LAND ROVER DISCOVERY 2002 Workshop Manual
Manufacturer: LAND ROVER, Model Year: 2002, Model line: DISCOVERY, Model: LAND ROVER DISCOVERY 2002Pages: 1672, PDF Size: 46.1 MB
Page 211 of 1672
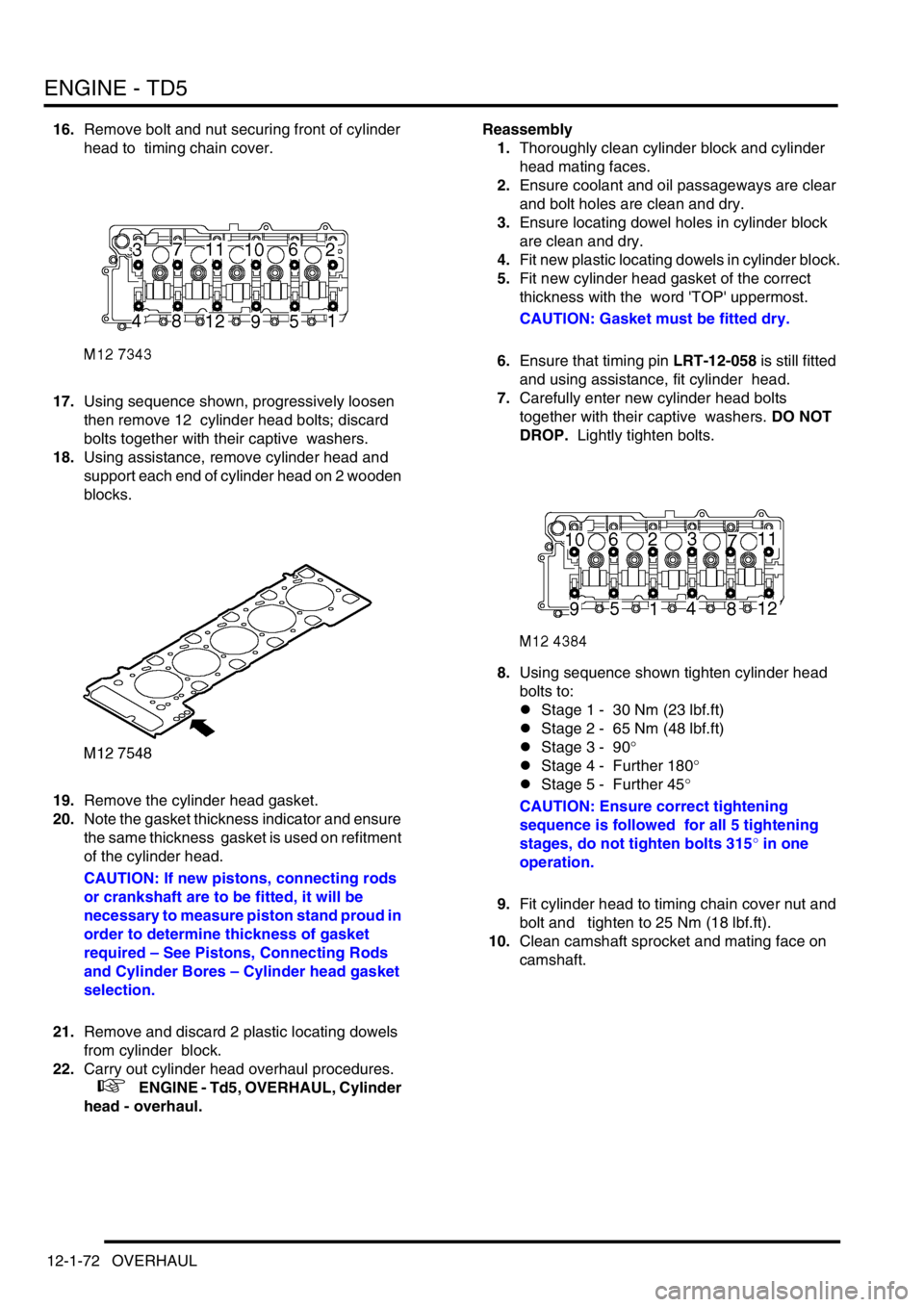
ENGINE - TD5
12-1-72 OVERHAUL
16.Remove bolt and nut securing front of cylinder
head to timing chain cover.
17.Using sequence shown, progressively loosen
then remove 12 cylinder head bolts; discard
bolts together with their captive washers.
18.Using assistance, remove cylinder head and
support each end of cylinder head on 2 wooden
blocks.
19.Remove the cylinder head gasket.
20.Note the gasket thickness indicator and ensure
the same thickness gasket is used on refitment
of the cylinder head.
CAUTION: If new pistons, connecting rods
or crankshaft are to be fitted, it will be
necessary to measure piston stand proud in
order to determine thickness of gasket
required – See Pistons, Connecting Rods
and Cylinder Bores – Cylinder head gasket
selection.
21.Remove and discard 2 plastic locating dowels
from cylinder block.
22.Carry out cylinder head overhaul procedures.
+ ENGINE - Td5, OVERHAUL, Cylinder
head - overhaul.Reassembly
1.Thoroughly clean cylinder block and cylinder
head mating faces.
2.Ensure coolant and oil passageways are clear
and bolt holes are clean and dry.
3.Ensure locating dowel holes in cylinder block
are clean and dry.
4.Fit new plastic locating dowels in cylinder block.
5.Fit new cylinder head gasket of the correct
thickness with the word 'TOP' uppermost.
CAUTION: Gasket must be fitted dry.
6.Ensure that timing pin LRT-12-058 is still fitted
and using assistance, fit cylinder head.
7.Carefully enter new cylinder head bolts
together with their captive washers. DO NOT
DROP. Lightly tighten bolts.
8.Using sequence shown tighten cylinder head
bolts to:
lStage 1 - 30 Nm (23 lbf.ft)
lStage 2 - 65 Nm (48 lbf.ft)
lStage 3 - 90
°
lStage 4 - Further 180
°
lStage 5 - Further 45°
CAUTION: Ensure correct tightening
sequence is followed for all 5 tightening
stages, do not tighten bolts 315
° in one
operation.
9.Fit cylinder head to timing chain cover nut and
bolt and tighten to 25 Nm (18 lbf.ft).
10.Clean camshaft sprocket and mating face on
camshaft.
Page 212 of 1672
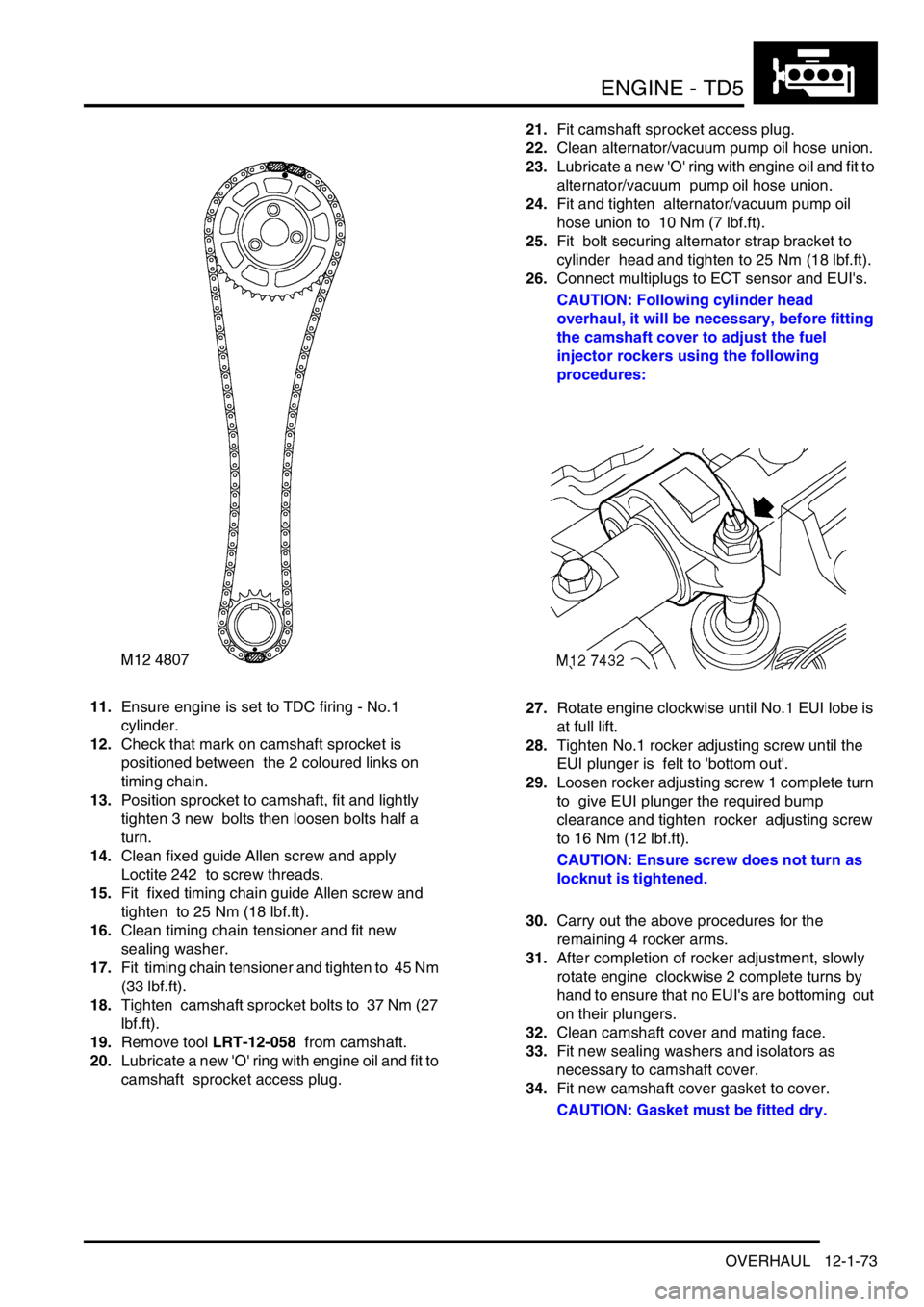
ENGINE - TD5
OVERHAUL 12-1-73
11.Ensure engine is set to TDC firing - No.1
cylinder.
12.Check that mark on camshaft sprocket is
positioned between the 2 coloured links on
timing chain.
13.Position sprocket to camshaft, fit and lightly
tighten 3 new bolts then loosen bolts half a
turn.
14.Clean fixed guide Allen screw and apply
Loctite 242 to screw threads.
15.Fit fixed timing chain guide Allen screw and
tighten to 25 Nm (18 lbf.ft).
16.Clean timing chain tensioner and fit new
sealing washer.
17.Fit timing chain tensioner and tighten to 45 Nm
(33 lbf.ft).
18.Tighten camshaft sprocket bolts to 37 Nm (27
lbf.ft).
19.Remove tool LRT-12-058 from camshaft.
20.Lubricate a new 'O' ring with engine oil and fit to
camshaft sprocket access plug.21.Fit camshaft sprocket access plug.
22.Clean alternator/vacuum pump oil hose union.
23.Lubricate a new 'O' ring with engine oil and fit to
alternator/vacuum pump oil hose union.
24.Fit and tighten alternator/vacuum pump oil
hose union to 10 Nm (7 lbf.ft).
25.Fit bolt securing alternator strap bracket to
cylinder head and tighten to 25 Nm (18 lbf.ft).
26.Connect multiplugs to ECT sensor and EUI's.
CAUTION: Following cylinder head
overhaul, it will be necessary, before fitting
the camshaft cover to adjust the fuel
injector rockers using the following
procedures:
27.Rotate engine clockwise until No.1 EUI lobe is
at full lift.
28.Tighten No.1 rocker adjusting screw until the
EUI plunger is felt to 'bottom out'.
29.Loosen rocker adjusting screw 1 complete turn
to give EUI plunger the required bump
clearance and tighten rocker adjusting screw
to 16 Nm (12 lbf.ft).
CAUTION: Ensure screw does not turn as
locknut is tightened.
30.Carry out the above procedures for the
remaining 4 rocker arms.
31.After completion of rocker adjustment, slowly
rotate engine clockwise 2 complete turns by
hand to ensure that no EUI's are bottoming out
on their plungers.
32.Clean camshaft cover and mating face.
33.Fit new sealing washers and isolators as
necessary to camshaft cover.
34.Fit new camshaft cover gasket to cover.
CAUTION: Gasket must be fitted dry.
Page 213 of 1672
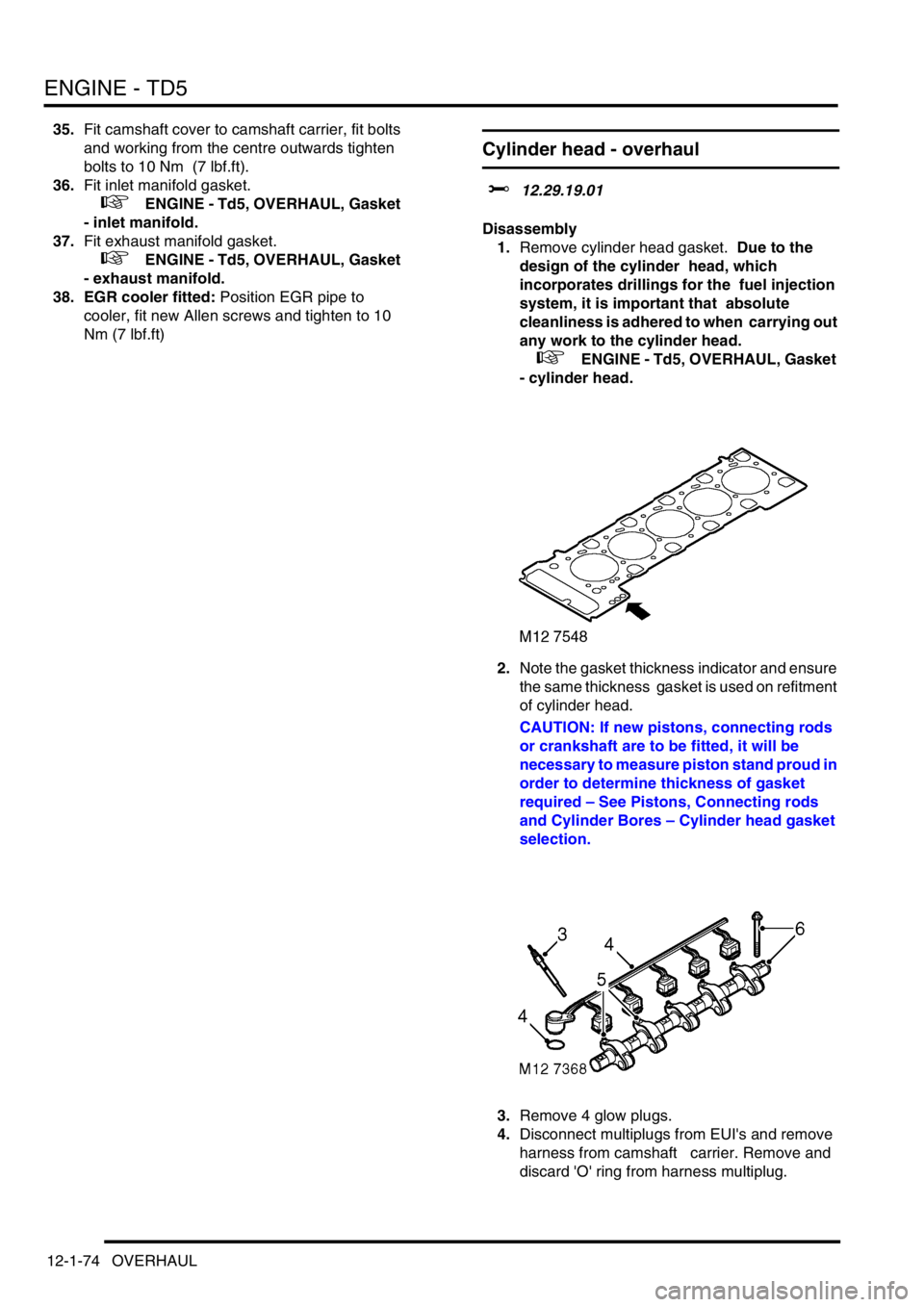
ENGINE - TD5
12-1-74 OVERHAUL
35.Fit camshaft cover to camshaft carrier, fit bolts
and working from the centre outwards tighten
bolts to 10 Nm (7 lbf.ft).
36.Fit inlet manifold gasket.
+ ENGINE - Td5, OVERHAUL, Gasket
- inlet manifold.
37.Fit exhaust manifold gasket.
+ ENGINE - Td5, OVERHAUL, Gasket
- exhaust manifold.
38. EGR cooler fitted: Position EGR pipe to
cooler, fit new Allen screws and tighten to 10
Nm (7 lbf.ft)
Cylinder head - overhaul
$% 12.29.19.01
Disassembly
1.Remove cylinder head gasket. Due to the
design of the cylinder head, which
incorporates drillings for the fuel injection
system, it is important that absolute
cleanliness is adhered to when carrying out
any work to the cylinder head.
+ ENGINE - Td5, OVERHAUL, Gasket
- cylinder head.
2.Note the gasket thickness indicator and ensure
the same thickness gasket is used on refitment
of cylinder head.
CAUTION: If new pistons, connecting rods
or crankshaft are to be fitted, it will be
necessary to measure piston stand proud in
order to determine thickness of gasket
required – See Pistons, Connecting rods
and Cylinder Bores – Cylinder head gasket
selection.
3.Remove 4 glow plugs.
4.Disconnect multiplugs from EUI's and remove
harness from camshaft carrier. Remove and
discard 'O' ring from harness multiplug.
Page 214 of 1672
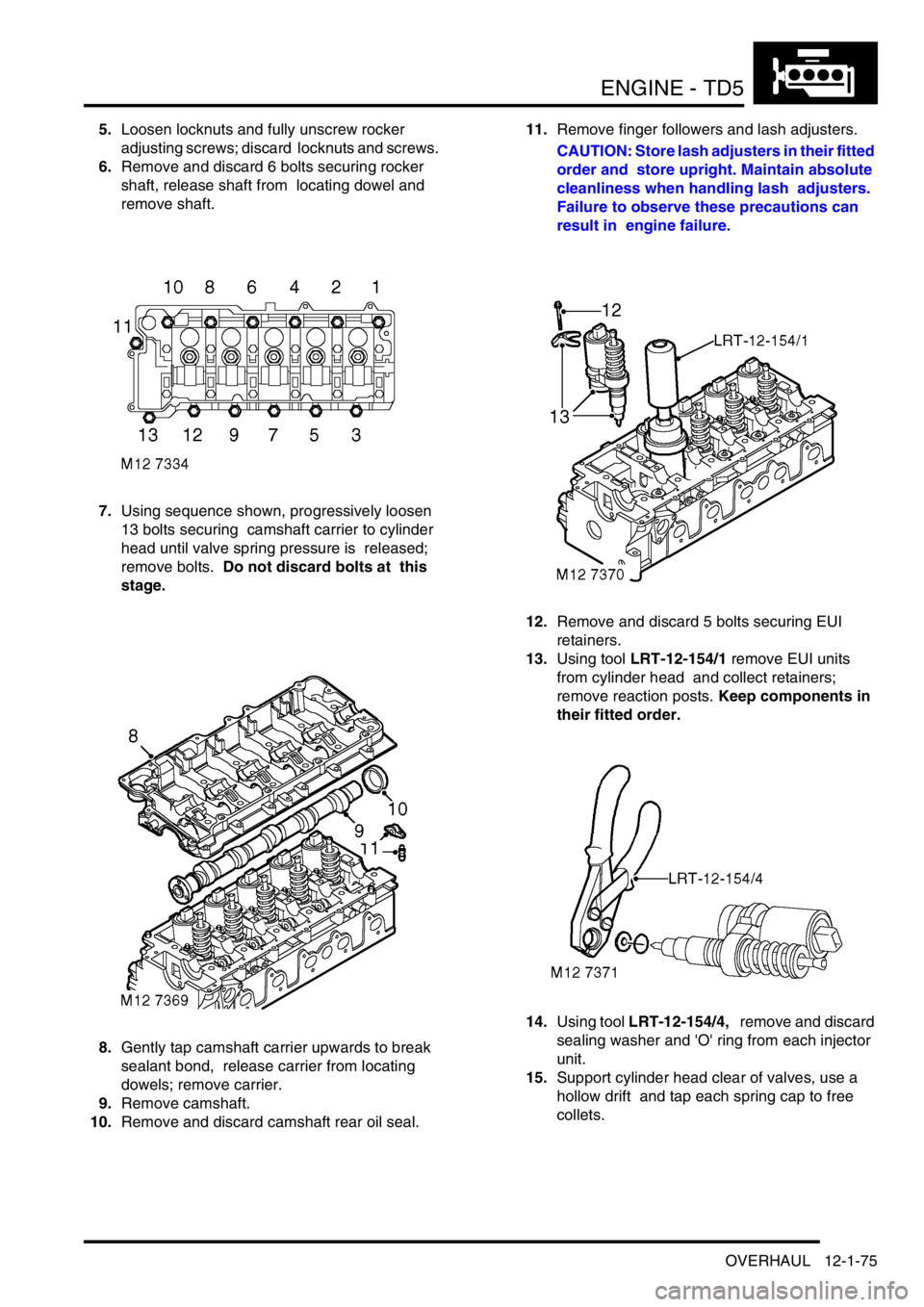
ENGINE - TD5
OVERHAUL 12-1-75
5.Loosen locknuts and fully unscrew rocker
adjusting screws; discard locknuts and screws.
6.Remove and discard 6 bolts securing rocker
shaft, release shaft from locating dowel and
remove shaft.
7.Using sequence shown, progressively loosen
13 bolts securing camshaft carrier to cylinder
head until valve spring pressure is released;
remove bolts. Do not discard bolts at this
stage.
8.Gently tap camshaft carrier upwards to break
sealant bond, release carrier from locating
dowels; remove carrier.
9.Remove camshaft.
10.Remove and discard camshaft rear oil seal.11.Remove finger followers and lash adjusters.
CAUTION: Store lash adjusters in their fitted
order and store upright. Maintain absolute
cleanliness when handling lash adjusters.
Failure to observe these precautions can
result in engine failure.
12.Remove and discard 5 bolts securing EUI
retainers.
13.Using tool LRT-12-154/1 remove EUI units
from cylinder head and collect retainers;
remove reaction posts. Keep components in
their fitted order.
14.Using tool LRT-12-154/4, remove and discard
sealing washer and 'O' ring from each injector
unit.
15.Support cylinder head clear of valves, use a
hollow drift and tap each spring cap to free
collets.
Page 215 of 1672
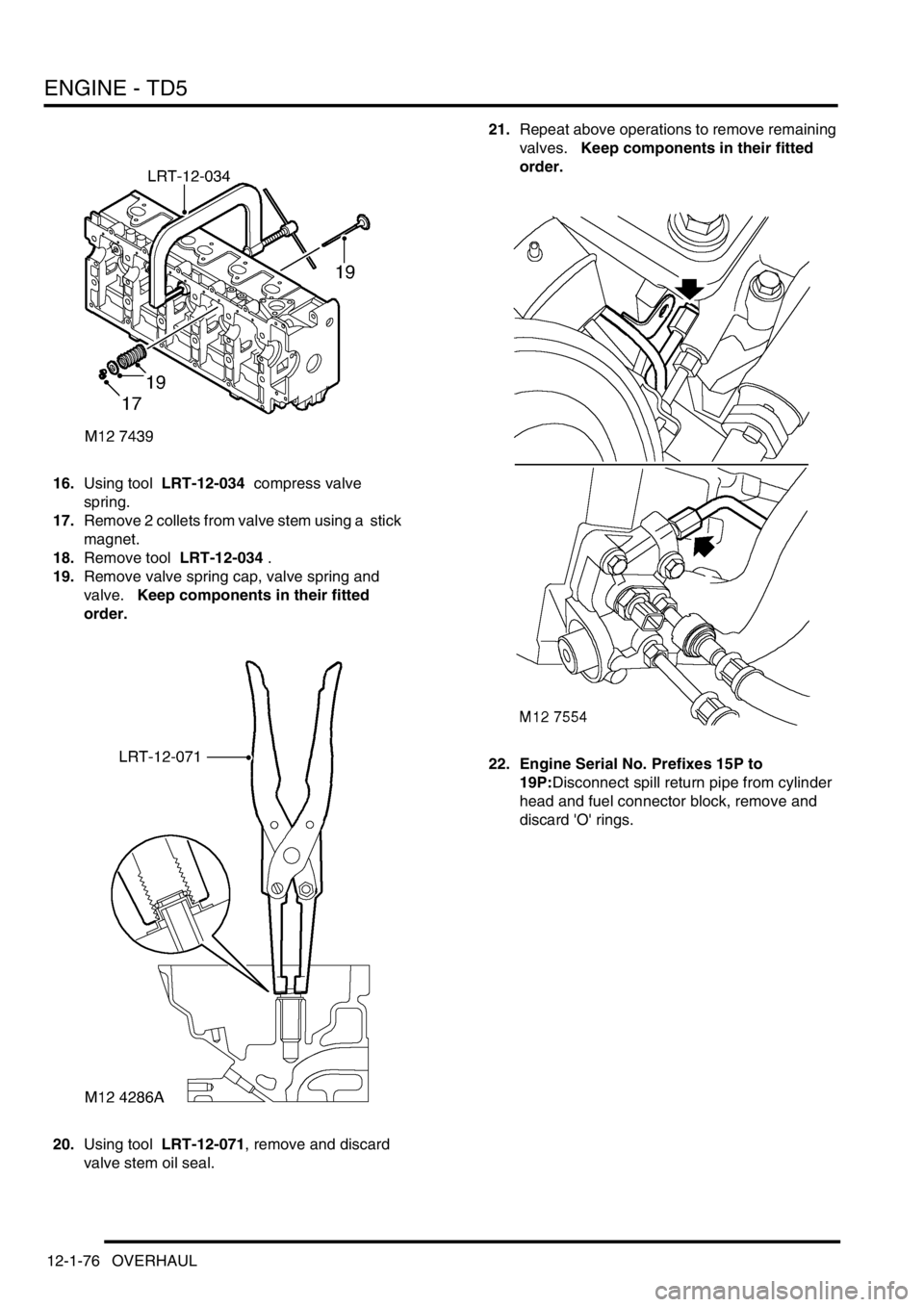
ENGINE - TD5
12-1-76 OVERHAUL
16.Using tool LRT-12-034 compress valve
spring.
17.Remove 2 collets from valve stem using a stick
magnet.
18.Remove tool LRT-12-034 .
19.Remove valve spring cap, valve spring and
valve. Keep components in their fitted
order.
20.Using tool LRT-12-071, remove and discard
valve stem oil seal. 21.Repeat above operations to remove remaining
valves. Keep components in their fitted
order.
22. Engine Serial No. Prefixes 15P to
19P:Disconnect spill return pipe from cylinder
head and fuel connector block, remove and
discard 'O' rings.
Page 216 of 1672
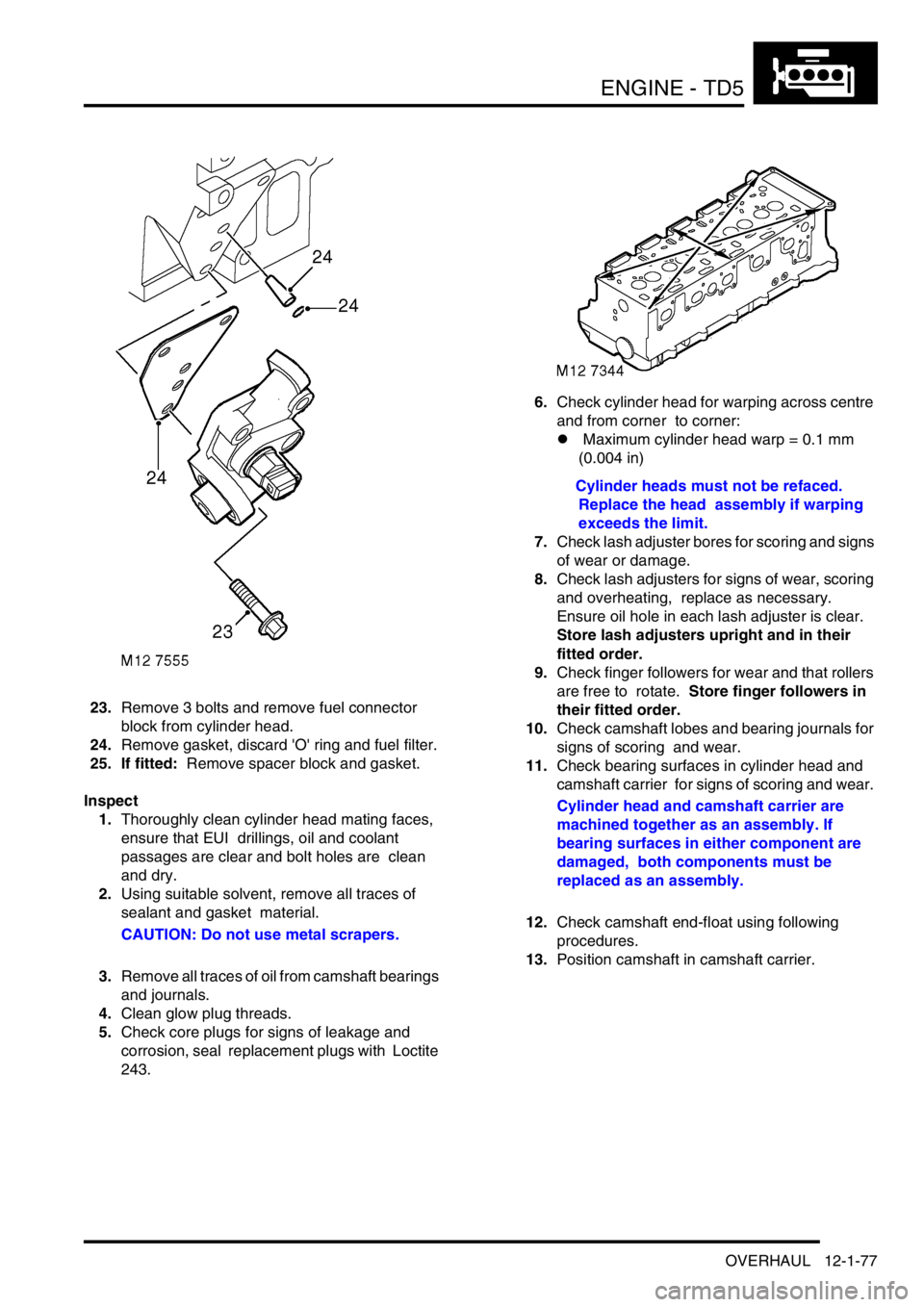
ENGINE - TD5
OVERHAUL 12-1-77
23.Remove 3 bolts and remove fuel connector
block from cylinder head.
24.Remove gasket, discard 'O' ring and fuel filter.
25. If fitted: Remove spacer block and gasket.
Inspect
1.Thoroughly clean cylinder head mating faces,
ensure that EUI drillings, oil and coolant
passages are clear and bolt holes are clean
and dry.
2.Using suitable solvent, remove all traces of
sealant and gasket material.
CAUTION: Do not use metal scrapers.
3.Remove all traces of oil from camshaft bearings
and journals.
4.Clean glow plug threads.
5.Check core plugs for signs of leakage and
corrosion, seal replacement plugs with Loctite
243.6.Check cylinder head for warping across centre
and from corner to corner:
l Maximum cylinder head warp = 0.1 mm
(0.004 in)
Cylinder heads must not be refaced.
Replace the head assembly if warping
exceeds the limit.
7.Check lash adjuster bores for scoring and signs
of wear or damage.
8.Check lash adjusters for signs of wear, scoring
and overheating, replace as necessary.
Ensure oil hole in each lash adjuster is clear.
Store lash adjusters upright and in their
fitted order.
9.Check finger followers for wear and that rollers
are free to rotate. Store finger followers in
their fitted order.
10.Check camshaft lobes and bearing journals for
signs of scoring and wear.
11.Check bearing surfaces in cylinder head and
camshaft carrier for signs of scoring and wear.
Cylinder head and camshaft carrier are
machined together as an assembly. If
bearing surfaces in either component are
damaged, both components must be
replaced as an assembly.
12.Check camshaft end-float using following
procedures.
13.Position camshaft in camshaft carrier.
Page 217 of 1672
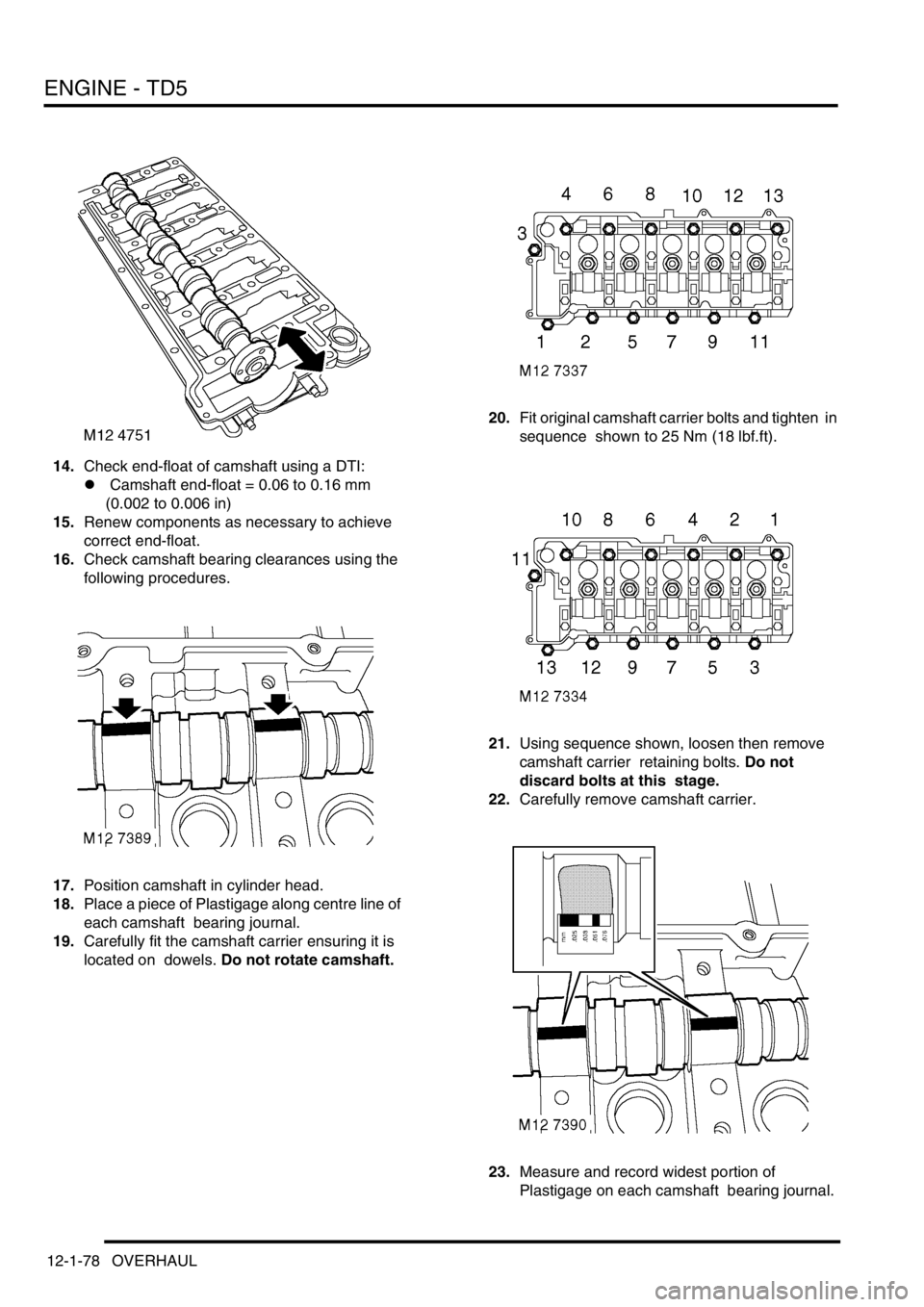
ENGINE - TD5
12-1-78 OVERHAUL
14.Check end-float of camshaft using a DTI:
l Camshaft end-float = 0.06 to 0.16 mm
(0.002 to 0.006 in)
15.Renew components as necessary to achieve
correct end-float.
16.Check camshaft bearing clearances using the
following procedures.
17.Position camshaft in cylinder head.
18.Place a piece of Plastigage along centre line of
each camshaft bearing journal.
19.Carefully fit the camshaft carrier ensuring it is
located on dowels. Do not rotate camshaft.20.Fit original camshaft carrier bolts and tighten in
sequence shown to 25 Nm (18 lbf.ft).
21.Using sequence shown, loosen then remove
camshaft carrier retaining bolts. Do not
discard bolts at this stage.
22.Carefully remove camshaft carrier.
23.Measure and record widest portion of
Plastigage on each camshaft bearing journal.
Page 218 of 1672
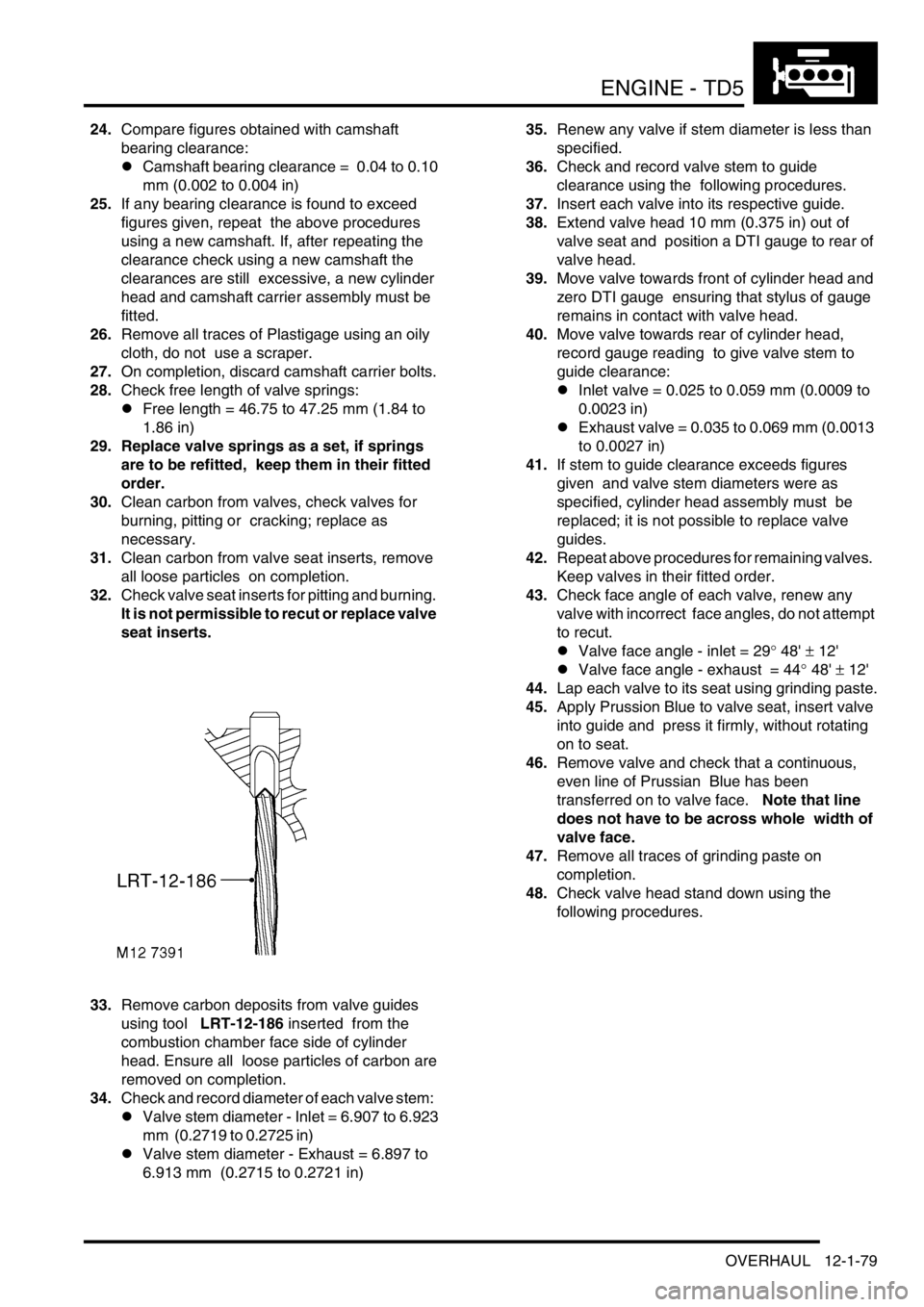
ENGINE - TD5
OVERHAUL 12-1-79
24.Compare figures obtained with camshaft
bearing clearance:
lCamshaft bearing clearance = 0.04 to 0.10
mm (0.002 to 0.004 in)
25.If any bearing clearance is found to exceed
figures given, repeat the above procedures
using a new camshaft. If, after repeating the
clearance check using a new camshaft the
clearances are still excessive, a new cylinder
head and camshaft carrier assembly must be
fitted.
26.Remove all traces of Plastigage using an oily
cloth, do not use a scraper.
27.On completion, discard camshaft carrier bolts.
28.Check free length of valve springs:
lFree length = 46.75 to 47.25 mm (1.84 to
1.86 in)
29. Replace valve springs as a set, if springs
are to be refitted, keep them in their fitted
order.
30.Clean carbon from valves, check valves for
burning, pitting or cracking; replace as
necessary.
31.Clean carbon from valve seat inserts, remove
all loose particles on completion.
32.Check valve seat inserts for pitting and burning.
It is not permissible to recut or replace valve
seat inserts.
33.Remove carbon deposits from valve guides
using tool LRT-12-186 inserted from the
combustion chamber face side of cylinder
head. Ensure all loose particles of carbon are
removed on completion.
34.Check and record diameter of each valve stem:
lValve stem diameter - Inlet = 6.907 to 6.923
mm (0.2719 to 0.2725 in)
lValve stem diameter - Exhaust = 6.897 to
6.913 mm (0.2715 to 0.2721 in)35.Renew any valve if stem diameter is less than
specified.
36.Check and record valve stem to guide
clearance using the following procedures.
37.Insert each valve into its respective guide.
38.Extend valve head 10 mm (0.375 in) out of
valve seat and position a DTI gauge to rear of
valve head.
39.Move valve towards front of cylinder head and
zero DTI gauge ensuring that stylus of gauge
remains in contact with valve head.
40.Move valve towards rear of cylinder head,
record gauge reading to give valve stem to
guide clearance:
lInlet valve = 0.025 to 0.059 mm (0.0009 to
0.0023 in)
lExhaust valve = 0.035 to 0.069 mm (0.0013
to 0.0027 in)
41.If stem to guide clearance exceeds figures
given and valve stem diameters were as
specified, cylinder head assembly must be
replaced; it is not possible to replace valve
guides.
42.Repeat above procedures for remaining valves.
Keep valves in their fitted order.
43.Check face angle of each valve, renew any
valve with incorrect face angles, do not attempt
to recut.
lValve face angle - inlet = 29
° 48' ± 12'
lValve face angle - exhaust = 44
° 48' ± 12'
44.Lap each valve to its seat using grinding paste.
45.Apply Prussion Blue to valve seat, insert valve
into guide and press it firmly, without rotating
on to seat.
46.Remove valve and check that a continuous,
even line of Prussian Blue has been
transferred on to valve face. Note that line
does not have to be across whole width of
valve face.
47.Remove all traces of grinding paste on
completion.
48.Check valve head stand down using the
following procedures.
Page 219 of 1672
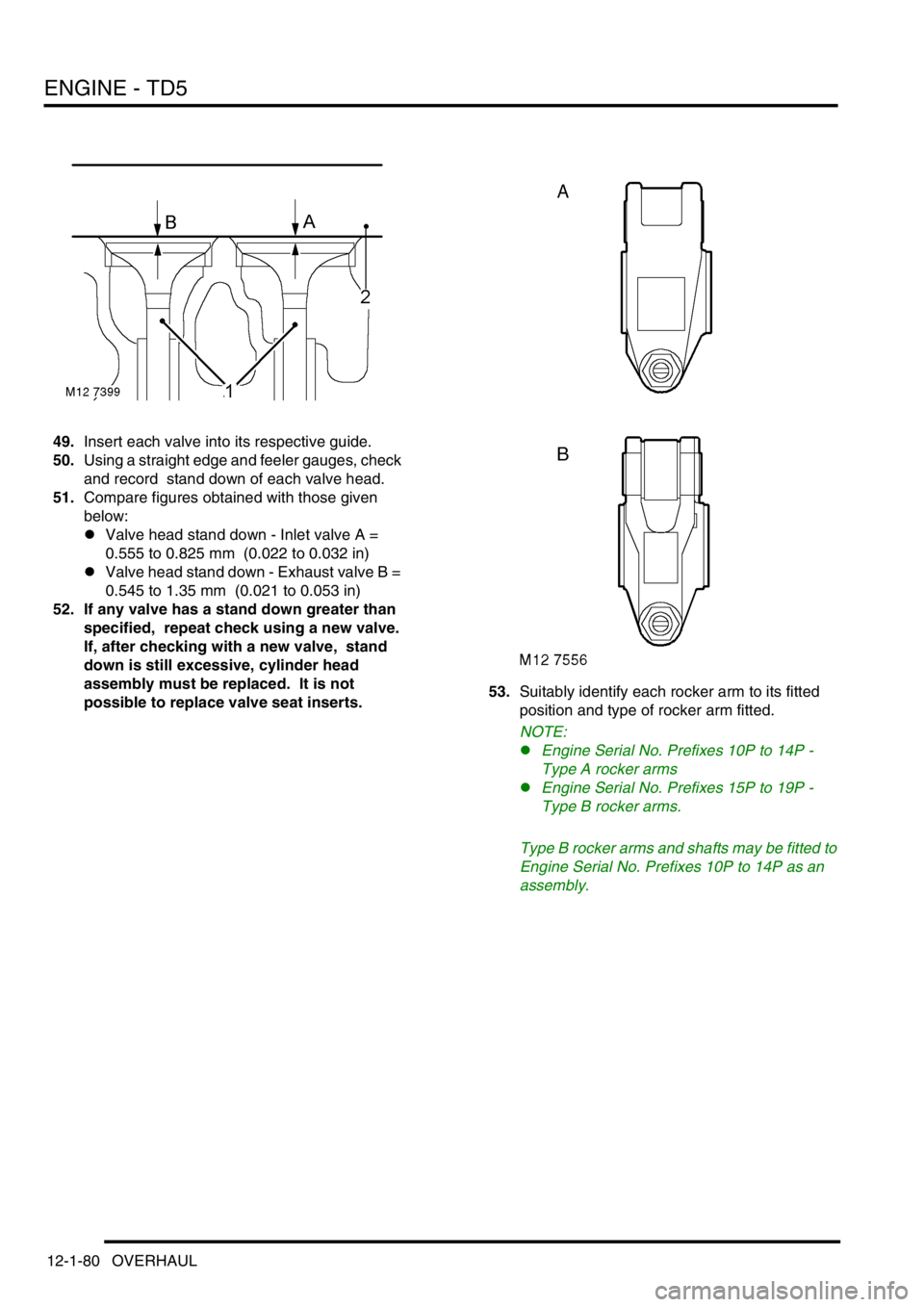
ENGINE - TD5
12-1-80 OVERHAUL
49.Insert each valve into its respective guide.
50.Using a straight edge and feeler gauges, check
and record stand down of each valve head.
51.Compare figures obtained with those given
below:
lValve head stand down - Inlet valve A =
0.555 to 0.825 mm (0.022 to 0.032 in)
lValve head stand down - Exhaust valve B =
0.545 to 1.35 mm (0.021 to 0.053 in)
52. If any valve has a stand down greater than
specified, repeat check using a new valve.
If, after checking with a new valve, stand
down is still excessive, cylinder head
assembly must be replaced. It is not
possible to replace valve seat inserts.53.Suitably identify each rocker arm to its fitted
position and type of rocker arm fitted.
NOTE:
lEngine Serial No. Prefixes 10P to 14P -
Type A rocker arms
lEngine Serial No. Prefixes 15P to 19P -
Type B rocker arms.
Type B rocker arms and shafts may be fitted to
Engine Serial No. Prefixes 10P to 14P as an
assembly.
Page 220 of 1672
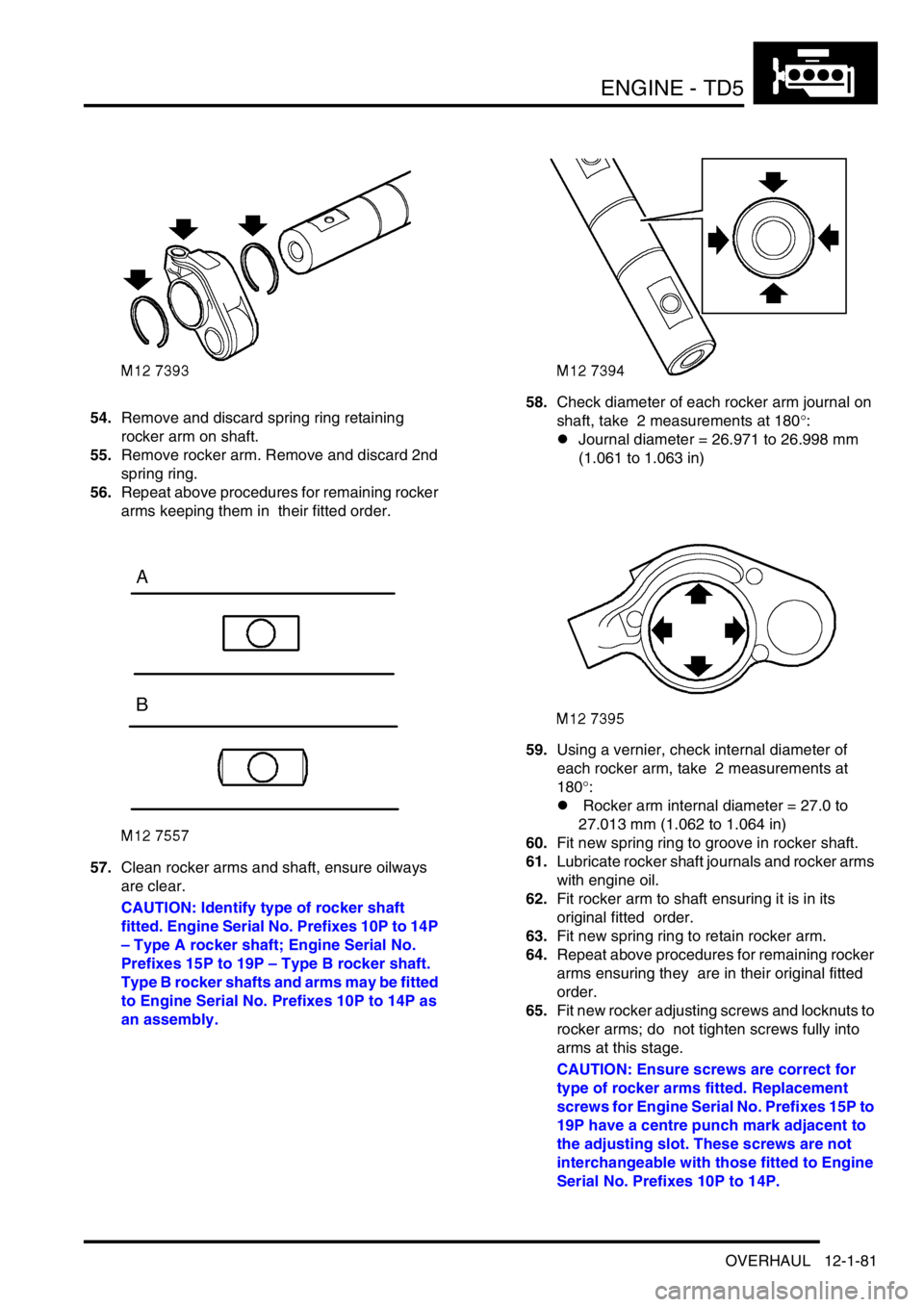
ENGINE - TD5
OVERHAUL 12-1-81
54.Remove and discard spring ring retaining
rocker arm on shaft.
55.Remove rocker arm. Remove and discard 2nd
spring ring.
56.Repeat above procedures for remaining rocker
arms keeping them in their fitted order.
57.Clean rocker arms and shaft, ensure oilways
are clear.
CAUTION: Identify type of rocker shaft
fitted. Engine Serial No. Prefixes 10P to 14P
– Type A rocker shaft; Engine Serial No.
Prefixes 15P to 19P – Type B rocker shaft.
Type B rocker shafts and arms may be fitted
to Engine Serial No. Prefixes 10P to 14P as
an assembly.58.Check diameter of each rocker arm journal on
shaft, take 2 measurements at 180°:
lJournal diameter = 26.971 to 26.998 mm
(1.061 to 1.063 in)
59.Using a vernier, check internal diameter of
each rocker arm, take 2 measurements at
180
°:
l Rocker arm internal diameter = 27.0 to
27.013 mm (1.062 to 1.064 in)
60.Fit new spring ring to groove in rocker shaft.
61.Lubricate rocker shaft journals and rocker arms
with engine oil.
62.Fit rocker arm to shaft ensuring it is in its
original fitted order.
63.Fit new spring ring to retain rocker arm.
64.Repeat above procedures for remaining rocker
arms ensuring they are in their original fitted
order.
65.Fit new rocker adjusting screws and locknuts to
rocker arms; do not tighten screws fully into
arms at this stage.
CAUTION: Ensure screws are correct for
type of rocker arms fitted. Replacement
screws for Engine Serial No. Prefixes 15P to
19P have a centre punch mark adjacent to
the adjusting slot. These screws are not
interchangeable with those fitted to Engine
Serial No. Prefixes 10P to 14P.