check engine light MITSUBISHI LANCER EVOLUTION VI 1999 User Guide
[x] Cancel search | Manufacturer: MITSUBISHI, Model Year: 1999, Model line: LANCER EVOLUTION VI, Model: MITSUBISHI LANCER EVOLUTION VI 1999Pages: 558, PDF Size: 9.73 MB
Page 176 of 558
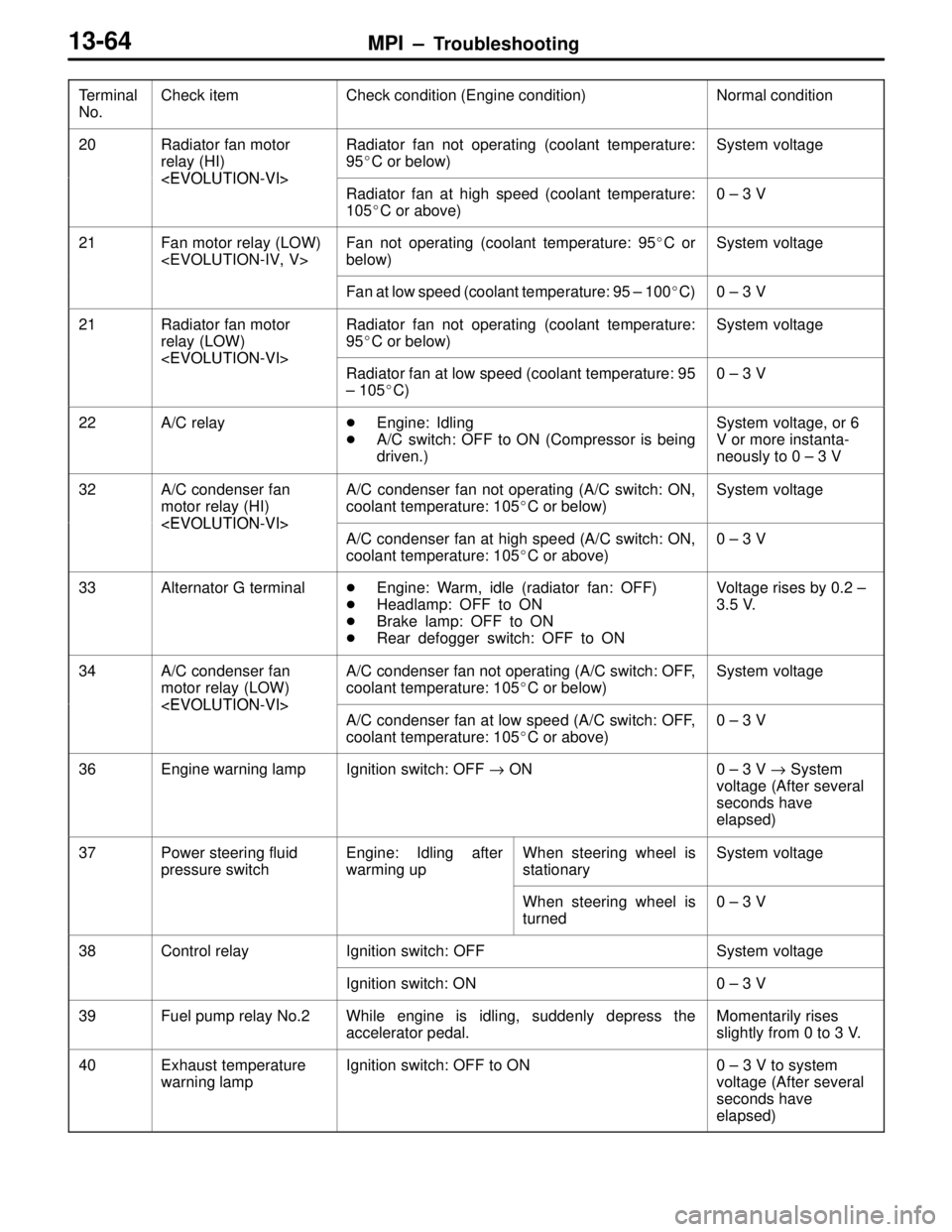
MPI – Troubleshooting13-64
Terminal
No.Normal condition Check condition (Engine condition) Check item
20Radiator fan motor
relay (HI)
Radiator fan not operating (coolant temperature:
95C or below)System voltage
105C or above)0 – 3 V
21Fan motor relay (LOW)
below)System voltage
Fan at low speed (coolant temperature: 95 – 100C)0 – 3 V
21Radiator fan motor
relay (LOW)
Radiator fan not operating (coolant temperature:
95C or below)System voltage
– 105C)0 – 3 V
22A/C relayEngine: Idling
A/C switch: OFF to ON (Compressor is being
driven.)System voltage, or 6
V or more instanta-
neously to 0 – 3 V
32A/C condenser fan
motor relay (HI)
A/C condenser fan not operating (A/C switch: ON,
coolant temperature: 105C or below)System voltage
coolant temperature: 105C or above)0 – 3 V
33Alternator G terminalEngine: Warm, idle (radiator fan: OFF)
Headlamp: OFF to ON
Brake lamp: OFF to ON
Rear defogger switch: OFF to ONVoltage rises by 0.2 –
3.5 V.
34A/C condenser fan
motor relay (LOW)
A/C condenser fan not operating (A/C switch: OFF,
coolant temperature: 105C or below)System voltage
coolant temperature: 105C or above)0 – 3 V
36Engine warning lampIgnition switch: OFF → ON0 – 3 V → System
voltage (After several
seconds have
elapsed)
37Power steering fluid
pressure switchEngine: Idling after
warming upWhen steering wheel is
stationarySystem voltage
When steering wheel is
turned0 – 3 V
38Control relayIgnition switch: OFFSystem voltage
Ignition switch: ON0 – 3 V
39Fuel pump relay No.2While engine is idling, suddenly depress the
accelerator pedal.Momentarily rises
slightly from 0 to 3 V.
40Exhaust temperature
warning lampIgnition switch: OFF to ON0 – 3 V to system
voltage (After several
seconds have
elapsed)
Page 178 of 558
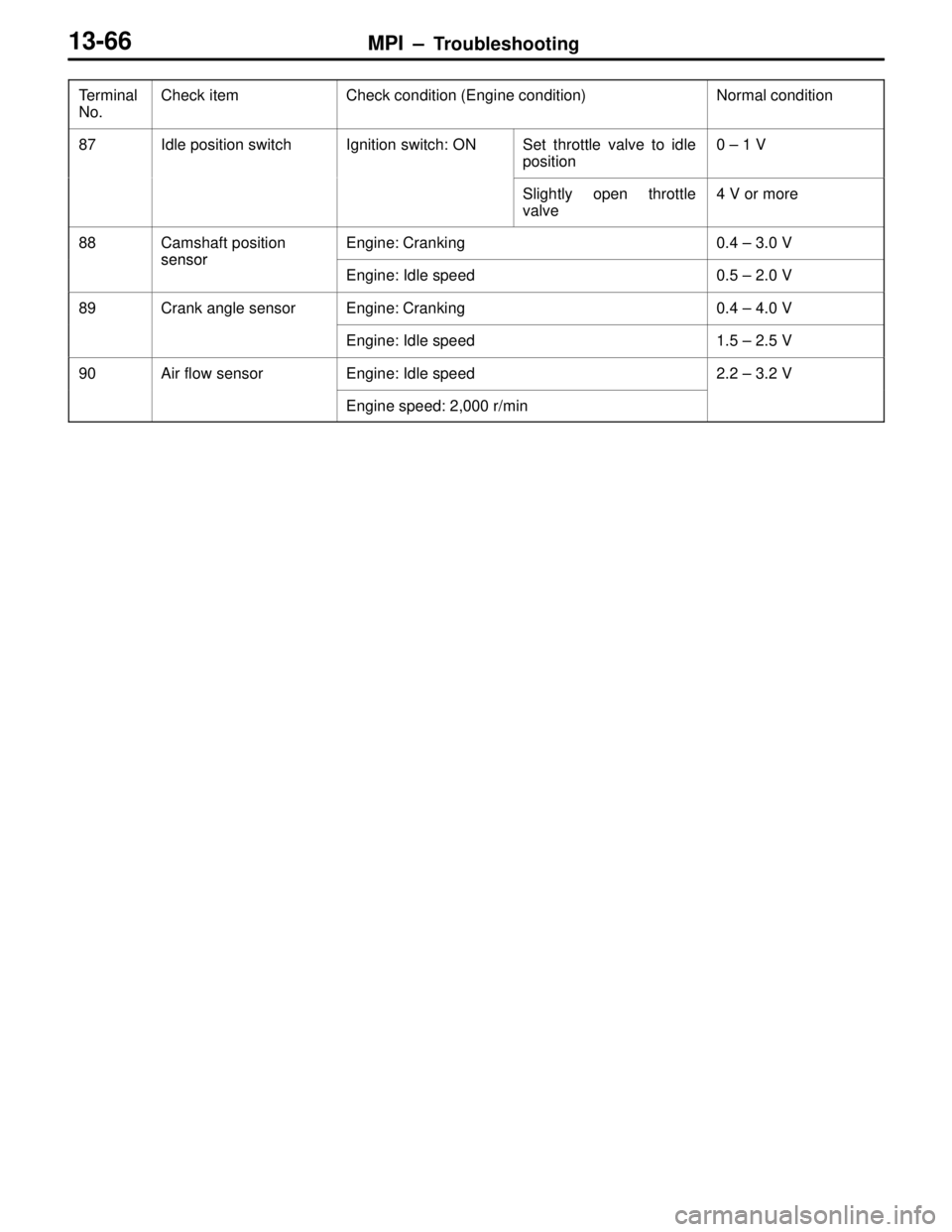
MPI – Troubleshooting13-66
Terminal
No.Normal condition Check condition (Engine condition) Check item
87Idle position switchIgnition switch: ONSet throttle valve to idle
position0 – 1 V
Slightly open throttle
valve4 V or more
88Camshaft position
sensor
Engine: Cranking0.4 – 3.0 V
sensor
Engine: Idle speed0.5 – 2.0 V
89Crank angle sensorEngine: Cranking0.4 – 4.0 V
Engine: Idle speed1.5 – 2.5 V
90Air flow sensorEngine: Idle speed2.2 – 3.2 V
Engine speed: 2,000 r/min
Page 179 of 558
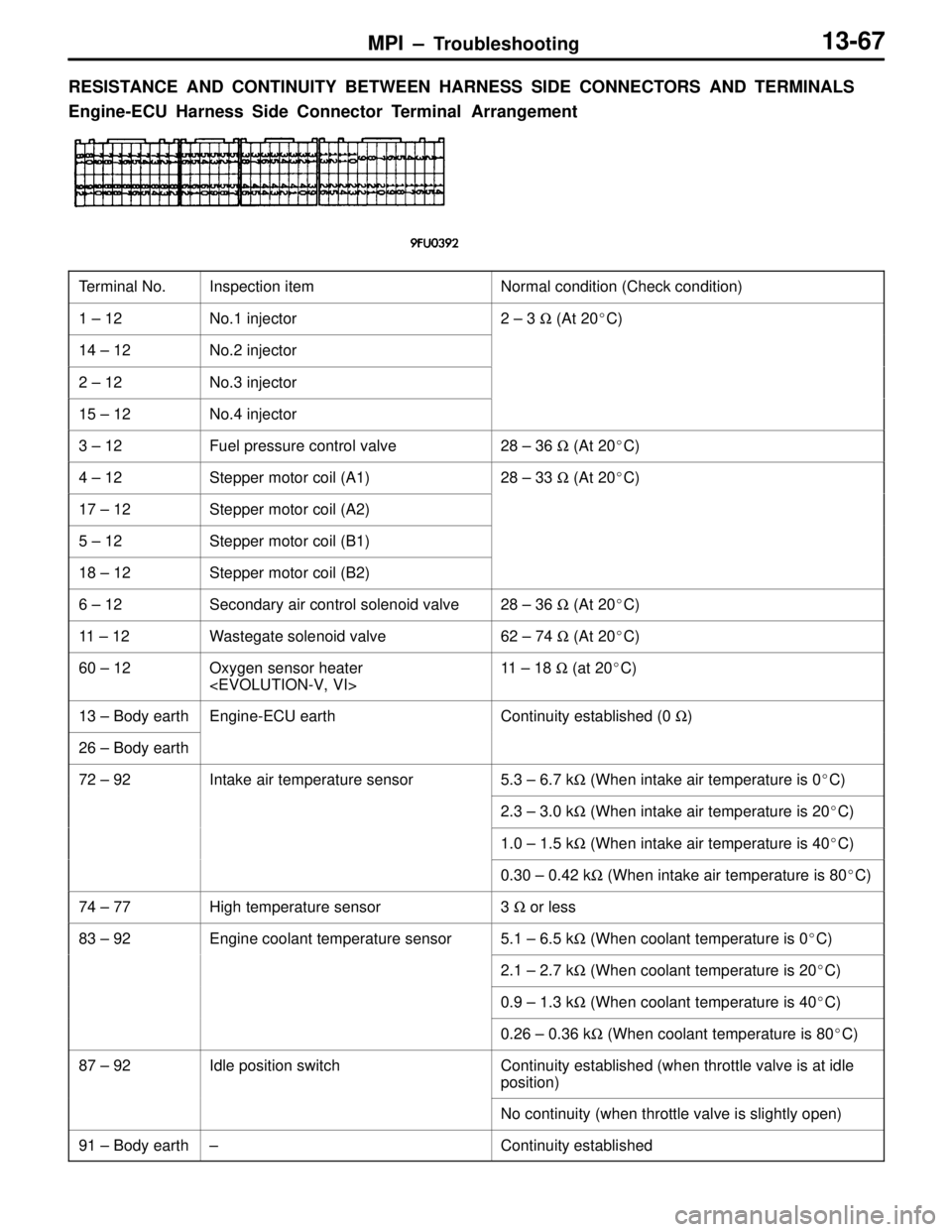
MPI – Troubleshooting13-67
RESISTANCE AND CONTINUITY BETWEEN HARNESS SIDE CONNECTORS AND TERMINALS
Engine-ECU Harness Side Connector Terminal Arrangement
Terminal No.Inspection itemNormal condition (Check condition)
1 – 12No.1 injector2 – 3 Ω (At 20C)
14 – 12No.2 injector
2 – 12No.3 injector
15 – 12No.4 injector
3 – 12Fuel pressure control valve28 – 36 Ω (At 20C)
4 – 12Stepper motor coil (A1)28 – 33 Ω (At 20C)
17 – 12Stepper motor coil (A2)
5 – 12Stepper motor coil (B1)
18 – 12Stepper motor coil (B2)
6 – 12Secondary air control solenoid valve28 – 36 Ω (At 20C)
11 – 12Wastegate solenoid valve62 – 74 Ω (At 20C)
60 – 12Oxygen sensor heater
13 – Body earthEngine-ECU earthContinuity established (0 Ω)
26 – Body earth
72 – 92Intake air temperature sensor5.3 – 6.7 kΩ (When intake air temperature is 0C)
2.3 – 3.0 kΩ (When intake air temperature is 20C)
1.0 – 1.5 kΩ (When intake air temperature is 40C)
0.30 – 0.42 kΩ (When intake air temperature is 80C)
74 – 77High temperature sensor3 Ω or less
83 – 92Engine coolant temperature sensor5.1 – 6.5 kΩ (When coolant temperature is 0C)
2.1 – 2.7 kΩ (When coolant temperature is 20C)
0.9 – 1.3 kΩ (When coolant temperature is 40C)
0.26 – 0.36 kΩ (When coolant temperature is 80C)
87 – 92Idle position switchContinuity established (when throttle valve is at idle
position)
No continuity (when throttle valve is slightly open)
91 – Body earth–Continuity established
Page 216 of 558
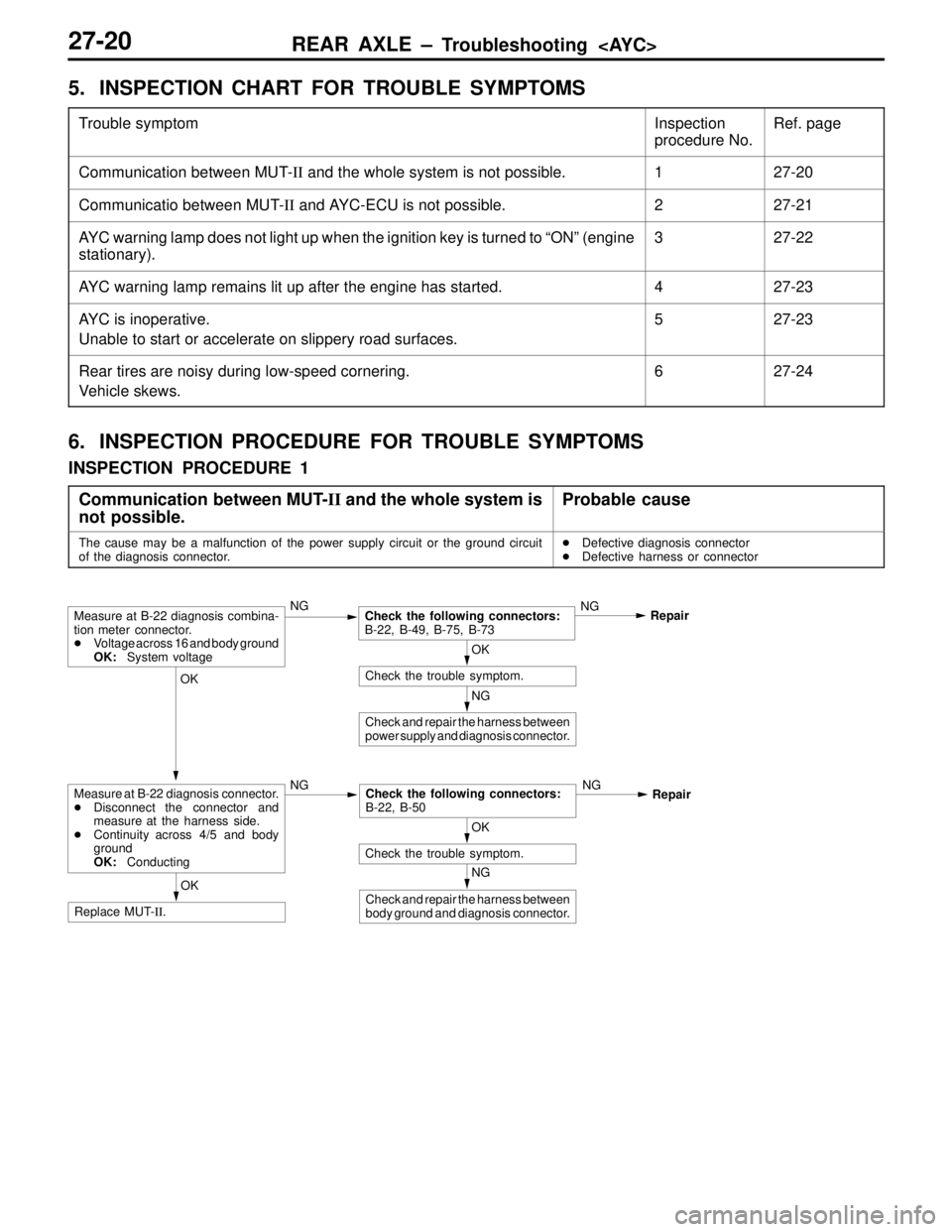
REAR AXLE – Troubleshooting
5. INSPECTION CHART FOR TROUBLE SYMPTOMS
Trouble symptomInspection
procedure No.Ref. page
Communication between MUT-II and the whole system is not possible.127-20
Communicatio between MUT-II and AYC-ECU is not possible.227-21
AYC warning lamp does not light up when the ignition key is turned to “ON” (engine
stationary).327-22
AYC warning lamp remains lit up after the engine has started.427-23
AYC is inoperative.
Unable to start or accelerate on slippery road surfaces.527-23
Rear tires are noisy during low-speed cornering.
Vehicle skews.627-24
6. INSPECTION PROCEDURE FOR TROUBLE SYMPTOMS
INSPECTION PROCEDURE 1
Communication between MUT-II and the whole system is
not possible.
Probable cause
The cause may be a malfunction of the power supply circuit or the ground circuit
of the diagnosis connector.Defective diagnosis connector
Defective harness or connector
NG
Check and repair the harness between
power supply and diagnosis connector.
OK
Check the trouble symptom.
NG
Check and repair the harness between
body ground and diagnosis connector.
OK
Check the trouble symptom.
OK
Replace MUT-II.
Check the following connectors:
B-22, B-50NG
Repair
OK
Measure at B-22 diagnosis connector.
Disconnect the connector and
measure at the harness side.
Continuity across 4/5 and body
ground
OK:ConductingNG
Measure at B-22 diagnosis combina-
tion meter connector.
Voltage across 16 and body ground
OK:System voltageNGCheck the following connectors:
B-22, B-49, B-75, B-73NG
Repair
Page 218 of 558
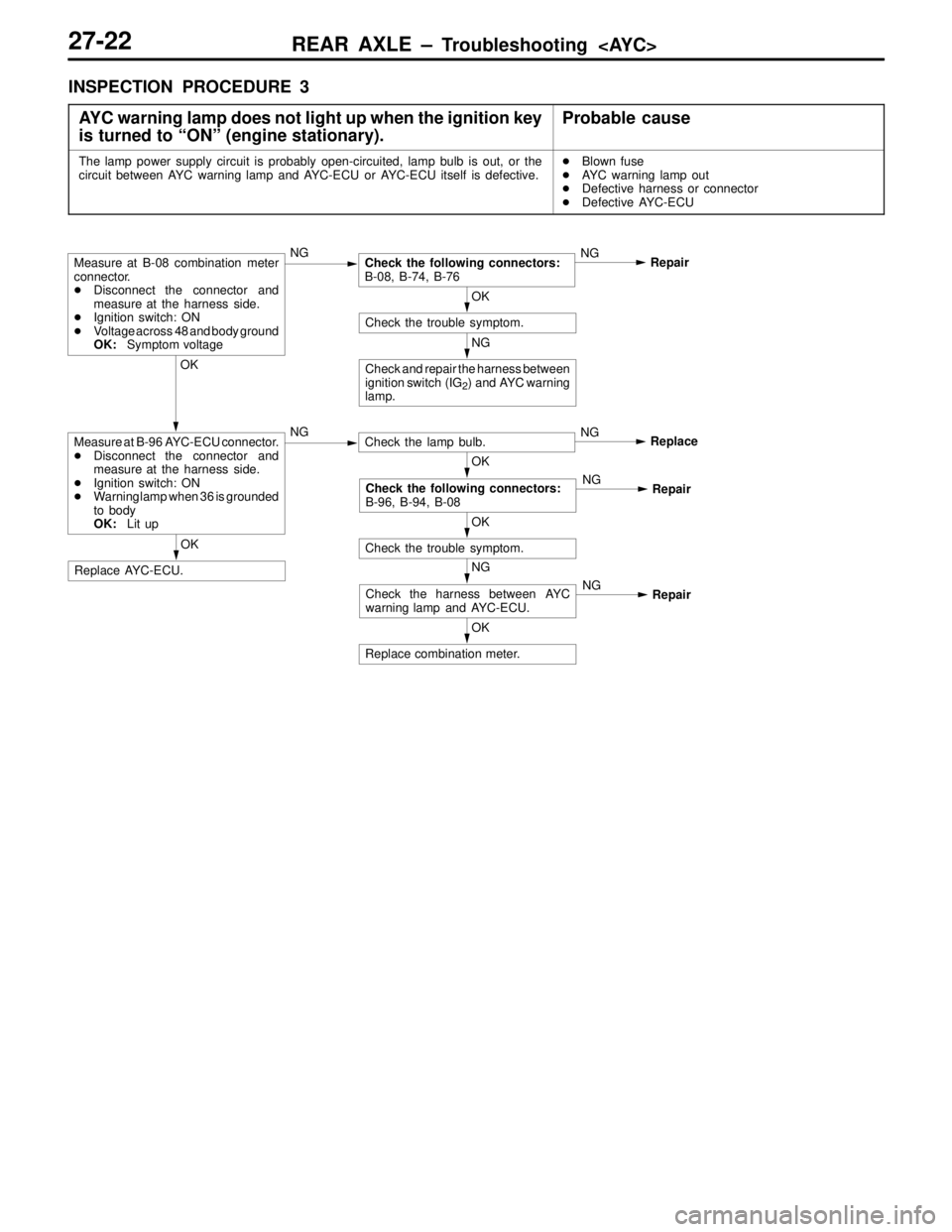
REAR AXLE – Troubleshooting
INSPECTION PROCEDURE 3
AYC warning lamp does not light up when the ignition key
is turned to “ON” (engine stationary).
Probable cause
The lamp power supply circuit is probably open-circuited, lamp bulb is out, or the
circuit between AYC warning lamp and AYC-ECU or AYC-ECU itself is defective.Blown fuse
AYC warning lamp out
Defective harness or connector
Defective AYC-ECU
NG
Check and repair the harness between
ignition switch (IG
2) and AYC warning
lamp.
OK
Check the trouble symptom.
OK
Replace combination meter.
NG
Check the harness between AYC
warning lamp and AYC-ECU.NG
Repair
OK
Check the trouble symptom.OK
Replace AYC-ECU.
OK
Check the following connectors:
B-96, B-94, B-08NG
Repair
OK
Measure at B-96 AYC-ECU connector.
Disconnect the connector and
measure at the harness side.
Ignition switch: ON
Warning lamp when 36 is grounded
to body
OK:Lit upNGCheck the lamp bulb.NG
Replace
Measure at B-08 combination meter
connector.
Disconnect the connector and
measure at the harness side.
Ignition switch: ON
Voltage across 48 and body ground
OK:Symptom voltageNGCheck the following connectors:
B-08, B-74, B-76NG
Repair
Page 234 of 558
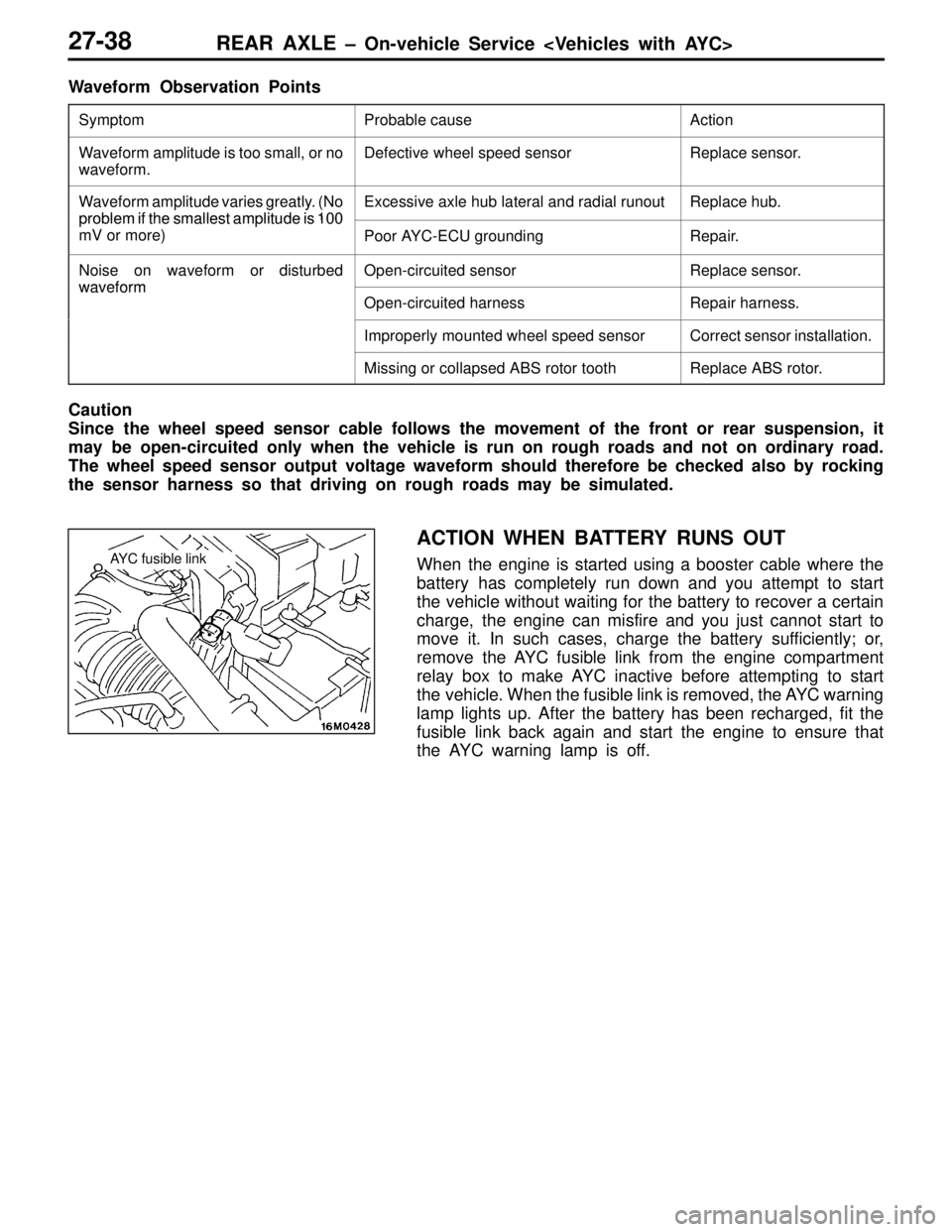
REAR AXLE – On-vehicle Service
Waveform Observation Points
SymptomProbable causeAction
Waveform amplitude is too small, or no
waveform.Defective wheel speed sensorReplace sensor.
Waveform amplitude varies greatly. (No
problem ifthe smallest amplitude is 100
Excessive axle hub lateral and radial runoutReplace hub.
problem if the smallest amplitude is 100
mV or more)Poor AYC-ECU groundingRepair.
Noise on waveform or disturbed
waveform
Open-circuited sensorReplace sensor.
waveform
Open-circuited harnessRepair harness.
Improperly mounted wheel speed sensorCorrect sensor installation.
Missing or collapsed ABS rotor toothReplace ABS rotor.
Caution
Since the wheel speed sensor cable follows the movement of the front or rear suspension, it
may be open-circuited only when the vehicle is run on rough roads and not on ordinary road.
The wheel speed sensor output voltage waveform should therefore be checked also by rocking
the sensor harness so that driving on rough roads may be simulated.
ACTION WHEN BATTERY RUNS OUT
When the engine is started using a booster cable where the
battery has completely run down and you attempt to start
the vehicle without waiting for the battery to recover a certain
charge, the engine can misfire and you just cannot start to
move it. In such cases, charge the battery sufficiently; or,
remove the AYC fusible link from the engine compartment
relay box to make AYC inactive before attempting to start
the vehicle. When the fusible link is removed, the AYC warning
lamp lights up. After the battery has been recharged, fit the
fusible link back again and start the engine to ensure that
the AYC warning lamp is off.AYC fusible link
Page 373 of 558
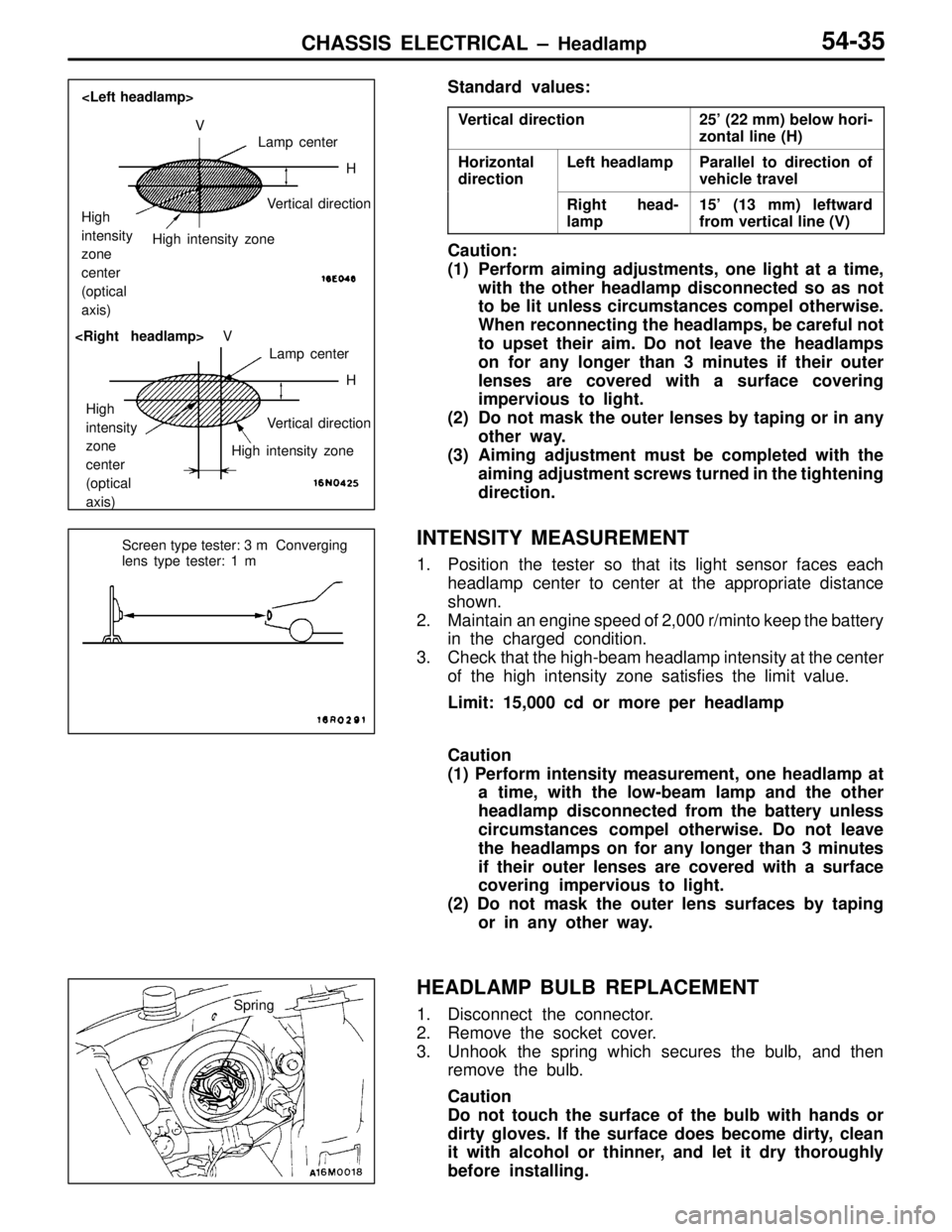
CHASSIS ELECTRICAL – Headlamp54-35
Standard values:
Vertical direction25’ (22 mm) below hori-
zontal line (H)
Horizontal
directionLeft headlampParallel to direction of
vehicle travel
Right head-
lamp15’ (13 mm) leftward
from vertical line (V)
Caution:
(1) Perform aiming adjustments, one light at a time,
with the other headlamp disconnected so as not
to be lit unless circumstances compel otherwise.
When reconnecting the headlamps, be careful not
to upset their aim. Do not leave the headlamps
on for any longer than 3 minutes if their outer
lenses are covered with a surface covering
impervious to light.
(2) Do not mask the outer lenses by taping or in any
other way.
(3) Aiming adjustment must be completed with the
aiming adjustment screws turned in the tightening
direction.
INTENSITY MEASUREMENT
1. Position the tester so that its light sensor faces each
headlamp center to center at the appropriate distance
shown.
2. Maintain an engine speed of 2,000 r/minto keep the battery
in the charged condition.
3. Check that the high-beam headlamp intensity at the center
of the high intensity zone satisfies the limit value.
Limit: 15,000 cd or more per headlamp
Caution
(1) Perform intensity measurement, one headlamp at
a time, with the low-beam lamp and the other
headlamp disconnected from the battery unless
circumstances compel otherwise. Do not leave
the headlamps on for any longer than 3 minutes
if their outer lenses are covered with a surface
covering impervious to light.
(2) Do not mask the outer lens surfaces by taping
or in any other way.
HEADLAMP BULB REPLACEMENT
1. Disconnect the connector.
2. Remove the socket cover.
3. Unhook the spring which secures the bulb, and then
remove the bulb.
Caution
Do not touch the surface of the bulb with hands or
dirty gloves. If the surface does become dirty, clean
it with alcohol or thinner, and let it dry thoroughly
before installing.
Lamp center
Vertical direction
Vertical direction High
intensity
zone
center
(optical
axis)
High
intensity
zone
center
(optical
axis)High intensity zone
High intensity zoneLamp center
H
V
H
Screen type tester: 3 m Converging
lens type tester: 1 m
Spring
Page 399 of 558
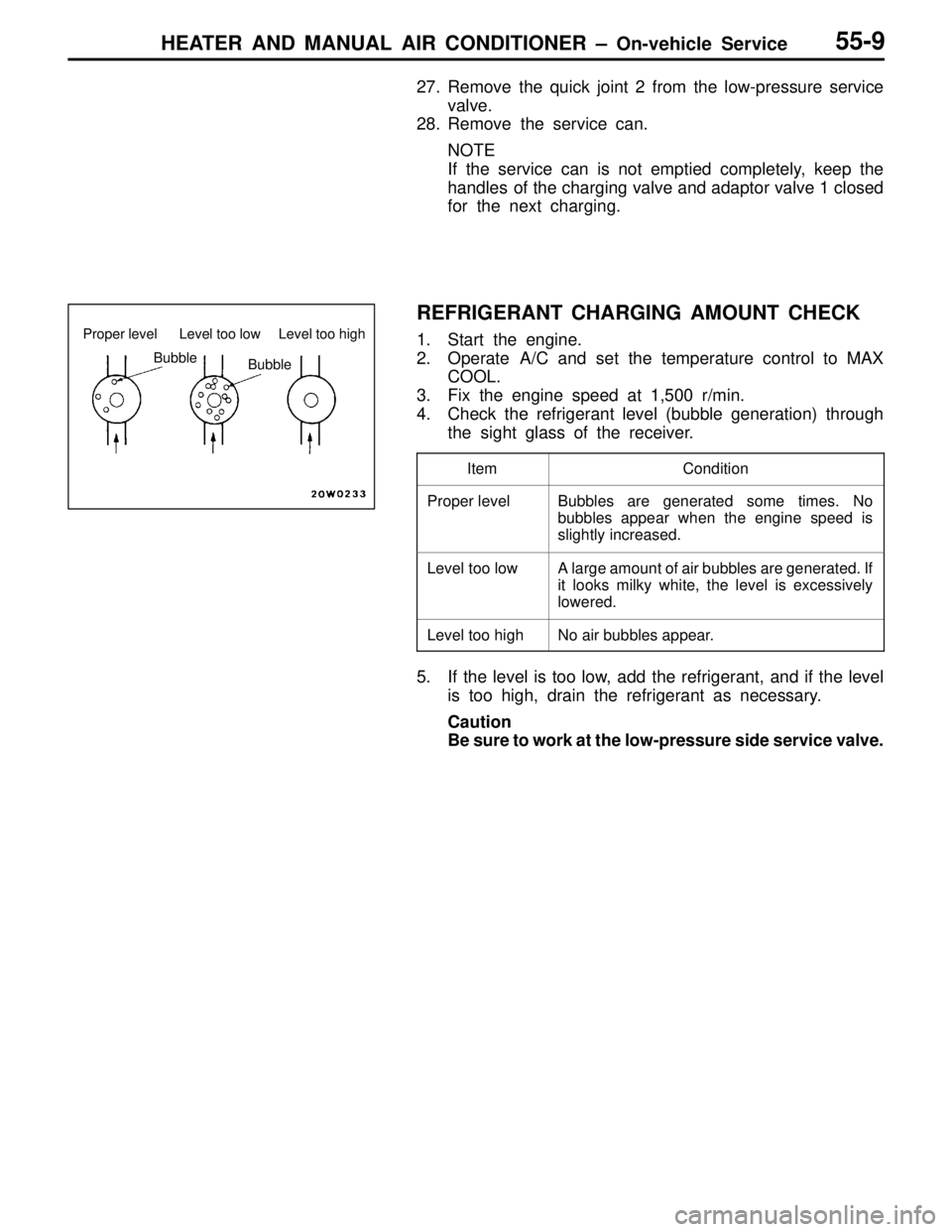
HEATER AND MANUAL AIR CONDITIONER – On-vehicle Service55-9
27. Remove the quick joint 2 from the low-pressure service
valve.
28. Remove the service can.
NOTE
If the service can is not emptied completely, keep the
handles of the charging valve and adaptor valve 1 closed
for the next charging.
REFRIGERANT CHARGING AMOUNT CHECK
1. Start the engine.
2. Operate A/C and set the temperature control to MAX
COOL.
3. Fix the engine speed at 1,500 r/min.
4. Check the refrigerant level (bubble generation) through
the sight glass of the receiver.
ItemCondition
Proper levelBubbles are generated some times. No
bubbles appear when the engine speed is
slightly increased.
Level too lowA large amount of air bubbles are generated. If
it looks milky white, the level is excessively
lowered.
Level too highNo air bubbles appear.
5. If the level is too low, add the refrigerant, and if the level
is too high, drain the refrigerant as necessary.
Caution
Be sure to work at the low-pressure side service valve.
Proper level Level too low Level too high
Bubble Bubble