ECU LAND ROVER DISCOVERY 2002 Workshop Manual
[x] Cancel search | Manufacturer: LAND ROVER, Model Year: 2002, Model line: DISCOVERY, Model: LAND ROVER DISCOVERY 2002Pages: 1672, PDF Size: 46.1 MB
Page 346 of 1672
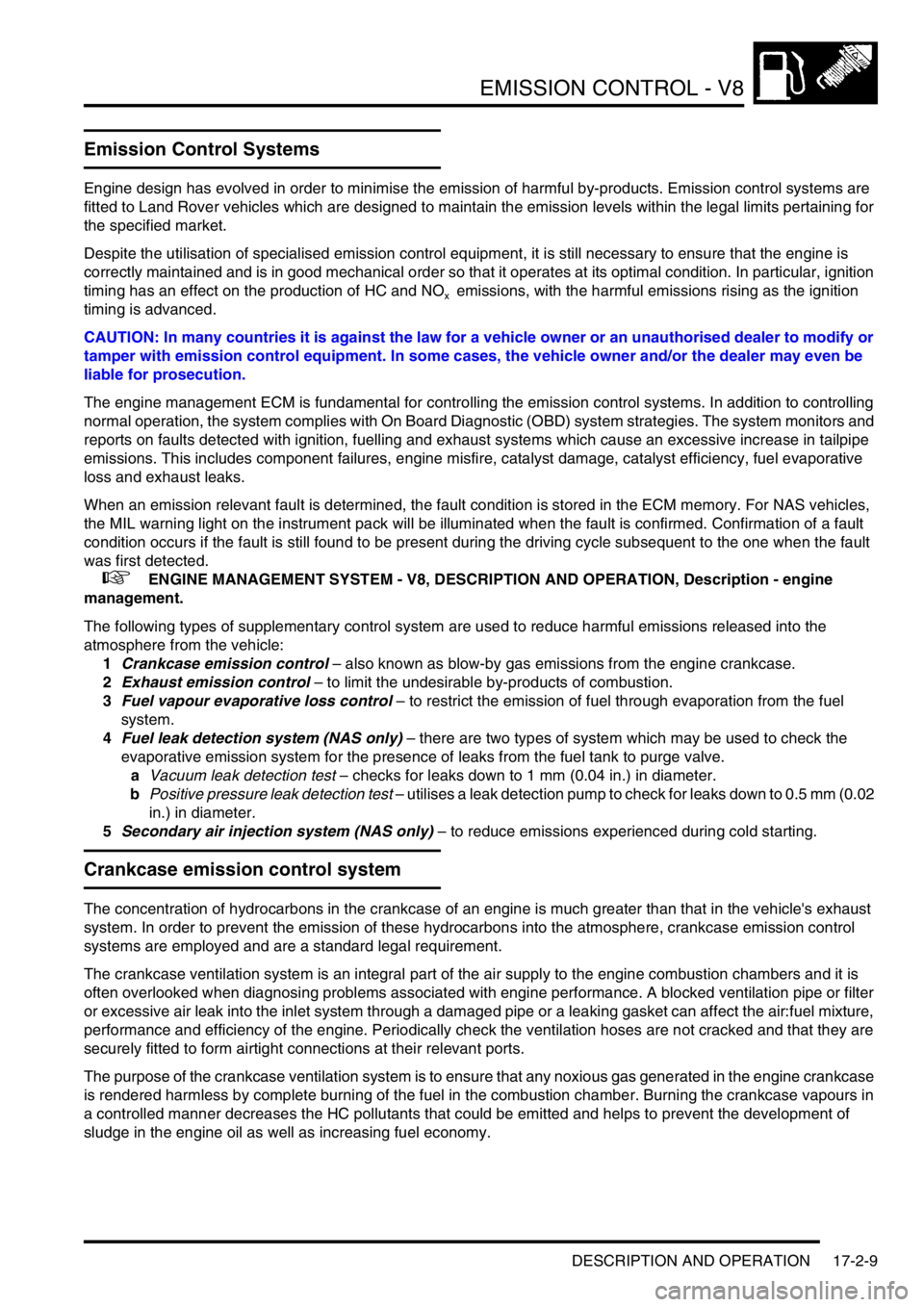
EMISSION CONTROL - V8
DESCRIPTION AND OPERATION 17-2-9
Emission Control Systems
Engine design has evolved in order to minimise the emission of harmful by-products. Emission control systems are
fitted to Land Rover vehicles which are designed to maintain the emission levels within the legal limits pertaining for
the specified market.
Despite the utilisation of specialised emission control equipment, it is still necessary to ensure that the engine is
correctly maintained and is in good mechanical order so that it operates at its optimal condition. In particular, ignition
timing has an effect on the production of HC and NO
x emissions, with the harmful emissions rising as the ignition
timing is advanced.
CAUTION: In many countries it is against the law for a vehicle owner or an unauthorised dealer to modify or
tamper with emission control equipment. In some cases, the vehicle owner and/or the dealer may even be
liable for prosecution.
The engine management ECM is fundamental for controlling the emission control systems. In addition to controlling
normal operation, the system complies with On Board Diagnostic (OBD) system strategies. The system monitors and
reports on faults detected with ignition, fuelling and exhaust systems which cause an excessive increase in tailpipe
emissions. This includes component failures, engine misfire, catalyst damage, catalyst efficiency, fuel evaporative
loss and exhaust leaks.
When an emission relevant fault is determined, the fault condition is stored in the ECM memory. For NAS vehicles,
the MIL warning light on the instrument pack will be illuminated when the fault is confirmed. Confirmation of a fault
condition occurs if the fault is still found to be present during the driving cycle subsequent to the one when the fault
was first detected.
+ ENGINE MANAGEMENT SYSTEM - V8, DESCRIPTION AND OPERATION, Description - engine
management.
The following types of supplementary control system are used to reduce harmful emissions released into the
atmosphere from the vehicle:
1Crankcase emission control – also known as blow-by gas emissions from the engine crankcase.
2Exhaust emission control – to limit the undesirable by-products of combustion.
3Fuel vapour evaporative loss control – to restrict the emission of fuel through evaporation from the fuel
system.
4Fuel leak detection system (NAS only) – there are two types of system which may be used to check the
evaporative emission system for the presence of leaks from the fuel tank to purge valve.
aVacuum leak detection test – checks for leaks down to 1 mm (0.04 in.) in diameter.
bPositive pressure leak detection test – utilises a leak detection pump to check for leaks down to 0.5 mm (0.02
in.) in diameter.
5Secondary air injection system (NAS only) – to reduce emissions experienced during cold starting.
Crankcase emission control system
The concentration of hydrocarbons in the crankcase of an engine is much greater than that in the vehicle's exhaust
system. In order to prevent the emission of these hydrocarbons into the atmosphere, crankcase emission control
systems are employed and are a standard legal requirement.
The crankcase ventilation system is an integral part of the air supply to the engine combustion chambers and it is
often overlooked when diagnosing problems associated with engine performance. A blocked ventilation pipe or filter
or excessive air leak into the inlet system through a damaged pipe or a leaking gasket can affect the air:fuel mixture,
performance and efficiency of the engine. Periodically check the ventilation hoses are not cracked and that they are
securely fitted to form airtight connections at their relevant ports.
The purpose of the crankcase ventilation system is to ensure that any noxious gas generated in the engine crankcase
is rendered harmless by complete burning of the fuel in the combustion chamber. Burning the crankcase vapours in
a controlled manner decreases the HC pollutants that could be emitted and helps to prevent the development of
sludge in the engine oil as well as increasing fuel economy.
Page 356 of 1672
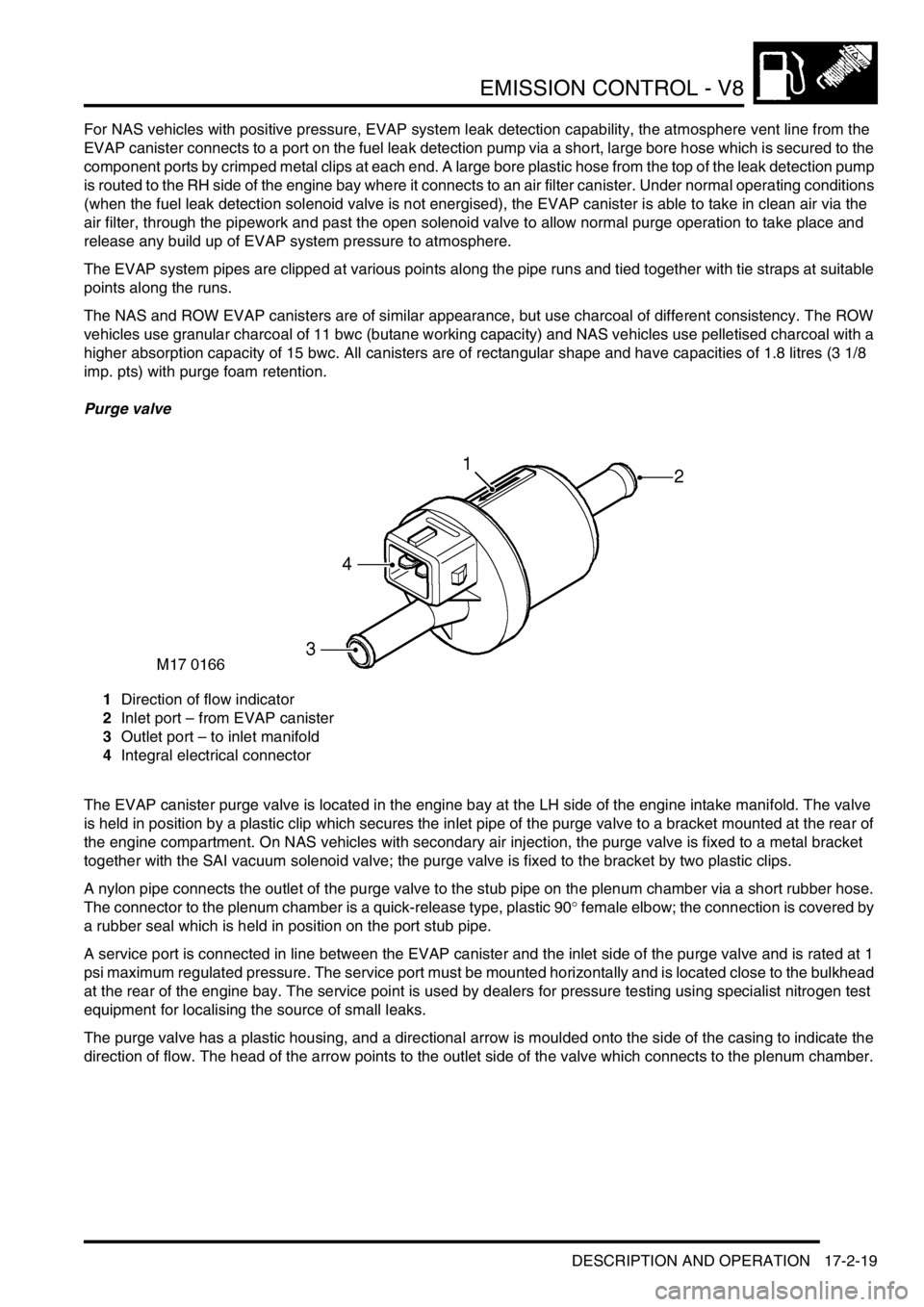
EMISSION CONTROL - V8
DESCRIPTION AND OPERATION 17-2-19
For NAS vehicles with positive pressure, EVAP system leak detection capability, the atmosphere vent line from the
EVAP canister connects to a port on the fuel leak detection pump via a short, large bore hose which is secured to the
component ports by crimped metal clips at each end. A large bore plastic hose from the top of the leak detection pump
is routed to the RH side of the engine bay where it connects to an air filter canister. Under normal operating conditions
(when the fuel leak detection solenoid valve is not energised), the EVAP canister is able to take in clean air via the
air filter, through the pipework and past the open solenoid valve to allow normal purge operation to take place and
release any build up of EVAP system pressure to atmosphere.
The EVAP system pipes are clipped at various points along the pipe runs and tied together with tie straps at suitable
points along the runs.
The NAS and ROW EVAP canisters are of similar appearance, but use charcoal of different consistency. The ROW
vehicles use granular charcoal of 11 bwc (butane working capacity) and NAS vehicles use pelletised charcoal with a
higher absorption capacity of 15 bwc. All canisters are of rectangular shape and have capacities of 1.8 litres (3 1/8
imp. pts) with purge foam retention.
Purge valve
1Direction of flow indicator
2Inlet port – from EVAP canister
3Outlet port – to inlet manifold
4Integral electrical connector
The EVAP canister purge valve is located in the engine bay at the LH side of the engine intake manifold. The valve
is held in position by a plastic clip which secures the inlet pipe of the purge valve to a bracket mounted at the rear of
the engine compartment. On NAS vehicles with secondary air injection, the purge valve is fixed to a metal bracket
together with the SAI vacuum solenoid valve; the purge valve is fixed to the bracket by two plastic clips.
A nylon pipe connects the outlet of the purge valve to the stub pipe on the plenum chamber via a short rubber hose.
The connector to the plenum chamber is a quick-release type, plastic 90
° female elbow; the connection is covered by
a rubber seal which is held in position on the port stub pipe.
A service port is connected in line between the EVAP canister and the inlet side of the purge valve and is rated at 1
psi maximum regulated pressure. The service port must be mounted horizontally and is located close to the bulkhead
at the rear of the engine bay. The service point is used by dealers for pressure testing using specialist nitrogen test
equipment for localising the source of small leaks.
The purge valve has a plastic housing, and a directional arrow is moulded onto the side of the casing to indicate the
direction of flow. The head of the arrow points to the outlet side of the valve which connects to the plenum chamber.
Page 361 of 1672
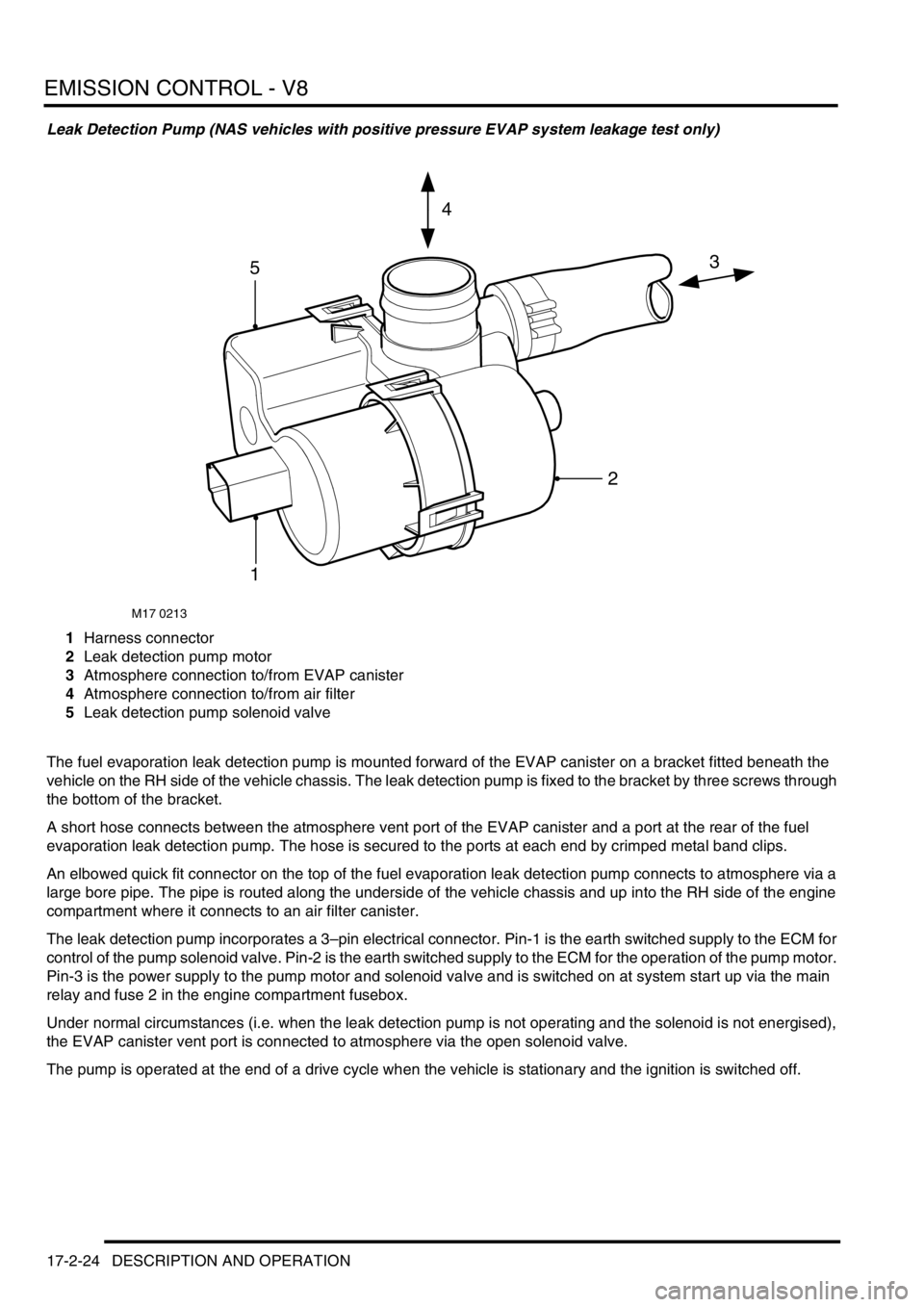
EMISSION CONTROL - V8
17-2-24 DESCRIPTION AND OPERATION
Leak Detection Pump (NAS vehicles with positive pressure EVAP system leakage test only)
1Harness connector
2Leak detection pump motor
3Atmosphere connection to/from EVAP canister
4Atmosphere connection to/from air filter
5Leak detection pump solenoid valve
The fuel evaporation leak detection pump is mounted forward of the EVAP canister on a bracket fitted beneath the
vehicle on the RH side of the vehicle chassis. The leak detection pump is fixed to the bracket by three screws through
the bottom of the bracket.
A short hose connects between the atmosphere vent port of the EVAP canister and a port at the rear of the fuel
evaporation leak detection pump. The hose is secured to the ports at each end by crimped metal band clips.
An elbowed quick fit connector on the top of the fuel evaporation leak detection pump connects to atmosphere via a
large bore pipe. The pipe is routed along the underside of the vehicle chassis and up into the RH side of the engine
compartment where it connects to an air filter canister.
The leak detection pump incorporates a 3–pin electrical connector. Pin-1 is the earth switched supply to the ECM for
control of the pump solenoid valve. Pin-2 is the earth switched supply to the ECM for the operation of the pump motor.
Pin-3 is the power supply to the pump motor and solenoid valve and is switched on at system start up via the main
relay and fuse 2 in the engine compartment fusebox.
Under normal circumstances (i.e. when the leak detection pump is not operating and the solenoid is not energised),
the EVAP canister vent port is connected to atmosphere via the open solenoid valve.
The pump is operated at the end of a drive cycle when the vehicle is stationary and the ignition is switched off.
M17 0213
3
4
5
1
2
Page 362 of 1672
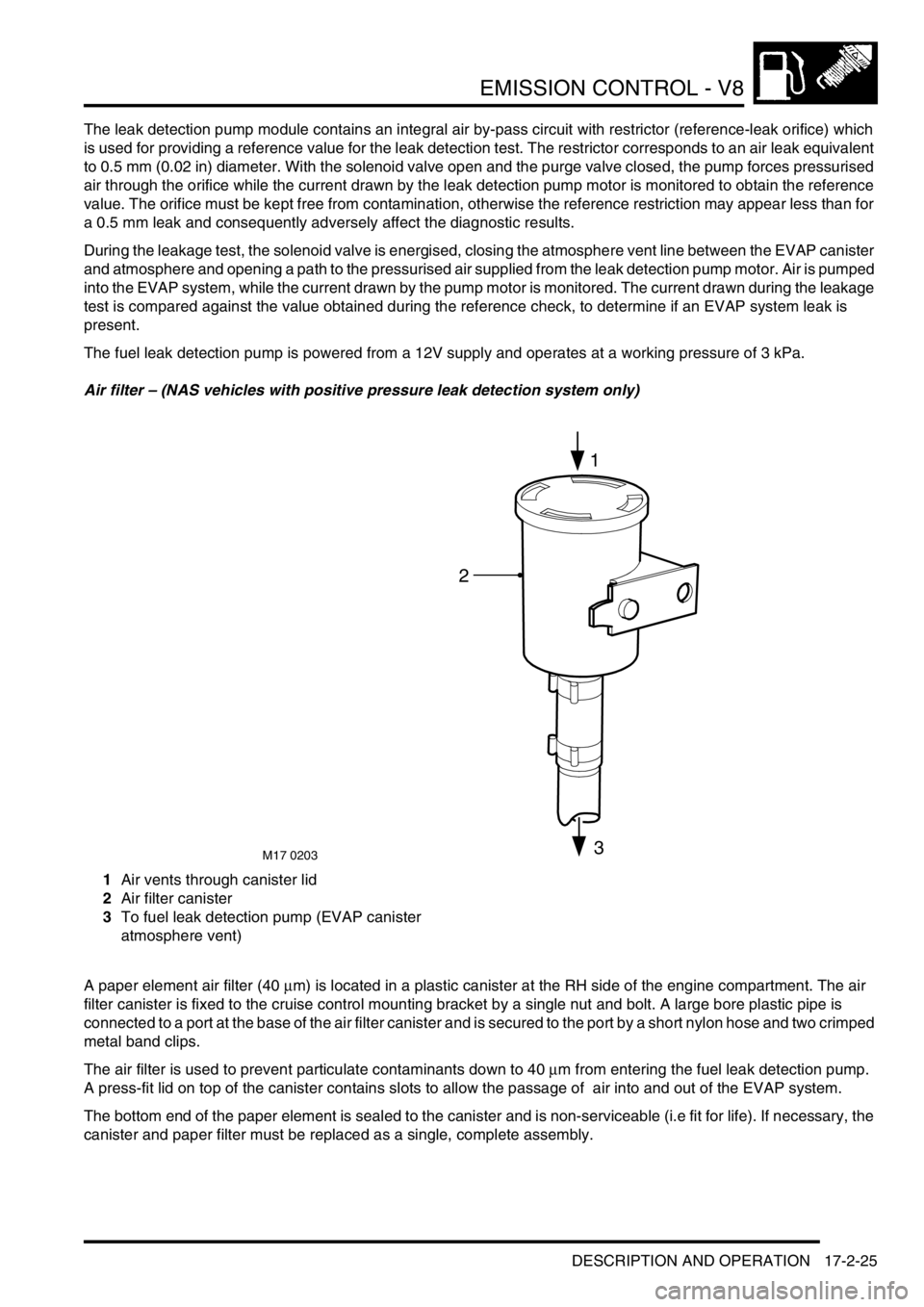
EMISSION CONTROL - V8
DESCRIPTION AND OPERATION 17-2-25
The leak detection pump module contains an integral air by-pass circuit with restrictor (reference-leak orifice) which
is used for providing a reference value for the leak detection test. The restrictor corresponds to an air leak equivalent
to 0.5 mm (0.02 in) diameter. With the solenoid valve open and the purge valve closed, the pump forces pressurised
air through the orifice while the current drawn by the leak detection pump motor is monitored to obtain the reference
value. The orifice must be kept free from contamination, otherwise the reference restriction may appear less than for
a 0.5 mm leak and consequently adversely affect the diagnostic results.
During the leakage test, the solenoid valve is energised, closing the atmosphere vent line between the EVAP canister
and atmosphere and opening a path to the pressurised air supplied from the leak detection pump motor. Air is pumped
into the EVAP system, while the current drawn by the pump motor is monitored. The current drawn during the leakage
test is compared against the value obtained during the reference check, to determine if an EVAP system leak is
present.
The fuel leak detection pump is powered from a 12V supply and operates at a working pressure of 3 kPa.
Air filter – (NAS vehicles with positive pressure leak detection system only)
1Air vents through canister lid
2Air filter canister
3To fuel leak detection pump (EVAP canister
atmosphere vent)
A paper element air filter (40
µm) is located in a plastic canister at the RH side of the engine compartment. The air
filter canister is fixed to the cruise control mounting bracket by a single nut and bolt. A large bore plastic pipe is
connected to a port at the base of the air filter canister and is secured to the port by a short nylon hose and two crimped
metal band clips.
The air filter is used to prevent particulate contaminants down to 40
µm from entering the fuel leak detection pump.
A press-fit lid on top of the canister contains slots to allow the passage of air into and out of the EVAP system.
The bottom end of the paper element is sealed to the canister and is non-serviceable (i.e fit for life). If necessary, the
canister and paper filter must be replaced as a single, complete assembly.
M17 0203
2
1
3
Page 376 of 1672
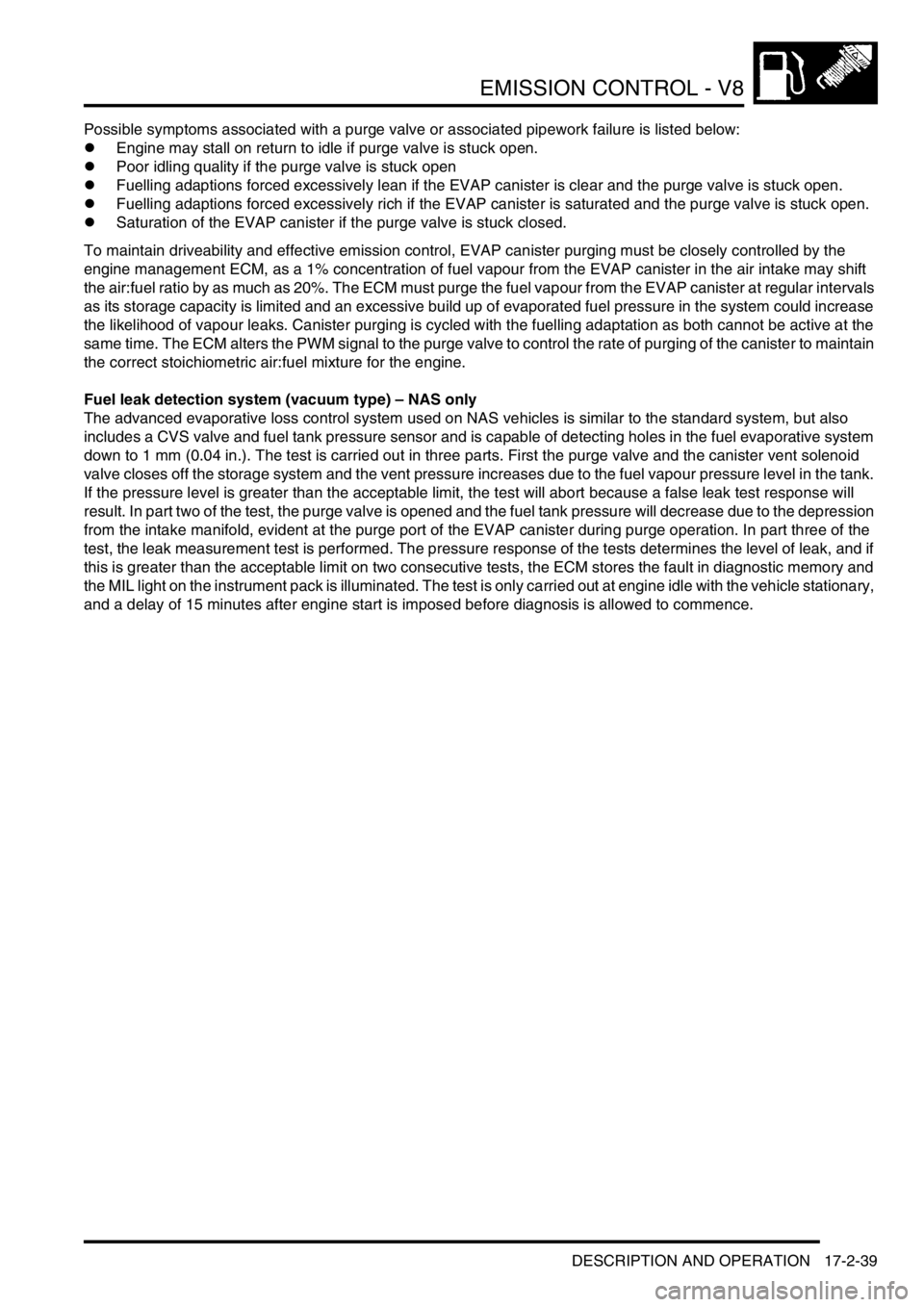
EMISSION CONTROL - V8
DESCRIPTION AND OPERATION 17-2-39
Possible symptoms associated with a purge valve or associated pipework failure is listed below:
lEngine may stall on return to idle if purge valve is stuck open.
lPoor idling quality if the purge valve is stuck open
lFuelling adaptions forced excessively lean if the EVAP canister is clear and the purge valve is stuck open.
lFuelling adaptions forced excessively rich if the EVAP canister is saturated and the purge valve is stuck open.
lSaturation of the EVAP canister if the purge valve is stuck closed.
To maintain driveability and effective emission control, EVAP canister purging must be closely controlled by the
engine management ECM, as a 1% concentration of fuel vapour from the EVAP canister in the air intake may shift
the air:fuel ratio by as much as 20%. The ECM must purge the fuel vapour from the EVAP canister at regular intervals
as its storage capacity is limited and an excessive build up of evaporated fuel pressure in the system could increase
the likelihood of vapour leaks. Canister purging is cycled with the fuelling adaptation as both cannot be active at the
same time. The ECM alters the PWM signal to the purge valve to control the rate of purging of the canister to maintain
the correct stoichiometric air:fuel mixture for the engine.
Fuel leak detection system (vacuum type) – NAS only
The advanced evaporative loss control system used on NAS vehicles is similar to the standard system, but also
includes a CVS valve and fuel tank pressure sensor and is capable of detecting holes in the fuel evaporative system
down to 1 mm (0.04 in.). The test is carried out in three parts. First the purge valve and the canister vent solenoid
valve closes off the storage system and the vent pressure increases due to the fuel vapour pressure level in the tank.
If the pressure level is greater than the acceptable limit, the test will abort because a false leak test response will
result. In part two of the test, the purge valve is opened and the fuel tank pressure will decrease due to the depression
from the intake manifold, evident at the purge port of the EVAP canister during purge operation. In part three of the
test, the leak measurement test is performed. The pressure response of the tests determines the level of leak, and if
this is greater than the acceptable limit on two consecutive tests, the ECM stores the fault in diagnostic memory and
the MIL light on the instrument pack is illuminated. The test is only carried out at engine idle with the vehicle stationary,
and a delay of 15 minutes after engine start is imposed before diagnosis is allowed to commence.
Page 380 of 1672
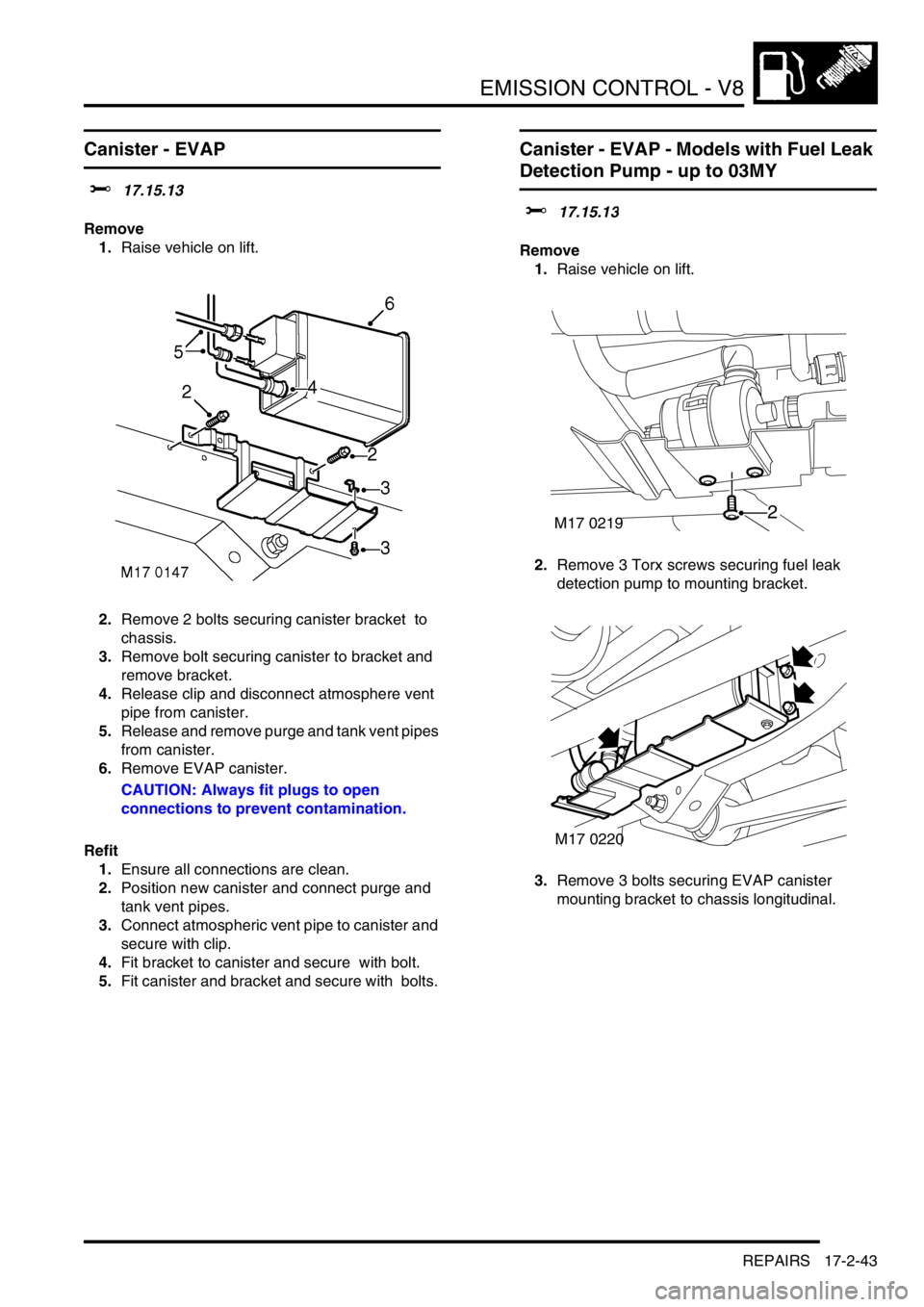
EMISSION CONTROL - V8
REPAIRS 17-2-43
REPAIRS
Canister - EVAP
$% 17.15.13
Remove
1.Raise vehicle on lift.
2.Remove 2 bolts securing canister bracket to
chassis.
3.Remove bolt securing canister to bracket and
remove bracket.
4.Release clip and disconnect atmosphere vent
pipe from canister.
5.Release and remove purge and tank vent pipes
from canister.
6.Remove EVAP canister.
CAUTION: Always fit plugs to open
connections to prevent contamination.
Refit
1.Ensure all connections are clean.
2.Position new canister and connect purge and
tank vent pipes.
3.Connect atmospheric vent pipe to canister and
secure with clip.
4.Fit bracket to canister and secure with bolt.
5.Fit canister and bracket and secure with bolts.
Canister - EVAP - Models with Fuel Leak
Detection Pump - up to 03MY
$% 17.15.13
Remove
1.Raise vehicle on lift.
2.Remove 3 Torx screws securing fuel leak
detection pump to mounting bracket.
3.Remove 3 bolts securing EVAP canister
mounting bracket to chassis longitudinal.
M17 02192
M17 0220
Page 381 of 1672
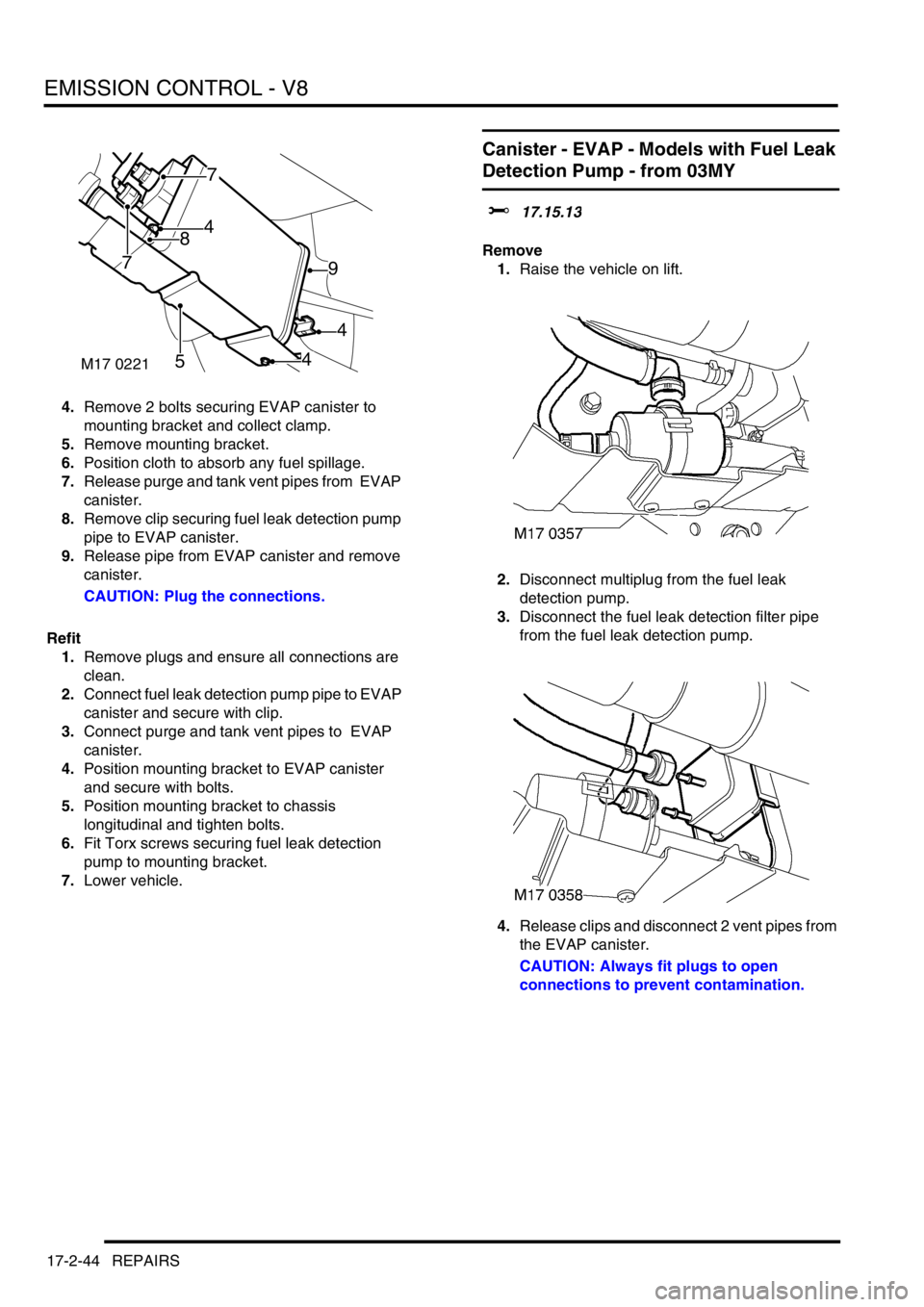
EMISSION CONTROL - V8
17-2-44 REPAIRS
4.Remove 2 bolts securing EVAP canister to
mounting bracket and collect clamp.
5.Remove mounting bracket.
6.Position cloth to absorb any fuel spillage.
7.Release purge and tank vent pipes from EVAP
canister.
8.Remove clip securing fuel leak detection pump
pipe to EVAP canister.
9.Release pipe from EVAP canister and remove
canister.
CAUTION: Plug the connections.
Refit
1.Remove plugs and ensure all connections are
clean.
2.Connect fuel leak detection pump pipe to EVAP
canister and secure with clip.
3.Connect purge and tank vent pipes to EVAP
canister.
4.Position mounting bracket to EVAP canister
and secure with bolts.
5.Position mounting bracket to chassis
longitudinal and tighten bolts.
6.Fit Torx screws securing fuel leak detection
pump to mounting bracket.
7.Lower vehicle.
Canister - EVAP - Models with Fuel Leak
Detection Pump - from 03MY
$% 17.15.13
Remove
1.Raise the vehicle on lift.
2.Disconnect multiplug from the fuel leak
detection pump.
3.Disconnect the fuel leak detection filter pipe
from the fuel leak detection pump.
4.Release clips and disconnect 2 vent pipes from
the EVAP canister.
CAUTION: Always fit plugs to open
connections to prevent contamination.
M17 0221
4
4
4
9
7
7
5
8
Page 382 of 1672
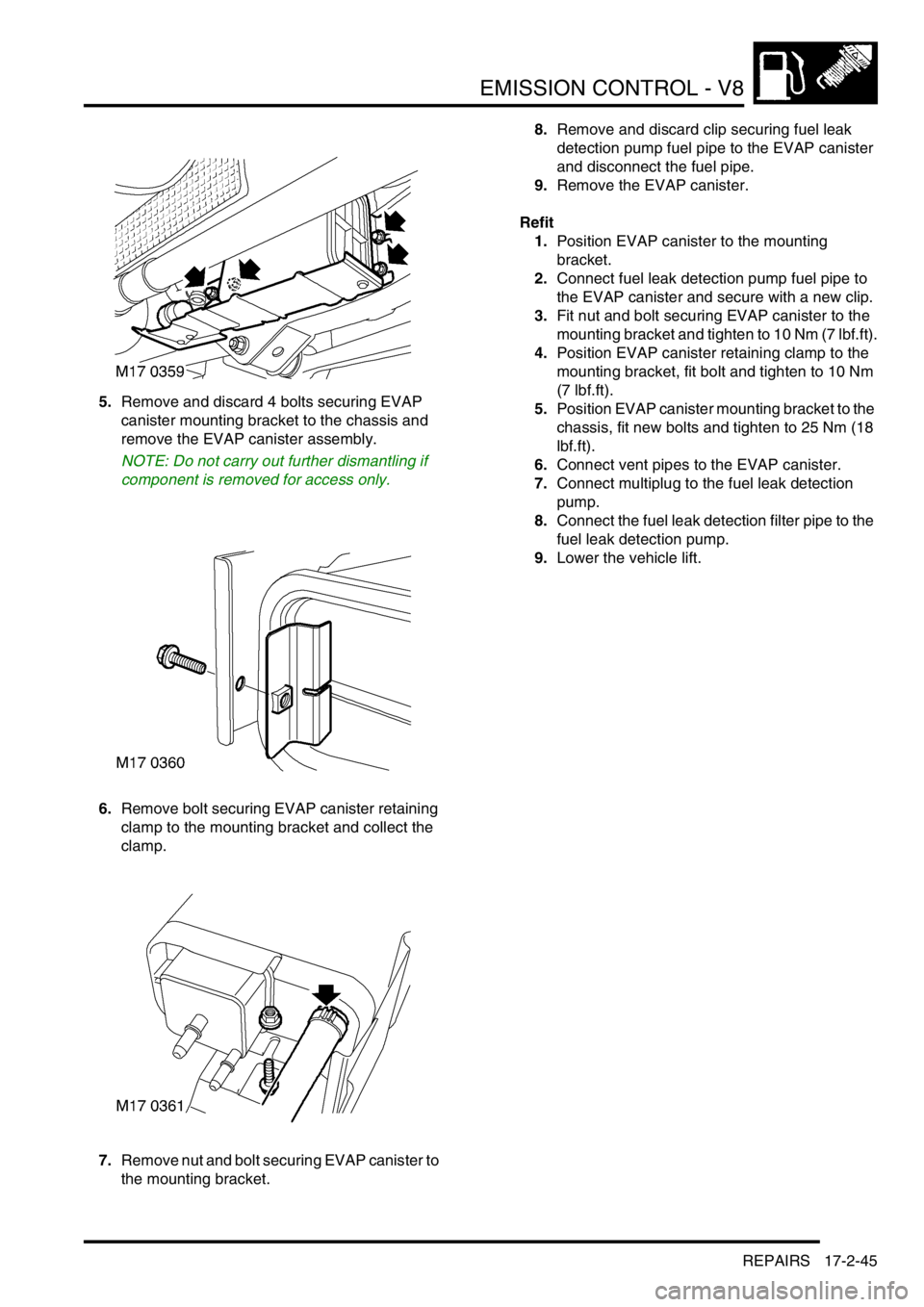
EMISSION CONTROL - V8
REPAIRS 17-2-45
5.Remove and discard 4 bolts securing EVAP
canister mounting bracket to the chassis and
remove the EVAP canister assembly.
NOTE: Do not carry out further dismantling if
component is removed for access only.
6.Remove bolt securing EVAP canister retaining
clamp to the mounting bracket and collect the
clamp.
7.Remove nut and bolt securing EVAP canister to
the mounting bracket.8.Remove and discard clip securing fuel leak
detection pump fuel pipe to the EVAP canister
and disconnect the fuel pipe.
9.Remove the EVAP canister.
Refit
1.Position EVAP canister to the mounting
bracket.
2.Connect fuel leak detection pump fuel pipe to
the EVAP canister and secure with a new clip.
3.Fit nut and bolt securing EVAP canister to the
mounting bracket and tighten to 10 Nm (7 lbf.ft).
4.Position EVAP canister retaining clamp to the
mounting bracket, fit bolt and tighten to 10 Nm
(7 lbf.ft).
5.Position EVAP canister mounting bracket to the
chassis, fit new bolts and tighten to 25 Nm (18
lbf.ft).
6.Connect vent pipes to the EVAP canister.
7.Connect multiplug to the fuel leak detection
pump.
8.Connect the fuel leak detection filter pipe to the
fuel leak detection pump.
9.Lower the vehicle lift.
Page 383 of 1672
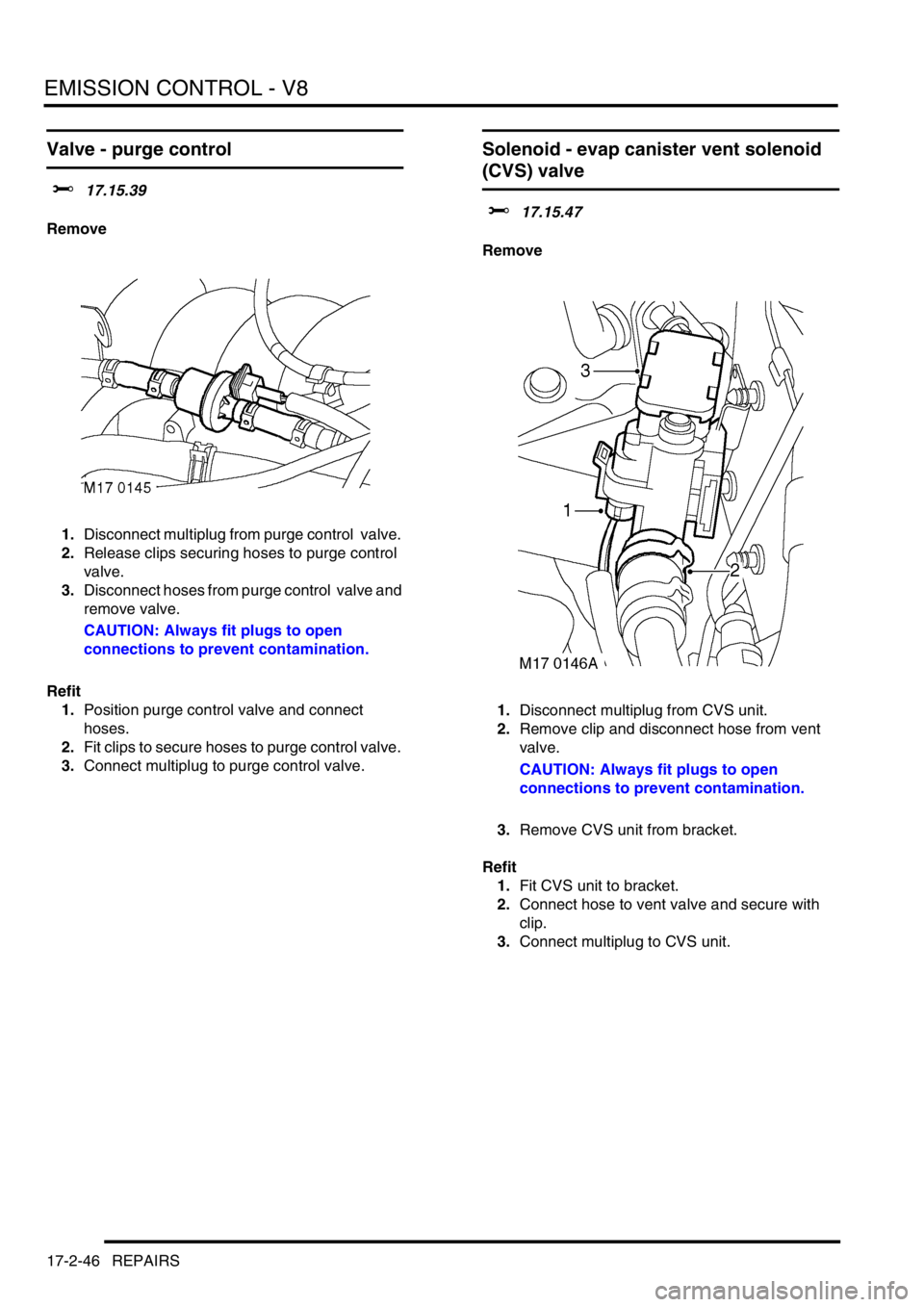
EMISSION CONTROL - V8
17-2-46 REPAIRS
Valve - purge control
$% 17.15.39
Remove
1.Disconnect multiplug from purge control valve.
2.Release clips securing hoses to purge control
valve.
3.Disconnect hoses from purge control valve and
remove valve.
CAUTION: Always fit plugs to open
connections to prevent contamination.
Refit
1.Position purge control valve and connect
hoses.
2.Fit clips to secure hoses to purge control valve.
3.Connect multiplug to purge control valve.
Solenoid - evap canister vent solenoid
(CVS) valve
$% 17.15.47
Remove
1.Disconnect multiplug from CVS unit.
2.Remove clip and disconnect hose from vent
valve.
CAUTION: Always fit plugs to open
connections to prevent contamination.
3.Remove CVS unit from bracket.
Refit
1.Fit CVS unit to bracket.
2.Connect hose to vent valve and secure with
clip.
3.Connect multiplug to CVS unit.
Page 384 of 1672
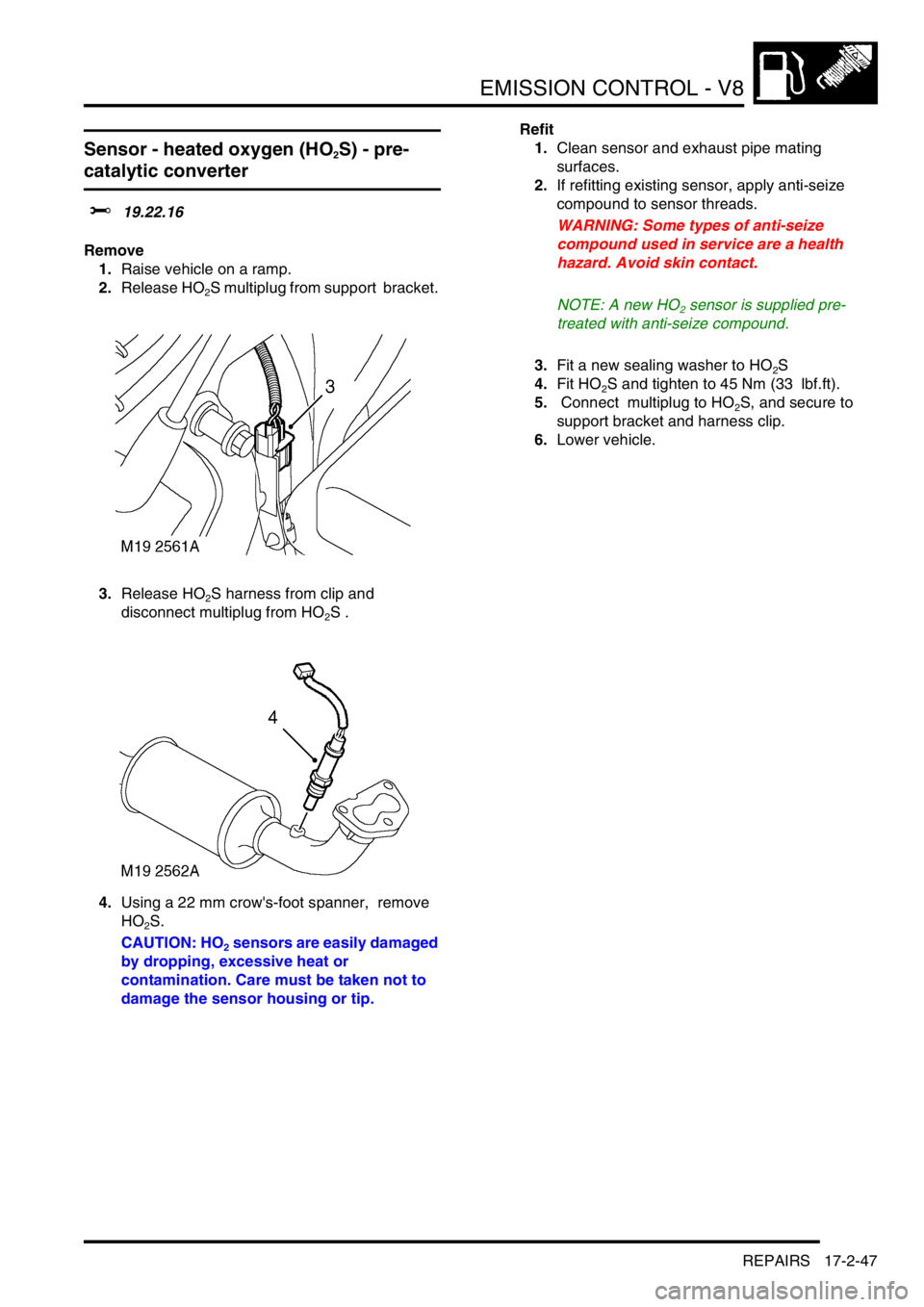
EMISSION CONTROL - V8
REPAIRS 17-2-47
Sensor - heated oxygen (HO2S) - pre-
catalytic converter
$% 19.22.16
Remove
1.Raise vehicle on a ramp.
2.Release HO
2S multiplug from support bracket.
3.Release HO
2S harness from clip and
disconnect multiplug from HO
2S .
4.Using a 22 mm crow's-foot spanner, remove
HO
2S.
CAUTION: HO
2 sensors are easily damaged
by dropping, excessive heat or
contamination. Care must be taken not to
damage the sensor housing or tip.Refit
1.Clean sensor and exhaust pipe mating
surfaces.
2.If refitting existing sensor, apply anti-seize
compound to sensor threads.
WARNING: Some types of anti-seize
compound used in service are a health
hazard. Avoid skin contact.
NOTE: A new HO
2 sensor is supplied pre-
treated with anti-seize compound.
3.Fit a new sealing washer to HO
2S
4.Fit HO
2S and tighten to 45 Nm (33 lbf.ft).
5. Connect multiplug to HO
2S, and secure to
support bracket and harness clip.
6.Lower vehicle.