LAND ROVER DISCOVERY 1995 Service Repair Manual
Manufacturer: LAND ROVER, Model Year: 1995, Model line: DISCOVERY, Model: LAND ROVER DISCOVERY 1995Pages: 976, PDF Size: 14.57 MB
Page 911 of 976

ENGINE
16
OVERHAUL
18.Check sealing washers for damage or
distortion, replace as necessary.
19.Position a new gasket - dry to rocker cover.
20.Position rocker cover to cylinder head, fit 3
flange nuts and working from centre outwards,
tighten to 10 Nm.
21.Lubricate a new 'O' ring with engine oil and fit
to crankcase breather cyclone unit.
22.Fit cyclone unit to rocker cover, fit bolt and
tighten to 9 Nm.
23.Connect breather hoses to cyclone unit, rocker
cover and cylinder block.
Page 912 of 976
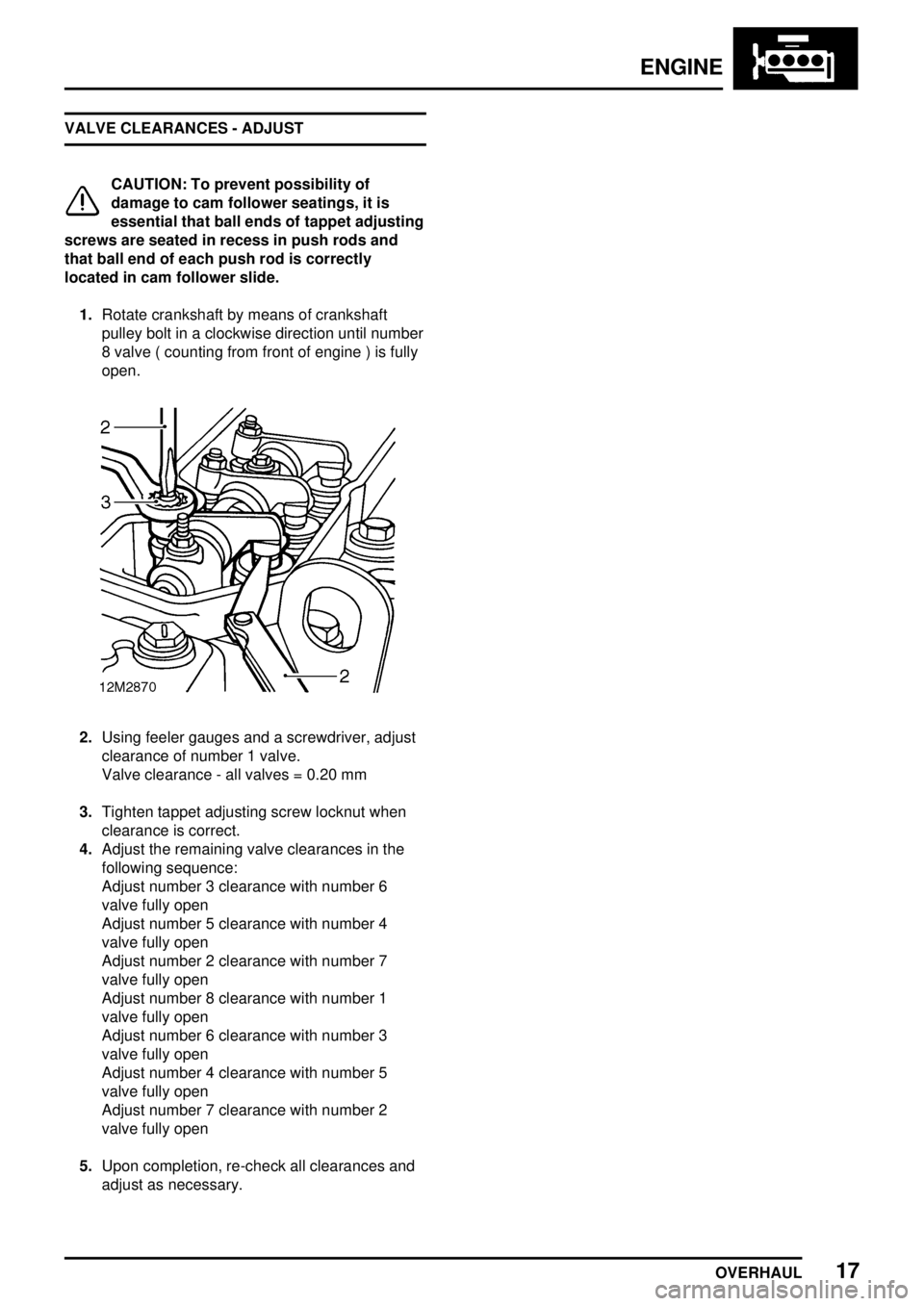
ENGINE
OVERHAUL17
VALVE CLEARANCES - ADJUST
CAUTION: To prevent possibility of
damage to cam follower seatings, it is
essential that ball ends of tappet adjusting
screws are seated in recess in push rods and
that ball end of each push rod is correctly
located in cam follower slide.
1.Rotate crankshaft by means of crankshaft
pulley bolt in a clockwise direction until number
8 valve ( counting from front of engine ) is fully
open.
2.Using feeler gauges and a screwdriver, adjust
clearance of number 1 valve.
Valve clearance - all valves = 0.20 mm
3.Tighten tappet adjusting screw locknut when
clearance is correct.
4.Adjust the remaining valve clearances in the
following sequence:
Adjust number 3 clearance with number 6
valve fully open
Adjust number 5 clearance with number 4
valve fully open
Adjust number 2 clearance with number 7
valve fully open
Adjust number 8 clearance with number 1
valve fully open
Adjust number 6 clearance with number 3
valve fully open
Adjust number 4 clearance with number 5
valve fully open
Adjust number 7 clearance with number 2
valve fully open
5.Upon completion, re-check all clearances and
adjust as necessary.
Page 913 of 976
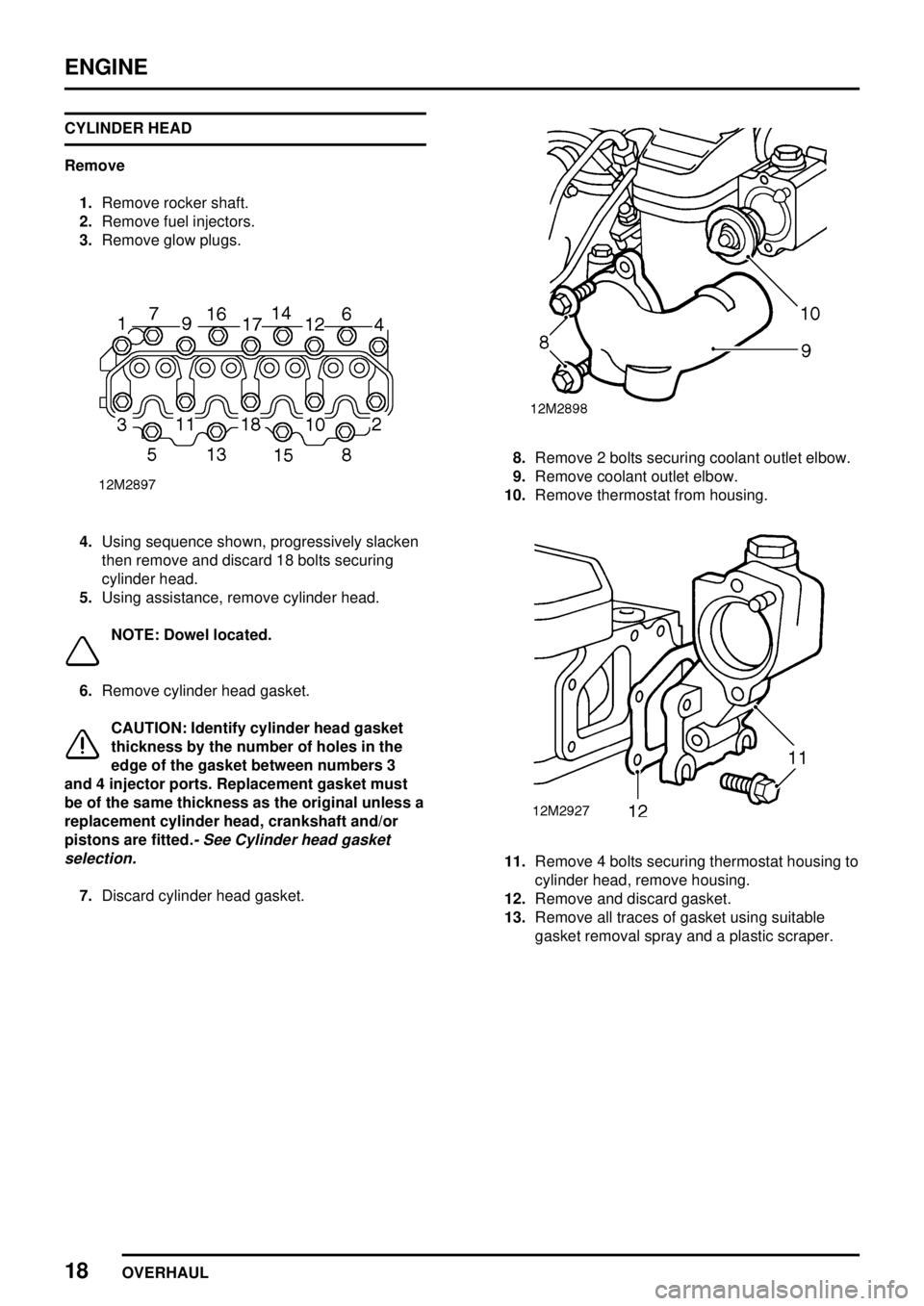
ENGINE
18
OVERHAUL CYLINDER HEAD
Remove
1.Remove rocker shaft.
2.Remove fuel injectors.
3.Remove glow plugs.
4.Using sequence shown, progressively slacken
then remove and discard 18 bolts securing
cylinder head.
5.Using assistance, remove cylinder head.
NOTE: Dowel located.
6.Remove cylinder head gasket.
CAUTION: Identify cylinder head gasket
thickness by the number of holes in the
edge of the gasket between numbers 3
and 4 injector ports. Replacement gasket must
be of the same thickness as the original unless a
replacement cylinder head, crankshaft and/or
pistons are fitted.
- See Cylinder head gasket
selection.
7.Discard cylinder head gasket.
8.Remove 2 bolts securing coolant outlet elbow.
9.Remove coolant outlet elbow.
10.Remove thermostat from housing.
11.Remove 4 bolts securing thermostat housing to
cylinder head, remove housing.
12.Remove and discard gasket.
13.Remove all traces of gasket using suitable
gasket removal spray and a plastic scraper.
Page 914 of 976
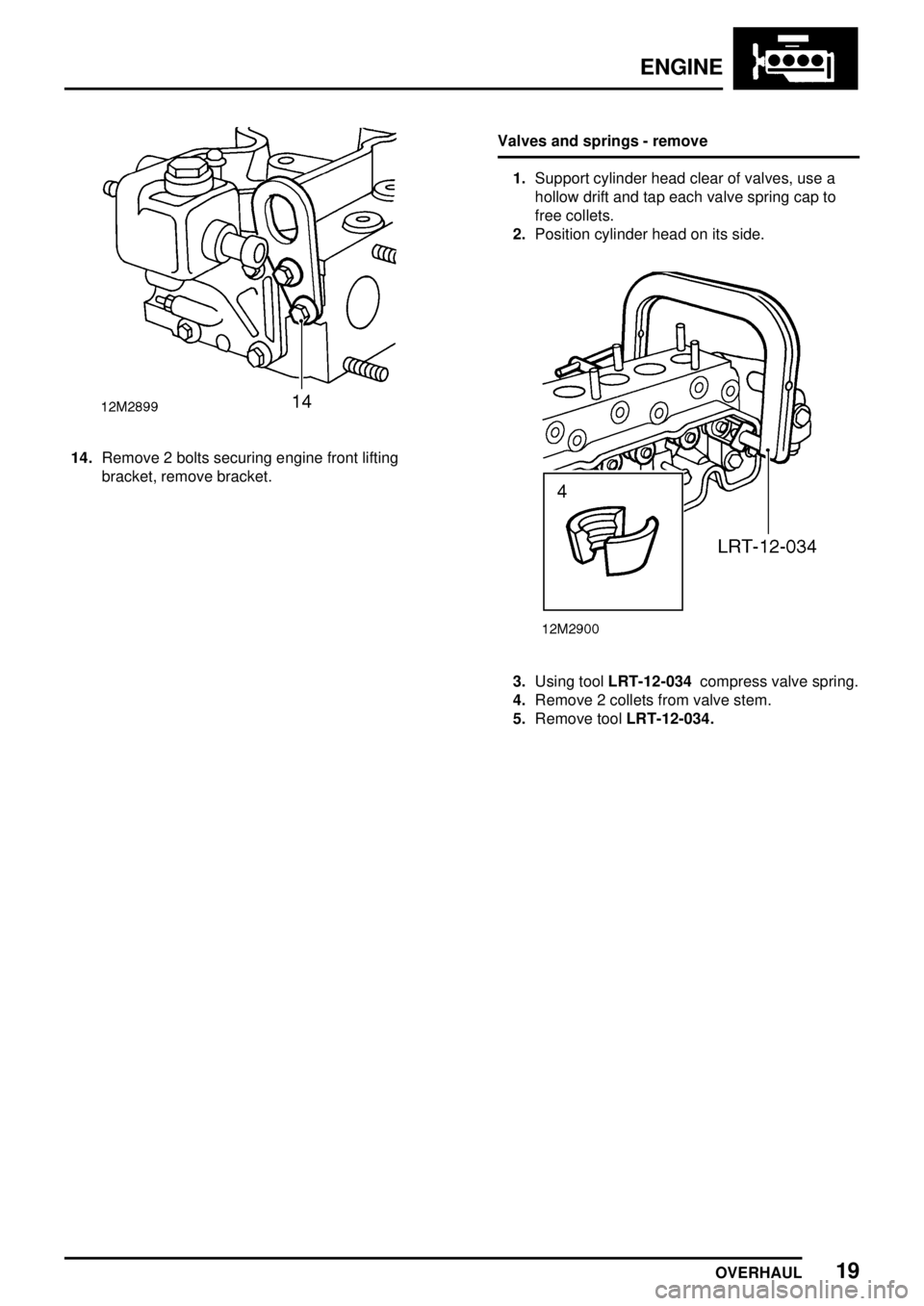
ENGINE
OVERHAUL19
14.Remove 2 bolts securing engine front lifting
bracket, remove bracket.Valves and springs - remove
1.Support cylinder head clear of valves, use a
hollow drift and tap each valve spring cap to
free collets.
2.Position cylinder head on its side.
3.Using toolLRT-12-034compress valve spring.
4.Remove 2 collets from valve stem.
5.Remove toolLRT-12-034.
Page 915 of 976
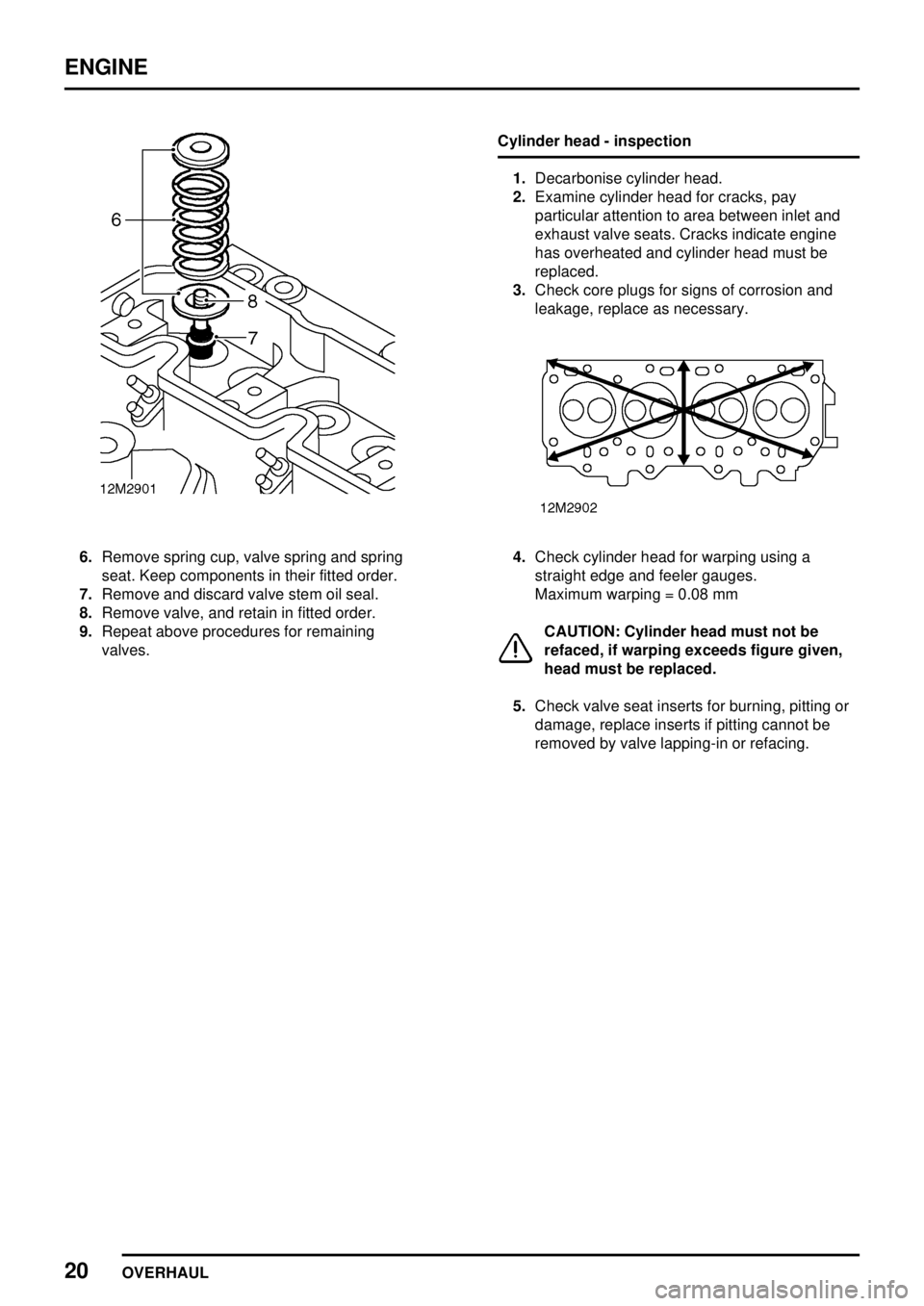
ENGINE
20
OVERHAUL
6.Remove spring cup, valve spring and spring
seat. Keep components in their fitted order.
7.Remove and discard valve stem oil seal.
8.Remove valve, and retain in fitted order.
9.Repeat above procedures for remaining
valves.Cylinder head - inspection
1.Decarbonise cylinder head.
2.Examine cylinder head for cracks, pay
particular attention to area between inlet and
exhaust valve seats. Cracks indicate engine
has overheated and cylinder head must be
replaced.
3.Check core plugs for signs of corrosion and
leakage, replace as necessary.4.Check cylinder head for warping using a
straight edge and feeler gauges.
Maximum warping = 0.08 mm
CAUTION: Cylinder head must not be
refaced, if warping exceeds figure given,
head must be replaced.
5.Check valve seat inserts for burning, pitting or
damage, replace inserts if pitting cannot be
removed by valve lapping-in or refacing.
Page 916 of 976
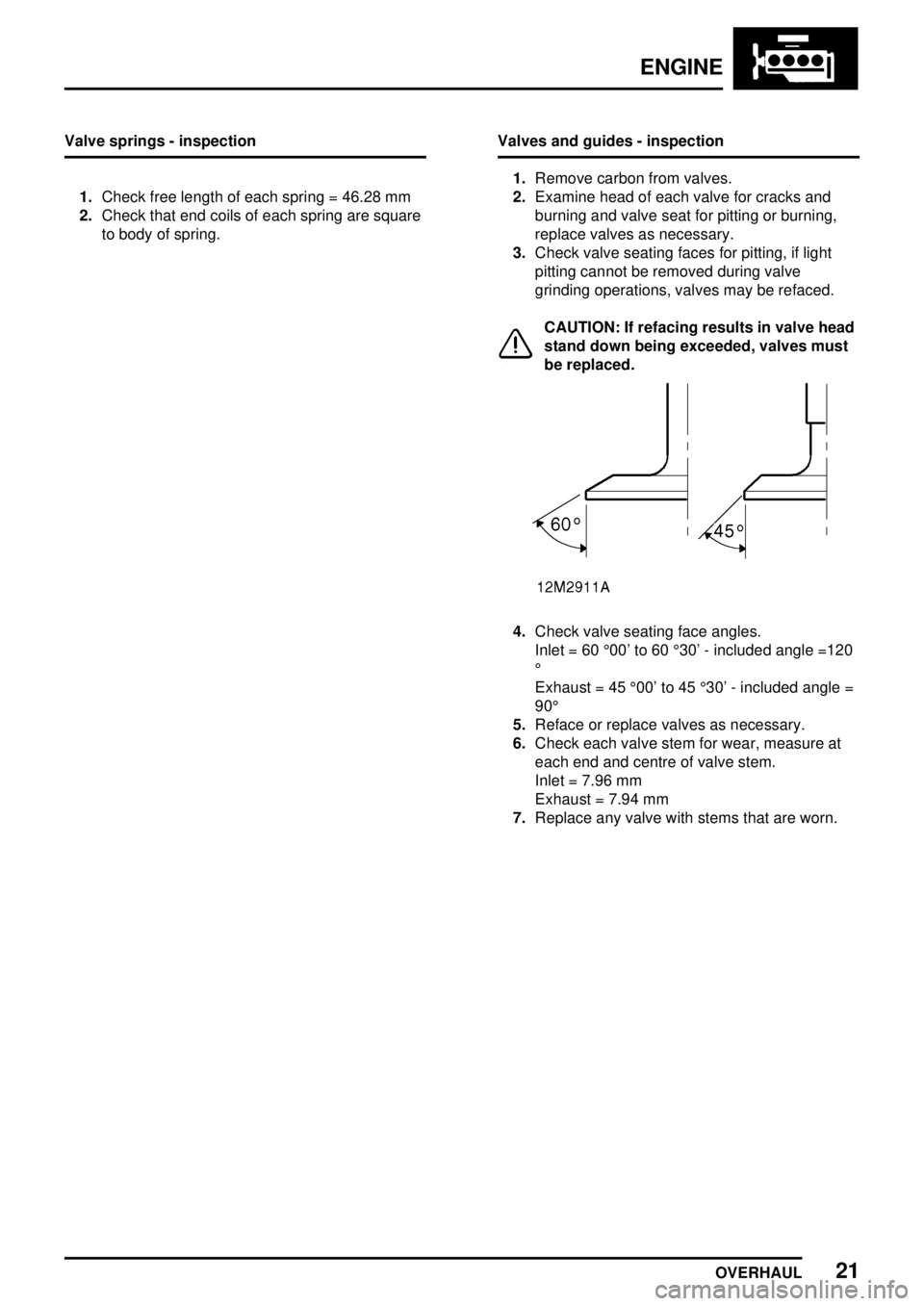
ENGINE
OVERHAUL21
Valve springs - inspection
1.Check free length of each spring = 46.28 mm
2.Check that end coils of each spring are square
to body of spring.Valves and guides - inspection
1.Remove carbon from valves.
2.Examine head of each valve for cracks and
burning and valve seat for pitting or burning,
replace valves as necessary.
3.Check valve seating faces for pitting, if light
pitting cannot be removed during valve
grinding operations, valves may be refaced.
CAUTION: If refacing results in valve head
stand down being exceeded, valves must
be replaced.
4.Check valve seating face angles.
Inlet = 60°00' to 60°30' - included angle =120
°
Exhaust = 45°00' to 45°30' - included angle =
90°
5.Reface or replace valves as necessary.
6.Check each valve stem for wear, measure at
each end and centre of valve stem.
Inlet = 7.96 mm
Exhaust = 7.94 mm
7.Replace any valve with stems that are worn.
Page 917 of 976
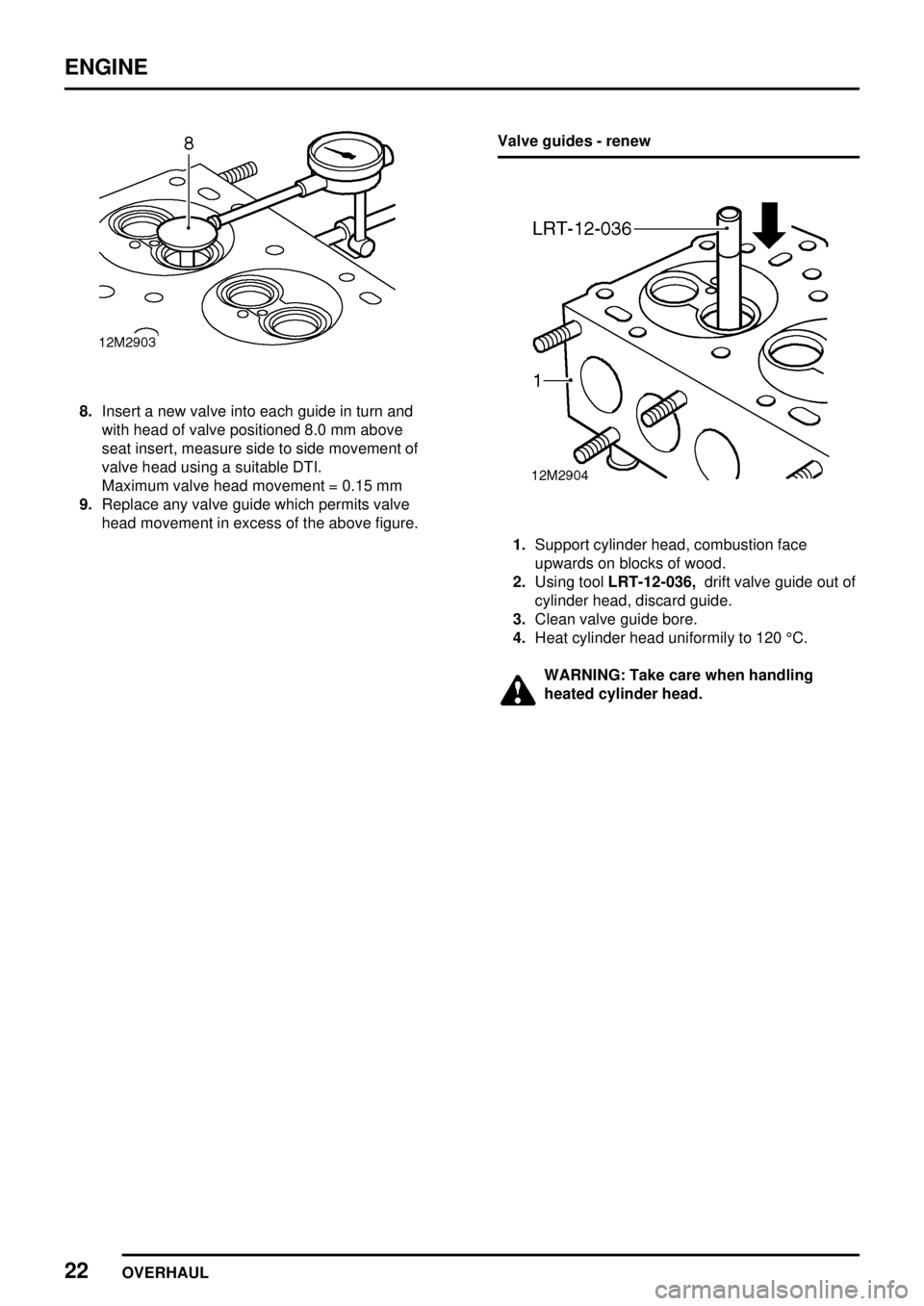
ENGINE
22
OVERHAUL
8.Insert a new valve into each guide in turn and
with head of valve positioned 8.0 mm above
seat insert, measure side to side movement of
valve head using a suitable DTI.
Maximum valve head movement = 0.15 mm
9.Replace any valve guide which permits valve
head movement in excess of the above figure.Valve guides - renew
1.Support cylinder head, combustion face
upwards on blocks of wood.
2.Using toolLRT-12-036,drift valve guide out of
cylinder head, discard guide.
3.Clean valve guide bore.
4.Heat cylinder head uniformily to 120°C.
WARNING: Take care when handling
heated cylinder head.
Page 918 of 976
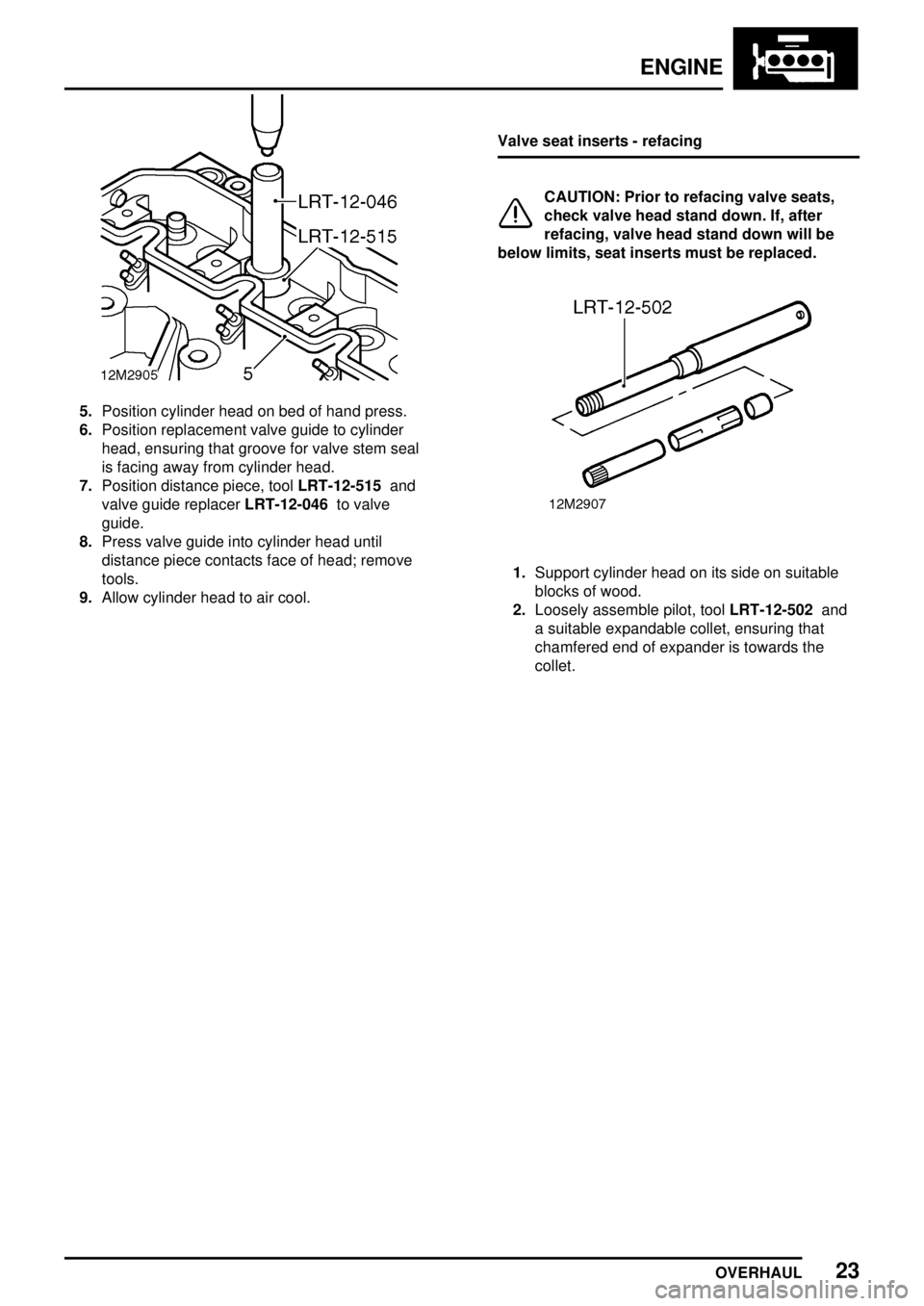
ENGINE
OVERHAUL23
5.Position cylinder head on bed of hand press.
6.Position replacement valve guide to cylinder
head, ensuring that groove for valve stem seal
is facing away from cylinder head.
7.Position distance piece, toolLRT-12-515and
valve guide replacerLRT-12-046to valve
guide.
8.Press valve guide into cylinder head until
distance piece contacts face of head; remove
tools.
9.Allow cylinder head to air cool.Valve seat inserts - refacing
CAUTION: Prior to refacing valve seats,
check valve head stand down. If, after
refacing, valve head stand down will be
below limits, seat inserts must be replaced.
1.Support cylinder head on its side on suitable
blocks of wood.
2.Loosely assemble pilot, toolLRT-12-502and
a suitable expandable collet, ensuring that
chamfered end of expander is towards the
collet.
Page 919 of 976
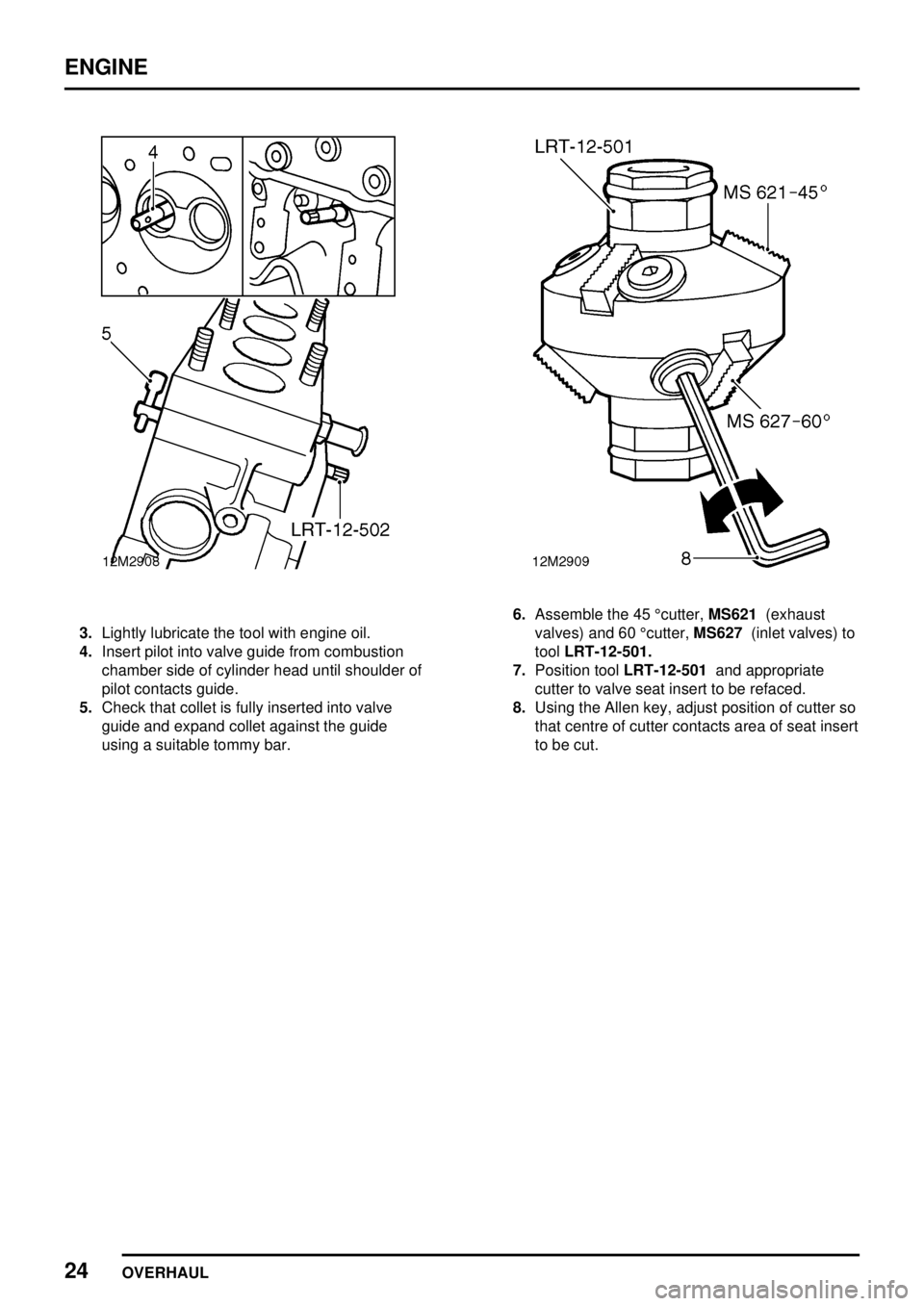
ENGINE
24
OVERHAUL
3.Lightly lubricate the tool with engine oil.
4.Insert pilot into valve guide from combustion
chamber side of cylinder head until shoulder of
pilot contacts guide.
5.Check that collet is fully inserted into valve
guide and expand collet against the guide
using a suitable tommy bar.
6.Assemble the 45°cutter,MS621(exhaust
valves) and 60°cutter,MS627(inlet valves) to
toolLRT-12-501.
7.Position toolLRT-12-501and appropriate
cutter to valve seat insert to be refaced.
8.Using the Allen key, adjust position of cutter so
that centre of cutter contacts area of seat insert
to be cut.
Page 920 of 976
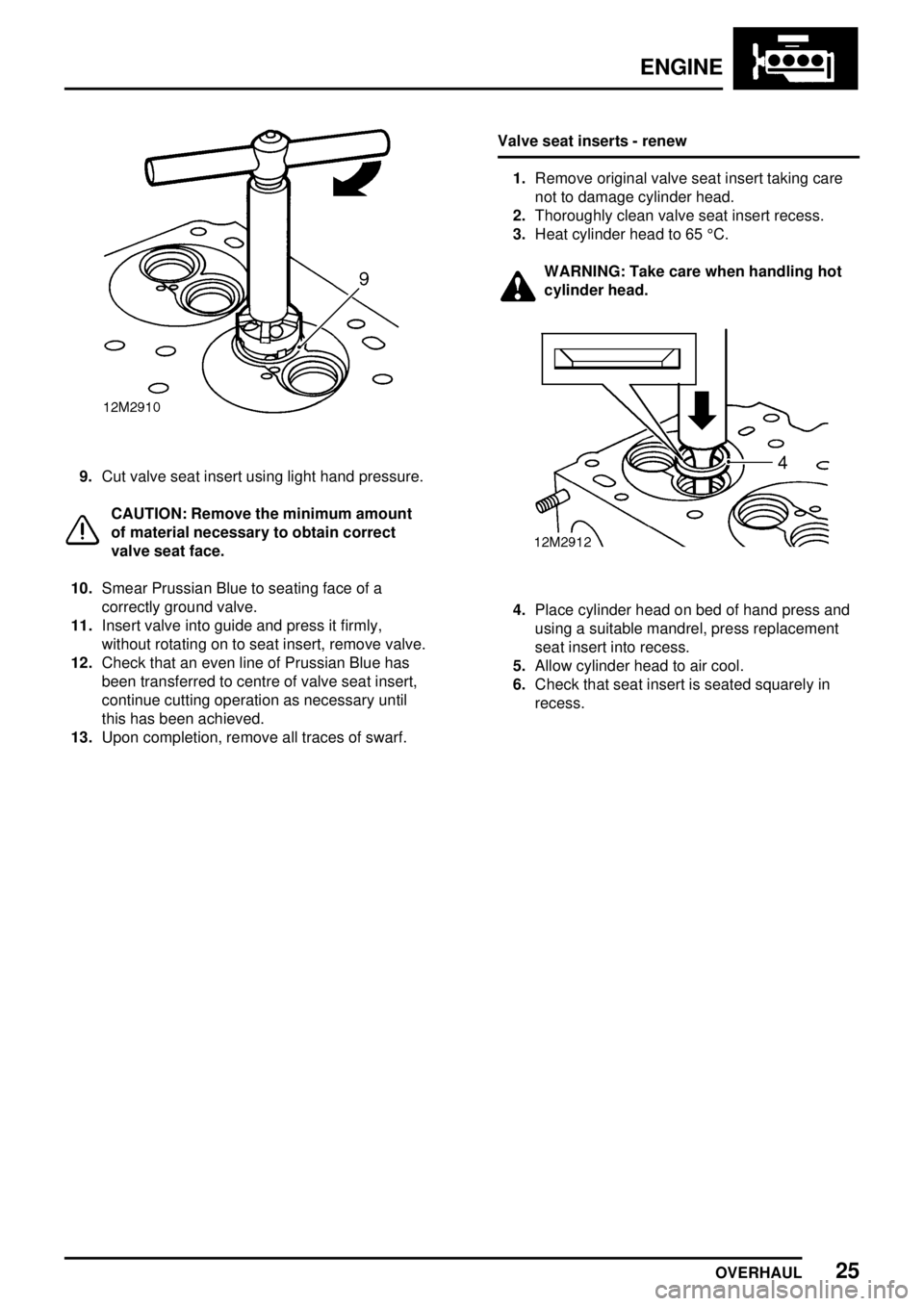
ENGINE
OVERHAUL25
9.Cut valve seat insert using light hand pressure.
CAUTION: Remove the minimum amount
of material necessary to obtain correct
valve seat face.
10.Smear Prussian Blue to seating face of a
correctly ground valve.
11.Insert valve into guide and press it firmly,
without rotating on to seat insert, remove valve.
12.Check that an even line of Prussian Blue has
been transferred to centre of valve seat insert,
continue cutting operation as necessary until
this has been achieved.
13.Upon completion, remove all traces of swarf.Valve seat inserts - renew
1.Remove original valve seat insert taking care
not to damage cylinder head.
2.Thoroughly clean valve seat insert recess.
3.Heat cylinder head to 65°C.
WARNING: Take care when handling hot
cylinder head.
4.Place cylinder head on bed of hand press and
using a suitable mandrel, press replacement
seat insert into recess.
5.Allow cylinder head to air cool.
6.Check that seat insert is seated squarely in
recess.