sensor LAND ROVER DISCOVERY 2002 Manual Online
[x] Cancel search | Manufacturer: LAND ROVER, Model Year: 2002, Model line: DISCOVERY, Model: LAND ROVER DISCOVERY 2002Pages: 1672, PDF Size: 46.1 MB
Page 405 of 1672
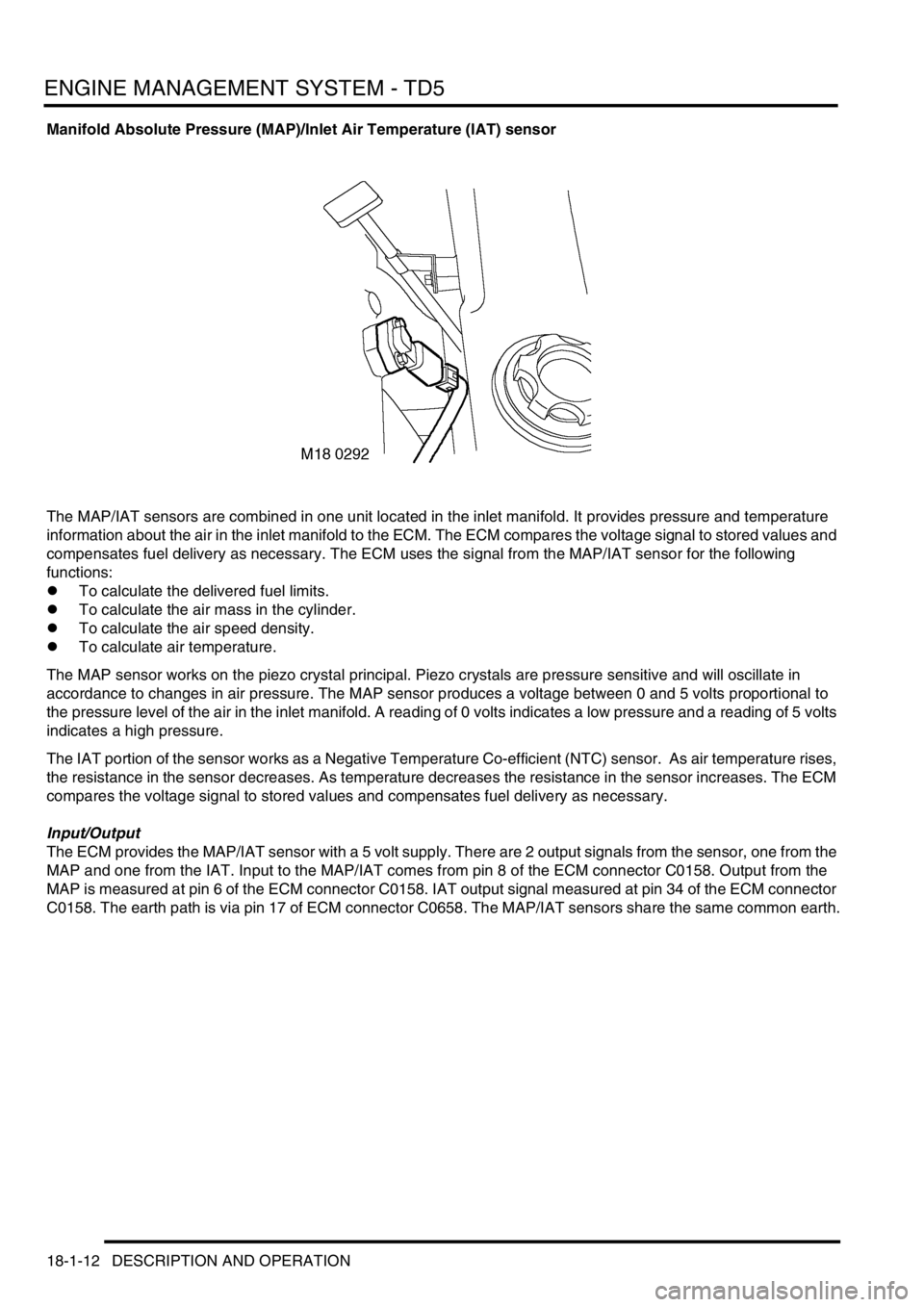
ENGINE MANAGEMENT SYSTEM - TD5
18-1-12 DESCRIPTION AND OPERATION
Manifold Absolute Pressure (MAP)/Inlet Air Temperature (IAT) sensor
The MAP/IAT sensors are combined in one unit located in the inlet manifold. It provides pressure and temperature
information about the air in the inlet manifold to the ECM. The ECM compares the voltage signal to stored values and
compensates fuel delivery as necessary. The ECM uses the signal from the MAP/IAT sensor for the following
functions:
lTo calculate the delivered fuel limits.
lTo calculate the air mass in the cylinder.
lTo calculate the air speed density.
lTo calculate air temperature.
The MAP sensor works on the piezo crystal principal. Piezo crystals are pressure sensitive and will oscillate in
accordance to changes in air pressure. The MAP sensor produces a voltage between 0 and 5 volts proportional to
the pressure level of the air in the inlet manifold. A reading of 0 volts indicates a low pressure and a reading of 5 volts
indicates a high pressure.
The IAT portion of the sensor works as a Negative Temperature Co-efficient (NTC) sensor. As air temperature rises,
the resistance in the sensor decreases. As temperature decreases the resistance in the sensor increases. The ECM
compares the voltage signal to stored values and compensates fuel delivery as necessary.
Input/Output
The ECM provides the MAP/IAT sensor with a 5 volt supply. There are 2 output signals from the sensor, one from the
MAP and one from the IAT. Input to the MAP/IAT comes from pin 8 of the ECM connector C0158. Output from the
MAP is measured at pin 6 of the ECM connector C0158. IAT output signal measured at pin 34 of the ECM connector
C0158. The earth path is via pin 17 of ECM connector C0658. The MAP/IAT sensors share the same common earth.
Page 406 of 1672
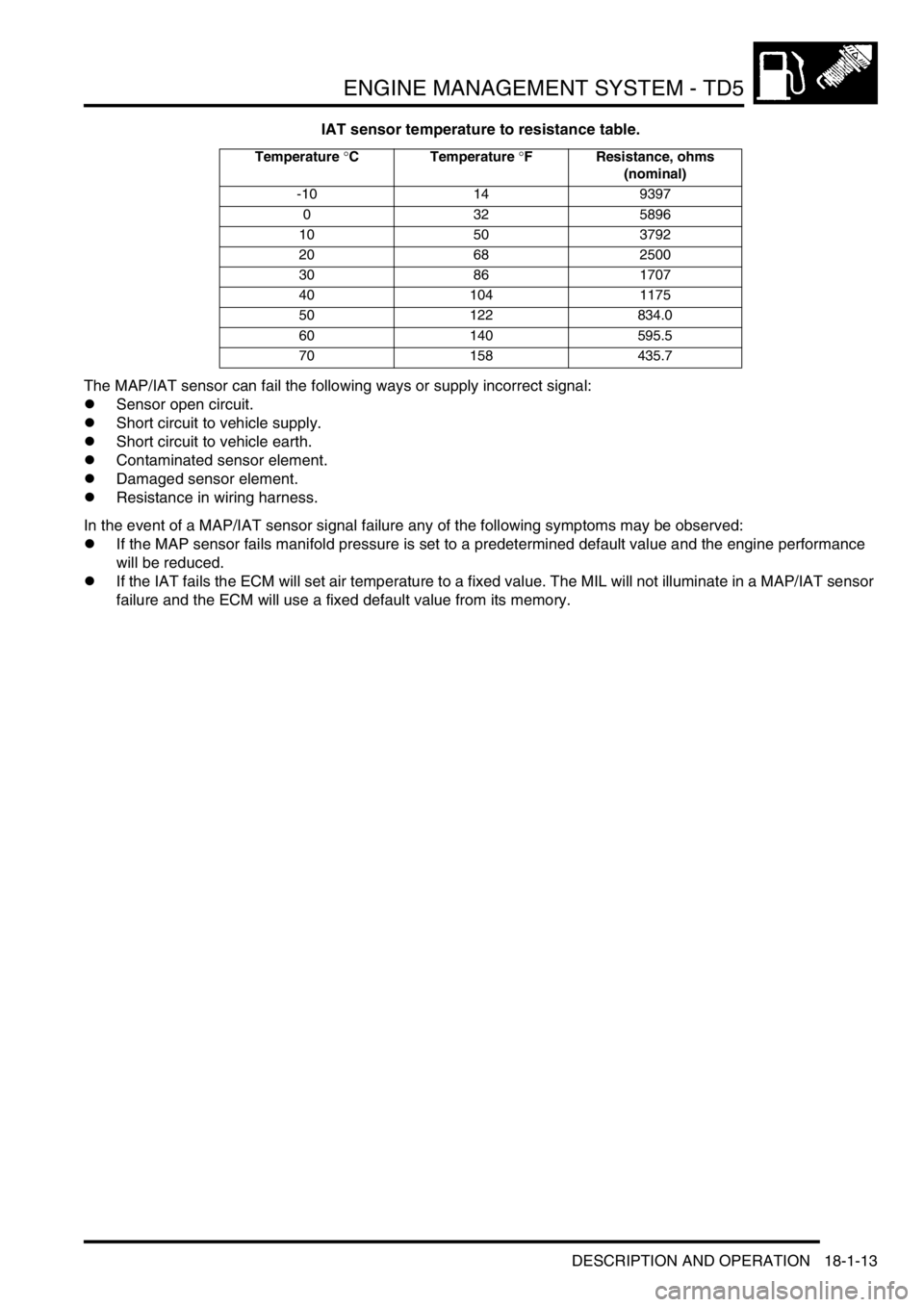
ENGINE MANAGEMENT SYSTEM - TD5
DESCRIPTION AND OPERATION 18-1-13
IAT sensor temperature to resistance table.
The MAP/IAT sensor can fail the following ways or supply incorrect signal:
lSensor open circuit.
lShort circuit to vehicle supply.
lShort circuit to vehicle earth.
lContaminated sensor element.
lDamaged sensor element.
lResistance in wiring harness.
In the event of a MAP/IAT sensor signal failure any of the following symptoms may be observed:
lIf the MAP sensor fails manifold pressure is set to a predetermined default value and the engine performance
will be reduced.
lIf the IAT fails the ECM will set air temperature to a fixed value. The MIL will not illuminate in a MAP/IAT sensor
failure and the ECM will use a fixed default value from its memory.
Temperature °CTemperature °F Resistance, ohms
(nominal)
-10 14 9397
0 32 5896
10 50 3792
20 68 2500
30 86 1707
40 104 1175
50 122 834.0
60 140 595.5
70 158 435.7
Page 407 of 1672
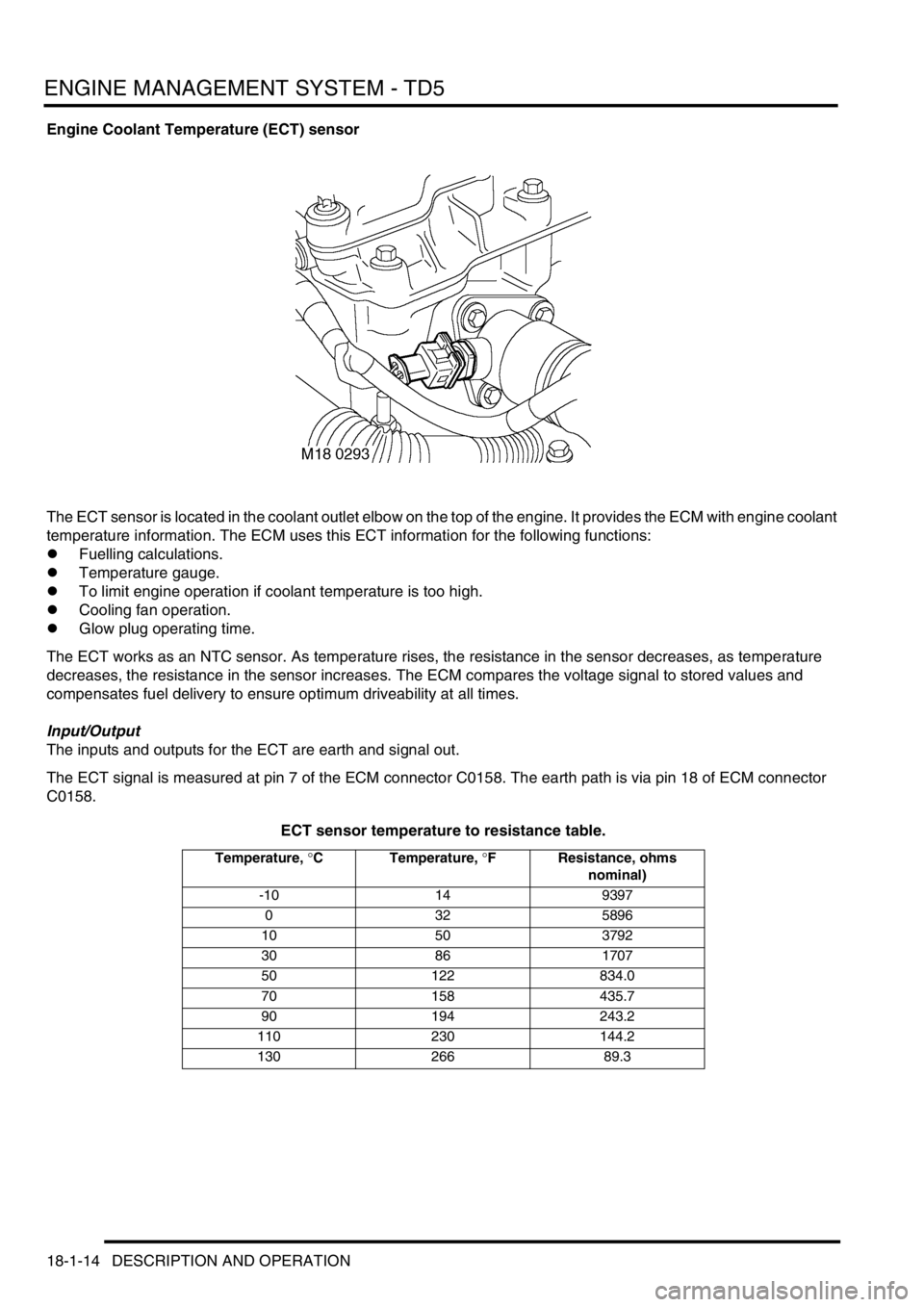
ENGINE MANAGEMENT SYSTEM - TD5
18-1-14 DESCRIPTION AND OPERATION
Engine Coolant Temperature (ECT) sensor
The ECT sensor is located in the coolant outlet elbow on the top of the engine. It provides the ECM with engine coolant
temperature information. The ECM uses this ECT information for the following functions:
lFuelling calculations.
lTemperature gauge.
lTo limit engine operation if coolant temperature is too high.
lCooling fan operation.
lGlow plug operating time.
The ECT works as an NTC sensor. As temperature rises, the resistance in the sensor decreases, as temperature
decreases, the resistance in the sensor increases. The ECM compares the voltage signal to stored values and
compensates fuel delivery to ensure optimum driveability at all times.
Input/Output
The inputs and outputs for the ECT are earth and signal out.
The ECT signal is measured at pin 7 of the ECM connector C0158. The earth path is via pin 18 of ECM connector
C0158.
ECT sensor temperature to resistance table.
Temperature, °C Temperature, °F Resistance, ohms
nominal)
-10 14 9397
0325896
10 50 3792
30 86 1707
50 122 834.0
70 158 435.7
90 194 243.2
110 230 144.2
130 266 89.3
Page 408 of 1672
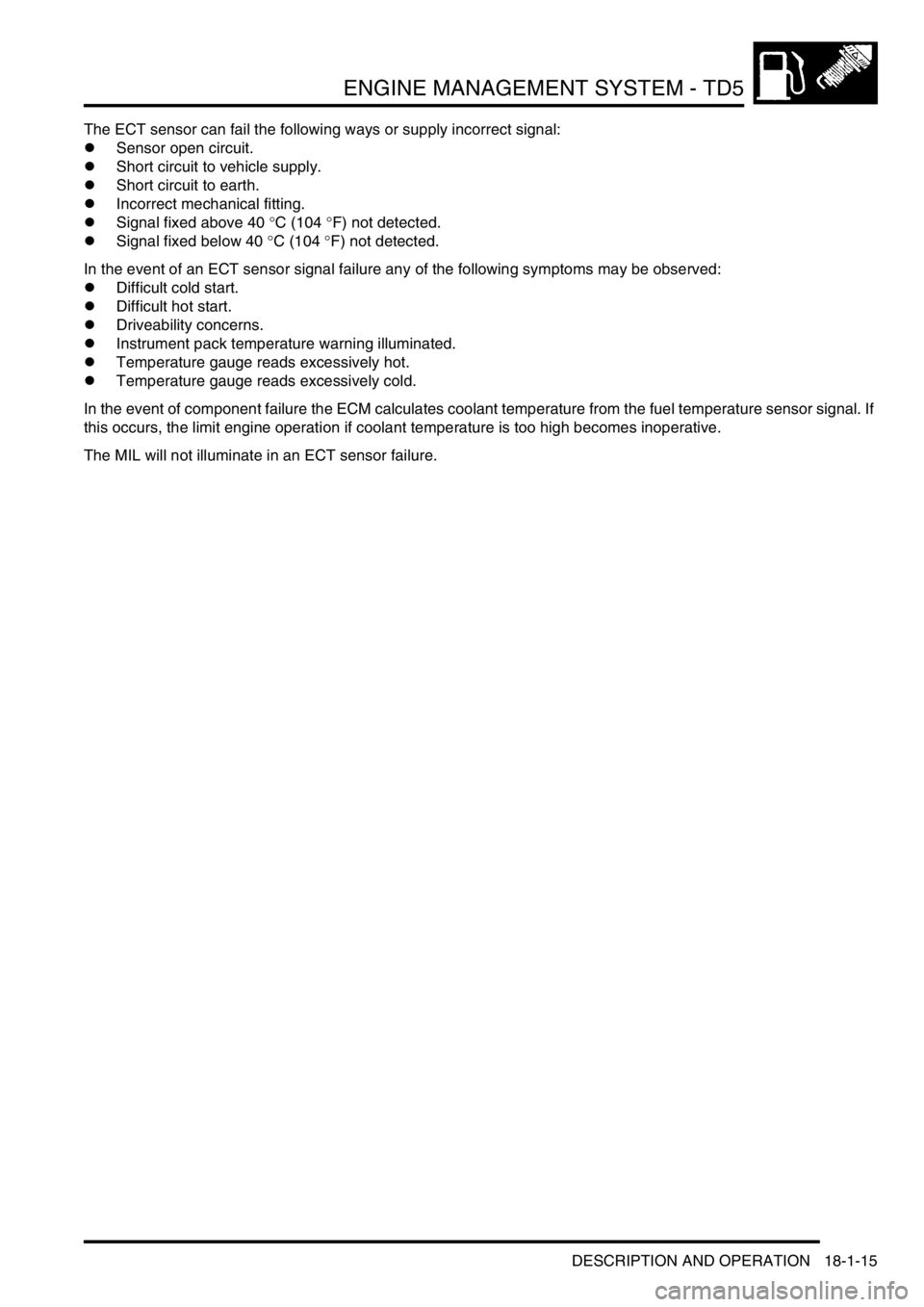
ENGINE MANAGEMENT SYSTEM - TD5
DESCRIPTION AND OPERATION 18-1-15
The ECT sensor can fail the following ways or supply incorrect signal:
lSensor open circuit.
lShort circuit to vehicle supply.
lShort circuit to earth.
lIncorrect mechanical fitting.
lSignal fixed above 40
°C (104 °F) not detected.
lSignal fixed below 40
°C (104 °F) not detected.
In the event of an ECT sensor signal failure any of the following symptoms may be observed:
lDifficult cold start.
lDifficult hot start.
lDriveability concerns.
lInstrument pack temperature warning illuminated.
lTemperature gauge reads excessively hot.
lTemperature gauge reads excessively cold.
In the event of component failure the ECM calculates coolant temperature from the fuel temperature sensor signal. If
this occurs, the limit engine operation if coolant temperature is too high becomes inoperative.
The MIL will not illuminate in an ECT sensor failure.
Page 409 of 1672
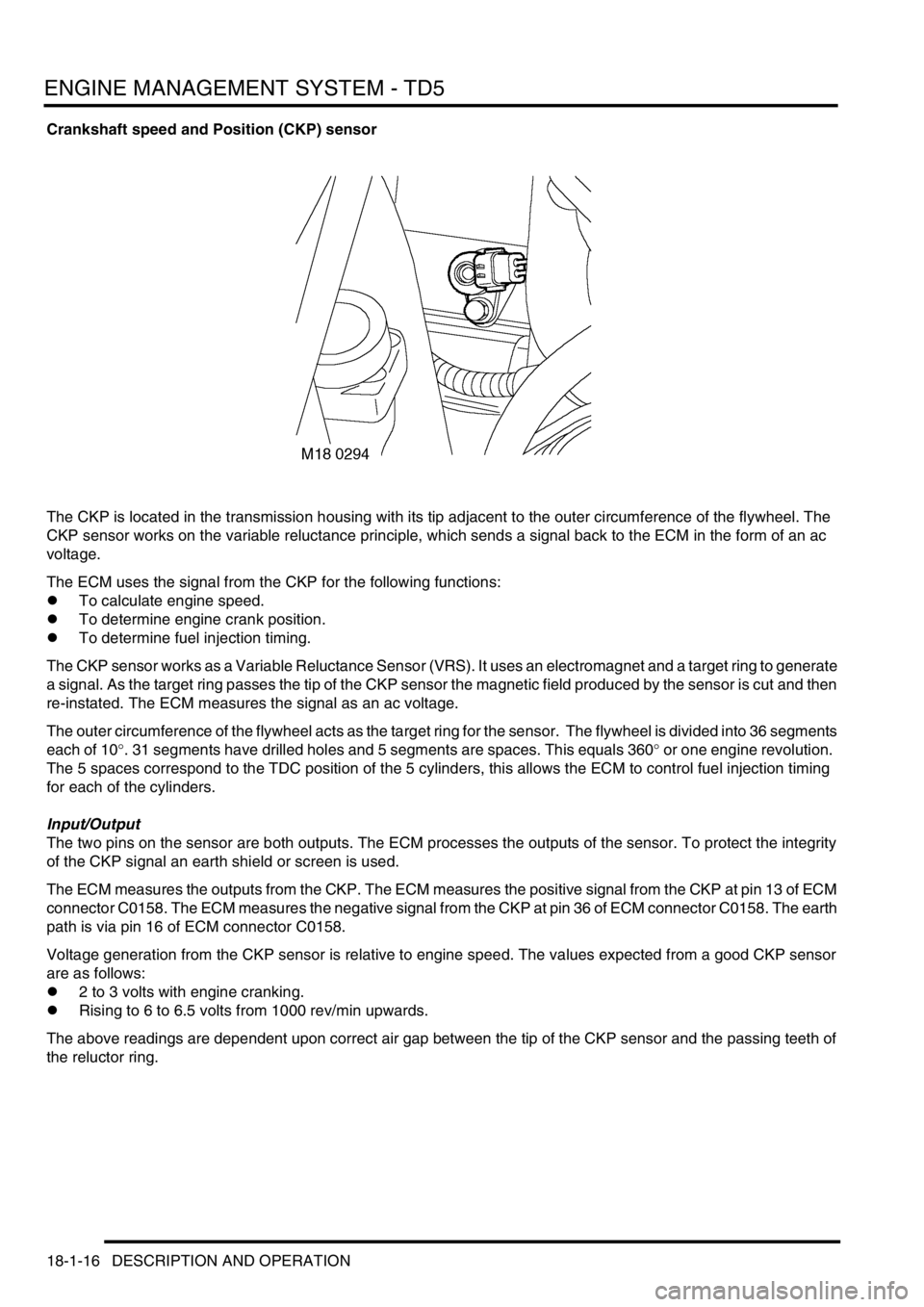
ENGINE MANAGEMENT SYSTEM - TD5
18-1-16 DESCRIPTION AND OPERATION
Crankshaft speed and Position (CKP) sensor
The CKP is located in the transmission housing with its tip adjacent to the outer circumference of the flywheel. The
CKP sensor works on the variable reluctance principle, which sends a signal back to the ECM in the form of an ac
voltage.
The ECM uses the signal from the CKP for the following functions:
lTo calculate engine speed.
lTo determine engine crank position.
lTo determine fuel injection timing.
The CKP sensor works as a Variable Reluctance Sensor (VRS). It uses an electromagnet and a target ring to generate
a signal. As the target ring passes the tip of the CKP sensor the magnetic field produced by the sensor is cut and then
re-instated. The ECM measures the signal as an ac voltage.
The outer circumference of the flywheel acts as the target ring for the sensor. The flywheel is divided into 36 segments
each of 10
°. 31 segments have drilled holes and 5 segments are spaces. This equals 360° or one engine revolution.
The 5 spaces correspond to the TDC position of the 5 cylinders, this allows the ECM to control fuel injection timing
for each of the cylinders.
Input/Output
The two pins on the sensor are both outputs. The ECM processes the outputs of the sensor. To protect the integrity
of the CKP signal an earth shield or screen is used.
The ECM measures the outputs from the CKP. The ECM measures the positive signal from the CKP at pin 13 of ECM
connector C0158. The ECM measures the negative signal from the CKP at pin 36 of ECM connector C0158. The earth
path is via pin 16 of ECM connector C0158.
Voltage generation from the CKP sensor is relative to engine speed. The values expected from a good CKP sensor
are as follows:
l2 to 3 volts with engine cranking.
lRising to 6 to 6.5 volts from 1000 rev/min upwards.
The above readings are dependent upon correct air gap between the tip of the CKP sensor and the passing teeth of
the reluctor ring.
Page 410 of 1672
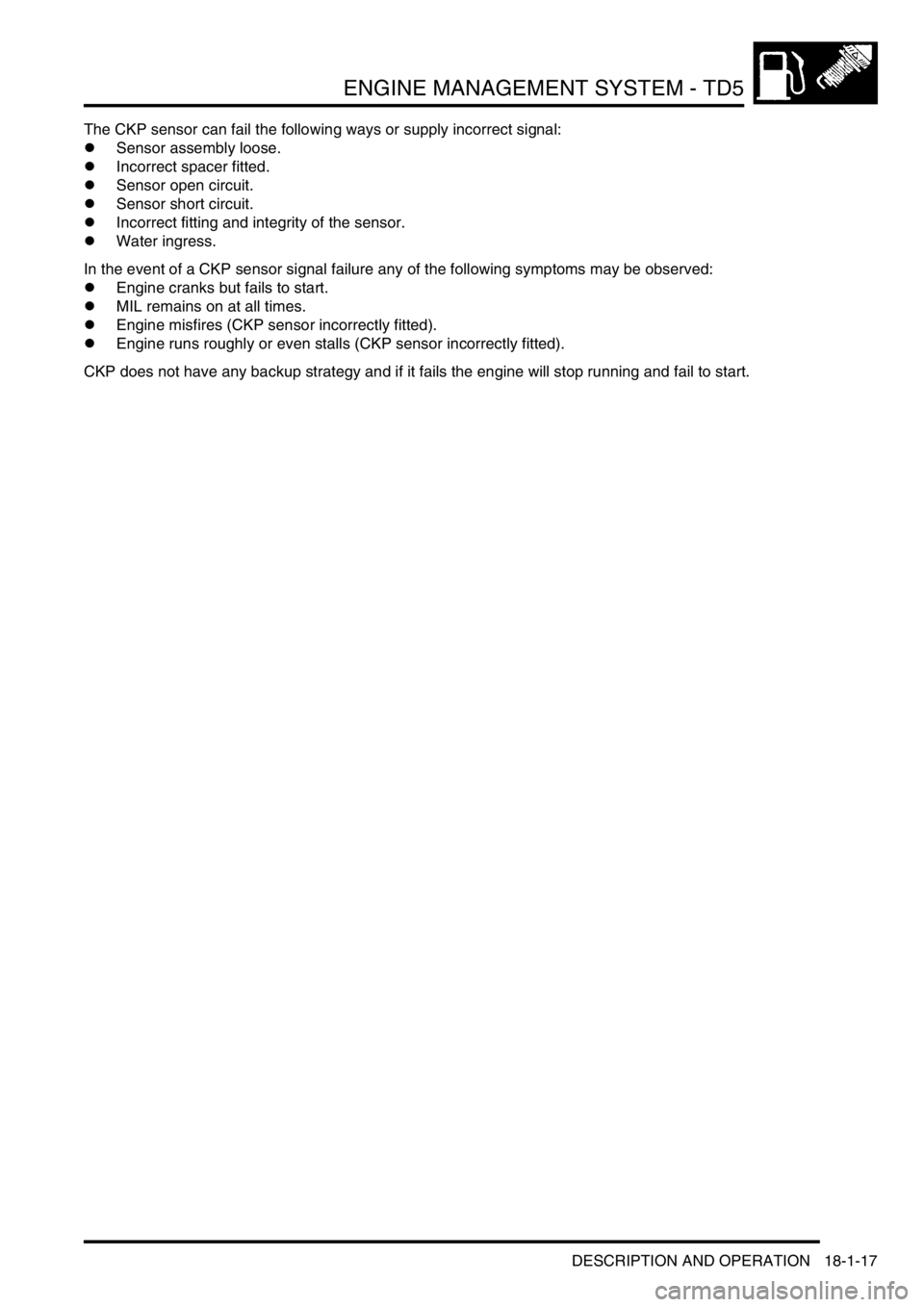
ENGINE MANAGEMENT SYSTEM - TD5
DESCRIPTION AND OPERATION 18-1-17
The CKP sensor can fail the following ways or supply incorrect signal:
lSensor assembly loose.
lIncorrect spacer fitted.
lSensor open circuit.
lSensor short circuit.
lIncorrect fitting and integrity of the sensor.
lWater ingress.
In the event of a CKP sensor signal failure any of the following symptoms may be observed:
lEngine cranks but fails to start.
lMIL remains on at all times.
lEngine misfires (CKP sensor incorrectly fitted).
lEngine runs roughly or even stalls (CKP sensor incorrectly fitted).
CKP does not have any backup strategy and if it fails the engine will stop running and fail to start.
Page 411 of 1672
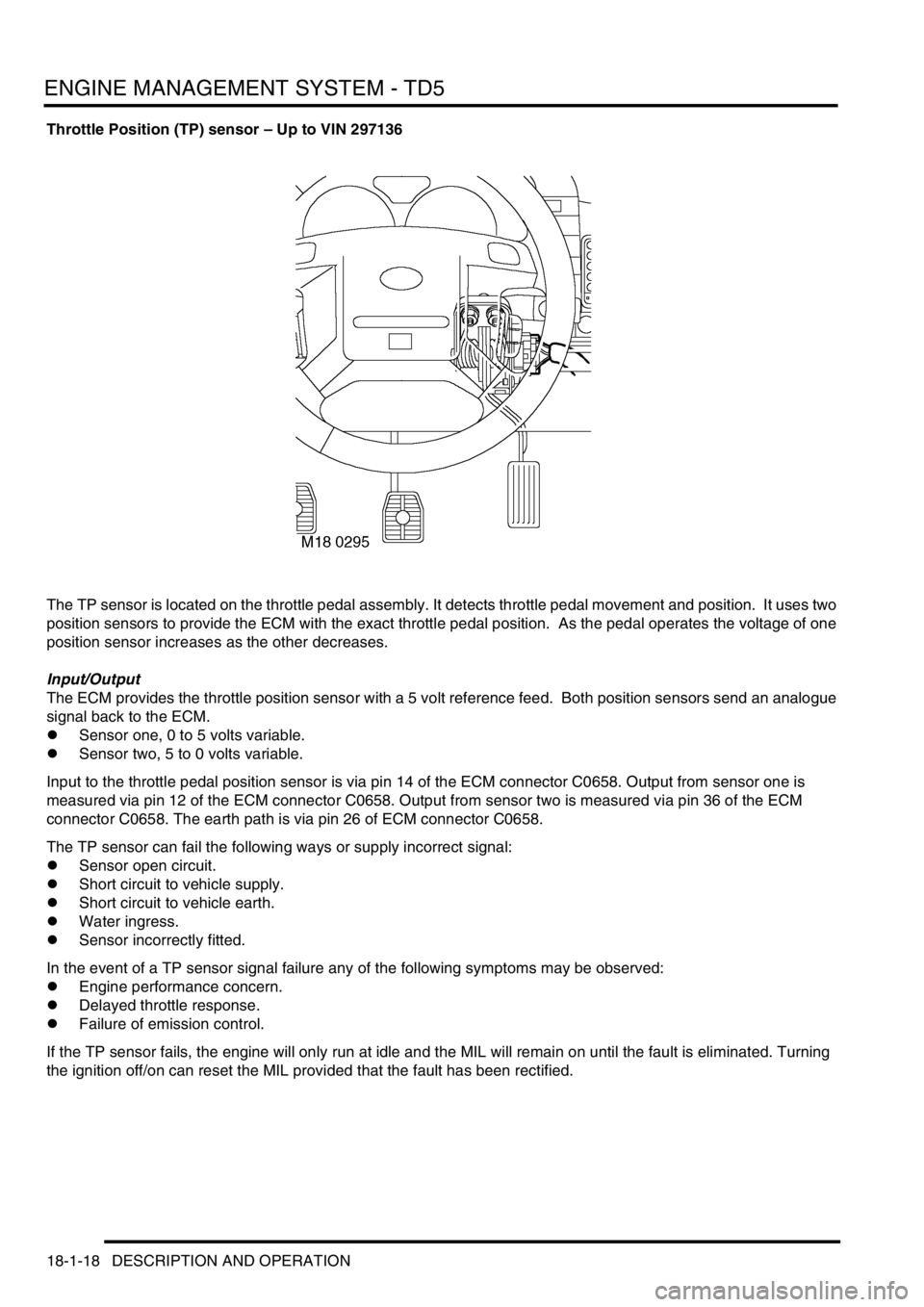
ENGINE MANAGEMENT SYSTEM - TD5
18-1-18 DESCRIPTION AND OPERATION
Throttle Position (TP) sensor – Up to VIN 297136
The TP sensor is located on the throttle pedal assembly. It detects throttle pedal movement and position. It uses two
position sensors to provide the ECM with the exact throttle pedal position. As the pedal operates the voltage of one
position sensor increases as the other decreases.
Input/Output
The ECM provides the throttle position sensor with a 5 volt reference feed. Both position sensors send an analogue
signal back to the ECM.
lSensor one, 0 to 5 volts variable.
lSensor two, 5 to 0 volts variable.
Input to the throttle pedal position sensor is via pin 14 of the ECM connector C0658. Output from sensor one is
measured via pin 12 of the ECM connector C0658. Output from sensor two is measured via pin 36 of the ECM
connector C0658. The earth path is via pin 26 of ECM connector C0658.
The TP sensor can fail the following ways or supply incorrect signal:
lSensor open circuit.
lShort circuit to vehicle supply.
lShort circuit to vehicle earth.
lWater ingress.
lSensor incorrectly fitted.
In the event of a TP sensor signal failure any of the following symptoms may be observed:
lEngine performance concern.
lDelayed throttle response.
lFailure of emission control.
If the TP sensor fails, the engine will only run at idle and the MIL will remain on until the fault is eliminated. Turning
the ignition off/on can reset the MIL provided that the fault has been rectified.
Page 412 of 1672
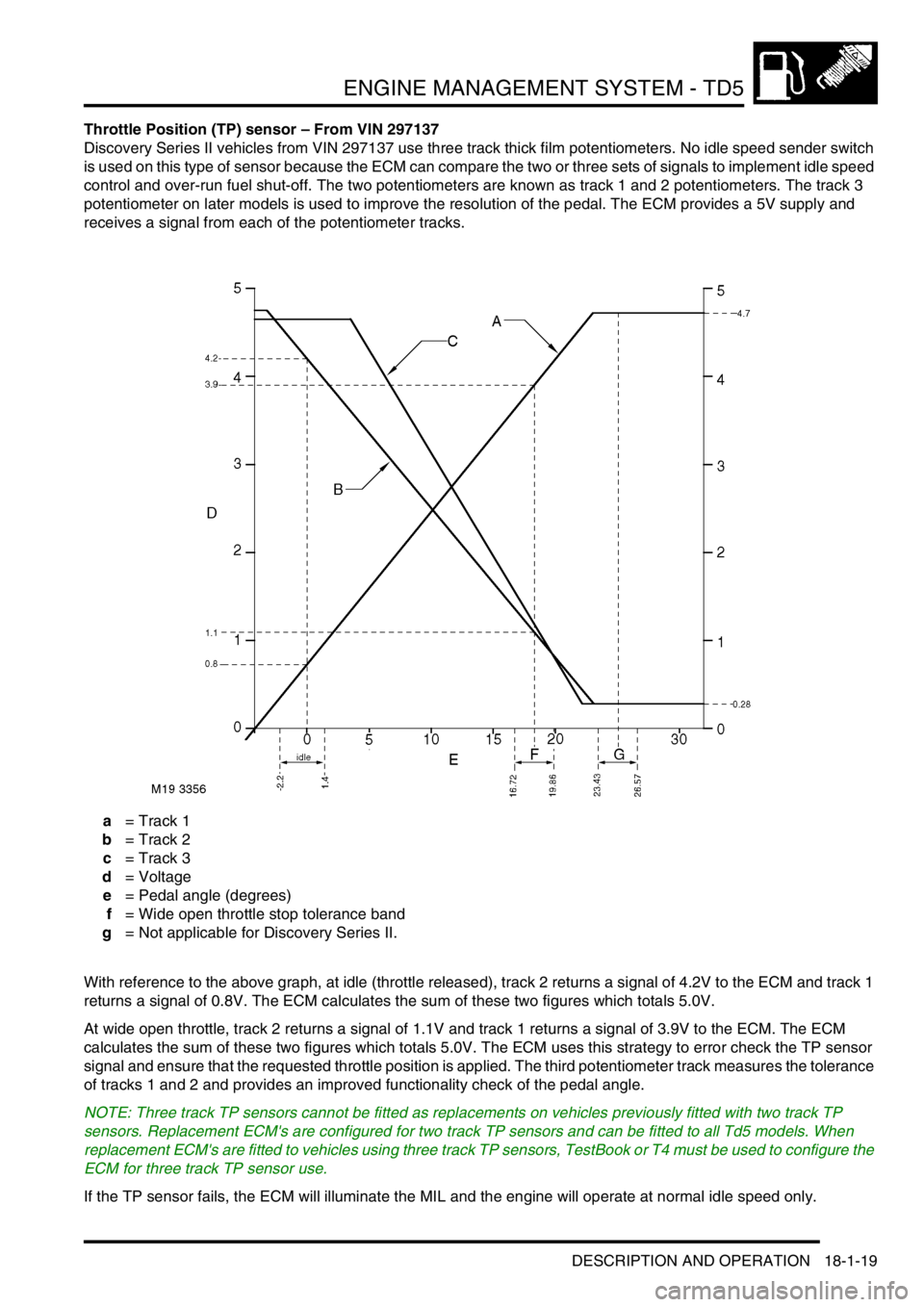
ENGINE MANAGEMENT SYSTEM - TD5
DESCRIPTION AND OPERATION 18-1-19
Throttle Position (TP) sensor – From VIN 297137
Discovery Series II vehicles from VIN 297137 use three track thick film potentiometers. No idle speed sender switch
is used on this type of sensor because the ECM can compare the two or three sets of signals to implement idle speed
control and over-run fuel shut-off. The two potentiometers are known as track 1 and 2 potentiometers. The track 3
potentiometer on later models is used to improve the resolution of the pedal. The ECM provides a 5V supply and
receives a signal from each of the potentiometer tracks.
a = Track 1
b = Track 2
c = Track 3
d = Voltage
e = Pedal angle (degrees)
f = Wide open throttle stop tolerance band
g = Not applicable for Discovery Series II.
With reference to the above graph, at idle (throttle released), track 2 returns a signal of 4.2V to the ECM and track 1
returns a signal of 0.8V. The ECM calculates the sum of these two figures which totals 5.0V.
At wide open throttle, track 2 returns a signal of 1.1V and track 1 returns a signal of 3.9V to the ECM. The ECM
calculates the sum of these two figures which totals 5.0V. The ECM uses this strategy to error check the TP sensor
signal and ensure that the requested throttle position is applied. The third potentiometer track measures the tolerance
of tracks 1 and 2 and provides an improved functionality check of the pedal angle.
NOTE: Three track TP sensors cannot be fitted as replacements on vehicles previously fitted with two track TP
sensors. Replacement ECM's are configured for two track TP sensors and can be fitted to all Td5 models. When
replacement ECM's are fitted to vehicles using three track TP sensors, TestBook or T4 must be used to configure the
ECM for three track TP sensor use.
If the TP sensor fails, the ECM will illuminate the MIL and the engine will operate at normal idle speed only.
Page 413 of 1672
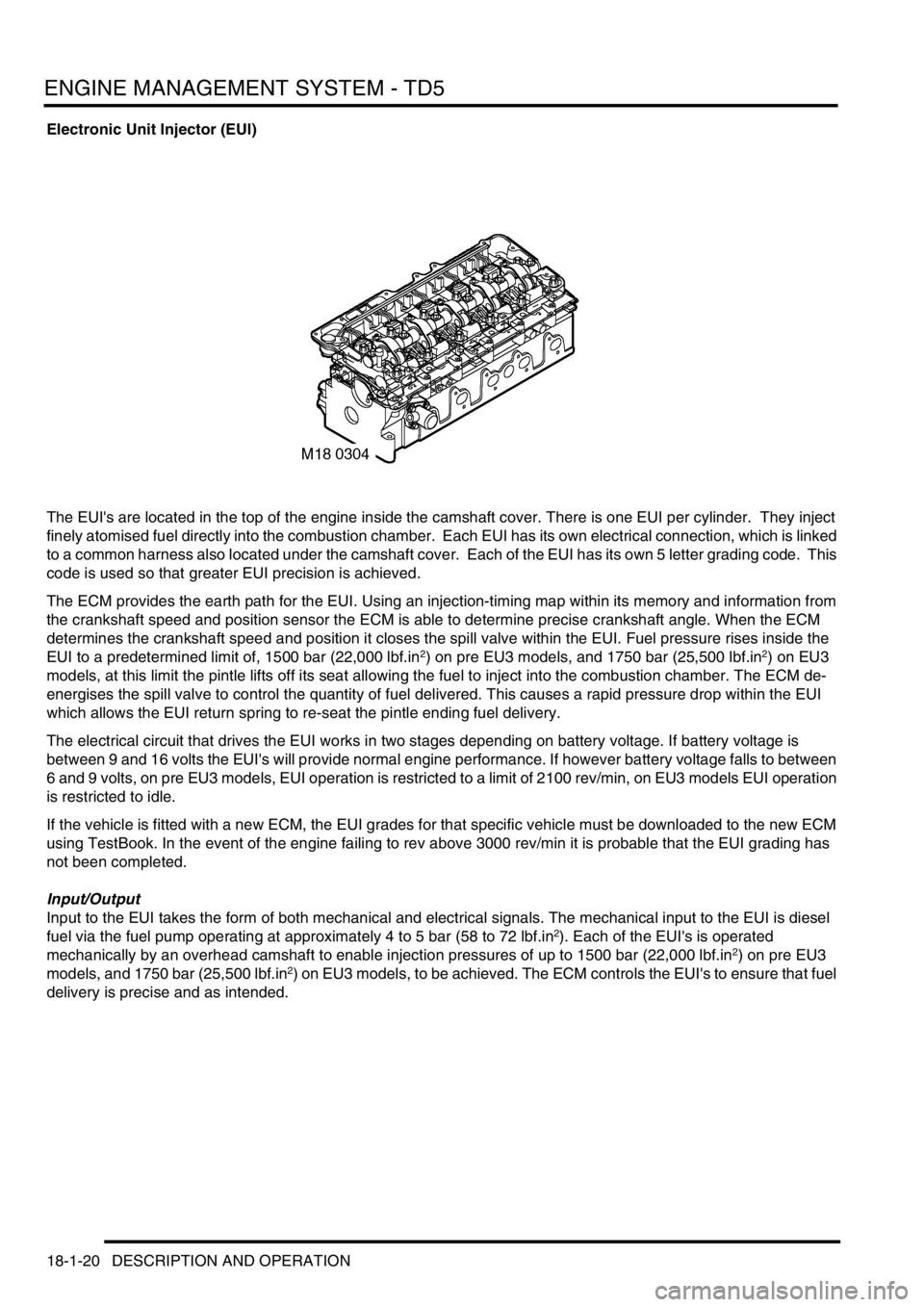
ENGINE MANAGEMENT SYSTEM - TD5
18-1-20 DESCRIPTION AND OPERATION
Electronic Unit Injector (EUI)
The EUI's are located in the top of the engine inside the camshaft cover. There is one EUI per cylinder. They inject
finely atomised fuel directly into the combustion chamber. Each EUI has its own electrical connection, which is linked
to a common harness also located under the camshaft cover. Each of the EUI has its own 5 letter grading code. This
code is used so that greater EUI precision is achieved.
The ECM provides the earth path for the EUI. Using an injection-timing map within its memory and information from
the crankshaft speed and position sensor the ECM is able to determine precise crankshaft angle. When the ECM
determines the crankshaft speed and position it closes the spill valve within the EUI. Fuel pressure rises inside the
EUI to a predetermined limit of, 1500 bar (22,000 lbf.in
2) on pre EU3 models, and 1750 bar (25,500 lbf.in2) on EU3
models, at this limit the pintle lifts off its seat allowing the fuel to inject into the combustion chamber. The ECM de-
energises the spill valve to control the quantity of fuel delivered. This causes a rapid pressure drop within the EUI
which allows the EUI return spring to re-seat the pintle ending fuel delivery.
The electrical circuit that drives the EUI works in two stages depending on battery voltage. If battery voltage is
between 9 and 16 volts the EUI's will provide normal engine performance. If however battery voltage falls to between
6 and 9 volts, on pre EU3 models, EUI operation is restricted to a limit of 2100 rev/min, on EU3 models EUI operation
is restricted to idle.
If the vehicle is fitted with a new ECM, the EUI grades for that specific vehicle must be downloaded to the new ECM
using TestBook. In the event of the engine failing to rev above 3000 rev/min it is probable that the EUI grading has
not been completed.
Input/Output
Input to the EUI takes the form of both mechanical and electrical signals. The mechanical input to the EUI is diesel
fuel via the fuel pump operating at approximately 4 to 5 bar (58 to 72 lbf.in
2). Each of the EUI's is operated
mechanically by an overhead camshaft to enable injection pressures of up to 1500 bar (22,000 lbf.in2) on pre EU3
models, and 1750 bar (25,500 lbf.in2) on EU3 models, to be achieved. The ECM controls the EUI's to ensure that fuel
delivery is precise and as intended.
Page 415 of 1672
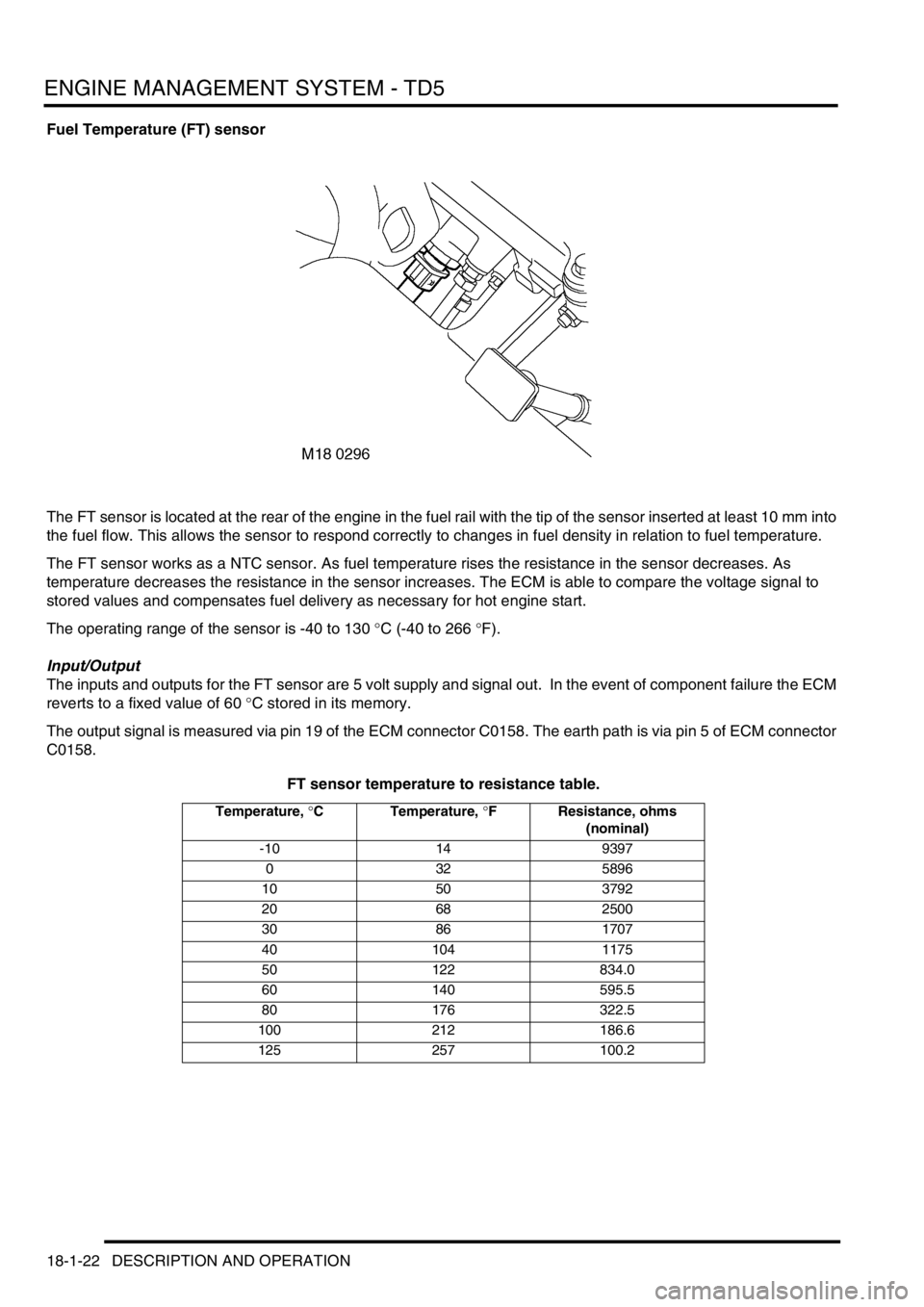
ENGINE MANAGEMENT SYSTEM - TD5
18-1-22 DESCRIPTION AND OPERATION
Fuel Temperature (FT) sensor
The FT sensor is located at the rear of the engine in the fuel rail with the tip of the sensor inserted at least 10 mm into
the fuel flow. This allows the sensor to respond correctly to changes in fuel density in relation to fuel temperature.
The FT sensor works as a NTC sensor. As fuel temperature rises the resistance in the sensor decreases. As
temperature decreases the resistance in the sensor increases. The ECM is able to compare the voltage signal to
stored values and compensates fuel delivery as necessary for hot engine start.
The operating range of the sensor is -40 to 130
°C (-40 to 266 °F).
Input/Output
The inputs and outputs for the FT sensor are 5 volt supply and signal out. In the event of component failure the ECM
reverts to a fixed value of 60
°C stored in its memory.
The output signal is measured via pin 19 of the ECM connector C0158. The earth path is via pin 5 of ECM connector
C0158.
FT sensor temperature to resistance table.
Temperature, °C Temperature, °F Resistance, ohms
(nominal)
-10 14 9397
0325896
10 50 3792
20 68 2500
30 86 1707
40 104 1175
50 122 834.0
60 140 595.5
80 176 322.5
100 212 186.6
125 257 100.2