direction MITSUBISHI LANCER 2005 Owner's Manual
[x] Cancel search | Manufacturer: MITSUBISHI, Model Year: 2005, Model line: LANCER, Model: MITSUBISHI LANCER 2005Pages: 788, PDF Size: 45.98 MB
Page 254 of 788
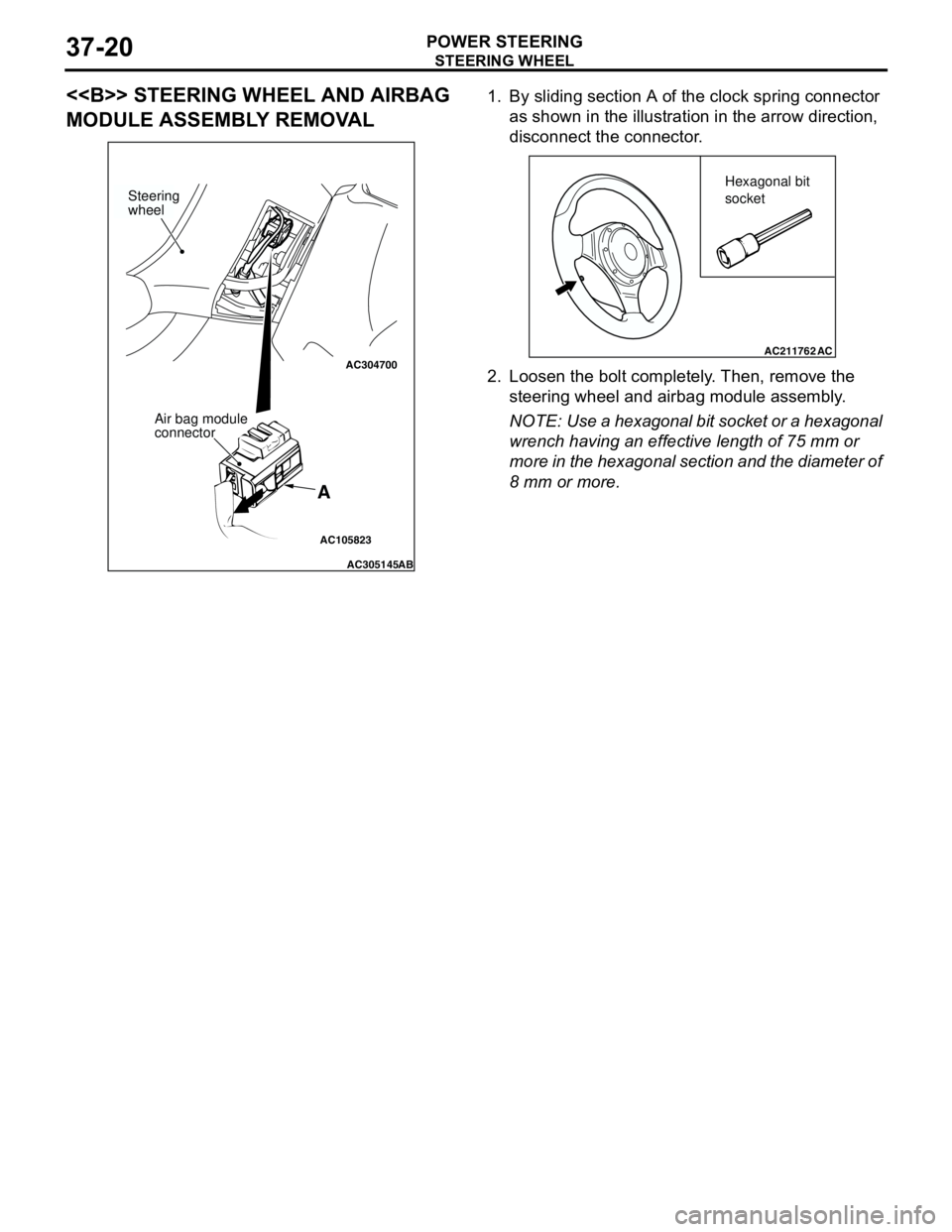
STEERING WHEEL
POWER STEERING37-20
<> STEERING WHEEL AND AIRBAG
MODULE ASSEMBLY REMOVAL1. By sliding section A of the clock spring connector
as shown in the illustration in the arrow direction,
disconnect the connector.
2. Loosen the bolt completely. Then, remove the
steering wheel and airbag module assembly.
NOTE: Use a hexagonal bit socket or a hexagonal
wrench having an effective length of 75 mm or
more in the hexagonal section and the diameter of
8 mm or more.
AC105823
AC304700
AC305145AB
A
Steering
wheel
Air bag module
connector
AC211762AC
Hexagonal bit
socket
Page 256 of 788
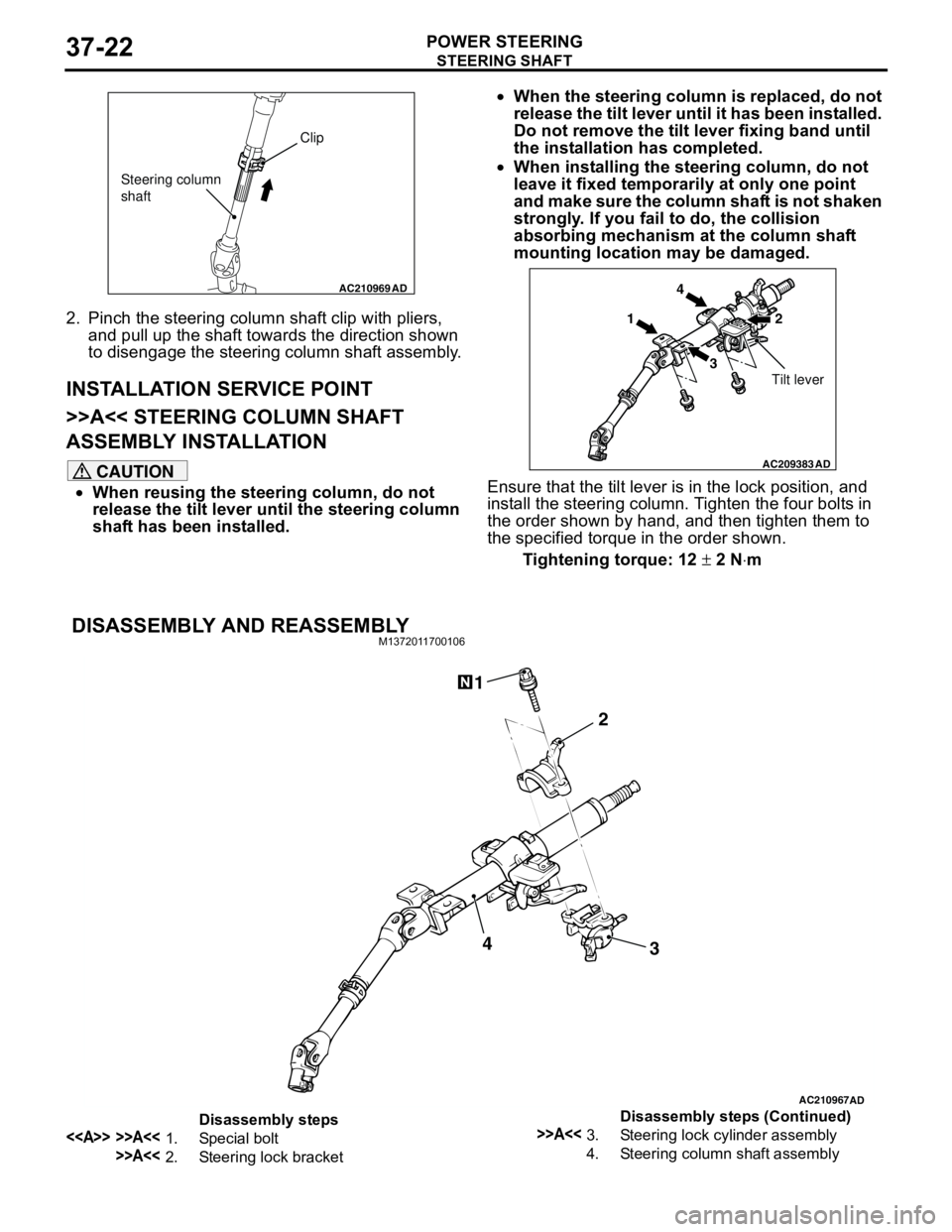
STEERING SHAFT
POWER STEERING37-22
2. Pinch the steering column shaft clip with pliers,
and pull up the shaft towards the direction shown
to disengage the steering column shaft assembly.
INSTALLATION SERVICE POINT
>>A<< STEERING COLUMN SHAFT
ASSEMBLY INSTALLATION
CAUTION
•When reusing the steering column, do not
release the tilt lever until the steering column
shaft has been installed.•When the steering column is replaced, do not
release the tilt lever until it has been installed.
Do not remove the tilt lever fixing band until
the installation has completed.
•When installing the steering column, do not
leave it fixed temporarily at only one point
and make sure the column shaft is not shaken
strongly. If you fail to do, the collision
absorbing mechanism at the column shaft
mounting location may be damaged.
Ensure that the tilt lever is in the lock position, and
install the steering column. Tighten the four bolts in
the order shown by hand, and then tighten them to
the specified torque in the order shown.
Tightening torque: 12 ± 2 N⋅m
DISASSEMBLY AND REASSEMBLYM1372011700106
AC210969AD
Clip
Steering column
shaft
AC209383
AD
14
32
Tilt lever
AC210967AD
3 2 14
Disassembly steps
<> >>A<<1. Special bolt
>>A<<2. Steering lock bracket
>>A<<3. Steering lock cylinder assembly
4. Steering column shaft assemblyDisassembly steps (Continued)
Page 275 of 788
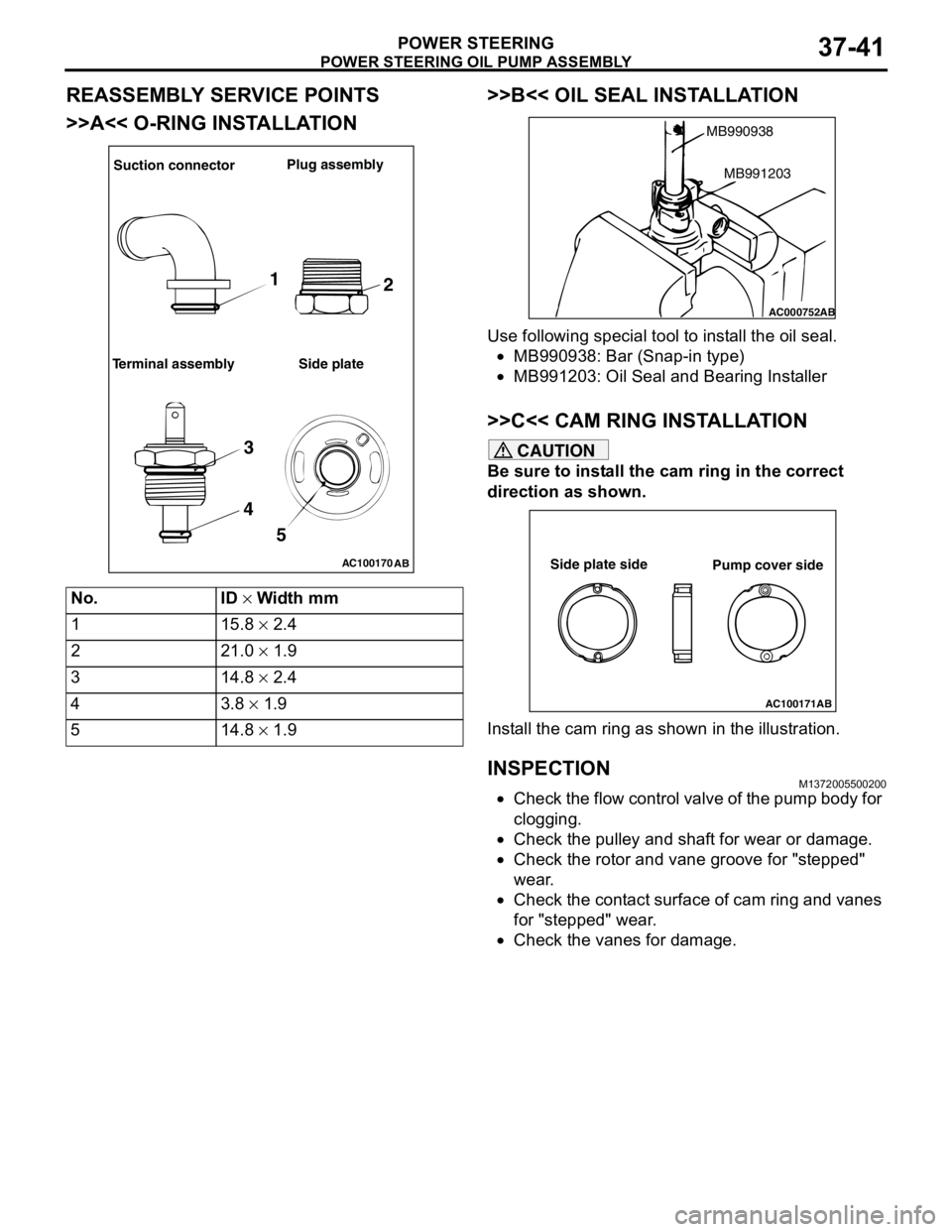
POWER STEERING OIL PUMP ASSEMBLY
POWER STEERING37-41
REASSEMBLY SERVICE POINTS
>>A<< O-RING INSTALLATION>>B<< OIL SEAL INSTALLATION
Use following special tool to install the oil seal.
•MB990938: Bar (Snap-in type)
•MB991203: Oil Seal and Bearing Installer
>>C<< CAM RING INSTALLATION
CAUTION
Be sure to install the cam ring in the correct
direction as shown.
Install the cam ring as shown in the illustration.
INSPECTIONM1372005500200
•Check the flow control valve of the pump body for
clogging.
•Check the pulley and shaft for wear or damage.
•Check the rotor and vane groove for "stepped"
wear.
•Check the contact surface of cam ring and vanes
for "stepped" wear.
•Check the vanes for damage. No. ID × Width mm
1 15.8 × 2.4
2 21.0 × 1.9
3 14.8 × 2.4
43.8 × 1.9
5 14.8 × 1.9
AC100170
AB
Suction connectorPlug assembly
Terminal assembly Side plate
1
2
3
4
5
AC000752
MB990938
AB
MB991203
AC100171AB
Side plate side
Pump cover side
Page 305 of 788
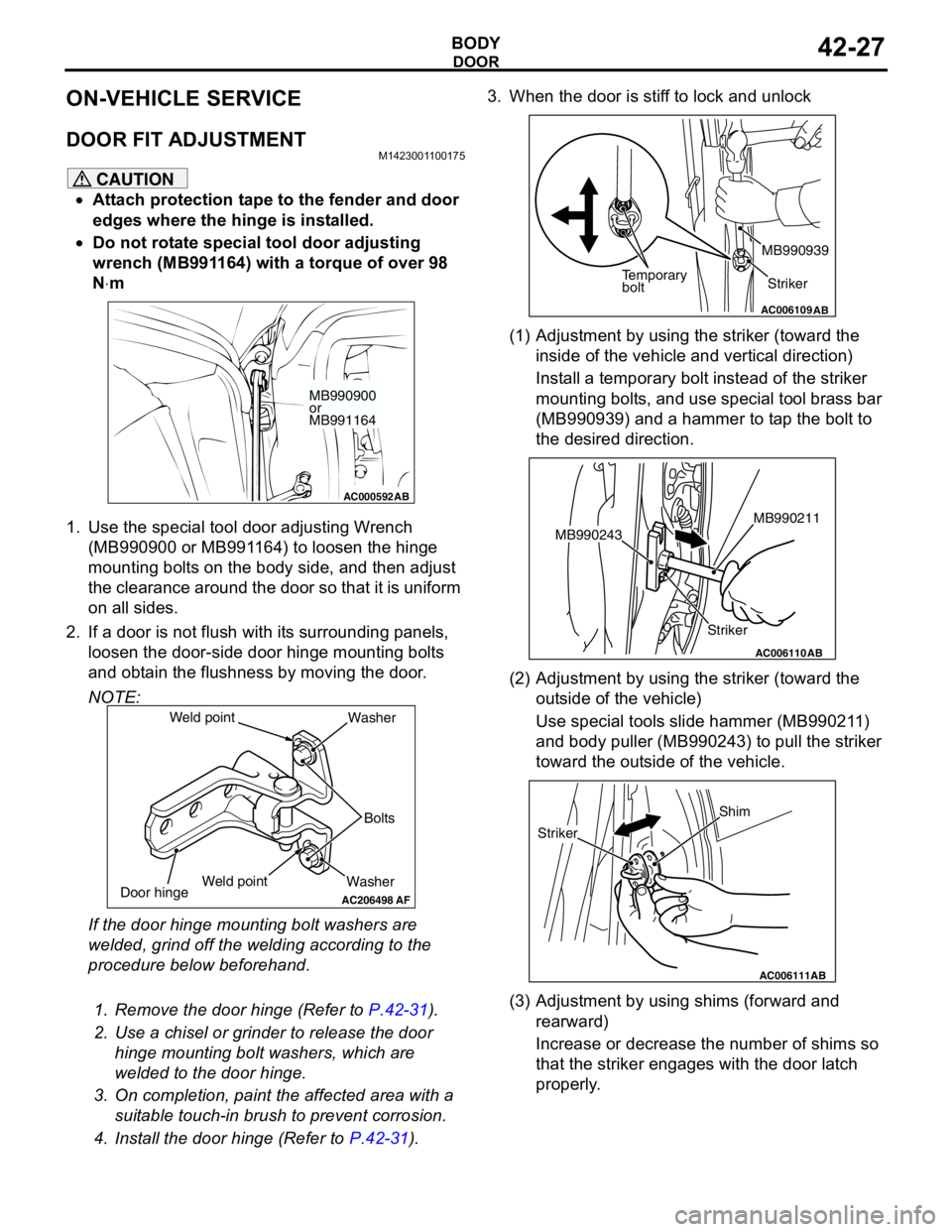
DOOR
BODY42-27
ON-VEHICLE SERVICE
DOOR FIT ADJUSTMENTM1423001100175
CAUTION
•Attach protection tape to the fender and door
edges where the hinge is installed.
•Do not rotate special tool door adjusting
wrench (MB991164) with a torque of over 98
N⋅m
1. Use the special tool door adjusting Wrench
(MB990900 or MB991164) to loosen the hinge
mounting bolts on the body side, and then adjust
the clearance around the door so that it is uniform
on all sides.
2. If a door is not flush with its surrounding panels,
loosen the door-side door hinge mounting bolts
and obtain the flushness by moving the door.
NOTE:
If the door hinge mounting bolt washers are
welded, grind off the welding according to the
procedure below beforehand.
.
1. Remove the door hinge (Refer to P.42-31).
2. Use a chisel or grinder to release the door
hinge mounting bolt washers, which are
welded to the door hinge.
3. On completion, paint the affected area with a
suitable touch-in brush to prevent corrosion.
4. Install the door hinge (Refer to P.42-31).3. When the door is stiff to lock and unlock
(1) Adjustment by using the striker (toward the
inside of the vehicle and vertical direction)
Install a temporary bolt instead of the striker
mounting bolts, and use special tool brass bar
(MB990939) and a hammer to tap the bolt to
the desired direction.
(2) Adjustment by using the striker (toward the
outside of the vehicle)
Use special tools slide hammer (MB990211)
and body puller (MB990243) to pull the striker
toward the outside of the vehicle.
(3) Adjustment by using shims (forward and
rearward)
Increase or decrease the number of shims so
that the striker engages with the door latch
properly.
AC000592
MB990900
or
MB991164
AB
AC206498
WasherBolts Washer
Door hinge
AF
Weld point Weld point
AC006109AB
Temporary
boltStriker MB990939
AC006110
StrikerMB990211
MB990243
AB
AC006111AB
Shim
Striker
Page 369 of 788
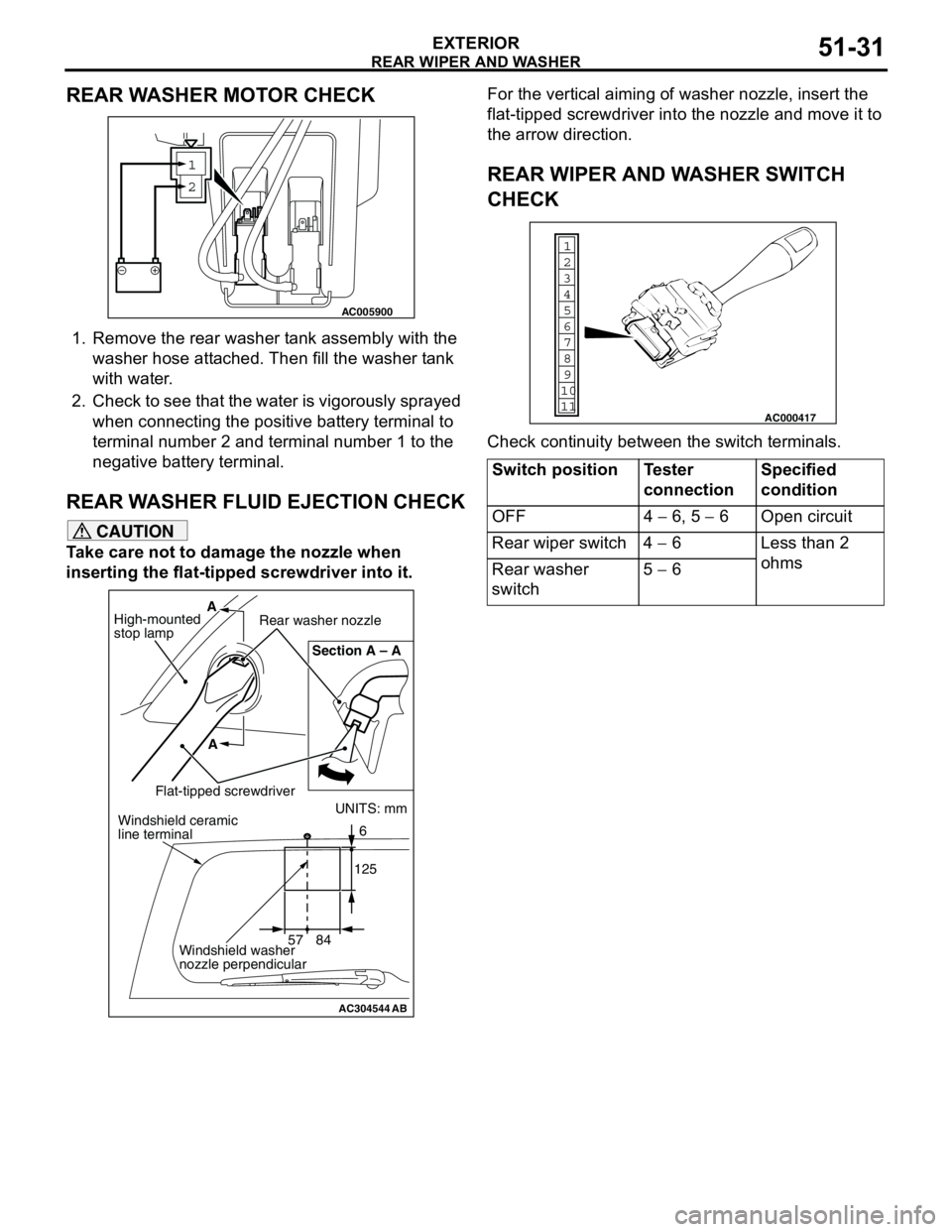
REAR WIPER AND WASHER
EXTERIOR51-31
REAR WASHER MOTOR CHECK
1. Remove the rear washer tank assembly with the
washer hose attached. Then fill the washer tank
with water.
2. Check to see that the water is vigorously sprayed
when connecting the positive battery terminal to
terminal number 2 and terminal number 1 to the
negative battery terminal.
REAR WASHER FLUID EJECTION CHECK
CAUTION
Take care not to damage the nozzle when
inserting the flat-tipped screwdriver into it.For the vertical aiming of washer nozzle, insert the
flat-tipped screwdriver into the nozzle and move it to
the arrow direction.
REAR WIPER AND WASHER SWITCH
CHECK
Check continuity between the switch terminals.
1
2
AC005900
AC304544AB
UNITS: mm
57 841256 Section A – A
A A
High-mounted
stop lampRear washer nozzle
Flat-tipped screwdriverWindshield ceramic
line terminal
Windshield washer
nozzle perpendicular
Switch position Tester
connectionSpecified
condition
OFF 4 − 6, 5 − 6 Open circuit
Rear wiper switch 4 − 6 Less than 2
ohms
Rear washer
switch5 − 6
1
6
8
11 109 7
5 4
3
2
AC000417
Page 385 of 788
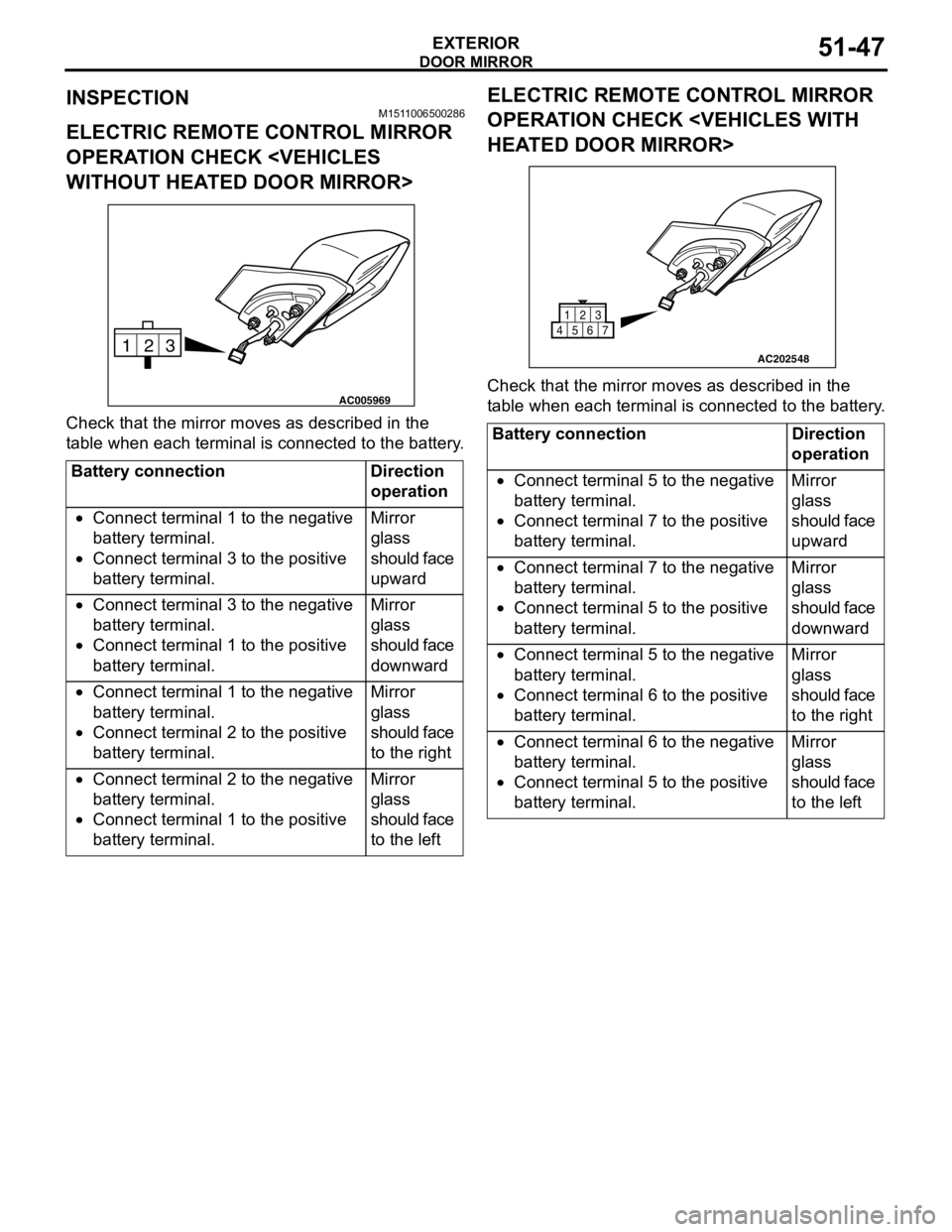
DOOR MIRROR
EXTERIOR51-47
INSPECTIONM1511006500286
ELECTRIC REMOTE CONTROL MIRROR
OPERATION CHECK
Check that the mirror moves as described in the
table when each terminal is connected to the battery.
ELECTRIC REMOTE CONTROL MIRROR
OPERATION CHECK
Check that the mirror moves as described in the
table when each terminal is connected to the battery.
Battery connection Direction
operation
•Connect terminal 1 to the negative
battery terminal.
•Connect terminal 3 to the positive
battery terminal.Mirror
glass
should face
upward
•Connect terminal 3 to the negative
battery terminal.
•Connect terminal 1 to the positive
battery terminal.Mirror
glass
should face
downward
•Connect terminal 1 to the negative
battery terminal.
•Connect terminal 2 to the positive
battery terminal.Mirror
glass
should face
to the right
•Connect terminal 2 to the negative
battery terminal.
•Connect terminal 1 to the positive
battery terminal.Mirror
glass
should face
to the left
3 2
1
AC005969
Battery connection Direction
operation
•Connect terminal 5 to the negative
battery terminal.
•Connect terminal 7 to the positive
battery terminal.Mirror
glass
should face
upward
•Connect terminal 7 to the negative
battery terminal.
•Connect terminal 5 to the positive
battery terminal.Mirror
glass
should face
downward
•Connect terminal 5 to the negative
battery terminal.
•Connect terminal 6 to the positive
battery terminal.Mirror
glass
should face
to the right
•Connect terminal 6 to the negative
battery terminal.
•Connect terminal 5 to the positive
battery terminal.Mirror
glass
should face
to the left
AC202548
1
456723
Page 454 of 788
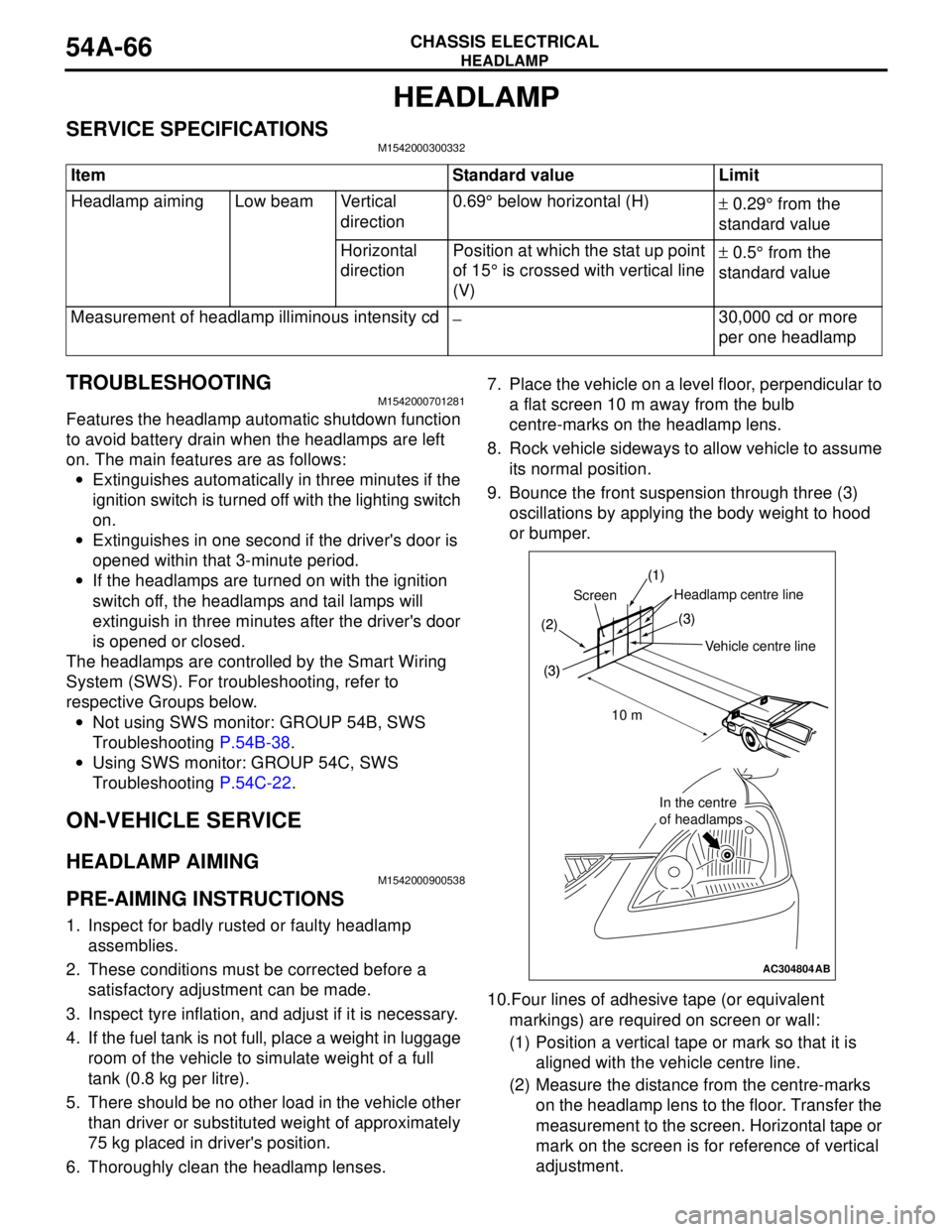
HEADLAMP
CHASSIS ELECTRICAL54A-66
HEADLAMP
SERVICE SPECIFICATIONSM1542000300332
TROUBLESHOOTING M1542000701281
Features the headlamp automatic shutdown function
to avoid battery drain when the headlamps are left
on. The main features are as follows:
•Extinguishes automatically in three minutes if the
ignition switch is turned off with the lighting switch
on.
•Extinguishes in one second if the driver's door is
opened within that 3-minute period.
•If the headlamps are turned on with the ignition
switch off, the headlamps and tail lamps will
extinguish in three minutes after the driver's door
is opened or closed.
The headlamps are controlled by the Smart Wiring
System (SWS). For troubleshooting, refer to
respective Groups below.
•Not using SWS monitor: GROUP 54B, SWS
Troubleshooting P.54B-38.
•Using SWS monitor: GROUP 54C, SWS
Troubleshooting P.54C-22.
ON-VEHICLE SERVICE
HEADLAMP AIMING
M1542000900538
PRE-AIMING INSTRUCTIONS
1. Inspect for badly rusted or faulty headlamp
assemblies.
2. These conditions must be corrected before a
satisfactory adjustment can be made.
3. Inspect tyre inflation, and adjust if it is necessary.
4. If the fuel tank is not full, place a weight in luggage
room of the vehicle to simulate weight of a full
tank (0.8 kg per litre).
5. There should be no other load in the vehicle other
than driver or substituted weight of approximately
75 kg placed in driver's position.
6. Thoroughly clean the headlamp lenses.7. Place the vehicle on a level floor, perpendicular to
a flat screen 10 m away from the bulb
centre-marks on the headlamp lens.
8. Rock vehicle sideways to allow vehicle to assume
its normal position.
9. Bounce the front suspension through three (3)
oscillations by applying the body weight to hood
or bumper.
10.Four lines of adhesive tape (or equivalent
markings) are required on screen or wall:
(1) Position a vertical tape or mark so that it is
aligned with the vehicle centre line.
(2) Measure the distance from the centre-marks
on the headlamp lens to the floor. Transfer the
measurement to the screen. Horizontal tape or
mark on the screen is for reference of vertical
adjustment. Item Standard value Limit
Headlamp aiming Low beam Vertical
direction0.69° below horizontal (H)
± 0.29° from the
standard value
Horizontal
directionPosition at which the stat up point
of 15° is crossed with vertical line
(V)± 0.5° from the
standard value
Measurement of headlamp illiminous intensity cd
−30,000 cd or more
per one headlamp
AC304804
(1)
(2)
(3)
Headlamp centre line
Vehicle crntre line Screen
(3)
10 m
In the centre
of headlamps
(1)
(2)
(3)(3)
In the centre
of headlamps
AB
Vehicle centre line
ScreenHeadlamp centre line
10 m
Page 455 of 788

HEADLAMP
CHASSIS ELECTRICAL54A-67
NOTE: Height from the floor to the centre of
the headlamps (Reference value): 840 mm
(3) Measure the distance from the centre line of
the vehicle to the centre of each headlamp.
Transfer the measurement to the screen.
Vertical tape or mark on the screen with
reference to the centre line of each headlamp
bulb.
HEADLAMP ADJUSTMENT
CAUTION
•Do not cover a headlamp for more than three
minutes to prevent the plastic headlamp lens
deformation.
•When adjusting one headlamp beam, make
sure that another headlamp is off by
disconnecting the connector from it. When
reconnecting the connector, make sure that
the headlamp beam is not disturbed
accidentally.
1. The low-beam headlamp should project on the
screen upper edge of the beam (cut-off).
2. If not the case, turn the adjusting screws to
achieve the specified low-beam cut-off location on
the aiming screen.Standard value:
(Vertical direction) 0.69° below horizontal (H)
(Horizontal direction) Position at which the
stat up point of 15° is crossed with vertical
line (V)
Limit:
Vertical direction; ± 0.29° from the standard
value
Horizontal direction; ± 0.5° from the standard
value
LUMINOUS INTENSITY MEASUREMENTM1542001000464
1. Set the headlamps to high-beam.
2. Using a photometer, and following its
manufacturer's instruction manual, measure the
headlamp centre intensity and check to be sure
that the limit value is satisfied.
Limit: 30,000 cd or more {When a screen is
set 25m ahead of the vehicle}
NOTE: When measuring the intensity, maintain an
engine speed of 2,000 r/min., with the battery fully
charged.
There may be special local regulations pertaining to
headlamp intensity. Be sure to make any
adjustments necessary to satisfy such regulations.
If an illuminometer is used to make the
measurements, convert its values to photometer
values by using the following formula.
I =E x r
2:
•I = intensity (cd)
•E = illumination (lux)
•r = distance (m) from headlamps to illuminometer
AC300567AB
Vertical
direction
Horizontal
direction
AC300658AB
Vertical
direction
Horizontal
direction
AC305155
(H)(V)
Distance of
vertical direction
[0.69˚]Headlamp
centre
High intensity
zone
15˚
AB
Page 460 of 788
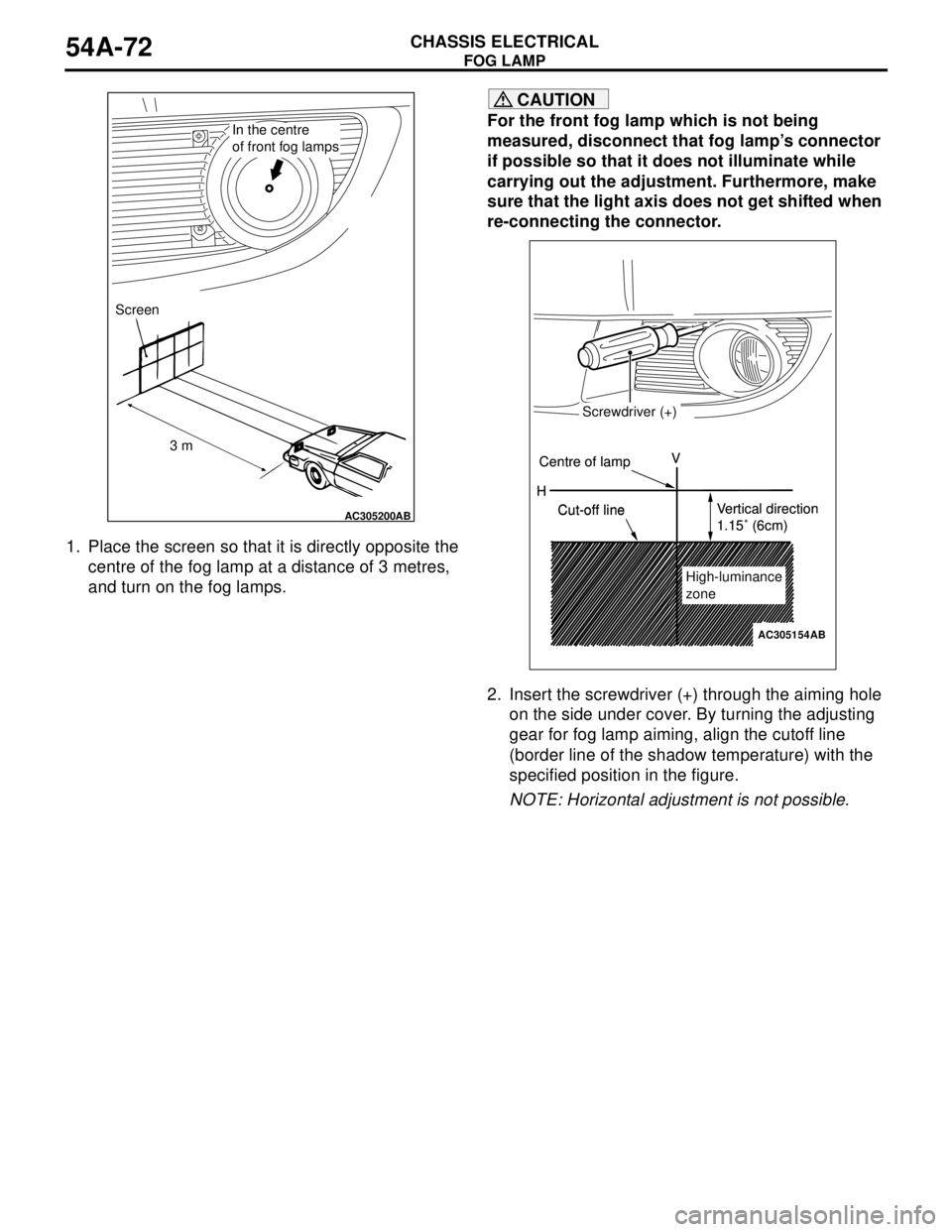
FOG LAMP
CHASSIS ELECTRICAL54A-72
1. Place the screen so that it is directly opposite the
centre of the fog lamp at a distance of 3 metres,
and turn on the fog lamps.
CAUTION
For the front fog lamp which is not being
measured, disconnect that fog lamp’s connector
if possible so that it does not illuminate while
carrying out the adjustment. Furthermore, make
sure that the light axis does not get shifted when
re-connecting the connector.
2. Insert the screwdriver (+) through the aiming hole
on the side under cover. By turning the adjusting
gear for fog lamp aiming, align the cutoff line
(border line of the shadow temperature) with the
specified position in the figure.
NOTE: Horizontal adjustment is not possible.
AC305200AB
In the centre
of front fog lamps
Screen
3 m
H V
AC305154
Screwdriver (+)
Centre of lamp
Cut-off lineVertical direction
1.15˚ (6cm)
High-luminance
zone H V
Screwdriver (+)
Centre of lamp
Cut-off lineVertical direction
1.15˚ (6cm)
High-luminance
zone
AB
Page 576 of 788
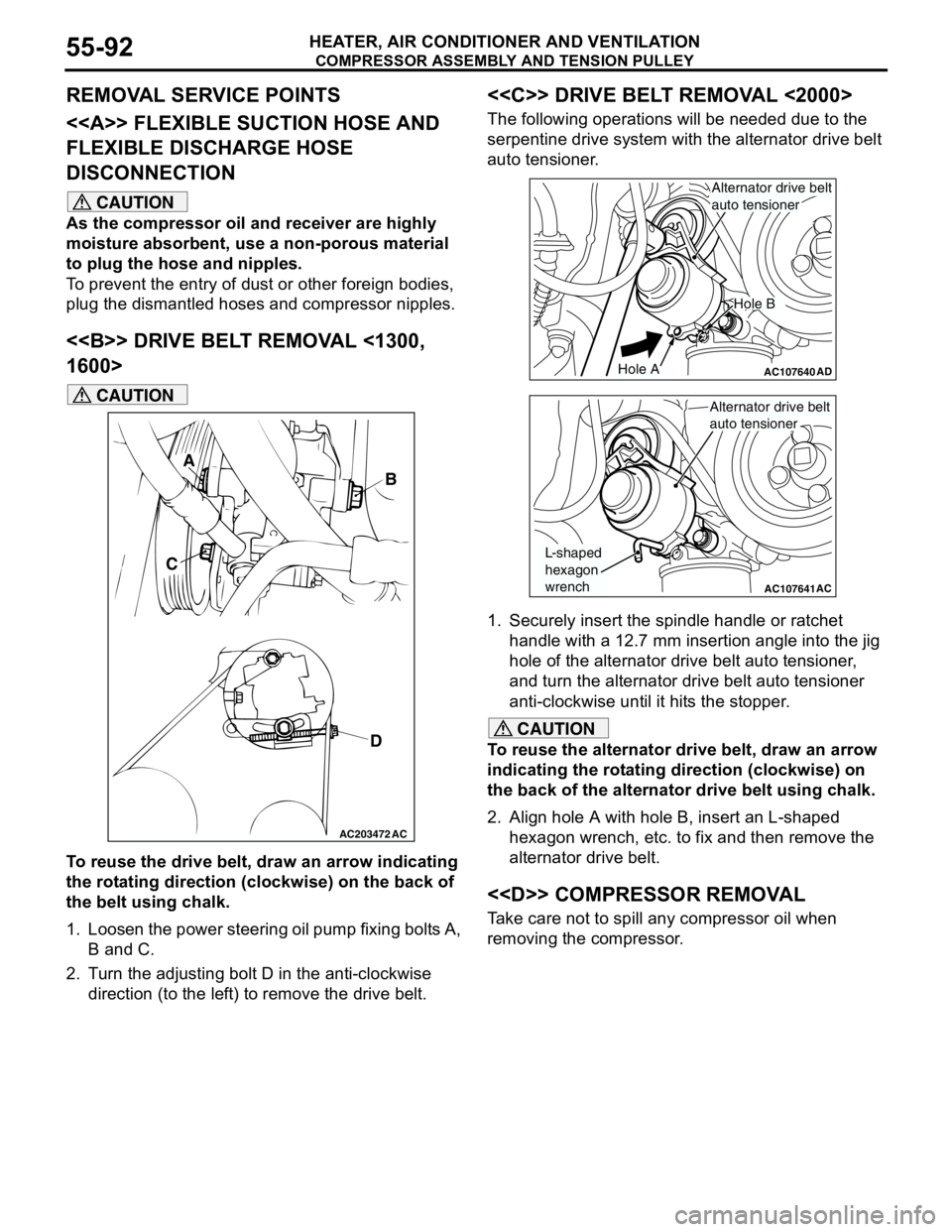