PONTIAC FIERO 1988 Service Repair Manual
Manufacturer: PONTIAC, Model Year: 1988, Model line: FIERO, Model: PONTIAC FIERO 1988Pages: 1825, PDF Size: 99.44 MB
Page 581 of 1825
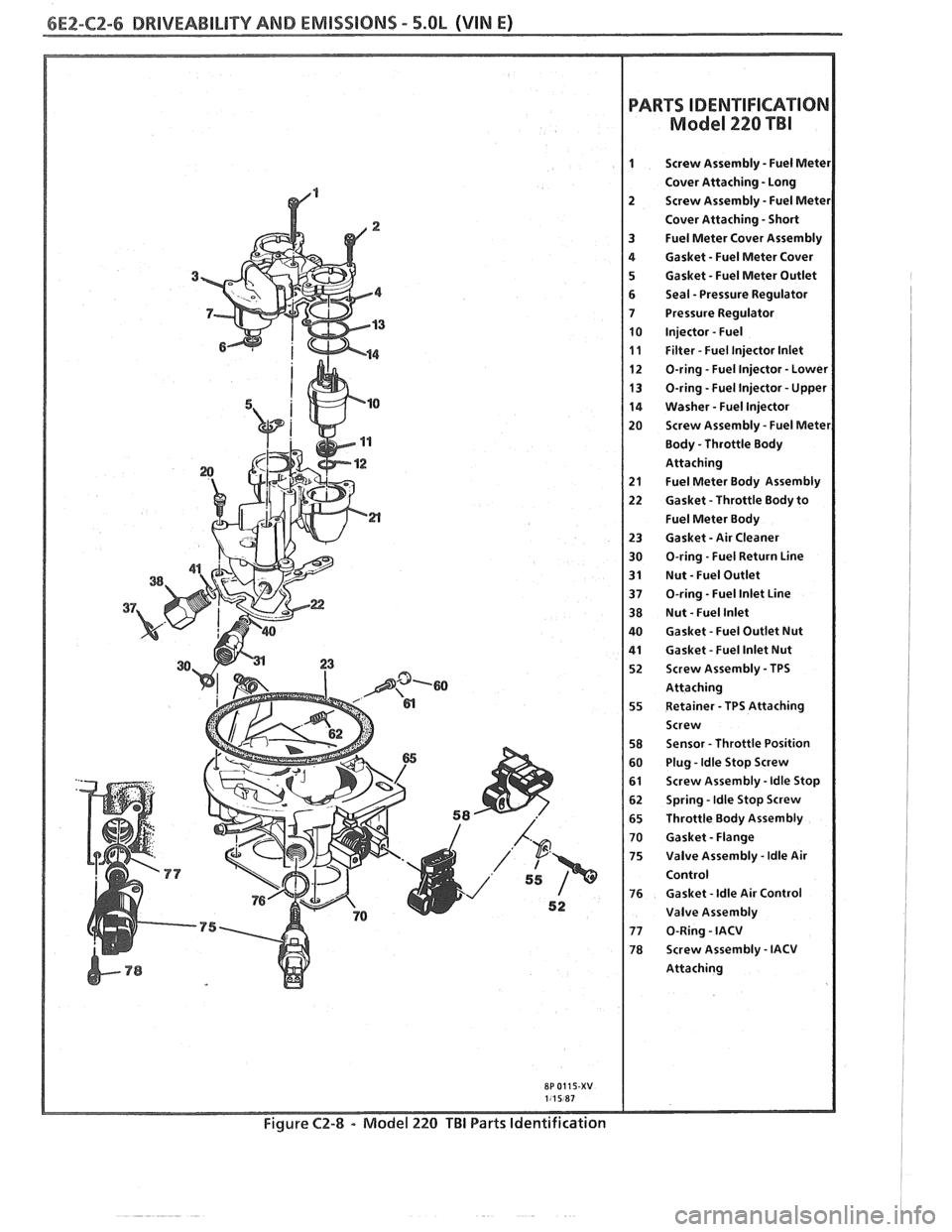
6E2-C2-6 DRIVEABILITY AND EMISSIONS - S.OL (VIN E)
PARTS
M
IDENTIFICATION
ode1 220 TBI
Screw Assembly - Fuel Mete1
Cover Attaching - Long
Screw Assembly
- Fuel Mete1
Cover Attaching - Short
Fuel Meter Cover Assembly
Gasket
- Fuel Meter Cover
Gasket
- Fuel Meter Outlet
Seal
- Pressure Regulator
Pressure Regulator
Injector
- Fuel
Filter
- Fuel lnjector lnlet
O-ring
- Fuel lnjector - Lower
O-ring
-Fuel lnjector - Upper
Washer
- Fuel lnjector
Screw Assembly - Fuel Metel
Body - Throttle Body
Attaching
Fuel Meter Body Assembly
Gasket -Throttle Body to
Fuel Meter Body
Gasket
- Air Cleaner
O-ring
- Fuel Return Line
Nut
- Fuel Outlet
O-ring
- Fuel lnlet Line
Nut
- Fuel lnlet
Gasket
- Fuel Outlet Nut
Gasket
- Fuel lnlet Nut
Screw Assembly
- TPS
Attaching Retainer
- TPS Attaching
Screw
Sensor
- Throttle Position
Plug
-Idle Stop Screw
Screw Assembly
- ldle Stop
Spring
- ldle Stop Screw
Throttle Body Assembly
Gasket
- Flange
Valve Assembly
- ldle Air
Control
Gasket
- ldle Air Control
Valve Assembly
0-Ring
- IACV
Screw Assembly
- IACV
Attaching
8P 0115-XV
Figure C2-8 - Model 220 TBI Parts Identification
Page 582 of 1825
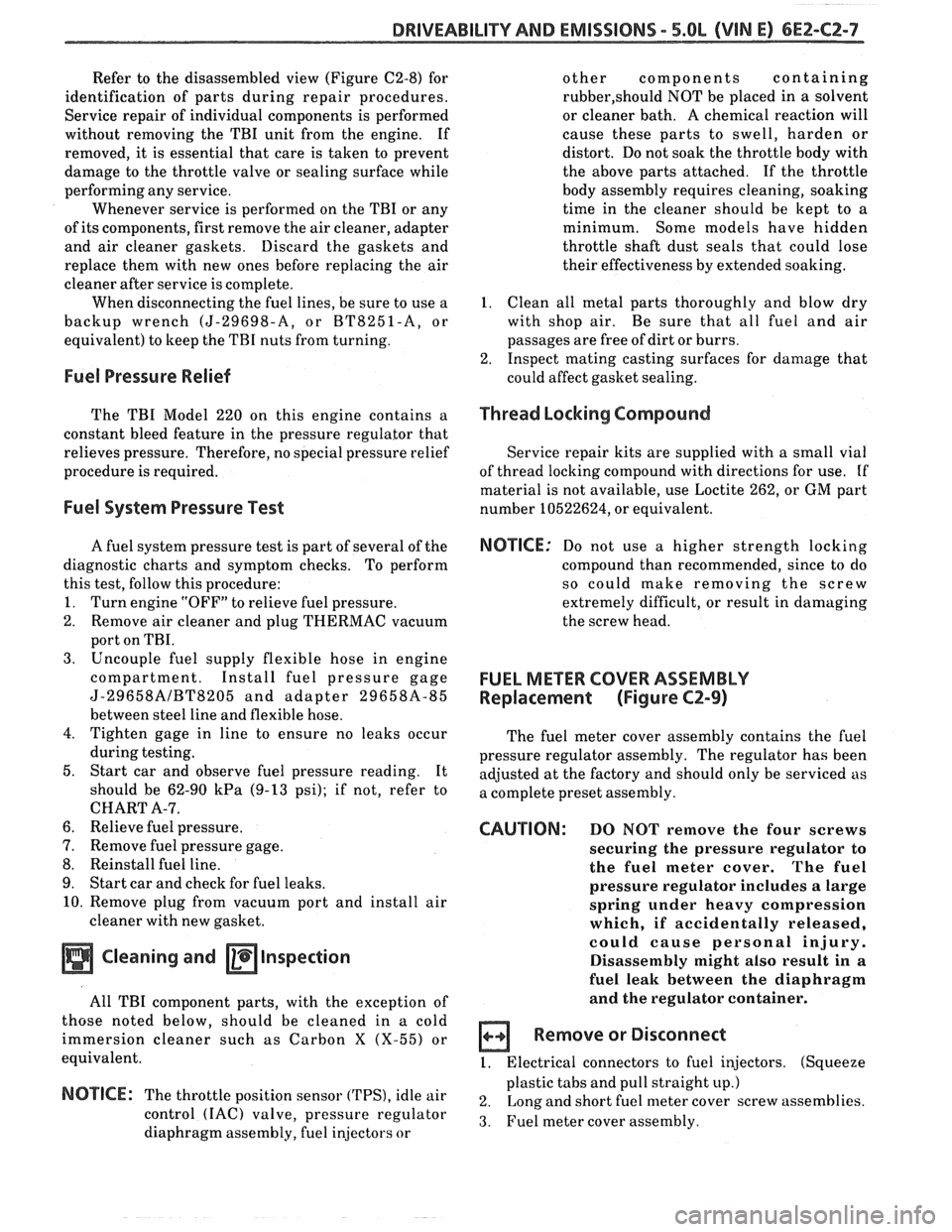
DRIVEABILITY AND EMISSIONS - 5.BL (VIN E) 6E2-CZ-7
Refer to the disassembled view (Figure C2-8) for
identification of parts during repair procedures.
Service repair of individual components is performed
without removing the TBI unit from the engine. If
removed, it is essential that care is taken to prevent
damage to the throttle valve or sealing surface while
performing any service.
Whenever service is performed on the TBI or any
of its components, first remove the air cleaner, adapter
and air cleaner gaskets. Discard the gaskets and
replace them with new ones before replacing the air
cleaner after service is complete.
When disconnecting the fuel lines, be sure to use a
backup wrench
(J-29698-A, or BT8251-A, or
equivalent) to keep the TBI nuts from turning.
Fuel Pressure Relief
The TBI Model 220 on this engine contains a
constant bleed feature in the pressure regulator that
relieves pressure. Therefore, no special pressure relief
procedure is required.
Fuel System Pressure Pest
A fuel system pressure test is part of several of the
diagnostic charts and symptom checks. To perform
this test, follow this procedure:
1. Turn engine "OFF" to relieve fuel pressure.
2. Remove air cleaner and plug THERMAC vacuum
port on TBI.
3. Uncouple fuel supply flexible hose in engine
compartment. Install fuel pressure gage
J-29658AlBT8205 and adapter 29658A-85
between steel line and flexible hose.
4. Tighten gage in line to ensure no leaks occur
during testing.
5. Start car and observe fuel pressure reading. It
should be 62-90
kPa (9-13 psi); if not, refer to
CHART A-7.
6. Relieve fuel pressure.
7. Remove fuel pressure gage.
8. Reinstall fuel line.
9. Start car and check for fuel leaks.
10. Remove plug from vacuum port and install air
cleaner with new gasket.
Cleaning and inspection
All TBI component parts, with the exception of
those noted below, should be cleaned in a cold
immersion cleaner such as Carbon
X (X-55) or
equivalent.
NOTICE: The throttle position sensor ('I'PS), idle air
control
(IAC) valve, pressure regulator
diaphragm assembly, fuel injectors or other
components containing
rubber,should NOT be placed in a solvent
or cleaner bath. A chemical reaction will
cause these parts to swell, harden or
distort. Do not soak the throttle body with
the above parts attached. If the throttle
body assembly requires cleaning, soaking
time in the cleaner should be kept to a
minimum. Some models have hidden
throttle shaft dust seals that could lose
their effectiveness by extended soaking.
1. Clean all metal parts thoroughly and blow dry
with shop air. Be sure that all fuel and air
passages are free of dirt or burrs.
2. Inspect mating casting surfaces for damage that
could affect gasket sealing.
Thread Locking Compound
Service repair kits are supplied with a small vial
of thread locking compound with directions for use. If
material is not available, use Loctite 262, or
GM part
number 10522624, or equivalent.
NOTICE: Do not use a higher strength locking
compound than recommended, since to do
so could make removing the screw
extremely difficult, or result in damaging
the screw head.
FUEL METER COVER ASSEMBLY
Replacement (Figure
C2-9)
The fuel meter cover assembly contains the fuel
pressure regulator assembly. The regulator has been
adjusted at the factory and should only be serviced as
a complete preset assembly.
CAUTION: DO NOT remove the four screws
securing the pressure regulator to
the fuel meter cover. The fuel
pressure regulator includes a large
spring under heavy compression
which, if accidentally released,
could cause personal injury.
Disassembly might also result in a
fuel leak between the diaphragm
and the regulator container.
Remove or Disconnect
I. Electrical connectors to fuel injectors. (Squeeze
plastic tabs and pull straight up.)
2. Long
and short fuel meter cover screw assemblies.
3. Fuel meter cover assembly.
Page 583 of 1825
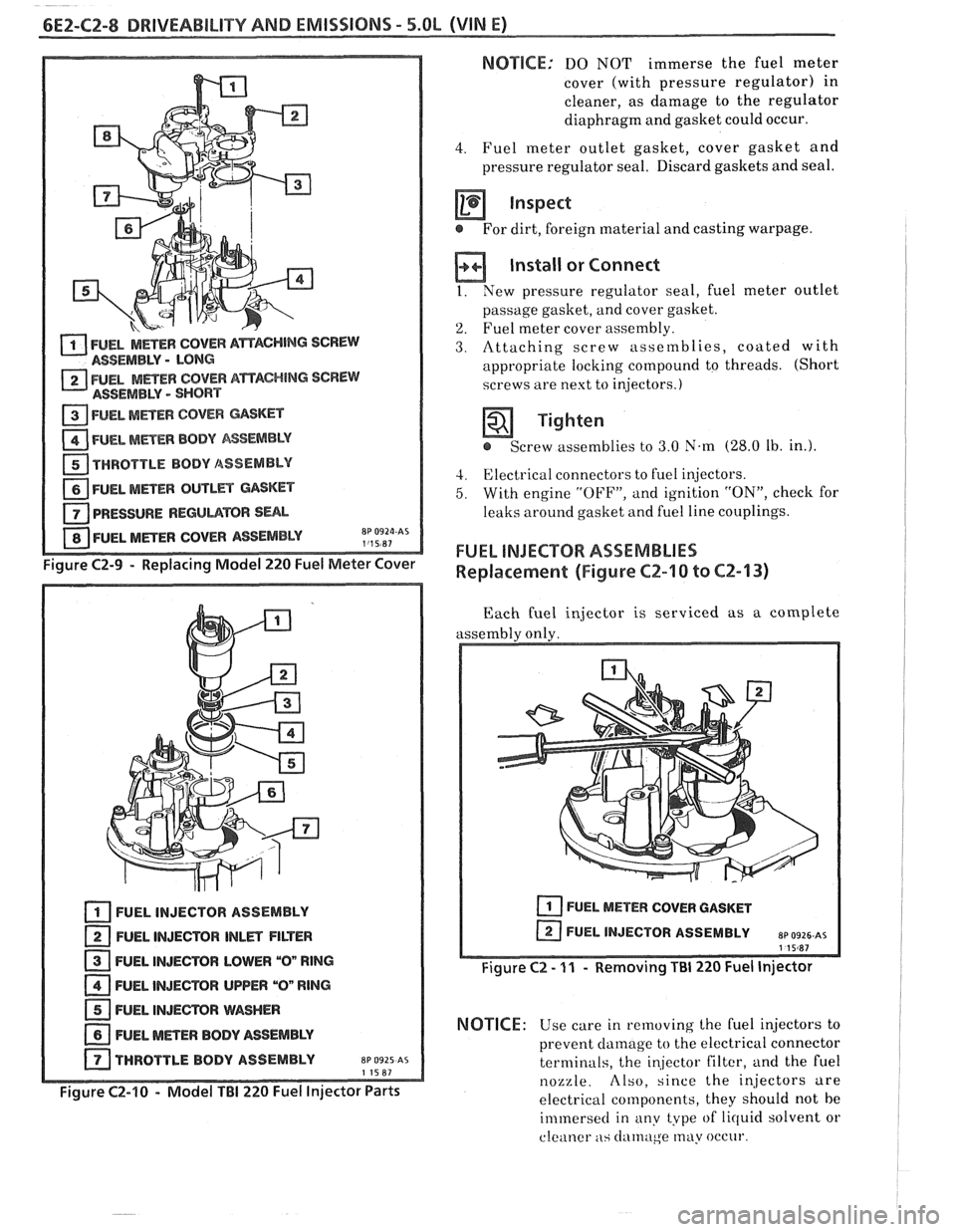
6E2-CZ-8 DRIVEABILITY AND EMISSIONS - 5.OL (VIN E)
a FUEL METER COVER A~ACHING SCREW ASSEMBLY - LONG
2 FUEL MmEW COVER AmAC#ING SCREW
ASSEMBLY - SHORT
1 FUEL MmEW COVER GASKET
FUEL METER BODY ASSEMBLY
a THROTTLE BODY /ASSEMBLY
FUEL MnER OUTL- GASKET
PRESSURE
REGUUTOR SUL
FUEL METER COVER ASSEMBLY
Figure C2-9 - Replacing Model 220 Fuel Meter Cover
FUEL INJECTOR ASSEMBLY
FUEL INJECTOR
lNLm FILTER
FUEL INJECTOR LOWER
"On RlNG
FUEL INJECTOR UPPER "On RlNG
FUEL INJEmR WASHER
NEL METER BODY ASSEMBLY
THROTTLE BODY ASSEMBLY
EP 0925 AS 11587
Figure C2-10 - Model TBI 220 Fuel Injector Parts
NOTSCE: DO NOT immerse the fuel meter
cover (with pressure regulator) in
cleaner, as damage to the regulator
diaphragm and gasket could occur.
4. Fuel meter outlet gasket, cover gasket and
pressure regulator seal. Discard gaskets and seal.
inspect
@ For dirt, foreign material and casting warpage.
Install or Connect
I. New pressure regulator seal, fuel meter outlet
passage gasket, and cover gasket.
'2. Fuel meter cover assembly.
3. Attaching screw assetnblies, coated with
appropriate locking compound to threads. (Short
screws are next to injectors.)
Tighten
e Screw assemblies to 3.0 N.m (28.0 Ib. in.).
4. Electrical connectors to fuel injectors.
5. With engine "OFF", and ignition "ON", check for
leaks around gasket and fuel line couplings.
FUEL INJECTOR ASSEMBLIES
Replacement (Figure CZ-10 to CZ-13)
Each fuel injector is serviced as a complete
assembly only.
FUEL METER COVER GASKET
I Figure C2 - 11 - Removing Ti31 220 Fuel Injector
NOTICE: Use care in removing the Cuel injectors to
prevent
clamage to the electrical connector
terminals, the
in,jector filter, and the fuel
nozzle. Also, since the injectors are
electrical components, they should not be
immersecl in any type of lirluid solvent or
cleaner
as clatnuge may occur.
Page 584 of 1825
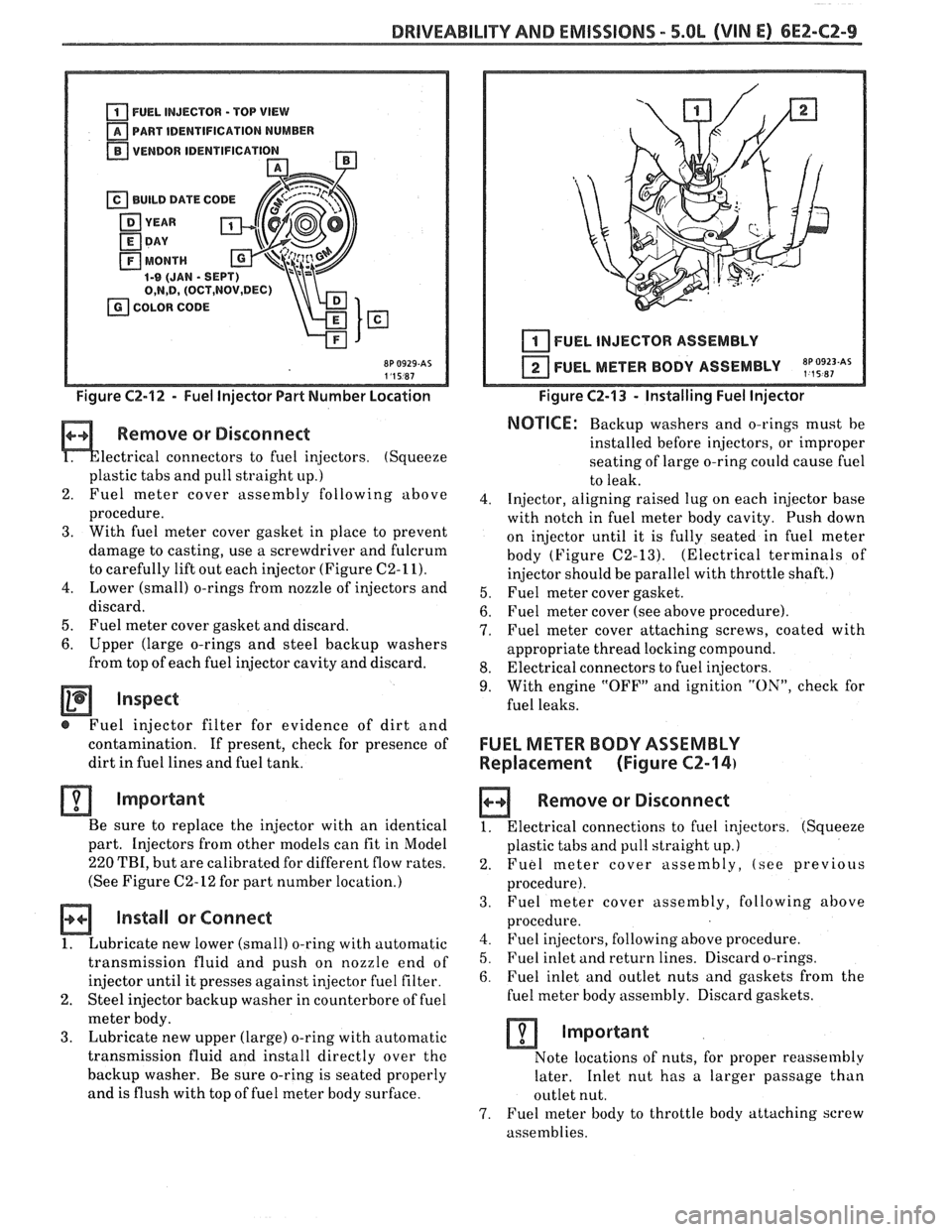
DRIVEABILITY AND EMISSIONS - 5.OL (VIN El CEZ-C2-9
u PART IDENTIFICATION NUMBER
VENDOR IDENTlFlCATl
Figure C2-12 - Fuel Injector Part Number Location
Remove or Disconnect
lectrical connectors to fuel injectors. (Squeeze
plastic tabs and pull straight
up.)
2. Fuel meter
cover assembly following above
procedure.
3. With fuel meter cover gasket in place to prevent
damage to casting, use a screwdriver and fulcrum
to carefully lift out each injector (Figure
C2-11).
4. Lower (small) o-rings from nozzle of injectors and
discard.
5. Fuel meter cover gasket and discard.
6. Upper (large o-rings and steel backup washers
from top of each fuel injector cavity and discard.
Inspect
@ Fuel injector filter for evidence of dirt and
contamination.
If present, check for presence of
dirt in fuel lines and fuel tank.
Important
Be sure to replace the injector with an identical
part. Injectors from other models can fit in Model
220 TBI, but are calibrated for different flow rates.
(See Figure
C2-12 for part number location.)
Install or Connect
1. Lubricate new lower (small) o-ring with automatic
transmission fluid and push on nozzle end of
injector until it presses against
in,jector fuel filter.
2. Steel injector backup washer in counterbore of fuel
meter body.
3. Lubricate new upper (large) o-ring with automatic
transmission fluid and install directly over
the
backup washer. Be sure o-ring is seated properly
and is flush with top of fuel meter body surface.
I I 1 I FUEL INJECTOR ASSEMBLY
FUEL METER BODY ASSEMBLY
~p,~9~~~As
Figure C2-13 - Installing Fuel Injector
NOTICE: Backup washers and o-rings must be
installed before injectors, or improper
seating of large o-ring
could cause fuel
to leak.
4. Injector, aligning raised lug on each injector base
with notch in fuel meter body cavity. Push down
on injector until it is fully seated in fuel meter
body (Figure
C2-13). (Electrical terminals of
injector should be parallel with throttle shaft.)
5. Fuel meter cover gasket.
6. Fuel meter cover (see above procedure).
7. Fuel meter cover attaching screws, coated with
appropriate thread locking compound.
8. Electrical connectors to fuel injectors.
9. With engine "OFF" and ignition "ON", check for
fuel leaks.
FUEL METER BODY ASSEMBLY
Replacement (Figure
CZ-14)
a Remove or Disconnect
1. Electrical connections to fuel injectors. (Squeeze
plastic tabs and pull straight up.)
2. Fuel meter cover assembly, (see previous
procedure).
3. Fuel
meter cover assembly, following above
procedure.
4. Fuel injectors, following above procedure.
5. Fuel inlet and return lines. Discard o-rings.
6. Fuel inlet and outlet nuts and gaskets from the
fuel meter body assembly. Discard gaskets.
Important
Note locations of nuts, for proper reassembly
later. Inlet nut has a larger passage than
outlet nut.
7. Fuel meter body to throttle body attaching screw
assemblies.
Page 585 of 1825
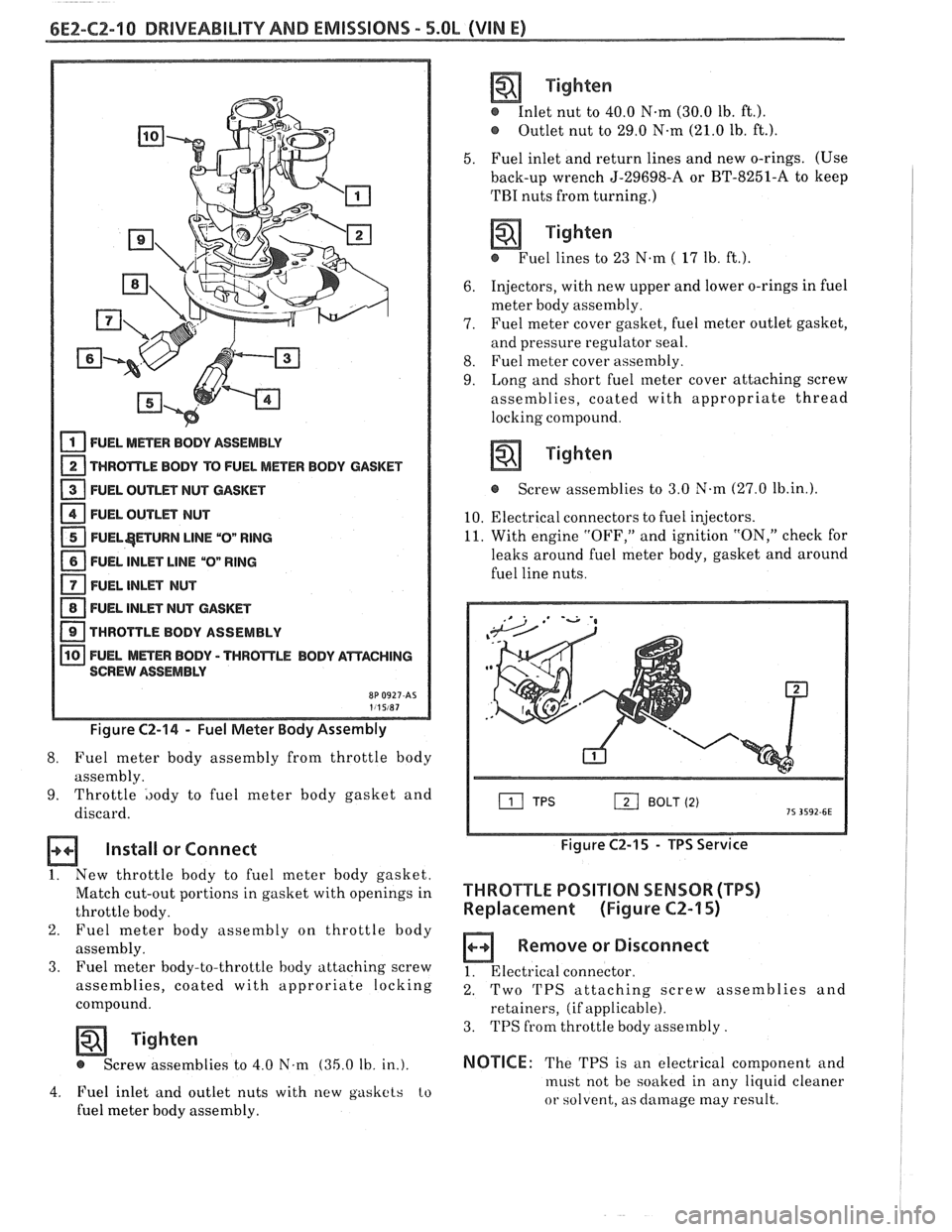
6E2-CZ-10 DRlVEABlLlTV AND EMISSIONS - 5.OL (WIN E)
FUEL METER BODY ASSEMBLY
THROTTLE BODY TO FUEL METER BODY GASKET
- 13 FUEL OUTLET NUT CASKET
1 FUEL OUTLET NUT - 1 FUEL$ETURN LlNE "Ow RING
1 FUEL INLET LlNE "Ow RlNG
FUEL INLET NUT
1 FUEL INLET NUT GASKET
1 THROTTLE BODY ASSEMBLY
FUEL
MmER BODY - TWROmLE BODY AWACHING
SCREW ASSEMBLY
Figure C2-14 - Fuel Meter Body Assembly
8. Fuel
meter body assembly from throttle body
assembly.
9. Throttle ,)ody to fuel meter body gasket and
discard.
a Install or Connect
1. New throttle hody to fuel meter body gasket.
Match cut-out portions in gasket with openings in
throttle body.
2. Fuel meter body assembly on throttle body
assembly.
3. Fuel meter body-to-throttle hody attaching screw
assemblies, coated with approriate locking
compound.
Tighten
@ Screw assemblies to 4.0 N.m (35.0 Ib. in.).
4. Fuel inlet and outlet nuts with new gaskets to
fuel meter body assembly.
Tighten
e Inlet nut to 40.0 N.m (30.0 lb. ft.).
Outlet nut to 29.0 N.m (21.0 lb. ft.).
5. Fuel inlet and return lines and new o-rings. (Use
back-up wrench J-29698-A or BT-8251-A to keep
TBI nuts from turning.)
Tighten
@ Fuel lines to 23 N.m ( 17 lb. ft.).
6. Injectors,
with new upper and lower o-rings in fuel
meter body assembly.
7. Fuel meter cover gasket, fuel meter outlet gasket,
and pressure regulator seal.
8. Fuel meter cover assembly.
9. Long and short fuel meter cover attaching screw
assemblies, coated with appropriate thread
locking compound.
Tighten
e Screw assemblies to 3.0 N.m (27.0 lb.in.1.
10. Electrical connectors to fuel injectors.
11. With engine "OFF," and ignition "ON," check for
leaks around fuel meter body, gasket and around
fuel line nuts.
12] BOLT (2)
Figure C2-15 - TPS Service
THROTTLE POSITION SENSOR (TPS)
Replacernent (Figure CZ-15)
Remove or Disconnect
1. Electrical connector.
2. Two 'I'PS attaching screw assemblies and
retainers, (if applicable).
3. TPS from throttle body assembly.
NOTICE: The TPS is an electrical component and
must not be soaked in any liquid cleaner
or solvent, as damage may result.
Page 586 of 1825
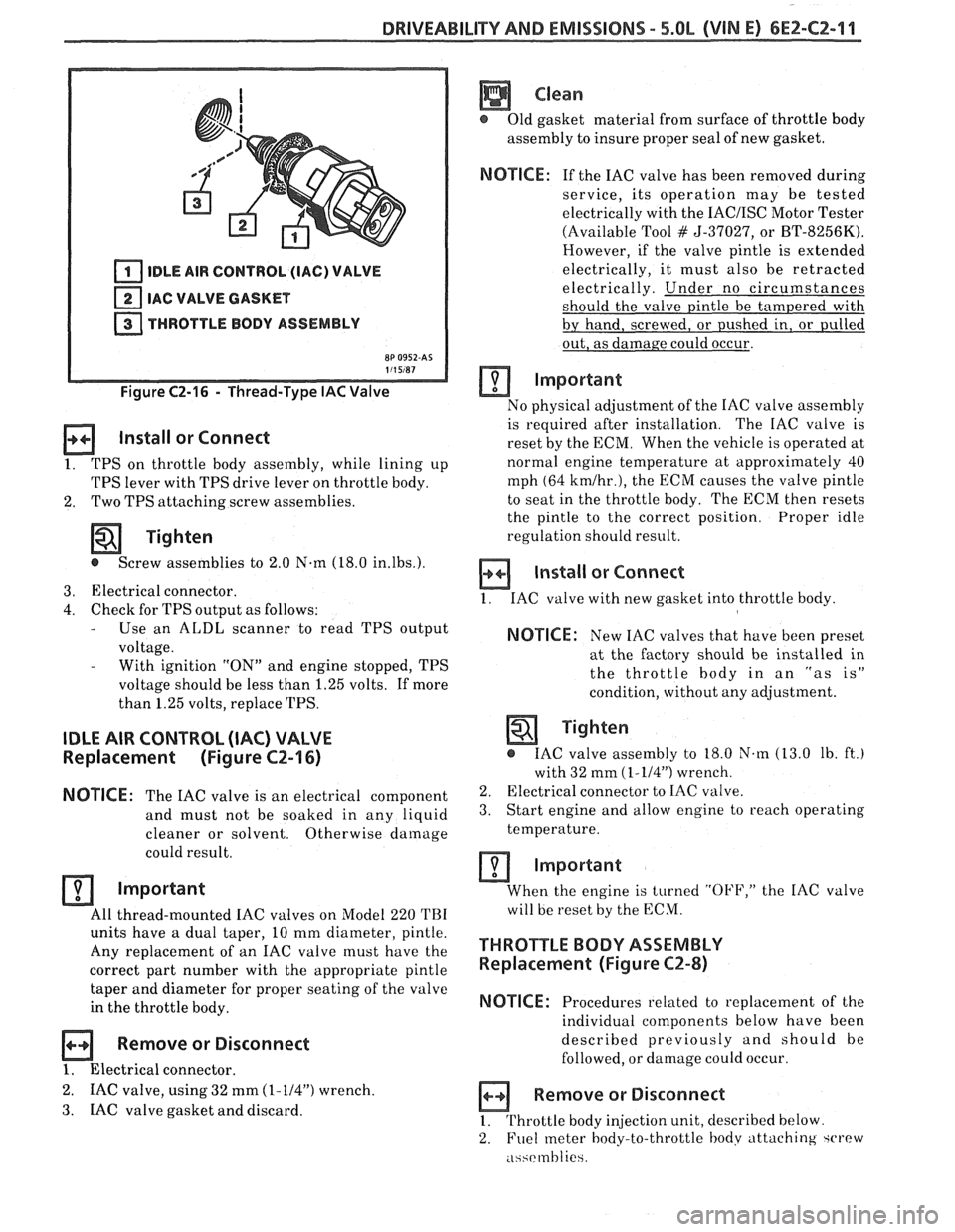
DRIVEABILITY AND EMISSIONS - 5.0L (VIN E) 6EZ-CZ-11
IDLE AIR CONTROL (IAC) VALVE
IAC VALVE GASKET
THROTTLE BODY ASSEMBLY
Figure C2-16 - Thread-Type IAC Valve
Install or Connect
1. TPS on throttle body assembly, while lining up
TPS lever with TPS drive lever on throttle body.
2. Two
TPS attaching screw assemblies.
Tighten
@ Screw assemblies to 2.0 N-m (18.0 in.lbs.).
3. Electrical connector.
4. Check for TPS output as follows: - Use an ALDL scanner to read TPS output
voltage.
- With ignition "ON" and engine stopped, TPS
voltage should be less than 1.25 volts. If more
than 1.25 volts, replace TPS.
IDLE AIR CONTROL (IAC) VALVE
Replacement (Figure CZ-16)
NOTICE:
The IAC valve is an electrical
component
and must not be soaked in any liquid
cleaner or solvent. Otherwise
damage
could result.
Important
All thread-mounted IAC valves on Model 220 TBI
units have a dual taper, 10 mm diameter, pintle.
Any replacement of an IAC valve must have the
correct part number with the appropriate pintle
taper and diameter for proper seating of the valve
in the throttle body.
Remove or Disconnect
1. Electrical connector.
2. IAC valve, using 32 mm (1-114") wrench.
3. IAC
valve gasket and discard.
Clean
@ Old gasket material from surface of throttle body
assembly to insure proper seal of new gasket.
NOTICE: If the IAC valve has been removed during
service, its operation may be tested
electrically with the
IACIISC Motor Tester
(Available Tool
# 5-37027, or BT-8256K).
However, if the valve pintle is extended
electrically, it must also be retracted
electrically. Under no circumstances
should the valve pintle be tampered with
by hand, screwed, or pushed in, or pulled
out, as damage could occur.
Important
No physical adjustment of the IAC valve assembly
is required after installation. The IAC valve is
reset by the ECM. When the vehicle is operated at
normal engine temperature at approximately 40
mph (64
kmlhr.), the ECM causes the valve pintle
to seat in the throttle body. The ECM then resets
the pintle to the correct position. Proper idle
regulation should result.
Install or Connect
1. IAC valve with new gasket into throttle body
NOTICE: New IAC valves that have been preset
at the factory should be installed in
the throttle
body in an "as is"
condition, without any adjustment.
Tighten
@ IAC valve assembly to 18.0 N.m (13.0 lb. ft.)
with 32 mm
(1-114") wrench.
2. Electrical connector to IAC valve.
3. Start engine and allow engine to reach operating
temperature.
Important
When the engine is turned "OFF," the IAC valve
will be reset by the ECM.
THROTTLE BODY ASSEMBLY
Replacement (Figure CZ-8)
NOTICE:
Procedures related to replacement of the
individual components below have been
described previously and should be
followed, or damage could occur.
Remove or Disconnect
1. Throttle body injection unit, described below
2. Fuel
meter body-to-throttle hodv attaching ~CI'PW
.i~~rmhlie
Page 587 of 1825
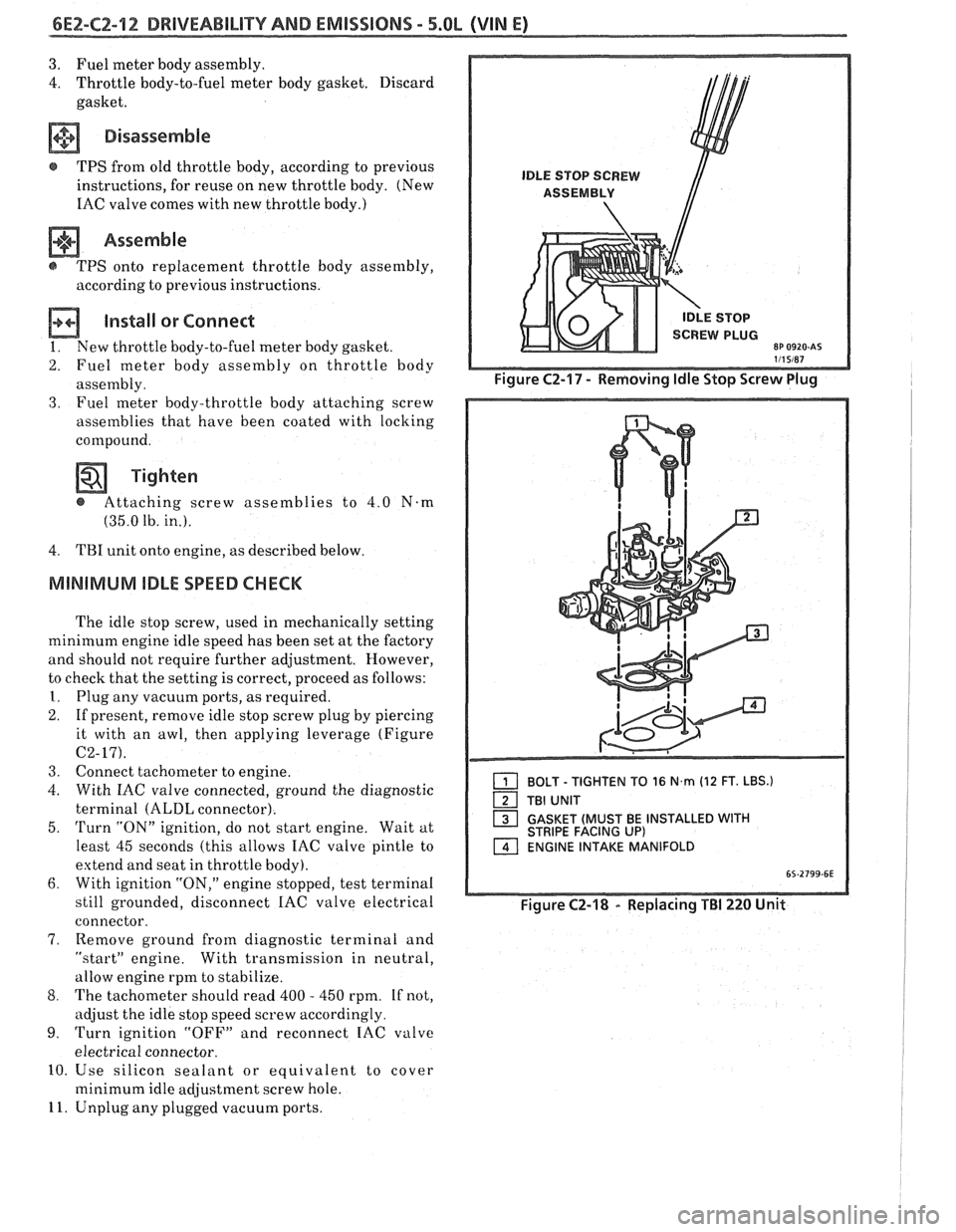
6E2-C2-12 DRIVEABILITY AND EMISSIONS - 5.0b (VIN E)
3. Fuel meter body assembly.
4. Throttle body-to-fuel meter body gasket. Discard
gasket.
a Disassemble
@ TPS from old throttle body, according to previous
instructions, for reuse on new throttle body. (New
IAC valve comes with new throttle body.)
Assemble
@ TPS onto replacement throttle body assembly,
according to previous instructions.
Install or Connect
1. New throttle body-to-fuel meter body gasket.
2. Fuel meter body assembly on throttle body
assembly.
3. Fuel meter body-throttle
body attaching screw
assemblies that have been coated with locking
compound.
Tighten
@ Attaching screw assemblies to 4.0 N.m
(35.0 Ib. in.).
4. TBI
unit onto engine, as described below.
MllMiMhlM IDLE SPEED CHECK
The idle stop screw, used in mechanically setting
minimum engine idle speed has been set at the factory
and should not require further adjustment. However,
to check that the setting is correct, proceed as follows:
I. Plug any vacuum ports, as required.
2. If present, remove idle stop screw plug by piercing
it with an awl, then applying leverage (Figure
C2-17).
3. Connect tachometer to engine.
4. With IAC valve connected, ground the diagnostic
terminal
(ALDL connector).
5.
Turn "ON" ignition, do not start engine. Wait at
least 45 seconds (this allows IAC valve pintle to
extend and seat in throttle body).
6. With ignition "ON," engine stopped, test terminal
still grounded, disconnect
IAC valve electrical
connector.
7, Remove ground from diagnostic terminal and
"startJ' engine. With transmission in neutral,
allow engine rpm to stabilize.
8. The tachometer should read 400 - 450 rpm. If not,
adjust the idle stop speed screw accordingly.
9. Turn ignition "OFF" and reconnect IAC valve
electrical connector.
10. Use silicon sealant or equivalent to cover
minimum idle adjustment screw hole.
11. Unplug any plugged vacuum ports.
1 BOLT - TIGHTEN TO 16 N,rn (12 FT. LBS.)
TBI UNIT
1 GASKET (MUST BE INSTALLED WITH STRIPE FACING UP) ENGINE INTAKE MANIFOLD
Figure C2-18 - Replacing TBI 220 Unit
Page 588 of 1825
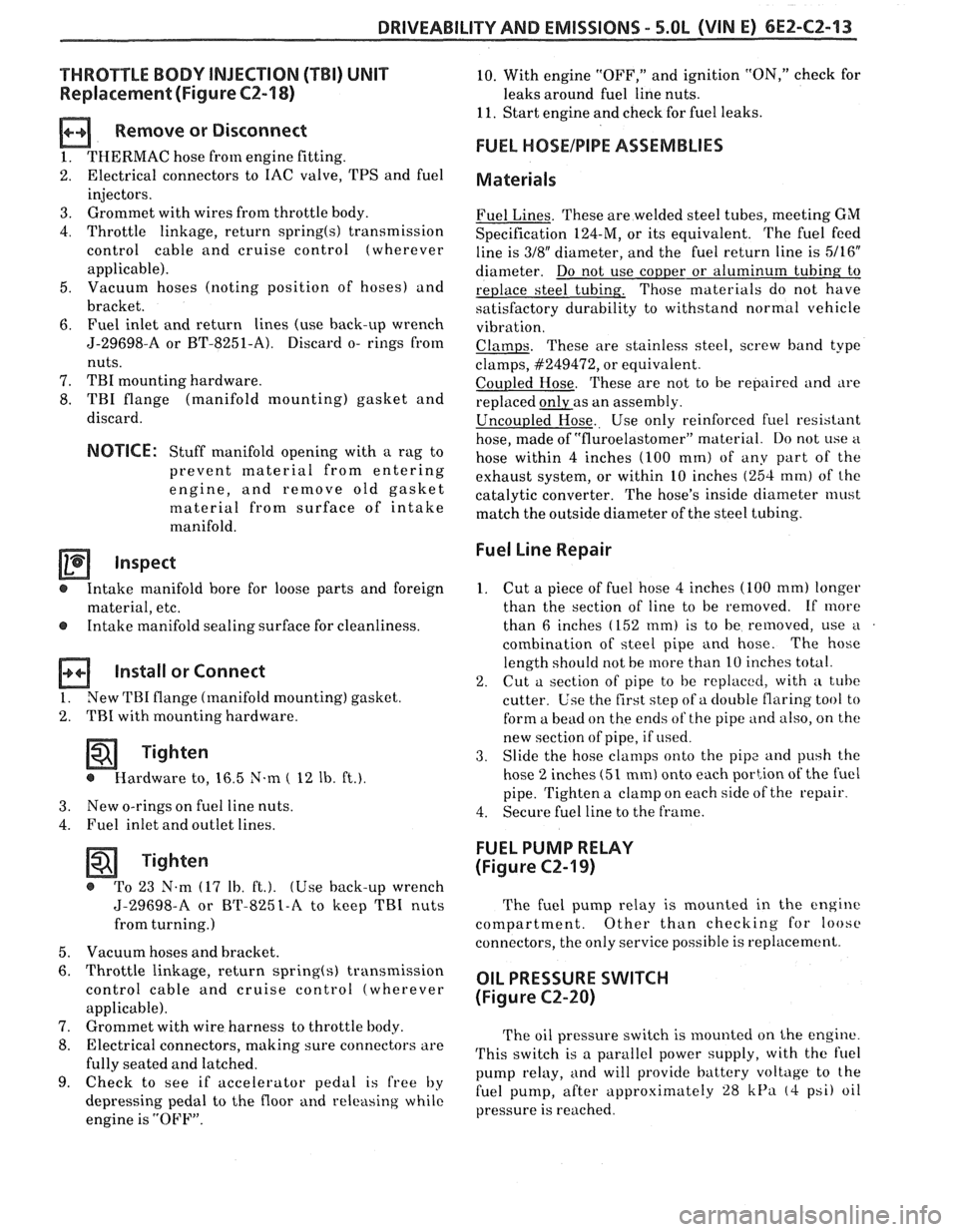
DRIVEABILITY AND EMISSIONS - S.0L (VIN E) 6EZ-C2-13
"THROTTLE BODY INJECTION (TBI) UNIT
Replacement (Figure C2-18)
a Remove or Disconnect
1. THERMAC hose from engine fitting.
2. Electrical connectors to IAC valve, TPS and fuel
injectors.
3. Grommet with wires from throttle body.
4. Throttle linkage, return
spring(s) transmission
control cable and cruise control (wherever
applicable).
5. Vacuum hoses (noting position of hoses) and
bracket.
6. Fuel inlet and return lines (use back-up wrench
J-29698-A or BT-8251-A). Discard o-
rings from
nuts.
7. TBI mounting hardware.
8. TBI flange (manifold mounting) gasket and
discard.
NOTICE: Stuff manifold opening with a rag to
prevent material from entering
engine, and remove old gasket
material from surface of intake
manifold.
Inspect
@ Intake manifold bore for loose parts and foreign
material, etc.
@ Intake manifold sealing surface for cleanliness.
Install or Connect
1. New TBI flange (manifold mounting) gasket.
2.
TI31 with mounting hardware.
Tighten
@ Hardwareto, 16.5N-m( 12Ib. ft.).
3. New o-rings on fuel line nuts
4. Fuel inlet and outlet lines.
Tighten - @ To 23 N.m (17 lb. ft.). (Use back-up wrench
J-29698-A or BT-8251-A to keep TBI nuts
from turning.)
5. Vacuum hoses and bracket.
6. Throttle linkage, return
spring(s) transmission
control cable and cruise control (wherever
applicable).
7. Grommet with wire harness to throttle body.
8. Electrical connectors, making sure connectors are
fully seated and latched.
9. Check to see if accelerator pedal is free by
depressing pedal to the floor
and releasing while
engine is "OFF".
10. With engine "OFF," and ignition "ON," check for
leaks around fuel line nuts.
11. Start engine and check for fuel leaks.
FUEL HOSEIPIPE ASSEMBLIES
Materials
Fuel Lines. These are welded steel tubes, meeting GM
Specification 124-M, or its equivalent. The fuel feed
line is
318" diameter, and the fuel return line is 5/16"
diameter. Do not use copper or aluminum tubing to
replace steel tubing. Those materials do not have
satisfactory durability to withstand normal vehicle
vibr, ii t' lon.
Clamps. These are stainless steel, screw band type
clamps,
#249472, or equivalent.
Coupled Hose. These are not to be repaired and are
replaced
&as an assembly.
Uncoupled Hose. Use only reinforced fuel resistant
hose, made of "fluroelastomer" material.
[lo not use w
hose within 4 inches (100 mm) of any part of the
exhaust system, or within 10 inches
(254 mm) of the
catalytic converter. The hose's inside diameter nus st
match the outside diameter of the steel tubing.
Fuel Line Repair
1. Cut
a piece of fuel hose 4 inches (100 mm) longer
than the section of line to be removed. If
more
than 6 inches (152 tnm) is to be removed, use a .
combination of steel pipe and hose. The
hose
length should not be more than 10 inches total.
2. Cut a section of pipe to be replacccl, with a tube
cutter. C'se the first step of a double flaring tool to
form a bead on the ends
of the pipe and also, on the
new section of pipe, if used.
3. Slide
the hose
clanlps onto the pip2 and push the
hose
2 inches (51 mm) onto each portion of the fuel
pipe. Tighten a
clamp on each side of the repair.
4. Secure
fuel line to the frame.
FUEL PUMP RELAY
(Figure
CZ-19)
The fuel pump relay is mounted in the engine
compartment. Other than checking for loose
connectors, the only service possible is replacement.
OIL PRESSURE SWITCH
(Figure C2-20)
The oil pressure switch is li~ounted on the engine.
This switch is a parallel power supply, with the fuel
pump relay, and will provide battery voltage to the
fuel
pump, after approximately 28 kPa (4 psi) oil
pressure is reached.
Page 589 of 1825
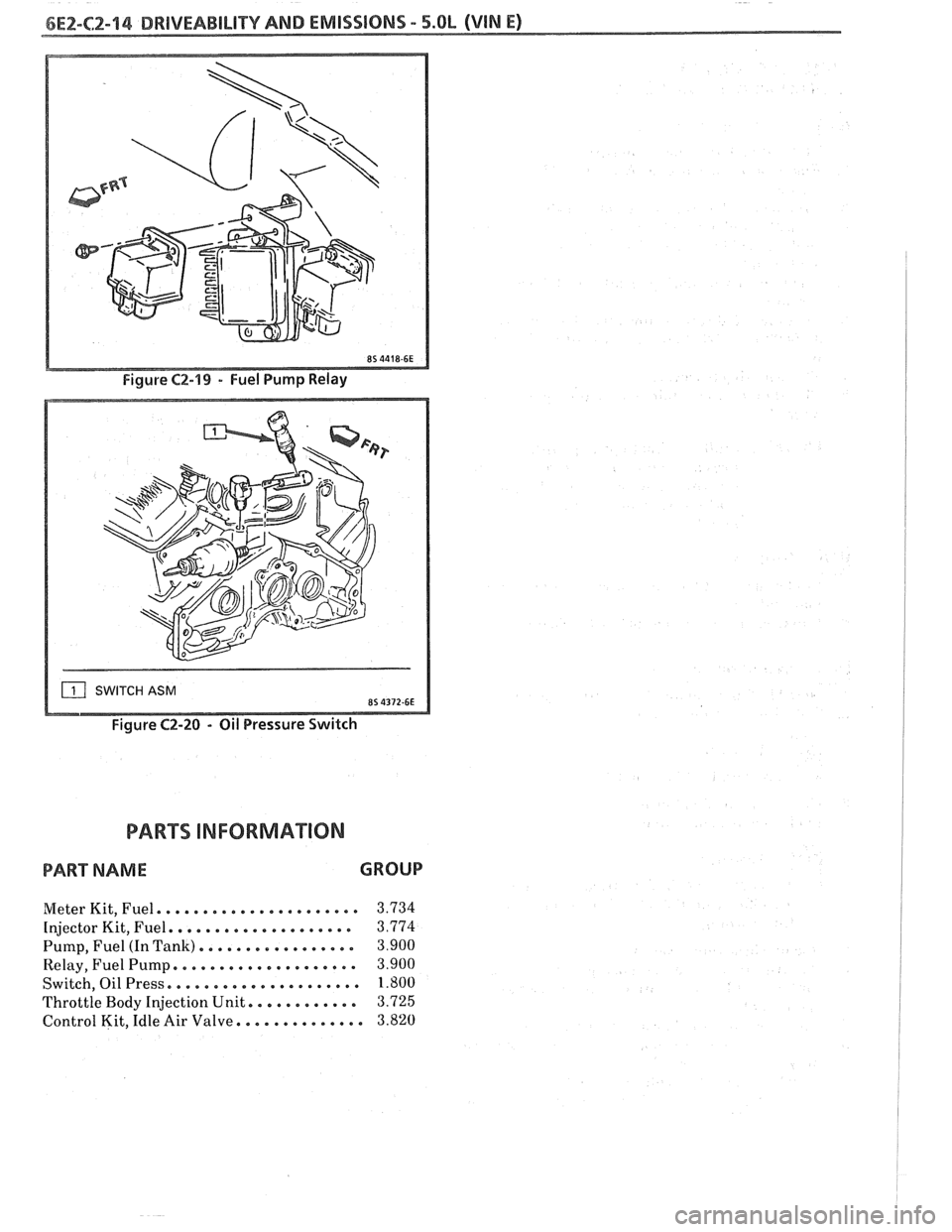
SWITCH ASM
Figure C2-20 - Oil Pressure Switch
PART D INFORMA"F0N
PART NAME GROUP
Meter Kit, Fuel. . . . . . . . . . . . . . . . . . . . . . 3.734
Injector Kit, Fuel. . . . . . , . . . . . . . . . . . . . 3.774
Pump, Fuel (In Tank). . . . . . . . . . . . . . . . . 3.900
Relay, Fuel Pump. . . . . . . . , . . . . . . . . . . . 3.900
Switch, Oil Press. . . . . . . . . . . . . . . . . . . . . 1.800
Throttle Body Injection Unit. . . . . . . . . . . . 3.725
Control Kit, Idle Air Valve. . . . . . . . . . . . . . 3.820
Page 590 of 1825
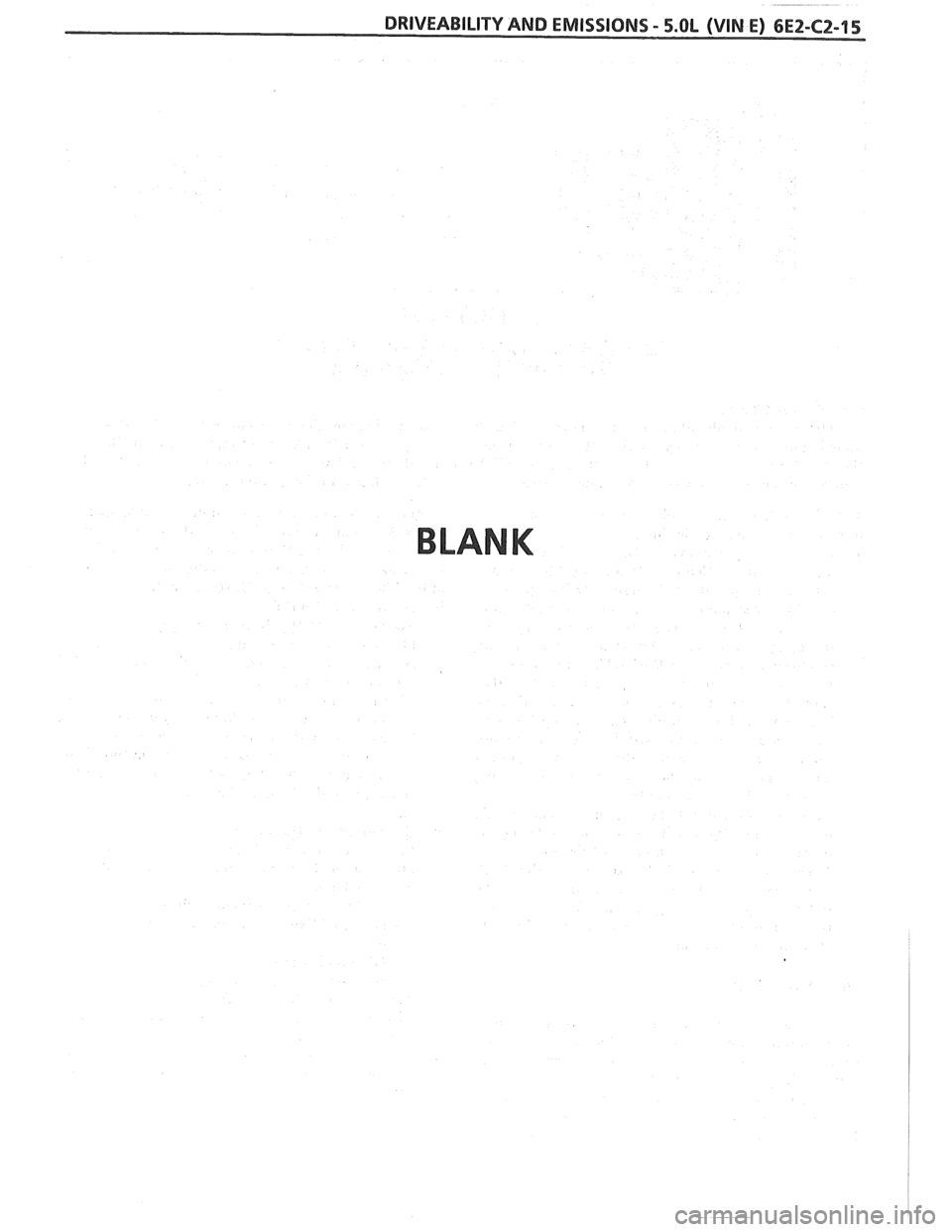
BLANK