tow MITSUBISHI ECLIPSE 1990 User Guide
[x] Cancel search | Manufacturer: MITSUBISHI, Model Year: 1990, Model line: ECLIPSE, Model: MITSUBISHI ECLIPSE 1990Pages: 391, PDF Size: 15.27 MB
Page 224 of 391
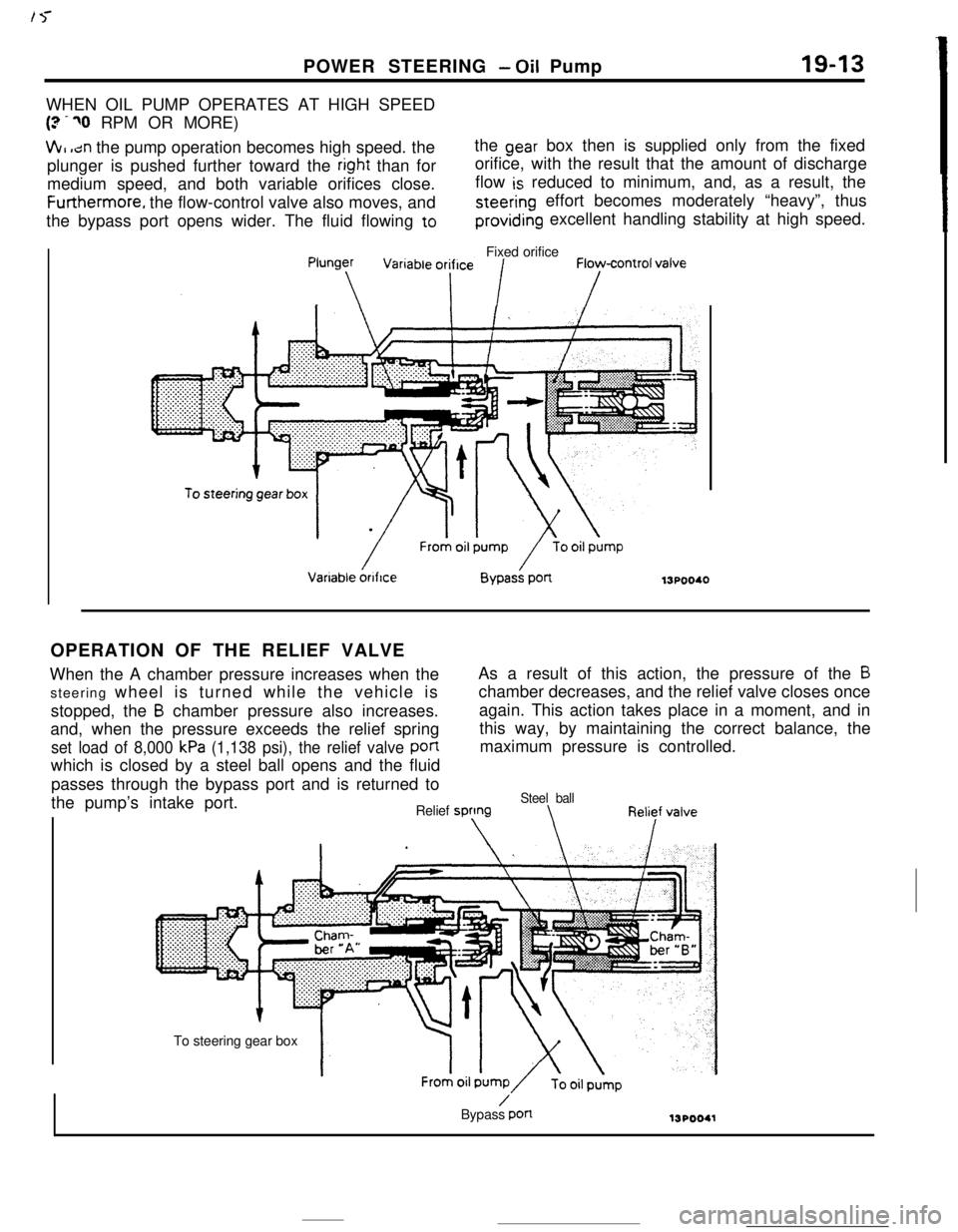
i t-7POWER STEERING
- Oil Pump19-13WHEN OIL PUMP OPERATES AT HIGH SPEED
(? -70 RPM OR MORE)
VII, ,dn the pump operation becomes high speed. thethe gear box then is supplied only from the fixed
plunger is pushed further toward the
right than fororifice, with the result that the amount of discharge
medium speed, and both variable orifices close.flow
is reduced to minimum, and, as a result, theFurthermore. the flow-control valve also moves, and
steering effort becomes moderately “heavy”, thus
the bypass port opens wider. The fluid flowing to
providing excellent handling stability at high speed.
Fixed orifice13POO40
OPERATION OF THE RELIEF VALVE
When the A chamber pressure increases when theAs a result of this action, the pressure of the
Bsteering wheel is turned while the vehicle ischamber decreases, and the relief valve closes once
stopped, the
B chamber pressure also increases.again. This action takes place in a moment, and in
and, when the pressure exceeds the relief springthis way, by maintaining the correct balance, the
set load of 8,000 kPa (1,138 psi), the relief valve panmaximum pressure is controlled.
which is closed by a steel ball opens and the fluid
passes through the bypass port and is returned to
the pump’s intake port.
Steel ballRelief sprtngTo steering gear box
/Bypass pan
WPOO41
Page 234 of 391
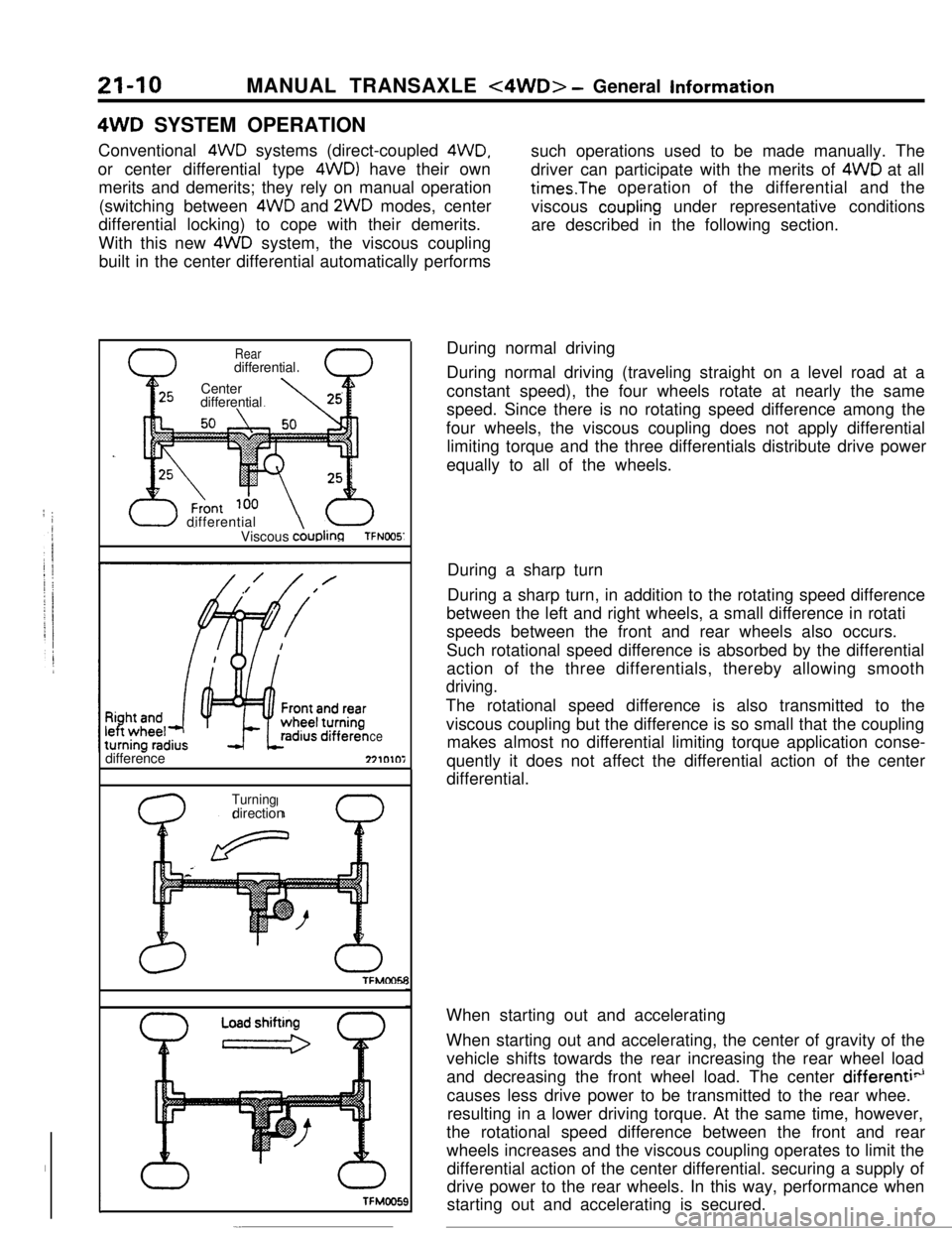
21-10MANUAL TRANSAXLE <4WD> - General Information4WD SYSTEM OPERATION
Conventional 4WD systems (direct-coupled
4WD,or center differential type 4WDl have their own
merits and demerits; they rely on manual operation
(switching between 4WD and 2WD modes, center
differential locking) to cope with their demerits.
With this new 4WD system, the viscous coupling
built in the center differential automatically performssuch operations used to be made manually. The
driver can participate with the merits of 4WD at alltimes.The operation of the differential and the
viscous
coupling under representative conditions
are described in the following section.
I
Reardifferential
Center
differential
U differential
Viscous AuDk?TFNOO5’difference
ce271010i
TFMMYTFMMY
0
Turningdirection
ITFMOO!X
-.During normal driving
During normal driving (traveling straight on a level road at a
constant speed), the four wheels rotate at nearly the same
speed. Since there is no rotating speed difference among the
four wheels, the viscous coupling does not apply differential
limiting torque and the three differentials distribute drive power
equally to all of the wheels.
During a sharp turn
During a sharp turn, in addition to the rotating speed difference
between the left and right wheels, a small difference in rotati
speeds between the front and rear wheels also occurs.
Such rotational speed difference is absorbed by the differential
action of the three differentials, thereby allowing smooth
driving.The rotational speed difference is also transmitted to the
viscous coupling but the difference is so small that the coupling
makes almost no differential limiting torque application conse-
quently it does not affect the differential action of the center
differential.
When starting out and accelerating
When starting out and accelerating, the center of gravity of the
vehicle shifts towards the rear increasing the rear wheel load
and decreasing the front wheel load. The center
differenti”causes less drive power to be transmitted to the rear whee.
resulting in a lower driving torque. At the same time, however,
the rotational speed difference between the front and rear
wheels increases and the viscous coupling operates to limit the
differential action of the center differential. securing a supply of
drive power to the rear wheels. In this way, performance when
starting out and accelerating is secured.
Page 252 of 391
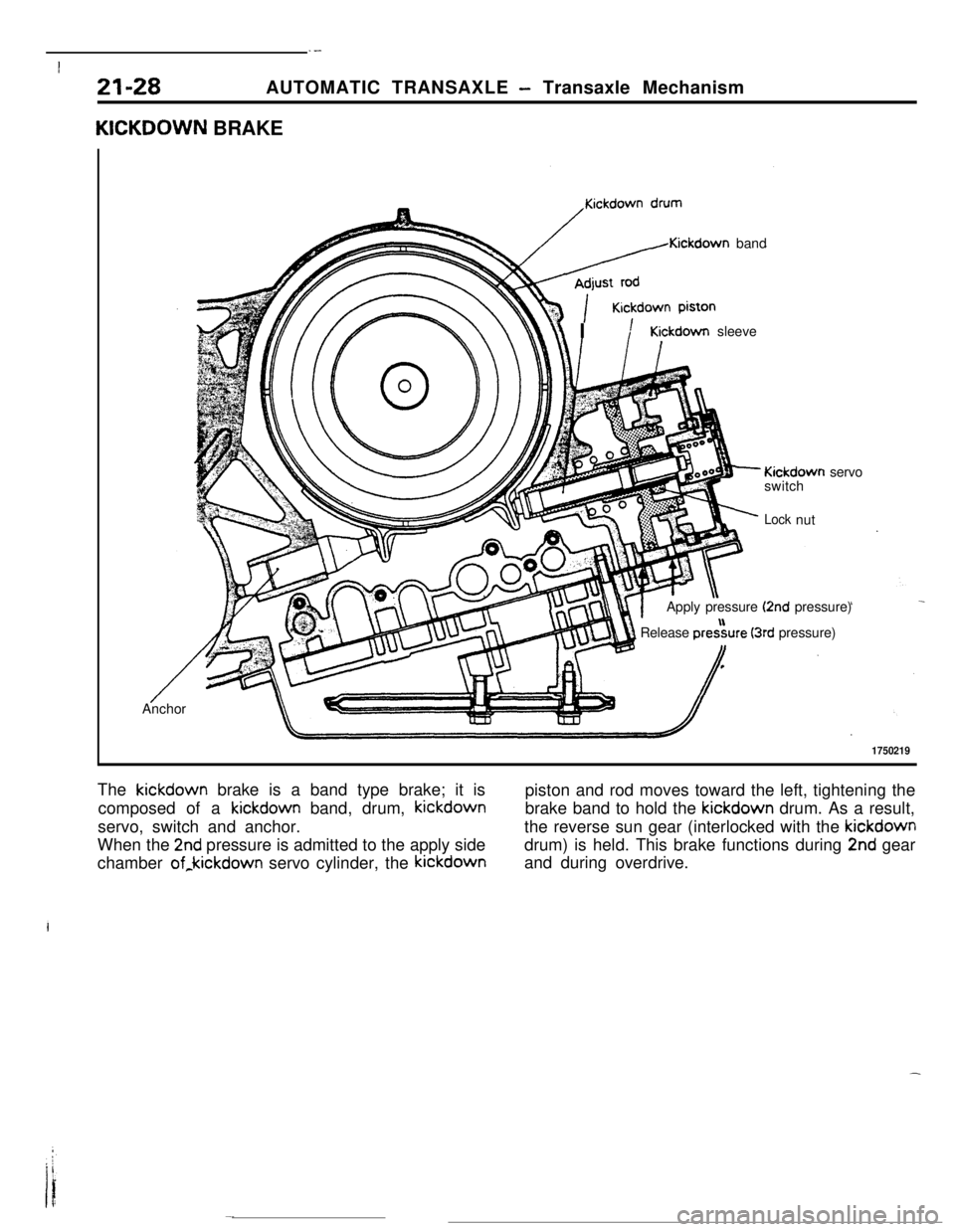
.-
I
21-28AUTOMATIC TRANSAXLE - Transaxle Mechanism
KICKDOWN BRAKE
/Kickdown band
r\\ IKickdown sleeve
- Kickdown servo
switch
;‘- Locknut
Apply pressure
(2nd pressure)
1 Release pre&re (3rd pressure)I,
/ --Anchor
1750219The kickdown brake is a band type brake; it is
piston and rod moves toward the left, tightening the
composed of a kickdown band, drum, kickdownbrake band to hold the kickdown drum. As a result,
servo, switch and anchor.the reverse sun gear (interlocked with the kickdown
When the
2nd pressure is admitted to the apply sidedrum) is held. This brake functions during 2nd gear
chamber of,kickdown servo cylinder, the kickdownand during overdrive.
Page 280 of 391
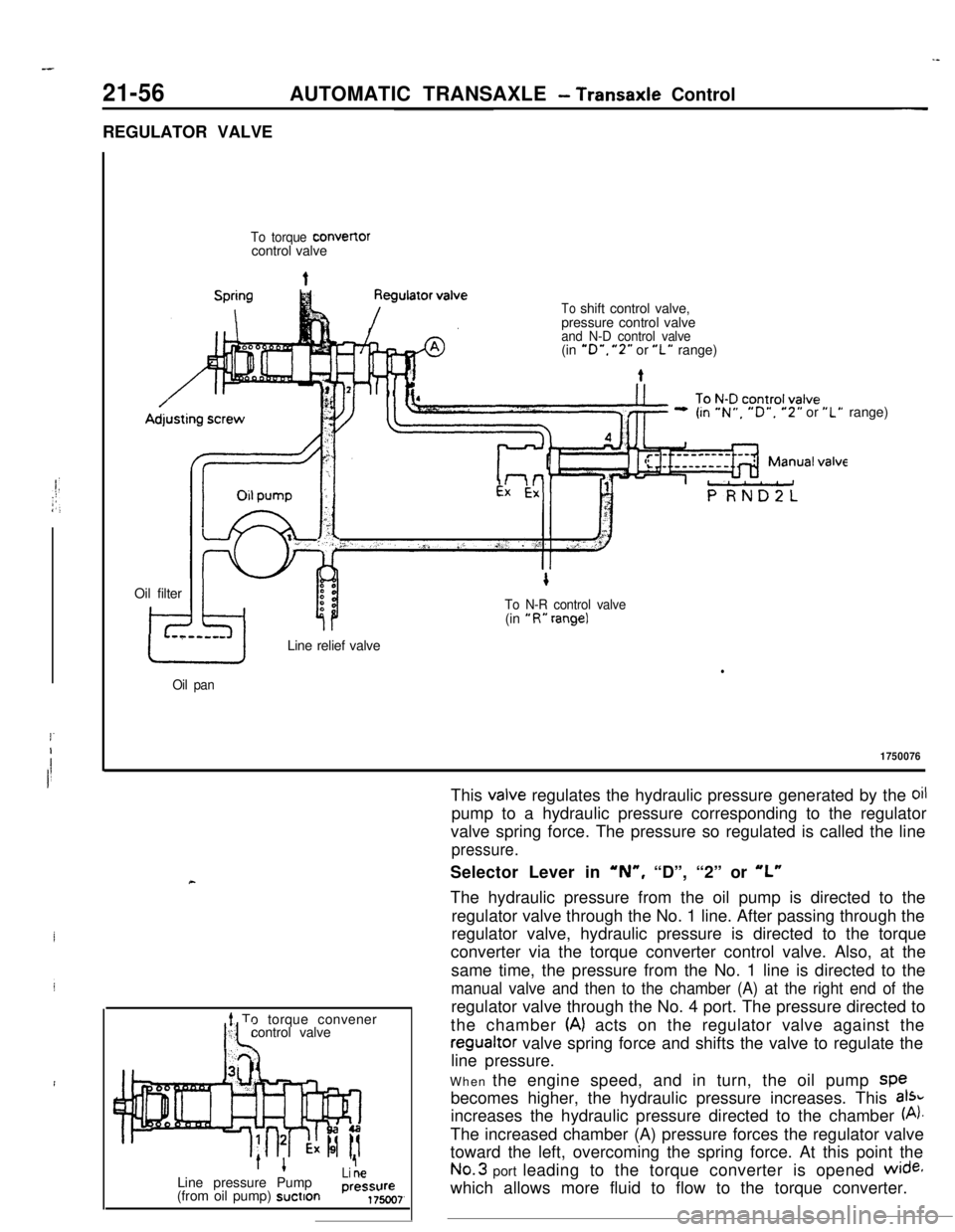
-
!-I
I!I
21-56AUTOMATIC TRANSAXLE - Transaxle Control~-REGULATOR VALVE
To torque convener
control valve
t
Toshift control valve,
pressure control valve
and N-D control valve(in “D”. ”2” or “L” range)
“D”.“2” or “L” range)
Oil filter
I1
To N-R control valve(in “R” range)Line relief valve
Oil pan
l
1750076
! To torque convener
IL‘I:control valve
Line pressure Pump
Li Ae(from oil pump) suctionprest$$)7,This
valve regulates the hydraulic pressure generated by the oilpump to a hydraulic pressure corresponding to the regulator
valve spring force. The pressure so regulated is called the line
pressure.Selector Lever in
‘N”, “D”, “2” or “L”The hydraulic pressure from the oil pump is directed to the
regulator valve through the No. 1 line. After passing through the
regulator valve, hydraulic pressure is directed to the torque
converter via the torque converter control valve. Also, at the
same time, the pressure from the No. 1 line is directed to the
manual valve and then to the chamber (A) at the right end of theregulator valve through the No. 4 port. The pressure directed to
the chamber
(A) acts on the regulator valve against theregualtor valve spring force and shifts the valve to regulate the
line pressure.
When the engine speed, and in turn, the oil pump spe
becomes higher, the hydraulic pressure increases. This
aI%increases the hydraulic pressure directed to the chamber
(A).The increased chamber (A) pressure forces the regulator valve
toward the left, overcoming the spring force. At this point theNo.3 port leading to the torque converter is opened
wide+which allows more fluid to flow to the torque converter.
Page 281 of 391
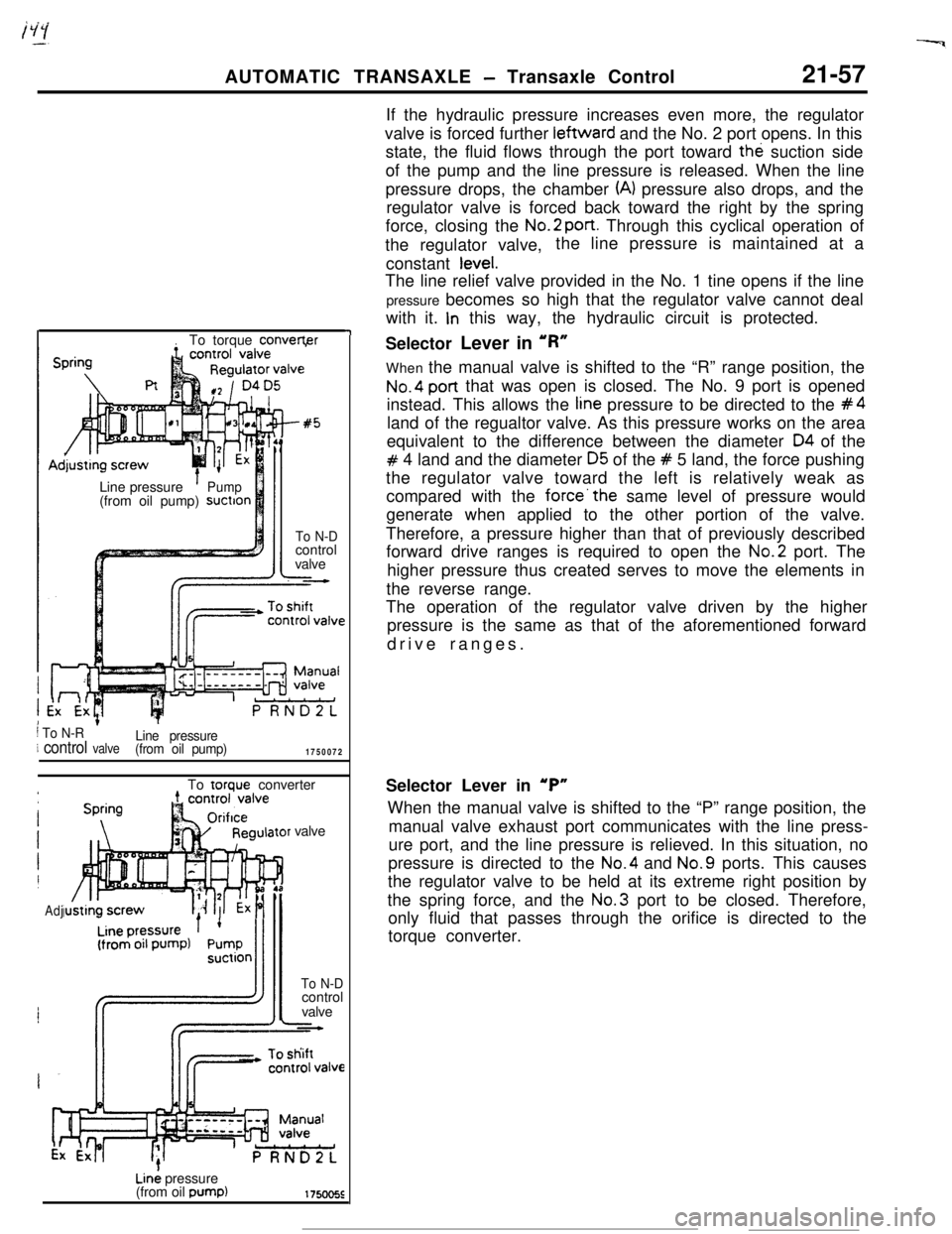
AUTOMATIC TRANSAXLE - Transaxle Control21-57
-7.To torque convert,erLine pressure
’Pump(from oil pump) suction
1 To N-RI control valveLine pressure
(from oil pump)1750072
-#5
To N-Dcontrol
valve
To toraueconverter
AdjLine pressure
1+(from oil pump)Pumpsuction
1 ~7valve
To N-Dcontrol
valve
s
Line pressure
(from oil pump)If the hydraulic pressure increases even more, the regulator
valve is forced further leftward and the No. 2 port opens. In this
state, the fluid flows through the port toward the suction side
of the pump and the line pressure is released. When the line
pressure drops, the chamber
(A) pressure also drops, and the
regulator valve is forced back toward the right by the spring
force, closing the No.2
port. Through this cyclical operation of
the regulator valve,the line pressure is maintained at a
constant
tevel.The line relief valve provided in the No. 1 tine opens if the line
pressure becomes so high that the regulator valve cannot deal
with it.
In this way, the hydraulic circuit is protected.
Selector Lever in ‘R”
When the manual valve is shifted to the “R” range position, the
No.4 post that was open is closed. The No. 9 port is opened
instead. This allows the
tine pressure to be directed to the #4land of the regualtor valve. As this pressure works on the area
equivalent to the difference between the diameter
04 of the
# 4 land and the diameter 05 of the # 5 land, the force pushing
the regulator valve toward the left is relatively weak as
compared with the
force’the same level of pressure would
generate when applied to the other portion of the valve.
Therefore, a pressure higher than that of previously described
forward drive ranges is required to open the No.2 port. The
higher pressure thus created serves to move the elements in
the reverse range.
The operation of the regulator valve driven by the higher
pressure is the same as that of the aforementioned forward
drive ranges.
Selector Lever in
‘P”When the manual valve is shifted to the “P” range position, the
manual valve exhaust port communicates with the line press-
ure port, and the line pressure is relieved. In this situation, no
pressure is directed to the No.4 and No.9 ports. This causes
the regulator valve to be held at its extreme right position by
the spring force, and the No.3 port to be closed. Therefore,
only fluid that passes through the orifice is directed to the
torque converter.
Page 282 of 391
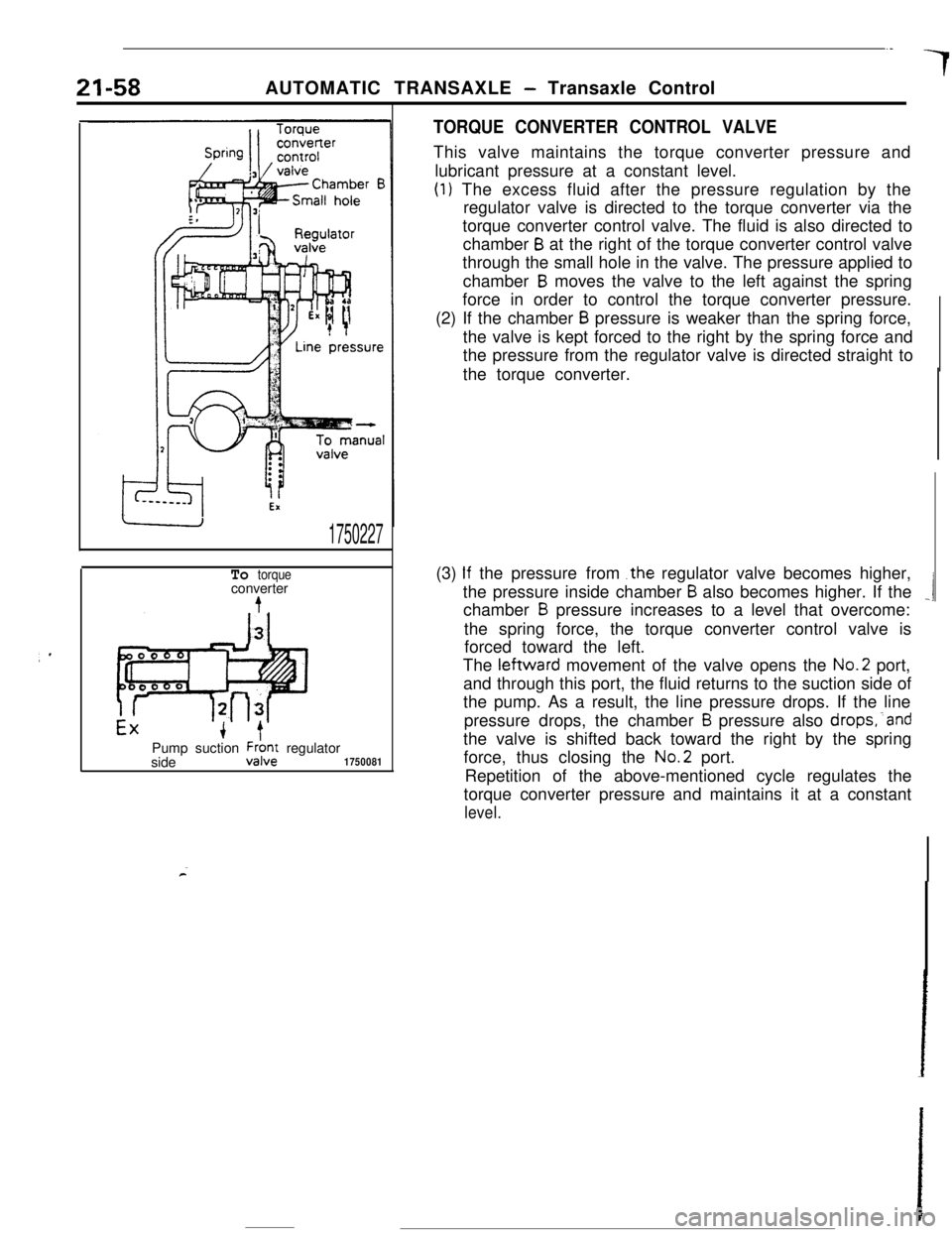
21-58AUTOMATIC TRANSAXLE - Transaxle Control
1750227
To torqueconverter
Pump suction
h& regulator
side1750081
TORQUE CONVERTER CONTROL VALVEThis valve maintains the torque converter pressure and
lubricant pressure at a constant level.
(1) The excess fluid after the pressure regulation by the
regulator valve is directed to the torque converter via the
torque converter control valve. The fluid is also directed to
chamber
B at the right of the torque converter control valve
through the small hole in the valve. The pressure applied to
chamber
B moves the valve to the left against the spring
force in order to control the torque converter pressure.
(2) If the chamber
B pressure is weaker than the spring force,
the valve is kept forced to the right by the spring force and
the pressure from the regulator valve is directed straight to
the torque converter.
(3)
If the pressurefrom .the regulator valve becomes higher,
the pressure inside chamber
B also becomes higher. If the_1chamber B pressure increases to a level that overcome:
the spring force, the torque converter control valve is
forced toward the left.
The leftward movement of the valve opens the No.2 port,
and through this port, the fluid returns to the suction side of
the pump. As a result, the line pressure drops. If the line
pressure drops, the chamber
B pressure also drops,‘and
the valve is shifted back toward the right by the spring
force, thus closing the No.2 port.
Repetition of the above-mentioned cycle regulates the
torque converter pressure and maintains it at a constant
level.
Page 283 of 391
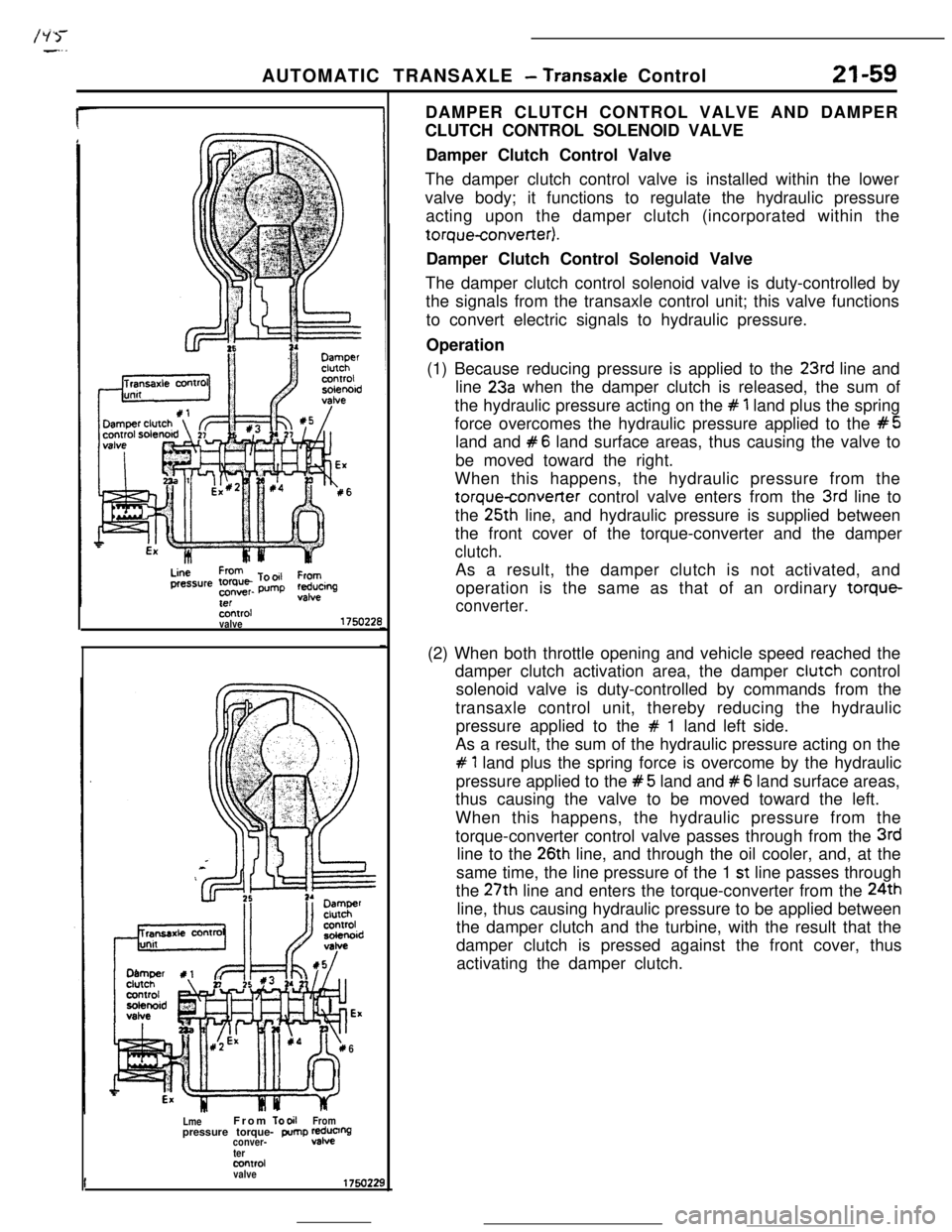
/ii>--..AUTOMATIC TRANSAXLE
- Transaxle Control21-59
Sxxrolvalve175022E
6
LmeFrom
TooilFrompressure torque- pump 2;0%conver-
termntrd
valveDAMPER CLUTCH CONTROL VALVE AND DAMPER
CLUTCH CONTROL SOLENOID VALVE
Damper Clutch Control Valve
The damper clutch control valve is installed within the lower
valve body; it functions to regulate the hydraulic pressure
acting upon the damper clutch (incorporated within thetorqueconverter).
Damper Clutch Control Solenoid Valve
The damper clutch control solenoid valve is duty-controlled by
the signals from the transaxle control unit; this valve functions
to convert electric signals to hydraulic pressure.
Operation
(1) Because reducing pressure is applied to the
23rd line and
line
23a when the damper clutch is released, the sum of
the hydraulic pressure acting on the
# 1 land plus the spring
force overcomes the hydraulic pressure applied to the
#5land and
#6 land surface areas, thus causing the valve to
be moved toward the right.
When this happens, the hydraulic pressure from the
torqueconverter control valve enters from the 3rd line to
the 25th line, and hydraulic pressure is supplied between
the front cover of the torque-converter and the damper
clutch.As a result, the damper clutch is not activated, and
operation is the same as that of an ordinary torque-
converter.(2) When both throttle opening and vehicle speed reached the
damper clutch activation area, the damper clutch control
solenoid valve is duty-controlled by commands from the
transaxle control unit, thereby reducing the hydraulic
pressure applied to the
# 1 land left side.
As a result, the sum of the hydraulic pressure acting on the
# 1 land plus the spring force is overcome by the hydraulic
pressure applied to the
#5 land and #6 land surface areas,
thus causing the valve to be moved toward the left.
When this happens, the hydraulic pressure from the
torque-converter control valve passes through from the
3rdline to the
26th line, and through the oil cooler, and, at the
same time, the line pressure of the 1
st line passes through
the 27th line and enters the torque-converter from the 24th
line, thus causing hydraulic pressure to be applied between
the damper clutch and the turbine, with the result that the
damper clutch is pressed against the front cover, thus
activating the damper clutch.
Page 284 of 391
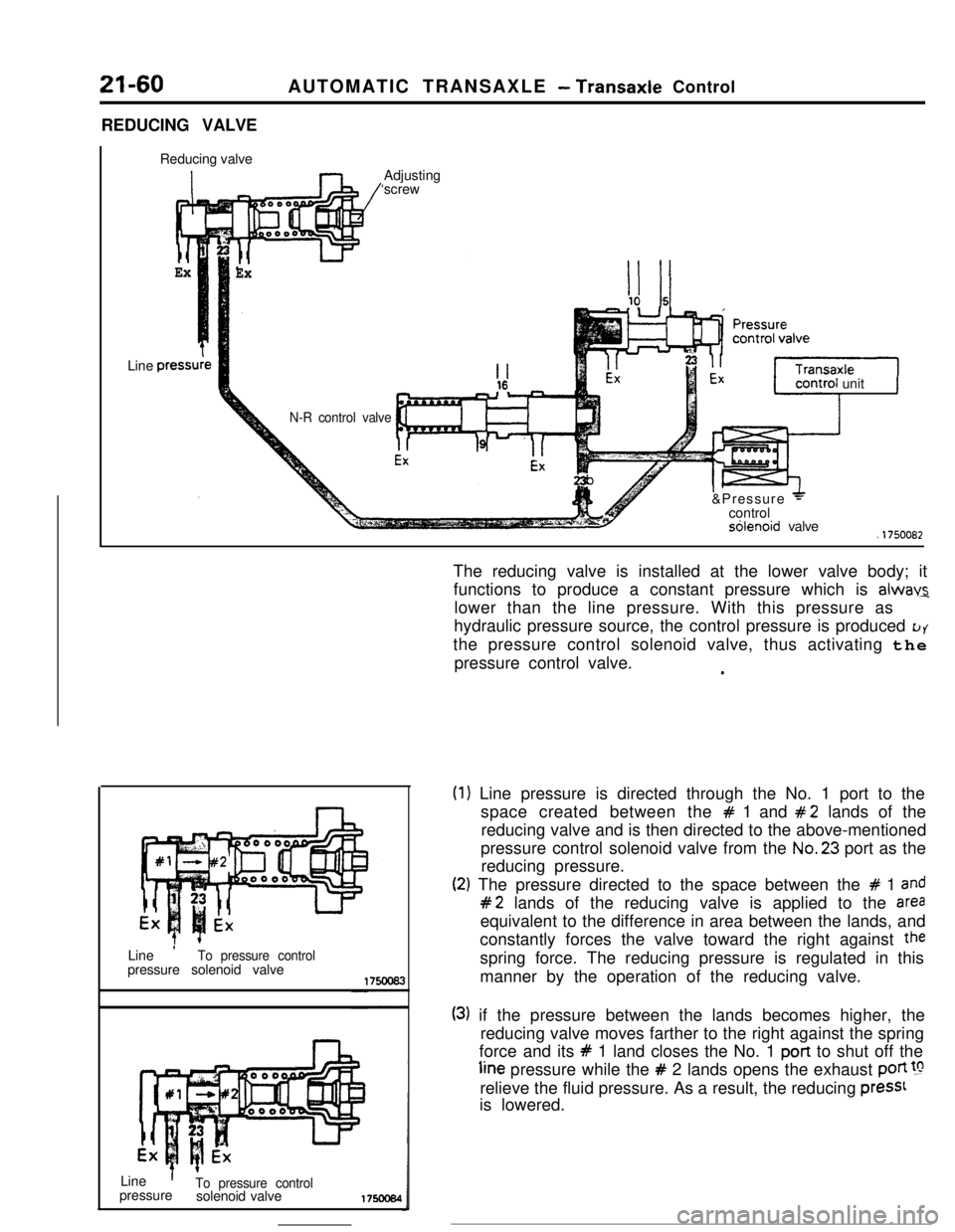
21-60AUTOMATIC TRANSAXLE - Transaxle Control
REDUCING VALVE
Reducing valve
ExLine
press1
ExAdjusting
‘screw
N-R control valveunit
J&Pressure
+controlsblenoid valve.1750082
Line
’To pressure controlpressure solenoid valve
Line
’To pressure controlpressure
solenoid valve175ocs4The reducing valve is installed at the lower valve body; it
functions to produce a constant pressure which is
alwav2lower than the line pressure. With this pressure as
hydraulic pressure source, the control pressure is produced
LJYthe pressure control solenoid valve, thus activating the
pressure control valve.
l
(1
(2
) Line pressure is directed through the No. 1 port to the
space created between the
# 1 and #2 lands of the
reducing valve and is then directed to the above-mentioned
pressure control solenoid valve from the No.23 port as the
reducing pressure.
:) The pressure directed to the space between the # 1 and
#2 lands of the reducing valve is applied to the areaequivalent to the difference in area between the lands, and
constantly forces the valve toward the right against
thespring force. The reducing pressure is regulated in this
manner by the operation of the reducing valve.
(3) if the pressure between the lands becomes higher, the
reducing valve moves farther to the right against the spring
force and its
# 1 land closes the No. 1 port to shut off theline pressure while the
# 2 lands opens the exhaust poti !grelieve the fluid pressure. As a result, the reducing
press1is lowered.
Page 285 of 391
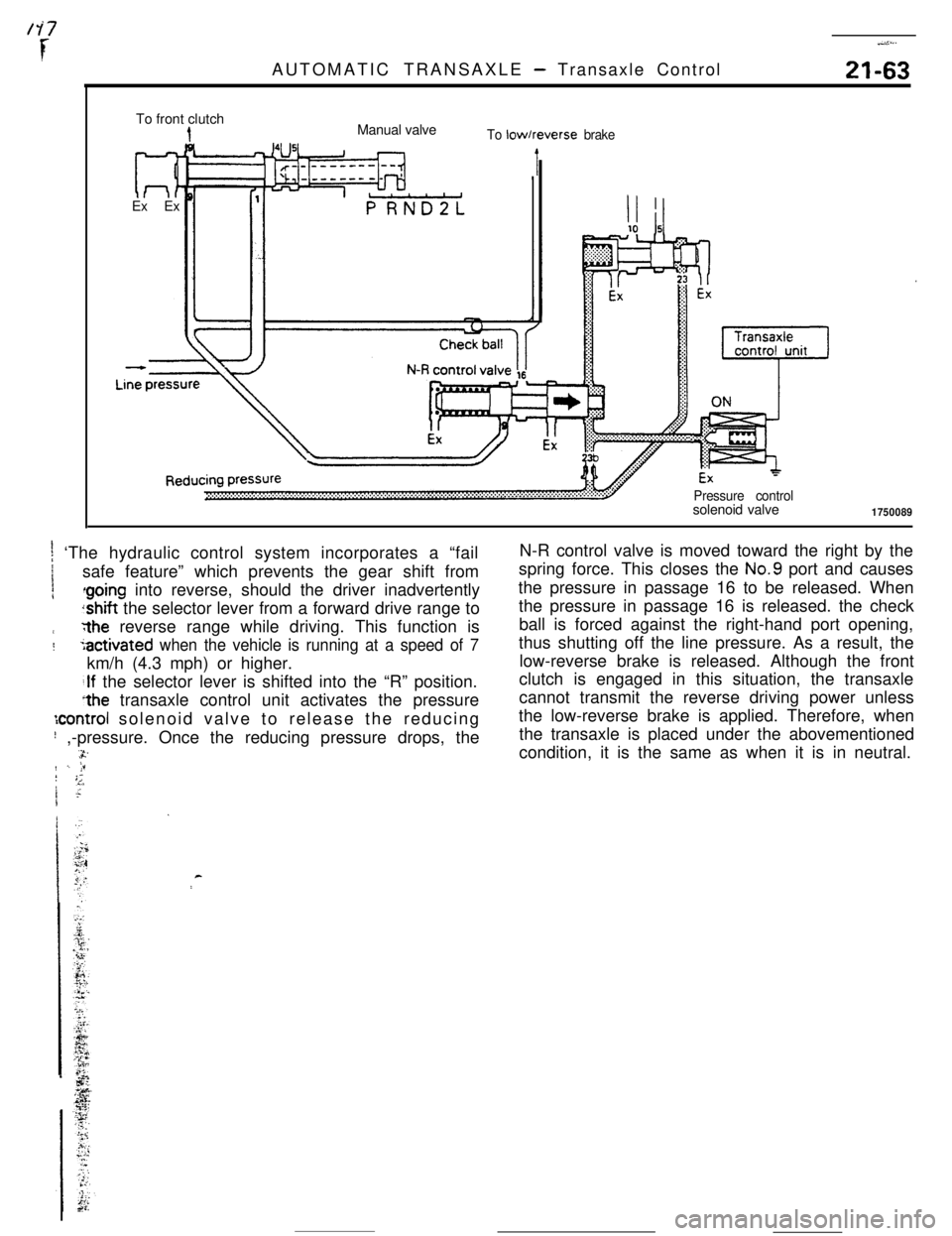
AUTOMATIC TRANSAXLE - Transaxle Control
.-i:...
21-63To front clutch
Ex ExManual valve
To low/reverse brake
Pressure controlsolenoid valve
1750089
t ‘The hydraulic control system incorporates a “fail1
1safe feature” which prevents the gear shift from
irthe reverse range while driving. This function is
:5activated when the vehicle is running at a speed of 7km/h (4.3 mph) or higher.
;If the selector lever is shifted into the “R” position.
*the transaxle control unit activates the pressure
:control solenoid valve to release the reducing
! ,-pressure. Once the reducing pressure drops, the.-a.rr./ -. jF! ;;1 ;I~N-R control valve is moved toward the right by the
spring force. This closes the No.9 port and causes
the pressure in passage 16 to be released. When
the pressure in passage 16 is released. the check
ball is forced against the right-hand port opening,
thus shutting off the line pressure. As a result, the
low-reverse brake is released. Although the front
clutch is engaged in this situation, the transaxle
cannot transmit the reverse driving power unless
the low-reverse brake is applied. Therefore, when
the transaxle is placed under the abovementioned
condition, it is the same as when it is in neutral.
c
Page 295 of 391
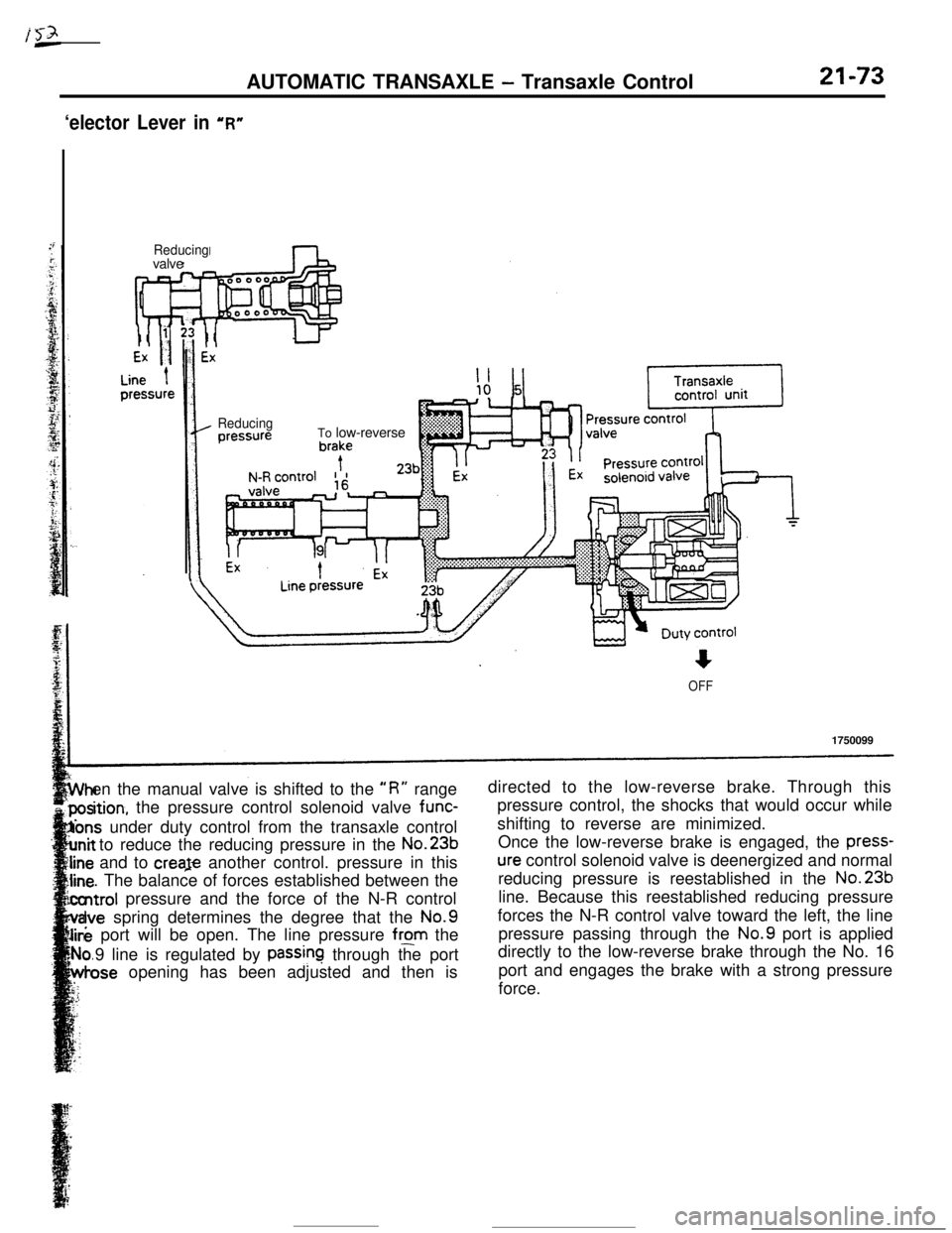
AUTOMATIC TRANSAXLE - Transaxle Control21-73
‘elector Lever in “R”
Reducingvalve
ReducingTo low-reverse
OFF1750099
en the manual valve is shifted to the
“R” rangedirected to the low-reverse brake. Through this
ition, the pressure control solenoid valve func-pressure control, the shocks that would occur while
Ions under duty control from the transaxle controlshifting to reverse are minimized.
to reduce the reducing pressure in the No.23bOnce the low-reverse brake is engaged, the press-and to creaje another control. pressure in this
ure control solenoid valve is deenergized and normal
. The balance of forces established between thereducing pressure is reestablished in the No.23bntrol pressure and the force of the N-R controlline. Because this reestablished reducing pressure
Ivespring determines the degree that the No.9forces the N-R control valve toward the left, the line
e port will be open. The line pressure from thepressure passing through the No.9 port is applied
9 line is regulated by
passinq through the portdirectly to the low-reverse brake through the No. 16
ose opening has been adjusted and then isport and engages the brake with a strong pressure
force.