engine MAZDA 626 1987 Workshop Manual
[x] Cancel search | Manufacturer: MAZDA, Model Year: 1987, Model line: 626, Model: MAZDA 626 1987Pages: 1865, PDF Size: 94.35 MB
Page 937 of 1865
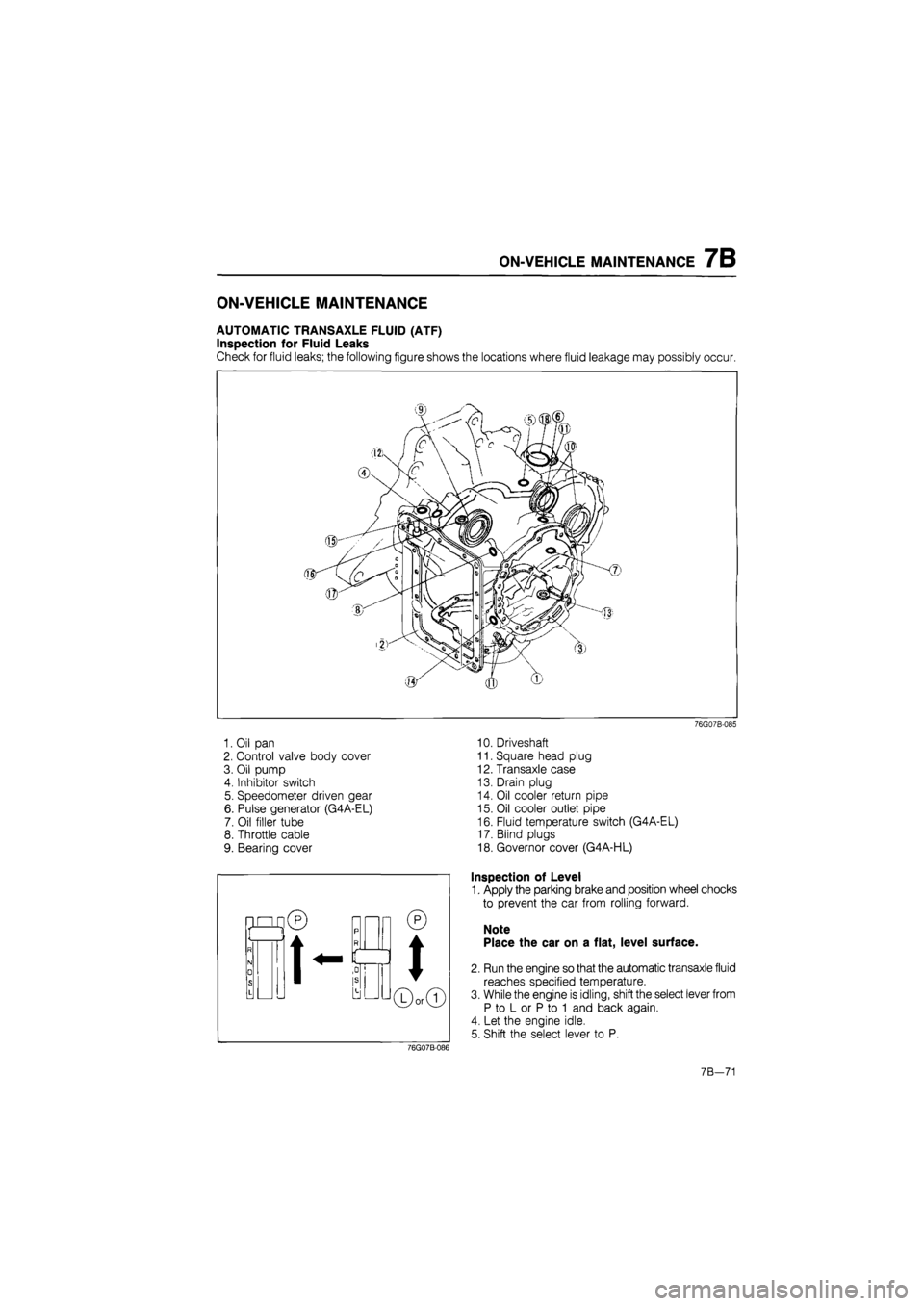
ON-VEHICLE MAINTENANCE 7B
ON-VEHICLE MAINTENANCE
AUTOMATIC TRANSAXLE FLUID (ATF)
Inspection for Fluid Leaks
Check for fluid leaks; the following figure shows the locations where fluid leakage may possibly occur.
1. Oil pan
2. Control valve body cover
3. Oil pump
4. Inhibitor switch
5. Speedometer driven gear
6. Pulse generator (G4A-EL)
7. Oil filler tube
8. Throttle cable
9. Bearing cover
76G07B-085
10. Driveshaft
11. Square head plug
12. Transaxle case
13. Drain plug
14. Oil cooler return pipe
15. Oil cooler outlet pipe
16. Fluid temperature switch (G4A-EL)
17. Blind plugs
18. Governor cover (G4A-HL)
Inspection of Level
1. Apply the parking brake and position wheel chocks
to prevent the car from rolling forward.
Note
Place the car on a flat, level surface.
2. Run the engine so that the automatic transaxle fluid
reaches specified temperature.
3. While the engine is idling, shift the select lever from
P to L or P to 1 and back again.
4. Let the engine idle.
5. Shift the select lever to P.
76G07B-086
7B—71
Page 941 of 1865
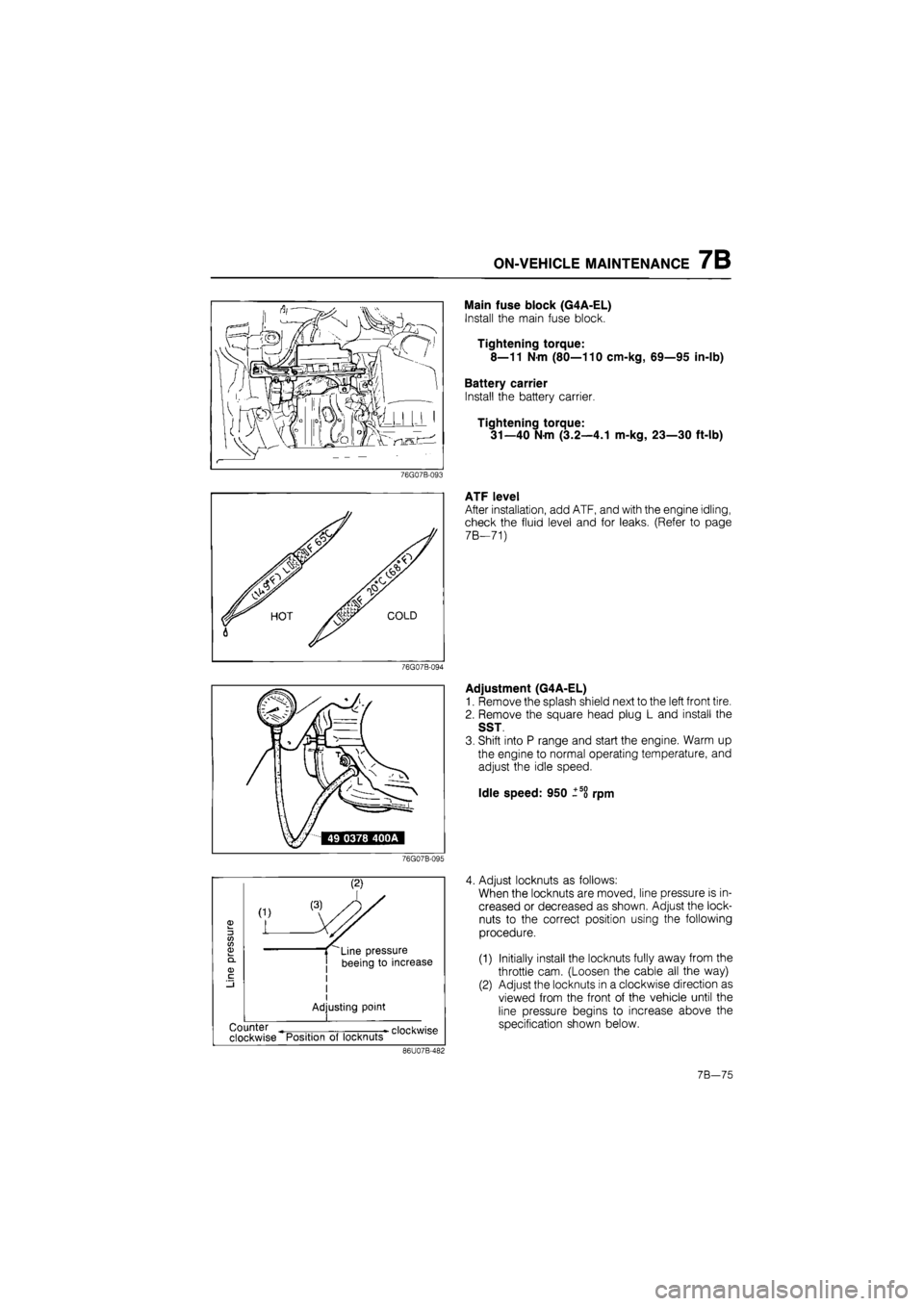
ON-VEHICLE MAINTENANCE 7B
'mfm^i! kfOl iff t—
76G07B-093
76G07B-094
Main fuse block (G4A-EL)
Install the main fuse block.
Tightening torque:
8—11 Nm (80—110 cm-kg, 69—95 in-lb)
Battery carrier
Install the battery carrier.
Tightening torque:
31—40 Nm (3.2—4.1 m-kg, 23—30 ft-lb)
ATF level
After installation, add ATF, and with the engine idling,
check the fluid level and for leaks. (Refer to page
7 B—71)
Adjustment (G4A-EL)
1. Remove the splash shield next to the left front tire.
2. Remove the square head plug L and install the
SST
3. Shift into P range and start the engine. Warm up
the engine to normal operating temperature, and
adjust the idle speed.
Idle speed: 950 ±5o rpm
76G07B-095
3 CO CO 03
(1)
L
Line pressure
beeing to increase
I
Adjusting point
•
clockwise Counter
clockwise Position of locknuts
86U07B-482
4. Adjust locknuts as follows:
When the locknuts are moved, line pressure is in-
creased or decreased as shown. Adjust the lock-
nuts to the correct position using the following
procedure.
(1) Initially install the locknuts fully away from the
throttle cam. (Loosen the cable all the way)
(2) Adjust the locknuts in a clockwise direction as
viewed from the front of the vehicle until the
line pressure begins to increase above the
specification shown below.
7B—75
Page 942 of 1865
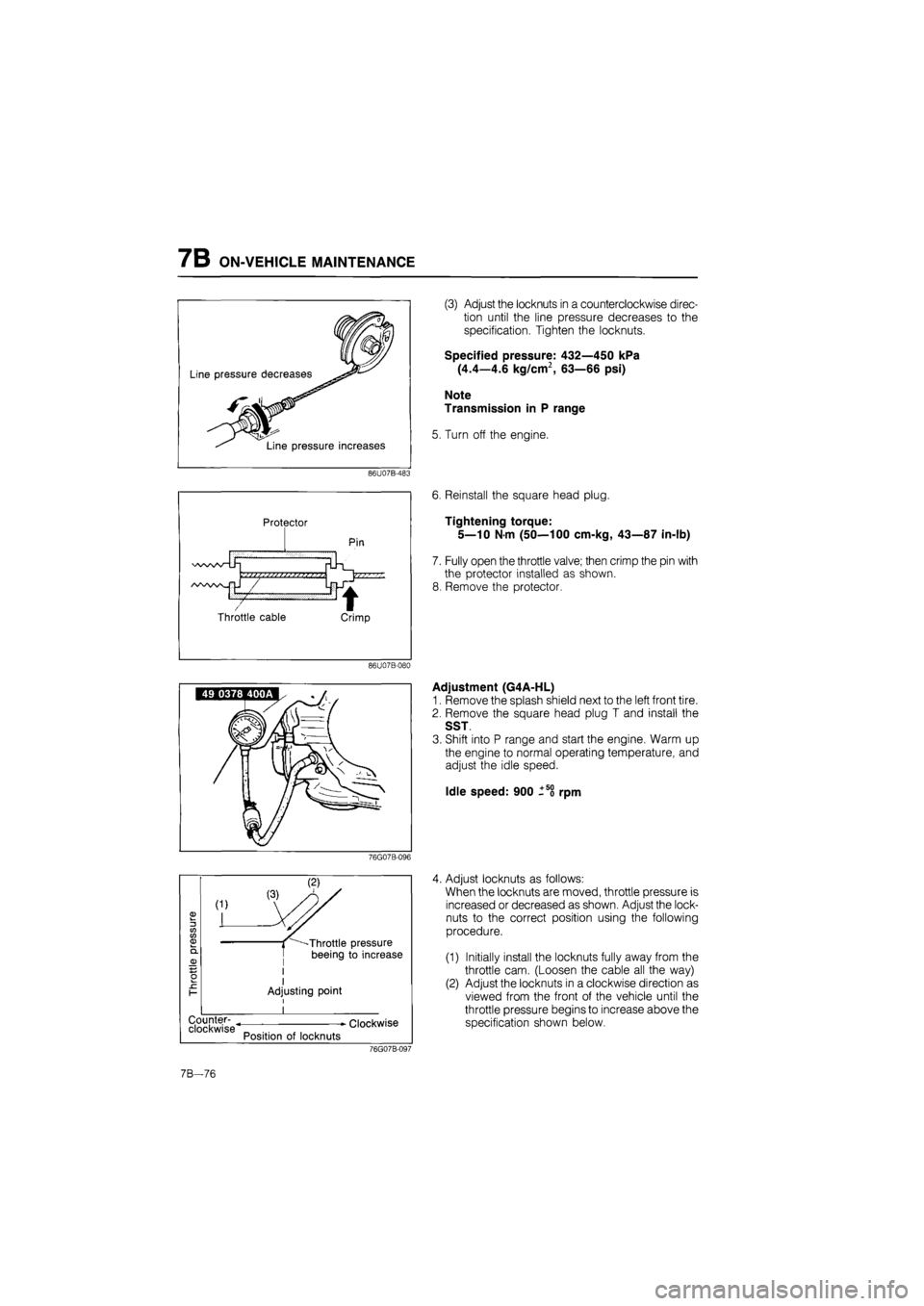
7B ON-VEHICLE MAINTENANCE
Line pressure decreases
Line pressure increases
86U07B-483
Protector
-7 / Throttle cable
86U07B-080
(3) Adjust the locknuts in a counterclockwise direc-
tion until the line pressure decreases to the
specification. Tighten the locknuts.
Specified pressure: 432—450 kPa
(4.4—4.6 kg/cm2, 63—66 psi)
Note
Transmission in P range
5. Turn off the engine.
6. Reinstall the square head plug.
Tightening torque:
5—10 N m (50—100 cm-kg, 43—87 in-lb)
7. Fully open the throttle valve; then crimp the pin with
the protector installed as shown.
8. Remove the protector.
Adjustment (G4A-HL)
1. Remove the splash shield next to the left front tire.
2. Remove the square head plug T and install the
SST
3. Shift into P range and start the engine. Warm up
the engine to normal operating temperature, and
adjust the idle speed.
Idle speed: 900 -5o rpm
76G07B-096
3 tn tn
L
Counter- ^ clockwise
Throttle pressure
beeing to increase
I Adjusting point
Position of locknuts
Clockwise
4. Adjust locknuts as follows:
When the locknuts are moved, throttle pressure is
increased or decreased as shown. Adjust the lock-
nuts to the correct position using the following
procedure.
(1) Initially install the locknuts fully away from the
throttle cam. (Loosen the cable all the way)
(2) Adjust the locknuts in a clockwise direction as
viewed from the front of the vehicle until the
throttle pressure begins to increase above the
specification shown below.
76G07B-097
7B—76
Page 943 of 1865
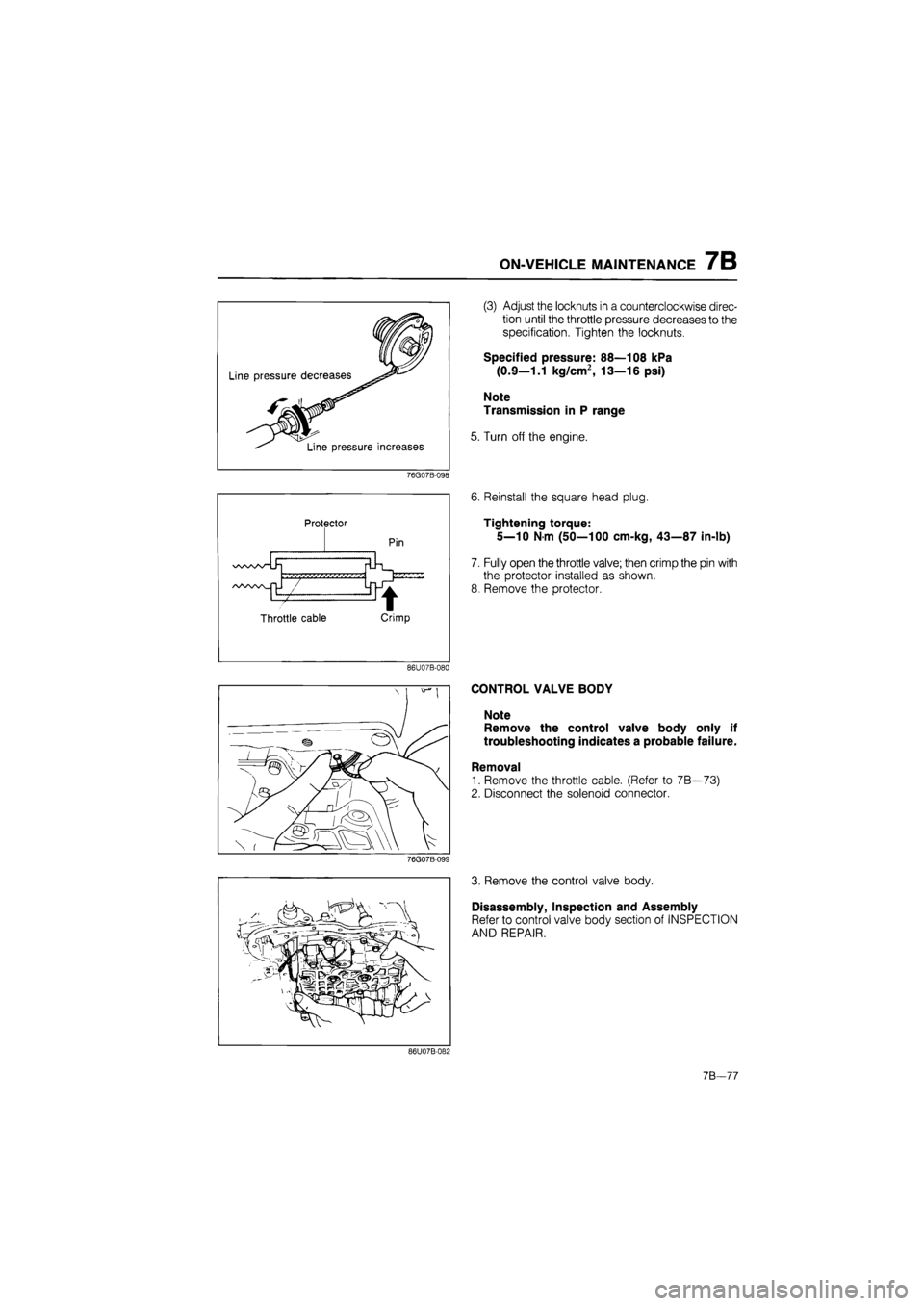
ON-VEHICLE MAINTENANCE 7B
Line pressure decreases
Line pressure increases
76G07B-098
Protector
NAAA/V^
/NA/w^nJ
Throttle cable Crimp
86U07B-080
(3) Adjust the locknuts in a counterclockwise direc-
tion until the throttle pressure decreases to the
specification. Tighten the locknuts.
Specified pressure: 88—108 kPa
(0.9—1.1 kg/cm2, 13—16 psi)
Note
Transmission in P range
5. Turn off the engine.
6. Reinstall the square head plug.
Tightening torque:
5—10 N m (50—100 cm-kg, 43—87 in-lb)
7. Fully open the throttle valve; then crimp the pin with
the protector installed as shown.
8. Remove the protector.
CONTROL VALVE BODY
Note
Remove the control valve body only if
troubleshooting indicates a probable failure.
Removal
1. Remove the throttle cable. (Refer to 7B—73)
2. Disconnect the solenoid connector.
76G07B-099
3. Remove the control valve body.
Disassembly, Inspection and Assembly
Refer to control valve body section of INSPECTION
AND REPAIR.
86U07B-082
7B—77
Page 944 of 1865
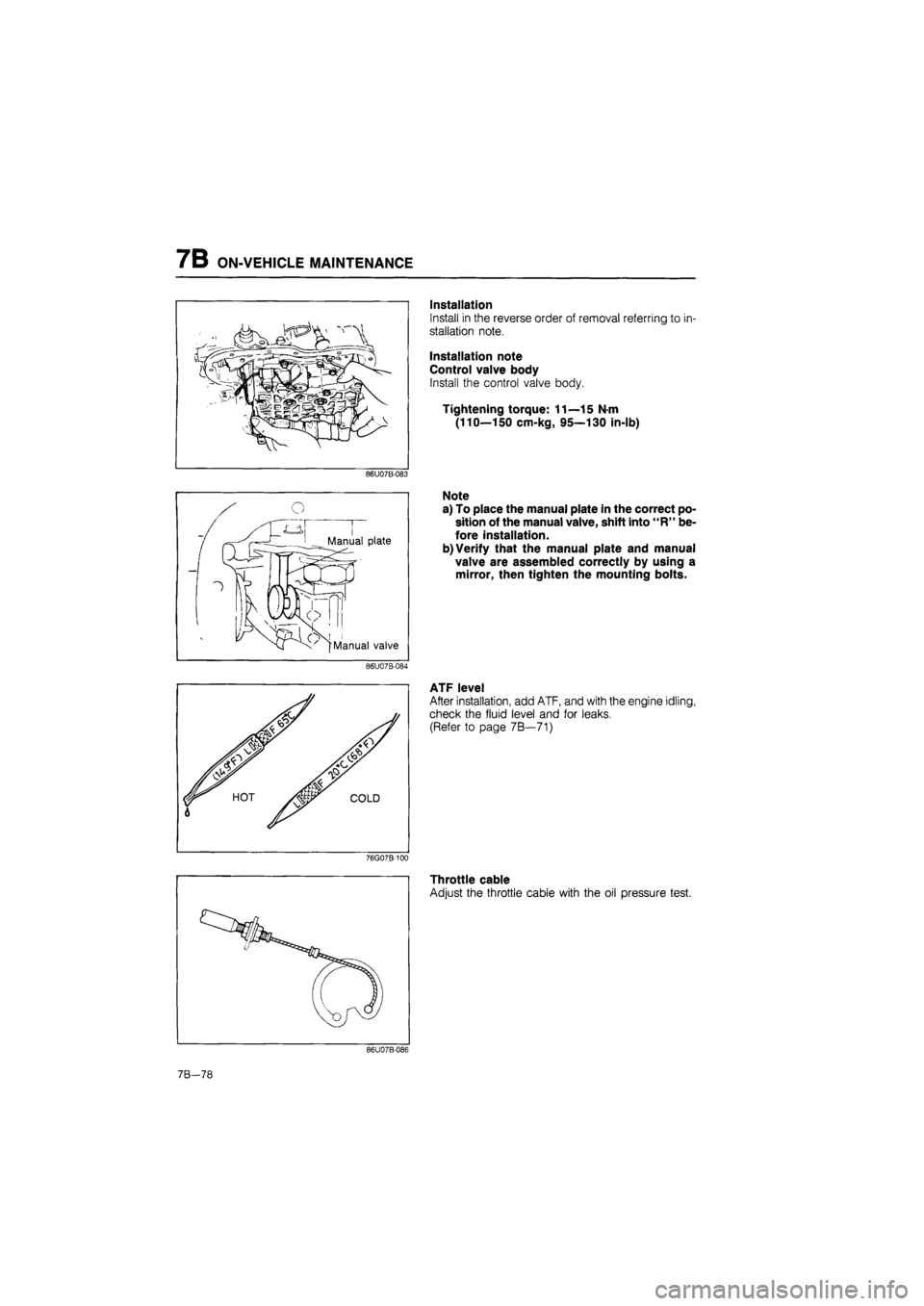
7B ON-VEHICLE MAINTENANCE
Installation
Install in the reverse order of removal referring to in-
stallation note.
Installation note
Control valve body
Install the control valve body.
Tightening torque: 11—15 N-m
(110—150 cm-kg, 95—130 in-lb)
86U07B-083
Note
a) To place the manual plate in the correct po-
sition of the manual valve, shift into "R" be-
fore installation.
b) Verify that the manual plate and manual
valve are assembled correctly by using a
mirror, then tighten the mounting bolts.
86U07B-084
w v
ATF level
After installation, add ATF, and with the engine idling,
check the fluid level and for leaks.
(Refer to page 7B—71)
76G07B-100
Throttle cable
Adjust the throttle cable with the oil pressure test.
86U07B-086
7B-78
Page 946 of 1865
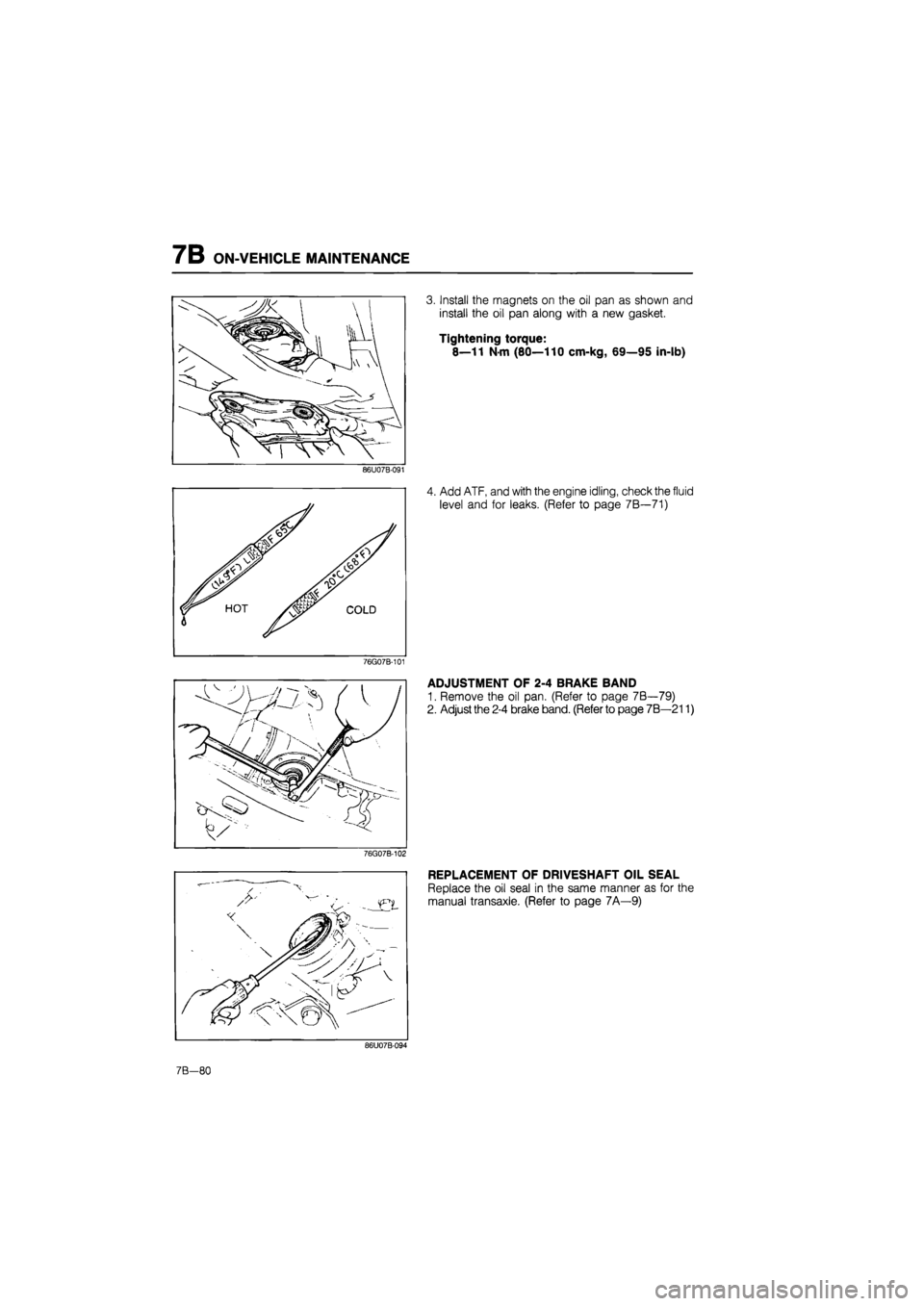
7B ON-VEHICLE MAINTENANCE
86U07B-091
76G07B-101
76G07B-102
3. Install the magnets on the oil pan as shown and
install the oil pan along with a new gasket.
Tightening torque:
8—11 Nm (80—110 cm-kg, 69—95 in-lb)
4. Add ATF, and with the engine idling, check the fluid
level and for leaks. (Refer to page 7B—71)
ADJUSTMENT OF 2-4 BRAKE BAND
1. Remove the oil pan. (Refer to page 7B—79)
2. Adjust the 2-4 brake band. (Refer to page 7B—211)
REPLACEMENT OF DRIVESHAFT OIL SEAL
Replace the oil seal in the same manner as for the
manual transaxle. (Refer to page 7A—9)
86U07B-094
7B-80
Page 949 of 1865
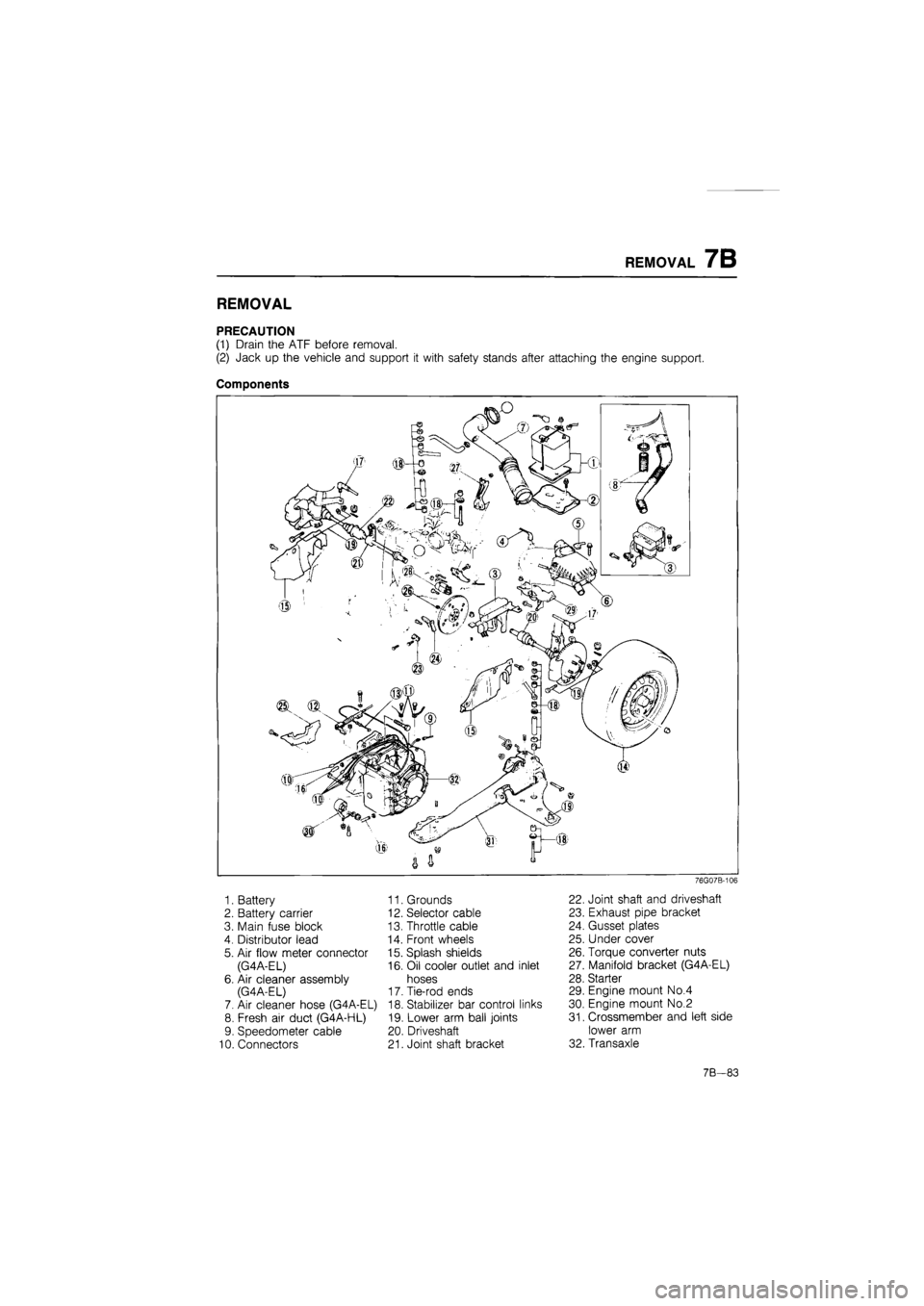
REMOVAL 7B
REMOVAL
PRECAUTION
(1) Drain the ATF before removal.
(2) Jack up the vehicle and support it with safety stands after attaching the engine support.
Components
1. Battery
2. Battery carrier
3. Main fuse block
4. Distributor lead
5. Air flow meter connector
(G4A-EL)
6. Air cleaner assembly
(G4A-EL)
7. Air cleaner hose (G4A-EL)
8. Fresh air duct (G4A-HL)
9. Speedometer cable
10. Connectors
11. Grounds
12. Selector cable
13. Throttle cable
14. Front wheels
15. Splash shields
16. Oil cooler outlet and inlet
hoses
17. Tie-rod ends
18. Stabilizer bar control links
19. Lower arm ball joints
20. Driveshaft
21. Joint shaft bracket
76G07B-106
22. Joint shaft and driveshaft
23. Exhaust pipe bracket
24. Gusset plates
25. Under cover
26. Torque converter nuts
27. Manifold bracket (G4A-EL)
28. Starter
29. Engine mount No.4
30. Engine mount No.2
31. Crossmember and left side
lower arm
32. Transaxle
7B—83
Page 952 of 1865
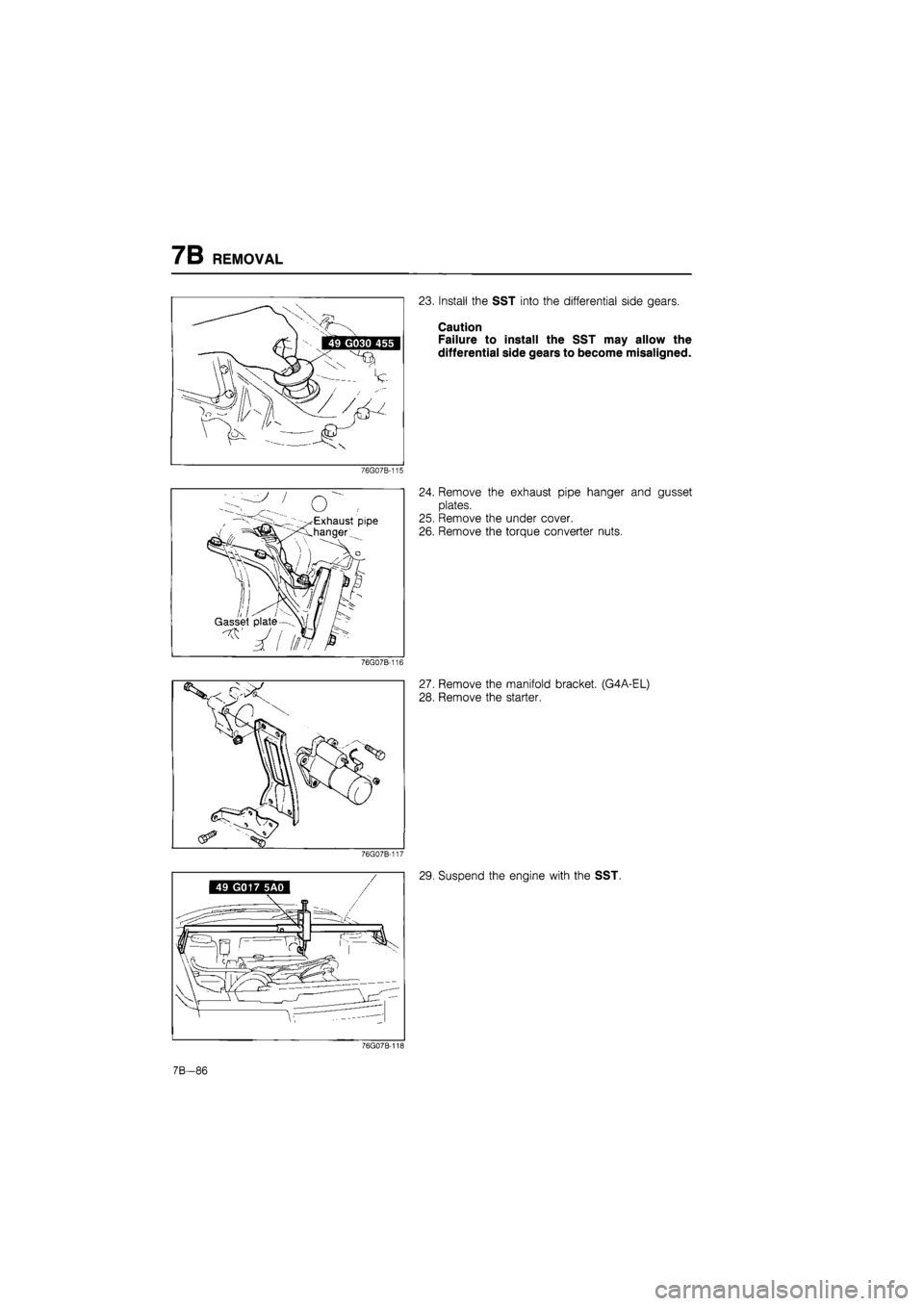
7B REMOVAL
76G07B-115
o ' ...
Exhaust pipe
hanger..
Gasset plate —
76G07B-116
23. Install the SST into the differential side gears.
Caution
Failure to install the SST may allow the
differential side gears to become misaligned.
24. Remove the exhaust pipe hanger and gusset
plates.
25. Remove the under cover.
26. Remove the torque converter nuts.
27. Remove the manifold bracket. (G4A-EL)
28. Remove the starter.
76G07B-117
49 G017 5A0
29. Suspend the engine with the SST.
76G07B-118
7B-86
Page 953 of 1865
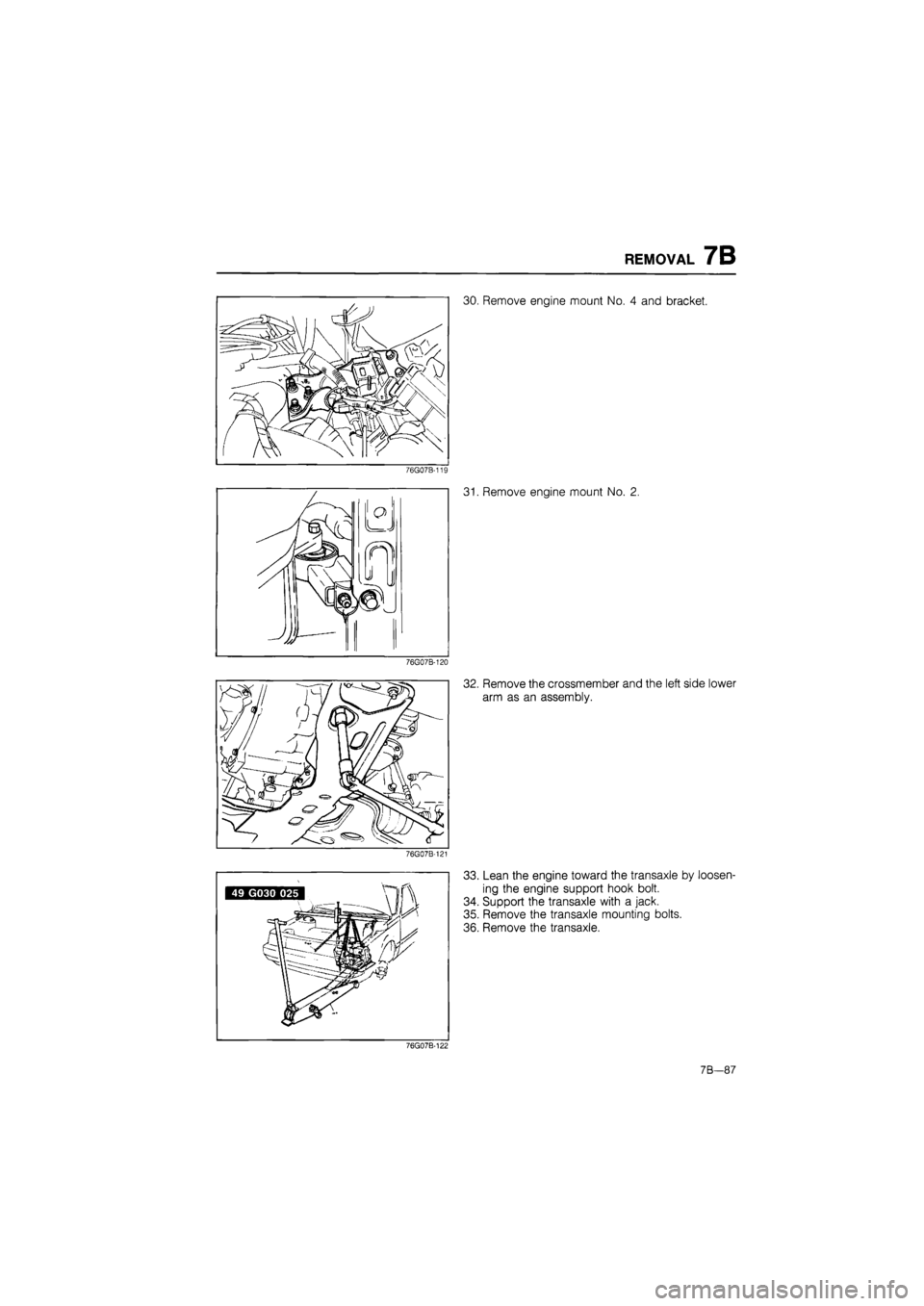
REMOVAL 7B
30. Remove engine mount No. 4 and bracket.
76G07B-119
76G07B-120
76G07B-121
31. Remove engine mount No. 2.
32. Remove the crossmember and the left side lower
arm as an assembly.
33. Lean the engine toward the transaxle by loosen-
ing the engine support hook bolt.
34. Support the transaxle with a jack.
35. Remove the transaxle mounting bolts.
36. Remove the transaxle.
76G07B-122
7B—87
Page 1001 of 1865
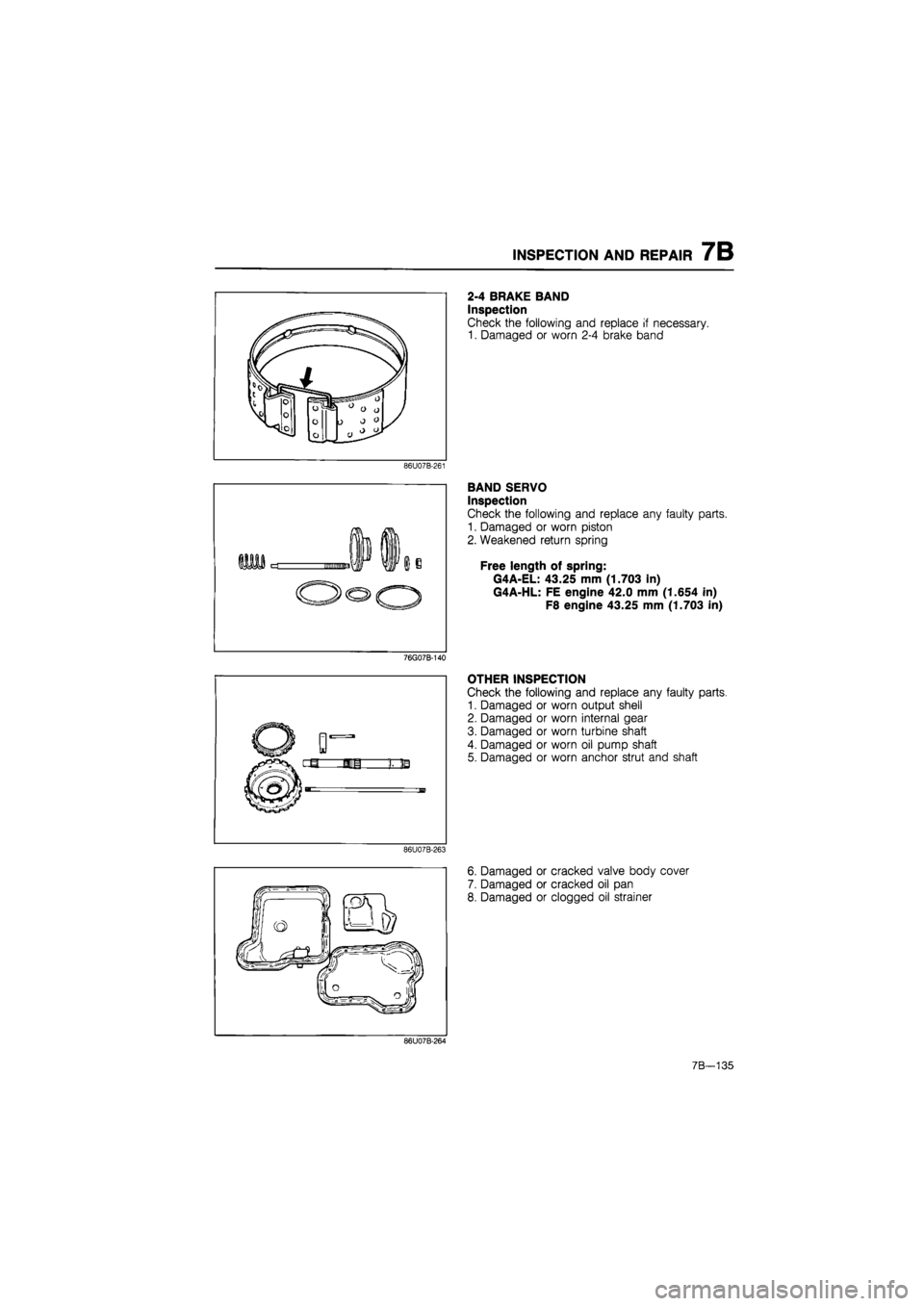
INSPECTION AND REPAIR 7B
2-4 BRAKE BAND
Inspection
Check the following and replace if necessary.
1. Damaged or worn 2-4 brake band
86U07B-261
BAND SERVO
Inspection
Check the following and replace any faulty parts.
1. Damaged or worn piston
2. Weakened return spring
Free length of spring:
G4A-EL: 43.25 mm (1.703 in)
G4A-HL: FE engine 42.0 mm (1.654 in)
F8 engine 43.25 mm (1.703 in)
76G07B-140
OTHER INSPECTION
Check the following and replace any faulty parts.
1. Damaged or worn output shell
2. Damaged or worn internal gear
3. Damaged or worn turbine shaft
4. Damaged or worn oil pump shaft
5. Damaged or worn anchor strut and shaft
86U07B-263
6. Damaged or cracked valve body cover
7. Damaged or cracked oil pan
8. Damaged or clogged oil strainer
86U07B-264
7B—135