LAND ROVER DISCOVERY 2002 Workshop Manual
Manufacturer: LAND ROVER, Model Year: 2002, Model line: DISCOVERY, Model: LAND ROVER DISCOVERY 2002Pages: 1672, PDF Size: 46.1 MB
Page 231 of 1672
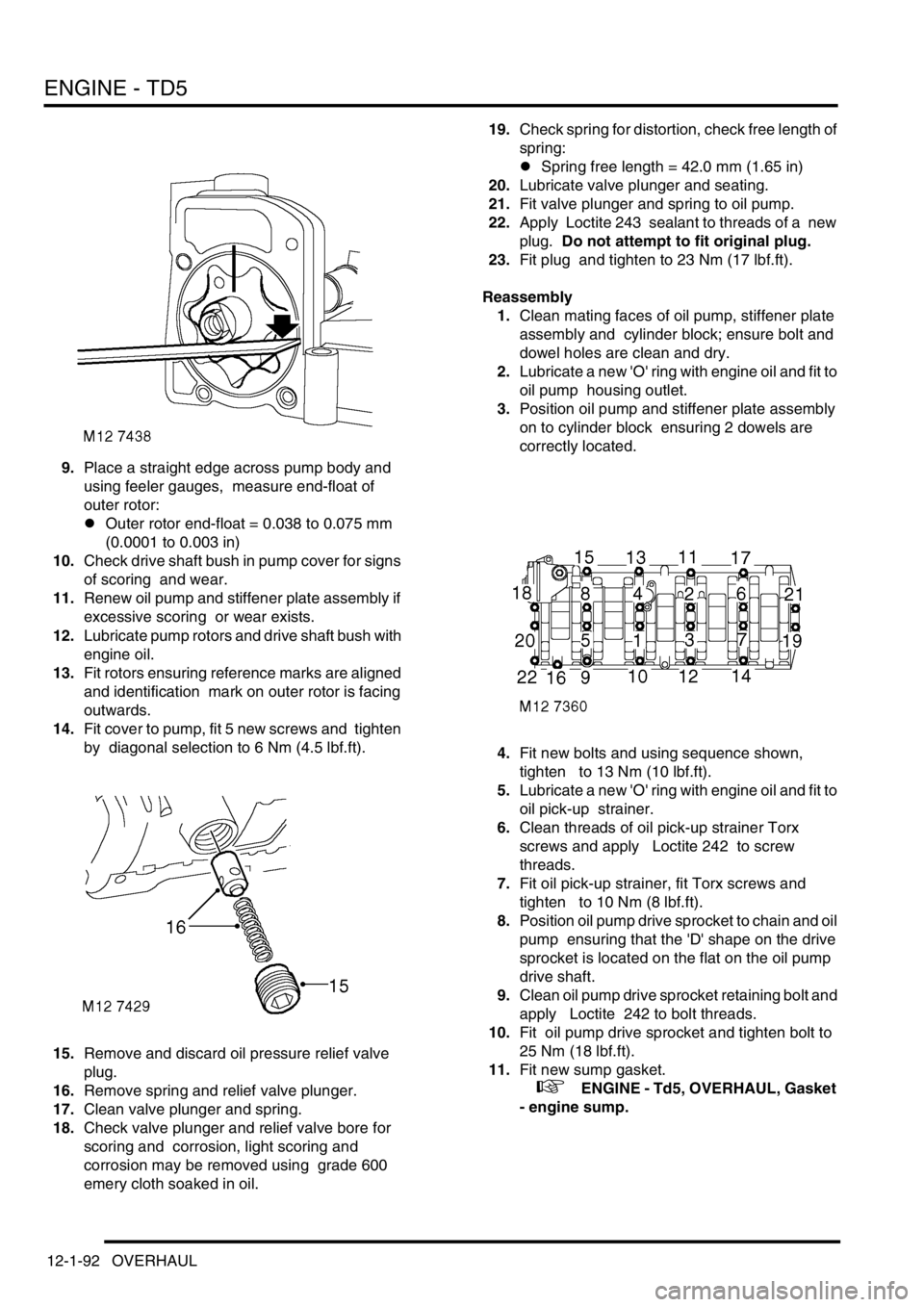
ENGINE - TD5
12-1-92 OVERHAUL
9.Place a straight edge across pump body and
using feeler gauges, measure end-float of
outer rotor:
lOuter rotor end-float = 0.038 to 0.075 mm
(0.0001 to 0.003 in)
10.Check drive shaft bush in pump cover for signs
of scoring and wear.
11.Renew oil pump and stiffener plate assembly if
excessive scoring or wear exists.
12.Lubricate pump rotors and drive shaft bush with
engine oil.
13.Fit rotors ensuring reference marks are aligned
and identification mark on outer rotor is facing
outwards.
14.Fit cover to pump, fit 5 new screws and tighten
by diagonal selection to 6 Nm (4.5 lbf.ft).
15.Remove and discard oil pressure relief valve
plug.
16.Remove spring and relief valve plunger.
17.Clean valve plunger and spring.
18.Check valve plunger and relief valve bore for
scoring and corrosion, light scoring and
corrosion may be removed using grade 600
emery cloth soaked in oil.19.Check spring for distortion, check free length of
spring:
lSpring free length = 42.0 mm (1.65 in)
20.Lubricate valve plunger and seating.
21.Fit valve plunger and spring to oil pump.
22.Apply Loctite 243 sealant to threads of a new
plug. Do not attempt to fit original plug.
23.Fit plug and tighten to 23 Nm (17 lbf.ft).
Reassembly
1.Clean mating faces of oil pump, stiffener plate
assembly and cylinder block; ensure bolt and
dowel holes are clean and dry.
2.Lubricate a new 'O' ring with engine oil and fit to
oil pump housing outlet.
3.Position oil pump and stiffener plate assembly
on to cylinder block ensuring 2 dowels are
correctly located.
4.Fit new bolts and using sequence shown,
tighten to 13 Nm (10 lbf.ft).
5.Lubricate a new 'O' ring with engine oil and fit to
oil pick-up strainer.
6.Clean threads of oil pick-up strainer Torx
screws and apply Loctite 242 to screw
threads.
7.Fit oil pick-up strainer, fit Torx screws and
tighten to 10 Nm (8 lbf.ft).
8.Position oil pump drive sprocket to chain and oil
pump ensuring that the 'D' shape on the drive
sprocket is located on the flat on the oil pump
drive shaft.
9.Clean oil pump drive sprocket retaining bolt and
apply Loctite 242 to bolt threads.
10.Fit oil pump drive sprocket and tighten bolt to
25 Nm (18 lbf.ft).
11.Fit new sump gasket.
+ ENGINE - Td5, OVERHAUL, Gasket
- engine sump.
Page 232 of 1672
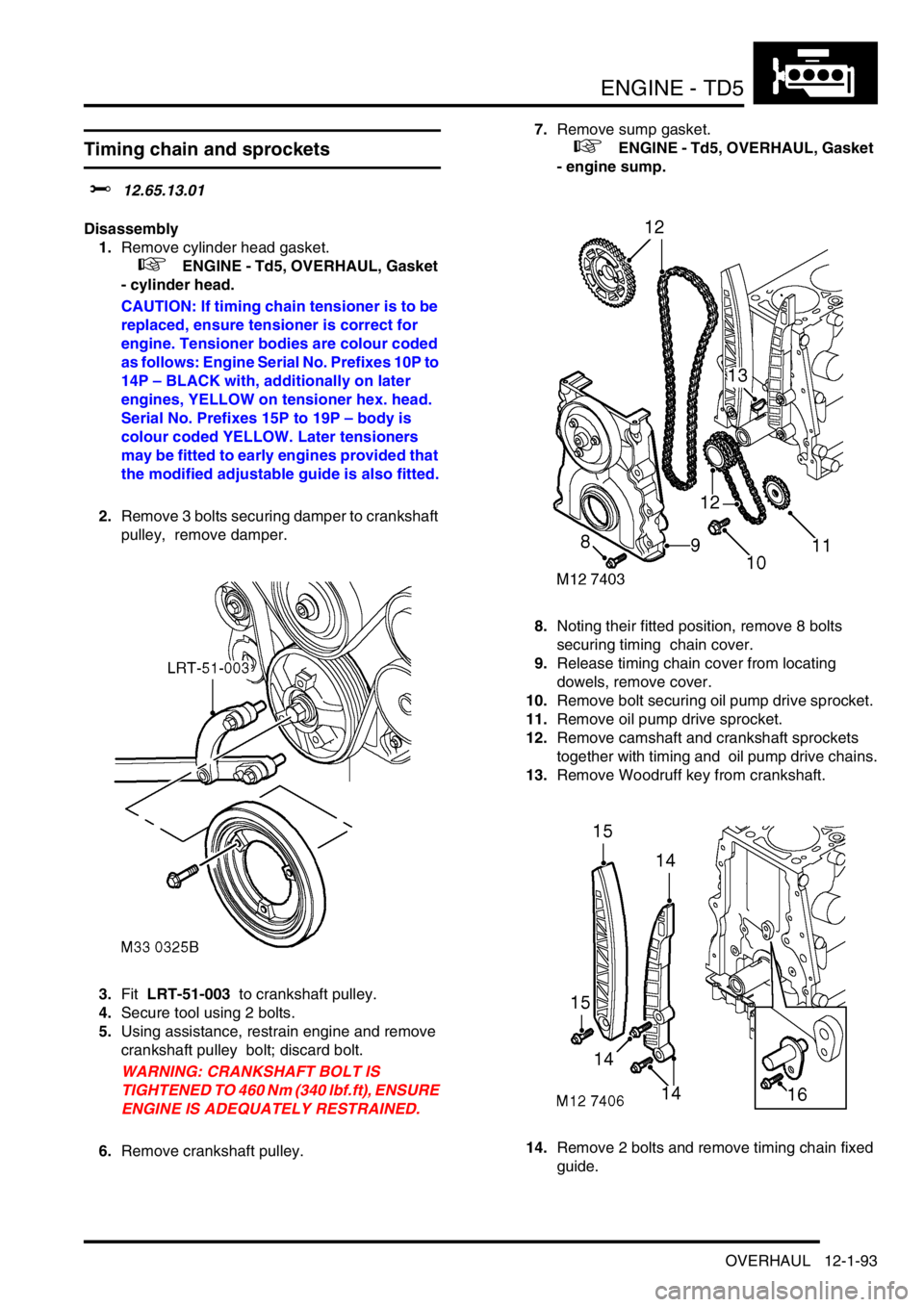
ENGINE - TD5
OVERHAUL 12-1-93
Timing chain and sprockets
$% 12.65.13.01
Disassembly
1.Remove cylinder head gasket.
+ ENGINE - Td5, OVERHAUL, Gasket
- cylinder head.
CAUTION: If timing chain tensioner is to be
replaced, ensure tensioner is correct for
engine. Tensioner bodies are colour coded
as follows: Engine Serial No. Prefixes 10P to
14P – BLACK with, additionally on later
engines, YELLOW on tensioner hex. head.
Serial No. Prefixes 15P to 19P – body is
colour coded YELLOW. Later tensioners
may be fitted to early engines provided that
the modified adjustable guide is also fitted.
2.Remove 3 bolts securing damper to crankshaft
pulley, remove damper.
3.Fit LRT-51-003 to crankshaft pulley.
4.Secure tool using 2 bolts.
5.Using assistance, restrain engine and remove
crankshaft pulley bolt; discard bolt.
WARNING: CRANKSHAFT BOLT IS
TIGHTENED TO 460 Nm (340 lbf.ft), ENSURE
ENGINE IS ADEQUATELY RESTRAINED.
6.Remove crankshaft pulley.7.Remove sump gasket.
+ ENGINE - Td5, OVERHAUL, Gasket
- engine sump.
8.Noting their fitted position, remove 8 bolts
securing timing chain cover.
9.Release timing chain cover from locating
dowels, remove cover.
10.Remove bolt securing oil pump drive sprocket.
11.Remove oil pump drive sprocket.
12.Remove camshaft and crankshaft sprockets
together with timing and oil pump drive chains.
13.Remove Woodruff key from crankshaft.
14.Remove 2 bolts and remove timing chain fixed
guide.
Page 233 of 1672
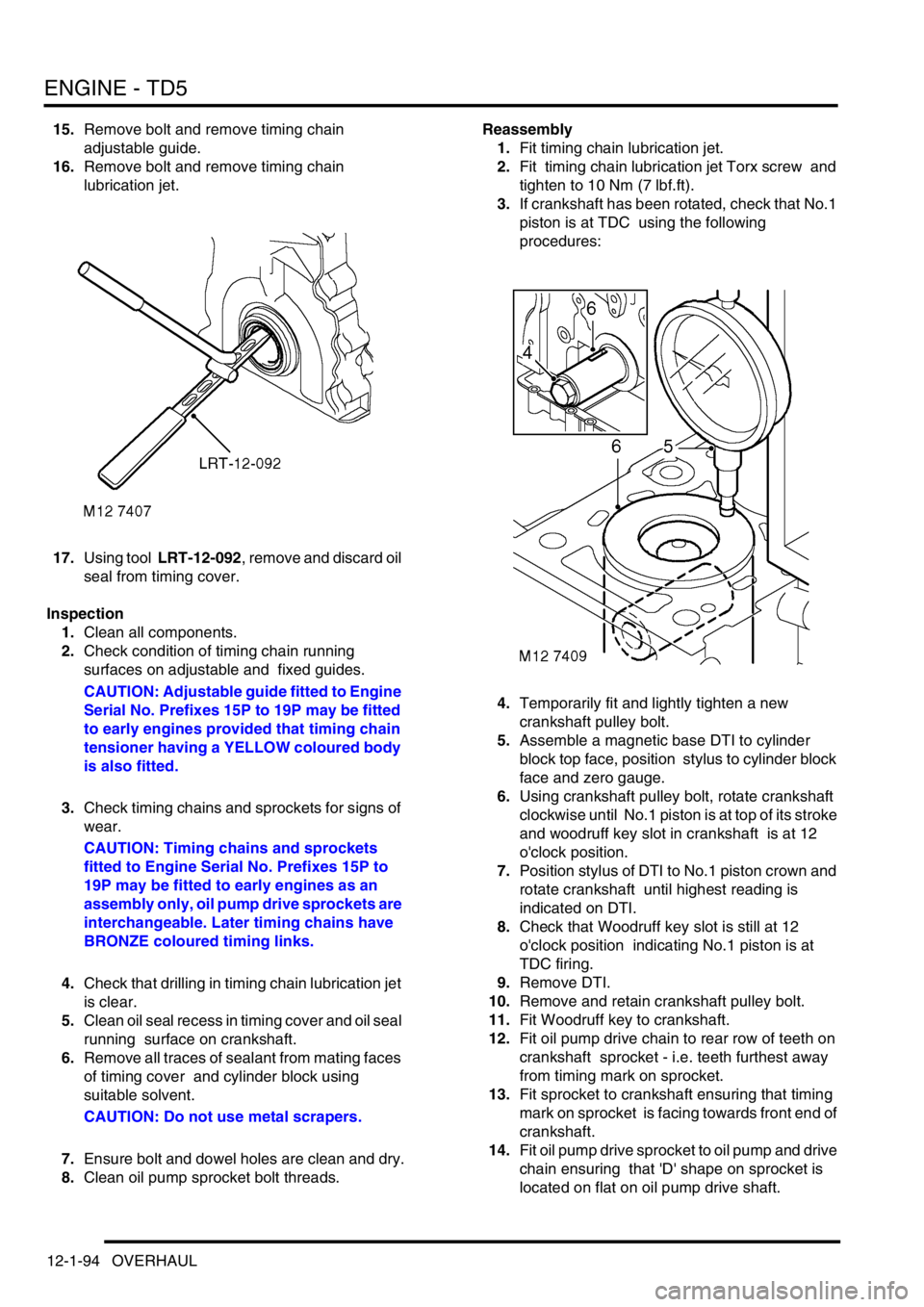
ENGINE - TD5
12-1-94 OVERHAUL
15.Remove bolt and remove timing chain
adjustable guide.
16.Remove bolt and remove timing chain
lubrication jet.
17.Using tool LRT-12-092, remove and discard oil
seal from timing cover.
Inspection
1.Clean all components.
2.Check condition of timing chain running
surfaces on adjustable and fixed guides.
CAUTION: Adjustable guide fitted to Engine
Serial No. Prefixes 15P to 19P may be fitted
to early engines provided that timing chain
tensioner having a YELLOW coloured body
is also fitted.
3.Check timing chains and sprockets for signs of
wear.
CAUTION: Timing chains and sprockets
fitted to Engine Serial No. Prefixes 15P to
19P may be fitted to early engines as an
assembly only, oil pump drive sprockets are
interchangeable. Later timing chains have
BRONZE coloured timing links.
4.Check that drilling in timing chain lubrication jet
is clear.
5.Clean oil seal recess in timing cover and oil seal
running surface on crankshaft.
6.Remove all traces of sealant from mating faces
of timing cover and cylinder block using
suitable solvent.
CAUTION: Do not use metal scrapers.
7.Ensure bolt and dowel holes are clean and dry.
8.Clean oil pump sprocket bolt threads.Reassembly
1.Fit timing chain lubrication jet.
2.Fit timing chain lubrication jet Torx screw and
tighten to 10 Nm (7 lbf.ft).
3.If crankshaft has been rotated, check that No.1
piston is at TDC using the following
procedures:
4.Temporarily fit and lightly tighten a new
crankshaft pulley bolt.
5.Assemble a magnetic base DTI to cylinder
block top face, position stylus to cylinder block
face and zero gauge.
6.Using crankshaft pulley bolt, rotate crankshaft
clockwise until No.1 piston is at top of its stroke
and woodruff key slot in crankshaft is at 12
o'clock position.
7.Position stylus of DTI to No.1 piston crown and
rotate crankshaft until highest reading is
indicated on DTI.
8.Check that Woodruff key slot is still at 12
o'clock position indicating No.1 piston is at
TDC firing.
9.Remove DTI.
10.Remove and retain crankshaft pulley bolt.
11.Fit Woodruff key to crankshaft.
12.Fit oil pump drive chain to rear row of teeth on
crankshaft sprocket - i.e. teeth furthest away
from timing mark on sprocket.
13.Fit sprocket to crankshaft ensuring that timing
mark on sprocket is facing towards front end of
crankshaft.
14.Fit oil pump drive sprocket to oil pump and drive
chain ensuring that 'D' shape on sprocket is
located on flat on oil pump drive shaft.
Page 234 of 1672
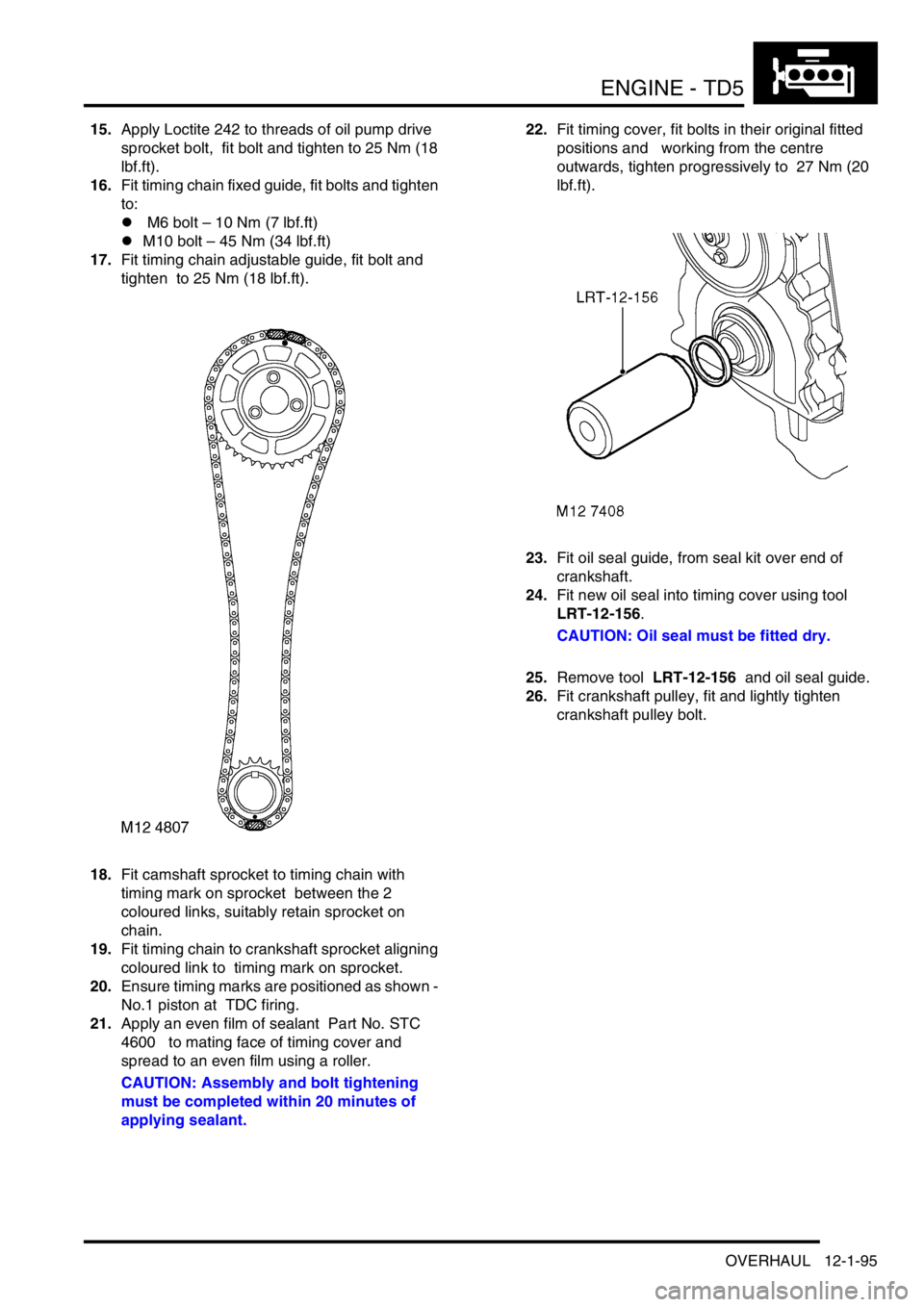
ENGINE - TD5
OVERHAUL 12-1-95
15.Apply Loctite 242 to threads of oil pump drive
sprocket bolt, fit bolt and tighten to 25 Nm (18
lbf.ft).
16.Fit timing chain fixed guide, fit bolts and tighten
to:
l M6 bolt – 10 Nm (7 lbf.ft)
lM10 bolt – 45 Nm (34 lbf.ft)
17.Fit timing chain adjustable guide, fit bolt and
tighten to 25 Nm (18 lbf.ft).
18.Fit camshaft sprocket to timing chain with
timing mark on sprocket between the 2
coloured links, suitably retain sprocket on
chain.
19.Fit timing chain to crankshaft sprocket aligning
coloured link to timing mark on sprocket.
20.Ensure timing marks are positioned as shown -
No.1 piston at TDC firing.
21.Apply an even film of sealant Part No. STC
4600 to mating face of timing cover and
spread to an even film using a roller.
CAUTION: Assembly and bolt tightening
must be completed within 20 minutes of
applying sealant.22.Fit timing cover, fit bolts in their original fitted
positions and working from the centre
outwards, tighten progressively to 27 Nm (20
lbf.ft).
23.Fit oil seal guide, from seal kit over end of
crankshaft.
24.Fit new oil seal into timing cover using tool
LRT-12-156.
CAUTION: Oil seal must be fitted dry.
25.Remove tool LRT-12-156 and oil seal guide.
26.Fit crankshaft pulley, fit and lightly tighten
crankshaft pulley bolt.
Page 235 of 1672
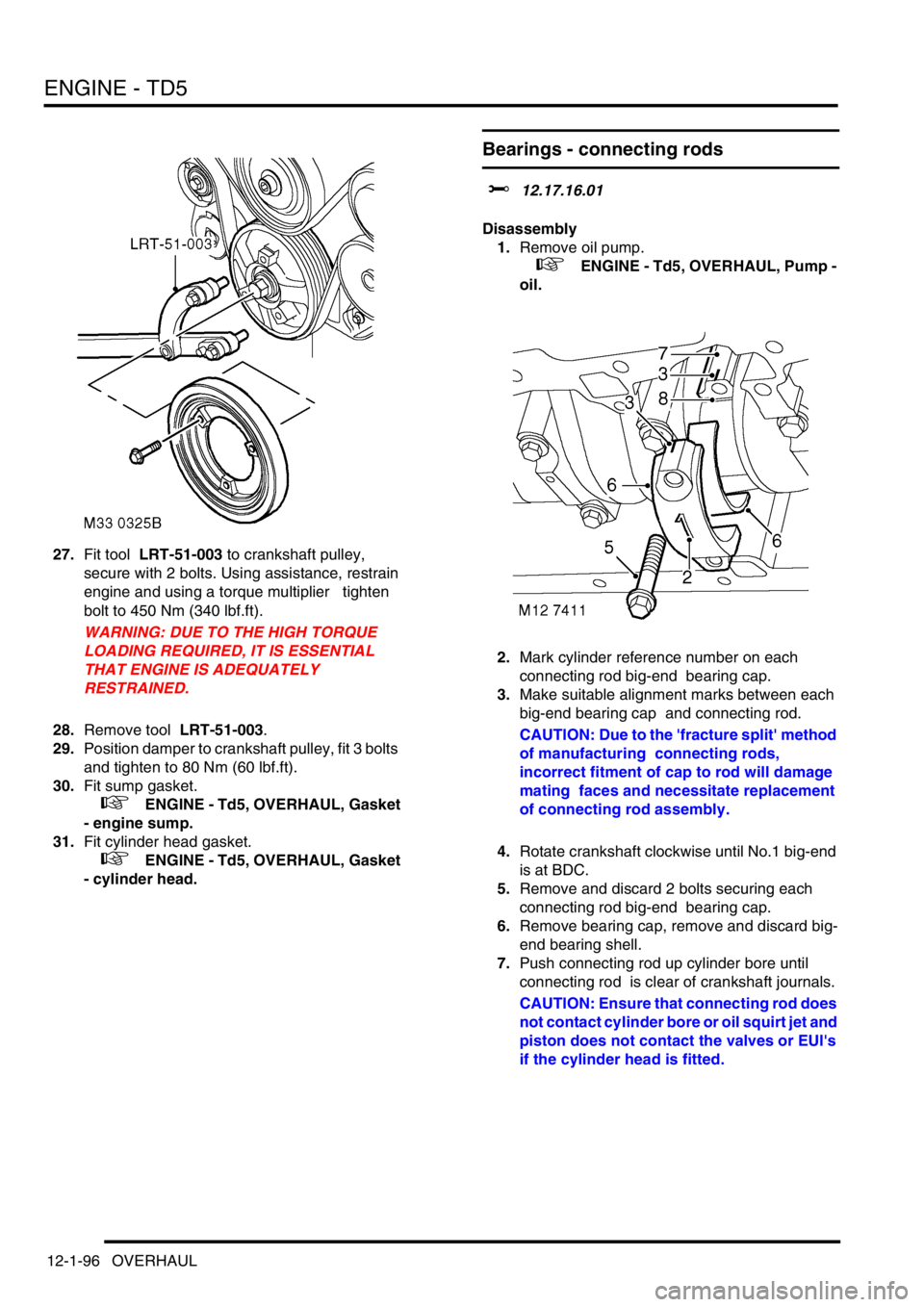
ENGINE - TD5
12-1-96 OVERHAUL
27.Fit tool LRT-51-003 to crankshaft pulley,
secure with 2 bolts. Using assistance, restrain
engine and using a torque multiplier tighten
bolt to 450 Nm (340 lbf.ft).
WARNING: DUE TO THE HIGH TORQUE
LOADING REQUIRED, IT IS ESSENTIAL
THAT ENGINE IS ADEQUATELY
RESTRAINED.
28.Remove tool LRT-51-003.
29.Position damper to crankshaft pulley, fit 3 bolts
and tighten to 80 Nm (60 lbf.ft).
30.Fit sump gasket.
+ ENGINE - Td5, OVERHAUL, Gasket
- engine sump.
31.Fit cylinder head gasket.
+ ENGINE - Td5, OVERHAUL, Gasket
- cylinder head.
Bearings - connecting rods
$% 12.17.16.01
Disassembly
1.Remove oil pump.
+ ENGINE - Td5, OVERHAUL, Pump -
oil.
2.Mark cylinder reference number on each
connecting rod big-end bearing cap.
3.Make suitable alignment marks between each
big-end bearing cap and connecting rod.
CAUTION: Due to the 'fracture split' method
of manufacturing connecting rods,
incorrect fitment of cap to rod will damage
mating faces and necessitate replacement
of connecting rod assembly.
4.Rotate crankshaft clockwise until No.1 big-end
is at BDC.
5.Remove and discard 2 bolts securing each
connecting rod big-end bearing cap.
6.Remove bearing cap, remove and discard big-
end bearing shell.
7.Push connecting rod up cylinder bore until
connecting rod is clear of crankshaft journals.
CAUTION: Ensure that connecting rod does
not contact cylinder bore or oil squirt jet and
piston does not contact the valves or EUI's
if the cylinder head is fitted.
Page 236 of 1672
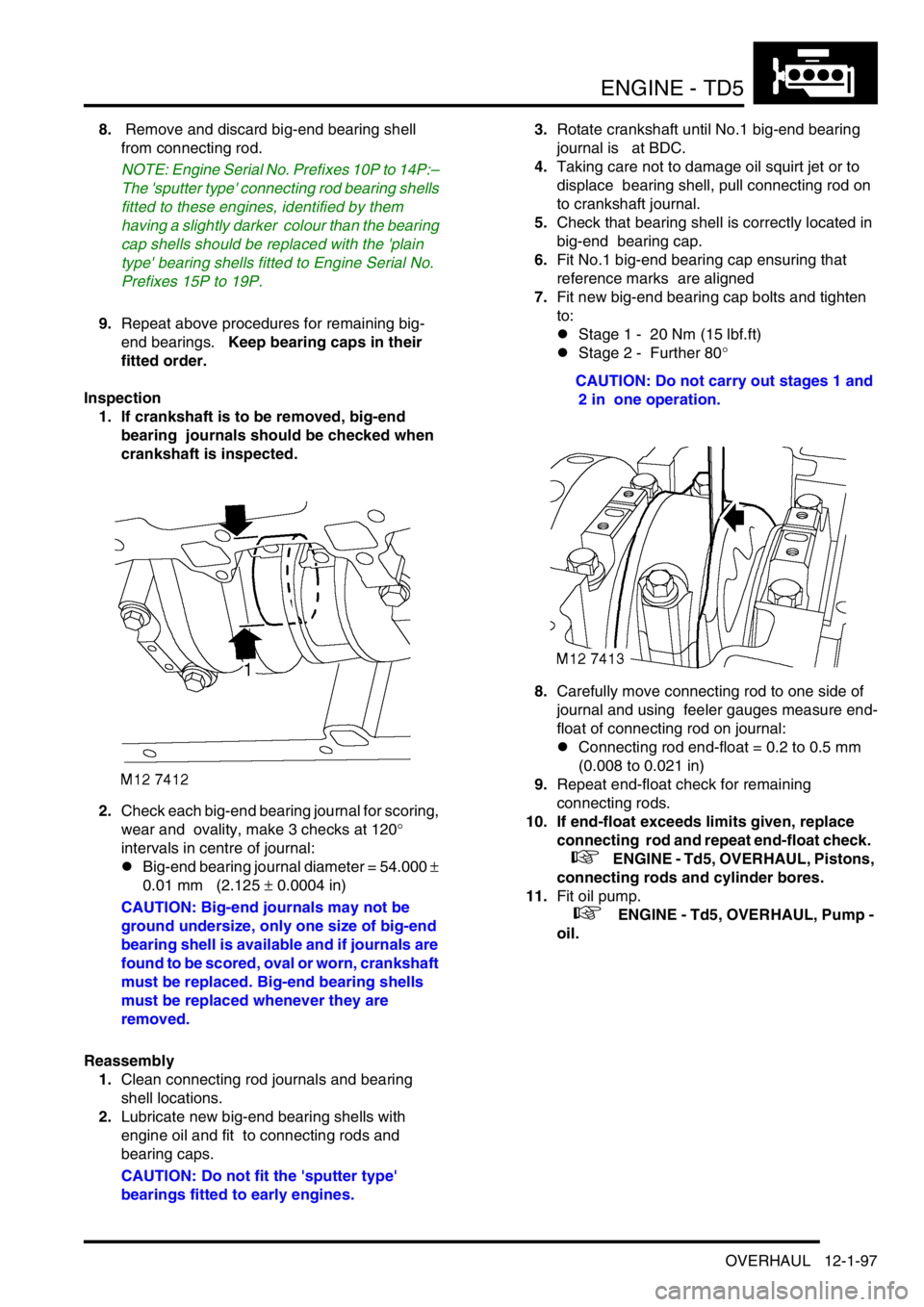
ENGINE - TD5
OVERHAUL 12-1-97
8. Remove and discard big-end bearing shell
from connecting rod.
NOTE: Engine Serial No. Prefixes 10P to 14P:–
The 'sputter type' connecting rod bearing shells
fitted to these engines, identified by them
having a slightly darker colour than the bearing
cap shells should be replaced with the 'plain
type' bearing shells fitted to Engine Serial No.
Prefixes 15P to 19P.
9.Repeat above procedures for remaining big-
end bearings. Keep bearing caps in their
fitted order.
Inspection
1. If crankshaft is to be removed, big-end
bearing journals should be checked when
crankshaft is inspected.
2.Check each big-end bearing journal for scoring,
wear and ovality, make 3 checks at 120
°
intervals in centre of journal:
lBig-end bearing journal diameter = 54.000
±
0.01 mm (2.125
± 0.0004 in)
CAUTION: Big-end journals may not be
ground undersize, only one size of big-end
bearing shell is available and if journals are
found to be scored, oval or worn, crankshaft
must be replaced. Big-end bearing shells
must be replaced whenever they are
removed.
Reassembly
1.Clean connecting rod journals and bearing
shell locations.
2.Lubricate new big-end bearing shells with
engine oil and fit to connecting rods and
bearing caps.
CAUTION: Do not fit the 'sputter type'
bearings fitted to early engines.3.Rotate crankshaft until No.1 big-end bearing
journal is at BDC.
4.Taking care not to damage oil squirt jet or to
displace bearing shell, pull connecting rod on
to crankshaft journal.
5.Check that bearing shell is correctly located in
big-end bearing cap.
6.Fit No.1 big-end bearing cap ensuring that
reference marks are aligned
7.Fit new big-end bearing cap bolts and tighten
to:
lStage 1 - 20 Nm (15 lbf.ft)
lStage 2 - Further 80
°
CAUTION: Do not carry out stages 1 and
2 in one operation.
8.Carefully move connecting rod to one side of
journal and using feeler gauges measure end-
float of connecting rod on journal:
lConnecting rod end-float = 0.2 to 0.5 mm
(0.008 to 0.021 in)
9.Repeat end-float check for remaining
connecting rods.
10. If end-float exceeds limits given, replace
connecting rod and repeat end-float check.
+ ENGINE - Td5, OVERHAUL, Pistons,
connecting rods and cylinder bores.
11.Fit oil pump.
+ ENGINE - Td5, OVERHAUL, Pump -
oil.
Page 237 of 1672
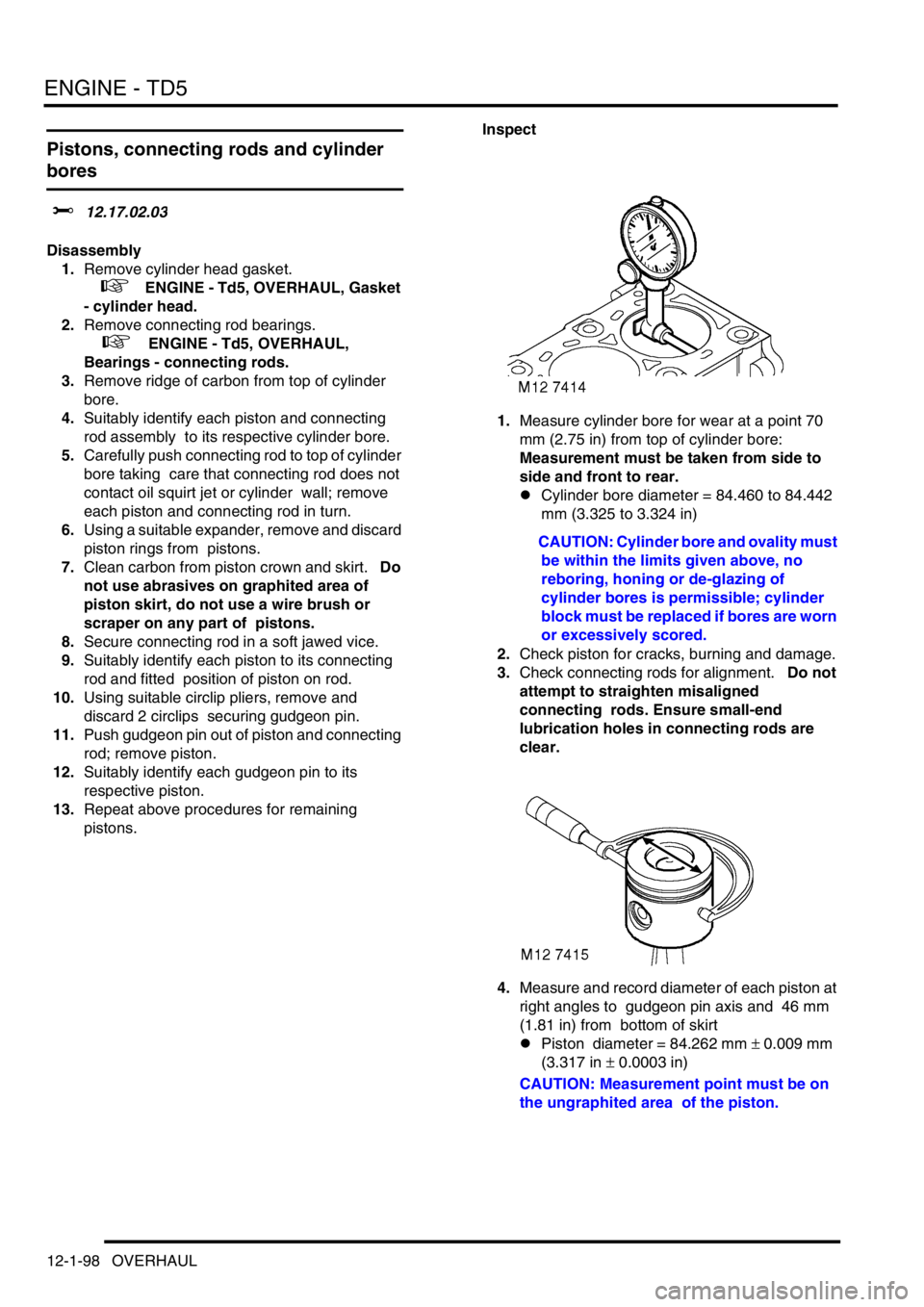
ENGINE - TD5
12-1-98 OVERHAUL
Pistons, connecting rods and cylinder
bores
$% 12.17.02.03
Disassembly
1.Remove cylinder head gasket.
+ ENGINE - Td5, OVERHAUL, Gasket
- cylinder head.
2.Remove connecting rod bearings.
+ ENGINE - Td5, OVERHAUL,
Bearings - connecting rods.
3.Remove ridge of carbon from top of cylinder
bore.
4.Suitably identify each piston and connecting
rod assembly to its respective cylinder bore.
5.Carefully push connecting rod to top of cylinder
bore taking care that connecting rod does not
contact oil squirt jet or cylinder wall; remove
each piston and connecting rod in turn.
6.Using a suitable expander, remove and discard
piston rings from pistons.
7.Clean carbon from piston crown and skirt. Do
not use abrasives on graphited area of
piston skirt, do not use a wire brush or
scraper on any part of pistons.
8.Secure connecting rod in a soft jawed vice.
9.Suitably identify each piston to its connecting
rod and fitted position of piston on rod.
10.Using suitable circlip pliers, remove and
discard 2 circlips securing gudgeon pin.
11.Push gudgeon pin out of piston and connecting
rod; remove piston.
12.Suitably identify each gudgeon pin to its
respective piston.
13.Repeat above procedures for remaining
pistons. Inspect
1.Measure cylinder bore for wear at a point 70
mm (2.75 in) from top of cylinder bore:
Measurement must be taken from side to
side and front to rear.
lCylinder bore diameter = 84.460 to 84.442
mm (3.325 to 3.324 in)
CAUTION: Cylinder bore and ovality must
be within the limits given above, no
reboring, honing or de-glazing of
cylinder bores is permissible; cylinder
block must be replaced if bores are worn
or excessively scored.
2.Check piston for cracks, burning and damage.
3.Check connecting rods for alignment. Do not
attempt to straighten misaligned
connecting rods. Ensure small-end
lubrication holes in connecting rods are
clear.
4.Measure and record diameter of each piston at
right angles to gudgeon pin axis and 46 mm
(1.81 in) from bottom of skirt
lPiston diameter = 84.262 mm
± 0.009 mm
(3.317 in
± 0.0003 in)
CAUTION: Measurement point must be on
the ungraphited area of the piston.
Page 238 of 1672
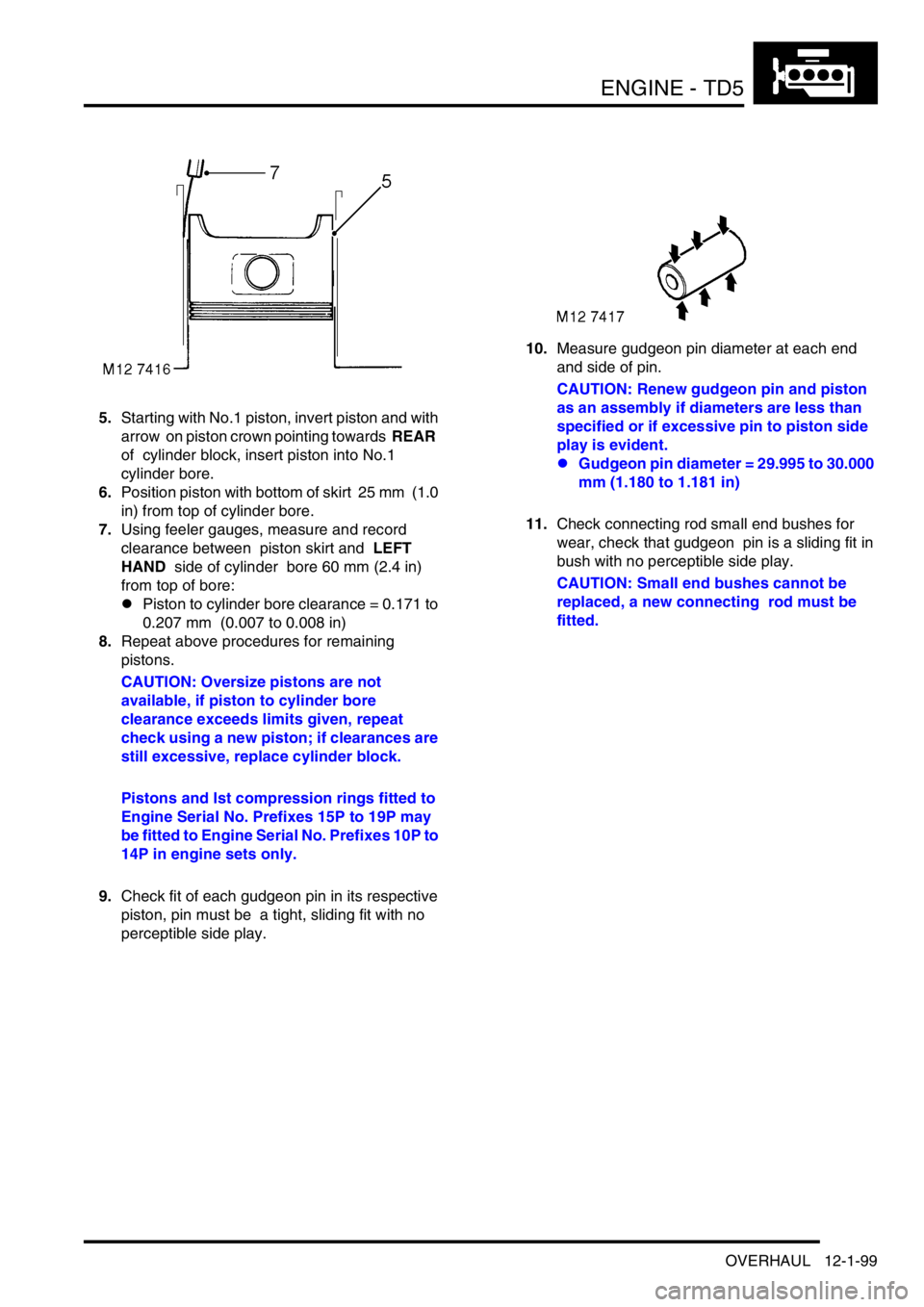
ENGINE - TD5
OVERHAUL 12-1-99
5.Starting with No.1 piston, invert piston and with
arrow on piston crown pointing towards REAR
of cylinder block, insert piston into No.1
cylinder bore.
6.Position piston with bottom of skirt 25 mm (1.0
in) from top of cylinder bore.
7.Using feeler gauges, measure and record
clearance between piston skirt and LEFT
HAND side of cylinder bore 60 mm (2.4 in)
from top of bore:
lPiston to cylinder bore clearance = 0.171 to
0.207 mm (0.007 to 0.008 in)
8.Repeat above procedures for remaining
pistons.
CAUTION: Oversize pistons are not
available, if piston to cylinder bore
clearance exceeds limits given, repeat
check using a new piston; if clearances are
still excessive, replace cylinder block.
Pistons and lst compression rings fitted to
Engine Serial No. Prefixes 15P to 19P may
be fitted to Engine Serial No. Prefixes 10P to
14P in engine sets only.
9.Check fit of each gudgeon pin in its respective
piston, pin must be a tight, sliding fit with no
perceptible side play.10.Measure gudgeon pin diameter at each end
and side of pin.
CAUTION: Renew gudgeon pin and piston
as an assembly if diameters are less than
specified or if excessive pin to piston side
play is evident.
lGudgeon pin diameter = 29.995 to 30.000
mm (1.180 to 1.181 in)
11.Check connecting rod small end bushes for
wear, check that gudgeon pin is a sliding fit in
bush with no perceptible side play.
CAUTION: Small end bushes cannot be
replaced, a new connecting rod must be
fitted.
Page 239 of 1672
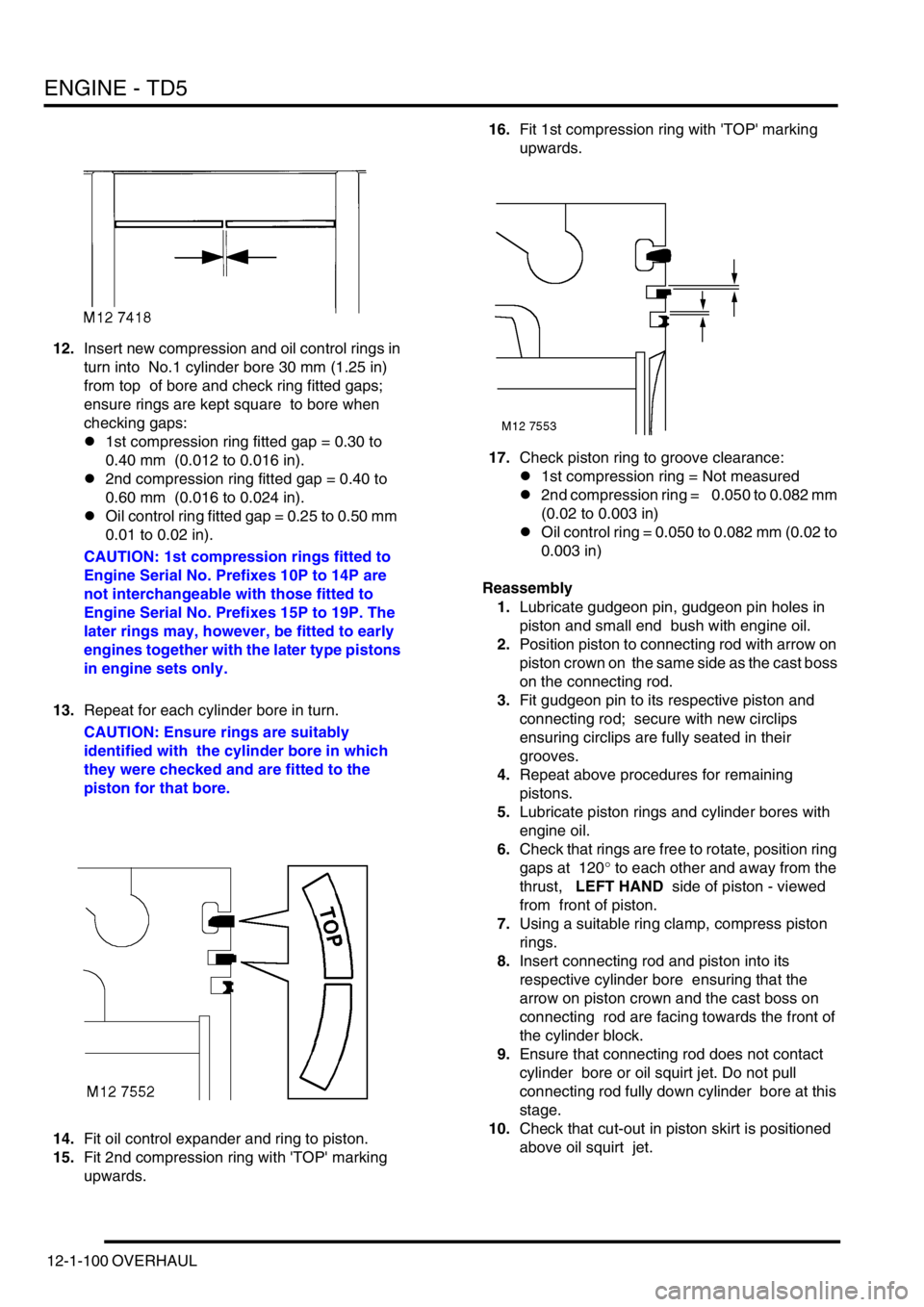
ENGINE - TD5
12-1-100 OVERHAUL
12.Insert new compression and oil control rings in
turn into No.1 cylinder bore 30 mm (1.25 in)
from top of bore and check ring fitted gaps;
ensure rings are kept square to bore when
checking gaps:
l1st compression ring fitted gap = 0.30 to
0.40 mm (0.012 to 0.016 in).
l2nd compression ring fitted gap = 0.40 to
0.60 mm (0.016 to 0.024 in).
lOil control ring fitted gap = 0.25 to 0.50 mm
0.01 to 0.02 in).
CAUTION: 1st compression rings fitted to
Engine Serial No. Prefixes 10P to 14P are
not interchangeable with those fitted to
Engine Serial No. Prefixes 15P to 19P. The
later rings may, however, be fitted to early
engines together with the later type pistons
in engine sets only.
13.Repeat for each cylinder bore in turn.
CAUTION: Ensure rings are suitably
identified with the cylinder bore in which
they were checked and are fitted to the
piston for that bore.
14.Fit oil control expander and ring to piston.
15.Fit 2nd compression ring with 'TOP' marking
upwards. 16.Fit 1st compression ring with 'TOP' marking
upwards.
17.Check piston ring to groove clearance:
l1st compression ring = Not measured
l2nd compression ring = 0.050 to 0.082 mm
(0.02 to 0.003 in)
lOil control ring = 0.050 to 0.082 mm (0.02 to
0.003 in)
Reassembly
1.Lubricate gudgeon pin, gudgeon pin holes in
piston and small end bush with engine oil.
2.Position piston to connecting rod with arrow on
piston crown on the same side as the cast boss
on the connecting rod.
3.Fit gudgeon pin to its respective piston and
connecting rod; secure with new circlips
ensuring circlips are fully seated in their
grooves.
4.Repeat above procedures for remaining
pistons.
5.Lubricate piston rings and cylinder bores with
engine oil.
6.Check that rings are free to rotate, position ring
gaps at 120
° to each other and away from the
thrust, LEFT HAND side of piston - viewed
from front of piston.
7.Using a suitable ring clamp, compress piston
rings.
8.Insert connecting rod and piston into its
respective cylinder bore ensuring that the
arrow on piston crown and the cast boss on
connecting rod are facing towards the front of
the cylinder block.
9.Ensure that connecting rod does not contact
cylinder bore or oil squirt jet. Do not pull
connecting rod fully down cylinder bore at this
stage.
10.Check that cut-out in piston skirt is positioned
above oil squirt jet.
Page 240 of 1672
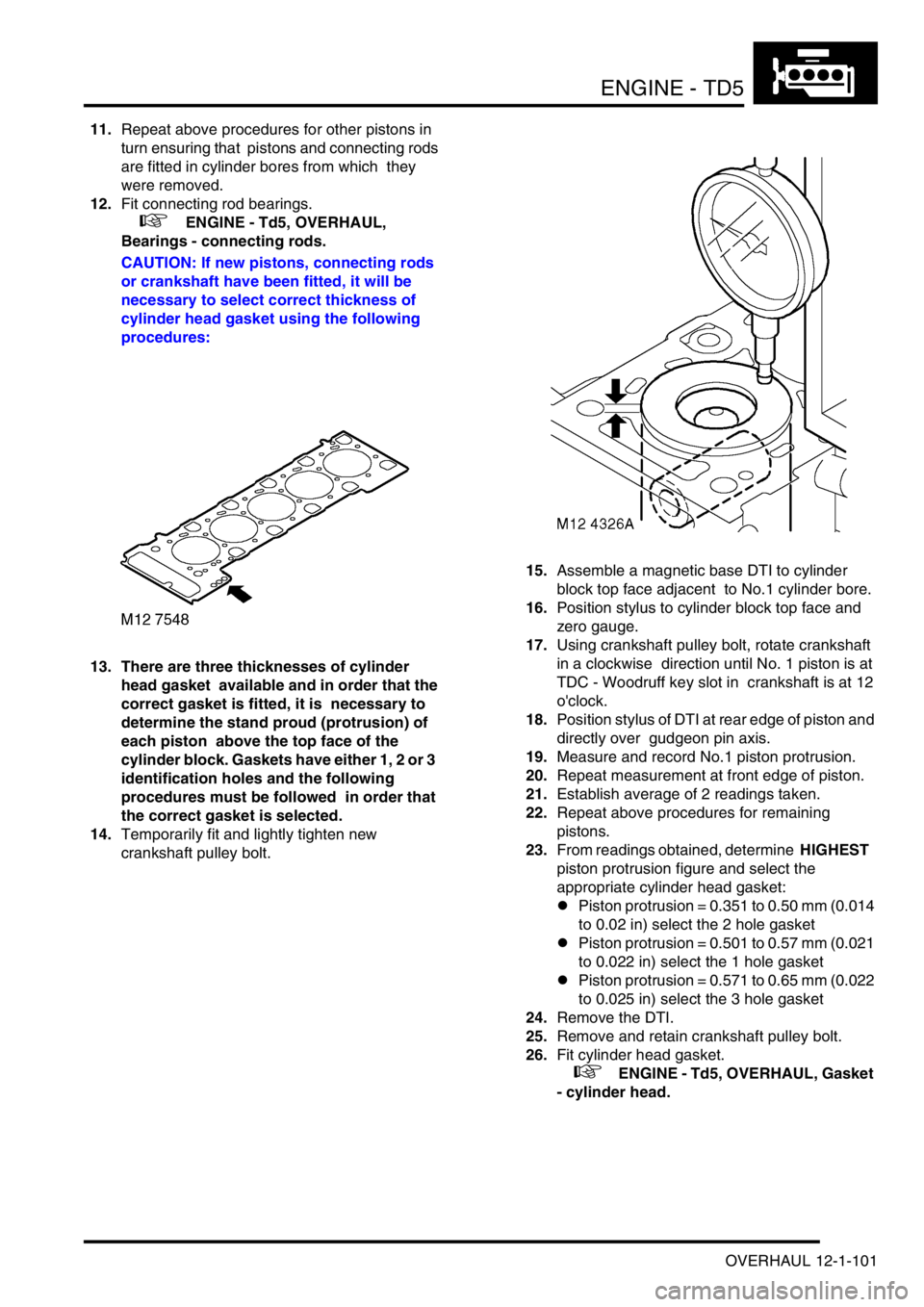
ENGINE - TD5
OVERHAUL 12-1-101
11.Repeat above procedures for other pistons in
turn ensuring that pistons and connecting rods
are fitted in cylinder bores from which they
were removed.
12.Fit connecting rod bearings.
+ ENGINE - Td5, OVERHAUL,
Bearings - connecting rods.
CAUTION: If new pistons, connecting rods
or crankshaft have been fitted, it will be
necessary to select correct thickness of
cylinder head gasket using the following
procedures:
13. There are three thicknesses of cylinder
head gasket available and in order that the
correct gasket is fitted, it is necessary to
determine the stand proud (protrusion) of
each piston above the top face of the
cylinder block. Gaskets have either 1, 2 or 3
identification holes and the following
procedures must be followed in order that
the correct gasket is selected.
14.Temporarily fit and lightly tighten new
crankshaft pulley bolt. 15.Assemble a magnetic base DTI to cylinder
block top face adjacent to No.1 cylinder bore.
16.Position stylus to cylinder block top face and
zero gauge.
17.Using crankshaft pulley bolt, rotate crankshaft
in a clockwise direction until No. 1 piston is at
TDC - Woodruff key slot in crankshaft is at 12
o'clock.
18.Position stylus of DTI at rear edge of piston and
directly over gudgeon pin axis.
19.Measure and record No.1 piston protrusion.
20.Repeat measurement at front edge of piston.
21.Establish average of 2 readings taken.
22.Repeat above procedures for remaining
pistons.
23.From readings obtained, determine HIGHEST
piston protrusion figure and select the
appropriate cylinder head gasket:
lPiston protrusion = 0.351 to 0.50 mm (0.014
to 0.02 in) select the 2 hole gasket
lPiston protrusion = 0.501 to 0.57 mm (0.021
to 0.022 in) select the 1 hole gasket
lPiston protrusion = 0.571 to 0.65 mm (0.022
to 0.025 in) select the 3 hole gasket
24.Remove the DTI.
25.Remove and retain crankshaft pulley bolt.
26.Fit cylinder head gasket.
+ ENGINE - Td5, OVERHAUL, Gasket
- cylinder head.