tow MITSUBISHI ECLIPSE 1990 Service Manual
[x] Cancel search | Manufacturer: MITSUBISHI, Model Year: 1990, Model line: ECLIPSE, Model: MITSUBISHI ECLIPSE 1990Pages: 391, PDF Size: 15.27 MB
Page 23 of 391
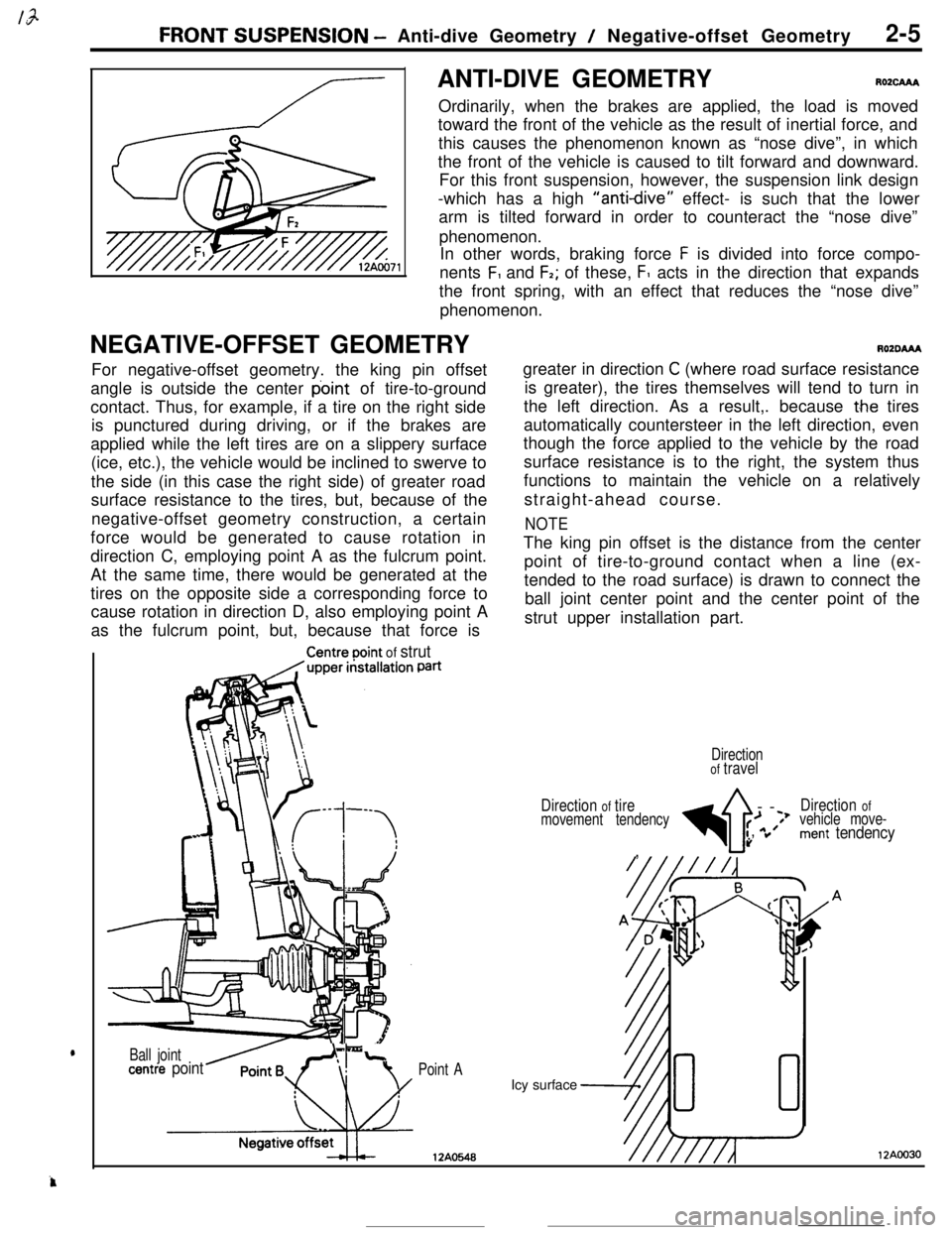
FRONT SUSPENSION - Anti-dive Geometry / Negative-offset Geometry2-5ANTI-DIVE GEOMETRY
RO2cAAAOrdinarily, when the brakes are applied, the load is moved
toward the front of the vehicle as the result of inertial force, and
this causes the phenomenon known as “nose dive”, in which
the front of the vehicle is caused to tilt forward and downward.
For this front suspension, however, the suspension link design
-which has a high
“anti-dive” effect- is such that the lower
arm is tilted forward in order to counteract the “nose dive”
phenomenon.
In other words, braking force
F is divided into force compo-
nents
F, and F2; of these, F1 acts in the direction that expands
the front spring, with an effect that reduces the “nose dive”
phenomenon.
NEGATIVE-OFFSET GEOMETRY
AOZDAAAFor negative-offset geometry. the king pin offset
angle is outside the center point of tire-to-ground
contact. Thus, for example, if a tire on the right side
is punctured during driving, or if the brakes are
applied while the left tires are on a slippery surface
(ice, etc.), the vehicle would be inclined to swerve to
the side (in this case the right side) of greater road
surface resistance to the tires, but, because of the
negative-offset geometry construction, a certain
force would be generated to cause rotation in
direction C, employing point A as the fulcrum point.
At the same time, there would be generated at the
tires on the opposite side a corresponding force to
cause rotation in direction D, also employing point A
as the fulcrum point, but, because that force is
Centreooint of strutPatigreater in direction
C (where road surface resistance
is greater), the tires themselves will tend to turn in
the left direction. As a result,. because
t.he tires
automatically countersteer in the left direction, even
though the force applied to the vehicle by the road
surface resistance is to the right, the system thus
functions to maintain the vehicle on a relatively
straight-ahead course.
NOTEThe king pin offset is the distance from the center
point of tire-to-ground contact when a line (ex-
tended to the road surface) is drawn to connect the
ball joint center point and the center point of the
strut upper installation part.
Point AIcy surface
12AO548
Ball jointLcentre point
t
Directionof travel
Direction
of tire
4--
Direction ofmovement tendency>f;’*Jvehicle move-:’
”ment tendency,
12AOO30
Page 24 of 391
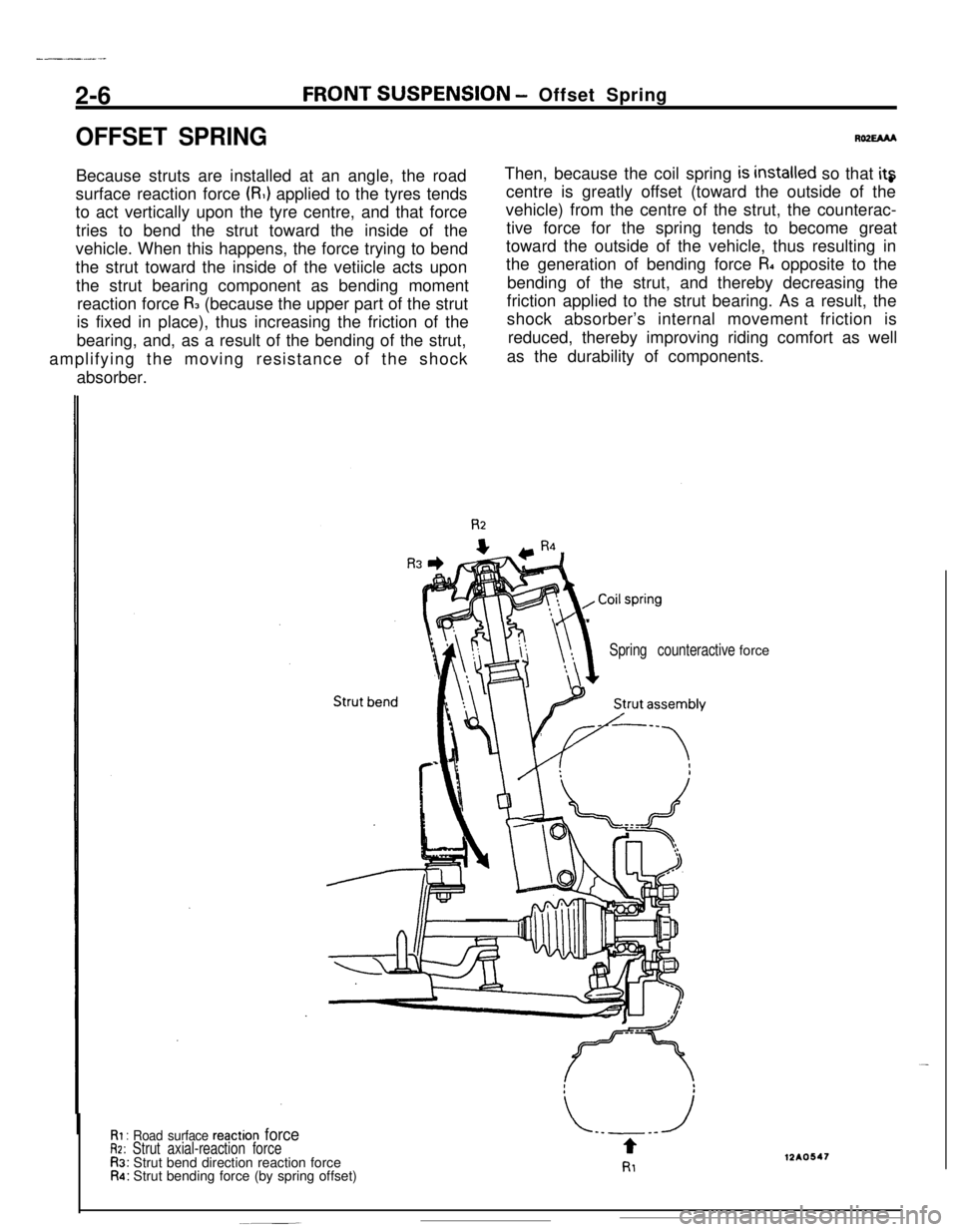
----2-6
FRONT SUSPENSION - Offset Spring
OFFSET SPRINGBecause struts are installed at an angle, the road
surface reaction force
(RI) applied to the tyres tends
to act vertically upon the tyre centre, and that force
tries to bend the strut toward the inside of the
vehicle. When this happens, the force trying to bend
the strut toward the inside of the vetiicle acts upon
the strut bearing component as bending moment
reaction force
FL (because the upper part of the strut
is fixed in place), thus increasing the friction of the
bearing, and, as a result of the bending of the strut,
amplifying the moving resistance of the shock
absorber.Ro2EMA
Then, because the coil spring
is installed so that itscentre is greatly offset (toward the outside of the
vehicle) from the centre of the strut, the counterac-
tive force for the spring tends to become great
toward the outside of the vehicle, thus resulting in
the generation of bending force
FL opposite to the
bending of the strut, and thereby decreasing the
friction applied to the strut bearing. As a result, the
shock absorber’s internal movement friction is
reduced, thereby improving riding comfort as well
as the durability of components.
Spring counteractiveforce
RI : Road surface reaction forceR2: Strut axial-reaction forceR3: Strut bend direction reaction forceR4: Strut bending force (by spring offset)
Page 43 of 391
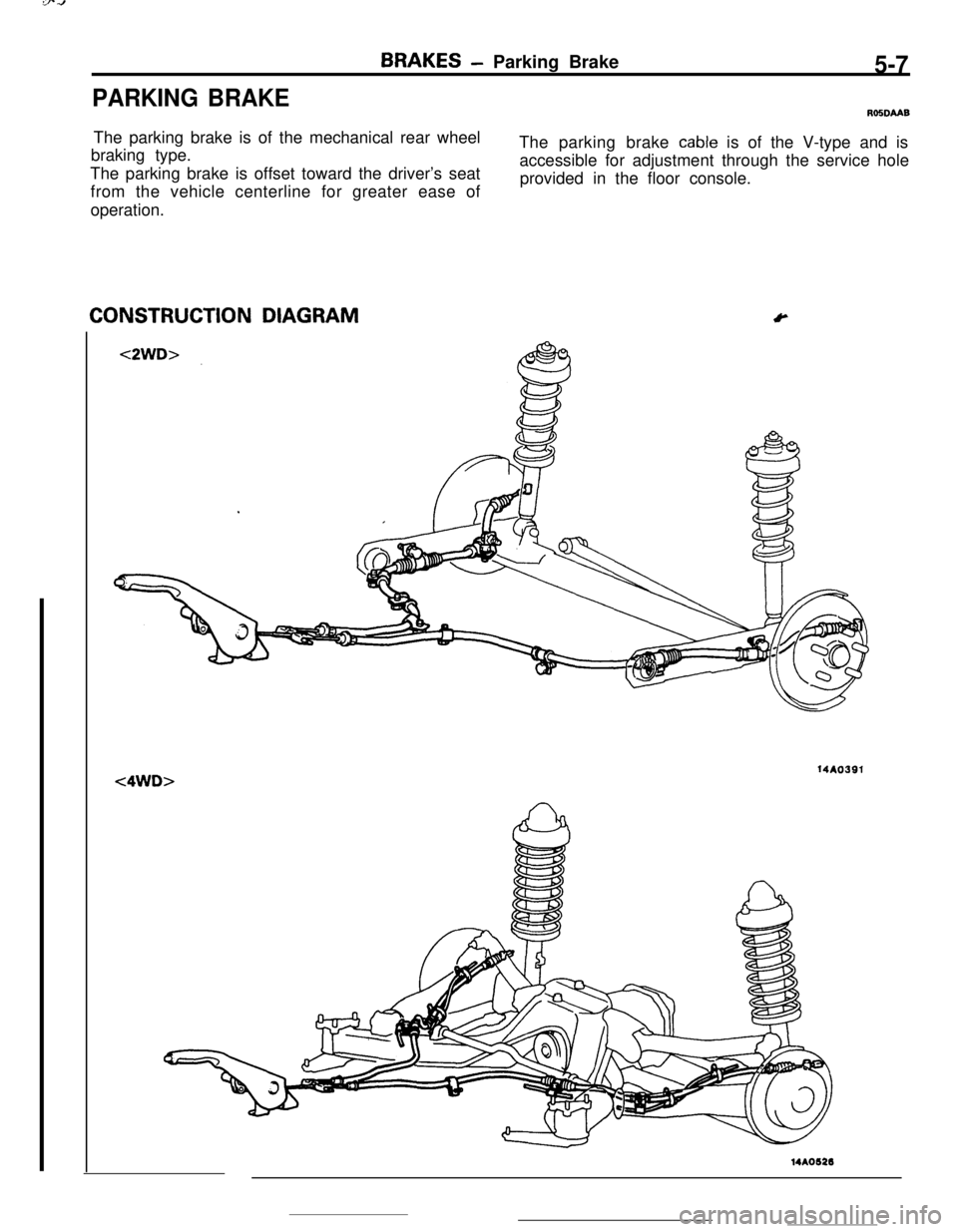
PARKING BRAKE
BRAKES- Parking Brake5-7
ROSDMBThe parking brake is of the mechanical rear wheel
braking type.The parking brake
cable is of the V-type and is
The parking brake is offset toward the driver’s seataccessible for adjustment through the service hole
provided in the floor console.
from the vehicle centerline for greater ease of
operation.CONSTRUCTION DIAGRAM
Y14AO391
<4WD>14A0626
Page 157 of 391
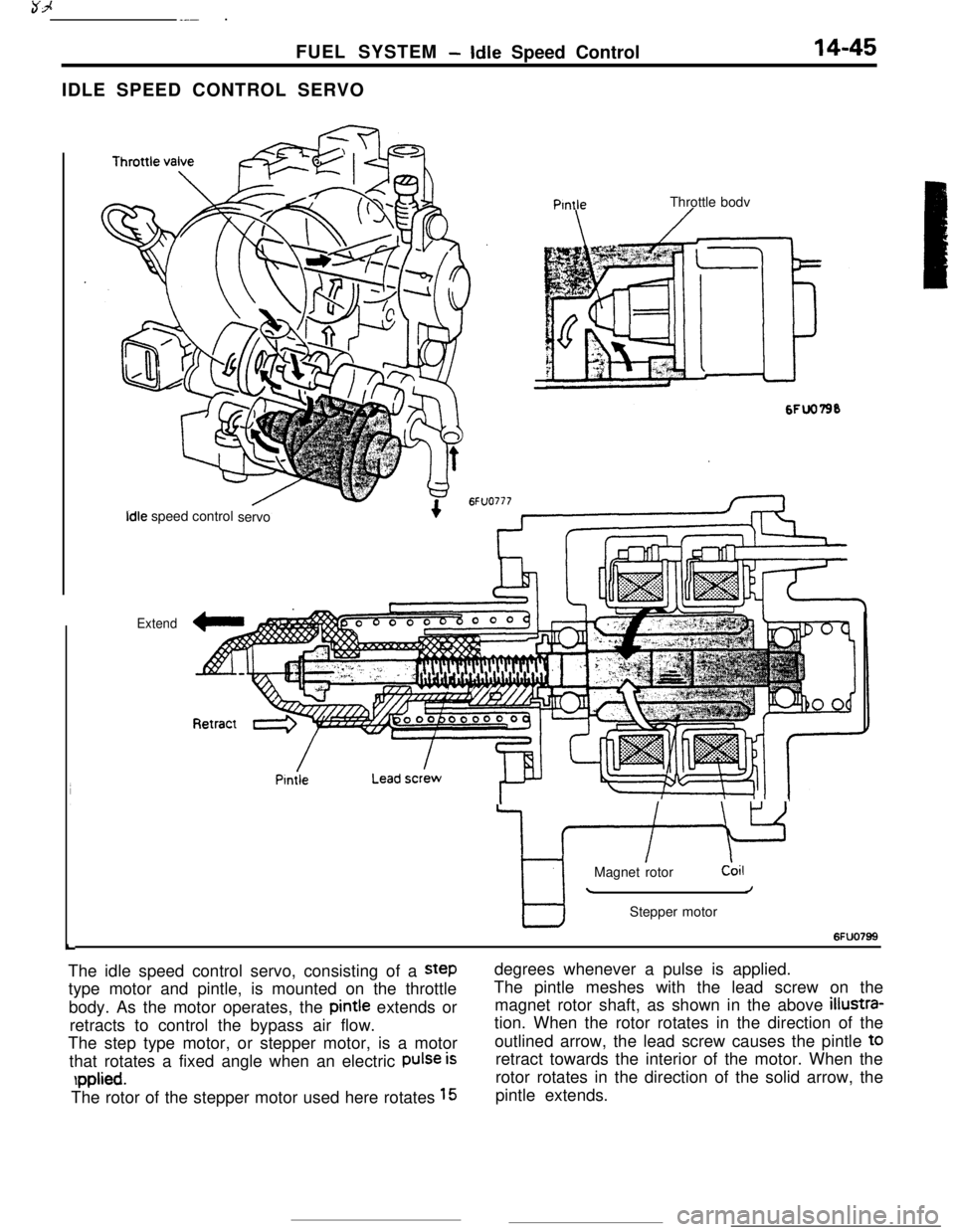
3-d__- .
FUEL SYSTEM
-Idle Speed Control14-45IDLE SPEED CONTROL SERVO
L
PtntleThrottle bodv
Idle speed control
servo
Extend
7 -IMagnet rotordoil
/Stepper motor
6FUO799The idle speed control servo, consisting of a
steptype motor and pintle, is mounted on the throttle
body. As the motor operates, the pintie extends or
retracts to control the bypass air flow.
The step type motor, or stepper motor, is a motor
that rotates a fixed angle when an electric
Pulse is
rpplied.The rotor of the stepper motor used here rotates
15degrees whenever a pulse is applied.
The pintle meshes with the lead screw on the
magnet rotor shaft, as shown in the above
illustra-tion. When the rotor rotates in the direction of the
outlined arrow, the lead screw causes the pintle t0
retract towards the interior of the motor. When the
rotor rotates in the direction of the solid arrow, the
pintle extends.
Page 181 of 391
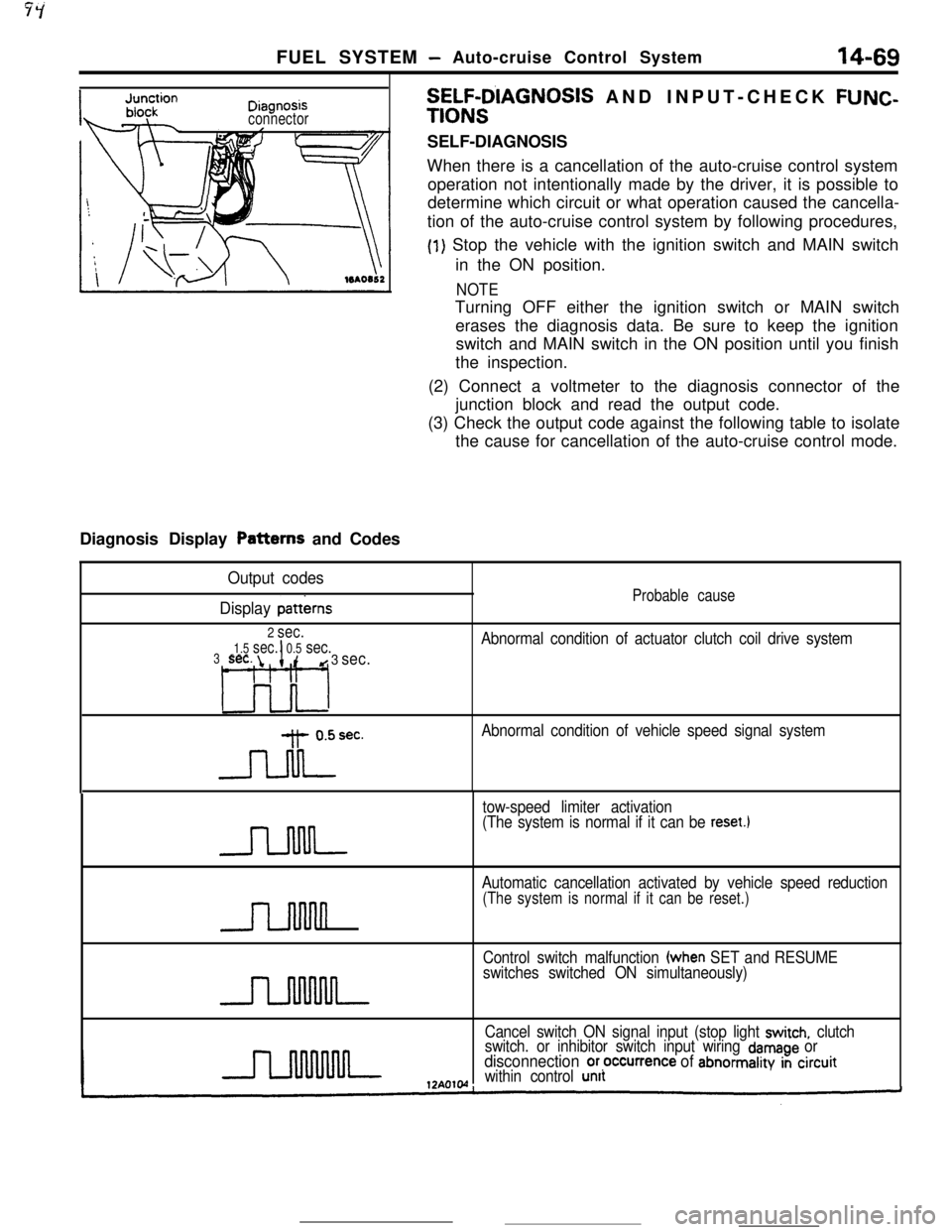
FUEL SYSTEM- Auto-cruise Control System14-69
ni2nnncisv,“y’I”“.-
connectorDiagnosis Display Patterns and Codes
SELF-D’IAGNOSIS AND INPUT-CHECK FUNC-
TIONSSELF-DIAGNOSIS
When there is a cancellation of the auto-cruise control system
operation not intentionally made by the driver, it is possible to
determine which circuit or what operation caused the cancella-
tion of the auto-cruise control system by following procedures,
(1) Stop the vehicle with the ignition switch and MAIN switch
in the ON position.
NOTETurning OFF either the ignition switch or MAIN switch
erases the diagnosis data. Be sure to keep the ignition
switch and MAIN switch in the ON position until you finish
the inspection.
(2) Connect a voltmeter to the diagnosis connector of the
junction block and read the output code.
(3) Check the output code against the following table to isolate
the cause for cancellation of the auto-cruise control mode.
Output codes
Display
patterns
2 sec.
1.5 sec.I0.5 sec.3sec. id 3 sec.
L3o-l
-Jdrec.
Probable cause
Abnormal condition of actuator clutch coil drive system
Abnormal condition of vehicle speed signal system
tow-speed limiter activation
(The system is normal if it can be
reset.1
n
Automatic cancellation activated by vehicle speed reduction
(The system is normal if it can be reset.)
Control switch malfunction (when SET and RESUME
switches switched ON simultaneously)
Cancel switch ON signal input (stop light
switch, clutch
switch. or inhibitor switch input wiring damage ordisconnection or,occurrence of abnormality in circuitwithin control unit
Page 197 of 391
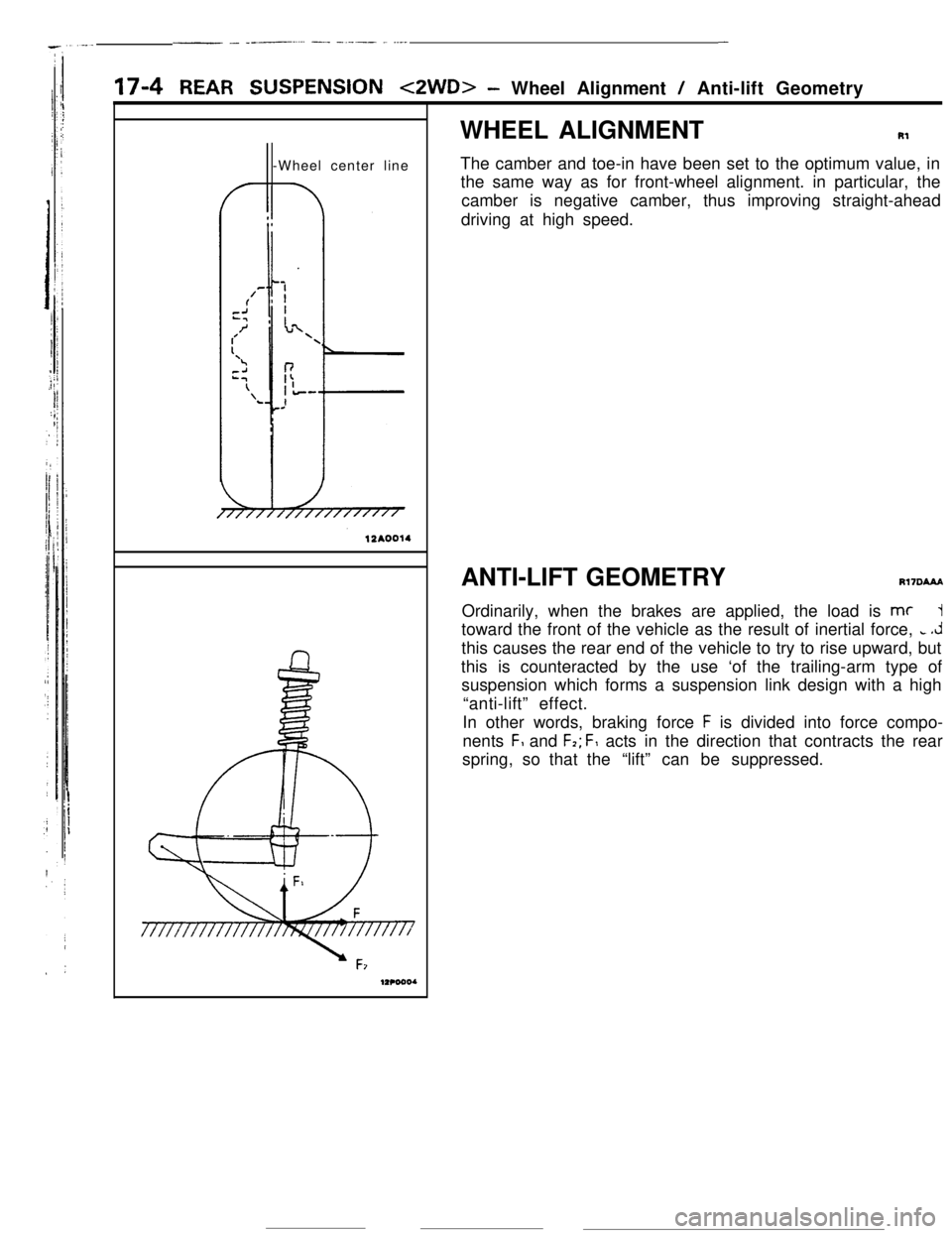
- ._ ____.-.-- -.._ -.-.- - ..__-
17-4 REAR SUSPENSION tZWD>- Wheel Alignment / Anti-lift Geometry
-Wheel center lineWHEEL ALIGNMENTRl
The camber and toe-in have been set to the optimum value, in
the same way as for front-wheel alignment. in particular, the
camber is negative camber, thus improving straight-ahead
driving at high speed.
ANTI-LIFT GEOMETRY
Rl7DAAAOrdinarily, when the brakes are applied, the load is
mc1toward the front of the vehicle as the result of inertial force,
c .Jthis causes the rear end of the vehicle to try to rise upward, but
this is counteracted by the use ‘of the trailing-arm type of
suspension which forms a suspension link design with a high
“anti-lift” effect.
In other words, braking force
F is divided into force compo-
nents
F, and F,; F, acts in the direction that contracts the rear
spring, so that the“lift” can be suppressed.
Page 205 of 391
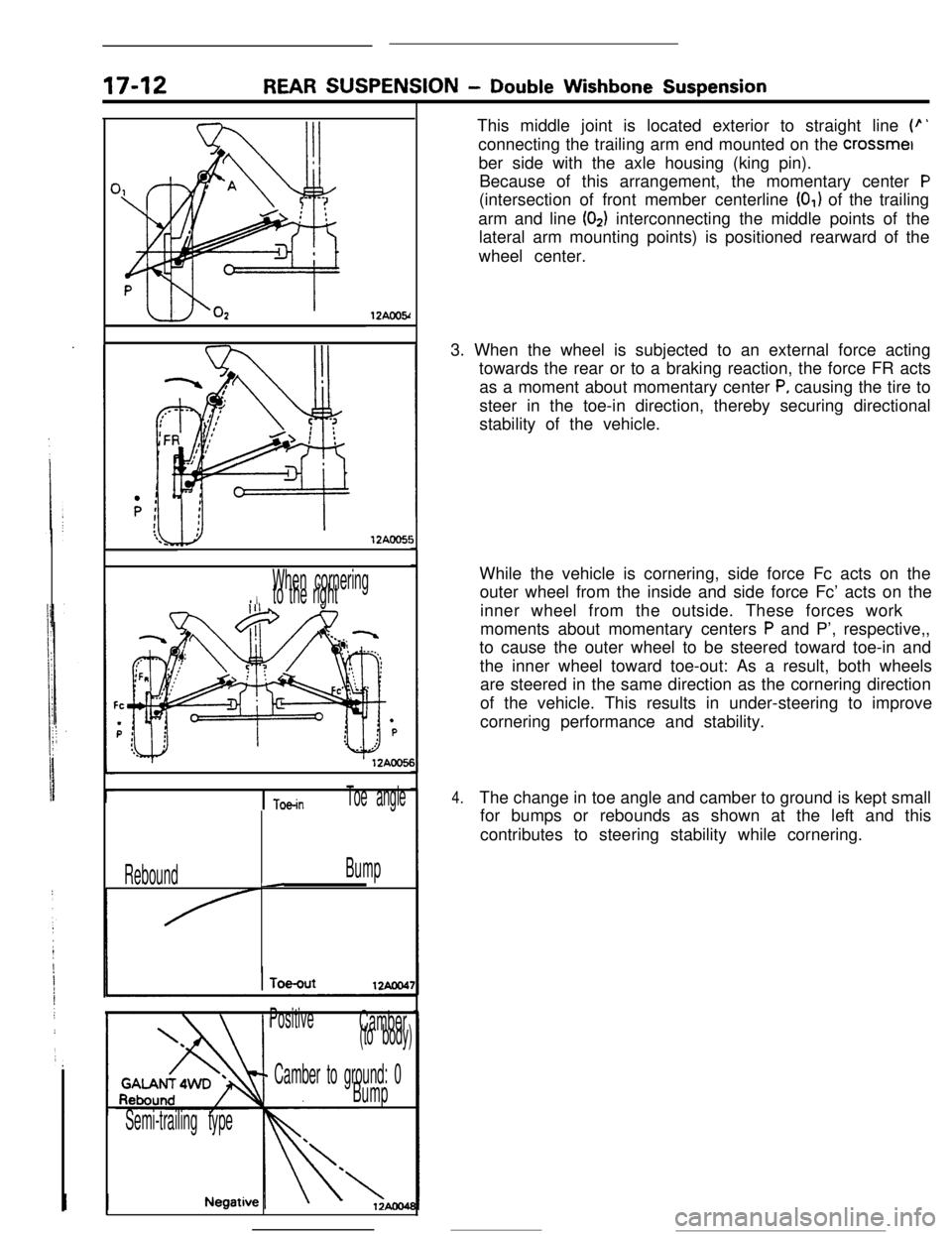
17-12REAR SUSPENSION - Double Wishbone Suspension
12AWY
lZAOOS!
When cornering. I.to the right
I Toe-inToe angle
ReboundBump-
PositiveCamber(to body)
- Camber to ground: 0
Bump
Semi-trailing typeThis middle joint is located exterior to straight line
(p’connecting the trailing arm end mounted on the crossmet
ber side with the axle housing (king pin).
Because of this arrangement, the momentary center
P(intersection of front member centerline
(0,) of the trailing
arm and line
(02) interconnecting the middle points of the
lateral arm mounting points) is positioned rearward of the
wheel center.
3. When the wheel is subjected to an external force acting
towards the rear or to a braking reaction, the force FR acts
as a moment about momentary center
P, causing the tire to
steer in the toe-in direction, thereby securing directional
stability of the vehicle.
While the vehicle is cornering, side force Fc acts on the
outer wheel from the inside and side force Fc’ acts on the
inner wheel from the outside. These forces work
moments about momentary centers
P and P’, respective,,
to cause the outer wheel to be steered toward toe-in and
the inner wheel toward toe-out: As a result, both wheels
are steered in the same direction as the cornering direction
of the vehicle. This results in under-steering to improve
cornering performance and stability.
4.The change in toe angle and camber to ground is kept small
for bumps or rebounds as shown at the left and this
contributes to steering stability while cornering.
Page 206 of 391
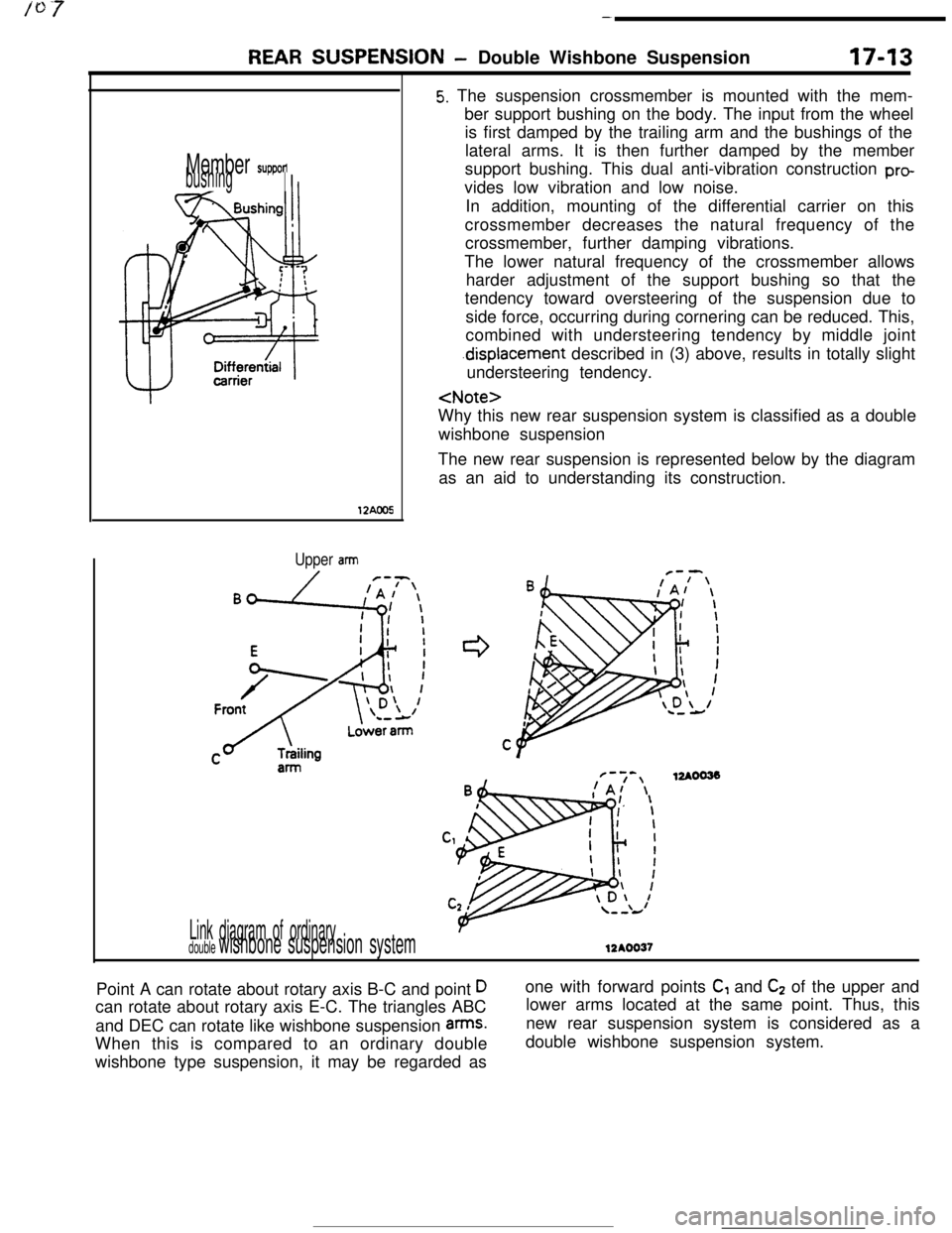
-
REAR SUSPENSION -Double Wishbone Suspension17-13
Member supponbushingI
12AOO5
Upper arm
Link diagram of ordinarydouble wishbone suspension system
5. The suspension crossmember is mounted with the mem-
ber support bushing on the body. The input from the wheel
is first damped by the trailing arm and the bushings of the
lateral arms. It is then further damped by the member
support bushing. This dual anti-vibration construction
provides low vibration and low noise.
In addition, mounting of the differential carrier on this
crossmember decreases the natural frequency of the
crossmember, further damping vibrations.
The lower natural frequency of the crossmember allows
harder adjustment of the support bushing so that the
tendency toward oversteering of the suspension due to
side force, occurring during cornering can be reduced. This,
combined with understeering tendency by middle joint
.displacement described in (3) above, results in totally slight
understeering tendency.
wishbone suspension
The new rear suspension is represented below by the diagram
as an aid to understanding its construction.
F-7-,12AOO33!A/ \
12AOO37Point A can rotate about rotary axis B-C and point
Dcan rotate about rotary axis E-C. The triangles ABC
and DEC can rotate like wishbone suspension
arms.When this is compared to an ordinary double
wishbone type suspension, it may be regarded asone with forward points
C, and C2 of the upper and
lower arms located at the same point. Thus, this
new rear suspension system is considered as a
double wishbone suspension system.
Page 213 of 391
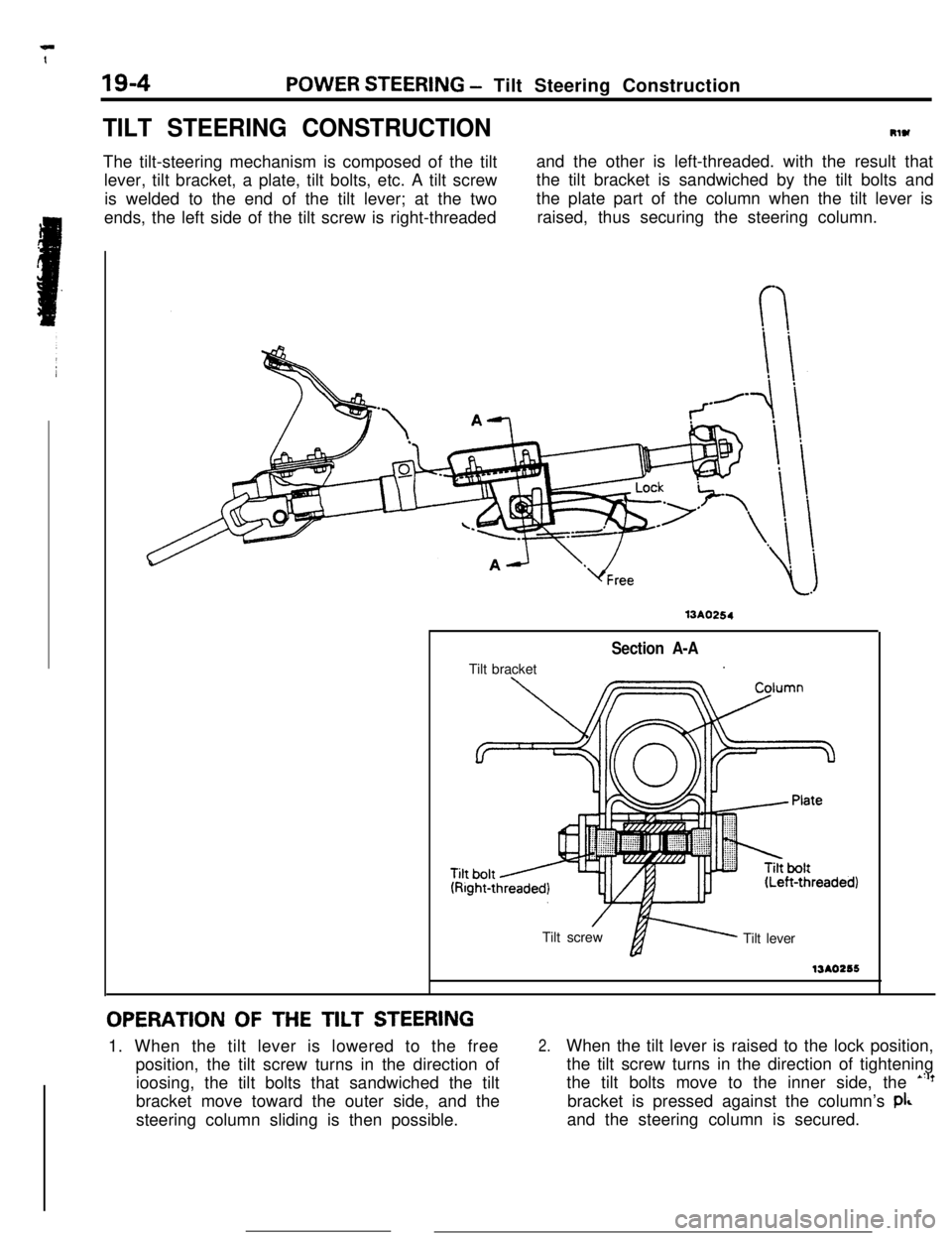
19-4POWER STEERING - Tilt Steering Construction
TILT STEERING CONSTRUCTIONRlW
The tilt-steering mechanism is composed of the tilt
lever, tilt bracket, a plate, tilt bolts, etc. A tilt screw
is welded to the end of the tilt lever; at the two
ends, the left side of the tilt screw is right-threadedand the other is left-threaded. with the result that
the tilt bracket is sandwiched by the tilt bolts and
the plate part of the column when the tilt lever is
raised, thus securing the steering column.
13A0254Tilt bracket
Section A-A.
’Tilt screwfi Tilt lever13AO256
OPERATION OF THE TILT STEERING1. When the tilt lever is lowered to the free
position, the tilt screw turns in the direction of
ioosing, the tilt bolts that sandwiched the tilt
bracket move toward the outer side, and the
steering column sliding is then possible.
2.When the tilt lever is raised to the lock position,
the tilt screw turns in the direction of tightening
the tilt bolts move to the inner side, the
*“?bracket is pressed against the column’s
pi&and the steering column is secured.
Page 223 of 391
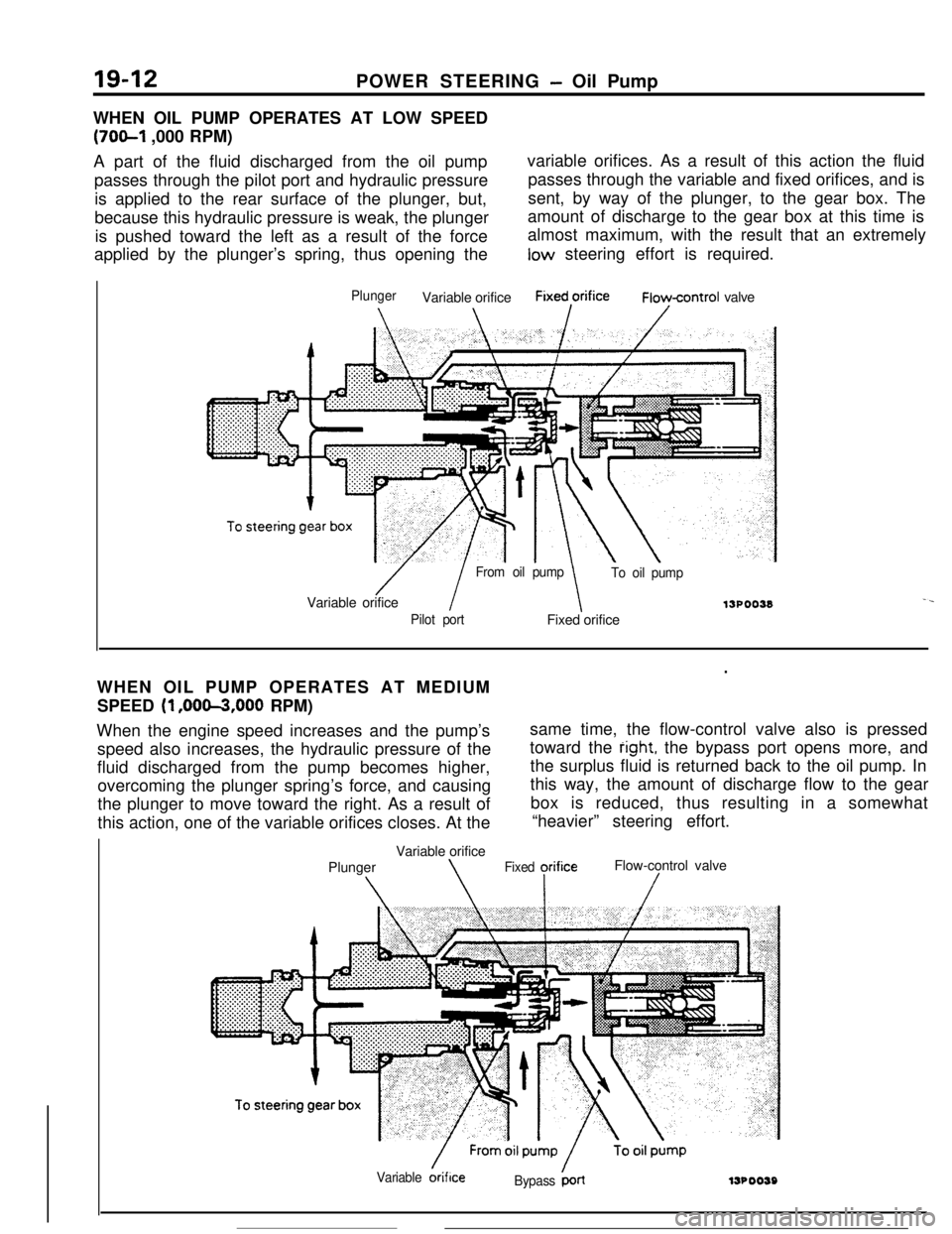
19-12POWER STEERING - Oil Pump
WHEN OIL PUMP OPERATES AT LOW SPEED
(70&l ,000 RPM)
A part of the fluid discharged from the oil pumpvariable orifices. As a result of this action the fluid
passes through the pilot port and hydraulic pressurepasses through the variable and fixed orifices, and is
is applied to the rear surface of the plunger, but,sent, by way of the plunger, to the gear box. The
because this hydraulic pressure is weak, the plungeramount of discharge to the gear box at this time is
is pushed toward the left as a result of the forcealmost maximum, with the result that an extremely
applied by the plunger’s spring, thus opening thelow steering effort is required.
PlungerVariable orificeFixed,orificeFioycontrol valve
/ I
From oil pump
To oil pumpVariable orifice
13POO38-.
Pilot portFixed orifice
.WHEN OIL PUMP OPERATES AT MEDIUM
SPEED
(1 ,OOm,OOO RPM)
When the engine speed increases and the pump’ssame time, the flow-control valve also is pressed
speed also increases, the hydraulic pressure of thetoward the
right, the bypass port opens more, and
fluid discharged from the pump becomes higher,the surplus fluid is returned back to the oil pump. In
overcoming the plunger spring’s force, and causingthis way, the amount of discharge flow to the gear
the plunger to move toward the right. As a result ofbox is reduced, thus resulting in a somewhat
this action, one of the variable orifices closes. At the“heavier” steering effort.
Variable orifice
PlungerFlow-control valve
\\Fixed yrifice/
Variable &iflceBypass ‘LrllJPOO59