engine OPEL FRONTERA 1998 Workshop Manual
[x] Cancel search | Manufacturer: OPEL, Model Year: 1998, Model line: FRONTERA, Model: OPEL FRONTERA 1998Pages: 6000, PDF Size: 97 MB
Page 1029 of 6000
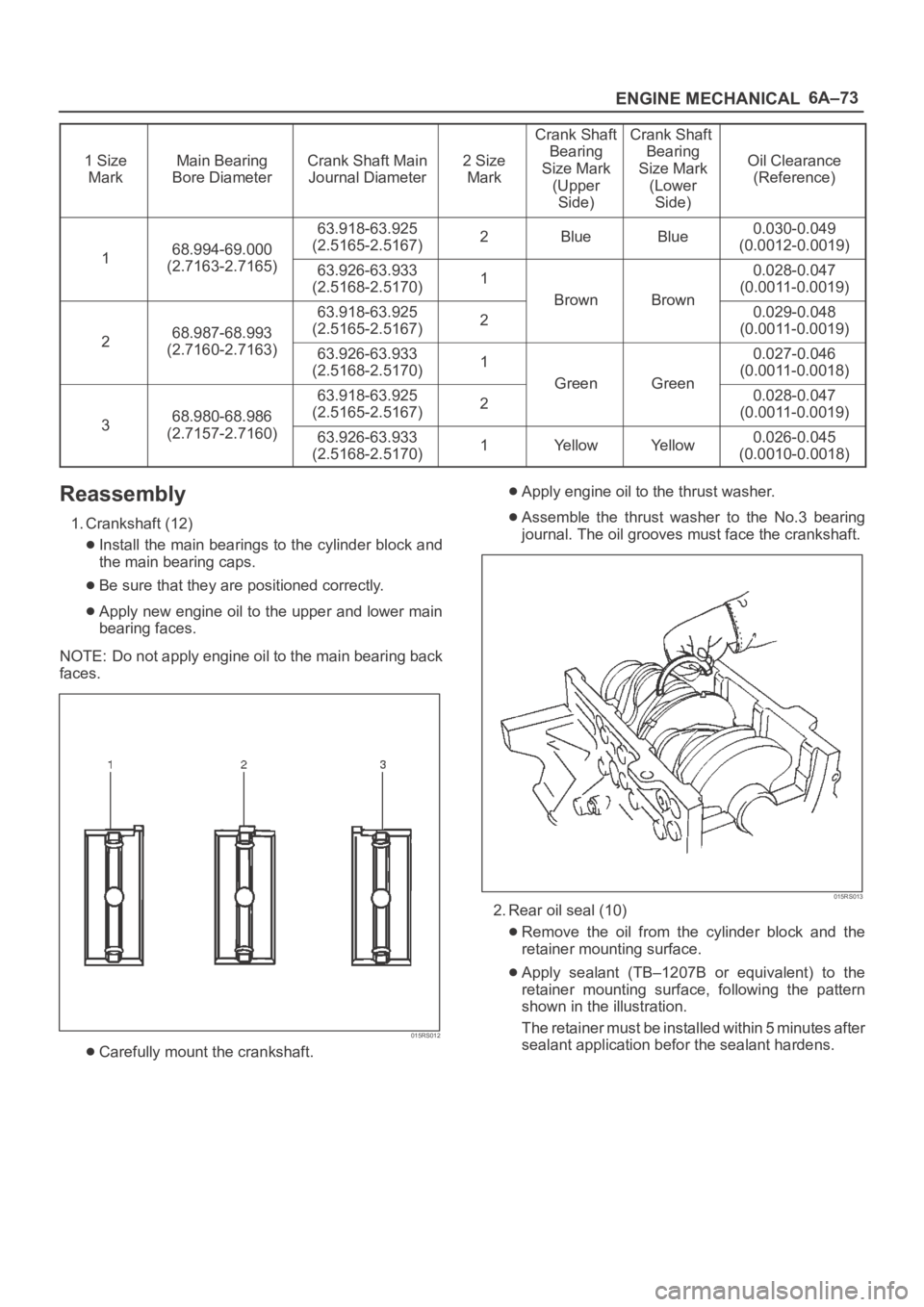
6A–73
ENGINE MECHANICAL
1 Size
MarkMain Bearing
Bore DiameterCrank Shaft Main
Journal Diameter2 Size
Mark
Crank Shaft
Bearing
Size Mark
(Upper
Side)Crank Shaft
Bearing
Size Mark
(Lower
Side)
Oil Clearance
(Reference)
168.994-69.000
63.918-63.925
(2.5165-2.5167)2BlueBlue0.030-0.049
(0.0012-0.0019)
1(2.7163-2.7165)63.926-63.933
(2.5168-2.5170)1
BrownBrown
0.028-0.047
(0.0011-0.0019)
268.987-68.993
63.918-63.925
(2.5165-2.5167)2
BrownBrown0.029-0.048
(0.0011-0.0019)
2(2.7160-2.7163)63.926-63.933
(2.5168-2.5170)1
GreenGreen
0.027-0.046
(0.0011-0.0018)
368.980-68.986
63.918-63.925
(2.5165-2.5167)2
GreenGreen0.028-0.047
(0.0011-0.0019)
3(2.7157-2.7160)63.926-63.933
(2.5168-2.5170)1Ye l l o wYe l l o w0.026-0.045
(0.0010-0.0018)
Reassembly
1. Crankshaft (12)
Install the main bearings to the cylinder block and
the main bearing caps.
Be sure that they are positioned correctly.
Apply new engine oil to the upper and lower main
bearing faces.
NOTE: Do not apply engine oil to the main bearing back
faces.
015RS012
Carefully mount the crankshaft.
Apply engine oil to the thrust washer.
Assemble the thrust washer to the No.3 bearing
journal. The oil grooves must face the crankshaft.
015RS013
2. Rear oil seal (10)
Remove the oil from the cylinder block and the
retainer mounting surface.
Apply sealant (TB–1207B or equivalent) to the
retainer mounting surface, following the pattern
shown in the illustration.
The retainer must be installed within 5 minutes after
sealant application befor the sealant hardens.
Page 1030 of 6000
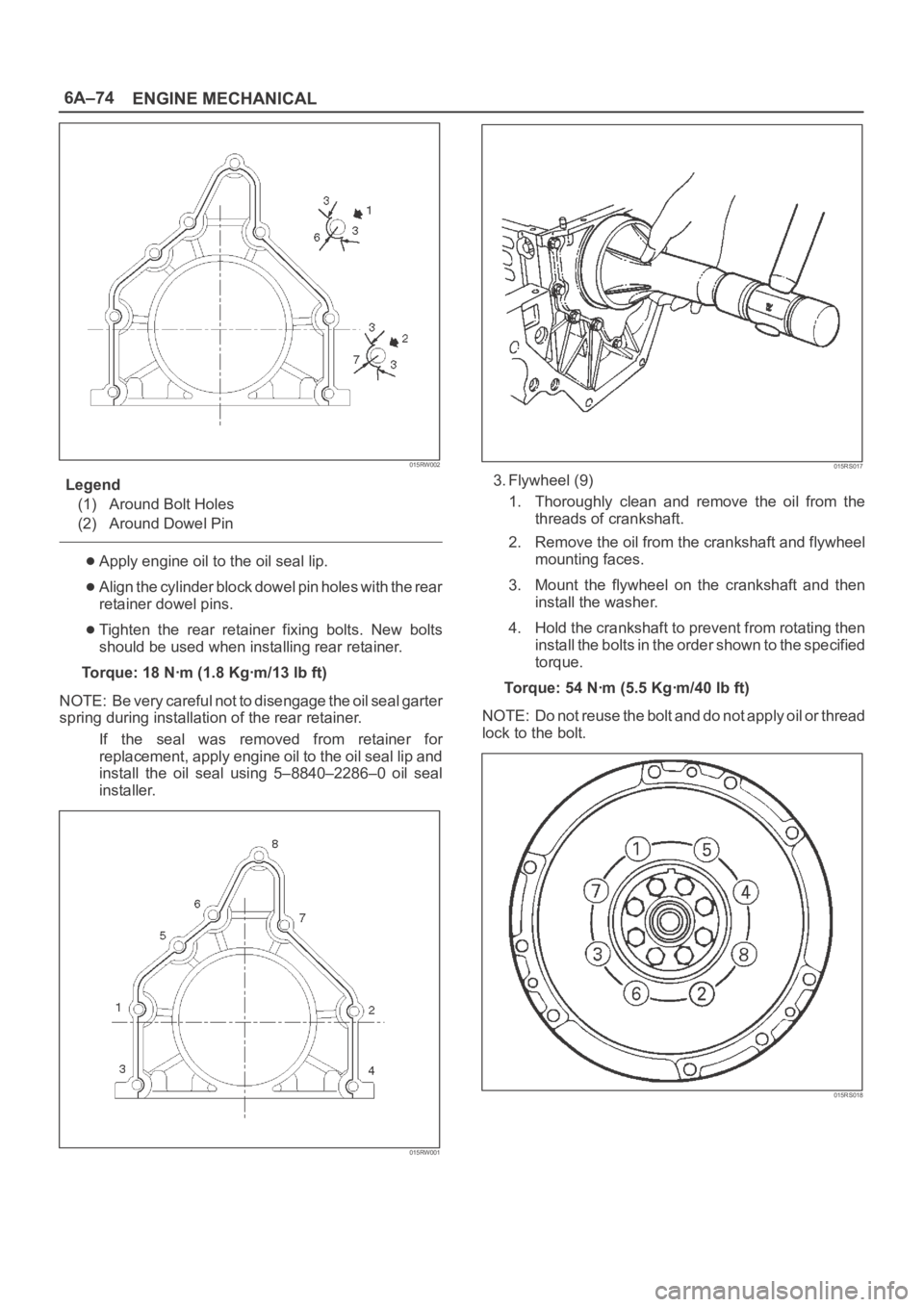
6A–74
ENGINE MECHANICAL
015RW002
Legend
(1) Around Bolt Holes
(2) Around Dowel Pin
Apply engine oil to the oil seal lip.
Align the cylinder block dowel pin holes with the rear
retainer dowel pins.
Tighten the rear retainer fixing bolts. New bolts
should be used when installing rear retainer.
Torque: 18 Nꞏm (1.8 Kgꞏm/13 lb ft)
NOTE: Be very careful not to disengage the oil seal garter
spring during installation of the rear retainer.
If the seal was removed from retainer for
replacement, apply engine oil to the oil seal lip and
install the oil seal using 5–8840–2286–0 oil seal
installer.
015RW001
015RS017
3. Flywheel (9)
1. Thoroughly clean and remove the oil from the
threads of crankshaft.
2. Remove the oil from the crankshaft and flywheel
mounting faces.
3. Mount the flywheel on the crankshaft and then
install the washer.
4. Hold the crankshaft to prevent from rotating then
install the bolts in the order shown to the specified
torque.
Torque: 54 Nꞏm (5.5 Kgꞏm/40 lb ft)
NOTE: Do not reuse the bolt and do not apply oil or thread
lock to the bolt.
015RS018
Page 1031 of 6000
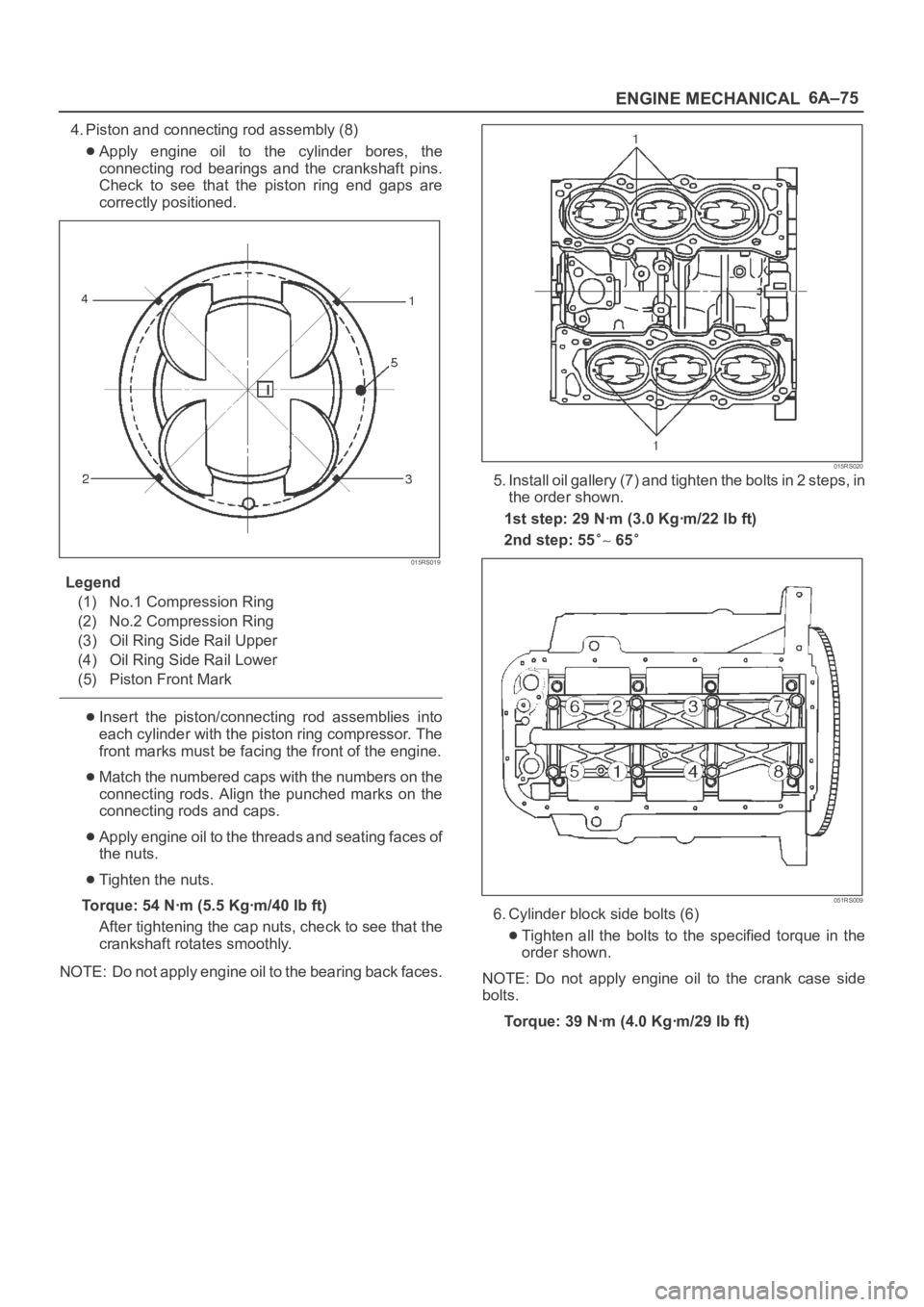
6A–75
ENGINE MECHANICAL
4. Piston and connecting rod assembly (8)
Apply engine oil to the cylinder bores, the
connecting rod bearings and the crankshaft pins.
Check to see that the piston ring end gaps are
correctly positioned.
015RS019
Legend
(1) No.1 Compression Ring
(2) No.2 Compression Ring
(3) Oil Ring Side Rail Upper
(4) Oil Ring Side Rail Lower
(5) Piston Front Mark
Insert the piston/connecting rod assemblies into
each cylinder with the piston ring compressor. The
front marks must be facing the front of the engine.
Match the numbered caps with the numbers on the
connecting rods. Align the punched marks on the
connecting rods and caps.
Apply engine oil to the threads and seating faces of
the nuts.
Tighten the nuts.
Torque: 54 Nꞏm (5.5 Kgꞏm/40 lb ft)
After tightening the cap nuts, check to see that the
crankshaft rotates smoothly.
NOTE: Do not apply engine oil to the bearing back faces.
015RS020
5. Install oil gallery (7) and tighten the bolts in 2 steps, in
the order shown.
1st step: 29 Nꞏm (3.0 Kgꞏm/22 lb ft)
2nd step: 55
65
051RS009
6. Cylinder block side bolts (6)
Tighten all the bolts to the specified torque in the
order shown.
NOTE: Do not apply engine oil to the crank case side
bolts.
Torque: 39 Nꞏm (4.0 Kgꞏm/29 lb ft)
Page 1032 of 6000
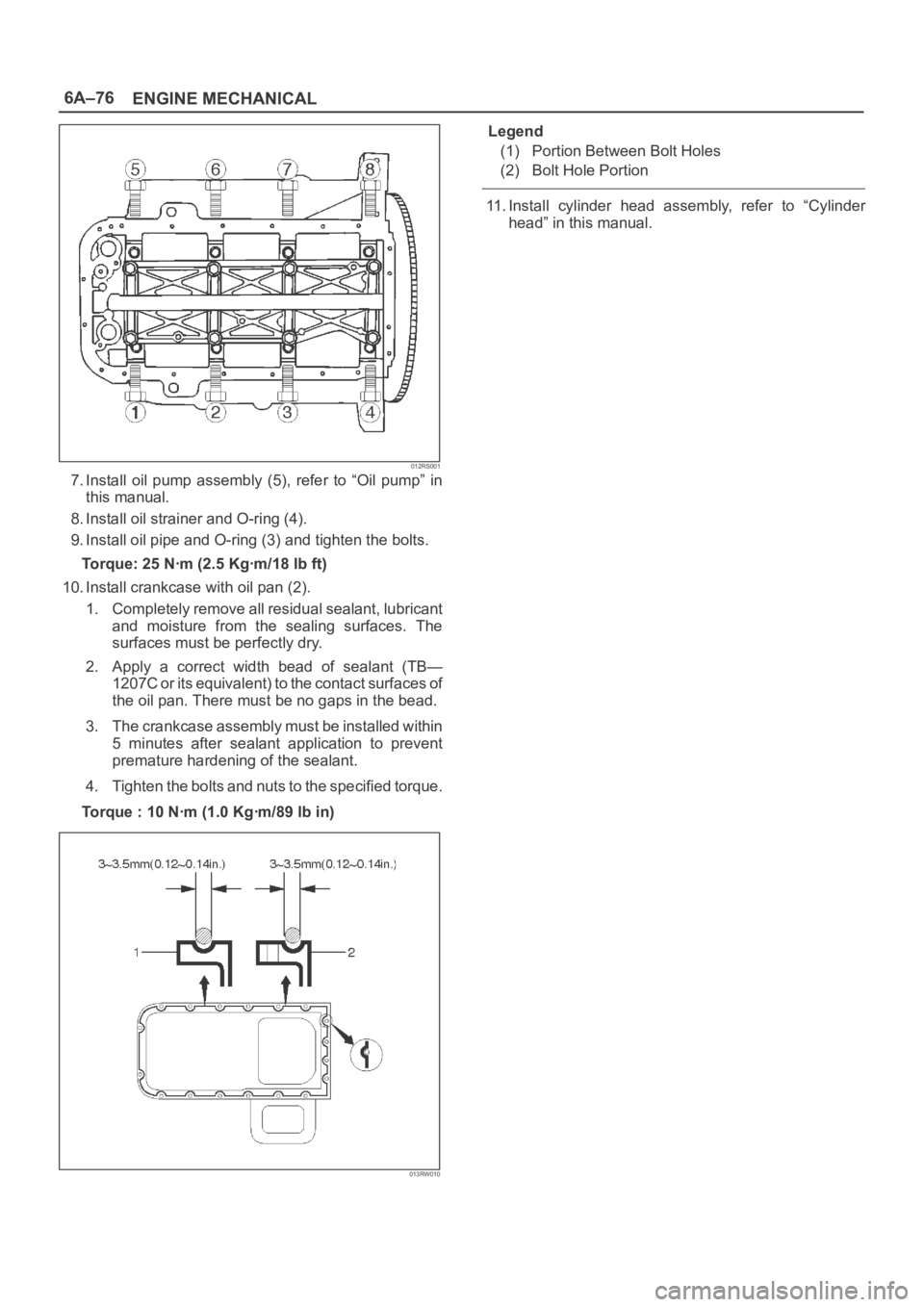
6A–76
ENGINE MECHANICAL
012RS001
7. Install oil pump assembly (5), refer to “Oil pump” in
this manual.
8. Install oil strainer and O-ring (4).
9. Install oil pipe and O-ring (3) and tighten the bolts.
Torque: 25 Nꞏm (2.5 Kgꞏm/18 lb ft)
10. Install crankcase with oil pan (2).
1. Completely remove all residual sealant, lubricant
and moisture from the sealing surfaces. The
surfaces must be perfectly dry.
2. Apply a correct width bead of sealant (TB—
1207C or its equivalent) to the contact surfaces of
the oil pan. There must be no gaps in the bead.
3. The crankcase assembly must be installed within
5 minutes after sealant application to prevent
premature hardening of the sealant.
4. Tighten the bolts and nuts to the specified torque.
Torque : 10 Nꞏm (1.0 Kgꞏm/89 lb in)
013RW010
Legend
(1) Portion Between Bolt Holes
(2) Bolt Hole Portion
11. Install cylinder head assembly, refer to “Cylinder
head” in this manual.
Page 1033 of 6000
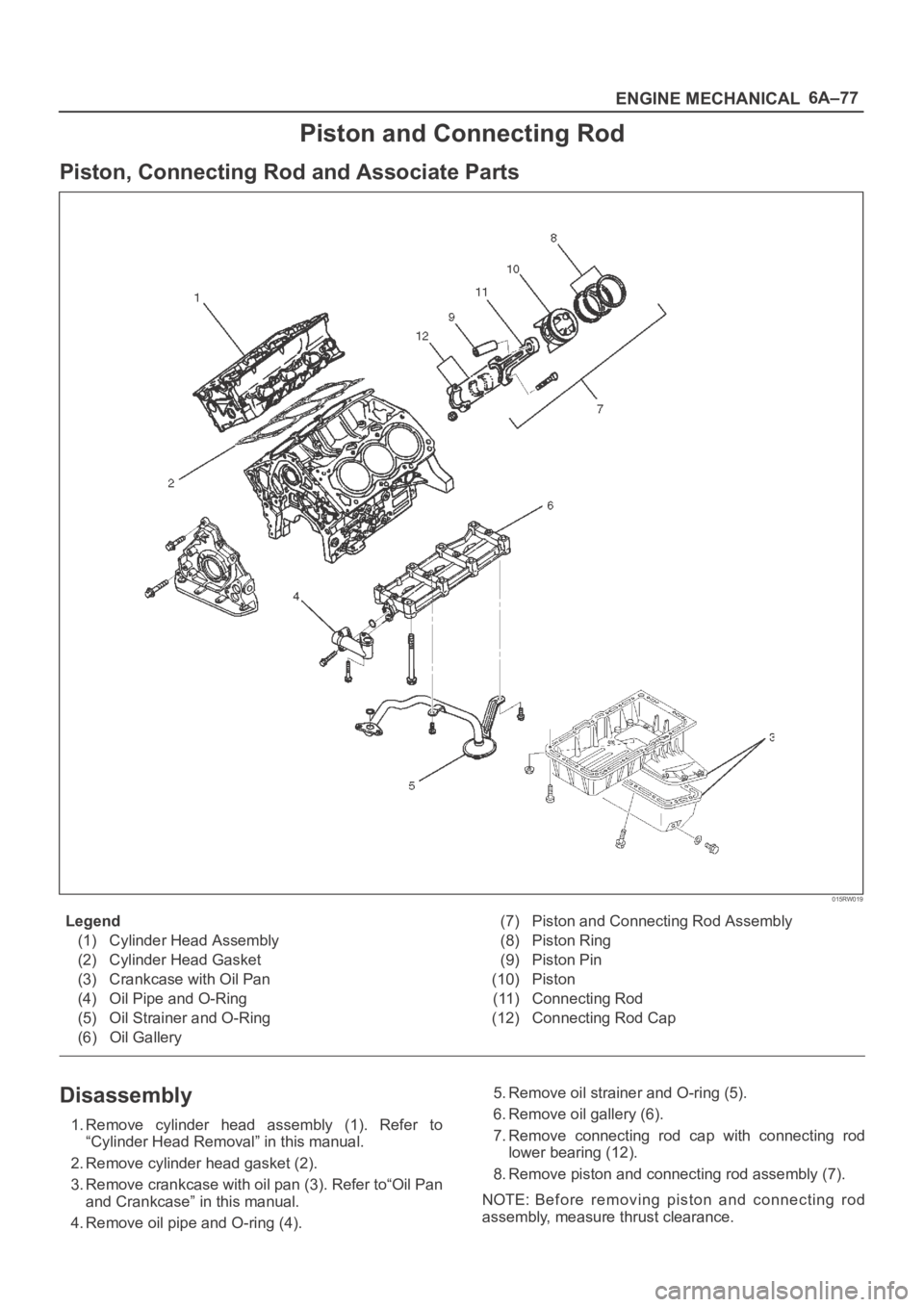
6A–77
ENGINE MECHANICAL
Piston and Connecting Rod
Piston, Connecting Rod and Associate Parts
015RW019
Legend
(1) Cylinder Head Assembly
(2) Cylinder Head Gasket
(3) Crankcase with Oil Pan
(4) Oil Pipe and O-Ring
(5) Oil Strainer and O-Ring
(6) Oil Gallery(7) Piston and Connecting Rod Assembly
(8) Piston Ring
(9) Piston Pin
(10) Piston
(11) Connecting Rod
(12) Connecting Rod Cap
Disassembly
1. Remove cylinder head assembly (1). Refer to
“Cylinder Head Removal” in this manual.
2. Remove cylinder head gasket (2).
3. Remove crankcase with oil pan (3). Refer to“Oil Pan
and Crankcase” in this manual.
4. Remove oil pipe and O-ring (4).5. Remove oil strainer and O-ring (5).
6. Remove oil gallery (6).
7. Remove connecting rod cap with connecting rod
lower bearing (12).
8. Remove piston and connecting rod assembly (7).
NOTE: Before removing piston and connecting rod
assembly, measure thrust clearance.
Page 1034 of 6000
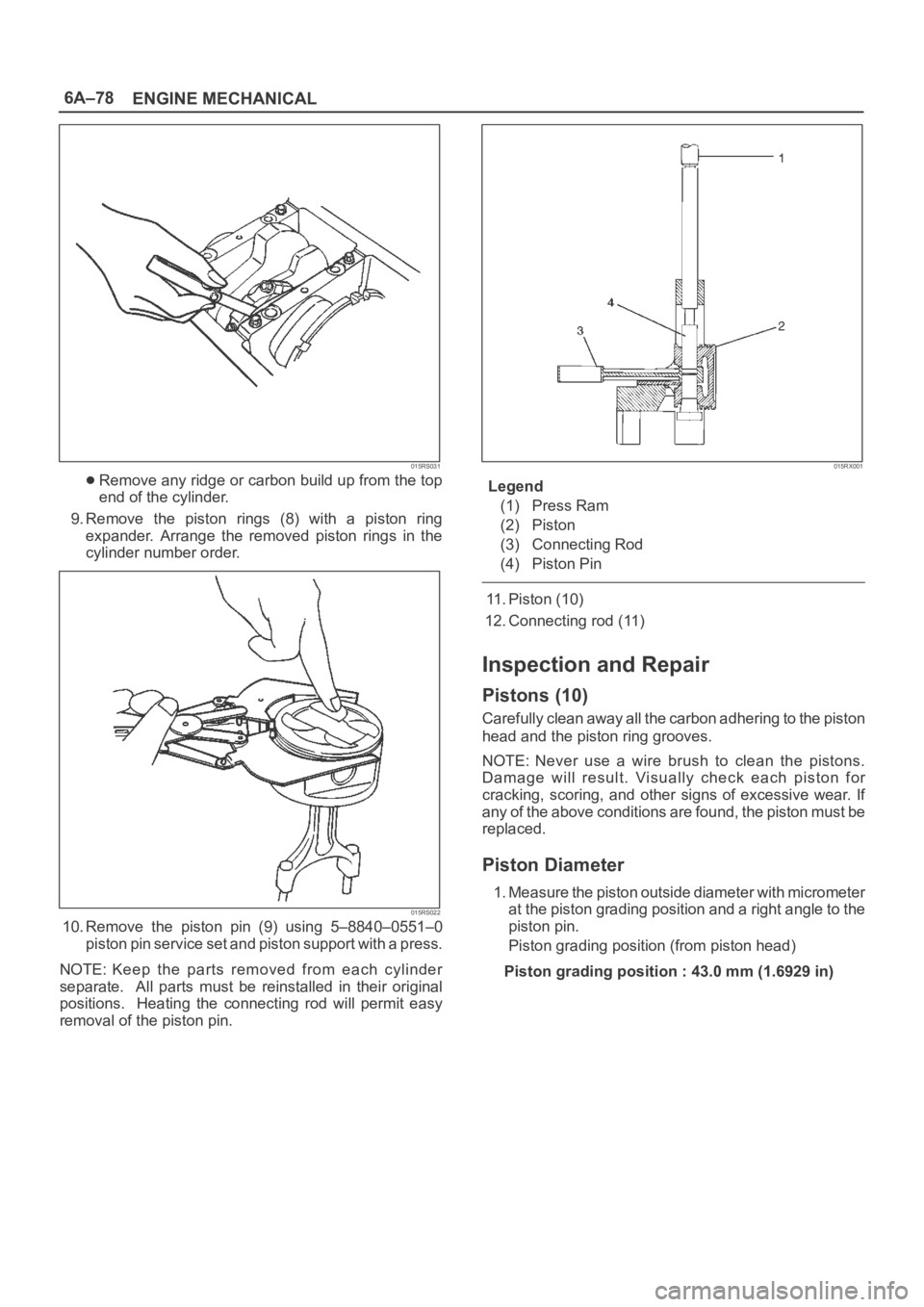
6A–78
ENGINE MECHANICAL
015RS031
Remove any ridge or carbon build up from the top
end of the cylinder.
9. Remove the piston rings (8) with a piston ring
expander. Arrange the removed piston rings in the
cylinder number order.
015RS022
10. Remove the piston pin (9) using 5–8840–0551–0
piston pin service set and piston support with a press.
NOTE: Keep the parts removed from each cylinder
separate. All parts must be reinstalled in their original
positions. Heating the connecting rod will permit easy
removal of the piston pin.
015RX001
Legend
(1) Press Ram
(2) Piston
(3) Connecting Rod
(4) Piston Pin
11. Piston (10)
12. Connecting rod (11)
Inspection and Repair
Pistons (10)
Carefully clean away all the carbon adhering to the piston
head and the piston ring grooves.
NOTE: Never use a wire brush to clean the pistons.
Damage will result. Visually check each piston for
cracking, scoring, and other signs of excessive wear. If
any of the above conditions are found, the piston must be
replaced.
Piston Diameter
1. Measure the piston outside diameter with micrometer
at the piston grading position and a right angle to the
piston pin.
Piston grading position (from piston head)
Piston grading position : 43.0 mm (1.6929 in)
Page 1035 of 6000
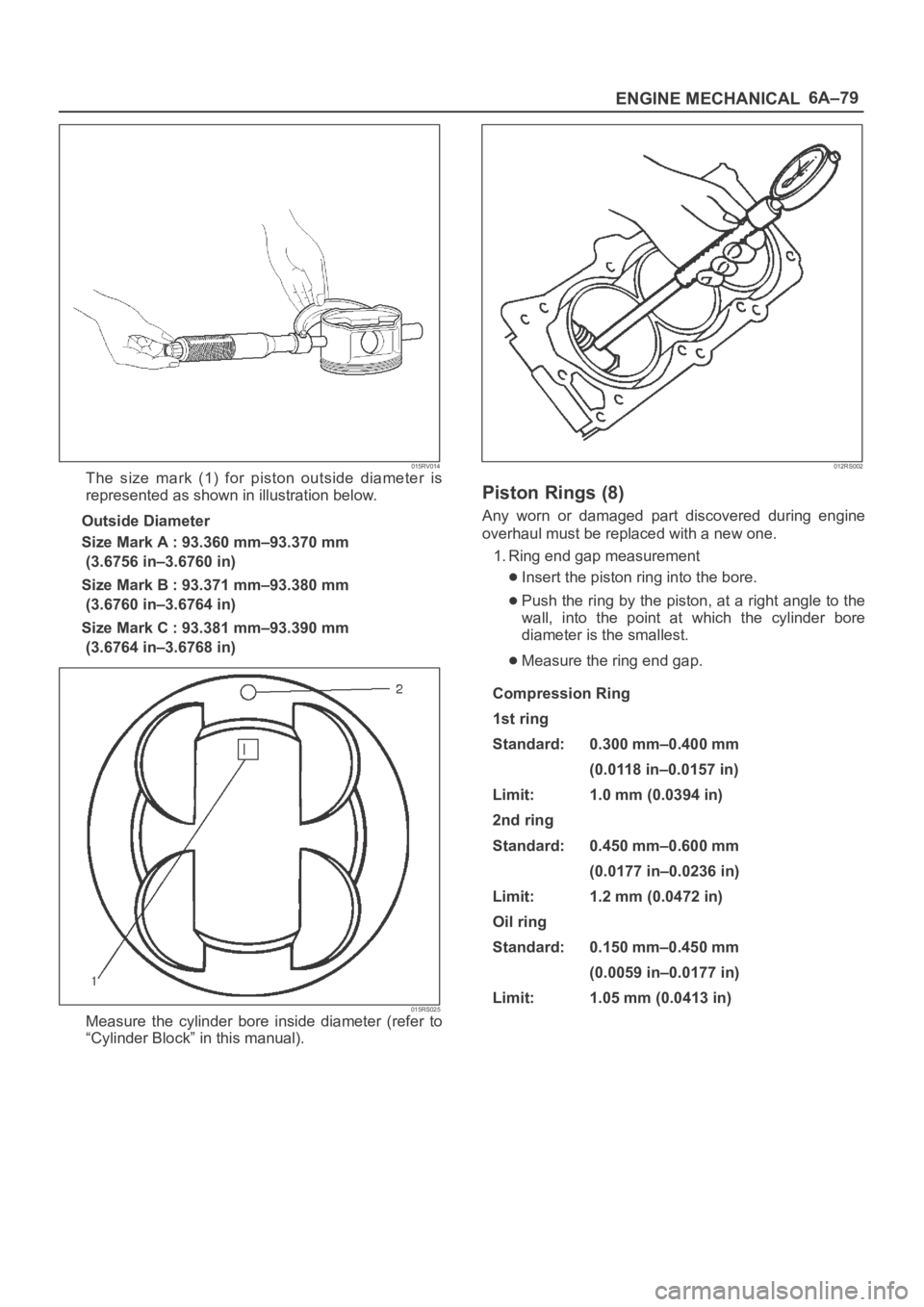
6A–79
ENGINE MECHANICAL
015RV014The size mark (1) for piston outside diameter is
represented as shown in illustration below.
Outside Diameter
Size Mark A : 93.360 mm–93.370 mm
(3.6756 in–3.6760 in)
Size Mark B : 93.371 mm–93.380 mm
(3.6760 in–3.6764 in)
Size Mark C : 93.381 mm–93.390 mm
(3.6764 in–3.6768 in)
015RS025Measure the cylinder bore inside diameter (refer to
“Cylinder Block” in this manual).
012RS002
Piston Rings (8)
Any worn or damaged part discovered during engine
overhaul must be replaced with a new one.
1. Ring end gap measurement
Insert the piston ring into the bore.
Push the ring by the piston, at a right angle to the
wall, into the point at which the cylinder bore
diameter is the smallest.
Measure the ring end gap.
Compression Ring
1st ring
Standard:
0.300 mm–0.400 mm
(0.0118 in–0.0157 in)
Limit: 1.0 mm (0.0394 in)
2nd ring
Standard: 0.450 mm–0.600 mm
(0.0177 in–0.0236 in)
Limit: 1.2 mm (0.0472 in)
Oil ring
Standard:
0.150 mm–0.450 mm
(0.0059 in–0.0177 in)
Limit: 1.05 mm (0.0413 in)
Page 1036 of 6000
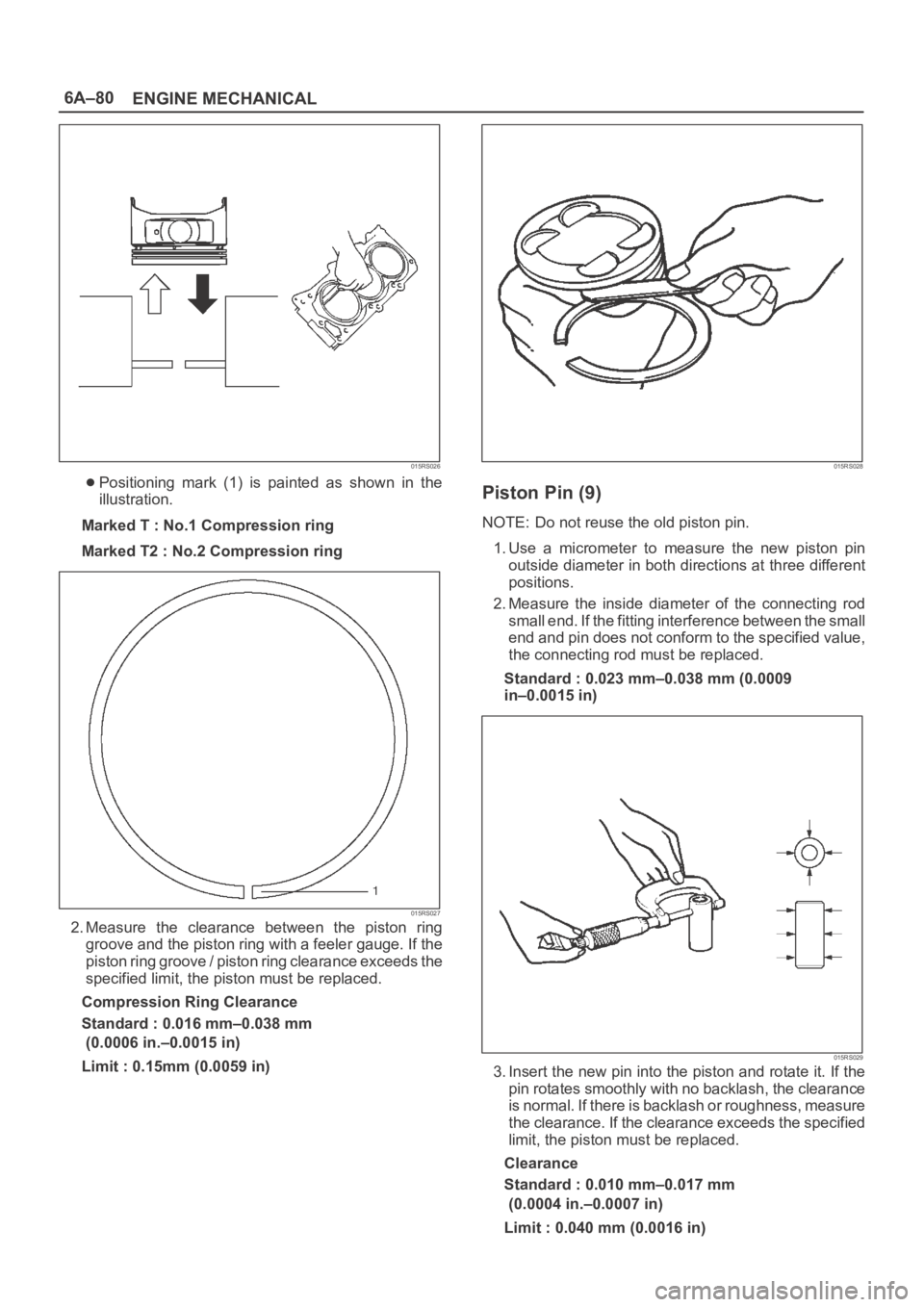
6A–80
ENGINE MECHANICAL
015RS026
Positioning mark (1) is painted as shown in the
illustration.
Marked T : No.1 Compression ring
Marked T2 : No.2 Compression ring
015RS027
2. Measure the clearance between the piston ring
groove and the piston ring with a feeler gauge. If the
piston ring groove / piston ring clearance exceeds the
specified limit, the piston must be replaced.
Compression Ring Clearance
Standard : 0.016 mm–0.038 mm
(0.0006 in.–0.0015 in)
Limit : 0.15mm (0.0059 in)
015RS028
Piston Pin (9)
NOTE: Do not reuse the old piston pin.
1. Use a micrometer to measure the new piston pin
outside diameter in both directions at three different
positions.
2. Measure the inside diameter of the connecting rod
small end. If the fitting interference between the small
end and pin does not conform to the specified value,
the connecting rod must be replaced.
Standard : 0.023 mm–0.038 mm (0.0009
in–0.0015 in)
015RS029
3. Insert the new pin into the piston and rotate it. If the
pin rotates smoothly with no backlash, the clearance
is normal. If there is backlash or roughness, measure
the clearance. If the clearance exceeds the specified
limit, the piston must be replaced.
Clearance
Standard : 0.010 mm–0.017 mm
(0.0004 in.–0.0007 in)
Limit : 0.040 mm (0.0016 in)
Page 1037 of 6000
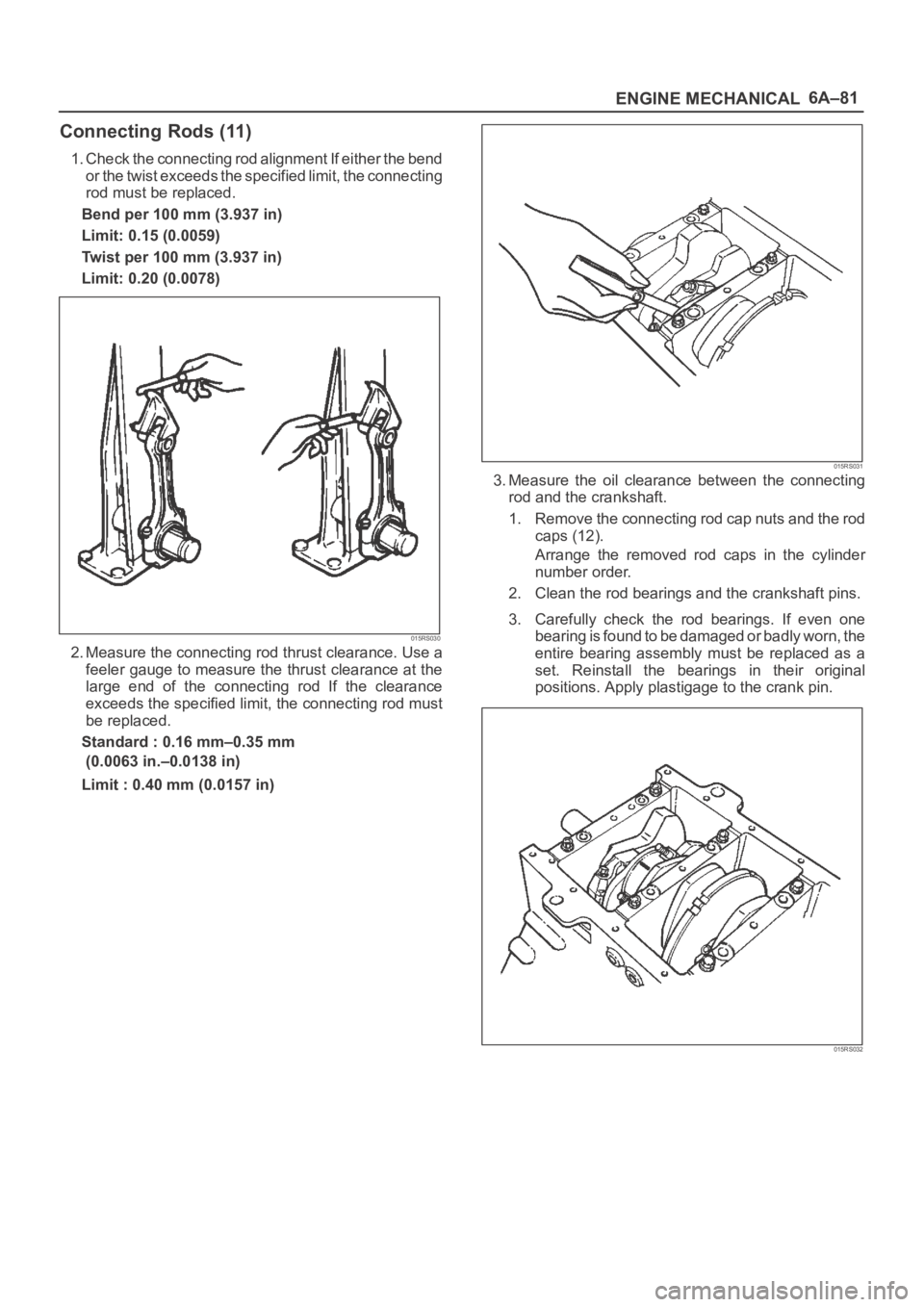
6A–81
ENGINE MECHANICAL
Connecting Rods (11)
1. Check the connecting rod alignment If either the bend
or the twist exceeds the specified limit, the connecting
rod must be replaced.
Bend per 100 mm (3.937 in)
Limit: 0.15 (0.0059)
Twist per 100 mm (3.937 in)
Limit: 0.20 (0.0078)
015RS030
2. Measure the connecting rod thrust clearance. Use a
feeler gauge to measure the thrust clearance at the
large end of the connecting rod If the clearance
exceeds the specified limit, the connecting rod must
be replaced.
Standard : 0.16 mm–0.35 mm
(0.0063 in.–0.0138 in)
Limit : 0.40 mm (0.0157 in)
015RS031
3. Measure the oil clearance between the connecting
rod and the crankshaft.
1. Remove the connecting rod cap nuts and the rod
caps (12).
Arrange the removed rod caps in the cylinder
number order.
2. Clean the rod bearings and the crankshaft pins.
3. Carefully check the rod bearings. If even one
bearing is found to be damaged or badly worn, the
entire bearing assembly must be replaced as a
set. Reinstall the bearings in their original
positions. Apply plastigage to the crank pin.
015RS032
Page 1038 of 6000
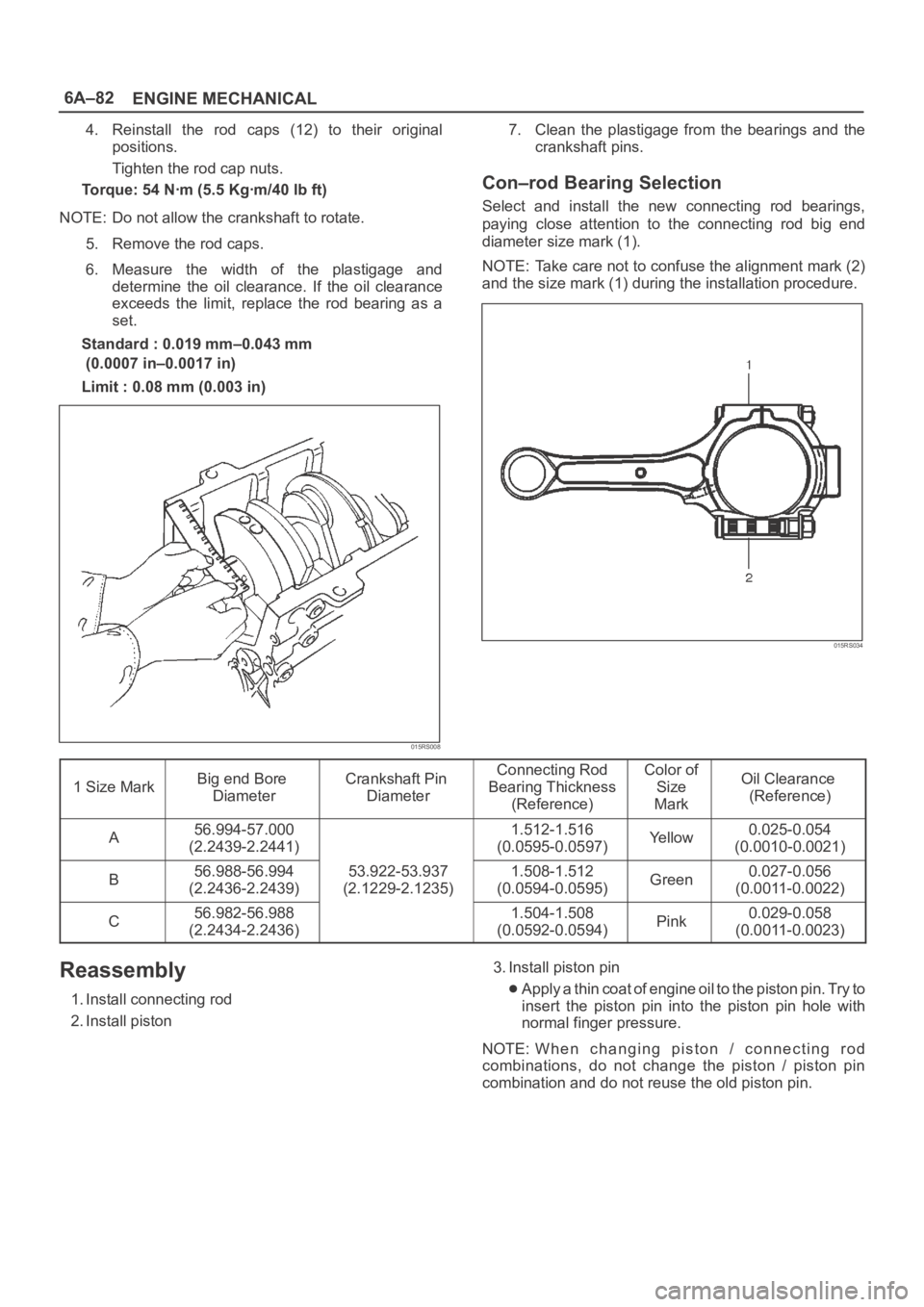
6A–82
ENGINE MECHANICAL
4. Reinstall the rod caps (12) to their original
positions.
Tighten the rod cap nuts.
Torque: 54 Nꞏm (5.5 Kgꞏm/40 lb ft)
NOTE: Do not allow the crankshaft to rotate.
5. Remove the rod caps.
6. Measure the width of the plastigage and
determine the oil clearance. If the oil clearance
exceeds the limit, replace the rod bearing as a
set.
Standard : 0.019 mm–0.043 mm
(0.0007 in–0.0017 in)
Limit : 0.08 mm (0.003 in)
015RS008
7. Clean the plastigage from the bearings and the
crankshaft pins.
Con–rod Bearing Selection
Select and install the new connecting rod bearings,
paying close attention to the connecting rod big end
diameter size mark (1).
NOTE: Take care not to confuse the alignment mark (2)
and the size mark (1) during the installation procedure.
015RS034
1 Size MarkBig end Bore
DiameterCrankshaft Pin
DiameterConnecting Rod
Bearing Thickness
(Reference)Color of
Size
MarkOil Clearance
(Reference)
A56.994-57.000
(2.2439-2.2441)1.512-1.516
(0.0595-0.0597)Ye l l o w0.025-0.054
(0.0010-0.0021)
B56.988-56.994
(2.2436-2.2439)53.922-53.937
(2.1229-2.1235)1.508-1.512
(0.0594-0.0595)Green0.027-0.056
(0.0011-0.0022)
C56.982-56.988
(2.2434-2.2436)1.504-1.508
(0.0592-0.0594)Pink0.029-0.058
(0.0011-0.0023)
Reassembly
1. Install connecting rod
2. Install piston3. Install piston pinApply a thin coat of engine oil to the piston pin. Try to
insert the piston pin into the piston pin hole with
normal finger pressure.
NOTE: When changing piston / connecting rod
combinations, do not change the piston / piston pin
combination and do not reuse the old piston pin.