gearbox LAND ROVER DISCOVERY 2002 Workshop Manual
[x] Cancel search | Manufacturer: LAND ROVER, Model Year: 2002, Model line: DISCOVERY, Model: LAND ROVER DISCOVERY 2002Pages: 1672, PDF Size: 46.1 MB
Page 850 of 1672
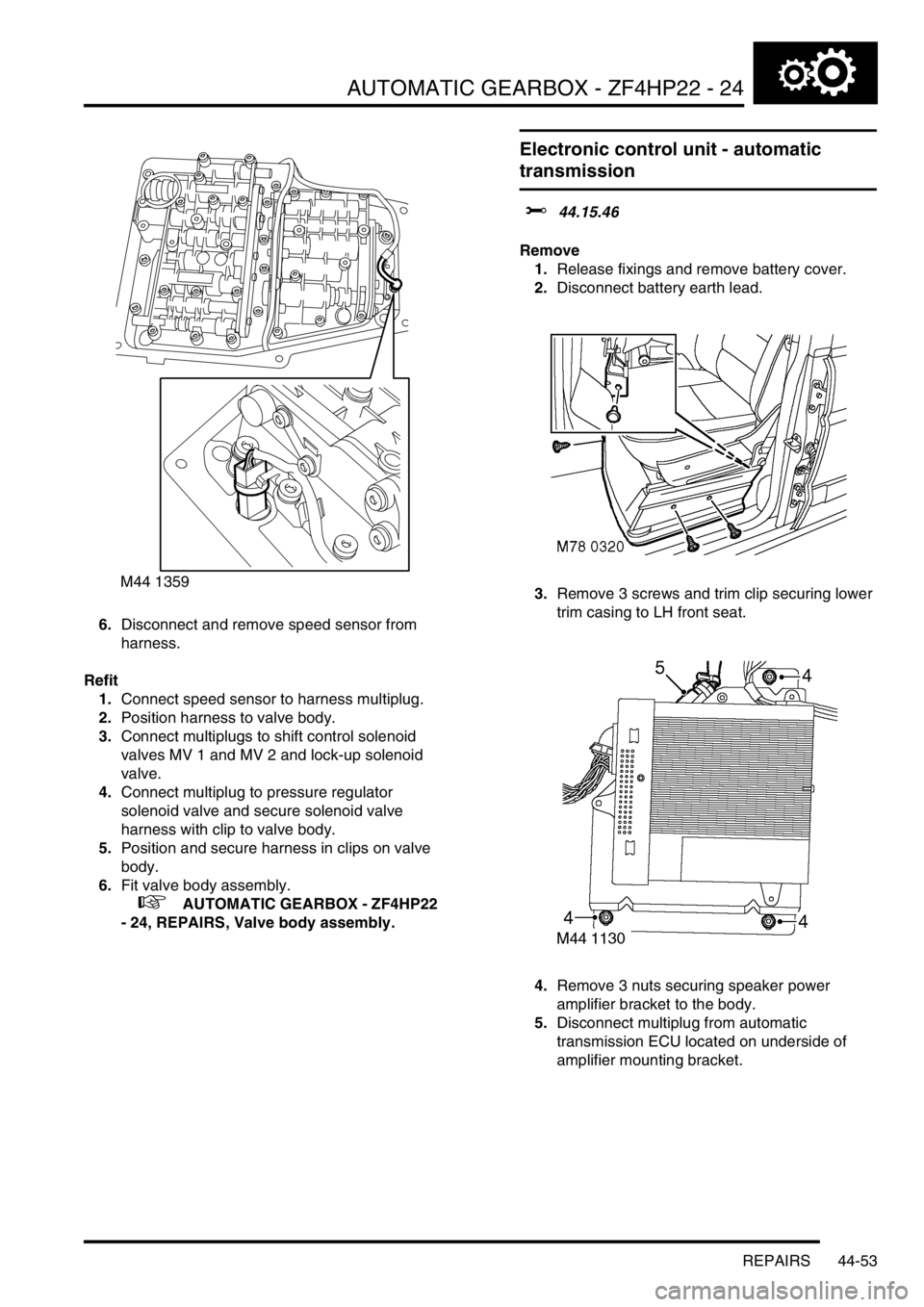
AUTOMATIC GEARBOX - ZF4HP22 - 24
REPAIRS 44-53
6.Disconnect and remove speed sensor from
harness.
Refit
1.Connect speed sensor to harness multiplug.
2.Position harness to valve body.
3.Connect multiplugs to shift control solenoid
valves MV 1 and MV 2 and lock-up solenoid
valve.
4.Connect multiplug to pressure regulator
solenoid valve and secure solenoid valve
harness with clip to valve body.
5.Position and secure harness in clips on valve
body.
6.Fit valve body assembly.
+ AUTOMATIC GEARBOX - ZF4HP22
- 24, REPAIRS, Valve body assembly.
Electronic control unit - automatic
transmission
$% 44.15.46
Remove
1.Release fixings and remove battery cover.
2.Disconnect battery earth lead.
3.Remove 3 screws and trim clip securing lower
trim casing to LH front seat.
4.Remove 3 nuts securing speaker power
amplifier bracket to the body.
5.Disconnect multiplug from automatic
transmission ECU located on underside of
amplifier mounting bracket.
M44 1359
Page 851 of 1672
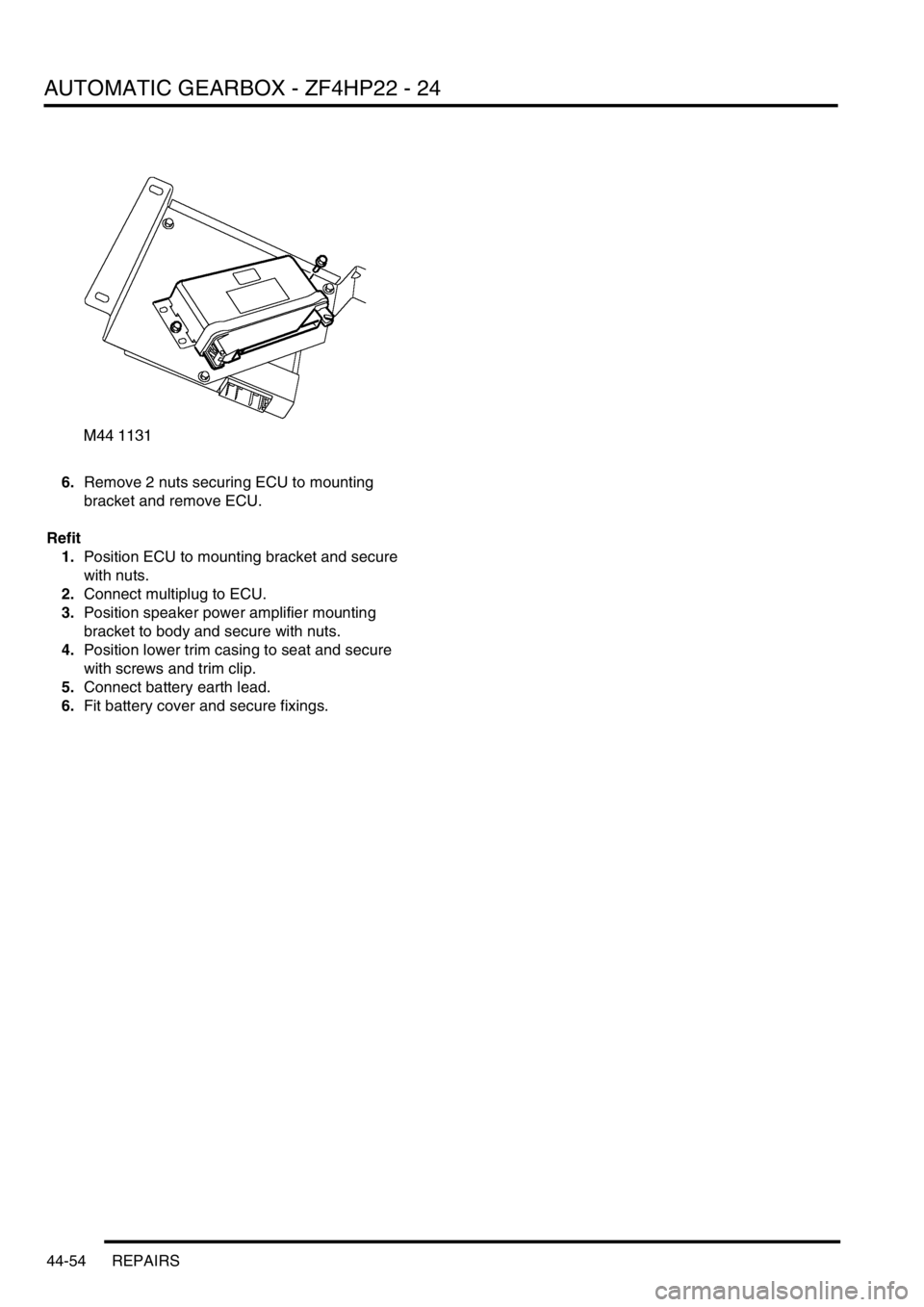
AUTOMATIC GEARBOX - ZF4HP22 - 24
44-54 REPAIRS
6.Remove 2 nuts securing ECU to mounting
bracket and remove ECU.
Refit
1.Position ECU to mounting bracket and secure
with nuts.
2.Connect multiplug to ECU.
3.Position speaker power amplifier mounting
bracket to body and secure with nuts.
4.Position lower trim casing to seat and secure
with screws and trim clip.
5.Connect battery earth lead.
6.Fit battery cover and secure fixings.
Page 856 of 1672
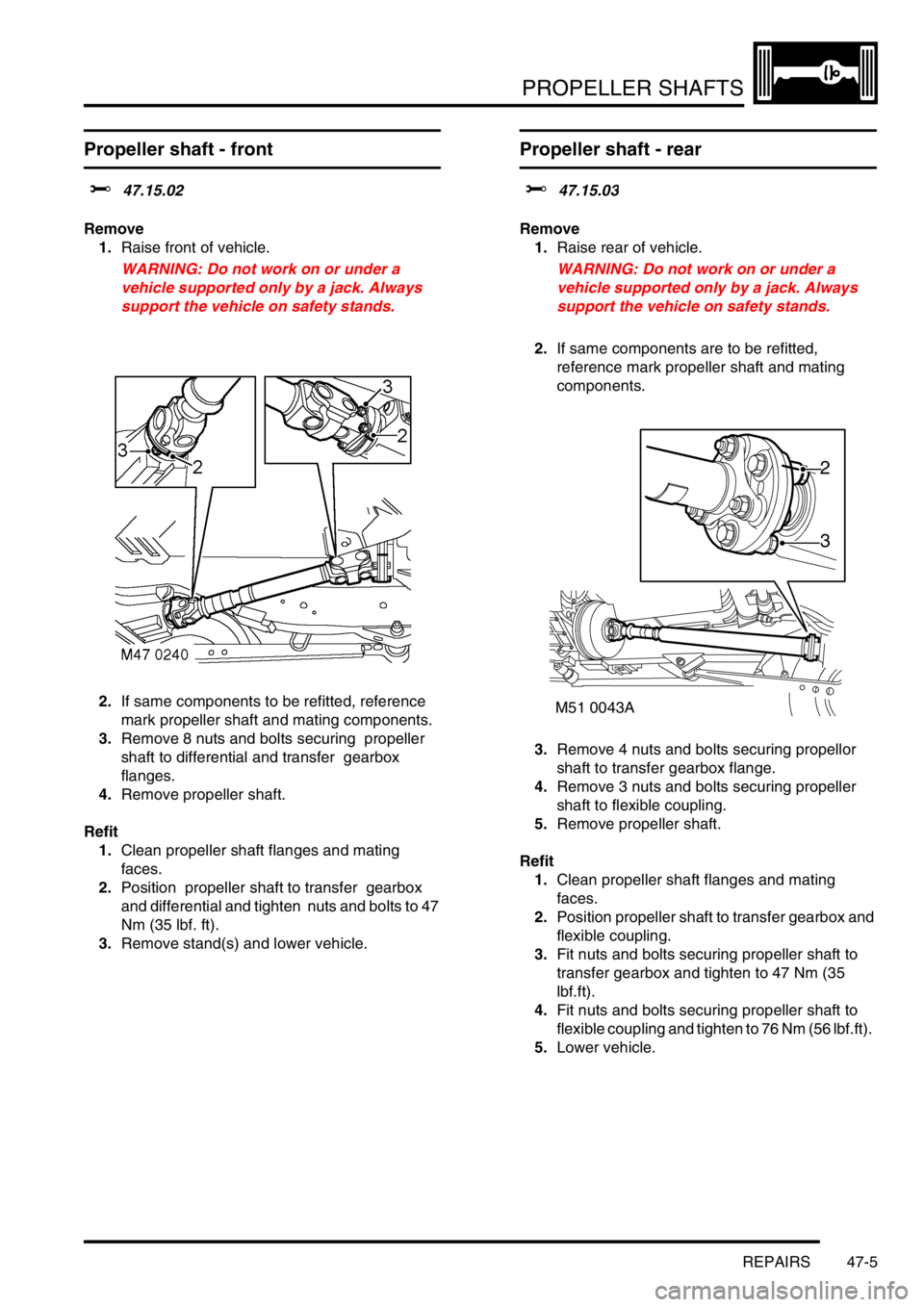
PROPELLER SHAFTS
REPAIRS 47-5
REPAIRS
Propeller shaft - front
$% 47.15.02
Remove
1.Raise front of vehicle.
WARNING: Do not work on or under a
vehicle supported only by a jack. Always
support the vehicle on safety stands.
2.If same components to be refitted, reference
mark propeller shaft and mating components.
3.Remove 8 nuts and bolts securing propeller
shaft to differential and transfer gearbox
flanges.
4.Remove propeller shaft.
Refit
1.Clean propeller shaft flanges and mating
faces.
2.Position propeller shaft to transfer gearbox
and differential and tighten nuts and bolts to 47
Nm (35 lbf. ft).
3.Remove stand(s) and lower vehicle.
Propeller shaft - rear
$% 47.15.03
Remove
1.Raise rear of vehicle.
WARNING: Do not work on or under a
vehicle supported only by a jack. Always
support the vehicle on safety stands.
2.If same components are to be refitted,
reference mark propeller shaft and mating
components.
3.Remove 4 nuts and bolts securing propellor
shaft to transfer gearbox flange.
4.Remove 3 nuts and bolts securing propeller
shaft to flexible coupling.
5.Remove propeller shaft.
Refit
1.Clean propeller shaft flanges and mating
faces.
2.Position propeller shaft to transfer gearbox and
flexible coupling.
3.Fit nuts and bolts securing propeller shaft to
transfer gearbox and tighten to 47 Nm (35
lbf.ft).
4.Fit nuts and bolts securing propeller shaft to
flexible coupling and tighten to 76 Nm (56 lbf.ft).
5.Lower vehicle.
M51 0043A
2
3
Page 1048 of 1672
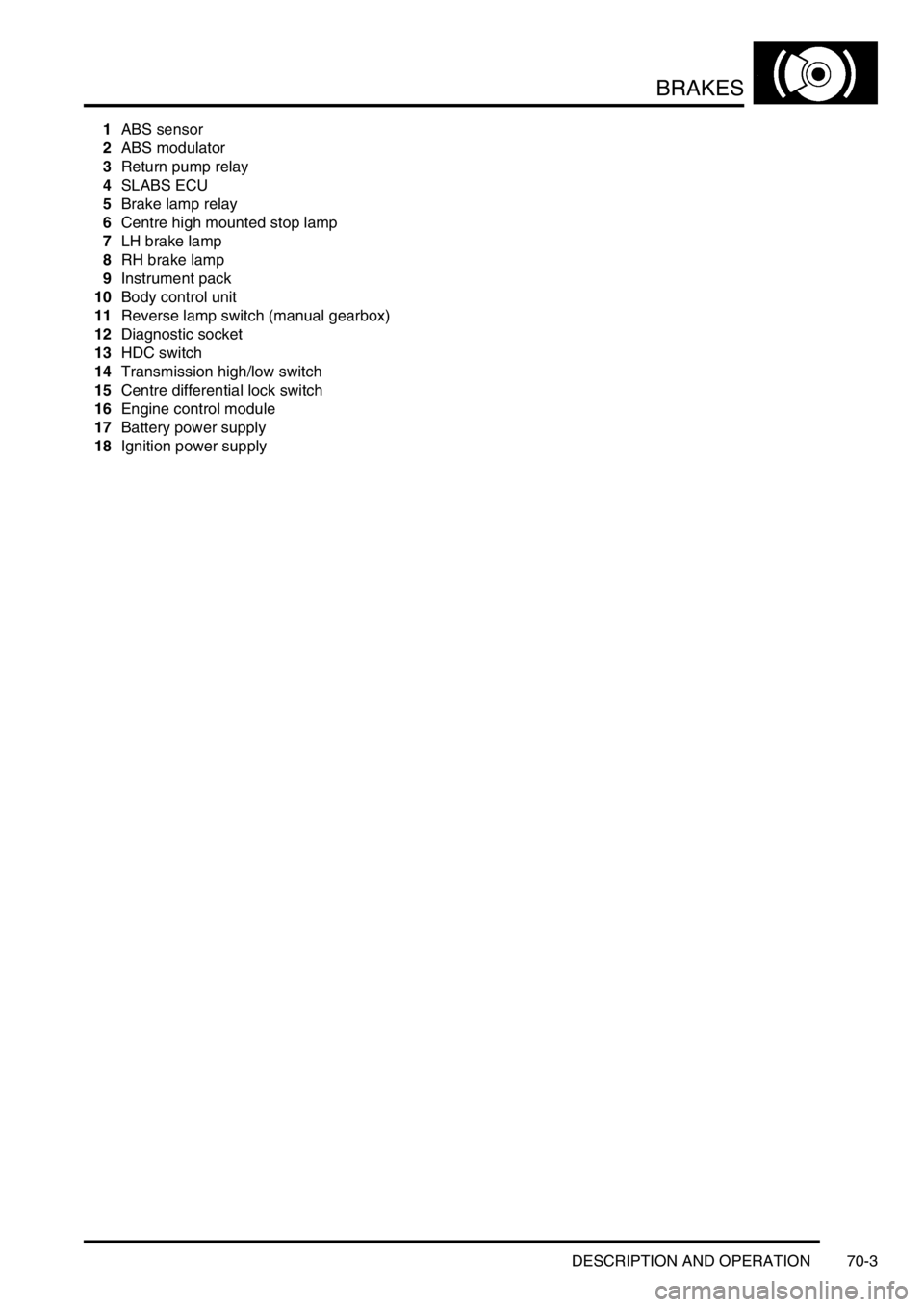
BRAKES
DESCRIPTION AND OPERATION 70-3
1ABS sensor
2ABS modulator
3Return pump relay
4SLABS ECU
5Brake lamp relay
6Centre high mounted stop lamp
7LH brake lamp
8RH brake lamp
9Instrument pack
10Body control unit
11Reverse lamp switch (manual gearbox)
12Diagnostic socket
13HDC switch
14Transmission high/low switch
15Centre differential lock switch
16Engine control module
17Battery power supply
18Ignition power supply
Page 1062 of 1672
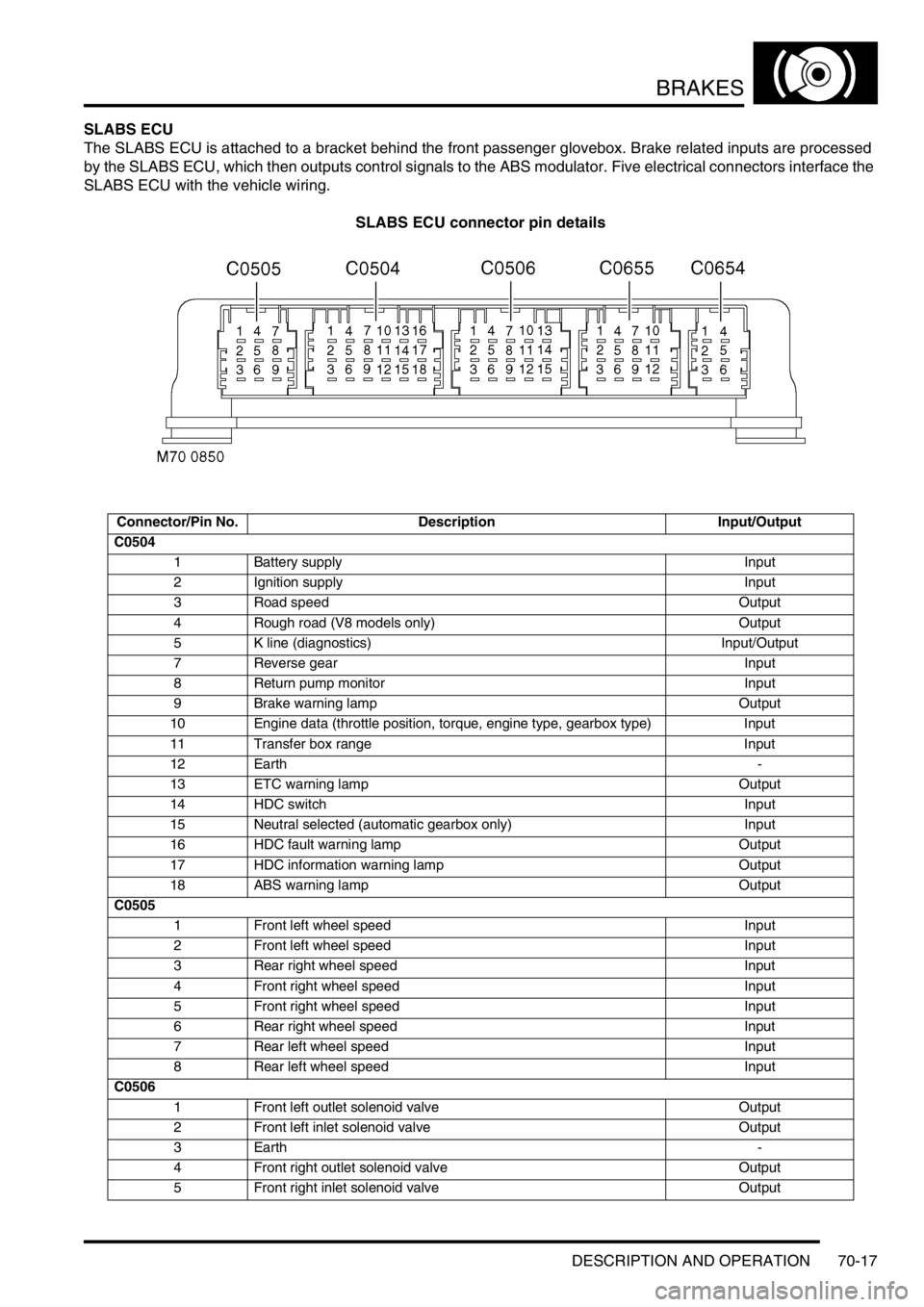
BRAKES
DESCRIPTION AND OPERATION 70-17
SLABS ECU
The SLABS ECU is attached to a bracket behind the front passenger glovebox. Brake related inputs are processed
by the SLABS ECU, which then outputs control signals to the ABS modulator. Five electrical connectors interface the
SLABS ECU with the vehicle wiring.
SLABS ECU connector pin details
Connector/Pin No. Description Input/Output
C0504
1 Battery supply Input
2 Ignition supply Input
3 Road speed Output
4 Rough road (V8 models only) Output
5 K line (diagnostics) Input/Output
7 Reverse gear Input
8 Return pump monitor Input
9 Brake warning lamp Output
10 Engine data (throttle position, torque, engine type, gearbox type) Input
11 Transfer box range Input
12 Earth-
13 ETC warning lamp Output
14 HDC switch Input
15 Neutral selected (automatic gearbox only) Input
16 HDC fault warning lamp Output
17 HDC information warning lamp Output
18 ABS warning lamp Output
C0505
1 Front left wheel speed Input
2 Front left wheel speed Input
3 Rear right wheel speed Input
4 Front right wheel speed Input
5 Front right wheel speed Input
6 Rear right wheel speed Input
7 Rear left wheel speed Input
8 Rear left wheel speed Input
C0506
1 Front left outlet solenoid valve Output
2 Front left inlet solenoid valve Output
3Earth-
4 Front right outlet solenoid valve Output
5 Front right inlet solenoid valve Output
Page 1063 of 1672
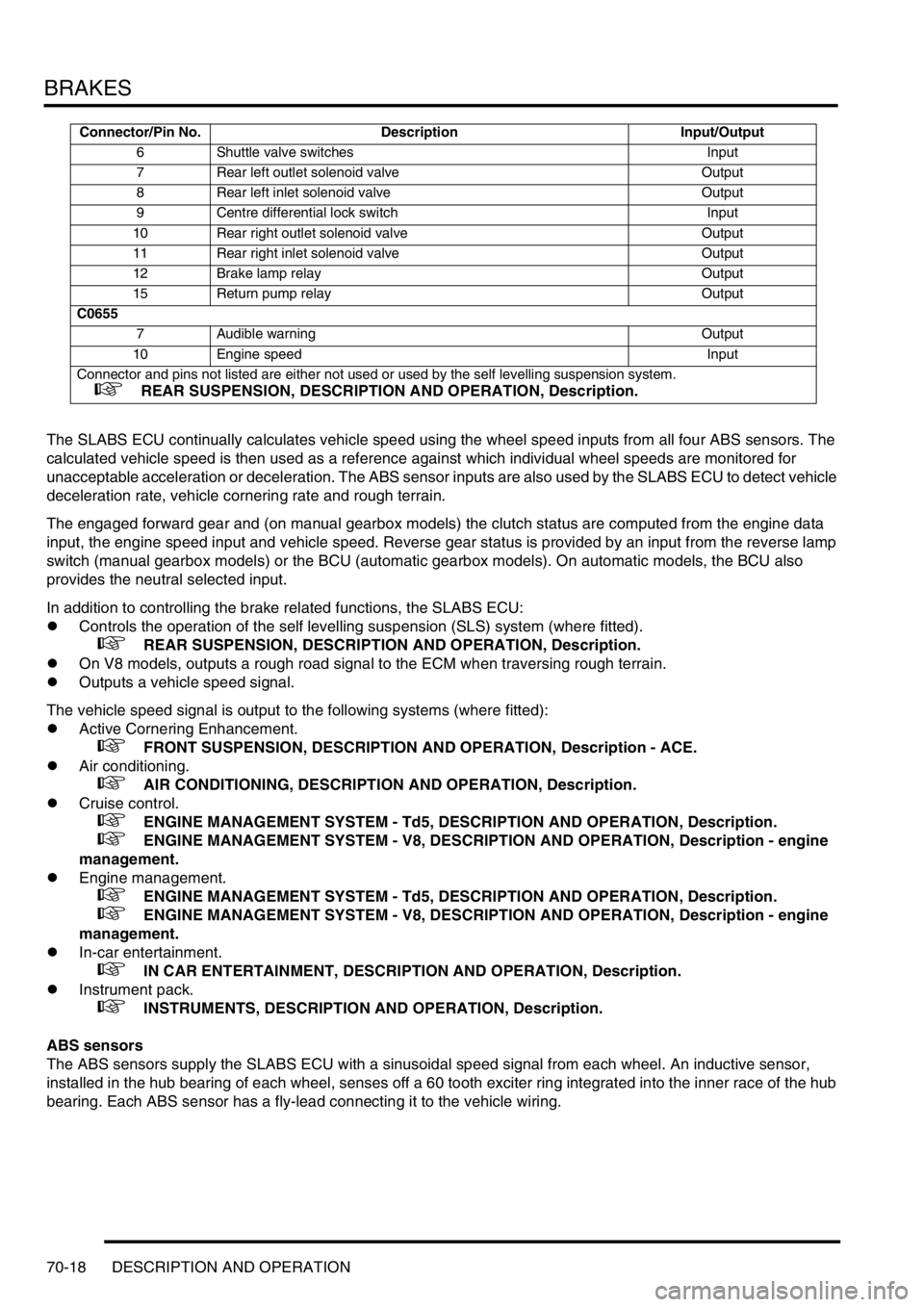
BRAKES
70-18 DESCRIPTION AND OPERATION
The SLABS ECU continually calculates vehicle speed using the wheel speed inputs from all four ABS sensors. The
calculated vehicle speed is then used as a reference against which individual wheel speeds are monitored for
unacceptable acceleration or deceleration. The ABS sensor inputs are also used by the SLABS ECU to detect vehicle
deceleration rate, vehicle cornering rate and rough terrain.
The engaged forward gear and (on manual gearbox models) the clutch status are computed from the engine data
input, the engine speed input and vehicle speed. Reverse gear status is provided by an input from the reverse lamp
switch (manual gearbox models) or the BCU (automatic gearbox models). On automatic models, the BCU also
provides the neutral selected input.
In addition to controlling the brake related functions, the SLABS ECU:
lControls the operation of the self levelling suspension (SLS) system (where fitted).
+ REAR SUSPENSION, DESCRIPTION AND OPERATION, Description.
lOn V8 models, outputs a rough road signal to the ECM when traversing rough terrain.
lOutputs a vehicle speed signal.
The vehicle speed signal is output to the following systems (where fitted):
lActive Cornering Enhancement.
+ FRONT SUSPENSION, DESCRIPTION AND OPERATION, Description - ACE.
lAir conditioning.
+ AIR CONDITIONING, DESCRIPTION AND OPERATION, Description.
lCruise control.
+ ENGINE MANAGEMENT SYSTEM - Td5, DESCRIPTION AND OPERATION, Description.
+ ENGINE MANAGEMENT SYSTEM - V8, DESCRIPTION AND OPERATION, Description - engine
management.
lEngine management.
+ ENGINE MANAGEMENT SYSTEM - Td5, DESCRIPTION AND OPERATION, Description.
+ ENGINE MANAGEMENT SYSTEM - V8, DESCRIPTION AND OPERATION, Description - engine
management.
lIn-car entertainment.
+ IN CAR ENTERTAINMENT, DESCRIPTION AND OPERATION, Description.
lInstrument pack.
+ INSTRUMENTS, DESCRIPTION AND OPERATION, Description.
ABS sensors
The ABS sensors supply the SLABS ECU with a sinusoidal speed signal from each wheel. An inductive sensor,
installed in the hub bearing of each wheel, senses off a 60 tooth exciter ring integrated into the inner race of the hub
bearing. Each ABS sensor has a fly-lead connecting it to the vehicle wiring.
6 Shuttle valve switches Input
7 Rear left outlet solenoid valve Output
8 Rear left inlet solenoid valve Output
9 Centre differential lock switch Input
10 Rear right outlet solenoid valve Output
11 Rear right inlet solenoid valve Output
12 Brake lamp relay Output
15 Return pump relay Output
C0655
7 Audible warning Output
10 Engine speed Input
Connector and pins not listed are either not used or used by the self levelling suspension system.
+ REAR SUSPENSION, DESCRIPTION AND OPERATION, Description.
Connector/Pin No. Description Input/Output
Page 1066 of 1672
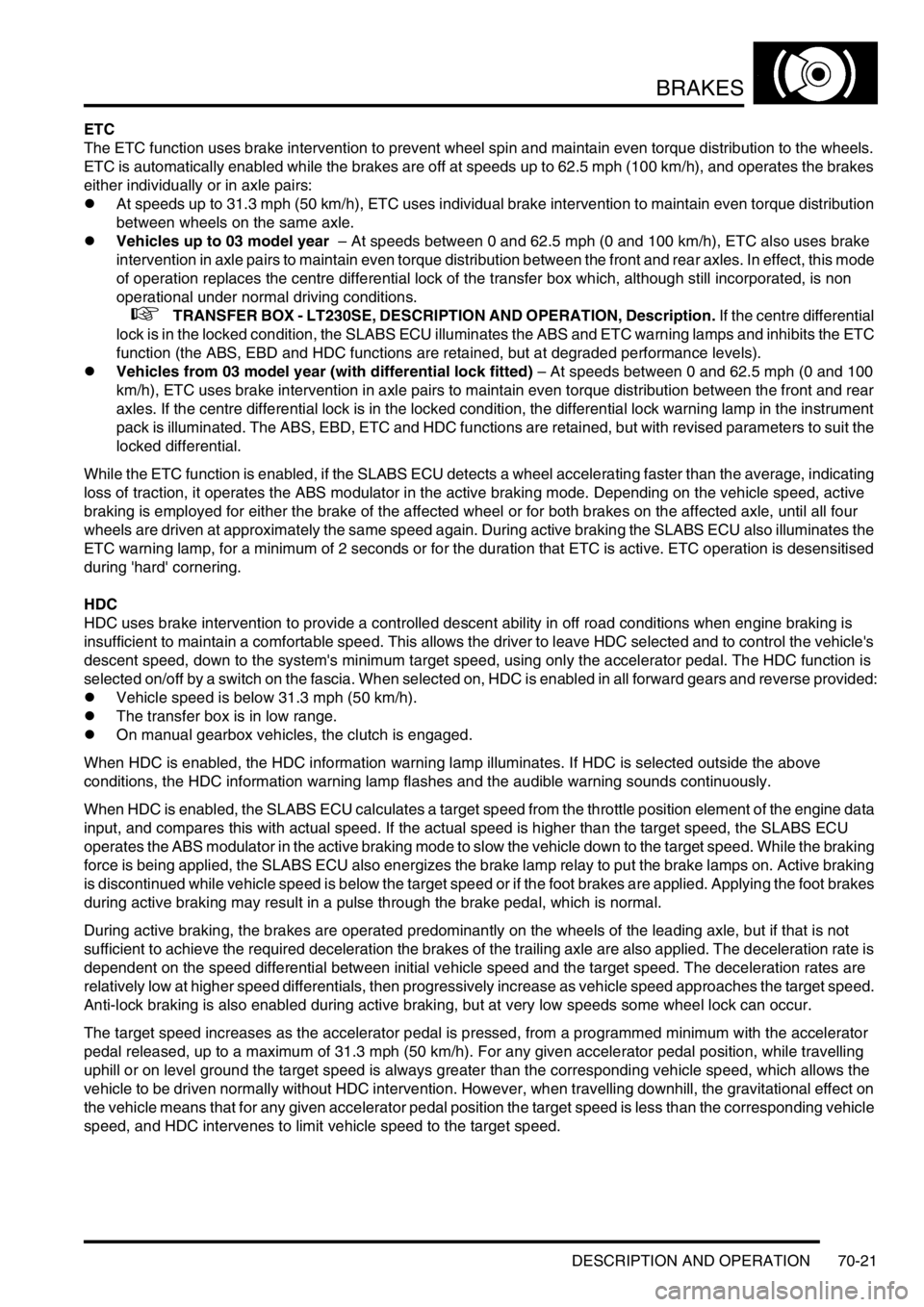
BRAKES
DESCRIPTION AND OPERATION 70-21
ETC
The ETC function uses brake intervention to prevent wheel spin and maintain even torque distribution to the wheels.
ETC is automatically enabled while the brakes are off at speeds up to 62.5 mph (100 km/h), and operates the brakes
either individually or in axle pairs:
lAt speeds up to 31.3 mph (50 km/h), ETC uses individual brake intervention to maintain even torque distribution
between wheels on the same axle.
lVehicles up to 03 model year – At speeds between 0 and 62.5 mph (0 and 100 km/h), ETC also uses brake
intervention in axle pairs to maintain even torque distribution between the front and rear axles. In effect, this mode
of operation replaces the centre differential lock of the transfer box which, although still incorporated, is non
operational under normal driving conditions.
+ TRANSFER BOX - LT230SE, DESCRIPTION AND OPERATION, Description. If the centre differential
lock is in the locked condition, the SLABS ECU illuminates the ABS and ETC warning lamps and inhibits the ETC
function (the ABS, EBD and HDC functions are retained, but at degraded performance levels).
lVehicles from 03 model year (with differential lock fitted) – At speeds between 0 and 62.5 mph (0 and 100
km/h), ETC uses brake intervention in axle pairs to maintain even torque distribution between the front and rear
axles. If the centre differential lock is in the locked condition, the differential lock warning lamp in the instrument
pack is illuminated. The ABS, EBD, ETC and HDC functions are retained, but with revised parameters to suit the
locked differential.
While the ETC function is enabled, if the SLABS ECU detects a wheel accelerating faster than the average, indicating
loss of traction, it operates the ABS modulator in the active braking mode. Depending on the vehicle speed, active
braking is employed for either the brake of the affected wheel or for both brakes on the affected axle, until all four
wheels are driven at approximately the same speed again. During active braking the SLABS ECU also illuminates the
ETC warning lamp, for a minimum of 2 seconds or for the duration that ETC is active. ETC operation is desensitised
during 'hard' cornering.
HDC
HDC uses brake intervention to provide a controlled descent ability in off road conditions when engine braking is
insufficient to maintain a comfortable speed. This allows the driver to leave HDC selected and to control the vehicle's
descent speed, down to the system's minimum target speed, using only the accelerator pedal. The HDC function is
selected on/off by a switch on the fascia. When selected on, HDC is enabled in all forward gears and reverse provided:
lVehicle speed is below 31.3 mph (50 km/h).
lThe transfer box is in low range.
lOn manual gearbox vehicles, the clutch is engaged.
When HDC is enabled, the HDC information warning lamp illuminates. If HDC is selected outside the above
conditions, the HDC information warning lamp flashes and the audible warning sounds continuously.
When HDC is enabled, the SLABS ECU calculates a target speed from the throttle position element of the engine data
input, and compares this with actual speed. If the actual speed is higher than the target speed, the SLABS ECU
operates the ABS modulator in the active braking mode to slow the vehicle down to the target speed. While the braking
force is being applied, the SLABS ECU also energizes the brake lamp relay to put the brake lamps on. Active braking
is discontinued while vehicle speed is below the target speed or if the foot brakes are applied. Applying the foot brakes
during active braking may result in a pulse through the brake pedal, which is normal.
During active braking, the brakes are operated predominantly on the wheels of the leading axle, but if that is not
sufficient to achieve the required deceleration the brakes of the trailing axle are also applied. The deceleration rate is
dependent on the speed differential between initial vehicle speed and the target speed. The deceleration rates are
relatively low at higher speed differentials, then progressively increase as vehicle speed approaches the target speed.
Anti-lock braking is also enabled during active braking, but at very low speeds some wheel lock can occur.
The target speed increases as the accelerator pedal is pressed, from a programmed minimum with the accelerator
pedal released, up to a maximum of 31.3 mph (50 km/h). For any given accelerator pedal position, while travelling
uphill or on level ground the target speed is always greater than the corresponding vehicle speed, which allows the
vehicle to be driven normally without HDC intervention. However, when travelling downhill, the gravitational effect on
the vehicle means that for any given accelerator pedal position the target speed is less than the corresponding vehicle
speed, and HDC intervenes to limit vehicle speed to the target speed.
Page 1067 of 1672
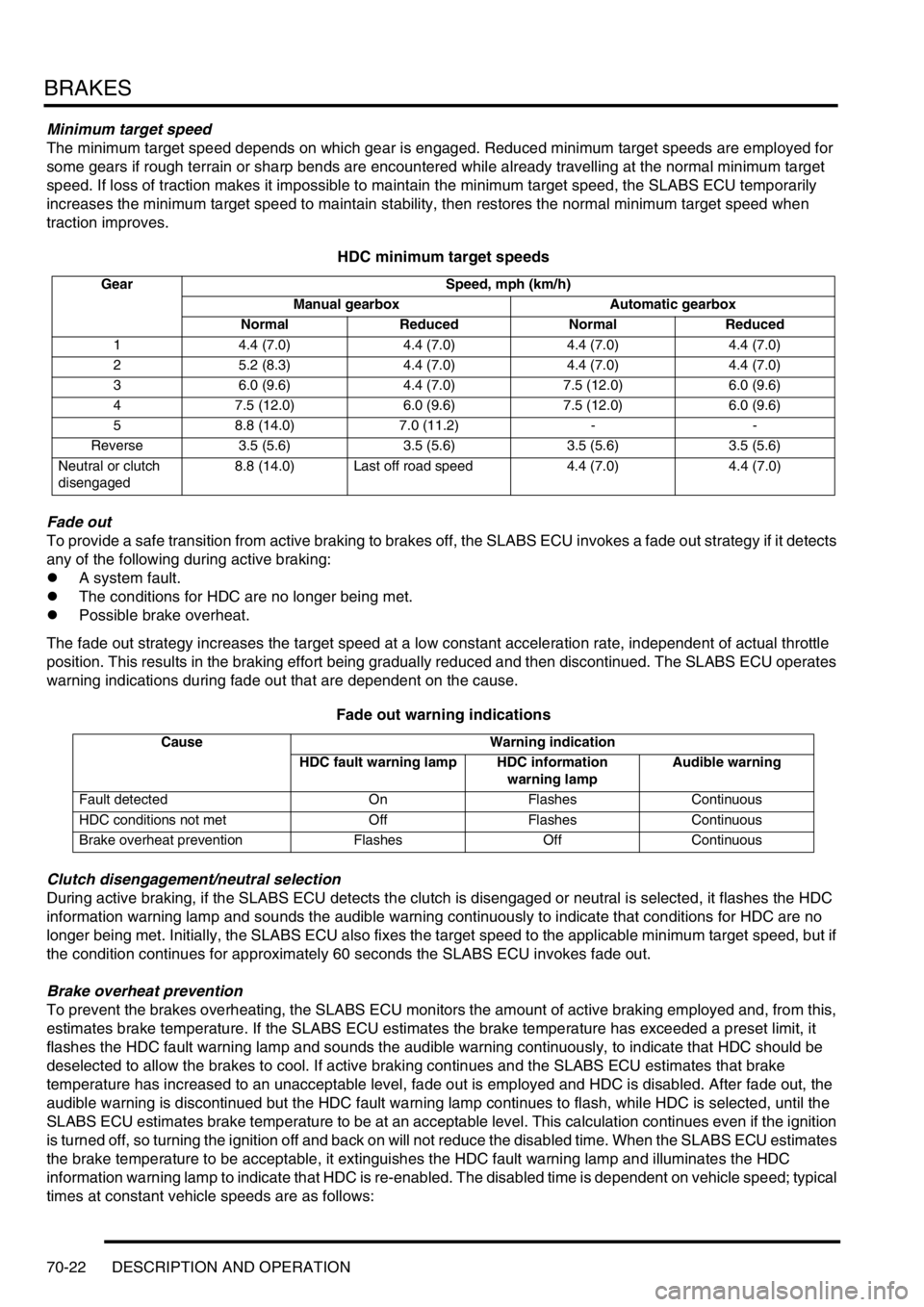
BRAKES
70-22 DESCRIPTION AND OPERATION
Minimum target speed
The minimum target speed depends on which gear is engaged. Reduced minimum target speeds are employed for
some gears if rough terrain or sharp bends are encountered while already travelling at the normal minimum target
speed. If loss of traction makes it impossible to maintain the minimum target speed, the SLABS ECU temporarily
increases the minimum target speed to maintain stability, then restores the normal minimum target speed when
traction improves.
HDC minimum target speeds
Fade out
To provide a safe transition from active braking to brakes off, the SLABS ECU invokes a fade out strategy if it detects
any of the following during active braking:
lA system fault.
lThe conditions for HDC are no longer being met.
lPossible brake overheat.
The fade out strategy increases the target speed at a low constant acceleration rate, independent of actual throttle
position. This results in the braking effort being gradually reduced and then discontinued. The SLABS ECU operates
warning indications during fade out that are dependent on the cause.
Fade out warning indications
Clutch disengagement/neutral selection
During active braking, if the SLABS ECU detects the clutch is disengaged or neutral is selected, it flashes the HDC
information warning lamp and sounds the audible warning continuously to indicate that conditions for HDC are no
longer being met. Initially, the SLABS ECU also fixes the target speed to the applicable minimum target speed, but if
the condition continues for approximately 60 seconds the SLABS ECU invokes fade out.
Brake overheat prevention
To prevent the brakes overheating, the SLABS ECU monitors the amount of active braking employed and, from this,
estimates brake temperature. If the SLABS ECU estimates the brake temperature has exceeded a preset limit, it
flashes the HDC fault warning lamp and sounds the audible warning continuously, to indicate that HDC should be
deselected to allow the brakes to cool. If active braking continues and the SLABS ECU estimates that brake
temperature has increased to an unacceptable level, fade out is employed and HDC is disabled. After fade out, the
audible warning is discontinued but the HDC fault warning lamp continues to flash, while HDC is selected, until the
SLABS ECU estimates brake temperature to be at an acceptable level. This calculation continues even if the ignition
is turned off, so turning the ignition off and back on will not reduce the disabled time. When the SLABS ECU estimates
the brake temperature to be acceptable, it extinguishes the HDC fault warning lamp and illuminates the HDC
information warning lamp to indicate that HDC is re-enabled. The disabled time is dependent on vehicle speed; typical
times at constant vehicle speeds are as follows:
Gear Speed, mph (km/h)
Manual gearbox Automatic gearbox
Normal Reduced Normal Reduced
1 4.4 (7.0) 4.4 (7.0) 4.4 (7.0) 4.4 (7.0)
2 5.2 (8.3) 4.4 (7.0) 4.4 (7.0) 4.4 (7.0)
3 6.0 (9.6) 4.4 (7.0) 7.5 (12.0) 6.0 (9.6)
4 7.5 (12.0) 6.0 (9.6) 7.5 (12.0) 6.0 (9.6)
5 8.8 (14.0) 7.0 (11.2) - -
Reverse 3.5 (5.6) 3.5 (5.6) 3.5 (5.6) 3.5 (5.6)
Neutral or clutch
disengaged8.8 (14.0) Last off road speed 4.4 (7.0) 4.4 (7.0)
Cause Warning indication
HDC fault warning lamp HDC information
warning lampAudible warning
Fault detected On Flashes Continuous
HDC conditions not met Off Flashes Continuous
Brake overheat prevention Flashes Off Continuous
Page 1080 of 1672
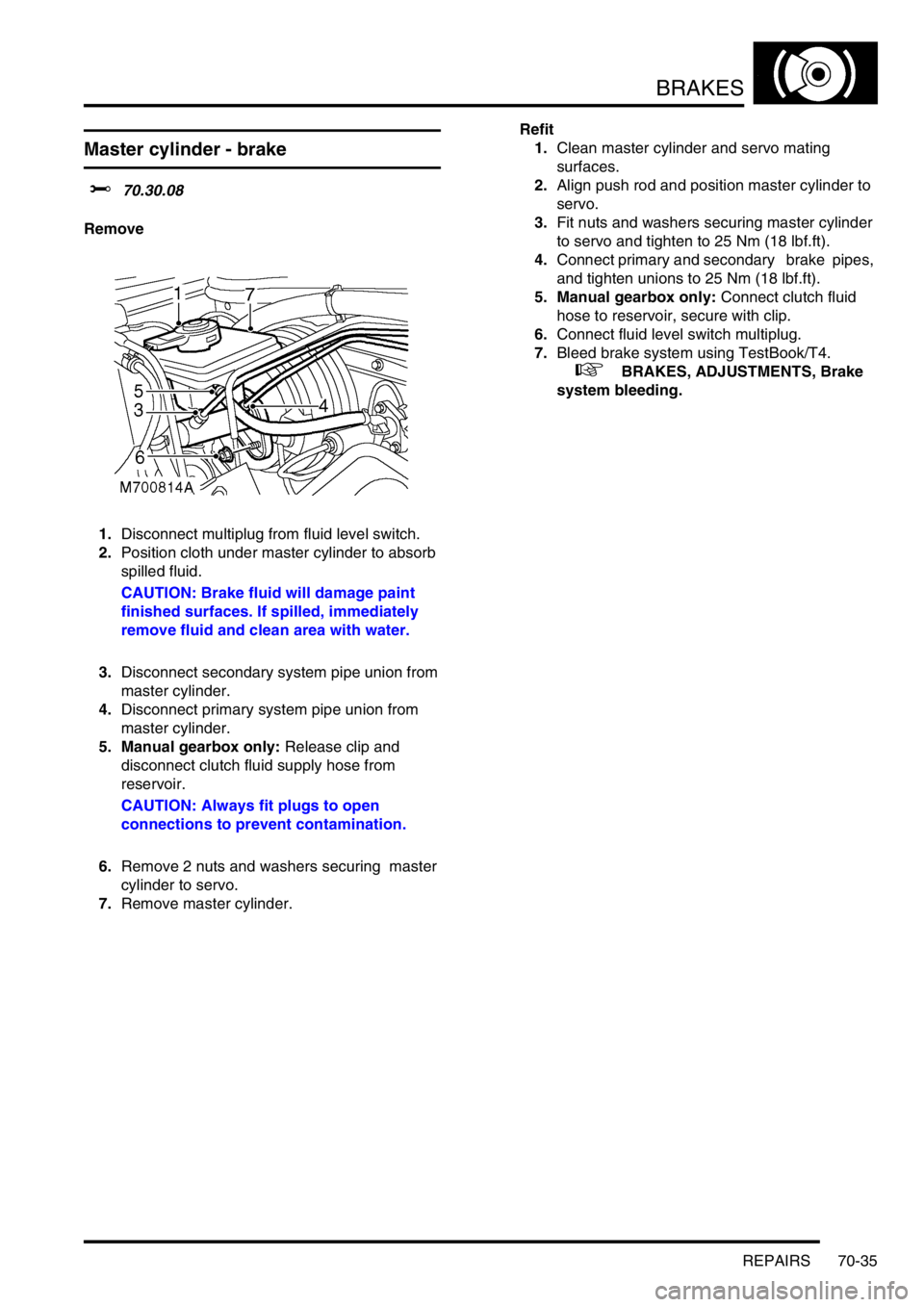
BRAKES
REPAIRS 70-35
Master cylinder - brake
$% 70.30.08
Remove
1.Disconnect multiplug from fluid level switch.
2.Position cloth under master cylinder to absorb
spilled fluid.
CAUTION: Brake fluid will damage paint
finished surfaces. If spilled, immediately
remove fluid and clean area with water.
3.Disconnect secondary system pipe union from
master cylinder.
4.Disconnect primary system pipe union from
master cylinder.
5. Manual gearbox only: Release clip and
disconnect clutch fluid supply hose from
reservoir.
CAUTION: Always fit plugs to open
connections to prevent contamination.
6.Remove 2 nuts and washers securing master
cylinder to servo.
7.Remove master cylinder. Refit
1.Clean master cylinder and servo mating
surfaces.
2.Align push rod and position master cylinder to
servo.
3.Fit nuts and washers securing master cylinder
to servo and tighten to 25 Nm (18 lbf.ft).
4.Connect primary and secondary brake pipes,
and tighten unions to 25 Nm (18 lbf.ft).
5. Manual gearbox only: Connect clutch fluid
hose to reservoir, secure with clip.
6.Connect fluid level switch multiplug.
7.Bleed brake system using TestBook/T4.
+ BRAKES, ADJUSTMENTS, Brake
system bleeding.
Page 1115 of 1672
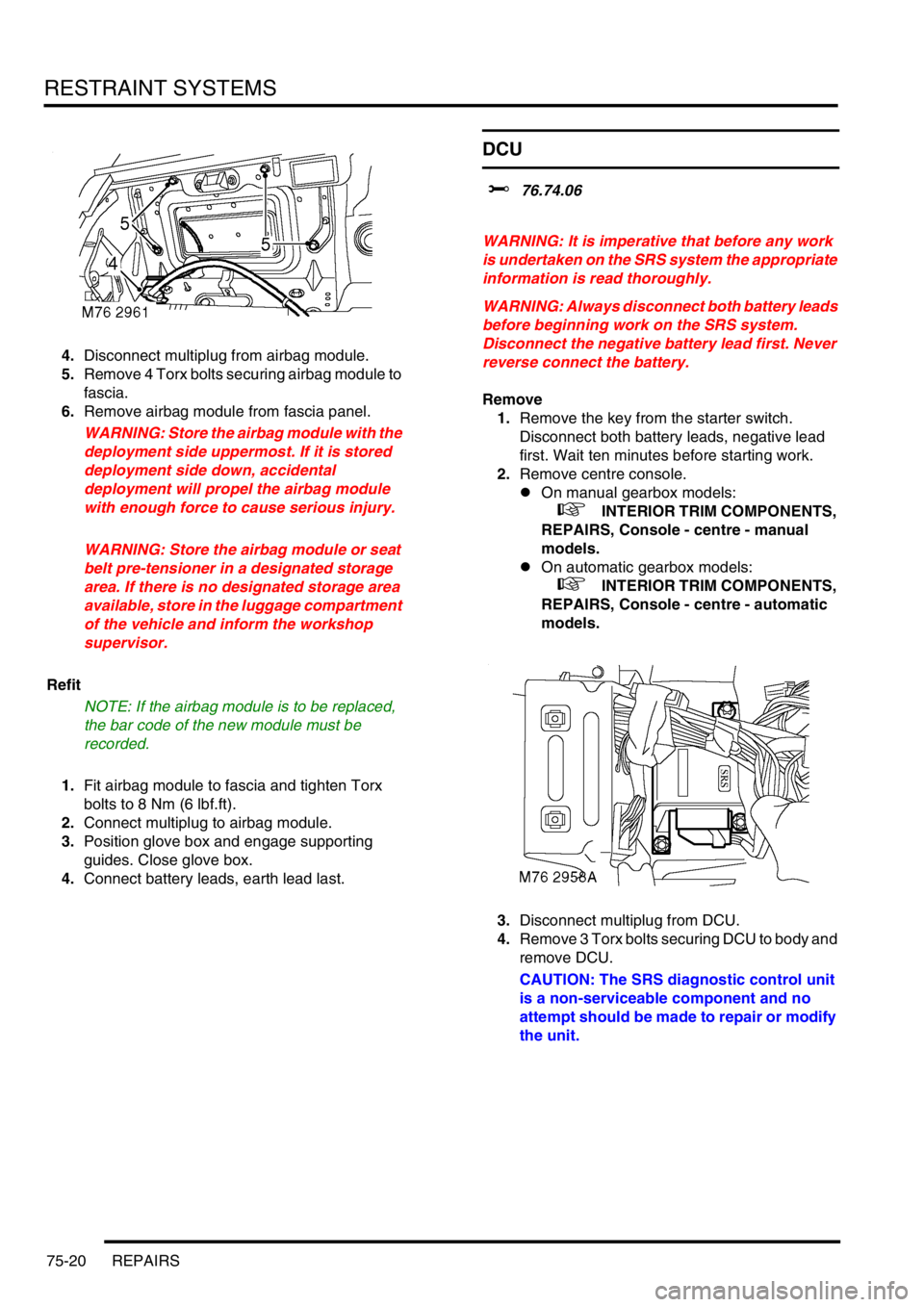
RESTRAINT SYSTEMS
75-20 REPAIRS
4.Disconnect multiplug from airbag module.
5.Remove 4 Torx bolts securing airbag module to
fascia.
6.Remove airbag module from fascia panel.
WARNING: Store the airbag module with the
deployment side uppermost. If it is stored
deployment side down, accidental
deployment will propel the airbag module
with enough force to cause serious injury.
WARNING: Store the airbag module or seat
belt pre-tensioner in a designated storage
area. If there is no designated storage area
available, store in the luggage compartment
of the vehicle and inform the workshop
supervisor.
Refit
NOTE: If the airbag module is to be replaced,
the bar code of the new module must be
recorded.
1.Fit airbag module to fascia and tighten Torx
bolts to 8 Nm (6 lbf.ft).
2.Connect multiplug to airbag module.
3.Position glove box and engage supporting
guides. Close glove box.
4.Connect battery leads, earth lead last.
DCU
$% 76.74.06
WARNING: It is imperative that before any work
is undertaken on the SRS system the appropriate
information is read thoroughly.
WARNING: Always disconnect both battery leads
before beginning work on the SRS system.
Disconnect the negative battery lead first. Never
reverse connect the battery.
Remove
1.Remove the key from the starter switch.
Disconnect both battery leads, negative lead
first. Wait ten minutes before starting work.
2.Remove centre console.
lOn manual gearbox models:
+ INTERIOR TRIM COMPONENTS,
REPAIRS, Console - centre - manual
models.
lOn automatic gearbox models:
+ INTERIOR TRIM COMPONENTS,
REPAIRS, Console - centre - automatic
models.
3.Disconnect multiplug from DCU.
4.Remove 3 Torx bolts securing DCU to body and
remove DCU.
CAUTION: The SRS diagnostic control unit
is a non-serviceable component and no
attempt should be made to repair or modify
the unit.