LEXUS SC400 1991 Service Repair Manual
Manufacturer: LEXUS, Model Year: 1991, Model line: SC400, Model: LEXUS SC400 1991Pages: 4087, PDF Size: 75.75 MB
Page 1611 of 4087
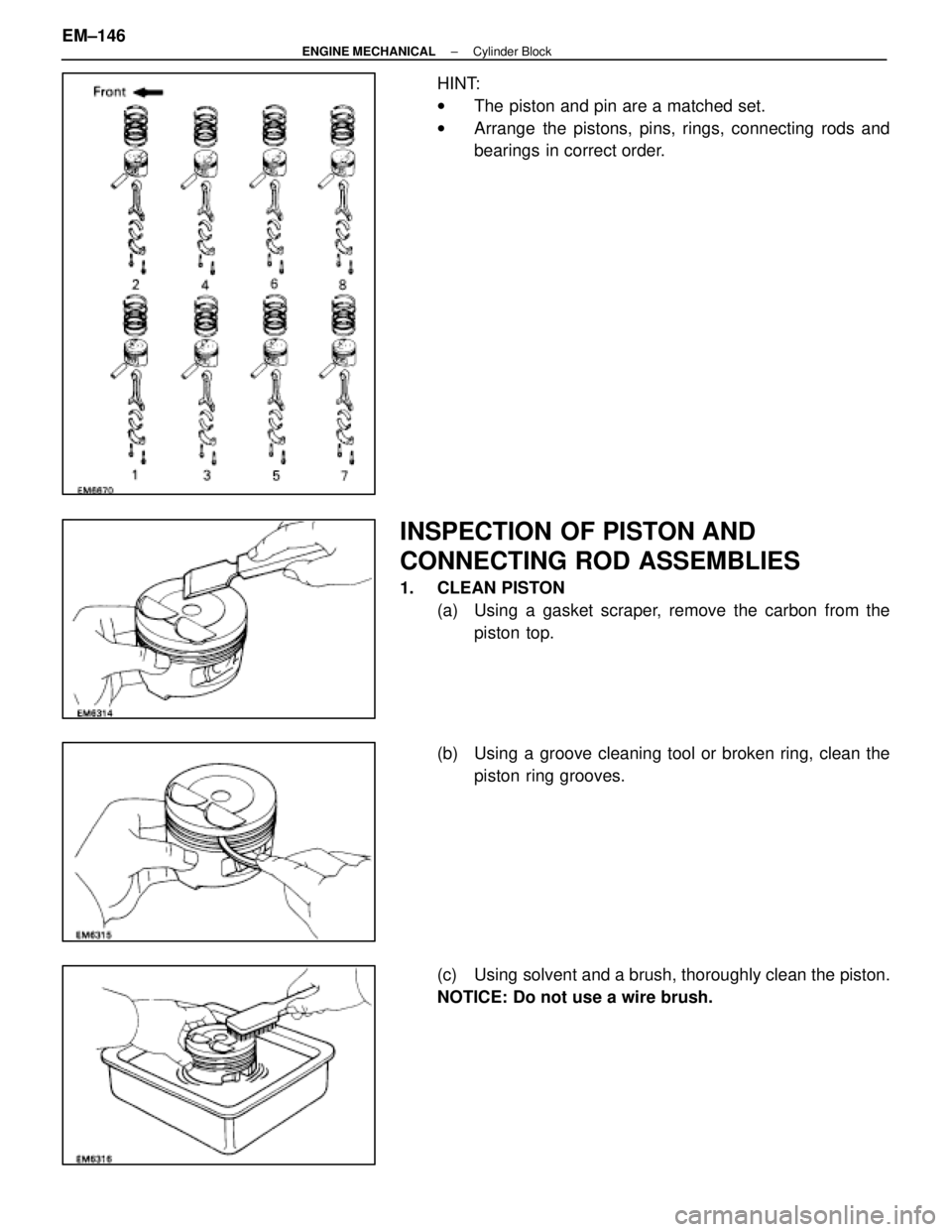
HINT:
wThe piston and pin are a matched set.
w Arrange the pistons, pins, rings, connecting rods and
bearings in correct order.
INSPECTION OF PISTON AND
CONNECTING ROD ASSEMBLIES
1. CLEAN PISTON
(a) Using a gasket scraper, remove the carbon from thepiston top.
(b) Using a groove cleaning tool or broken ring, clean the piston ring grooves.
(c) Using solvent and a brush, thoroughly clean the piston.
NOTICE: Do not use a wire brush.
EM±146
±
ENGINE MECHANICAL Cylinder Block
WhereEverybodyKnowsYourName
Page 1612 of 4087
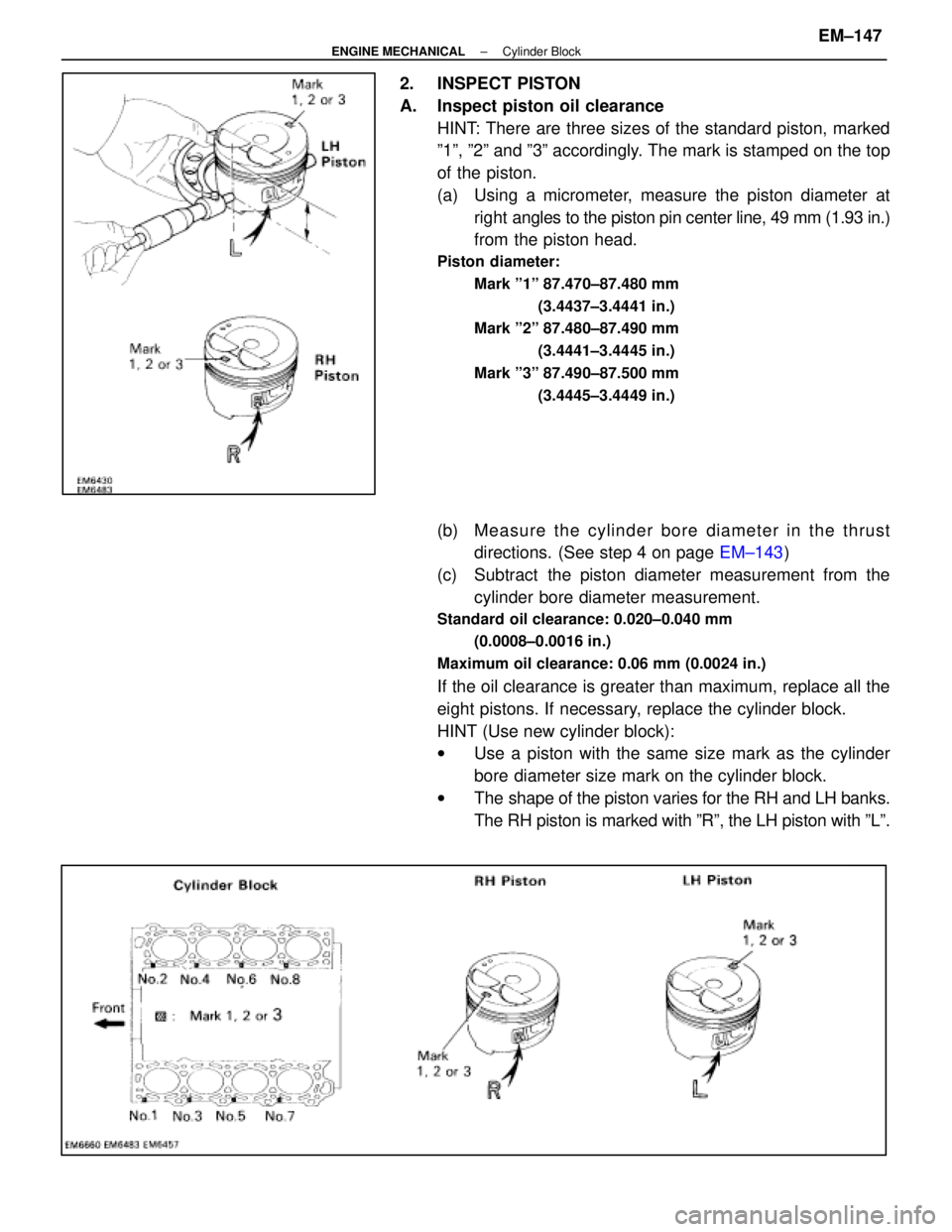
2. INSPECT PISTON
A. Inspect piston oil clearanceHINT: There are three sizes of the standard piston, marked
º1º, º2º and º3º accordingly. The mark is stamped on the top
of the piston.
(a) Using a micrometer, measure the piston diameter atright angles to the piston pin center line, 49 mm (1.93 in.)
from the piston head.
Piston diameter:
Mark º1º 87.470±87.480 mm (3.4437±3.4441 in.)
Mark º2º 87.480±87.490 mm
(3.4441±3.4445 in.)
Mark º3º 87.490±87.500 mm (3.4445±3.4449 in.)
(b) Me a su re th e cyli nder bore diameter in the thrust
directions. (See step 4 on page EM±143)
(c) Subtract the piston diameter measurement from the cylinder bore diameter measurement.
Standard oil clearance: 0.020±0.040 mm
(0.0008±0.0016 in.)
Maximum oil clearance: 0.06 mm (0.0024 in.)
If the oil clearance is greater than maximum, replace all the
eight pistons. If necessary, replace the cylinder block.
HINT (Use new cylinder block):
w Use a piston with the same size mark as the cylinder
bore diameter size mark on the cylinder block.
w The shape of the piston varies for the RH and LH banks.
The RH piston is marked with ºRº, the LH piston with ºLº.
±
ENGINE MECHANICAL Cylinder BlockEM±147
WhereEverybodyKnowsYourName
Page 1613 of 4087
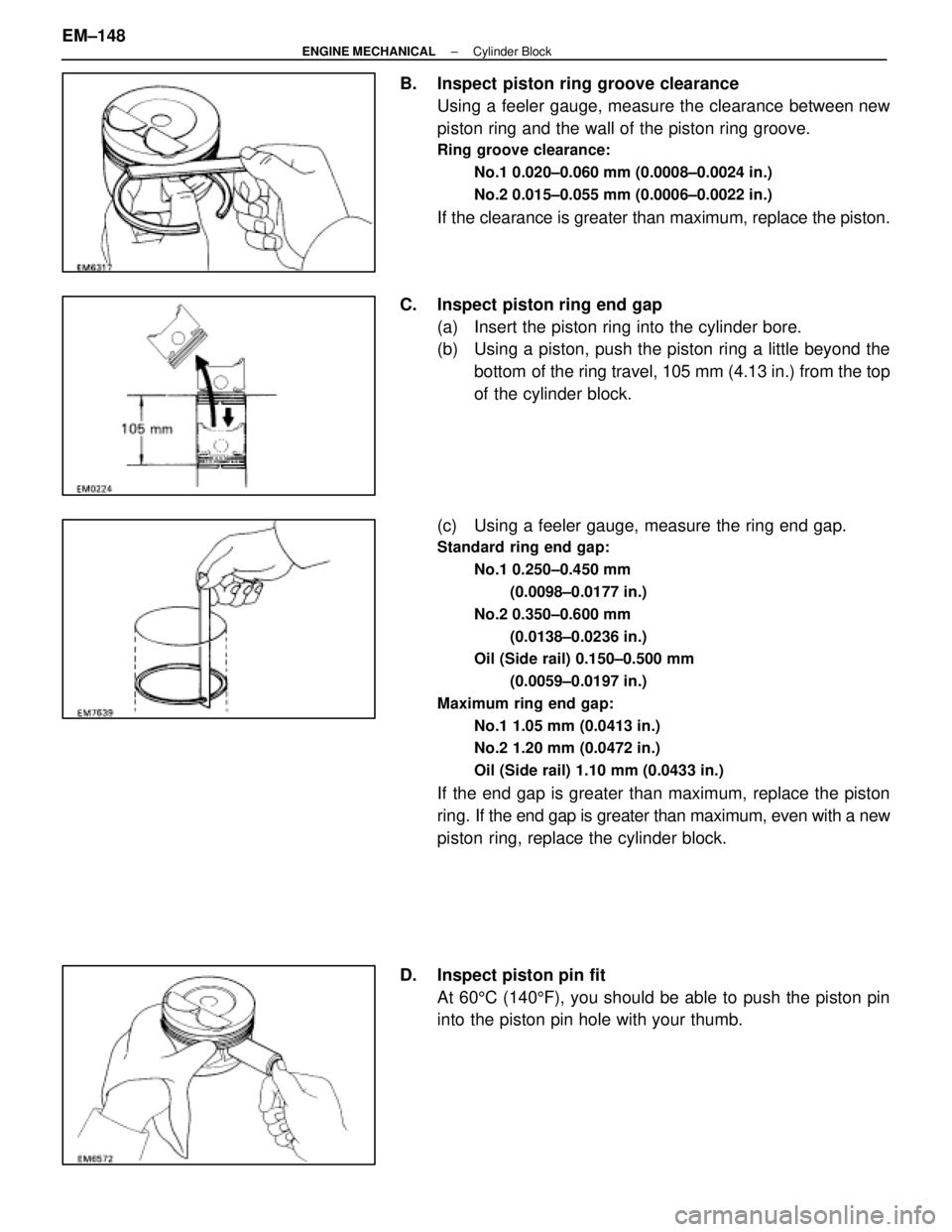
B. Inspect piston ring groove clearanceUsing a feeler gauge, measure the clearance between new
piston ring and the wall of the piston ring groove.
Ring groove clearance:
No.1 0.020±0.060 mm (0.0008±0.0024 in.)
No.2 0.015±0.055 mm (0.0006±0.0022 in.)
If the clearance is greater than maximum, replace the piston.
C. Inspect piston ring end gap (a) Insert the piston ring into the cylinder bore.
(b) Using a piston, push the piston ring a little beyond thebottom of the ring travel, 105 mm (4.13 in.) from the top
of the cylinder block.
(c) Using a feeler gauge, measure the ring end gap.
Standard ring end gap: No.1 0.250±0.450 mm(0.0098±0.0177 in.)
No.2 0.350±0.600 mm (0.0138±0.0236 in.)
Oil (Side rail) 0.150±0.500 mm
(0.0059±0.0197 in.)
Maximum ring end gap: No.1 1.05 mm (0.0413 in.)
No.2 1.20 mm (0.0472 in.)
Oil (Side rail) 1.10 mm (0.0433 in.)
If the end gap is greater than maximum, replace the piston
ring. If the end gap is greater than maximum, even with a new
piston ring, replace the cylinder block.
D. Inspect piston pin fit At 60 5C (140 5F), you should be able to push the piston pin
into the piston pin hole with your thumb.
EM±148
±
ENGINE MECHANICAL Cylinder Block
WhereEverybodyKnowsYourName
Page 1614 of 4087
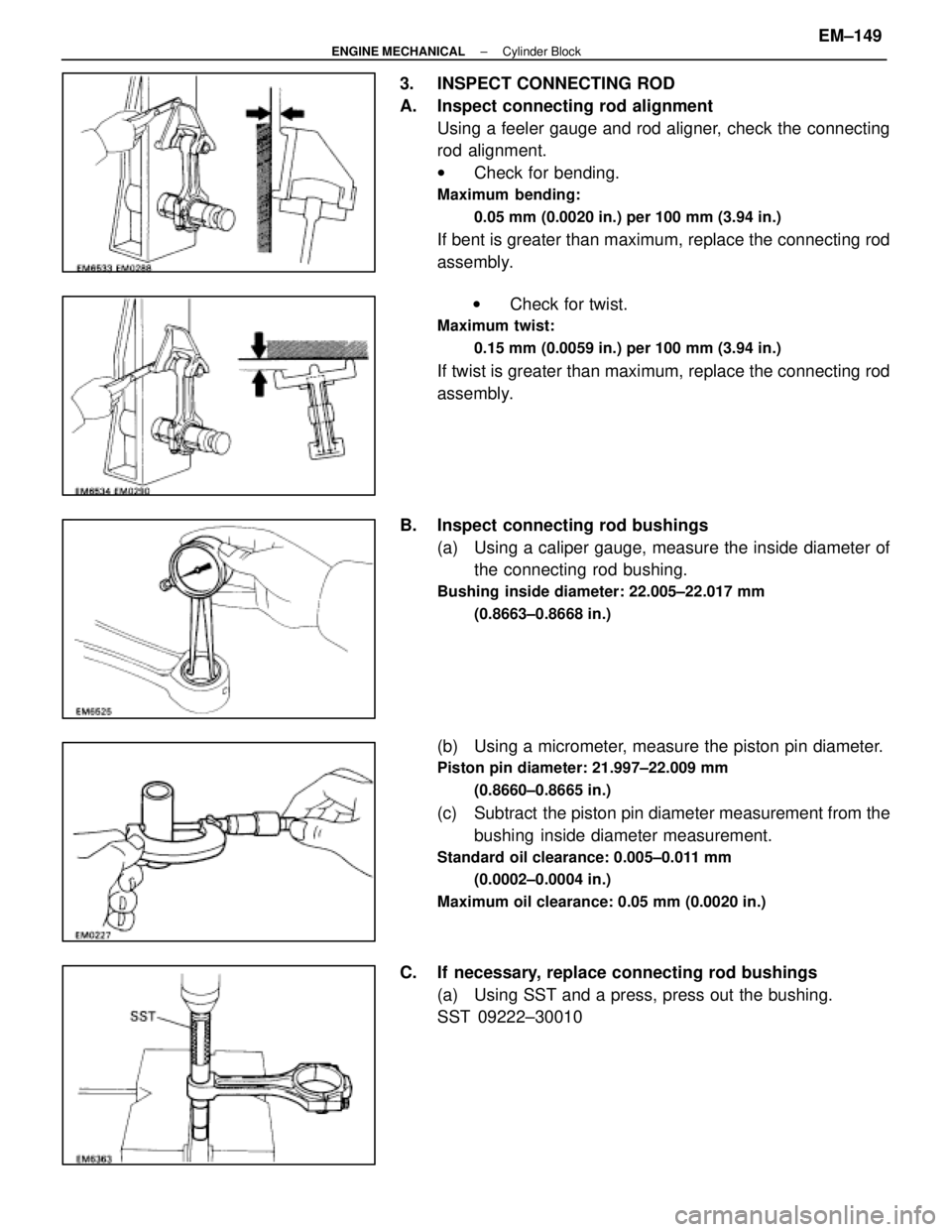
3. INSPECT CONNECTING ROD
A. Inspect connecting rod alignmentUsing a feeler gauge and rod aligner, check the connecting
rod alignment.
wCheck for bending.
Maximum bending:
0.05 mm (0.0020 in.) per 100 mm (3.94 in.)
If bent is greater than maximum, replace the connecting rod
assembly.
w Check for twist.
Maximum twist:
0.15 mm (0.0059 in.) per 100 mm (3.94 in.)
If twist is greater than maximum, replace the connecting rod
assembly.
B. Inspect connecting rod bushings (a) Using a caliper gauge, measure the inside diameter ofthe connecting rod bushing.
Bushing inside diameter: 22.005±22.017 mm
(0.8663±0.8668 in.)
(b) Using a micrometer, measure the piston pin diameter.
Piston pin diameter: 21.997±22.009 mm(0.8660±0.8665 in.)
(c) Subtract the piston pin diameter measurement from thebushing inside diameter measurement.
Standard oil clearance: 0.005±0.011 mm
(0.0002±0.0004 in.)
Maximum oil clearance: 0.05 mm (0.0020 in.)
C. If necessary, replace connecting rod bushings (a) Using SST and a press, press out the bushing.
SST 09222±30010
±
ENGINE MECHANICAL Cylinder BlockEM±149
WhereEverybodyKnowsYourName
Page 1615 of 4087
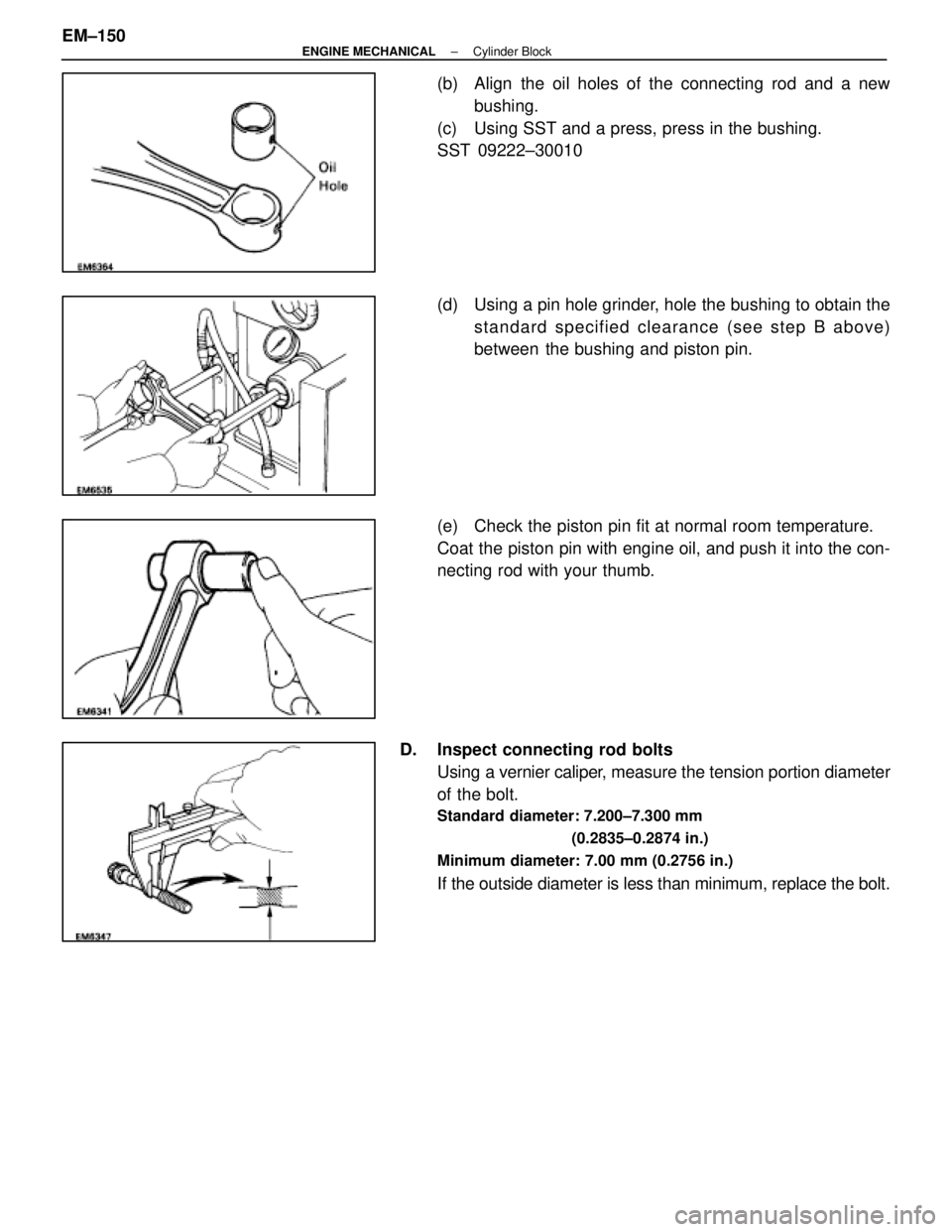
(b) Align the oil holes of the connecting rod and a newbushing.
(c) Using SST and a press, press in the bushing.
SST 09222±30010
(d) Using a pin hole grinder, hole the bushing to obtain the standard specified clearance (see step B above)
between the bushing and piston pin.
(e) Check the piston pin fit at normal room temperature.
Coat the piston pin with engine oil, and push it into the con-
necting rod with your thumb.
D. Inspect connecting rod bolts Using a vernier caliper, measure the tension portion diameter
of the bolt.
Standard diameter: 7.200±7.300 mm
(0.2835±0.2874 in.)
Minimum diameter: 7.00 mm (0.2756 in.)
If the outside diameter is less than minimum, replace the bolt.
EM±150
±
ENGINE MECHANICAL Cylinder Block
WhereEverybodyKnowsYourName
Page 1616 of 4087
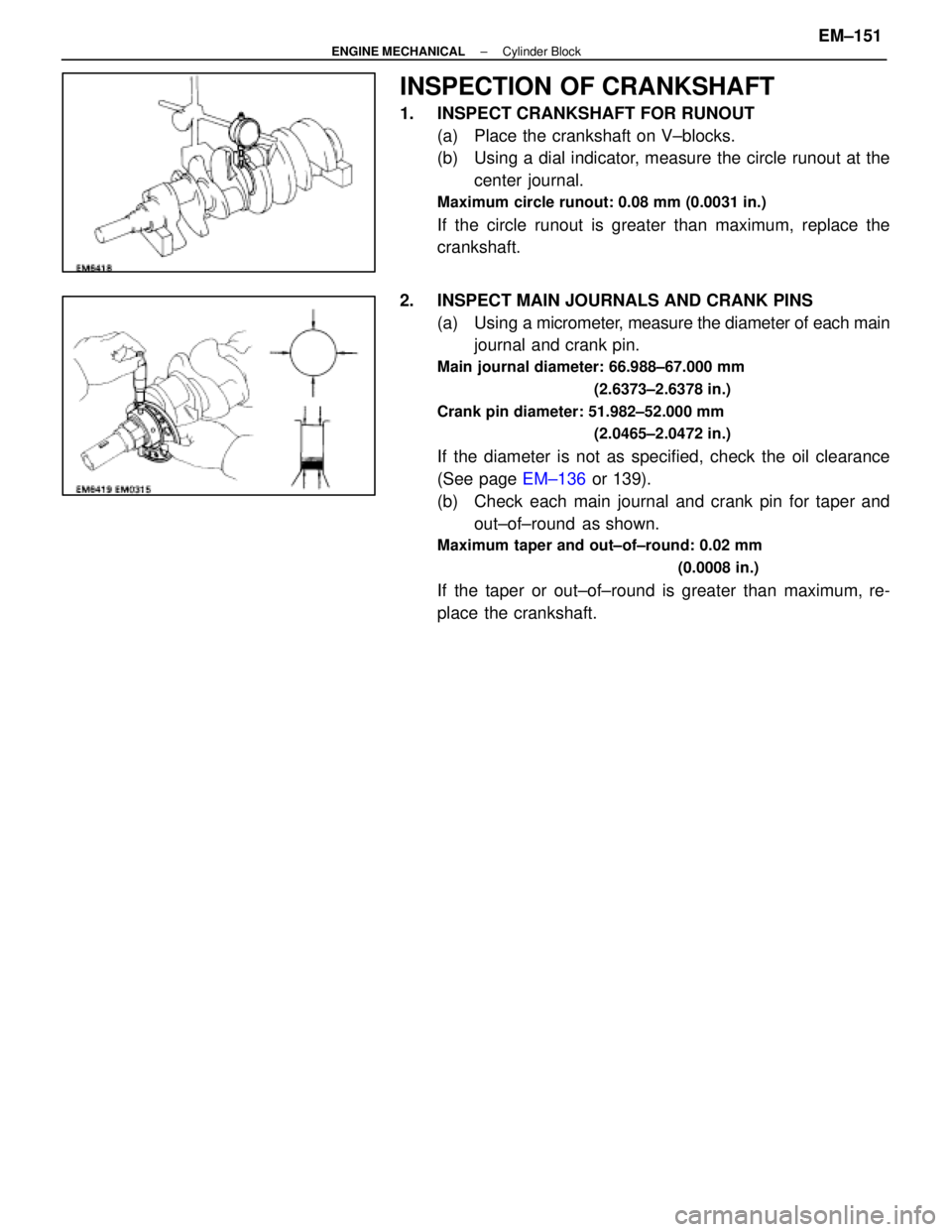
INSPECTION OF CRANKSHAFT
1. INSPECT CRANKSHAFT FOR RUNOUT(a) Place the crankshaft on V±blocks.
(b) Using a dial indicator, measure the circle runout at thecenter journal.
Maximum circle runout: 0.08 mm (0.0031 in.)
If the circle runout is greater than maximum, replace the
crankshaft.
2. INSPECT MAIN JOURNALS AND CRANK PINS (a) Using a micr ometer, measure the diameter of each main
journal and crank pin.
Main journal diameter: 66.988±67.000 mm
(2.6373±2.6378 in.)
Crank pin diameter: 51.982±52.000 mm (2.0465±2.0472 in.)
If the diameter is not as specified, check the oil clearance
(See page EM±136 or 139).
(b) Check each main journal and crank pin for taper and out±of±round as shown.
Maximum taper and out±of±round: 0.02 mm
(0.0008 in.)
If the taper or out±of±round is greater than maximum, re-
place the crankshaft.
±
ENGINE MECHANICAL Cylinder BlockEM±151
WhereEverybodyKnowsYourName
Page 1617 of 4087
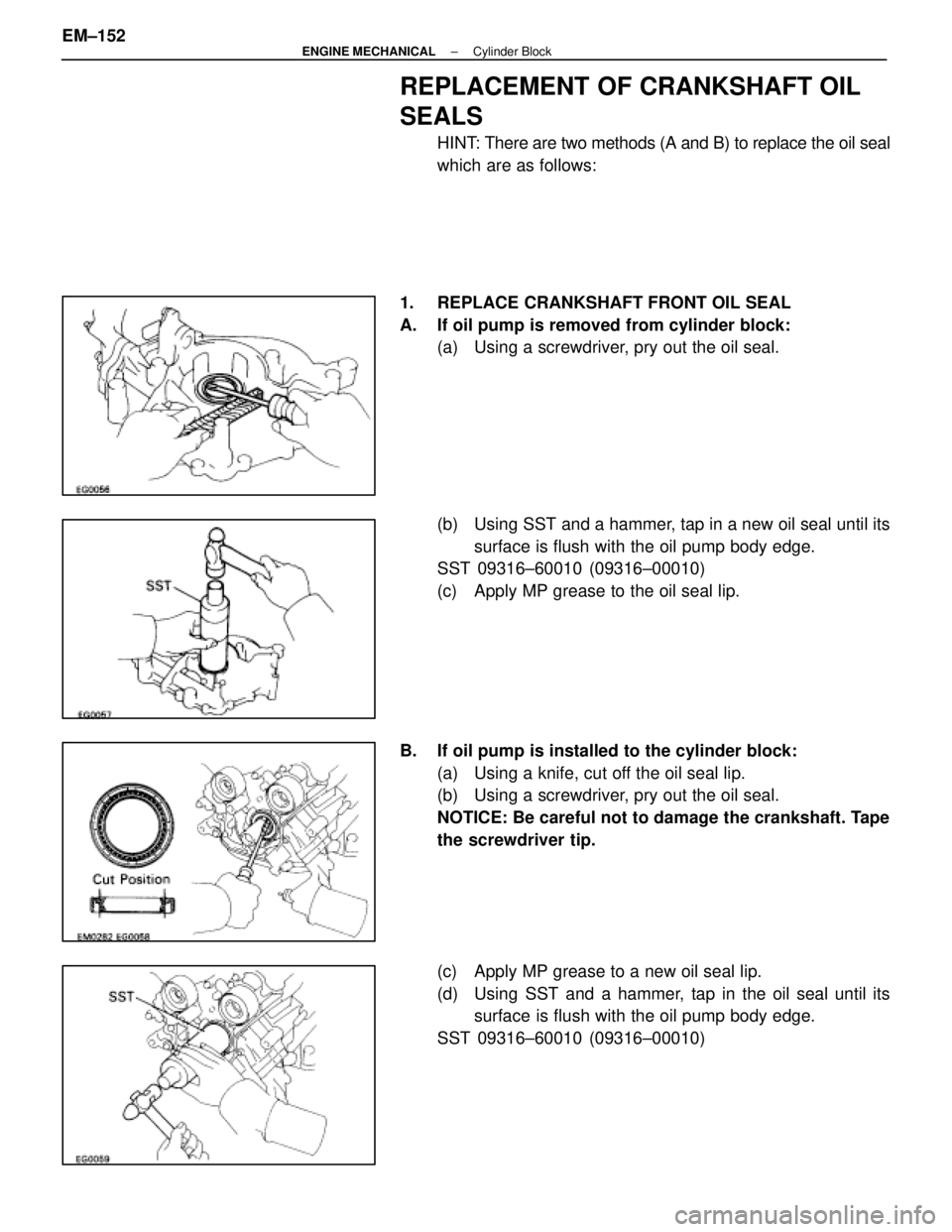
REPLACEMENT OF CRANKSHAFT OIL
SEALS
HINT: There are two methods (A and B) to replace the oil seal
which are as follows:
1. REPLACE CRANKSHAFT FRONT OIL SEAL
A. If oil pump is removed from cylinder block: (a) Using a screwdriver, pry out the oil seal.
(b) Using SST and a hammer, tap in a new oil seal until its
surface is flush with the oil pump body edge.
SST 09316±60010 (09316±00010)
(c) Apply MP grease to the oil seal lip.
B. If oil pump is installed to the cylinder block: (a) Using a knife, cut off the oil seal lip.
(b) Using a screwdriver, pry out the oil seal.
NOTICE: Be careful not to damage the crankshaft. Tape
the screwdriver tip.
(c) Apply MP grease to a new oil seal lip.
(d) Using SST and a hammer, tap in the oil seal until itssurface is flush with the oil pump body edge.
SST 09316±60010 (09316±00010)
EM±152
±
ENGINE MECHANICAL Cylinder Block
WhereEverybodyKnowsYourName
Page 1618 of 4087
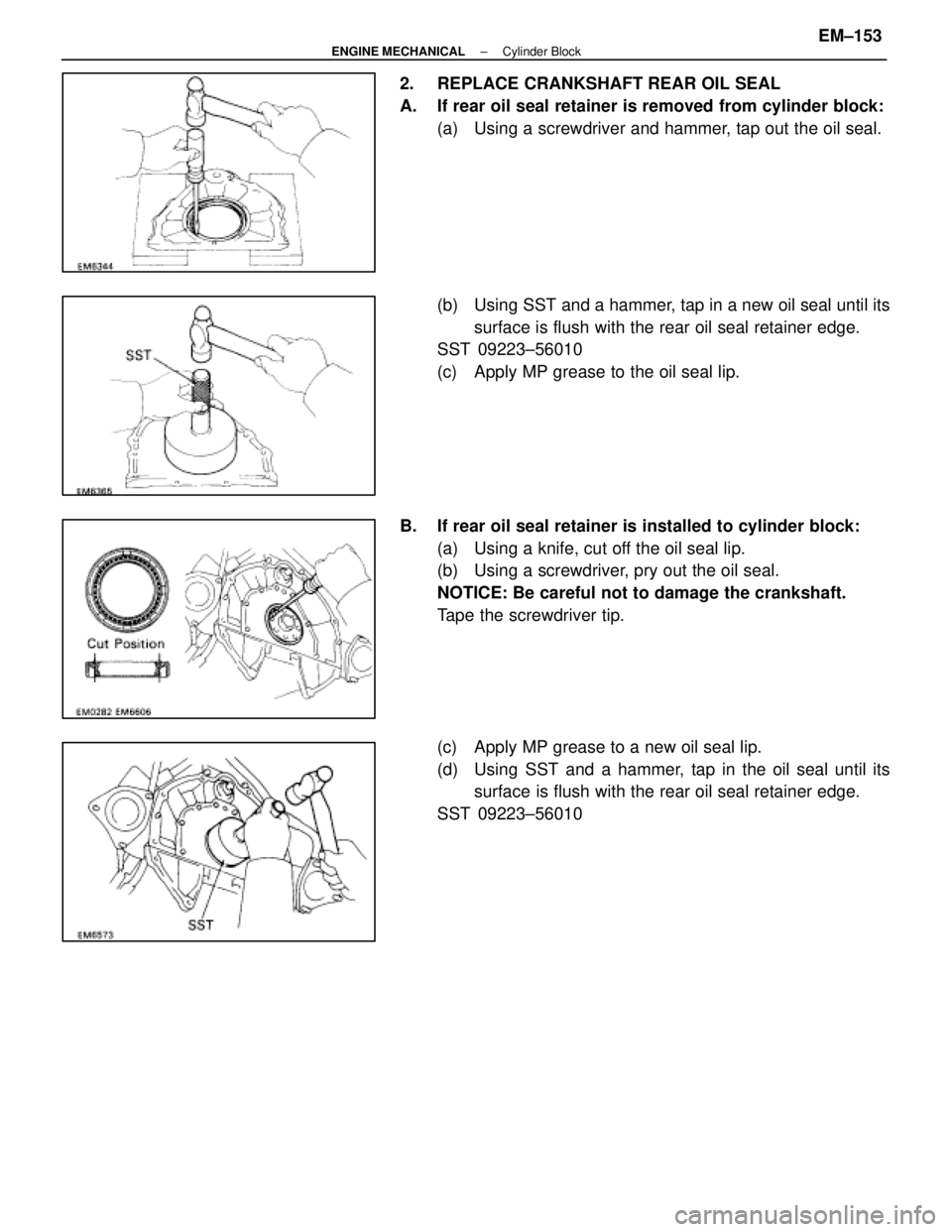
2. REPLACE CRANKSHAFT REAR OIL SEAL
A. If rear oil seal retainer is removed from cylinder block:(a) Using a screwdriver and hammer, tap out the oil seal.
(b) Using SST and a hammer, tap in a new oil seal until itssurface is flush with the rear oil seal retainer edge.
SST 09223±56010
(c) Apply MP grease to the oil seal lip.
B. If rear oil seal retainer is installed to cylinder block: (a) Using a knife, cut off the oil seal lip.
(b) Using a screwdriver, pry out the oil seal.
NOTICE: Be careful not to damage the crankshaft.
Tape the screwdriver tip.
(c) Apply MP grease to a new oil seal lip.
(d) Using SST and a hammer, tap in the oil seal until itssurface is flush with the rear oil seal retainer edge.
SST 09223±56010
±
ENGINE MECHANICAL Cylinder BlockEM±153
WhereEverybodyKnowsYourName
Page 1619 of 4087
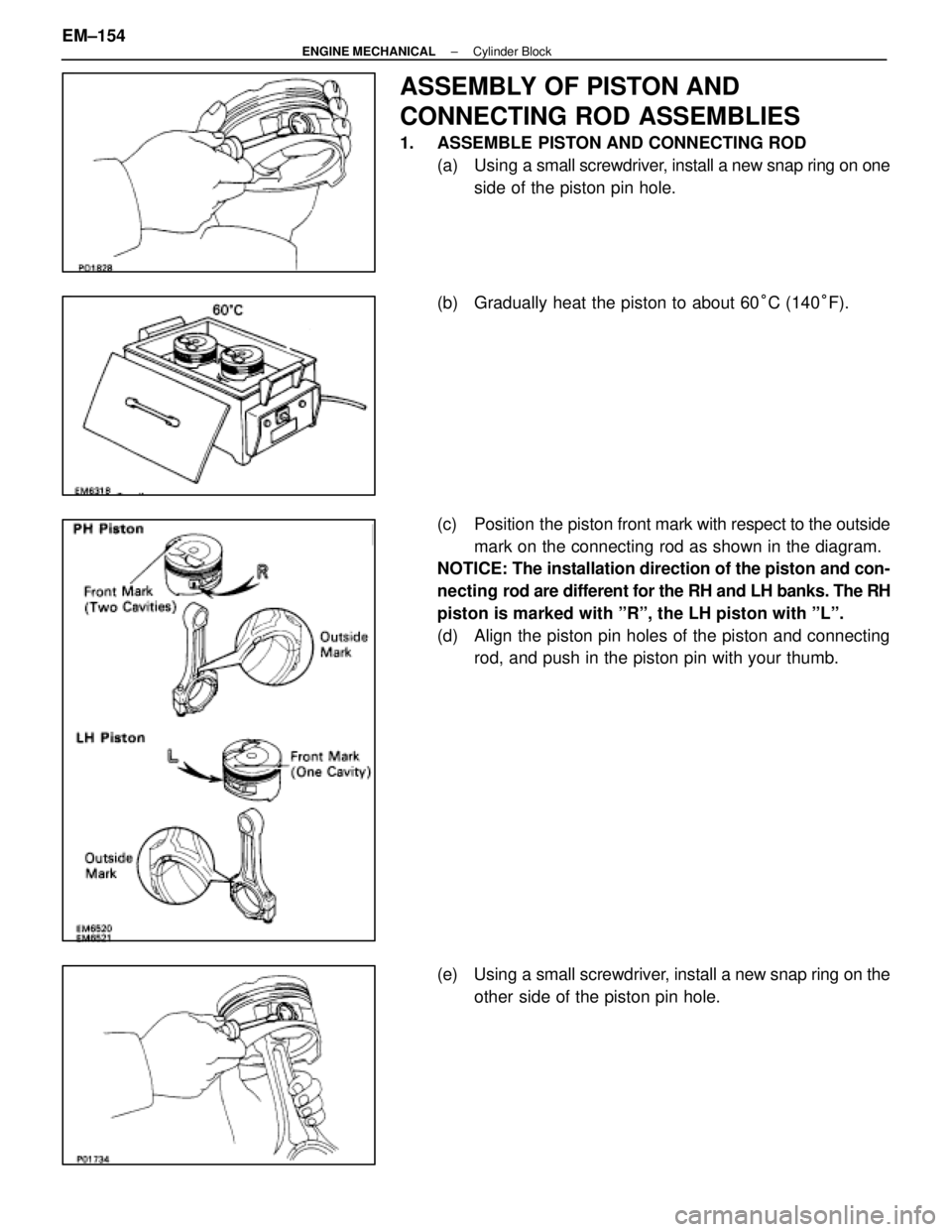
ASSEMBLY OF PISTON AND
CONNECTING ROD ASSEMBLIES
1. ASSEMBLE PISTON AND CONNECTING ROD(a) Using a small screwdriver, install a new snap ring on one
side of the piston pin hole.
(b) Gradually heat the piston to about 60 °C (140 °F).
(c) Position the piston front mark with respect to the outside
mark on the connecting rod as shown in the diagram.
NOTICE: The installation direction of the piston and con-
necting rod are different for the RH and LH banks. The RH
piston is marked with ºRº, the LH piston with ºLº.
(d) Align the piston pin holes of the piston and connecting rod, and push in the piston pin with your thumb.
(e) Using a small screwdriver, install a new snap ring on the
other side of the piston pin hole.
EM±154
±
ENGINE MECHANICAL Cylinder Block
WhereEverybodyKnowsYourName
Page 1620 of 4087
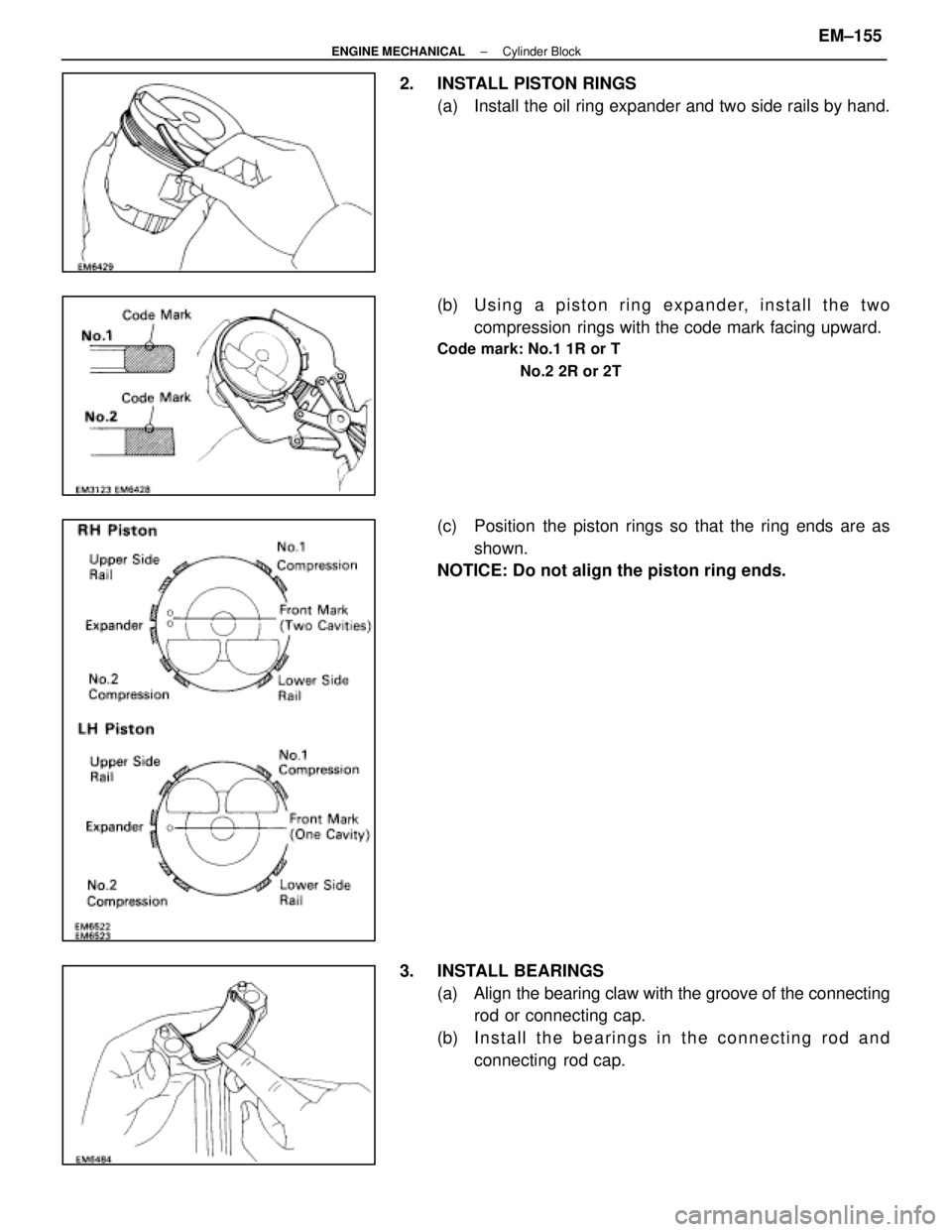
2. INSTALL PISTON RINGS(a) Install the oil ring expander and two side rails by hand.
(b) U s i n g a p i s t o n r i n g e x pander, install the two
compression rings with the code mark facing upward.
Code mark: No.1 1R or T
No.2 2R or 2T
(c) Position the piston rings so that the ring ends are asshown.
NOTICE: Do not align the piston ring ends.
3. INSTALL BEARINGS (a) Align the bearing claw with the groove of the connectingrod or connecting cap.
(b) I n s t a l l t h e b e a r i n g s i n t h e c onnecting rod and
connecting rod cap.
±
ENGINE MECHANICAL Cylinder BlockEM±155
WhereEverybodyKnowsYourName