check engine MITSUBISHI LANCER 2005 Workshop Manual
[x] Cancel search | Manufacturer: MITSUBISHI, Model Year: 2005, Model line: LANCER, Model: MITSUBISHI LANCER 2005Pages: 788, PDF Size: 45.98 MB
Page 511 of 788
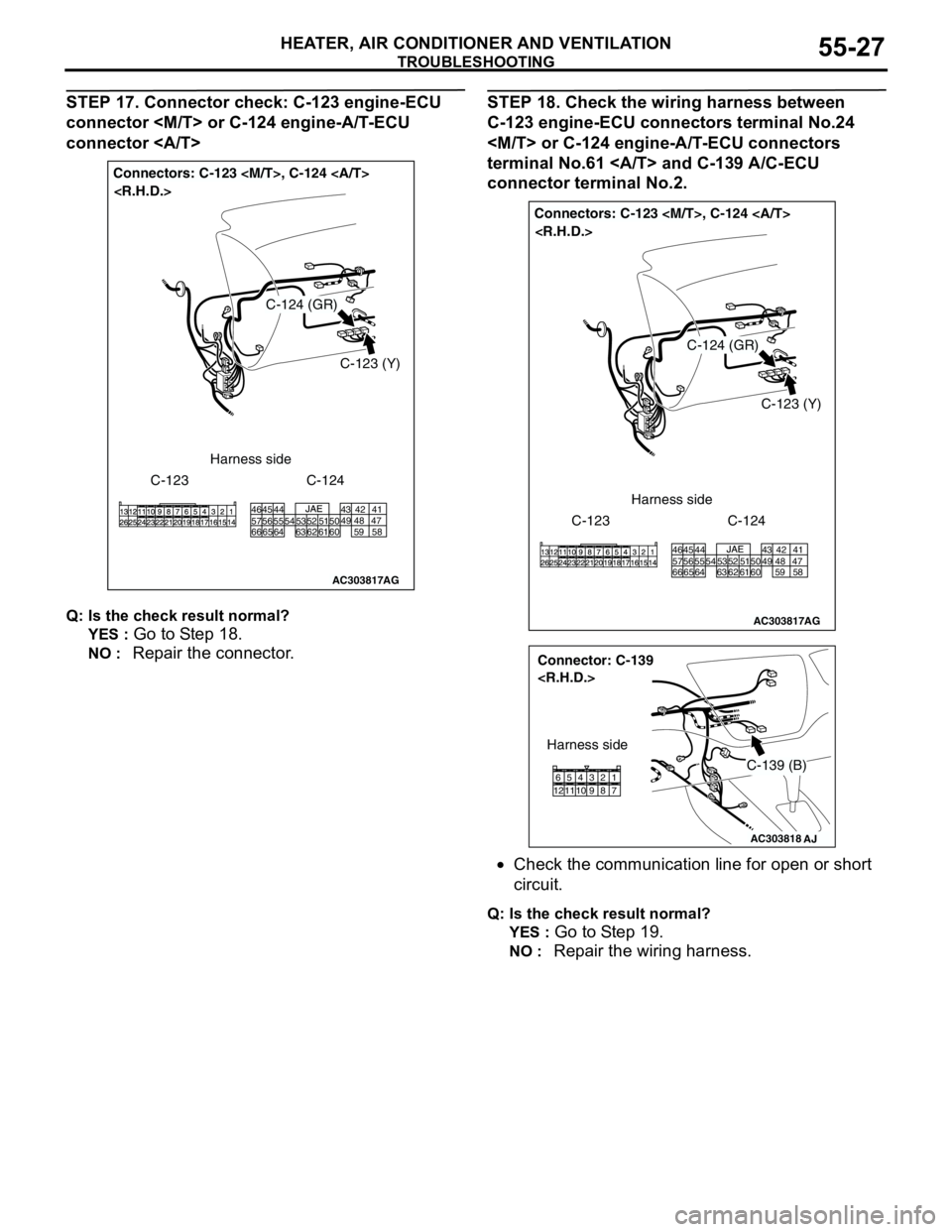
TROUBLESHOOTING
HEATER, AIR CONDITIONER AND VENTILATION55-27
STEP 17. Connector check: C-123 engine-ECU
connector
connector
Q: Is the check result normal?
YES :
Go to Step 18.
NO : Repair the connector.
STEP 18. Check the wiring harness between
C-123 engine-ECU connectors terminal No.24
terminal No.61 and C-139 A/C-ECU
connector terminal No.2.
•Check the communication line for open or short
circuit.
Q: Is the check result normal?
YES :
Go to Step 19.
NO : Repair the wiring harness.
AC303817
Connectors: C-123
AG
C-123 (Y)
C-123Harness side
C-124 (GR)
46 45 44 43 42 41
57 56 55 54 53 52 515049 48 47
66 65 64 63 62 61 60 59 58
C-124
AC303817
Connectors: C-123
AG
C-123 (Y)
C-123Harness side
C-124 (GR)
46 45 44 43 42 41
57 56 55 54 53 52 515049 48 47
66 65 64 63 62 61 60 59 58
C-124
AC303818
Connector: C-139
AJ
Harness side
C-139 (B)
11 12657 8 9 103 421
Page 512 of 788
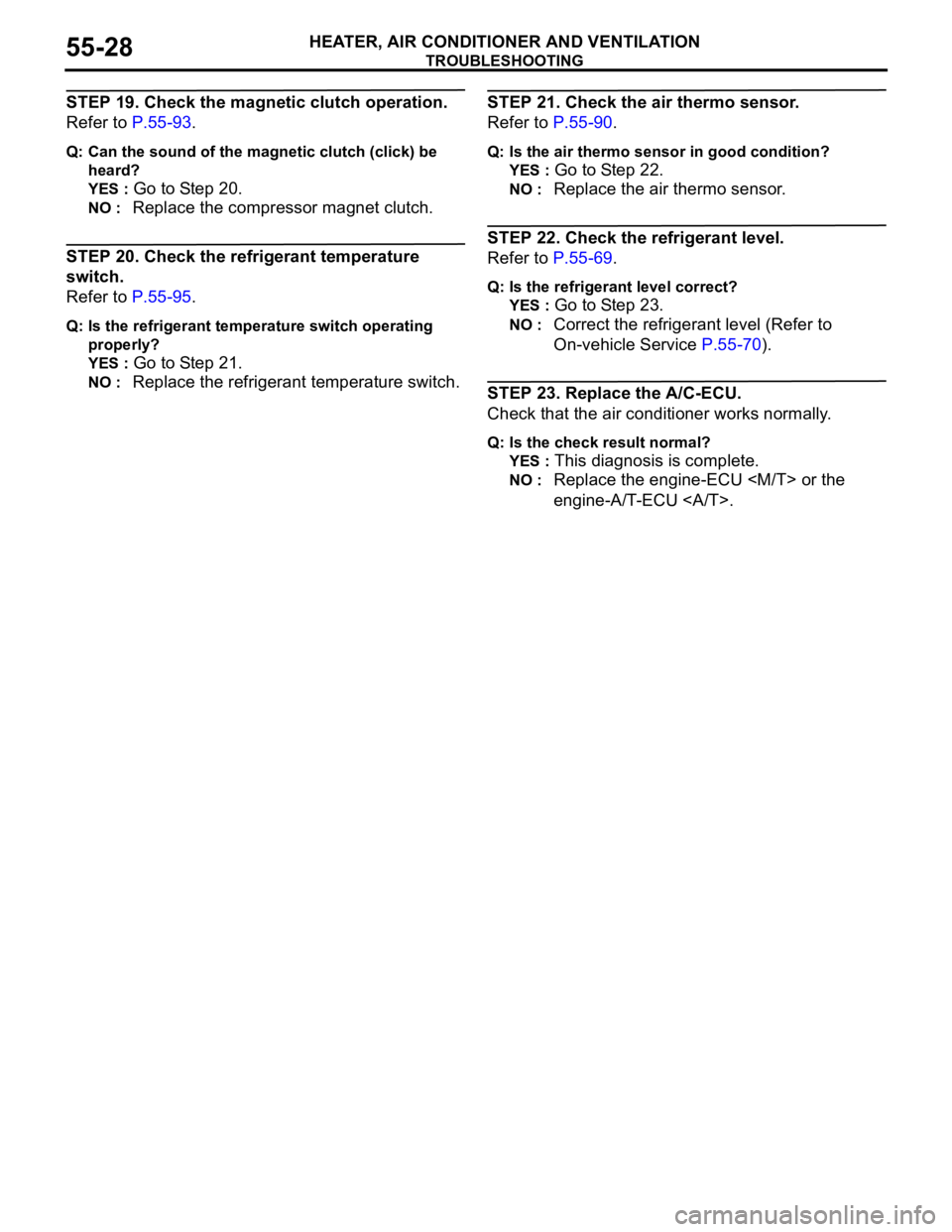
TROUBLESHOOTING
HEATER, AIR CONDITIONER AND VENTILATION55-28
STEP 19. Check the magnetic clutch operation.
Refer to P.55-93.
Q: Can the sound of the magnetic clutch (click) be
heard?
YES :
Go to Step 20.
NO : Replace the compressor magnet clutch.
STEP 20. Check the refrigerant temperature
switch.
Refer to P.55-95.
Q: Is the refrigerant temperature switch operating
properly?
YES :
Go to Step 21.
NO : Replace the refrigerant temperature switch.
STEP 21. Check the air thermo sensor.
Refer to P.55-90.
Q: Is the air thermo sensor in good condition?
YES :
Go to Step 22.
NO : Replace the air thermo sensor.
STEP 22. Check the refrigerant level.
Refer to P.55-69.
Q: Is the refrigerant level correct?
YES :
Go to Step 23.
NO : Correct the refrigerant level (Refer to
On-vehicle Service P.55-70).
STEP 23. Replace the A/C-ECU.
Check that the air conditioner works normally.
Q: Is the check result normal?
YES :
This diagnosis is complete.
NO : Replace the engine-ECU
engine-A/T-ECU .
Page 549 of 788
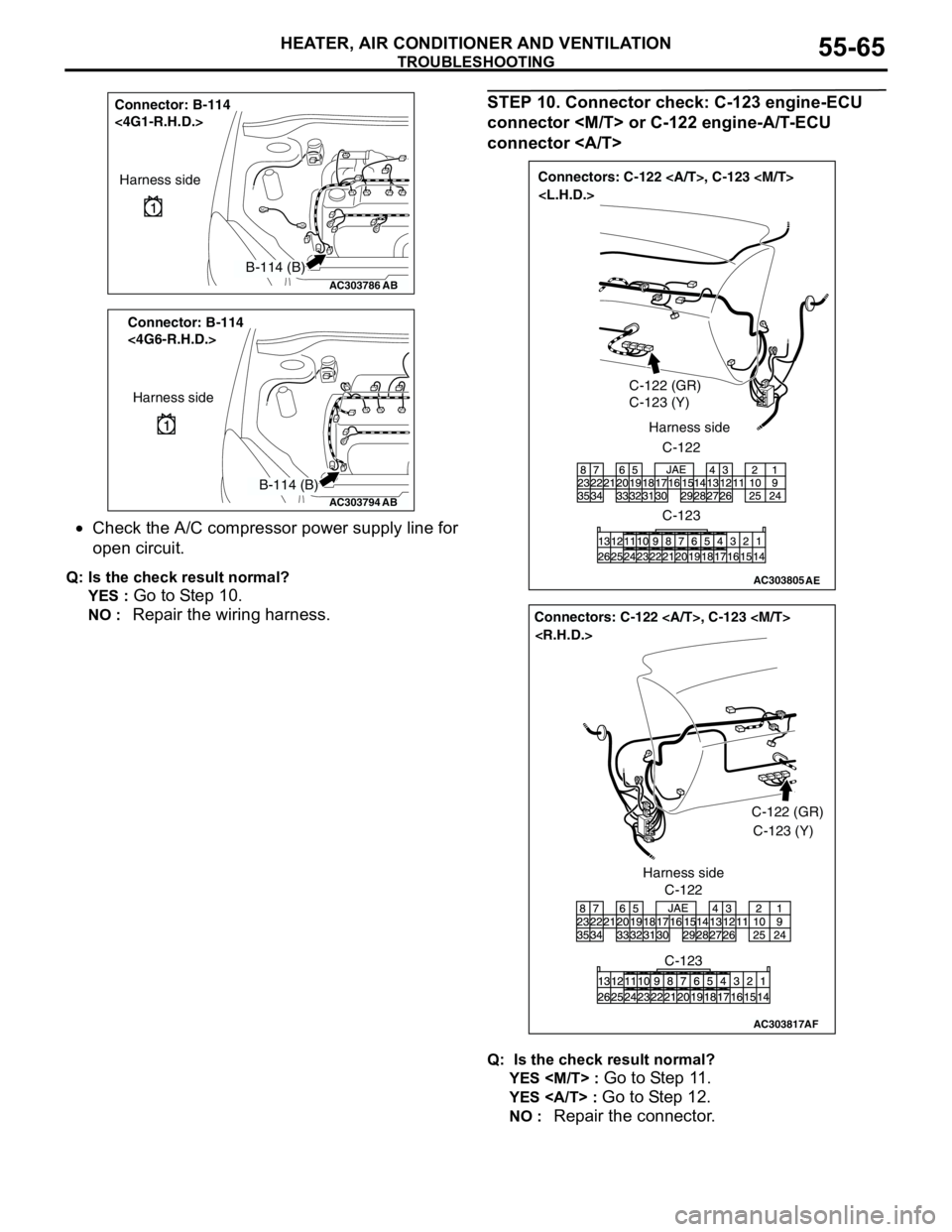
TROUBLESHOOTING
HEATER, AIR CONDITIONER AND VENTILATION55-65
•Check the A/C compressor power supply line for
open circuit.
Q: Is the check result normal?
YES :
Go to Step 10.
NO : Repair the wiring harness.
STEP 10. Connector check: C-123 engine-ECU
connector
connector
Q: Is the check result normal?
YES
Go to Step 11.
YES : Go to Step 12.
NO : Repair the connector.
AC303786
Connector: B-114
<4G1-R.H.D.>
AB
Harness side
B-114 (B)
AC303794
Connector: B-114
<4G6-R.H.D.>
AB
Harness side
B-114 (B)
AC303805
Connectors: C-122 , C-123
C-122 (GR)
C-123 (Y)
C-122 Harness side
C-123
AE
AC303817
Connectors: C-122 , C-123
AF
C-122C-122 (GR)
C-123 (Y)
C-123 Harness side
Page 550 of 788
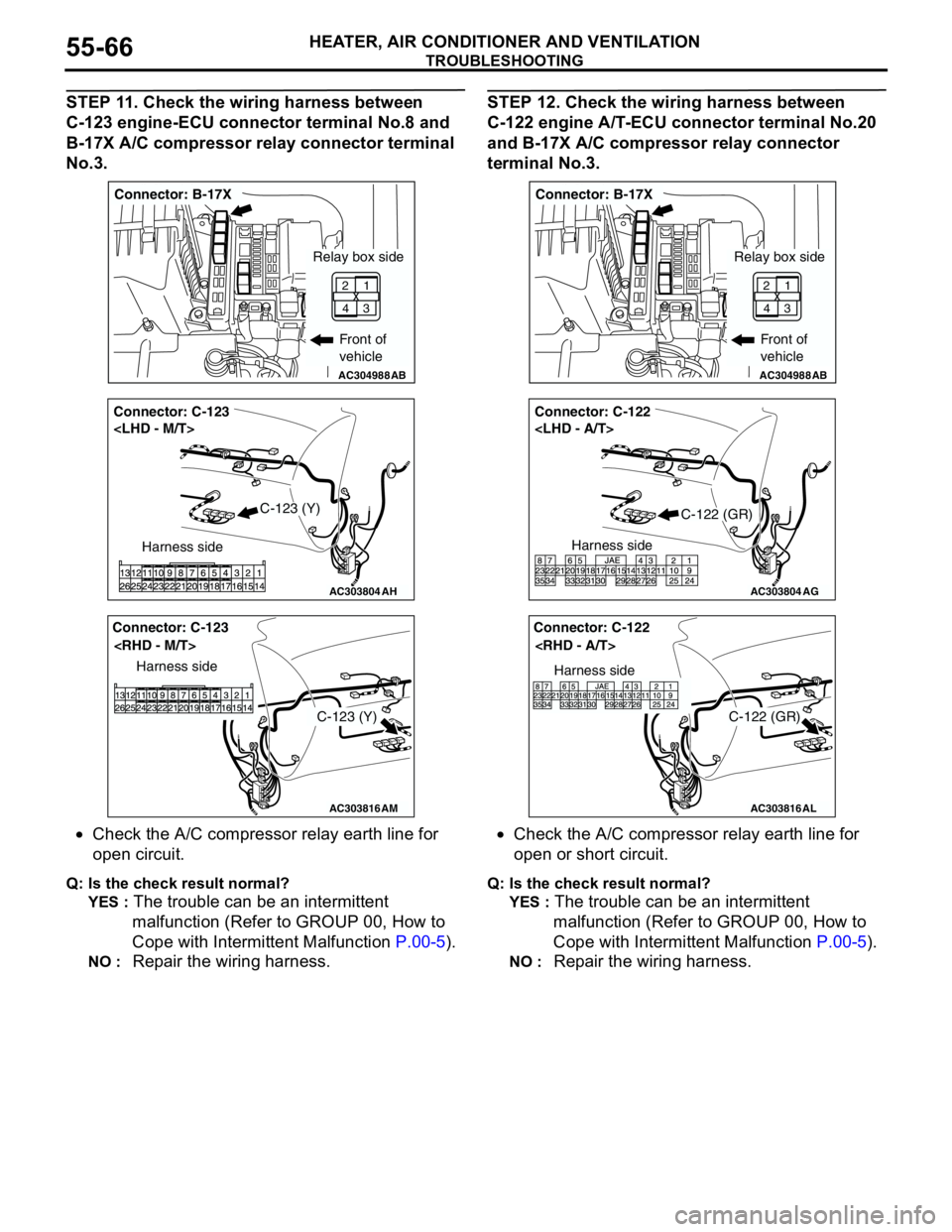
TROUBLESHOOTING
HEATER, AIR CONDITIONER AND VENTILATION55-66
STEP 11. Check the wiring harness between
C-123 engine-ECU connector terminal No.8 and
B-17X A/C compressor relay connector terminal
No.3.
•Check the A/C compressor relay earth line for
open circuit.
Q: Is the check result normal?
YES :
The trouble can be an intermittent
malfunction (Refer to GROUP 00, How to
Cope with Intermittent Malfunction P.00-5).
NO : Repair the wiring harness.
STEP 12. Check the wiring harness between
C-122 engine A/T-ECU connector terminal No.20
and B-17X A/C compressor relay connector
terminal No.3.
•Check the A/C compressor relay earth line for
open or short circuit.
Q: Is the check result normal?
YES :
The trouble can be an intermittent
malfunction (Refer to GROUP 00, How to
Cope with Intermittent Malfunction P.00-5).
NO : Repair the wiring harness.
AC304988AB
Connector: B-17X
Front of
vehicle
1
3 2
4
Relay box side
AC303804
Connector: C-123
AH
Harness side
C-123 (Y)
AC303816
Connector: C-123
AM
Harness side
C-123 (Y)
AC304988AB
Connector: B-17X
Front of
vehicle
1
3 2
4
Relay box side
AC303804
Connector: C-122
AG
Harness side
C-122 (GR)
AC303816
Connector: C-122
AL
Harness side
C-122 (GR)
Page 551 of 788
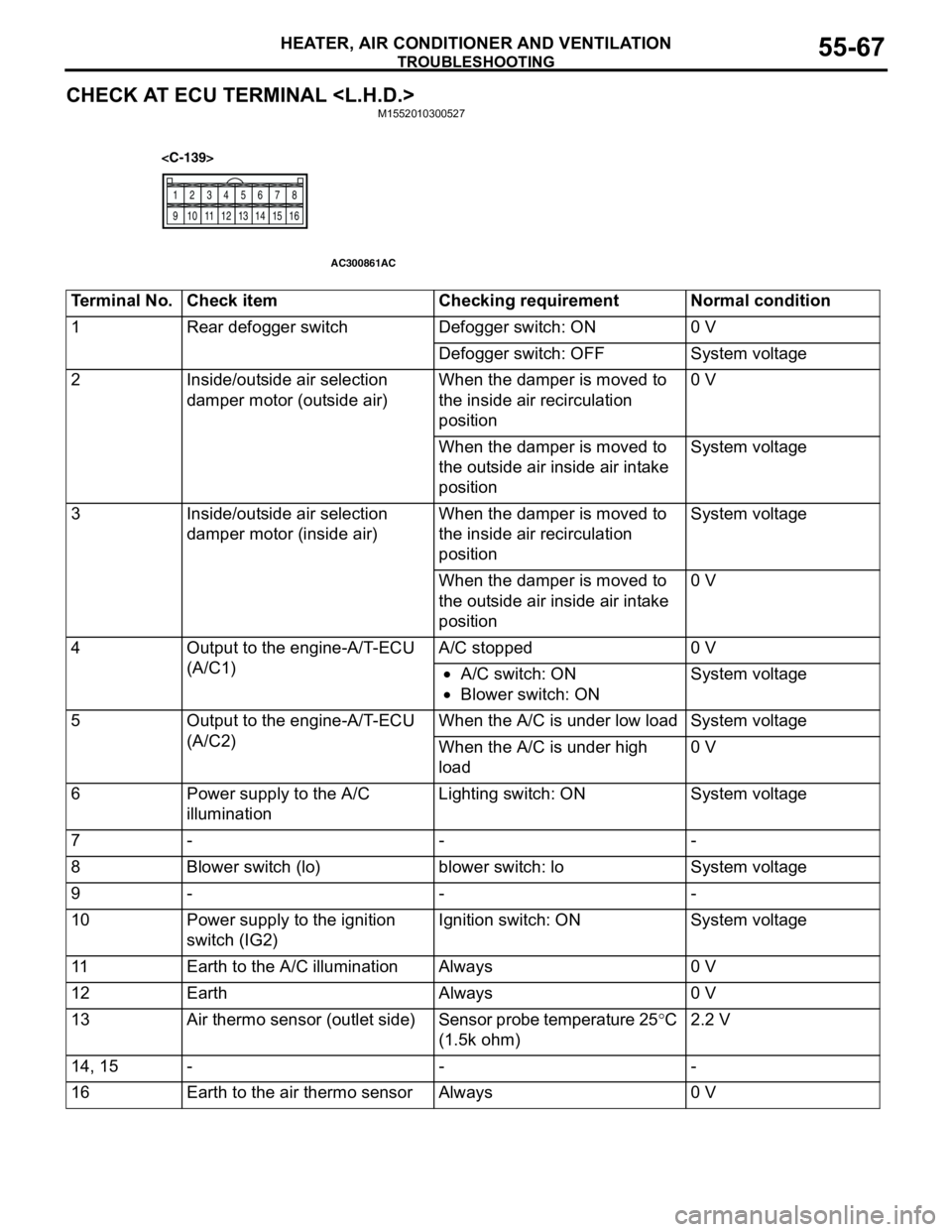
TROUBLESHOOTING
HEATER, AIR CONDITIONER AND VENTILATION55-67
CHECK AT ECU TERMINAL
12
345
678
9 10111213141516
AC300861AC
Terminal No. Check item Checking requirement Normal condition
1 Rear defogger switch Defogger switch: ON 0 V
Defogger switch: OFF System voltage
2 Inside/outside air selection
damper motor (outside air)When the damper is moved to
the inside air recirculation
position0 V
When the damper is moved to
the outside air inside air intake
positionSystem voltage
3 Inside/outside air selection
damper motor (inside air)When the damper is moved to
the inside air recirculation
positionSystem voltage
When the damper is moved to
the outside air inside air intake
position0 V
4 Output to the engine-A/T-ECU
(A/C1)A/C stopped 0 V
•A/C switch: ON
•Blower switch: ONSystem voltage
5 Output to the engine-A/T-ECU
(A/C2)When the A/C is under low load System voltage
When the A/C is under high
load0 V
6 Power supply to the A/C
illuminationLighting switch: ON System voltage
7---
8 Blower switch (lo) blower switch: lo System voltage
9---
10 Power supply to the ignition
switch (IG2)Ignition switch: ON System voltage
11 Earth to the A/C illumination Always 0 V
12 Earth Always 0 V
13 Air thermo sensor (outlet side) Sensor probe temperature 25°C
(1.5k ohm)2.2 V
14, 15 - - -
16 Earth to the air thermo sensor Always 0 V
Page 552 of 788
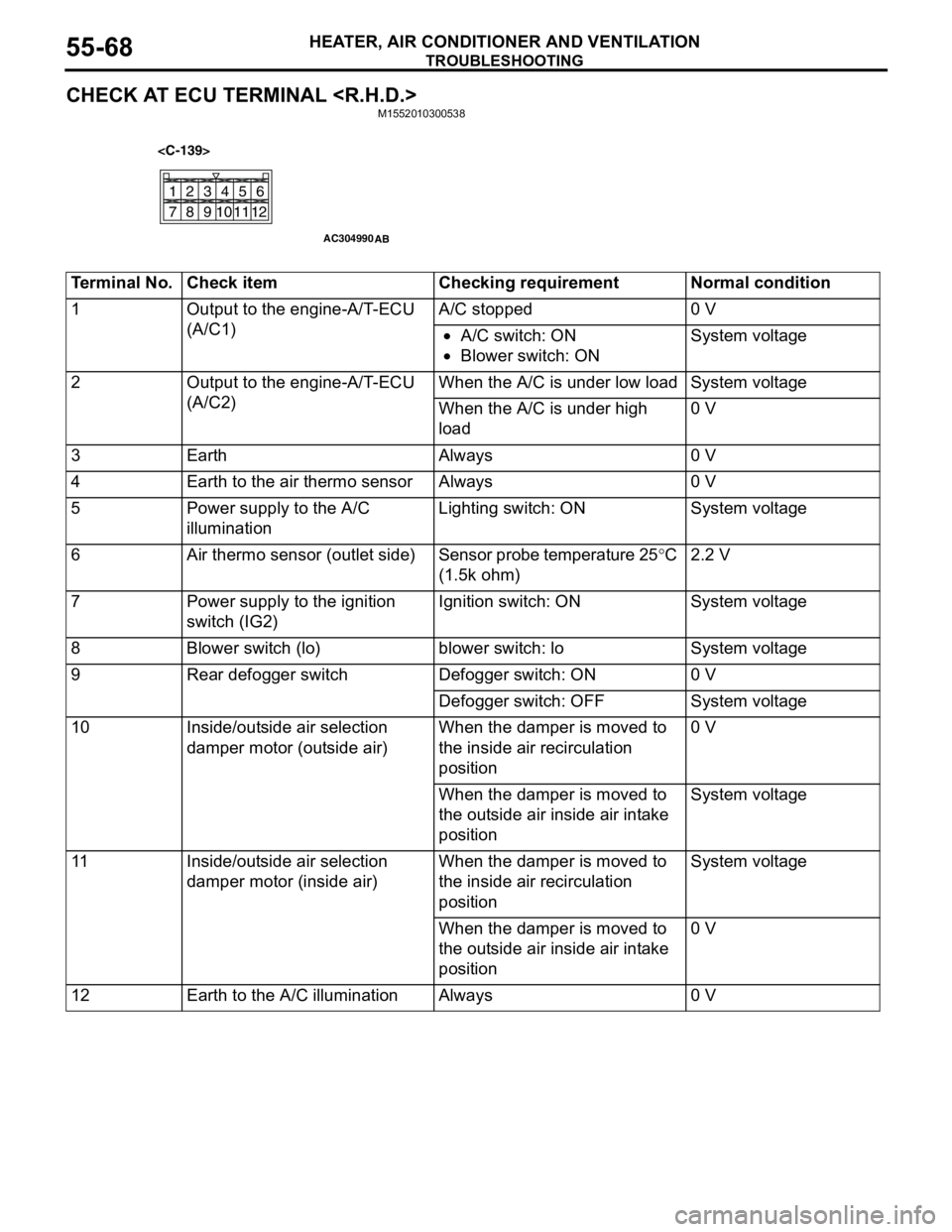
TROUBLESHOOTING
HEATER, AIR CONDITIONER AND VENTILATION55-68
CHECK AT ECU TERMINAL
21
78
6 534
11
10912
AC304990
AB
Terminal No. Check item Checking requirement Normal condition
1 Output to the engine-A/T-ECU
(A/C1)A/C stopped 0 V
•A/C switch: ON
•Blower switch: ONSystem voltage
2 Output to the engine-A/T-ECU
(A/C2)When the A/C is under low load System voltage
When the A/C is under high
load0 V
3 Earth Always 0 V
4 Earth to the air thermo sensor Always 0 V
5 Power supply to the A/C
illuminationLighting switch: ON System voltage
6 Air thermo sensor (outlet side) Sensor probe temperature 25°C
(1.5k ohm)2.2 V
7 Power supply to the ignition
switch (IG2)Ignition switch: ON System voltage
8 Blower switch (lo) blower switch: lo System voltage
9 Rear defogger switch Defogger switch: ON 0 V
Defogger switch: OFF System voltage
10 Inside/outside air selection
damper motor (outside air)When the damper is moved to
the inside air recirculation
position0 V
When the damper is moved to
the outside air inside air intake
positionSystem voltage
11 Inside/outside air selection
damper motor (inside air)When the damper is moved to
the inside air recirculation
positionSystem voltage
When the damper is moved to
the outside air inside air intake
position0 V
12 Earth to the A/C illumination Always 0 V
Page 553 of 788
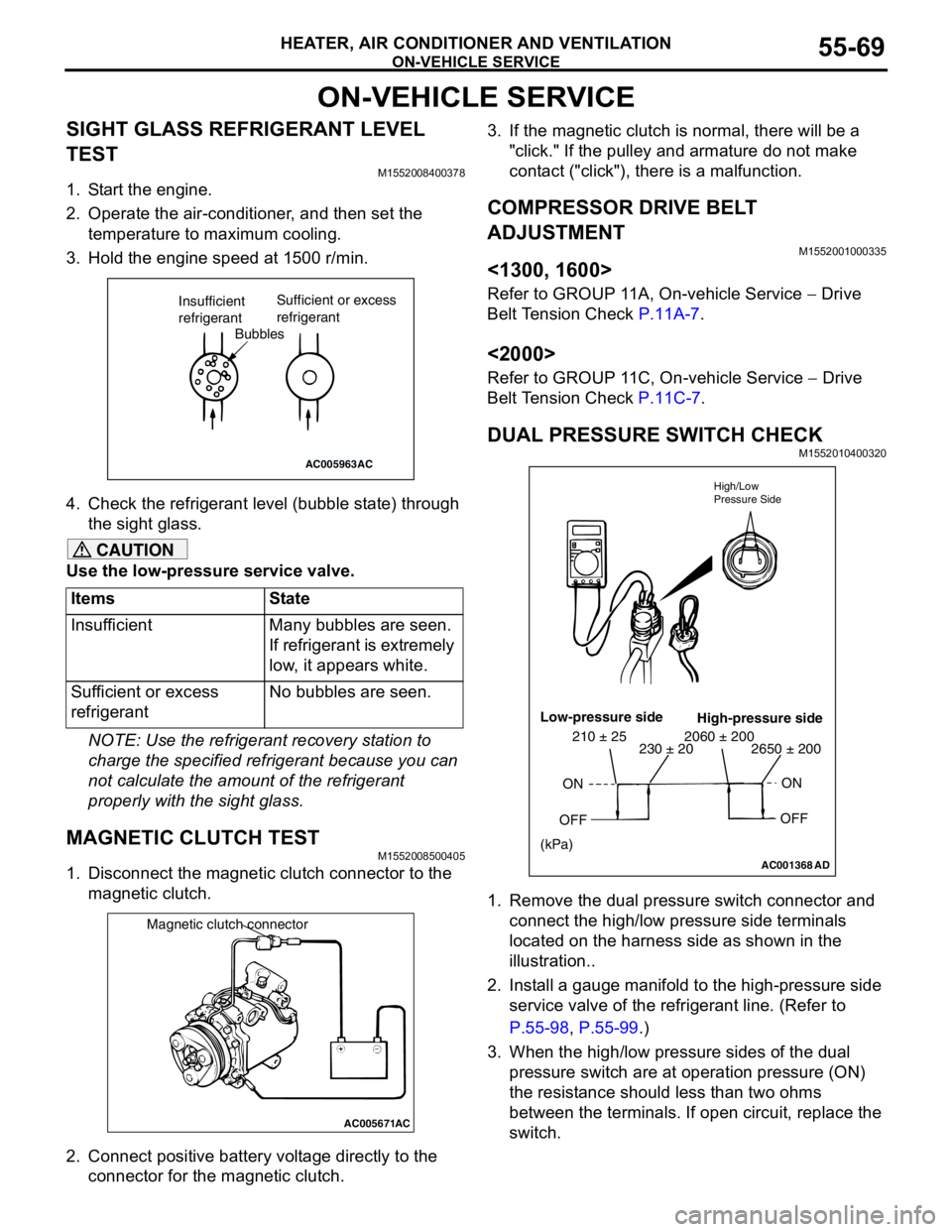
ON-VEHICLE SERVICE
HEATER, AIR CONDITIONER AND VENTILATION55-69
ON-VEHICLE SERVICE
SIGHT GLASS REFRIGERANT LEVEL
TEST
M1552008400378
1. Start the engine.
2. Operate the air-conditioner, and then set the
temperature to maximum cooling.
3. Hold the engine speed at 1500 r/min.
4. Check the refrigerant level (bubble state) through
the sight glass.
CAUTION
Use the low-pressure service valve.
NOTE: Use the refrigerant recovery station to
charge the specified refrigerant because you can
not calculate the amount of the refrigerant
properly with the sight glass.
MAGNETIC CLUTCH TESTM1552008500405
1. Disconnect the magnetic clutch connector to the
magnetic clutch.
2. Connect positive battery voltage directly to the
connector for the magnetic clutch.3. If the magnetic clutch is normal, there will be a
"click." If the pulley and armature do not make
contact ("click"), there is a malfunction.
COMPRESSOR DRIVE BELT
ADJUSTMENT
M1552001000335
<1300, 1600>
Refer to GROUP 11A, On-vehicle Service − Drive
Belt Tension Check P.11A-7.
<2000>
Refer to GROUP 11C, On-vehicle Service − Drive
Belt Tension Check P.11C-7.
DUAL PRESSURE SWITCH CHECKM1552010400320
1. Remove the dual pressure switch connector and
connect the high/low pressure side terminals
located on the harness side as shown in the
illustration..
2. Install a gauge manifold to the high-pressure side
service valve of the refrigerant line. (Refer to
P.55-98, P.55-99.)
3. When the high/low pressure sides of the dual
pressure switch are at operation pressure (ON)
the resistance should less than two ohms
between the terminals. If open circuit, replace the
switch. Items State
Insufficient Many bubbles are seen.
If refrigerant is extremely
low, it appears white.
Sufficient or excess
refrigerantNo bubbles are seen.
AC005963
Bubbles Insufficient
refrigerantSufficient or excess
refrigerant
AC
AC005671
Magnetic clutch connector
AC
AC001368AD High/Low
Pressure Side
Low-pressure side
High-pressure side
ON
OFFON
OFF
2650 ± 200 2060 ± 200230 ± 20 210 ± 25
(kPa)
Page 555 of 788
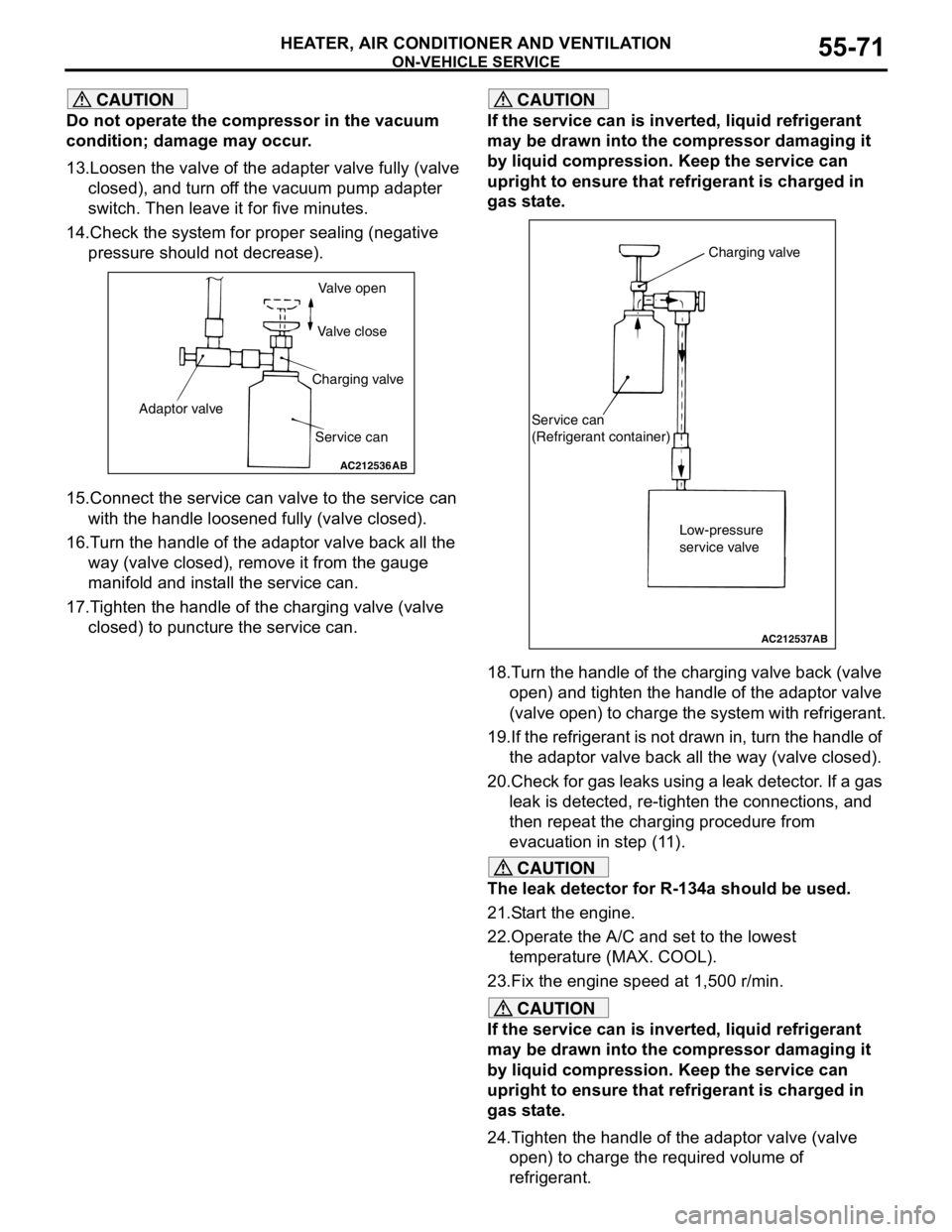
ON-VEHICLE SERVICE
HEATER, AIR CONDITIONER AND VENTILATION55-71
CAUTION
Do not operate the compressor in the vacuum
condition; damage may occur.
13.Loosen the valve of the adapter valve fully (valve
closed), and turn off the vacuum pump adapter
switch. Then leave it for five minutes.
14.Check the system for proper sealing (negative
pressure should not decrease).
15.Connect the service can valve to the service can
with the handle loosened fully (valve closed).
16.Turn the handle of the adaptor valve back all the
way (valve closed), remove it from the gauge
manifold and install the service can.
17.Tighten the handle of the charging valve (valve
closed) to puncture the service can.
CAUTION
If the service can is inverted, liquid refrigerant
may be drawn into the compressor damaging it
by liquid compression. Keep the service can
upright to ensure that refrigerant is charged in
gas state.
18.Turn the handle of the charging valve back (valve
open) and tighten the handle of the adaptor valve
(valve open) to charge the system with refrigerant.
19.If the refrigerant is not drawn in, turn the handle of
the adaptor valve back all the way (valve closed).
20.Check for gas leaks using a leak detector. If a gas
leak is detected, re-tighten the connections, and
then repeat the charging procedure from
evacuation in step (11).
CAUTION
The leak detector for R-134a should be used.
21.Start the engine.
22.Operate the A/C and set to the lowest
temperature (MAX. COOL).
23.Fix the engine speed at 1,500 r/min.
CAUTION
If the service can is inverted, liquid refrigerant
may be drawn into the compressor damaging it
by liquid compression. Keep the service can
upright to ensure that refrigerant is charged in
gas state.
24.Tighten the handle of the adaptor valve (valve
open) to charge the required volume of
refrigerant.
AC212536
Valve open
Valve close
Charging valve
Service can Adaptor valve
AB
AC212537
Charging valve
Service can
(Refrigerant container)
Low-pressure
service valve
AB
Page 556 of 788
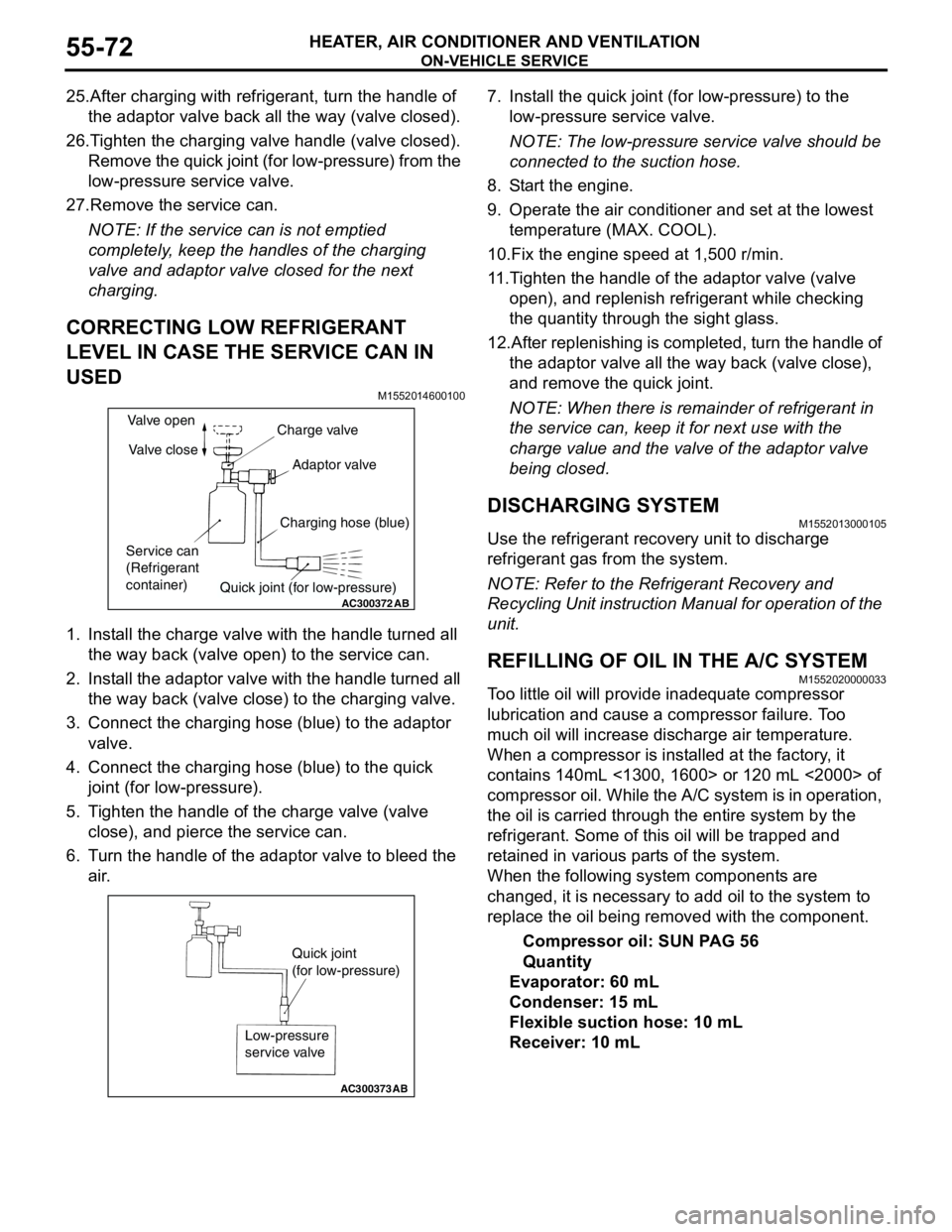
ON-VEHICLE SERVICE
HEATER, AIR CONDITIONER AND VENTILATION55-72
25.After charging with refrigerant, turn the handle of
the adaptor valve back all the way (valve closed).
26.Tighten the charging valve handle (valve closed).
Remove the quick joint (for low-pressure) from the
low-pressure service valve.
27.Remove the service can.
NOTE: If the service can is not emptied
completely, keep the handles of the charging
valve and adaptor valve closed for the next
charging.
CORRECTING LOW REFRIGERANT
LEVEL IN CASE THE SERVICE CAN IN
USED
M1552014600100
1. Install the charge valve with the handle turned all
the way back (valve open) to the service can.
2. Install the adaptor valve with the handle turned all
the way back (valve close) to the charging valve.
3. Connect the charging hose (blue) to the adaptor
valve.
4. Connect the charging hose (blue) to the quick
joint (for low-pressure).
5. Tighten the handle of the charge valve (valve
close), and pierce the service can.
6. Turn the handle of the adaptor valve to bleed the
air.7. Install the quick joint (for low-pressure) to the
low-pressure service valve.
NOTE: The low-pressure service valve should be
connected to the suction hose.
8. Start the engine.
9. Operate the air conditioner and set at the lowest
temperature (MAX. COOL).
10.Fix the engine speed at 1,500 r/min.
11.Tighten the handle of the adaptor valve (valve
open), and replenish refrigerant while checking
the quantity through the sight glass.
12.After replenishing is completed, turn the handle of
the adaptor valve all the way back (valve close),
and remove the quick joint.
NOTE: When there is remainder of refrigerant in
the service can, keep it for next use with the
charge value and the valve of the adaptor valve
being closed.
DISCHARGING SYSTEMM1552013000105
Use the refrigerant recovery unit to discharge
refrigerant gas from the system.
NOTE: Refer to the Refrigerant Recovery and
Recycling Unit instruction Manual for operation of the
unit.
REFILLING OF OIL IN THE A/C SYSTEMM1552020000033
Too little oil will provide inadequate compressor
lubrication and cause a compressor failure. Too
much oil will increase discharge air temperature.
When a compressor is installed at the factory, it
contains 140mL <1300, 1600> or 120 mL <2000> of
compressor oil. While the A/C system is in operation,
the oil is carried through the entire system by the
refrigerant. Some of this oil will be trapped and
retained in various parts of the system.
When the following system components are
changed, it is necessary to add oil to the system to
replace the oil being removed with the component.
Compressor oil: SUN PAG 56
Quantity
Evaporator: 60 mL
Condenser: 15 mL
Flexible suction hose: 10 mL
Receiver: 10 mL
AC300372
AB
Valve open
Valve close
Service can
(Refrigerant
container)Charge valve
Adaptor valve
Charging hose (blue)
Quick joint (for low-pressure)
AC300373
Quick joint
(for low-pressure)
Low-pressure
service valve
AB
Page 558 of 788
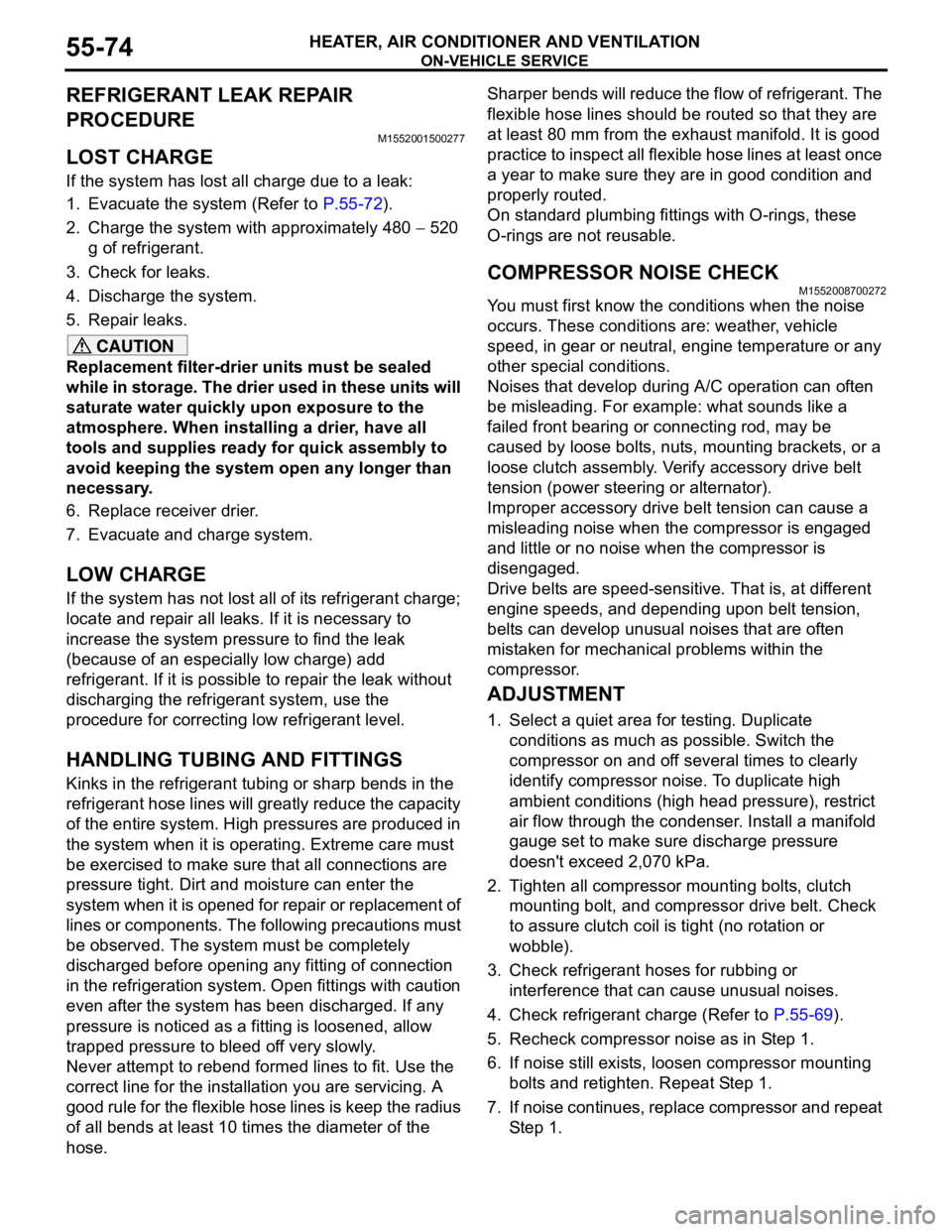
ON-VEHICLE SERVICE
HEATER, AIR CONDITIONER AND VENTILATION55-74
REFRIGERANT LEAK REPAIR
PROCEDURE
M1552001500277
LOST CHARGE
If the system has lost all charge due to a leak:
1. Evacuate the system (Refer to P.55-72).
2. Charge the system with approximately 480 − 520
g of refrigerant.
3. Check for leaks.
4. Discharge the system.
5. Repair leaks.
CAUTION
Replacement filter-drier units must be sealed
while in storage. The drier used in these units will
saturate water quickly upon exposure to the
atmosphere. When installing a drier, have all
tools and supplies ready for quick assembly to
avoid keeping the system open any longer than
necessary.
6. Replace receiver drier.
7. Evacuate and charge system.
LOW CHARGE
If the system has not lost all of its refrigerant charge;
locate and repair all leaks. If it is necessary to
increase the system pressure to find the leak
(because of an especially low charge) add
refrigerant. If it is possible to repair the leak without
discharging the refrigerant system, use the
procedure for correcting low refrigerant level.
HANDLING TUBING AND FITTINGS
Kinks in the refrigerant tubing or sharp bends in the
refrigerant hose lines will greatly reduce the capacity
of the entire system. High pressures are produced in
the system when it is operating. Extreme care must
be exercised to make sure that all connections are
pressure tight. Dirt and moisture can enter the
system when it is opened for repair or replacement of
lines or components. The following precautions must
be observed. The system must be completely
discharged before opening any fitting of connection
in the refrigeration system. Open fittings with caution
even after the system has been discharged. If any
pressure is noticed as a fitting is loosened, allow
trapped pressure to bleed off very slowly.
Never attempt to rebend formed lines to fit. Use the
correct line for the installation you are servicing. A
good rule for the flexible hose lines is keep the radius
of all bends at least 10 times the diameter of the
hose.Sharper bends will reduce the flow of refrigerant. The
flexible hose lines should be routed so that they are
at least 80 mm from the exhaust manifold. It is good
practice to inspect all flexible hose lines at least once
a year to make sure they are in good condition and
properly routed.
On standard plumbing fittings with O-rings, these
O-rings are not reusable.
COMPRESSOR NOISE CHECKM1552008700272
You must first know the conditions when the noise
occurs. These conditions are: weather, vehicle
speed, in gear or neutral, engine temperature or any
other special conditions.
Noises that develop during A/C operation can often
be misleading. For example: what sounds like a
failed front bearing or connecting rod, may be
caused by loose bolts, nuts, mounting brackets, or a
loose clutch assembly. Verify accessory drive belt
tension (power steering or alternator).
Improper accessory drive belt tension can cause a
misleading noise when the compressor is engaged
and little or no noise when the compressor is
disengaged.
Drive belts are speed-sensitive. That is, at different
engine speeds, and depending upon belt tension,
belts can develop unusual noises that are often
mistaken for mechanical problems within the
compressor.
ADJUSTMENT
1. Select a quiet area for testing. Duplicate
conditions as much as possible. Switch the
compressor on and off several times to clearly
identify compressor noise. To duplicate high
ambient conditions (high head pressure), restrict
air flow through the condenser. Install a manifold
gauge set to make sure discharge pressure
doesn't exceed 2,070 kPa.
2. Tighten all compressor mounting bolts, clutch
mounting bolt, and compressor drive belt. Check
to assure clutch coil is tight (no rotation or
wobble).
3. Check refrigerant hoses for rubbing or
interference that can cause unusual noises.
4. Check refrigerant charge (Refer to P.55-69).
5. Recheck compressor noise as in Step 1.
6. If noise still exists, loosen compressor mounting
bolts and retighten. Repeat Step 1.
7. If noise continues, replace compressor and repeat
Step 1.