display RENAULT SCENIC 2011 J95 / 3.G Engine And Peripherals EDC16C36 Workshop Manual
[x] Cancel search | Manufacturer: RENAULT, Model Year: 2011, Model line: SCENIC, Model: RENAULT SCENIC 2011 J95 / 3.GPages: 431, PDF Size: 2.03 MB
Page 3 of 431
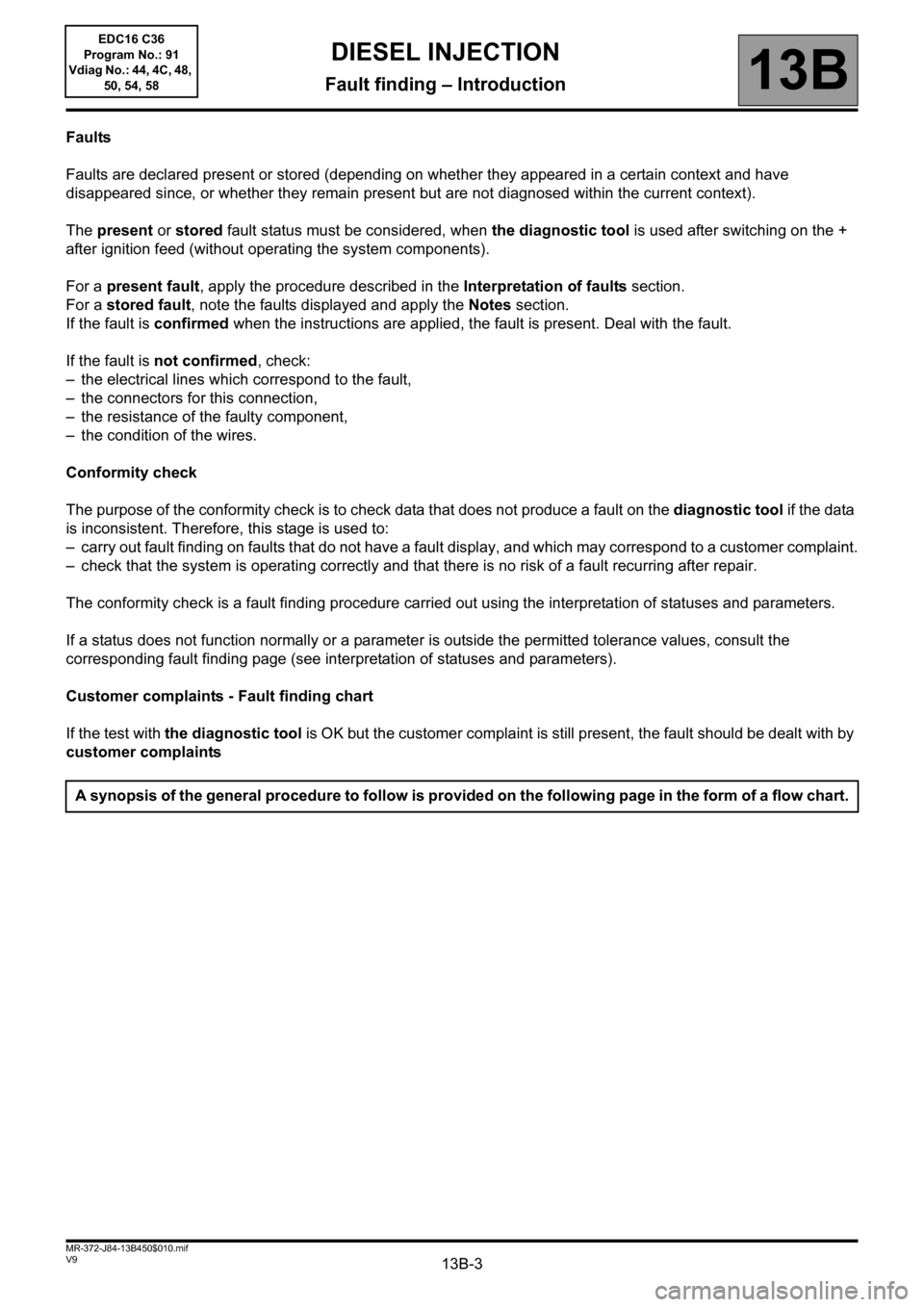
13B-3V9 MR-372-J84-13B450$010.mif
DIESEL INJECTION
Fault finding – Introduction13B
EDC16 C36
Program No.: 91
Vdiag No.: 44, 4C, 48,
50, 54, 58
Faults
Faults are declared present or stored (depending on whether they appeared in a certain context and have
disappeared since, or whether they remain present but are not diagnosed within the current context).
The present or stored fault status must be considered, when the diagnostic tool is used after switching on the +
after ignition feed (without operating the system components).
For a present fault, apply the procedure described in the Interpretation of faults section.
For a stored fault, note the faults displayed and apply the Notes section.
If the fault is confirmed when the instructions are applied, the fault is present. Deal with the fault.
If the fault is not confirmed, check:
– the electrical lines which correspond to the fault,
– the connectors for this connection,
– the resistance of the faulty component,
– the condition of the wires.
Conformity check
The purpose of the conformity check is to check data that does not produce a fault on the diagnostic tool if the data
is inconsistent. Therefore, this stage is used to:
– carry out fault finding on faults that do not have a fault display, and which may correspond to a customer complaint.
– check that the system is operating correctly and that there is no risk of a fault recurring after repair.
The conformity check is a fault finding procedure carried out using the interpretation of statuses and parameters.
If a status does not function normally or a parameter is outside the permitted tolerance values, consult the
corresponding fault finding page (see interpretation of statuses and parameters).
Customer complaints - Fault finding chart
If the test with the diagnostic tool is OK but the customer complaint is still present, the fault should be dealt with by
customer complaints
A synopsis of the general procedure to follow is provided on the following page in the form of a flow chart.
Page 18 of 431
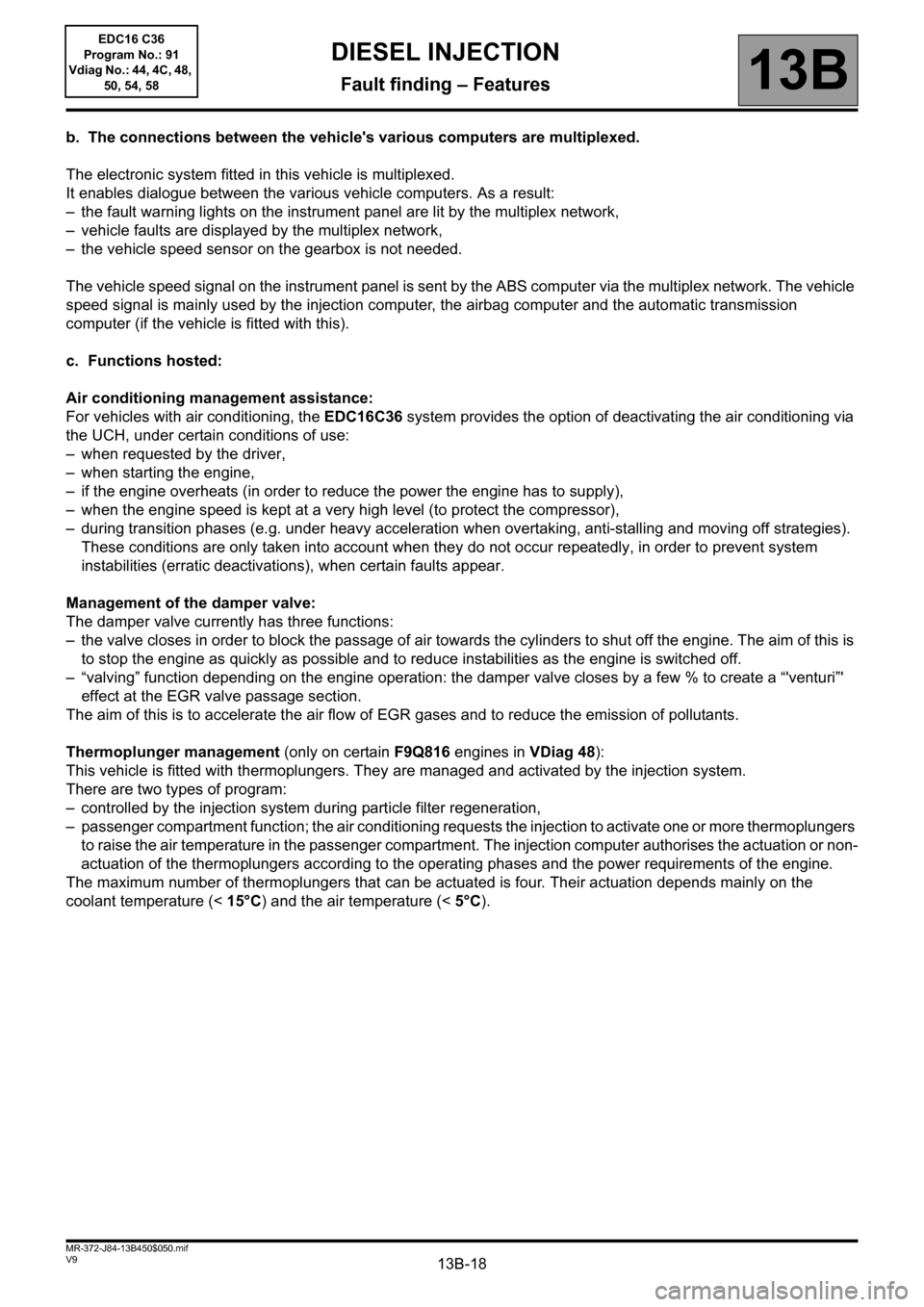
13B-18V9 MR-372-J84-13B450$050.mif
DIESEL INJECTION
Fault finding – Features13B
EDC16 C36
Program No.: 91
Vdiag No.: 44, 4C, 48,
50, 54, 58
b. The connections between the vehicle's various computers are multiplexed.
The electronic system fitted in this vehicle is multiplexed.
It enables dialogue between the various vehicle computers. As a result:
– the fault warning lights on the instrument panel are lit by the multiplex network,
– vehicle faults are displayed by the multiplex network,
– the vehicle speed sensor on the gearbox is not needed.
The vehicle speed signal on the instrument panel is sent by the ABS computer via the multiplex network. The vehicle
speed signal is mainly used by the injection computer, the airbag computer and the automatic transmission
computer (if the vehicle is fitted with this).
c. Functions hosted:
Air conditioning management assistance:
For vehicles with air conditioning, the EDC16C36 system provides the option of deactivating the air conditioning via
the UCH, under certain conditions of use:
– when requested by the driver,
– when starting the engine,
– if the engine overheats (in order to reduce the power the engine has to supply),
– when the engine speed is kept at a very high level (to protect the compressor),
– during transition phases (e.g. under heavy acceleration when overtaking, anti-stalling and moving off strategies).
These conditions are only taken into account when they do not occur repeatedly, in order to prevent system
instabilities (erratic deactivations), when certain faults appear.
Management of the damper valve:
The damper valve currently has three functions:
– the valve closes in order to block the passage of air towards the cylinders to shut off the engine. The aim of this is
to stop the engine as quickly as possible and to reduce instabilities as the engine is switched off.
– “valving” function depending on the engine operation: the damper valve closes by a few % to create a “'venturi”'
effect at the EGR valve passage section.
The aim of this is to accelerate the air flow of EGR gases and to reduce the emission of pollutants.
Thermoplunger management (only on certain F9Q816 engines in VDiag 48):
This vehicle is fitted with thermoplungers. They are managed and activated by the injection system.
There are two types of program:
– controlled by the injection system during particle filter regeneration,
– passenger compartment function; the air conditioning requests the injection to activate one or more thermoplungers
to raise the air temperature in the passenger compartment. The injection computer authorises the actuation or non-
actuation of the thermoplungers according to the operating phases and the power requirements of the engine.
The maximum number of thermoplungers that can be actuated is four. Their actuation depends mainly on the
coolant temperature (< 15°C) and the air temperature (< 5°C).
Page 20 of 431
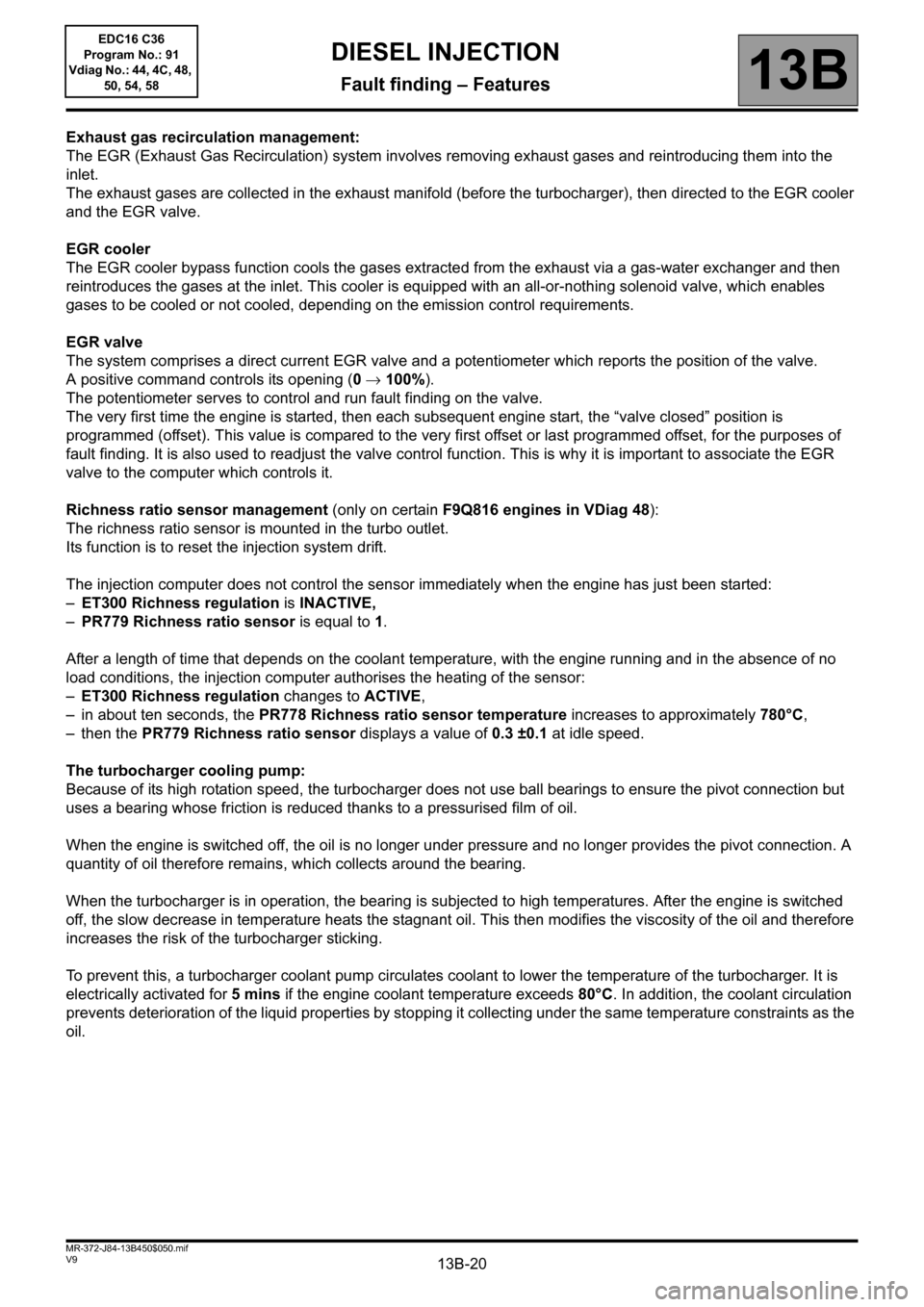
13B-20V9 MR-372-J84-13B450$050.mif
DIESEL INJECTION
Fault finding – Features13B
EDC16 C36
Program No.: 91
Vdiag No.: 44, 4C, 48,
50, 54, 58
Exhaust gas recirculation management:
The EGR (Exhaust Gas Recirculation) system involves removing exhaust gases and reintroducing them into the
inlet.
The exhaust gases are collected in the exhaust manifold (before the turbocharger), then directed to the EGR cooler
and the EGR valve.
EGR cooler
The EGR cooler bypass function cools the gases extracted from the exhaust via a gas-water exchanger and then
reintroduces the gases at the inlet. This cooler is equipped with an all-or-nothing solenoid valve, which enables
gases to be cooled or not cooled, depending on the emission control requirements.
EGR valve
The system comprises a direct current EGR valve and a potentiometer which reports the position of the valve.
A positive command controls its opening (0 → 100%).
The potentiometer serves to control and run fault finding on the valve.
The very first time the engine is started, then each subsequent engine start, the “valve closed” position is
programmed (offset). This value is compared to the very first offset or last programmed offset, for the purposes of
fault finding. It is also used to readjust the valve control function. This is why it is important to associate the EGR
valve to the computer which controls it.
Richness ratio sensor management (only on certain F9Q816 engines in VDiag 48):
The richness ratio sensor is mounted in the turbo outlet.
Its function is to reset the injection system drift.
The injection computer does not control the sensor immediately when the engine has just been started:
–ET300 Richness regulation is INACTIVE,
–PR779 Richness ratio sensor is equal to 1.
After a length of time that depends on the coolant temperature, with the engine running and in the absence of no
load conditions, the injection computer authorises the heating of the sensor:
–ET300 Richness regulation changes to ACTIVE,
– in about ten seconds, the PR778 Richness ratio sensor temperature increases to approximately 780°C,
– then the PR779 Richness ratio sensor displays a value of 0.3 ±0.1 at idle speed.
The turbocharger cooling pump:
Because of its high rotation speed, the turbocharger does not use ball bearings to ensure the pivot connection but
uses a bearing whose friction is reduced thanks to a pressurised film of oil.
When the engine is switched off, the oil is no longer under pressure and no longer provides the pivot connection. A
quantity of oil therefore remains, which collects around the bearing.
When the turbocharger is in operation, the bearing is subjected to high temperatures. After the engine is switched
off, the slow decrease in temperature heats the stagnant oil. This then modifies the viscosity of the oil and therefore
increases the risk of the turbocharger sticking.
To prevent this, a turbocharger coolant pump circulates coolant to lower the temperature of the turbocharger. It is
electrically activated for 5 mins if the engine coolant temperature exceeds 80°C. In addition, the coolant circulation
prevents deterioration of the liquid properties by stopping it collecting under the same temperature constraints as the
oil.
Page 22 of 431
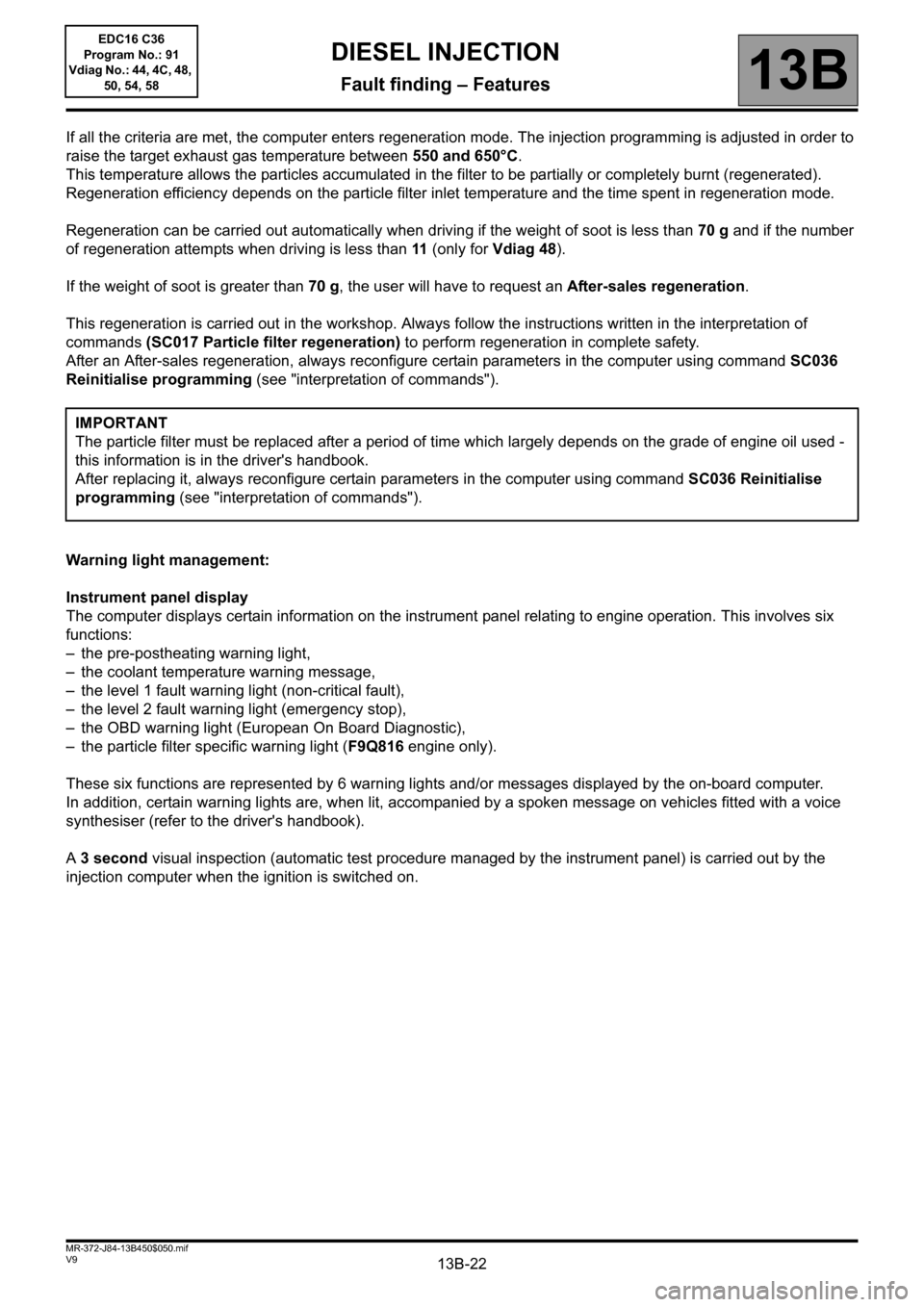
13B-22V9 MR-372-J84-13B450$050.mif
DIESEL INJECTION
Fault finding – Features13B
EDC16 C36
Program No.: 91
Vdiag No.: 44, 4C, 48,
50, 54, 58
If all the criteria are met, the computer enters regeneration mode. The injection programming is adjusted in order to
raise the target exhaust gas temperature between 550 and 650°C.
This temperature allows the particles accumulated in the filter to be partially or completely burnt (regenerated).
Regeneration efficiency depends on the particle filter inlet temperature and the time spent in regeneration mode.
Regeneration can be carried out automatically when driving if the weight of soot is less than 70 g and if the number
of regeneration attempts when driving is less than 11 (only for Vdiag 48).
If the weight of soot is greater than 70 g, the user will have to request an After-sales regeneration.
This regeneration is carried out in the workshop. Always follow the instructions written in the interpretation of
commands (SC017 Particle filter regeneration) to perform regeneration in complete safety.
After an After-sales regeneration, always reconfigure certain parameters in the computer using command SC036
Reinitialise programming (see "interpretation of commands").
Warning light management:
Instrument panel display
The computer displays certain information on the instrument panel relating to engine operation. This involves six
functions:
– the pre-postheating warning light,
– the coolant temperature warning message,
– the level 1 fault warning light (non-critical fault),
– the level 2 fault warning light (emergency stop),
– the OBD warning light (European On Board Diagnostic),
– the particle filter specific warning light (F9Q816 engine only).
These six functions are represented by 6 warning lights and/or messages displayed by the on-board computer.
In addition, certain warning lights are, when lit, accompanied by a spoken message on vehicles fitted with a voice
synthesiser (refer to the driver's handbook).
A 3 second visual inspection (automatic test procedure managed by the instrument panel) is carried out by the
injection computer when the ignition is switched on.IMPORTANT
The particle filter must be replaced after a period of time which largely depends on the grade of engine oil used -
this information is in the driver's handbook.
After replacing it, always reconfigure certain parameters in the computer using command SC036 Reinitialise
programming (see "interpretation of commands").
Page 24 of 431
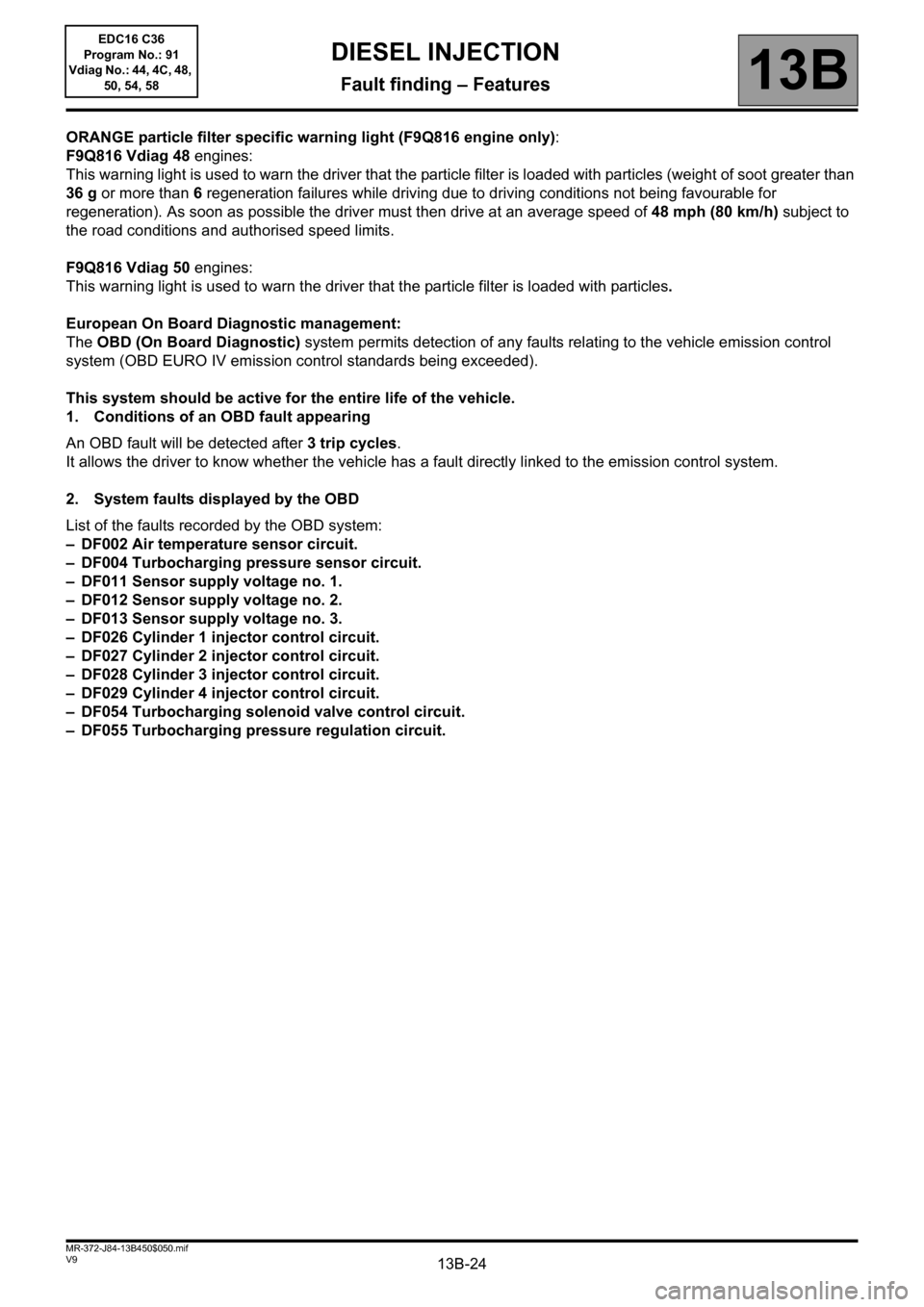
13B-24V9 MR-372-J84-13B450$050.mif
DIESEL INJECTION
Fault finding – Features13B
EDC16 C36
Program No.: 91
Vdiag No.: 44, 4C, 48,
50, 54, 58
ORANGE particle filter specific warning light (F9Q816 engine only):
F9Q816 Vdiag 48 engines:
This warning light is used to warn the driver that the particle filter is loaded with particles (weight of soot greater than
36 g or more than 6 regeneration failures while driving due to driving conditions not being favourable for
regeneration). As soon as possible the driver must then drive at an average speed of 48 mph (80 km/h) subject to
the road conditions and authorised speed limits.
F9Q816 Vdiag 50 engines:
This warning light is used to warn the driver that the particle filter is loaded with particles.
European On Board Diagnostic management:
The OBD (On Board Diagnostic) system permits detection of any faults relating to the vehicle emission control
system (OBD EURO IV emission control standards being exceeded).
This system should be active for the entire life of the vehicle.
1. Conditions of an OBD fault appearing
An OBD fault will be detected after 3 trip cycles.
It allows the driver to know whether the vehicle has a fault directly linked to the emission control system.
2. System faults displayed by the OBD
List of the faults recorded by the OBD system:
– DF002 Air temperature sensor circuit.
– DF004 Turbocharging pressure sensor circuit.
– DF011 Sensor supply voltage no. 1.
– DF012 Sensor supply voltage no. 2.
– DF013 Sensor supply voltage no. 3.
– DF026 Cylinder 1 injector control circuit.
– DF027 Cylinder 2 injector control circuit.
– DF028 Cylinder 3 injector control circuit.
– DF029 Cylinder 4 injector control circuit.
– DF054 Turbocharging solenoid valve control circuit.
– DF055 Turbocharging pressure regulation circuit.
Page 25 of 431
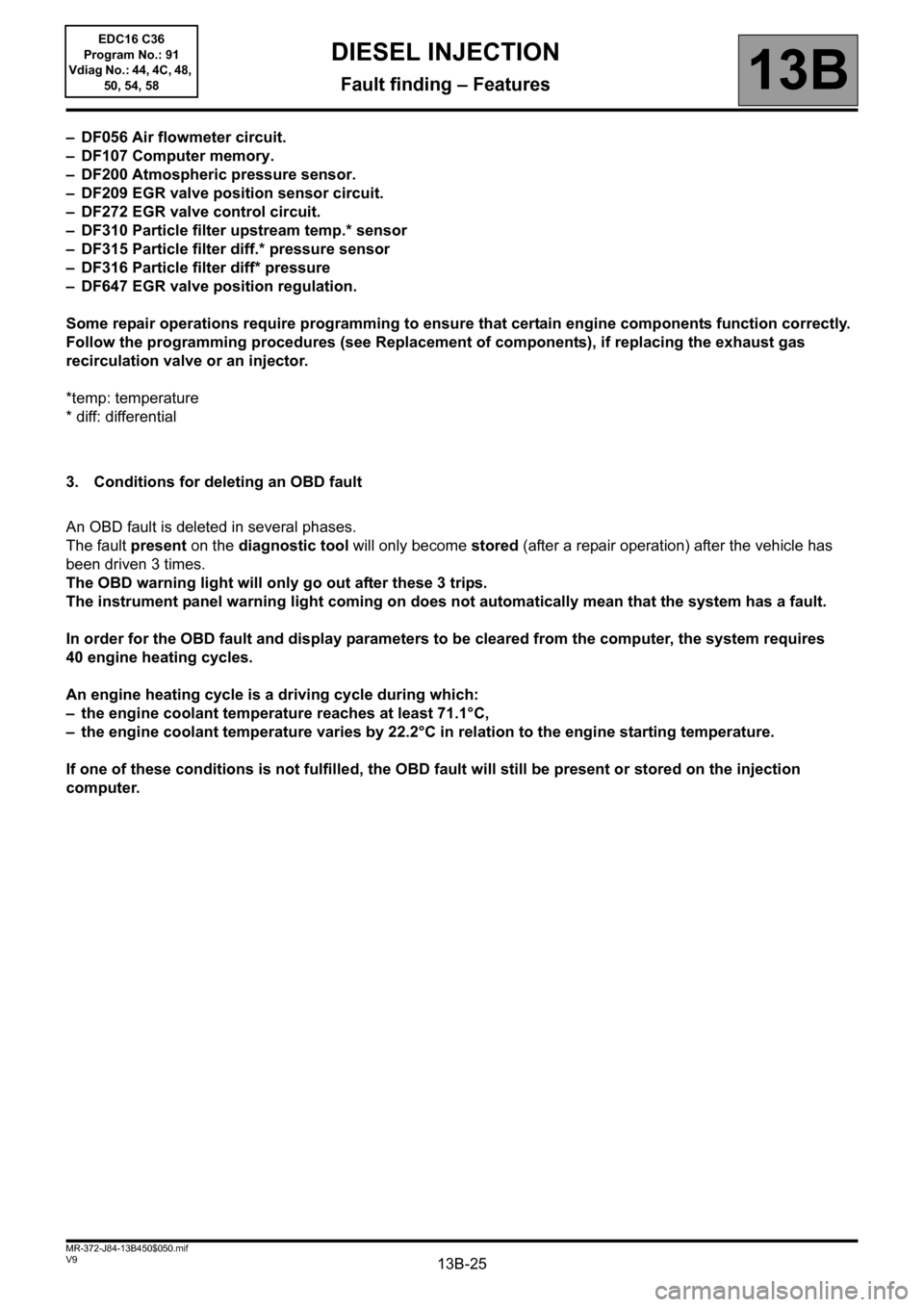
13B-25V9 MR-372-J84-13B450$050.mif
DIESEL INJECTION
Fault finding – Features13B
EDC16 C36
Program No.: 91
Vdiag No.: 44, 4C, 48,
50, 54, 58
– DF056 Air flowmeter circuit.
– DF107 Computer memory.
– DF200 Atmospheric pressure sensor.
– DF209 EGR valve position sensor circuit.
– DF272 EGR valve control circuit.
– DF310 Particle filter upstream temp.* sensor
– DF315 Particle filter diff.* pressure sensor
– DF316 Particle filter diff* pressure
– DF647 EGR valve position regulation.
Some repair operations require programming to ensure that certain engine components function correctly.
Follow the programming procedures (see Replacement of components), if replacing the exhaust gas
recirculation valve or an injector.
*temp: temperature
* diff: differential
3. Conditions for deleting an OBD fault
An OBD fault is deleted in several phases.
The fault present on the diagnostic tool will only become stored (after a repair operation) after the vehicle has
been driven 3 times.
The OBD warning light will only go out after these 3 trips.
The instrument panel warning light coming on does not automatically mean that the system has a fault.
In order for the OBD fault and display parameters to be cleared from the computer, the system requires
40 engine heating cycles.
An engine heating cycle is a driving cycle during which:
– the engine coolant temperature reaches at least 71.1°C,
– the engine coolant temperature varies by 22.2°C in relation to the engine starting temperature.
If one of these conditions is not fulfilled, the OBD fault will still be present or stored on the injection
computer.
Page 29 of 431
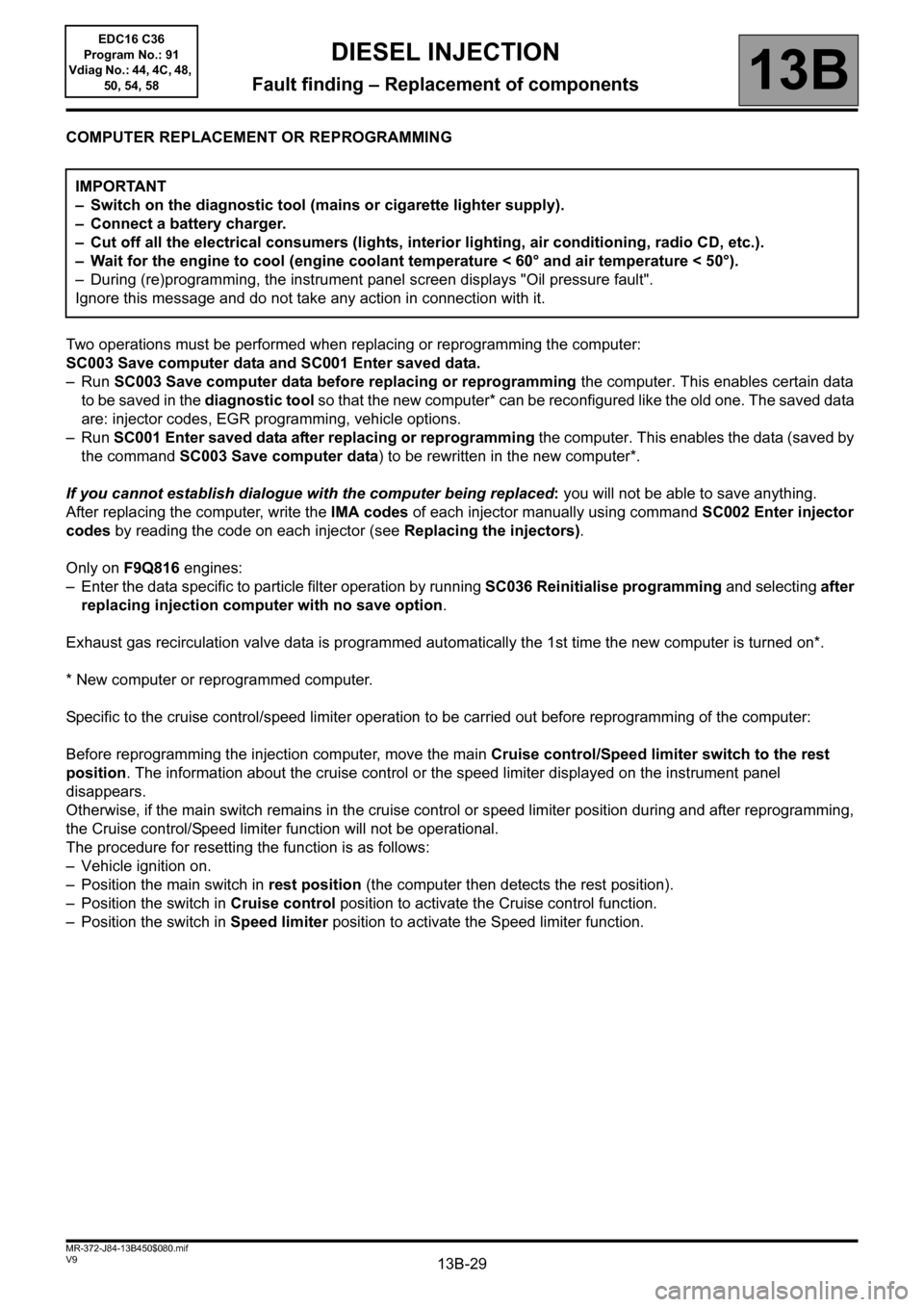
13B-29V9 MR-372-J84-13B450$080.mif
13B
EDC16 C36
Program No.: 91
Vdiag No.: 44, 4C, 48,
50, 54, 58
COMPUTER REPLACEMENT OR REPROGRAMMING
Two operations must be performed when replacing or reprogramming the computer:
SC003 Save computer data and SC001 Enter saved data.
–Run SC003 Save computer data before replacing or reprogramming the computer. This enables certain data
to be saved in the diagnostic tool so that the new computer* can be reconfigured like the old one. The saved data
are: injector codes, EGR programming, vehicle options.
–Run SC001 Enter saved data after replacing or reprogramming the computer. This enables the data (saved by
the command SC003 Save computer data) to be rewritten in the new computer*.
If you cannot establish dialogue with the computer being replaced: you will not be able to save anything.
After replacing the computer, write the IMA codes of each injector manually using command SC002 Enter injector
codes by reading the code on each injector (see Replacing the injectors).
Only on F9Q816 engines:
– Enter the data specific to particle filter operation by running SC036 Reinitialise programming and selecting after
replacing injection computer with no save option.
Exhaust gas recirculation valve data is programmed automatically the 1st time the new computer is turned on*.
* New computer or reprogrammed computer.
Specific to the cruise control/speed limiter operation to be carried out before reprogramming of the computer:
Before reprogramming the injection computer, move the main Cruise control/Speed limiter switch to the rest
position. The information about the cruise control or the speed limiter displayed on the instrument panel
disappears.
Otherwise, if the main switch remains in the cruise control or speed limiter position during and after reprogramming,
the Cruise control/Speed limiter function will not be operational.
The procedure for resetting the function is as follows:
– Vehicle ignition on.
– Position the main switch in rest position (the computer then detects the rest position).
– Position the switch in Cruise control position to activate the Cruise control function.
– Position the switch in Speed limiter position to activate the Speed limiter function. IMPORTANT
– Switch on the diagnostic tool (mains or cigarette lighter supply).
– Connect a battery charger.
– Cut off all the electrical consumers (lights, interior lighting, air conditioning, radio CD, etc.).
– Wait for the engine to cool (engine coolant temperature < 60° and air temperature < 50°).
– During (re)programming, the instrument panel screen displays "Oil pressure fault".
Ignore this message and do not take any action in connection with it.
DIESEL INJECTION
Fault finding – Replacement of components
Page 32 of 431
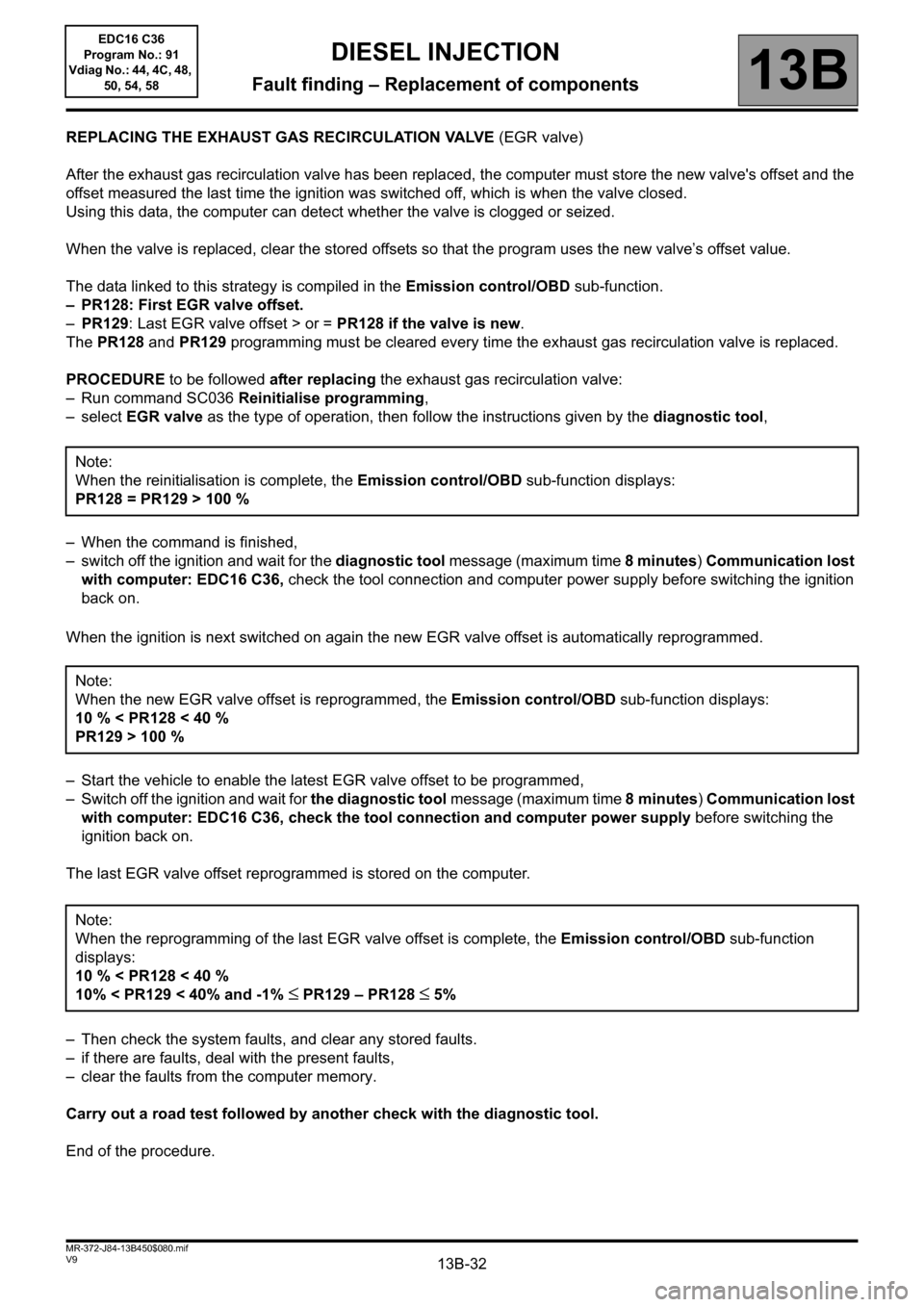
13B-32V9 MR-372-J84-13B450$080.mif
DIESEL INJECTION
Fault finding – Replacement of components13B
EDC16 C36
Program No.: 91
Vdiag No.: 44, 4C, 48,
50, 54, 58
REPLACING THE EXHAUST GAS RECIRCULATION VALVE (EGR valve)
After the exhaust gas recirculation valve has been replaced, the computer must store the new valve's offset and the
offset measured the last time the ignition was switched off, which is when the valve closed.
Using this data, the computer can detect whether the valve is clogged or seized.
When the valve is replaced, clear the stored offsets so that the program uses the new valve’s offset value.
The data linked to this strategy is compiled in the Emission control/OBD sub-function.
– PR128: First EGR valve offset.
–PR129: Last EGR valve offset > or = PR128 if the valve is new.
The PR128 and PR129 programming must be cleared every time the exhaust gas recirculation valve is replaced.
PROCEDURE to be followed after replacing the exhaust gas recirculation valve:
– Run command SC036 Reinitialise programming,
–select EGR valve as the type of operation, then follow the instructions given by the diagnostic tool,
– When the command is finished,
– switch off the ignition and wait for the diagnostic tool message (maximum time 8 minutes) Communication lost
with computer: EDC16 C36, check the tool connection and computer power supply before switching the ignition
back on.
When the ignition is next switched on again the new EGR valve offset is automatically reprogrammed.
– Start the vehicle to enable the latest EGR valve offset to be programmed,
– Switch off the ignition and wait for the diagnostic tool message (maximum time 8 minutes) Communication lost
with computer: EDC16 C36, check the tool connection and computer power supply before switching the
ignition back on.
The last EGR valve offset reprogrammed is stored on the computer.
– Then check the system faults, and clear any stored faults.
– if there are faults, deal with the present faults,
– clear the faults from the computer memory.
Carry out a road test followed by another check with the diagnostic tool.
End of the procedure.Note:
When the reinitialisation is complete, the Emission control/OBD sub-function displays:
PR128 = PR129 > 100 %
Note:
When the new EGR valve offset is reprogrammed, the Emission control/OBD sub-function displays:
10 % < PR128 < 40 %
PR129 > 100 %
Note:
When the reprogramming of the last EGR valve offset is complete, the Emission control/OBD sub-function
displays:
10 % < PR128 < 40 %
10% < PR129 < 40% and -1%
≤ PR129 – PR128 ≤ 5%
Page 83 of 431
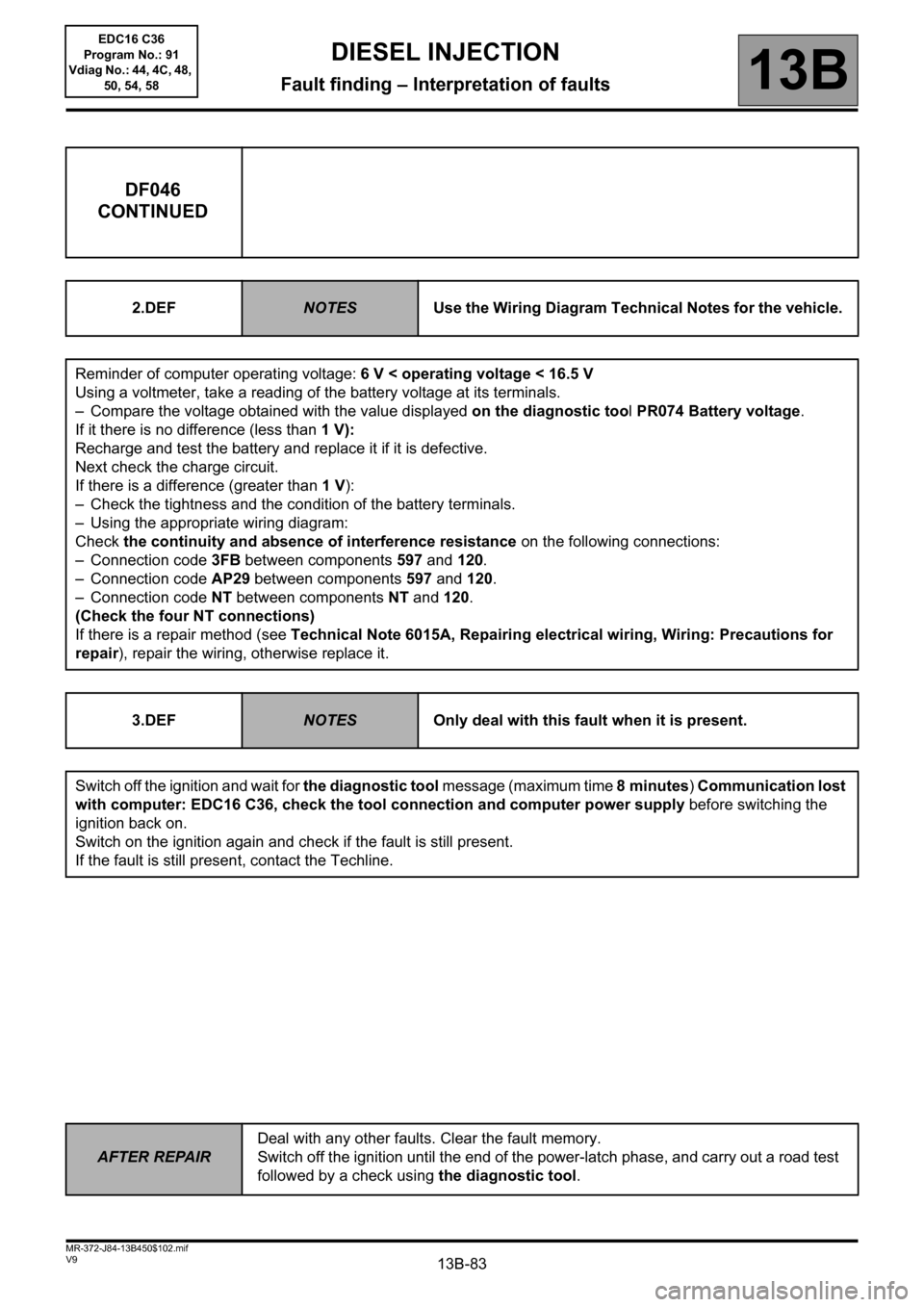
13B-83V9 MR-372-J84-13B450$102.mif
DIESEL INJECTION
Fault finding – Interpretation of faults13B
DF046
CONTINUED
2.DEFNOTESUse the Wiring Diagram Technical Notes for the vehicle.
Reminder of computer operating voltage: 6 V < operating voltage < 16.5 V
Using a voltmeter, take a reading of the battery voltage at its terminals.
– Compare the voltage obtained with the value displayed on the diagnostic tool PR074 Battery voltage.
If it there is no difference (less than 1 V):
Recharge and test the battery and replace it if it is defective.
Next check the charge circuit.
If there is a difference (greater than 1 V):
– Check the tightness and the condition of the battery terminals.
– Using the appropriate wiring diagram:
Check the continuity and absence of interference resistance on the following connections:
– Connection code 3FB between components 597 and 120.
– Connection code AP29 between components 597 and 120.
– Connection code NT between components NT and 120.
(Check the four NT connections)
If there is a repair method (see Technical Note 6015A, Repairing electrical wiring, Wiring: Precautions for
repair), repair the wiring, otherwise replace it.
3.DEF
NOTESOnly deal with this fault when it is present.
Switch off the ignition and wait for the diagnostic tool message (maximum time 8minutes) Communication lost
with computer: EDC16 C36, check the tool connection and computer power supply before switching the
ignition back on.
Switch on the ignition again and check if the fault is still present.
If the fault is still present, contact the Techline.
AFTER REPAIRDeal with any other faults. Clear the fault memory.
Switch off the ignition until the end of the power-latch phase, and carry out a road test
followed by a check using the diagnostic tool.
EDC16 C36
Program No.: 91
Vdiag No.: 44, 4C, 48,
50, 54, 58
Page 87 of 431
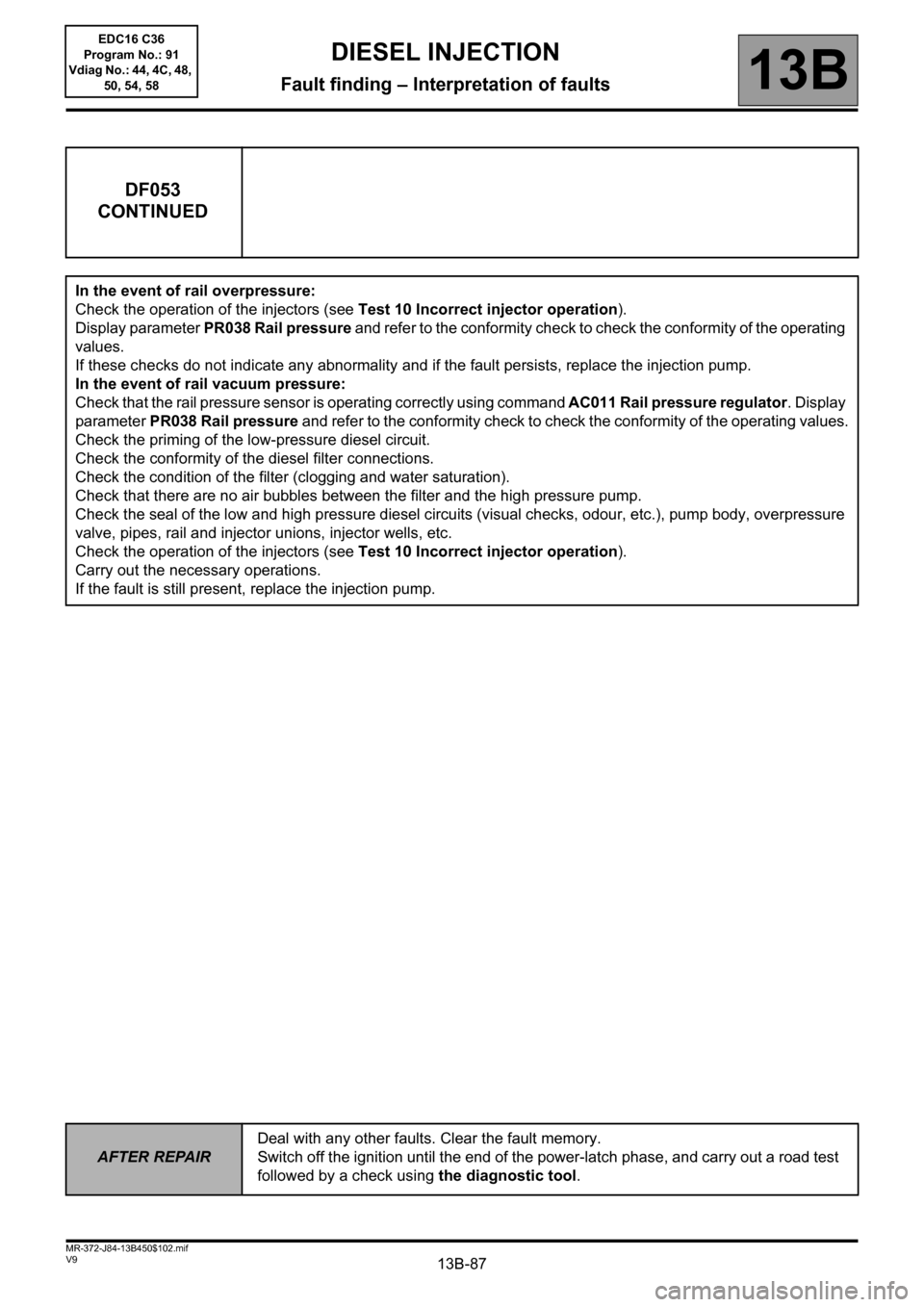
13B-87V9 MR-372-J84-13B450$102.mif
DIESEL INJECTION
Fault finding – Interpretation of faults13B
DF053
CONTINUED
In the event of rail overpressure:
Check the operation of the injectors (see Test 10 Incorrect injector operation).
Display parameter PR038 Rail pressure and refer to the conformity check to check the conformity of the operating
values.
If these checks do not indicate any abnormality and if the fault persists, replace the injection pump.
In the event of rail vacuum pressure:
Check that the rail pressure sensor is operating correctly using command AC011 Rail pressure regulator. Display
parameter PR038 Rail pressure and refer to the conformity check to check the conformity of the operating values.
Check the priming of the low-pressure diesel circuit.
Check the conformity of the diesel filter connections.
Check the condition of the filter (clogging and water saturation).
Check that there are no air bubbles between the filter and the high pressure pump.
Check the seal of the low and high pressure diesel circuits (visual checks, odour, etc.), pump body, overpressure
valve, pipes, rail and injector unions, injector wells, etc.
Check the operation of the injectors (see Test 10 Incorrect injector operation).
Carry out the necessary operations.
If the fault is still present, replace the injection pump.
AFTER REPAIRDeal with any other faults. Clear the fault memory.
Switch off the ignition until the end of the power-latch phase, and carry out a road test
followed by a check using the diagnostic tool.
EDC16 C36
Program No.: 91
Vdiag No.: 44, 4C, 48,
50, 54, 58