sensor LAND ROVER DEFENDER 1999 Repair Manual
[x] Cancel search | Manufacturer: LAND ROVER, Model Year: 1999, Model line: DEFENDER, Model: LAND ROVER DEFENDER 1999Pages: 667, PDF Size: 8.76 MB
Page 293 of 667
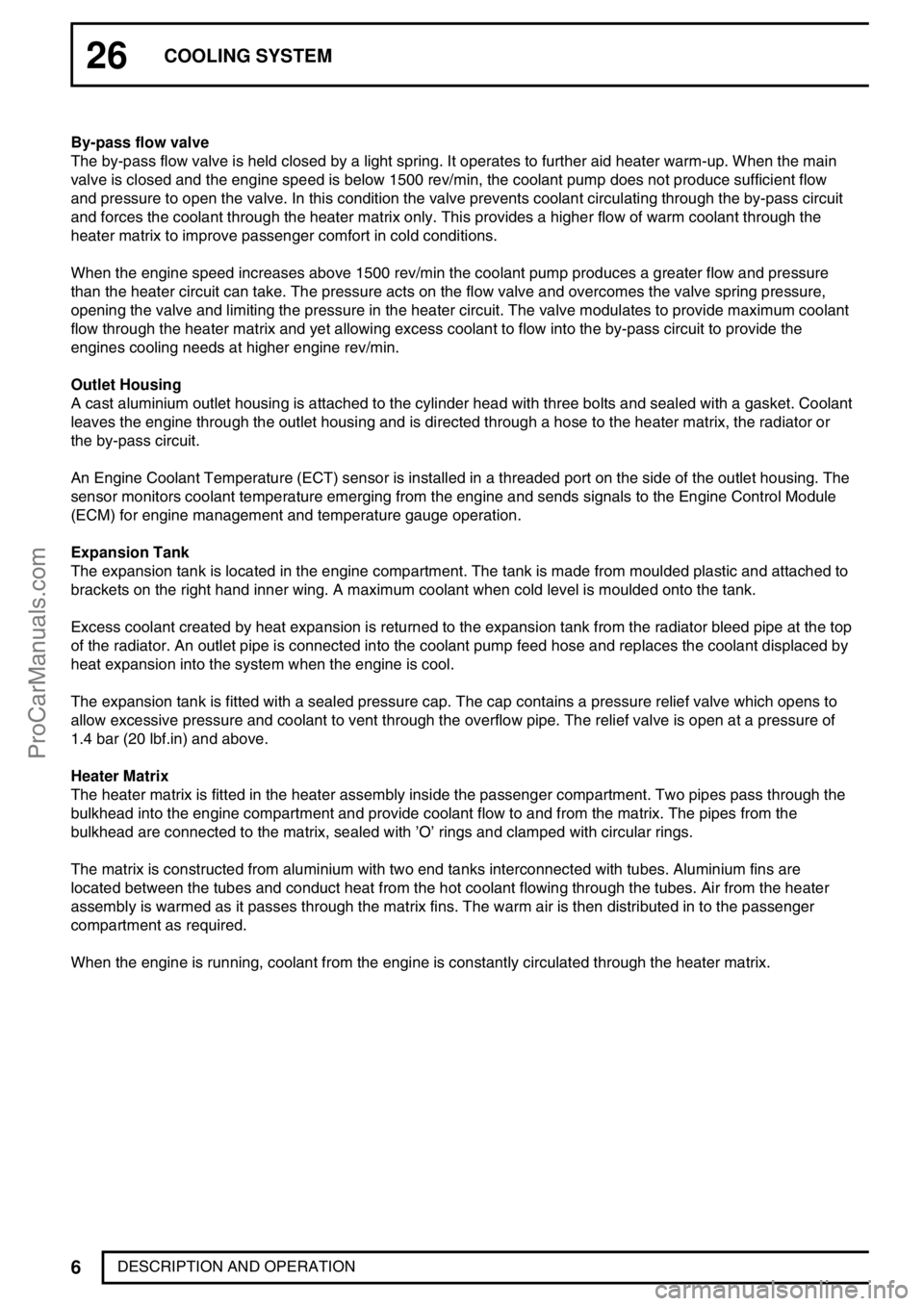
26COOLING SYSTEM
6
DESCRIPTION AND OPERATION By-pass flow valve
The by-pass flow valve is held closed by a light spring. It operates to further aid heater warm-up. When the main
valve is closed and the engine speed is below 1500 rev/min, the coolant pump does not produce sufficient flow
and pressure to open the valve. In this condition the valve prevents coolant circulating through the by-pass circuit
and forces the coolant through the heater matrix only. This provides a higher flow of warm coolant through the
heater matrix to improve passenger comfort in cold conditions.
When the engine speed increases above 1500 rev/min the coolant pump produces a greater flow and pressure
than the heater circuit can take. The pressure acts on the flow valve and overcomes the valve spring pressure,
opening the valve and limiting the pressure in the heater circuit. The valve modulates to provide maximum coolant
flow through the heater matrix and yet allowing excess coolant to flow into the by-pass circuit to provide the
engines cooling needs at higher engine rev/min.
Outlet Housing
A cast aluminium outlet housing is attached to the cylinder head with three bolts and sealed with a gasket. Coolant
leaves the engine through the outlet housing and is directed through a hose to the heater matrix, the radiator or
the by-pass circuit.
An Engine Coolant Temperature (ECT) sensor is installed in a threaded port on the side of the outlet housing. The
sensor monitors coolant temperature emerging from the engine and sends signals to the Engine Control Module
(ECM) for engine management and temperature gauge operation.
Expansion Tank
The expansion tank is located in the engine compartment. The tank is made from moulded plastic and attached to
brackets on the right hand inner wing. A maximum coolant when cold level is moulded onto the tank.
Excess coolant created by heat expansion is returned to the expansion tank from the radiator bleed pipe at the top
of the radiator. An outlet pipe is connected into the coolant pump feed hose and replaces the coolant displaced by
heat expansion into the system when the engine is cool.
The expansion tank is fitted with a sealed pressure cap. The cap contains a pressure relief valve which opens to
allow excessive pressure and coolant to vent through the overflow pipe. The relief valve is open at a pressure of
1.4 bar (20 lbf.in) and above.
Heater Matrix
The heater matrix is fitted in the heater assembly inside the passenger compartment. Two pipes pass through the
bulkhead into the engine compartment and provide coolant flow to and from the matrix. The pipes from the
bulkhead are connected to the matrix, sealed with’O’rings and clamped with circular rings.
The matrix is constructed from aluminium with two end tanks interconnected with tubes. Aluminium fins are
located between the tubes and conduct heat from the hot coolant flowing through the tubes. Air from the heater
assembly is warmed as it passes through the matrix fins. The warm air is then distributed in to the passenger
compartment as required.
When the engine is running, coolant from the engine is constantly circulated through the heater matrix.
ProCarManuals.com
Page 313 of 667
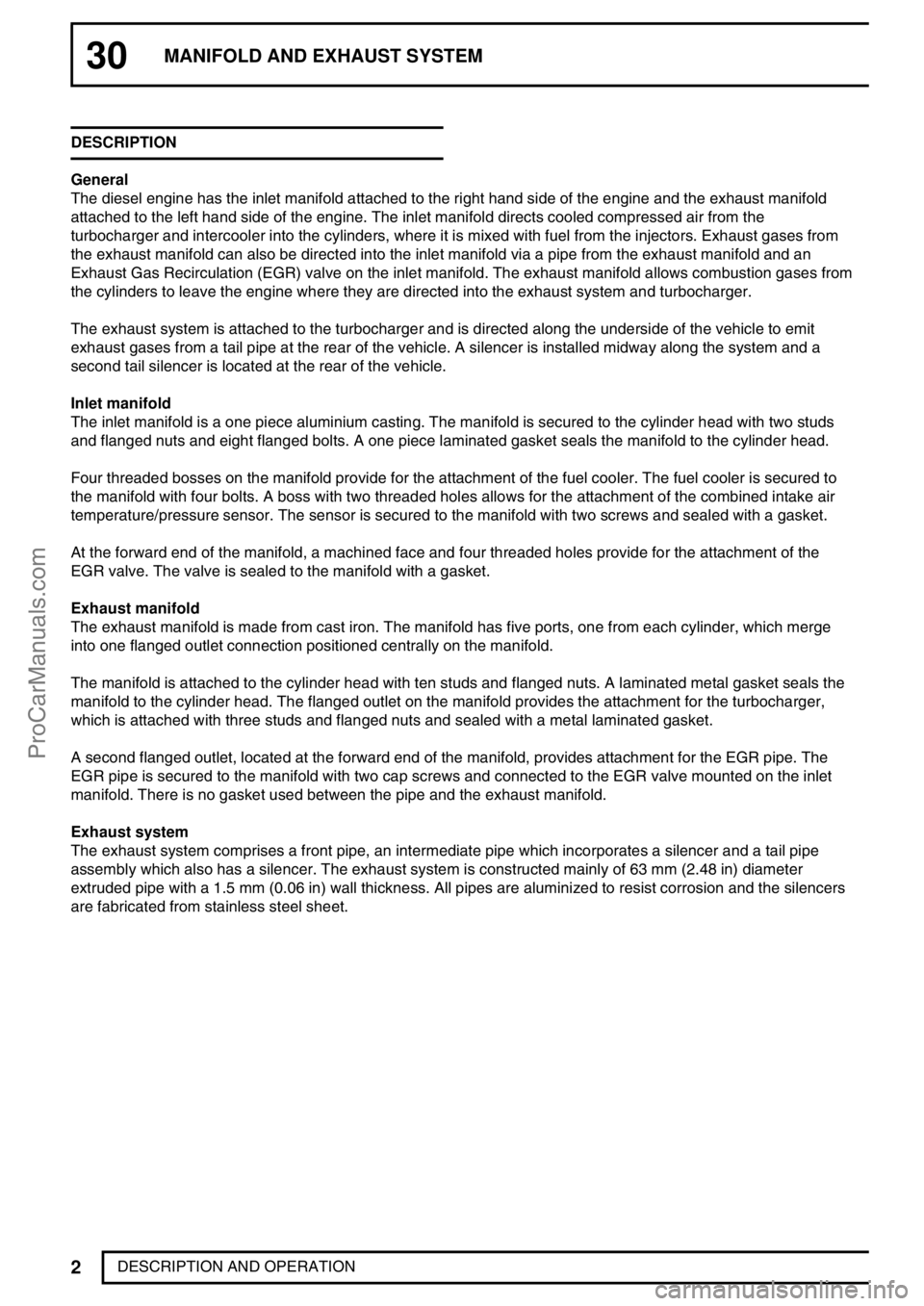
30MANIFOLD AND EXHAUST SYSTEM
2
DESCRIPTION AND OPERATION DESCRIPTION
General
The diesel engine has the inlet manifold attached to the right hand side of the engine and the exhaust manifold
attached to the left hand side of the engine. The inlet manifold directs cooled compressed air from the
turbocharger and intercooler into the cylinders, where it is mixed with fuel from the injectors. Exhaust gases from
the exhaust manifold can also be directed into the inlet manifold via a pipe from the exhaust manifold and an
Exhaust Gas Recirculation (EGR) valve on the inlet manifold. The exhaust manifold allows combustion gases from
the cylinders to leave the engine where they are directed into the exhaust system and turbocharger.
The exhaust system is attached to the turbocharger and is directed along the underside of the vehicle to emit
exhaust gases from a tail pipe at the rear of the vehicle. A silencer is installed midway along the system and a
second tail silencer is located at the rear of the vehicle.
Inlet manifold
The inlet manifold is a one piece aluminium casting. The manifold is secured to the cylinder head with two studs
and flanged nuts and eight flanged bolts. A one piece laminated gasket seals the manifold to the cylinder head.
Four threaded bosses on the manifold provide for the attachment of the fuel cooler. The fuel cooler is secured to
the manifold with four bolts. A boss with two threaded holes allows for the attachment of the combined intake air
temperature/pressure sensor. The sensor is secured to the manifold with two screws and sealed with a gasket.
At the forward end of the manifold, a machined face and four threaded holes provide for the attachment of the
EGR valve. The valve is sealed to the manifold with a gasket.
Exhaust manifold
The exhaust manifold is made from cast iron. The manifold has five ports, one from each cylinder, which merge
into one flanged outlet connection positioned centrally on the manifold.
The manifold is attached to the cylinder head with ten studs and flanged nuts. A laminated metal gasket seals the
manifold to the cylinder head. The flanged outlet on the manifold provides the attachment for the turbocharger,
which is attached with three studs and flanged nuts and sealed with a metal laminated gasket.
A second flanged outlet, located at the forward end of the manifold, provides attachment for the EGR pipe. The
EGR pipe is secured to the manifold with two cap screws and connected to the EGR valve mounted on the inlet
manifold. There is no gasket used between the pipe and the exhaust manifold.
Exhaust system
The exhaust system comprises a front pipe, an intermediate pipe which incorporates a silencer and a tail pipe
assembly which also has a silencer. The exhaust system is constructed mainly of 63 mm (2.48 in) diameter
extruded pipe with a 1.5 mm (0.06 in) wall thickness. All pipes are aluminized to resist corrosion and the silencers
are fabricated from stainless steel sheet.
ProCarManuals.com
Page 318 of 667
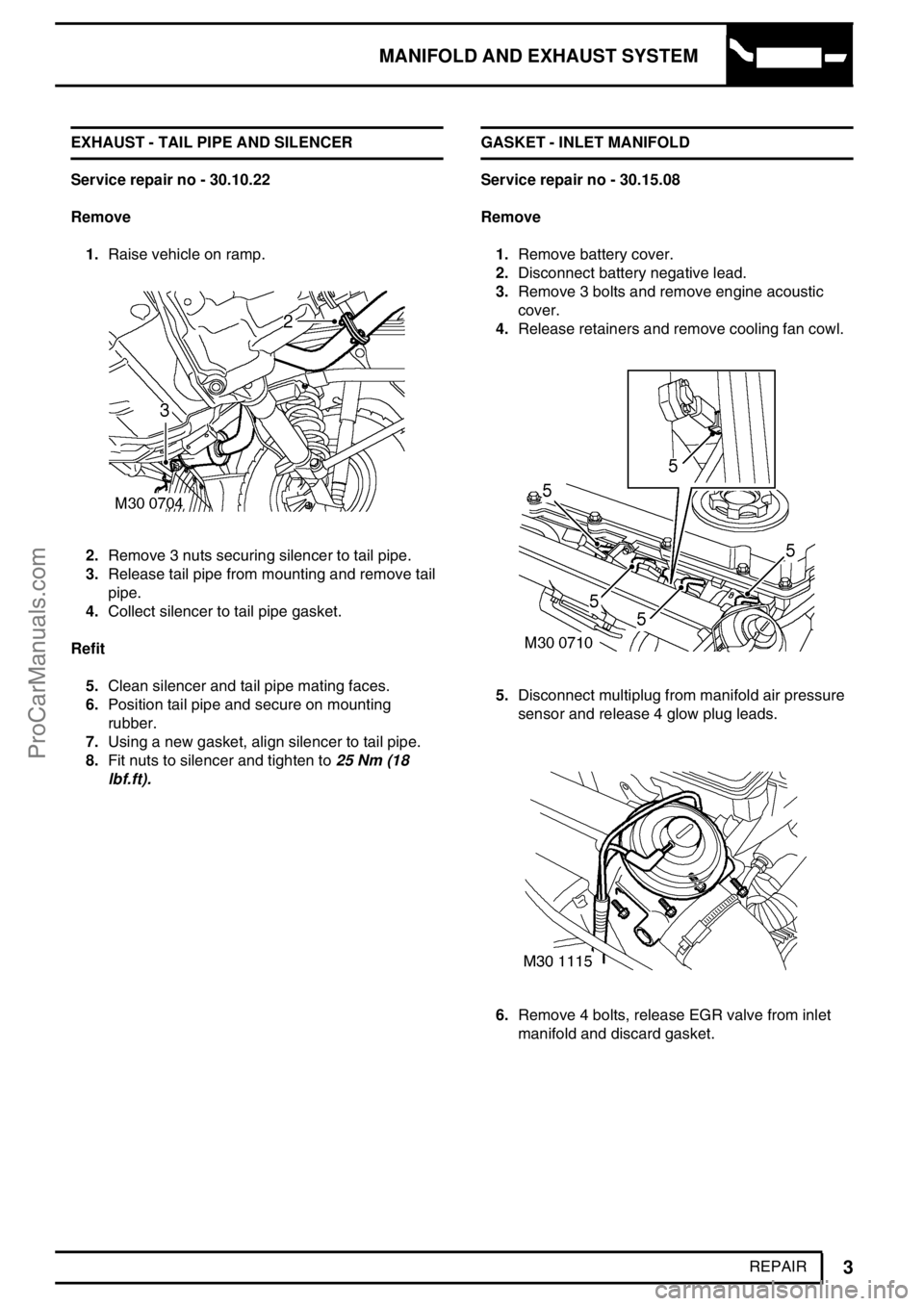
MANIFOLD AND EXHAUST SYSTEM
3
REPAIR EXHAUST - TAIL PIPE AND SILENCER
Service repair no - 30.10.22
Remove
1.Raise vehicle on ramp.
2.Remove 3 nuts securing silencer to tail pipe.
3.Release tail pipe from mounting and remove tail
pipe.
4.Collect silencer to tail pipe gasket.
Refit
5.Clean silencer and tail pipe mating faces.
6.Position tail pipe and secure on mounting
rubber.
7.Using a new gasket, align silencer to tail pipe.
8.Fit nuts to silencer and tighten to25 Nm (18
lbf.ft).GASKET - INLET MANIFOLD
Service repair no - 30.15.08
Remove
1.Remove battery cover.
2.Disconnect battery negative lead.
3.Remove 3 bolts and remove engine acoustic
cover.
4.Release retainers and remove cooling fan cowl.
5.Disconnect multiplug from manifold air pressure
sensor and release 4 glow plug leads.
6.Remove 4 bolts, release EGR valve from inlet
manifold and discard gasket.
ProCarManuals.com
Page 319 of 667
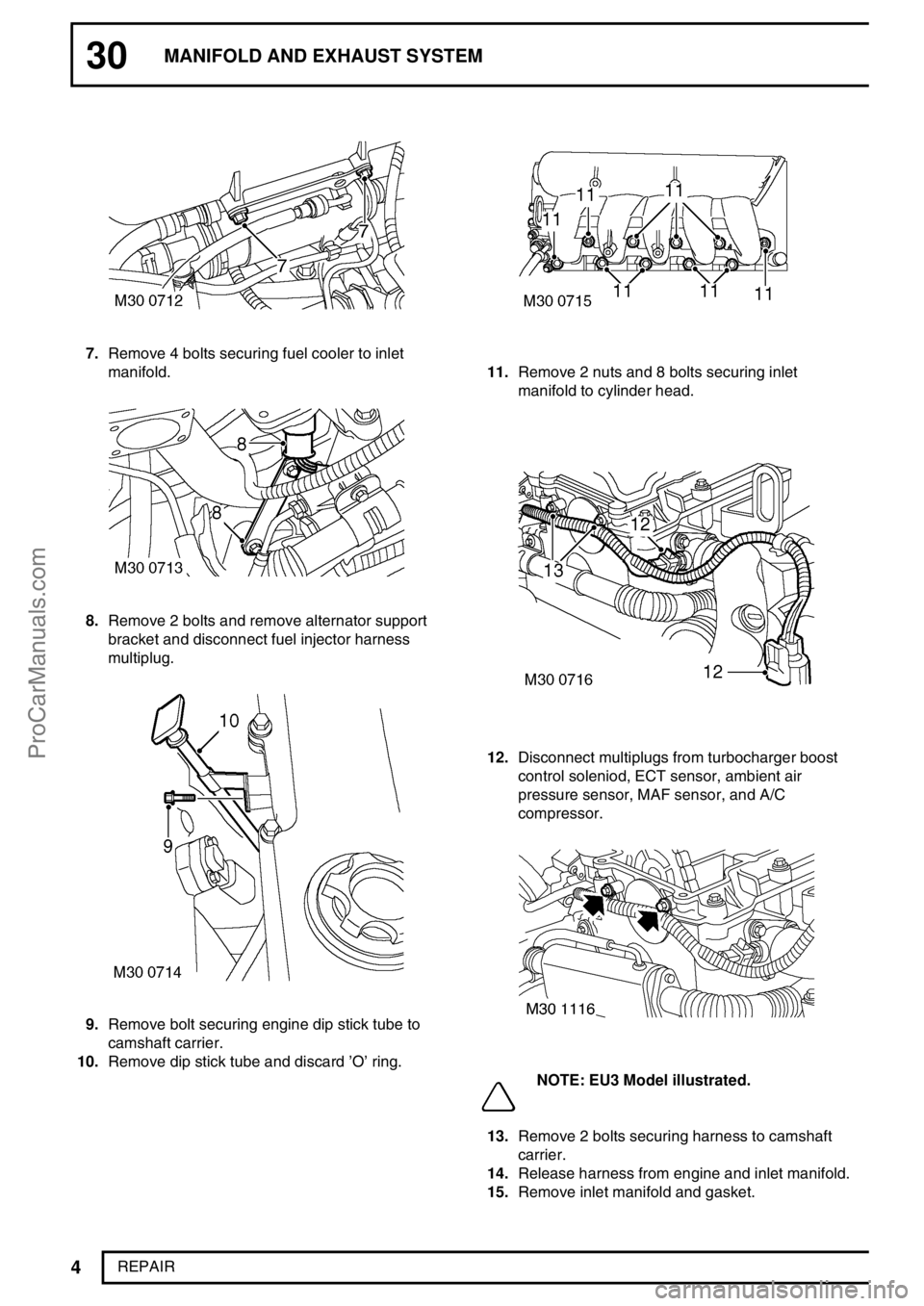
30MANIFOLD AND EXHAUST SYSTEM
4
REPAIR
7.Remove 4 bolts securing fuel cooler to inlet
manifold.
8.Remove 2 bolts and remove alternator support
bracket and disconnect fuel injector harness
multiplug.
9.Remove bolt securing engine dip stick tube to
camshaft carrier.
10.Remove dip stick tube and discard’O’ring.
11.Remove 2 nuts and 8 bolts securing inlet
manifold to cylinder head.
12.Disconnect multiplugs from turbocharger boost
control soleniod, ECT sensor, ambient air
pressure sensor, MAF sensor, and A/C
compressor.
NOTE: EU3 Model illustrated.
13.Remove 2 bolts securing harness to camshaft
carrier.
14.Release harness from engine and inlet manifold.
15.Remove inlet manifold and gasket.
ProCarManuals.com
Page 320 of 667
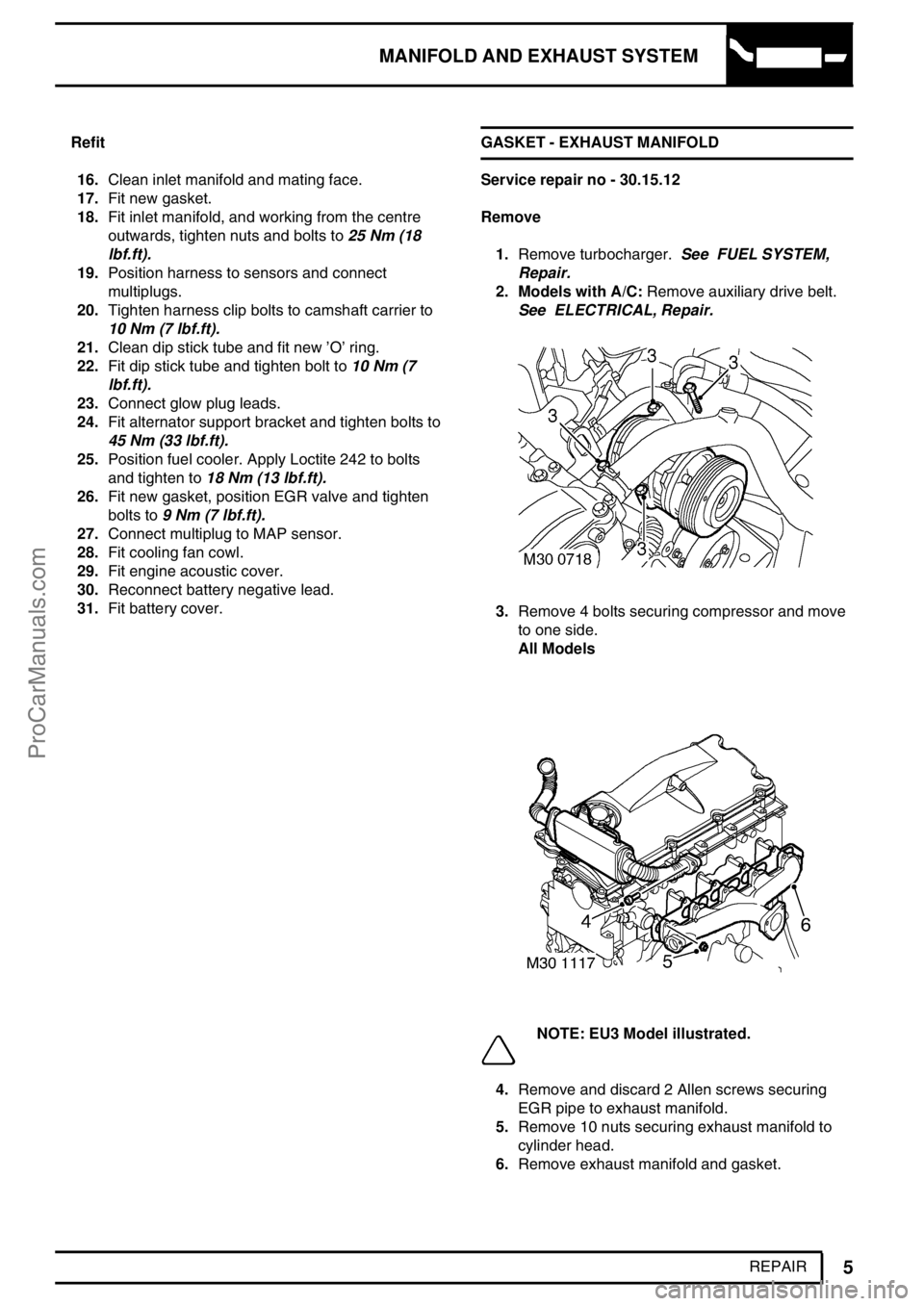
MANIFOLD AND EXHAUST SYSTEM
5
REPAIR Refit
16.Clean inlet manifold and mating face.
17.Fit new gasket.
18.Fit inlet manifold, and working from the centre
outwards, tighten nuts and bolts to25 Nm (18
lbf.ft).
19.Position harness to sensors and connect
multiplugs.
20.Tighten harness clip bolts to camshaft carrier to
10 Nm (7 lbf.ft).
21.Clean dip stick tube and fit new’O’ring.
22.Fit dip stick tube and tighten bolt to10 Nm (7
lbf.ft).
23.Connect glow plug leads.
24.Fit alternator support bracket and tighten bolts to
45 Nm (33 lbf.ft).
25.Position fuel cooler. Apply Loctite 242 to bolts
and tighten to18 Nm (13 lbf.ft).
26.Fit new gasket, position EGR valve and tighten
bolts to9 Nm (7 lbf.ft).
27.Connect multiplug to MAP sensor.
28.Fit cooling fan cowl.
29.Fit engine acoustic cover.
30.Reconnect battery negative lead.
31.Fit battery cover.GASKET - EXHAUST MANIFOLD
Service repair no - 30.15.12
Remove
1.Remove turbocharger.See FUEL SYSTEM,
Repair.
2. Models with A/C:Remove auxiliary drive belt.
See ELECTRICAL, Repair.
3.Remove 4 bolts securing compressor and move
to one side.
All Models
NOTE: EU3 Model illustrated.
4.Remove and discard 2 Allen screws securing
EGR pipe to exhaust manifold.
5.Remove 10 nuts securing exhaust manifold to
cylinder head.
6.Remove exhaust manifold and gasket.
ProCarManuals.com
Page 331 of 667
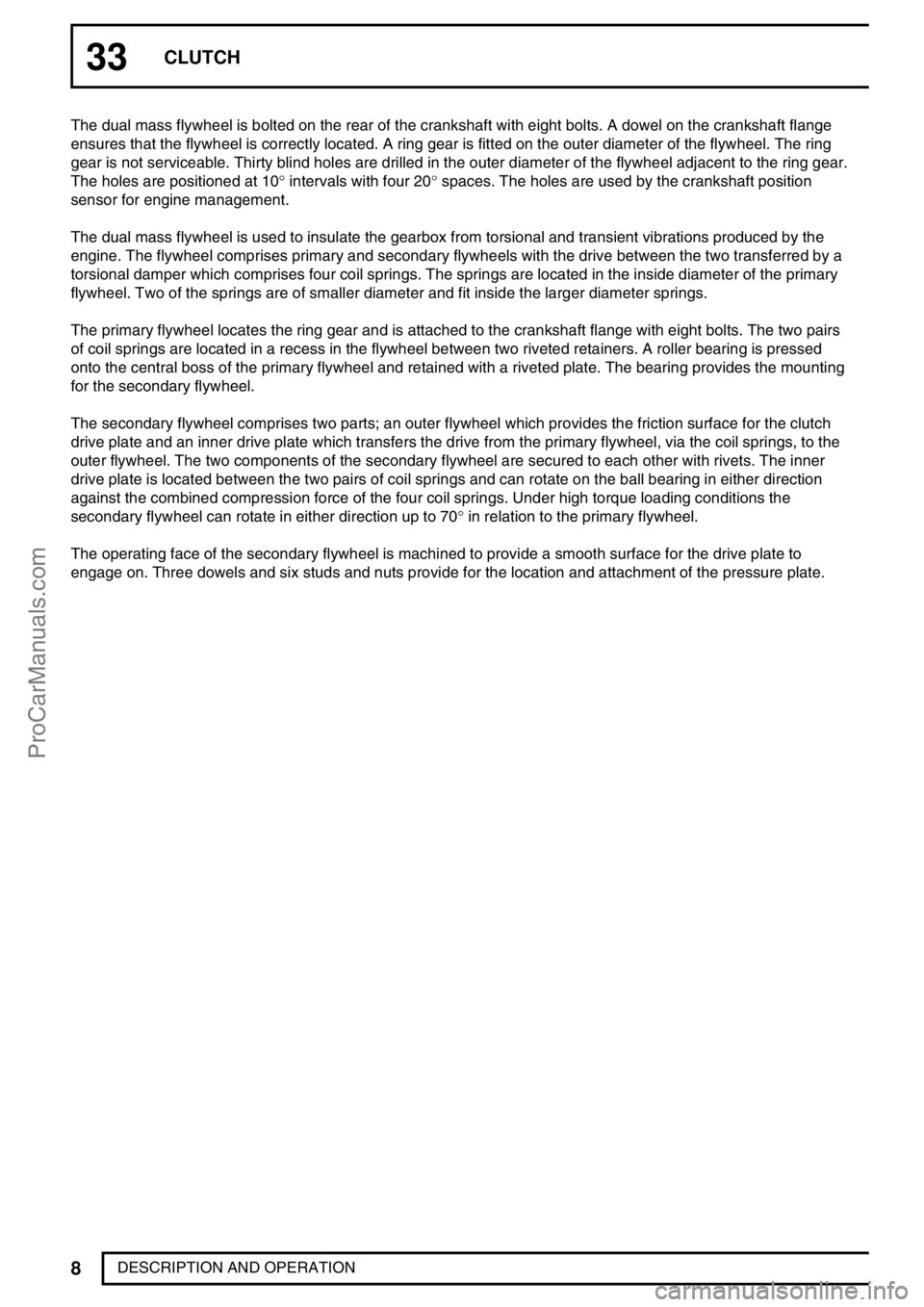
33CLUTCH
8
DESCRIPTION AND OPERATION The dual mass flywheel is bolted on the rear of the crankshaft with eight bolts. A dowel on the crankshaft flange
ensures that the flywheel is correctly located. A ring gear is fitted on the outer diameter of the flywheel. The ring
gear is not serviceable. Thirty blind holes are drilled in the outer diameter of the flywheel adjacent to the ring gear.
The holes are positioned at 10°intervals with four 20°spaces. The holes are used by the crankshaft position
sensor for engine management.
The dual mass flywheel is used to insulate the gearbox from torsional and transient vibrations produced by the
engine. The flywheel comprises primary and secondary flywheels with the drive between the two transferred by a
torsional damper which comprises four coil springs. The springs are located in the inside diameter of the primary
flywheel. Two of the springs are of smaller diameter and fit inside the larger diameter springs.
The primary flywheel locates the ring gear and is attached to the crankshaft flange with eight bolts. The two pairs
of coil springs are located in a recess in the flywheel between two riveted retainers. A roller bearing is pressed
onto the central boss of the primary flywheel and retained with a riveted plate. The bearing provides the mounting
for the secondary flywheel.
The secondary flywheel comprises two parts; an outer flywheel which provides the friction surface for the clutch
drive plate and an inner drive plate which transfers the drive from the primary flywheel, via the coil springs, to the
outer flywheel. The two components of the secondary flywheel are secured to each other with rivets. The inner
drive plate is located between the two pairs of coil springs and can rotate on the ball bearing in either direction
against the combined compression force of the four coil springs. Under high torque loading conditions the
secondary flywheel can rotate in either direction up to 70°in relation to the primary flywheel.
The operating face of the secondary flywheel is machined to provide a smooth surface for the drive plate to
engage on. Three dowels and six studs and nuts provide for the location and attachment of the pressure plate.
ProCarManuals.com
Page 340 of 667
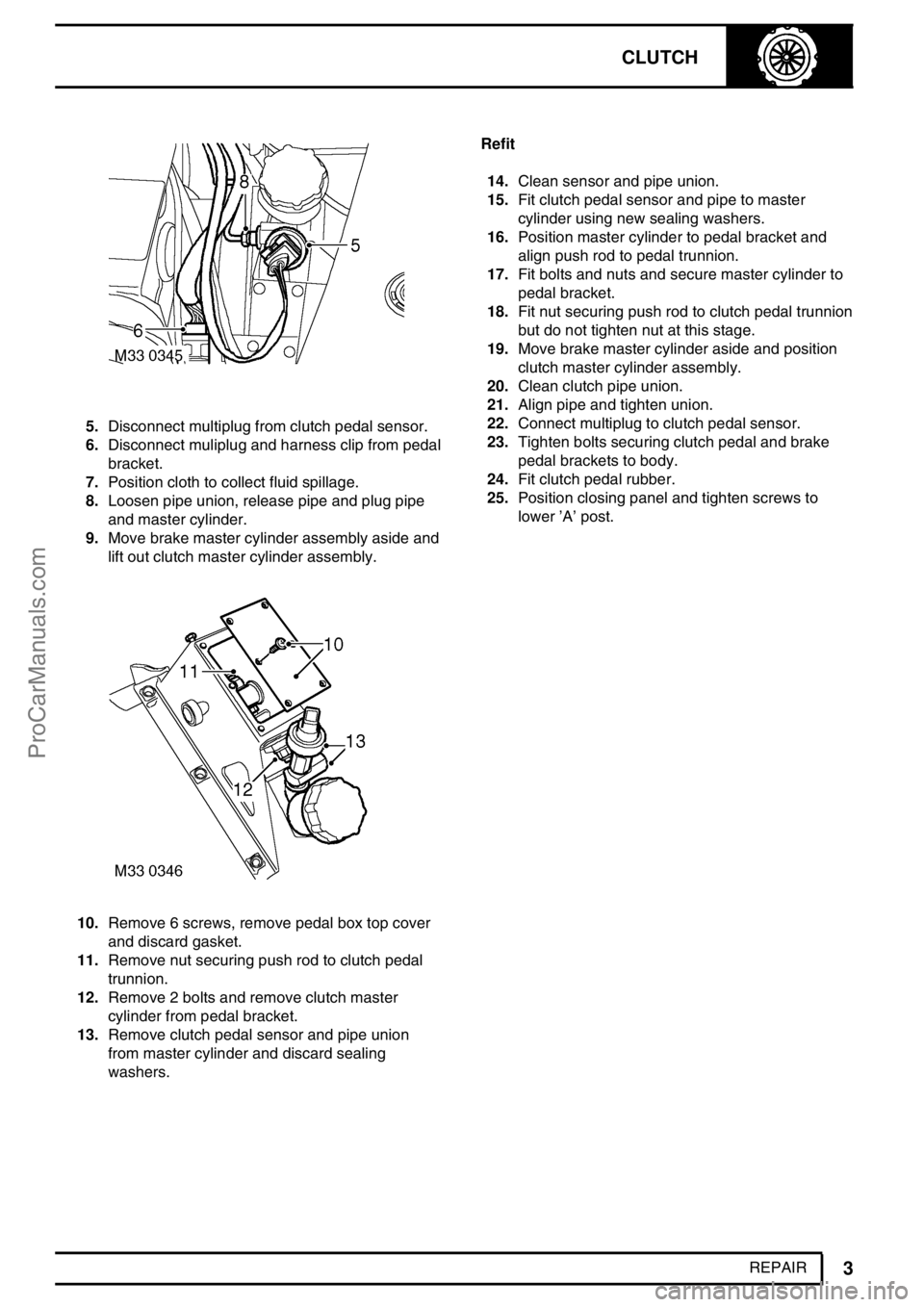
CLUTCH
3
REPAIR
5.Disconnect multiplug from clutch pedal sensor.
6.Disconnect muliplug and harness clip from pedal
bracket.
7.Position cloth to collect fluid spillage.
8.Loosen pipe union, release pipe and plug pipe
and master cylinder.
9.Move brake master cylinder assembly aside and
lift out clutch master cylinder assembly.
10.Remove 6 screws, remove pedal box top cover
and discard gasket.
11.Remove nut securing push rod to clutch pedal
trunnion.
12.Remove 2 bolts and remove clutch master
cylinder from pedal bracket.
13.Remove clutch pedal sensor and pipe union
from master cylinder and discard sealing
washers.Refit
14.Clean sensor and pipe union.
15.Fit clutch pedal sensor and pipe to master
cylinder using new sealing washers.
16.Position master cylinder to pedal bracket and
align push rod to pedal trunnion.
17.Fit bolts and nuts and secure master cylinder to
pedal bracket.
18.Fit nut securing push rod to clutch pedal trunnion
but do not tighten nut at this stage.
19.Move brake master cylinder aside and position
clutch master cylinder assembly.
20.Clean clutch pipe union.
21.Align pipe and tighten union.
22.Connect multiplug to clutch pedal sensor.
23.Tighten bolts securing clutch pedal and brake
pedal brackets to body.
24.Fit clutch pedal rubber.
25.Position closing panel and tighten screws to
lower’A’post.
ProCarManuals.com
Page 355 of 667
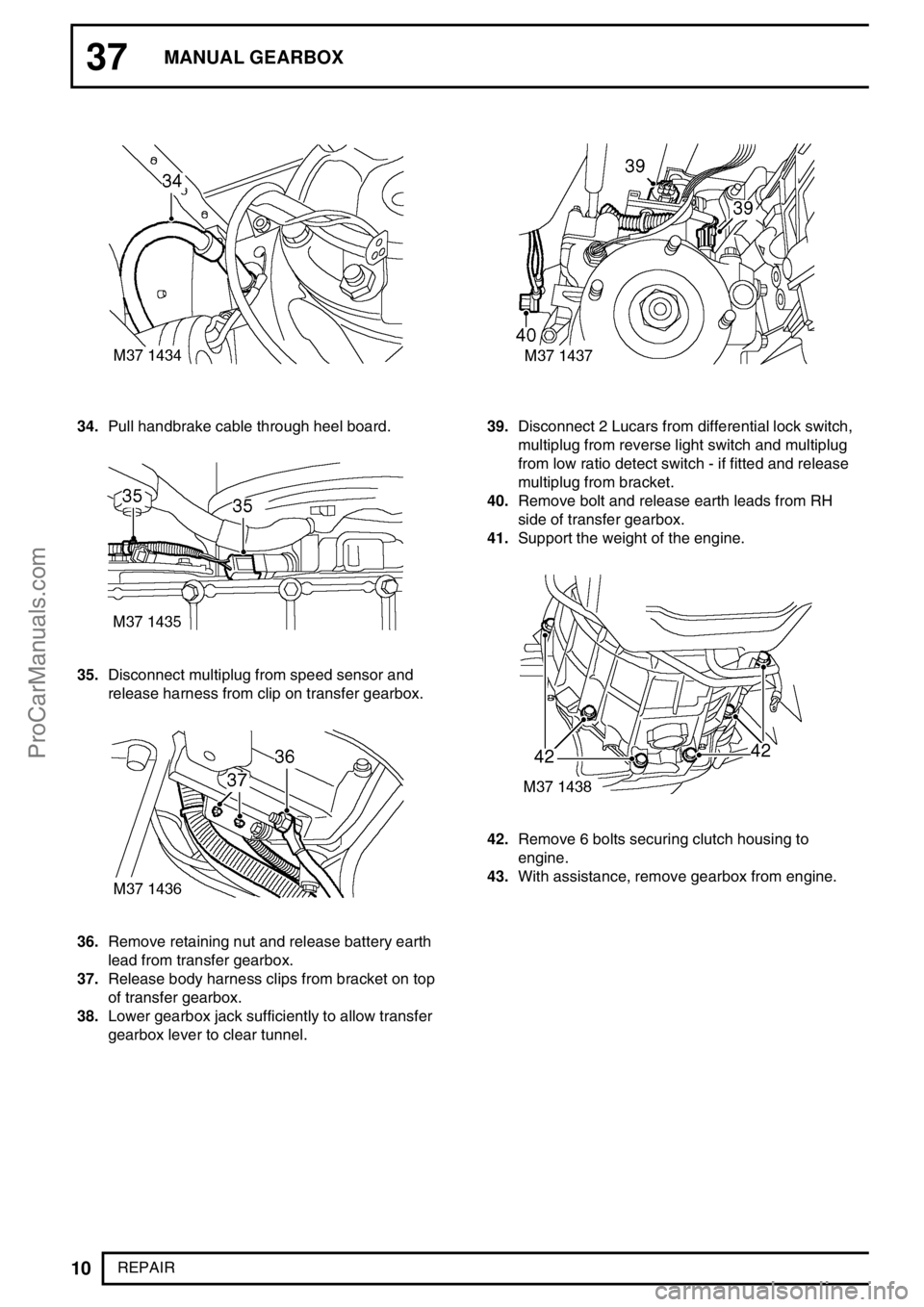
37MANUAL GEARBOX
10
REPAIR
34.Pull handbrake cable through heel board.
35.Disconnect multiplug from speed sensor and
release harness from clip on transfer gearbox.
36.Remove retaining nut and release battery earth
lead from transfer gearbox.
37.Release body harness clips from bracket on top
of transfer gearbox.
38.Lower gearbox jack sufficiently to allow transfer
gearbox lever to clear tunnel.
39.Disconnect 2 Lucars from differential lock switch,
multiplug from reverse light switch and multiplug
from low ratio detect switch - if fitted and release
multiplug from bracket.
40.Remove bolt and release earth leads from RH
side of transfer gearbox.
41.Support the weight of the engine.
42.Remove 6 bolts securing clutch housing to
engine.
43.With assistance, remove gearbox from engine.
ProCarManuals.com
Page 356 of 667
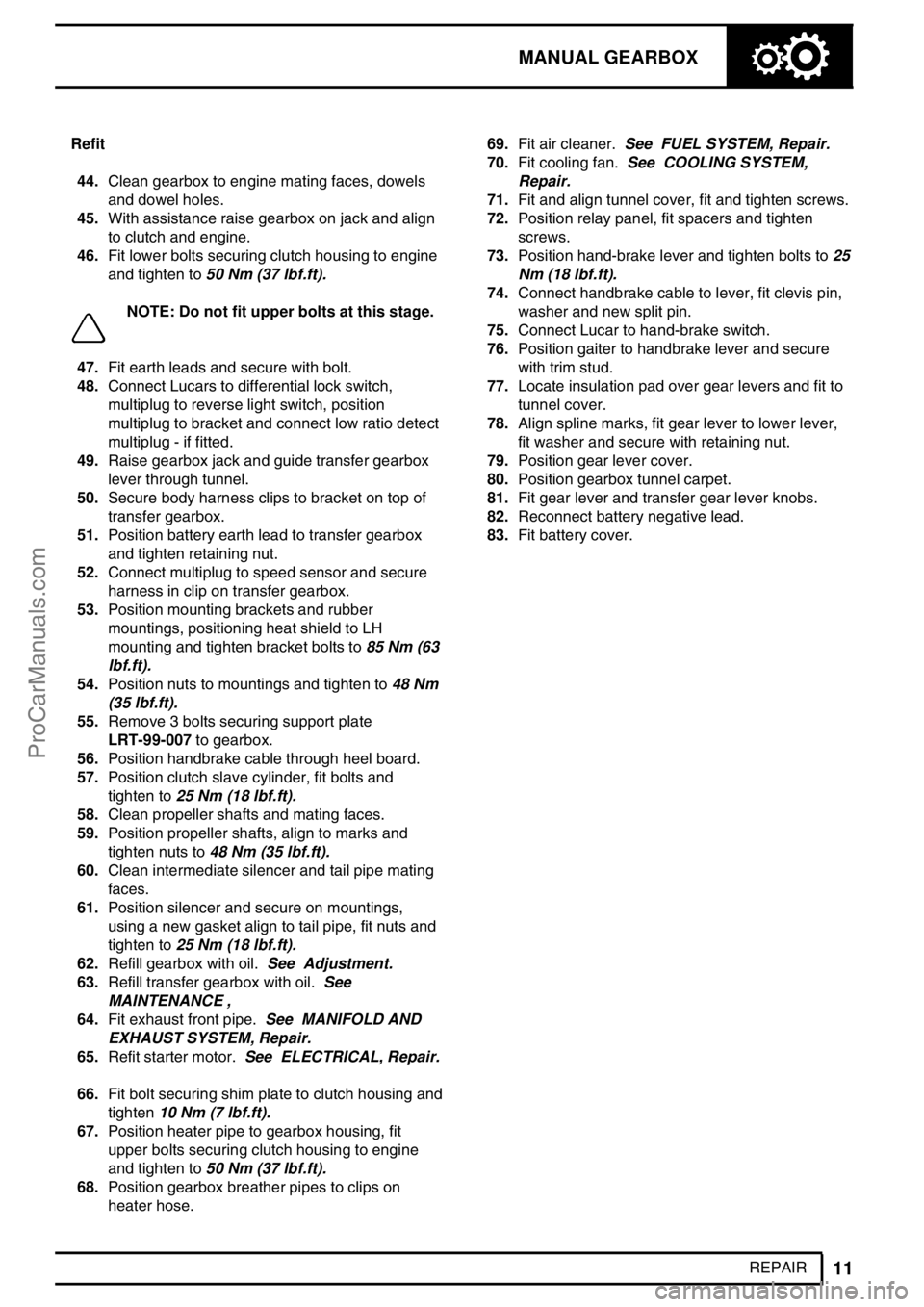
MANUAL GEARBOX
11
REPAIR Refit
44.Clean gearbox to engine mating faces, dowels
and dowel holes.
45.With assistance raise gearbox on jack and align
to clutch and engine.
46.Fit lower bolts securing clutch housing to engine
and tighten to50 Nm (37 lbf.ft).
NOTE: Do not fit upper bolts at this stage.
47.Fit earth leads and secure with bolt.
48.Connect Lucars to differential lock switch,
multiplug to reverse light switch, position
multiplug to bracket and connect low ratio detect
multiplug - if fitted.
49.Raise gearbox jack and guide transfer gearbox
lever through tunnel.
50.Secure body harness clips to bracket on top of
transfer gearbox.
51.Position battery earth lead to transfer gearbox
and tighten retaining nut.
52.Connect multiplug to speed sensor and secure
harness in clip on transfer gearbox.
53.Position mounting brackets and rubber
mountings, positioning heat shield to LH
mounting and tighten bracket bolts to85 Nm (63
lbf.ft).
54.Position nuts to mountings and tighten to48 Nm
(35 lbf.ft).
55.Remove 3 bolts securing support plate
LRT-99-007to gearbox.
56.Position handbrake cable through heel board.
57.Position clutch slave cylinder, fit bolts and
tighten to25 Nm (18 lbf.ft).
58.Clean propeller shafts and mating faces.
59.Position propeller shafts, align to marks and
tighten nuts to48 Nm (35 lbf.ft).
60.Clean intermediate silencer and tail pipe mating
faces.
61.Position silencer and secure on mountings,
using a new gasket align to tail pipe, fit nuts and
tighten to25 Nm (18 lbf.ft).
62.Refill gearbox with oil.See Adjustment.
63.Refill transfer gearbox with oil.See
MAINTENANCE ,
64.Fit exhaust front pipe.See MANIFOLD AND
EXHAUST SYSTEM, Repair.
65.Refit starter motor.See ELECTRICAL, Repair.
66.Fit bolt securing shim plate to clutch housing and
tighten10 Nm (7 lbf.ft).
67.Position heater pipe to gearbox housing, fit
upper bolts securing clutch housing to engine
and tighten to50 Nm (37 lbf.ft).
68.Position gearbox breather pipes to clips on
heater hose.69.Fit air cleaner.See FUEL SYSTEM, Repair.
70.Fit cooling fan.See COOLING SYSTEM,
Repair.
71.Fit and align tunnel cover, fit and tighten screws.
72.Position relay panel, fit spacers and tighten
screws.
73.Position hand-brake lever and tighten bolts to25
Nm (18 lbf.ft).
74.Connect handbrake cable to lever, fit clevis pin,
washer and new split pin.
75.Connect Lucar to hand-brake switch.
76.Position gaiter to handbrake lever and secure
with trim stud.
77.Locate insulation pad over gear levers and fit to
tunnel cover.
78.Align spline marks, fit gear lever to lower lever,
fit washer and secure with retaining nut.
79.Position gear lever cover.
80.Position gearbox tunnel carpet.
81.Fit gear lever and transfer gear lever knobs.
82.Reconnect battery negative lead.
83.Fit battery cover.
ProCarManuals.com
Page 364 of 667
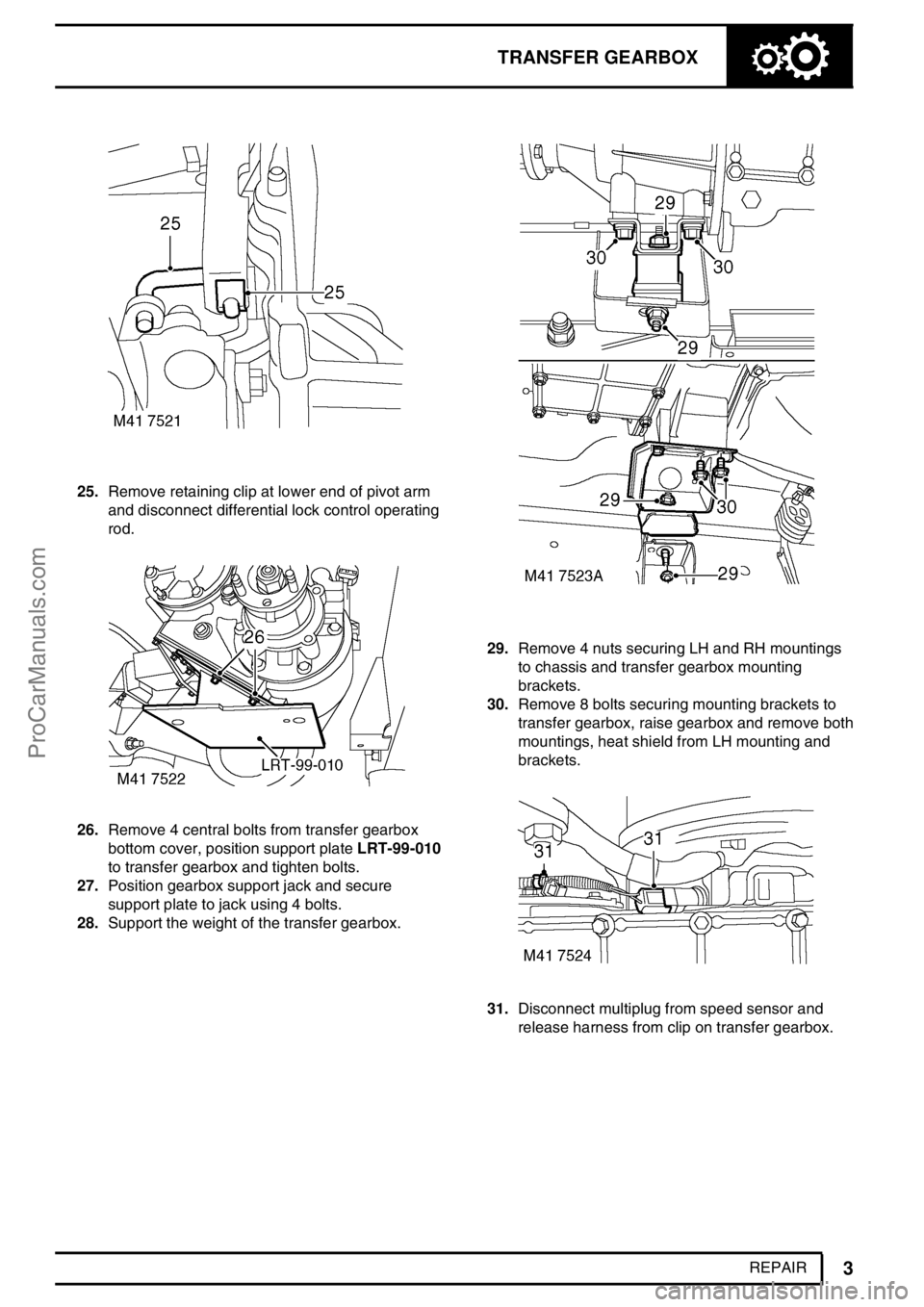
TRANSFER GEARBOX
3
REPAIR
25.Remove retaining clip at lower end of pivot arm
and disconnect differential lock control operating
rod.
26.Remove 4 central bolts from transfer gearbox
bottom cover, position support plateLRT-99-010
to transfer gearbox and tighten bolts.
27.Position gearbox support jack and secure
support plate to jack using 4 bolts.
28.Support the weight of the transfer gearbox.
29.Remove 4 nuts securing LH and RH mountings
to chassis and transfer gearbox mounting
brackets.
30.Remove 8 bolts securing mounting brackets to
transfer gearbox, raise gearbox and remove both
mountings, heat shield from LH mounting and
brackets.
31.Disconnect multiplug from speed sensor and
release harness from clip on transfer gearbox.
ProCarManuals.com