RENAULT SCENIC 2012 J95 / 3.G Engine And Peripherals EDC16CP33 Workshop Manual
Manufacturer: RENAULT, Model Year: 2012, Model line: SCENIC, Model: RENAULT SCENIC 2012 J95 / 3.GPages: 510, PDF Size: 2.98 MB
Page 1 of 510
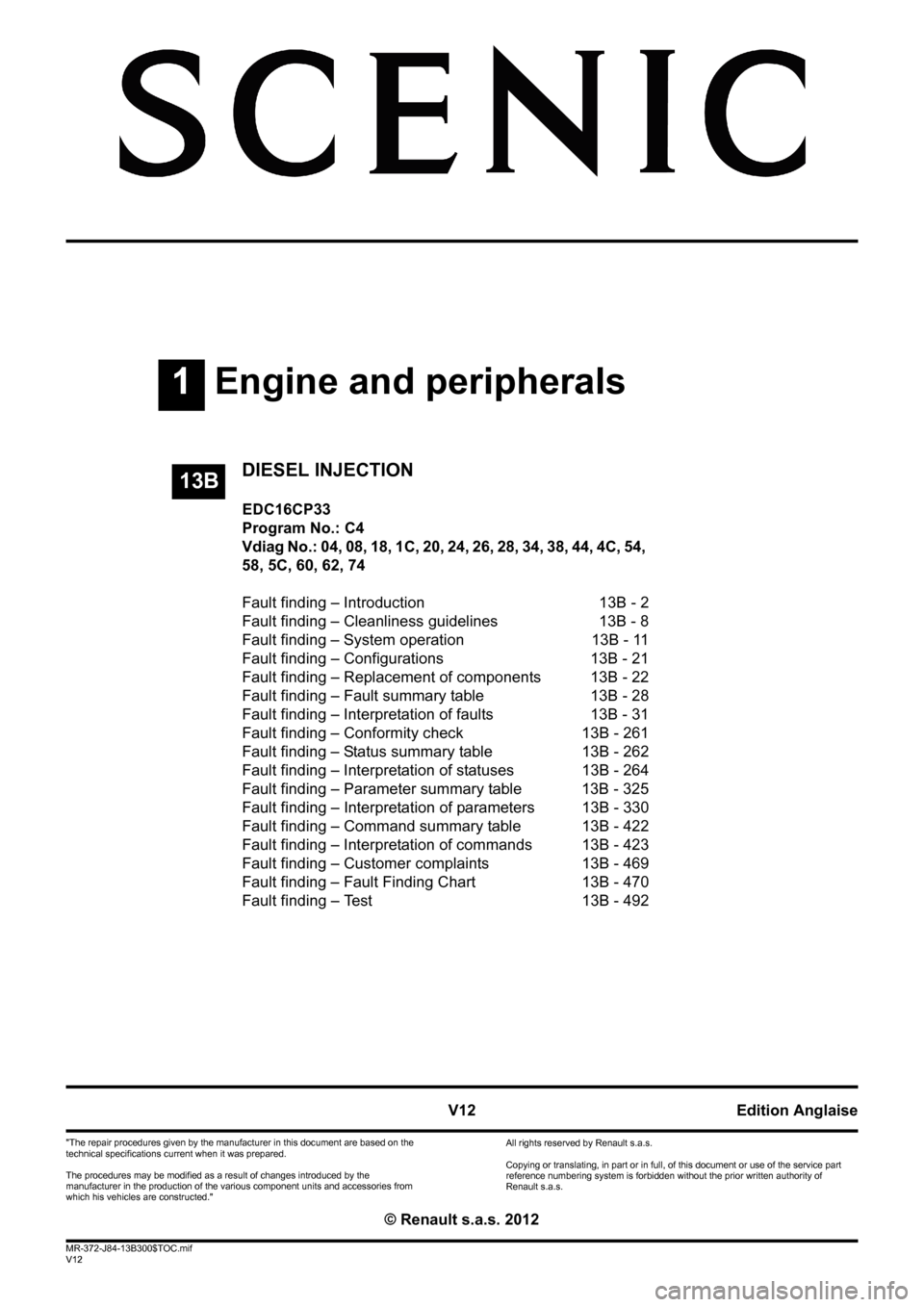
1Engine and peripherals
V12 MR-372-J84-13B300$TOC.mif
V12
13B
"The repair procedures given by the manufacturer in this document are based on the
technical specifications current when it was prepared.
The procedures may be modified as a result of changes introduced by the
manufacturer in the production of the various component units and accessories from
which his vehicles are constructed."
V12
All rights reserved by Renault s.a.s.
Edition Anglaise
Copying or translating, in part or in full, of this document or use of the service part
reference numbering system is forbidden without the prior written authority of
Renault s.a.s.
© Renault s.a.s. 2012
DIESEL INJECTION
EDC16CP33
Program No.: C4
Vdiag No.: 04, 08, 18, 1C, 20, 24, 26, 28, 34, 38, 44, 4C, 54,
58, 5C, 60, 62, 74
Fault finding – Introduction 13B - 2
Fault finding – Cleanliness guidelines 13B - 8
Fault finding – System operation 13B - 11
Fault finding – Configurations 13B - 21
Fault finding – Replacement of components 13B - 22
Fault finding – Fault summary table 13B - 28
Fault finding – Interpretation of faults 13B - 31
Fault finding – Conformity check 13B - 261
Fault finding – Status summary table 13B - 262
Fault finding – Interpretation of statuses 13B - 264
Fault finding – Parameter summary table 13B - 325
Fault finding – Interpretation of parameters 13B - 330
Fault finding – Command summary table 13B - 422
Fault finding – Interpretation of commands 13B - 423
Fault finding – Customer complaints 13B - 469
Fault finding – Fault Finding Chart 13B - 470
Fault finding – Test 13B - 492
Page 2 of 510
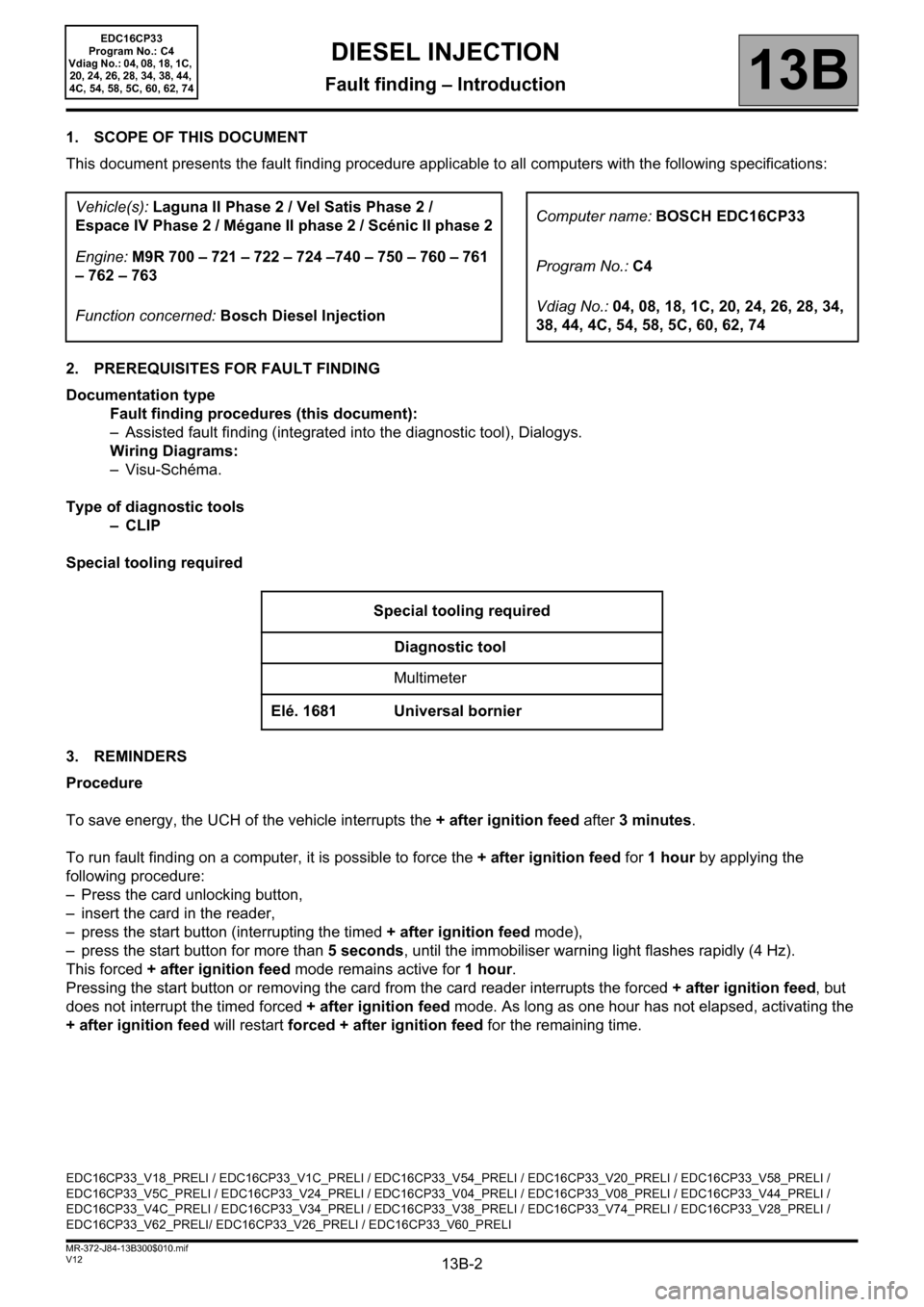
13B-2V12 MR-372-J84-13B300$010.mif
13B
EDC16CP33
Program No.: C4
Vdiag No.: 04, 08, 18, 1C,
20, 24, 26, 28, 34, 38, 44,
4C, 54, 58, 5C, 60, 62, 74
1. SCOPE OF THIS DOCUMENT
This document presents the fault finding procedure applicable to all computers with the following specifications:
2. PREREQUISITES FOR FAULT FINDING
Documentation type
Fault finding procedures (this document):
– Assisted fault finding (integrated into the diagnostic tool), Dialogys.
Wiring Diagrams:
–Visu-Schéma.
Type of diagnostic tools
–CLIP
Special tooling required
3. REMINDERS
Procedure
To save energy, the UCH of the vehicle interrupts the + after ignition feed after 3 minutes.
To run fault finding on a computer, it is possible to force the + after ignition feed for 1 hour by applying the
following procedure:
– Press the card unlocking button,
– insert the card in the reader,
– press the start button (interrupting the timed + after ignition feed mode),
– press the start button for more than 5 seconds, until the immobiliser warning light flashes rapidly (4 Hz).
This forced + after ignition feed mode remains active for 1 hour.
Pressing the start button or removing the card from the card reader interrupts the forced + after ignition feed, but
does not interrupt the timed forced + after ignition feed mode. As long as one hour has not elapsed, activating the
+ after ignition feed will restart forced + after ignition feed for the remaining time. Vehicle(s): Laguna II Phase 2 / Vel Satis Phase 2 /
Espace IV Phase 2 / Mégane II phase 2 / Scénic II phase 2Computer name: BOSCH EDC16CP33
Engine: M9R 700 – 721 – 722 – 724 –740 – 750 – 760 – 761
– 762 – 763Program No.: C4
Function concerned: Bosch Diesel InjectionVdiag No.: 04, 08, 18, 1C, 20, 24, 26, 28, 34,
38, 44, 4C, 54, 58, 5C, 60, 62, 74
Special tooling required
Diagnostic tool
Multimeter
Elé. 1681 Universal bornier
EDC16CP33_V18_PRELI / EDC16CP33_V1C_PRELI / EDC16CP33_V54_PRELI / EDC16CP33_V20_PRELI / EDC16CP33_V58_PRELI /
EDC16CP33_V5C_PRELI / EDC16CP33_V24_PRELI / EDC16CP33_V04_PRELI / EDC16CP33_V08_PRELI / EDC16CP33_V44_PRELI /
EDC16CP33_V4C_PRELI / EDC16CP33_V34_PRELI / EDC16CP33_V38_PRELI / EDC16CP33_V74_PRELI / EDC16CP33_V28_PRELI /
EDC16CP33_V62_PRELI/ EDC16CP33_V26_PRELI / EDC16CP33_V60_PRELI
DIESEL INJECTION
Fault finding – Introduction
Page 3 of 510
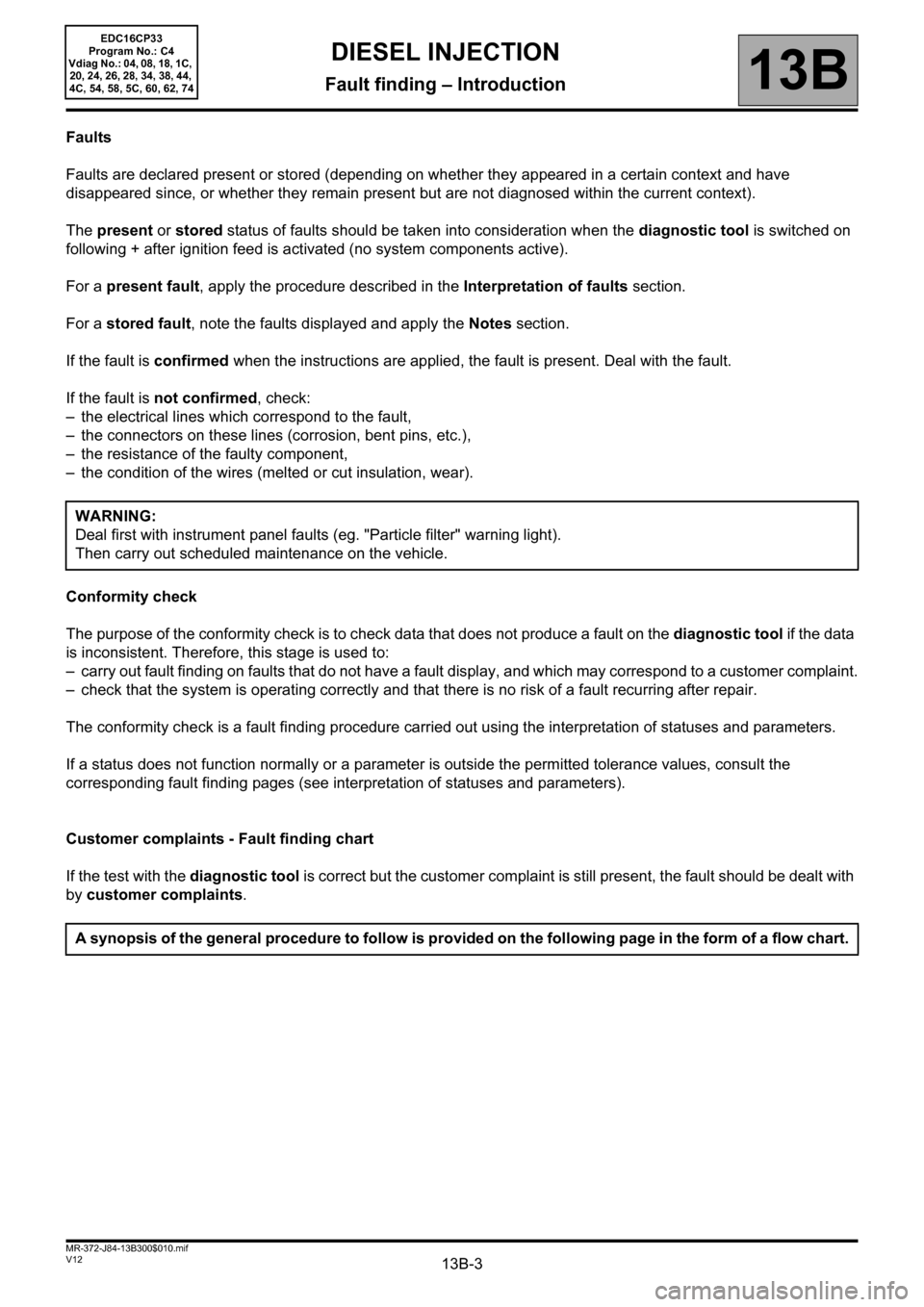
13B-3V12 MR-372-J84-13B300$010.mif
DIESEL INJECTION
Fault finding – Introduction13B
EDC16CP33
Program No.: C4
Vdiag No.: 04, 08, 18, 1C,
20, 24, 26, 28, 34, 38, 44,
4C, 54, 58, 5C, 60, 62, 74
Faults
Faults are declared present or stored (depending on whether they appeared in a certain context and have
disappeared since, or whether they remain present but are not diagnosed within the current context).
The present or stored status of faults should be taken into consideration when the diagnostic tool is switched on
following + after ignition feed is activated (no system components active).
For a present fault, apply the procedure described in the Interpretation of faults section.
For a stored fault, note the faults displayed and apply the Notes section.
If the fault is confirmed when the instructions are applied, the fault is present. Deal with the fault.
If the fault is not confirmed, check:
– the electrical lines which correspond to the fault,
– the connectors on these lines (corrosion, bent pins, etc.),
– the resistance of the faulty component,
– the condition of the wires (melted or cut insulation, wear).
Conformity check
The purpose of the conformity check is to check data that does not produce a fault on the diagnostic tool if the data
is inconsistent. Therefore, this stage is used to:
– carry out fault finding on faults that do not have a fault display, and which may correspond to a customer complaint.
– check that the system is operating correctly and that there is no risk of a fault recurring after repair.
The conformity check is a fault finding procedure carried out using the interpretation of statuses and parameters.
If a status does not function normally or a parameter is outside the permitted tolerance values, consult the
corresponding fault finding pages (see interpretation of statuses and parameters).
Customer complaints - Fault finding chart
If the test with the diagnostic tool is correct but the customer complaint is still present, the fault should be dealt with
by customer complaints. WARNING:
Deal first with instrument panel faults (eg. "Particle filter" warning light).
Then carry out scheduled maintenance on the vehicle.
A synopsis of the general procedure to follow is provided on the following page in the form of a flow chart.
Page 4 of 510
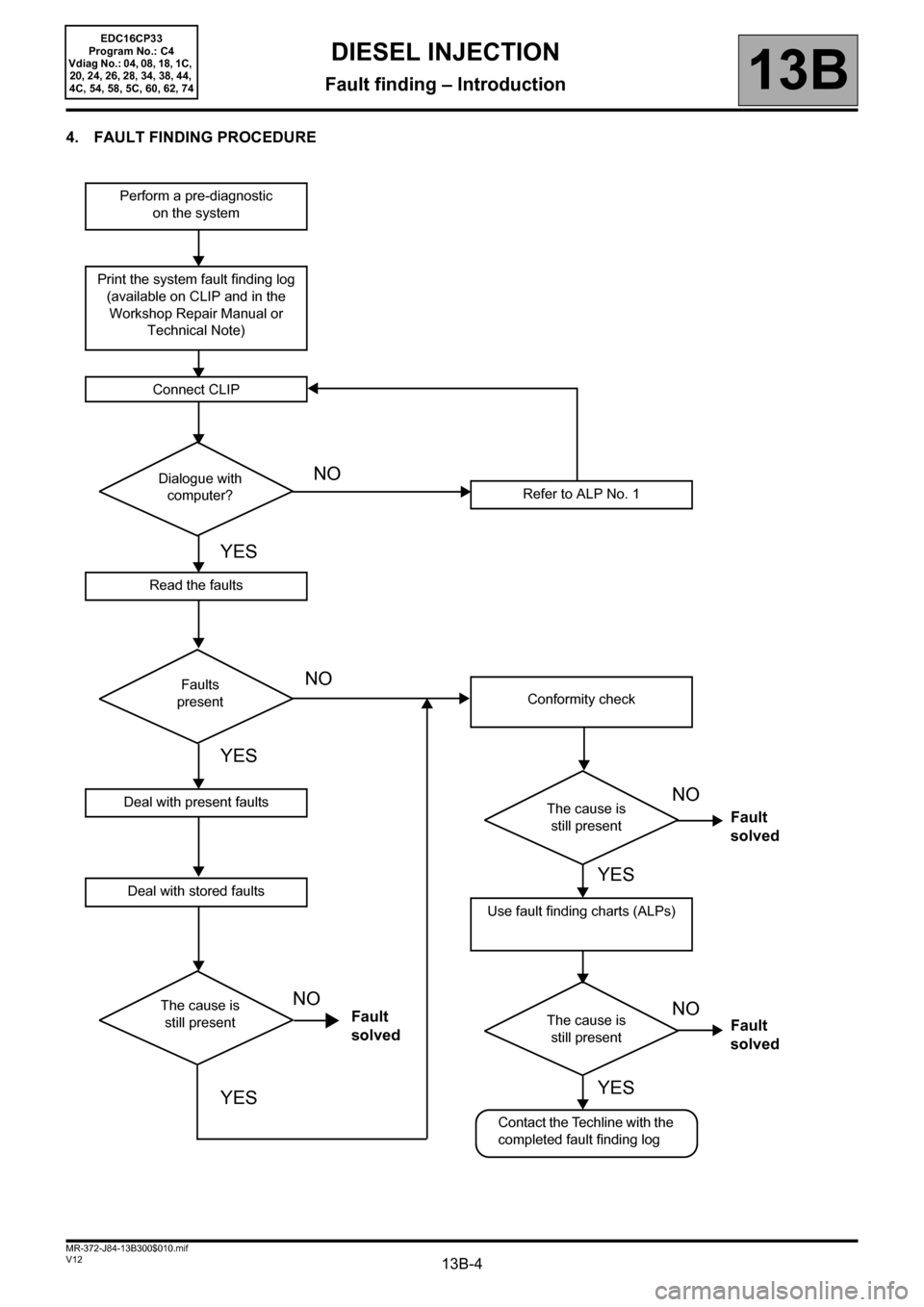
13B-4V12 MR-372-J84-13B300$010.mif
DIESEL INJECTION
Fault finding – Introduction13B
EDC16CP33
Program No.: C4
Vdiag No.: 04, 08, 18, 1C,
20, 24, 26, 28, 34, 38, 44,
4C, 54, 58, 5C, 60, 62, 74
4. FAULT FINDING PROCEDURE
Perform a pre-diagnostic
on the system
Print the system fault finding log
(available on CLIP and in the
Workshop Repair Manual or
Technical Note)
Connect CLIP
Refer to ALP No. 1
Read the faults
Deal with present faults
Deal with stored faults
Conformity check
Use fault finding charts (ALPs)
Dialogue with
computer?
Faults
present
The cause is
still present
The cause is
still presentThe cause is
still present
Contact the Techline with the
completed fault finding log
NO
NONO
NO NO
YES
YES
YES
Fault
solvedFault
solved Fault
solved
YES YES
Page 5 of 510
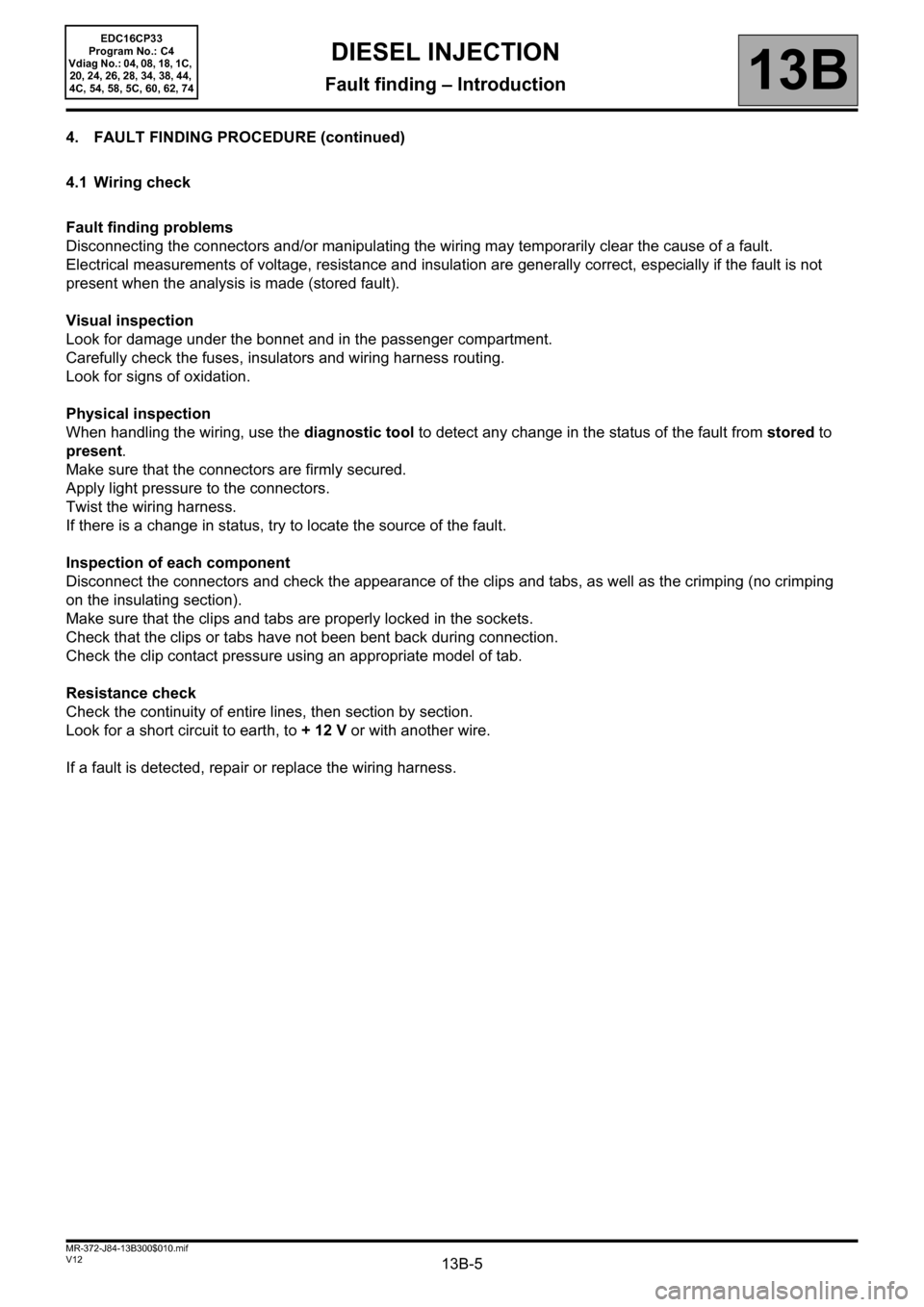
13B-5V12 MR-372-J84-13B300$010.mif
DIESEL INJECTION
Fault finding – Introduction13B
EDC16CP33
Program No.: C4
Vdiag No.: 04, 08, 18, 1C,
20, 24, 26, 28, 34, 38, 44,
4C, 54, 58, 5C, 60, 62, 74
4. FAULT FINDING PROCEDURE (continued)
4.1 Wiring check
Fault finding problems
Disconnecting the connectors and/or manipulating the wiring may temporarily clear the cause of a fault.
Electrical measurements of voltage, resistance and insulation are generally correct, especially if the fault is not
present when the analysis is made (stored fault).
Visual inspection
Look for damage under the bonnet and in the passenger compartment.
Carefully check the fuses, insulators and wiring harness routing.
Look for signs of oxidation.
Physical inspection
When handling the wiring, use the diagnostic tool to detect any change in the status of the fault from stored to
present.
Make sure that the connectors are firmly secured.
Apply light pressure to the connectors.
Twist the wiring harness.
If there is a change in status, try to locate the source of the fault.
Inspection of each component
Disconnect the connectors and check the appearance of the clips and tabs, as well as the crimping (no crimping
on the insulating section).
Make sure that the clips and tabs are properly locked in the sockets.
Check that the clips or tabs have not been bent back during connection.
Check the clip contact pressure using an appropriate model of tab.
Resistance check
Check the continuity of entire lines, then section by section.
Look for a short circuit to earth, to + 12 V or with another wire.
If a fault is detected, repair or replace the wiring harness.
Page 6 of 510
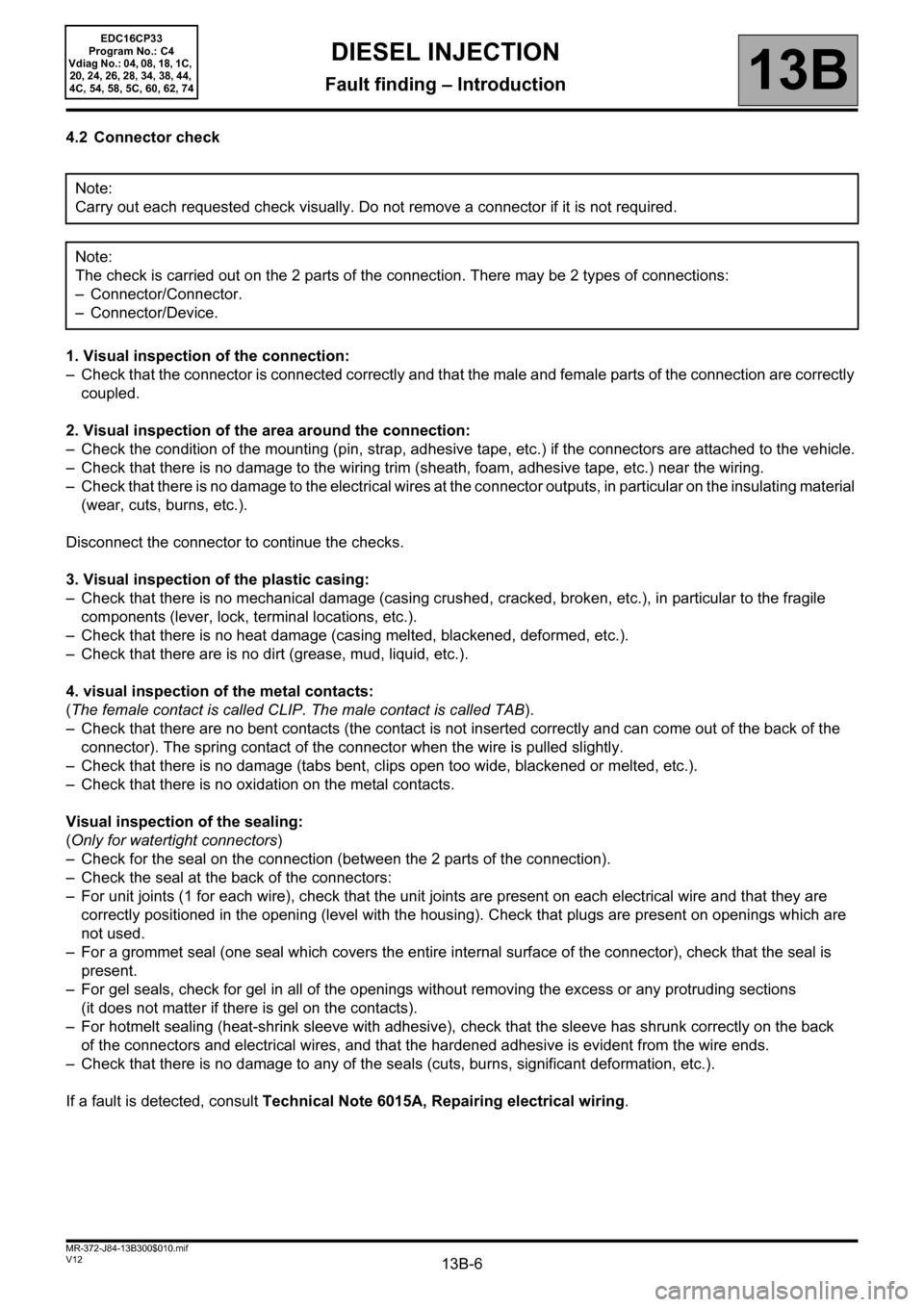
13B-6V12 MR-372-J84-13B300$010.mif
DIESEL INJECTION
Fault finding – Introduction13B
EDC16CP33
Program No.: C4
Vdiag No.: 04, 08, 18, 1C,
20, 24, 26, 28, 34, 38, 44,
4C, 54, 58, 5C, 60, 62, 74
4.2 Connector check
1. Visual inspection of the connection:
– Check that the connector is connected correctly and that the male and female parts of the connection are correctly
coupled.
2. Visual inspection of the area around the connection:
– Check the condition of the mounting (pin, strap, adhesive tape, etc.) if the connectors are attached to the vehicle.
– Check that there is no damage to the wiring trim (sheath, foam, adhesive tape, etc.) near the wiring.
– Check that there is no damage to the electrical wires at the connector outputs, in particular on the insulating material
(wear, cuts, burns, etc.).
Disconnect the connector to continue the checks.
3. Visual inspection of the plastic casing:
– Check that there is no mechanical damage (casing crushed, cracked, broken, etc.), in particular to the fragile
components (lever, lock, terminal locations, etc.).
– Check that there is no heat damage (casing melted, blackened, deformed, etc.).
– Check that there are is no dirt (grease, mud, liquid, etc.).
4. visual inspection of the metal contacts:
(The female contact is called CLIP. The male contact is called TAB).
– Check that there are no bent contacts (the contact is not inserted correctly and can come out of the back of the
connector). The spring contact of the connector when the wire is pulled slightly.
– Check that there is no damage (tabs bent, clips open too wide, blackened or melted, etc.).
– Check that there is no oxidation on the metal contacts.
Visual inspection of the sealing:
(Only for watertight connectors)
– Check for the seal on the connection (between the 2 parts of the connection).
– Check the seal at the back of the connectors:
– For unit joints (1 for each wire), check that the unit joints are present on each electrical wire and that they are
correctly positioned in the opening (level with the housing). Check that plugs are present on openings which are
not used.
– For a grommet seal (one seal which covers the entire internal surface of the connector), check that the seal is
present.
– For gel seals, check for gel in all of the openings without removing the excess or any protruding sections
(it does not matter if there is gel on the contacts).
– For hotmelt sealing (heat-shrink sleeve with adhesive), check that the sleeve has shrunk correctly on the back
of the connectors and electrical wires, and that the hardened adhesive is evident from the wire ends.
– Check that there is no damage to any of the seals (cuts, burns, significant deformation, etc.).
If a fault is detected, consult Technical Note 6015A, Repairing electrical wiring. Note:
Carry out each requested check visually. Do not remove a connector if it is not required.
Note:
The check is carried out on the 2 parts of the connection. There may be 2 types of connections:
– Connector/Connector.
– Connector/Device.
Page 7 of 510
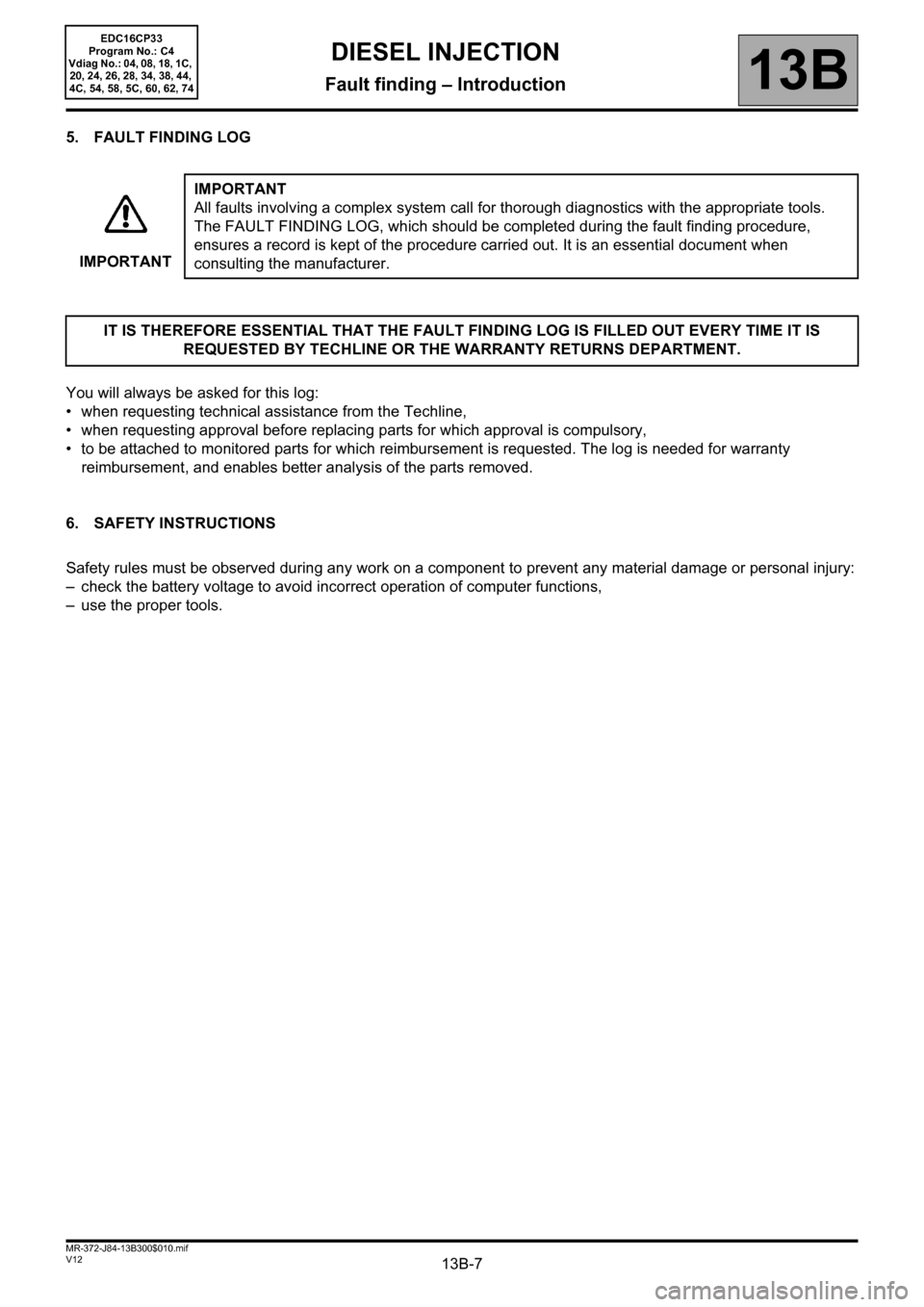
13B-7V12 MR-372-J84-13B300$010.mif
DIESEL INJECTION
Fault finding – Introduction13B
EDC16CP33
Program No.: C4
Vdiag No.: 04, 08, 18, 1C,
20, 24, 26, 28, 34, 38, 44,
4C, 54, 58, 5C, 60, 62, 74
5. FAULT FINDING LOG
You will always be asked for this log:
• when requesting technical assistance from the Techline,
• when requesting approval before replacing parts for which approval is compulsory,
• to be attached to monitored parts for which reimbursement is requested. The log is needed for warranty
reimbursement, and enables better analysis of the parts removed.
6. SAFETY INSTRUCTIONS
Safety rules must be observed during any work on a component to prevent any material damage or personal injury:
– check the battery voltage to avoid incorrect operation of computer functions,
– use the proper tools.IMPORTANTIMPORTANT
All faults involving a complex system call for thorough diagnostics with the appropriate tools.
The FAULT FINDING LOG, which should be completed during the fault finding procedure,
ensures a record is kept of the procedure carried out. It is an essential document when
consulting the manufacturer.
IT IS THEREFORE ESSENTIAL THAT THE FAULT FINDING LOG IS FILLED OUT EVERY TIME IT IS
REQUESTED BY TECHLINE OR THE WARRANTY RETURNS DEPARTMENT.
Page 8 of 510
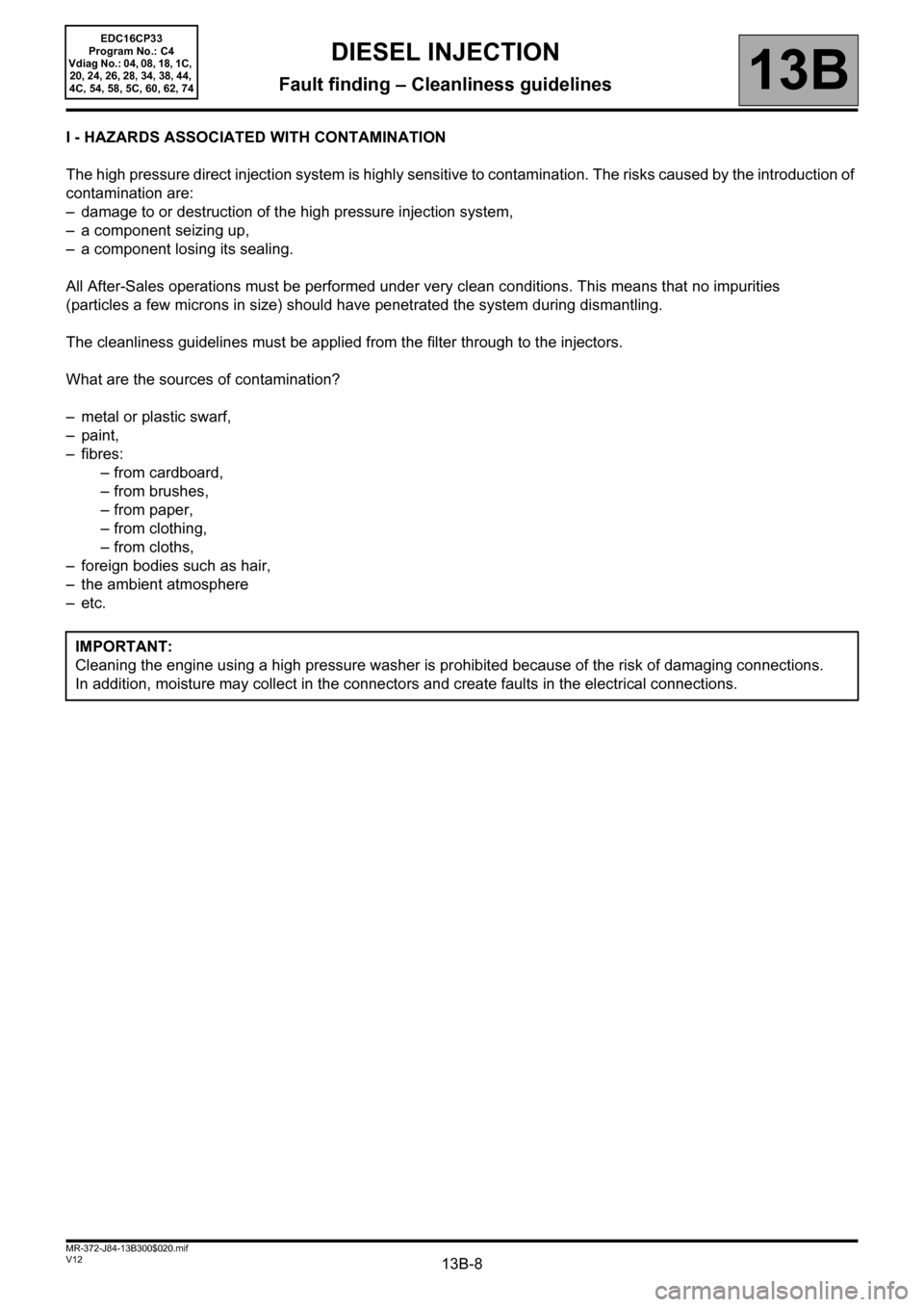
13B-8V12 MR-372-J84-13B300$020.mif
13B
EDC16CP33
Program No.: C4
Vdiag No.: 04, 08, 18, 1C,
20, 24, 26, 28, 34, 38, 44,
4C, 54, 58, 5C, 60, 62, 74
I - HAZARDS ASSOCIATED WITH CONTAMINATION
The high pressure direct injection system is highly sensitive to contamination. The risks caused by the introduction of
contamination are:
– damage to or destruction of the high pressure injection system,
– a component seizing up,
– a component losing its sealing.
All After-Sales operations must be performed under very clean conditions. This means that no impurities
(particles a few microns in size) should have penetrated the system during dismantling.
The cleanliness guidelines must be applied from the filter through to the injectors.
What are the sources of contamination?
– metal or plastic swarf,
– paint,
–fibres:
– from cardboard,
– from brushes,
– from paper,
– from clothing,
– from cloths,
– foreign bodies such as hair,
– the ambient atmosphere
–etc.
IMPORTANT:
Cleaning the engine using a high pressure washer is prohibited because of the risk of damaging connections.
In addition, moisture may collect in the connectors and create faults in the electrical connections.
DIESEL INJECTION
Fault finding – Cleanliness guidelines
Page 9 of 510
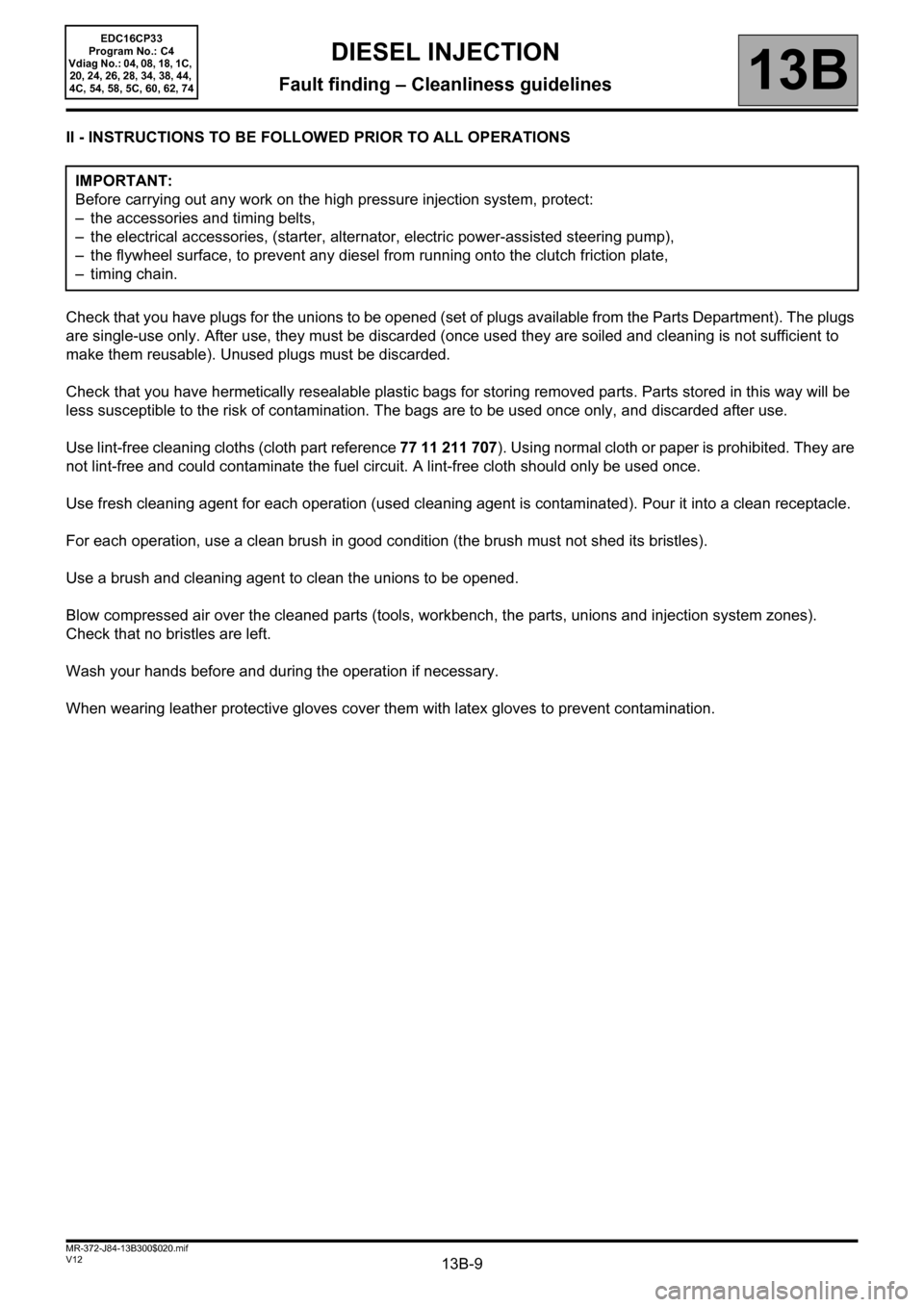
13B-9V12 MR-372-J84-13B300$020.mif
DIESEL INJECTION
Fault finding – Cleanliness guidelines13B
EDC16CP33
Program No.: C4
Vdiag No.: 04, 08, 18, 1C,
20, 24, 26, 28, 34, 38, 44,
4C, 54, 58, 5C, 60, 62, 74
II - INSTRUCTIONS TO BE FOLLOWED PRIOR TO ALL OPERATIONS
Check that you have plugs for the unions to be opened (set of plugs available from the Parts Department). The plugs
are single-use only. After use, they must be discarded (once used they are soiled and cleaning is not sufficient to
make them reusable). Unused plugs must be discarded.
Check that you have hermetically resealable plastic bags for storing removed parts. Parts stored in this way will be
less susceptible to the risk of contamination. The bags are to be used once only, and discarded after use.
Use lint-free cleaning cloths (cloth part reference 77 11 211 707). Using normal cloth or paper is prohibited. They are
not lint-free and could contaminate the fuel circuit. A lint-free cloth should only be used once.
Use fresh cleaning agent for each operation (used cleaning agent is contaminated). Pour it into a clean receptacle.
For each operation, use a clean brush in good condition (the brush must not shed its bristles).
Use a brush and cleaning agent to clean the unions to be opened.
Blow compressed air over the cleaned parts (tools, workbench, the parts, unions and injection system zones).
Check that no bristles are left.
Wash your hands before and during the operation if necessary.
When wearing leather protective gloves cover them with latex gloves to prevent contamination. IMPORTANT:
Before carrying out any work on the high pressure injection system, protect:
– the accessories and timing belts,
– the electrical accessories, (starter, alternator, electric power-assisted steering pump),
– the flywheel surface, to prevent any diesel from running onto the clutch friction plate,
– timing chain.
Page 10 of 510

13B-10V12 MR-372-J84-13B300$020.mif
DIESEL INJECTION
Fault finding – Cleanliness guidelines13B
EDC16CP33
Program No.: C4
Vdiag No.: 04, 08, 18, 1C,
20, 24, 26, 28, 34, 38, 44,
4C, 54, 58, 5C, 60, 62, 74
III - INSTRUCTIONS TO BE FOLLOWED DURING THE OPERATION
As soon as the circuit is open, all openings must be plugged to prevent impurities from entering the system. The
plugs to be used are available from the Parts Department. The plugs must not be reused under any circumstances.
Seal the pouch shut, even if it has to be opened shortly afterwards. The ambient atmosphere carries contamination.
All components removed from the injection system must be stored in a hermetically-sealed plastic bag once the
plugs have been inserted.
Using a brush, cleaning agent, air gun, brush or normal cloth is strictly prohibited once the circuit has been opened.
These items could allow contamination to enter the system.
A new component replacing an old one must not be removed from its packaging until it is to be fitted to the vehicle.