NISSAN ALMERA 2001 Service Manual
Manufacturer: NISSAN, Model Year: 2001, Model line: ALMERA, Model: NISSAN ALMERA 2001Pages: 2898, PDF Size: 60.76 MB
Page 441 of 2898
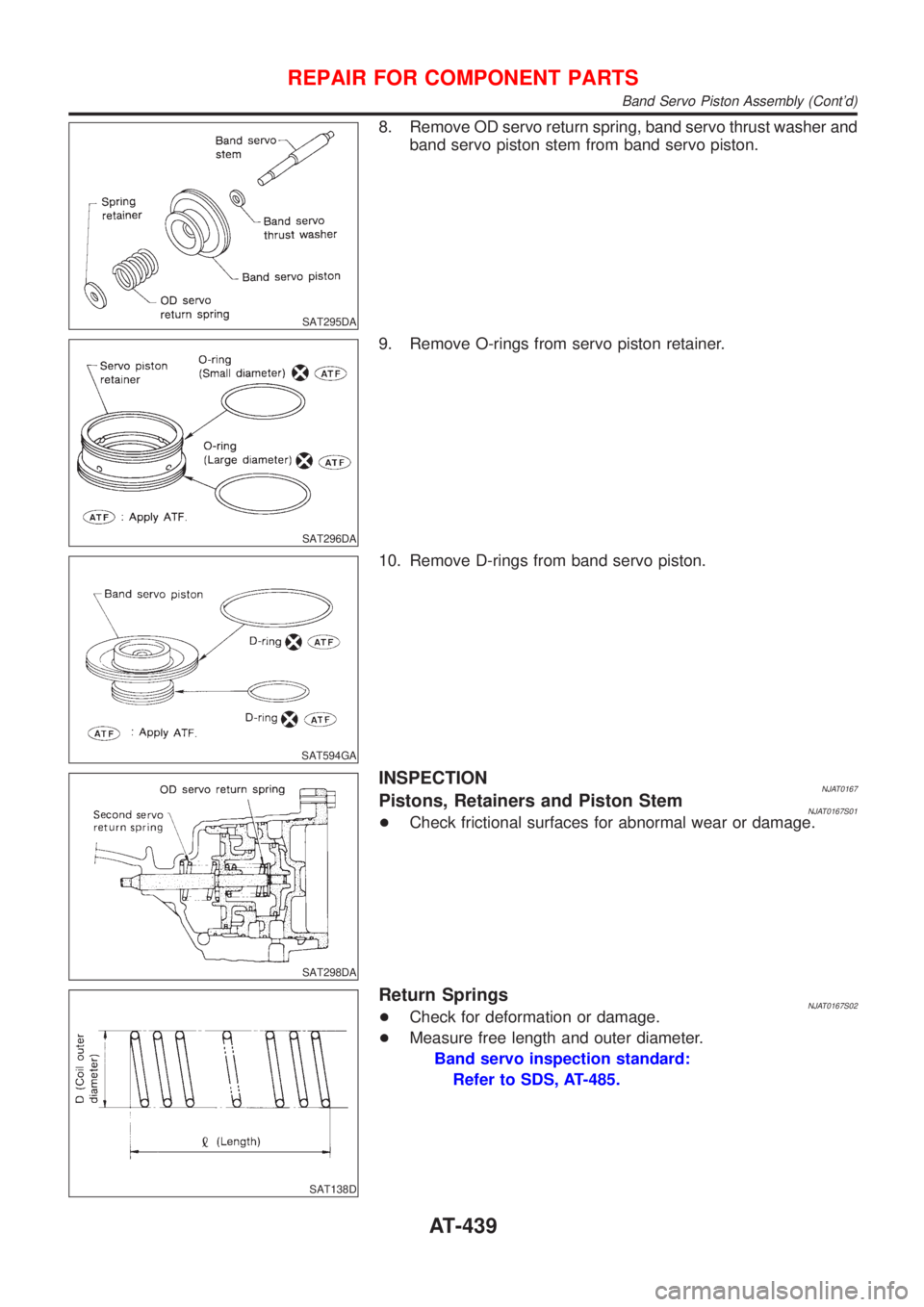
SAT295DA
8. Remove OD servo return spring, band servo thrust washer and
band servo piston stem from band servo piston.
SAT296DA
9. Remove O-rings from servo piston retainer.
SAT594GA
10. Remove D-rings from band servo piston.
SAT298DA
INSPECTIONNJAT0167Pistons, Retainers and Piston StemNJAT0167S01+Check frictional surfaces for abnormal wear or damage.
SAT138D
Return SpringsNJAT0167S02+Check for deformation or damage.
+Measure free length and outer diameter.
Band servo inspection standard:
Refer to SDS, AT-485.
REPAIR FOR COMPONENT PARTS
Band Servo Piston Assembly (Cont'd)
AT-439
Page 442 of 2898
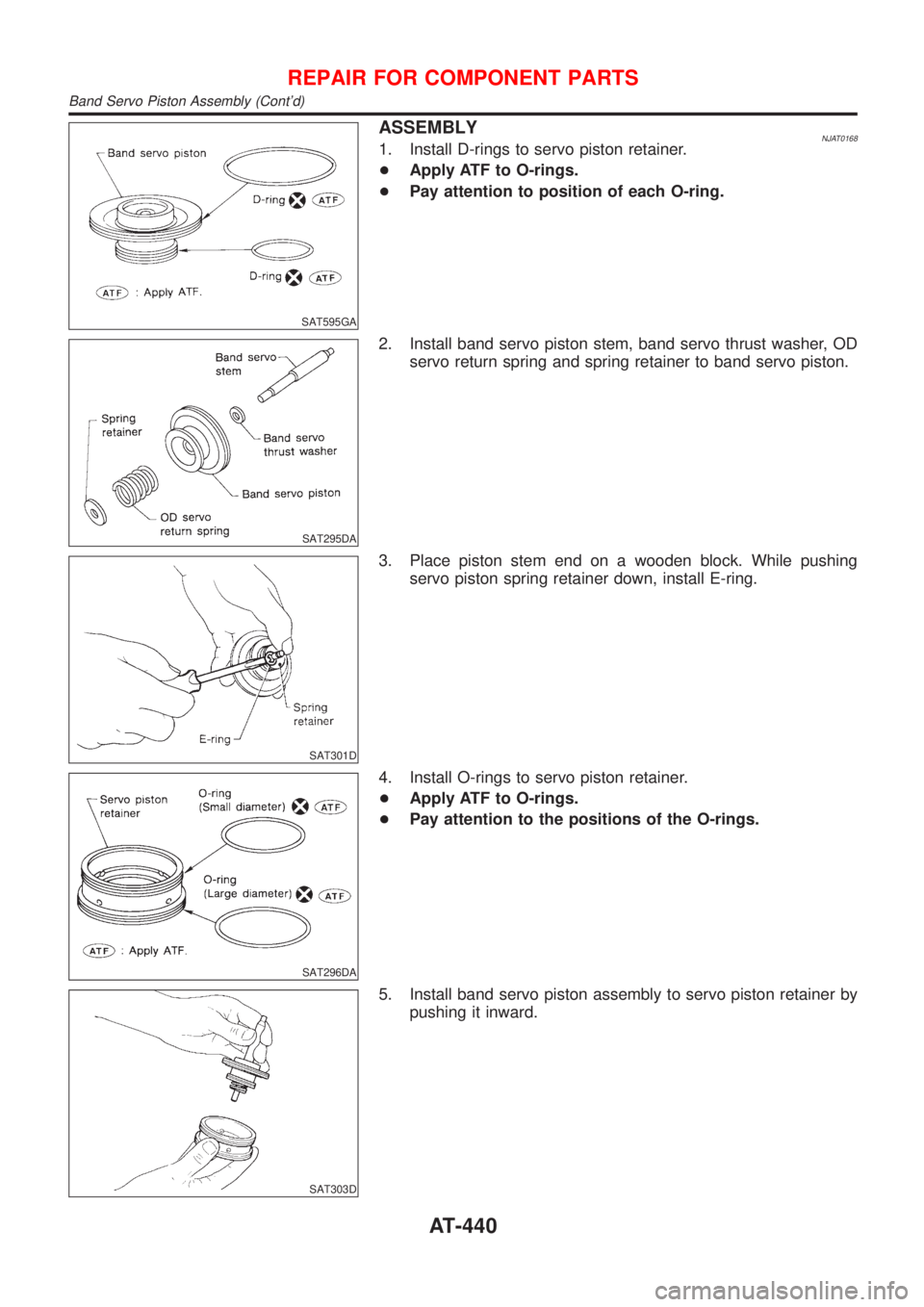
SAT595GA
ASSEMBLYNJAT01681. Install D-rings to servo piston retainer.
+Apply ATF to O-rings.
+Pay attention to position of each O-ring.
SAT295DA
2. Install band servo piston stem, band servo thrust washer, OD
servo return spring and spring retainer to band servo piston.
SAT301D
3. Place piston stem end on a wooden block. While pushing
servo piston spring retainer down, install E-ring.
SAT296DA
4. Install O-rings to servo piston retainer.
+Apply ATF to O-rings.
+Pay attention to the positions of the O-rings.
SAT303D
5. Install band servo piston assembly to servo piston retainer by
pushing it inward.
REPAIR FOR COMPONENT PARTS
Band Servo Piston Assembly (Cont'd)
AT-440
Page 443 of 2898
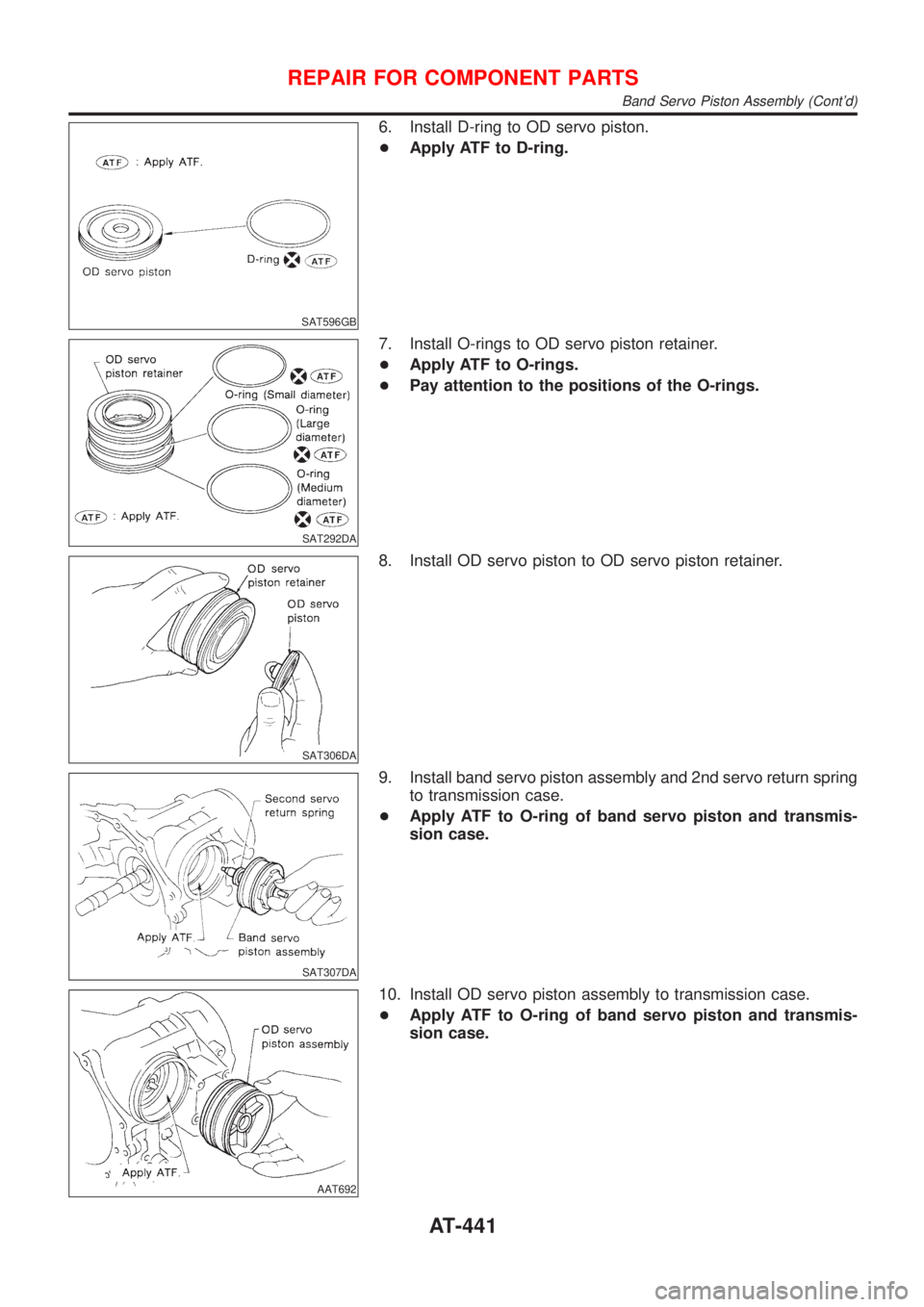
SAT596GB
6. Install D-ring to OD servo piston.
+Apply ATF to D-ring.
SAT292DA
7. Install O-rings to OD servo piston retainer.
+Apply ATF to O-rings.
+Pay attention to the positions of the O-rings.
SAT306DA
8. Install OD servo piston to OD servo piston retainer.
SAT307DA
9. Install band servo piston assembly and 2nd servo return spring
to transmission case.
+Apply ATF to O-ring of band servo piston and transmis-
sion case.
AAT692
10. Install OD servo piston assembly to transmission case.
+Apply ATF to O-ring of band servo piston and transmis-
sion case.
REPAIR FOR COMPONENT PARTS
Band Servo Piston Assembly (Cont'd)
AT-441
Page 444 of 2898
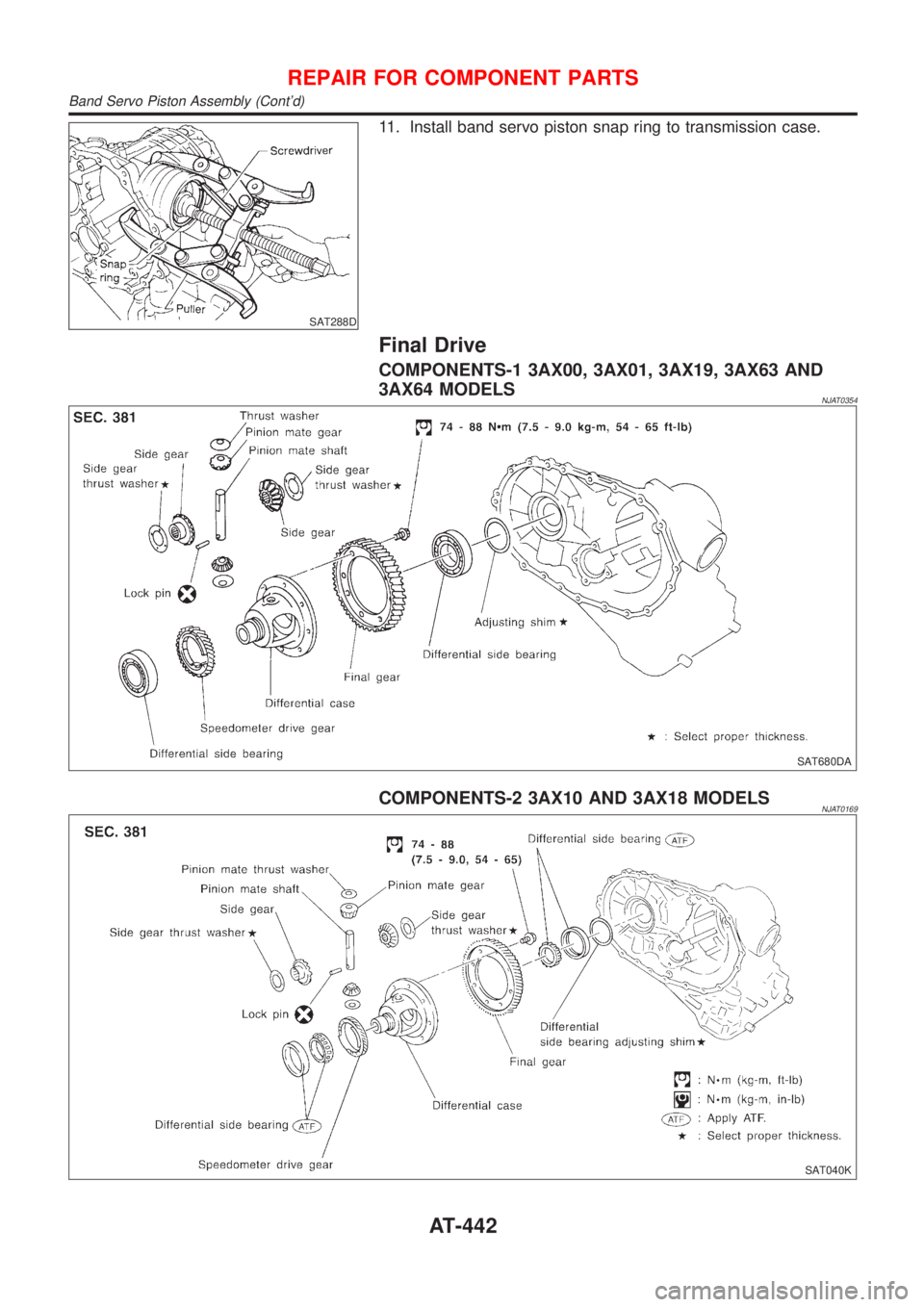
SAT288D
11. Install band servo piston snap ring to transmission case.
Final Drive
COMPONENTS-1 3AX00, 3AX01, 3AX19, 3AX63 AND
3AX64 MODELS
NJAT0354
SAT680DA
COMPONENTS-2 3AX10 AND 3AX18 MODELSNJAT0169
SAT040K
REPAIR FOR COMPONENT PARTS
Band Servo Piston Assembly (Cont'd)
AT-442
Page 445 of 2898
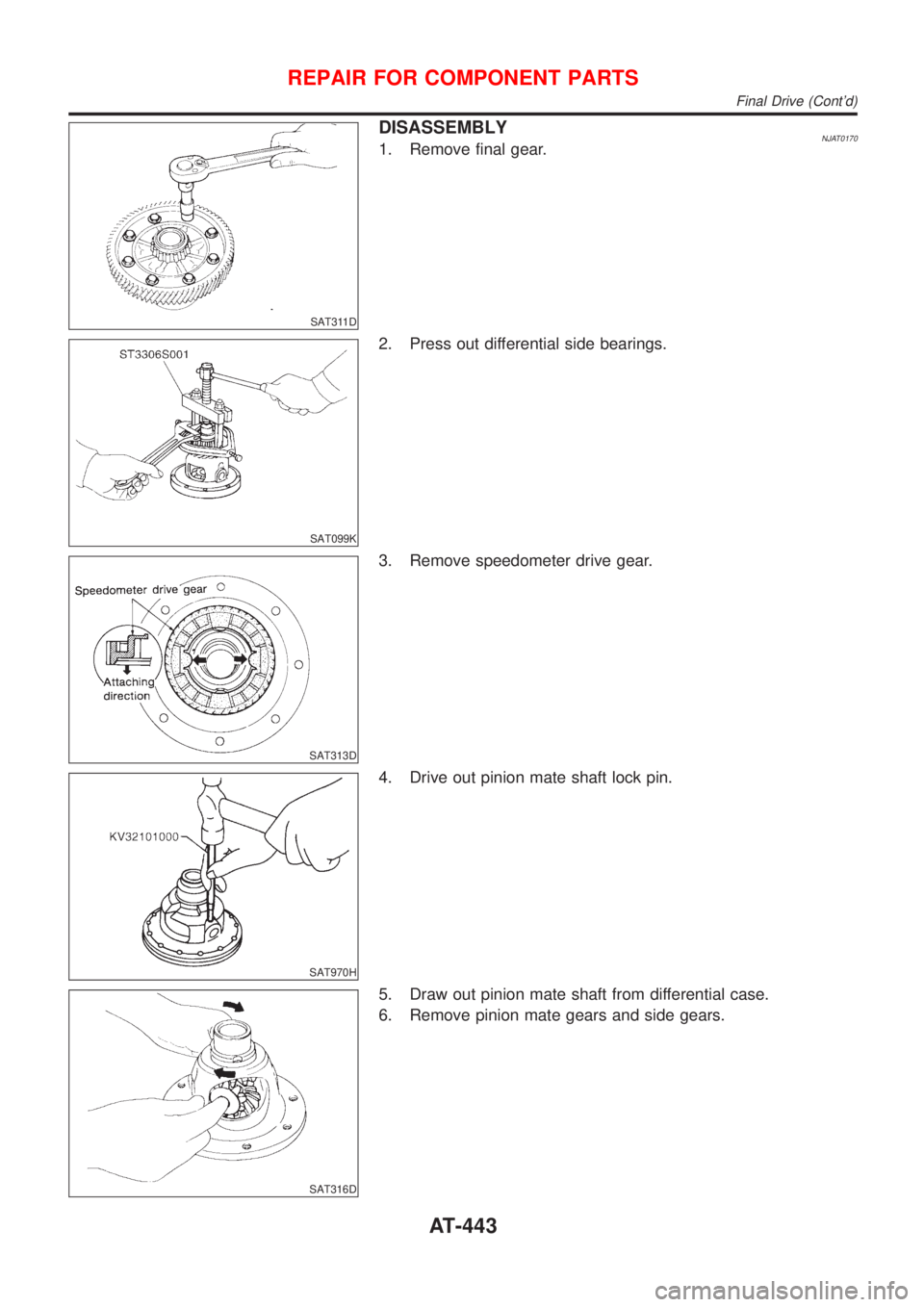
SAT311D
DISASSEMBLYNJAT01701. Remove final gear.
SAT099K
2. Press out differential side bearings.
SAT313D
3. Remove speedometer drive gear.
SAT970H
4. Drive out pinion mate shaft lock pin.
SAT316D
5. Draw out pinion mate shaft from differential case.
6. Remove pinion mate gears and side gears.
REPAIR FOR COMPONENT PARTS
Final Drive (Cont'd)
AT-443
Page 446 of 2898
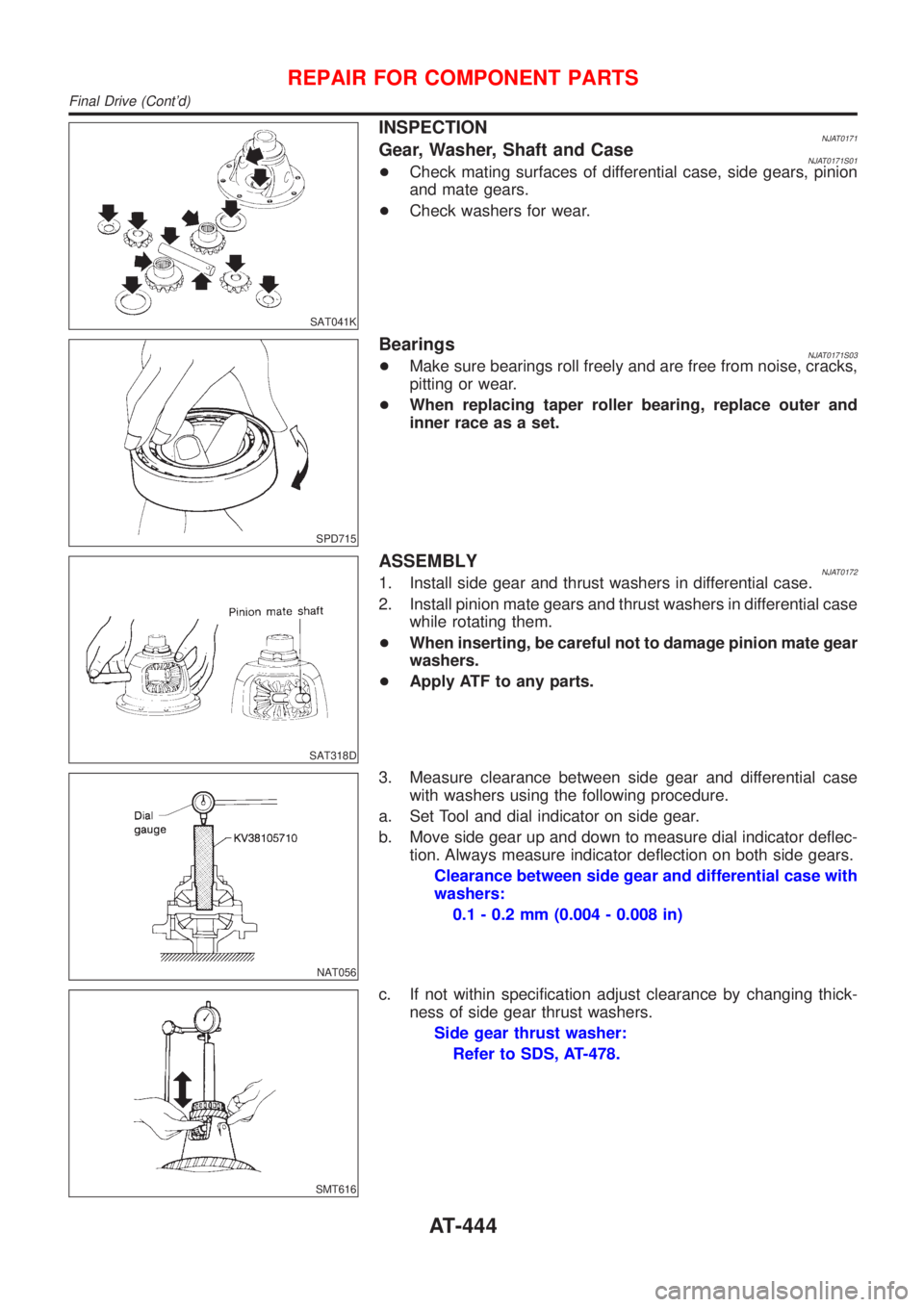
SAT041K
INSPECTIONNJAT0171Gear, Washer, Shaft and CaseNJAT0171S01+Check mating surfaces of differential case, side gears, pinion
and mate gears.
+Check washers for wear.
SPD715
BearingsNJAT0171S03+Make sure bearings roll freely and are free from noise, cracks,
pitting or wear.
+When replacing taper roller bearing, replace outer and
inner race as a set.
SAT318D
ASSEMBLYNJAT01721. Install side gear and thrust washers in differential case.
2. Install pinion mate gears and thrust washers in differential case
while rotating them.
+When inserting, be careful not to damage pinion mate gear
washers.
+Apply ATF to any parts.
NAT056
3. Measure clearance between side gear and differential case
with washers using the following procedure.
a. Set Tool and dial indicator on side gear.
b. Move side gear up and down to measure dial indicator deflec-
tion. Always measure indicator deflection on both side gears.
Clearance between side gear and differential case with
washers:
0.1 - 0.2 mm (0.004 - 0.008 in)
SMT616
c. If not within specification adjust clearance by changing thick-
ness of side gear thrust washers.
Side gear thrust washer:
Refer to SDS, AT-478.
REPAIR FOR COMPONENT PARTS
Final Drive (Cont'd)
AT-444
Page 447 of 2898
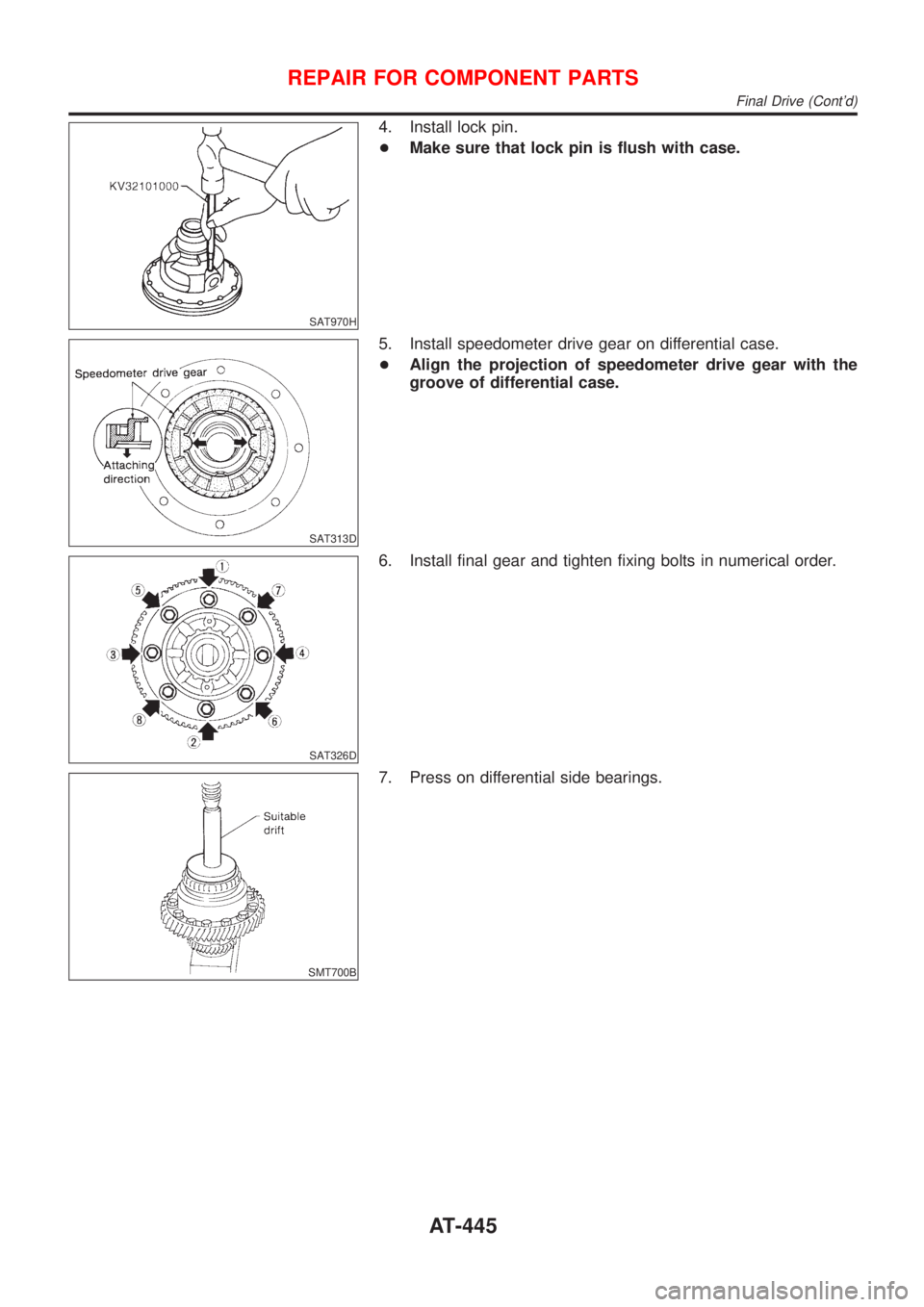
SAT970H
4. Install lock pin.
+Make sure that lock pin is flush with case.
SAT313D
5. Install speedometer drive gear on differential case.
+Align the projection of speedometer drive gear with the
groove of differential case.
SAT326D
6. Install final gear and tighten fixing bolts in numerical order.
SMT700B
7. Press on differential side bearings.
REPAIR FOR COMPONENT PARTS
Final Drive (Cont'd)
AT-445
Page 448 of 2898
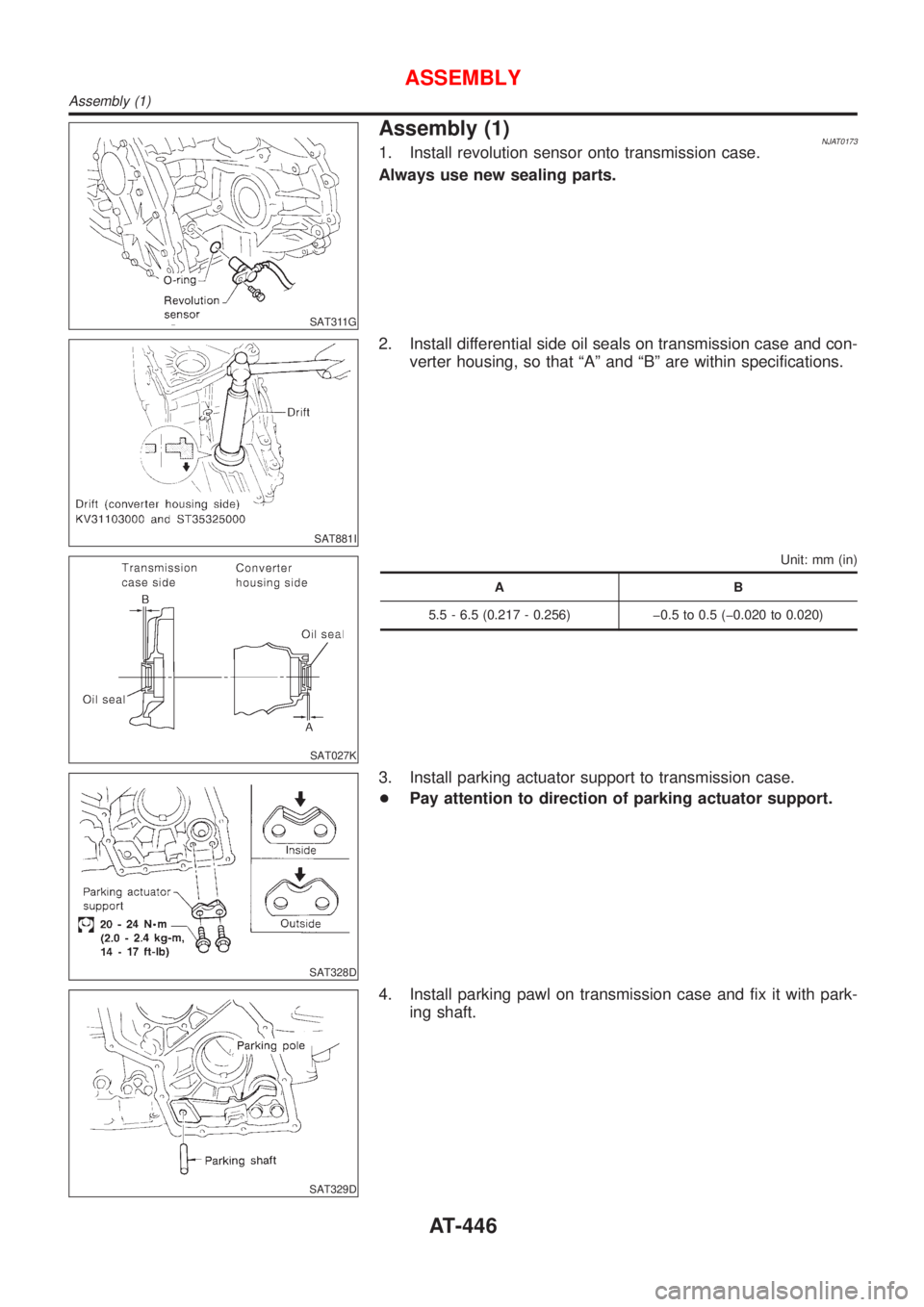
SAT311G
Assembly (1)NJAT01731. Install revolution sensor onto transmission case.
Always use new sealing parts.
SAT881I
2. Install differential side oil seals on transmission case and con-
verter housing, so that ªAº and ªBº are within specifications.
SAT027K
Unit: mm (in)
AB
5.5 - 6.5 (0.217 - 0.256) þ0.5 to 0.5 (þ0.020 to 0.020)
SAT328D
3. Install parking actuator support to transmission case.
+Pay attention to direction of parking actuator support.
SAT329D
4. Install parking pawl on transmission case and fix it with park-
ing shaft.
ASSEMBLY
Assembly (1)
AT-446
Page 449 of 2898
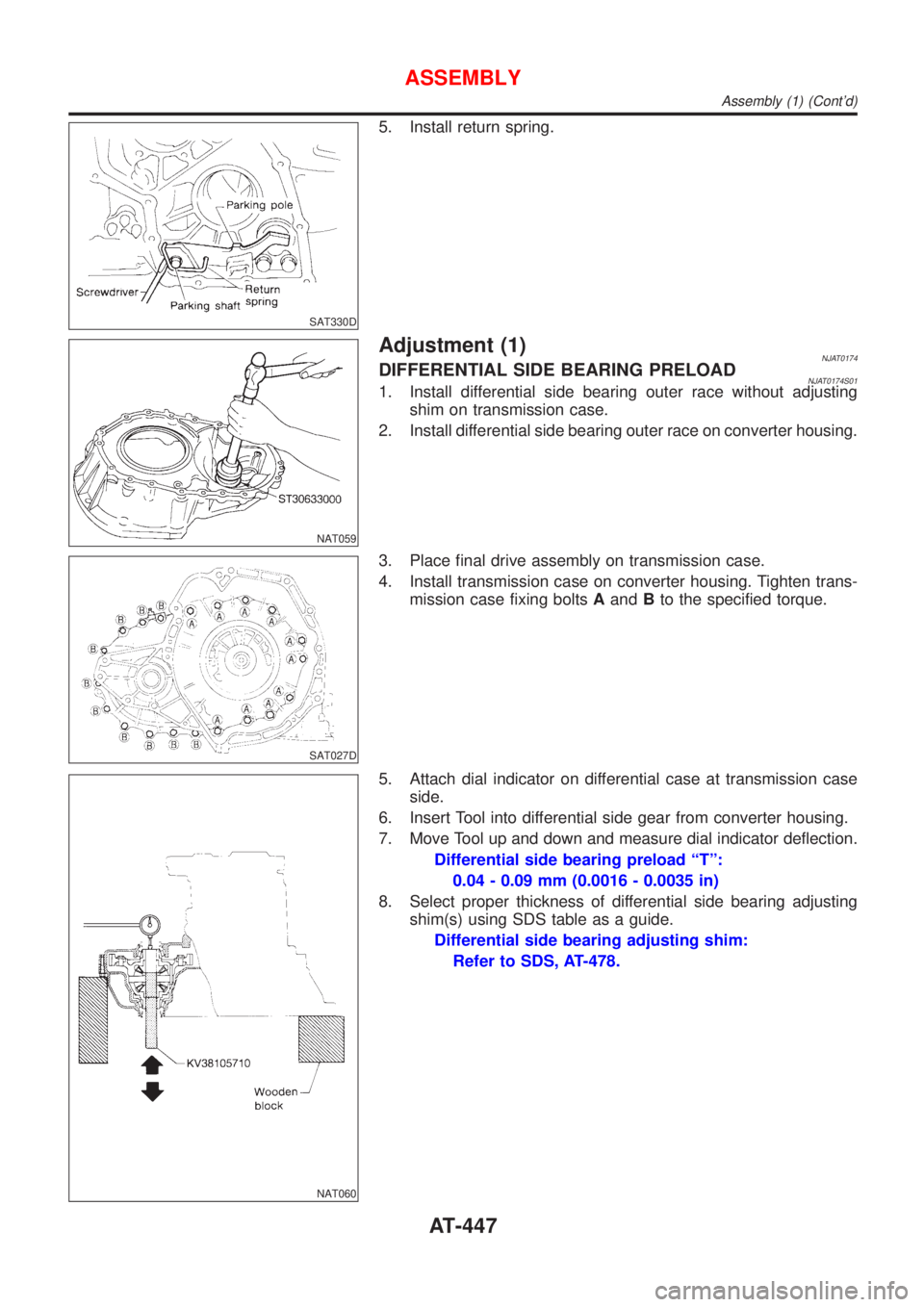
SAT330D
5. Install return spring.
NAT059
Adjustment (1)NJAT0174DIFFERENTIAL SIDE BEARING PRELOADNJAT0174S011. Install differential side bearing outer race without adjusting
shim on transmission case.
2. Install differential side bearing outer race on converter housing.
SAT027D
3. Place final drive assembly on transmission case.
4. Install transmission case on converter housing. Tighten trans-
mission case fixing boltsAandBto the specified torque.
NAT060
5. Attach dial indicator on differential case at transmission case
side.
6. Insert Tool into differential side gear from converter housing.
7. Move Tool up and down and measure dial indicator deflection.
Differential side bearing preload ªTº:
0.04 - 0.09 mm (0.0016 - 0.0035 in)
8. Select proper thickness of differential side bearing adjusting
shim(s) using SDS table as a guide.
Differential side bearing adjusting shim:
Refer to SDS, AT-478.
ASSEMBLY
Assembly (1) (Cont'd)
AT-447
Page 450 of 2898
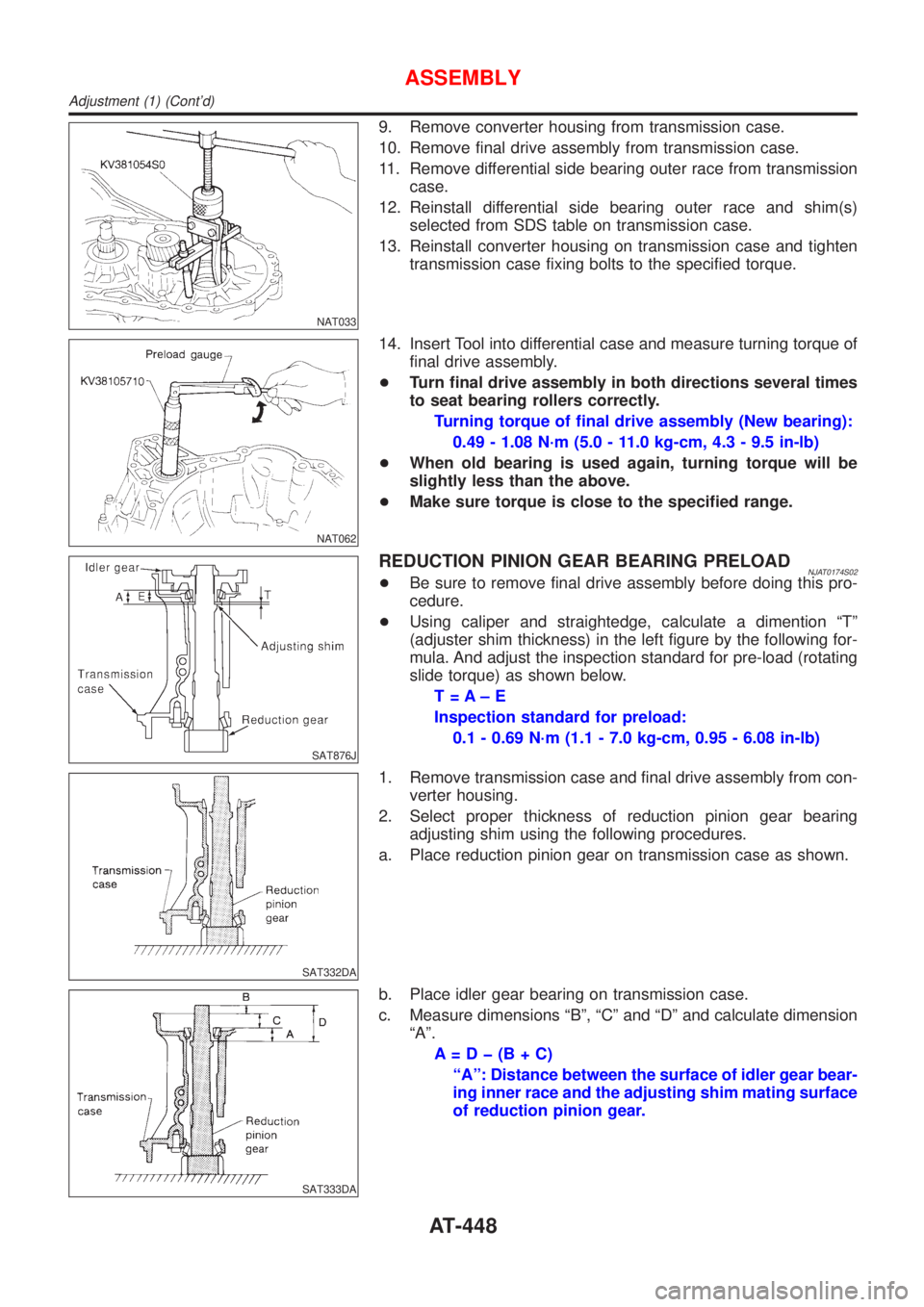
NAT033
9. Remove converter housing from transmission case.
10. Remove final drive assembly from transmission case.
11. Remove differential side bearing outer race from transmission
case.
12. Reinstall differential side bearing outer race and shim(s)
selected from SDS table on transmission case.
13. Reinstall converter housing on transmission case and tighten
transmission case fixing bolts to the specified torque.
NAT062
14. Insert Tool into differential case and measure turning torque of
final drive assembly.
+Turn final drive assembly in both directions several times
to seat bearing rollers correctly.
Turning torque of final drive assembly (New bearing):
0.49 - 1.08 N´m (5.0 - 11.0 kg-cm, 4.3 - 9.5 in-lb)
+When old bearing is used again, turning torque will be
slightly less than the above.
+Make sure torque is close to the specified range.
SAT876J
REDUCTION PINION GEAR BEARING PRELOADNJAT0174S02+Be sure to remove final drive assembly before doing this pro-
cedure.
+Using caliper and straightedge, calculate a dimention ªTº
(adjuster shim thickness) in the left figure by the following for-
mula. And adjust the inspection standard for pre-load (rotating
slide torque) as shown below.
T=A±E
Inspection standard for preload:
0.1 - 0.69 N´m (1.1 - 7.0 kg-cm, 0.95 - 6.08 in-lb)
SAT332DA
1. Remove transmission case and final drive assembly from con-
verter housing.
2. Select proper thickness of reduction pinion gear bearing
adjusting shim using the following procedures.
a. Place reduction pinion gear on transmission case as shown.
SAT333DA
b. Place idler gear bearing on transmission case.
c. Measure dimensions ªBº, ªCº and ªDº and calculate dimension
ªAº.
A=Dþ(B+C)
ªAº: Distance between the surface of idler gear bear-
ing inner race and the adjusting shim mating surface
of reduction pinion gear.
ASSEMBLY
Adjustment (1) (Cont'd)
AT-448