connector JEEP GRAND CHEROKEE 2002 WJ / 2.G Workshop Manual
[x] Cancel search | Manufacturer: JEEP, Model Year: 2002, Model line: GRAND CHEROKEE, Model: JEEP GRAND CHEROKEE 2002 WJ / 2.GPages: 2199, PDF Size: 76.01 MB
Page 1764 of 2199
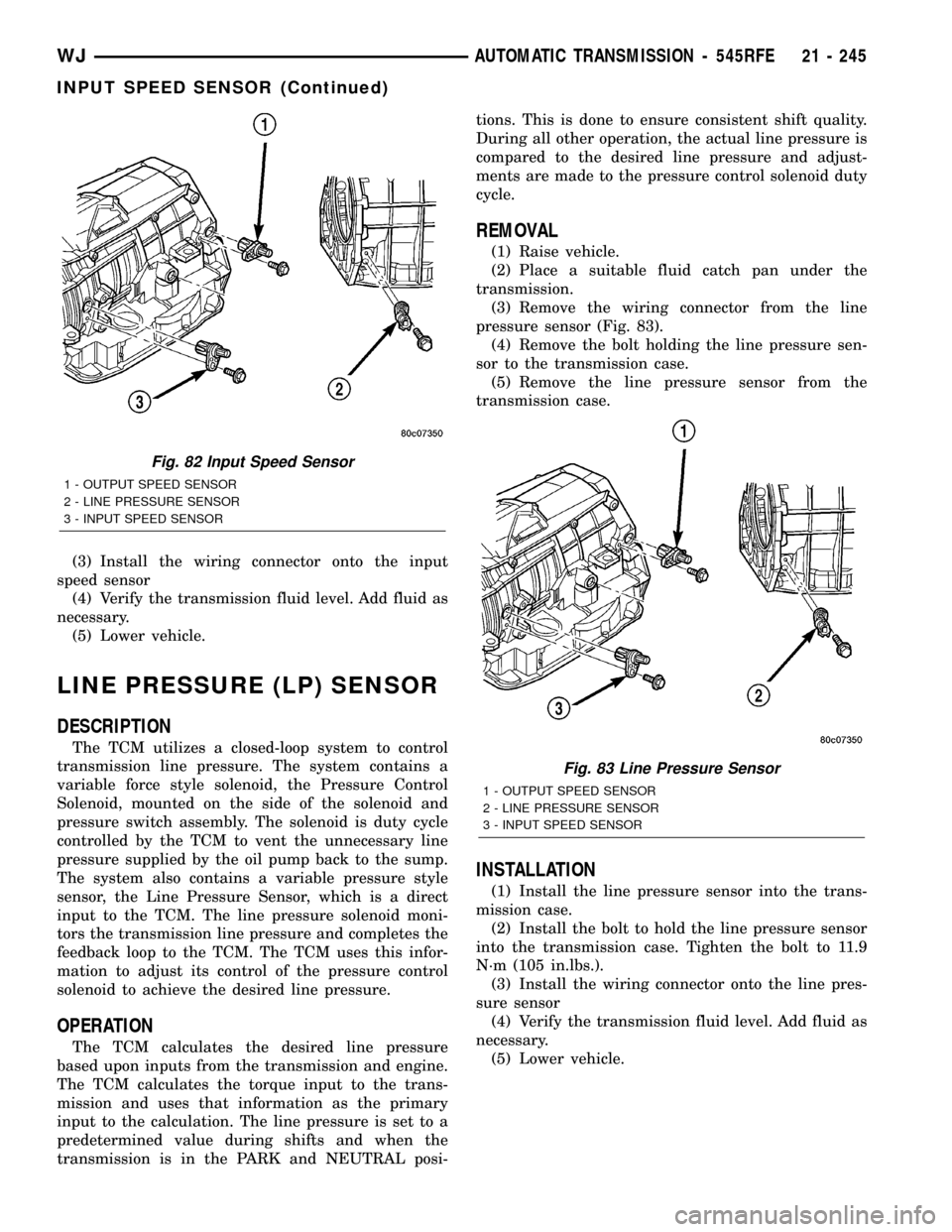
(3) Install the wiring connector onto the input
speed sensor
(4) Verify the transmission fluid level. Add fluid as
necessary.
(5) Lower vehicle.
LINE PRESSURE (LP) SENSOR
DESCRIPTION
The TCM utilizes a closed-loop system to control
transmission line pressure. The system contains a
variable force style solenoid, the Pressure Control
Solenoid, mounted on the side of the solenoid and
pressure switch assembly. The solenoid is duty cycle
controlled by the TCM to vent the unnecessary line
pressure supplied by the oil pump back to the sump.
The system also contains a variable pressure style
sensor, the Line Pressure Sensor, which is a direct
input to the TCM. The line pressure solenoid moni-
tors the transmission line pressure and completes the
feedback loop to the TCM. The TCM uses this infor-
mation to adjust its control of the pressure control
solenoid to achieve the desired line pressure.
OPERATION
The TCM calculates the desired line pressure
based upon inputs from the transmission and engine.
The TCM calculates the torque input to the trans-
mission and uses that information as the primary
input to the calculation. The line pressure is set to a
predetermined value during shifts and when the
transmission is in the PARK and NEUTRAL posi-tions. This is done to ensure consistent shift quality.
During all other operation, the actual line pressure is
compared to the desired line pressure and adjust-
ments are made to the pressure control solenoid duty
cycle.
REMOVAL
(1) Raise vehicle.
(2) Place a suitable fluid catch pan under the
transmission.
(3) Remove the wiring connector from the line
pressure sensor (Fig. 83).
(4) Remove the bolt holding the line pressure sen-
sor to the transmission case.
(5) Remove the line pressure sensor from the
transmission case.
INSTALLATION
(1) Install the line pressure sensor into the trans-
mission case.
(2) Install the bolt to hold the line pressure sensor
into the transmission case. Tighten the bolt to 11.9
N´m (105 in.lbs.).
(3) Install the wiring connector onto the line pres-
sure sensor
(4) Verify the transmission fluid level. Add fluid as
necessary.
(5) Lower vehicle.
Fig. 82 Input Speed Sensor
1 - OUTPUT SPEED SENSOR
2 - LINE PRESSURE SENSOR
3 - INPUT SPEED SENSOR
Fig. 83 Line Pressure Sensor
1 - OUTPUT SPEED SENSOR
2 - LINE PRESSURE SENSOR
3 - INPUT SPEED SENSOR
WJAUTOMATIC TRANSMISSION - 545RFE 21 - 245
INPUT SPEED SENSOR (Continued)
Page 1773 of 2199
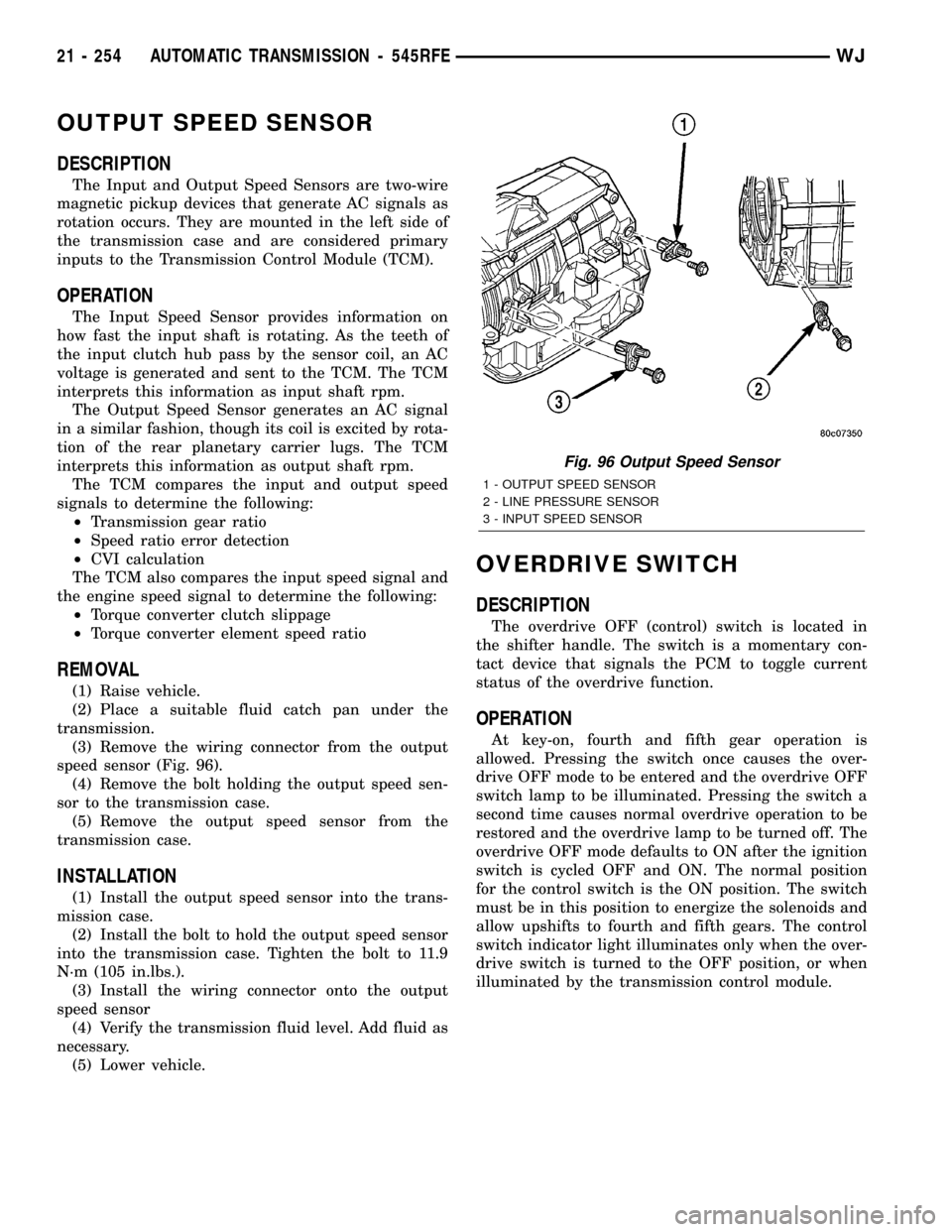
OUTPUT SPEED SENSOR
DESCRIPTION
The Input and Output Speed Sensors are two-wire
magnetic pickup devices that generate AC signals as
rotation occurs. They are mounted in the left side of
the transmission case and are considered primary
inputs to the Transmission Control Module (TCM).
OPERATION
The Input Speed Sensor provides information on
how fast the input shaft is rotating. As the teeth of
the input clutch hub pass by the sensor coil, an AC
voltage is generated and sent to the TCM. The TCM
interprets this information as input shaft rpm.
The Output Speed Sensor generates an AC signal
in a similar fashion, though its coil is excited by rota-
tion of the rear planetary carrier lugs. The TCM
interprets this information as output shaft rpm.
The TCM compares the input and output speed
signals to determine the following:
²Transmission gear ratio
²Speed ratio error detection
²CVI calculation
The TCM also compares the input speed signal and
the engine speed signal to determine the following:
²Torque converter clutch slippage
²Torque converter element speed ratio
REMOVAL
(1) Raise vehicle.
(2) Place a suitable fluid catch pan under the
transmission.
(3) Remove the wiring connector from the output
speed sensor (Fig. 96).
(4) Remove the bolt holding the output speed sen-
sor to the transmission case.
(5) Remove the output speed sensor from the
transmission case.
INSTALLATION
(1) Install the output speed sensor into the trans-
mission case.
(2) Install the bolt to hold the output speed sensor
into the transmission case. Tighten the bolt to 11.9
N´m (105 in.lbs.).
(3) Install the wiring connector onto the output
speed sensor
(4) Verify the transmission fluid level. Add fluid as
necessary.
(5) Lower vehicle.
OVERDRIVE SWITCH
DESCRIPTION
The overdrive OFF (control) switch is located in
the shifter handle. The switch is a momentary con-
tact device that signals the PCM to toggle current
status of the overdrive function.
OPERATION
At key-on, fourth and fifth gear operation is
allowed. Pressing the switch once causes the over-
drive OFF mode to be entered and the overdrive OFF
switch lamp to be illuminated. Pressing the switch a
second time causes normal overdrive operation to be
restored and the overdrive lamp to be turned off. The
overdrive OFF mode defaults to ON after the ignition
switch is cycled OFF and ON. The normal position
for the control switch is the ON position. The switch
must be in this position to energize the solenoids and
allow upshifts to fourth and fifth gears. The control
switch indicator light illuminates only when the over-
drive switch is turned to the OFF position, or when
illuminated by the transmission control module.
Fig. 96 Output Speed Sensor
1 - OUTPUT SPEED SENSOR
2 - LINE PRESSURE SENSOR
3 - INPUT SPEED SENSOR
21 - 254 AUTOMATIC TRANSMISSION - 545RFEWJ
Page 1774 of 2199
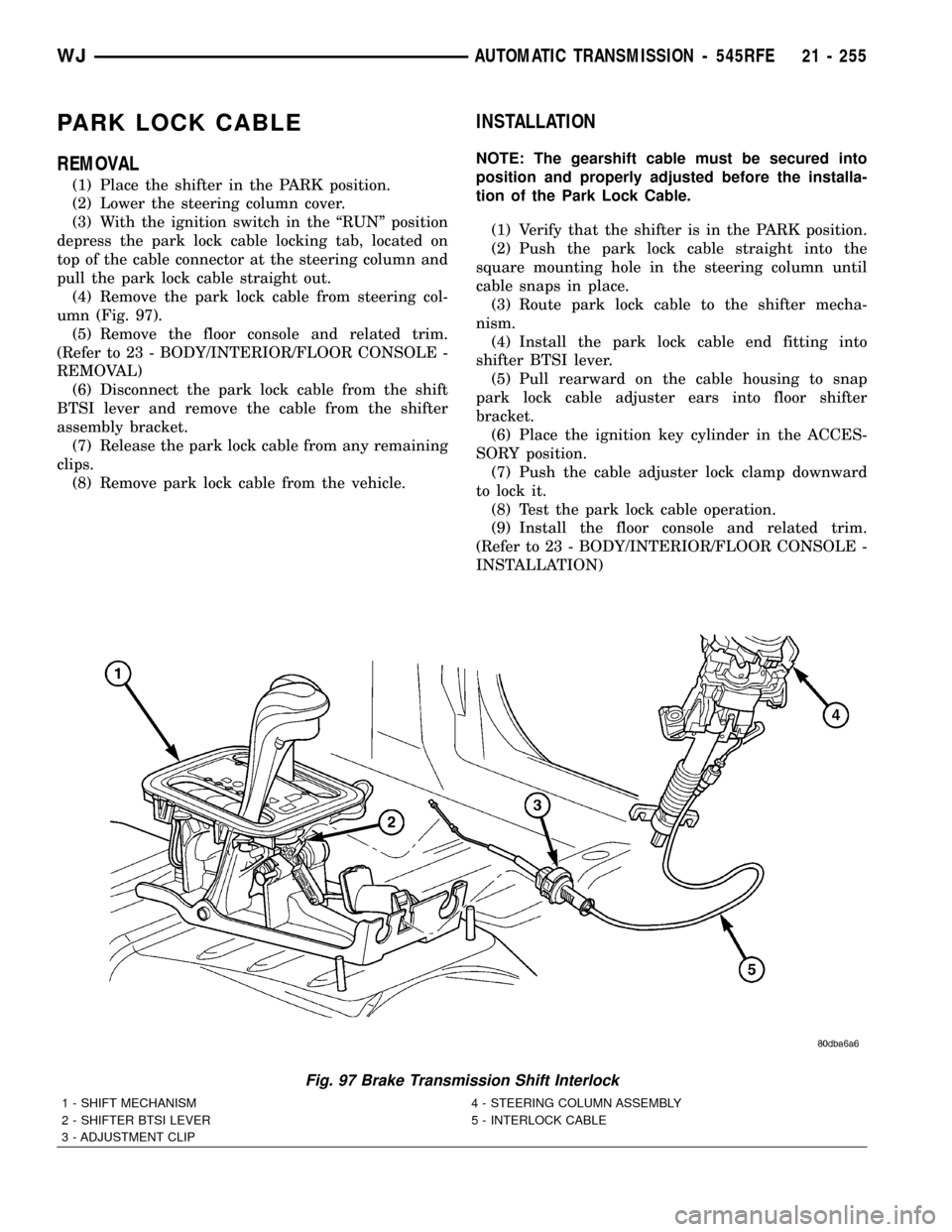
PARK LOCK CABLE
REMOVAL
(1) Place the shifter in the PARK position.
(2) Lower the steering column cover.
(3) With the ignition switch in the ªRUNº position
depress the park lock cable locking tab, located on
top of the cable connector at the steering column and
pull the park lock cable straight out.
(4) Remove the park lock cable from steering col-
umn (Fig. 97).
(5) Remove the floor console and related trim.
(Refer to 23 - BODY/INTERIOR/FLOOR CONSOLE -
REMOVAL)
(6) Disconnect the park lock cable from the shift
BTSI lever and remove the cable from the shifter
assembly bracket.
(7) Release the park lock cable from any remaining
clips.
(8) Remove park lock cable from the vehicle.
INSTALLATION
NOTE: The gearshift cable must be secured into
position and properly adjusted before the installa-
tion of the Park Lock Cable.
(1) Verify that the shifter is in the PARK position.
(2) Push the park lock cable straight into the
square mounting hole in the steering column until
cable snaps in place.
(3) Route park lock cable to the shifter mecha-
nism.
(4) Install the park lock cable end fitting into
shifter BTSI lever.
(5) Pull rearward on the cable housing to snap
park lock cable adjuster ears into floor shifter
bracket.
(6) Place the ignition key cylinder in the ACCES-
SORY position.
(7) Push the cable adjuster lock clamp downward
to lock it.
(8) Test the park lock cable operation.
(9) Install the floor console and related trim.
(Refer to 23 - BODY/INTERIOR/FLOOR CONSOLE -
INSTALLATION)
Fig. 97 Brake Transmission Shift Interlock
1 - SHIFT MECHANISM 4 - STEERING COLUMN ASSEMBLY
2 - SHIFTER BTSI LEVER 5 - INTERLOCK CABLE
3 - ADJUSTMENT CLIP
WJAUTOMATIC TRANSMISSION - 545RFE 21 - 255
Page 1780 of 2199
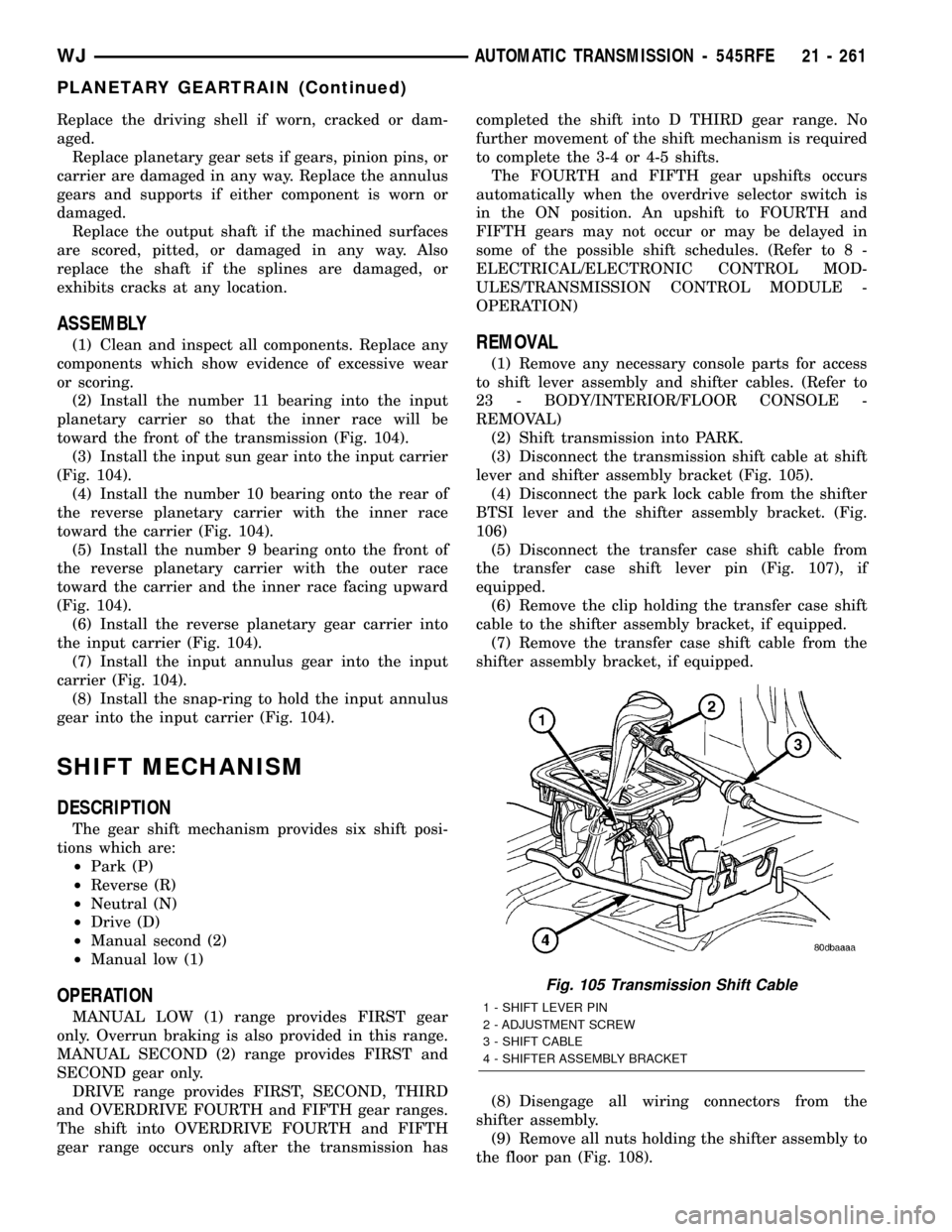
Replace the driving shell if worn, cracked or dam-
aged.
Replace planetary gear sets if gears, pinion pins, or
carrier are damaged in any way. Replace the annulus
gears and supports if either component is worn or
damaged.
Replace the output shaft if the machined surfaces
are scored, pitted, or damaged in any way. Also
replace the shaft if the splines are damaged, or
exhibits cracks at any location.
ASSEMBLY
(1) Clean and inspect all components. Replace any
components which show evidence of excessive wear
or scoring.
(2) Install the number 11 bearing into the input
planetary carrier so that the inner race will be
toward the front of the transmission (Fig. 104).
(3) Install the input sun gear into the input carrier
(Fig. 104).
(4) Install the number 10 bearing onto the rear of
the reverse planetary carrier with the inner race
toward the carrier (Fig. 104).
(5) Install the number 9 bearing onto the front of
the reverse planetary carrier with the outer race
toward the carrier and the inner race facing upward
(Fig. 104).
(6) Install the reverse planetary gear carrier into
the input carrier (Fig. 104).
(7) Install the input annulus gear into the input
carrier (Fig. 104).
(8) Install the snap-ring to hold the input annulus
gear into the input carrier (Fig. 104).
SHIFT MECHANISM
DESCRIPTION
The gear shift mechanism provides six shift posi-
tions which are:
²Park (P)
²Reverse (R)
²Neutral (N)
²Drive (D)
²Manual second (2)
²Manual low (1)
OPERATION
MANUAL LOW (1) range provides FIRST gear
only. Overrun braking is also provided in this range.
MANUAL SECOND (2) range provides FIRST and
SECOND gear only.
DRIVE range provides FIRST, SECOND, THIRD
and OVERDRIVE FOURTH and FIFTH gear ranges.
The shift into OVERDRIVE FOURTH and FIFTH
gear range occurs only after the transmission hascompleted the shift into D THIRD gear range. No
further movement of the shift mechanism is required
to complete the 3-4 or 4-5 shifts.
The FOURTH and FIFTH gear upshifts occurs
automatically when the overdrive selector switch is
in the ON position. An upshift to FOURTH and
FIFTH gears may not occur or may be delayed in
some of the possible shift schedules. (Refer to 8 -
ELECTRICAL/ELECTRONIC CONTROL MOD-
ULES/TRANSMISSION CONTROL MODULE -
OPERATION)
REMOVAL
(1) Remove any necessary console parts for access
to shift lever assembly and shifter cables. (Refer to
23 - BODY/INTERIOR/FLOOR CONSOLE -
REMOVAL)
(2) Shift transmission into PARK.
(3) Disconnect the transmission shift cable at shift
lever and shifter assembly bracket (Fig. 105).
(4) Disconnect the park lock cable from the shifter
BTSI lever and the shifter assembly bracket. (Fig.
106)
(5) Disconnect the transfer case shift cable from
the transfer case shift lever pin (Fig. 107), if
equipped.
(6) Remove the clip holding the transfer case shift
cable to the shifter assembly bracket, if equipped.
(7) Remove the transfer case shift cable from the
shifter assembly bracket, if equipped.
(8) Disengage all wiring connectors from the
shifter assembly.
(9) Remove all nuts holding the shifter assembly to
the floor pan (Fig. 108).
Fig. 105 Transmission Shift Cable
1 - SHIFT LEVER PIN
2 - ADJUSTMENT SCREW
3 - SHIFT CABLE
4 - SHIFTER ASSEMBLY BRACKET
WJAUTOMATIC TRANSMISSION - 545RFE 21 - 261
PLANETARY GEARTRAIN (Continued)
Page 1782 of 2199
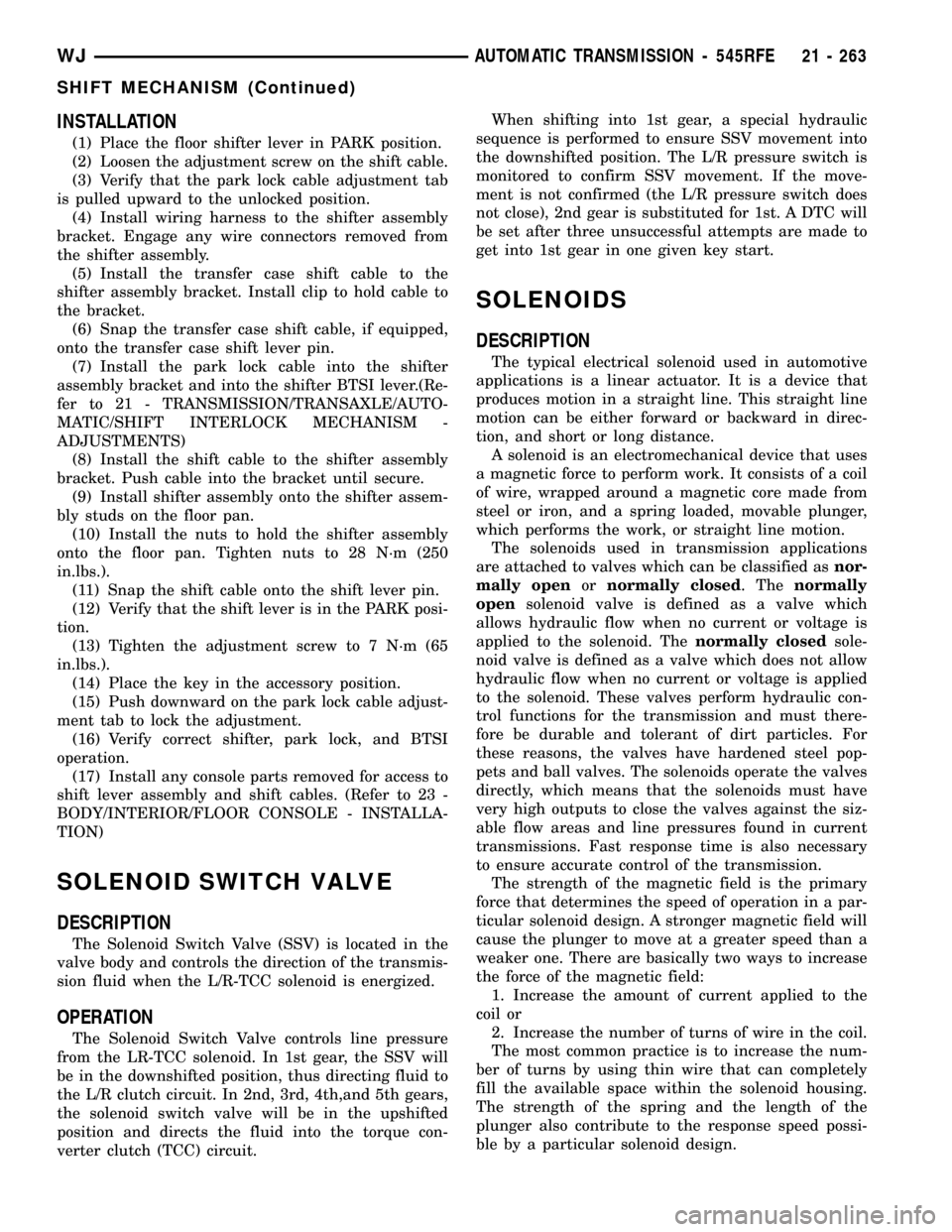
INSTALLATION
(1) Place the floor shifter lever in PARK position.
(2) Loosen the adjustment screw on the shift cable.
(3) Verify that the park lock cable adjustment tab
is pulled upward to the unlocked position.
(4) Install wiring harness to the shifter assembly
bracket. Engage any wire connectors removed from
the shifter assembly.
(5) Install the transfer case shift cable to the
shifter assembly bracket. Install clip to hold cable to
the bracket.
(6) Snap the transfer case shift cable, if equipped,
onto the transfer case shift lever pin.
(7) Install the park lock cable into the shifter
assembly bracket and into the shifter BTSI lever.(Re-
fer to 21 - TRANSMISSION/TRANSAXLE/AUTO-
MATIC/SHIFT INTERLOCK MECHANISM -
ADJUSTMENTS)
(8) Install the shift cable to the shifter assembly
bracket. Push cable into the bracket until secure.
(9) Install shifter assembly onto the shifter assem-
bly studs on the floor pan.
(10) Install the nuts to hold the shifter assembly
onto the floor pan. Tighten nuts to 28 N´m (250
in.lbs.).
(11) Snap the shift cable onto the shift lever pin.
(12) Verify that the shift lever is in the PARK posi-
tion.
(13) Tighten the adjustment screw to 7 N´m (65
in.lbs.).
(14) Place the key in the accessory position.
(15) Push downward on the park lock cable adjust-
ment tab to lock the adjustment.
(16) Verify correct shifter, park lock, and BTSI
operation.
(17) Install any console parts removed for access to
shift lever assembly and shift cables. (Refer to 23 -
BODY/INTERIOR/FLOOR CONSOLE - INSTALLA-
TION)
SOLENOID SWITCH VALVE
DESCRIPTION
The Solenoid Switch Valve (SSV) is located in the
valve body and controls the direction of the transmis-
sion fluid when the L/R-TCC solenoid is energized.
OPERATION
The Solenoid Switch Valve controls line pressure
from the LR-TCC solenoid. In 1st gear, the SSV will
be in the downshifted position, thus directing fluid to
the L/R clutch circuit. In 2nd, 3rd, 4th,and 5th gears,
the solenoid switch valve will be in the upshifted
position and directs the fluid into the torque con-
verter clutch (TCC) circuit.When shifting into 1st gear, a special hydraulic
sequence is performed to ensure SSV movement into
the downshifted position. The L/R pressure switch is
monitored to confirm SSV movement. If the move-
ment is not confirmed (the L/R pressure switch does
not close), 2nd gear is substituted for 1st. A DTC will
be set after three unsuccessful attempts are made to
get into 1st gear in one given key start.
SOLENOIDS
DESCRIPTION
The typical electrical solenoid used in automotive
applications is a linear actuator. It is a device that
produces motion in a straight line. This straight line
motion can be either forward or backward in direc-
tion, and short or long distance.
A solenoid is an electromechanical device that uses
a magnetic force to perform work. It consists of a coil
of wire, wrapped around a magnetic core made from
steel or iron, and a spring loaded, movable plunger,
which performs the work, or straight line motion.
The solenoids used in transmission applications
are attached to valves which can be classified asnor-
mally openornormally closed. Thenormally
opensolenoid valve is defined as a valve which
allows hydraulic flow when no current or voltage is
applied to the solenoid. Thenormally closedsole-
noid valve is defined as a valve which does not allow
hydraulic flow when no current or voltage is applied
to the solenoid. These valves perform hydraulic con-
trol functions for the transmission and must there-
fore be durable and tolerant of dirt particles. For
these reasons, the valves have hardened steel pop-
pets and ball valves. The solenoids operate the valves
directly, which means that the solenoids must have
very high outputs to close the valves against the siz-
able flow areas and line pressures found in current
transmissions. Fast response time is also necessary
to ensure accurate control of the transmission.
The strength of the magnetic field is the primary
force that determines the speed of operation in a par-
ticular solenoid design. A stronger magnetic field will
cause the plunger to move at a greater speed than a
weaker one. There are basically two ways to increase
the force of the magnetic field:
1. Increase the amount of current applied to the
coil or
2. Increase the number of turns of wire in the coil.
The most common practice is to increase the num-
ber of turns by using thin wire that can completely
fill the available space within the solenoid housing.
The strength of the spring and the length of the
plunger also contribute to the response speed possi-
ble by a particular solenoid design.
WJAUTOMATIC TRANSMISSION - 545RFE 21 - 263
SHIFT MECHANISM (Continued)
Page 1790 of 2199
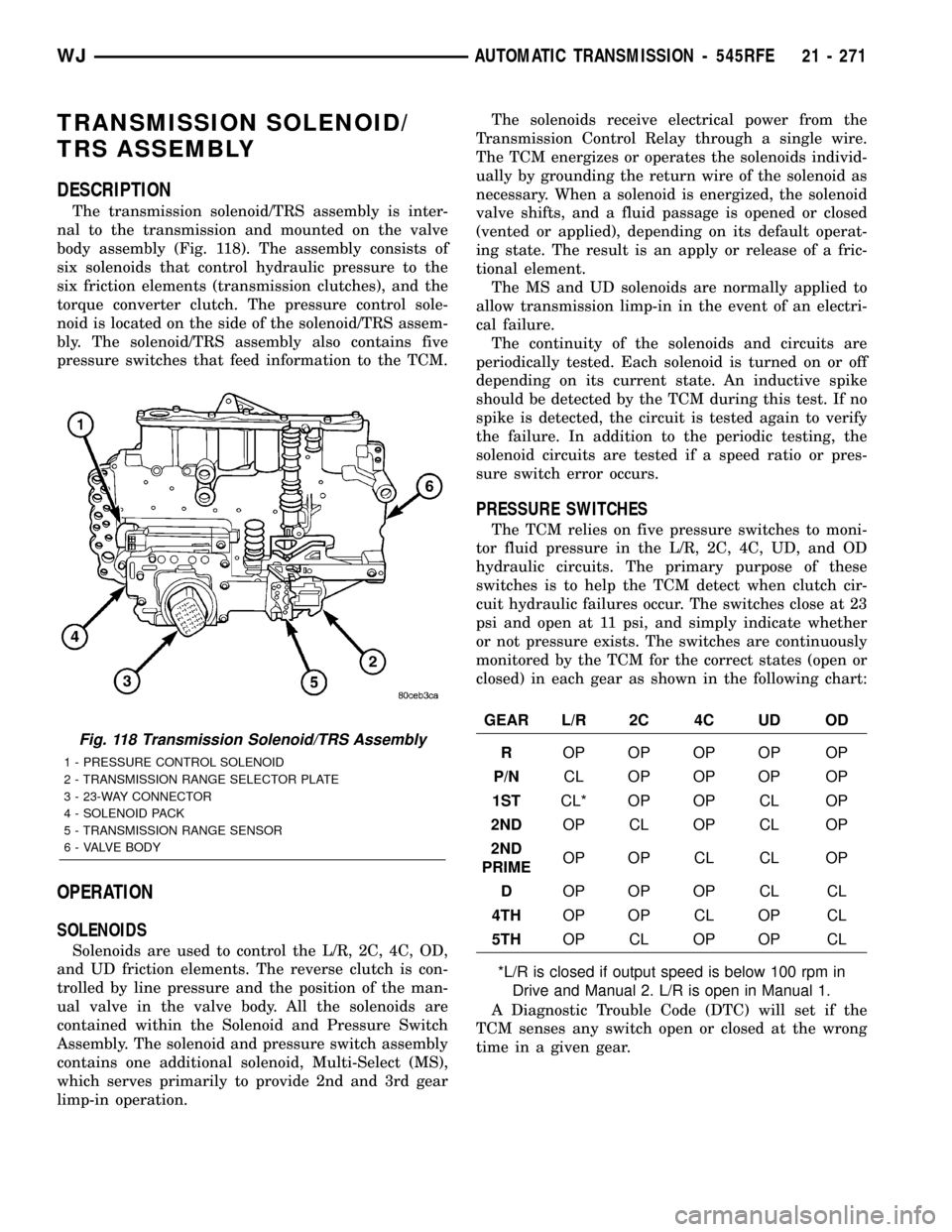
TRANSMISSION SOLENOID/
TRS ASSEMBLY
DESCRIPTION
The transmission solenoid/TRS assembly is inter-
nal to the transmission and mounted on the valve
body assembly (Fig. 118). The assembly consists of
six solenoids that control hydraulic pressure to the
six friction elements (transmission clutches), and the
torque converter clutch. The pressure control sole-
noid is located on the side of the solenoid/TRS assem-
bly. The solenoid/TRS assembly also contains five
pressure switches that feed information to the TCM.
OPERATION
SOLENOIDS
Solenoids are used to control the L/R, 2C, 4C, OD,
and UD friction elements. The reverse clutch is con-
trolled by line pressure and the position of the man-
ual valve in the valve body. All the solenoids are
contained within the Solenoid and Pressure Switch
Assembly. The solenoid and pressure switch assembly
contains one additional solenoid, Multi-Select (MS),
which serves primarily to provide 2nd and 3rd gear
limp-in operation.The solenoids receive electrical power from the
Transmission Control Relay through a single wire.
The TCM energizes or operates the solenoids individ-
ually by grounding the return wire of the solenoid as
necessary. When a solenoid is energized, the solenoid
valve shifts, and a fluid passage is opened or closed
(vented or applied), depending on its default operat-
ing state. The result is an apply or release of a fric-
tional element.
The MS and UD solenoids are normally applied to
allow transmission limp-in in the event of an electri-
cal failure.
The continuity of the solenoids and circuits are
periodically tested. Each solenoid is turned on or off
depending on its current state. An inductive spike
should be detected by the TCM during this test. If no
spike is detected, the circuit is tested again to verify
the failure. In addition to the periodic testing, the
solenoid circuits are tested if a speed ratio or pres-
sure switch error occurs.
PRESSURE SWITCHES
The TCM relies on five pressure switches to moni-
tor fluid pressure in the L/R, 2C, 4C, UD, and OD
hydraulic circuits. The primary purpose of these
switches is to help the TCM detect when clutch cir-
cuit hydraulic failures occur. The switches close at 23
psi and open at 11 psi, and simply indicate whether
or not pressure exists. The switches are continuously
monitored by the TCM for the correct states (open or
closed) in each gear as shown in the following chart:
GEAR L/R 2C 4C UD OD
ROP OP OP OP OP
P/NCL OP OP OP OP
1STCL* OP OP CL OP
2NDOP CL OP CL OP
2ND
PRIMEOP OP CL CL OP
DOP OP OP CL CL
4THOP OP CL OP CL
5THOP CL OP OP CL
*L/R is closed if output speed is below 100 rpm in
Drive and Manual 2. L/R is open in Manual 1.
A Diagnostic Trouble Code (DTC) will set if the
TCM senses any switch open or closed at the wrong
time in a given gear.
Fig. 118 Transmission Solenoid/TRS Assembly
1 - PRESSURE CONTROL SOLENOID
2 - TRANSMISSION RANGE SELECTOR PLATE
3 - 23-WAY CONNECTOR
4 - SOLENOID PACK
5 - TRANSMISSION RANGE SENSOR
6 - VALVE BODY
WJAUTOMATIC TRANSMISSION - 545RFE 21 - 271
Page 1793 of 2199
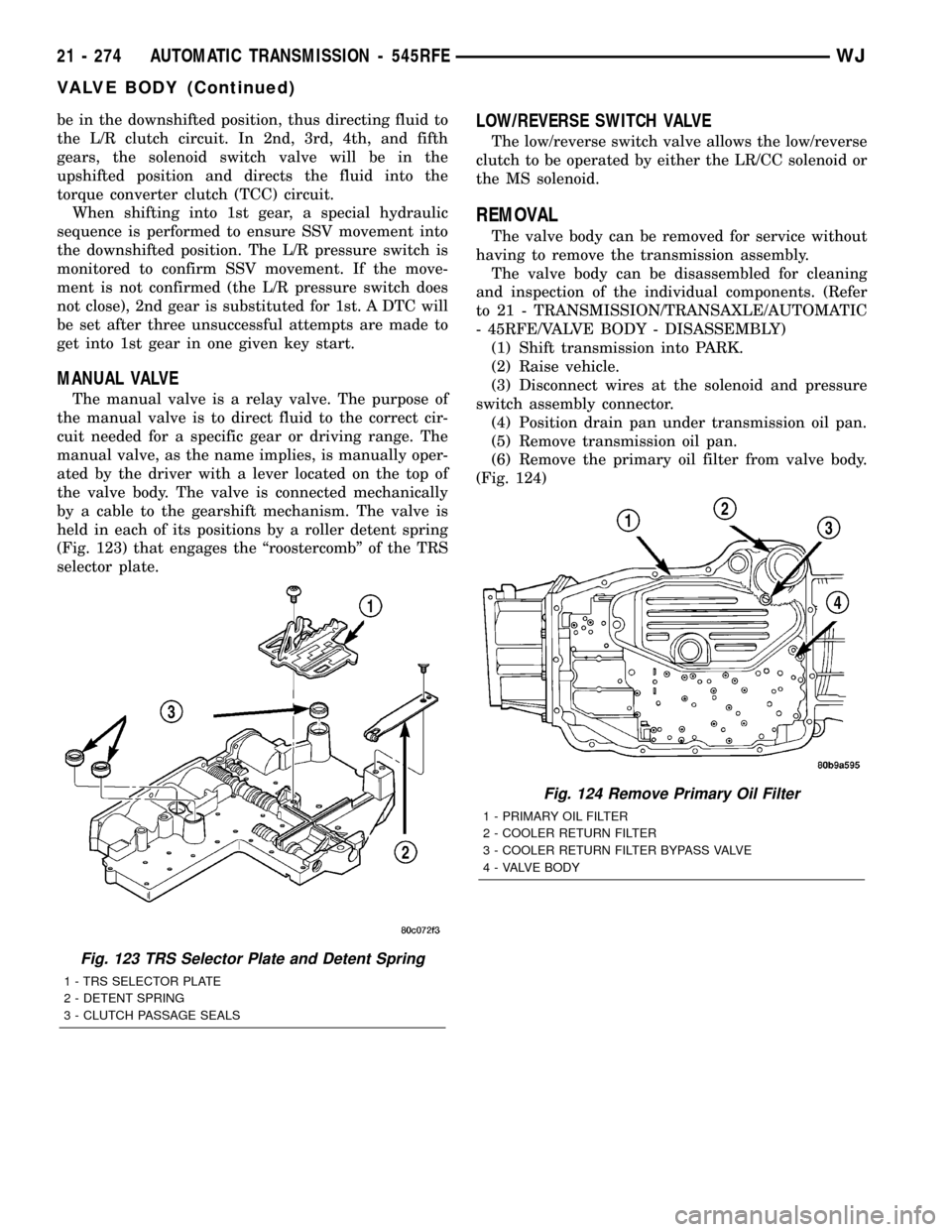
be in the downshifted position, thus directing fluid to
the L/R clutch circuit. In 2nd, 3rd, 4th, and fifth
gears, the solenoid switch valve will be in the
upshifted position and directs the fluid into the
torque converter clutch (TCC) circuit.
When shifting into 1st gear, a special hydraulic
sequence is performed to ensure SSV movement into
the downshifted position. The L/R pressure switch is
monitored to confirm SSV movement. If the move-
ment is not confirmed (the L/R pressure switch does
not close), 2nd gear is substituted for 1st. A DTC will
be set after three unsuccessful attempts are made to
get into 1st gear in one given key start.
MANUAL VALVE
The manual valve is a relay valve. The purpose of
the manual valve is to direct fluid to the correct cir-
cuit needed for a specific gear or driving range. The
manual valve, as the name implies, is manually oper-
ated by the driver with a lever located on the top of
the valve body. The valve is connected mechanically
by a cable to the gearshift mechanism. The valve is
held in each of its positions by a roller detent spring
(Fig. 123) that engages the ªroostercombº of the TRS
selector plate.
LOW/REVERSE SWITCH VALVE
The low/reverse switch valve allows the low/reverse
clutch to be operated by either the LR/CC solenoid or
the MS solenoid.
REMOVAL
The valve body can be removed for service without
having to remove the transmission assembly.
The valve body can be disassembled for cleaning
and inspection of the individual components. (Refer
to 21 - TRANSMISSION/TRANSAXLE/AUTOMATIC
- 45RFE/VALVE BODY - DISASSEMBLY)
(1) Shift transmission into PARK.
(2) Raise vehicle.
(3) Disconnect wires at the solenoid and pressure
switch assembly connector.
(4) Position drain pan under transmission oil pan.
(5) Remove transmission oil pan.
(6) Remove the primary oil filter from valve body.
(Fig. 124)
Fig. 123 TRS Selector Plate and Detent Spring
1 - TRS SELECTOR PLATE
2 - DETENT SPRING
3 - CLUTCH PASSAGE SEALS
Fig. 124 Remove Primary Oil Filter
1 - PRIMARY OIL FILTER
2 - COOLER RETURN FILTER
3 - COOLER RETURN FILTER BYPASS VALVE
4 - VALVE BODY
21 - 274 AUTOMATIC TRANSMISSION - 545RFEWJ
VALVE BODY (Continued)
Page 1794 of 2199
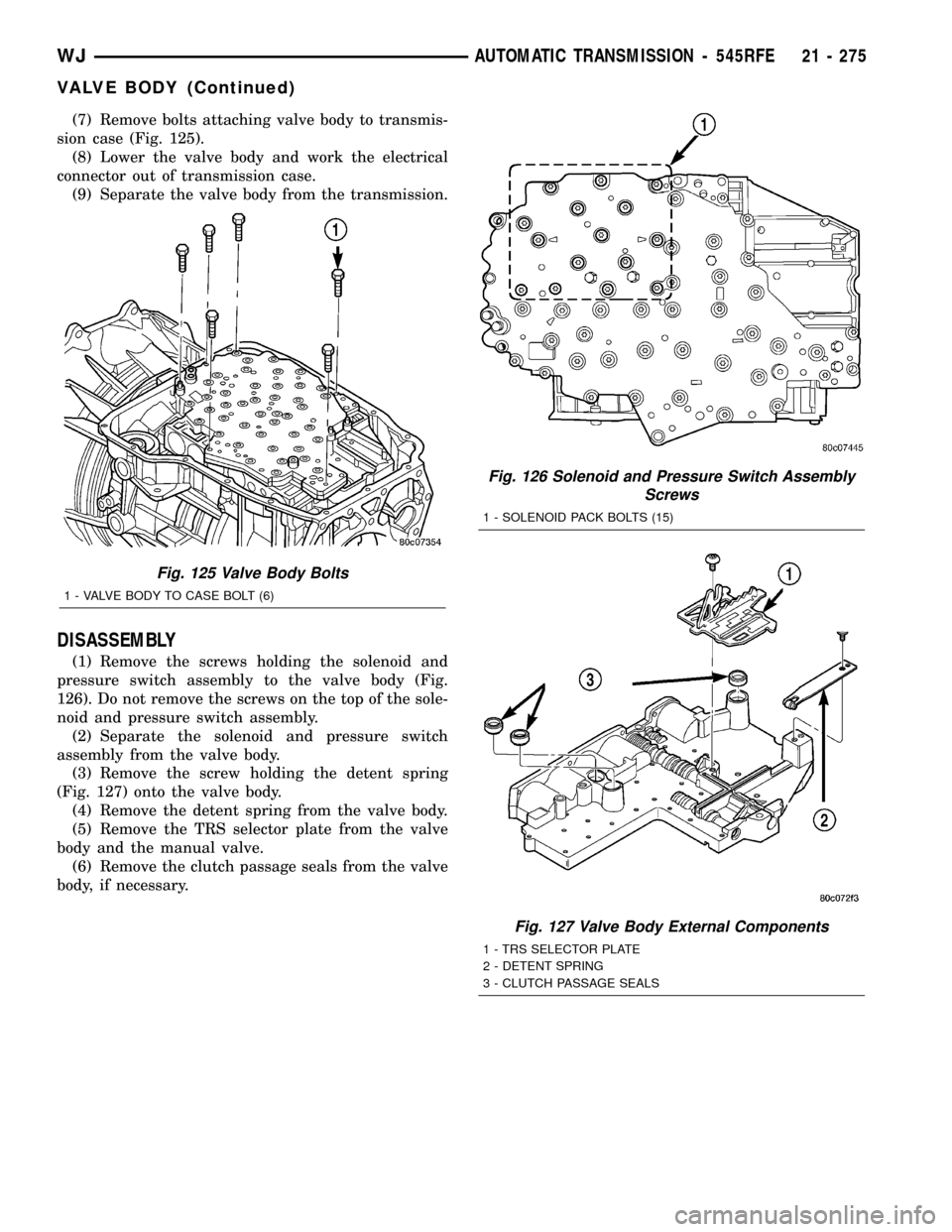
(7) Remove bolts attaching valve body to transmis-
sion case (Fig. 125).
(8) Lower the valve body and work the electrical
connector out of transmission case.
(9) Separate the valve body from the transmission.
DISASSEMBLY
(1) Remove the screws holding the solenoid and
pressure switch assembly to the valve body (Fig.
126). Do not remove the screws on the top of the sole-
noid and pressure switch assembly.
(2) Separate the solenoid and pressure switch
assembly from the valve body.
(3) Remove the screw holding the detent spring
(Fig. 127) onto the valve body.
(4) Remove the detent spring from the valve body.
(5) Remove the TRS selector plate from the valve
body and the manual valve.
(6) Remove the clutch passage seals from the valve
body, if necessary.
Fig. 125 Valve Body Bolts
1 - VALVE BODY TO CASE BOLT (6)
Fig. 126 Solenoid and Pressure Switch Assembly
Screws
1 - SOLENOID PACK BOLTS (15)
Fig. 127 Valve Body External Components
1 - TRS SELECTOR PLATE
2 - DETENT SPRING
3 - CLUTCH PASSAGE SEALS
WJAUTOMATIC TRANSMISSION - 545RFE 21 - 275
VALVE BODY (Continued)
Page 1798 of 2199
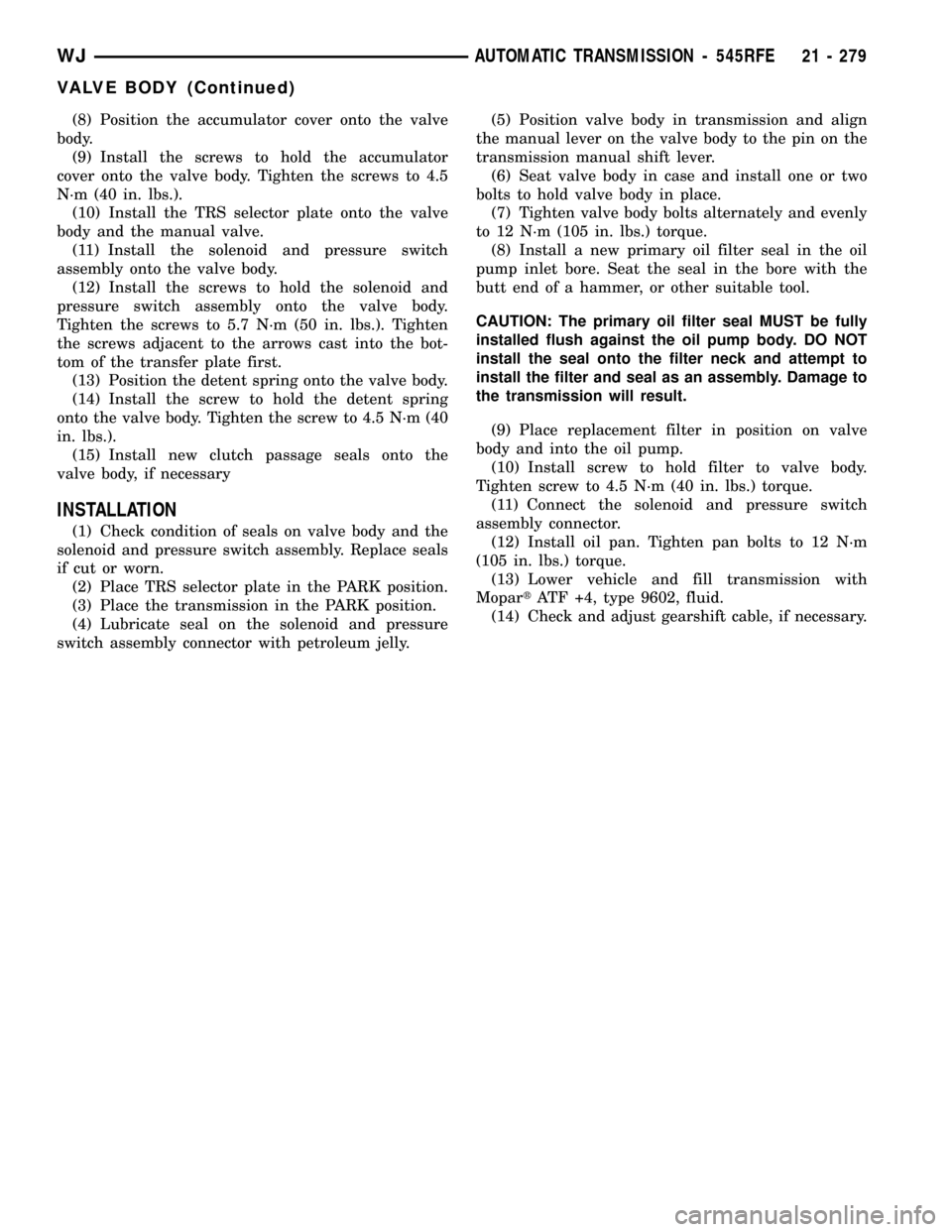
(8) Position the accumulator cover onto the valve
body.
(9) Install the screws to hold the accumulator
cover onto the valve body. Tighten the screws to 4.5
N´m (40 in. lbs.).
(10) Install the TRS selector plate onto the valve
body and the manual valve.
(11) Install the solenoid and pressure switch
assembly onto the valve body.
(12) Install the screws to hold the solenoid and
pressure switch assembly onto the valve body.
Tighten the screws to 5.7 N´m (50 in. lbs.). Tighten
the screws adjacent to the arrows cast into the bot-
tom of the transfer plate first.
(13) Position the detent spring onto the valve body.
(14) Install the screw to hold the detent spring
onto the valve body. Tighten the screw to 4.5 N´m (40
in. lbs.).
(15) Install new clutch passage seals onto the
valve body, if necessary
INSTALLATION
(1) Check condition of seals on valve body and the
solenoid and pressure switch assembly. Replace seals
if cut or worn.
(2) Place TRS selector plate in the PARK position.
(3) Place the transmission in the PARK position.
(4) Lubricate seal on the solenoid and pressure
switch assembly connector with petroleum jelly.(5) Position valve body in transmission and align
the manual lever on the valve body to the pin on the
transmission manual shift lever.
(6) Seat valve body in case and install one or two
bolts to hold valve body in place.
(7) Tighten valve body bolts alternately and evenly
to 12 N´m (105 in. lbs.) torque.
(8) Install a new primary oil filter seal in the oil
pump inlet bore. Seat the seal in the bore with the
butt end of a hammer, or other suitable tool.
CAUTION: The primary oil filter seal MUST be fully
installed flush against the oil pump body. DO NOT
install the seal onto the filter neck and attempt to
install the filter and seal as an assembly. Damage to
the transmission will result.
(9) Place replacement filter in position on valve
body and into the oil pump.
(10) Install screw to hold filter to valve body.
Tighten screw to 4.5 N´m (40 in. lbs.) torque.
(11) Connect the solenoid and pressure switch
assembly connector.
(12) Install oil pan. Tighten pan bolts to 12 N´m
(105 in. lbs.) torque.
(13) Lower vehicle and fill transmission with
MopartATF +4, type 9602, fluid.
(14) Check and adjust gearshift cable, if necessary.
WJAUTOMATIC TRANSMISSION - 545RFE 21 - 279
VALVE BODY (Continued)
Page 1824 of 2199
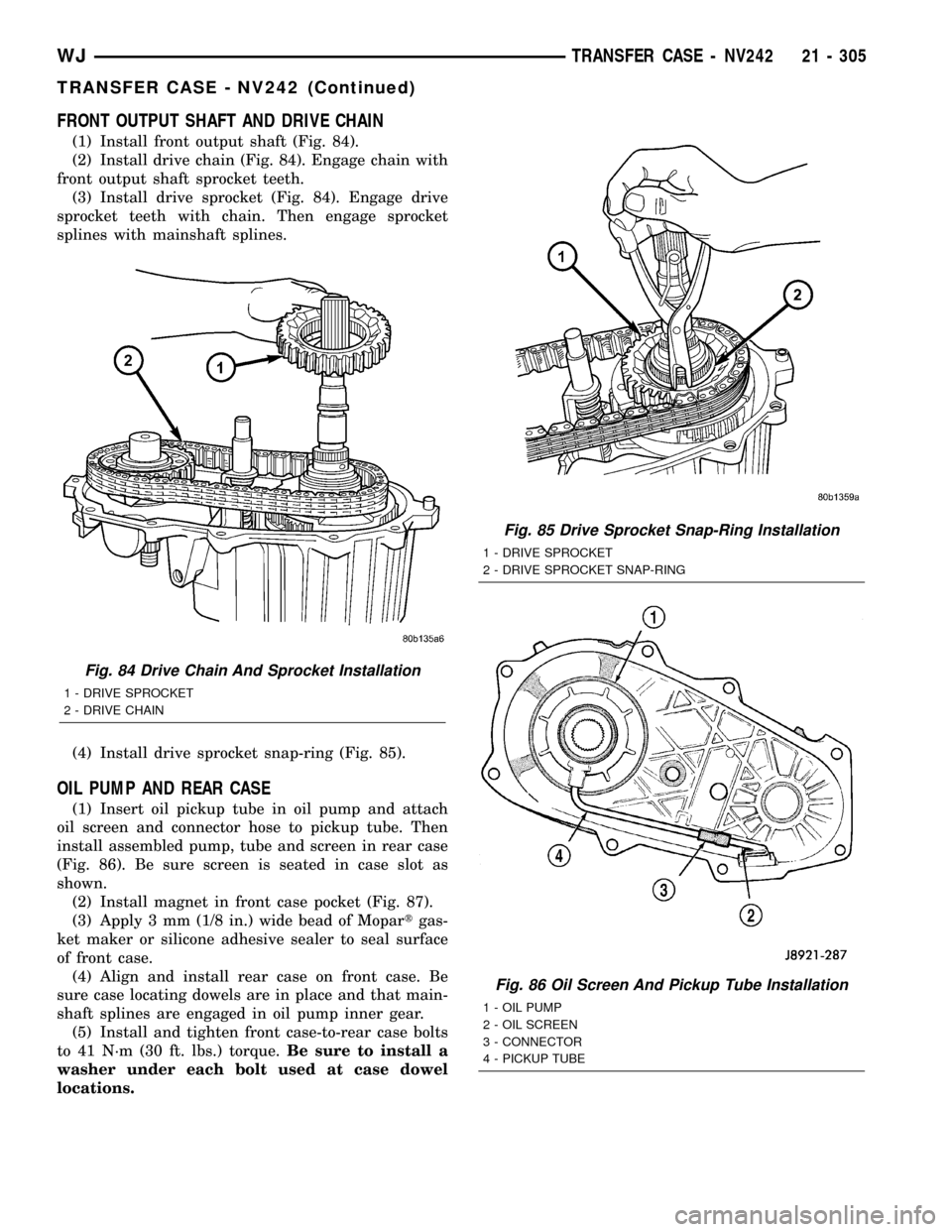
FRONT OUTPUT SHAFT AND DRIVE CHAIN
(1) Install front output shaft (Fig. 84).
(2) Install drive chain (Fig. 84). Engage chain with
front output shaft sprocket teeth.
(3) Install drive sprocket (Fig. 84). Engage drive
sprocket teeth with chain. Then engage sprocket
splines with mainshaft splines.
(4) Install drive sprocket snap-ring (Fig. 85).
OIL PUMP AND REAR CASE
(1) Insert oil pickup tube in oil pump and attach
oil screen and connector hose to pickup tube. Then
install assembled pump, tube and screen in rear case
(Fig. 86). Be sure screen is seated in case slot as
shown.
(2) Install magnet in front case pocket (Fig. 87).
(3) Apply 3 mm (1/8 in.) wide bead of Mopartgas-
ket maker or silicone adhesive sealer to seal surface
of front case.
(4) Align and install rear case on front case. Be
sure case locating dowels are in place and that main-
shaft splines are engaged in oil pump inner gear.
(5) Install and tighten front case-to-rear case bolts
to 41 N´m (30 ft. lbs.) torque.Be sure to install a
washer under each bolt used at case dowel
locations.
Fig. 84 Drive Chain And Sprocket Installation
1 - DRIVE SPROCKET
2 - DRIVE CHAIN
Fig. 85 Drive Sprocket Snap-Ring Installation
1 - DRIVE SPROCKET
2 - DRIVE SPROCKET SNAP-RING
Fig. 86 Oil Screen And Pickup Tube Installation
1 - OIL PUMP
2 - OIL SCREEN
3 - CONNECTOR
4 - PICKUP TUBE
WJTRANSFER CASE - NV242 21 - 305
TRANSFER CASE - NV242 (Continued)