relay LAND ROVER DISCOVERY 1999 Owner's Manual
[x] Cancel search | Manufacturer: LAND ROVER, Model Year: 1999, Model line: DISCOVERY, Model: LAND ROVER DISCOVERY 1999Pages: 1529, PDF Size: 34.8 MB
Page 337 of 1529
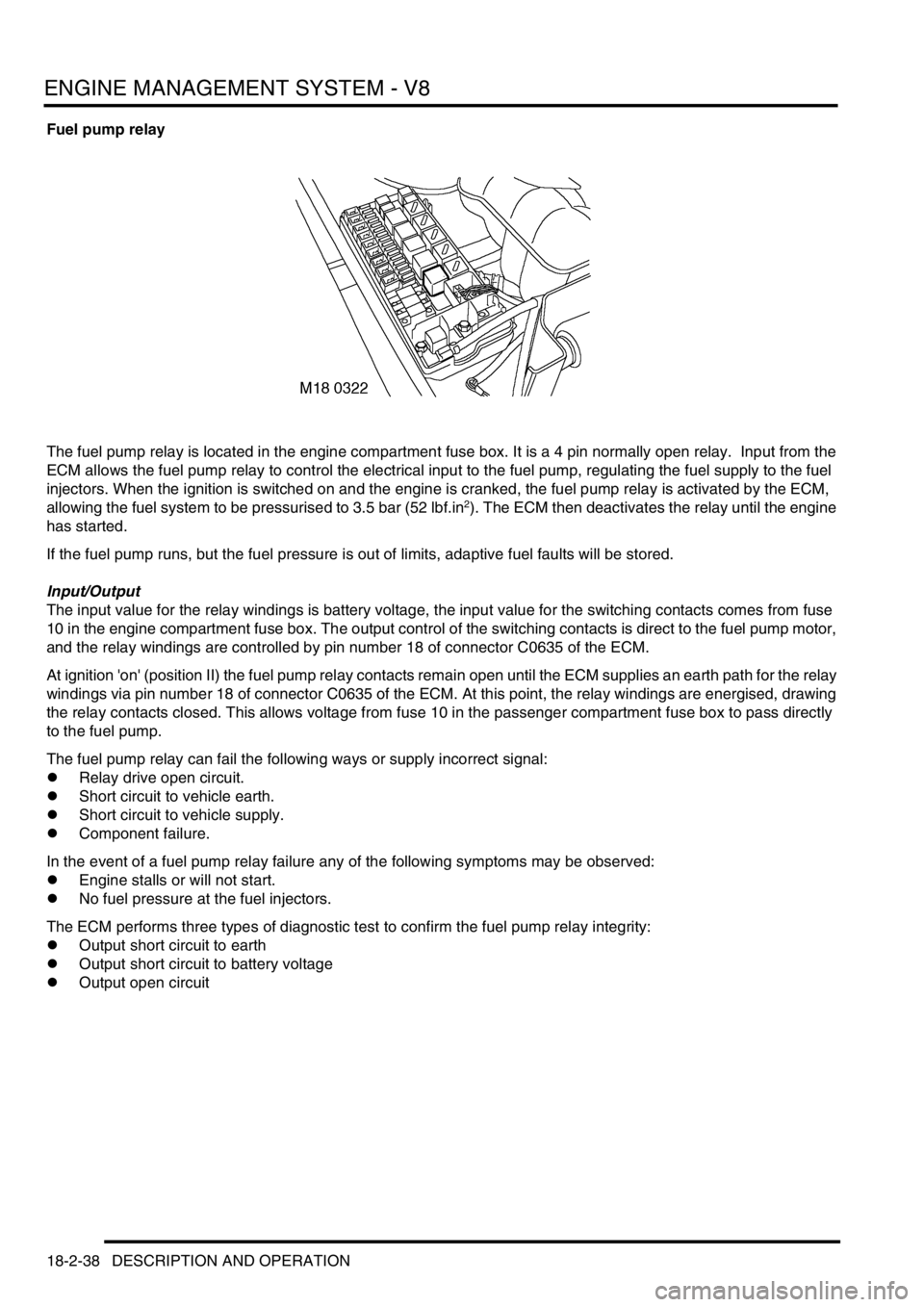
ENGINE MANAGEMENT SYSTEM - V8
18-2-38 DESCRIPTION AND OPERATION
Fuel pump relay
The fuel pump relay is located in the engine compartment fuse box. It is a 4 pin normally open relay. Input from the
ECM allows the fuel pump relay to control the electrical input to the fuel pump, regulating the fuel supply to the fuel
injectors. When the ignition is switched on and the engine is cranked, the fuel pump relay is activated by the ECM,
allowing the fuel system to be pressurised to 3.5 bar (52 lbf.in
2). The ECM then deactivates the relay until the engine
has started.
If the fuel pump runs, but the fuel pressure is out of limits, adaptive fuel faults will be stored.
Input/Output
The input value for the relay windings is battery voltage, the input value for the switching contacts comes from fuse
10 in the engine compartment fuse box. The output control of the switching contacts is direct to the fuel pump motor,
and the relay windings are controlled by pin number 18 of connector C0635 of the ECM.
At ignition 'on' (position II) the fuel pump relay contacts remain open until the ECM supplies an earth path for the relay
windings via pin number 18 of connector C0635 of the ECM. At this point, the relay windings are energised, drawing
the relay contacts closed. This allows voltage from fuse 10 in the passenger compartment fuse box to pass directly
to the fuel pump.
The fuel pump relay can fail the following ways or supply incorrect signal:
lRelay drive open circuit.
lShort circuit to vehicle earth.
lShort circuit to vehicle supply.
lComponent failure.
In the event of a fuel pump relay failure any of the following symptoms may be observed:
lEngine stalls or will not start.
lNo fuel pressure at the fuel injectors.
The ECM performs three types of diagnostic test to confirm the fuel pump relay integrity:
lOutput short circuit to earth
lOutput short circuit to battery voltage
lOutput open circuit
Page 338 of 1529
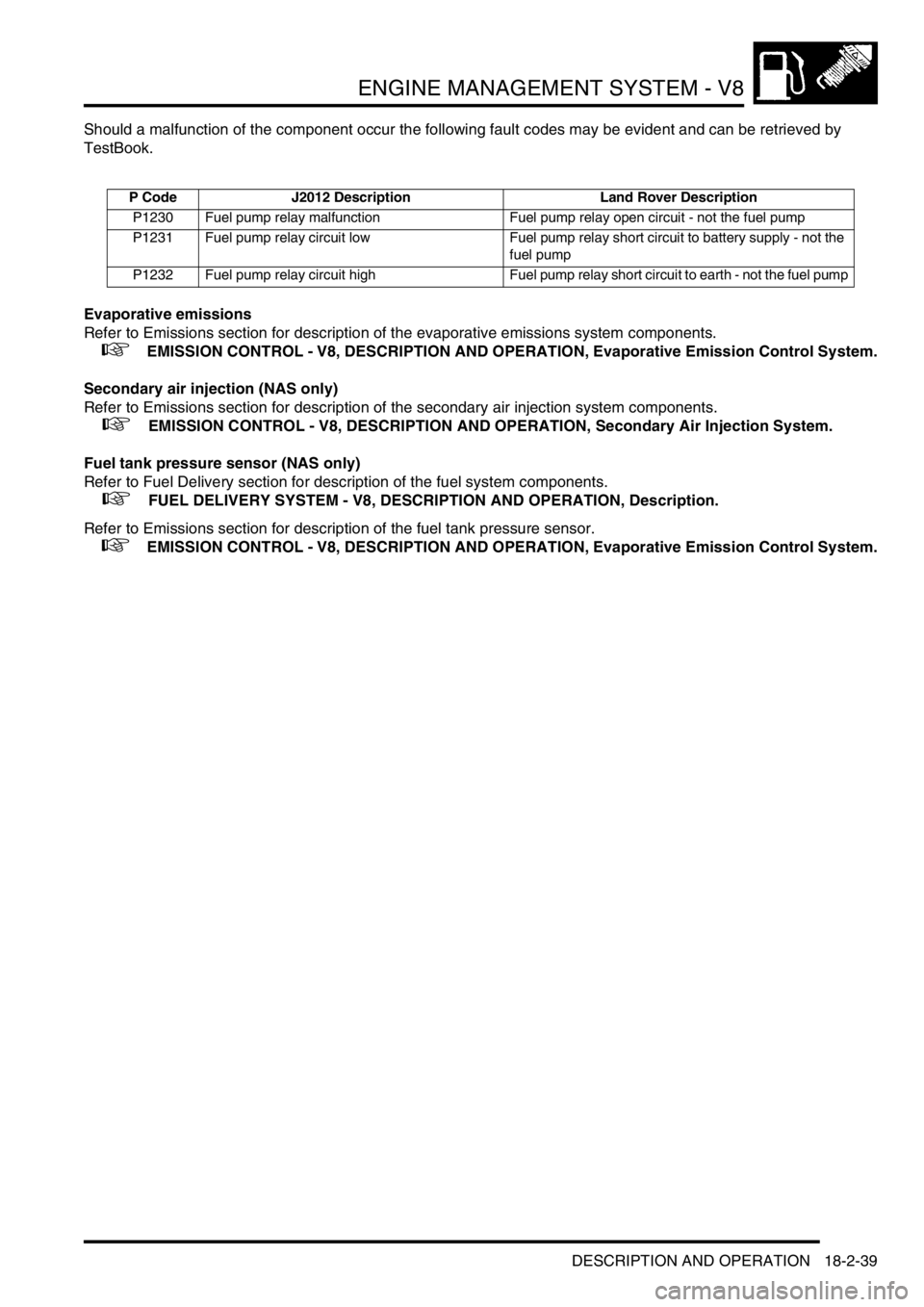
ENGINE MANAGEMENT SYSTEM - V8
DESCRIPTION AND OPERATION 18-2-39
Should a malfunction of the component occur the following fault codes may be evident and can be retrieved by
TestBook.
Evaporative emissions
Refer to Emissions section for description of the evaporative emissions system components.
+ EMISSION CONTROL - V8, DESCRIPTION AND OPERATION, Evaporative Emission Control System.
Secondary air injection (NAS only)
Refer to Emissions section for description of the secondary air injection system components.
+ EMISSION CONTROL - V8, DESCRIPTION AND OPERATION, Secondary Air Injection System.
Fuel tank pressure sensor (NAS only)
Refer to Fuel Delivery section for description of the fuel system components.
+ FUEL DELIVERY SYSTEM - V8, DESCRIPTION AND OPERATION, Description.
Refer to Emissions section for description of the fuel tank pressure sensor.
+ EMISSION CONTROL - V8, DESCRIPTION AND OPERATION, Evaporative Emission Control System.
P Code J2012 Description Land Rover Description
P1230 Fuel pump relay malfunction Fuel pump relay open circuit - not the fuel pump
P1231 Fuel pump relay circuit low Fuel pump relay short circuit to battery supply - not the
fuel pump
P1232 Fuel pump relay circuit high Fuel pump relay short circuit to earth - not the fuel pump
Page 346 of 1529
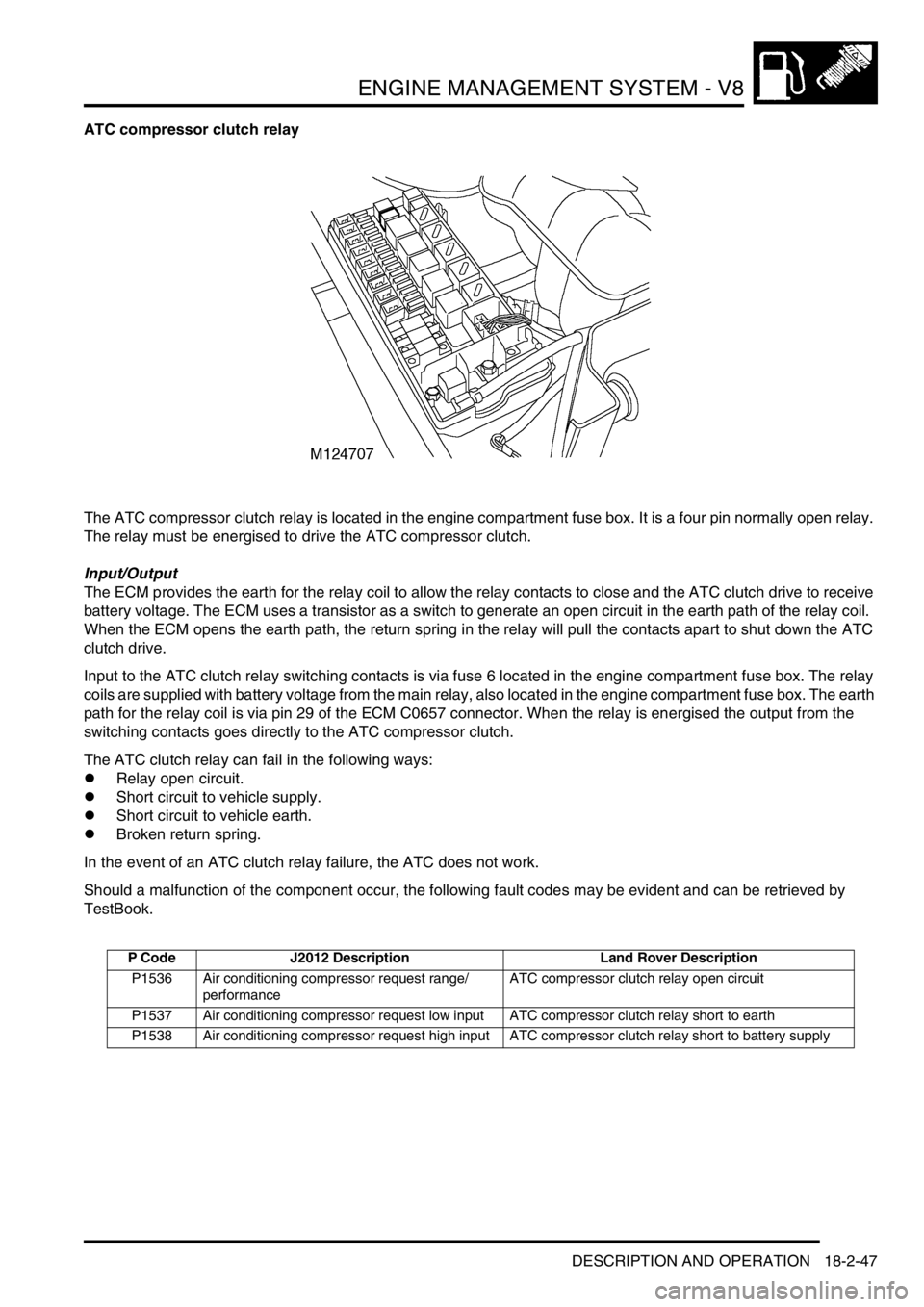
ENGINE MANAGEMENT SYSTEM - V8
DESCRIPTION AND OPERATION 18-2-47
ATC compressor clutch relay
The ATC compressor clutch relay is located in the engine compartment fuse box. It is a four pin normally open relay.
The relay must be energised to drive the ATC compressor clutch.
Input/Output
The ECM provides the earth for the relay coil to allow the relay contacts to close and the ATC clutch drive to receive
battery voltage. The ECM uses a transistor as a switch to generate an open circuit in the earth path of the relay coil.
When the ECM opens the earth path, the return spring in the relay will pull the contacts apart to shut down the ATC
clutch drive.
Input to the ATC clutch relay switching contacts is via fuse 6 located in the engine compartment fuse box. The relay
coils are supplied with battery voltage from the main relay, also located in the engine compartment fuse box. The earth
path for the relay coil is via pin 29 of the ECM C0657 connector. When the relay is energised the output from the
switching contacts goes directly to the ATC compressor clutch.
The ATC clutch relay can fail in the following ways:
lRelay open circuit.
lShort circuit to vehicle supply.
lShort circuit to vehicle earth.
lBroken return spring.
In the event of an ATC clutch relay failure, the ATC does not work.
Should a malfunction of the component occur, the following fault codes may be evident and can be retrieved by
TestBook.
P Code J2012 Description Land Rover Description
P1536 Air conditioning compressor request range/
performanceATC compressor clutch relay open circuit
P1537 Air conditioning compressor request low input ATC compressor clutch relay short to earth
P1538 Air conditioning compressor request high input ATC compressor clutch relay short to battery supply
Page 347 of 1529
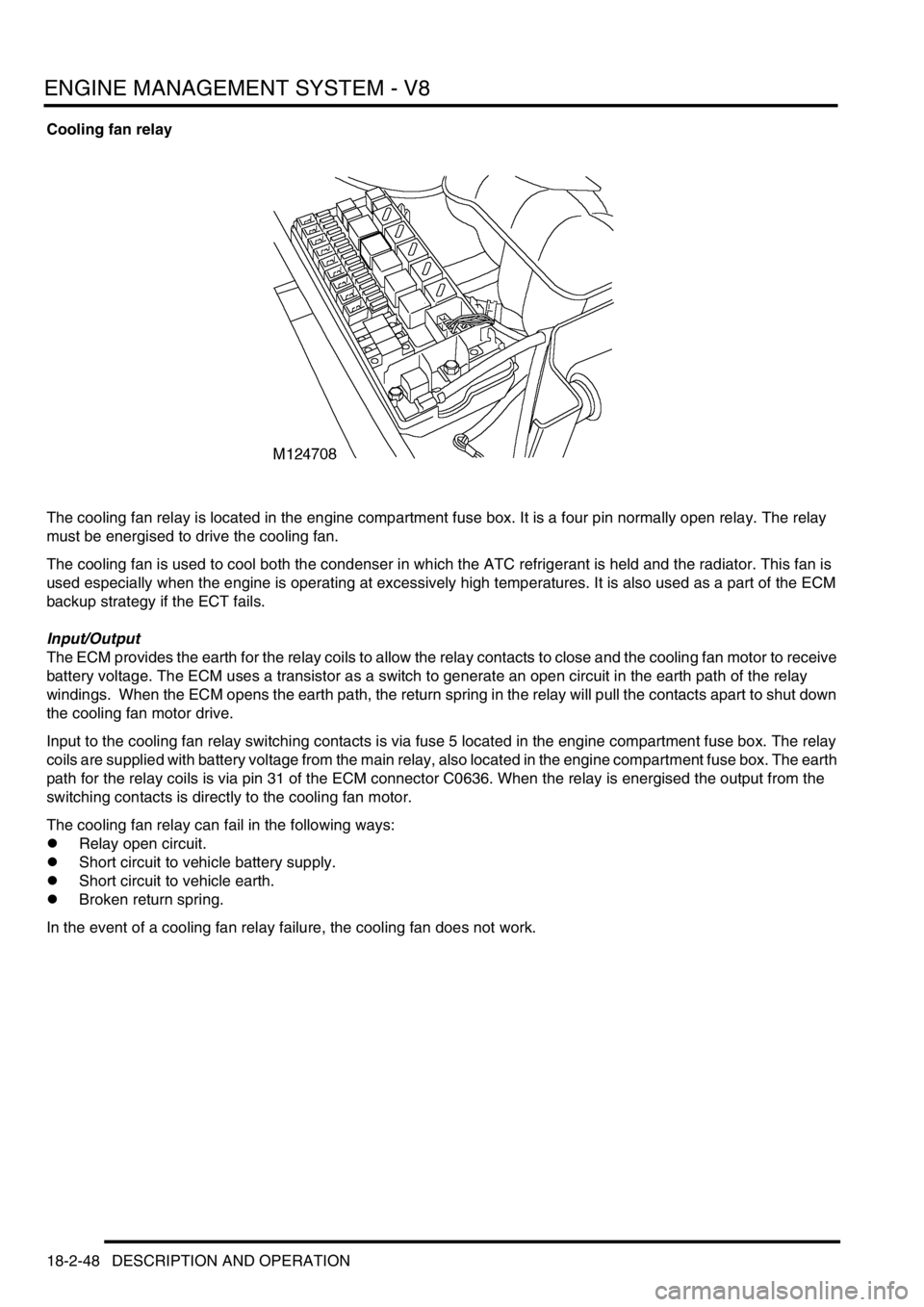
ENGINE MANAGEMENT SYSTEM - V8
18-2-48 DESCRIPTION AND OPERATION
Cooling fan relay
The cooling fan relay is located in the engine compartment fuse box. It is a four pin normally open relay. The relay
must be energised to drive the cooling fan.
The cooling fan is used to cool both the condenser in which the ATC refrigerant is held and the radiator. This fan is
used especially when the engine is operating at excessively high temperatures. It is also used as a part of the ECM
backup strategy if the ECT fails.
Input/Output
The ECM provides the earth for the relay coils to allow the relay contacts to close and the cooling fan motor to receive
battery voltage. The ECM uses a transistor as a switch to generate an open circuit in the earth path of the relay
windings. When the ECM opens the earth path, the return spring in the relay will pull the contacts apart to shut down
the cooling fan motor drive.
Input to the cooling fan relay switching contacts is via fuse 5 located in the engine compartment fuse box. The relay
coils are supplied with battery voltage from the main relay, also located in the engine compartment fuse box. The earth
path for the relay coils is via pin 31 of the ECM connector C0636. When the relay is energised the output from the
switching contacts is directly to the cooling fan motor.
The cooling fan relay can fail in the following ways:
lRelay open circuit.
lShort circuit to vehicle battery supply.
lShort circuit to vehicle earth.
lBroken return spring.
In the event of a cooling fan relay failure, the cooling fan does not work.
Page 401 of 1529
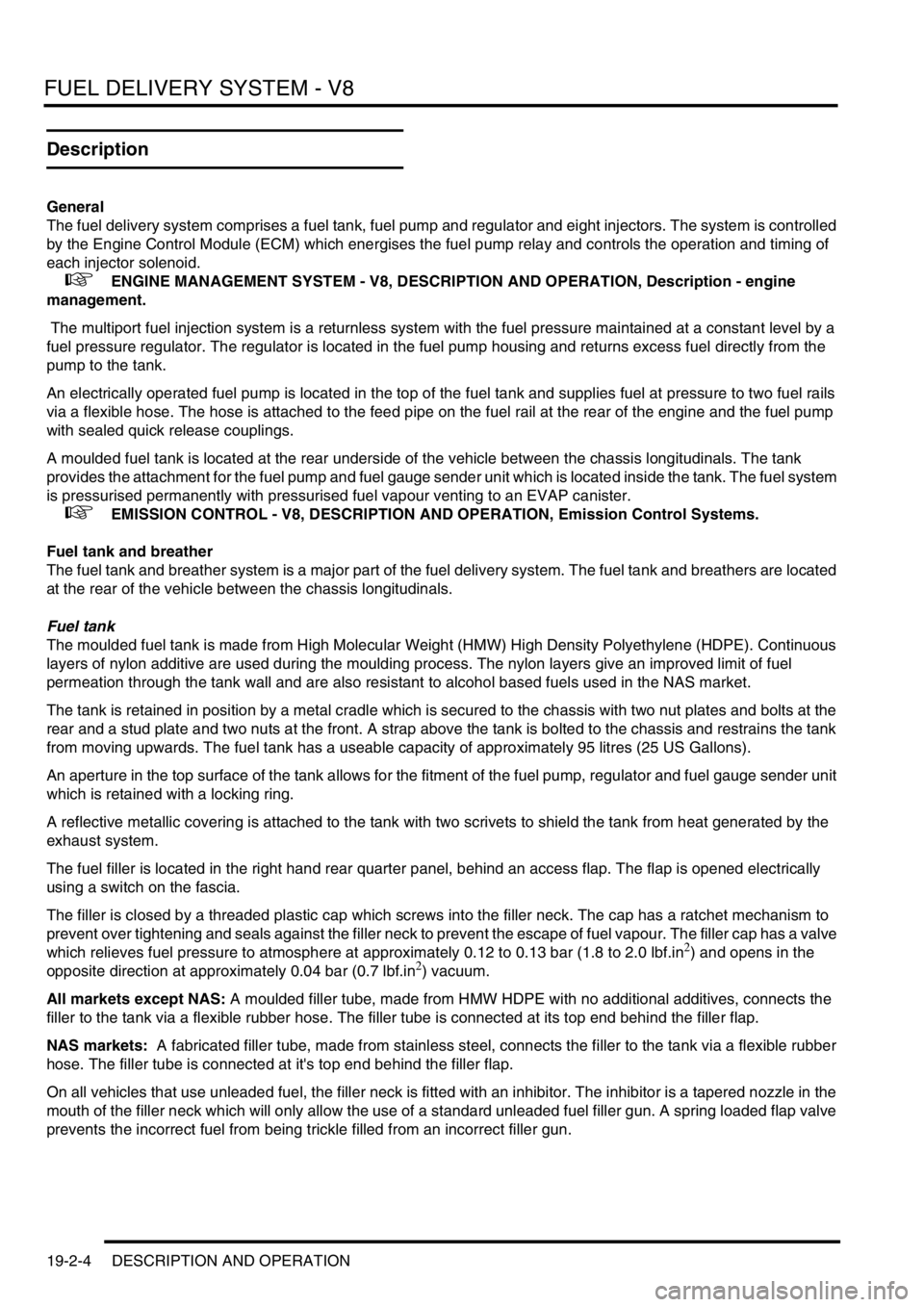
FUEL DELIVERY SYSTEM - V8
19-2-4 DESCRIPTION AND OPERATION
Description
General
The fuel delivery system comprises a fuel tank, fuel pump and regulator and eight injectors. The system is controlled
by the Engine Control Module (ECM) which energises the fuel pump relay and controls the operation and timing of
each injector solenoid.
+ ENGINE MANAGEMENT SYSTEM - V8, DESCRIPTION AND OPERATION, Description - engine
management.
The multiport fuel injection system is a returnless system with the fuel pressure maintained at a constant level by a
fuel pressure regulator. The regulator is located in the fuel pump housing and returns excess fuel directly from the
pump to the tank.
An electrically operated fuel pump is located in the top of the fuel tank and supplies fuel at pressure to two fuel rails
via a flexible hose. The hose is attached to the feed pipe on the fuel rail at the rear of the engine and the fuel pump
with sealed quick release couplings.
A moulded fuel tank is located at the rear underside of the vehicle between the chassis longitudinals. The tank
provides the attachment for the fuel pump and fuel gauge sender unit which is located inside the tank. The fuel system
is pressurised permanently with pressurised fuel vapour venting to an EVAP canister.
+ EMISSION CONTROL - V8, DESCRIPTION AND OPERATION, Emission Control Systems.
Fuel tank and breather
The fuel tank and breather system is a major part of the fuel delivery system. The fuel tank and breathers are located
at the rear of the vehicle between the chassis longitudinals.
Fuel tank
The moulded fuel tank is made from High Molecular Weight (HMW) High Density Polyethylene (HDPE). Continuous
layers of nylon additive are used during the moulding process. The nylon layers give an improved limit of fuel
permeation through the tank wall and are also resistant to alcohol based fuels used in the NAS market.
The tank is retained in position by a metal cradle which is secured to the chassis with two nut plates and bolts at the
rear and a stud plate and two nuts at the front. A strap above the tank is bolted to the chassis and restrains the tank
from moving upwards. The fuel tank has a useable capacity of approximately 95 litres (25 US Gallons).
An aperture in the top surface of the tank allows for the fitment of the fuel pump, regulator and fuel gauge sender unit
which is retained with a locking ring.
A reflective metallic covering is attached to the tank with two scrivets to shield the tank from heat generated by the
exhaust system.
The fuel filler is located in the right hand rear quarter panel, behind an access flap. The flap is opened electrically
using a switch on the fascia.
The filler is closed by a threaded plastic cap which screws into the filler neck. The cap has a ratchet mechanism to
prevent over tightening and seals against the filler neck to prevent the escape of fuel vapour. The filler cap has a valve
which relieves fuel pressure to atmosphere at approximately 0.12 to 0.13 bar (1.8 to 2.0 lbf.in
2) and opens in the
opposite direction at approximately 0.04 bar (0.7 lbf.in2) vacuum.
All markets except NAS: A moulded filler tube, made from HMW HDPE with no additional additives, connects the
filler to the tank via a flexible rubber hose. The filler tube is connected at its top end behind the filler flap.
NAS markets: A fabricated filler tube, made from stainless steel, connects the filler to the tank via a flexible rubber
hose. The filler tube is connected at it's top end behind the filler flap.
On all vehicles that use unleaded fuel, the filler neck is fitted with an inhibitor. The inhibitor is a tapered nozzle in the
mouth of the filler neck which will only allow the use of a standard unleaded fuel filler gun. A spring loaded flap valve
prevents the incorrect fuel from being trickle filled from an incorrect filler gun.
Page 403 of 1529
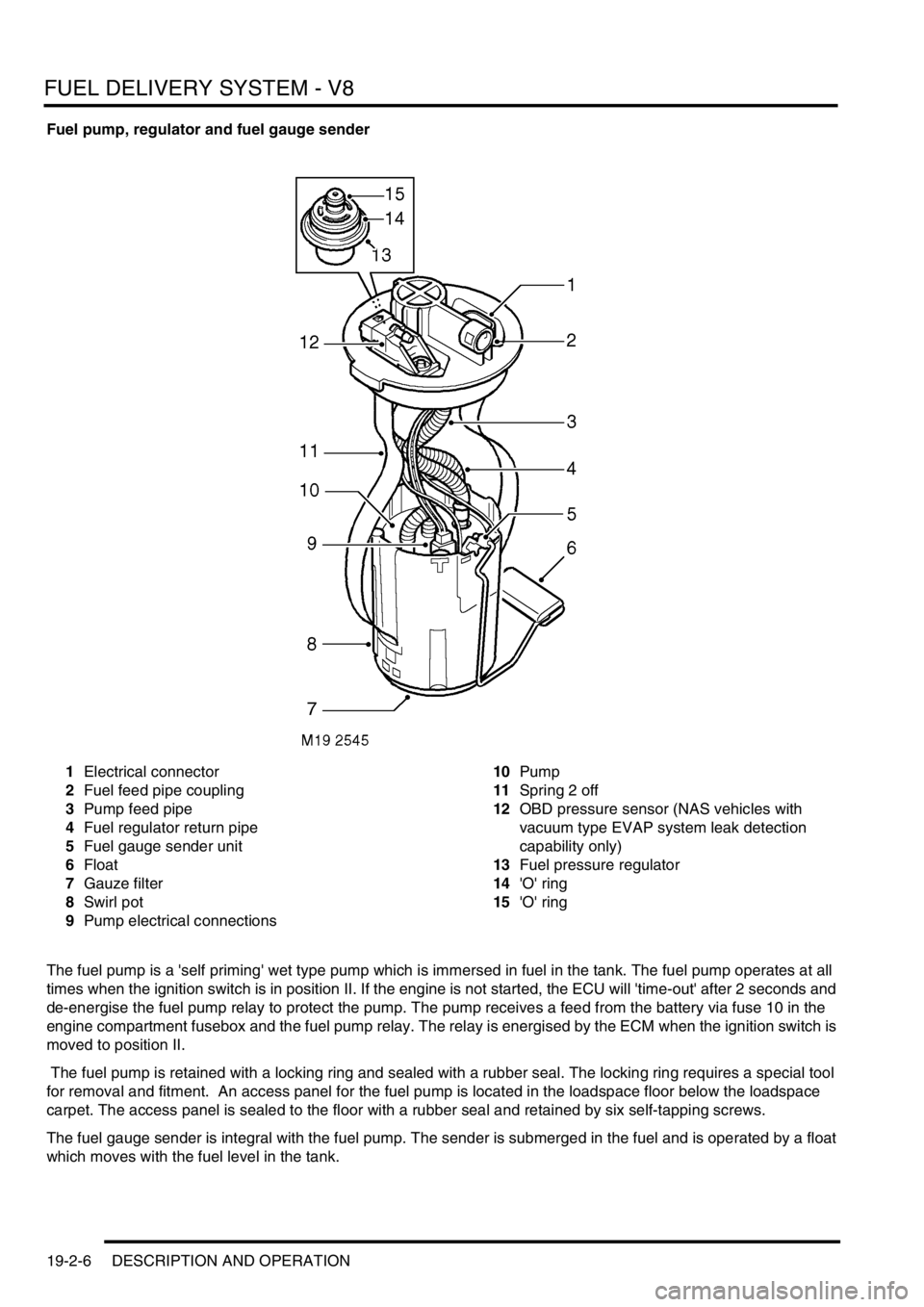
FUEL DELIVERY SYSTEM - V8
19-2-6 DESCRIPTION AND OPERATION
Fuel pump, regulator and fuel gauge sender
1Electrical connector
2Fuel feed pipe coupling
3Pump feed pipe
4Fuel regulator return pipe
5Fuel gauge sender unit
6Float
7Gauze filter
8Swirl pot
9Pump electrical connections10Pump
11Spring 2 off
12OBD pressure sensor (NAS vehicles with
vacuum type EVAP system leak detection
capability only)
13Fuel pressure regulator
14'O' ring
15'O' ring
The fuel pump is a 'self priming' wet type pump which is immersed in fuel in the tank. The fuel pump operates at all
times when the ignition switch is in position II. If the engine is not started, the ECU will 'time-out' after 2 seconds and
de-energise the fuel pump relay to protect the pump. The pump receives a feed from the battery via fuse 10 in the
engine compartment fusebox and the fuel pump relay. The relay is energised by the ECM when the ignition switch is
moved to position II.
The fuel pump is retained with a locking ring and sealed with a rubber seal. The locking ring requires a special tool
for removal and fitment. An access panel for the fuel pump is located in the loadspace floor below the loadspace
carpet. The access panel is sealed to the floor with a rubber seal and retained by six self-tapping screws.
The fuel gauge sender is integral with the fuel pump. The sender is submerged in the fuel and is operated by a float
which moves with the fuel level in the tank.
Page 407 of 1529
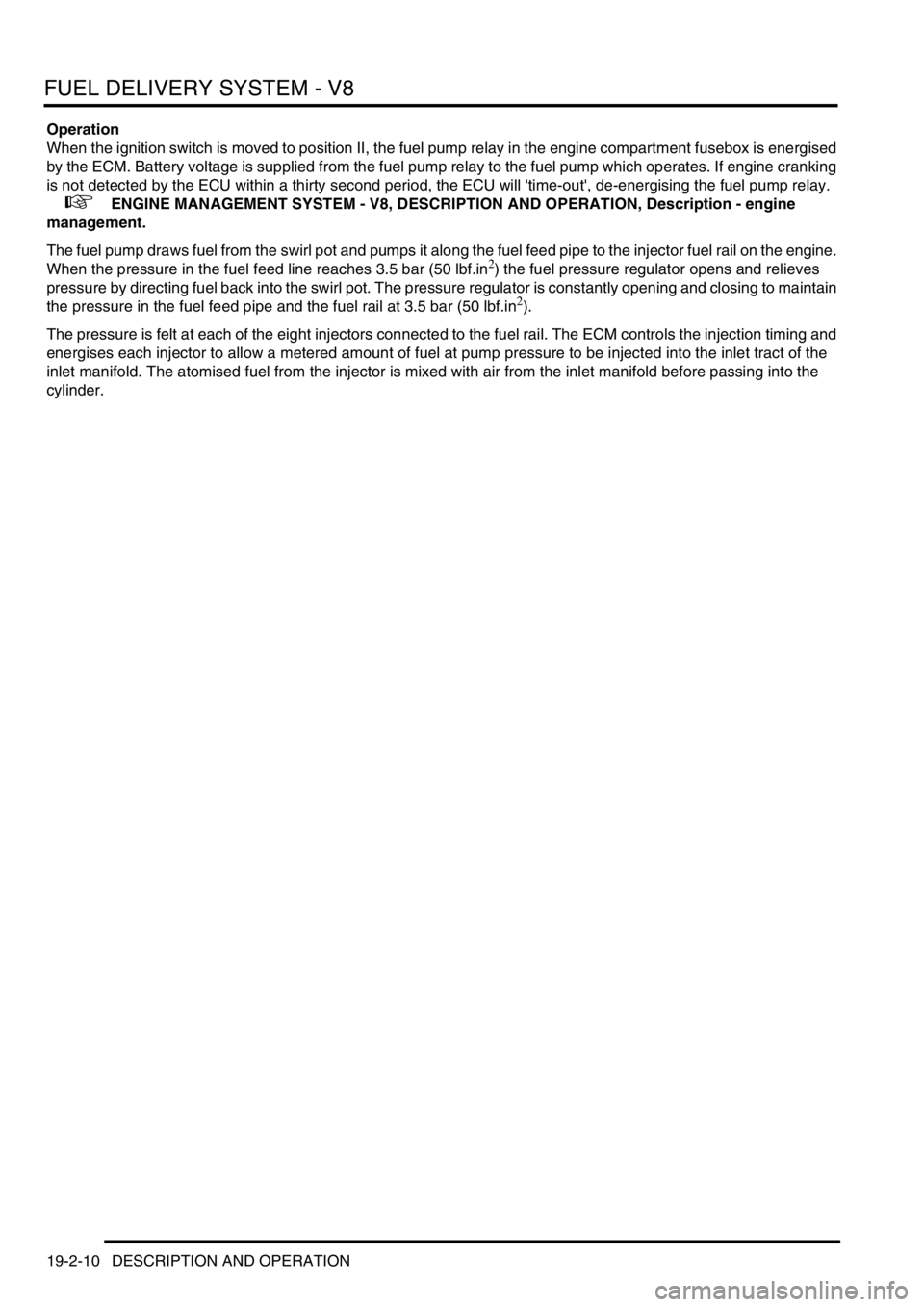
FUEL DELIVERY SYSTEM - V8
19-2-10 DESCRIPTION AND OPERATION
Operation
When the ignition switch is moved to position II, the fuel pump relay in the engine compartment fusebox is energised
by the ECM. Battery voltage is supplied from the fuel pump relay to the fuel pump which operates. If engine cranking
is not detected by the ECU within a thirty second period, the ECU will 'time-out', de-energising the fuel pump relay.
+ ENGINE MANAGEMENT SYSTEM - V8, DESCRIPTION AND OPERATION, Description - engine
management.
The fuel pump draws fuel from the swirl pot and pumps it along the fuel feed pipe to the injector fuel rail on the engine.
When the pressure in the fuel feed line reaches 3.5 bar (50 lbf.in
2) the fuel pressure regulator opens and relieves
pressure by directing fuel back into the swirl pot. The pressure regulator is constantly opening and closing to maintain
the pressure in the fuel feed pipe and the fuel rail at 3.5 bar (50 lbf.in
2).
The pressure is felt at each of the eight injectors connected to the fuel rail. The ECM controls the injection timing and
energises each injector to allow a metered amount of fuel at pump pressure to be injected into the inlet tract of the
inlet manifold. The atomised fuel from the injector is mixed with air from the inlet manifold before passing into the
cylinder.
Page 538 of 1529
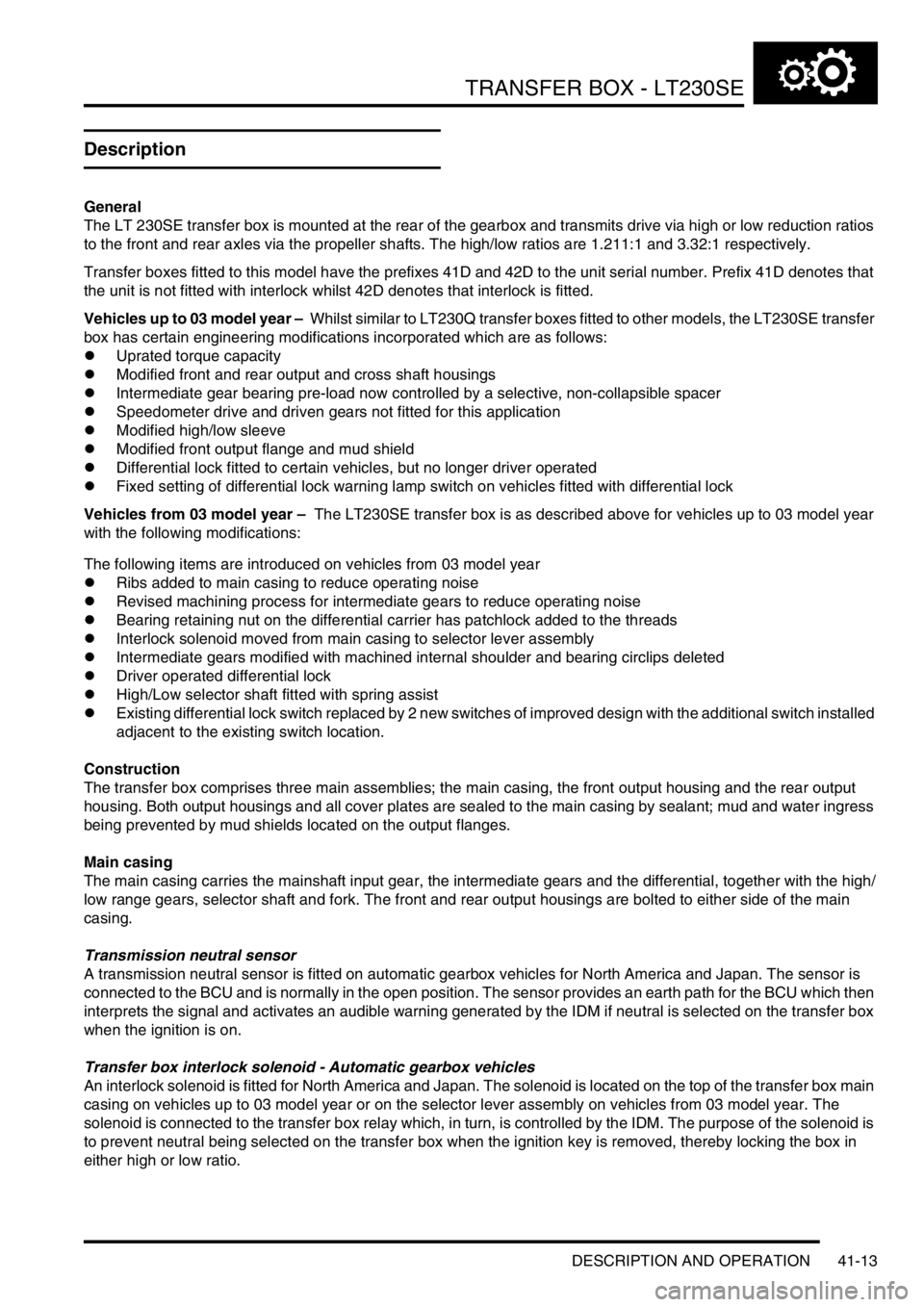
TRANSFER BOX - LT230SE
DESCRIPTION AND OPERATION 41-13
Description
General
The LT 230SE transfer box is mounted at the rear of the gearbox and transmits drive via high or low reduction ratios
to the front and rear axles via the propeller shafts. The high/low ratios are 1.211:1 and 3.32:1 respectively.
Transfer boxes fitted to this model have the prefixes 41D and 42D to the unit serial number. Prefix 41D denotes that
the unit is not fitted with interlock whilst 42D denotes that interlock is fitted.
Vehicles up to 03 model year – Whilst similar to LT230Q transfer boxes fitted to other models, the LT230SE transfer
box has certain engineering modifications incorporated which are as follows:
lUprated torque capacity
lModified front and rear output and cross shaft housings
lIntermediate gear bearing pre-load now controlled by a selective, non-collapsible spacer
lSpeedometer drive and driven gears not fitted for this application
lModified high/low sleeve
lModified front output flange and mud shield
lDifferential lock fitted to certain vehicles, but no longer driver operated
lFixed setting of differential lock warning lamp switch on vehicles fitted with differential lock
Vehicles from 03 model year – The LT230SE transfer box is as described above for vehicles up to 03 model year
with the following modifications:
The following items are introduced on vehicles from 03 model year
lRibs added to main casing to reduce operating noise
lRevised machining process for intermediate gears to reduce operating noise
lBearing retaining nut on the differential carrier has patchlock added to the threads
lInterlock solenoid moved from main casing to selector lever assembly
lIntermediate gears modified with machined internal shoulder and bearing circlips deleted
lDriver operated differential lock
lHigh/Low selector shaft fitted with spring assist
lExisting differential lock switch replaced by 2 new switches of improved design with the additional switch installed
adjacent to the existing switch location.
Construction
The transfer box comprises three main assemblies; the main casing, the front output housing and the rear output
housing. Both output housings and all cover plates are sealed to the main casing by sealant; mud and water ingress
being prevented by mud shields located on the output flanges.
Main casing
The main casing carries the mainshaft input gear, the intermediate gears and the differential, together with the high/
low range gears, selector shaft and fork. The front and rear output housings are bolted to either side of the main
casing.
Transmission neutral sensor
A transmission neutral sensor is fitted on automatic gearbox vehicles for North America and Japan. The sensor is
connected to the BCU and is normally in the open position. The sensor provides an earth path for the BCU which then
interprets the signal and activates an audible warning generated by the IDM if neutral is selected on the transfer box
when the ignition is on.
Transfer box interlock solenoid - Automatic gearbox vehicles
An interlock solenoid is fitted for North America and Japan. The solenoid is located on the top of the transfer box main
casing on vehicles up to 03 model year or on the selector lever assembly on vehicles from 03 model year. The
solenoid is connected to the transfer box relay which, in turn, is controlled by the IDM. The purpose of the solenoid is
to prevent neutral being selected on the transfer box when the ignition key is removed, thereby locking the box in
either high or low ratio.
Page 616 of 1529
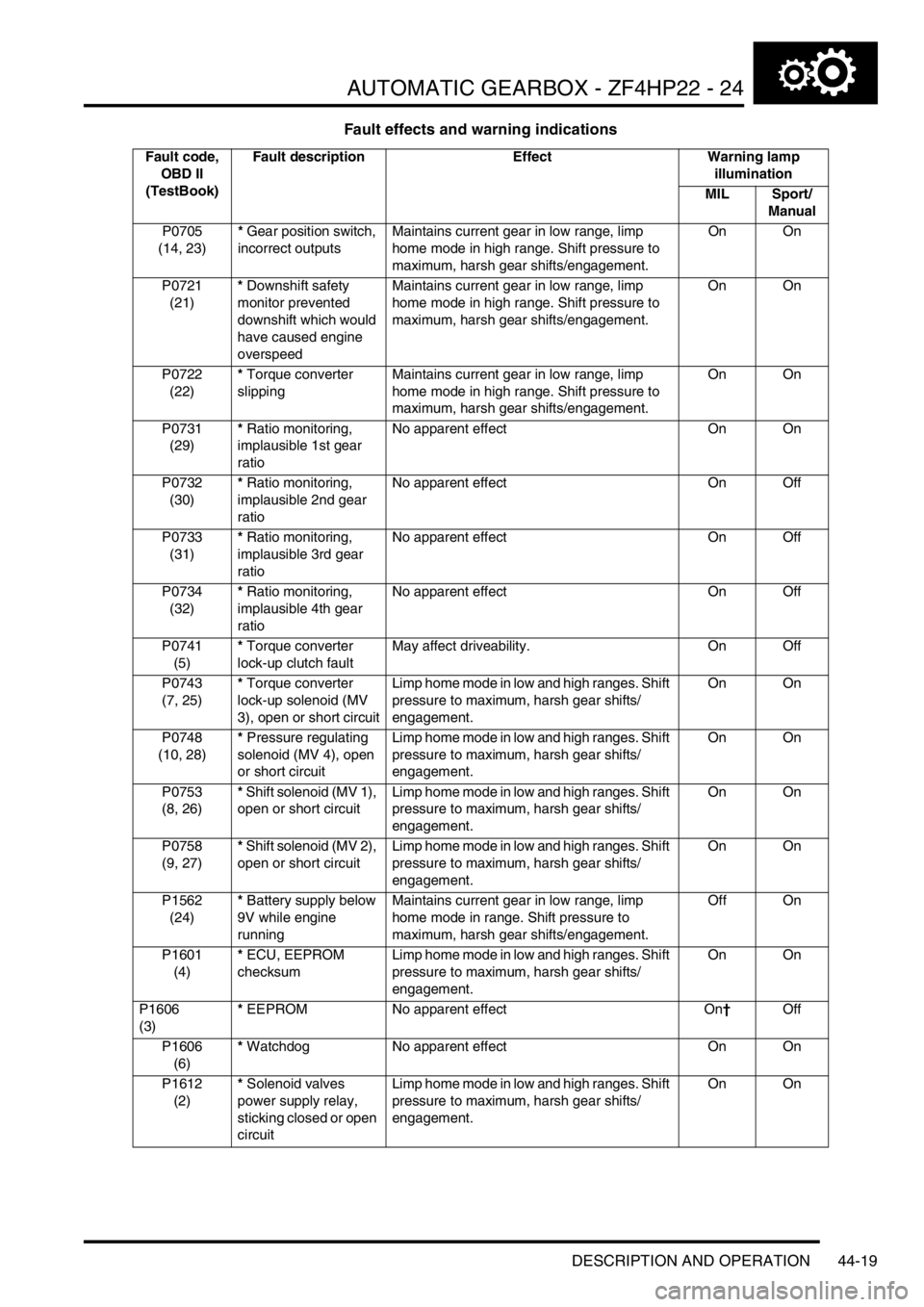
AUTOMATIC GEARBOX - ZF4HP22 - 24
DESCRIPTION AND OPERATION 44-19
Fault effects and warning indications
Fault code,
OBD II
(TestBook)Fault description Effect Warning lamp
illumination
MIL Sport/
Manual
P0705
(14, 23)* Gear position switch,
incorrect outputsMaintains current gear in low range, limp
home mode in high range. Shift pressure to
maximum, harsh gear shifts/engagement.On On
P0721
(21)* Downshift safety
monitor prevented
downshift which would
have caused engine
overspeedMaintains current gear in low range, limp
home mode in high range. Shift pressure to
maximum, harsh gear shifts/engagement.On On
P0722
(22)* Torque converter
slippingMaintains current gear in low range, limp
home mode in high range. Shift pressure to
maximum, harsh gear shifts/engagement.On On
P0731
(29)* Ratio monitoring,
implausible 1st gear
ratioNo apparent effect On On
P0732
(30)* Ratio monitoring,
implausible 2nd gear
ratioNo apparent effect On Off
P0733
(31)* Ratio monitoring,
implausible 3rd gear
ratioNo apparent effect On Off
P0734
(32)* Ratio monitoring,
implausible 4th gear
ratioNo apparent effect On Off
P0741
(5)* Torque converter
lock-up clutch faultMay affect driveability. On Off
P0743
(7, 25)* Torque converter
lock-up solenoid (MV
3), open or short circuitLimp home mode in low and high ranges. Shift
pressure to maximum, harsh gear shifts/
engagement.On On
P0748
(10, 28)* Pressure regulating
solenoid (MV 4), open
or short circuitLimp home mode in low and high ranges. Shift
pressure to maximum, harsh gear shifts/
engagement.On On
P0753
(8, 26)* Shift solenoid (MV 1),
open or short circuitLimp home mode in low and high ranges. Shift
pressure to maximum, harsh gear shifts/
engagement.On On
P0758
(9, 27)* Shift solenoid (MV 2),
open or short circuitLimp home mode in low and high ranges. Shift
pressure to maximum, harsh gear shifts/
engagement.On On
P1562
(24)* Battery supply below
9V while engine
runningMaintains current gear in low range, limp
home mode in range. Shift pressure to
maximum, harsh gear shifts/engagement.Off On
P1601
(4)* ECU, EEPROM
checksumLimp home mode in low and high ranges. Shift
pressure to maximum, harsh gear shifts/
engagement.On On
P1606
(3)* EEPROM No apparent effect On†Off
P1606
(6)* Watchdog No apparent effect On On
P1612
(2)* Solenoid valves
power supply relay,
sticking closed or open
circuitLimp home mode in low and high ranges. Shift
pressure to maximum, harsh gear shifts/
engagement.On On
Page 617 of 1529
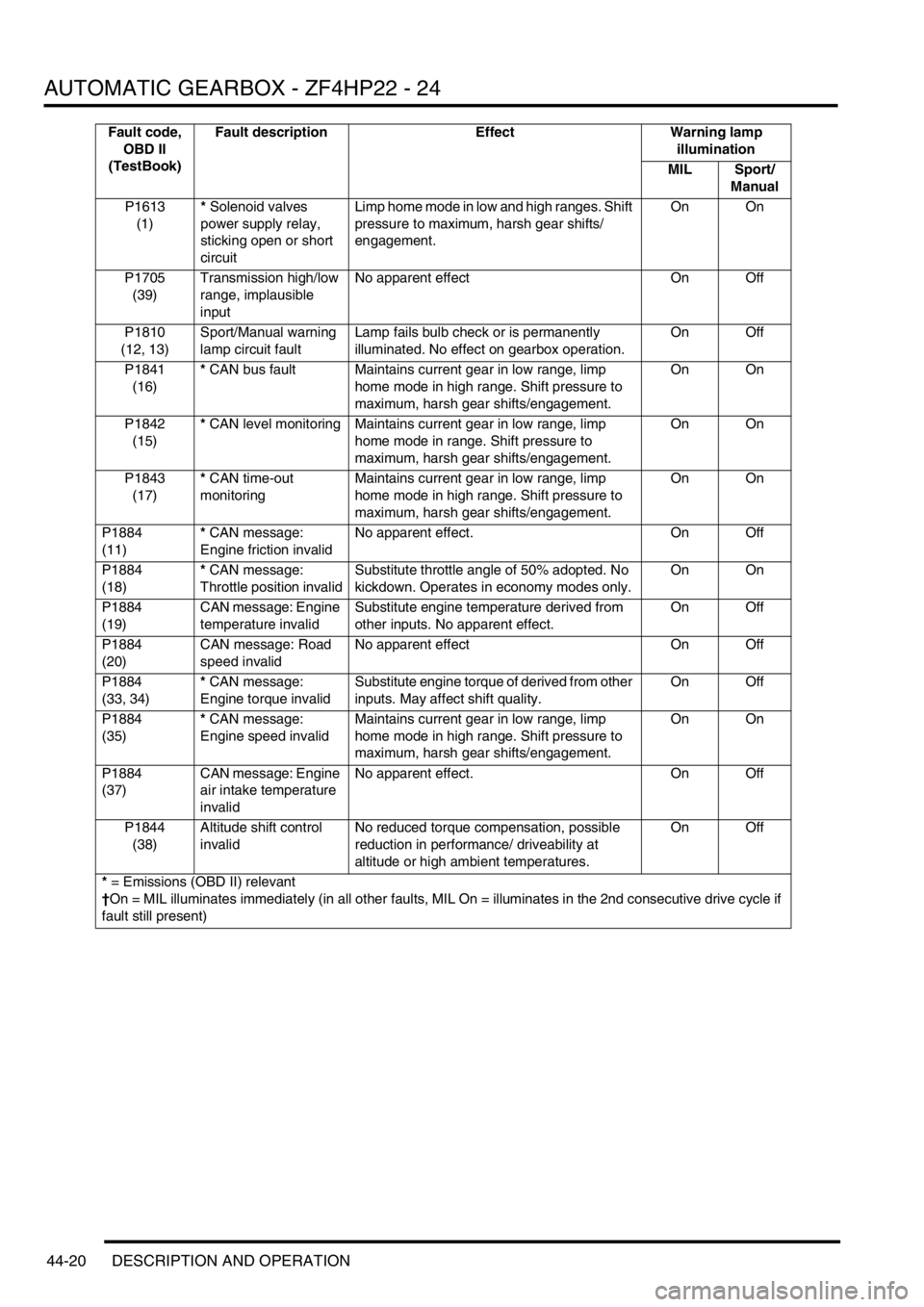
AUTOMATIC GEARBOX - ZF4HP22 - 24
44-20 DESCRIPTION AND OPERATION
P1613
(1)* Solenoid valves
power supply relay,
sticking open or short
circuitLimp home mode in low and high ranges. Shift
pressure to maximum, harsh gear shifts/
engagement.On On
P1705
(39)Transmission high/low
range, implausible
inputNo apparent effect On Off
P1810
(12, 13)Sport/Manual warning
lamp circuit faultLamp fails bulb check or is permanently
illuminated. No effect on gearbox operation.On Off
P1841
(16)* CAN bus fault Maintains current gear in low range, limp
home mode in high range. Shift pressure to
maximum, harsh gear shifts/engagement.On On
P1842
(15)* CAN level monitoring Maintains current gear in low range, limp
home mode in range. Shift pressure to
maximum, harsh gear shifts/engagement.On On
P1843
(17)* CAN time-out
monitoringMaintains current gear in low range, limp
home mode in high range. Shift pressure to
maximum, harsh gear shifts/engagement.On On
P1884
(11)* CAN message:
Engine friction invalidNo apparent effect. On Off
P1884
(18)* CAN message:
Throttle position invalidSubstitute throttle angle of 50% adopted. No
kickdown. Operates in economy modes only.On On
P1884
(19)CAN message: Engine
temperature invalidSubstitute engine temperature derived from
other inputs. No apparent effect.On Off
P1884
(20)CAN message: Road
speed invalidNo apparent effect On Off
P1884
(33, 34)* CAN message:
Engine torque invalidSubstitute engine torque of derived from other
inputs. May affect shift quality.On Off
P1884
(35)* CAN message:
Engine speed invalidMaintains current gear in low range, limp
home mode in high range. Shift pressure to
maximum, harsh gear shifts/engagement.On On
P1884
(37)CAN message: Engine
air intake temperature
invalidNo apparent effect. On Off
P1844
(38)Altitude shift control
invalidNo reduced torque compensation, possible
reduction in performance/ driveability at
altitude or high ambient temperatures.On Off
* = Emissions (OBD II) relevant
†On = MIL illuminates immediately (in all other faults, MIL On = illuminates in the 2nd consecutive drive cycle if
fault still present)Fault code,
OBD II
(TestBook)Fault description Effect Warning lamp
illumination
MIL Sport/
Manual