running
clearance.
D-110. Positive
Crankcase
Ventilation
Be
sure there are no air leaks at the tube connec
tions
between
the air cleaner and the oil filler tube,
and
that the oil filler tube cap gasket is in
good
condition. Always keep the cap locked securely in
place. When tuning the
engine
or grinding valves, remove the control valve and clean it thoroughly.
If
the valve is blocked with carbon, the ventilating
system
will
not operate and, should the valve
fail
to seat, it
will
be impossible to make the
engine
idle satisfactorily. Refer to Par. C-6 for servicing.
D-111. Oil
Filter
The
engine
is equipped with a throw-away type
oil
filter.
This
oil filter must be serviced periodi
cally
as outlined in the
Lubrication
Section. 69
Page 70 of 376
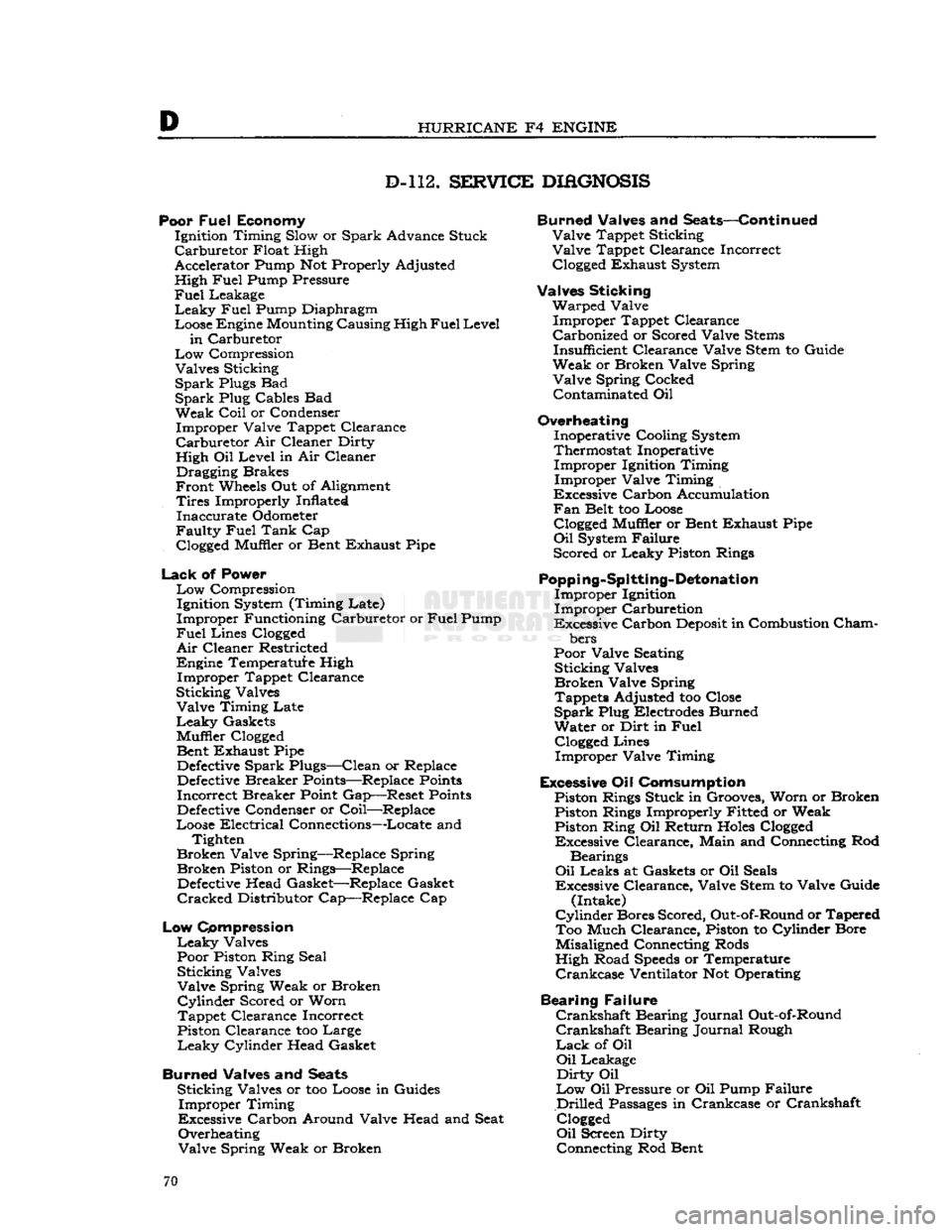
D
HURRICANE
F4
ENGINE
D-112.
SERVICE
DIAGNOSIS
Poor
Fuel
Economy Ignition Timing Slow or Spark Advance Stuck
Carburetor
Float High
Accelerator Pump Not Properly Adjusted
High
Fuel
Pump Pressure
Fuel
Leakage
Leaky
Fuel
Pump Diaphragm
Loose Engine Mounting Causing High
Fuel
Level
in
Carburetor
Low
Compression Valves Sticking
Spark
Plugs Bad
Spark
Plug Cables Bad Weak
Coil
or Condenser Improper Valve Tappet Clearance
Carburetor
Air Cleaner Dirty
High Oil Level in Air Cleaner Dragging Brakes
Front
Wheels Out of Alignment
Tires
Improperly Inflated Inaccurate Odometer
Faulty
Fuel
Tank
Cap
Clogged
Muffler or Bent Exhaust Pipe
Lack
of Power
Low
Compression Ignition System (Timing Late)
Improper Functioning Carburetor or
Fuel
Pump
Fuel
Lines
Clogged
Air
Cleaner Restricted
Engine Temperature High Improper Tappet Clearance
Sticking Valves Valve Timing Late
Leaky
Gaskets
Muffler
Clogged
Bent Exhaust Pipe
Defective
Spark Plugs—Clean or Replace
Defective
Breaker Points—Replace
Points
Incorrect Breaker Point Gap—Reset
Points
Defective
Condenser or Coil—Replace
Loose Electrical Connections—Locate and Tighten
Broken Valve Spring—Replace Spring Broken Piston or Rings—Replace
Defective
Head Gasket—Replace Gasket
Cracked
Distributor Cap—Replace Cap
Low
Compression
Leaky
Valves
Poor Piston Ring Seal Sticking Valves
Valve Spring Weak or Broken
Cylinder
Scored or Worn
Tappet Clearance Incorrect
Piston Clearance too Large
Leaky
Cylinder Head Gasket
Burned Valves and
Seats
Sticking Valves or too Loose in Guides Improper Timing
Excessive Carbon Around Valve Head and Seat Overheating
Valve Spring Weak or Broken Burned Valves and Seats—Continued
Valve Tappet Sticking
Valve Tappet Clearance Incorrect
Clogged
Exhaust System
Valves Sticking Warped Valve Improper Tappet Clearance
Carbonized or Scored Valve
Stems
Insufficient Clearance Valve Stem to Guide
Weak or Broken Valve Spring Valve Spring Cocked Contaminated Oil
Overheating Inoperative Cooling System
Thermostat Inoperative Improper Ignition Timing
Improper Valve Timing
Excessive Carbon Accumulation
Fan
Belt too Loose
Clogged
Muffler or Bent Exhaust Pipe
Oil
System Failure
Scored or Leaky Piston Rings
Popping-Spitting-Detonation
Improper Ignition
Improper Carburetion
Excessive Carbon
Deposit
in Combustion
Cham
bers
Poor Valve Seating Sticking Valves
Broken Valve Spring Tappets Adjusted too Close
Spark
Plug Electrodes Burned
Water or Dirt in
Fuel
Clogged
Lines Improper Valve Timing
Excessive Oil Comsumption Piston Rings Stuck in Grooves, Worn or Broken Piston Rings Improperly Fitted or Weak Piston Ring Oil Return
Holes
Clogged
Excessive Clearance, Main and Connecting Rod
Bearings
Oil
Leaks at Gaskets or Oil Seals
Excessive Clearance, Valve Stem to Valve Guide (Intake)
Cylinder
Bores Scored, Out-of-Round or Tapered Too Much Clearance, Piston to Cylinder Bore
Misaligned Connecting Rods
High Road
Speeds
or Temperature
Crankcase
Ventilator Not Operating
Bearing Failure
Crankshaft
Bearing Journal Out-of-Round
Crankshaft
Bearing Journal Rough
Lack
of Oil
Oil
Leakage
Dirty
Oil
Low
Oil Pressure or Oil Pump Failure
Drilled
Passages
in Crankcase or Crankshaft
Clogged
Oil
Screen Dirty Connecting Rod Bent 70
Page 71 of 376
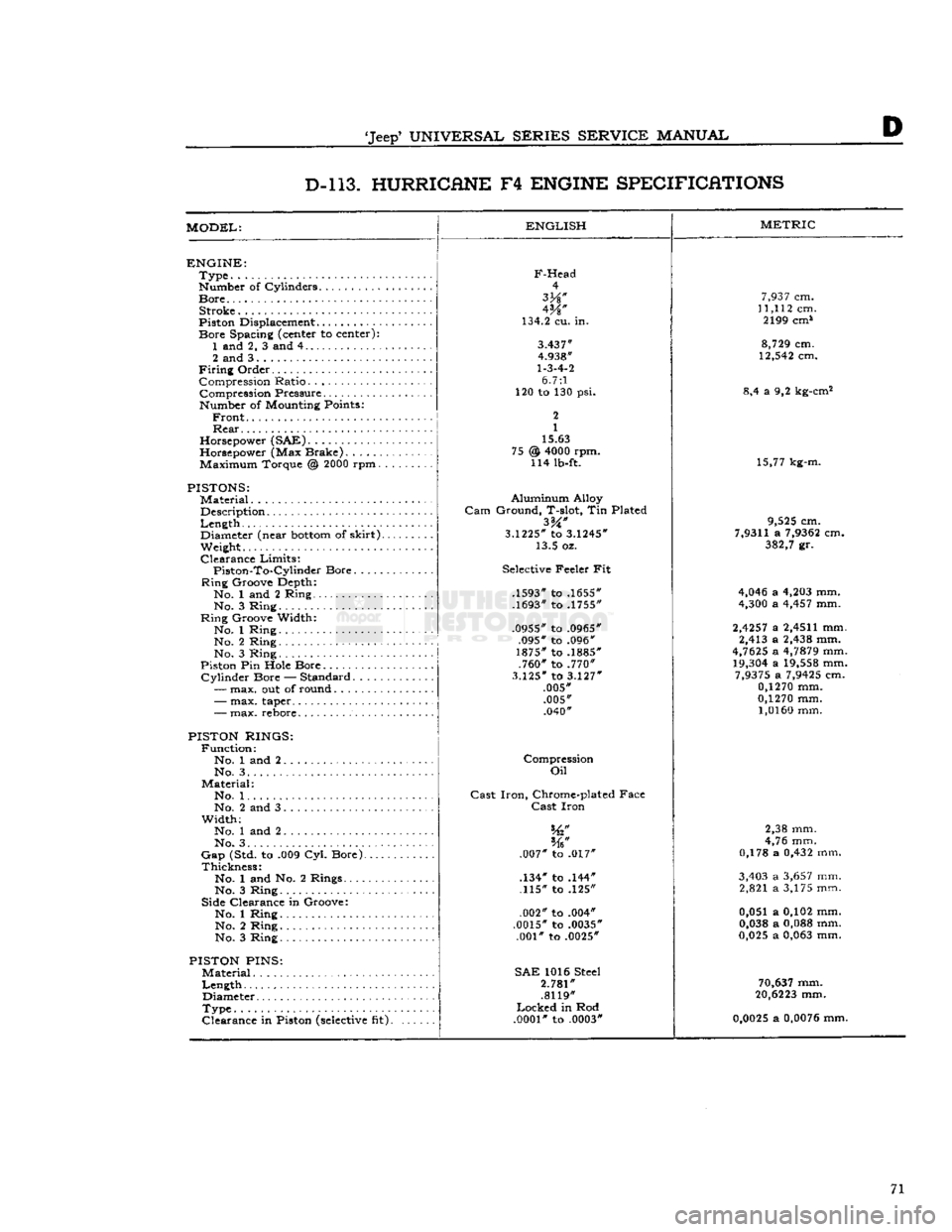
'Jeep*
UNIVERSAL
SERIES
SERVICE
MANUAL
D D-l 13. HURRICANE
F4
ENGINE SPECIFICATIONS
MODEL:
ENGLISH
ENGINE:
Type
Number of Cylinders
Bore
Stroke
Piston Displacement...........
Bore
Spacing (center to center): 1 and 2, 3 and 4
2 and 3
Firing
Order Compression Ratio Compression Pressure... .
Number of Mounting Points:
Front
Rear
Horsepower (SAE)
Horsepower (Max Brake) Maximum Torque @
2000
rpm.
PISTONS:
Material
Description
Length
,.
Diameter (near
bottom
of
skirt).
Weight.
Clearance
Limits:
Piston-To-Cylindcr
Bore
Ring
Groove Depth:
No. 1 and 2 Ring No. 3 Ring
Ring
Groove Width:
No. 1 Ring No. 2 Ring
No. 3 Ring
Piston Pin Hole Bore
Cylinder
Bore — Standard.....
—
max. out of round
F-Head
4
W
134.2 cu. in.
3.437"
4.938"
1-3-4-2
6.7:1
120 to 130 psi.
2
1
15.63
@
4000
rpm. 114 lb-ft. 75
-
max. taper..
-
max. rebore.
PISTON RINGS:
Function:
No. 1 and 2 No. 3. .
Material:
No. 1. .
No. 2 and 3
Width;
No. 1 and 2
No. 3. . . .
Gap
(Std. to .009 Cyl. Bore).
Thickness:
No. 1 and No. 2 Rings....
No. 3 Ring
Side Clearance in Groove:
No. 1 Ring No. 2 Ring
No. 3 Ring
PISTON
PINS:
Material
Length
Diameter
Type
Clearance
in Piston
(selective
fit).
Aluminum
Alloy
Gam
Ground, T-slot, Tin Plated
3.1225*
to
3.1245*
13.5 oz.
Selective Feeler Fit
.1593" to .1655"
.1693" to .1755"
.0955" to .0965" .095" to .096"
1875" to .1885" .760" to .770"
3.125"
to
3.127"
.005" .005" .040"
Compression
Oil
Cast
Iron,
Chrome-plated Face
Cast
Iron
.007" to .017"
.134" to .144" .115" to .125"
.002" to .004"
.0015" to .0035" .001" to .0025"
SAE
1016 Steel
2.781"
.8119"
Locked
in Rod
.0001"
to .0003"
METRIC
7,937
cm.
11,112
cm. 2199 cm*
8,729
cm.
12,542
cm.
8,4 a 9,2 kg-cm2
15,77 kg-m.
9,525
cm.
7,9311
a
7,9362
cm.
382,7
gr.
4,046
a
4,203
mm.
4,300
a
4,457
mm.
2,4257
a
2,4511
mm. 2,413 a
2,438
mm.
4,7625
a
4,7879
mm.
19,304
a
19,558
mm.
7,9375
a
7,9425
cm.
0,1270
mm.
0,1270
mm.
1,0160
mm.
2,38 mm.
4,76 mm.
0,178 a
0,432
mm.
3,403
a
3,657
mm. 2,821 a 3,175 mm.
0,051 a 0,102 mm.
0,038
a
0,088
mm.
0,025
a
0,063
mm.
70,637
mm.
20,6223
mm.
0,0025
a
0,0076
mm. 71
Page 72 of 376
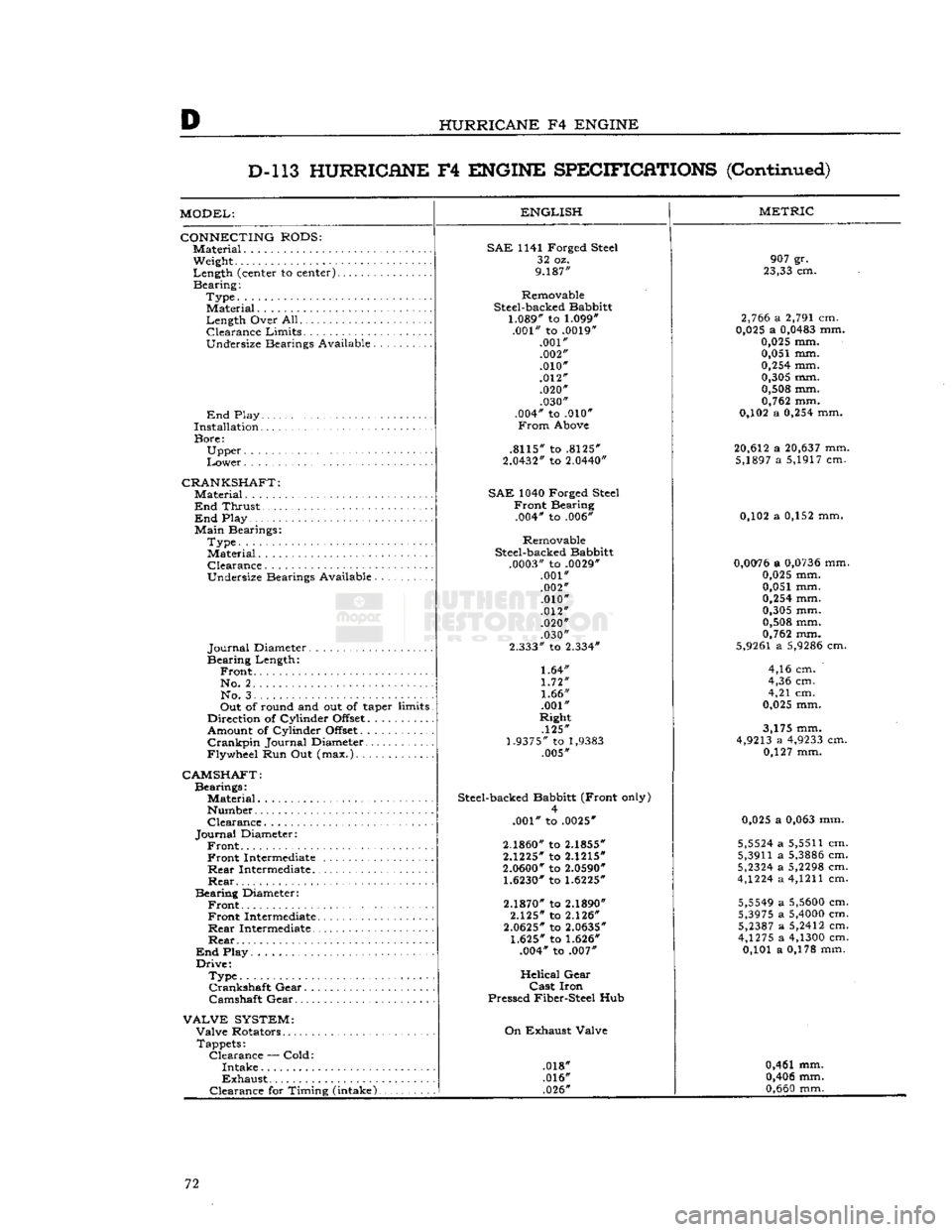
D
HURRICANE
F4
ENGINE
D-l
13
HURRICHNE
F4
ENGINE
SPECIFICATIONS
(Continued)
MODEL:
CONNECTING
RODS:
Material.
Weight
Length
(center to
center)......
Bearing:
Type.
Material
Length
Over
All
Clearance
Limits.
..........
Undersize
Bearings
Available
End
Play
Installation
Bore:
Upper
Lower
CRANKSHAFT:
Material....................
End
Thrust
End
Play
Main
Bearings:
Type.
Material
Clearance
Undersize
Bearings
Available
Journal
Diameter
Bearing
Length:
Front.
No.
2. . .
No.
3
Out
of
round
and out of taper
limits
Direction
of
Cylinder
Offset..........
Amount
of
Cylinder
Offset
Crankpin
Journal
Diameter
Flywheel
Run Out
(max.)
ENGLISH
CAMSHAFT:
Bearings:
Material..........
Number
Clearance.
Journal
Diameter:
Front Front
Intermediate.
Rear
Intermediate..
Rear
Bearing
Diameter:
Front Front
Intermediate.
Rear
Intermediate..
Rear
End
Play
Drive:
Type.............
Crankshaft
Gear.
. .
Camshaft
Gear
VALVE
SYSTEM:
Valve
Rotators
Tappets:
Clearance
—
Cold:
Intake
Exhaust
Clearance
for
Timing
(intake).
SAE
1141
Forged
Steel
32 oz.
9.187"
Removable
Steel-backed
Babbitt
1.089" to 1.099"
.001"
to .0019"
.001" .002"
.010"
.012" .020" .030"
.004"
to .010"
From
Above
.8115"
to .8125"
2.0432"
to 2.0440"
SAE
1040
Forged
Steel
Front
Bearing
.004*
to .006*
Removable
Steel-backed
Babbitt
.0003"
to .0029*
.001"
.002" .010"
.012" .020"
.030"
2.333"
to 2.334"
1.64"
1.72"
1.66"
.001"
Right
.125"
1.9375" to
1,9383
.005"
Steel-backed
Babbitt
(Front
only) 4
.001"
to .0025"
2.1860" to 2.1855"
2.1225"
to 2.1215"
2.0600" to 2.0590" 1.6230" to 1.6225"
2.1870" to 2.1890"
2.125"
to 2.126"
2.0625"
to 2.0635"
1.625" to 1.626"
.004*
to .007"
Helical
Gear
Cast
Iron
Pressed
Fiber-Steel
Hub
On
Exhaust
Valve
.018*
.016* .026"
METRIC
907
gr.
23,33 cm.
2,766 a 2,791 cm.
0,025 a 0,0483 mm.
0,025 mm. 0,051 mm.
0,254
mm.
0,305 mm. 0,508 mm.
0,762 mm.
0,102 a
0,254
mm.
20,612 a 20,637 mm. 5,1897 a 5,1917 cm.
0,102 a 0,152 mm,
0,0076 a 0,0736 mm. 0,025 mm.
0,051 mm.
0,254
mm.
0,305 mm.
0,508 mm.
0,762 mm.
5,9261
a 5,9286 cm.
4,16 cm.
4,36 cm.
4,21 cm.
0,025 mm.
3,175 mm.
4,9213 a 4,9233 cm. 0,127 mm.
0,025 a
0,063
mm.
5,5524 a
5,5511
cm.
5,3911
a 5,3886 cm.
5,2324 a 5,2298 cm.
4,1224 a
4,1211
cm.
5,5549 a 5,5600 cm.
5,3975 a 5,4000 cm. 5,2387 a 5,2412 cm.
4,1275 a 4,1300 cm. 0,101 a 0,178 mm.
0,461 mm. 0,406 mm.
0,660
mm. 72
Page 73 of 376
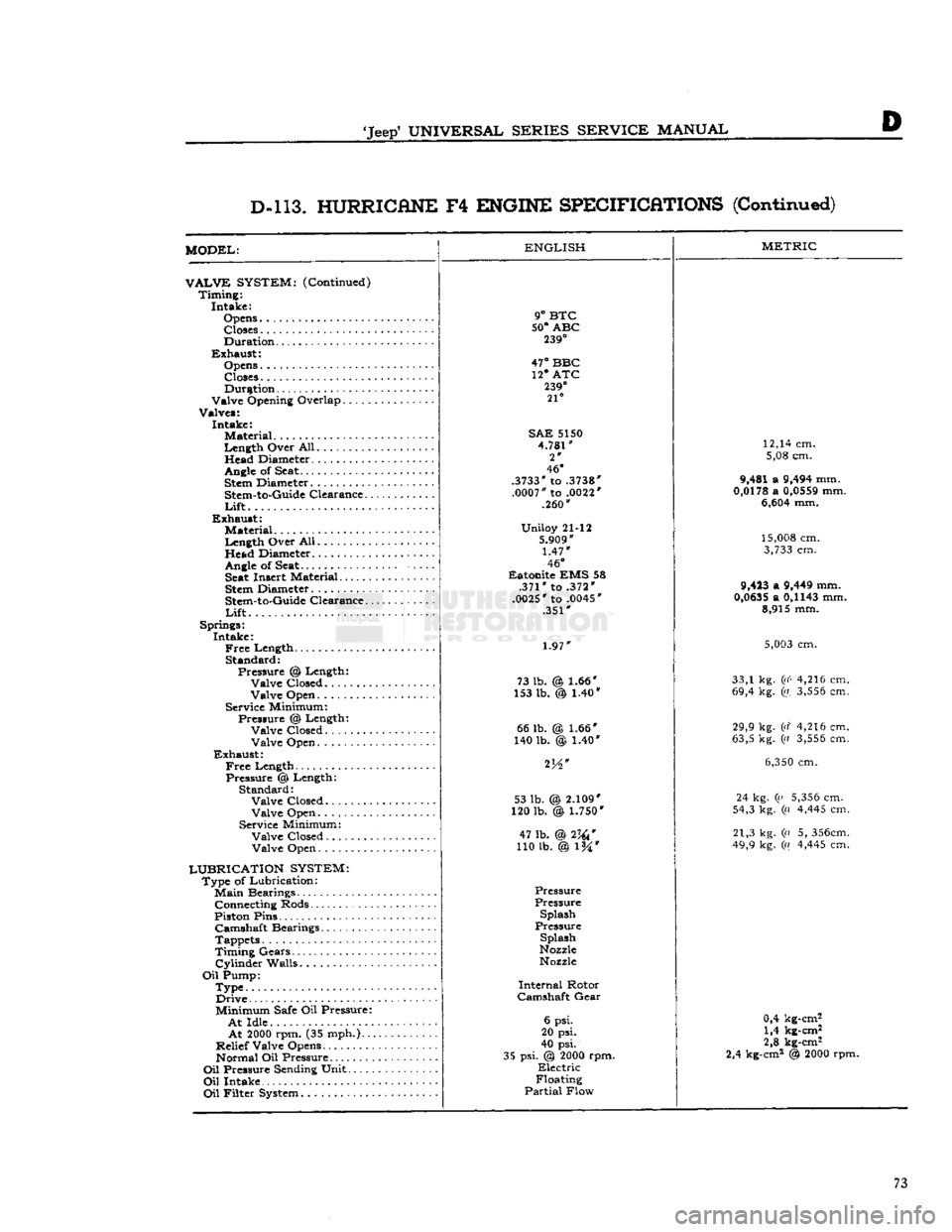
'Jeep'
UNIVERSAL SERIES SERVICE
MANUAL
D
D-l 13. HURRICANE
F4
ENGINE SPECIFICATIONS
(Continued)
MODEL:
VALVE
SYSTEM:
(Continued) Timing: Intake:
Opens Closes
Duration
Exhaust: Opens
Closes Duration
Valve Opening Overlap
Valves: Intake: Material
Length Over All. Head Diameter.
.........
Angle
of Seat.
Stem
Diameter
Stem-to-Guide
Clearance..
Lift
Exhaust: Material
Length Over All Head Diameter
Angle
of
Seat Seat
Insert Material
Stem
Diameter
Stem-to-Guide
Clearance..
Lift
Springs: Intake:
Free
Length Standard: Pressure % Length: Valve Closed........
Valve Open
Service Minimum: Pressure @ Length: Valve Closed Valve Open
Exhaust:
Free
Length Pressure @ Length: Standard: Valve Closed
Valve Open
Service Minimum: Valve Closed. Valve Open
LUBRICATION SYSTEM:
Type of Lubrication:
Main
Bearings Connecting Rods
Piston Pins Camshaft Bearings
Tappets
Timing Gears.'.
Cylinder
Walls
Oil
Pump: Type Drive
Minimum
Safe
Oil Pressure:
At
Idle
At
2000
rpm. (35 mph.)..
Relief Valve Opens Normal Oil Pressure
Oil
Pressure
Sending
Unit
Oil
Intake
Oil
Filter
System
ENGLISH
9°
BTC
50°
ABC
239°
47°
BBC 12* ATC
239°
21°
SAE
5150
4.781"
2*
46°
.3733"
to
.3738"
.0007"
to
.0022'
.260"
Uniloy 21-12
5.909"
1.47"
46°
Eatonite EMS 58 .371" to .372"
.0025"
to
.0045'
.351"
1.97"
73 lb. @ 1.66"
153 lb. @ 1.40* 66 lb.
140 lb. 1.66*
)
1.40" 53 lb. (
120 lb.
2.109"
\
1.750*
47 lb. @2W
110 lb. @ l%*
Pressure
Pressure Splash
Pressure
Splash
Nozzle
Nozzle
Internal
Rotor
Camshaft
Gear
6 psi.
20 psi.
40 psi.
35 psi. @
2000
rpm.
Electric
Floating
Partial
Flow
METRIC
12,14 cm. 5,08 cm.
9,481 a
9,494
mm.
0,0178
a
0,0559
mm.
6,604
mm.
15,008
cm.
3,733
cm.
9,423
a
9,449
mm.
0,0635
a
0,1143
mm. 8,915 mm.
5,003
cm.
33,1 kg.
(i(<
4,216 cm.
69,4 kg. (a.
3,556
cm.
29,9 kg. (d 4,216 cm.
63,5 kg. ((i
3,556
cm.
6,350
cm.
24 kg. (a
5,356
cm.
54,3 kg. (a
4,445
cm.
21,3 kg. (n 5,
356cm.
49,9 kg. («
4,445
cm.
0,4 kg-cm2 1,4 kg-cm2
2,8 kg-cm2
2,4 kg-cm2 @
2000
rpm. 73