check engine LAND ROVER DISCOVERY 2002 Workshop Manual
[x] Cancel search | Manufacturer: LAND ROVER, Model Year: 2002, Model line: DISCOVERY, Model: LAND ROVER DISCOVERY 2002Pages: 1672, PDF Size: 46.1 MB
Page 1105 of 1672
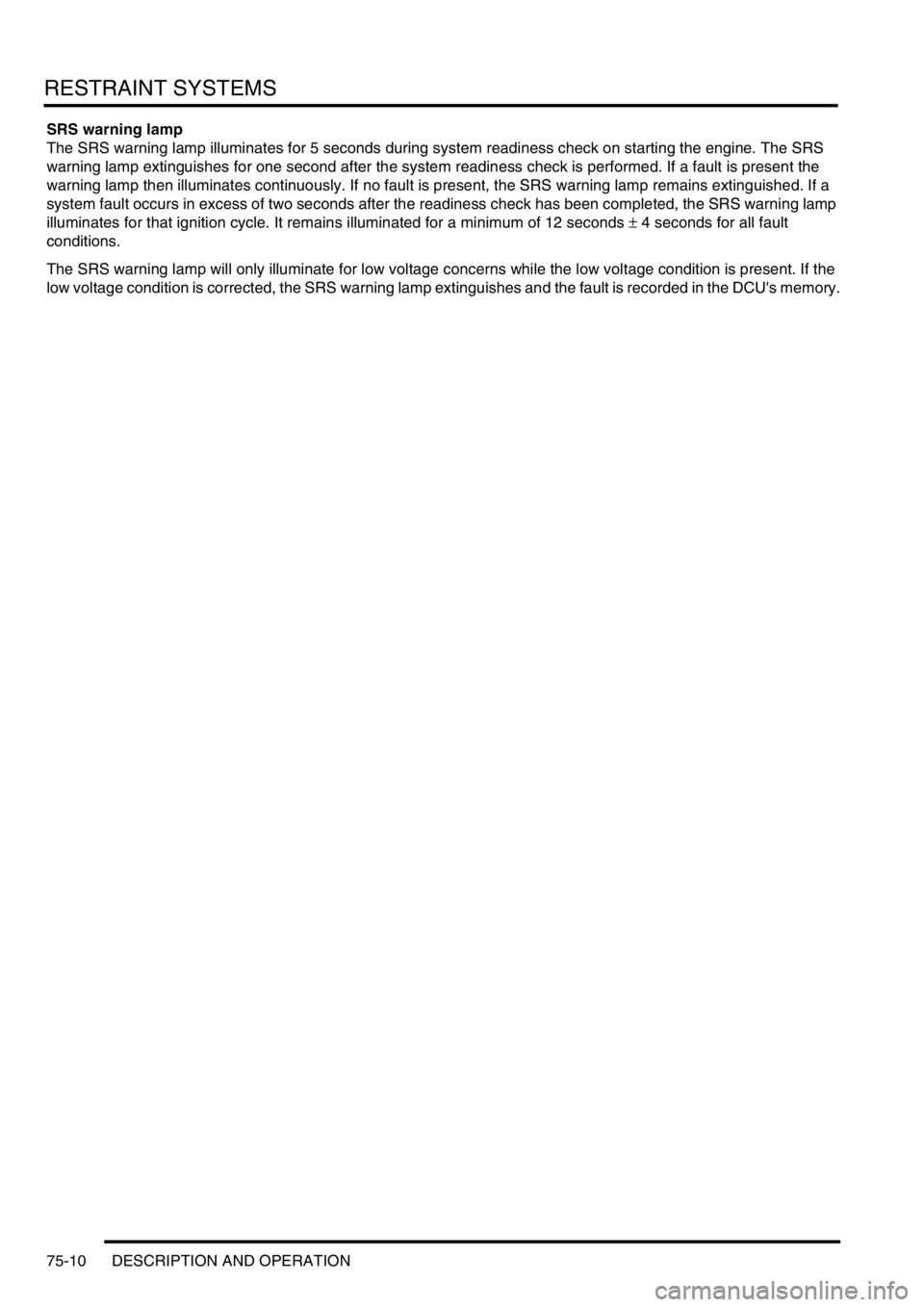
RESTRAINT SYSTEMS
75-10 DESCRIPTION AND OPERATION
SRS warning lamp
The SRS warning lamp illuminates for 5 seconds during system readiness check on starting the engine. The SRS
warning lamp extinguishes for one second after the system readiness check is performed. If a fault is present the
warning lamp then illuminates continuously. If no fault is present, the SRS warning lamp remains extinguished. If a
system fault occurs in excess of two seconds after the readiness check has been completed, the SRS warning lamp
illuminates for that ignition cycle. It remains illuminated for a minimum of 12 seconds
± 4 seconds for all fault
conditions.
The SRS warning lamp will only illuminate for low voltage concerns while the low voltage condition is present. If the
low voltage condition is corrected, the SRS warning lamp extinguishes and the fault is recorded in the DCU's memory.
Page 1147 of 1672
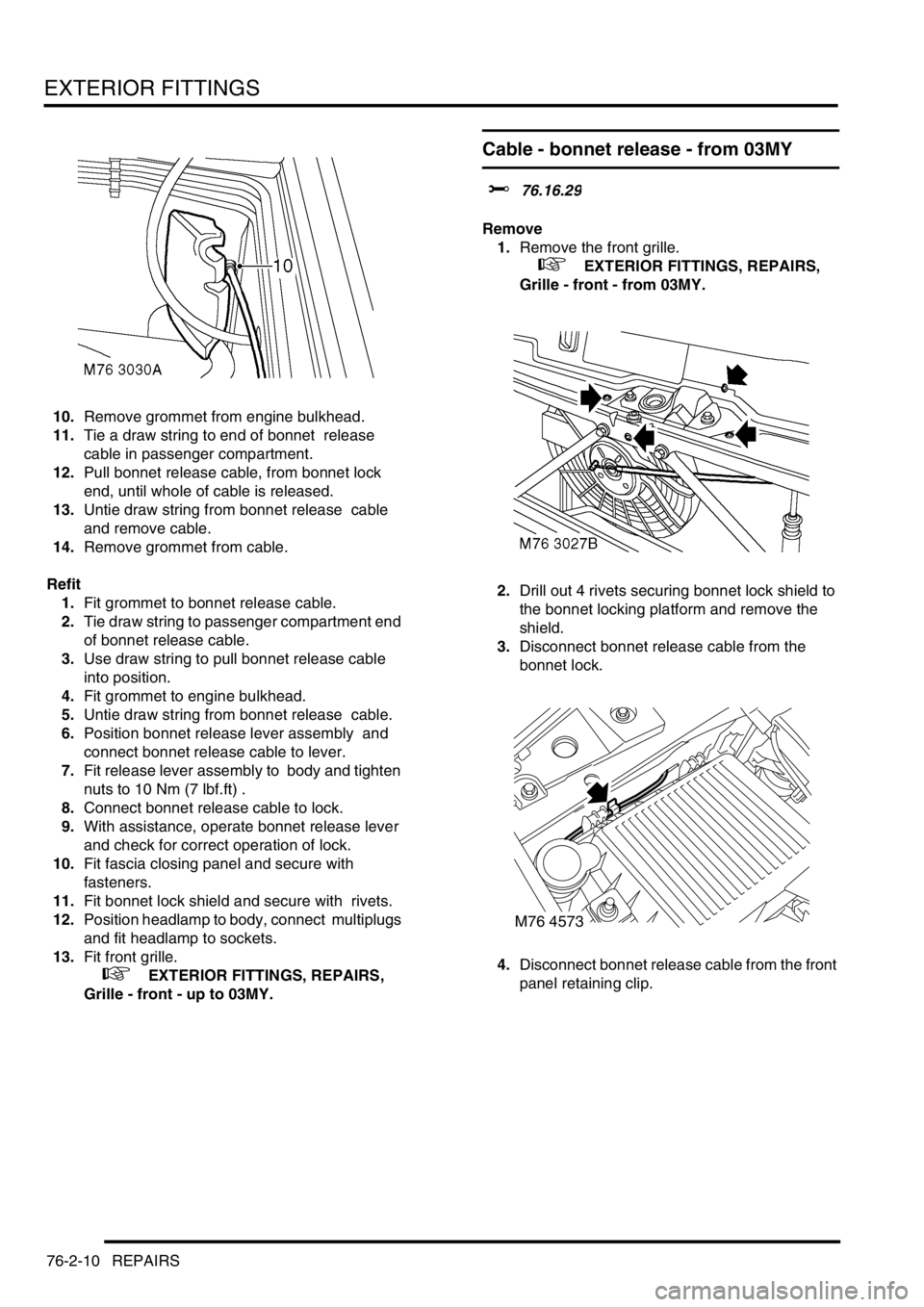
EXTERIOR FITTINGS
76-2-10 REPAIRS
10.Remove grommet from engine bulkhead.
11.Tie a draw string to end of bonnet release
cable in passenger compartment.
12.Pull bonnet release cable, from bonnet lock
end, until whole of cable is released.
13.Untie draw string from bonnet release cable
and remove cable.
14.Remove grommet from cable.
Refit
1.Fit grommet to bonnet release cable.
2.Tie draw string to passenger compartment end
of bonnet release cable.
3.Use draw string to pull bonnet release cable
into position.
4.Fit grommet to engine bulkhead.
5.Untie draw string from bonnet release cable.
6.Position bonnet release lever assembly and
connect bonnet release cable to lever.
7.Fit release lever assembly to body and tighten
nuts to 10 Nm (7 lbf.ft) .
8.Connect bonnet release cable to lock.
9.With assistance, operate bonnet release lever
and check for correct operation of lock.
10.Fit fascia closing panel and secure with
fasteners.
11.Fit bonnet lock shield and secure with rivets.
12.Position headlamp to body, connect multiplugs
and fit headlamp to sockets.
13.Fit front grille.
+ EXTERIOR FITTINGS, REPAIRS,
Grille - front - up to 03MY.
Cable - bonnet release - from 03MY
$% 76.16.29
Remove
1.Remove the front grille.
+ EXTERIOR FITTINGS, REPAIRS,
Grille - front - from 03MY.
2.Drill out 4 rivets securing bonnet lock shield to
the bonnet locking platform and remove the
shield.
3.Disconnect bonnet release cable from the
bonnet lock.
4.Disconnect bonnet release cable from the front
panel retaining clip.
M76 4573
Page 1321 of 1672
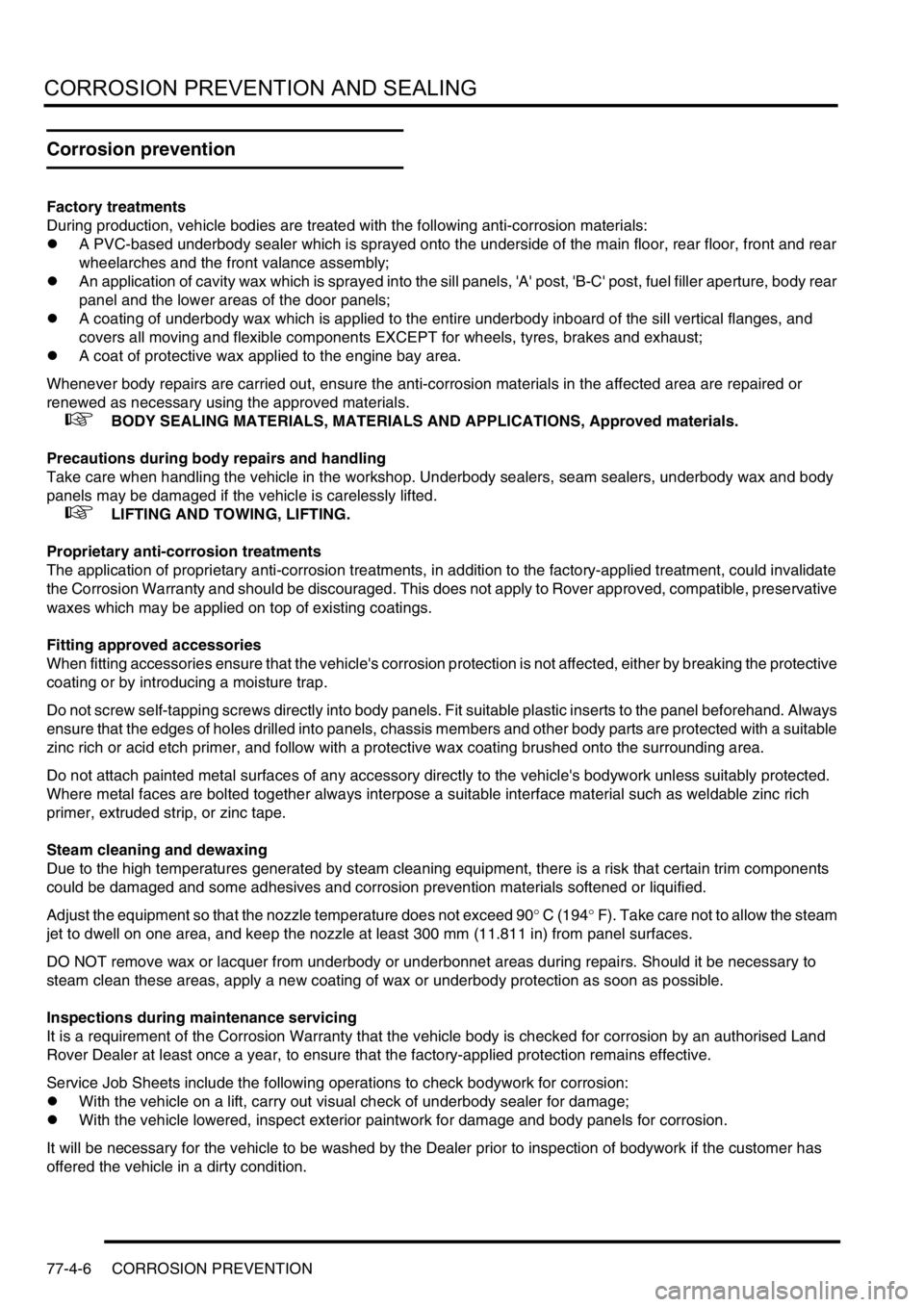
CORROSION PREVENTION AND SEALING
77-4-6 CORROSION PREVENTION
Corrosion prevention
Factory treatments
During production, vehicle bodies are treated with the following anti-corrosion materials:
lA PVC-based underbody sealer which is sprayed onto the underside of the main floor, rear floor, front and rear
wheelarches and the front valance assembly;
lAn application of cavity wax which is sprayed into the sill panels, 'A' post, 'B-C' post, fuel filler aperture, body rear
panel and the lower areas of the door panels;
lA coating of underbody wax which is applied to the entire underbody inboard of the sill vertical flanges, and
covers all moving and flexible components EXCEPT for wheels, tyres, brakes and exhaust;
lA coat of protective wax applied to the engine bay area.
Whenever body repairs are carried out, ensure the anti-corrosion materials in the affected area are repaired or
renewed as necessary using the approved materials.
+ BODY SEALING MATERIALS, MATERIALS AND APPLICATIONS, Approved materials.
Precautions during body repairs and handling
Take care when handling the vehicle in the workshop. Underbody sealers, seam sealers, underbody wax and body
panels may be damaged if the vehicle is carelessly lifted.
+ LIFTING AND TOWING, LIFTING.
Proprietary anti-corrosion treatments
The application of proprietary anti-corrosion treatments, in addition to the factory-applied treatment, could invalidate
the Corrosion Warranty and should be discouraged. This does not apply to Rover approved, compatible, preservative
waxes which may be applied on top of existing coatings.
Fitting approved accessories
When fitting accessories ensure that the vehicle's corrosion protection is not affected, either by breaking the protective
coating or by introducing a moisture trap.
Do not screw self-tapping screws directly into body panels. Fit suitable plastic inserts to the panel beforehand. Always
ensure that the edges of holes drilled into panels, chassis members and other body parts are protected with a suitable
zinc rich or acid etch primer, and follow with a protective wax coating brushed onto the surrounding area.
Do not attach painted metal surfaces of any accessory directly to the vehicle's bodywork unless suitably protected.
Where metal faces are bolted together always interpose a suitable interface material such as weldable zinc rich
primer, extruded strip, or zinc tape.
Steam cleaning and dewaxing
Due to the high temperatures generated by steam cleaning equipment, there is a risk that certain trim components
could be damaged and some adhesives and corrosion prevention materials softened or liquified.
Adjust the equipment so that the nozzle temperature does not exceed 90
° C (194° F). Take care not to allow the steam
jet to dwell on one area, and keep the nozzle at least 300 mm (11.811 in) from panel surfaces.
DO NOT remove wax or lacquer from underbody or underbonnet areas during repairs. Should it be necessary to
steam clean these areas, apply a new coating of wax or underbody protection as soon as possible.
Inspections during maintenance servicing
It is a requirement of the Corrosion Warranty that the vehicle body is checked for corrosion by an authorised Land
Rover Dealer at least once a year, to ensure that the factory-applied protection remains effective.
Service Job Sheets include the following operations to check bodywork for corrosion:
lWith the vehicle on a lift, carry out visual check of underbody sealer for damage;
lWith the vehicle lowered, inspect exterior paintwork for damage and body panels for corrosion.
It will be necessary for the vehicle to be washed by the Dealer prior to inspection of bodywork if the customer has
offered the vehicle in a dirty condition.
Page 1322 of 1672
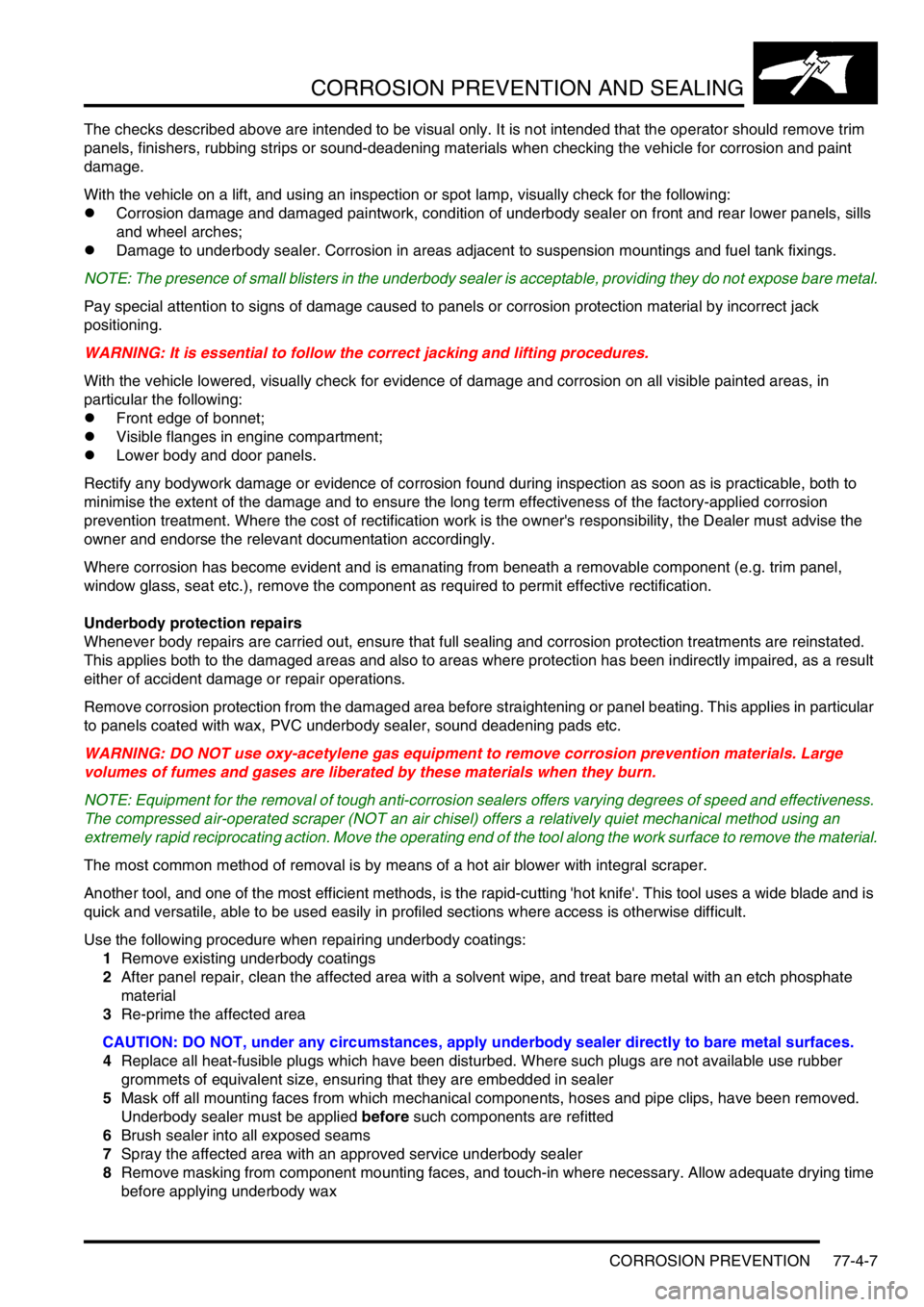
CORROSION PREVENTION AND SEALING
CORROSION PREVENTION 77-4-7
The checks described above are intended to be visual only. It is not intended that the operator should remove trim
panels, finishers, rubbing strips or sound-deadening materials when checking the vehicle for corrosion and paint
damage.
With the vehicle on a lift, and using an inspection or spot lamp, visually check for the following:
lCorrosion damage and damaged paintwork, condition of underbody sealer on front and rear lower panels, sills
and wheel arches;
lDamage to underbody sealer. Corrosion in areas adjacent to suspension mountings and fuel tank fixings.
NOTE: The presence of small blisters in the underbody sealer is acceptable, providing they do not expose bare metal.
Pay special attention to signs of damage caused to panels or corrosion protection material by incorrect jack
positioning.
WARNING: It is essential to follow the correct jacking and lifting procedures.
With the vehicle lowered, visually check for evidence of damage and corrosion on all visible painted areas, in
particular the following:
lFront edge of bonnet;
lVisible flanges in engine compartment;
lLower body and door panels.
Rectify any bodywork damage or evidence of corrosion found during inspection as soon as is practicable, both to
minimise the extent of the damage and to ensure the long term effectiveness of the factory-applied corrosion
prevention treatment. Where the cost of rectification work is the owner's responsibility, the Dealer must advise the
owner and endorse the relevant documentation accordingly.
Where corrosion has become evident and is emanating from beneath a removable component (e.g. trim panel,
window glass, seat etc.), remove the component as required to permit effective rectification.
Underbody protection repairs
Whenever body repairs are carried out, ensure that full sealing and corrosion protection treatments are reinstated.
This applies both to the damaged areas and also to areas where protection has been indirectly impaired, as a result
either of accident damage or repair operations.
Remove corrosion protection from the damaged area before straightening or panel beating. This applies in particular
to panels coated with wax, PVC underbody sealer, sound deadening pads etc.
WARNING: DO NOT use oxy-acetylene gas equipment to remove corrosion prevention materials. Large
volumes of fumes and gases are liberated by these materials when they burn.
NOTE: Equipment for the removal of tough anti-corrosion sealers offers varying degrees of speed and effectiveness.
The compressed air-operated scraper (NOT an air chisel) offers a relatively quiet mechanical method using an
extremely rapid reciprocating action. Move the operating end of the tool along the work surface to remove the material.
The most common method of removal is by means of a hot air blower with integral scraper.
Another tool, and one of the most efficient methods, is the rapid-cutting 'hot knife'. This tool uses a wide blade and is
quick and versatile, able to be used easily in profiled sections where access is otherwise difficult.
Use the following procedure when repairing underbody coatings:
1Remove existing underbody coatings
2After panel repair, clean the affected area with a solvent wipe, and treat bare metal with an etch phosphate
material
3Re-prime the affected area
CAUTION: DO NOT, under any circumstances, apply underbody sealer directly to bare metal surfaces.
4Replace all heat-fusible plugs which have been disturbed. Where such plugs are not available use rubber
grommets of equivalent size, ensuring that they are embedded in sealer
5Mask off all mounting faces from which mechanical components, hoses and pipe clips, have been removed.
Underbody sealer must be applied before such components are refitted
6Brush sealer into all exposed seams
7Spray the affected area with an approved service underbody sealer
8Remove masking from component mounting faces, and touch-in where necessary. Allow adequate drying time
before applying underbody wax
Page 1323 of 1672
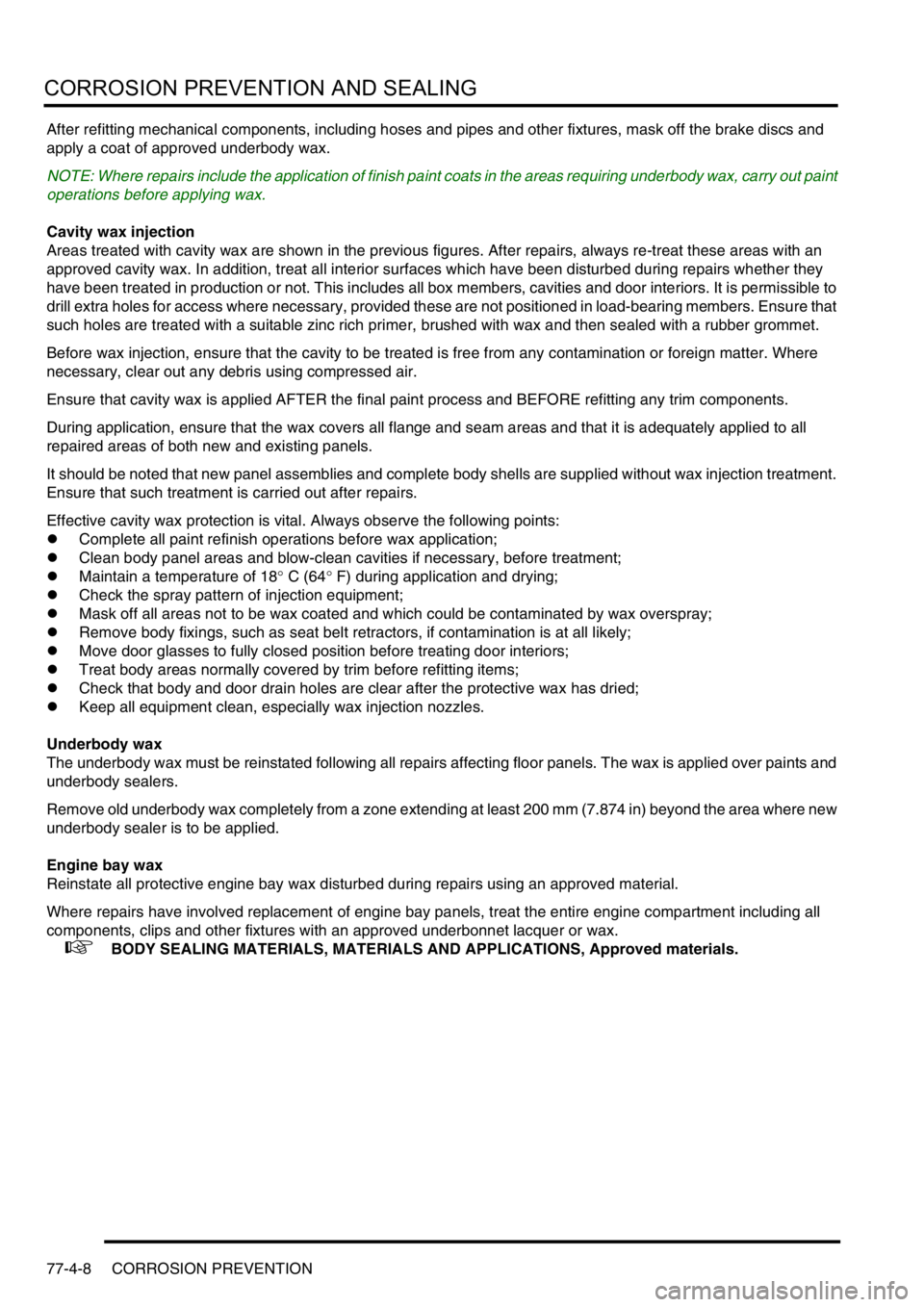
CORROSION PREVENTION AND SEALING
77-4-8 CORROSION PREVENTION
After refitting mechanical components, including hoses and pipes and other fixtures, mask off the brake discs and
apply a coat of approved underbody wax.
NOTE: Where repairs include the application of finish paint coats in the areas requiring underbody wax, carry out paint
operations before applying wax.
Cavity wax injection
Areas treated with cavity wax are shown in the previous figures. After repairs, always re-treat these areas with an
approved cavity wax. In addition, treat all interior surfaces which have been disturbed during repairs whether they
have been treated in production or not. This includes all box members, cavities and door interiors. It is permissible to
drill extra holes for access where necessary, provided these are not positioned in load-bearing members. Ensure that
such holes are treated with a suitable zinc rich primer, brushed with wax and then sealed with a rubber grommet.
Before wax injection, ensure that the cavity to be treated is free from any contamination or foreign matter. Where
necessary, clear out any debris using compressed air.
Ensure that cavity wax is applied AFTER the final paint process and BEFORE refitting any trim components.
During application, ensure that the wax covers all flange and seam areas and that it is adequately applied to all
repaired areas of both new and existing panels.
It should be noted that new panel assemblies and complete body shells are supplied without wax injection treatment.
Ensure that such treatment is carried out after repairs.
Effective cavity wax protection is vital. Always observe the following points:
lComplete all paint refinish operations before wax application;
lClean body panel areas and blow-clean cavities if necessary, before treatment;
lMaintain a temperature of 18
° C (64° F) during application and drying;
lCheck the spray pattern of injection equipment;
lMask off all areas not to be wax coated and which could be contaminated by wax overspray;
lRemove body fixings, such as seat belt retractors, if contamination is at all likely;
lMove door glasses to fully closed position before treating door interiors;
lTreat body areas normally covered by trim before refitting items;
lCheck that body and door drain holes are clear after the protective wax has dried;
lKeep all equipment clean, especially wax injection nozzles.
Underbody wax
The underbody wax must be reinstated following all repairs affecting floor panels. The wax is applied over paints and
underbody sealers.
Remove old underbody wax completely from a zone extending at least 200 mm (7.874 in) beyond the area where new
underbody sealer is to be applied.
Engine bay wax
Reinstate all protective engine bay wax disturbed during repairs using an approved material.
Where repairs have involved replacement of engine bay panels, treat the entire engine compartment including all
components, clips and other fixtures with an approved underbonnet lacquer or wax.
+ BODY SEALING MATERIALS, MATERIALS AND APPLICATIONS, Approved materials.
Page 1472 of 1672
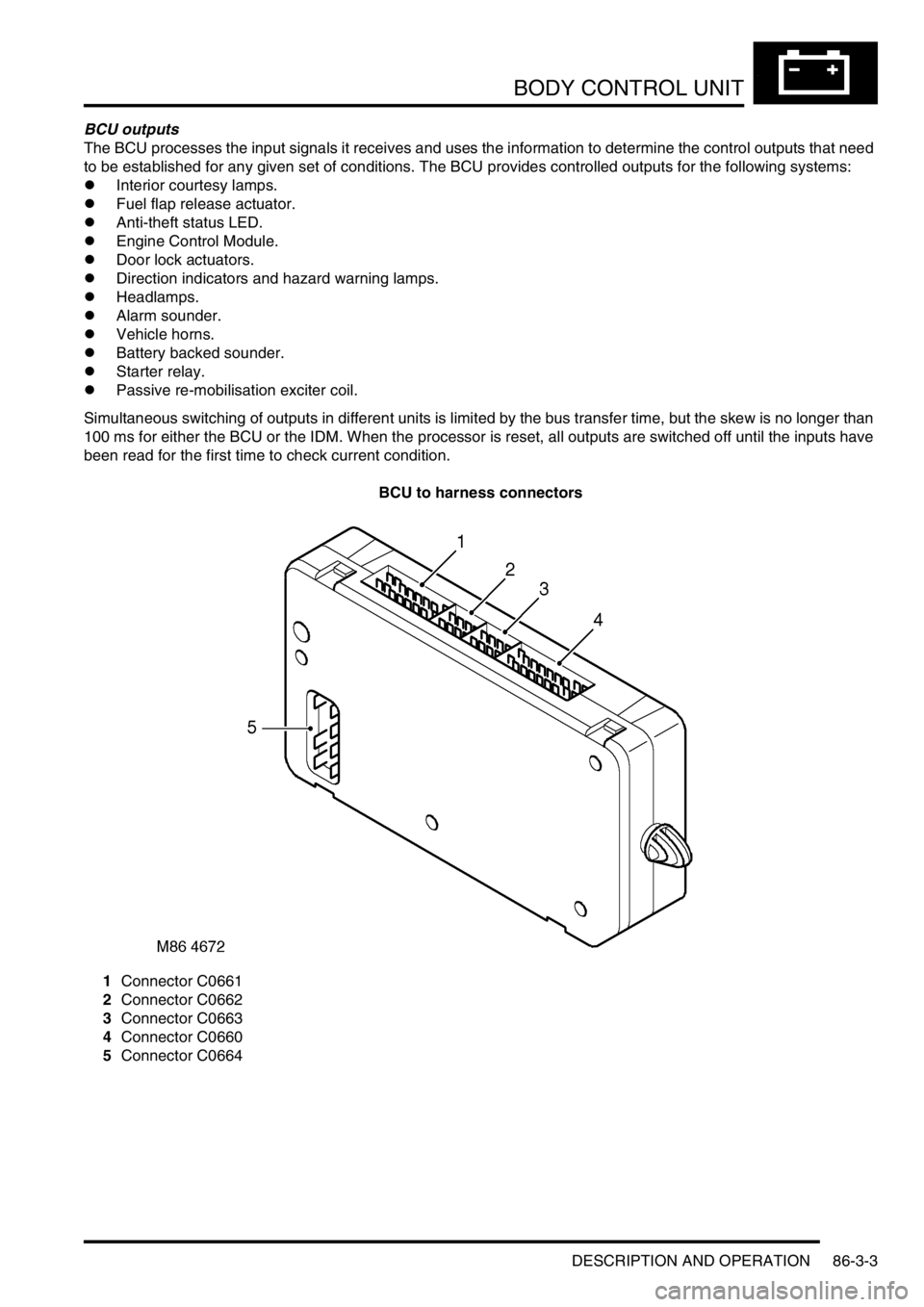
BODY CONTROL UNIT
DESCRIPTION AND OPERATION 86-3-3
BCU outputs
The BCU processes the input signals it receives and uses the information to determine the control outputs that need
to be established for any given set of conditions. The BCU provides controlled outputs for the following systems:
lInterior courtesy lamps.
lFuel flap release actuator.
lAnti-theft status LED.
lEngine Control Module.
lDoor lock actuators.
lDirection indicators and hazard warning lamps.
lHeadlamps.
lAlarm sounder.
lVehicle horns.
lBattery backed sounder.
lStarter relay.
lPassive re-mobilisation exciter coil.
Simultaneous switching of outputs in different units is limited by the bus transfer time, but the skew is no longer than
100 ms for either the BCU or the IDM. When the processor is reset, all outputs are switched off until the inputs have
been read for the first time to check current condition.
BCU to harness connectors
1Connector C0661
2Connector C0662
3Connector C0663
4Connector C0660
5Connector C0664
Page 1487 of 1672
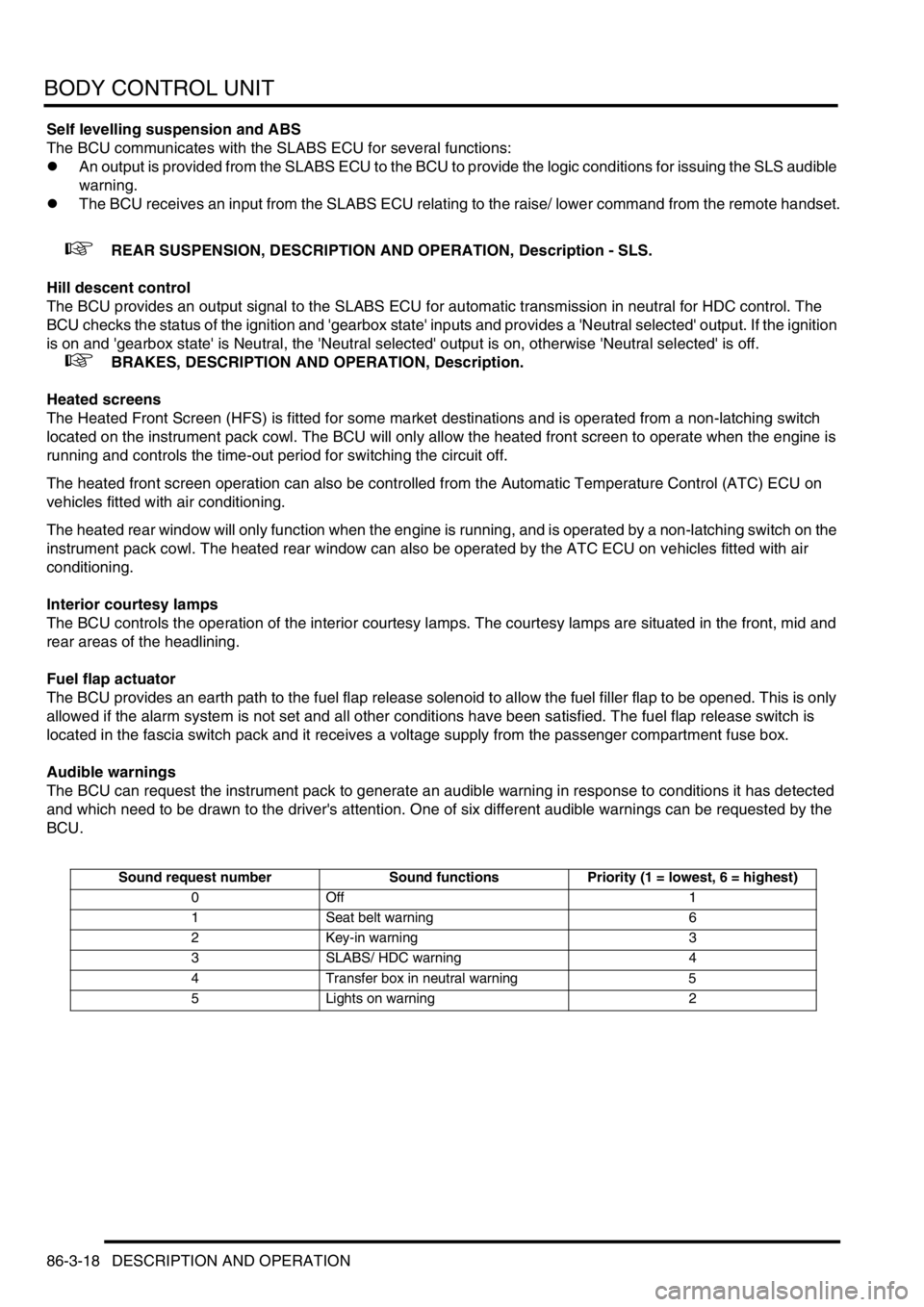
BODY CONTROL UNIT
86-3-18 DESCRIPTION AND OPERATION
Self levelling suspension and ABS
The BCU communicates with the SLABS ECU for several functions:
lAn output is provided from the SLABS ECU to the BCU to provide the logic conditions for issuing the SLS audible
warning.
lThe BCU receives an input from the SLABS ECU relating to the raise/ lower command from the remote handset.
+ REAR SUSPENSION, DESCRIPTION AND OPERATION, Description - SLS.
Hill descent control
The BCU provides an output signal to the SLABS ECU for automatic transmission in neutral for HDC control. The
BCU checks the status of the ignition and 'gearbox state' inputs and provides a 'Neutral selected' output. If the ignition
is on and 'gearbox state' is Neutral, the 'Neutral selected' output is on, otherwise 'Neutral selected' is off.
+ BRAKES, DESCRIPTION AND OPERATION, Description.
Heated screens
The Heated Front Screen (HFS) is fitted for some market destinations and is operated from a non-latching switch
located on the instrument pack cowl. The BCU will only allow the heated front screen to operate when the engine is
running and controls the time-out period for switching the circuit off.
The heated front screen operation can also be controlled from the Automatic Temperature Control (ATC) ECU on
vehicles fitted with air conditioning.
The heated rear window will only function when the engine is running, and is operated by a non-latching switch on the
instrument pack cowl. The heated rear window can also be operated by the ATC ECU on vehicles fitted with air
conditioning.
Interior courtesy lamps
The BCU controls the operation of the interior courtesy lamps. The courtesy lamps are situated in the front, mid and
rear areas of the headlining.
Fuel flap actuator
The BCU provides an earth path to the fuel flap release solenoid to allow the fuel filler flap to be opened. This is only
allowed if the alarm system is not set and all other conditions have been satisfied. The fuel flap release switch is
located in the fascia switch pack and it receives a voltage supply from the passenger compartment fuse box.
Audible warnings
The BCU can request the instrument pack to generate an audible warning in response to conditions it has detected
and which need to be drawn to the driver's attention. One of six different audible warnings can be requested by the
BCU.
Sound request number Sound functions Priority (1 = lowest, 6 = highest)
0Off 1
1 Seat belt warning 6
2 Key-in warning 3
3 SLABS/ HDC warning 4
4 Transfer box in neutral warning 5
5 Lights on warning 2
Page 1488 of 1672
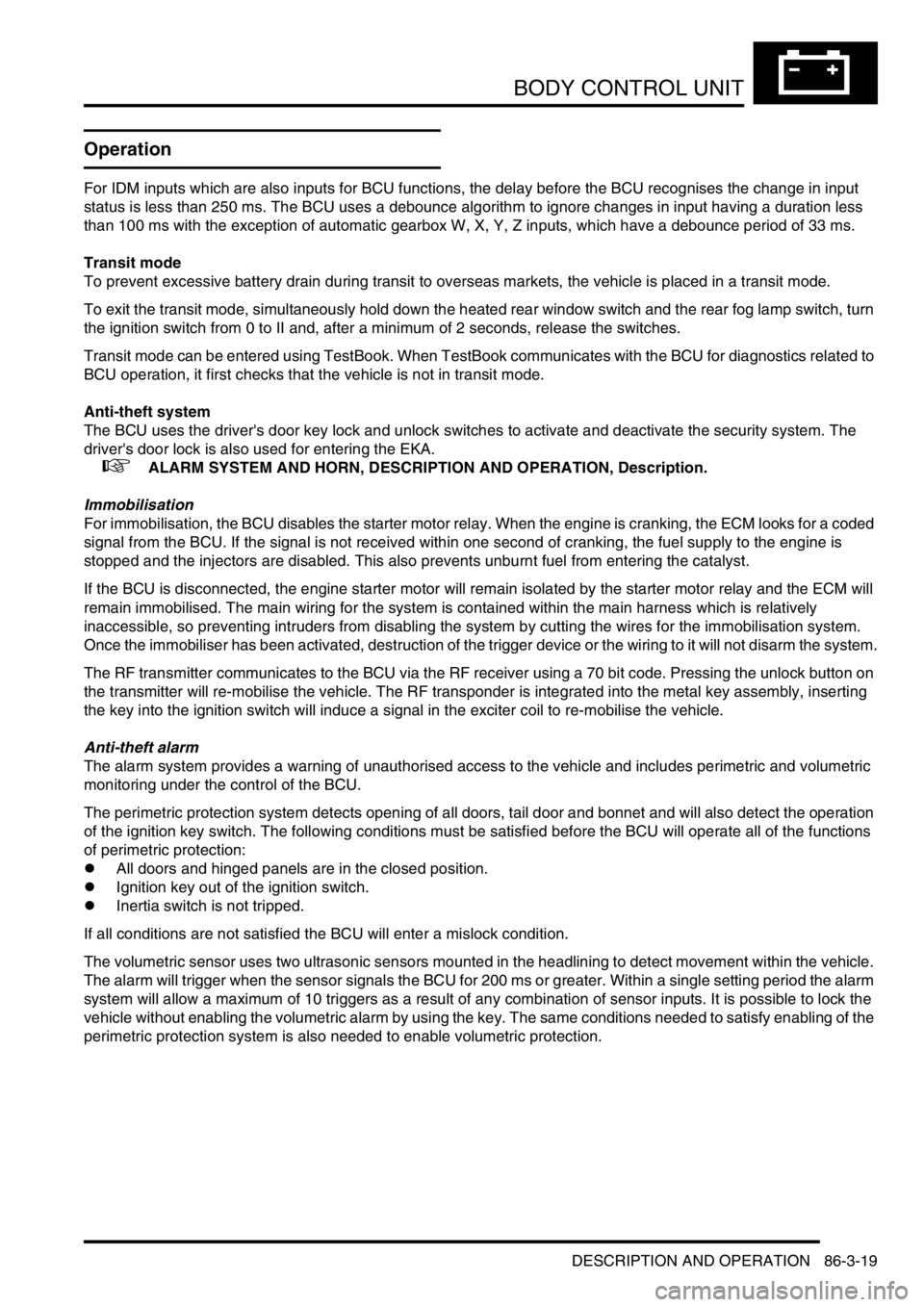
BODY CONTROL UNIT
DESCRIPTION AND OPERATION 86-3-19
Operation
For IDM inputs which are also inputs for BCU functions, the delay before the BCU recognises the change in input
status is less than 250 ms. The BCU uses a debounce algorithm to ignore changes in input having a duration less
than 100 ms with the exception of automatic gearbox W, X, Y, Z inputs, which have a debounce period of 33 ms.
Transit mode
To prevent excessive battery drain during transit to overseas markets, the vehicle is placed in a transit mode.
To exit the transit mode, simultaneously hold down the heated rear window switch and the rear fog lamp switch, turn
the ignition switch from 0 to II and, after a minimum of 2 seconds, release the switches.
Transit mode can be entered using TestBook. When TestBook communicates with the BCU for diagnostics related to
BCU operation, it first checks that the vehicle is not in transit mode.
Anti-theft system
The BCU uses the driver's door key lock and unlock switches to activate and deactivate the security system. The
driver's door lock is also used for entering the EKA.
+ ALARM SYSTEM AND HORN, DESCRIPTION AND OPERATION, Description.
Immobilisation
For immobilisation, the BCU disables the starter motor relay. When the engine is cranking, the ECM looks for a coded
signal from the BCU. If the signal is not received within one second of cranking, the fuel supply to the engine is
stopped and the injectors are disabled. This also prevents unburnt fuel from entering the catalyst.
If the BCU is disconnected, the engine starter motor will remain isolated by the starter motor relay and the ECM will
remain immobilised. The main wiring for the system is contained within the main harness which is relatively
inaccessible, so preventing intruders from disabling the system by cutting the wires for the immobilisation system.
Once the immobiliser has been activated, destruction of the trigger device or the wiring to it will not disarm the system.
The RF transmitter communicates to the BCU via the RF receiver using a 70 bit code. Pressing the unlock button on
the transmitter will re-mobilise the vehicle. The RF transponder is integrated into the metal key assembly, inserting
the key into the ignition switch will induce a signal in the exciter coil to re-mobilise the vehicle.
Anti-theft alarm
The alarm system provides a warning of unauthorised access to the vehicle and includes perimetric and volumetric
monitoring under the control of the BCU.
The perimetric protection system detects opening of all doors, tail door and bonnet and will also detect the operation
of the ignition key switch. The following conditions must be satisfied before the BCU will operate all of the functions
of perimetric protection:
lAll doors and hinged panels are in the closed position.
lIgnition key out of the ignition switch.
lInertia switch is not tripped.
If all conditions are not satisfied the BCU will enter a mislock condition.
The volumetric sensor uses two ultrasonic sensors mounted in the headlining to detect movement within the vehicle.
The alarm will trigger when the sensor signals the BCU for 200 ms or greater. Within a single setting period the alarm
system will allow a maximum of 10 triggers as a result of any combination of sensor inputs. It is possible to lock the
vehicle without enabling the volumetric alarm by using the key. The same conditions needed to satisfy enabling of the
perimetric protection system is also needed to enable volumetric protection.
Page 1495 of 1672
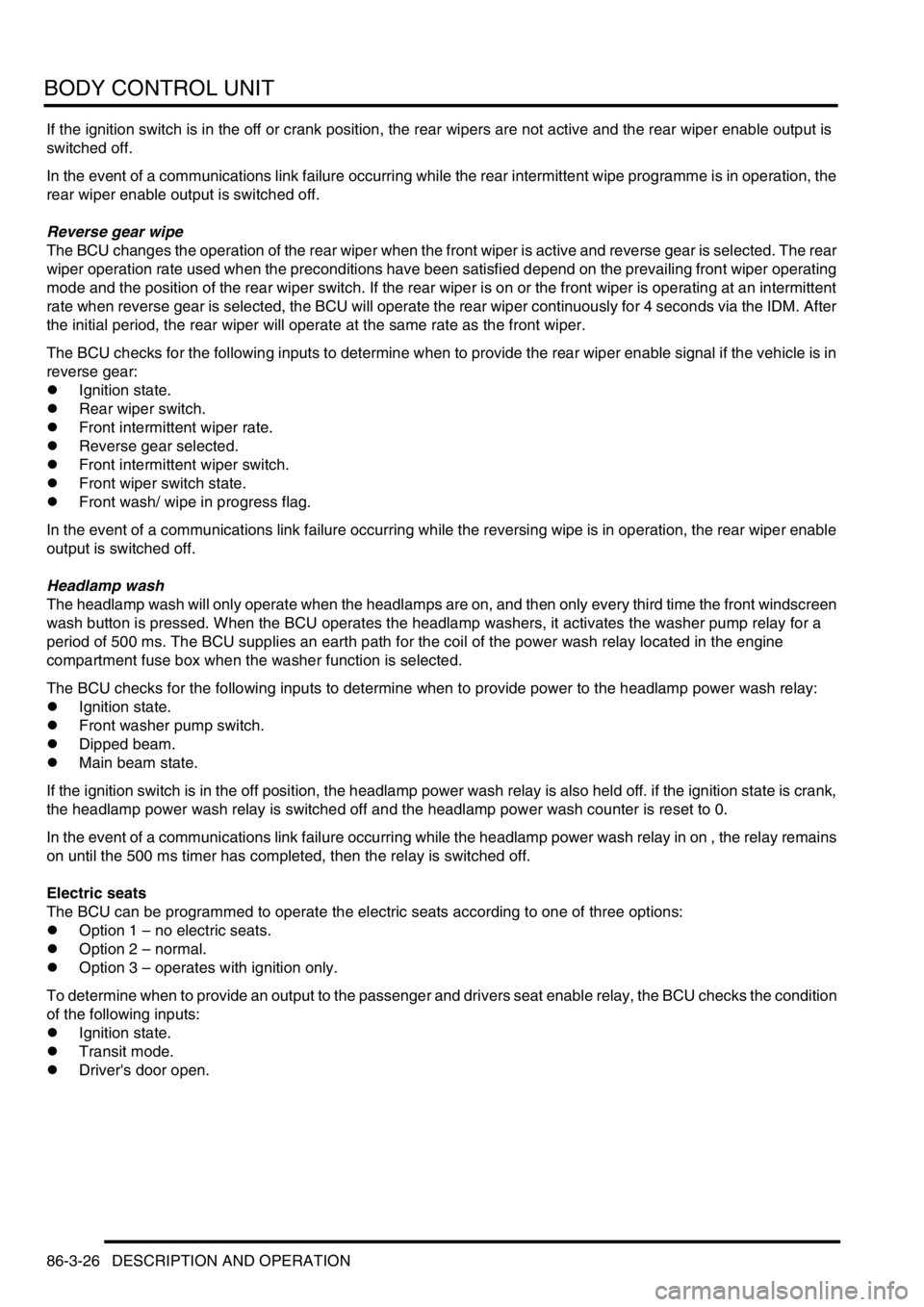
BODY CONTROL UNIT
86-3-26 DESCRIPTION AND OPERATION
If the ignition switch is in the off or crank position, the rear wipers are not active and the rear wiper enable output is
switched off.
In the event of a communications link failure occurring while the rear intermittent wipe programme is in operation, the
rear wiper enable output is switched off.
Reverse gear wipe
The BCU changes the operation of the rear wiper when the front wiper is active and reverse gear is selected. The rear
wiper operation rate used when the preconditions have been satisfied depend on the prevailing front wiper operating
mode and the position of the rear wiper switch. If the rear wiper is on or the front wiper is operating at an intermittent
rate when reverse gear is selected, the BCU will operate the rear wiper continuously for 4 seconds via the IDM. After
the initial period, the rear wiper will operate at the same rate as the front wiper.
The BCU checks for the following inputs to determine when to provide the rear wiper enable signal if the vehicle is in
reverse gear:
lIgnition state.
lRear wiper switch.
lFront intermittent wiper rate.
lReverse gear selected.
lFront intermittent wiper switch.
lFront wiper switch state.
lFront wash/ wipe in progress flag.
In the event of a communications link failure occurring while the reversing wipe is in operation, the rear wiper enable
output is switched off.
Headlamp wash
The headlamp wash will only operate when the headlamps are on, and then only every third time the front windscreen
wash button is pressed. When the BCU operates the headlamp washers, it activates the washer pump relay for a
period of 500 ms. The BCU supplies an earth path for the coil of the power wash relay located in the engine
compartment fuse box when the washer function is selected.
The BCU checks for the following inputs to determine when to provide power to the headlamp power wash relay:
lIgnition state.
lFront washer pump switch.
lDipped beam.
lMain beam state.
If the ignition switch is in the off position, the headlamp power wash relay is also held off. if the ignition state is crank,
the headlamp power wash relay is switched off and the headlamp power wash counter is reset to 0.
In the event of a communications link failure occurring while the headlamp power wash relay in on , the relay remains
on until the 500 ms timer has completed, then the relay is switched off.
Electric seats
The BCU can be programmed to operate the electric seats according to one of three options:
lOption 1 – no electric seats.
lOption 2 – normal.
lOption 3 – operates with ignition only.
To determine when to provide an output to the passenger and drivers seat enable relay, the BCU checks the condition
of the following inputs:
lIgnition state.
lTransit mode.
lDriver's door open.
Page 1498 of 1672
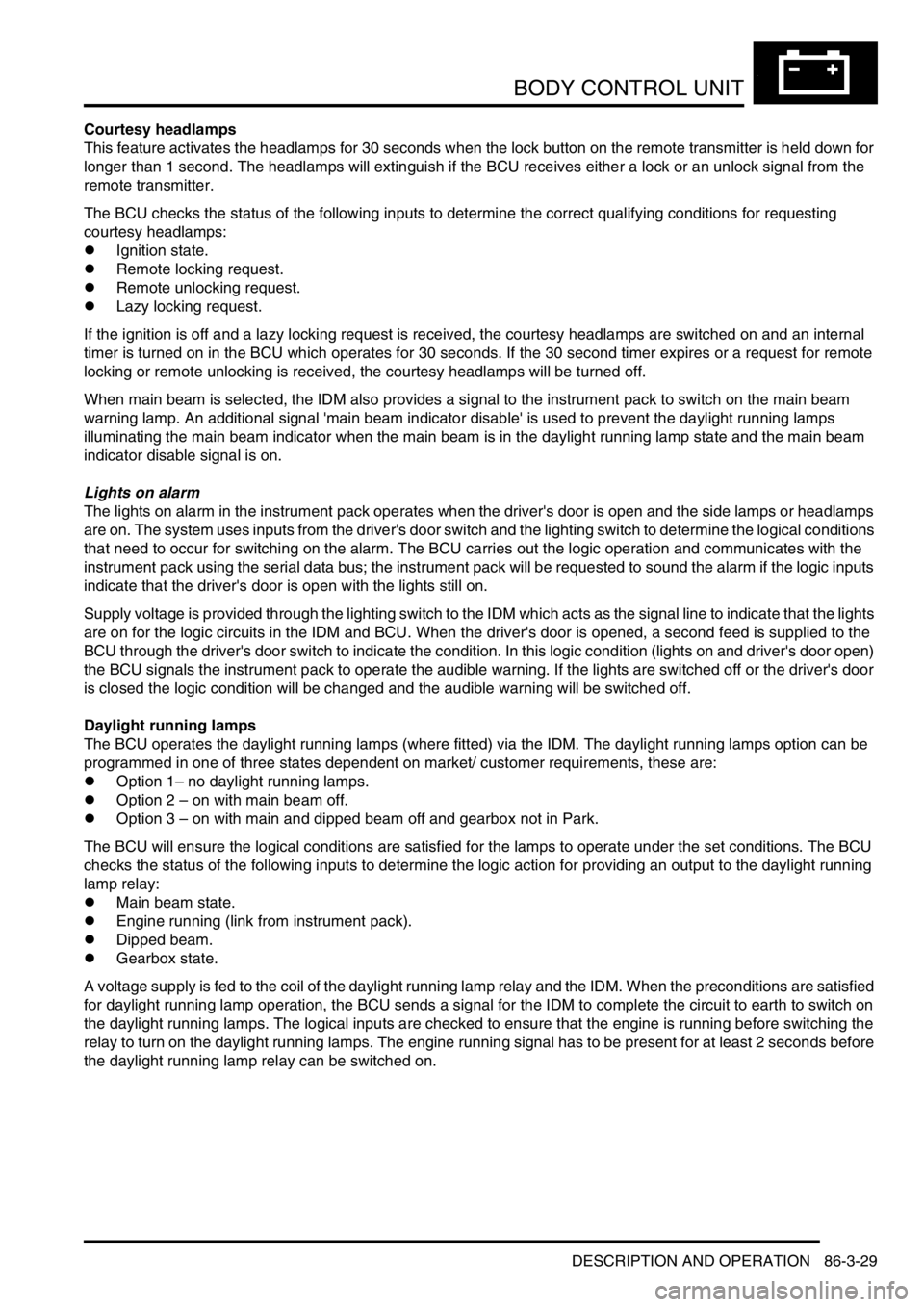
BODY CONTROL UNIT
DESCRIPTION AND OPERATION 86-3-29
Courtesy headlamps
This feature activates the headlamps for 30 seconds when the lock button on the remote transmitter is held down for
longer than 1 second. The headlamps will extinguish if the BCU receives either a lock or an unlock signal from the
remote transmitter.
The BCU checks the status of the following inputs to determine the correct qualifying conditions for requesting
courtesy headlamps:
lIgnition state.
lRemote locking request.
lRemote unlocking request.
lLazy locking request.
If the ignition is off and a lazy locking request is received, the courtesy headlamps are switched on and an internal
timer is turned on in the BCU which operates for 30 seconds. If the 30 second timer expires or a request for remote
locking or remote unlocking is received, the courtesy headlamps will be turned off.
When main beam is selected, the IDM also provides a signal to the instrument pack to switch on the main beam
warning lamp. An additional signal 'main beam indicator disable' is used to prevent the daylight running lamps
illuminating the main beam indicator when the main beam is in the daylight running lamp state and the main beam
indicator disable signal is on.
Lights on alarm
The lights on alarm in the instrument pack operates when the driver's door is open and the side lamps or headlamps
are on. The system uses inputs from the driver's door switch and the lighting switch to determine the logical conditions
that need to occur for switching on the alarm. The BCU carries out the logic operation and communicates with the
instrument pack using the serial data bus; the instrument pack will be requested to sound the alarm if the logic inputs
indicate that the driver's door is open with the lights still on.
Supply voltage is provided through the lighting switch to the IDM which acts as the signal line to indicate that the lights
are on for the logic circuits in the IDM and BCU. When the driver's door is opened, a second feed is supplied to the
BCU through the driver's door switch to indicate the condition. In this logic condition (lights on and driver's door open)
the BCU signals the instrument pack to operate the audible warning. If the lights are switched off or the driver's door
is closed the logic condition will be changed and the audible warning will be switched off.
Daylight running lamps
The BCU operates the daylight running lamps (where fitted) via the IDM. The daylight running lamps option can be
programmed in one of three states dependent on market/ customer requirements, these are:
lOption 1– no daylight running lamps.
lOption 2 – on with main beam off.
lOption 3 – on with main and dipped beam off and gearbox not in Park.
The BCU will ensure the logical conditions are satisfied for the lamps to operate under the set conditions. The BCU
checks the status of the following inputs to determine the logic action for providing an output to the daylight running
lamp relay:
lMain beam state.
lEngine running (link from instrument pack).
lDipped beam.
lGearbox state.
A voltage supply is fed to the coil of the daylight running lamp relay and the IDM. When the preconditions are satisfied
for daylight running lamp operation, the BCU sends a signal for the IDM to complete the circuit to earth to switch on
the daylight running lamps. The logical inputs are checked to ensure that the engine is running before switching the
relay to turn on the daylight running lamps. The engine running signal has to be present for at least 2 seconds before
the daylight running lamp relay can be switched on.