engine LAND ROVER DISCOVERY 1999 Workshop Manual
[x] Cancel search | Manufacturer: LAND ROVER, Model Year: 1999, Model line: DISCOVERY, Model: LAND ROVER DISCOVERY 1999Pages: 1529, PDF Size: 34.8 MB
Page 756 of 1529
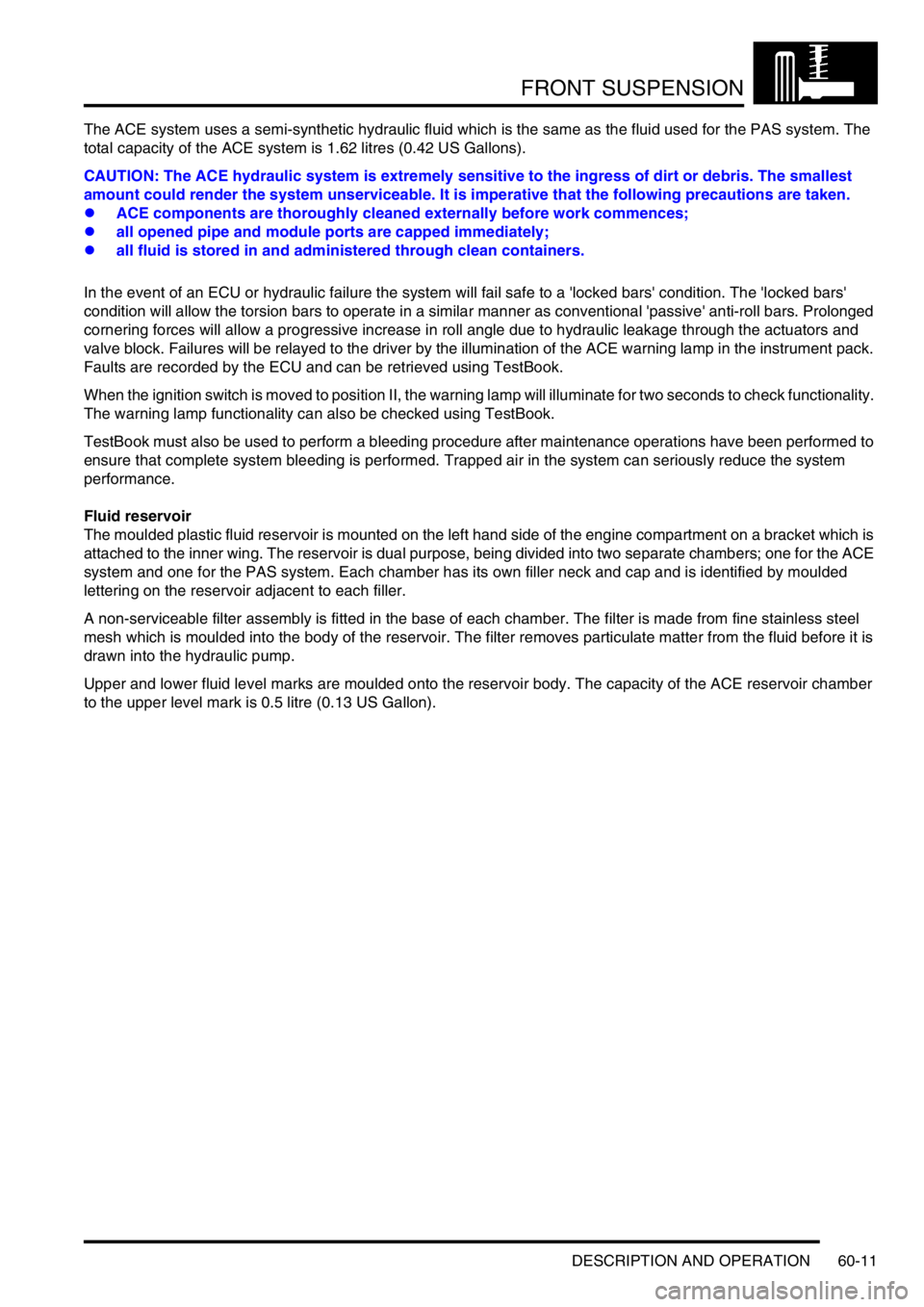
FRONT SUSPENSION
DESCRIPTION AND OPERATION 60-11
The ACE system uses a semi-synthetic hydraulic fluid which is the same as the fluid used for the PAS system. The
total capacity of the ACE system is 1.62 litres (0.42 US Gallons).
CAUTION: The ACE hydraulic system is extremely sensitive to the ingress of dirt or debris. The smallest
amount could render the system unserviceable. It is imperative that the following precautions are taken.
lACE components are thoroughly cleaned externally before work commences;
lall opened pipe and module ports are capped immediately;
lall fluid is stored in and administered through clean containers.
In the event of an ECU or hydraulic failure the system will fail safe to a 'locked bars' condition. The 'locked bars'
condition will allow the torsion bars to operate in a similar manner as conventional 'passive' anti-roll bars. Prolonged
cornering forces will allow a progressive increase in roll angle due to hydraulic leakage through the actuators and
valve block. Failures will be relayed to the driver by the illumination of the ACE warning lamp in the instrument pack.
Faults are recorded by the ECU and can be retrieved using TestBook.
When the ignition switch is moved to position II, the warning lamp will illuminate for two seconds to check functionality.
The warning lamp functionality can also be checked using TestBook.
TestBook must also be used to perform a bleeding procedure after maintenance operations have been performed to
ensure that complete system bleeding is performed. Trapped air in the system can seriously reduce the system
performance.
Fluid reservoir
The moulded plastic fluid reservoir is mounted on the left hand side of the engine compartment on a bracket which is
attached to the inner wing. The reservoir is dual purpose, being divided into two separate chambers; one for the ACE
system and one for the PAS system. Each chamber has its own filler neck and cap and is identified by moulded
lettering on the reservoir adjacent to each filler.
A non-serviceable filter assembly is fitted in the base of each chamber. The filter is made from fine stainless steel
mesh which is moulded into the body of the reservoir. The filter removes particulate matter from the fluid before it is
drawn into the hydraulic pump.
Upper and lower fluid level marks are moulded onto the reservoir body. The capacity of the ACE reservoir chamber
to the upper level mark is 0.5 litre (0.13 US Gallon).
Page 757 of 1529
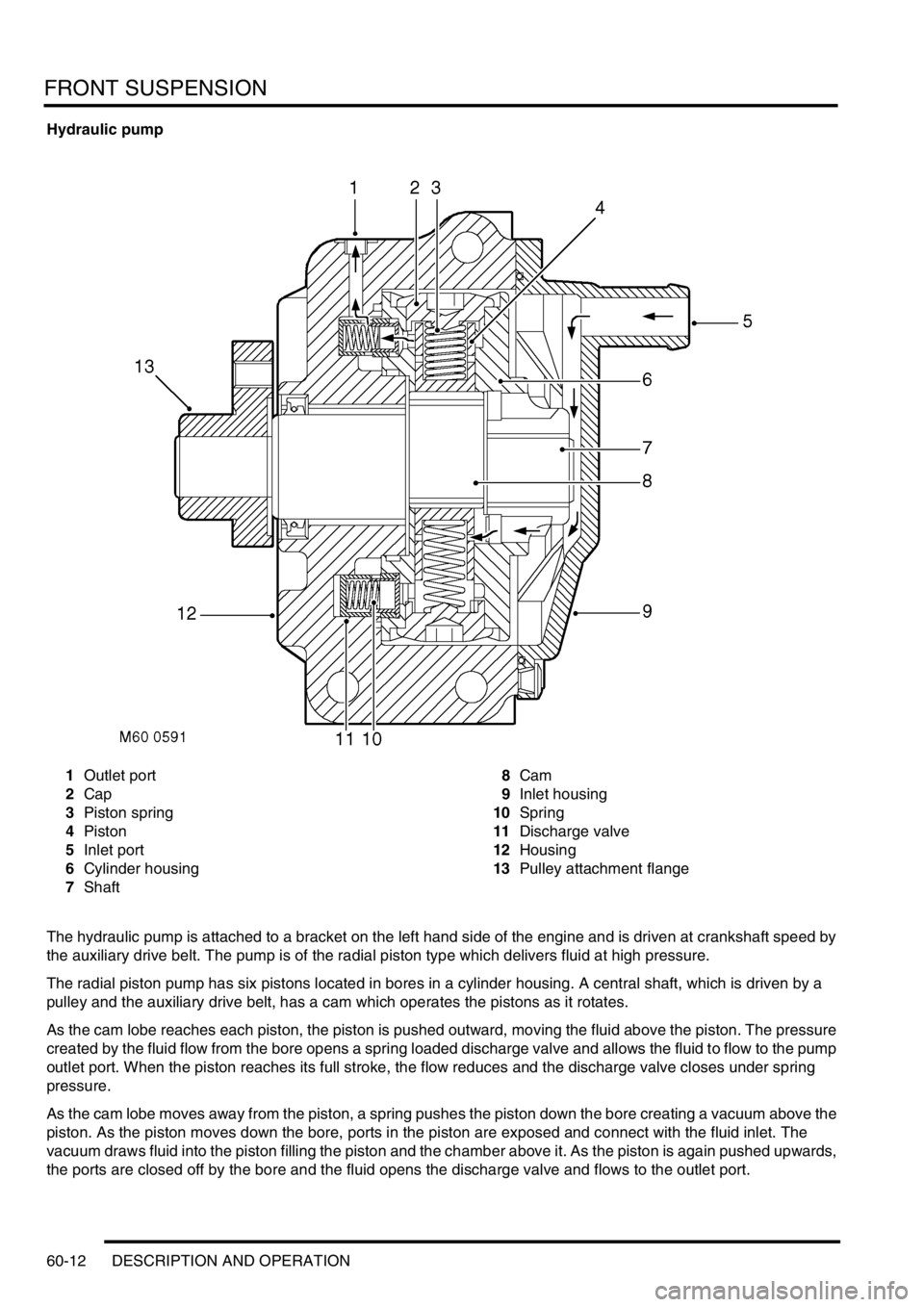
FRONT SUSPENSION
60-12 DESCRIPTION AND OPERATION
Hydraulic pump
1Outlet port
2Cap
3Piston spring
4Piston
5Inlet port
6Cylinder housing
7Shaft8Cam
9Inlet housing
10Spring
11Discharge valve
12Housing
13Pulley attachment flange
The hydraulic pump is attached to a bracket on the left hand side of the engine and is driven at crankshaft speed by
the auxiliary drive belt. The pump is of the radial piston type which delivers fluid at high pressure.
The radial piston pump has six pistons located in bores in a cylinder housing. A central shaft, which is driven by a
pulley and the auxiliary drive belt, has a cam which operates the pistons as it rotates.
As the cam lobe reaches each piston, the piston is pushed outward, moving the fluid above the piston. The pressure
created by the fluid flow from the bore opens a spring loaded discharge valve and allows the fluid to flow to the pump
outlet port. When the piston reaches its full stroke, the flow reduces and the discharge valve closes under spring
pressure.
As the cam lobe moves away from the piston, a spring pushes the piston down the bore creating a vacuum above the
piston. As the piston moves down the bore, ports in the piston are exposed and connect with the fluid inlet. The
vacuum draws fluid into the piston filling the piston and the chamber above it. As the piston is again pushed upwards,
the ports are closed off by the bore and the fluid opens the discharge valve and flows to the outlet port.
Page 758 of 1529
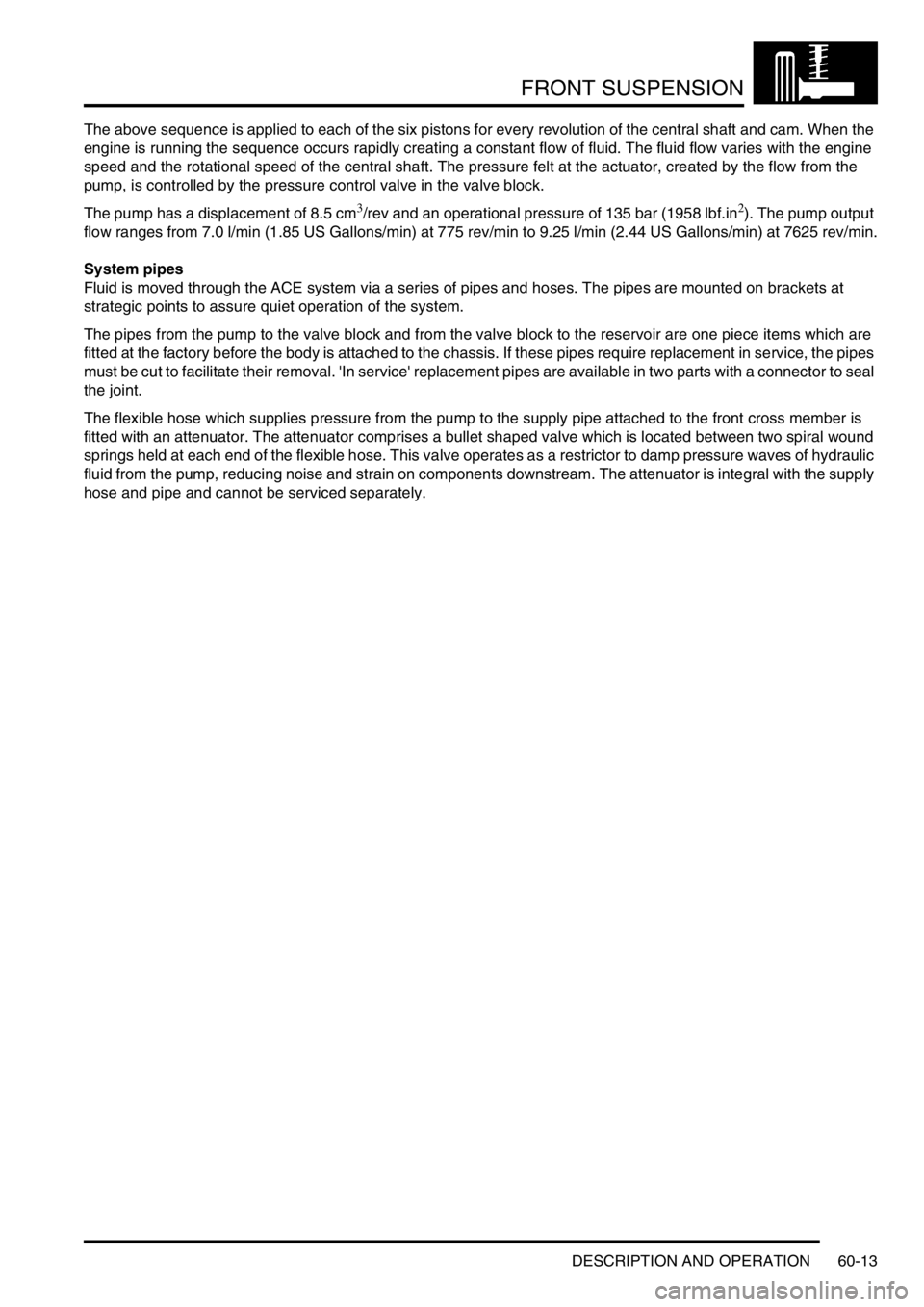
FRONT SUSPENSION
DESCRIPTION AND OPERATION 60-13
The above sequence is applied to each of the six pistons for every revolution of the central shaft and cam. When the
engine is running the sequence occurs rapidly creating a constant flow of fluid. The fluid flow varies with the engine
speed and the rotational speed of the central shaft. The pressure felt at the actuator, created by the flow from the
pump, is controlled by the pressure control valve in the valve block.
The pump has a displacement of 8.5 cm
3/rev and an operational pressure of 135 bar (1958 lbf.in2). The pump output
flow ranges from 7.0 l/min (1.85 US Gallons/min) at 775 rev/min to 9.25 l/min (2.44 US Gallons/min) at 7625 rev/min.
System pipes
Fluid is moved through the ACE system via a series of pipes and hoses. The pipes are mounted on brackets at
strategic points to assure quiet operation of the system.
The pipes from the pump to the valve block and from the valve block to the reservoir are one piece items which are
fitted at the factory before the body is attached to the chassis. If these pipes require replacement in service, the pipes
must be cut to facilitate their removal. 'In service' replacement pipes are available in two parts with a connector to seal
the joint.
The flexible hose which supplies pressure from the pump to the supply pipe attached to the front cross member is
fitted with an attenuator. The attenuator comprises a bullet shaped valve which is located between two spiral wound
springs held at each end of the flexible hose. This valve operates as a restrictor to damp pressure waves of hydraulic
fluid from the pump, reducing noise and strain on components downstream. The attenuator is integral with the supply
hose and pipe and cannot be serviced separately.
Page 763 of 1529
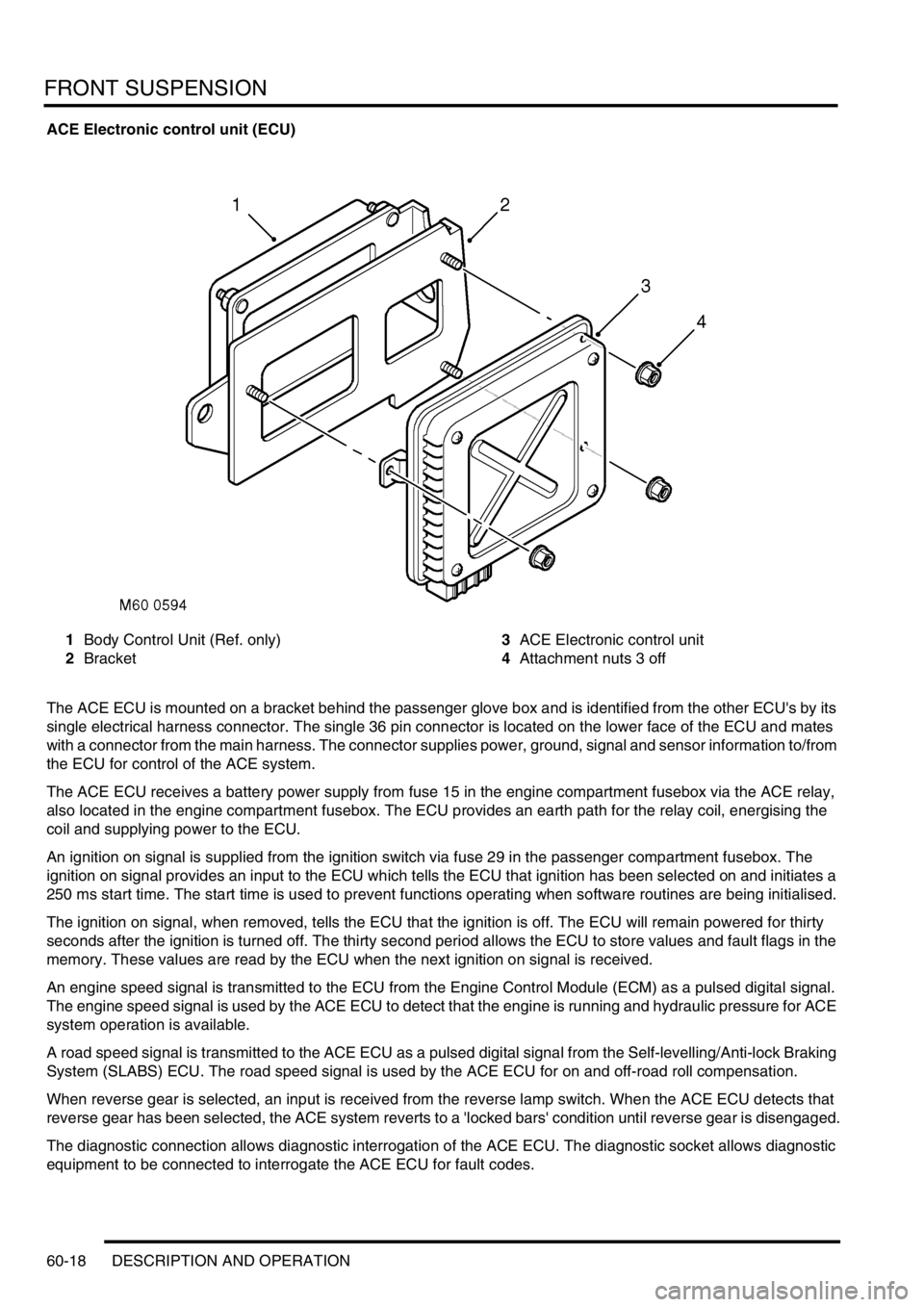
FRONT SUSPENSION
60-18 DESCRIPTION AND OPERATION
ACE Electronic control unit (ECU)
1Body Control Unit (Ref. only)
2Bracket3ACE Electronic control unit
4Attachment nuts 3 off
The ACE ECU is mounted on a bracket behind the passenger glove box and is identified from the other ECU's by its
single electrical harness connector. The single 36 pin connector is located on the lower face of the ECU and mates
with a connector from the main harness. The connector supplies power, ground, signal and sensor information to/from
the ECU for control of the ACE system.
The ACE ECU receives a battery power supply from fuse 15 in the engine compartment fusebox via the ACE relay,
also located in the engine compartment fusebox. The ECU provides an earth path for the relay coil, energising the
coil and supplying power to the ECU.
An ignition on signal is supplied from the ignition switch via fuse 29 in the passenger compartment fusebox. The
ignition on signal provides an input to the ECU which tells the ECU that ignition has been selected on and initiates a
250 ms start time. The start time is used to prevent functions operating when software routines are being initialised.
The ignition on signal, when removed, tells the ECU that the ignition is off. The ECU will remain powered for thirty
seconds after the ignition is turned off. The thirty second period allows the ECU to store values and fault flags in the
memory. These values are read by the ECU when the next ignition on signal is received.
An engine speed signal is transmitted to the ECU from the Engine Control Module (ECM) as a pulsed digital signal.
The engine speed signal is used by the ACE ECU to detect that the engine is running and hydraulic pressure for ACE
system operation is available.
A road speed signal is transmitted to the ACE ECU as a pulsed digital signal from the Self-levelling/Anti-lock Braking
System (SLABS) ECU. The road speed signal is used by the ACE ECU for on and off-road roll compensation.
When reverse gear is selected, an input is received from the reverse lamp switch. When the ACE ECU detects that
reverse gear has been selected, the ACE system reverts to a 'locked bars' condition until reverse gear is disengaged.
The diagnostic connection allows diagnostic interrogation of the ACE ECU. The diagnostic socket allows diagnostic
equipment to be connected to interrogate the ACE ECU for fault codes.
Page 764 of 1529
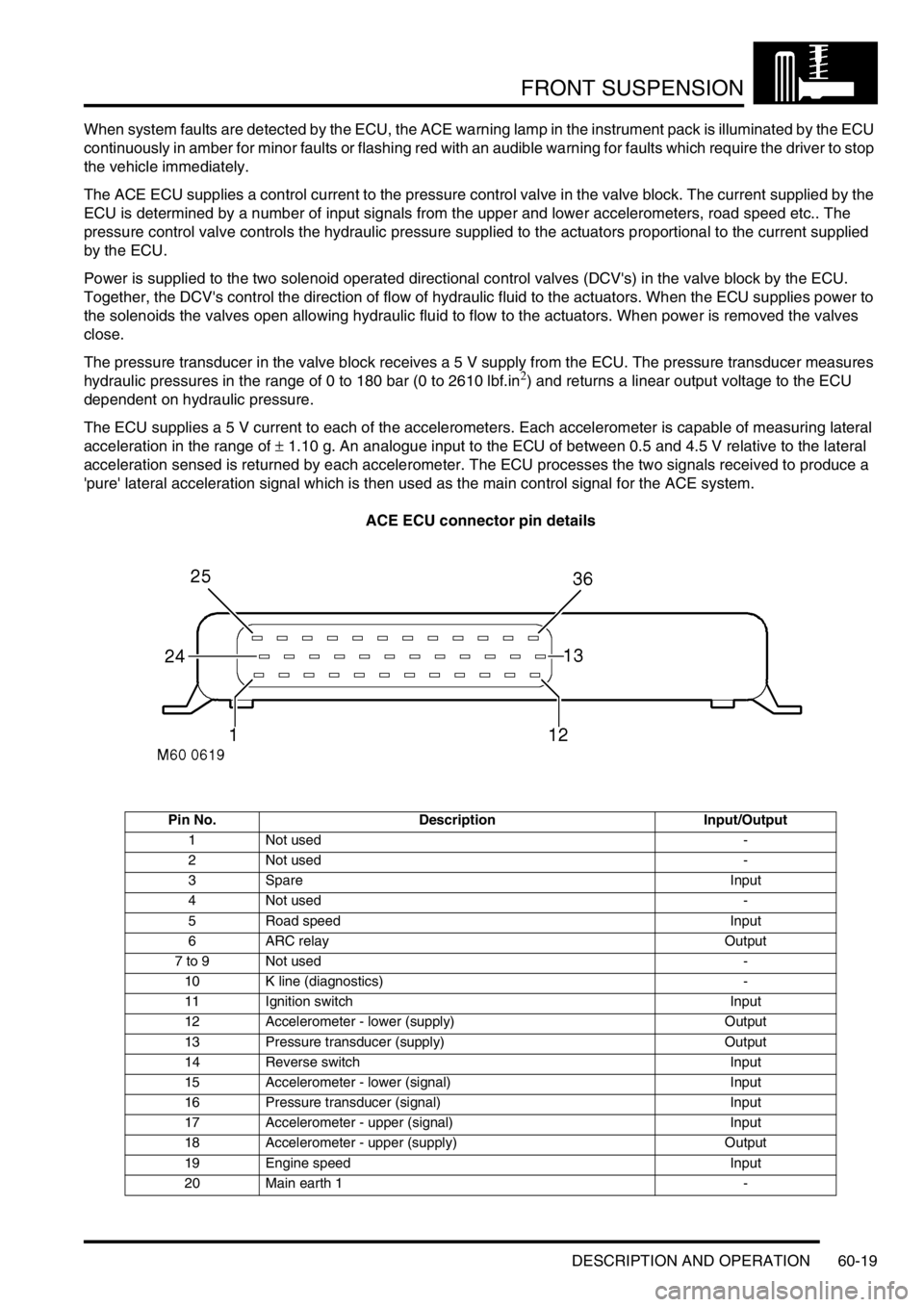
FRONT SUSPENSION
DESCRIPTION AND OPERATION 60-19
When system faults are detected by the ECU, the ACE warning lamp in the instrument pack is illuminated by the ECU
continuously in amber for minor faults or flashing red with an audible warning for faults which require the driver to stop
the vehicle immediately.
The ACE ECU supplies a control current to the pressure control valve in the valve block. The current supplied by the
ECU is determined by a number of input signals from the upper and lower accelerometers, road speed etc.. The
pressure control valve controls the hydraulic pressure supplied to the actuators proportional to the current supplied
by the ECU.
Power is supplied to the two solenoid operated directional control valves (DCV's) in the valve block by the ECU.
Together, the DCV's control the direction of flow of hydraulic fluid to the actuators. When the ECU supplies power to
the solenoids the valves open allowing hydraulic fluid to flow to the actuators. When power is removed the valves
close.
The pressure transducer in the valve block receives a 5 V supply from the ECU. The pressure transducer measures
hydraulic pressures in the range of 0 to 180 bar (0 to 2610 lbf.in
2) and returns a linear output voltage to the ECU
dependent on hydraulic pressure.
The ECU supplies a 5 V current to each of the accelerometers. Each accelerometer is capable of measuring lateral
acceleration in the range of ± 1.10 g. An analogue input to the ECU of between 0.5 and 4.5 V relative to the lateral
acceleration sensed is returned by each accelerometer. The ECU processes the two signals received to produce a
'pure' lateral acceleration signal which is then used as the main control signal for the ACE system.
ACE ECU connector pin details
Pin No. Description Input/Output
1 Not used -
2 Not used -
3 Spare Input
4 Not used -
5 Road speed Input
6ARC relay Output
7 to 9 Not used -
10 K line (diagnostics) -
11 Ignition switch Input
12 Accelerometer - lower (supply) Output
13 Pressure transducer (supply) Output
14 Reverse switch Input
15 Accelerometer - lower (signal) Input
16 Pressure transducer (signal) Input
17 Accelerometer - upper (signal) Input
18 Accelerometer - upper (supply) Output
19 Engine speed Input
20 Main earth 1 -
Page 766 of 1529
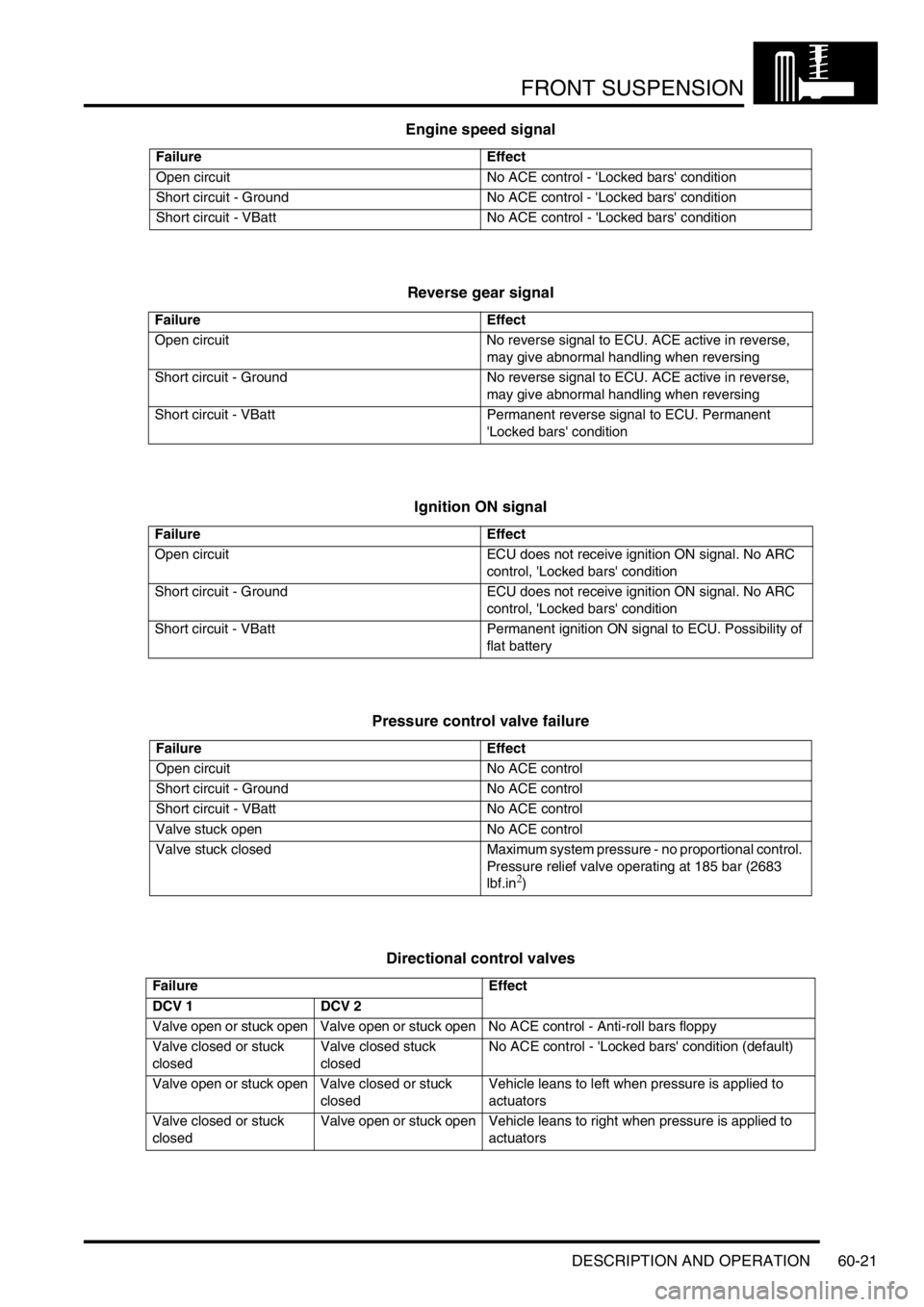
FRONT SUSPENSION
DESCRIPTION AND OPERATION 60-21
Engine speed signal
Reverse gear signal
Ignition ON signal
Pressure control valve failure
Directional control valves
Failure Effect
Open circuit No ACE control - 'Locked bars' condition
Short circuit - Ground No ACE control - 'Locked bars' condition
Short circuit - VBatt No ACE control - 'Locked bars' condition
Failure Effect
Open circuit No reverse signal to ECU. ACE active in reverse,
may give abnormal handling when reversing
Short circuit - Ground No reverse signal to ECU. ACE active in reverse,
may give abnormal handling when reversing
Short circuit - VBatt Permanent reverse signal to ECU. Permanent
'Locked bars' condition
Failure Effect
Open circuit ECU does not receive ignition ON signal. No ARC
control, 'Locked bars' condition
Short circuit - Ground ECU does not receive ignition ON signal. No ARC
control, 'Locked bars' condition
Short circuit - VBatt Permanent ignition ON signal to ECU. Possibility of
flat battery
Failure Effect
Open circuit No ACE control
Short circuit - Ground No ACE control
Short circuit - VBatt No ACE control
Valve stuck open No ACE control
Valve stuck closed Maximum system pressure - no proportional control.
Pressure relief valve operating at 185 bar (2683
lbf.in
2)
Failure Effect
DCV 1 DCV 2
Valve open or stuck open Valve open or stuck open No ACE control - Anti-roll bars floppy
Valve closed or stuck
closedValve closed stuck
closedNo ACE control - 'Locked bars' condition (default)
Valve open or stuck open Valve closed or stuck
closedVehicle leans to left when pressure is applied to
actuators
Valve closed or stuck
closedValve open or stuck open Vehicle leans to right when pressure is applied to
actuators
Page 767 of 1529

FRONT SUSPENSION
60-22 DESCRIPTION AND OPERATION
Operation
Hydraulic circuit diagram
1Pressure transducer
2Directional control valve 2
3Front torsion bar assembly
4Actuator
5Actuator
6Rear torsion bar assembly
7Directional control valve 18Valve block
9Pressure control valve
10Reservoir
11Filter
12High pressure filter
13Hydraulic pump
14Attenuator hose
Vehicle not moving
When the engine is running and the vehicle is not moving, both DCV's are closed, locking fluid in each side of the
actuator pistons. The hydraulic pump draws fluid from the reservoir and passes it at very low pressure to the valve
block. Because both DCV's are closed, after the fluid passes through the high pressure filter, it is directed through the
pressure control valve to the reservoir. The pressure control valve is open fully to allow the full flow to pass to the
reservoir. The DCV's will remain closed until the ECU detects a need to operate.
Page 770 of 1529
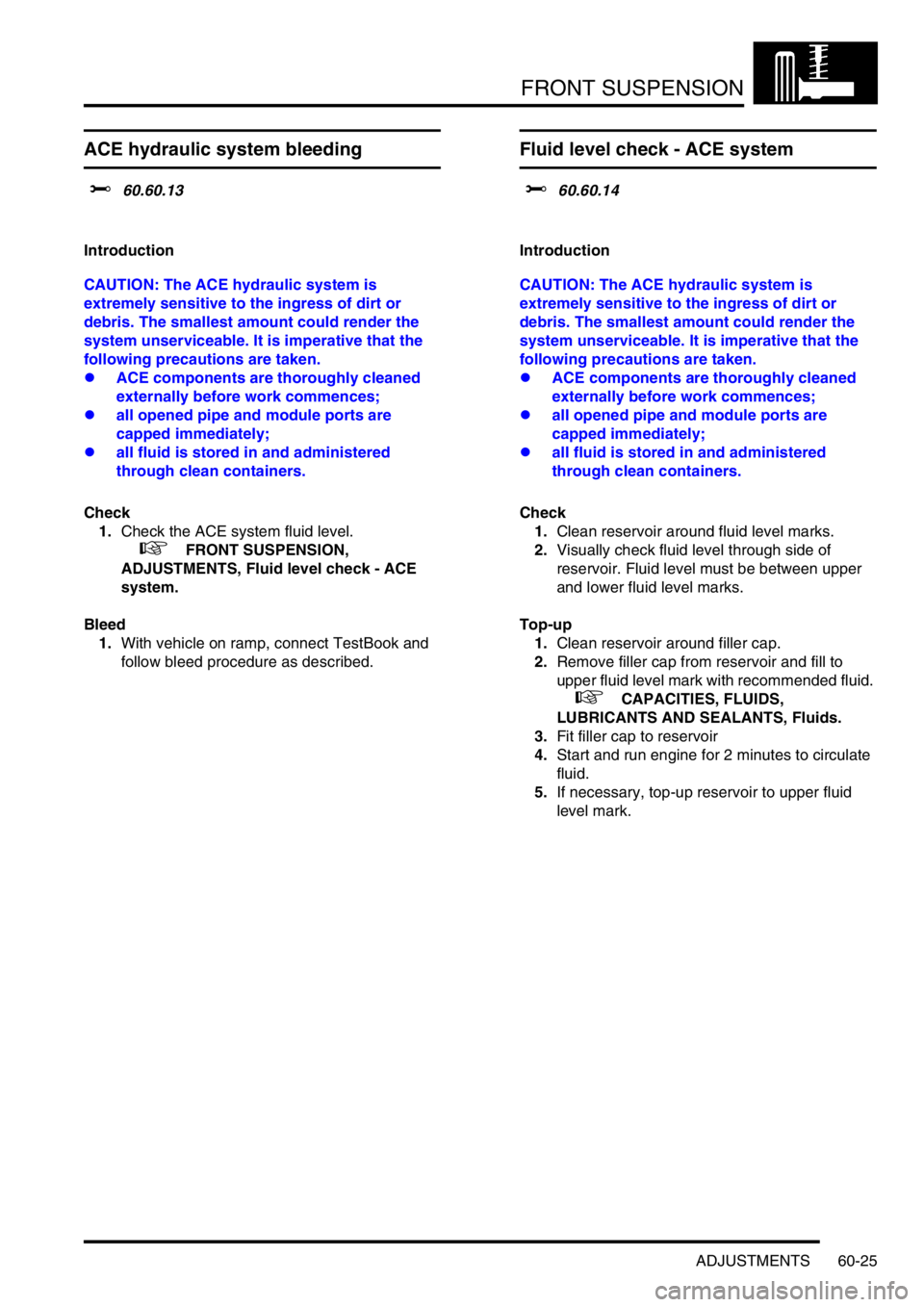
FRONT SUSPENSION
ADJUSTMENTS 60-25
ADJUST ME NTS
ACE hydraulic system bleeding
$% 60.60.13
Introduction
CAUTION: The ACE hydraulic system is
extremely sensitive to the ingress of dirt or
debris. The smallest amount could render the
system unserviceable. It is imperative that the
following precautions are taken.
lACE components are thoroughly cleaned
externally before work commences;
lall opened pipe and module ports are
capped immediately;
lall fluid is stored in and administered
through clean containers.
Check
1.Check the ACE system fluid level.
+ FRONT SUSPENSION,
ADJUSTMENTS, Fluid level check - ACE
system.
Bleed
1.With vehicle on ramp, connect TestBook and
follow bleed procedure as described.
Fluid level check - ACE system
$% 60.60.14
Introduction
CAUTION: The ACE hydraulic system is
extremely sensitive to the ingress of dirt or
debris. The smallest amount could render the
system unserviceable. It is imperative that the
following precautions are taken.
lACE components are thoroughly cleaned
externally before work commences;
lall opened pipe and module ports are
capped immediately;
lall fluid is stored in and administered
through clean containers.
Check
1.Clean reservoir around fluid level marks.
2.Visually check fluid level through side of
reservoir. Fluid level must be between upper
and lower fluid level marks.
Top-up
1.Clean reservoir around filler cap.
2.Remove filler cap from reservoir and fill to
upper fluid level mark with recommended fluid.
+ CAPACITIES, FLUIDS,
LUBRICANTS AND SEALANTS, Fluids.
3.Fit filler cap to reservoir
4.Start and run engine for 2 minutes to circulate
fluid.
5.If necessary, top-up reservoir to upper fluid
level mark.
Page 781 of 1529
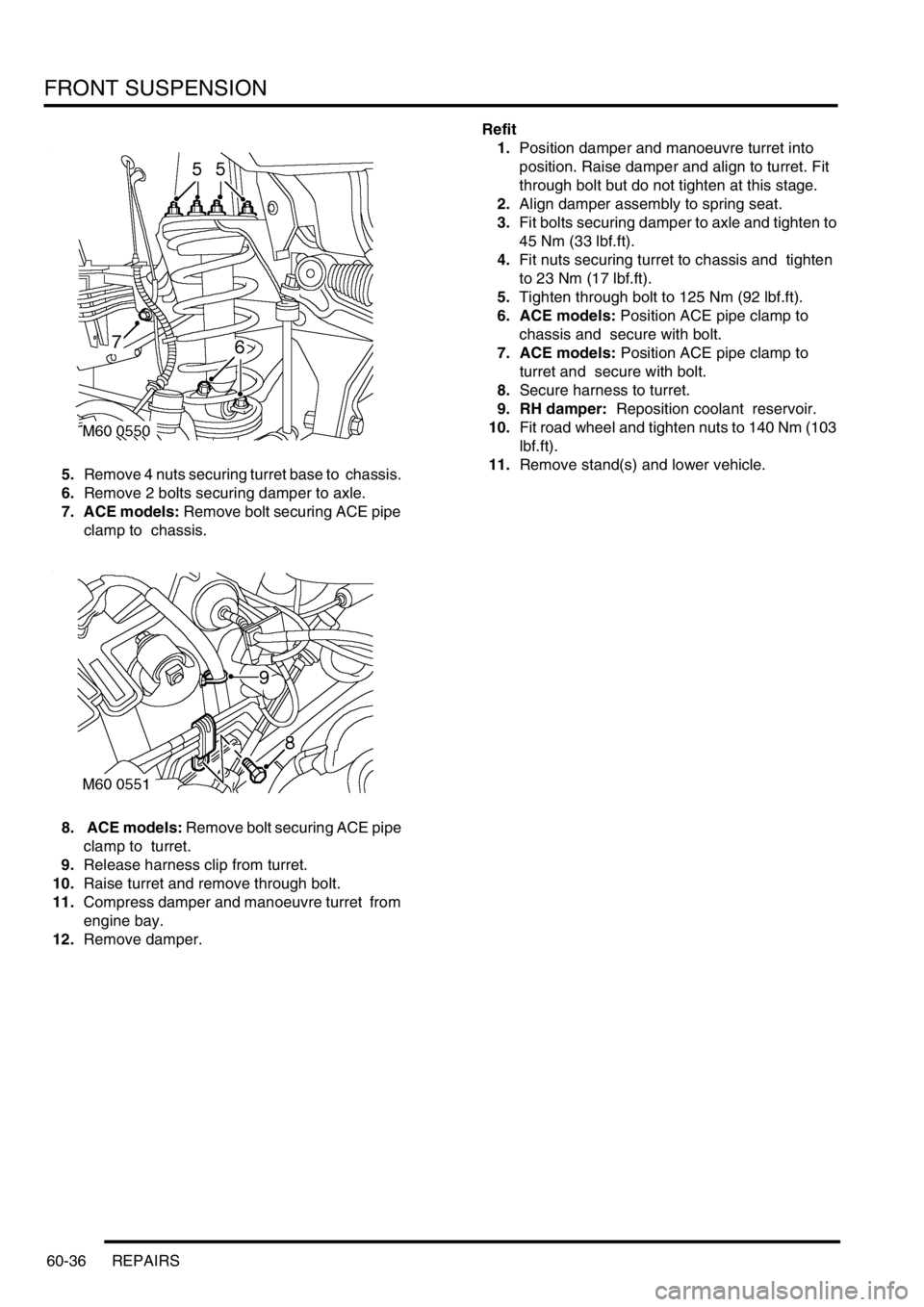
FRONT SUSPENSION
60-36 REPAIRS
5.Remove 4 nuts securing turret base to chassis.
6.Remove 2 bolts securing damper to axle.
7. ACE models: Remove bolt securing ACE pipe
clamp to chassis.
8. ACE models: Remove bolt securing ACE pipe
clamp to turret.
9.Release harness clip from turret.
10.Raise turret and remove through bolt.
11.Compress damper and manoeuvre turret from
engine bay.
12.Remove damper. Refit
1.Position damper and manoeuvre turret into
position. Raise damper and align to turret. Fit
through bolt but do not tighten at this stage.
2.Align damper assembly to spring seat.
3.Fit bolts securing damper to axle and tighten to
45 Nm (33 lbf.ft).
4.Fit nuts securing turret to chassis and tighten
to 23 Nm (17 lbf.ft).
5.Tighten through bolt to 125 Nm (92 lbf.ft).
6. ACE models: Position ACE pipe clamp to
chassis and secure with bolt.
7. ACE models: Position ACE pipe clamp to
turret and secure with bolt.
8.Secure harness to turret.
9. RH damper: Reposition coolant reservoir.
10.Fit road wheel and tighten nuts to 140 Nm (103
lbf.ft).
11.Remove stand(s) and lower vehicle.
Page 792 of 1529
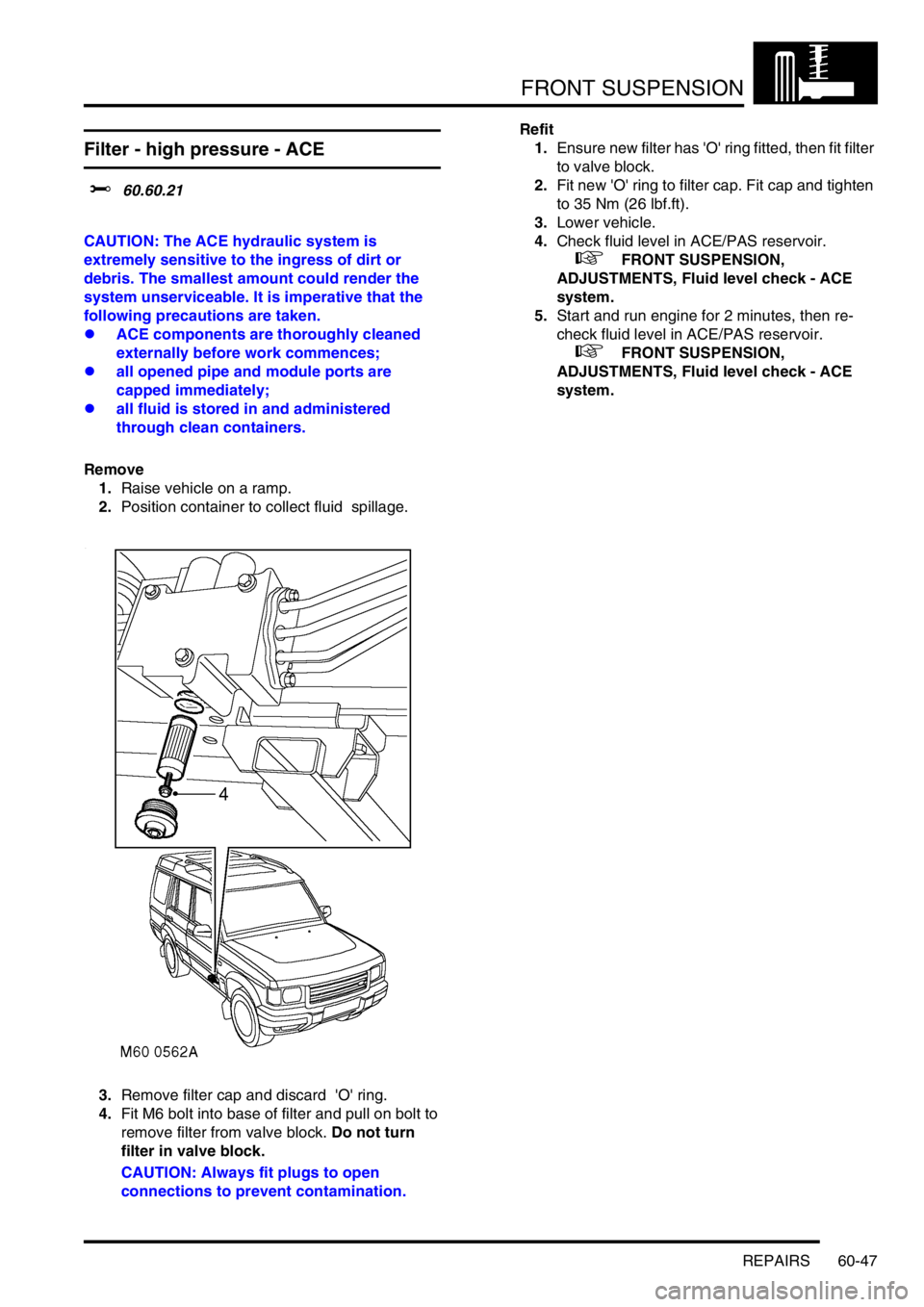
FRONT SUSPENSION
REPAIRS 60-47
Filter - high pressure - ACE
$% 60.60.21
CAUTION: The ACE hydraulic system is
extremely sensitive to the ingress of dirt or
debris. The smallest amount could render the
system unserviceable. It is imperative that the
following precautions are taken.
lACE components are thoroughly cleaned
externally before work commences;
lall opened pipe and module ports are
capped immediately;
lall fluid is stored in and administered
through clean containers.
Remove
1.Raise vehicle on a ramp.
2.Position container to collect fluid spillage.
3.Remove filter cap and discard 'O' ring.
4.Fit M6 bolt into base of filter and pull on bolt to
remove filter from valve block. Do not turn
filter in valve block.
CAUTION: Always fit plugs to open
connections to prevent contamination.Refit
1.Ensure new filter has 'O' ring fitted, then fit filter
to valve block.
2.Fit new 'O' ring to filter cap. Fit cap and tighten
to 35 Nm (26 lbf.ft).
3.Lower vehicle.
4.Check fluid level in ACE/PAS reservoir.
+ FRONT SUSPENSION,
ADJUSTMENTS, Fluid level check - ACE
system.
5.Start and run engine for 2 minutes, then re-
check fluid level in ACE/PAS reservoir.
+ FRONT SUSPENSION,
ADJUSTMENTS, Fluid level check - ACE
system.