engine coolant LAND ROVER DISCOVERY 2002 Workshop Manual
[x] Cancel search | Manufacturer: LAND ROVER, Model Year: 2002, Model line: DISCOVERY, Model: LAND ROVER DISCOVERY 2002Pages: 1672, PDF Size: 46.1 MB
Page 10 of 1672
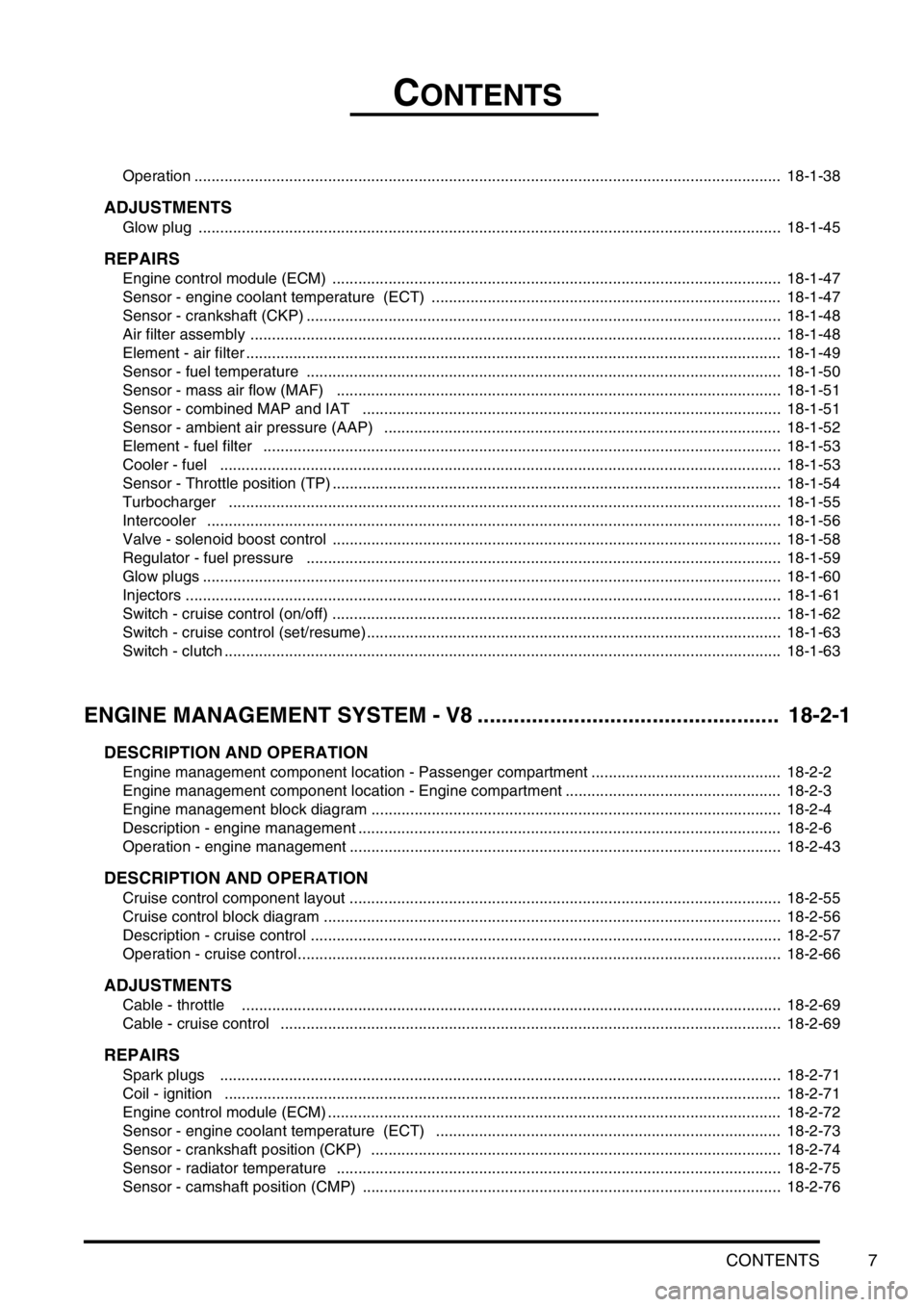
CONTENTS
CONTENTS 7
Operation ........................................................................................................................................ 18-1-38
ADJUSTMENTS
Glow plug ....................................................................................................................................... 18-1-45
REPAIRS
Engine control module (ECM) ........................................................................................................ 18-1-47
Sensor - engine coolant temperature (ECT) ................................................................................. 18-1-47
Sensor - crankshaft (CKP) .............................................................................................................. 18-1-48
Air filter assembly ........................................................................................................................... 18-1-48
Element - air filter ............................................................................................................................ 18-1-49
Sensor - fuel temperature .............................................................................................................. 18-1-50
Sensor - mass air flow (MAF) ....................................................................................................... 18-1-51
Sensor - combined MAP and IAT ................................................................................................. 18-1-51
Sensor - ambient air pressure (AAP) ............................................................................................ 18-1-52
Element - fuel filter ........................................................................................................................ 18-1-53
Cooler - fuel .................................................................................................................................. 18-1-53
Sensor - Throttle position (TP) ........................................................................................................ 18-1-54
Turbocharger ................................................................................................................................ 18-1-55
Intercooler ..................................................................................................................................... 18-1-56
Valve - solenoid boost control ........................................................................................................ 18-1-58
Regulator - fuel pressure .............................................................................................................. 18-1-59
Glow plugs ...................................................................................................................................... 18-1-60
Injectors .......................................................................................................................................... 18-1-61
Switch - cruise control (on/off) ........................................................................................................ 18-1-62
Switch - cruise control (set/resume) ................................................................................................ 18-1-63
Switch - clutch ................................................................................................................................. 18-1-63
ENGINE MANAGEMENT SYSTEM - V8 .................................................. 18-2-1
DESCRIPTION AND OPERATION
Engine management component location - Passenger compartment ............................................ 18-2-2
Engine management component location - Engine compartment .................................................. 18-2-3
Engine management block diagram ............................................................................................... 18-2-4
Description - engine management .................................................................................................. 18-2-6
Operation - engine management .................................................................................................... 18-2-43
DESCRIPTION AND OPERATION
Cruise control component layout .................................................................................................... 18-2-55
Cruise control block diagram .......................................................................................................... 18-2-56
Description - cruise control ............................................................................................................. 18-2-57
Operation - cruise control................................................................................................................ 18-2-66
ADJUSTMENTS
Cable - throttle ............................................................................................................................. 18-2-69
Cable - cruise control .................................................................................................................... 18-2-69
REPAIRS
Spark plugs .................................................................................................................................. 18-2-71
Coil - ignition ................................................................................................................................. 18-2-71
Engine control module (ECM) ......................................................................................................... 18-2-72
Sensor - engine coolant temperature (ECT) ................................................................................ 18-2-73
Sensor - crankshaft position (CKP) ............................................................................................... 18-2-74
Sensor - radiator temperature ....................................................................................................... 18-2-75
Sensor - camshaft position (CMP) ................................................................................................. 18-2-76
Page 32 of 1672
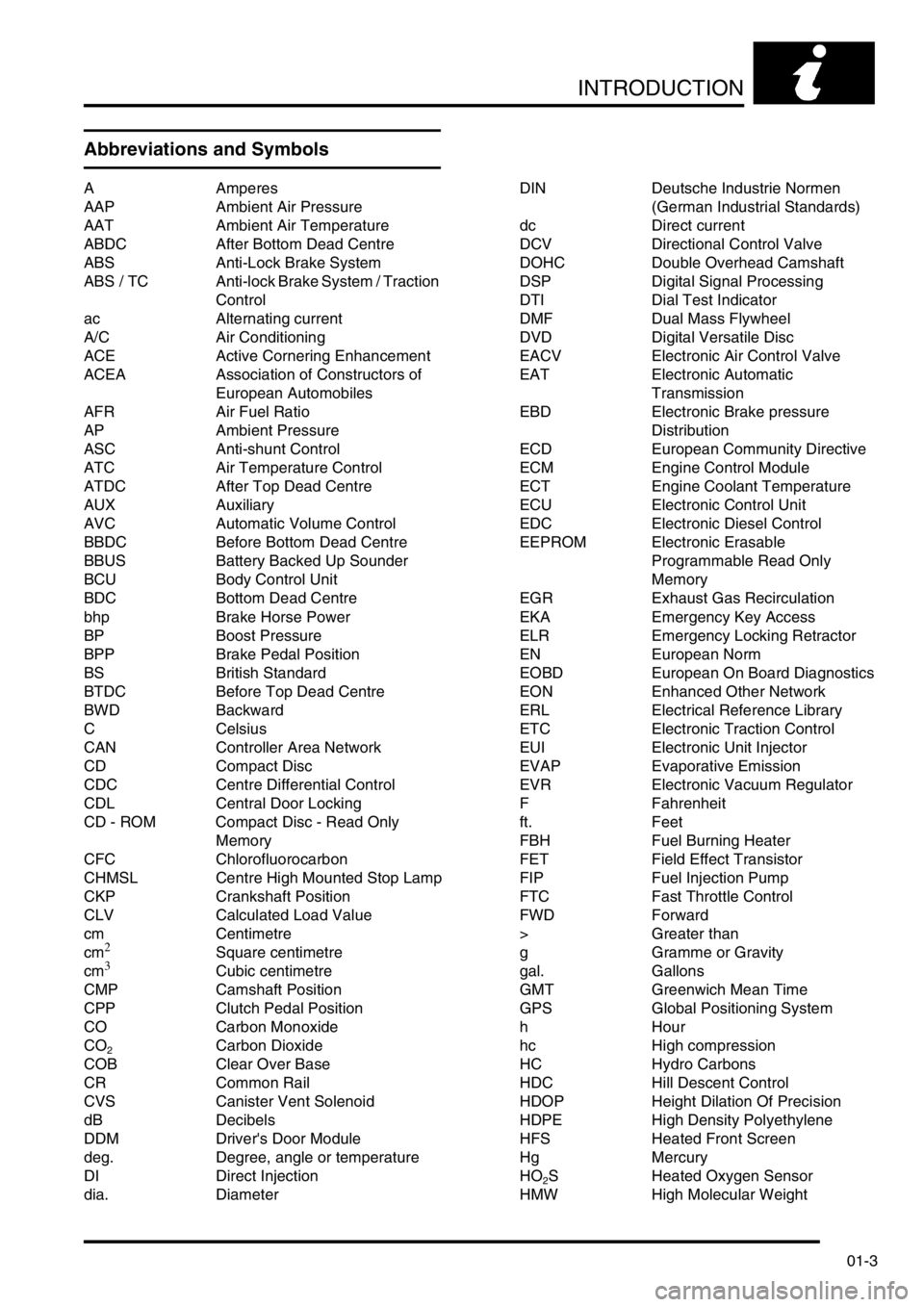
INTRODUCTION
01-3
Abbreviations and Symbols
A Amperes
AAP Ambient Air Pressure
AAT Ambient Air Temperature
ABDC After Bottom Dead Centre
ABS Anti-Lock Brake System
ABS / TC Anti-lock Brake System / Traction
Control
ac Alternating current
A/C Air Conditioning
ACE Active Cornering Enhancement
ACEA Association of Constructors of
European Automobiles
AFR Air Fuel Ratio
AP Ambient Pressure
ASC Anti-shunt Control
ATC Air Temperature Control
ATDC After Top Dead Centre
AUX Auxiliary
AVC Automatic Volume Control
BBDC Before Bottom Dead Centre
BBUS Battery Backed Up Sounder
BCU Body Control Unit
BDC Bottom Dead Centre
bhp Brake Horse Power
BP Boost Pressure
BPP Brake Pedal Position
BS British Standard
BTDC Before Top Dead Centre
BWD Backward
C Celsius
CAN Controller Area Network
CD Compact Disc
CDC Centre Differential Control
CDL Central Door Locking
CD - ROM Compact Disc - Read Only
Memory
CFC Chlorofluorocarbon
CHMSL Centre High Mounted Stop Lamp
CKP Crankshaft Position
CLV Calculated Load Value
cm Centimetre
cm
2Square centimetre
cm3Cubic centimetre
CMP Camshaft Position
CPP Clutch Pedal Position
CO Carbon Monoxide
CO
2Carbon Dioxide
COB Clear Over Base
CR Common Rail
CVS Canister Vent Solenoid
dB Decibels
DDM Driver's Door Module
deg. Degree, angle or temperature
DI Direct Injection
dia. DiameterDIN Deutsche Industrie Normen
(German Industrial Standards)
dc Direct current
DCV Directional Control Valve
DOHC Double Overhead Camshaft
DSP Digital Signal Processing
DTI Dial Test Indicator
DMF Dual Mass Flywheel
DVD Digital Versatile Disc
EACV Electronic Air Control Valve
EAT Electronic Automatic
Transmission
EBD Electronic Brake pressure
Distribution
ECD European Community Directive
ECM Engine Control Module
ECT Engine Coolant Temperature
ECU Electronic Control Unit
EDC Electronic Diesel Control
EEPROM Electronic Erasable
Programmable Read Only
Memory
EGR Exhaust Gas Recirculation
EKA Emergency Key Access
ELR Emergency Locking Retractor
EN European Norm
EOBD European On Board Diagnostics
EON Enhanced Other Network
ERL Electrical Reference Library
ETC Electronic Traction Control
EUI Electronic Unit Injector
EVAP Evaporative Emission
EVR Electronic Vacuum Regulator
F Fahrenheit
ft. Feet
FBH Fuel Burning Heater
FET Field Effect Transistor
FIP Fuel Injection Pump
FTC Fast Throttle Control
FWD Forward
> Greater than
g Gramme or Gravity
gal. Gallons
GMT Greenwich Mean Time
GPS Global Positioning System
hHour
hc High compression
HC Hydro Carbons
HDC Hill Descent Control
HDOP Height Dilation Of Precision
HDPE High Density Polyethylene
HFS Heated Front Screen
Hg Mercury
HO
2S Heated Oxygen Sensor
HMW High Molecular Weight
Page 37 of 1672
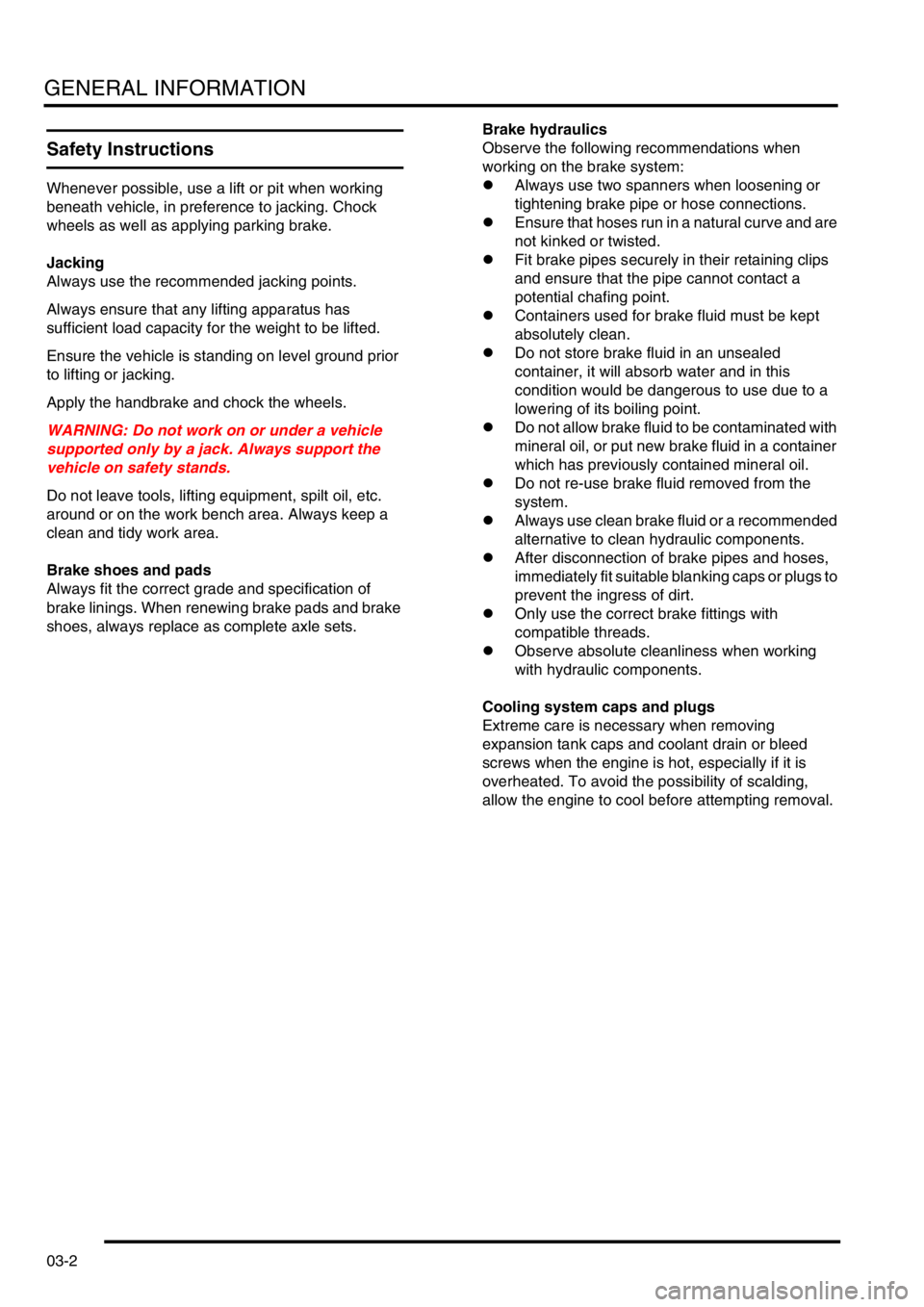
GENERAL INFORMATION
03-2
Safety Instructions
Whenever possible, use a lift or pit when working
beneath vehicle, in preference to jacking. Chock
wheels as well as applying parking brake.
Jacking
Always use the recommended jacking points.
Always ensure that any lifting apparatus has
sufficient load capacity for the weight to be lifted.
Ensure the vehicle is standing on level ground prior
to lifting or jacking.
Apply the handbrake and chock the wheels.
WARNING: Do not work on or under a vehicle
supported only by a jack. Always support the
vehicle on safety stands.
Do not leave tools, lifting equipment, spilt oil, etc.
around or on the work bench area. Always keep a
clean and tidy work area.
Brake shoes and pads
Always fit the correct grade and specification of
brake linings. When renewing brake pads and brake
shoes, always replace as complete axle sets.Brake hydraulics
Observe the following recommendations when
working on the brake system:
lAlways use two spanners when loosening or
tightening brake pipe or hose connections.
lEnsure that hoses run in a natural curve and are
not kinked or twisted.
lFit brake pipes securely in their retaining clips
and ensure that the pipe cannot contact a
potential chafing point.
lContainers used for brake fluid must be kept
absolutely clean.
lDo not store brake fluid in an unsealed
container, it will absorb water and in this
condition would be dangerous to use due to a
lowering of its boiling point.
lDo not allow brake fluid to be contaminated with
mineral oil, or put new brake fluid in a container
which has previously contained mineral oil.
lDo not re-use brake fluid removed from the
system.
lAlways use clean brake fluid or a recommended
alternative to clean hydraulic components.
lAfter disconnection of brake pipes and hoses,
immediately fit suitable blanking caps or plugs to
prevent the ingress of dirt.
lOnly use the correct brake fittings with
compatible threads.
lObserve absolute cleanliness when working
with hydraulic components.
Cooling system caps and plugs
Extreme care is necessary when removing
expansion tank caps and coolant drain or bleed
screws when the engine is hot, especially if it is
overheated. To avoid the possibility of scalding,
allow the engine to cool before attempting removal.
Page 52 of 1672
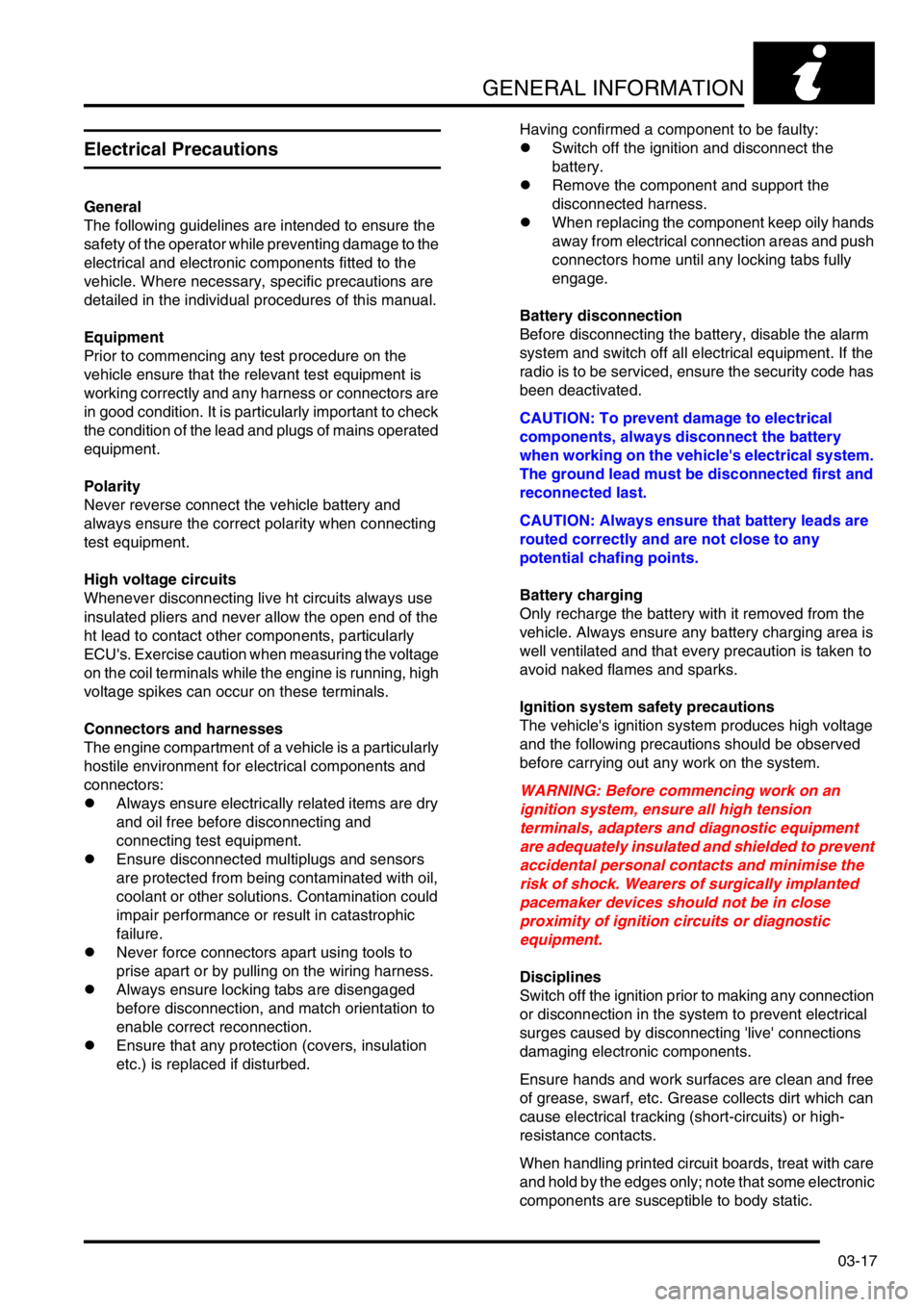
GENERAL INFORMATION
03-17
Electrical Precautions
General
The following guidelines are intended to ensure the
safety of the operator while preventing damage to the
electrical and electronic components fitted to the
vehicle. Where necessary, specific precautions are
detailed in the individual procedures of this manual.
Equipment
Prior to commencing any test procedure on the
vehicle ensure that the relevant test equipment is
working correctly and any harness or connectors are
in good condition. It is particularly important to check
the condition of the lead and plugs of mains operated
equipment.
Polarity
Never reverse connect the vehicle battery and
always ensure the correct polarity when connecting
test equipment.
High voltage circuits
Whenever disconnecting live ht circuits always use
insulated pliers and never allow the open end of the
ht lead to contact other components, particularly
ECU's. Exercise caution when measuring the voltage
on the coil terminals while the engine is running, high
voltage spikes can occur on these terminals.
Connectors and harnesses
The engine compartment of a vehicle is a particularly
hostile environment for electrical components and
connectors:
lAlways ensure electrically related items are dry
and oil free before disconnecting and
connecting test equipment.
lEnsure disconnected multiplugs and sensors
are protected from being contaminated with oil,
coolant or other solutions. Contamination could
impair performance or result in catastrophic
failure.
lNever force connectors apart using tools to
prise apart or by pulling on the wiring harness.
lAlways ensure locking tabs are disengaged
before disconnection, and match orientation to
enable correct reconnection.
lEnsure that any protection (covers, insulation
etc.) is replaced if disturbed.Having confirmed a component to be faulty:
lSwitch off the ignition and disconnect the
battery.
lRemove the component and support the
disconnected harness.
lWhen replacing the component keep oily hands
away from electrical connection areas and push
connectors home until any locking tabs fully
engage.
Battery disconnection
Before disconnecting the battery, disable the alarm
system and switch off all electrical equipment. If the
radio is to be serviced, ensure the security code has
been deactivated.
CAUTION: To prevent damage to electrical
components, always disconnect the battery
when working on the vehicle's electrical system.
The ground lead must be disconnected first and
reconnected last.
CAUTION: Always ensure that battery leads are
routed correctly and are not close to any
potential chafing points.
Battery charging
Only recharge the battery with it removed from the
vehicle. Always ensure any battery charging area is
well ventilated and that every precaution is taken to
avoid naked flames and sparks.
Ignition system safety precautions
The vehicle's ignition system produces high voltage
and the following precautions should be observed
before carrying out any work on the system.
WARNING: Before commencing work on an
ignition system, ensure all high tension
terminals, adapters and diagnostic equipment
are adequately insulated and shielded to prevent
accidental personal contacts and minimise the
risk of shock. Wearers of surgically implanted
pacemaker devices should not be in close
proximity of ignition circuits or diagnostic
equipment.
Disciplines
Switch off the ignition prior to making any connection
or disconnection in the system to prevent electrical
surges caused by disconnecting 'live' connections
damaging electronic components.
Ensure hands and work surfaces are clean and free
of grease, swarf, etc. Grease collects dirt which can
cause electrical tracking (short-circuits) or high-
resistance contacts.
When handling printed circuit boards, treat with care
and hold by the edges only; note that some electronic
components are susceptible to body static.
Page 72 of 1672
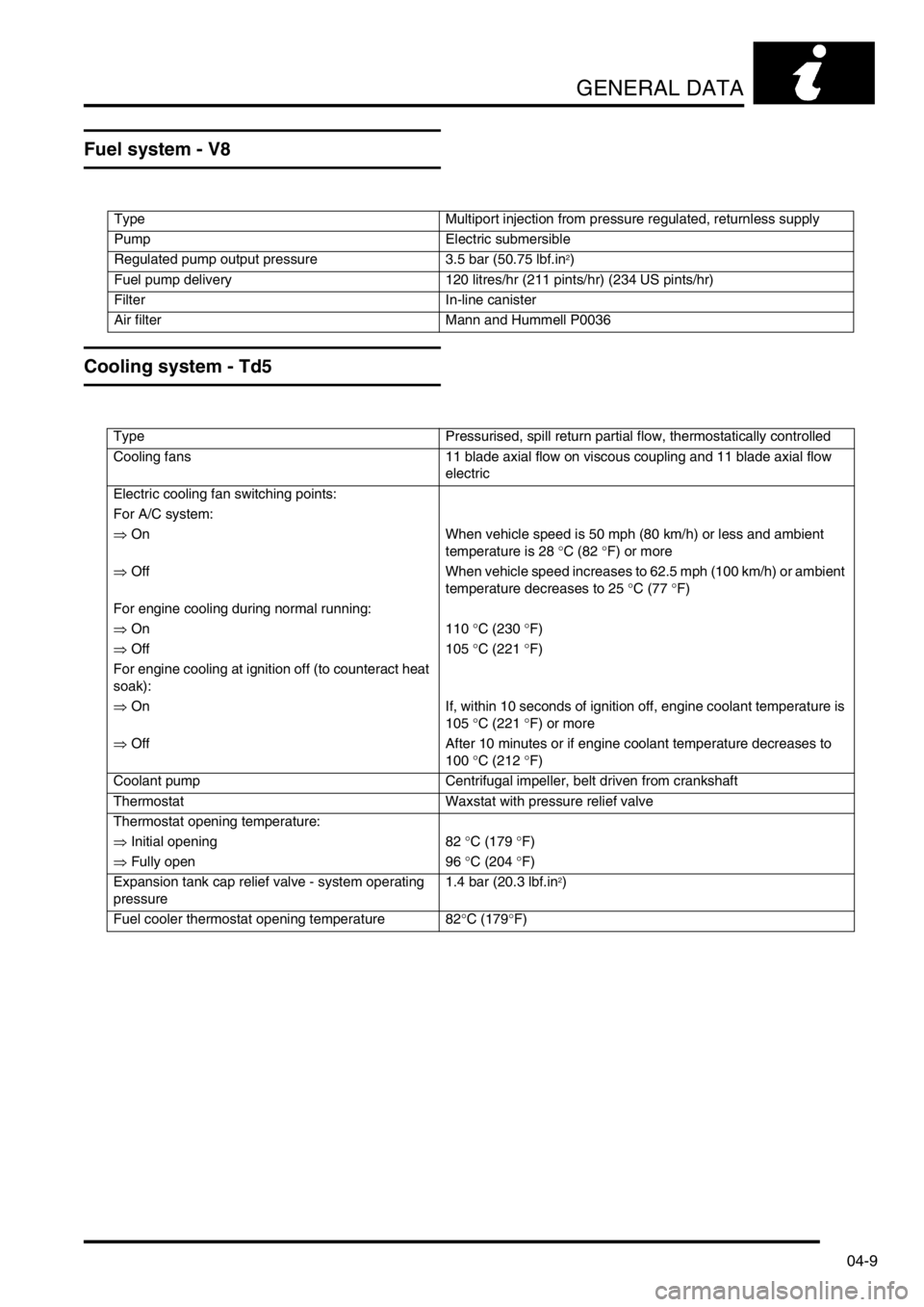
GENERAL DATA
04-9
Fuel system - V8
Cooling system - Td5
Type Multiport injection from pressure regulated, returnless supply
Pump Electric submersible
Regulated pump output pressure 3.5 bar (50.75 lbf.in
2)
Fuel pump delivery 120 litres/hr (211 pints/hr) (234 US pints/hr)
Filter In-line canister
Air filter Mann and Hummell P0036
Type Pressurised, spill return partial flow, thermostatically controlled
Cooling fans 11 blade axial flow on viscous coupling and 11 blade axial flow
electric
Electric cooling fan switching points:
For A/C system:
On When vehicle speed is 50 mph (80 km/h) or less and ambient
temperature is 28 °C (82 °F) or more
Off When vehicle speed increases to 62.5 mph (100 km/h) or ambient
temperature decreases to 25 °C (77 °F)
For engine cooling during normal running:
On 110 °C (230 °F)
Off 105 °C (221 °F)
For engine cooling at ignition off (to counteract heat
soak):
On If, within 10 seconds of ignition off, engine coolant temperature is
105 °C (221 °F) or more
Off After 10 minutes or if engine coolant temperature decreases to
100 °C (212 °F)
Coolant pump Centrifugal impeller, belt driven from crankshaft
Thermostat Waxstat with pressure relief valve
Thermostat opening temperature:
Initial opening 82 °C (179 °F)
Fully open 96 °C (204 °F)
Expansion tank cap relief valve - system operating
pressure1.4 bar (20.3 lbf.in
2)
Fuel cooler thermostat opening temperature 82°C (179°F)
Page 73 of 1672
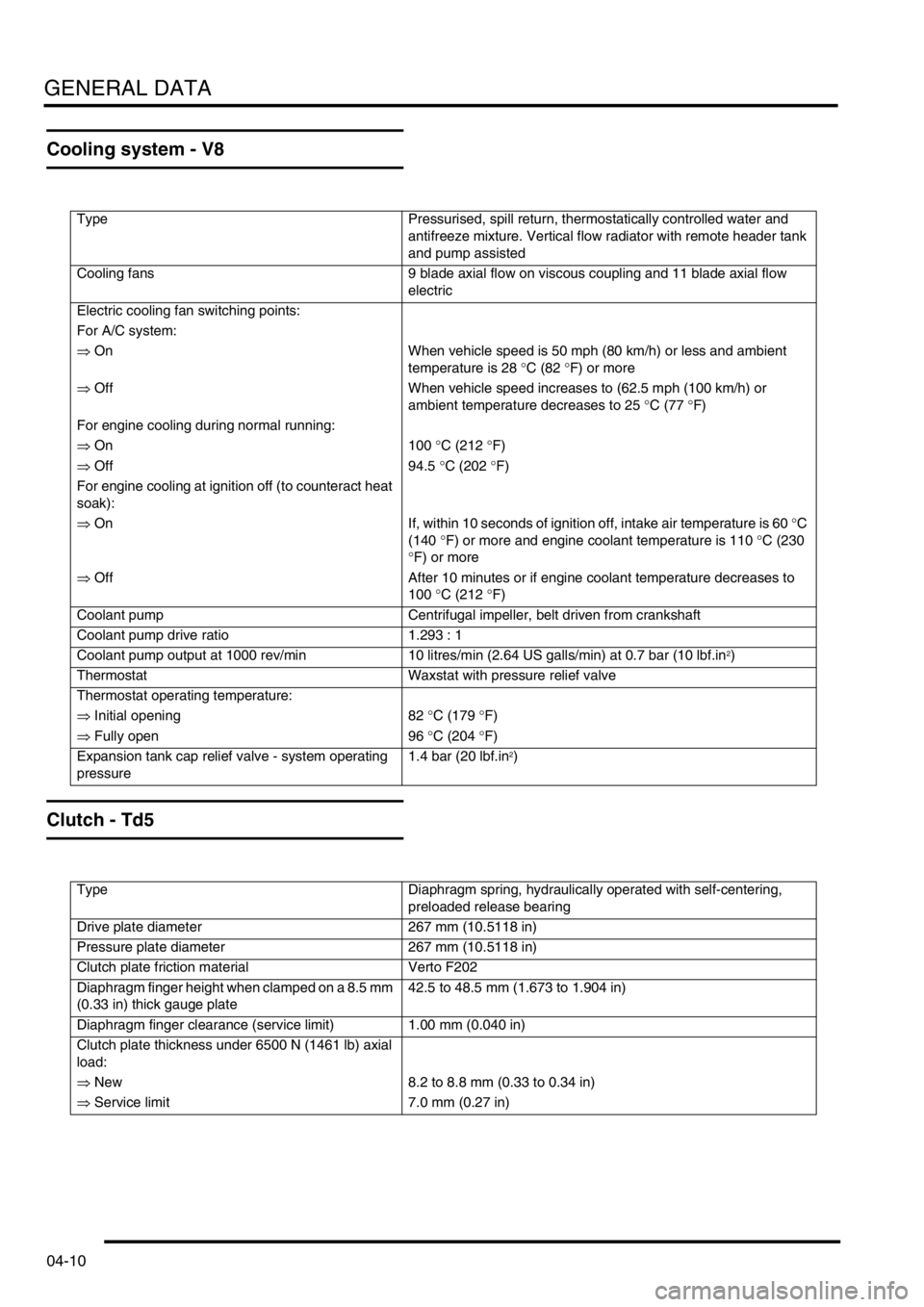
GENERAL DATA
04-10
Cooling system - V8
Clutch - Td5
Type Pressurised, spill return, thermostatically controlled water and
antifreeze mixture. Vertical flow radiator with remote header tank
and pump assisted
Cooling fans 9 blade axial flow on viscous coupling and 11 blade axial flow
electric
Electric cooling fan switching points:
For A/C system:
On When vehicle speed is 50 mph (80 km/h) or less and ambient
temperature is 28 °C (82 °F) or more
Off When vehicle speed increases to (62.5 mph (100 km/h) or
ambient temperature decreases to 25 °C (77 °F)
For engine cooling during normal running:
On 100 °C (212 °F)
Off 94.5 °C (202 °F)
For engine cooling at ignition off (to counteract heat
soak):
On If, within 10 seconds of ignition off, intake air temperature is 60 °C
(140 °F) or more and engine coolant temperature is 110 °C (230
°F) or more
Off After 10 minutes or if engine coolant temperature decreases to
100 °C (212 °F)
Coolant pump Centrifugal impeller, belt driven from crankshaft
Coolant pump drive ratio 1.293 : 1
Coolant pump output at 1000 rev/min 10 litres/min (2.64 US galls/min) at 0.7 bar (10 lbf.in
2)
Thermostat Waxstat with pressure relief valve
Thermostat operating temperature:
Initial opening 82 °C (179 °F)
Fully open 96 °C (204 °F)
Expansion tank cap relief valve - system operating
pressure1.4 bar (20 lbf.in
2)
Type Diaphragm spring, hydraulically operated with self-centering,
preloaded release bearing
Drive plate diameter 267 mm (10.5118 in)
Pressure plate diameter 267 mm (10.5118 in)
Clutch plate friction material Verto F202
Diaphragm finger height when clamped on a 8.5 mm
(0.33 in) thick gauge plate42.5 to 48.5 mm (1.673 to 1.904 in)
Diaphragm finger clearance (service limit) 1.00 mm (0.040 in)
Clutch plate thickness under 6500 N (1461 lb) axial
load:
New 8.2 to 8.8 mm (0.33 to 0.34 in)
Service limit 7.0 mm (0.27 in)
Page 87 of 1672
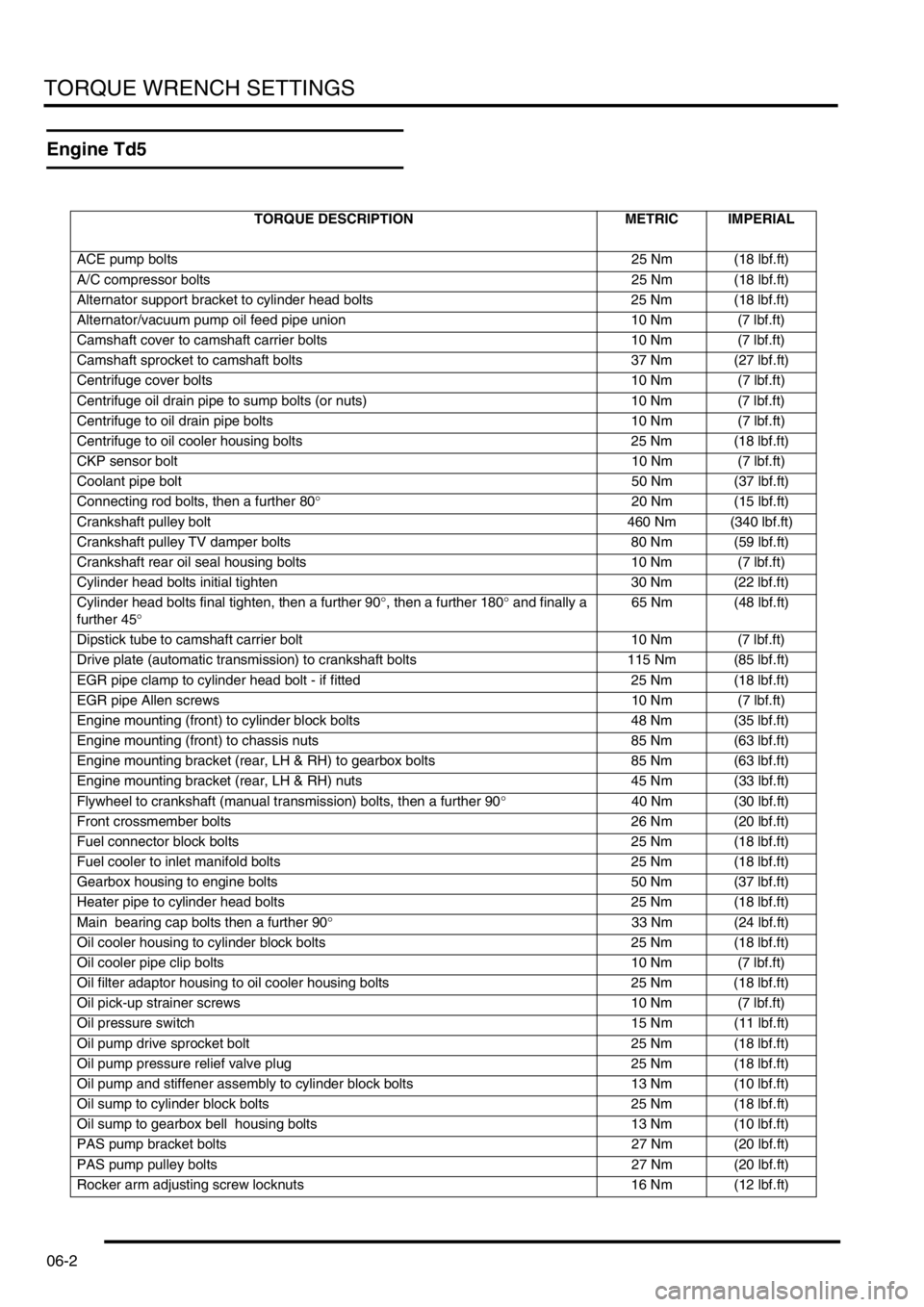
TORQUE WRENCH SETTINGS
06-2
Engine Td5
TORQUE DESCRIPTION METRIC IMPERIAL
ACE pump bolts25 Nm (18 lbf.ft)
A/C compressor bolts 25 Nm (18 lbf.ft)
Alternator support bracket to cylinder head bolts 25 Nm (18 lbf.ft)
Alternator/vacuum pump oil feed pipe union 10 Nm (7 lbf.ft)
Camshaft cover to camshaft carrier bolts 10 Nm (7 lbf.ft)
Camshaft sprocket to camshaft bolts 37 Nm (27 lbf.ft)
Centrifuge cover bolts 10 Nm (7 lbf.ft)
Centrifuge oil drain pipe to sump bolts (or nuts) 10 Nm (7 lbf.ft)
Centrifuge to oil drain pipe bolts 10 Nm (7 lbf.ft)
Centrifuge to oil cooler housing bolts 25 Nm (18 lbf.ft)
CKP sensor bolt10 Nm (7 lbf.ft)
Coolant pipe bolt50 Nm (37 lbf.ft)
Connecting rod bolts, then a further 80°20 Nm (15 lbf.ft)
Crankshaft pulley bolt 460 Nm (340 lbf.ft)
Crankshaft pulley TV damper bolts 80 Nm (59 lbf.ft)
Crankshaft rear oil seal housing bolts 10 Nm (7 lbf.ft)
Cylinder head bolts initial tighten 30 Nm (22 lbf.ft)
Cylinder head bolts final tighten, then a further 90°, then a further 180° and finally a
further 45°65 Nm (48 lbf.ft)
Dipstick tube to camshaft carrier bolt 10 Nm (7 lbf.ft)
Drive plate (automatic transmission) to crankshaft bolts 115 Nm (85 lbf.ft)
EGR pipe clamp to cylinder head bolt - if fitted 25 Nm (18 lbf.ft)
EGR pipe Allen screws 10 Nm (7 lbf.ft)
Engine mounting (front) to cylinder block bolts 48 Nm (35 lbf.ft)
Engine mounting (front) to chassis nuts 85 Nm (63 lbf.ft)
Engine mounting bracket (rear, LH & RH) to gearbox bolts 85 Nm (63 lbf.ft)
Engine mounting bracket (rear, LH & RH) nuts 45 Nm (33 lbf.ft)
Flywheel to crankshaft (manual transmission) bolts, then a further 90°40 Nm (30 lbf.ft)
Front crossmember bolts 26 Nm (20 lbf.ft)
Fuel connector block bolts 25 Nm (18 lbf.ft)
Fuel cooler to inlet manifold bolts 25 Nm (18 lbf.ft)
Gearbox housing to engine bolts 50 Nm (37 lbf.ft)
Heater pipe to cylinder head bolts 25 Nm (18 lbf.ft)
Main bearing cap bolts then a further 90°33 Nm (24 lbf.ft)
Oil cooler housing to cylinder block bolts 25 Nm (18 lbf.ft)
Oil cooler pipe clip bolts 10 Nm (7 lbf.ft)
Oil filter adaptor housing to oil cooler housing bolts 25 Nm (18 lbf.ft)
Oil pick-up strainer screws 10 Nm (7 lbf.ft)
Oil pressure switch 15 Nm (11 lbf.ft)
Oil pump drive sprocket bolt 25 Nm (18 lbf.ft)
Oil pump pressure relief valve plug 25 Nm (18 lbf.ft)
Oil pump and stiffener assembly to cylinder block bolts 13 Nm (10 lbf.ft)
Oil sump to cylinder block bolts 25 Nm (18 lbf.ft)
Oil sump to gearbox bell housing bolts 13 Nm (10 lbf.ft)
PAS pump bracket bolts 27 Nm (20 lbf.ft)
PAS pump pulley bolts 27 Nm (20 lbf.ft)
Rocker arm adjusting screw locknuts 16 Nm (12 lbf.ft)
Page 89 of 1672
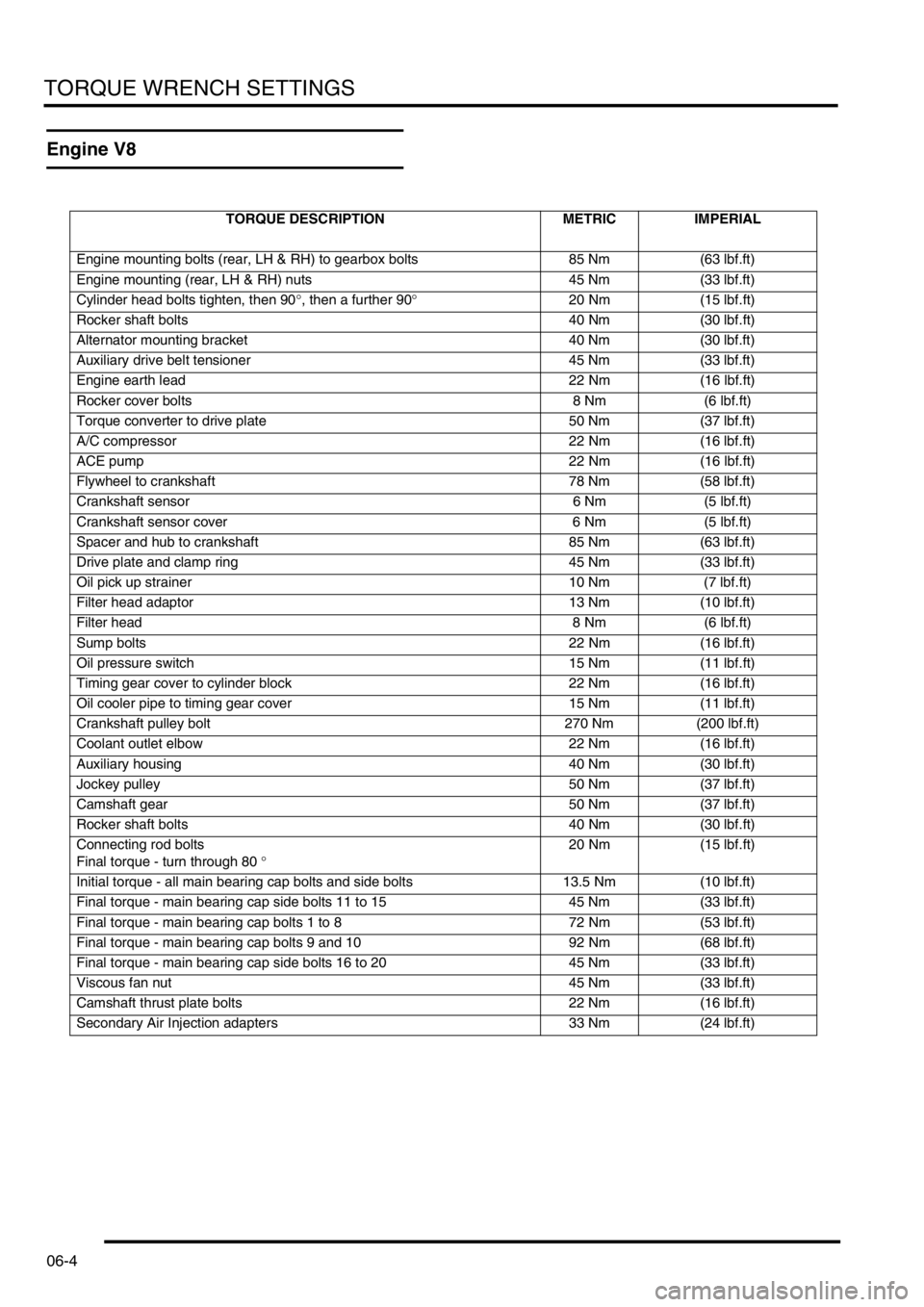
TORQUE WRENCH SETTINGS
06-4
Engine V8
TORQUE DESCRIPTION METRIC IMPERIAL
Engine mounting bolts (rear, LH & RH) to gearbox bolts 85 Nm (63 lbf.ft)
Engine mounting (rear, LH & RH) nuts 45 Nm (33 lbf.ft)
Cylinder head bolts tighten, then 90°, then a further 90°20 Nm (15 lbf.ft)
Rocker shaft bolts 40 Nm (30 lbf.ft)
Alternator mounting bracket 40 Nm (30 lbf.ft)
Auxiliary drive belt tensioner 45 Nm (33 lbf.ft)
Engine earth lead 22 Nm (16 lbf.ft)
Rocker cover bolts 8 Nm (6 lbf.ft)
Torque converter to drive plate 50 Nm (37 lbf.ft)
A/C compressor 22 Nm (16 lbf.ft)
ACE pump 22 Nm (16 lbf.ft)
Flywheel to crankshaft 78 Nm (58 lbf.ft)
Crankshaft sensor 6 Nm (5 lbf.ft)
Crankshaft sensor cover 6 Nm (5 lbf.ft)
Spacer and hub to crankshaft 85 Nm (63 lbf.ft)
Drive plate and clamp ring 45 Nm (33 lbf.ft)
Oil pick up strainer 10 Nm (7 lbf.ft)
Filter head adaptor 13 Nm (10 lbf.ft)
Filter head 8 Nm (6 lbf.ft)
Sump bolts 22 Nm (16 lbf.ft)
Oil pressure switch 15 Nm (11 lbf.ft)
Timing gear cover to cylinder block 22 Nm (16 lbf.ft)
Oil cooler pipe to timing gear cover 15 Nm (11 lbf.ft)
Crankshaft pulley bolt 270 Nm (200 lbf.ft)
Coolant outlet elbow 22 Nm (16 lbf.ft)
Auxiliary housing 40 Nm (30 lbf.ft)
Jockey pulley 50 Nm (37 lbf.ft)
Camshaft gear 50 Nm (37 lbf.ft)
Rocker shaft bolts 40 Nm (30 lbf.ft)
Connecting rod bolts
Final torque - turn through 80 °20 Nm (15 lbf.ft)
Initial torque - all main bearing cap bolts and side bolts 13.5 Nm (10 lbf.ft)
Final torque - main bearing cap side bolts 11 to 15 45 Nm (33 lbf.ft)
Final torque - main bearing cap bolts 1 to 8 72 Nm (53 lbf.ft)
Final torque - main bearing cap bolts 9 and 10 92 Nm (68 lbf.ft)
Final torque - main bearing cap side bolts 16 to 20 45 Nm (33 lbf.ft)
Viscous fan nut 45 Nm (33 lbf.ft)
Camshaft thrust plate bolts 22 Nm (16 lbf.ft)
Secondary Air Injection adapters 33 Nm (24 lbf.ft)
Page 91 of 1672
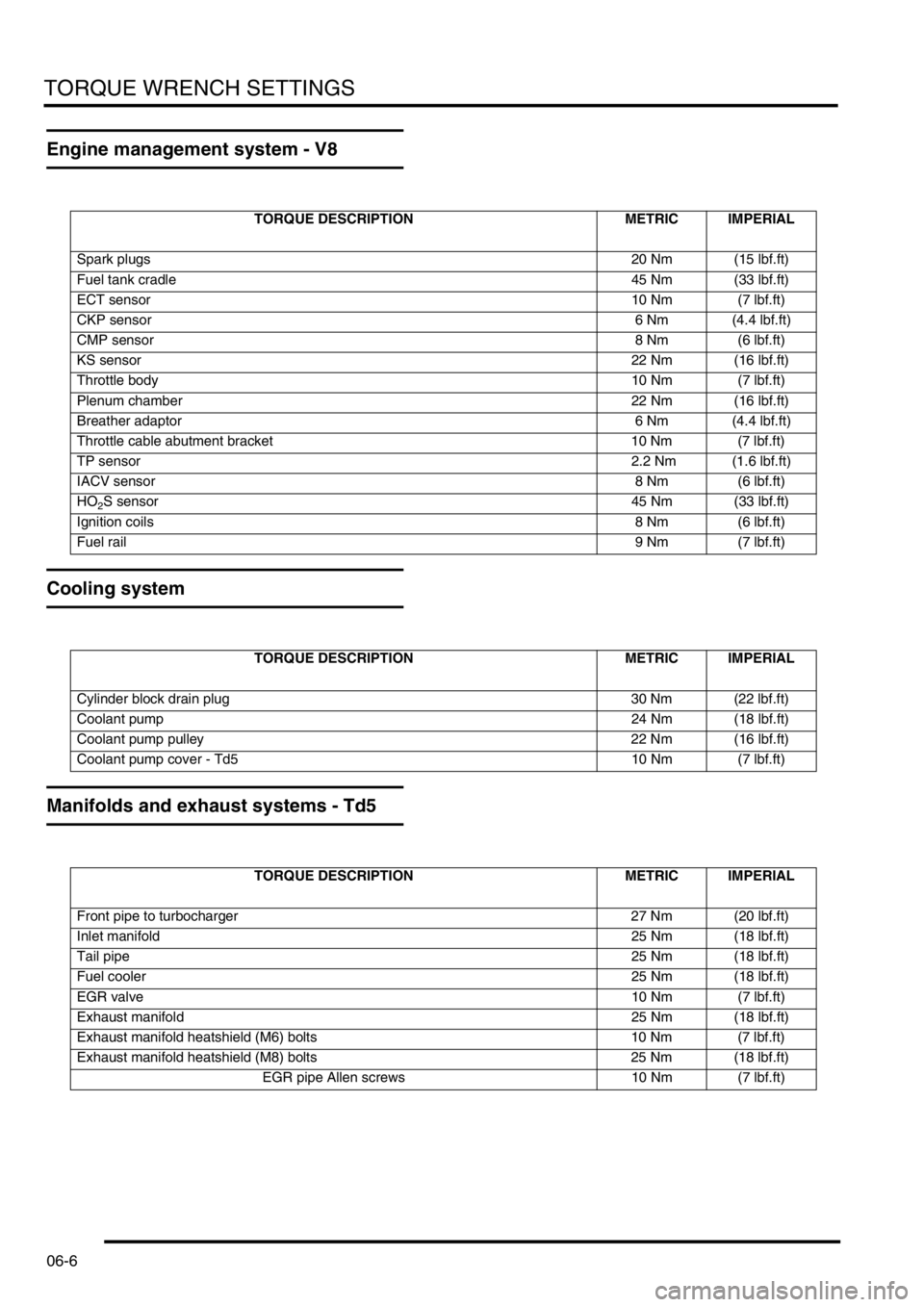
TORQUE WRENCH SETTINGS
06-6
Engine management system - V8
Cooling system
Manifolds and exhaust systems - Td5
TORQUE DESCRIPTION METRIC IMPERIAL
Spark plugs20 Nm (15 lbf.ft)
Fuel tank cradle45 Nm (33 lbf.ft)
ECT sensor10 Nm (7 lbf.ft)
CKP sensor6 Nm (4.4 lbf.ft)
CMP sensor8 Nm (6 lbf.ft)
KS sensor22 Nm (16 lbf.ft)
Throttle body10 Nm (7 lbf.ft)
Plenum chamber22 Nm (16 lbf.ft)
Breather adaptor6 Nm (4.4 lbf.ft)
Throttle cable abutment bracket 10 Nm (7 lbf.ft)
TP sensor 2.2 Nm (1.6 lbf.ft)
IACV sensor8 Nm (6 lbf.ft)
HO
2S sensor45 Nm (33 lbf.ft)
Ignition coils8 Nm (6 lbf.ft)
Fuel rail9 Nm (7 lbf.ft)
TORQUE DESCRIPTION METRIC IMPERIAL
Cylinder block drain plug 30 Nm (22 lbf.ft)
Coolant pump24 Nm (18 lbf.ft)
Coolant pump pulley 22 Nm (16 lbf.ft)
Coolant pump cover - Td5 10 Nm (7 lbf.ft)
TORQUE DESCRIPTION METRIC IMPERIAL
Front pipe to turbocharger 27 Nm (20 lbf.ft)
Inlet manifold25 Nm (18 lbf.ft)
Tail pipe25 Nm (18 lbf.ft)
Fuel cooler25 Nm (18 lbf.ft)
EGR valve10 Nm (7 lbf.ft)
Exhaust manifold25 Nm (18 lbf.ft)
Exhaust manifold heatshield (M6) bolts 10 Nm (7 lbf.ft)
Exhaust manifold heatshield (M8) bolts 25 Nm (18 lbf.ft)
EGR pipe Allen screws 10 Nm (7 lbf.ft)
Page 93 of 1672
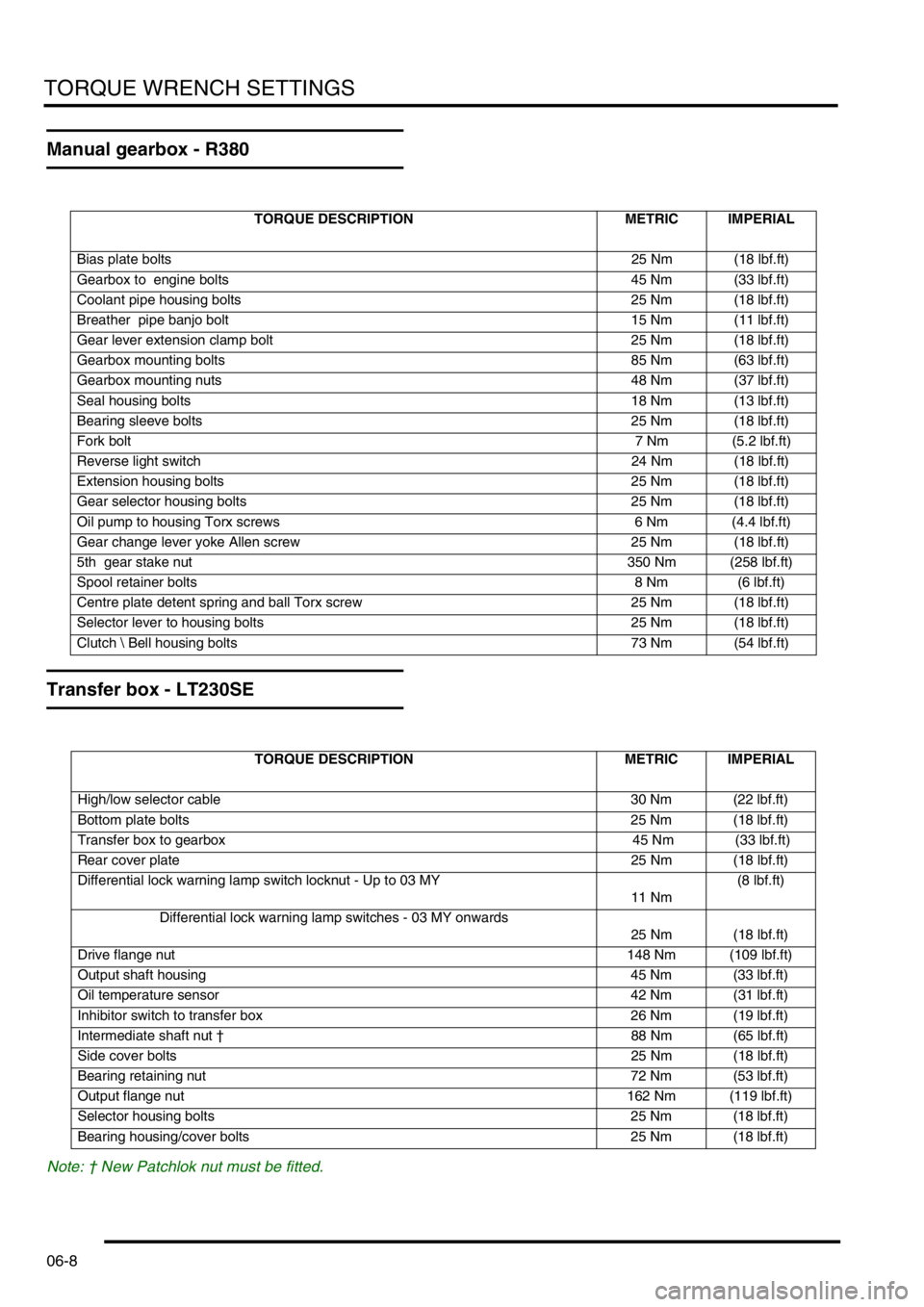
TORQUE WRENCH SETTINGS
06-8
Manual gearbox - R380
Transfer box - LT230SE
Note: † New Patchlok nut must be fitted.
TORQUE DESCRIPTION METRIC IMPERIAL
Bias plate bolts25 Nm (18 lbf.ft)
Gearbox to engine bolts 45 Nm (33 lbf.ft)
Coolant pipe housing bolts 25 Nm (18 lbf.ft)
Breather pipe banjo bolt 15 Nm (11 lbf.ft)
Gear lever extension clamp bolt 25 Nm (18 lbf.ft)
Gearbox mounting bolts 85 Nm (63 lbf.ft)
Gearbox mounting nuts 48 Nm (37 lbf.ft)
Seal housing bolts 18 Nm (13 lbf.ft)
Bearing sleeve bolts 25 Nm (18 lbf.ft)
Fork bolt7 Nm (5.2 lbf.ft)
Reverse light switch 24 Nm (18 lbf.ft)
Extension housing bolts 25 Nm (18 lbf.ft)
Gear selector housing bolts 25 Nm (18 lbf.ft)
Oil pump to housing Torx screws 6 Nm (4.4 lbf.ft)
Gear change lever yoke Allen screw 25 Nm (18 lbf.ft)
5th gear stake nut 350 Nm (258 lbf.ft)
Spool retainer bolts 8 Nm (6 lbf.ft)
Centre plate detent spring and ball Torx screw 25 Nm (18 lbf.ft)
Selector lever to housing bolts 25 Nm (18 lbf.ft)
Clutch Bell housing bolts 73 Nm (54 lbf.ft)
TORQUE DESCRIPTION METRIC IMPERIAL
High/low selector cable 30 Nm (22 lbf.ft)
Bottom plate bolts 25 Nm (18 lbf.ft)
Transfer box to gearbox 45 Nm (33 lbf.ft)
Rear cover plate25 Nm (18 lbf.ft)
Differential lock warning lamp switch locknut - Up to 03 MY
11 Nm(8 lbf.ft)
Differential lock warning lamp switches - 03 MY onwards
25 Nm (18 lbf.ft)
Drive flange nut148 Nm (109 lbf.ft)
Output shaft housing 45 Nm (33 lbf.ft)
Oil temperature sensor 42 Nm (31 lbf.ft)
Inhibitor switch to transfer box 26 Nm (19 lbf.ft)
Intermediate shaft nut †88 Nm (65 lbf.ft)
Side cover bolts25 Nm (18 lbf.ft)
Bearing retaining nut 72 Nm (53 lbf.ft)
Output flange nut 162 Nm (119 lbf.ft)
Selector housing bolts 25 Nm (18 lbf.ft)
Bearing housing/cover bolts 25 Nm (18 lbf.ft)