MERCEDES-BENZ SPRINTER 2005 Service Owners Manual
Manufacturer: MERCEDES-BENZ, Model Year: 2005, Model line: SPRINTER, Model: MERCEDES-BENZ SPRINTER 2005Pages: 1232, PDF Size: 39.23 MB
Page 91 of 1232
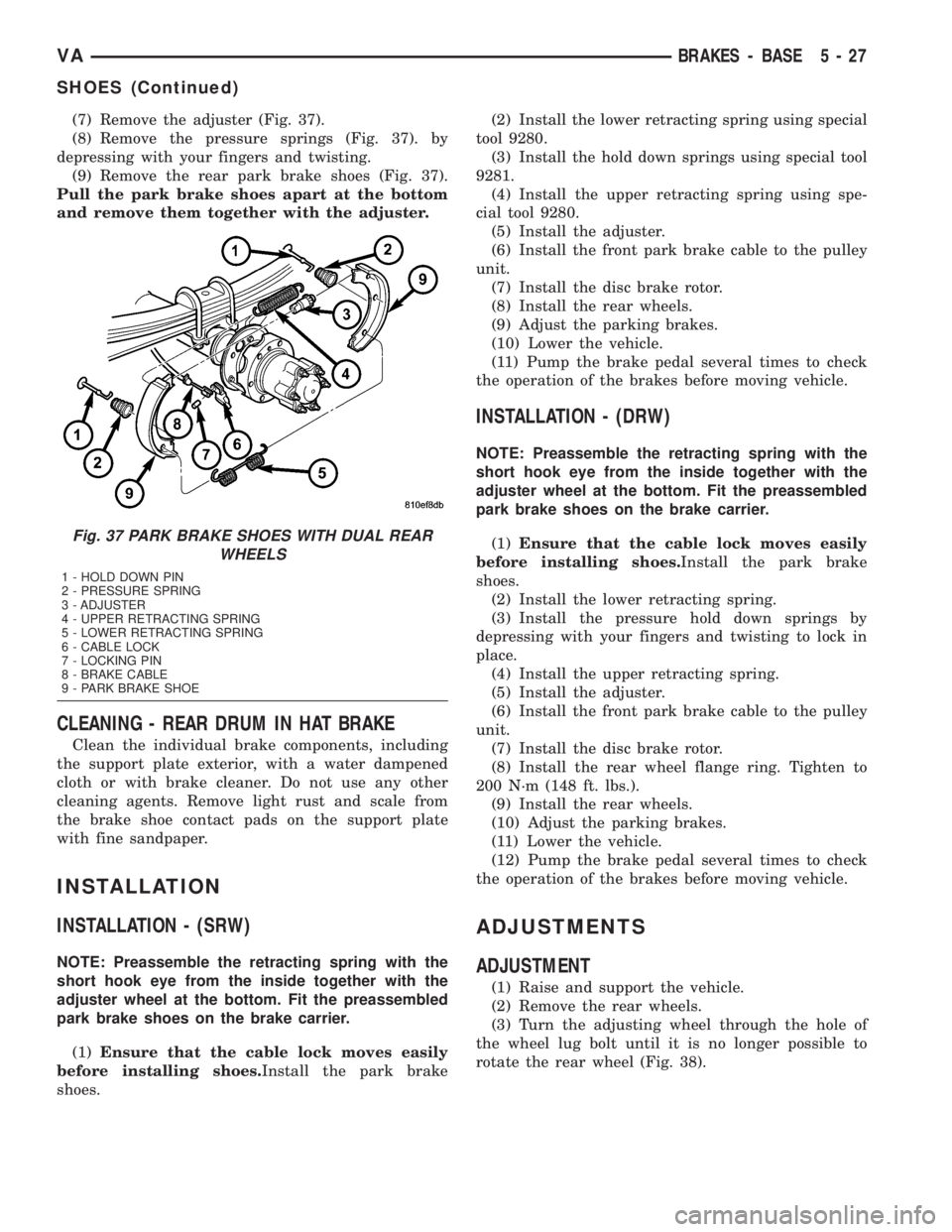
(7) Remove the adjuster (Fig. 37).
(8) Remove the pressure springs (Fig. 37). by
depressing with your fingers and twisting.
(9) Remove the rear park brake shoes (Fig. 37).
Pull the park brake shoes apart at the bottom
and remove them together with the adjuster.
CLEANING - REAR DRUM IN HAT BRAKE
Clean the individual brake components, including
the support plate exterior, with a water dampened
cloth or with brake cleaner. Do not use any other
cleaning agents. Remove light rust and scale from
the brake shoe contact pads on the support plate
with fine sandpaper.
INSTALLATION
INSTALLATION - (SRW)
NOTE: Preassemble the retracting spring with the
short hook eye from the inside together with the
adjuster wheel at the bottom. Fit the preassembled
park brake shoes on the brake carrier.
(1)Ensure that the cable lock moves easily
before installing shoes.Install the park brake
shoes.(2) Install the lower retracting spring using special
tool 9280.
(3) Install the hold down springs using special tool
9281.
(4) Install the upper retracting spring using spe-
cial tool 9280.
(5) Install the adjuster.
(6) Install the front park brake cable to the pulley
unit.
(7) Install the disc brake rotor.
(8) Install the rear wheels.
(9) Adjust the parking brakes.
(10) Lower the vehicle.
(11) Pump the brake pedal several times to check
the operation of the brakes before moving vehicle.
INSTALLATION - (DRW)
NOTE: Preassemble the retracting spring with the
short hook eye from the inside together with the
adjuster wheel at the bottom. Fit the preassembled
park brake shoes on the brake carrier.
(1)Ensure that the cable lock moves easily
before installing shoes.Install the park brake
shoes.
(2) Install the lower retracting spring.
(3) Install the pressure hold down springs by
depressing with your fingers and twisting to lock in
place.
(4) Install the upper retracting spring.
(5) Install the adjuster.
(6) Install the front park brake cable to the pulley
unit.
(7) Install the disc brake rotor.
(8) Install the rear wheel flange ring. Tighten to
200 N´m (148 ft. lbs.).
(9) Install the rear wheels.
(10) Adjust the parking brakes.
(11) Lower the vehicle.
(12) Pump the brake pedal several times to check
the operation of the brakes before moving vehicle.
ADJUSTMENTS
ADJUSTMENT
(1) Raise and support the vehicle.
(2) Remove the rear wheels.
(3) Turn the adjusting wheel through the hole of
the wheel lug bolt until it is no longer possible to
rotate the rear wheel (Fig. 38).
Fig. 37 PARK BRAKE SHOES WITH DUAL REAR
WHEELS
1 - HOLD DOWN PIN
2 - PRESSURE SPRING
3 - ADJUSTER
4 - UPPER RETRACTING SPRING
5 - LOWER RETRACTING SPRING
6 - CABLE LOCK
7 - LOCKING PIN
8 - BRAKE CABLE
9 - PARK BRAKE SHOE
VABRAKES - BASE 5 - 27
SHOES (Continued)
Page 92 of 1232
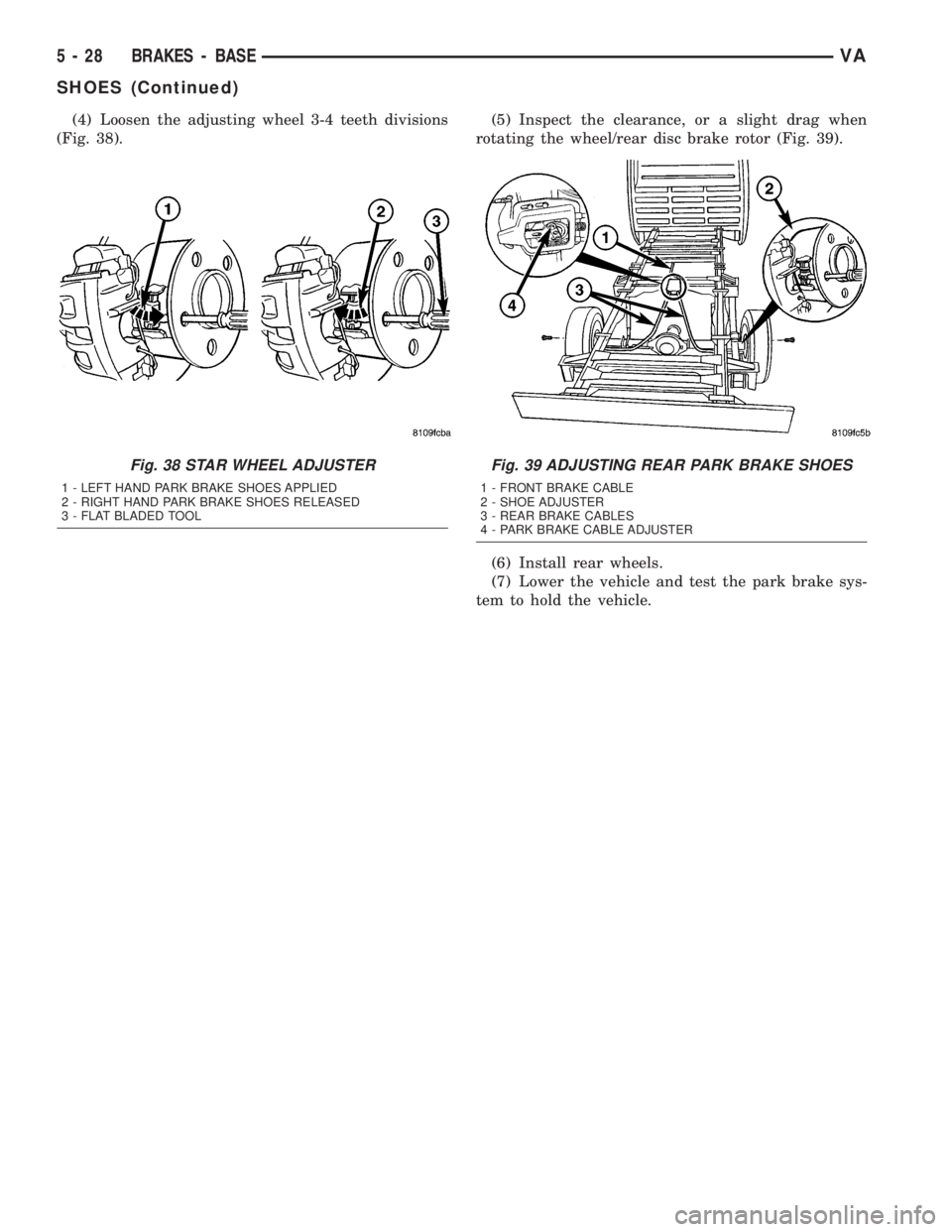
(4) Loosen the adjusting wheel 3-4 teeth divisions
(Fig. 38).(5) Inspect the clearance, or a slight drag when
rotating the wheel/rear disc brake rotor (Fig. 39).
(6) Install rear wheels.
(7) Lower the vehicle and test the park brake sys-
tem to hold the vehicle.
Fig. 38 STAR WHEEL ADJUSTER
1 - LEFT HAND PARK BRAKE SHOES APPLIED
2 - RIGHT HAND PARK BRAKE SHOES RELEASED
3 - FLAT BLADED TOOL
Fig. 39 ADJUSTING REAR PARK BRAKE SHOES
1 - FRONT BRAKE CABLE
2 - SHOE ADJUSTER
3 - REAR BRAKE CABLES
4 - PARK BRAKE CABLE ADJUSTER
5 - 28 BRAKES - BASEVA
SHOES (Continued)
Page 93 of 1232
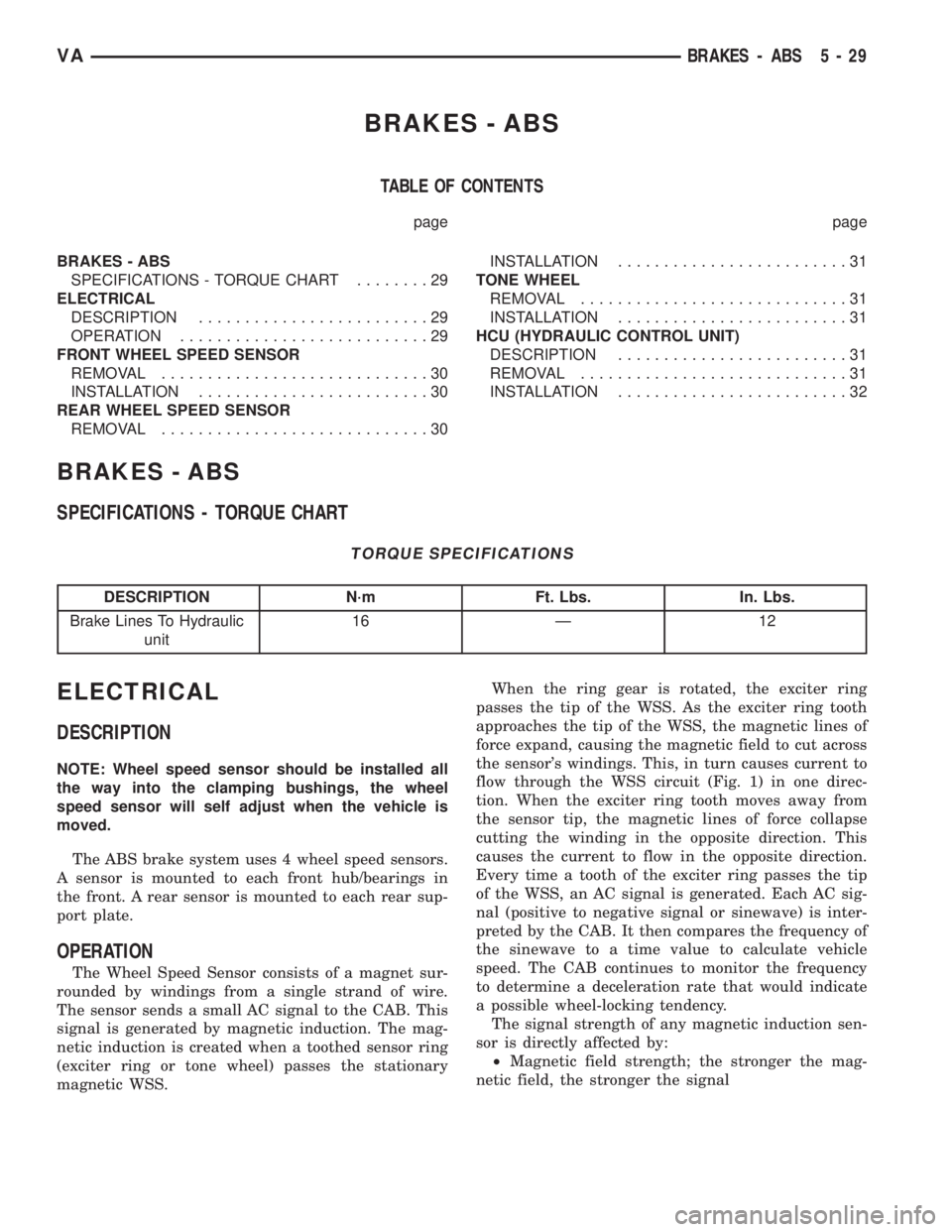
BRAKES - ABS
TABLE OF CONTENTS
page page
BRAKES - ABS
SPECIFICATIONS - TORQUE CHART........29
ELECTRICAL
DESCRIPTION.........................29
OPERATION...........................29
FRONT WHEEL SPEED SENSOR
REMOVAL.............................30
INSTALLATION.........................30
REAR WHEEL SPEED SENSOR
REMOVAL.............................30INSTALLATION.........................31
TONE WHEEL
REMOVAL.............................31
INSTALLATION.........................31
HCU (HYDRAULIC CONTROL UNIT)
DESCRIPTION.........................31
REMOVAL.............................31
INSTALLATION.........................32
BRAKES - ABS
SPECIFICATIONS - TORQUE CHART
TORQUE SPECIFICATIONS
DESCRIPTION N´m Ft. Lbs. In. Lbs.
Brake Lines To Hydraulic
unit16 Ð 12
ELECTRICAL
DESCRIPTION
NOTE: Wheel speed sensor should be installed all
the way into the clamping bushings, the wheel
speed sensor will self adjust when the vehicle is
moved.
The ABS brake system uses 4 wheel speed sensors.
A sensor is mounted to each front hub/bearings in
the front. A rear sensor is mounted to each rear sup-
port plate.
OPERATION
The Wheel Speed Sensor consists of a magnet sur-
rounded by windings from a single strand of wire.
The sensor sends a small AC signal to the CAB. This
signal is generated by magnetic induction. The mag-
netic induction is created when a toothed sensor ring
(exciter ring or tone wheel) passes the stationary
magnetic WSS.When the ring gear is rotated, the exciter ring
passes the tip of the WSS. As the exciter ring tooth
approaches the tip of the WSS, the magnetic lines of
force expand, causing the magnetic field to cut across
the sensor's windings. This, in turn causes current to
flow through the WSS circuit (Fig. 1) in one direc-
tion. When the exciter ring tooth moves away from
the sensor tip, the magnetic lines of force collapse
cutting the winding in the opposite direction. This
causes the current to flow in the opposite direction.
Every time a tooth of the exciter ring passes the tip
of the WSS, an AC signal is generated. Each AC sig-
nal (positive to negative signal or sinewave) is inter-
preted by the CAB. It then compares the frequency of
the sinewave to a time value to calculate vehicle
speed. The CAB continues to monitor the frequency
to determine a deceleration rate that would indicate
a possible wheel-locking tendency.
The signal strength of any magnetic induction sen-
sor is directly affected by:
²Magnetic field strength; the stronger the mag-
netic field, the stronger the signal
VABRAKES - ABS 5 - 29
Page 94 of 1232
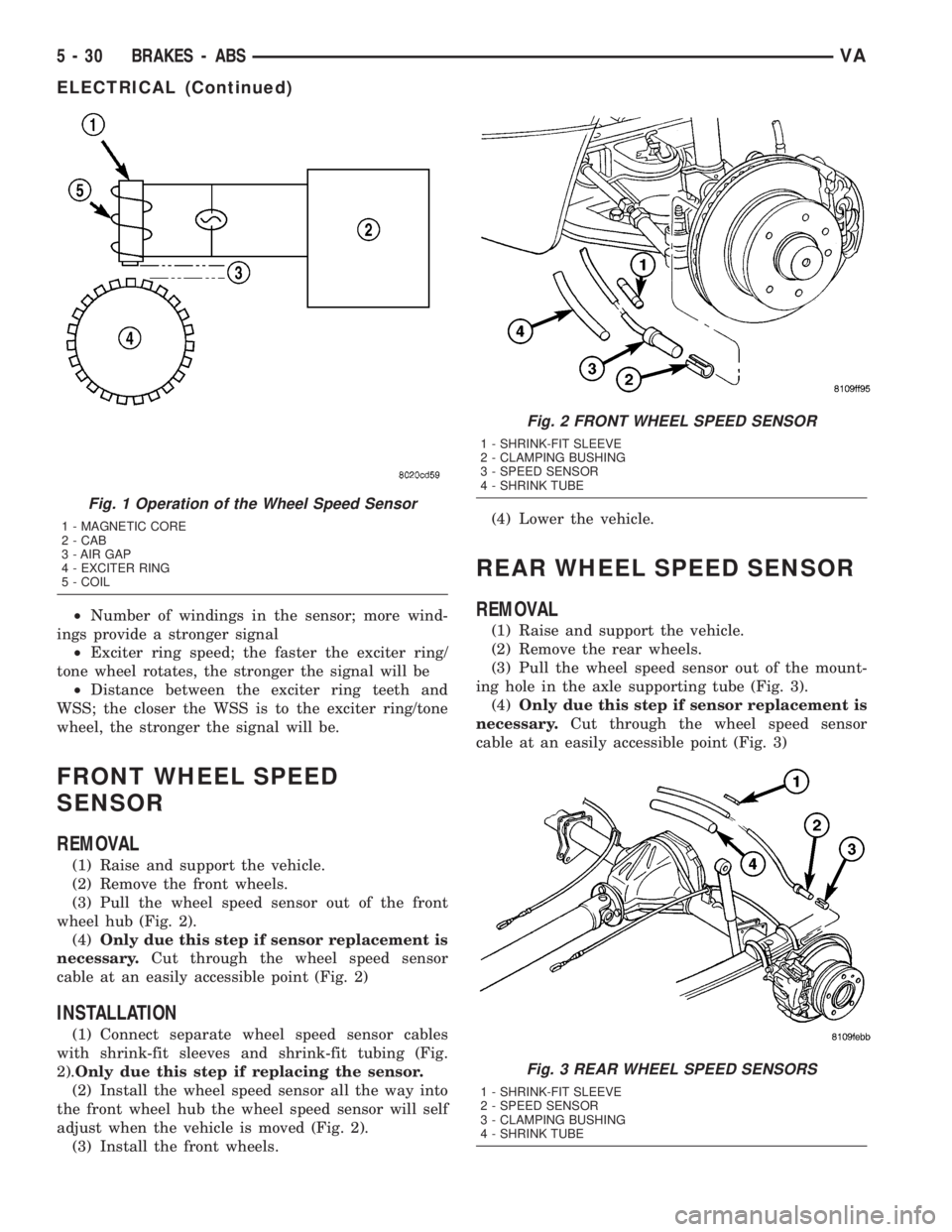
²Number of windings in the sensor; more wind-
ings provide a stronger signal
²Exciter ring speed; the faster the exciter ring/
tone wheel rotates, the stronger the signal will be
²Distance between the exciter ring teeth and
WSS; the closer the WSS is to the exciter ring/tone
wheel, the stronger the signal will be.
FRONT WHEEL SPEED
SENSOR
REMOVAL
(1) Raise and support the vehicle.
(2) Remove the front wheels.
(3) Pull the wheel speed sensor out of the front
wheel hub (Fig. 2).
(4)Only due this step if sensor replacement is
necessary.Cut through the wheel speed sensor
cable at an easily accessible point (Fig. 2)
INSTALLATION
(1) Connect separate wheel speed sensor cables
with shrink-fit sleeves and shrink-fit tubing (Fig.
2).Only due this step if replacing the sensor.
(2) Install the wheel speed sensor all the way into
the front wheel hub the wheel speed sensor will self
adjust when the vehicle is moved (Fig. 2).
(3) Install the front wheels.(4) Lower the vehicle.
REAR WHEEL SPEED SENSOR
REMOVAL
(1) Raise and support the vehicle.
(2) Remove the rear wheels.
(3) Pull the wheel speed sensor out of the mount-
ing hole in the axle supporting tube (Fig. 3).
(4)Only due this step if sensor replacement is
necessary.Cut through the wheel speed sensor
cable at an easily accessible point (Fig. 3)
Fig. 1 Operation of the Wheel Speed Sensor
1 - MAGNETIC CORE
2 - CAB
3 - AIR GAP
4 - EXCITER RING
5 - COIL
Fig. 2 FRONT WHEEL SPEED SENSOR
1 - SHRINK-FIT SLEEVE
2 - CLAMPING BUSHING
3 - SPEED SENSOR
4 - SHRINK TUBE
Fig. 3 REAR WHEEL SPEED SENSORS
1 - SHRINK-FIT SLEEVE
2 - SPEED SENSOR
3 - CLAMPING BUSHING
4 - SHRINK TUBE
5 - 30 BRAKES - ABSVA
ELECTRICAL (Continued)
Page 95 of 1232
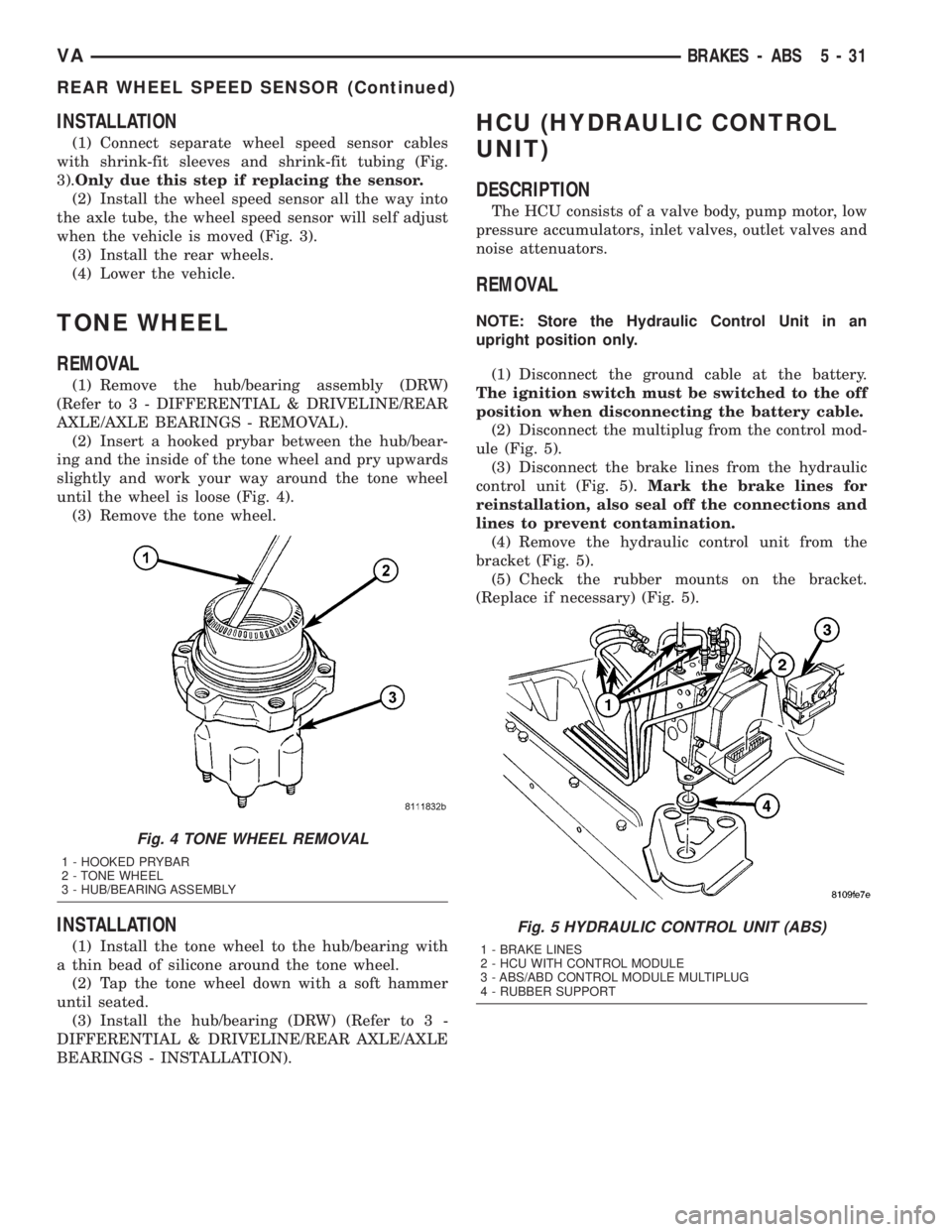
INSTALLATION
(1) Connect separate wheel speed sensor cables
with shrink-fit sleeves and shrink-fit tubing (Fig.
3).Only due this step if replacing the sensor.
(2) Install the wheel speed sensor all the way into
the axle tube, the wheel speed sensor will self adjust
when the vehicle is moved (Fig. 3).
(3) Install the rear wheels.
(4) Lower the vehicle.
TONE WHEEL
REMOVAL
(1) Remove the hub/bearing assembly (DRW)
(Refer to 3 - DIFFERENTIAL & DRIVELINE/REAR
AXLE/AXLE BEARINGS - REMOVAL).
(2) Insert a hooked prybar between the hub/bear-
ing and the inside of the tone wheel and pry upwards
slightly and work your way around the tone wheel
until the wheel is loose (Fig. 4).
(3) Remove the tone wheel.
INSTALLATION
(1) Install the tone wheel to the hub/bearing with
a thin bead of silicone around the tone wheel.
(2) Tap the tone wheel down with a soft hammer
until seated.
(3) Install the hub/bearing (DRW) (Refer to 3 -
DIFFERENTIAL & DRIVELINE/REAR AXLE/AXLE
BEARINGS - INSTALLATION).
HCU (HYDRAULIC CONTROL
UNIT)
DESCRIPTION
The HCU consists of a valve body, pump motor, low
pressure accumulators, inlet valves, outlet valves and
noise attenuators.
REMOVAL
NOTE: Store the Hydraulic Control Unit in an
upright position only.
(1) Disconnect the ground cable at the battery.
The ignition switch must be switched to the off
position when disconnecting the battery cable.
(2) Disconnect the multiplug from the control mod-
ule (Fig. 5).
(3) Disconnect the brake lines from the hydraulic
control unit (Fig. 5).Mark the brake lines for
reinstallation, also seal off the connections and
lines to prevent contamination.
(4) Remove the hydraulic control unit from the
bracket (Fig. 5).
(5) Check the rubber mounts on the bracket.
(Replace if necessary) (Fig. 5).
Fig. 4 TONE WHEEL REMOVAL
1 - HOOKED PRYBAR
2 - TONE WHEEL
3 - HUB/BEARING ASSEMBLY
Fig. 5 HYDRAULIC CONTROL UNIT (ABS)
1 - BRAKE LINES
2 - HCU WITH CONTROL MODULE
3 - ABS/ABD CONTROL MODULE MULTIPLUG
4 - RUBBER SUPPORT
VABRAKES - ABS 5 - 31
REAR WHEEL SPEED SENSOR (Continued)
Page 96 of 1232
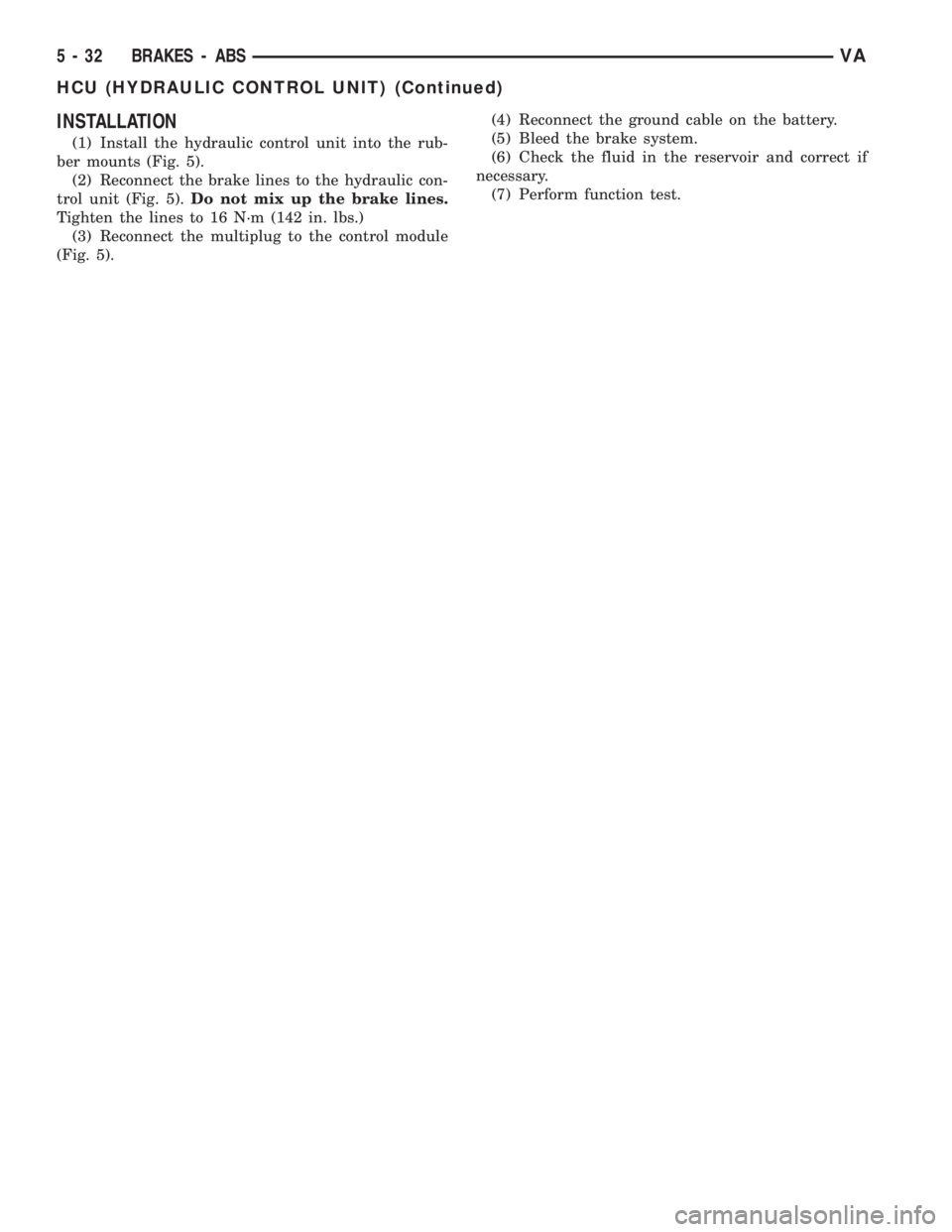
INSTALLATION
(1) Install the hydraulic control unit into the rub-
ber mounts (Fig. 5).
(2) Reconnect the brake lines to the hydraulic con-
trol unit (Fig. 5).Do not mix up the brake lines.
Tighten the lines to 16 N´m (142 in. lbs.)
(3) Reconnect the multiplug to the control module
(Fig. 5).(4) Reconnect the ground cable on the battery.
(5) Bleed the brake system.
(6) Check the fluid in the reservoir and correct if
necessary.
(7) Perform function test.
5 - 32 BRAKES - ABSVA
HCU (HYDRAULIC CONTROL UNIT) (Continued)
Page 97 of 1232
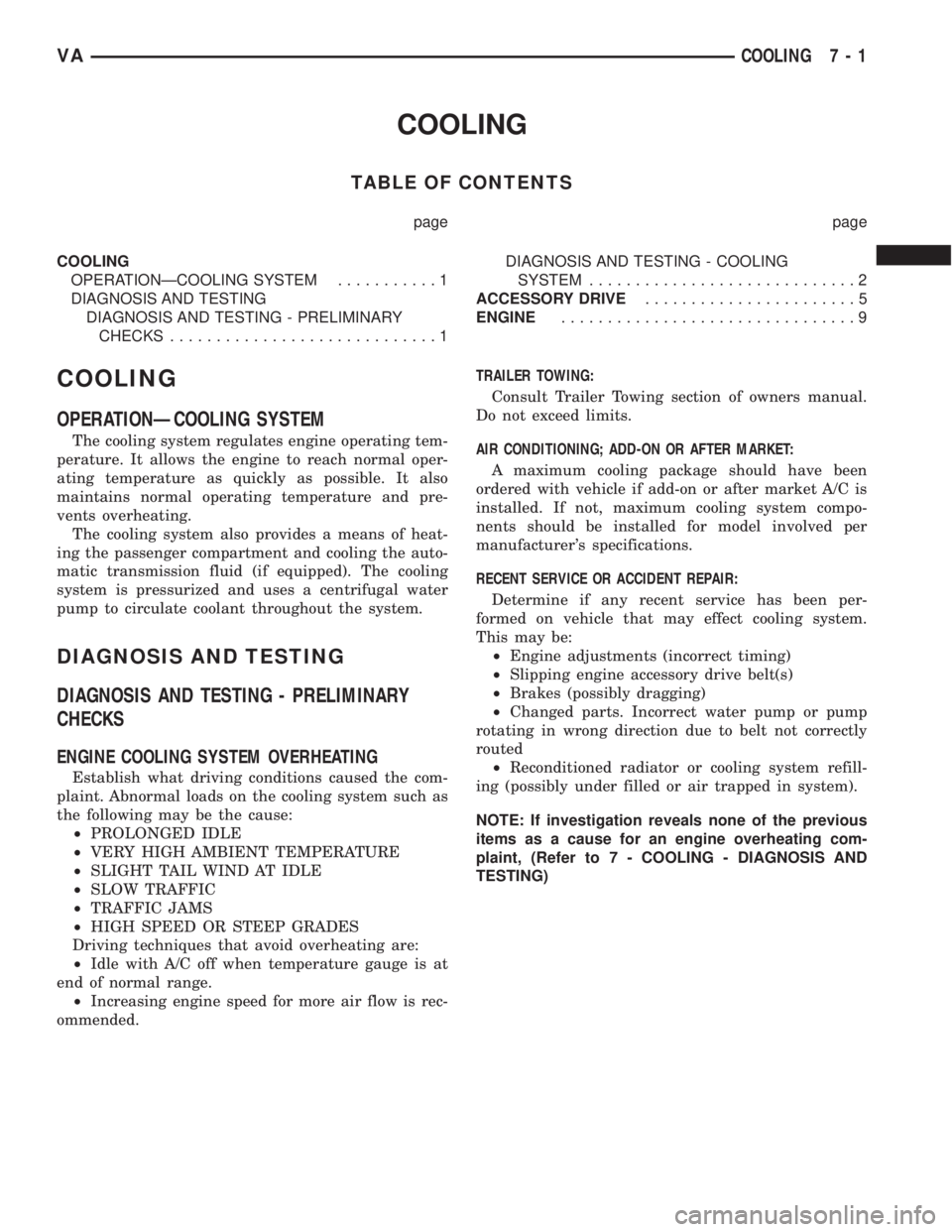
COOLING
TABLE OF CONTENTS
page page
COOLING
OPERATIONÐCOOLING SYSTEM...........1
DIAGNOSIS AND TESTING
DIAGNOSIS AND TESTING - PRELIMINARY
CHECKS.............................1DIAGNOSIS AND TESTING - COOLING
SYSTEM.............................2
ACCESSORY DRIVE.......................5
ENGINE................................9
COOLING
OPERATIONÐCOOLING SYSTEM
The cooling system regulates engine operating tem-
perature. It allows the engine to reach normal oper-
ating temperature as quickly as possible. It also
maintains normal operating temperature and pre-
vents overheating.
The cooling system also provides a means of heat-
ing the passenger compartment and cooling the auto-
matic transmission fluid (if equipped). The cooling
system is pressurized and uses a centrifugal water
pump to circulate coolant throughout the system.
DIAGNOSIS AND TESTING
DIAGNOSIS AND TESTING - PRELIMINARY
CHECKS
ENGINE COOLING SYSTEM OVERHEATING
Establish what driving conditions caused the com-
plaint. Abnormal loads on the cooling system such as
the following may be the cause:
²PROLONGED IDLE
²VERY HIGH AMBIENT TEMPERATURE
²SLIGHT TAIL WIND AT IDLE
²SLOW TRAFFIC
²TRAFFIC JAMS
²HIGH SPEED OR STEEP GRADES
Driving techniques that avoid overheating are:
²Idle with A/C off when temperature gauge is at
end of normal range.
²Increasing engine speed for more air flow is rec-
ommended.TRAILER TOWING:
Consult Trailer Towing section of owners manual.
Do not exceed limits.
AIR CONDITIONING; ADD-ON OR AFTER MARKET:
A maximum cooling package should have been
ordered with vehicle if add-on or after market A/C is
installed. If not, maximum cooling system compo-
nents should be installed for model involved per
manufacturer's specifications.
RECENT SERVICE OR ACCIDENT REPAIR:
Determine if any recent service has been per-
formed on vehicle that may effect cooling system.
This may be:
²Engine adjustments (incorrect timing)
²Slipping engine accessory drive belt(s)
²Brakes (possibly dragging)
²Changed parts. Incorrect water pump or pump
rotating in wrong direction due to belt not correctly
routed
²Reconditioned radiator or cooling system refill-
ing (possibly under filled or air trapped in system).
NOTE: If investigation reveals none of the previous
items as a cause for an engine overheating com-
plaint, (Refer to 7 - COOLING - DIAGNOSIS AND
TESTING)
VACOOLING 7 - 1
Page 98 of 1232
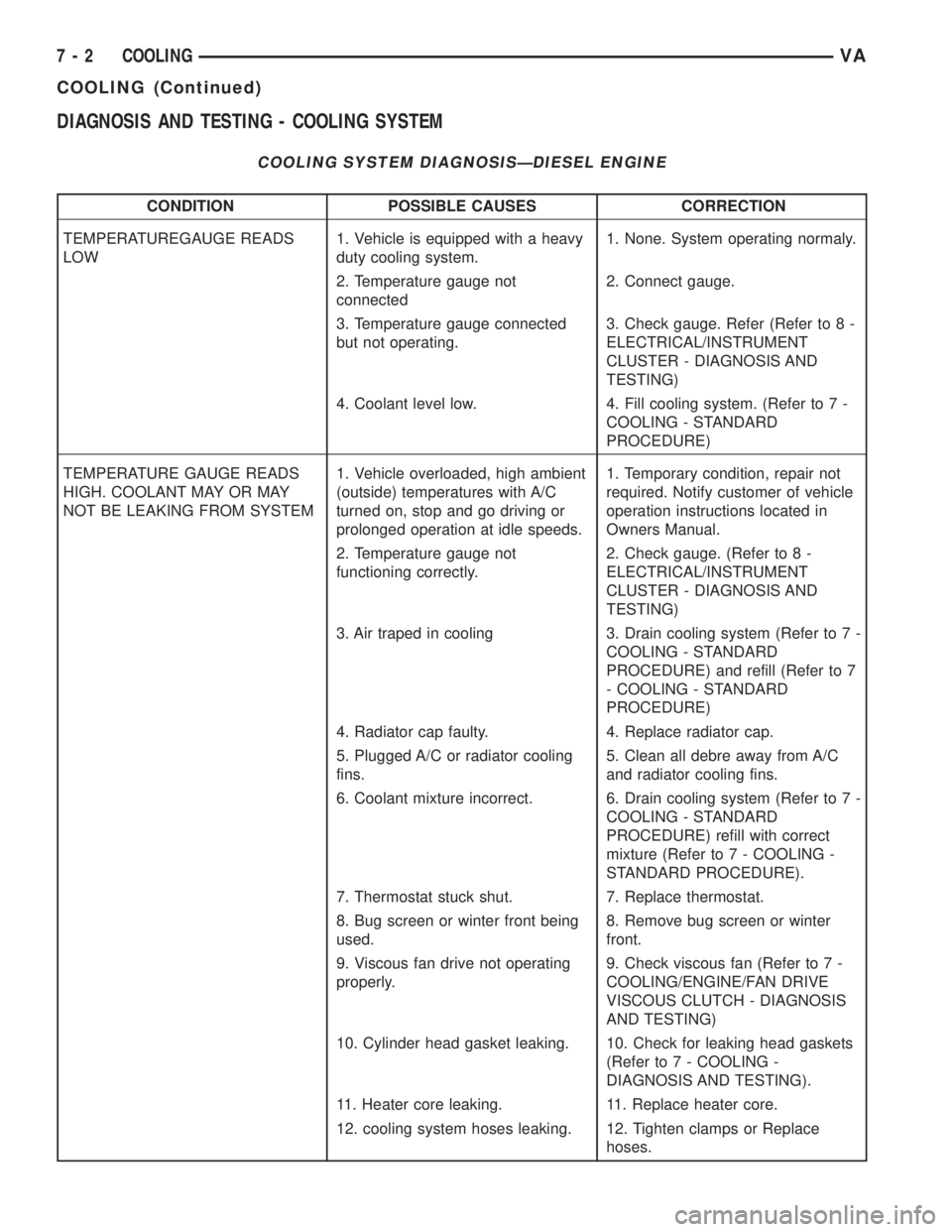
DIAGNOSIS AND TESTING - COOLING SYSTEM
COOLING SYSTEM DIAGNOSISÐDIESEL ENGINE
CONDITION POSSIBLE CAUSES CORRECTION
TEMPERATUREGAUGE READS
LOW1. Vehicle is equipped with a heavy
duty cooling system.1. None. System operating normaly.
2. Temperature gauge not
connected2. Connect gauge.
3. Temperature gauge connected
but not operating.3. Check gauge. Refer (Refer to 8 -
ELECTRICAL/INSTRUMENT
CLUSTER - DIAGNOSIS AND
TESTING)
4. Coolant level low. 4. Fill cooling system. (Refer to 7 -
COOLING - STANDARD
PROCEDURE)
TEMPERATURE GAUGE READS
HIGH. COOLANT MAY OR MAY
NOT BE LEAKING FROM SYSTEM1. Vehicle overloaded, high ambient
(outside) temperatures with A/C
turned on, stop and go driving or
prolonged operation at idle speeds.1. Temporary condition, repair not
required. Notify customer of vehicle
operation instructions located in
Owners Manual.
2. Temperature gauge not
functioning correctly.2. Check gauge. (Refer to 8 -
ELECTRICAL/INSTRUMENT
CLUSTER - DIAGNOSIS AND
TESTING)
3. Air traped in cooling 3. Drain cooling system (Refer to 7 -
COOLING - STANDARD
PROCEDURE) and refill (Refer to 7
- COOLING - STANDARD
PROCEDURE)
4. Radiator cap faulty. 4. Replace radiator cap.
5. Plugged A/C or radiator cooling
fins.5. Clean all debre away from A/C
and radiator cooling fins.
6. Coolant mixture incorrect. 6. Drain cooling system (Refer to 7 -
COOLING - STANDARD
PROCEDURE) refill with correct
mixture (Refer to 7 - COOLING -
STANDARD PROCEDURE).
7. Thermostat stuck shut. 7. Replace thermostat.
8. Bug screen or winter front being
used.8. Remove bug screen or winter
front.
9. Viscous fan drive not operating
properly.9. Check viscous fan (Refer to 7 -
COOLING/ENGINE/FAN DRIVE
VISCOUS CLUTCH - DIAGNOSIS
AND TESTING)
10. Cylinder head gasket leaking. 10. Check for leaking head gaskets
(Refer to 7 - COOLING -
DIAGNOSIS AND TESTING).
11. Heater core leaking. 11. Replace heater core.
12. cooling system hoses leaking. 12. Tighten clamps or Replace
hoses.
7 - 2 COOLINGVA
COOLING (Continued)
Page 99 of 1232
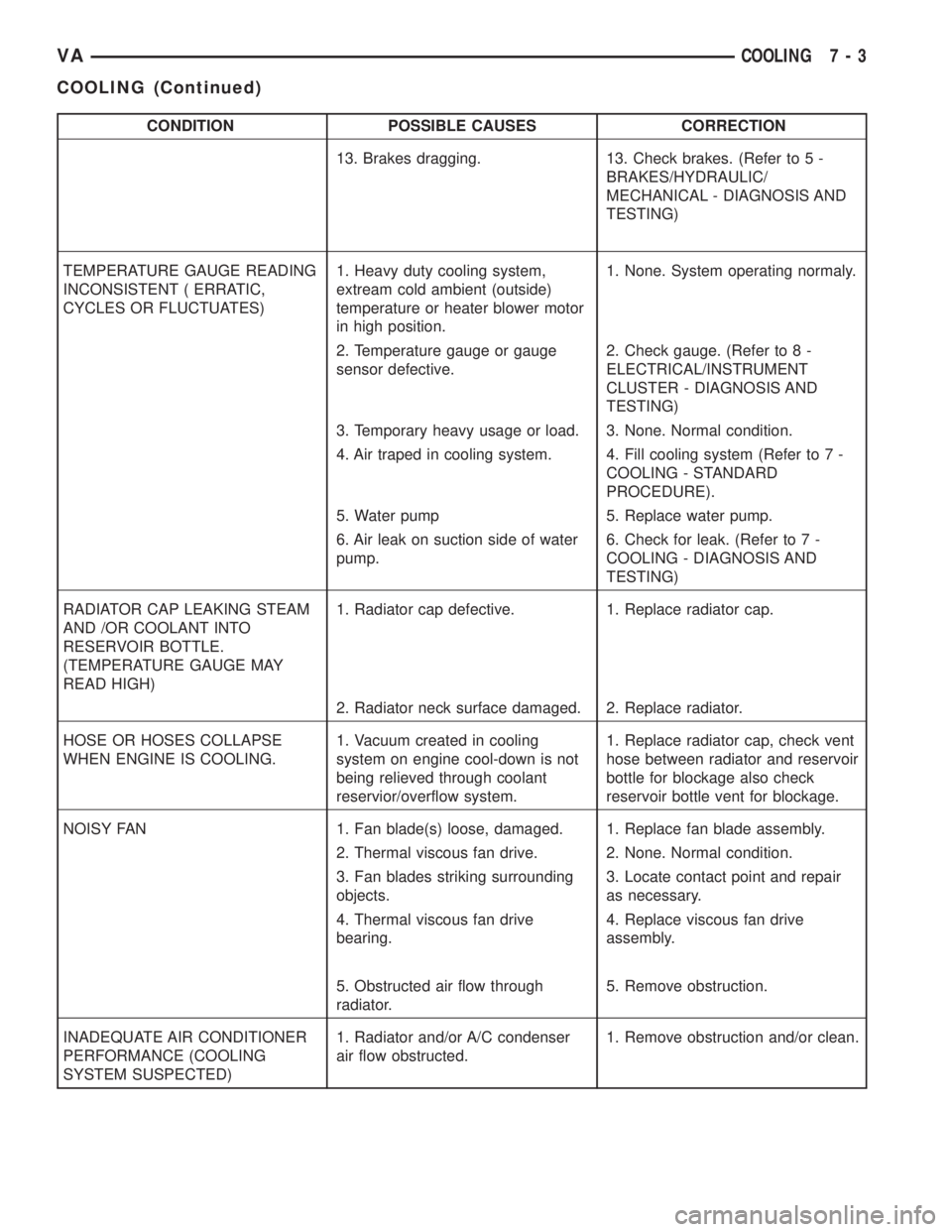
CONDITION POSSIBLE CAUSES CORRECTION
13. Brakes dragging. 13. Check brakes. (Refer to 5 -
BRAKES/HYDRAULIC/
MECHANICAL - DIAGNOSIS AND
TESTING)
TEMPERATURE GAUGE READING
INCONSISTENT ( ERRATIC,
CYCLES OR FLUCTUATES)1. Heavy duty cooling system,
extream cold ambient (outside)
temperature or heater blower motor
in high position.1. None. System operating normaly.
2. Temperature gauge or gauge
sensor defective.2. Check gauge. (Refer to 8 -
ELECTRICAL/INSTRUMENT
CLUSTER - DIAGNOSIS AND
TESTING)
3. Temporary heavy usage or load. 3. None. Normal condition.
4. Air traped in cooling system. 4. Fill cooling system (Refer to 7 -
COOLING - STANDARD
PROCEDURE).
5. Water pump 5. Replace water pump.
6. Air leak on suction side of water
pump.6. Check for leak. (Refer to 7 -
COOLING - DIAGNOSIS AND
TESTING)
RADIATOR CAP LEAKING STEAM
AND /OR COOLANT INTO
RESERVOIR BOTTLE.
(TEMPERATURE GAUGE MAY
READ HIGH)1. Radiator cap defective. 1. Replace radiator cap.
2. Radiator neck surface damaged. 2. Replace radiator.
HOSE OR HOSES COLLAPSE
WHEN ENGINE IS COOLING.1. Vacuum created in cooling
system on engine cool-down is not
being relieved through coolant
reservior/overflow system.1. Replace radiator cap, check vent
hose between radiator and reservoir
bottle for blockage also check
reservoir bottle vent for blockage.
NOISY FAN 1. Fan blade(s) loose, damaged. 1. Replace fan blade assembly.
2. Thermal viscous fan drive. 2. None. Normal condition.
3. Fan blades striking surrounding
objects.3. Locate contact point and repair
as necessary.
4. Thermal viscous fan drive
bearing.4. Replace viscous fan drive
assembly.
5. Obstructed air flow through
radiator.5. Remove obstruction.
INADEQUATE AIR CONDITIONER
PERFORMANCE (COOLING
SYSTEM SUSPECTED)1. Radiator and/or A/C condenser
air flow obstructed.1. Remove obstruction and/or clean.
VACOOLING 7 - 3
COOLING (Continued)
Page 100 of 1232
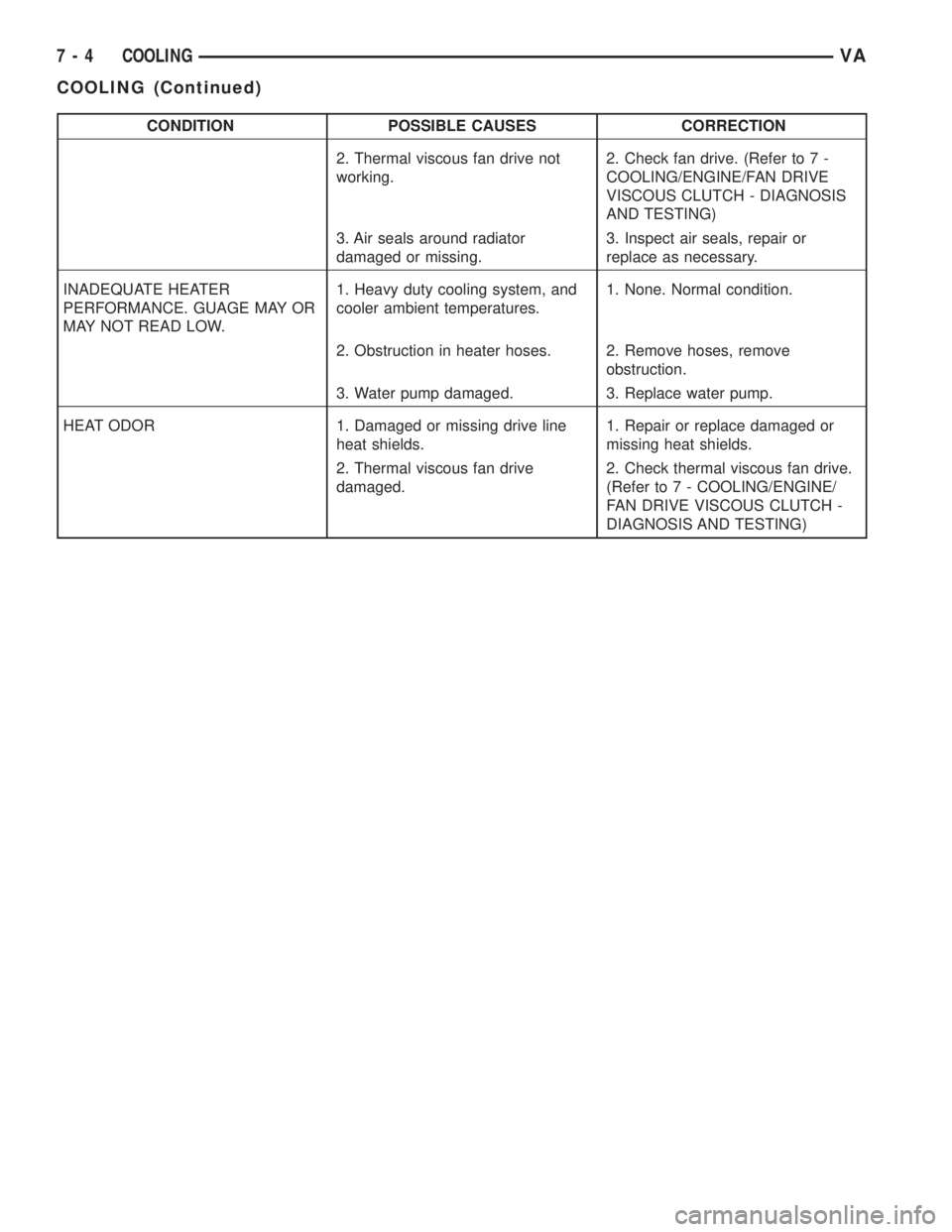
CONDITION POSSIBLE CAUSES CORRECTION
2. Thermal viscous fan drive not
working.2. Check fan drive. (Refer to 7 -
COOLING/ENGINE/FAN DRIVE
VISCOUS CLUTCH - DIAGNOSIS
AND TESTING)
3. Air seals around radiator
damaged or missing.3. Inspect air seals, repair or
replace as necessary.
INADEQUATE HEATER
PERFORMANCE. GUAGE MAY OR
MAY NOT READ LOW.1. Heavy duty cooling system, and
cooler ambient temperatures.1. None. Normal condition.
2. Obstruction in heater hoses. 2. Remove hoses, remove
obstruction.
3. Water pump damaged. 3. Replace water pump.
HEAT ODOR 1. Damaged or missing drive line
heat shields.1. Repair or replace damaged or
missing heat shields.
2. Thermal viscous fan drive
damaged.2. Check thermal viscous fan drive.
(Refer to 7 - COOLING/ENGINE/
FAN DRIVE VISCOUS CLUTCH -
DIAGNOSIS AND TESTING)
7 - 4 COOLINGVA
COOLING (Continued)