check engine OPEL GT-R 1973 Workshop Manual
[x] Cancel search | Manufacturer: OPEL, Model Year: 1973, Model line: GT-R, Model: OPEL GT-R 1973Pages: 625, PDF Size: 17.22 MB
Page 367 of 625
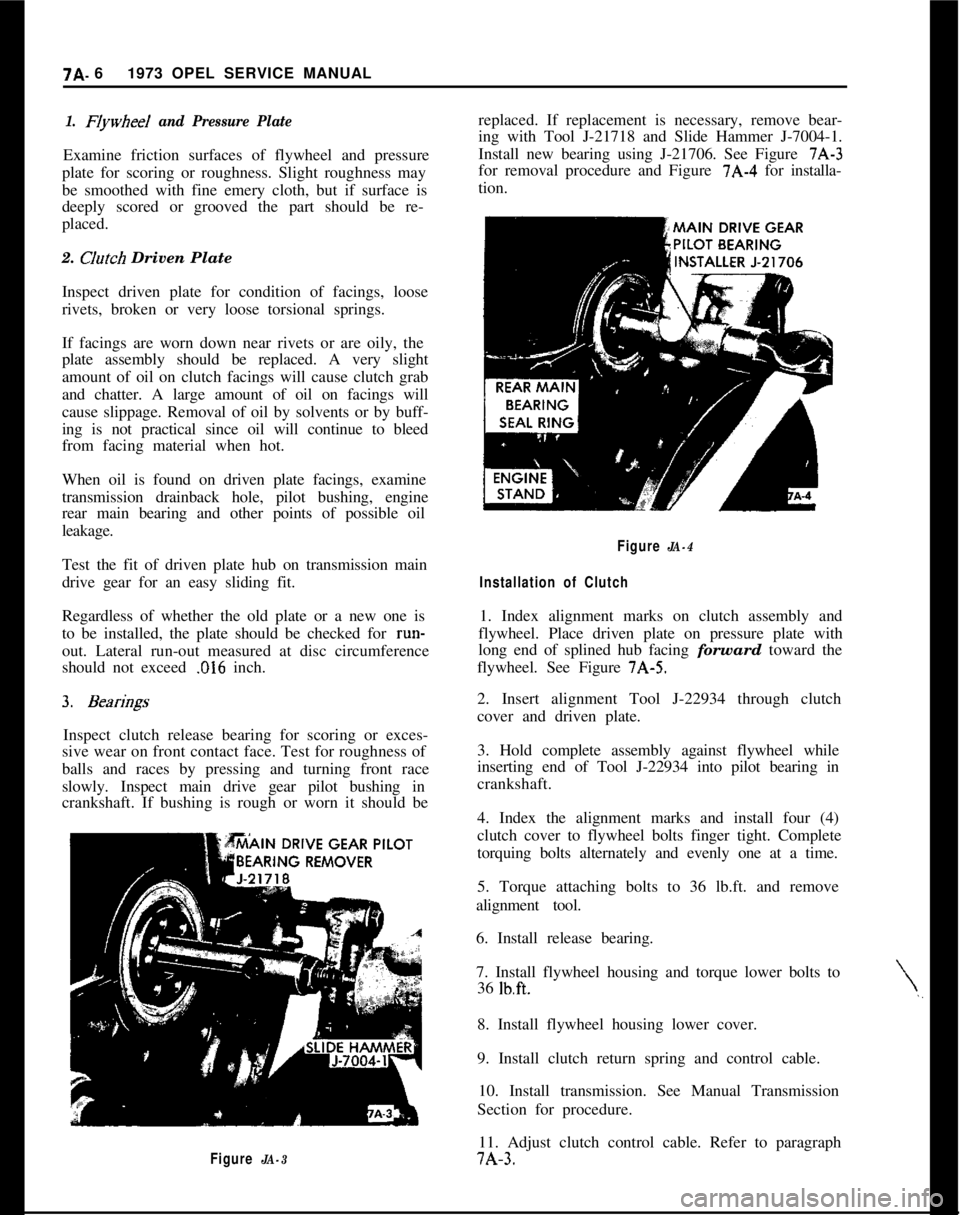
7A- 61973 OPEL SERVICE MANUAL1. FIywheeI and Pressure PlateExamine friction surfaces of flywheel and pressure
plate for scoring or roughness. Slight roughness may
be smoothed with fine emery cloth, but if surface is
deeply scored or grooved the part should be re-
placed.
2.
CJutch Driven Plate
Inspect driven plate for condition of facings, loose
rivets, broken or very loose torsional springs.
If facings are worn down near rivets or are oily, the
plate assembly should be replaced. A very slight
amount of oil on clutch facings will cause clutch grab
and chatter. A large amount of oil on facings will
cause slippage. Removal of oil by solvents or by buff-
ing is not practical since oil will continue to bleed
from facing material when hot.
When oil is found on driven plate facings, examine
transmission drainback hole, pilot bushing, engine
rear main bearing and other points of possible oil
leakage.
Test the fit of driven plate hub on transmission main
drive gear for an easy sliding fit.
Regardless of whether the old plate or a new one is
to be installed, the plate should be checked for run-
out. Lateral run-out measured at disc circumference
should not exceed
.016 inch.
Inspect clutch release bearing for scoring or exces-
sive wear on front contact face. Test for roughness of
balls and races by pressing and turning front race
slowly. Inspect main drive gear pilot bushing in
crankshaft. If bushing is rough or worn it should be
Figure JA-3replaced. If replacement is necessary, remove bear-
ing with Tool J-21718 and Slide Hammer J-7004-1.
Install new bearing using J-21706. See Figure 7A-3
for removal procedure and Figure 7A-4 for installa-
tion.
\,,
Figure JA-4
Installation of Clutch1. Index alignment marks on clutch assembly and
flywheel. Place driven plate on pressure plate with
long end of splined hub facing forward toward the
flywheel. See Figure 7A-5.
2. Insert alignment Tool J-22934 through clutch
cover and driven plate.
3. Hold complete assembly against flywheel while
inserting end of Tool J-22934 into pilot bearing in
crankshaft.
4. Index the alignment marks and install four (4)
clutch cover to flywheel bolts finger tight. Complete
torquing bolts alternately and evenly one at a time.
5. Torque attaching bolts to 36 lb.ft. and remove
alignment tool.
6. Install release bearing.
7. Install flywheel housing and torque lower bolts to
36
lb.ft.8. Install flywheel housing lower cover.
9. Install clutch return spring and control cable.
10. Install transmission. See Manual Transmission
Section for procedure.
11. Adjust clutch control cable. Refer to paragraph7A-3.
Page 417 of 625
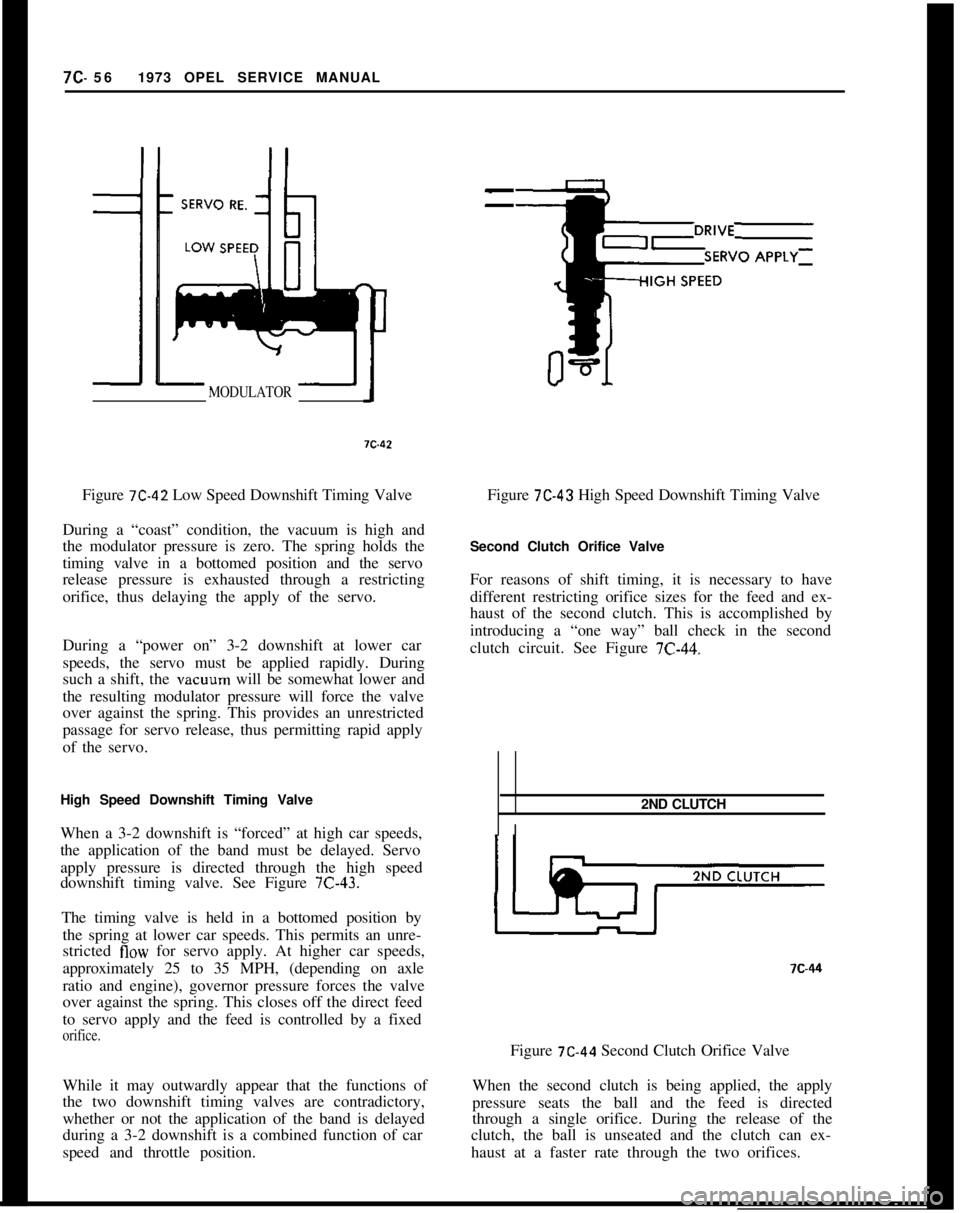
7C- 561973 OPEL SERVICE MANUALMODULATORFigure
7C-42 Low Speed Downshift Timing Valve
During a “coast” condition, the vacuum is high and
the modulator pressure is zero. The spring holds the
timing valve in a bottomed position and the servo
release pressure is exhausted through a restricting
orifice, thus delaying the apply of the servo.
During a “power on” 3-2 downshift at lower car
speeds, the servo must be applied rapidly. During
such a shift, the vacuum will be somewhat lower and
the resulting modulator pressure will force the valve
over against the spring. This provides an unrestricted
passage for servo release, thus permitting rapid apply
of the servo.
High Speed Downshift Timing Valve
When a 3-2 downshift is “forced” at high car speeds,
the application of the band must be delayed. Servo
apply pressure is directed through the high speed
downshift timing valve. See Figure
7C-43.The timing valve is held in a bottomed position by
the spring at lower car speeds. This permits an unre-
stricted
flow for servo apply. At higher car speeds,
approximately 25 to 35 MPH, (depending on axle
ratio and engine), governor pressure forces the valve
over against the spring. This closes off the direct feed
to servo apply and the feed is controlled by a fixed
orifice.While it may outwardly appear that the functions of
the two downshift timing valves are contradictory,
whether or not the application of the band is delayed
during a 3-2 downshift is a combined function of car
speed and throttle position.
--Figure
7C-43 High Speed Downshift Timing Valve
Second Clutch Orifice Valve
For reasons of shift timing, it is necessary to have
different restricting orifice sizes for the feed and ex-
haust of the second clutch. This is accomplished by
introducing a “one way” ball check in the second
clutch circuit. See Figure
7C-44.2ND CLUTCH
I?C-44
Figure
7C-44 Second Clutch Orifice Valve
When the second clutch is being applied, the apply
pressure seats the ball and the feed is directed
through a single orifice. During the release of the
clutch, the ball is unseated and the clutch can ex-
haust at a faster rate through the two orifices.
Page 442 of 625
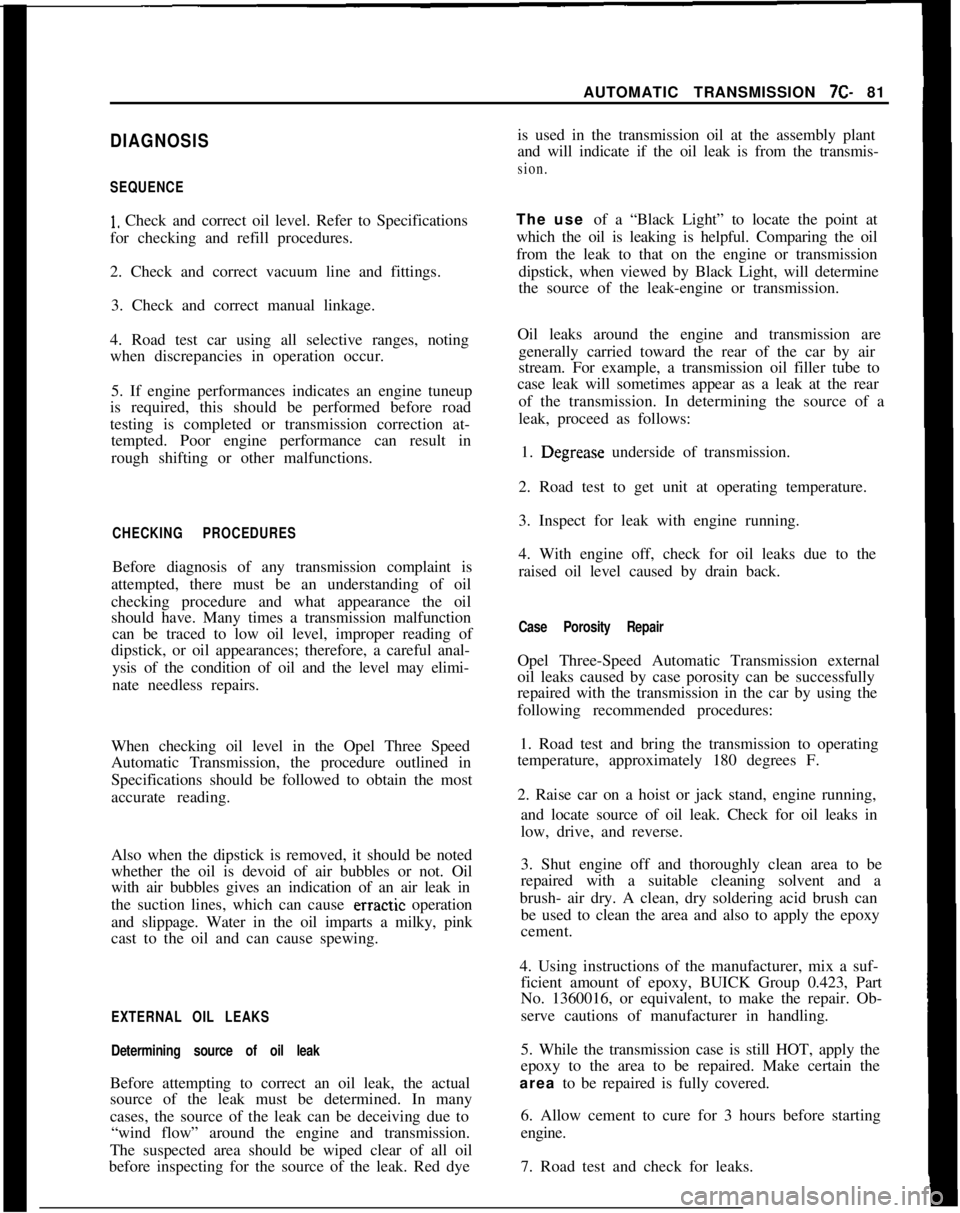
DIAGNOSIS
SEQUENCE
1. Check and correct oil level. Refer to Specifications
for checking and refill procedures.
2. Check and correct vacuum line and fittings.
3. Check and correct manual linkage.
4. Road test car using all selective ranges, noting
when discrepancies in operation occur.
5. If engine performances indicates an engine tuneup
is required, this should be performed before road
testing is completed or transmission correction at-
tempted. Poor engine performance can result in
rough shifting or other malfunctions.
CHECKING PROCEDURESBefore diagnosis of any transmission complaint is
attempted, there must be an understanding of oil
checking procedure and what appearance the oil
should have. Many times a transmission malfunction
can be traced to low oil level, improper reading of
dipstick, or oil appearances; therefore, a careful anal-
ysis of the condition of oil and the level may elimi-
nate needless repairs.
When checking oil level in the Opel Three Speed
Automatic Transmission, the procedure outlined in
Specifications should be followed to obtain the most
accurate reading.
Also when the dipstick is removed, it should be noted
whether the oil is devoid of air bubbles or not. Oil
with air bubbles gives an indication of an air leak in
the suction lines, which can cause erractic operation
and slippage. Water in the oil imparts a milky, pink
cast to the oil and can cause spewing.
EXTERNAL OIL LEAKS
Determining source of oil leakBefore attempting to correct an oil leak, the actual
source of the leak must be determined. In many
cases, the source of the leak can be deceiving due to
“wind flow” around the engine and transmission.
The suspected area should be wiped clear of all oil
before inspecting for the source of the leak. Red dyeAUTOMATIC TRANSMISSION 7C- 81
is used in the transmission oil at the assembly plant
and will indicate if the oil leak is from the transmis-
sion.The use of a “Black Light” to locate the point at
which the oil is leaking is helpful. Comparing the oil
from the leak to that on the engine or transmission
dipstick, when viewed by Black Light, will determine
the source of the leak-engine or transmission.
Oil leaks around the engine and transmission are
generally carried toward the rear of the car by air
stream. For example, a transmission oil filler tube to
case leak will sometimes appear as a leak at the rear
of the transmission. In determining the source of a
leak, proceed as follows:
1. Degrease underside of transmission.
2. Road test to get unit at operating temperature.
3. Inspect for leak with engine running.
4. With engine off, check for oil leaks due to the
raised oil level caused by drain back.
Case Porosity RepairOpel Three-Speed Automatic Transmission external
oil leaks caused by case porosity can be successfully
repaired with the transmission in the car by using the
following recommended procedures:
1. Road test and bring the transmission to operating
temperature, approximately 180 degrees F.
2. Raise car on a hoist or jack stand, engine running,
and locate source of oil leak. Check for oil leaks in
low, drive, and reverse.
3. Shut engine off and thoroughly clean area to be
repaired with a suitable cleaning solvent and a
brush- air dry. A clean, dry soldering acid brush can
be used to clean the area and also to apply the epoxy
cement.
4. Using instructions of the manufacturer, mix a suf-
ficient amount of epoxy, BUICK Group 0.423, Part
No. 1360016, or equivalent, to make the repair. Ob-
serve cautions of manufacturer in handling.
5. While the transmission case is still HOT, apply the
epoxy to the area to be repaired. Make certain the
area to be repaired is fully covered.
6. Allow cement to cure for 3 hours before starting
engine.
7. Road test and check for leaks.
Page 447 of 625
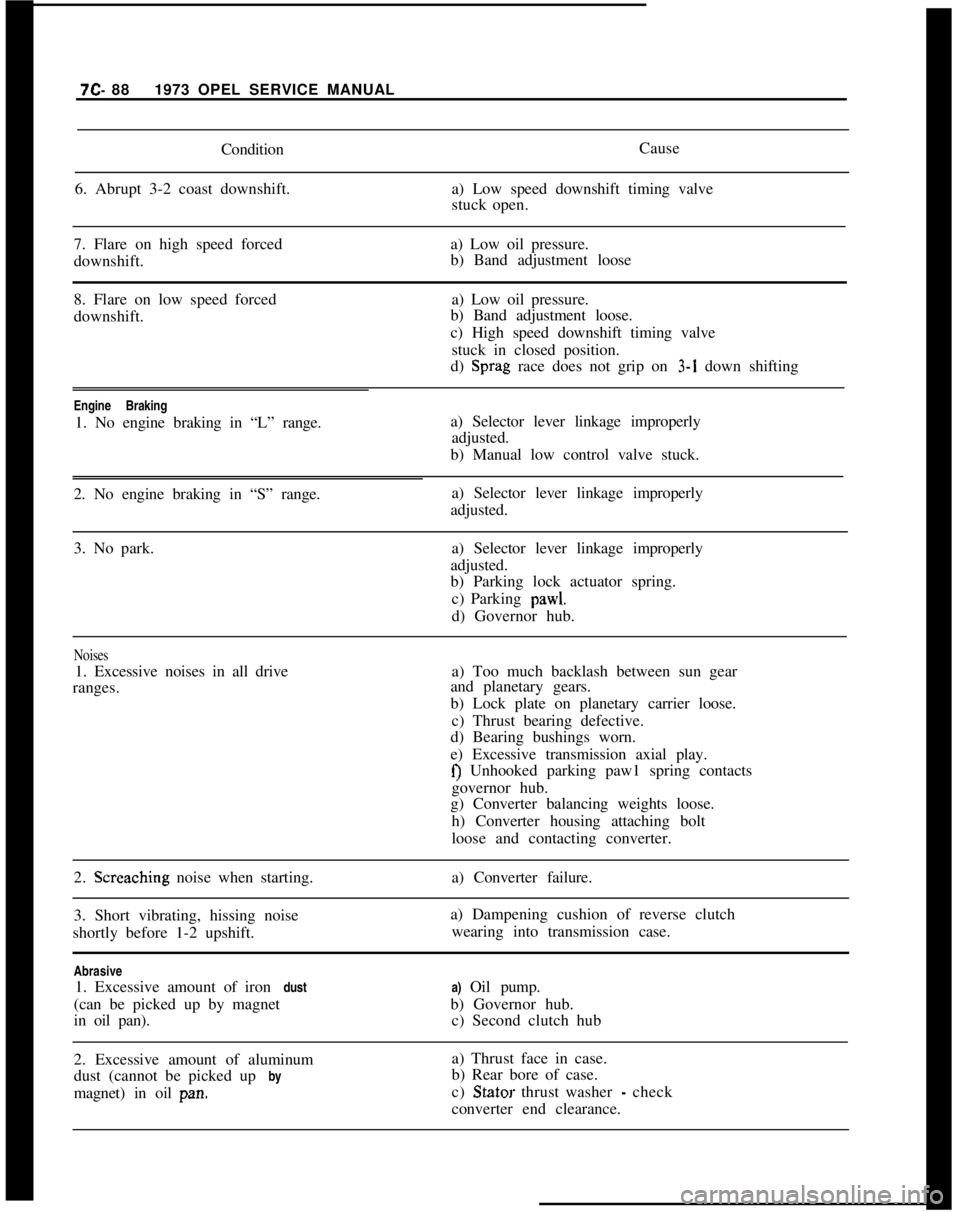
7C- 881973 OPEL SERVICE MANUAL
Condition
6. Abrupt 3-2 coast downshift.Cause
a) Low speed downshift timing valve
stuck open.
7. Flare on high speed forceda) Low oil pressure.
downshift.b) Band adjustment loose
8. Flare on low speed forced
downshift.a) Low oil pressure.
b) Band adjustment loose.
c) High speed downshift timing valve
stuck in closed position.
d) Sprag race does not grip on 3-1 down shifting
Engine Braking
1. No engine braking in “L” range.a) Selector lever linkage improperly
adjusted.
b) Manual low control valve stuck.
2. No engine braking in “S” range.a) Selector lever linkage improperly
adjusted.
3. No park.a) Selector lever linkage improperly
adjusted.
b) Parking lock actuator spring.
c) Parking pawl.
d) Governor hub.
Noises1. Excessive noises in all drive
ranges.a) Too much backlash between sun gear
and planetary gears.
b) Lock plate on planetary carrier loose.
c) Thrust bearing defective.
d) Bearing bushings worn.
e) Excessive transmission axial play.
f) Unhooked parking paw1 spring contacts
governor hub.
g) Converter balancing weights loose.
h) Converter housing attaching bolt
loose and contacting converter.
2. Screaching noise when starting.
3. Short vibrating, hissing noise
shortly before 1-2 upshift.a) Converter failure.
a) Dampening cushion of reverse clutch
wearing into transmission case.
Abrasive
1. Excessive amount of iron dust
(can be picked up by magnet
in oil pan).a) Oil pump.
b) Governor hub.
c) Second clutch hub
2. Excessive amount of aluminum
dust (cannot be picked up by
magnet) in oil pan.a) Thrust face in case.
b) Rear bore of case.
c) Stator thrust washer
- check
converter end clearance.
Page 456 of 625
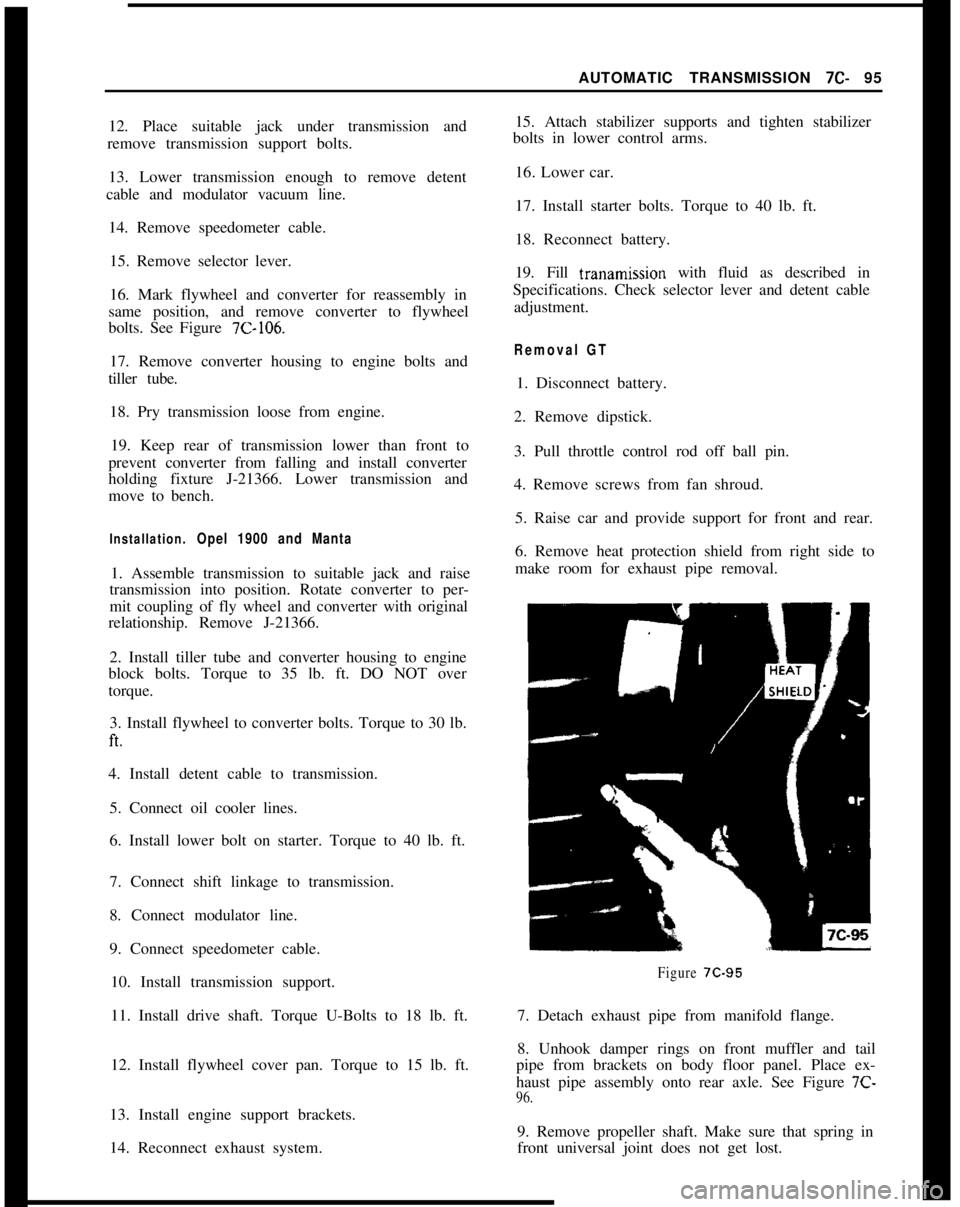
AUTOMATIC TRANSMISSION 7C- 95
12. Place suitable jack under transmission and
remove transmission support bolts.
13. Lower transmission enough to remove detent
cable and modulator vacuum line.
14. Remove speedometer cable.
15. Remove selector lever.
16. Mark flywheel and converter for reassembly in
same position, and remove converter to flywheel
bolts. See Figure 7C-106.17. Remove converter housing to engine bolts and
tiller tube.
18. Pry transmission loose from engine.
19. Keep rear of transmission lower than front to
prevent converter from falling and install converter
holding fixture J-21366. Lower transmission and
move to bench.
Installation. Opel 1900 and Manta1. Assemble transmission to suitable jack and raise
transmission into position. Rotate converter to per-
mit coupling of fly wheel and converter with original
relationship. Remove J-21366.
2. Install tiller tube and converter housing to engine
block bolts. Torque to 35 lb. ft. DO NOT over
torque.
3. Install flywheel to converter bolts. Torque to 30 lb.
ft.4. Install detent cable to transmission.
5. Connect oil cooler lines.
6. Install lower bolt on starter. Torque to 40 lb. ft.
7. Connect shift linkage to transmission.
8. Connect modulator line.
9. Connect speedometer cable.
10. Install transmission support.
11. Install drive shaft. Torque U-Bolts to 18 lb. ft.
12. Install flywheel cover pan. Torque to 15 lb. ft.
13. Install engine support brackets.
14. Reconnect exhaust system.15. Attach stabilizer supports and tighten stabilizer
bolts in lower control arms.
16. Lower car.
17. Install starter bolts. Torque to 40 lb. ft.
18. Reconnect battery.
19. Fill transmission with fluid as described in
Specifications. Check selector lever and detent cable
adjustment.
Removal GT1. Disconnect battery.
2. Remove dipstick.
3. Pull throttle control rod off ball pin.
4. Remove screws from fan shroud.
5. Raise car and provide support for front and rear.
6. Remove heat protection shield from right side to
make room for exhaust pipe removal.
Figure 7C-957. Detach exhaust pipe from manifold flange.
8. Unhook damper rings on front muffler and tail
pipe from brackets on body floor panel. Place ex-
haust pipe assembly onto rear axle. See Figure 7C-
96.9. Remove propeller shaft. Make sure that spring in
front universal joint does not get lost.
Page 459 of 625
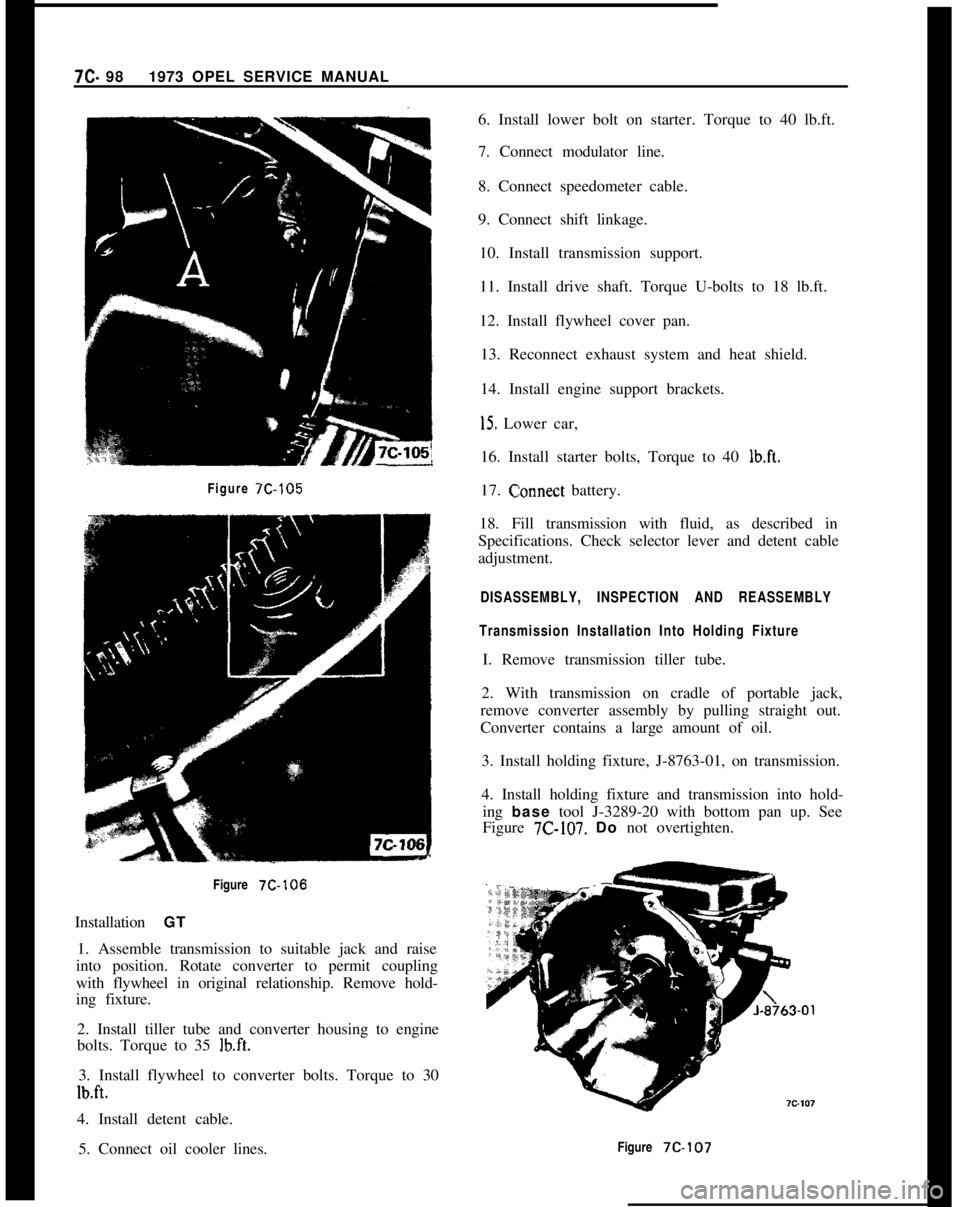
7C- 981973 OPEL SERVICE MANUAL
Figure 7C-105Figure
7C-106Installation GT
1. Assemble transmission to suitable jack and raise
into position. Rotate converter to permit coupling
with flywheel in original relationship. Remove hold-
ing fixture.
2. Install tiller tube and converter housing to engine
bolts. Torque to 35
lb.ft.3. Install flywheel to converter bolts. Torque to 30
lb.ft.4. Install detent cable.
5. Connect oil cooler lines.6. Install lower bolt on starter. Torque to 40 lb.ft.
7. Connect modulator line.
8. Connect speedometer cable.
9. Connect shift linkage.
10. Install transmission support.
11. Install drive shaft. Torque U-bolts to 18 lb.ft.
12. Install flywheel cover pan.
13. Reconnect exhaust system and heat shield.
14. Install engine support brackets.
15. Lower car,
16. Install starter bolts, Torque to 40
lb.ft.17.
C:onnect battery.
18. Fill transmission with fluid, as described in
Specifications. Check selector lever and detent cable
adjustment.
DISASSEMBLY, INSPECTION AND REASSEMBLY
Transmission Installation Into Holding FixtureI. Remove transmission tiller tube.
2. With transmission on cradle of portable jack,
remove converter assembly by pulling straight out.
Converter contains a large amount of oil.
3. Install holding fixture, J-8763-01, on transmission.
4. Install holding fixture and transmission into hold-
ing base tool J-3289-20 with bottom pan up. See
Figure
7C-107. Do not overtighten.
Figure
7C-107
Page 495 of 625
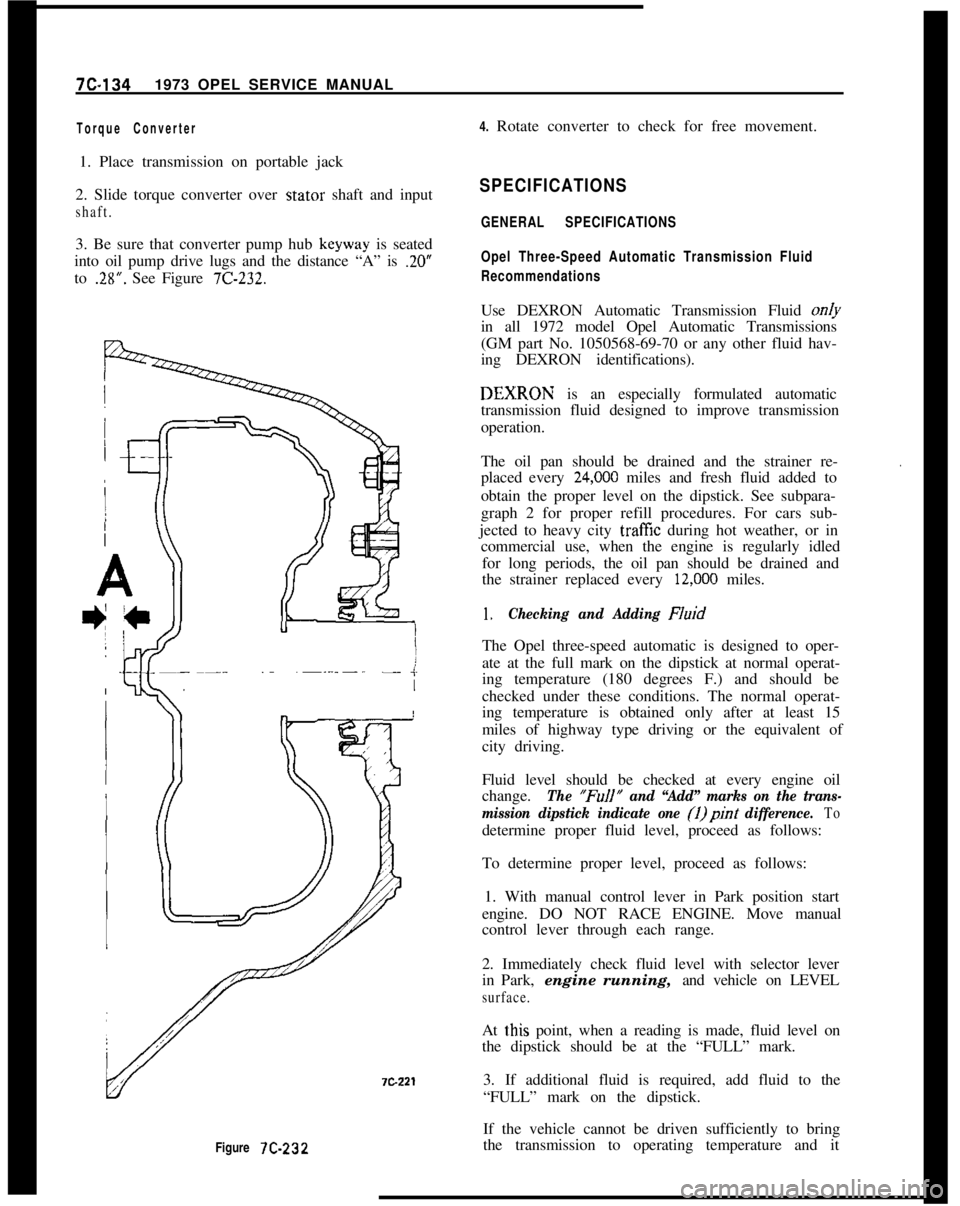
7C-1341973 OPEL SERVICE MANUAL
Figure 7C-232
Torque Converter4. Rotate converter to check for free movement.
1. Place transmission on portable jack
2. Slide torque converter over stator shaft and input
shaft.3. Be sure that converter pump hub keyway is seated
into oil pump drive lugs and the distance “A” is
.20”to
.28”. See Figure 7C-232.
SPECIFICATIONS
GENERAL SPECIFICATIONS
Opel Three-Speed Automatic Transmission Fluid
RecommendationsUse DEXRON Automatic Transmission Fluid on/y
in all 1972 model Opel Automatic Transmissions
(GM part No. 1050568-69-70 or any other fluid hav-
ing DEXRON identifications).DEXIRON is an especially formulated automatic
transmission fluid designed to improve transmission
operation.
The oil pan should be drained and the strainer re-
placed every
24,ooO miles and fresh fluid added to
obtain the proper level on the dipstick. See subpara-
graph 2 for proper refill procedures. For cars sub-
jected to heavy city
traff%z during hot weather, or in
commercial use, when the engine is regularly idled
for long periods, the oil pan should be drained and
the strainer replaced every
12,ooO miles.
.
1.Checking and Adding FluidThe Opel three-speed automatic is designed to oper-
ate at the full mark on the dipstick at normal operat-
ing temperature (180 degrees F.) and should be
checked under these conditions. The normal operat-
ing temperature is obtained only after at least 15
miles of highway type driving or the equivalent of
city driving.
Fluid level should be checked at every engine oil
change.
The “FuIl” and “Add” marks on the trans-
mission dipstick indicate one (1)pint
difference. Todetermine proper fluid level, proceed as follows:
To determine proper level, proceed as follows:
1. With manual control lever in Park position start
engine. DO NOT RACE ENGINE. Move manual
control lever through each range.
2. Immediately check fluid level with selector lever
in Park, engine running, and vehicle on LEVEL
surface.At
t,his point, when a reading is made, fluid level on
the dipstick should be at the “FULL” mark.
3. If additional fluid is required, add fluid to the
“FULL” mark on the dipstick.
If the vehicle cannot be driven sufficiently to bring
the transmission to operating temperature and it
Page 496 of 625
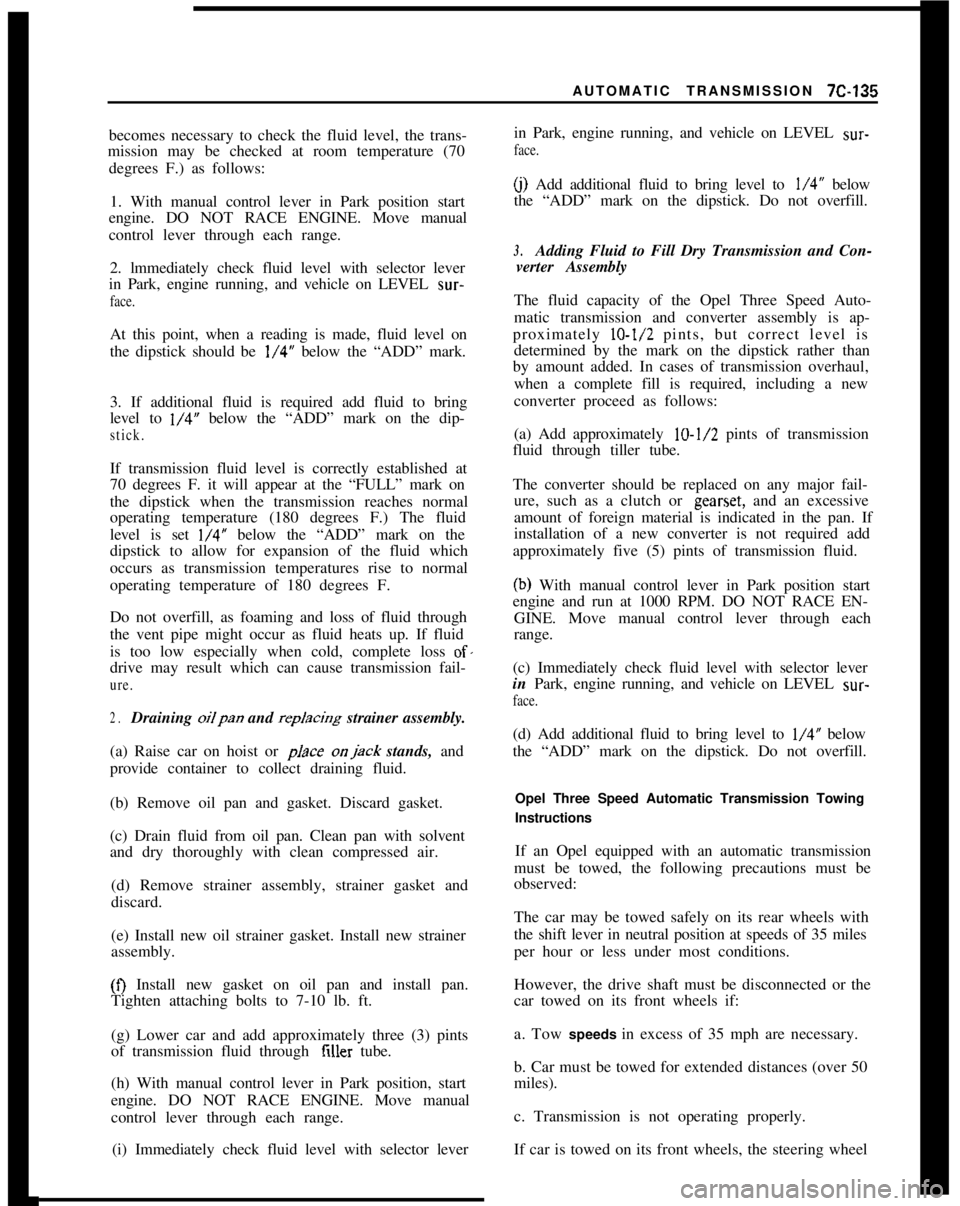
AUTOMATIC TRANSMISSION 7C-135
becomes necessary to check the fluid level, the trans-
mission may be checked at room temperature (70
degrees F.) as follows:
1. With manual control lever in Park position start
engine. DO NOT RACE ENGINE. Move manual
control lever through each range.
2. lmmediately check fluid level with selector lever
in Park, engine running, and vehicle on LEVEL sur-
face.At this point, when a reading is made, fluid level on
the dipstick should be I/4” below the “ADD” mark.
3. If additional fluid is required add fluid to bring
level to
l/4” below the “ADD” mark on the dip-
stick.If transmission fluid level is correctly established at
70 degrees F. it will appear at the “FULL” mark on
the dipstick when the transmission reaches normal
operating temperature (180 degrees F.) The fluid
level is set
l/4” below the “ADD” mark on the
dipstick to allow for expansion of the fluid which
occurs as transmission temperatures rise to normal
operating temperature of 180 degrees F.
Do not overfill, as foaming and loss of fluid through
the vent pipe might occur as fluid heats up. If fluid
is too low especially when cold, complete loss
of’drive may result which can cause transmission fail-
ure.
2.Draining oilpan and rep/a&g strainer assembly.
(a) Raise car on hoist or p/ace OnJxk stands, and
provide container to collect draining fluid.
(b) Remove oil pan and gasket. Discard gasket.
(c) Drain fluid from oil pan. Clean pan with solvent
and dry thoroughly with clean compressed air.
(d) Remove strainer assembly, strainer gasket and
discard.
(e) Install new oil strainer gasket. Install new strainer
assembly.
(f) Install new gasket on oil pan and install pan.
Tighten attaching bolts to 7-10 lb. ft.
(g) Lower car and add approximately three (3) pints
of transmission fluid through filler tube.
(h) With manual control lever in Park position, start
engine. DO NOT RACE ENGINE. Move manual
control lever through each range.
(i) Immediately check fluid level with selector leverin Park, engine running, and vehicle on LEVEL
sur-
face.(i) Add additional fluid to bring level to
l/4” below
the “ADD” mark on the dipstick. Do not overfill.
3.Adding Fluid to Fill Dry Transmission and Con-
verter Assembly
The fluid capacity of the Opel Three Speed Auto-
matic transmission and converter assembly is ap-
proximately IO-l/2 pints, but correct level is
determined by the mark on the dipstick rather than
by amount added. In cases of transmission overhaul,
when a complete fill is required, including a new
converter proceed as follows:
(a) Add approximately 10-l/2 pints of transmission
fluid through tiller tube.
The converter should be replaced on any major fail-
ure, such as a clutch or gearset, and an excessive
amount of foreign material is indicated in the pan. If
installation of a new converter is not required add
approximately five (5) pints of transmission fluid.
(b) With manual control lever in Park position start
engine and run at 1000 RPM. DO NOT RACE EN-
GINE. Move manual control lever through each
range.
(c) Immediately check fluid level with selector lever
in Park, engine running, and vehicle on LEVEL
sur-
face.(d) Add additional fluid to bring level to
l/4” below
the “ADD” mark on the dipstick. Do not overfill.
Opel Three Speed Automatic Transmission Towing
Instructions
If an Opel equipped with an automatic transmission
must be towed, the following precautions must be
observed:
The car may be towed safely on its rear wheels with
the shift lever in neutral position at speeds of 35 miles
per hour or less under most conditions.
However, the drive shaft must be disconnected or the
car towed on its front wheels if:
a. Tow speeds in excess of 35 mph are necessary.
b. Car must be towed for extended distances (over 50
miles).
c. Transmission is not operating properly.
If car is towed on its front wheels, the steering wheel
Page 497 of 625
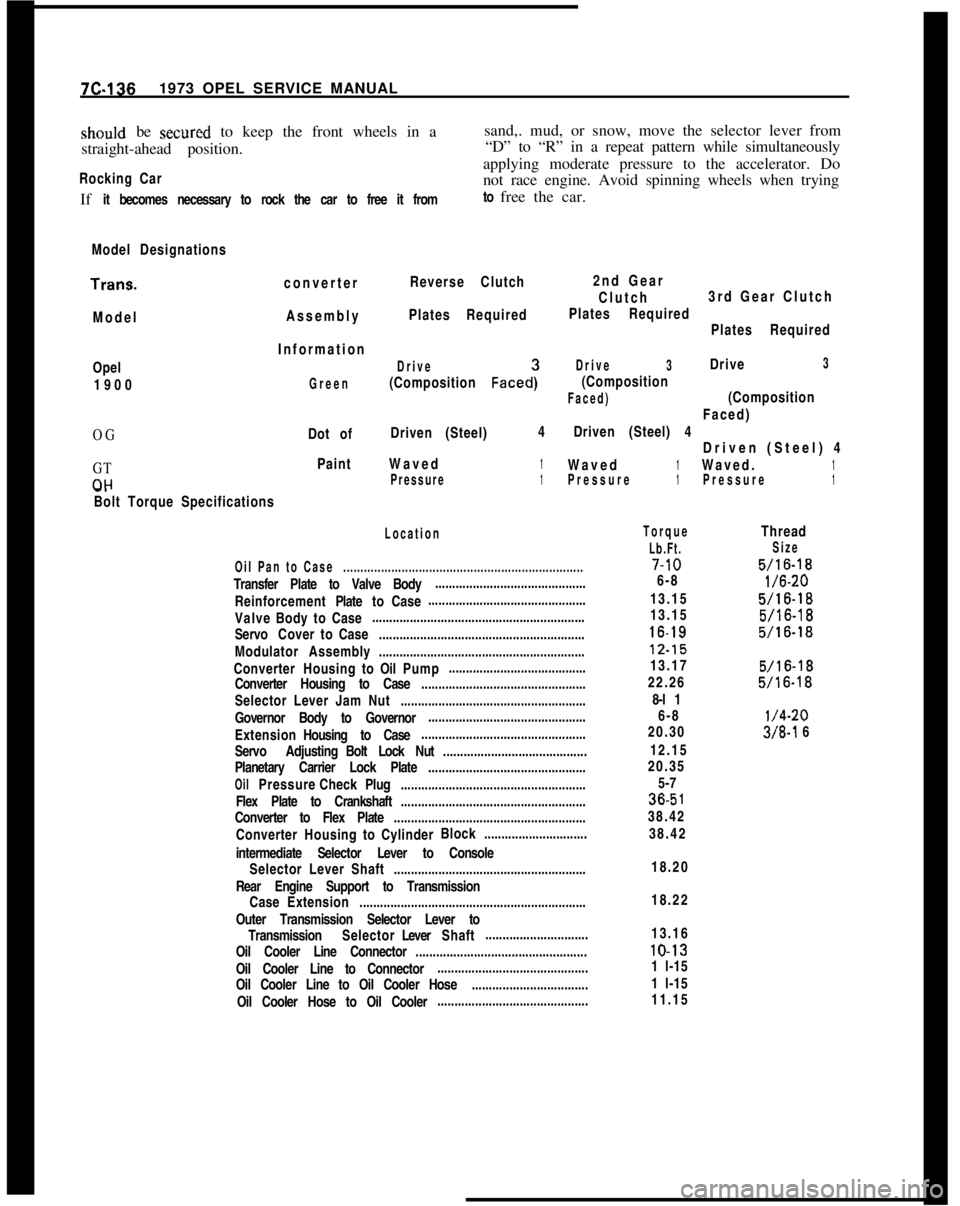
7C-1361973 OPEL SERVICE MANUALshould be secured to keep the front wheels in a
straight-ahead position.sand,. mud, or snow, move the selector lever from
“D” to “R” in a repeat pattern while simultaneously
applying moderate pressure to the accelerator. DoRocking Carnot race engine. Avoid spinning wheels when trying
If it becomes necessary to rock the car to free it fromto free the car.
Model DesignationsTrans.
converterReverse Clutch
ModelAssemblyPlates Required2nd Gear
Clutch3rd Gear Clutch
Plates Required
Plates RequiredOpel
1900
OG
GT
CIHInformation
Drive
(Composition Faced:
Drive3Drive3
Green
(Composition
Faced)(CompositionFaced)
Dot ofDriven (Steel)4Driven (Steel) 4
Driven (Steel) 4
PaintWaved1Waved1Waved.1Pressure1Pressure1Pressure1-.
Bolt Torque Specifications
Location
Oil Pan to Case......................................................................Transfer Plate to Valve Body............................................
ReinforcementPlatetoCase..............................................
ValveBodytoCase..............................................................
ServoCovertoCase............................................................
Modulator Assembly............................................................
ConverterHousingtoOilPump........................................
Converter Housing to Case................................................
Selector Lever Jam Nut......................................................
Governor Body to Governor..............................................
ExtensionHousing to Case................................................
Servo AdjustingBolt Lock Nut..........................................
Planetary Carrier Lock Plate..............................................
OilPressureCheckPlug......................................................
Flex Plate to Crankshaft......................................................
Converter to Flex Plate........................................................
ConverterHousingtoCylinderBlock..............................
intermediate Selector Lever to Console
Selector Lever Shaft........................................................
Rear Engine Support to Transmission
CaseExtension..................................................................
Outer Transmission Selector Lever to
TransmissionSelectorLeverShaft..............................
Oil Cooler Line Connector..................................................
Oil Cooler Line to Connector............................................
Oil Cooler Line to Oil Cooler Hose..................................
Oil Cooler Hose to Oil Cooler............................................
Torque
Lb.Ft.7-10
6-8
13.15
13.1516-1812.15
13.17
22.26
8-l 1
6-8
20.30
12.15
20.35
5-736.5
138.42
38.42
Thread
Size
5/16-18
l/6-20
5/16-18
5/16-18
5/16-18
5/16-18
5/16-18
l/4-20
3/8-l 6
18.20
18.22
13.1610-13
1 l-15
1 l-15
11.15
Page 517 of 625
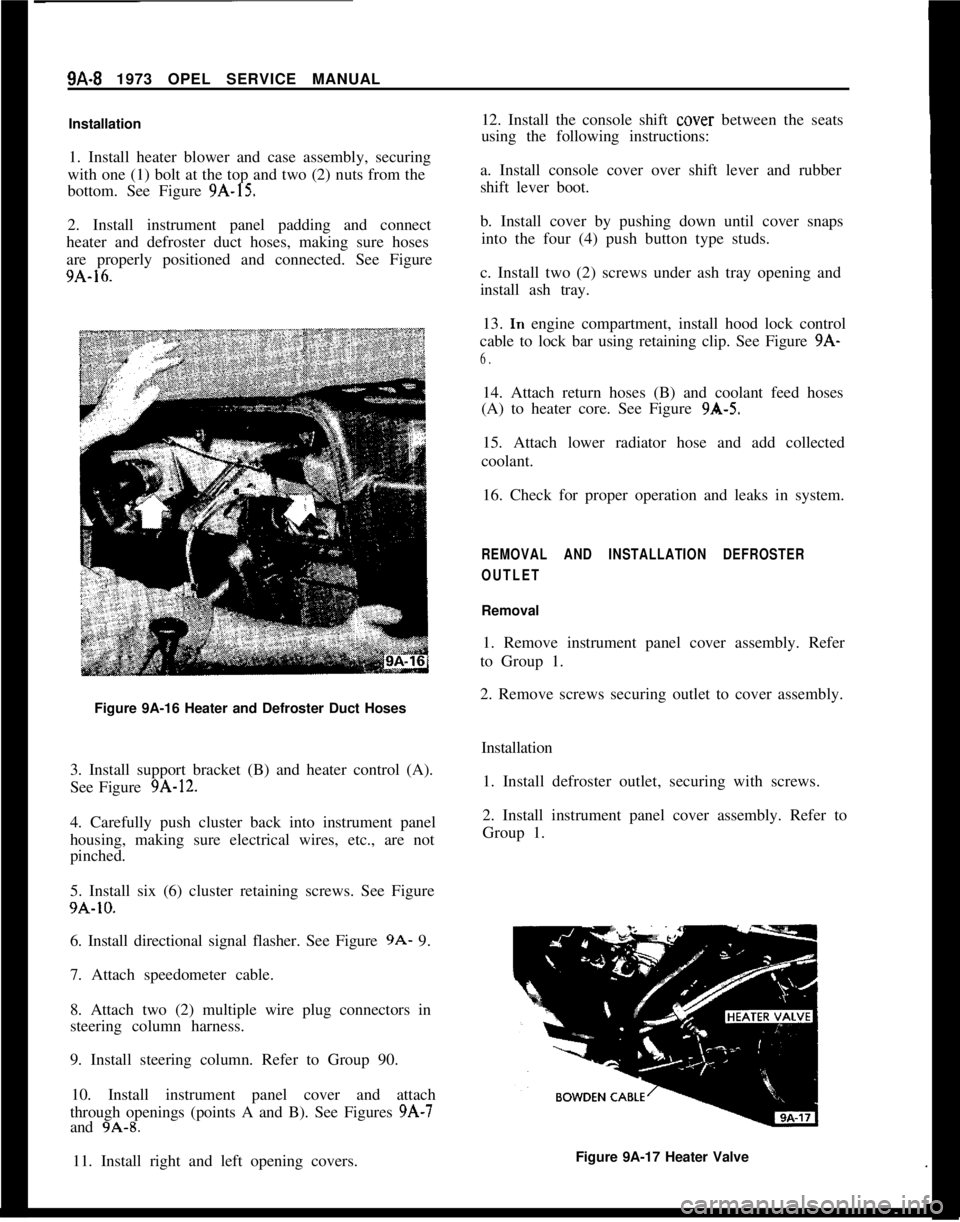
9A-8 1973 OPEL SERVICE MANUAL
Installation
1. Install heater blower and case assembly, securing
with one (1) bolt at the top and two (2) nuts from the
bottom. See Figure
9A-15.
2. Install instrument panel padding and connect
heater and defroster duct hoses, making sure hoses
are properly positioned and connected. See Figure
9A-16.
Figure 9A-16 Heater and Defroster Duct Hoses
3. Install support bracket (B) and heater control (A).
See Figure
9A-12.
4. Carefully push cluster back into instrument panel
housing, making sure electrical wires, etc., are not
pinched.
5. Install six (6) cluster retaining screws. See Figure
9A-10.
6. Install directional signal flasher. See Figure
9A- 9.
7. Attach speedometer cable.
8. Attach two (2) multiple wire plug connectors in
steering column harness.
9. Install steering column. Refer to Group 90.
10. Install instrument panel cover and attach
through openings (points A and B). See Figures
9A-7
and 9A-8.
11. Install right and left opening covers. 12. Install the console shift
cover
between the seats
using the following instructions:
a. Install console cover over shift lever and rubber
shift lever boot.
b. Install cover by pushing down until cover snaps into the four (4) push button type studs.
c. Install two (2) screws under ash tray opening and
install ash tray. 13.
In engine compartment, install hood lock control
cable to lock bar using retaining clip. See Figure
9A-
6.
14. Attach return hoses (B) and coolant feed hoses
(A) to heater core. See Figure
9A-5.
15. Attach lower radiator hose and add collected
coolant.
16. Check for proper operation and leaks in system.
REMOVAL AND INSTALLATION DEFROSTER
OUTLET
Removal
1. Remove instrument panel cover assembly. Refer
to Group 1.
2. Remove screws securing outlet to cover assembly.
Installation1. Install defroster outlet, securing with screws.
2. Install instrument panel cover assembly. Refer to
Group 1.
Figure 9A-17 Heater Valve