sensor OPEL FRONTERA 1998 Manual PDF
[x] Cancel search | Manufacturer: OPEL, Model Year: 1998, Model line: FRONTERA, Model: OPEL FRONTERA 1998Pages: 6000, PDF Size: 97 MB
Page 814 of 6000
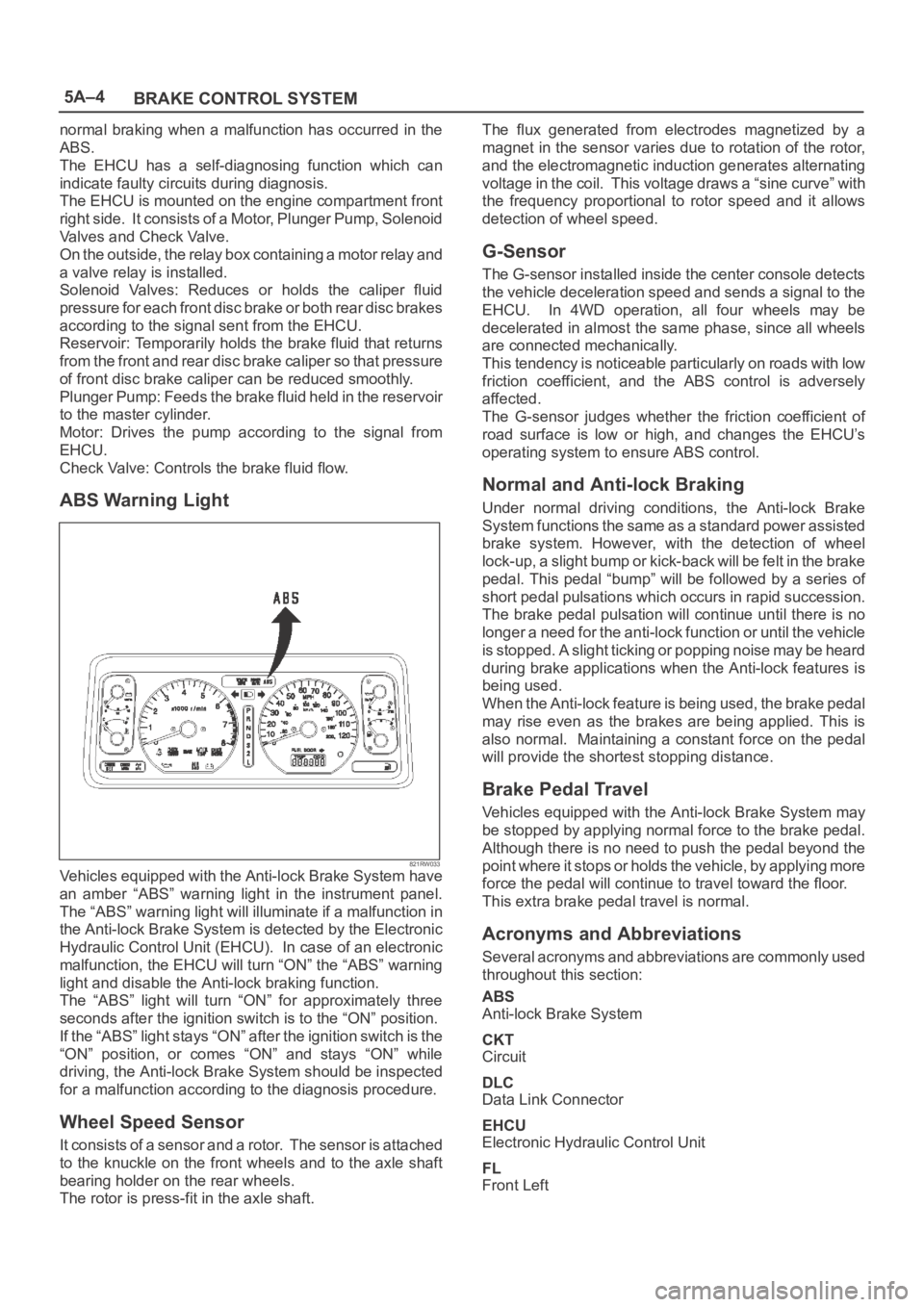
5A–4
BRAKE CONTROL SYSTEM
normal braking when a malfunction has occurred in the
ABS.
The EHCU has a self-diagnosing function which can
indicate faulty circuits during diagnosis.
The EHCU is mounted on the engine compartment front
right side. It consists of a Motor, Plunger Pump, Solenoid
Valves and Check Valve.
On the outside, the relay box containing a motor relay and
a valve relay is installed.
Solenoid Valves: Reduces or holds the caliper fluid
pressure for each front disc brake or both rear disc brakes
according to the signal sent from the EHCU.
Reservoir: Temporarily holds the brake fluid that returns
from the front and rear disc brake caliper so that pressure
of front disc brake caliper can be reduced smoothly.
Plunger Pump: Feeds the brake fluid held in the reservoir
to the master cylinder.
Motor: Drives the pump according to the signal from
EHCU.
Check Valve: Controls the brake fluid flow.
ABS Warning Light
821RW033Vehicles equipped with the Anti-lock Brake System have
an amber “ABS” warning light in the instrument panel.
The “ABS” warning light will illuminate if a malfunction in
the Anti-lock Brake System is detected by the Electronic
Hydraulic Control Unit (EHCU). In case of an electronic
malfunction, the EHCU will turn “ON” the “ABS” warning
light and disable the Anti-lock braking function.
The “ABS” light will turn “ON” for approximately three
seconds after the ignition switch is to the “ON” position.
If the “ABS” light stays “ON” after the ignition switch is the
“ON” position, or comes “ON” and stays “ON” while
driving, the Anti-lock Brake System should be inspected
for a malfunction according to the diagnosis procedure.
Wheel Speed Sensor
It consists of a sensor and a rotor. The sensor is attached
to the knuckle on the front wheels and to the axle shaft
bearing holder on the rear wheels.
The rotor is press-fit in the axle shaft.The flux generated from electrodes magnetized by a
magnet in the sensor varies due to rotation of the rotor,
and the electromagnetic induction generates alternating
voltage in the coil. This voltage draws a “sine curve” with
the frequency proportional to rotor speed and it allows
detection of wheel speed.
G-Sensor
The G-sensor installed inside the center console detects
the vehicle deceleration speed and sends a signal to the
EHCU. In 4WD operation, all four wheels may be
decelerated in almost the same phase, since all wheels
are connected mechanically.
This tendency is noticeable particularly on roads with low
friction coefficient, and the ABS control is adversely
affected.
The G-sensor judges whether the friction coefficient of
road surface is low or high, and changes the EHCU’s
operating system to ensure ABS control.
Normal and Anti-lock Braking
Under normal driving conditions, the Anti-lock Brake
System functions the same as a standard power assisted
brake system. However, with the detection of wheel
lock-up, a slight bump or kick-back will be felt in the brake
pedal. This pedal “bump” will be followed by a series of
short pedal pulsations which occurs in rapid succession.
The brake pedal pulsation will continue until there is no
longer a need for the anti-lock function or until the vehicle
is stopped. A slight ticking or popping noise may be heard
during brake applications when the Anti-lock features is
being used.
When the Anti-lock feature is being used, the brake pedal
may rise even as the brakes are being applied. This is
also normal. Maintaining a constant force on the pedal
will provide the shortest stopping distance.
Brake Pedal Travel
Vehicles equipped with the Anti-lock Brake System may
be stopped by applying normal force to the brake pedal.
Although there is no need to push the pedal beyond the
point where it stops or holds the vehicle, by applying more
force the pedal will continue to travel toward the floor.
This extra brake pedal travel is normal.
Acronyms and Abbreviations
Several acronyms and abbreviations are commonly used
throughout this section:
ABS
Anti-lock Brake System
CKT
Circuit
DLC
Data Link Connector
EHCU
Electronic Hydraulic Control Unit
FL
Front Left
Page 815 of 6000
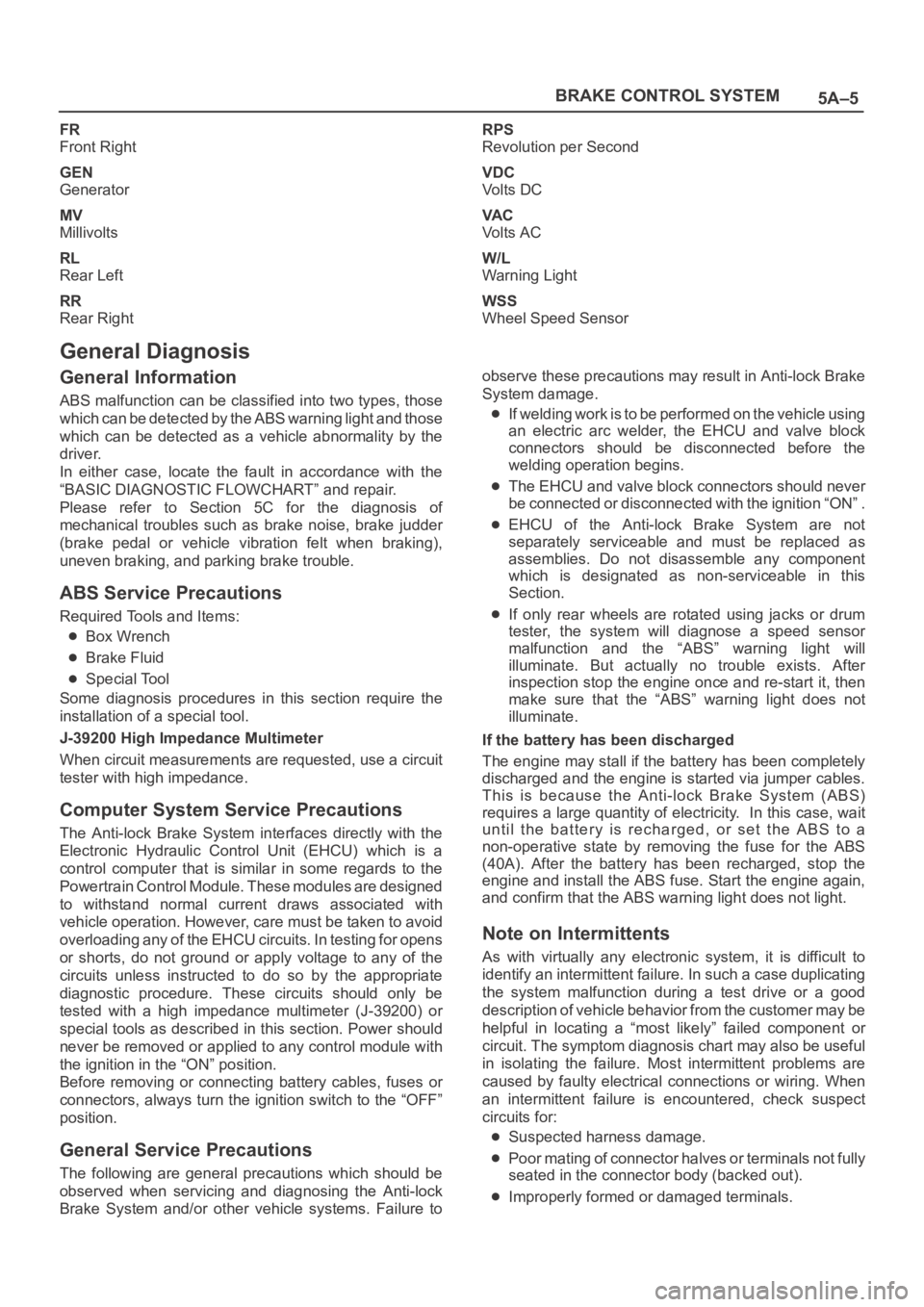
5A–5 BRAKE CONTROL SYSTEM
FR
Front Right
GEN
Generator
MV
Millivolts
RL
Rear Left
RR
Rear RightRPS
Revolution per Second
VDC
Vo l t s D C
VA C
Vo l t s A C
W/L
Warning Light
WSS
Wheel Speed Sensor
General Diagnosis
General Information
ABS malfunction can be classified into two types, those
which can be detected by the ABS warning light and those
which can be detected as a vehicle abnormality by the
driver.
In either case, locate the fault in accordance with the
“BASIC DIAGNOSTIC FLOWCHART” and repair.
Please refer to Section 5C for the diagnosis of
mechanical troubles such as brake noise, brake judder
(brake pedal or vehicle vibration felt when braking),
uneven braking, and parking brake trouble.
ABS Service Precautions
Required Tools and Items:
Box Wrench
Brake Fluid
Special Tool
Some diagnosis procedures in this section require the
installation of a special tool.
J-39200 High Impedance Multimeter
When circuit measurements are requested, use a circuit
tester with high impedance.
Computer System Service Precautions
The Anti-lock Brake System interfaces directly with the
Electronic Hydraulic Control Unit (EHCU) which is a
control computer that is similar in some regards to the
Powertrain Control Module. These modules are designed
to withstand normal current draws associated with
vehicle operation. However, care must be taken to avoid
overloading any of the EHCU circuits. In testing for opens
or shorts, do not ground or apply voltage to any of the
circuits unless instructed to do so by the appropriate
diagnostic procedure. These circuits should only be
tested with a high impedance multimeter (J-39200) or
special tools as described in this section. Power should
never be removed or applied to any control module with
the ignition in the “ON” position.
Before removing or connecting battery cables, fuses or
connectors, always turn the ignition switch to the “OFF”
position.
General Service Precautions
The following are general precautions which should be
observed when servicing and diagnosing the Anti-lock
Brake System and/or other vehicle systems. Failure toobserve these precautions may result in Anti-lock Brake
System damage.
If welding work is to be performed on the vehicle using
an electric arc welder, the EHCU and valve block
connectors should be disconnected before the
welding operation begins.
The EHCU and valve block connectors should never
be connected or disconnected with the ignition “ON” .
EHCU of the Anti-lock Brake System are not
separately serviceable and must be replaced as
assemblies. Do not disassemble any component
which is designated as non-serviceable in this
Section.
If only rear wheels are rotated using jacks or drum
tester, the system will diagnose a speed sensor
malfunction and the “ABS” warning light will
illuminate. But actually no trouble exists. After
inspection stop the engine once and re-start it, then
make sure that the “ABS” warning light does not
illuminate.
If the battery has been discharged
The engine may stall if the battery has been completely
discharged and the engine is started via jumper cables.
This is because the Anti-lock Brake System (ABS)
requires a large quantity of electricity. In this case, wait
until the battery is recharged, or set the ABS to a
non-operative state by removing the fuse for the ABS
(40A). After the battery has been recharged, stop the
engine and install the ABS fuse. Start the engine again,
and confirm that the ABS warning light does not light.
Note on Intermittents
As with virtually any electronic system, it is difficult to
identify an intermittent failure. In such a case duplicating
the system malfunction during a test drive or a good
description of vehicle behavior from the customer may be
helpful in locating a “most likely” failed component or
circuit. The symptom diagnosis chart may also be useful
in isolating the failure. Most intermittent problems are
caused by faulty electrical connections or wiring. When
an intermittent failure is encountered, check suspect
circuits for:
Suspected harness damage.
Poor mating of connector halves or terminals not fully
seated in the connector body (backed out).
Improperly formed or damaged terminals.
Page 821 of 6000
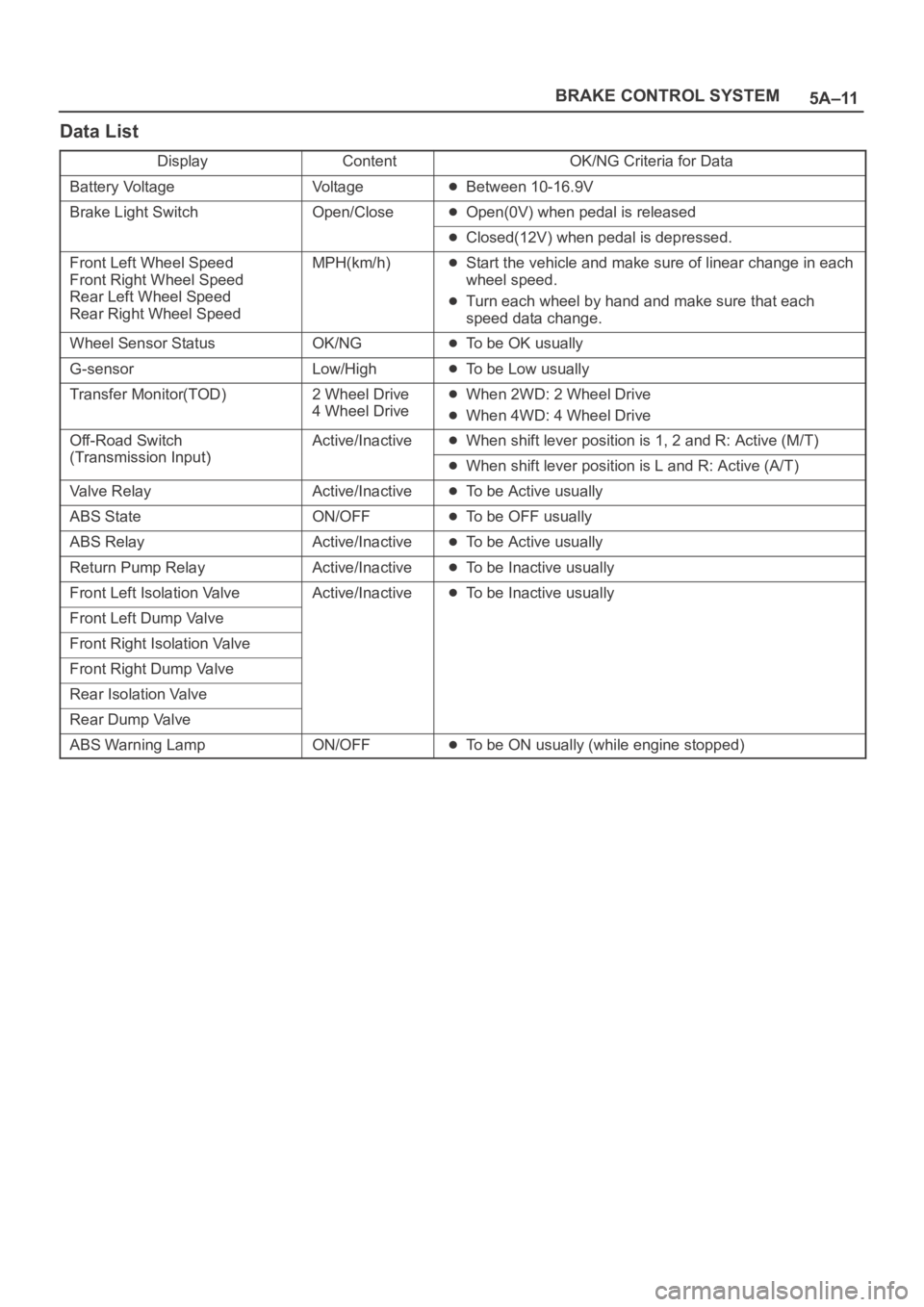
5A–11 BRAKE CONTROL SYSTEM
Data List
DisplayContentOK/NG Criteria for Data
Battery VoltageVo l t a g eBetween 10-16.9V
Brake Light SwitchOpen/CloseOpen(0V) when pedal is released
Closed(12V) when pedal is depressed.
Front Left Wheel Speed
Front Right Wheel Speed
Rear Left Wheel Speed
Rear Right Wheel SpeedMPH(km/h)Start the vehicle and make sure of linear change in each
wheel speed.
Turn each wheel by hand and make sure that each
speed data change.
Wheel Sensor StatusOK/NGTo be OK usually
G-sensorLow/HighTo be Low usually
Transfer Monitor(TOD)2 Wheel Drive
4 Wheel DriveWhen 2WD: 2 Wheel Drive
When 4WD: 4 Wheel Drive
Off-Road Switch
(Transmission Input)
Active/InactiveWhen shift lever position is 1, 2 and R: Active (M/T)
(Transmission Input)When shift lever position is L and R: Active (A/T)
Valve RelayActive/InactiveTo be Active usually
ABS StateON/OFFTo be OFF usually
ABS RelayActive/InactiveTo be Active usually
Return Pump RelayActive/InactiveTo be Inactive usually
Front Left Isolation ValveActive/InactiveTo be Inactive usually
Front Left Dump Valve
Front Right Isolation Valve
Front Right Dump Valve
Rear Isolation Valve
Rear Dump Valve
ABS Warning LampON/OFFTo be ON usually (while engine stopped)
Page 822 of 6000
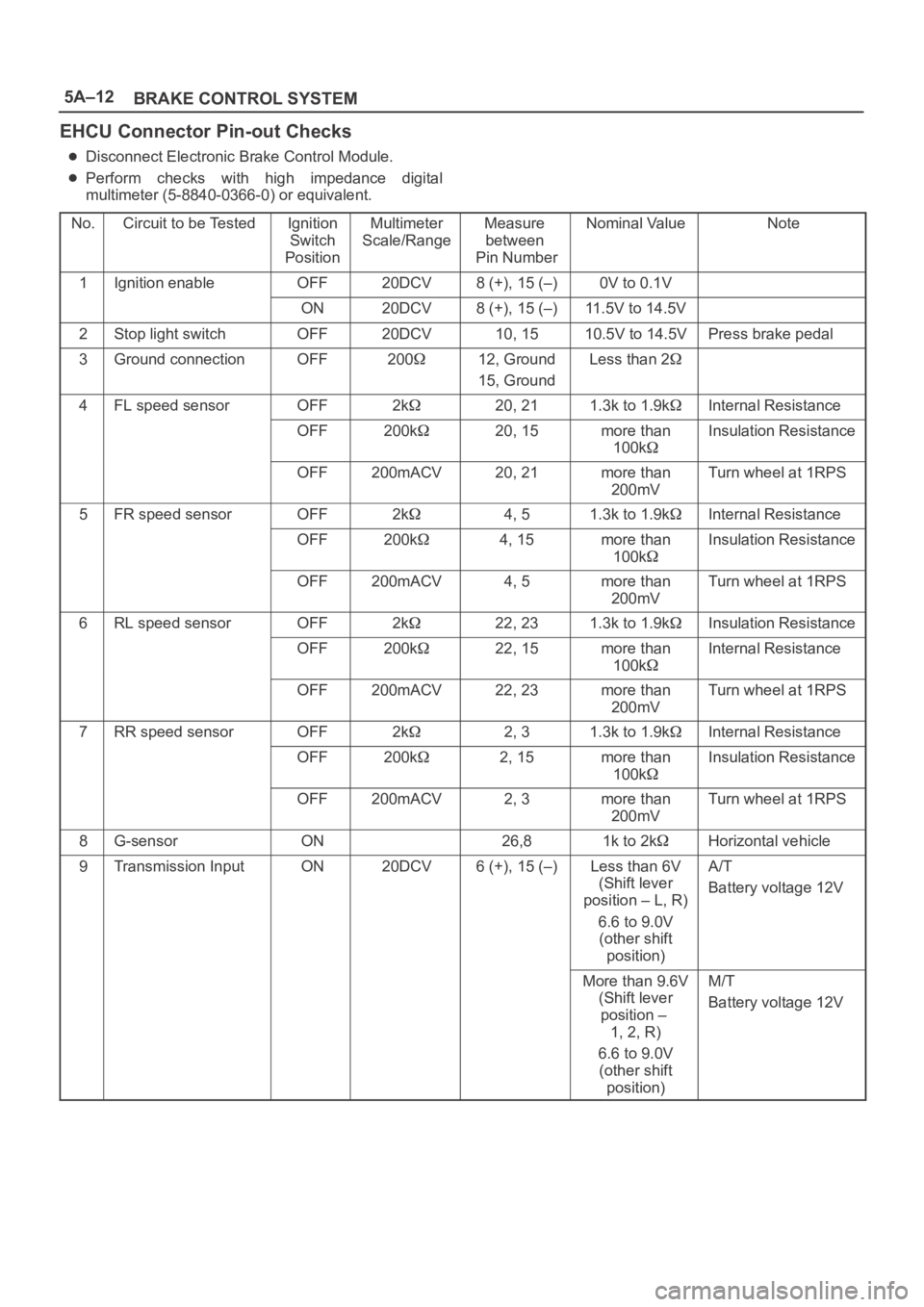
5A–12
BRAKE CONTROL SYSTEM
EHCU Connector Pin-out Checks
Disconnect Electronic Brake Control Module.
Perform checks with high impedance digital
multimeter (5-8840-0366-0) or equivalent.
No.
Circuit to be TestedIgnition
Switch
PositionMultimeter
Scale/RangeMeasure
between
Pin NumberNominal ValueNote
1Ignition enableOFF20DCV8 (+), 15 (–)0V to 0.1V
ON20DCV8 (+), 15 (–)11.5V to 14.5V
2Stop light switchOFF20DCV10, 1510.5V to 14.5VPress brake pedal
3Ground connectionOFF20012, Ground
15, GroundLess than 2
4FL speed sensorOFF2k20, 211.3k to 1.9kInternal Resistance
OFF200k20, 15more than
100kInsulation Resistance
OFF200mACV20, 21more than
200mVTurn wheel at 1RPS
5FR speed sensorOFF2k4, 51.3k to 1.9kInternal Resistance
OFF200k4, 15more than
100kInsulation Resistance
OFF200mACV4, 5more than
200mVTurn wheel at 1RPS
6RL speed sensorOFF2k22, 231.3k to 1.9kInsulation Resistance
OFF200k22, 15more than
100kInternal Resistance
OFF200mACV22, 23more than
200mVTurn wheel at 1RPS
7RR speed sensorOFF2k2, 31.3k to 1.9kInternal Resistance
OFF200k2, 15more than
100kInsulation Resistance
OFF200mACV2, 3more than
200mVTurn wheel at 1RPS
8G-sensorON26,81k to 2kHorizontal vehicle
9Transmission InputON20DCV6 (+), 15 (–)Less than 6V
(Shift lever
position – L, R)
6.6 to 9.0V
(other shift
position)A/T
Battery voltage 12V
More than 9.6V
(Shift lever
position –
1, 2, R)
6.6 to 9.0V
(other shift
position)M/T
Battery voltage 12V
Page 845 of 6000
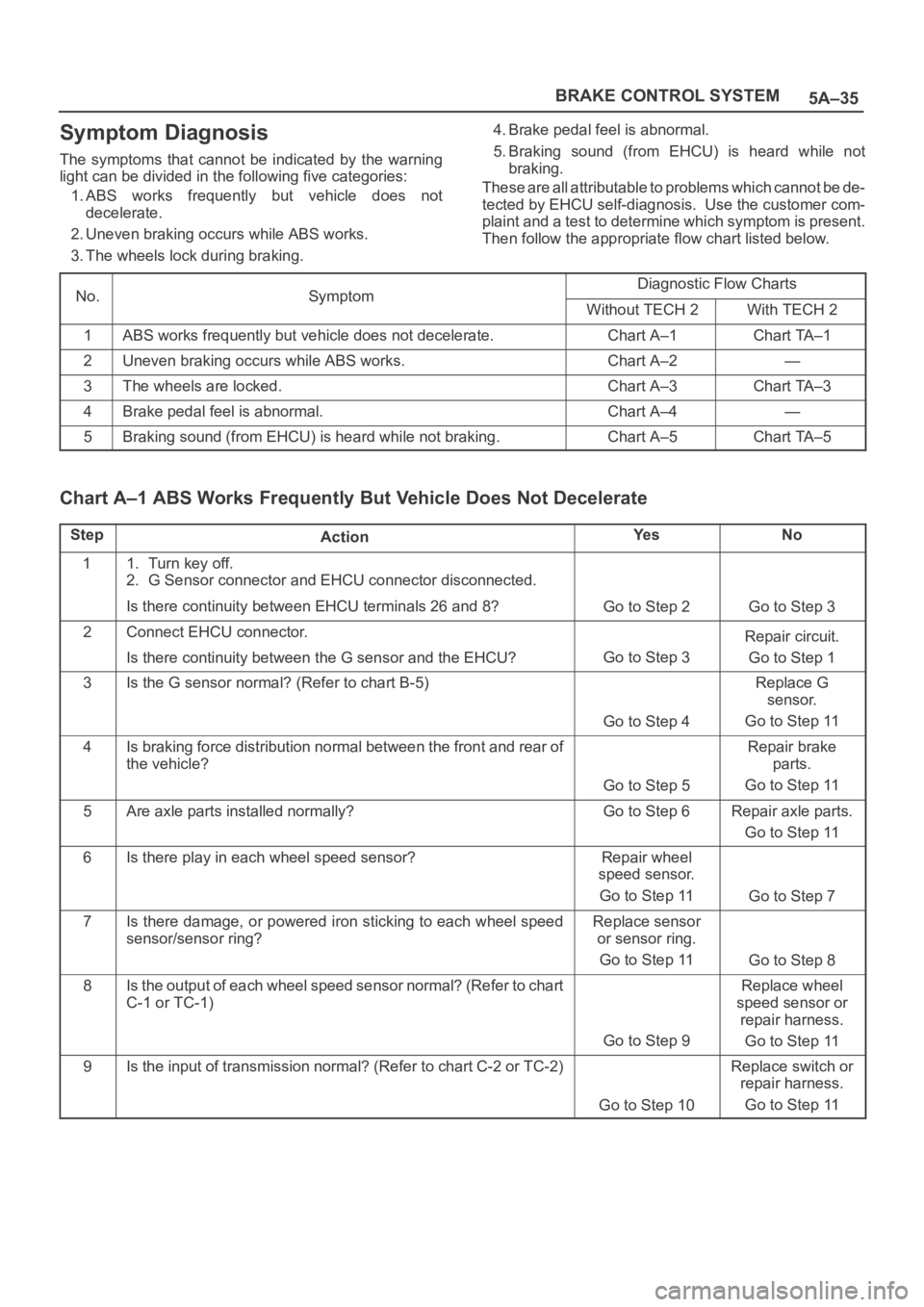
5A–35 BRAKE CONTROL SYSTEM
Symptom Diagnosis
The symptoms that cannot be indicated by the warning
light can be divided in the following five categories:
1. ABS works frequently but vehicle does not
decelerate.
2. Uneven braking occurs while ABS works.
3. The wheels lock during braking.4. Brake pedal feel is abnormal.
5. Braking sound (from EHCU) is heard while not
braking.
These are all attributable to problems which cannot be de-
tected by EHCU self-diagnosis. Use the customer com-
plaint and a test to determine which symptom is present.
Then follow the appropriate flow chart listed below.
NoSymptomDiagnostic Flow ChartsNo.Sym tomWithout TECH 2With TECH 2
1ABS works frequently but vehicle does not decelerate.Chart A–1Chart TA–1
2Uneven braking occurs while ABS works.Chart A–2—
3The wheels are locked.Chart A–3Chart TA–3
4Brake pedal feel is abnormal.Chart A–4—
5Braking sound (from EHCU) is heard while not braking. Chart A–5Chart TA–5
Chart A–1 ABS Works Frequently But Vehicle Does Not Decelerate
StepActionYe sNo
11. Turn key off.
2. G Sensor connector and EHCU connector disconnected.
Is there continuity between EHCU terminals 26 and 8?
Go to Step 2Go to Step 3
2Connect EHCU connector.
Is there continuity between the G sensor and the EHCU?
Go to Step 3
Repair circuit.
Go to Step 1
3Is the G sensor normal? (Refer to chart B-5)
Go to Step 4
Replace G
sensor.
Go to Step 11
4Is braking force distribution normal between the front and rear of
the vehicle?
Go to Step 5
Repair brake
parts.
Go to Step 11
5Are axle parts installed normally?Go to Step 6Repair axle parts.
Go to Step 11
6Is there play in each wheel speed sensor?Repair wheel
speed sensor.
Go to Step 11
Go to Step 7
7Is there damage, or powered iron sticking to each wheel speed
sensor/sensor ring?Replace sensor
or sensor ring.
Go to Step 11
Go to Step 8
8Is the output of each wheel speed sensor normal? (Refer to chart
C-1 or TC-1)
Go to Step 9
Replace wheel
speed sensor or
repair harness.
Go to Step 11
9Is the input of transmission normal? (Refer to chart C-2 or TC-2)
Go to Step 10
Replace switch or
repair harness.
Go to Step 11
Page 846 of 6000
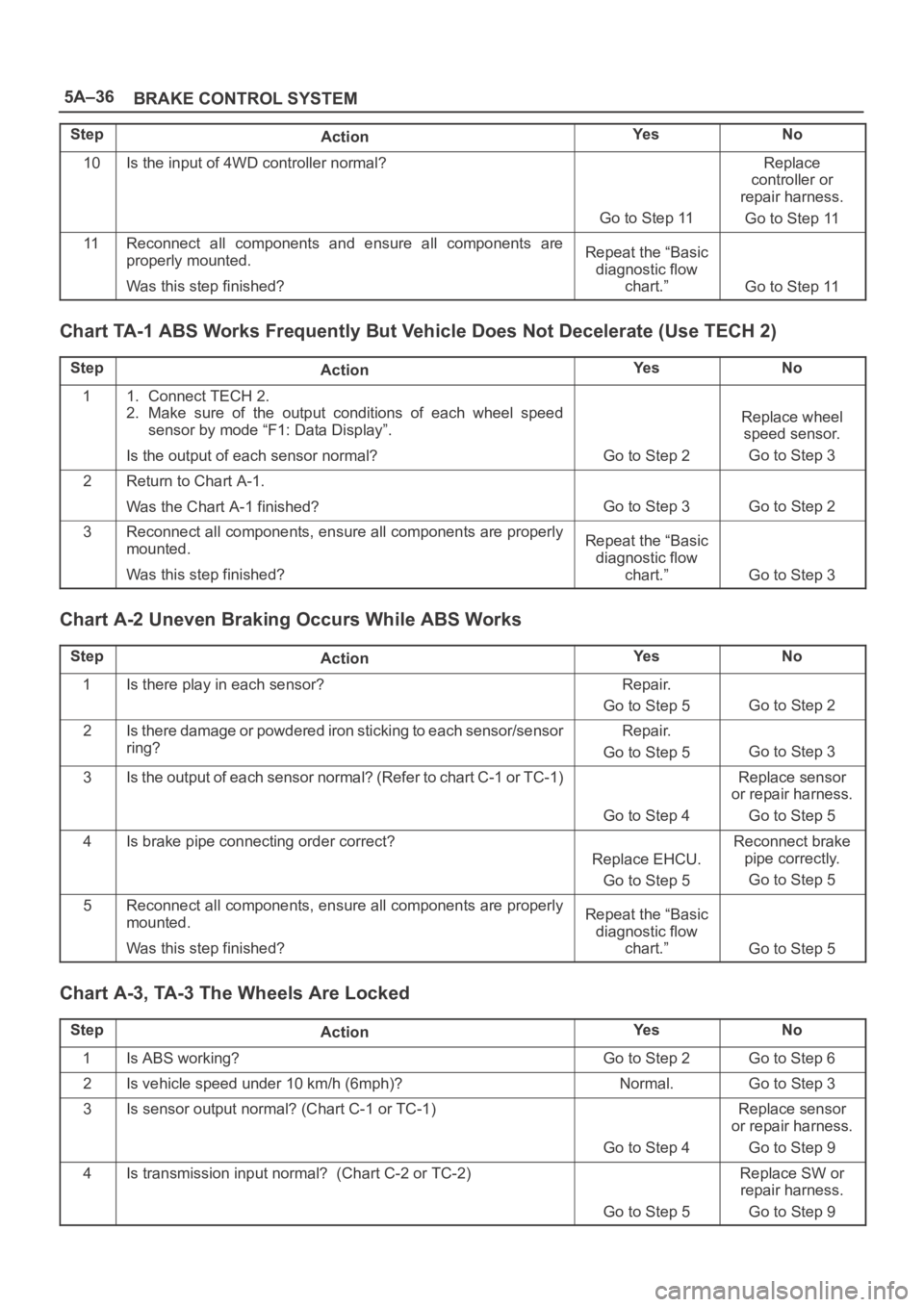
5A–36
BRAKE CONTROL SYSTEM
StepNo Ye s
Action
10Is the input of 4WD controller normal?
Go to Step 11
Replace
controller or
repair harness.
Go to Step 11
11Reconnect all components and ensure all components are
properly mounted.
Was this step finished?Repeat the “Basic
diagnostic flow
chart.”
Go to Step 11
Chart TA-1 ABS Works Frequently But Vehicle Does Not Decelerate (Use TECH 2)
StepActionYe sNo
11. Connect TECH 2.
2. Make sure of the output conditions of each wheel speed
sensor by mode “F1: Data Display”.
Is the output of each sensor normal?
Go to Step 2
Replace wheel
speed sensor.
Go to Step 3
2Return to Chart A-1.
Was the Chart A-1 finished?
Go to Step 3Go to Step 2
3Reconnect all components, ensure all components are properly
mounted.
Was this step finished?Repeat the “Basic
diagnostic flow
chart.”
Go to Step 3
Chart A-2 Uneven Braking Occurs While ABS Works
StepActionYe sNo
1Is there play in each sensor?Repair.
Go to Step 5
Go to Step 2
2Is there damage or powdered iron sticking to each sensor/sensor
ring?Repair.
Go to Step 5
Go to Step 3
3Is the output of each sensor normal? (Refer to chart C-1 or TC-1)
Go to Step 4
Replace sensor
or repair harness.
Go to Step 5
4Is brake pipe connecting order correct?
Replace EHCU.
Go to Step 5
Reconnect brake
pipe correctly.
Go to Step 5
5Reconnect all components, ensure all components are properly
mounted.
Was this step finished?Repeat the “Basic
diagnostic flow
chart.”
Go to Step 5
Chart A-3, TA-3 The Wheels Are Locked
StepActionYe sNo
1Is ABS working?Go to Step 2Go to Step 6
2Is vehicle speed under 10 km/h (6mph)?Normal.Go to Step 3
3Is sensor output normal? (Chart C-1 or TC-1)
Go to Step 4
Replace sensor
or repair harness.
Go to Step 9
4Is transmission input normal? (Chart C-2 or TC-2)
Go to Step 5
Replace SW or
repair harness.
Go to Step 9
Page 848 of 6000
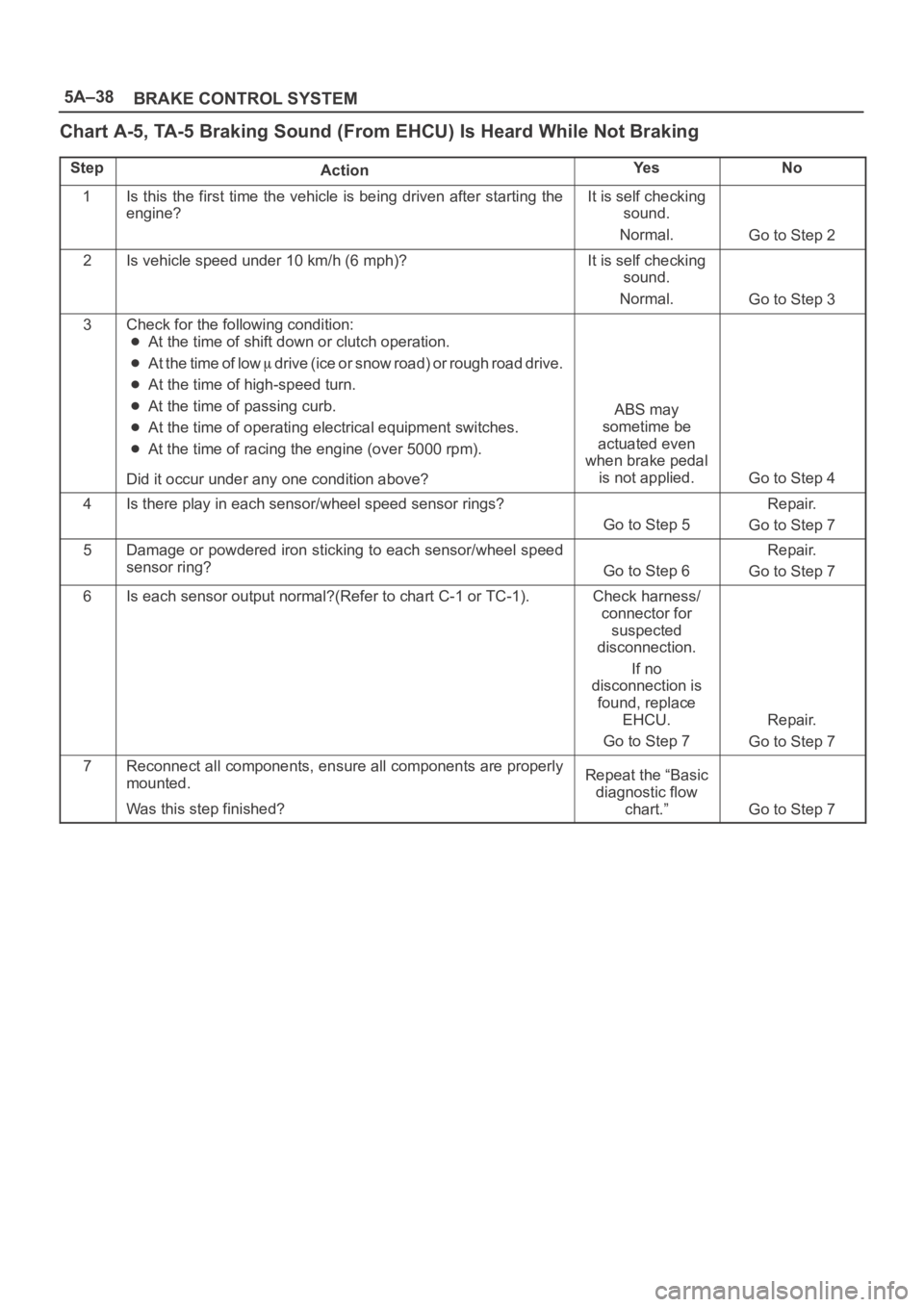
5A–38
BRAKE CONTROL SYSTEM
Chart A-5, TA-5 Braking Sound (From EHCU) Is Heard While Not Braking
StepActionYe sNo
1Is this the first time the vehicle is being driven after starting the
engine?It is self checking
sound.
Normal.
Go to Step 2
2Is vehicle speed under 10 km/h (6 mph)?It is self checking
sound.
Normal.
Go to Step 3
3Check for the following condition:
At the time of shift down or clutch operation.
A t t h e t i m e o f l o w drive (ice or snow road) or rough road drive.
At the time of high-speed turn.
At the time of passing curb.
At the time of operating electrical equipment switches.
At the time of racing the engine (over 5000 rpm).
Did it occur under any one condition above?
ABS may
sometime be
actuated even
when brake pedal
is not applied.
Go to Step 4
4Is there play in each sensor/wheel speed sensor rings?
Go to Step 5
Repair.
Go to Step 7
5Damage or powdered iron sticking to each sensor/wheel speed
sensor ring?
Go to Step 6
Repair.
Go to Step 7
6Is each sensor output normal?(Refer to chart C-1 or TC-1).Check harness/
connector for
suspected
disconnection.
If no
disconnection is
found, replace
EHCU.
Go to Step 7
Repair.
Go to Step 7
7Reconnect all components, ensure all components are properly
mounted.
Was this step finished?Repeat the “Basic
diagnostic flow
chart.”
Go to Step 7
Page 849 of 6000
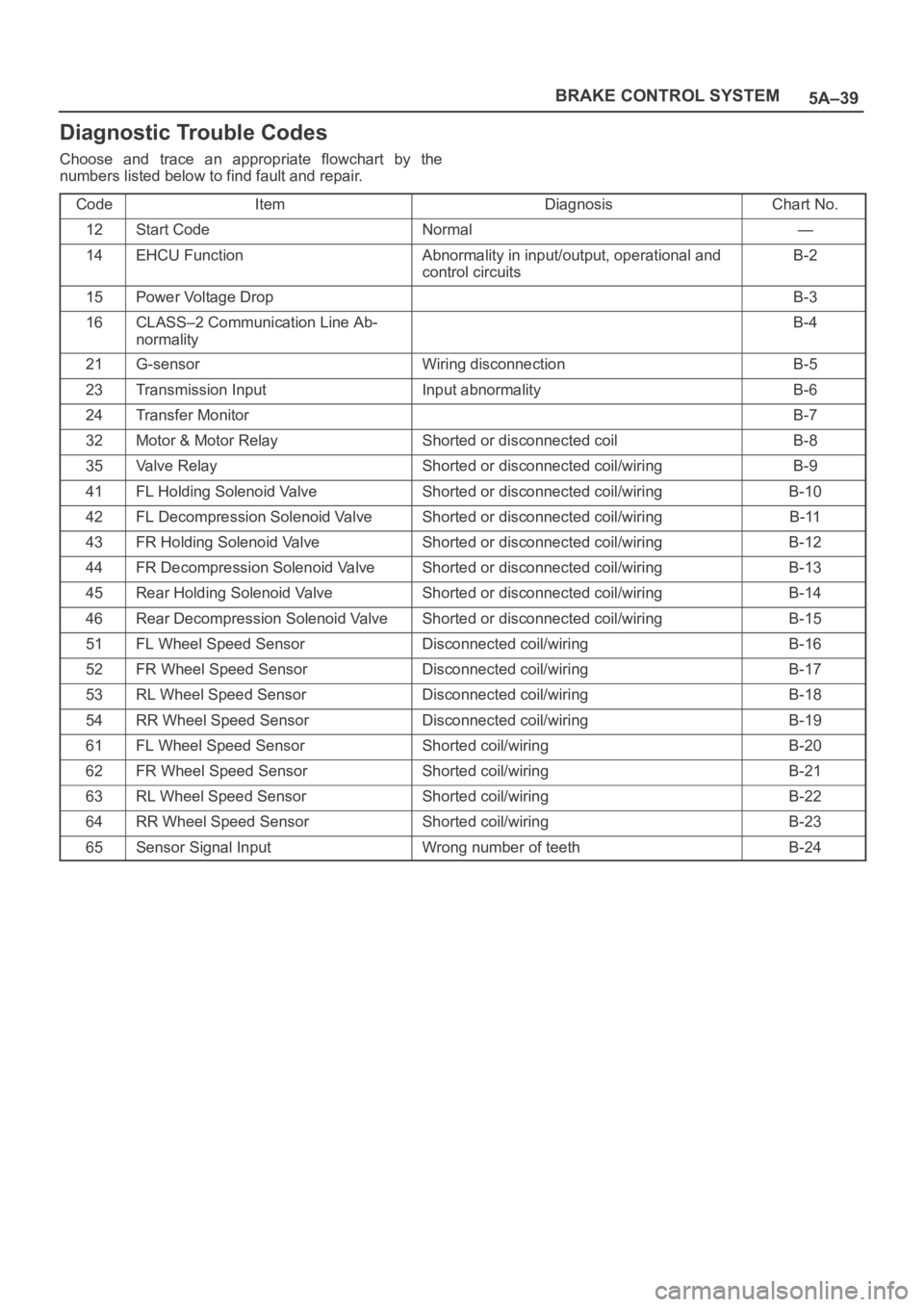
5A–39 BRAKE CONTROL SYSTEM
Diagnostic Trouble Codes
Choose and trace an appropriate flowchart by the
numbers listed below to find fault and repair.
Code
ItemDiagnosisChart No.
12Start CodeNormal—
14EHCU FunctionAbnormality in input/output, operational and
control circuitsB-2
15Power Voltage DropB-3
16CLASS–2 Communication Line Ab-
normalityB-4
21G-sensorWiring disconnectionB-5
23Transmission InputInput abnormalityB-6
24Transfer MonitorB-7
32Motor & Motor RelayShorted or disconnected coilB-8
35Valve RelayShorted or disconnected coil/wiringB-9
41FL Holding Solenoid ValveShorted or disconnected coil/wiringB-10
42FL Decompression Solenoid ValveShorted or disconnected coil/wiringB-11
43FR Holding Solenoid ValveShorted or disconnected coil/wiringB-12
44FR Decompression Solenoid ValveShorted or disconnected coil/wiringB-13
45Rear Holding Solenoid ValveShorted or disconnected coil/wiringB-14
46Rear Decompression Solenoid ValveShorted or disconnected coil/wiringB-15
51FL Wheel Speed SensorDisconnected coil/wiringB-16
52FR Wheel Speed SensorDisconnected coil/wiringB-17
53RL Wheel Speed SensorDisconnected coil/wiringB-18
54RR Wheel Speed SensorDisconnected coil/wiringB-19
61FL Wheel Speed SensorShorted coil/wiringB-20
62FR Wheel Speed SensorShorted coil/wiringB-21
63RL Wheel Speed SensorShorted coil/wiringB-22
64RR Wheel Speed SensorShorted coil/wiringB-23
65Sensor Signal InputWrong number of teethB-24
Page 855 of 6000
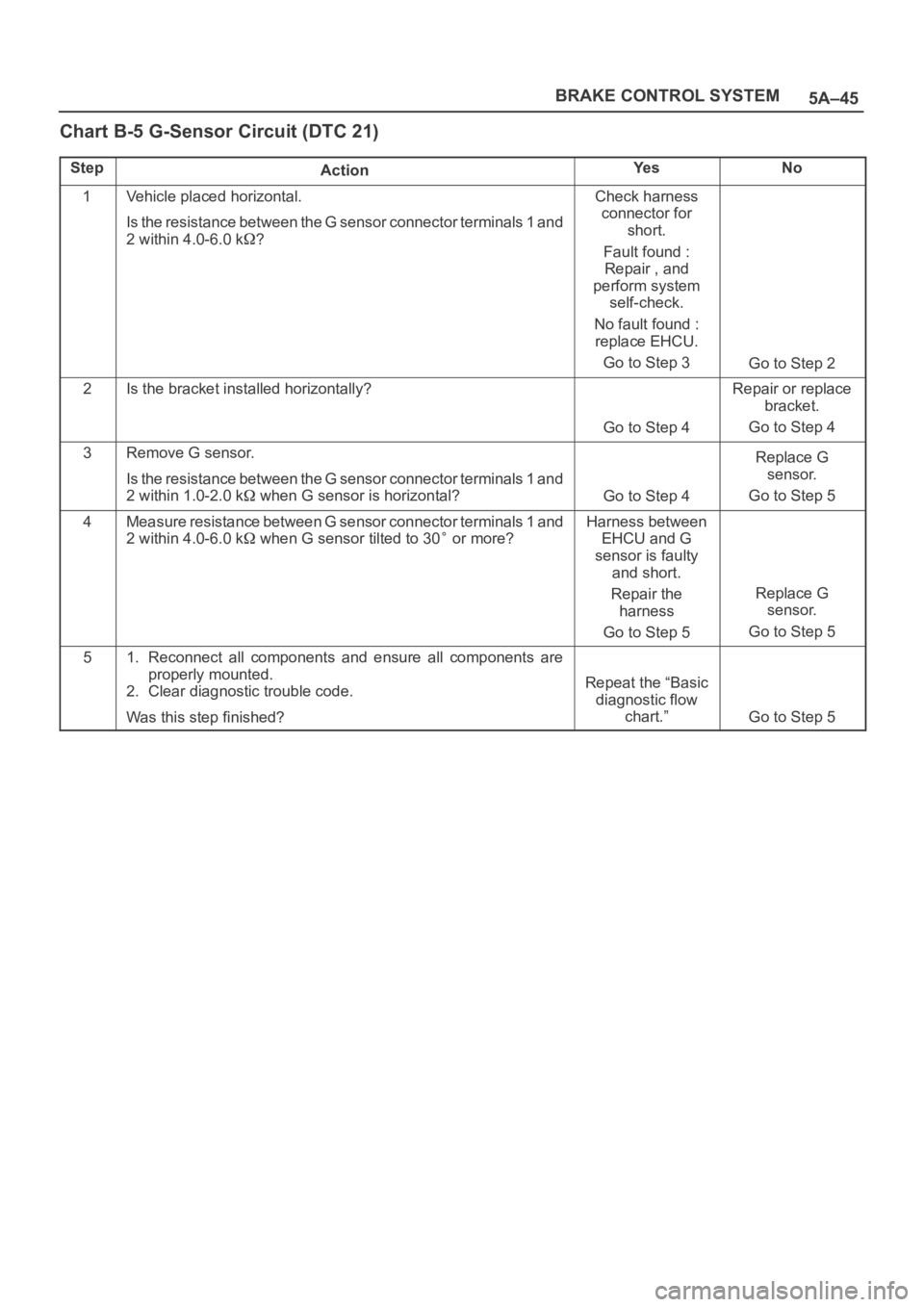
5A–45 BRAKE CONTROL SYSTEM
Chart B-5 G-Sensor Circuit (DTC 21)
StepActionYe sNo
1Vehicle placed horizontal.
Is the resistance between the G sensor connector terminals 1 and
2 within 4.0-6.0 k
?
Check harness
connector for
short.
Fault found :
Repair , and
perform system
self-check.
No fault found :
replace EHCU.
Go to Step 3
Go to Step 2
2Is the bracket installed horizontally?
Go to Step 4
Repair or replace
bracket.
Go to Step 4
3Remove G sensor.
Is the resistance between the G sensor connector terminals 1 and
2 within 1.0-2.0 k
when G sensor is horizontal?Go to Step 4
Replace G
sensor.
Go to Step 5
4Measure resistance between G sensor connector terminals 1 and
2 within 4.0-6.0 k
when G sensor tilted to 30 or more?
Harness between
EHCU and G
sensor is faulty
and short.
Repair the
harness
Go to Step 5
Replace G
sensor.
Go to Step 5
51. Reconnect all components and ensure all components are
properly mounted.
2. Clear diagnostic trouble code.
Was this step finished?
Repeat the “Basic
diagnostic flow
chart.”
Go to Step 5
Page 860 of 6000
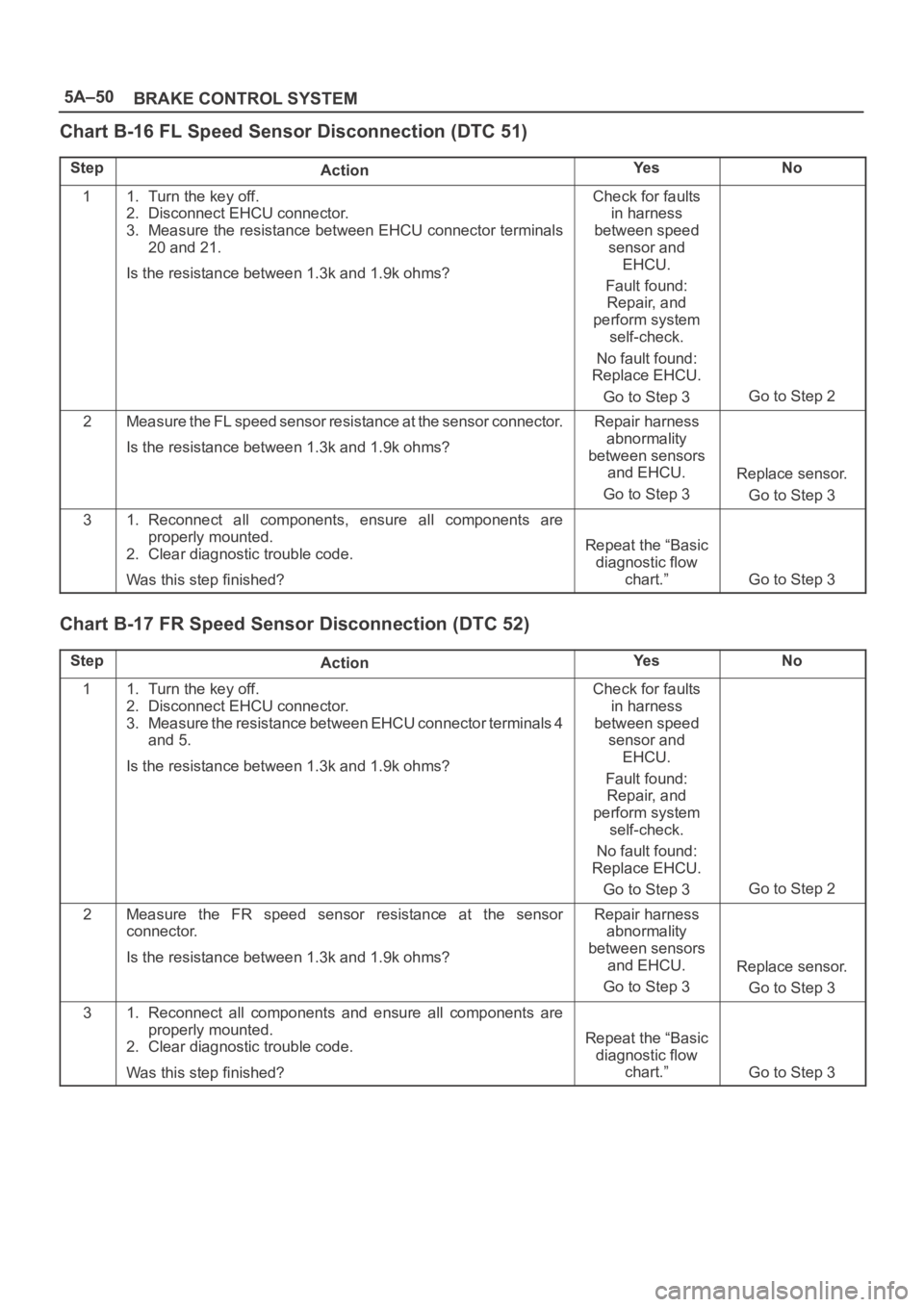
5A–50
BRAKE CONTROL SYSTEM
Chart B-16 FL Speed Sensor Disconnection (DTC 51)
StepActionYe sNo
11. Turn the key off.
2. Disconnect EHCU connector.
3. Measure the resistance between EHCU connector terminals
20 and 21.
Is the resistance between 1.3k and 1.9k ohms?Check for faults
in harness
between speed
sensor and
EHCU.
Fault found:
Repair, and
perform system
self-check.
No fault found:
Replace EHCU.
Go to Step 3
Go to Step 2
2Measure the FL speed sensor resistance at the sensor connector.
Is the resistance between 1.3k and 1.9k ohms?Repair harness
abnormality
between sensors
and EHCU.
Go to Step 3
Replace sensor.
Go to Step 3
31. Reconnect all components, ensure all components are
properly mounted.
2. Clear diagnostic trouble code.
Was this step finished?
Repeat the “Basic
diagnostic flow
chart.”
Go to Step 3
Chart B-17 FR Speed Sensor Disconnection (DTC 52)
StepActionYe sNo
11. Turn the key off.
2. Disconnect EHCU connector.
3. Measure the resistance between EHCU connector terminals 4
and 5.
Is the resistance between 1.3k and 1.9k ohms?Check for faults
in harness
between speed
sensor and
EHCU.
Fault found:
Repair, and
perform system
self-check.
No fault found:
Replace EHCU.
Go to Step 3
Go to Step 2
2Measure the FR speed sensor resistance at the sensor
connector.
Is the resistance between 1.3k and 1.9k ohms?Repair harness
abnormality
between sensors
and EHCU.
Go to Step 3
Replace sensor.
Go to Step 3
31. Reconnect all components and ensure all components are
properly mounted.
2. Clear diagnostic trouble code.
Was this step finished?
Repeat the “Basic
diagnostic flow
chart.”
Go to Step 3